To achieve the best drilling results, it's important to know the right techniques and tips for using diamond core bits. Whether you're experienced or new to construction and drilling, using these bits properly can make your work more efficient and help prevent early wear and tear on your equipment. This comprehensive guide will help you choose the correct bit for the material you're working with and teach you how to manage the pressure and speed during drilling. With this knowledge, you'll be able to perform smooth and precise drilling every time.
Share this Article with Friend or Colleague
Selecting the Right Drilling Equipment
When it comes to drilling in concrete and other construction materials, the choice of drilling equipment that will be used is crucial. The effectiveness of a diamond core bit is significantly influenced by the type of drilling machine used. It's important to select a drill that can accommodate the specific demands of diamond core drilling, which includes the ability to handle the bit’s rigidity and the power requirements of the drilling process. Here, we discuss the considerations for choosing the most suitable drill for your project.
Drill Types
Stand-Mounted Drills are ideal for heavy-duty drilling tasks that require more precision and stability, making them especially useful for creating larger diameter holes or working on hard materials such as reinforced concrete. These drills often offer more power and stability, allowing for straighter holes and minimizing the risk of bit deviation under heavy loads. They also typically feature a water feed system, which is vital for cooling and dust management. However, stand-mounted drills require setup time and can be less portable than other options, making them best used in scenarios where the drilling angle and depth must be precisely controlled.
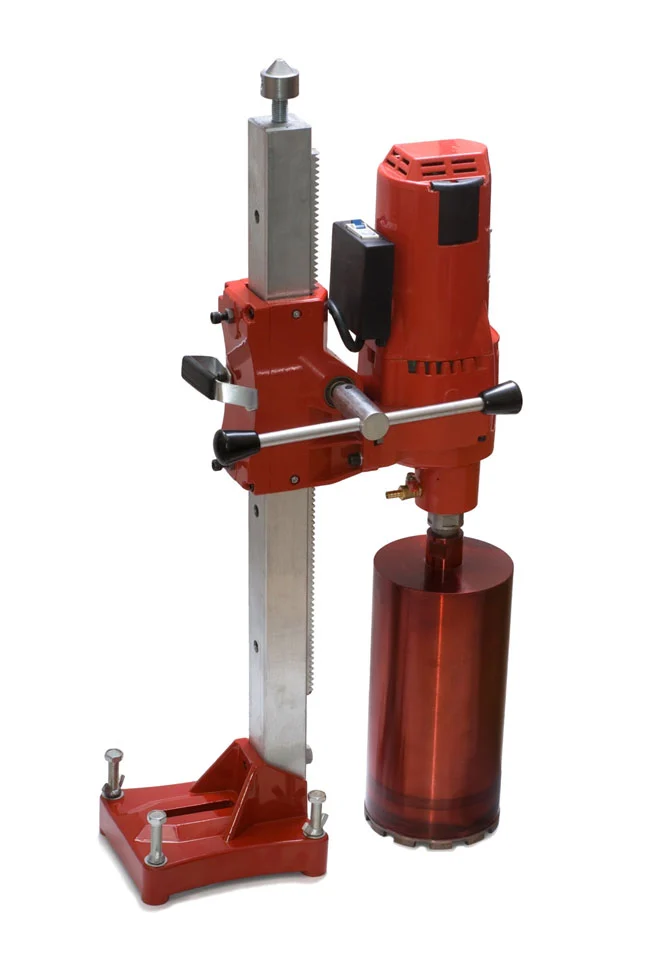
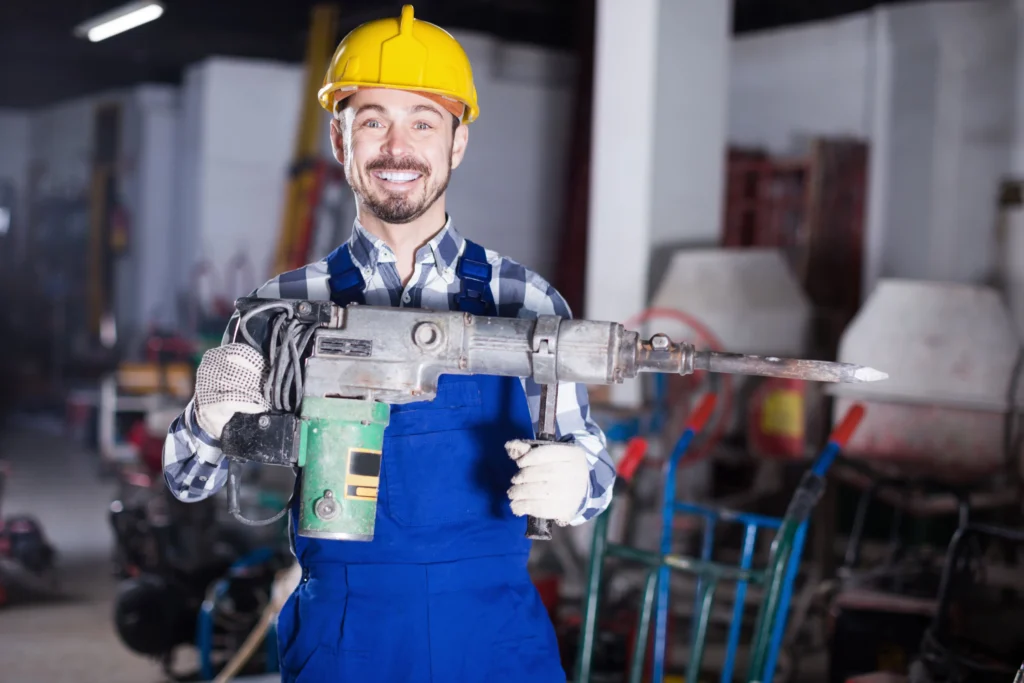
Handheld Drills are more suited for smaller or quick jobs, or in spaces where setting up a stand-mounted drill is impractical. They prove useful for drilling in walls or ceilings and for tasks requiring mobility. These drills offer greater flexibility and ease of use, especially in confined or difficult-to-reach areas, and are typically lighter and easier to maneuver. While handheld drills provide convenience and portability, they may lack the power needed for larger or more challenging projects and require a steady hand to maintain accuracy, as they are more prone to movement during drilling.
Power Requirements
Electric Drills are commonly used due to their high power output and reliability. Suitable for both indoor and outdoor applications, electric drills require access to a power source, which can limit mobility unless extension cords are used. Hydraulic Drills are used for high-strength materials and large-scale construction projects, providing substantial power and endurance suitable for intensive drilling operations. Pneumatic Drills, ideal for environments where electricity use is restricted, such as in wet conditions or where explosive gases may be present, are lighter than hydraulic drills but require a compressed air source.
Additional Features to Consider
The ability to adjust speeds is critical, as different materials and bit sizes require different drilling speeds, known as Speed Control. A Water Feed System is integral for cooling the bit and reducing dust during drilling. Ensure the drill can either accommodate a built-in system or can be adapted for an external water source. Ergonomics are especially important for handheld models; features like padded handles and vibration control can significantly improve operator comfort and safety.
Comparison table that outlines the key features and considerations between stand-mounted and handheld drills for diamond core drilling in construction materials.
Feature/Consideration |
Stand-Mounted Drills |
Handheld Drills |
---|---|---|
Primary Application |
Ideal for precision drilling on large-scale or challenging projects. Suitable for creating larger diameter holes and penetrating hard materials like reinforced concrete. |
Best for smaller, quick jobs, and areas where mobility is crucial. Suitable for drilling in walls, ceilings, and confined spaces. |
Power and Performance |
Generally offer more power, which is necessary for penetrating tougher materials and maintaining stability during drilling. |
Provide sufficient power for light to medium tasks but may struggle with very hard materials or large diameters. |
Stability and Precision |
High stability due to the fixed setup, leading to more accurate and consistent holes. |
Less stable as they rely on the operator’s ability to hold the drill steady, which can affect precision. |
Mobility and Portability |
Less portable and requires setup time. Not ideal for situations where the drill needs to be moved frequently between locations. |
Highly portable, easy to transport and set up, making them ideal for multiple quick jobs across different locations. |
Water Feed System |
Often have integrated water feed systems for efficient cooling and dust management. |
May require external water sources if not integrated, which can add to setup complexity in remote locations. |
Ergonomics and User Fatigue |
User fatigue is less of an issue as the drill is mounted on a stand. |
Higher potential for user fatigue due to the need to manually support and operate the drill, especially important to consider ergonomic designs. |
Safety Features |
Typically safer to operate due to their stability and integrated safety features. |
Require careful handling to maintain safety, especially when used in awkward positions or at heights. |
Typical Use Cases |
Construction sites, large renovation projects, and any application requiring deep or precise holes. |
Home renovations, light construction work, and utility installations where ease of use and speed are valued. |
Cost |
Generally more expensive due to their larger size and additional features. |
Usually less expensive, offering a cost-effective solution for less demanding tasks. |
Challenges of Drilling Concrete of Different Composition & Geographical Region
Drilling through different types of concrete presents challenges due to variations in hardness, material composition, and geographic factors. The composition of concrete, including the type of aggregate, cement, and reinforcements, significantly influences its hardness and how it reacts to drilling. Concrete characteristics also vary by region, influenced by local materials and climate conditions, which further affect the drilling process.
Concrete is made up of cement, aggregate (gravel, sand, or crushed stone), and water. The type and ratio of these components impact the hardness of the concrete. For example, harder aggregates like granite or quartz make the concrete more difficult to drill, while softer materials like limestone are easier to penetrate. The water-to-cement ratio also affects hardness; less water in the mix usually results in a harder, more durable concrete. Reinforced concrete, which includes steel bars (rebar), adds another layer of difficulty. The hardness of steel is much greater than concrete, requiring specialized diamond core bits that can handle both materials without damage.
Geography plays a role in concrete composition. In coastal areas, concrete may include marine aggregates like shells or coral, which can make it more abrasive. In cold climates, additives are often included to help concrete resist freeze-thaw cycles, making it denser and harder. Desert regions, on the other hand, may use local aggregates like sandstone, and concrete in these areas may harden more quickly due to the dry heat. Urban areas often use recycled materials in their concrete mixes, adding variability in hardness, while rural areas may rely on more uniform local aggregates.
Drilling through different types of concrete can pose several challenges. Concrete with hard aggregates like granite or quartz causes increased wear on diamond core bits, leading to more frequent bit changes or the need for specialized bits with tougher bonds. Reinforced concrete requires careful technique when encountering rebar, as the combination of metal and concrete can damage standard diamond bits. Variability in strength is another common challenge, especially when concrete is poured in different batches or under varying conditions, which can cause inconsistent drilling performance. Concrete cured in high temperatures tends to harden more quickly and can be tougher to drill, while exposure to moisture can result in softer, easier-to-drill concrete. Additionally, harder concrete generates more heat and dust during drilling, which can clog the cutting area and reduce efficiency.
To address these challenges, it’s important to choose the right diamond core bit for the specific concrete type. Bits with higher diamond concentration and tougher bonds are better for harder concrete. Adjusting the drill’s RPM and pressure when encountering harder materials or rebar helps avoid overheating and segment damage. Regularly monitoring bit wear during the drilling process ensures optimal performance, especially when dealing with reinforced or variable-strength concrete. Wet drilling is often more effective for harder concrete, as it helps manage dust and heat, while dry drilling can be suitable for softer concrete, particularly in environments where water use is restricted.
Conversely, smaller aggregate sizes, about 3/8 inches in diameter, make the concrete act softer, facilitating faster drilling. The smaller size of the aggregate means there are more points of contact between the aggregate and the cement paste, which might create a less cohesive matrix, allowing for easier penetration by drilling tools.
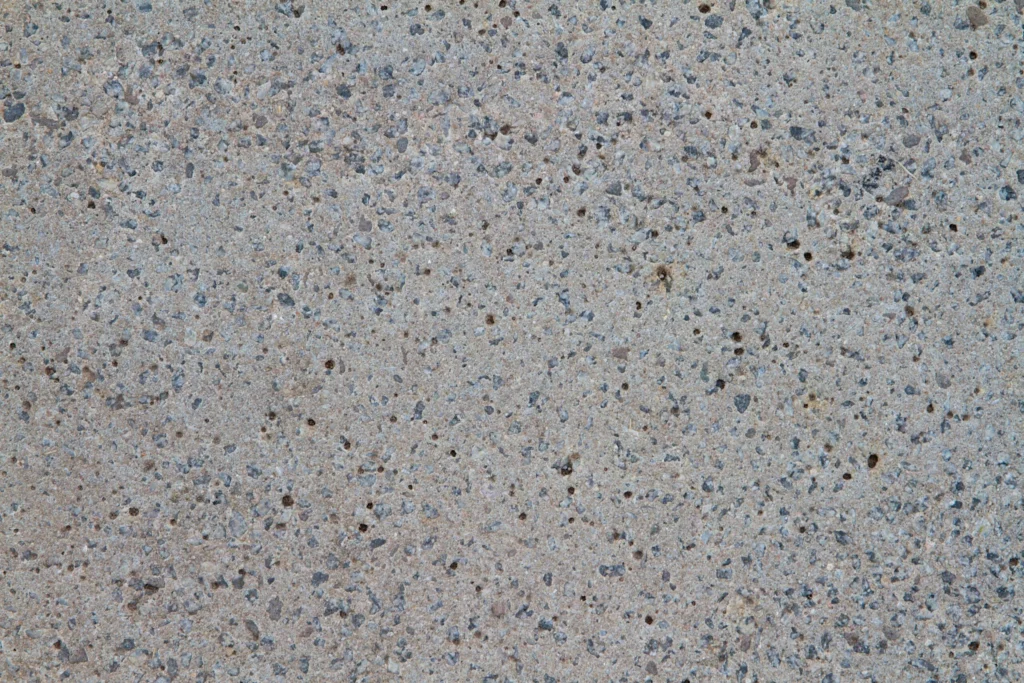
AGGREGATE
Both the size and type of aggregate have a great impact on the overall hardness of concrete. The aggregate can make up as much as 75% of the total volume. As a general rule, larger aggregate tends to make the concrete act harder, slowing drilling process. Smaller aggregate makes the concrete act softer, allowing for faster drilling.
Aggregate Size Impact
Larger pieces of aggregate, typically measuring up to 1.5 inches in diameter, increase the hardness of the concrete. This occurs because the larger stones provide a robust matrix that is more challenging to penetrate, leading to slower drilling speeds. Such aggregates often require more robust drilling equipment with higher torque and power to effectively break through the concrete.
Conversely, smaller aggregate sizes, about 3/8 inches in diameter, make the concrete act softer, facilitating faster drilling. The smaller size of the aggregate means there are more points of contact between the aggregate and the cement paste, which might create a less cohesive matrix, allowing for easier penetration by drilling tools.
Aggregate Type Impact
The mineral composition of the aggregate significantly affects the concrete's hardness. Aggregates are chosen based on availability, cost, and the specific needs of the construction project, including the desired durability and finish of the concrete. Granite, known for its hardness and durability, has a Mohs hardness rating of around 6-7 and is commonly used in high-traffic areas or structures requiring high strength. Limestone, typically softer than granite, has a Mohs hardness of about 3-4, is easier to drill but provides less wear resistance. Sandstone, with a Mohs hardness of 6-7, similar to granite, is also durable but varies significantly in density and strength based on its composition and the depth at which it was quarried. Gravel, often used as a coarse aggregate, has a hardness that depends on the types of rocks included, generally ranging from 6-7 on the Mohs scale.
The type of diamond core bit used must correspond to the hardness of the aggregate. For harder aggregates like granite, soft bond type diamond core bits preferable for their ability to handle tough materials. Adjustments in drilling speed and the power of the drilling equipment may be necessary depending on the aggregate size and type. Harder aggregates require slower speeds to prevent overheating and wear on the drill bits. The use of coolants can help in reducing the temperature and removing debris during the drilling process, which is particularly important in harder concrete to prolong the life of the drill bits.
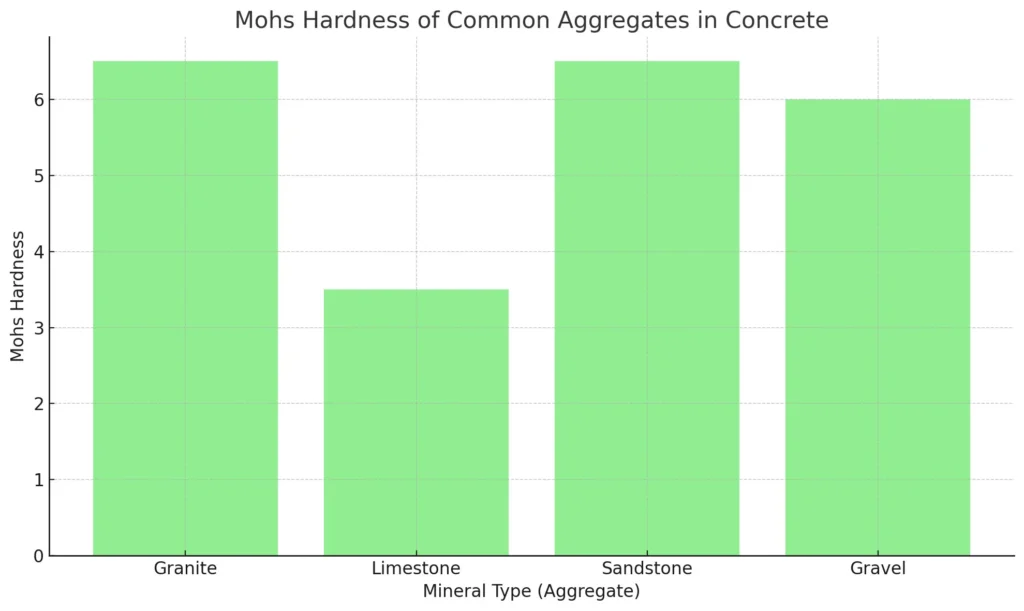
Differences between large and small aggregates
ASPECT |
LARGE AGGREGATE |
SMALL AGGREGATE |
---|---|---|
Size |
Up to 1.5 inches in diameter |
About 3/8 inches in diameter |
Concrete Hardness |
Increases concrete hardness; acts as a robust matrix, slowing drilling |
Makes concrete act softer, allowing for faster drilling |
Drilling Speed |
Slower due to increased hardness and resistance |
Faster due to less cohesive matrix |
Drill Bit Type |
Requires more robust drilling equipment (e.g., high-torque drill bits) |
Can use standard drilling equipment |
Typical Use |
Ideal for high-strength applications and areas with high traffic |
Suitable for projects requiring less wear resistance |
Detail the types of minerals commonly used for aggregate and their relative hardness:
MINERAL TYPE |
COMMON USE |
MOHS HARDNESS |
---|---|---|
Granite |
High traffic areas, structures requiring high strength |
6-7 |
Limestone |
General construction where less wear resistance is adequate |
3-4 |
Sandstone |
Diverse applications depending on specific stone qualities |
6-7 |
Gravel |
Coarse aggregate, varied applications depending on rock type |
Dependent on rock type, typically 6-7 |
Mounting the Diamond Core Bit
Mounting a diamond core bit correctly is essential for achieving optimal drilling performance and maintaining safety. Here are the detailed steps and considerations for ensuring the bit is properly mounted onto your drill.
Step 1: Select the Correct Bit Adapter
Start by ensuring the core bit’s arbor is compatible with your drill’s chuck or adapter. If the sizes do not match, you will need a bit adapter. Adapters are crucial for facilitating the connection between the drill and the bit, and they come in various types to accommodate different thread sizes and shank types. Selecting the right adapter is the first step toward ensuring the stability and efficacy of the drilling operation.
Step 2: Inspect the Bit and Drill
Before mounting, thoroughly inspect the diamond core bit for any signs of damage such as worn segments, visible cracks, or any form of distortion. Damaged bits can compromise drilling accuracy and safety. Similarly, inspect the drill’s chuck and mounting area to ensure there is no debris or damage that could impair the bit’s secure attachment. Cleaning both the bit and the drill ensures a clean, secure fit, which is essential for accurate drilling.
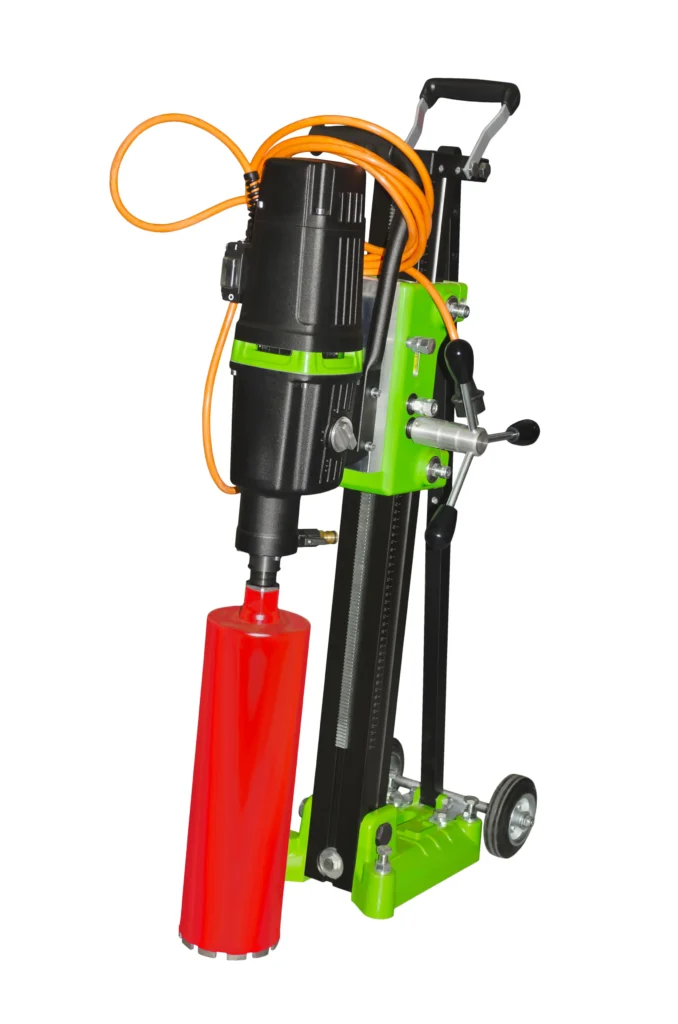
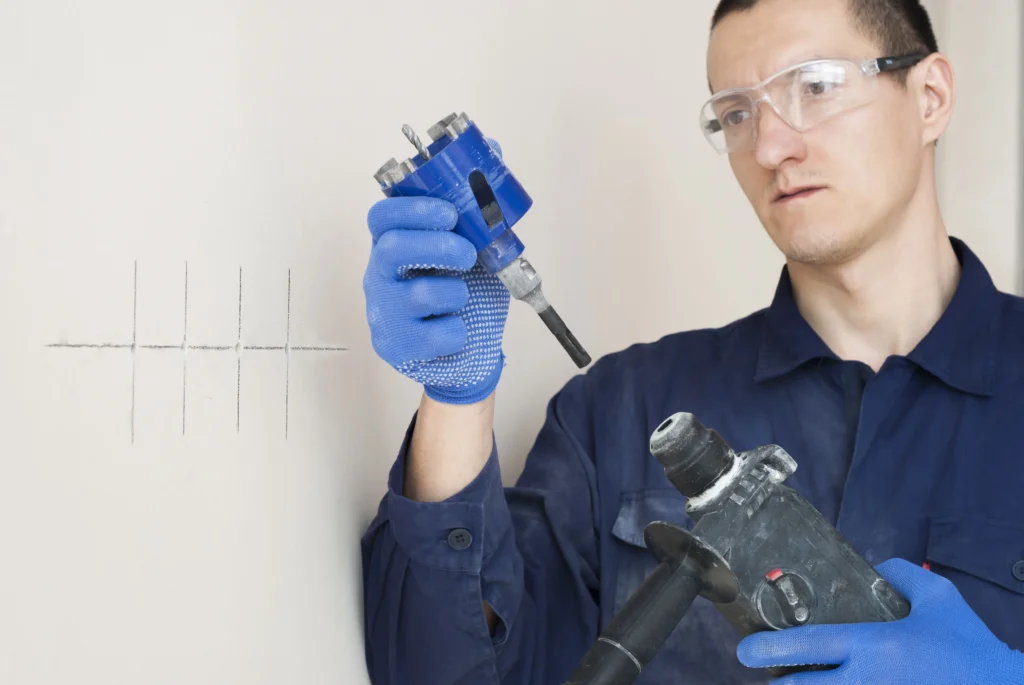
Step 3: Inserting the Bit
Align the core bit carefully with the drill’s chuck, ensuring it is perfectly perpendicular. This alignment is crucial as it affects the drill’s ability to produce a straight hole. Insert the bit into the chuck or adapter, pushing it in as far as possible to maximize the surface contact area. This increases the bit’s stability and the efficiency of power transmission from the drill to the bit.
Step 4: Securing the Bit
Use the appropriate tools, like a chuck key, to tighten the chuck or adapter according to the manufacturer's specifications. While tightening, ensure that it is secure but avoid overtightening which could damage the bit or the drill. After securing the bit, perform a manual check by tugging gently to ensure it is firmly in place. This step is crucial for verifying that the bit will remain stable during operation, thus preventing hazardous situations.
Step 5: Performing a Test Run
Once the bit is mounted, conduct a test run on a scrap piece of material similar to the material you will be working on. This test is vital for verifying that the bit is correctly mounted and functioning as expected. Monitor the drill for any signs of wobbling or vibrations, which could indicate an issue with the mounting. If you detect any irregularities, stop drilling immediately, recheck the tightness and realignment of the bit, and adjust as necessary.
Step 6: Continuous Monitoring
Maintain vigilance by regularly checking the bit’s tightness and alignment throughout the drilling process, especially during extensive or challenging projects. Vibration and mechanical stress can sometimes loosen the bit, posing risks to both the operator and the project. Implement routine checks to catch and correct any loosening promptly.
Starting the Hole: Effective Techniques for Diamond Core Drilling
Initiating the drill hole correctly is crucial for achieving precision and efficiency when using diamond core bits. Properly starting the hole involves beginning at a lower speed to establish control and precision, which ensures the bit does not wander or slip off the mark. This initial low-speed drilling helps stabilize the bit and allows it to start cutting a groove into the material without excessive pressure, which can cause damage to both the bit and the material.
Once the hole has been started and a shallow depth is achieved, it's important to gradually increase the drill speed. This adjustment should be based on the hardness and abrasiveness of the material being drilled. Hard materials generally require slower speeds to minimize the heat generated by friction, which can degrade the diamond segments. Conversely, for less abrasive materials, the speed can be increased cautiously to enhance drilling efficiency while continuously monitoring for signs of overheating, such as discoloration of the bit or excessive dust production.
Maintaining a steady, gentle pressure during the drilling process is key. The objective is to let the bit’s own weight do the majority of the work without forcing it, as pushing too hard can lead to premature wear or even breakage of the bit, especially when dealing with hard materials like reinforced concrete. Ensuring a continuous water feed throughout the drilling helps in cooling the bit and removing debris, which facilitates smoother cutting and prolongs the life of the bit.
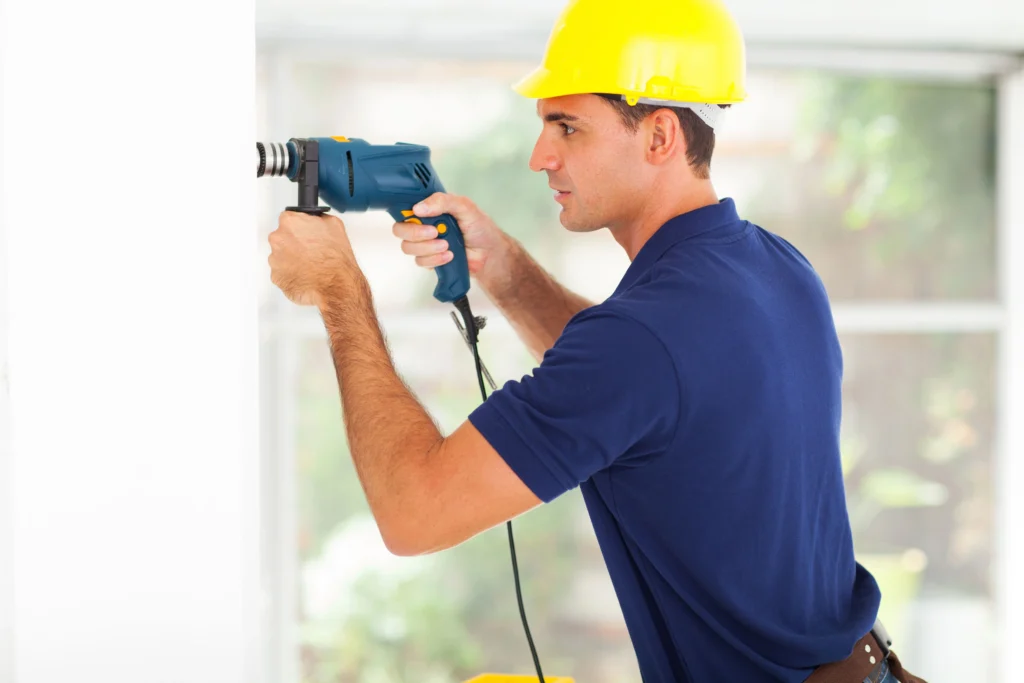
Periodically pausing to inspect the bit and the hole is also vital. These checks help to confirm that the bit is not wearing unevenly and that the hole is being drilled at the correct angle and diameter. If challenges such as bit stalling or binding occur, it’s important to stop drilling immediately, withdraw the bit slightly, check for obstructions or damage, and then proceed carefully with adjusted settings to accommodate the changed conditions.
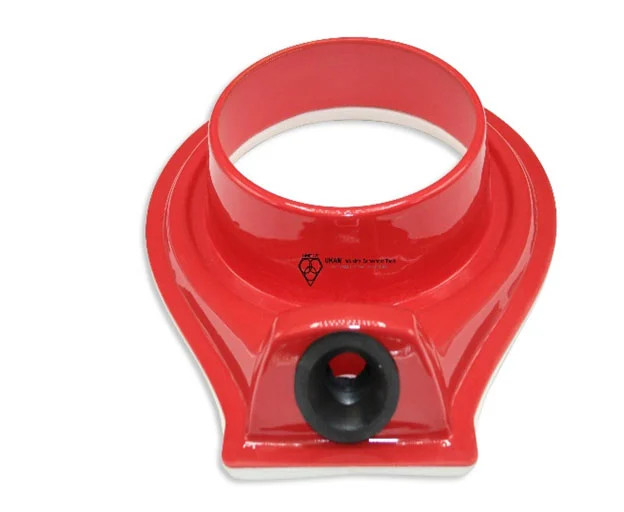
Using Template to Help Start the Hole
When drilling into concrete with diamond core bits, starting the hole accurately can be one of the most challenging steps, especially on hard or smooth surfaces. To help with precision and ensure a clean, controlled entry, using a drilling template or guide is an effective solution. A template stabilizes the drill bit at the beginning of the operation, preventing it from wandering or slipping on the surface.
Concrete, particularly when smooth or polished, doesn’t provide much friction for the bit to grip, making it difficult to start drilling without a guide. A template acts as a guide for the diamond core bit, holding it in place as the bit begins to cut into the surface. This ensures that the drill enters the material at the correct location and angle, which is especially important when precision is required, such as in structural work or installations.
The template itself can be made of various materials, such as wood, metal, or plastic, and features a hole slightly larger than the diameter of the core bit. The template is positioned over the spot where the hole will be drilled and secured to the concrete surface. This can be done by clamping or temporarily attaching the template to the concrete, ensuring it doesn’t move while the bit is starting.
Once the bit begins to penetrate the concrete, the template’s role becomes less critical as the bit establishes its path. At this point, the template can often be removed, allowing the operator to continue drilling without it. This method is particularly useful for handheld drills, where stability is more difficult to maintain than with larger rig-mounted systems.
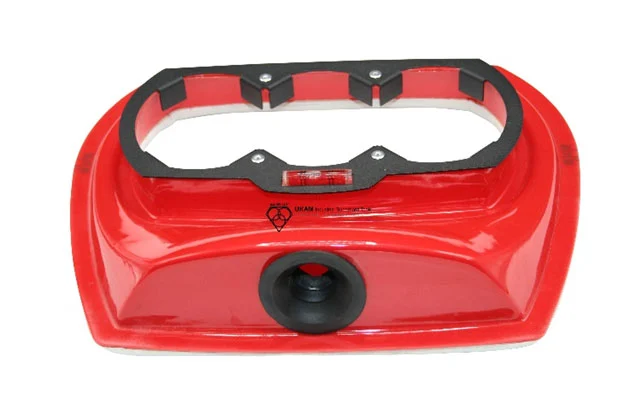
Using a template also minimizes the risk of damaging the diamond core bit at the start of the drilling process. When a bit wanders or slips, it can cause uneven wear on the diamond segments, reducing their effectiveness and shortening the bit’s lifespan. By guiding the bit into the material smoothly, a template helps ensure that the diamond segments wear evenly, leading to more efficient drilling and longer tool life.
For larger or more complex drilling operations, templates can also be customized to accommodate multiple holes or specific patterns, increasing efficiency and ensuring uniform results across a project.
Using with Coolant
Using water or coolant is essential in diamond core drilling when working with concrete and other construction materials. It serves multiple critical functions, including cooling the diamond bit to prevent overheating, reducing dust production to enhance worker safety, and removing debris from the cutting area for smoother operation.
Water cools the diamond bit by dissipating the intense heat generated from the friction during drilling. This not only maintains the integrity of the bit but also allows for more efficient cutting. The presence of water is crucial in binding dust particles generated during the drilling process, preventing them from becoming airborne which is beneficial in enclosed spaces or urban environments where dust can be a significant health hazard. Additionally, as the bit penetrates the material, it produces debris or slurry which can clog the cutting area and impede drilling progress. Water helps wash away this slurry, keeping the cutting area clear.
Many modern drills come equipped with built-in water feed systems which deliver a consistent and controlled flow of water directly to the bit, optimizing cooling and dust control. For drills without integrated water feed systems, an external water source, such as a portable water tank with a pump or water swivel adapter, can be used. This setup allows flexibility in adjusting water flow and can be adapted to various drilling rigs, although it requires more management during operations.
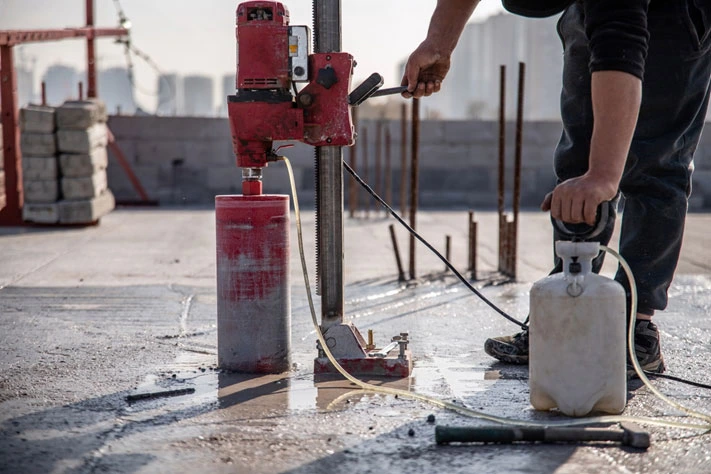
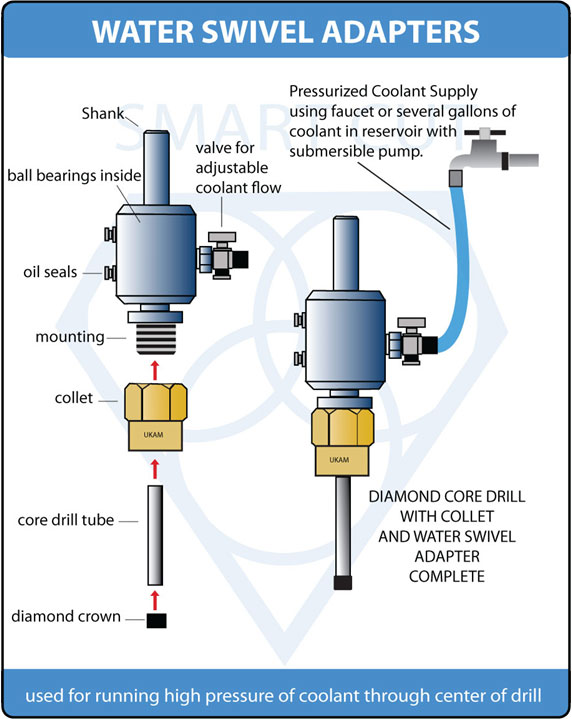
Using With Water Swivel Adapter
In many cases, drilling rigs or handheld equipment do not have built-in capabilities to run coolant through the center of the core bit. This is where water swivel adapters come in, allowing operators to introduce coolant directly through the bit, even on equipment without this feature.
Water swivel adapters are specially designed to connect between the drill motor and the diamond core bit, enabling water or coolant to flow through the center of the bit. This helps to effectively cool both the bit and the material being drilled. By running coolant through the center, heat generated from friction during drilling is dissipated more efficiently, reducing the risk of overheating, which can cause rapid wear on the diamond segments and compromise the integrity of the bit. Additionally, the constant flow of water flushes out debris and slurry, keeping the cutting area clear and improving the drilling speed and precision.
Using a water swivel adapter offers significant advantages when drilling concrete, especially in demanding applications like reinforced concrete or harder materials. Coolant applied through the center of the bit reaches the cutting surface more directly, leading to better cooling compared to simply spraying water externally. This is particularly important in deep hole drilling, where heat and debris can accumulate, potentially causing the bit to bind or stall. The adapter ensures that water or coolant is delivered exactly where it’s needed, improving bit performance and extending its life.
When working with handheld drilling equipment or smaller rigs that lack built-in coolant systems, a water swivel adapter is a simple, effective solution to achieve the necessary cooling. The adapter is easy to attach and works with most standard diamond core bits, making it a versatile tool for operators who need to perform wet drilling on portable or non-specialized equipment. Additionally, it is highly portable, making it suitable for jobsites where more complex cooling systems may not be feasible.
For optimal results when using a water swivel adapter, it's important to ensure that the water flow rate matches the size of the bit and the material being drilled. Larger bits or harder materials require higher water flow to keep the bit cool and flush out debris. Regular checks to ensure that water is reaching the cutting edge of the bit are essential. Without proper flow, heat can still build up, defeating the purpose of the coolant system. Operators should also be mindful of water pressure, as too low a pressure may be ineffective, while excessive pressure could damage the equipment.
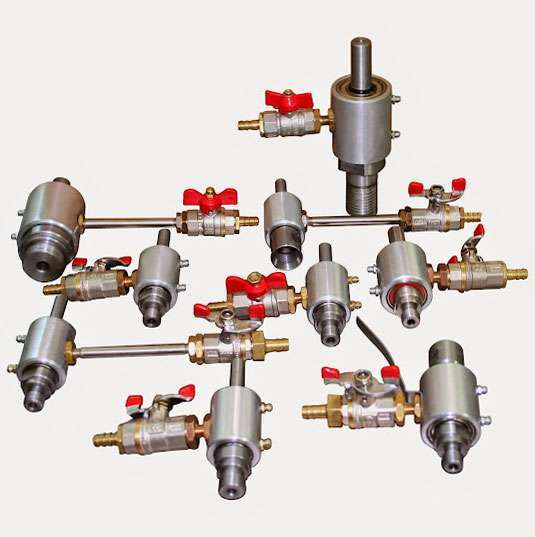
Adjusting Coolant Flow
When using water or coolant, it’s important to adjust the water flow based on the material's hardness and the bit's diameter, with softer materials and larger bits typically requiring more water. Regular checks to ensure that water is reaching the tip of the bit and not just running off the surface are crucial for effective cooling and dust suppression. Additionally, in sensitive environments or locations where water runoff could pose a problem, measures should be taken to collect and recycle the water or ensure its disposal complies with local regulations.
In colder conditions, adding antifreeze agents to the water can prevent it from freezing, which could block the water feed system and halt drilling operations. Managing water use effectively not only extends the life of diamond core bits but also enhances operational efficiency and safety, maintaining compliance with health and safety standards.
Dry Drilling
Dry diamond core bits are specialized diamond core bit designed for drilling operations where water use is impractical. These bits are perfect for various applications, particularly in construction and renovation projects requiring quick, clean, and water-free operations. Proper use of dry diamond core bits involves ensuring the drill is compatible with the bit, securing it firmly in the drill chuck, and starting the drill at a low speed to establish the cutting path. As the bit begins to penetrate the surface, gradually increase the speed and apply steady, moderate pressure. Periodically withdrawing the bit helps remove accumulated dust and debris, reducing friction and preventing overheating.
Dry diamond core bits are best used on softer masonry materials like bricks, limestone, and some sandstones, which do not require the cooling effect of water. They are ideal for indoor environments where moisture could damage electrical systems or other installations and are particularly useful for quick or shallow drilling tasks where setting up a water supply would be cumbersome.
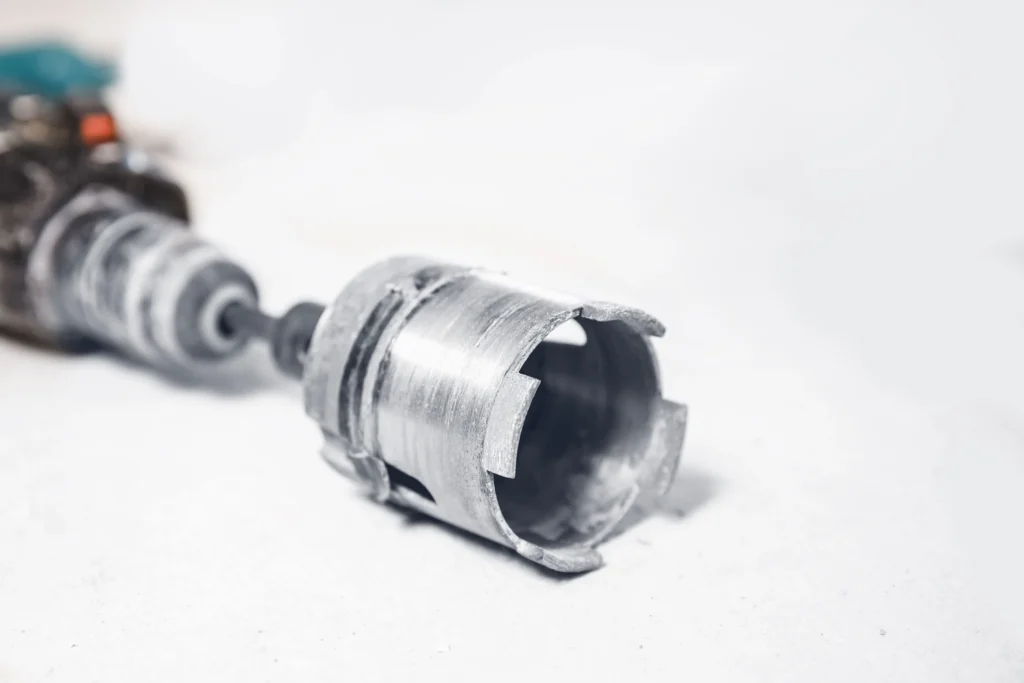
Using dry diamond core bits in indoor construction sites or during renovation projects in residential or commercial buildings can simplify operations by eliminating the mess and hazard of water. The primary benefit of these bits is that they do not require water, simplifying both setup and cleanup, and allowing for rapid deployment. These bits also ensure precise cuts with minimal dust, enhancing efficiency and cleanliness in environments where these factors are priorities.
However, the main challenge with dry diamond core bits is managing the heat generated during drilling, as there's no water to cool the bit. This increases the risk of overheating and potentially damaging both the bit and the material. Additionally, dry drilling produces a significant amount of dust, posing health hazards if not managed with adequate ventilation and respiratory protection. When used correctly, dry diamond core bits offer an efficient alternative to wet drilling, especially suitable for quick operations or situations where maintaining a clean work environment is crucial.
Table outlining the differences between wet and dry drilling when using diamond core bits:
Feature |
Wet Drilling |
Dry Drilling |
---|---|---|
Cooling Method |
Uses water to cool the diamond bit, effectively dissipating heat generated from friction during drilling. |
Relies on air cooling, which is less effective than water, increasing the risk of overheating the bit. |
Dust Control |
Water binds dust particles, preventing them from becoming airborne and reducing health hazards, especially in enclosed spaces. |
Produces significant amounts of dust, requiring careful management with adequate ventilation and respiratory protection. |
Debris Removal |
Water helps wash away slurry and debris from the cutting area, keeping the drill path clear for smoother operation. |
Debris must be manually cleared by periodically withdrawing the bit, which can slow down the drilling process. |
Equipment Requirements |
Often requires built-in or external water feed systems to deliver a consistent and controlled flow of water. |
Does not require water feed systems, simplifying setup but necessitating frequent stops to manage heat and debris. |
Material Suitability |
Ideal for a wide range of materials, including harder and more abrasive materials like reinforced concrete. |
Best used on softer masonry materials such as bricks, limestone, and some sandstones that do not require water cooling. |
Operational Flexibility |
Requires access to water, which can complicate setups in certain environments but provides more flexibility in material handling. |
Offers greater flexibility in environments where water use is impractical, such as indoor areas sensitive to moisture. |
Environmental Considerations |
Needs measures to manage water runoff and disposal, particularly in sensitive environments; antifreeze may be added in cold conditions. |
Eliminates issues with water runoff and disposal, making it suitable for environmentally sensitive areas. |
Health and Safety |
Reduces airborne dust, enhancing operator safety but requires management of water for safe handling and disposal. |
Increased dust can pose health risks if not properly managed with dust extraction systems and personal protective equipment (PPE). |
Setup and Cleanup |
Generally involves more complex setup and cleanup due to the need for water supply and handling of wastewater. |
Simplifies setup and cleanup as no water is involved, reducing the operational mess and hazards associated with water. |
Heat Management |
Effective cooling with water reduces the risk of overheating the bit, allowing for longer drilling periods without damage. |
Heat management is crucial; without water, the bit can quickly overheat, requiring careful monitoring and frequent pauses. |
Running High Pressure of Air through Center for Coolant
Using a water swivel adapter with high-pressure air as a coolant for diamond core bits is an effective solution for drilling when water-based cooling isn't feasible. High-pressure air provides several benefits, particularly in environments where water use could be problematic, such as indoor construction sites or areas where moisture could damage nearby materials. One of the primary advantages of using high-pressure air is its ability to manage heat generated during drilling. By running air through the center of the diamond core bit, heat is dissipated efficiently without introducing moisture. This makes it ideal for sensitive environments while still preventing overheating, which can wear down the bit prematurely.
Another significant benefit of using air is the way it clears debris and dust from the drilling area. Concrete and other materials can generate a lot of dust during drilling, especially when water isn't used to bind the particles. High-pressure air helps blow debris out of the hole, ensuring a clearer and smoother path for the drill bit. This not only keeps the drilling area clean but also enhances the speed and precision of drilling by maintaining better contact between the bit and the material.
The absence of moisture also means that this method is cleaner, as there's no water runoff to manage. It can extend the life of the diamond core bit by reducing heat buildup, while the continuous flow of air ensures that dust and debris do not accumulate, which can otherwise cause the bit to bind or wear unevenly. When using handheld equipment or rigs without integrated cooling systems, the water swivel adapter allows the operator to benefit from cooling and debris removal without the need for more complex machinery.
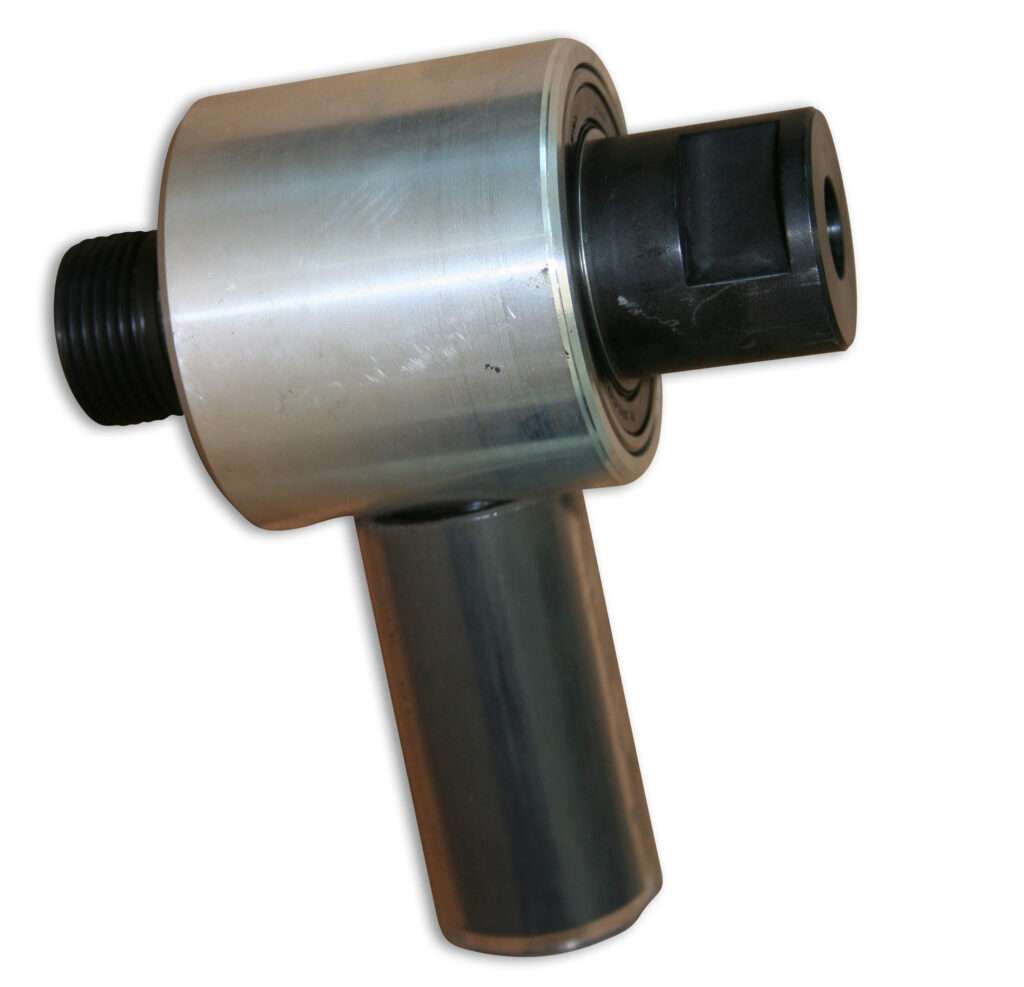
However, there are some challenges to consider. Using air as a coolant produces a lot of dust, which can become a health hazard if not properly managed. It's essential to implement dust extraction systems and ensure that operators are equipped with appropriate personal protective gear, such as respirators. In settings where air quality must be maintained, such as indoor environments, additional filtration systems might be necessary to keep the dust under control.
Furthermore, the use of high-pressure air requires a reliable air compressor that can maintain sufficient pressure throughout the drilling operation. The compressor must be matched to the job's demands, particularly when drilling through harder materials or using larger bits. Regular maintenance of both the air swivel adapter and the air compressor is crucial to ensure optimal performance and prevent interruptions during drilling.
This method also requires careful monitoring of the air pressure to ensure it's not too low to be ineffective or too high, which could potentially damage the equipment. Adjustments in pressure should be made based on the material being drilled and the size of the bit to ensure efficient cooling and debris removal.
Heat Management
Heat management is crucial for both wet and dry diamond core drilling, even though the presence of water in wet drilling helps with cooling. Effective heat management in wet diamond core drilling involves ensuring a continuous and adequate flow of water, which not only cools the diamond core bit but also assists in flushing out the slurry created from drilling. This prevents the accumulation of material that can cause friction and increase heat.
The speed at which the drill operates also significantly impacts heat management. Even with the cooling effects of water, operating the drill at too high a speed can generate excessive heat that water may not adequately dissipate, especially when drilling deeper holes or harder materials. Adjusting the drill speed to an optimal level is crucial for maintaining a balance between efficiency and prolonging the life of the bit.
It's important to monitor the water flow continuously during drilling to ensure that it remains consistent and adequate. Any interruptions in water flow can lead to rapid increases in temperature, potentially damaging both the bit and the material being drilled. Checking for blockages or equipment malfunctions that could impede water flow is essential for preventing overheating.
Like in dry drilling, the amount of pressure applied during wet drilling affects heat generation. Excessive pressure can counteract the cooling effect of the water, leading to increased friction and heat. Maintaining a steady, moderate pressure helps the bit to cut efficiently without creating undue stress and heat.
In more advanced setups, temperature sensors can monitor the heat at the drill bit, providing critical data to help prevent overheating. This is particularly useful when working with very hard materials or in challenging drilling scenarios where heat generation is significant.
Experienced operators can also adjust their drilling techniques based on changes in the feel of the drill and the behavior of the material being cut. Sensing changes in vibration or resistance can indicate when adjustments in water flow, speed, or pressure might be necessary to manage heat effectively.
Regular inspections and maintenance of both the drill and the bit ensure that all components function correctly, maximizing cooling efficiencies. Worn bits or malfunctioning drills can lead to inefficient cutting and increased heat generation, highlighting the importance of routine checks.
Dust Management
Effective dust management is crucial during diamond core drilling, especially in dry drilling scenarios where dust is not naturally suppressed by water. Managing dust not only ensures a cleaner work environment but also protects the health of workers, maintains high visibility for precision drilling, and extends the longevity of drilling equipment.
Dust generated during drilling, particularly silica dust from materials like concrete and stone, poses serious health risks. Inhalation of respirable crystalline silica can lead to severe respiratory diseases, including silicosis and lung cancer. Therefore, controlling dust right at its source is vital for safety.
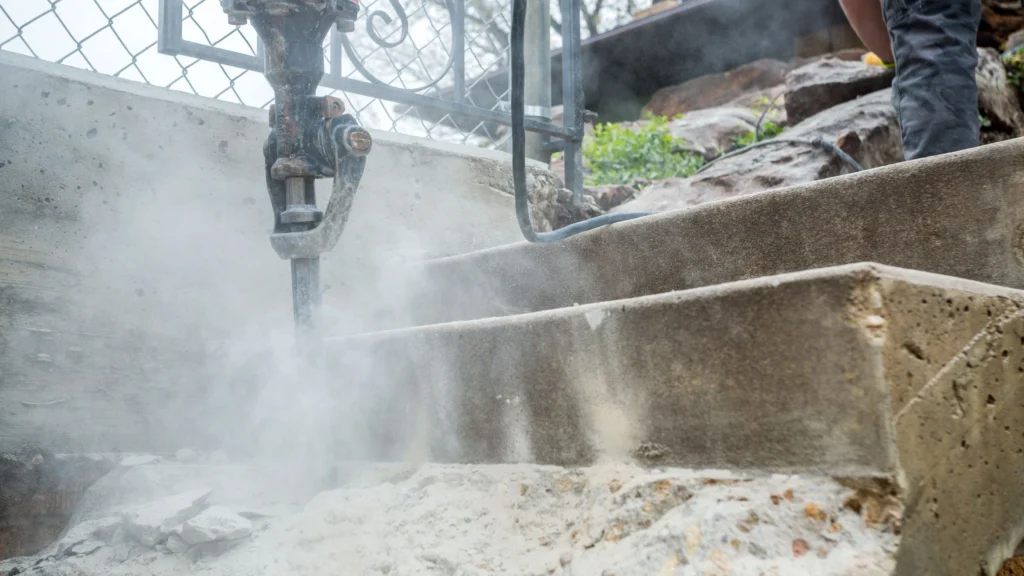
Using dust extraction systems is one of the most efficient ways to manage dust. These systems directly vacuum dust from the point of creation, keeping the air clean and the work area clear. Portable dust extractors can be directly attached to the drilling equipment, ensuring that dust is collected as it is produced.
Maintaining good ventilation is crucial, especially in enclosed spaces. Employing air movers or exhaust fans helps disperse and remove airborne particles from the drilling area. Additionally, regular cleaning with industrial vacuums or other equipment prevents dust build-up, keeping the site safe and enhancing operational efficiency.
It's essential for all operators and nearby workers to wear appropriate personal protective equipment (PPE), including respiratory protection like N95 masks or respirators, goggles or safety glasses, and protective clothing. This PPE guards against harmful dust inhalation and protects eyes and skin from flying particles.
When possible, opting for wet drilling techniques can significantly reduce dust creation. Water binds the dust particles, preventing them from becoming airborne and is particularly effective for controlling silica dust when drilling materials like concrete and stone.
Adjusting drilling speed can also help manage dust production. Higher speeds tend to generate more dust, so optimizing the drill speed according to the material hardness and the bit type can reduce dust levels. Employing correct drilling techniques, such as peck drilling where the bit is periodically withdrawn from the hole, helps clear dust from the drill path and further minimizes airborne particles.
Drilling Speed and Pressure
Properly adjusting the drilling speed and pressure is essential for optimizing the performance and extending the lifespan of diamond core bits, as well as preserving the condition of the drill itself. The material hardness significantly impacts how the drill should be operated to achieve optimal results.
Drilling Speed
Drilling speed is critical for maximizing the performance and durability of diamond core bits. When drilling into hard materials like reinforced concrete or granite, it is essential to use slower speeds. This helps reduce the heat generated from friction, which can prematurely wear down the diamond segments or even cause thermal damage. Slower speeds ensure the structural integrity of the bit is maintained, providing consistent and efficient cutting while minimizing the risk of chipping or damaging the material.
In contrast, softer materials such as soft stone or lightly reinforced concrete can handle higher drilling speeds. This can speed up the drilling process safely since these materials offer less resistance and generate less heat. However, it is crucial to control the drilling speed to avoid inefficiencies. Excessive speed may cause the bit to skip or jump, impacting the precision of the hole and potentially creating safety hazards if the drill becomes difficult to manage.
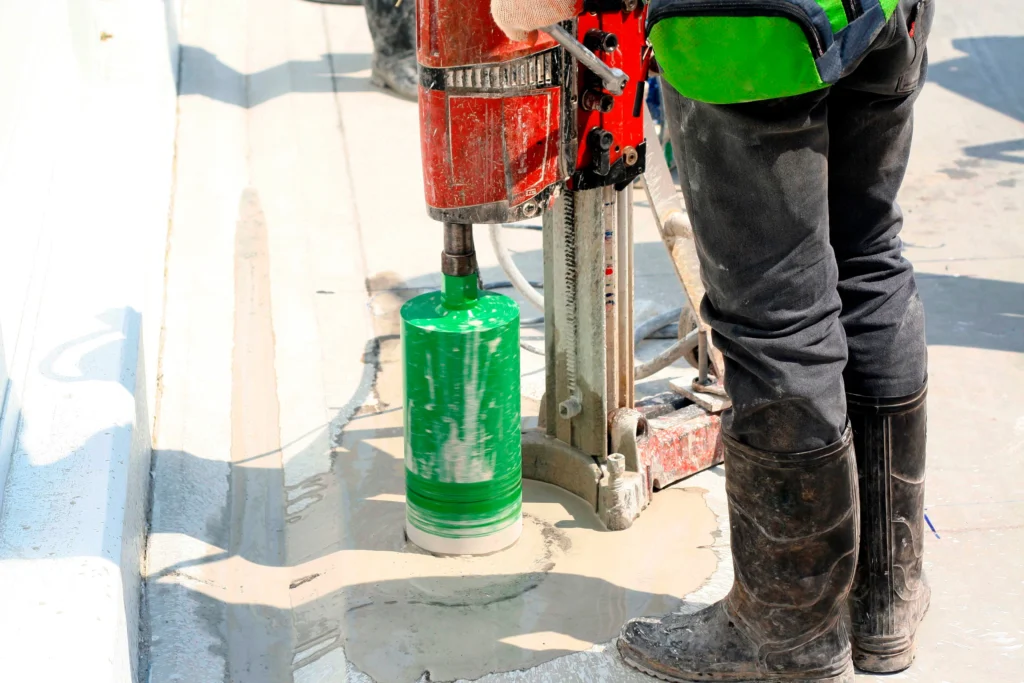
Inappropriate drilling speeds—whether too slow or too fast—can compromise the performance of the diamond core bit. A speed that is too low may not effectively penetrate certain materials, unnecessarily prolonging the drilling process and causing operator fatigue and equipment stress. Conversely, excessively high speeds can lead to overheating, potentially damaging both the bit and the drill motor.
Starting at a moderate speed and adjusting based on feedback from the material and the drill's performance is advisable. Listening for changes in the drill's sound and monitoring the ease or difficulty of penetration can provide insights into whether speed adjustments are necessary. Many modern drills come equipped with variable speed settings and feedback systems that automatically adjust based on detected resistance and torque. This adaptability is crucial for optimizing drilling efficiency and protecting the equipment.
Moreover, the diameter of the drill bit also plays a critical role in determining the appropriate speed. Larger diameter bits typically require slower speeds due to the increased surface area in contact with the material, generating more friction and heat. Smaller bits, however, can be operated at higher speeds because they have less surface contact and are less prone to heat buildup.
The type of drilling equipment used should also be considered. Advanced drills with variable speed settings and feedback systems can automatically adjust the speed to match the resistance and torque during drilling. These features allow for real-time adjustments that enhance the drilling process and prevent damage to the equipment.
Managing drilling speed effectively not only prolongs the life of the diamond core bits but also ensures safety during drilling operations. Incorrect speeds can cause the bit to seize or stall, leading to dangerous kickback scenarios that pose risks to the operator.
The RPM (Revolutions Per Minute) of a diamond core bit is a crucial factor that directly influences its cutting performance, efficiency, and the quality of the drilled hole in concrete and construction applications. The RPM must be adjusted based on the diameter of the core bit, the material being drilled, and the power of the drilling equipment. An optimal drilling speed ensures effective cutting, prolongs the bit's lifespan, and prevents overheating or premature wear.
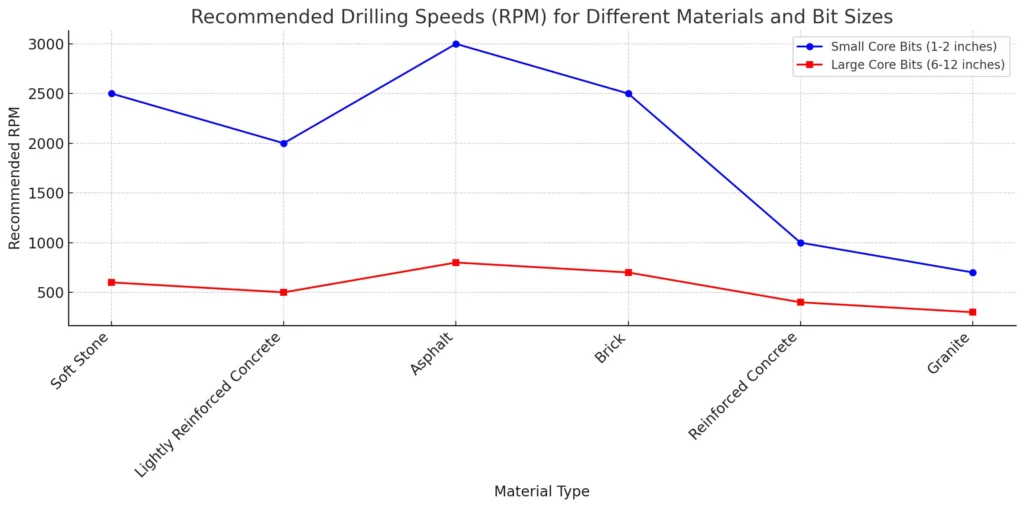
One critical aspect when determining the correct RPM for a diamond core bit is the bit's diameter. Generally, as the diameter increases, the RPM should decrease. Larger core bits cover more surface area, creating more friction and heat during drilling, so they require slower speeds to maintain effective cutting without generating excessive heat.
For instance, a small-diameter core bit (e.g., 1-2 inches) can operate at higher RPMs, typically between 1,000 to 3,000 RPM, depending on the material and equipment. However, larger core bits with diameters of 6-12 inches may need much lower speeds, typically between 300 to 600 RPM, to avoid overheating and ensure steady material removal.
Regarding the material type, harder materials like reinforced concrete and granite necessitate slower drilling speeds to prevent rapid wear and overheating. Lower RPMs, often in the range of 300 to 600 RPM for larger bits, are advisable for maintaining cutting efficiency. Softer materials like asphalt and brick can tolerate higher speeds, facilitating faster material removal without significant wear on the bit.
The drilling depth also impacts the optimal RPM. For shallow drilling, higher RPMs can be effective because the bit does not generate excessive heat over a short distance. However, as the depth increases, especially when drilling through thick materials, heat buildup becomes a concern, necessitating a reduction in RPM to ensure efficient cutting without excessive heating.
Wet drilling, where water is used to cool the diamond core bit and remove debris, generally allows for slightly higher RPMs since the cooling effect prevents the bit from overheating. This method is preferred in most construction applications, especially when drilling through tough materials like reinforced concrete. Conversely, in dry drilling where no water is used, the core bit must operate at lower RPMs to prevent overheating and rapid wear.
Using incorrect RPM can lead to excessive wear, overheating, slower drilling speeds, or chipping and uneven cuts. Higher RPMs might cause premature wear due to excessive heat and friction, reducing the lifespan of the bit and increasing operational costs. Conversely, too low RPMs for the size of the core bit or material type can make the drilling process inefficient, leading to slower cutting speeds and longer project durations.
Finally, the experience and skill of the operator are crucial in determining the ideal RPM. Experienced operators can adjust RPMs on the fly, responding to changes in conditions such as increased friction, the presence of rebar, or deeper drilling. The ability to adapt RPM based on real-time feedback maximizes the performance of diamond core bits in various concrete and construction projects.
Recommended RPMs for various commonly drilled materials using diamond core bits:
Material |
Small Bits (1-2 inches) |
Medium Bits (3-6 inches) |
Large Bits (7+ inches) |
---|---|---|---|
Reinforced Concrete |
500-700 RPM |
350-500 RPM |
250-350 RPM |
Standard Concrete |
600-800 RPM |
400-600 RPM |
300-500 RPM |
Precast Concrete |
650-850 RPM |
450-650 RPM |
300-450 RPM |
Green Concrete |
700-900 RPM |
500-700 RPM |
350-550 RPM |
Asphalt |
800-1000 RPM |
600-800 RPM |
400-600 RPM |
Brick |
1000-1200 RPM |
800-1000 RPM |
600-800 RPM |
Block (Concrete Masonry Units) |
900-1100 RPM |
700-900 RPM |
500-700 RPM |
Granite |
500-700 RPM |
300-500 RPM |
200-400 RPM |
Limestone |
1100-1300 RPM |
900-1100 RPM |
700-900 RPM |
Sandstone |
1000-1200 RPM |
800-1000 RPM |
600-800 RPM |
Terrazzo |
900-1100 RPM |
700-900 RPM |
500-700 RPM |
Field Stone |
800-1000 RPM |
600-800 RPM |
400-600 RPM |
Slate |
1000-1200 RPM |
800-1000 RPM |
600-800 RPM |
Cinder Block |
1000-1200 RPM |
800-1000 RPM |
600-800 RPM |
Fiber Cement |
1100-1300 RPM |
900-1100 RPM |
700-900 RPM |
Plaster |
1300-1500 RPM |
1100-1300 RPM |
900-1100 RPM |
Drilling Pressure
Maintaining the correct drilling pressure is essential for optimizing the performance and longevity of diamond core bits, as well as ensuring the safety of the drilling equipment and workpiece. The appropriate amount of pressure varies depending on the hardness of the material being drilled and the size and type of the bit. For instance, harder materials like granite or dense concrete require a moderate amount of pressure to allow the bit to engage effectively without overloading the drill’s motor. Softer materials, however, might need less pressure to prevent the bit from wearing out too quickly or digging too aggressively, which could compromise the hole's quality.
One effective strategy for ensuring appropriate pressure is to utilize the drill's natural weight.
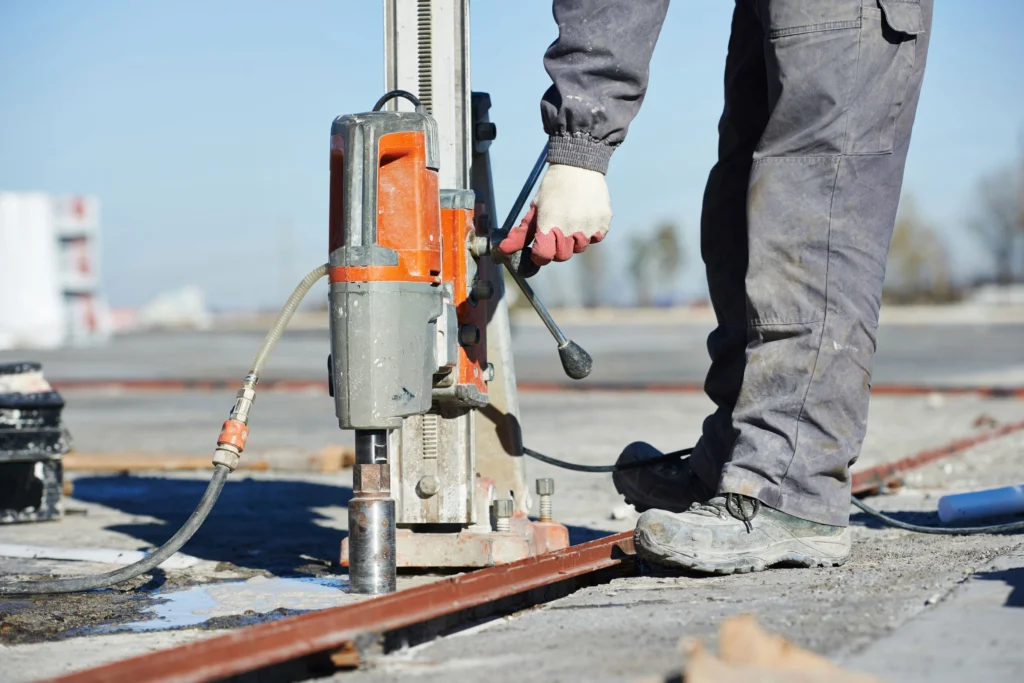
Many core drilling rigs and stands are designed to leverage this weight to apply a steady, controlled force, minimizing operator fatigue and maintaining consistent pressure, especially beneficial during extended drilling sessions. It’s crucial to sense and respond to feedback from the drill: if the drill begins to labor or the bit starts to stall, it's an indication that the pressure might be too high. Conversely, if the drill advances too slowly, this might suggest the pressure is too low. Making gradual adjustments can help find the optimal balance that allows the drill to advance steadily without straining the motor.
Maintaining the correct drilling pressure is essential for optimizing the performance and longevity of diamond core bits, as well as ensuring the safety of the drilling equipment and workpiece. The appropriate amount of pressure varies depending on the hardness of the material being drilled and the size and type of the bit. For instance, harder materials like granite or dense concrete require a moderate amount of pressure to allow the bit to engage effectively without overloading the drill’s motor. Softer materials, however, might need less pressure to prevent the bit from wearing out too quickly or digging too aggressively, which could compromise the hole's quality.
One effective strategy for ensuring appropriate pressure is to utilize the drill's natural weight.
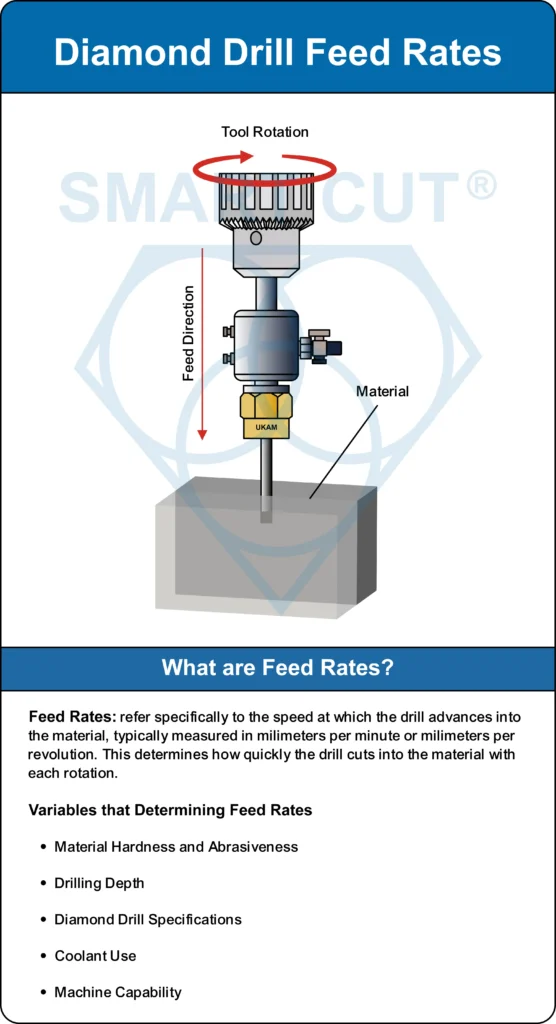
Applying excessive pressure can strain the drill and generate excessive heat, significantly reducing the bit's lifespan by wearing down the diamond segments. Additionally, too much force can risk bending or breaking the bit, particularly when drilling through materials with unexpected pockets of resistance, such as embedded rebar or uneven rock formations.
Periodic adjustments in pressure are necessary as the bit goes deeper into the material, encountering different layers or varying densities that may require different handling. Mastering the appropriate application of pressure often comes with experience, as skilled operators learn to interpret the sounds of the drill and the feel of the bit's progress to determine whether adjustments are needed. This careful management of pressure ensures that the drilling process remains effective, efficient, and safe, preventing potential damage to both the equipment and the material.
table with rough estimates of recommended feed rates and pressures for diamond core drilling across various materials. The feed rates are typically measured in inches per minute (IPM), while pressure can be described in terms of light, moderate, or heavy force applied during drilling. These numbers vary based on bit size, equipment, and specific job conditions, but this table provides general guidelines:
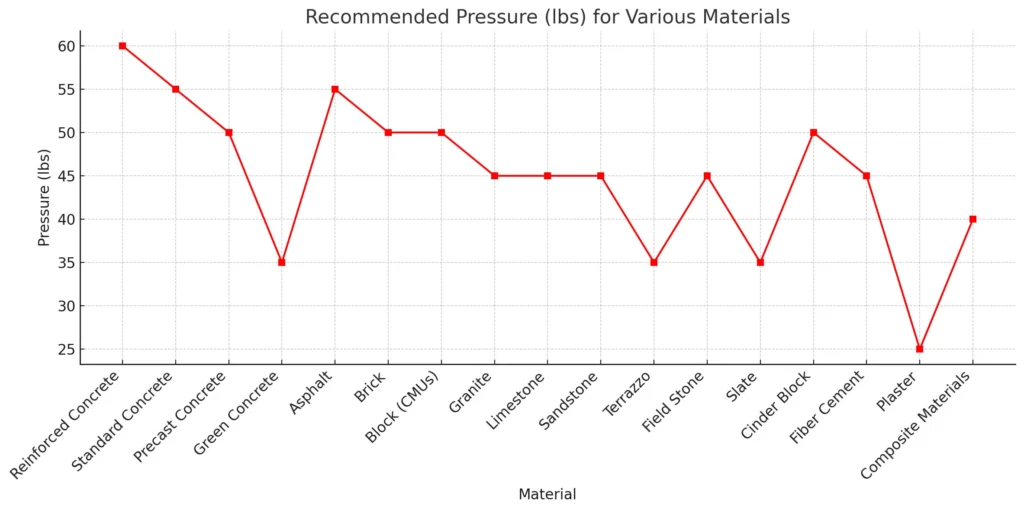
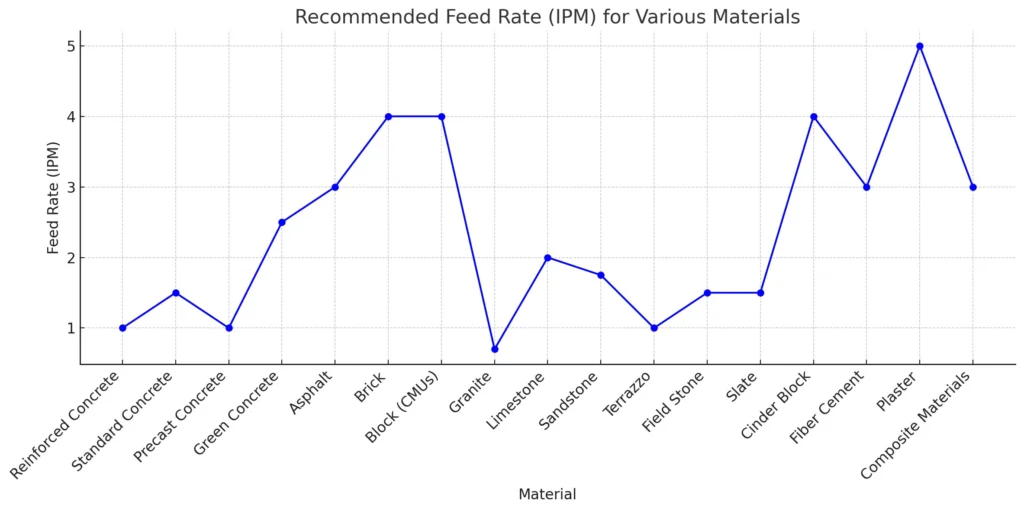
Material |
Recommended Feed Rate (IPM) |
Recommended Pressure |
---|---|---|
Reinforced Concrete |
0.5 - 1.5 IPM |
Moderate pressure (50-70 lbs) |
Standard Concrete |
1 - 2 IPM |
Moderate pressure (50-60 lbs) |
Precast Concrete |
0.5 - 1.5 IPM |
Light to moderate pressure (40-60 lbs) |
Green Concrete |
2 - 3 IPM |
Light pressure (30-40 lbs) |
Asphalt |
2 - 4 IPM |
Moderate pressure (50-60 lbs) |
Brick |
3 - 5 IPM |
Moderate pressure (40-60 lbs) |
Block (Concrete Masonry Units) |
3 - 5 IPM |
Moderate pressure (40-60 lbs) |
Granite |
0.3 - 1 IPM |
Light to moderate pressure (40-50 lbs) |
Limestone |
1.5 - 3 IPM |
Light to moderate pressure (40-50 lbs) |
Sandstone |
1 - 2.5 IPM |
Light to moderate pressure (40-50 lbs) |
Terrazzo |
0.5 - 1.5 IPM |
Light pressure (30-40 lbs) |
Field Stone |
1 - 2 IPM |
Moderate pressure (40-50 lbs) |
Slate |
1 - 2 IPM |
Light pressure (30-40 lbs) |
Cinder Block |
3 - 5 IPM |
Moderate pressure (40-60 lbs) |
Fiber Cement |
2 - 4 IPM |
Moderate pressure (40-50 lbs) |
Plaster |
4 - 6 IPM |
Light pressure (20-30 lbs) |
Composite Materials |
2 - 4 IPM |
Light to moderate pressure (30-50 lbs) |
Notes:
-
Light Pressure (20-40 lbs): Typically used for softer materials where too much pressure can cause material damage or bit overheating.
-
Moderate Pressure (40-60 lbs): Most commonly applied across a range of materials, offering a balance between fast drilling and bit preservation.
-
Heavy Pressure (70 lbs and up): Rarely used in diamond core drilling, as excessive pressure can cause bit overheating, damage to the material, or rapid wear.
Factors to Consider:
-
Bit Size: Larger bits generally require slower feed rates and more controlled pressure to prevent damage to both the bit and material.
-
Material Hardness: Harder materials like granite or reinforced concrete need lower feed rates and lighter pressure to avoid overheating or bit failure.
-
Operator Skill: Experienced operators can adjust pressure and feed rate based on the real-time feedback from the drill’s performance.
Drilling Reinforced Concrete
When drilling into materials with reinforcement bars, it's crucial to adjust your approach to avoid damaging the diamond core bit. Reinforcement bars, or rebar, significantly increase the resistance against the bit, posing risks to both the bit and the stability of the drilling operation.
Upon encountering rebar, immediately reduce the drill speed. High speeds can cause the diamond segments on the core bit to overheat or become dislodged when striking the harder steel. Slowing down helps to preserve the integrity of the bit and prevents the loss of segments, ensuring a longer lifespan and continued effectiveness.
For projects where encountering rebar is anticipated, consider using bits designed specifically for cutting through metal. These bits are typically equipped with segments that have a different composition, often containing higher grades of diamond and a tougher bonding matrix capable of handling the rigors of cutting through steel. This makes them more effective and reduces the risk of damage when drilling through heavily reinforced areas.
Adjusting your drilling technique is also crucial when dealing with rebar. Instead of applying constant pressure, a pulsing or pecking method can be more effective. This technique involves drilling for a short period, then withdrawing the bit slightly to allow any accumulated heat to dissipate and to help clear the cuttings from the hole. Repeating this action helps maintain the bit’s temperature and ensures that debris does not clog the cutting surface, which could lead to increased wear or even bit seizure.
Continuously monitor the progress while drilling through reinforcement bars. Be alert for changes in the sound or vibration of the drill, as these can indicate that the bit is under stress or has become lodged in the rebar. Periodic inspections of the bit during the drilling process can help catch any signs of wear or damage early, allowing for timely adjustments or replacements before significant problems occur.
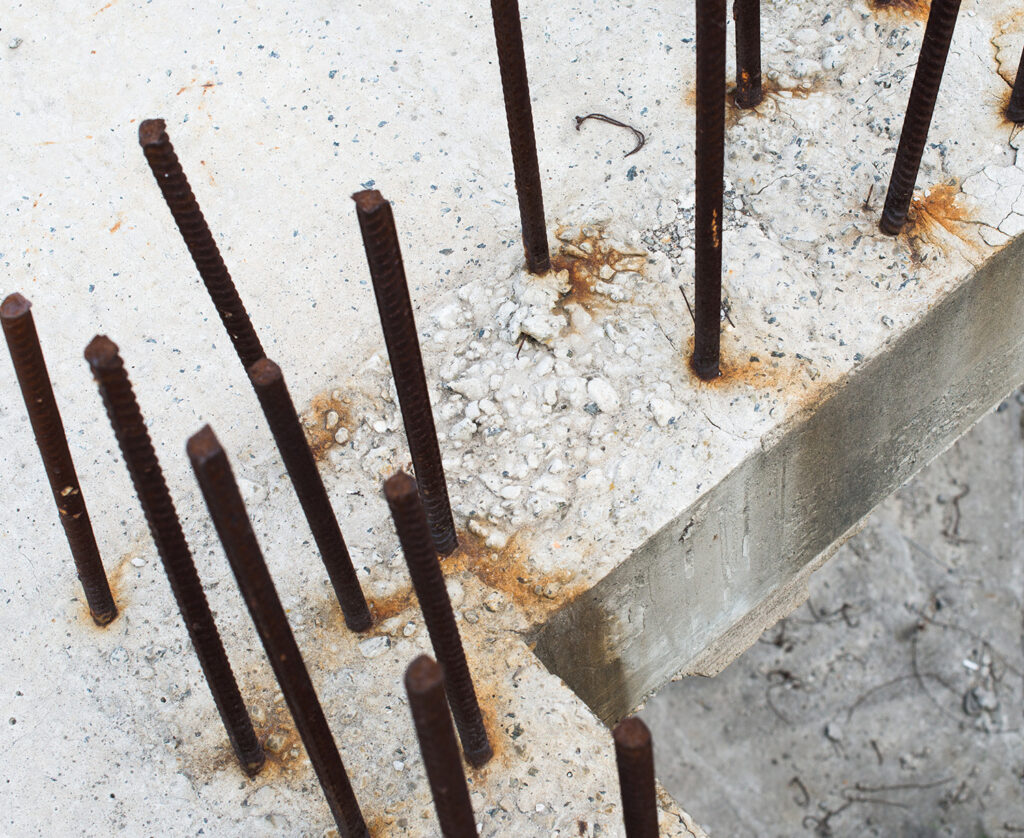
Although water is typically used for cooling during concrete drilling, additional lubrication can sometimes be beneficial when cutting through metal. Certain coolants or cutting fluids designed for metal drilling can help reduce friction and heat buildup, further protecting the bit when it interacts with rebar.
Extracting the Core
Extracting the core during drilling operations is a crucial step to ensure efficient, safe, and clean cuts, especially when using diamond core bits. This process involves periodically withdrawing the bit from the hole to manage debris and maintain optimal cooling. Proper execution of this technique not only enhances the cutting process but also prolongs the life of the drill bit.
When drilling with a diamond core bit, it's essential to allow water to continuously flow to the cutting surface. This cooling method helps to prevent overheating, which can damage both the material being drilled and the drill bit itself. However, even with constant water flow, debris from the drilling can accumulate in the hole. Over time, this accumulation can impede the progress of the drill, increase wear and tear on the bit, and potentially lead to jamming or other mechanical issues.
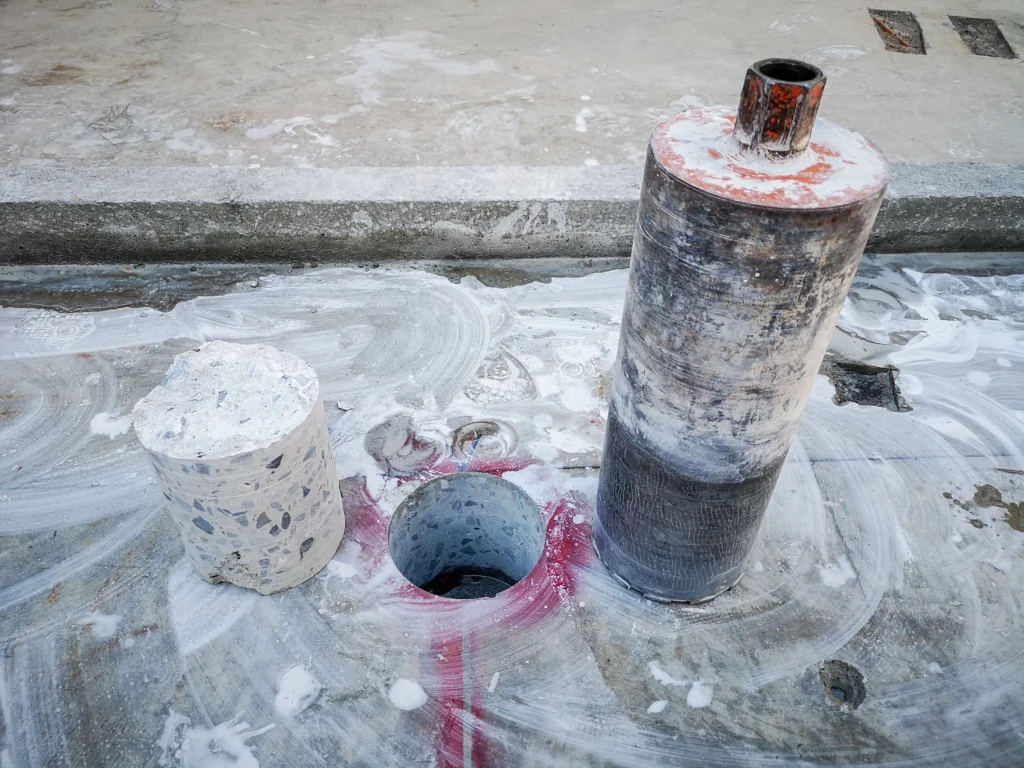
To effectively manage this, periodically withdraw the drill bit from the hole to clear out this debris. This action allows the cooling water to flush out the slurry that forms from the mix of water and the ground material, clearing the cutting path and ensuring a smoother drilling operation. It also provides an opportunity to inspect the bit for wear or damage, which is crucial for maintaining high-performance standards and ensuring safety.
This method of intermittently pulling out the bit not only helps in removing the debris but also aids in redistributing the cooling water along the depth of the hole. It ensures that the entire depth of the cut remains cool and lubricated, reducing the risk of overheating any section of the core or the bit.
Additionally, this practice can improve the accuracy of the drill. By regularly clearing the hole, you reduce the likelihood of the bit deviating from its intended path due to obstructions. It also minimizes the chance of the material cracking or breaking in an unintended manner due to pressure buildup from debris in the hole.
Dressing Diamond Core Bits
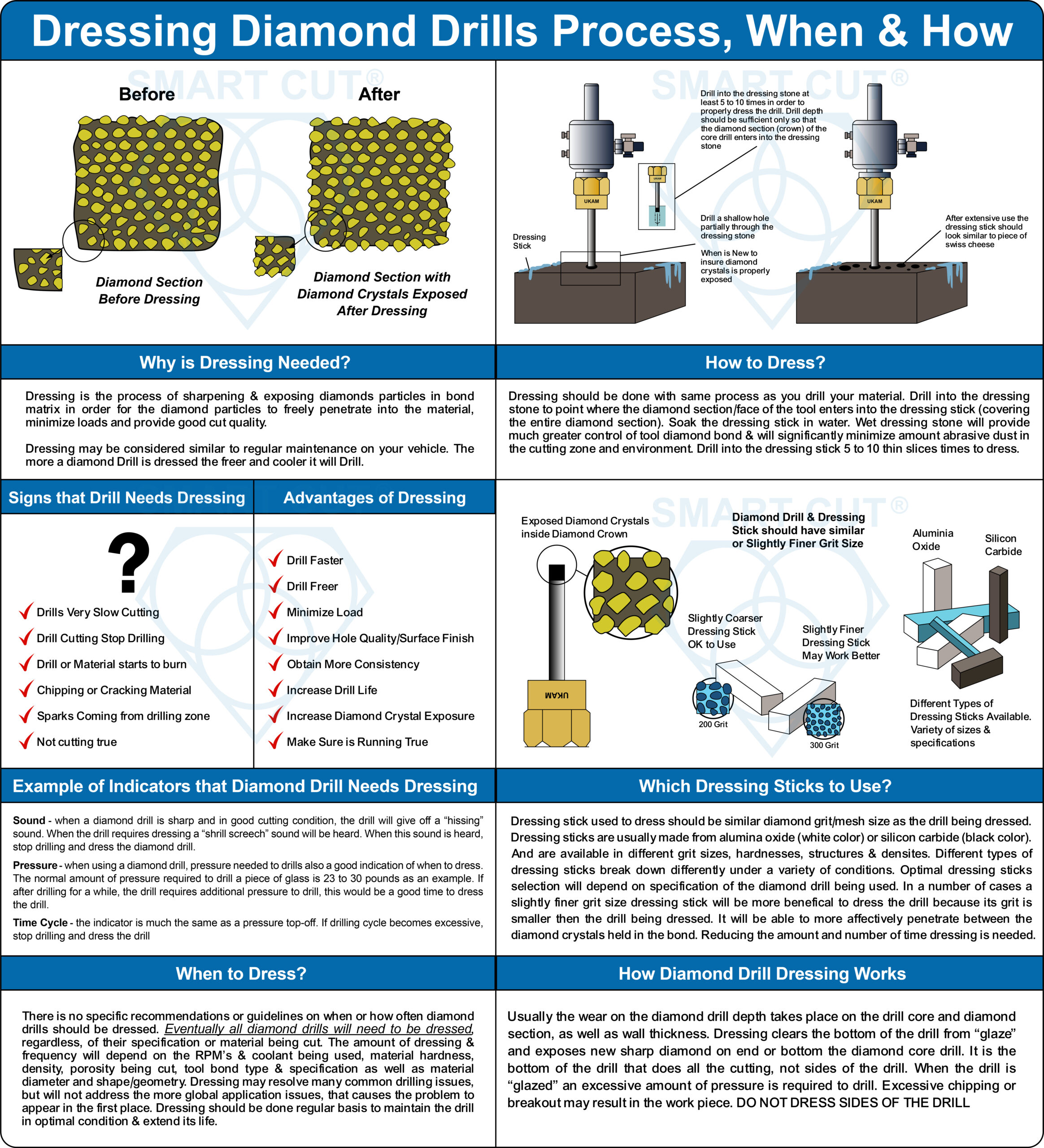
Dressing or sharpening diamond core bits is an essential maintenance procedure that extends their lifespan and enhances their cutting efficiency. Over time, these bits can become glazed or covered with a material layer that diminishes their effectiveness. This occurs when the diamonds embedded within the matrix become dull or when the matrix itself wears unevenly. To restore the cutting edge of these bits, a process known as dressing or sharpening is employed.
Dressing diamond core bits involves removing the outermost layer of the bit's matrix to expose new, sharp diamond particles. This is crucial because as the bit operates, the matrix is designed to wear away gradually, continuously exposing new diamond particles. However, if the wear is not even, or the diamonds at the surface become too blunt, the bit's performance decreases, making drilling less efficient and increasing the time and energy required to drill through materials.
One common method for dressing a diamond core bit is using a dressing stone, typically made from silicon carbide or a similar hard material. To dress the bit, you simply run the diamond core bit against the dressing stone at a moderate speed. This action grinds away the worn surface of the matrix, revealing new, sharp diamonds.
Alternatively, a concrete block can be used to dress the bit. This method involves lightly drilling into a concrete block with the bit. The abrasiveness of the concrete helps to wear away the matrix evenly and exposes fresh diamond particles. It’s important to use light pressure and low speed during this process to avoid damaging the bit or dislodging the diamonds from the matrix.
When dressing the bit, it is crucial to use light pressure to prevent overheating and potential damage to the bit. Overheating can cause the metal matrix to soften, risking the premature loss of diamond particles. If your drill setup allows, keep water flowing to the bit during the dressing process to help keep the bit cool and wash away debris from the dressing process.
After dressing, inspect the bit to ensure that new diamonds are exposed and that the surface is even. An uneven surface can lead to unstable drilling and reduced performance. By regularly dressing your diamond core bits, you ensure that they remain sharp and efficient, reducing drilling time and effort while extending the operational life of the bits.
Deep Hole Drilling & Extending Drilling Depth

Deep hole drilling and extending drilling depth effectively and safely require meticulous planning and execution. It's crucial to select the right drill bit for the job. Drill bits designed for deeper drilling often feature longer barrels and specialized cutting surfaces to handle increased stress and higher temperatures. Diamond core bits are particularly effective due to their durability and ability to drill through hard materials.
Using robust drilling equipment capable of generating sufficient torque and maintaining stability at extended lengths is essential. Drills with powerful motors and high torque capabilities are ideal, and stabilizers should be used to prevent the drill shaft from deflecting as depth increases. Starting with a pilot hole can significantly improve the accuracy and efficiency of deep drilling, acting as a guide for the main drill bit to maintain trajectory and reduce the risk of deviations.
Employing a gradual step drilling technique is beneficial; beginning with a smaller diameter bit and gradually increasing the size helps manage the strain on the drill bit and machinery, reducing wear and preventing potential failures. Effective lubrication and cooling are vital to prevent overheating and reduce friction. Continuous water or coolant flow is necessary to keep the bit cool and to flush out debris, maintaining clear and smooth operation. For very deep drilling, specialized cooling systems may be required.
Periodically withdrawing the drill bit allows for the removal of accumulated cuttings and helps prevent blockages that can halt drilling progress or damage the equipment. Monitoring drilling parameters such as speed, torque, and drill pressure closely and adjusting these based on feedback from the drilling process is crucial. Modern drilling equipment often includes sensors that provide real-time data to help manage these adjustments.
Conducting regular inspections of the drill bit and machinery is important, especially when operating at greater depths. Checking for signs of wear, damage, or misalignment can prevent costly repairs and downtime. Ensuring that drilling crews are well-trained and prepared for the specifics of deep drilling is vital for safety and efficiency. Proper training in handling equipment, responding to drilling data, and emergency procedures is essential.
Investing in high-quality, durable drilling equipment and maintaining it meticulously is critical when aiming to extend drilling depth. Well-maintained equipment performs better, lasts longer, and is less likely to encounter issues during deep drilling operations.
Using Drilling Equipment with Right Horse Power
The horsepower (HP) of a drilling machine significantly affects its ability to handle various types of diamond core bits for concrete and construction applications. Horsepower measures the power output of drilling equipment, directly impacting the torque, drilling speed, and overall efficiency of the operation. Adequate horsepower ensures the machine can maintain a steady drilling rate, handle the resistance of hard materials, and operate larger core bits effectively without stalling or losing power.
In diamond core drilling, the machine’s horsepower translates to its capacity to drive the core bit through tough materials like concrete, masonry, and reinforced concrete. Higher horsepower allows the equipment to generate more torque (rotational force), which is crucial for overcoming resistance, especially when drilling large-diameter holes or penetrating hard materials.
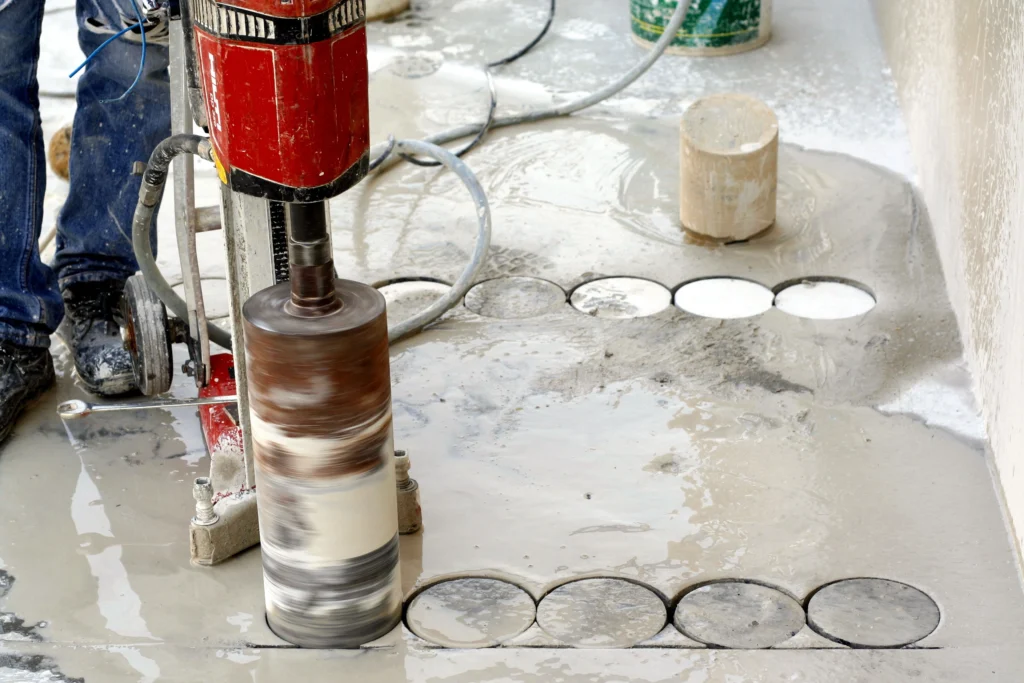
Torque is particularly important for maintaining consistent cutting pressure on the bit, which helps prevent it from slowing down or stalling during difficult drilling conditions. Machines with insufficient horsepower may struggle to maintain the necessary torque, especially when encountering steel rebar or dense aggregates, resulting in slower drilling speeds, increased wear on the bit, and potential equipment failure.
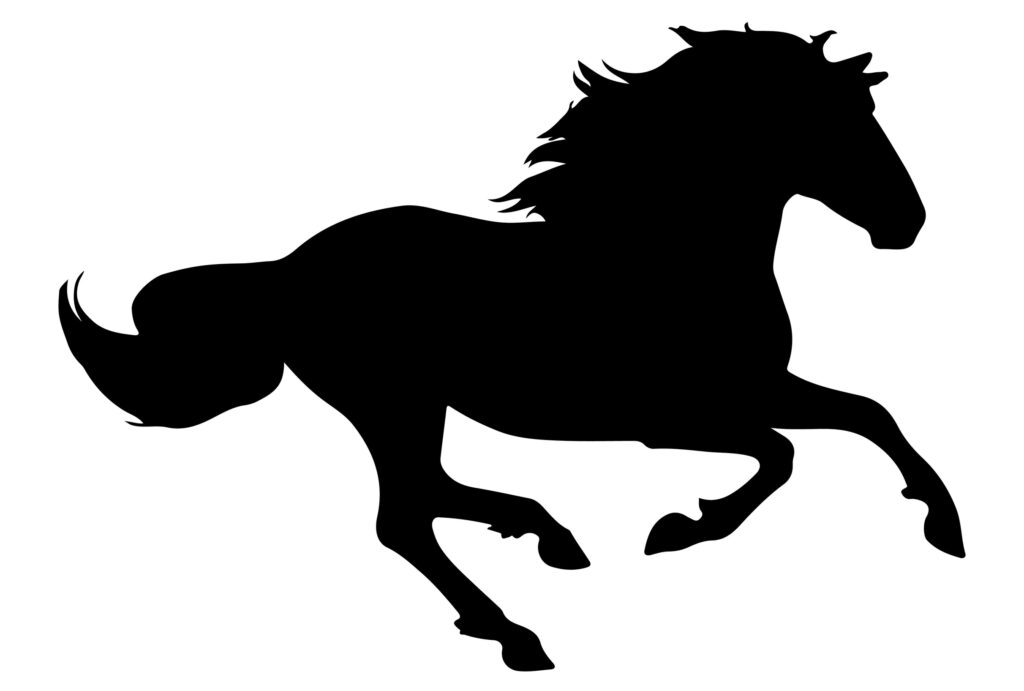
Horsepower requirements increase with the diameter of the core bit. Larger core bits require more power to cut through the material efficiently due to their greater surface area and the higher amount of friction generated during drilling. Smaller core bits, on the other hand, can be driven by machines with lower horsepower, as they encounter less resistance and require less torque to maintain drilling speed.
For small-diameter core bits (1-2 inches), typically used in handheld or portable core drills, machines with 1 to 2 HP are sufficient. These bits require less torque, allowing the equipment to run at higher RPMs. Smaller core bits are used for light-duty drilling in materials like brick, block, or non-reinforced concrete.
Medium-sized core bits (3-6 inches) need around 2 to 5 HP to provide the necessary torque for efficient cutting. These bits are commonly used for creating medium-sized holes in concrete walls, floors, or slabs for plumbing, electrical conduit, or anchor installations. The additional horsepower ensures that the machine can maintain steady drilling pressure even when cutting through harder materials like reinforced concrete.
Larger core bits (6-12+ inches) require significantly more horsepower to maintain torque and cutting speed. Machines with 5 to 10+ HP are typically required for these heavy-duty tasks. Large core bits are used in rig-mounted drills for creating large openings in concrete slabs, structural walls, and foundations. The high power output ensures the bit can cut through both concrete and embedded rebar without slowing down or losing efficiency.
The material being drilled also influences the horsepower requirements. Harder materials, such as reinforced concrete or granite, generate more resistance and require more power to drill through effectively. In contrast, softer materials like asphalt or non-reinforced concrete can be drilled with lower horsepower machines, as these materials offer less resistance.
Drilling depth is another factor that influences horsepower requirements. As the depth of the hole increases, especially in thick concrete slabs or walls, the resistance encountered by the core bit also increases. The deeper the bit goes, the more torque is required to maintain steady cutting pressure. Machines with higher horsepower are better equipped to handle deep drilling because they can sustain the torque necessary to cut through dense materials over long distances without losing speed.
In wet drilling, where water is used to cool the core bit and flush out debris, machines in the 1 to 10+ HP range, depending on the material and bit size, can perform more efficiently due to the cooling effect of water. This reduces wear on the bit and the machine. In dry drilling, where no water is used, machines must have higher horsepower to compensate for the increased friction and heat. Machines with higher horsepower, generally around 5 to 10 HP, are often required for dry drilling in hard materials like concrete or stone. The extra power helps the machine maintain torque and speed without overheating, even though dry drilling generates more friction.
Higher horsepower machines provide more control over the drilling process, especially in challenging materials. However, they also require experienced operators who understand how to manage the power output effectively. Misuse of high-powered drilling machines can lead to tool damage, overheating, or safety issues if not handled properly.
Experienced operators can adjust drilling speed, torque, and pressure to match the material and application, ensuring that the machine’s horsepower is fully utilized without overloading the equipment or the bit. Operators must also monitor the machine’s performance to avoid stalling, especially when drilling through materials with variable density, such as reinforced concrete with steel rebar.
Using a machine with insufficient horsepower for the task can lead to several issues, including stalling when the bit encounters high resistance, such as steel rebar or dense aggregates, which can lead to incomplete drilling and the need to restart the operation. Machines with low horsepower may also overheat more quickly when drilling into hard or abrasive materials, especially if dry drilling is used. This can damage the motor, the core bit, and the material being drilled. Insufficient horsepower reduces the torque available to drive the core bit through the material, leading to slower cutting speeds and longer project times. When the machine struggles to maintain torque, the core bit experiences uneven wear, reducing its lifespan and increasing costs for bit replacements.
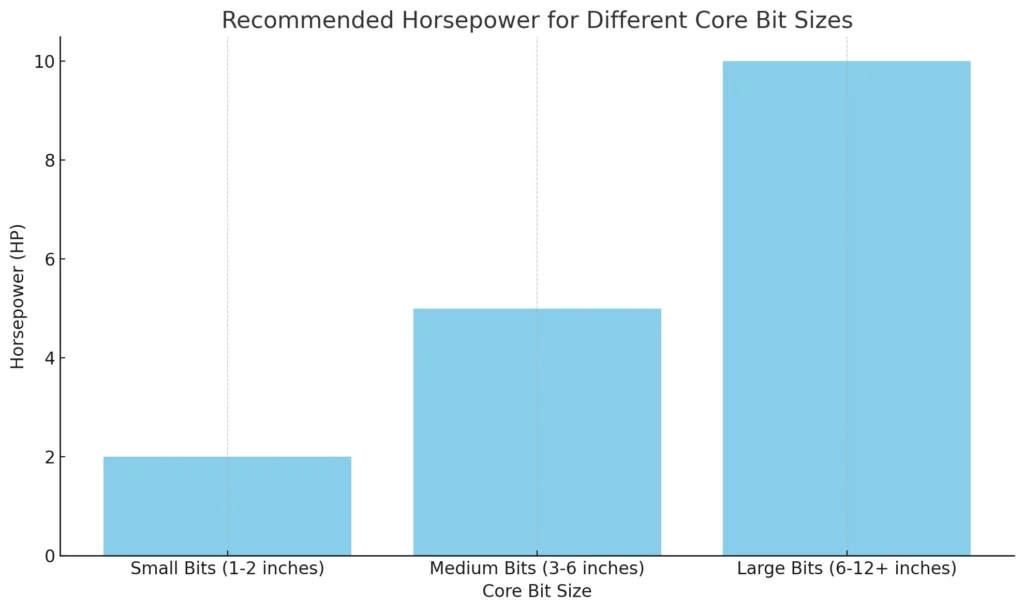
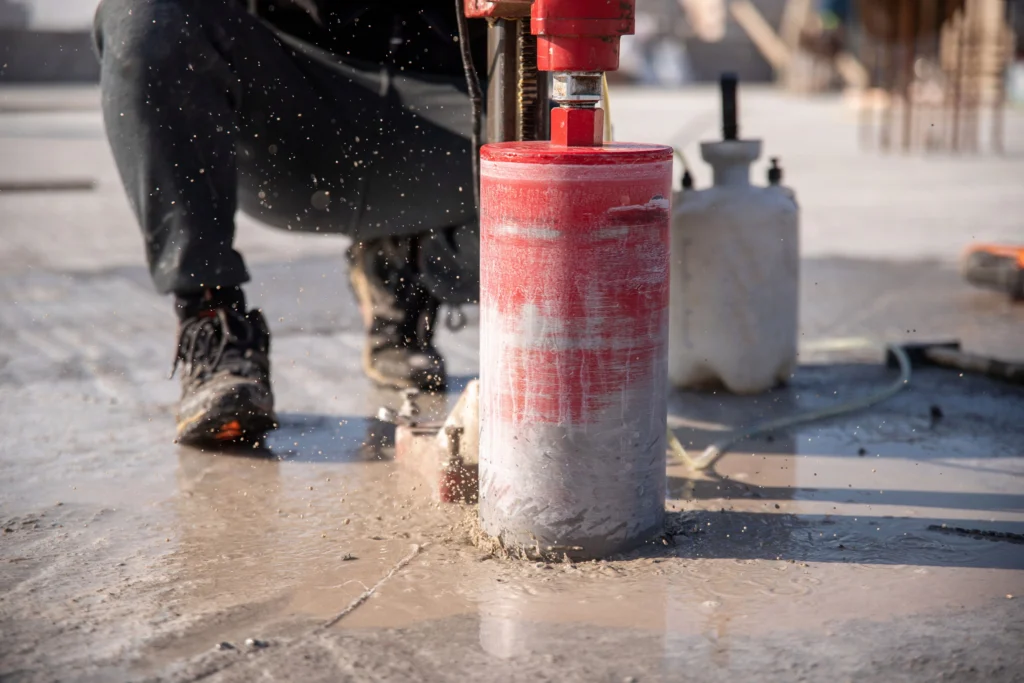
Vertical vs Horizontal Drilling
Drilling concrete with diamond core bits, whether vertically or horizontally, involves unique challenges that require specific techniques and considerations to achieve optimal results and extend the lifespan of the tools.
When drilling vertically, gravity plays a beneficial role by assisting in the removal of debris from the drill hole. This natural clearing helps maintain the effectiveness of the diamond core bit by reducing the risk of clogging and overheating. Additionally, leveraging the weight of the drill in vertical drilling allows for easier control over the pressure applied, making it possible to use the drill’s own weight to enhance the drilling process without exerting excessive force. This steady pressure helps maintain consistent drilling speeds and reduces the likelihood of the bit becoming lodged or deviating from its intended path. Cooling efficiency is also generally better in vertical drilling, as water can flow more freely down the shaft, continuously cooling the bit and washing away debris.
In contrast, horizontal drilling does not benefit from gravity for debris removal, which can lead to slurry and cuttings accumulating in the drill hole. This accumulation may clog the bit and lead to overheating if not managed properly through effective debris management strategies, such as frequent withdrawal of the bit to clear material or using advanced slurry extraction systems. Applying the correct amount of pressure in horizontal drilling requires careful handling to ensure that the bit does not bind or stall, particularly in deeper holes. Cooling in horizontal drilling also demands more attention since water or cooling fluids need to be pumped with enough pressure to effectively reach the bit, as natural flow is hindered.
Regardless of the drilling orientation, selecting the right diamond core bit for the concrete type and the specific job is crucial. Factors such as segment bond and diamond concentration significantly affect performance and are influenced by the drilling orientation due to differences in debris removal and cooling. Proper alignment and stabilization of the drilling rig are also essential in both vertical and horizontal drilling to prevent bit deviation and ensure precise, clean holes. The rigs should be robust enough to handle the specific stresses of the chosen drilling orientation without shifting.
Skilled operation is crucial in both vertical and horizontal drilling. Experienced operators who understand how to adjust techniques and handle equipment specific to the drilling orientation will achieve better results and reduce wear on the tools.
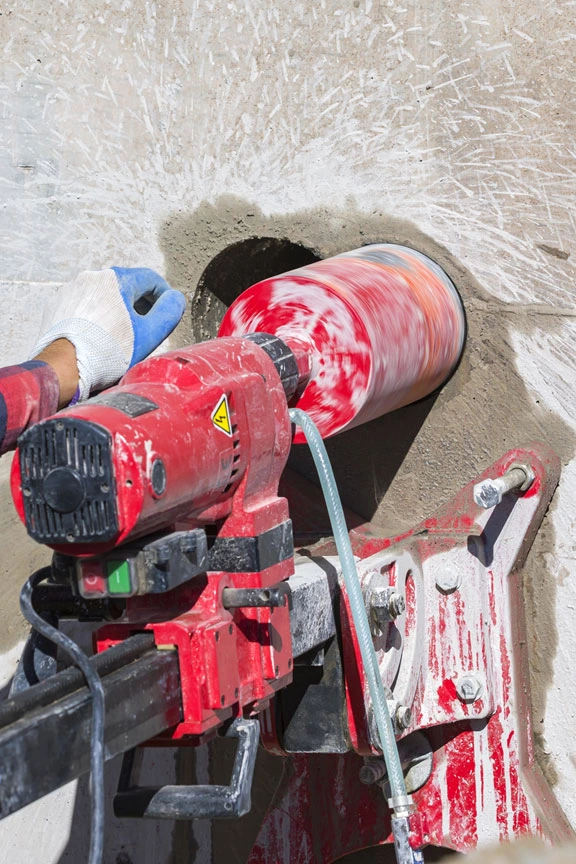
Comparison Table of Vertical & Horizontal Drilling
Aspect |
Vertical Drilling |
Horizontal Drilling |
---|---|---|
Gravity Assistance |
Gravity helps in debris removal, allowing cuttings and slurry to fall away from the bit, reducing clogging and heat. |
No gravity assistance; debris tends to accumulate in the hole, requiring active removal to prevent clogging and overheating. |
Pressure Control |
Easier to apply pressure as the drill's weight can be used to enhance drilling without excessive force. |
Applying correct pressure is more challenging; requires careful handling to avoid bit binding or stalling. |
Cooling Efficiency |
Water flows freely down the shaft, enhancing cooling and debris removal, leading to better overall efficiency. |
Cooling requires more effort; water must be pumped with adequate pressure to reach the bit, ensuring effective cooling. |
Debris Management |
Debris naturally falls out of the hole due to gravity, simplifying management. |
Frequent withdrawal of the bit may be necessary to clear debris, complicating the drilling process. |
Quality of Cut |
Generally smoother as consistent pressure and effective debris removal are easier to maintain. |
Potential for uneven cuts if debris is not adequately managed or if the bit moves due to inadequate pressure control. |
Operator Effort |
Typically less physically demanding due to the assistance of gravity in handling the drill and managing debris. |
More physically demanding as it requires constant attention to pressure and manual debris management. |
Evaluating Diamond Core Bit Performance
Evaluating the performance of diamond core bits is essential for ensuring efficient, cost-effective drilling operations and maintaining high-quality outcomes. There are several key indicators that professionals in the field use to assess how well a diamond core bit is performing. These include the rate of penetration, the wear rate of the diamond segments, the quality of the cut, and overall bit life. Understanding these factors can help in selecting the right bit for specific materials and conditions, and in making adjustments to drilling techniques as needed.
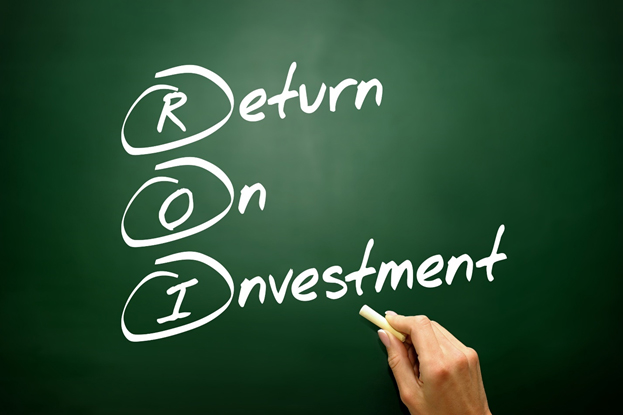
Rate of Penetration - The rate of penetration (ROP), or the speed at which a diamond core bit drills through material, is a primary measure of performance. A high ROP indicates that the bit is well-suited to the material and is being operated under optimal conditions. Factors affecting ROP include the diamond grade and concentration, the hardness of the bond matrix, and the drilling parameters such as speed and pressure. Evaluating ROP helps in determining if the bit is not only efficient but also cost-effective, as faster drilling speeds can significantly reduce project times and costs.
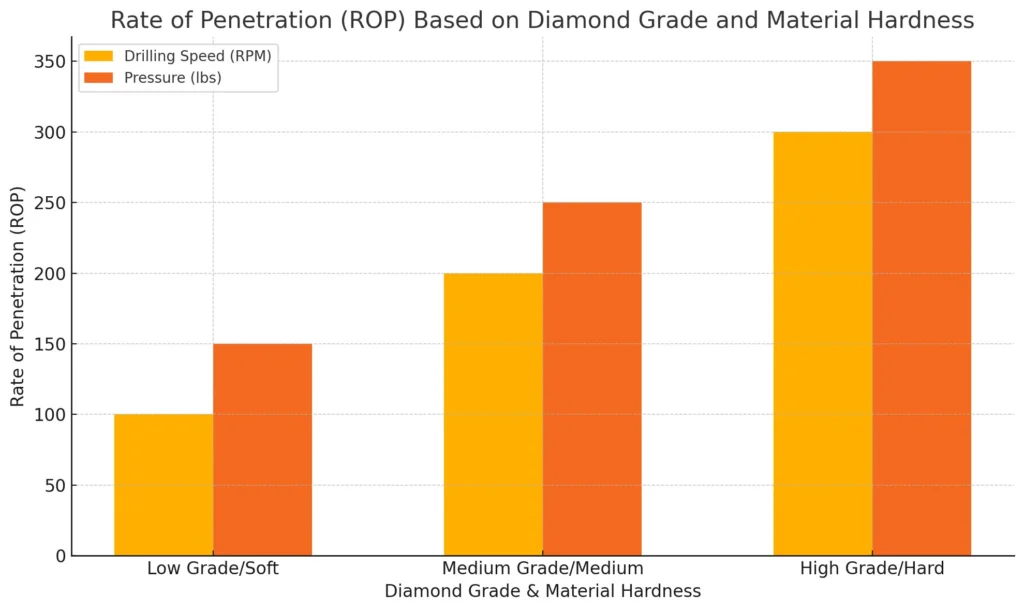
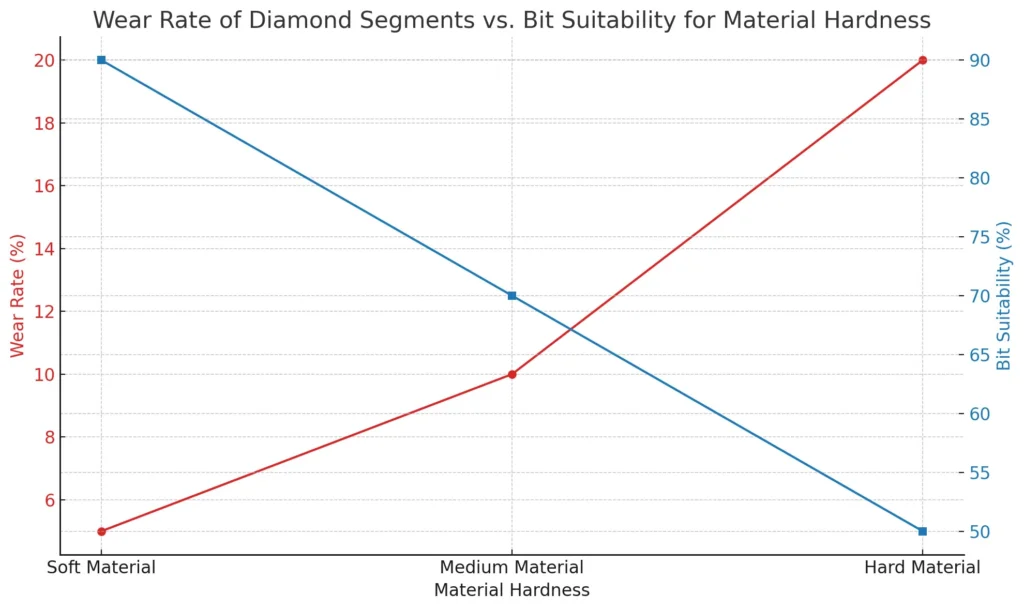
Wear Rate of Diamond Segments - The wear rate of the diamond segments on the core bit provides insight into the bit’s durability and the appropriateness of its use for a particular material. Premature segment wear can suggest that the bit is either too soft for the material or being operated under inappropriate conditions. Monitoring wear rate is crucial for predicting bit life and scheduling replacements without unexpected downtimes. Regular inspection of the segments for signs of unusual wear patterns or segment loss is part of a comprehensive performance evaluation.
Quality of the Cut - The quality of the cut, characterized by smoothness, accuracy, and the absence of chipping or material breakage, is another critical factor in evaluating diamond core bit performance. A high-quality cut not only reflects the efficiency of the bit but also affects the structural integrity of the material being drilled. Imperfections in the cut can compromise the installation of fixtures or reinforcements, especially in construction applications. Factors influencing cut quality include the choice of diamond size, the concentration, and the matching of the bit’s specifications to the material’s characteristics.
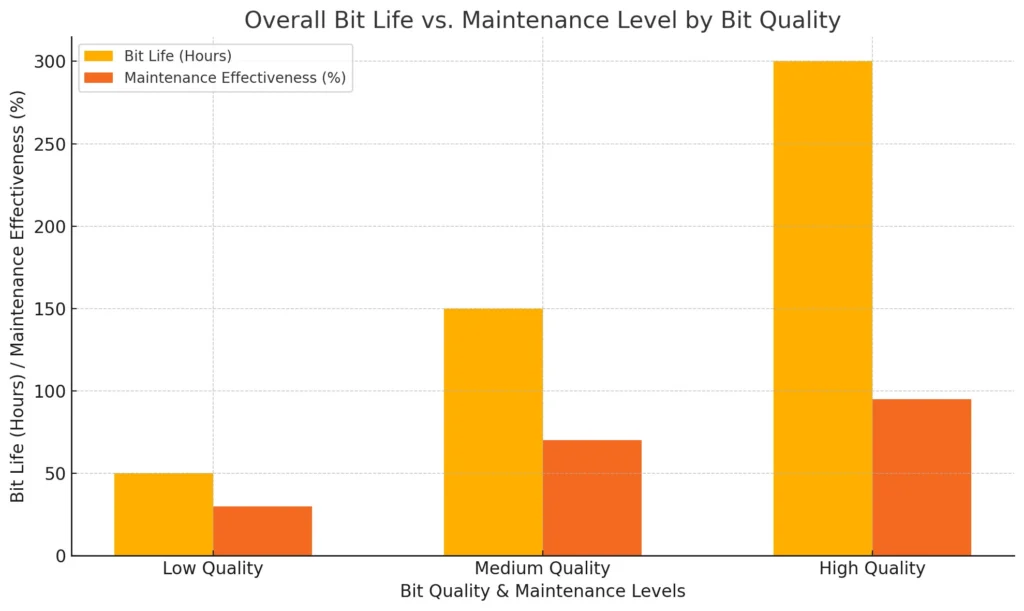
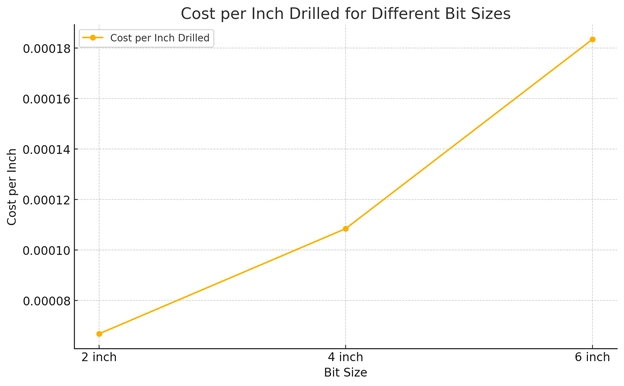
Overall Bit Life - The overall life of a diamond core bit is a comprehensive indicator of its performance. A bit that maintains its cutting ability for a long duration under expected conditions offers greater value and reliability. Bit life is influenced by the quality of the diamond and matrix materials, the precision of the manufacturing process, and how well the bit is maintained and operated, including proper cooling and correct RPM settings.
Operational Feedback - Operational feedback from the drilling personnel can provide invaluable insights into the performance of a diamond core bit. Operators can offer real-time observations on how the bit handles different materials, its response to adjustments in drilling techniques, and any issues encountered during the drilling process. This feedback is crucial for continuous improvement in bit selection and drilling operations.
Diamond Core Bit Trouble Shooting Guide
Diamond Core Bit Life & Overall Performance will vary with material hardness, density, Drilling Depth. Few other factors that play a role in diamond drill life include: RPM's (drilling speed), Feed Rate, Coolant being Used, Coolant feed rate and Direction. Drilling Equipment, & experience of operator.
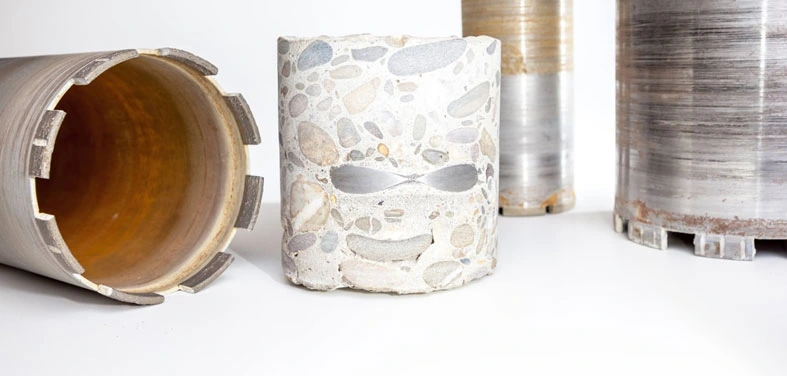
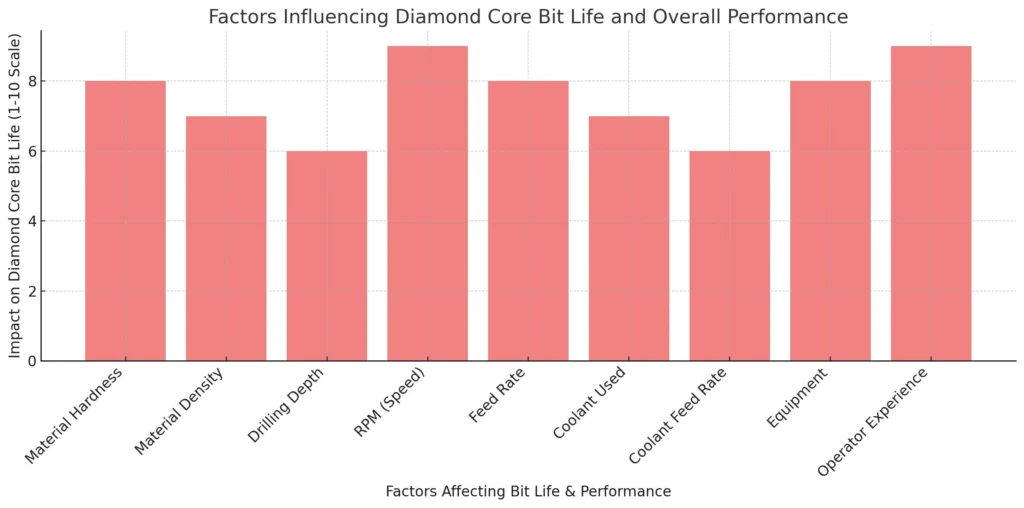
While there is now way of accurately predicting Life of your diamond core bit. It can be optimized by following Principals of Proper Diamond Drill / Tool Usage.
There may also be some experimenting, as well as trial & error involved in the part of the end user. Highly experienced diamond core bit users may find some variations in diamond core bit life or performance even when working on same material & application for several years.
The trouble shooting guide below will cover most issues people experience when using diamond core bits
Problem |
Possible Causes |
Solutions |
---|---|---|
Bit is not cutting |
|
|
Bit is overheating |
|
|
Excessive wear |
|
|
Bit is stalling |
|
|
Chipping or uneven cuts
|
|
|
Core bit jams or binds |
|
|
Segment or Diamond Section Loss
|
|
|
Slow Drilling Speed |
|
|
Unusual Vibration |
|
|
Noise During Operation |
|
|
Excessive Bit Wear
|
|
|
Bit Skidding or Slipping |
|
|
Inefficient Debris Removal |
|
|
Increased Operational Costs |
|
|
Frequent Bit Replacement |
|
|
Loss of Cutting Efficiency |
|
|
Drill Motor Overload |
|
|
Material Cracking |
|
|
Water Management Issues |
|
|
Operational Delays |
|
|
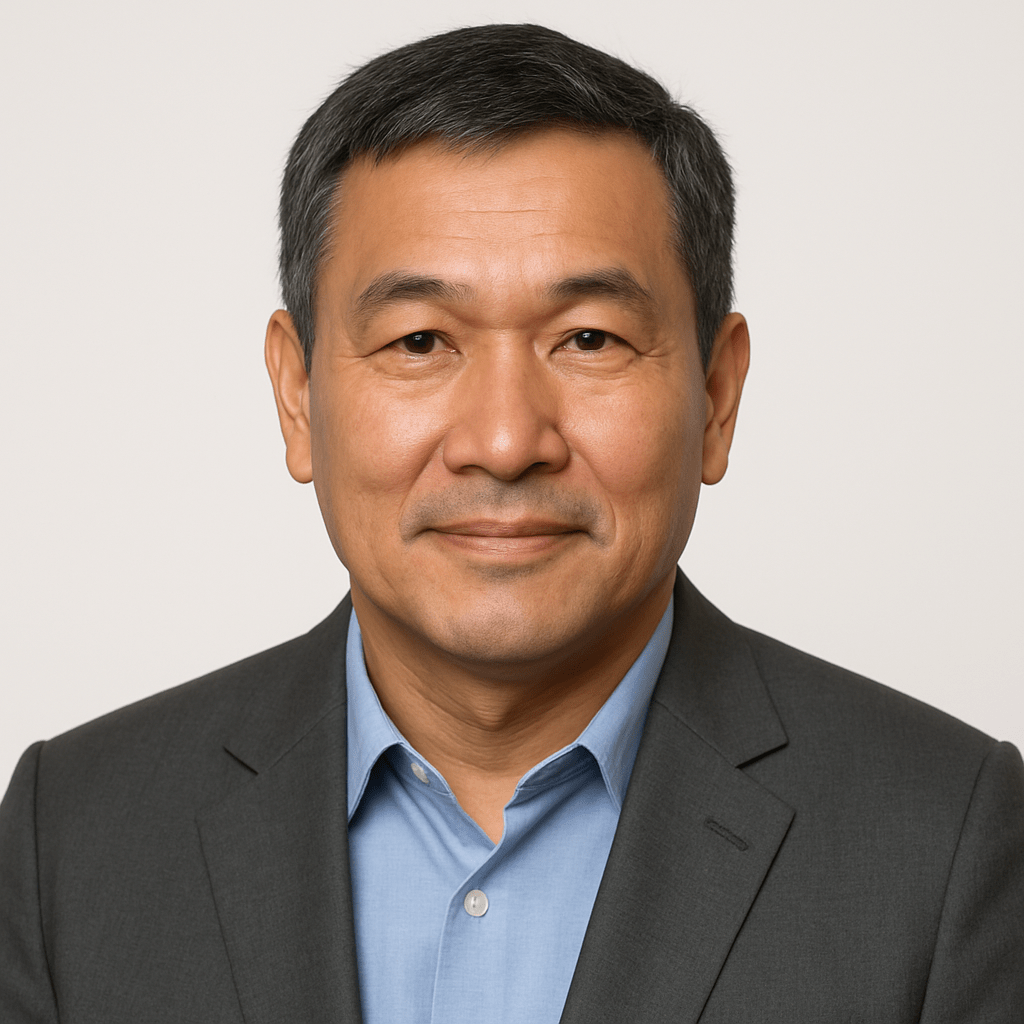
Ayan Sadyk is a materials scientist and process engineer with over two decades of experience in the industrial diamond tooling sector. His expertise lies in integrating ultra-thin diamond blades, CBN wheels, and advanced cutting systems into precision manufacturing workflows for applications in optics, semiconductors, and technical ceramics.
With a background in materials behavior and surface integrity, Mr. Sadyk brings a data-driven, application-specific approach to cutting and grinding process development. He has worked closely with manufacturers and R&D facilities across Eastern Europe, North America, and the Middle East, helping optimize tool life, surface finish, and process stability.
As an author, he focuses on bridging materials science with tooling innovation—writing on topics such as blade wear mechanisms, thermal effects in hard material sectioning, and adaptive process design.
ARE YOU USING DIAMOND CORE BITS
FOR YOUR APPLICATION?
LET US
HELP YOU
HAVING ISSUES WITH
YOUR CURRENT DIAMOND CORE BITS?
Knowledge Center
Diamond Core Bit Ultimate Guide
Concrete Drilling Metrics – Optimizing your Diamond Core Bit
Optimal Drilling Performance – How to Properly Use Diamond Core Bits
Select right Diamond Drill for your application
How to Properly Use Precision Diamond Drills
Diamond Drills Guide
Diamond Tools Guide – Selecting Right Drills & Tools for your application
Optimizing your Diamond Drilling Operation
Diamond Core Drill & Drill Trouble Shooting Guide
Understanding & Calculating Return on Investment for Diamond Core Drills & Other Tools
Understanding Tradeoffs – Searching for Perfect Diamond Drill & Tool
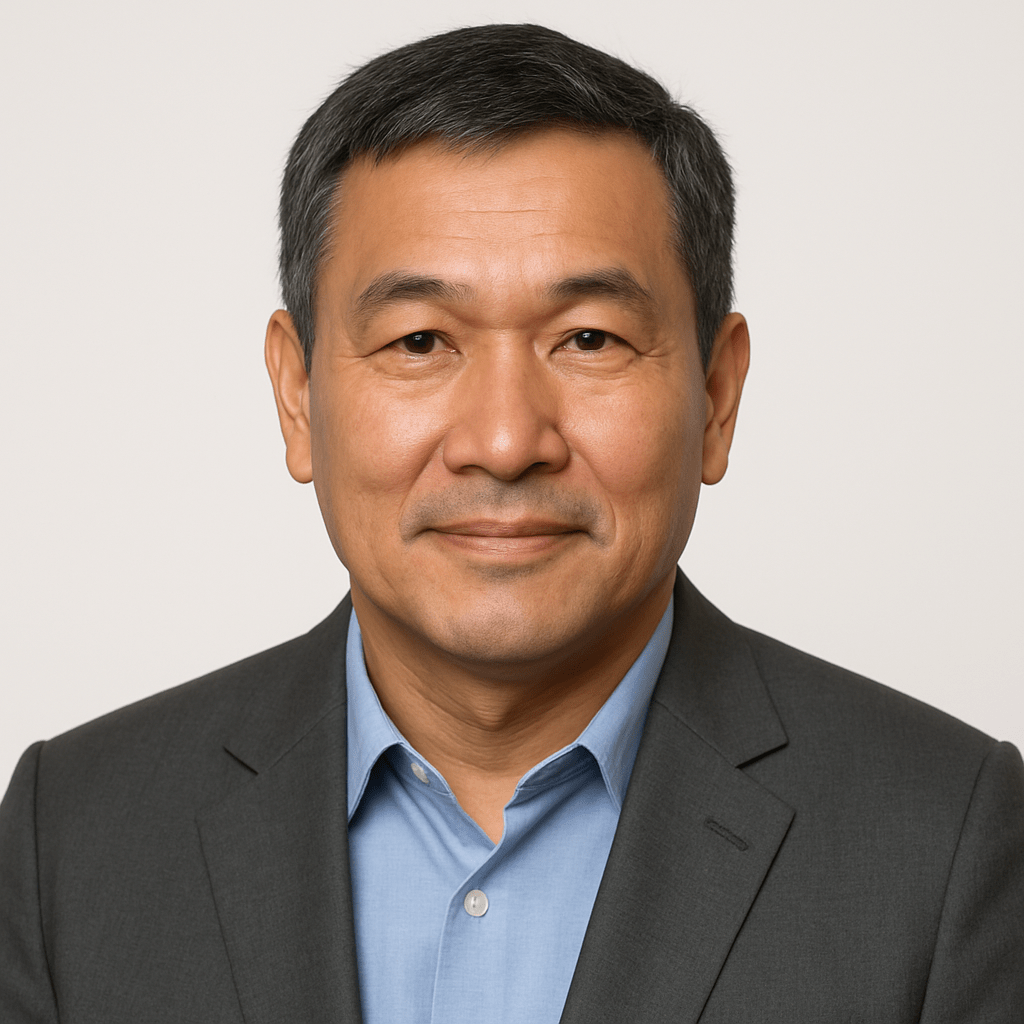
Ayan Sadyk is a materials scientist and process engineer with over two decades of experience in the industrial diamond tooling sector. His expertise lies in integrating ultra-thin diamond blades, CBN wheels, and advanced cutting systems into precision manufacturing workflows for applications in optics, semiconductors, and technical ceramics.
With a background in materials behavior and surface integrity, Mr. Sadyk brings a data-driven, application-specific approach to cutting and grinding process development. He has worked closely with manufacturers and R&D facilities across Eastern Europe, North America, and the Middle East, helping optimize tool life, surface finish, and process stability.
As an author, he focuses on bridging materials science with tooling innovation—writing on topics such as blade wear mechanisms, thermal effects in hard material sectioning, and adaptive process design.