Table of Contents
ToggleDressing is the process of sharpening and exposing diamond particles within the bond matrix, allowing them to penetrate materials more effectively, minimize operational loads, and ensure high-quality cuts. Despite its critical role in tool performance, dressing is often overlooked, misunderstood, and underappreciated. Along with proper coolant application, dressing is essential for achieving successful and optimal tool usage. All diamond tools, regardless of the material being cut, will eventually require dressing.
What is Dressing?
Dressing can be likened to routine maintenance on a vehicle. Just as regular oil changes and tire rotations keep a car running smoothly, dressing keeps diamond tools in optimal condition. Neglecting this maintenance can lead to problems such as reduced cutting efficiency and eventual tool failure. Conversely, consistent dressing ensures that diamond tools function effectively for extended periods.
For diamond tools to perform optimally, frequent dressing is necessary to properly expose the diamonds. Without adequate dressing, the tool surface may glaze over, causing the tool to tear rather than grind. This tearing generates excessive friction, leading to uneven wear, heat cracks in the tool, and damage to the material being machined. Such conditions result in premature tool wear, blade tensioning issues, and potential destruction of the diamond tool. Regular dressing keeps the tool cooler, enhancing its cutting performance.
Additionally, dressing is crucial for cleaning blades loaded with debris, which can clog the pores between abrasive particles. Cutting into a dressing plate introduces mechanical and thermal stress, which helps produce a clean tool surface.
Well-protruded and exposed diamonds are essential for easy material penetration. Poorly dressed diamond tools tend to push against the material, leading to high loads, elevated cutting temperatures, and suboptimal cut quality. This can also increase the risk of tool breakage. There are no universal guidelines on the frequency or timing of dressing; it depends on various factors such as diamond bond type, tool type, bond hardness, diamond grit size, and tool concentration. Application-specific factors also play a role, including the material’s hardness, density, porosity, diameter, shape, cut depth, equipment used, coolant, and operational RPMs.
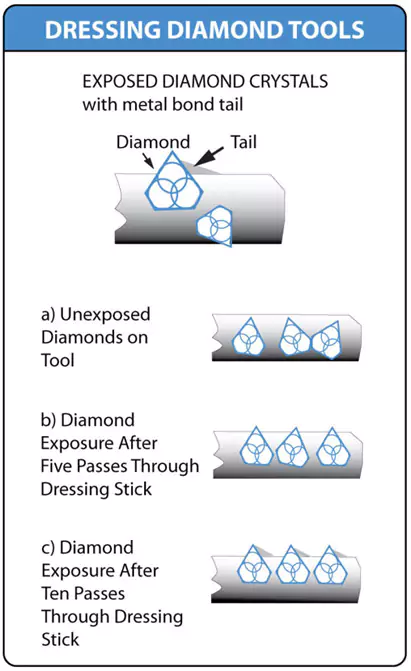
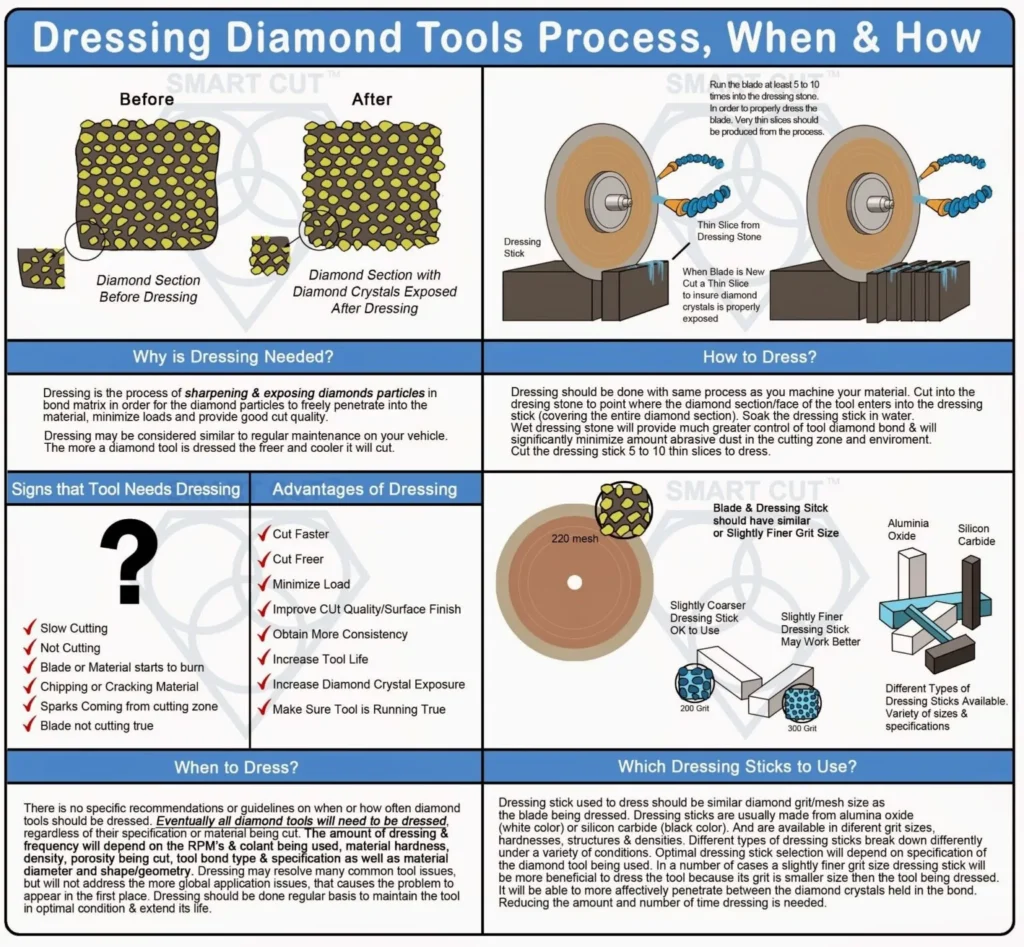
Factors Influencing Dressing Frequency and Technique
The need for dressing, and the frequency with which it should be done, depends on several factors:
-
Tool and Bond Characteristics: The type of diamond tool, the hardness of the bond, the diamond grit size, and the concentration of diamonds all influence how quickly a tool might need dressing.
-
Material Characteristics: The hardness, density, porosity, and the physical dimensions and shape of the material being cut also affect how a diamond tool wears and when it should be dressed.
-
Cutting Conditions: The depth of cut, the type of equipment used, the rotational speed of the tool, and the type of coolant applied can all impact the rate of wear and the effectiveness of the diamond tool.
Detailed Analysis: Factors Influencing Dressing Frequency and Technique in Diamond Tools
Key Factors Affecting Diamond Tool Dressing
Dressing frequency and the techniques employed are crucial for maximizing the performance and lifespan of diamond tools. Understanding the factors that influence these aspects can help optimize the dressing process for different tools and applications. Here are some of the primary factors:
1. Tool and Bond Characteristics
-
Type of Diamond Tool: The specific design and purpose of a diamond tool determine how it interacts with the material it cuts and, consequently, how it wears. For example, tools used for cutting hard, abrasive materials like reinforced concrete or granite will wear differently from those used for softer, less abrasive materials like marble.
-
Type of Cutting Edge: The configuration of the cutting edge—be it segmented, continuous, or turbo—significantly affects how the tool interacts with the material. Segmented blades are typically used for harder materials due to their ability to dissipate heat more effectively, while continuous rim blades are preferred for cutting softer, more brittle materials with a need for a smoother finish. Each type demands different dressing intervals and techniques to maintain optimal performance.
-
Edge Geometry: The shape and angle of the cutting edge also influence how a tool wears. A sharper angle might cut more aggressively but could also wear down more quickly, requiring more frequent dressing. Conversely, a blunter angle may endure longer but might not provide as precise of a cut, particularly in harder materials.
Bond Type and Its Impact on Dressing
-
Metal Bond: Metal-bonded diamond tools are common for cutting very hard materials such as stone and concrete. The bond is designed to wear at a rate that exposes new diamonds at the right time. Metal bonds can be hard or soft, with harder bonds generally requiring more forceful dressing to release new diamond particles.
-
Resin Bond: Resin-bonded diamond tools are often used for applications requiring a finer finish, such as in the polishing of stones or concrete. These bonds wear away more quickly than metal bonds and typically need less aggressive dressing techniques to maintain the cutting edges.
-
Ceramic Bond: Ceramic bonds are used when there’s a need for significant heat resistance, often in applications involving high-speed cutting. These bonds may require specific dressing techniques that take into account their thermal stability and wear characteristics.
-
Bond Hardness: The bond's hardness is critical in determining how the tool retains its diamonds and how quickly the bond wears away to expose new diamonds. A harder bond is generally more durable but may require more aggressive or frequent dressing to maintain cutting efficiency. Conversely, a softer bond may wear down more quickly, necessitating less aggressive dressing.
Diamond Crystal Characteristics
-
Grit Size: The size of the diamond particles plays a crucial role in how the tool performs and how often it needs dressing. Finer grits are typically used for finishing applications where a smooth surface finish is critical, but they may become dull more quickly and thus require more frequent dressing. Coarser grits are more durable and are used for initial rough cuts, potentially requiring less frequent dressing but more forceful techniques when needed.
-
Diamond Crystal Quality and Distribution: The quality of the diamonds and their distribution within the bond matrix can also affect dressing needs. High-quality diamonds evenly distributed in the matrix will result in more consistent wear and potentially longer intervals between dressings. In contrast, poorer quality or unevenly distributed diamonds might lead to uneven tool wear and more frequent need for corrective dressing.
-
Diamond Grit Size: Smaller diamond grits present a greater surface area and can become blunt more quickly than larger grits. Consequently, tools with finer grits may require more frequent dressing to maintain sharpness compared to those with coarser grits.
-
Concentration of Diamonds: The density of diamonds within the bond matrix also impacts dressing needs. High diamond concentration can slow down the rate of wear because more diamonds share the cutting load, reducing the wear on individual diamonds. However, this can also lead to glazing if not managed properly, as fewer bond areas are available to wear away and expose new diamonds.
2. Material Being Cut
-
Hardness and Abrasiveness: The material's hardness and abrasiveness directly impact how quickly a diamond tool wears. Harder and more abrasive materials can cause faster diamond dulling and matrix wear, requiring more frequent dressing.
-
Material Properties: Other properties, such as the brittleness or ductility of the material, also affect how a diamond tool interacts with it. Brittle materials tend to cause more shock and impact on the tool, potentially necessitating different dressing techniques compared to more ductile materials that may smear or load the tool.
3. Cutting Parameters
-
Cut Depth and Feed Rate: Deeper cuts and higher feed rates increase the load on the diamond tool, potentially accelerating wear and requiring more frequent dressing. Adjusting these parameters can help manage tool life and dressing frequency.
-
Spindle Speed (RPM): The rotational speed of the tool affects the cutting dynamics and heat generation. Higher speeds can lead to increased temperature, which may affect the bond's wear rate and the need for dressing.
4. Equipment Used
-
Tool Rigidity and Stability: Tools that operate in a more stable and rigid setup experience less vibration and thus wear more predictably, potentially reducing the frequency of dressing needed.
-
Machine Power and Capability: The power of the cutting machine can also influence how the tool performs and wears. Higher-power machines might drive the tool through materials more quickly but can also increase the wear rate if not matched with appropriate cutting parameters.
Signs your Diamond or CBN Tool needs Dressing – What you should look for
Diamond Section Glazing
The glazing of the diamond section in cutting blades is not just a superficial issue; it is often symptomatic of deeper underlying problems associated with the blade's operational settings, the material being cut, and the blade's specifications. Understanding these causes in detail is crucial for diagnosing and preventing glazing effectively.
Recognizing the early signs of diamond section glazing is crucial for maintaining the performance and longevity of diamond cutting blades. One of the most definitive indicators of this issue is the appearance of the blade's diamond section itself.
Dressing can be likened to routine maintenance on a vehicle. Just as regular oil changes and tire rotations keep a car running smoothly, dressing keeps diamond tools in optimal condition. Neglecting this maintenance can lead to problems such as reduced cutting efficiency and eventual tool failure. Conversely, consistent dressing ensures that diamond tools function effectively for extended periods.
For diamond tools to perform optimally, frequent dressing is necessary to properly expose the diamonds. Without adequate dressing, the tool surface may glaze over, causing the tool to tear rather than grind. This tearing generates excessive friction, leading to uneven wear, heat cracks in the tool, and damage to the material being machined. Such conditions result in premature tool wear, blade tensioning issues, and potential destruction of the diamond tool. Regular dressing keeps the tool cooler, enhancing its cutting performance.
Additionally, dressing is crucial for cleaning blades loaded with debris, which can clog the pores between abrasive particles. Cutting into a dressing plate introduces mechanical and thermal stress, which helps produce a clean tool surface.
Well-protruded and exposed diamonds are essential for easy material penetration. Poorly dressed diamond tools tend to push against the material, leading to high loads, elevated cutting temperatures, and suboptimal cut quality. This can also increase the risk of tool breakage. There are no universal guidelines on the frequency or timing of dressing; it depends on various factors such as diamond bond type, tool type, bond hardness, diamond grit size, and tool concentration. Application-specific factors also play a role, including the material’s hardness, density, porosity, diameter, shape, cut depth, equipment used, coolant, and operational RPMs.
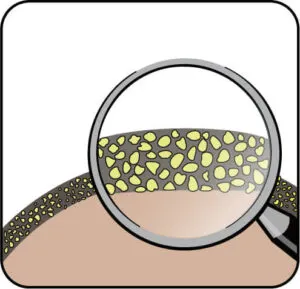
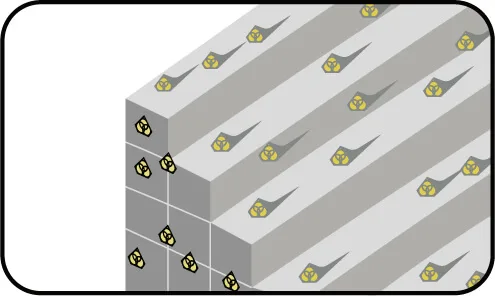
Smooth Surface on Diamond Section
When a diamond cutting blade is in optimal condition, the surface of the diamond section should show visible diamond particles protruding from the bond matrix. These exposed diamonds are critical for effective cutting, as they provide the abrasive action needed to cut through materials. However, when the blade becomes glazed, these diamond particles are no longer visible. Instead, the surface appears unusually smooth and may even have a shiny or reflective quality. This smoothness indicates that the diamonds are buried beneath the surface of the bond matrix, rendering them ineffective for cutting.
Lack of Visible Diamond Particles
In a healthy blade, the diamond particles are intentionally distributed throughout the bond matrix at varying depths. This staggered placement ensures that as the outermost diamonds wear down, new diamonds are exposed, maintaining the blade's cutting ability. A glazed blade, however, shows no such protrusion of diamonds. This can be due to several factors such as the diamonds being too deeply embedded within a hard bond matrix or the premature wearing down of the diamond tips without adequate exposure of new diamonds.
Reflective or Shiny Appearance
The reflective or shiny appearance of the blade's diamond section is another sign of glazing. This occurs when the metal bond around the diamonds becomes polished by contact with the material being cut, without sufficient diamond exposure to maintain abrasion. This polished surface reflects light, unlike a properly functioning diamond blade, which should appear matte due to the rough texture provided by the exposed diamonds.
Consistency Across the Blade Surface
Another aspect to consider is the consistency of the surface appearance across the entire diamond section. In cases of glazing, the smooth and reflective characteristics are typically uniform across the blade's surface, indicating a widespread issue with diamond exposure. This uniformity differentiates glazing from other wear patterns, such as localized wear or segment damage, which might affect only part of the blade.
By paying close attention to these signs—smoothness, lack of visible diamonds, shiny appearance, and uniformity—operators can identify potential glazing issues before they significantly impact the blade’s performance. Early detection allows for timely intervention, such as blade dressing or adjustments in operational parameters, to restore the blade's cutting efficiency and extend its usable life.
Slow Cutting
A significant slowdown in the cutting speed of a diamond tool is often the first indicator that dressing is needed. This usually occurs because the diamond cutting edges are becoming dull or have been glazed over by material residues. Dressing the tool can expose new, sharp diamond particles, restoring its cutting efficiency.
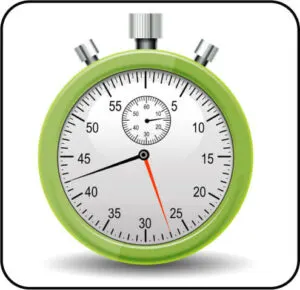
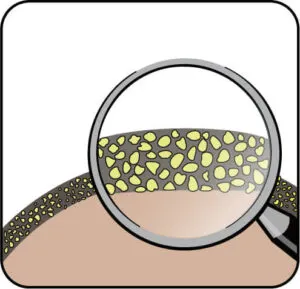
Not Cutting
If a diamond tool stops cutting entirely, it may be due to the diamond particles being completely worn down or covered by swarf and other debris. This state requires immediate dressing to remove the blunt or blocked diamonds and reveal new, sharp layers.
Diamond Tool Starts to Burn
Burning of the diamond tool itself generally indicates excessive heat buildup during the cutting process. This excessive heat could be due to a lack of adequate coolant, overly dull diamond edges, or inappropriate cutting parameters. Dressing helps in re-exposing sharp diamonds and reducing the friction and heat generation. it might be due to increased friction caused by a dull tool. Excessive heat can damage both the tool and the machine, so if you notice unusual heat accumulation, it could be time to check and dress the tool.
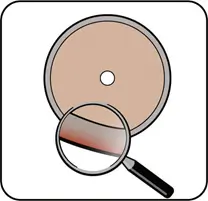
Sparks Coming from Cutting Zone
The presence of sparks during cutting typically signals that the tool is either too dull or that the bond holding the diamonds is wearing unevenly. Sparks are a result of excessive friction and metal-to-metal contact, which should not occur if the diamonds are cutting efficiently. Dressing removes the worn diamond layer and helps realign the tool's cutting surface.
Diamond Tool not Cutting True
If a diamond tool does not produce straight or accurate cuts, it might be misaligned or unevenly worn. This misalignment can result from uneven diamond wear or mechanical issues with the tool itself. Dressing and realigning the tool can correct this, ensuring accurate and precise cuts.
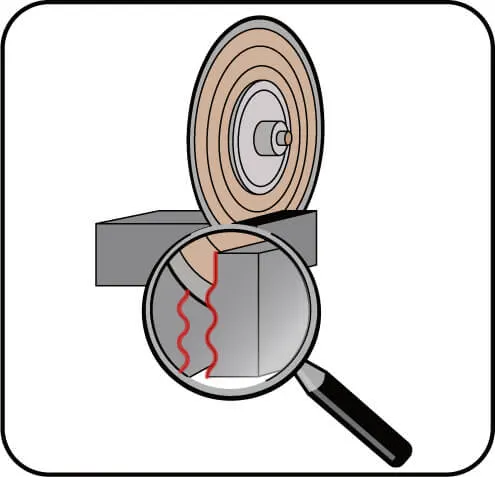
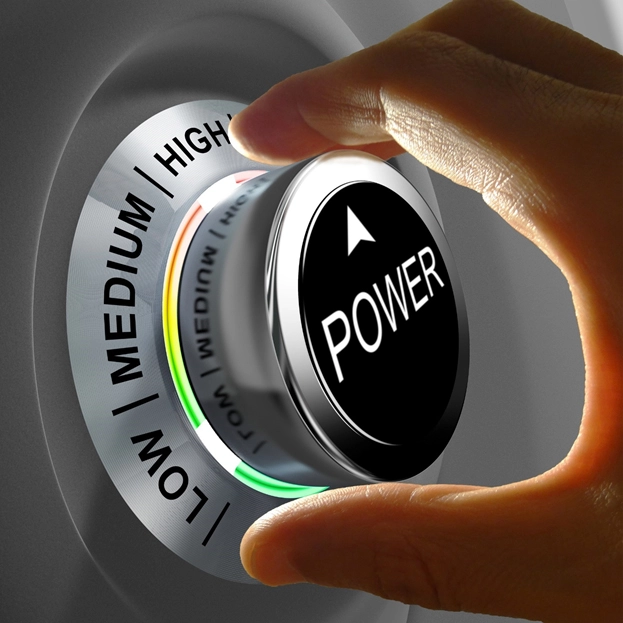
Increased Power Consumption
An increase in the power required to operate the tool can indicate that the tool is working harder than normal to achieve the same results. This is often due to a dull blade or worn diamonds, which increase the resistance during cutting, thus requiring more power.
Unusual Noise or Vibration / Changes in Sound During Cutting
Unusual noises or increased vibration during operation can be a sign of an unbalanced tool or one that has uneven wear. These vibrations are not only a sign that the tool needs dressing but can also be detrimental to the precision of the cuts and the overall health of the machinery. Aside from general noise or vibration, a change in the sound quality during cutting—such as a higher-pitched screeching or grinding noise—can indicate that the diamonds are not cutting cleanly. This auditory cue often suggests the tool needs immediate attention.
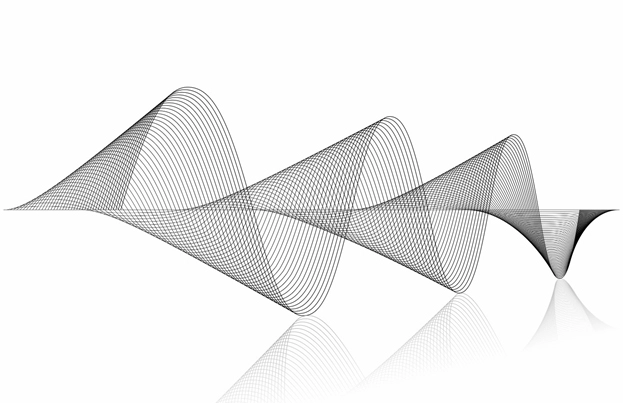
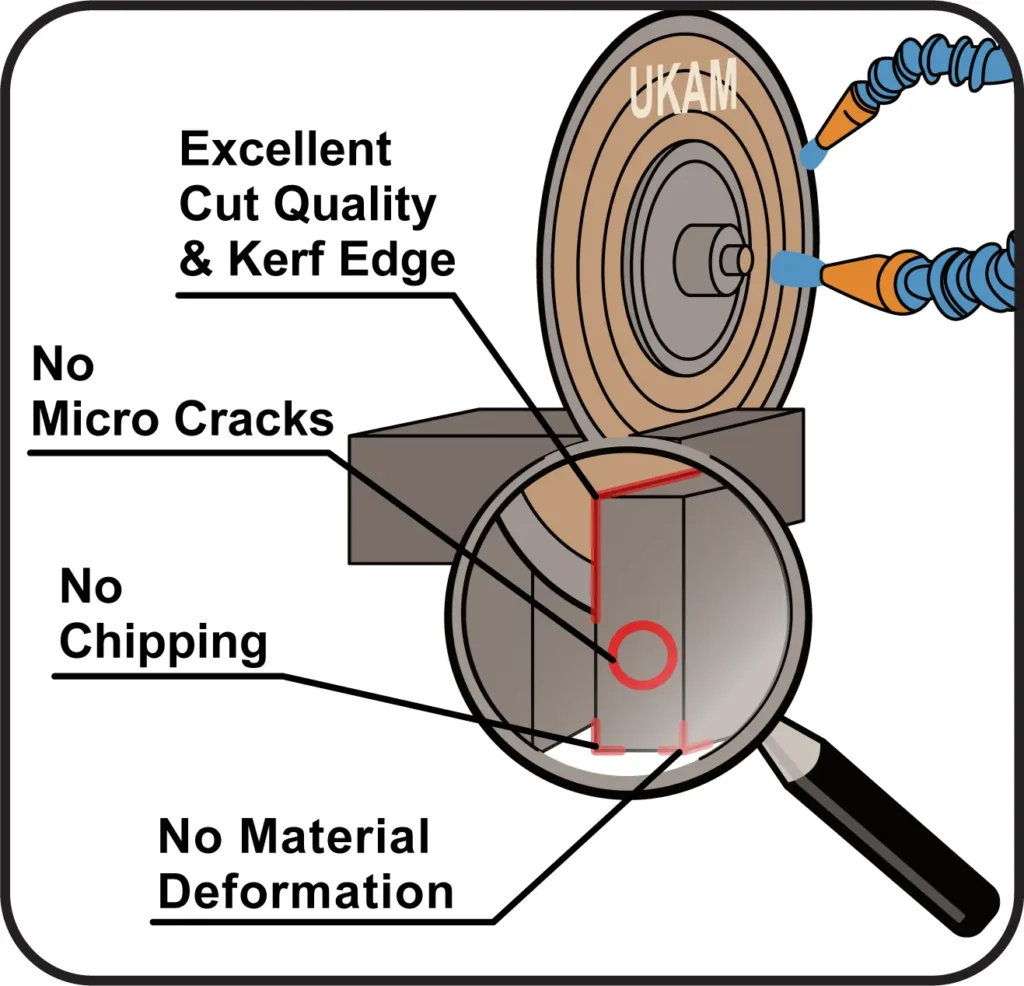
Reduced Cutting Quality
If the finish of the cut starts deteriorating, with the outcomes appearing less smooth or precise than usual, it might indicate that the tool’s diamonds are becoming dull. Dressing the tool can help restore its ability to produce a high-quality finish.
Change in Chip Size or Type
In processes where material removal is visible, such as sawing or grinding, a change in the size or type of chips can indicate tool dullness. Sharp tools produce consistent, predictable chips, while dull tools often create fine dust or very small, irregular particles.
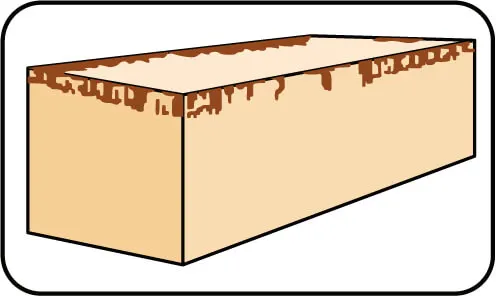
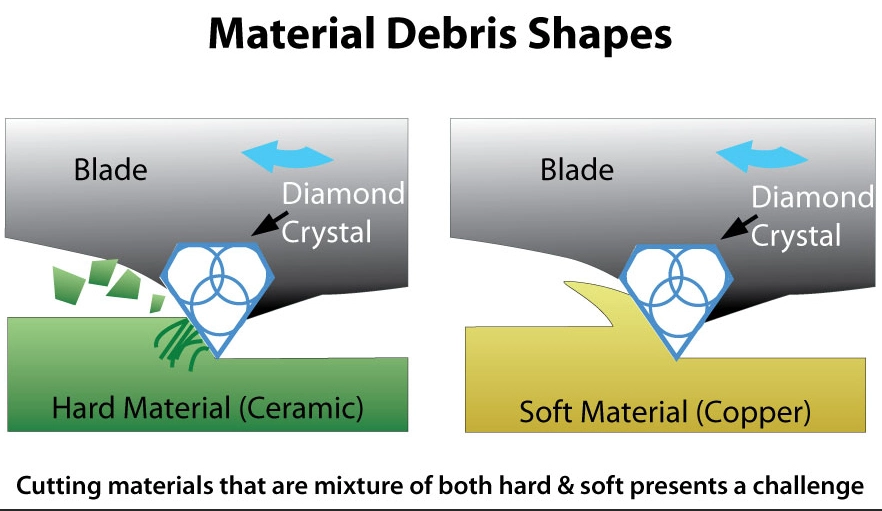
Difficulty in Initiating Cuts
If a tool struggles to begin a cut or requires more force to penetrate the material, this can be a clear sign that the cutting edges are no longer effective. Dressing the tool can help to reinstate the sharpness needed for easy material penetration.
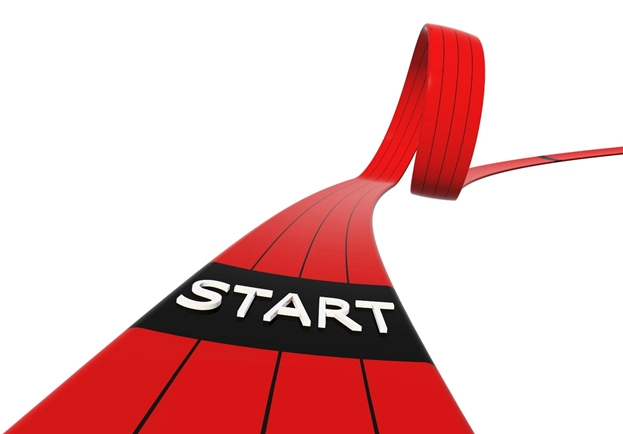
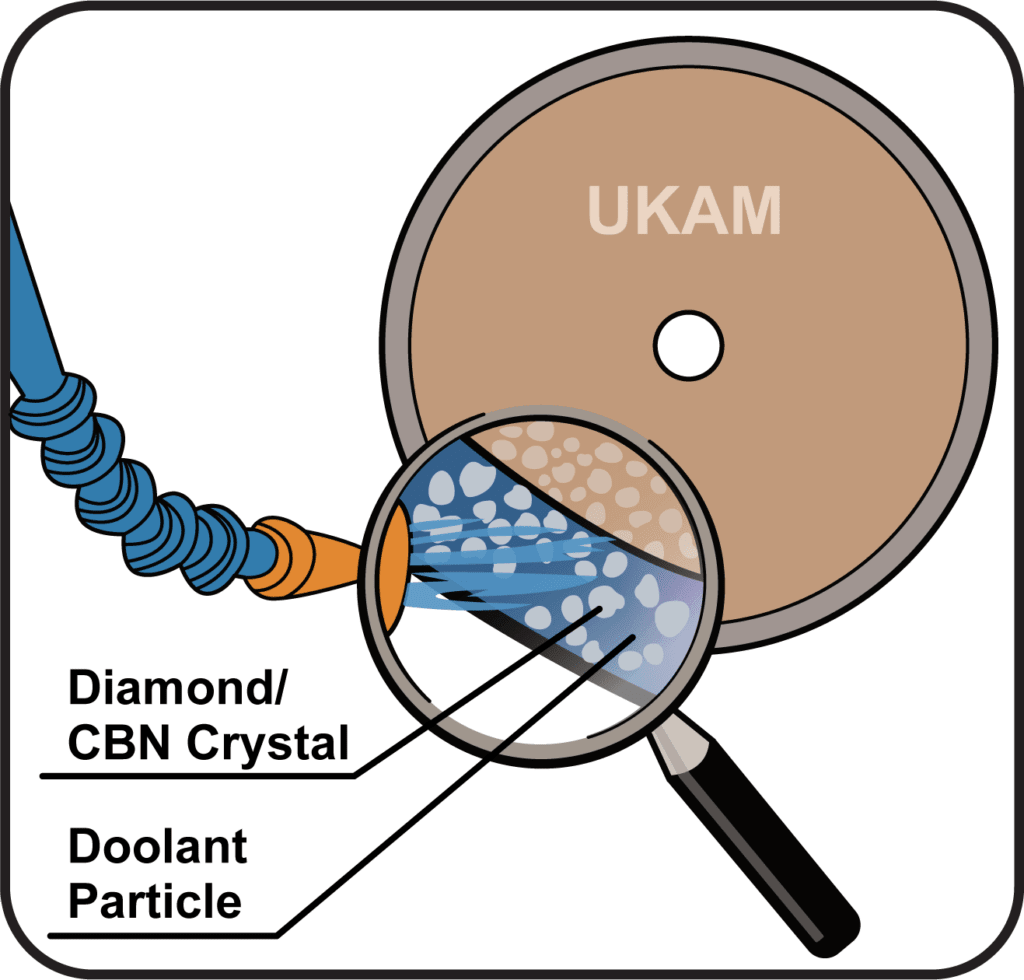
Increase in Coolant Usage
Needing more coolant than usual can signal that the tool is generating excessive heat due to dullness. While increasing coolant flow can help manage the temperature, it's often a temporary solution compared to dressing, which addresses the root cause.
Increased Tool Deflection
Tool deflection refers to the bending or deviation of the tool away from its intended path during cutting. This can be caused by blunt diamond particles not cutting effectively, thereby applying uneven forces on the tool. Dressing the tool restores its precision and reduces deflection.
Increase in Downforce Required
Needing to apply more downforce to achieve cuts can be a sign that the diamonds on the tool's surface are worn out. This is particularly relevant in processes like grinding, where effective cutting relies on minimal force with maximum contact.
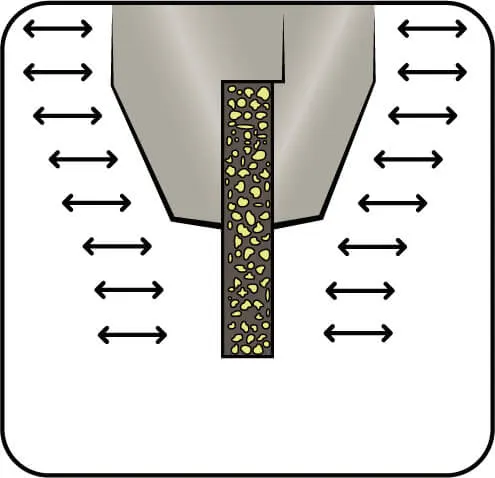
Buildup of Material on the Tool /Material Particles Smeared over Diamond section
Material buildup on the tool can impede the cutting process, obscuring the diamonds and preventing them from engaging with the material properly. Regular cleaning and dressing can remove this buildup and maintain cutting efficiency. Material swarf, which comprises fine debris, particles, or remnants from the cutting process, can adhere to the diamond section of a blade, especially when using certain materials that have a tendency to melt or gum up. This can occur due to several factors, including excessive heat generation, inadequate coolant flow, or the use of improper cutting parameters for the material.
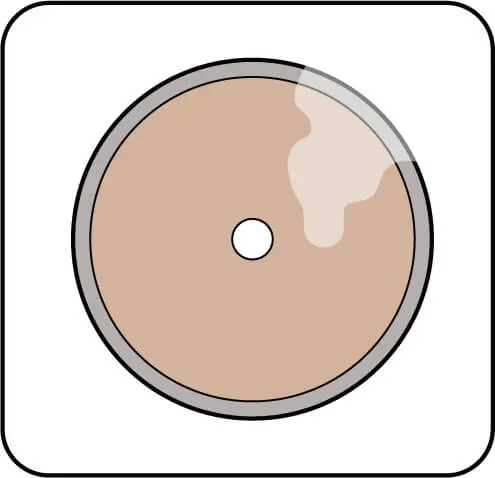
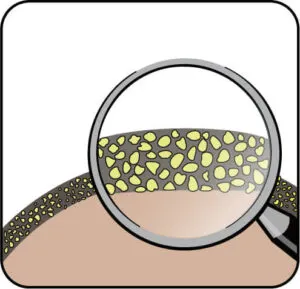
Excessive Visual Wear on Diamond Layer
A visual inspection might reveal significant wear on the diamond layer itself, such as flattened or smoothed-over diamonds. This wear is a clear indication that the cutting edges are no longer optimal and require dressing.
Visible signs of wear on the tool body itself, such as on the binder or the core, might suggest that the diamonds are not protruding enough to do their job effectively. This can force the body of the tool to make contact with the material, which it is not designed to do.
Unexpected Patterns on Cut Surfaces
If the surfaces being cut start showing unexpected patterns, marks, or indentations, it could suggest uneven wear or exposure of the diamond particles on the tool. These surface marks often highlight the need for a dressing process to even out the tool's cutting face.
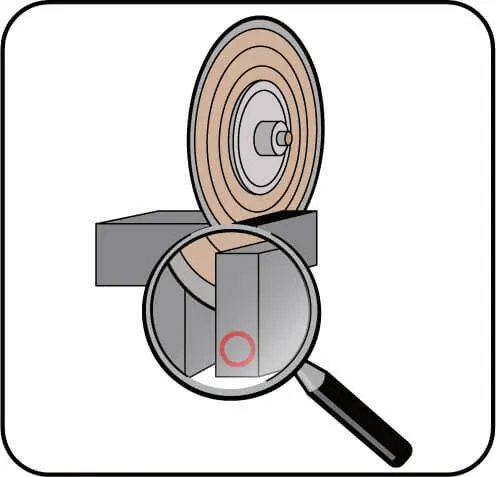
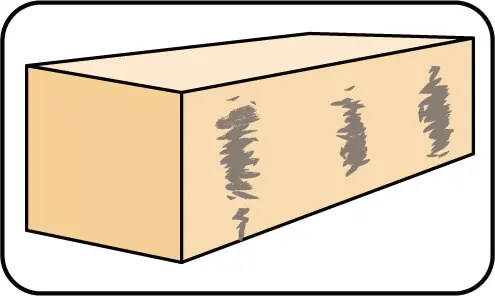
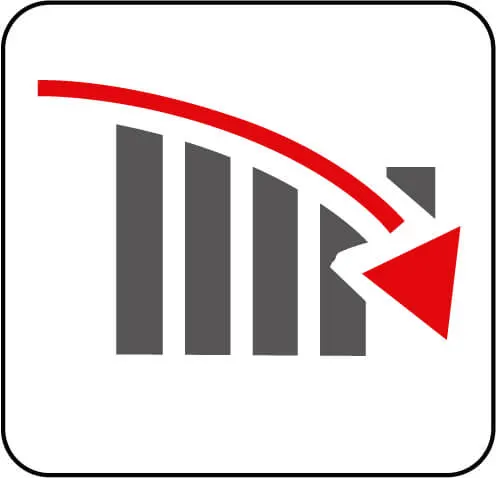
Slow Cutting
As previously mentioned, slow cutting can be one of the first indicators that a diamond tool needs attention. This typically occurs when the cutting edges of the diamonds become blunt or are coated with material residue. The tool struggles to cut at its usual pace, leading to reduced productivity and potentially suboptimal cuts.
Stops Cutting
When a diamond tool stops cutting entirely, it indicates that the diamonds on the surface are either completely worn out or excessively clogged with debris. This prevents them from engaging with the material effectively, necessitating immediate dressing or potentially even replacement if the tool is beyond repair.
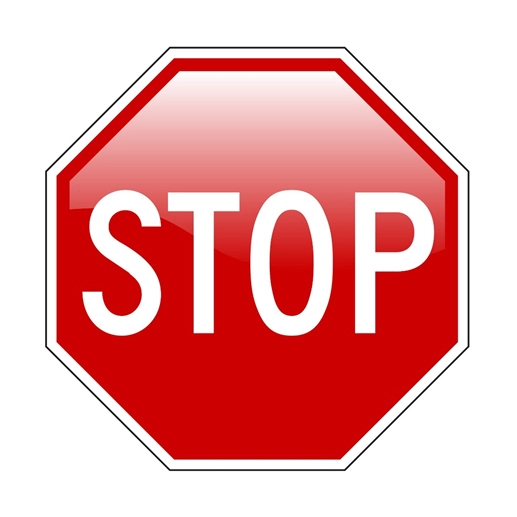
Material Burning / Overheating
Material burning occurs when the tool generates excessive heat due to friction, often because the diamonds are too dull to cut efficiently. The heat can cause the material to burn or melt, especially in sensitive materials like plastics or certain metals. This not only affects the integrity of the material but can also damage the tool itself.

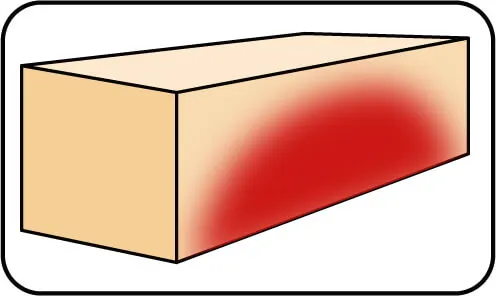
Material Chipping
Chipping can result from several issues, including the use of a diamond tool that has uneven or damaged diamond particles. If the diamonds do not cut smoothly, they can cause the material to chip around the edges, leading to a lack of precision and potentially ruining the workpiece.
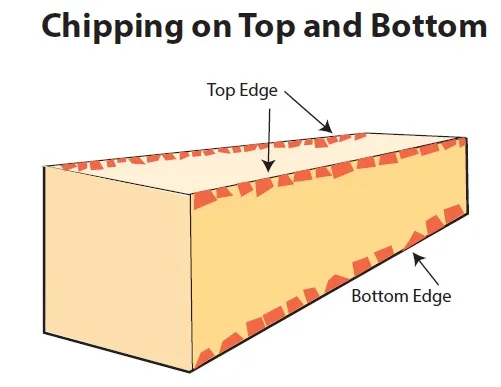
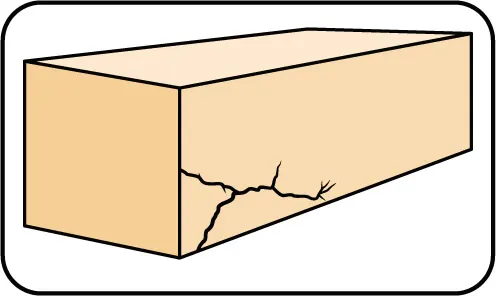
Material Micro Cracks
Micro cracks in the material being cut are often a sign of excessive vibration or uneven cutting pressure from the tool. This can be due to misalignment, uneven wear of the diamonds, or improper cutting parameters. Dressing the tool can help realign the diamonds and reduce these vibrations.
Sparks Coming from Point of Material Contact
Sparks during the cutting process are typically a sign of excessive wear and friction at the point of contact. This usually means the diamonds are too worn to cut efficiently, leading the metal backing or bond material to contact the workpiece, generating sparks. It’s crucial to address this immediately to avoid further damage.
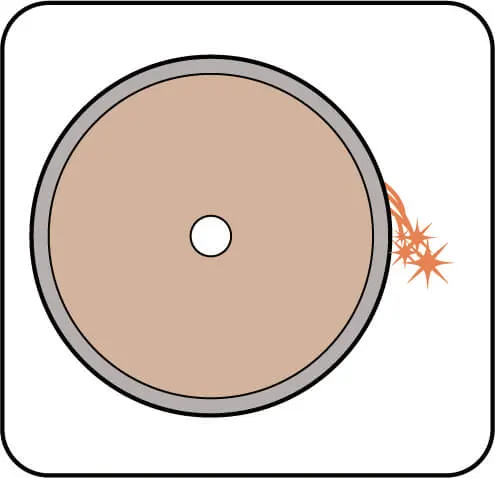
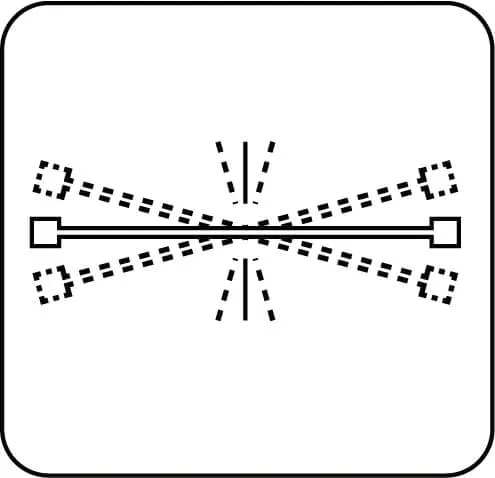
Not Cutting True
If a diamond tool does not produce straight or accurate cuts, it suggests an issue with the alignment or uniformity of the diamond particles. This could be due to uneven wear, poor initial alignment, or a deformation of the tool under stress. Dressing and correctly aligning the tool can correct this issue and ensure precise cuts.
How to dress:
Dressing procedures are established by the end user and based on experience and the application concerned. There is not one common method that applies to all applications.
Dressing stick used to dress the blade should be same or similar diamond grit/mesh size as the wafering blade being dressed.
To begin the dressing of diamond tools, ensure that both the dressing stone and the diamond tool are clean and free of any debris to avoid embedding foreign particles during the dressing process. Consider using a dressing stick that is slightly finer than the grit size of the diamond tool to achieve a smoother finish and better expose new diamonds.
Align the diamond tool with the dressing stone, ensuring stable and consistent contact for even dressing across the tool's surface. Engage the tool into the dressing stone to a depth typically a few millimeters to expose the diamonds embedded within the matrix. Perform multiple, light passes instead of a single heavy pass to evenly expose the diamond particles and reduce the risk of removing too much material from the tool. Soaking the dressing stick in water before use helps keep both the stone and tool cool, minimizing the risk of thermal damage to the diamond particles, which can affect their cutting efficiency.
After several passes, stop to examine the tool for even exposure of diamond particles across the cutting surface. Test the tool on a piece of scrap material to assess its cutting performance. If the results are not satisfactory, further dressing may be necessary.
Regular inspection of the tool for wear and maintaining the dressing stone in good condition are crucial. Replace the dressing stone if it becomes too smooth or contaminated as it can impact the effectiveness of the dressing process. Regular and proper dressing of diamond tools not only increases the efficiency, enabling faster and easier cuts which improve productivity but also enhances cutting quality by maintaining a clean and sharp cutting edge. This leads to better surface finish and dimensional accuracy of the material being cut. Moreover, regular exposure of new diamond particles reduces tool wear, extending the operational life of the tool and improving safety by reducing the likelihood of binding or kickback during operation.
When dressing the tool, it's important to apply consistent pressure and maintain the correct angle relative to the dressing stone to achieve an even wear and proper exposure of new diamonds. This careful handling helps avoid undue stress on any part of the tool, which can lead to premature wear or failure.
Difference between dressing and truing
Understanding the difference between truing and dressing of diamond tools is crucial for maintaining their performance and longevity. Both processes are essential, yet they serve distinct purposes and are often confused. Here's a detailed look at each process and its significance:
Truing
Truing is primarily focused on ensuring that the diamond tool is geometrically correct and concentric with the axis of rotation. This process involves:
-
Grinding Away the Diamond Bond Matrix: The objective is to reshape the tool so that it spins with minimal vibration when in use. This is vital for precision cutting where even minor deviations can lead to significant discrepancies in the final product.
-
Achieving Concentricity: The tool must be reshaped so that its cutting surface is perfectly aligned with the desired cutting path. This alignment minimizes the tool's deviation from the axis and ensures that the cutting force is uniformly distributed.
-
Surface Condition After Truing: Typically, truing leaves the diamond tool with a smooth surface. While this might be ideal for some applications, it often results in reduced efficiency in material removal as there is less diamond crystal protrusion for effective cutting.
Dressing
Dressing takes over where truing leaves off. It is aimed at enhancing the tool's cutting efficiency by exposing the sharp diamond crystals. The process involves:
-
Opening the Bond Face: This is done to expose new, sharp diamond crystals at the surface of the tool. It ensures that the tool can cut more effectively by providing new cutting edges.
-
Exposing Sharp Diamond Crystals: By removing some of the bond matrix, dressing exposes the diamonds embedded within. These exposed diamonds are critical for chip generation and removal, which is essential for efficient cutting and prevents the tool from burning the material due to friction.
-
Enhanced Cutting Performance: Properly dressed tools provide faster and freer cutting speeds, which not only increase efficiency but also reduce the thermal stress on both the tool and the material being processed.
Why Both Truing and Dressing are Necessary
Ensuring that diamond tools are both trued and dressed on the machine on which they will be used guarantees optimal performance:
-
Thorough Exposure of Diamonds: Dressing after truing ensures that enough diamond crystals are exposed for effective cutting. This is critical because a smoothly trued tool without adequate diamond exposure will not perform efficiently.
-
True in Running (T.I.R.): This refers to the tool running true to the machine's axis, minimizing mechanical and thermal stresses during operation. When a tool is trued and dressed on the machine it will be used on, it aligns perfectly with the operational parameters of that specific setup.
Differences between the truing and dressing processes for diamond tools:
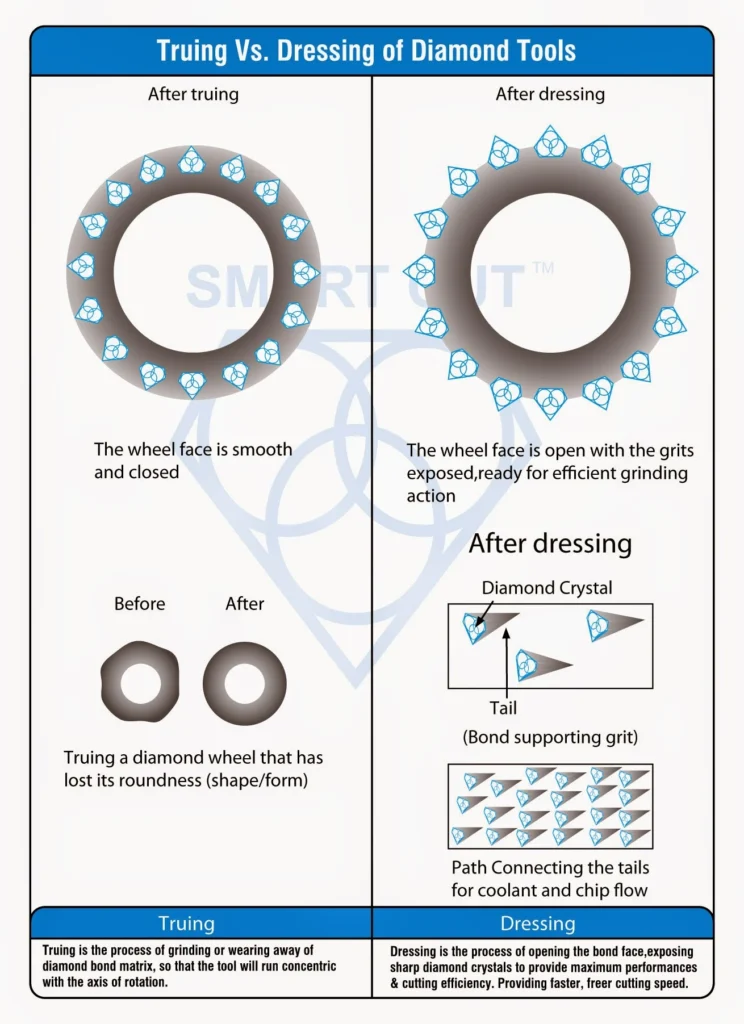
Aspect |
Truing |
Dressing |
---|---|---|
Purpose |
To make the tool concentric with the machine's axis of rotation. |
To expose new, sharp diamond crystals for effective cutting. |
Process |
Grinding away part of the diamond bond matrix to reshape the tool. |
Removing parts of the bond matrix to expose sharp diamond crystals. |
Result on Tool |
Creates a smooth surface with little or no diamond crystal protrusion. |
Creates a rougher surface with prominent diamond crystals for efficient cutting. |
Objective |
To ensure the tool runs without vibration and is geometrically accurate. |
To increase cutting efficiency, speed, and material removal capability. |
Surface Condition |
Smooth, which can lead to less efficient material removal and potential for burning the material. |
Rough, with exposed diamonds that enhance chip generation and removal. |
Chip Generation |
Limited due to smooth surface. |
Enhanced due to exposed sharp diamonds. |
When Necessary |
Initially to correct geometrical errors or after significant wear that affects the tool's concentricity. |
Regularly, to maintain optimal cutting efficiency as the tool is used and diamonds become worn or covered. |
Effectiveness |
Essential for precision and reducing tool wear due to imbalance. |
Crucial for maintaining cutting speed and efficiency, especially important in continuous or heavy-duty operations. |
Machine Dependency |
Must be performed on the machine where the tool will be used to ensure accuracy. |
Also should be performed on the machine where the tool will be used to ensure effective cutting. |
Aspect |
Truing |
Dressing |
Frequency of Need |
Often required less frequently than dressing, unless the tool is subjected to abnormal wear or damage. |
Needed more frequently to ensure continuous exposure of new diamonds for optimal cutting. |
Technique |
Involves precision machining techniques, which might include using specialized truing devices. |
Typically done using a dressing stick or stone that matches or is slightly finer than the tool's diamond grit. |
Time and Cost |
Can be time-consuming and may require costly equipment, but it is essential for tool precision. |
Relatively quicker and less costly compared to truing, but critical for maintaining tool efficiency. |
Material Impact |
Minimal material is removed from the tool itself, mostly reshaping existing materials. |
More material is removed from the tool to expose new cutting surfaces, which can slightly reduce the tool's life. |
Operational Impact |
Improves the balance and reduces vibrations, leading to smoother operations and better precision. |
Directly increases the cutting performance and can reduce the force required for cutting, saving energy. |
Safety |
Reduces the risk of tool breakage or damage due to imbalance or misalignment. |
Reduces the risk of overheating and potential damage to both the tool and the material being processed. |
Skill Level Required |
Generally requires more technical skill and understanding of machine dynamics. |
Less technically demanding but requires consistent application to maintain peak tool performance. |
Overall Benefit |
Maximizes the tool's life by ensuring it runs true, thereby avoiding premature wear. |
Maximizes the tool's cutting ability and efficiency, directly impacting productivity and output quality. |
Remember that every machine runs differently. And even if the diamond tool is trued at the factory, it can still “run-out” of tolerance when you place it on your machine. Blades must be trued and drills must be indicated in. Truing a tool is the operation of squaring a tool so it runs within your tolerances. This may be done with a hard stone that will knock diamonds out. This operation differs from dressing. It is still necessary to dress the tool after truing as the diamonds will no longer be sticking-up.
After truing the diamond tool, it is important to dress it to make sure the diamonds are exposed. The diamonds must be sticking up “exposed” from the bond matrix. If this is not accomplished, you will experience difficulty with your new diamond tool. A diamond tool that is thoroughly dressed will have diamond “tails” extending from the back of the diamond. Your diamond tool is now “directional”. This means it should always run in the direction the leading edge of the diamond, away from the tail. So the sharper, leading edge of the diamond can achieve desired cutting action.
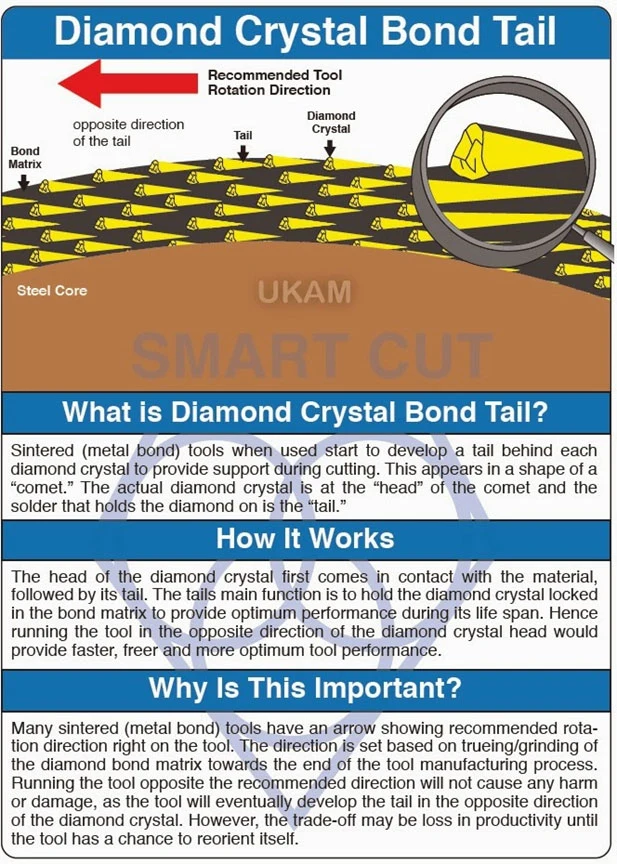
Selecting the Right Dressing Stick for Your Application
Selecting the appropriate dressing stick for your diamond or CBN tools is critical to maintaining tool performance and achieving optimal cutting or grinding results. This guide delves into the key factors and variables involved in choosing the right dressing stick for various applications.
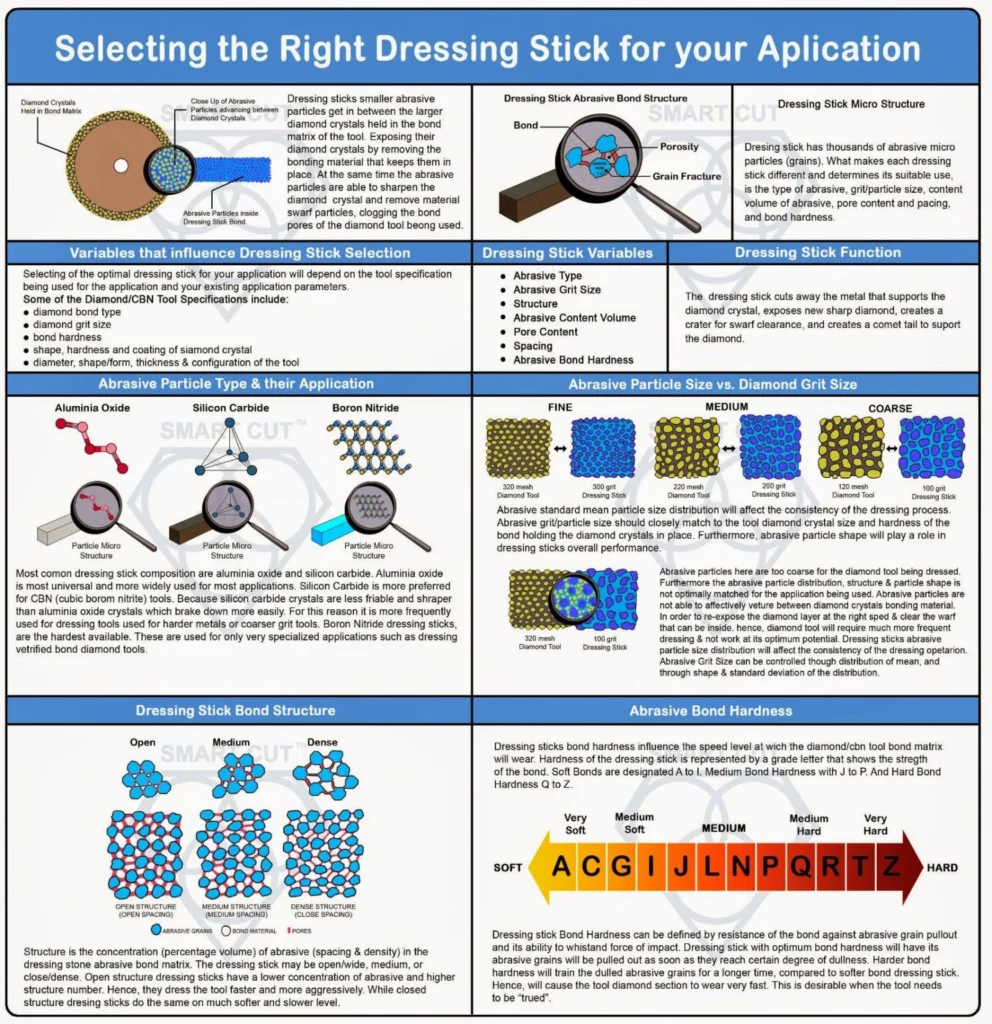
1. Variables Influencing Dressing Stick Selection
To determine the optimal dressing stick, consider the following specifications of your diamond/CBN tool:
-
Diamond Grit Size: The size of the diamond particles in the tool.
-
Bond Hardness: The material binding the diamond particles together.
-
Shape, Hardness, and Coating of Diamond Crystals: These factors impact the cutting or grinding efficiency.
-
Tool Geometry: The diameter, shape, and configuration of the tool influence the dressing stick choice.
When selecting the appropriate dressing stick for diamond or CBN tools, it is crucial to consider several key factors to ensure optimal tool performance and efficiency.
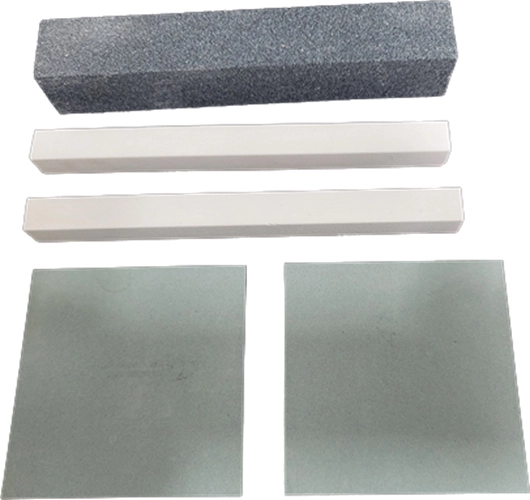
Firstly, the diamond grit size, which measures the size of the diamond particles within the tool’s matrix, plays a significant role. Fine grits, ranging from 100 to 220 mesh, are ideal for applications requiring precision and a smooth surface finish. Medium grits, between 230 and 300 mesh, offer a balanced approach, providing both cutting speed and quality finish, making them suitable for general-purpose applications. Coarse grits, from 310 to 400 mesh, are preferred for rough cutting operations due to their capability for rapid material removal. When selecting a dressing stick, it is important to match its abrasive grit size with that of the tool to ensure effective dressing without causing excessive wear. Utilizing a dressing stick with a slightly finer grit than the tool can further enhance cutting efficiency by exposing fresh, sharp diamond edges more effectively.
Bond hardness, the strength of the material binding the diamond particles, is another critical factor. Tools with hard bonds are designed for high-load applications, providing greater durability and stability under heavy cutting conditions. In contrast, soft bonds are more suitable for lower-load applications, as they allow for easier dressing and greater flexibility. It is essential to choose a dressing stick with an abrasive hardness that can break down the bond material effectively without damaging the tool. For high-precision applications, a softer bond may be advantageous, permitting more frequent and precise dressing to maintain optimal tool sharpness.
The shape, hardness, and coating of diamond crystals also significantly impact tool performance. The geometric form of the crystals can be blocky, angular, or irregular, influencing cutting dynamics and wear resistance. Blocky crystals tend to be more durable and provide consistent cutting, while angular crystals offer more aggressive cutting but may wear out faster. The hardness of the crystals, typically measured on the Mohs scale, determines their ability to maintain sharpness, with harder crystals being more suitable for abrasive materials. Coatings such as nickel or titanium can enhance the crystals’ thermal stability and reduce friction, thereby improving tool life and performance. When choosing a dressing stick, it is important to ensure it can effectively shape and maintain the geometry of the diamond crystals and penetrate any coatings to expose the underlying diamond for optimal cutting.
Tool geometry, which includes the shape, size, and configuration of the tool, is another important consideration. Large-diameter tools require dressing sticks that provide even coverage across the entire surface, while thin or precision tools need dressing sticks designed for delicate operations to avoid damage. Selecting dressing sticks that complement the tool’s geometry ensures uniform dressing and maintains the tool’s structural integrity. For tools with unique shapes, custom or specially designed dressing sticks may be necessary to match specific contours and profiles.
2. Dressing Stick Variables
Several critical variables affect the performance of dressing sticks:
-
Abrasive Type: Common types include aluminum oxide, silicon carbide, and boron nitride.
-
Abrasive Grit Size: Should be matched or slightly finer than the diamond tool’s grit size.
-
Abrasive Content Volume: The amount of abrasive material present in the stick.
-
Pore Content and Spacing: Influence the stick’s ability to expose diamond particles.
-
Abrasive Bond Hardness: Determines the durability and effectiveness of the stick.
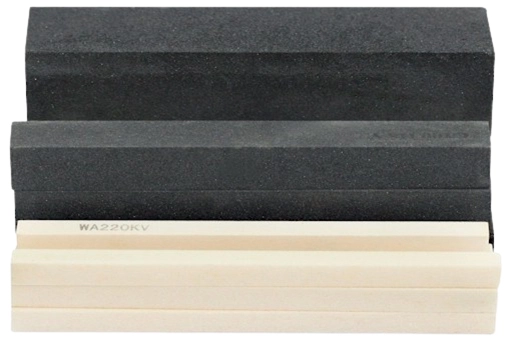
The performance of dressing sticks is influenced by several critical variables, each playing a significant role in ensuring effective tool maintenance and optimal operational outcomes.
One of the primary factors is the abrasive type used in the dressing stick. The most common abrasives include aluminum oxide, silicon carbide, and boron nitride. Aluminum oxide is widely utilized for general applications due to its versatility and cost-effectiveness. It is suitable for a range of materials and provides a good balance between durability and cutting efficiency. Silicon carbide is preferred for applications involving cubic boron nitride (CBN) tools, as its sharper and harder particles are effective in conditioning the cutting edges. This makes silicon carbide ideal for operations requiring high precision and minimal surface roughness. Boron nitride, though less common, is employed for specialized applications that demand extremely high hardness and thermal stability. Its unique properties make it suitable for advanced and demanding grinding tasks, where conventional abrasives may not suffice.
Abrasive grit size is another crucial variable, significantly impacting the dressing stick’s effectiveness. It is essential to match the abrasive grit size of the dressing stick with the diamond tool’s grit size to ensure efficient dressing. A grit size that is slightly finer than the tool’s grit can enhance the sharpness of the cutting edges by exposing fresh diamond particles more effectively. This matching ensures that the dressing stick can efficiently abrade the bond material without excessive wear, maintaining the tool’s cutting efficiency and surface finish quality.
The abrasive content volume within the dressing stick is also a vital consideration. This refers to the amount of abrasive material present in the stick, influencing its ability to maintain consistent dressing performance. A higher abrasive content volume generally provides more aggressive dressing action, facilitating quicker exposure of new diamond particles. Conversely, a lower abrasive content volume may be suitable for fine or delicate operations, where precision is more critical than rapid material removal.
Pore content and spacing within the dressing stick are important for controlling the exposure of diamond particles. The pores in the dressing stick help to remove debris and prevent clogging, ensuring continuous and effective dressing. Proper spacing of these pores is crucial to balance the removal of bond material with the maintenance of tool sharpness. Adequate pore content allows for efficient swarf removal, reducing the risk of overheating and ensuring a cleaner cutting process. This characteristic is particularly important in applications involving high-speed or high-pressure operations, where heat management is critical.
Abrasive bond hardness determines the dressing stick’s durability and effectiveness. The bond hardness refers to the strength of the material that holds the abrasive particles together. Dressing sticks with softer bonds break down more quickly, exposing fresh abrasive grains and providing a sharper cutting action. These are ideal for softer materials or applications requiring frequent dressing. Harder bonds, on the other hand, offer greater durability and are suitable for harder materials or applications where dressing is less frequent. The choice of bond hardness should align with the hardness of the diamond tool’s bond to ensure efficient dressing without excessive wear on the dressing stick or the tool.
3. Dressing Stick Function
The primary function of a dressing stick is to expose new diamond particles by removing the worn matrix material. This creates a clean, sharp edge on the tool, enhancing cutting performance and extending tool life.
4. Abrasive Particle Type and Their Application
-
Aluminum Oxide: Widely used for general applications due to its versatility and availability.
-
Silicon Carbide: Preferred for CBN (cubic boron nitride) tools due to its sharper, harder particles, which are effective in conditioning the tool’s cutting edges.
-
Boron Nitride: Utilized for specialized applications requiring very high hardness and thermal stability.
The performance and suitability of dressing sticks are greatly influenced by the type of abrasive particles they contain. Each type of abrasive particle brings unique characteristics that make it suitable for specific tasks and materials, thereby playing a crucial role in tool maintenance.
Aluminum oxide is a widely used abrasive due to its versatility and availability. It is favored for general-purpose applications because of its cost-effectiveness and balanced properties, making it an ideal choice for a variety of dressing tasks. The particles of aluminum oxide are durable, providing a good balance between toughness and hardness, which allows them to maintain their shape and cutting efficiency over time. This makes aluminum oxide dressing sticks particularly effective for conditioning tools used in metalworking, woodworking, and various fabrication processes. They are compatible with a broad range of tools, including diamond grinding wheels and cutting blades, due to their well-rounded performance characteristics. Additionally, aluminum oxide is especially effective in achieving smooth surface finishes on workpieces, making it a preferred choice for applications that demand fine surface quality.
Silicon carbide, known for its sharper and harder particles, offers enhanced cutting and grinding capabilities compared to aluminum oxide. It boasts excellent thermal conductivity, which helps dissipate heat during the dressing process, thus reducing the risk of overheating. Silicon carbide dressing sticks are particularly well-suited for conditioning CBN (cubic boron nitride) tools, as their sharper and harder particles effectively dress the harder bond materials found in these tools, exposing fresh cutting edges.
This makes silicon carbide ideal for precision grinding and finishing tasks where maintaining tool sharpness is critical. Furthermore, its properties make it suitable for high-pressure applications, such as grinding hard metals and ceramics, where aggressive material removal is required.
Boron nitride stands out due to its extreme hardness and superior thermal stability. These characteristics make it an exceptional choice for high-temperature applications where other abrasives might fail. Boron nitride dressing sticks are used in specialized applications that demand very high hardness and thermal stability, such as machining superalloys, advanced ceramics, and other extremely hard materials.
This makes them particularly useful in precision machining tasks that require consistent performance and minimal tool wear. Due to its remarkable properties, boron nitride is commonly employed in the aerospace and automotive industries for dressing tools involved in manufacturing high-performance components. Its extreme hardness ensures extended tool life, significantly reducing the frequency of dressing and tool replacement, while its thermal stability maintains tool sharpness and efficiency even under high temperatures.
5. Abrasive Particle Size vs. Diamond Grit Size
-
Fine Grit (100-220 Mesh): Ideal for precise, fine finishes. Use a dressing stick with a similar or slightly finer grit.
-
Medium Grit (230-300 Mesh): Suitable for a balance of cutting efficiency and surface finish. Match with a medium-grit dressing stick.
-
Coarse Grit (310-400 Mesh): Best for aggressive material removal. Pair with a coarser dressing stick.
Fine Grit (320-600 Mesh)
Fine grits are essential for applications requiring high precision and a very fine surface finish. These grits are ideal for finishing operations where the smoothness and detail of the final product are critical. When using tools with fine diamond grit, it is advisable to select a dressing stick with a similar or slightly finer grit. This ensures that the dressing stick can effectively expose new diamond particles while maintaining the tool’s precision, resulting in a clean and polished finish on the workpiece.
Medium Grit (150-320 Mesh)
Medium grits provide a balanced approach between cutting efficiency and surface finish quality. They are suitable for general-purpose applications where both cutting speed and surface quality are important. For tools with medium diamond grit, a medium-grit dressing stick is appropriate. This selection allows the dressing stick to condition the tool effectively, enhancing its cutting ability while ensuring a good surface finish. The medium grit size is versatile, making it suitable for a wide range of tasks.
Coarse Grit (100-150 Mesh)
Coarse grits are best suited for tasks that require aggressive material removal. These grits are typically used in rough cutting or grinding operations where rapid material removal is more important than the quality of the surface finish. For tools with coarse diamond grit, it is recommended to use a coarser dressing stick. This ensures that the dressing stick can efficiently remove the bond material and expose new, sharp diamond particles, thereby maintaining the tool’s aggressive cutting capability, which is crucial for high-speed material removal.
6. Dressing Stick Bond Structure
-
Open Structure: Features lower density, allowing for more aggressive dressing and effective debris removal.
-
Dense Structure: Higher concentration of abrasive particles, suitable for fine, precise dressing applications.
The bond structure of a dressing stick is crucial in determining its performance and suitability for different dressing tasks. Dressing sticks with an open structure are characterized by a lower density of abrasive particles and a higher volume of pores. This structure allows for more aggressive dressing, making it ideal for quickly removing large amounts of bond material and exposing new diamond particles. This aggressive nature is especially beneficial for initial tool conditioning or dealing with heavily glazed tools.
The higher volume of pores in an open structure also facilitates efficient debris removal during the dressing process, preventing clogging and ensuring that the dressing stick remains effective throughout its use. This quick debris clearance helps maintain consistent dressing performance and reduces the risk of overheating, which can otherwise damage both the tool and the dressing stick. Additionally, the open structure allows better penetration of coolants and lubricants, enhancing the cooling effect and reducing friction, which is particularly advantageous in high-speed or high-pressure dressing operations where heat management is critical to avoid thermal damage to the tool and workpiece.
On the other hand, dressing sticks with a dense structure have a higher concentration of abrasive particles and fewer pores. This configuration allows for fine, precise dressing, making dense structure dressing sticks ideal for applications requiring high accuracy and a smooth surface finish. The dense arrangement of particles ensures close contact with the tool surface, providing consistent and controlled dressing action, which is crucial for maintaining the fine geometry and sharpness of precision tools.
Dense structure dressing sticks are designed to remove minimal amounts of bond material, preserving the tool's integrity while exposing new diamond particles. This controlled material removal is essential for maintaining the tool's fine geometry and sharpness. The dense structure also contributes to a superior surface finish on the tool, making it suitable for applications where the quality of the finished surface is critical. The fine dressing action ensures that the tool remains sharp and capable of producing high-quality finishes on the workpiece.
Open structure dressing sticks are ideal for use with coarse grit diamond tools or in applications requiring aggressive dressing and efficient debris management, such as heavy-duty grinding and cutting operations. In contrast, dense structure dressing sticks are best suited for fine grit diamond tools and applications requiring precision and high surface finish quality, such as finishing operations, precision grinding, and tasks involving delicate materials.
7. Abrasive Bond Hardness
-
Soft Bonds (A-C-G): Best for soft materials where a quicker breakdown of the dressing stick is beneficial.
-
Medium Bonds (I-J-L-N): Provide a balance between wear resistance and cutting efficiency.
-
Hard Bonds (P-R-T-Z): Ideal for hard materials, offering prolonged durability and consistent performance.
Abrasive bond hardness is a critical factor in the performance of dressing sticks, influencing their suitability for various applications and materials. Soft bonds, classified as A, C, or G, are particularly effective when working with soft materials. These bonds break down more quickly, which is beneficial as it continuously exposes fresh abrasive particles, ensuring that the dressing stick maintains its cutting efficiency. This rapid breakdown is advantageous in applications where maintaining a sharp edge is more important than the longevity of the dressing stick, allowing for effective conditioning of tools used on softer materials.
Medium bonds, ranging from I, J, L to N, offer a balanced approach between wear resistance and cutting efficiency. They are versatile and suitable for a broad range of applications, making them a popular choice for general-purpose dressing tasks. Medium bonds provide sufficient durability to withstand moderate wear while still exposing fresh abrasive particles at an adequate rate to maintain the tool's sharpness. This balance makes them ideal for operations that require a combination of cutting speed and surface finish quality, ensuring consistent tool performance across various tasks.
Hard bonds, designated as P, R, T, or Z, are designed for use with hard materials. These bonds are characterized by their prolonged durability and ability to maintain consistent performance over extended periods. Hard bonds break down more slowly, which is advantageous in high-load applications where the dressing stick needs to withstand significant pressure and wear. This slow breakdown rate ensures that the dressing stick remains effective for a longer duration, providing continuous exposure of abrasive particles and maintaining the tool's cutting efficiency. Hard bonds are particularly suitable for applications involving hard materials, such as hardened steel or ceramics, where tool durability and consistent performance are crucial.
In practical terms, the choice of abrasive bond hardness should align with the hardness of the material being worked on. For softer materials, soft bonds are preferable as they ensure quick exposure of new abrasive particles, maintaining effective cutting action. For general applications, medium bonds provide a good compromise between durability and efficiency, making them versatile and reliable for a variety of tasks. For hard materials, hard bonds are essential as they offer the necessary durability and performance consistency to handle demanding conditions and extended use.
We offer large variety of dressing stick specifications to fit most applications and can provide custom dressing sticks to fit your specialized requirements
Using Diamond Dressers to Dress Diamond & CBN Wheels
Diamond dressers are essential tools used to maintain and restore the sharpness, shape, and functionality of grinding wheels and diamond tools. These dressers come in various forms, including single-point, multi-point, and rotary types, each embedded with diamond particles due to their exceptional hardness and abrasion resistance.
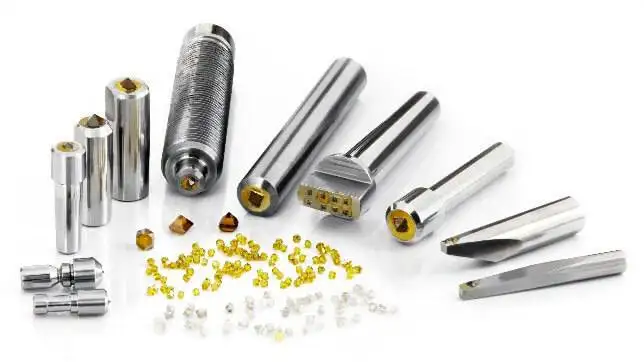
Single Point Diamond Dressers
Single-point diamond dressers feature a single diamond mounted on the tool tip, making them ideal for precision dressing and truing applications. Multi-point diamond dressers contain multiple diamond particles distributed over the tool’s surface, providing a more uniform dressing action, which is suitable for larger grinding wheels.
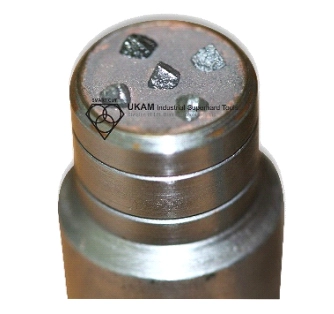
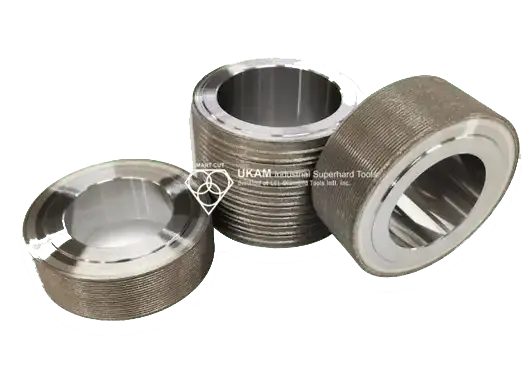
Rotary Diamond Dressers
Rotary diamond dressers consist of a rotating wheel embedded with diamond particles and are used for high-precision dressing and truing of complex wheel profiles.
Diamond dressers are particularly useful when grinding wheels become glazed, meaning the surface is smooth and shiny, which reduces cutting efficiency. They are also employed to restore the wheel’s shape, ensuring precise grinding operations, and to enhance grinding efficiency by removing embedded debris or worn abrasive grains. They are essential when high precision and consistency are required in the grinding process and when maintaining complex wheel profiles in high-precision applications.
To use diamond dressers, one must first ensure that the grinding wheel is securely mounted. The appropriate diamond dresser type is then selected based on the wheel size and the required precision. For single-point dressers, the tool is positioned at an angle to the wheel and applied with light pressure, traversing across the wheel’s surface to dress and true it. Multi-point dressers are positioned parallel to the wheel’s surface and moved uniformly across to achieve even dressing. For rotary dressers, the tool is aligned with the grinding wheel, ensuring it rotates at the recommended speed before engaging with the wheel surface to dress and true it. After dressing, it is important to inspect the wheel for any residual debris or glazing and run it at operating speed to check for balance and surface smoothness.
Compared to truing or using dressing sticks, diamond dressers provide several advantages. They offer precise control over the dressing and truing process, making them ideal for applications requiring high accuracy and for maintaining complex wheel profiles. They provide consistent and efficient removal of glaze and debris, ensuring the grinding wheel maintains optimal cutting performance. Diamond dressers are also highly durable and can handle repeated use, making them cost-effective over time. Their versatility makes them suitable for a wide range of grinding wheels and applications, from simple dressing to complex truing tasks.
While truing focuses on restoring the wheel’s shape and geometric accuracy, diamond dressers can perform both truing and removing glaze and debris, offering a dual function. When truing alone is not sufficient, diamond dressers are preferable as they enhance both the wheel’s shape and cutting surface. Compared to dressing sticks, which are typically used for routine sharpening and exposing new abrasive grains, diamond dressers offer a higher level of precision and control. This makes them better suited for high-precision applications and maintaining complex wheel geometries.
Comparing Dressing using Dressing Sticks, Truing, & Using Diamond Dressers
Aspect |
Dressing with Dressing Sticks |
Truing Diamond Tools |
Using Diamond Dressers |
---|---|---|---|
Purpose |
Sharpening and exposing new diamond particles by removing bond material. |
Correcting the tool’s shape and geometry to ensure precision. |
Removing glaze, exposing fresh abrasive, and maintaining tool sharpness. |
Method |
Abrasive stick is applied to the tool’s surface to remove worn matrix material. |
A truing device (often a single-point diamond) reshapes the tool. |
A diamond dresser (single/multi-point) is used to clean and sharpen the tool. |
Primary Function |
Enhances cutting performance and minimizes load on the tool. |
Ensures the tool maintains its original shape and precise dimensions. |
Maintains cutting efficiency and removes embedded debris. |
Material Removal |
Removes a small amount of bond material to expose diamonds. |
Removes material to correct tool geometry and roundness. |
Removes glazing and exposes new abrasive grains by cutting away debris. |
Application Frequency |
Frequently, based on tool wear and application demands. |
Periodically, when tool shape deviation is detected. |
Regularly, to maintain sharpness and prevent glazing. |
Tool Types |
Suitable for diamond blades, wheels, and grinding tools. |
Applicable to precision grinding wheels and other high-precision tools. |
Applicable to grinding wheels and tools requiring frequent maintenance. |
Precision Impact |
Maintains sharpness and cutting efficiency. |
Restores tool to precise geometric specifications. |
Maintains and restores tool sharpness and cutting surface. |
Surface Finish |
Improves surface finish by exposing fresh, sharp diamonds. |
Ensures consistent tool geometry, affecting surface finish quality. |
Improves surface finish by removing debris and glazing. |
Tool Lifespan Impact |
Extends tool life by maintaining cutting efficiency. |
Extends tool life by preserving accurate shape and balance. |
Extends tool life by maintaining sharpness and preventing damage. |
Cost Implications |
Generally low cost, effective for routine maintenance. |
Can be higher cost due to precision equipment required. |
Moderate cost, essential for regular tool maintenance. |
Operational Considerations |
Requires manual application and monitoring. |
May require specialized equipment and skilled operators. |
Requires consistent application to prevent glazing and maintain performance. |
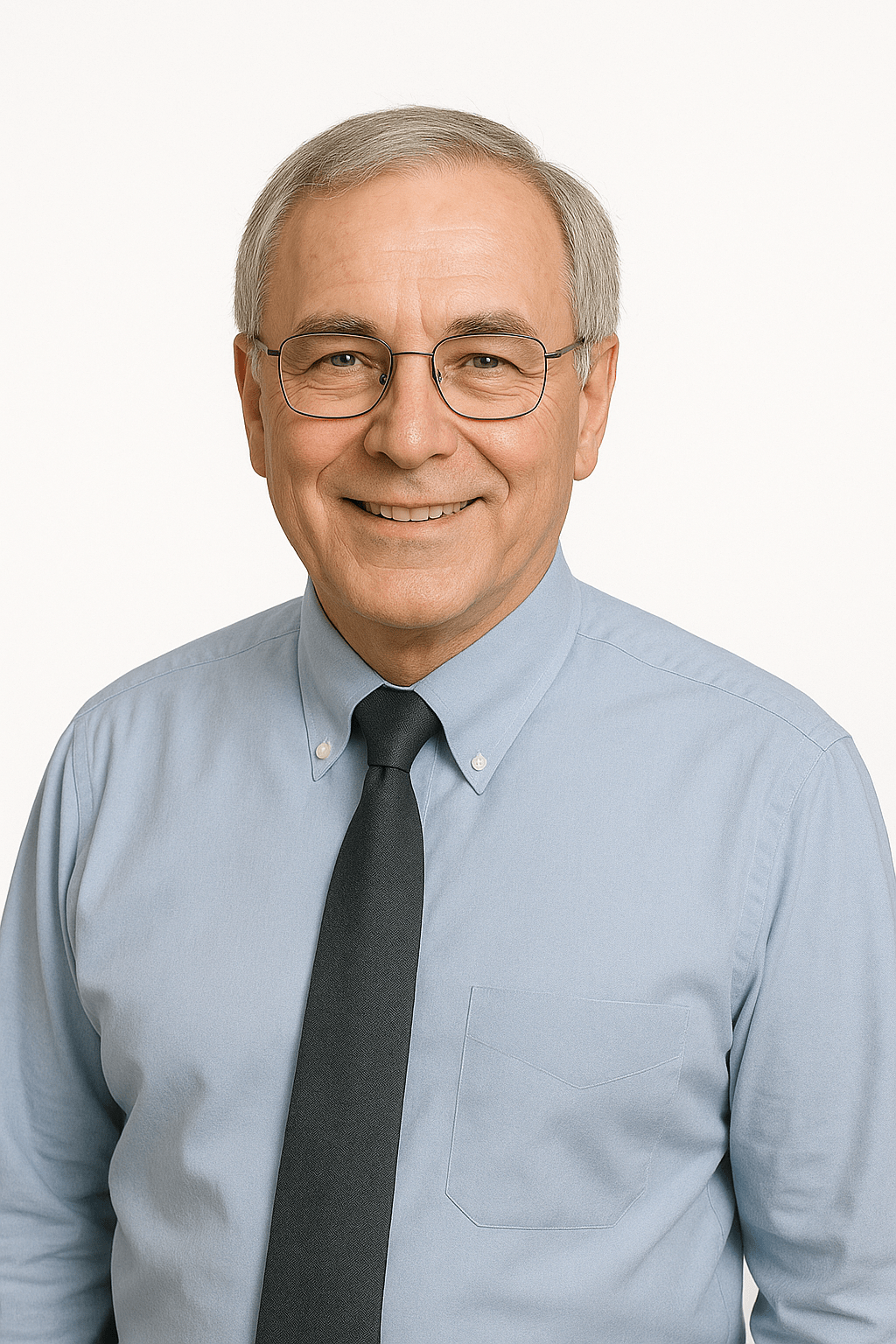
Alexander Schneider is a senior applications engineer and leading authority in the industrial diamond tooling industry, with over 35 years of hands-on experience in the development, application, and optimization of ultra-thin and high-precision diamond blades, diamond core drills, and diamond and CBN grinding wheels. His work spans a wide range of advanced materials including ceramics, glass, composites, semiconductors, and high-performance metals.
Throughout his career, he has collaborated with leading R&D institutions, national laboratories, and high-tech manufacturing companies across Europe, North America, and Asia, providing technical expertise and tailored solutions for demanding cutting and surface preparation applications.
Mr. Schneider has played a pivotal role in advancing precision cutting, sectioning, dicing, and grinding technologies used in research, production, and failure analysis. He is widely respected for his ability to optimize tool design and cutting parameters to meet exacting industry standards—balancing factors such as cut quality, blade life, material integrity, and process consistency.
As an author, Mr. Schneider is known for delivering practical, application-focused insights that translate complex technical challenges into clear, actionable strategies. His articles and technical guides serve as trusted resources for engineers, researchers, and manufacturers seeking to improve precision, reduce process variability, and enhance tool performance in critical applications.
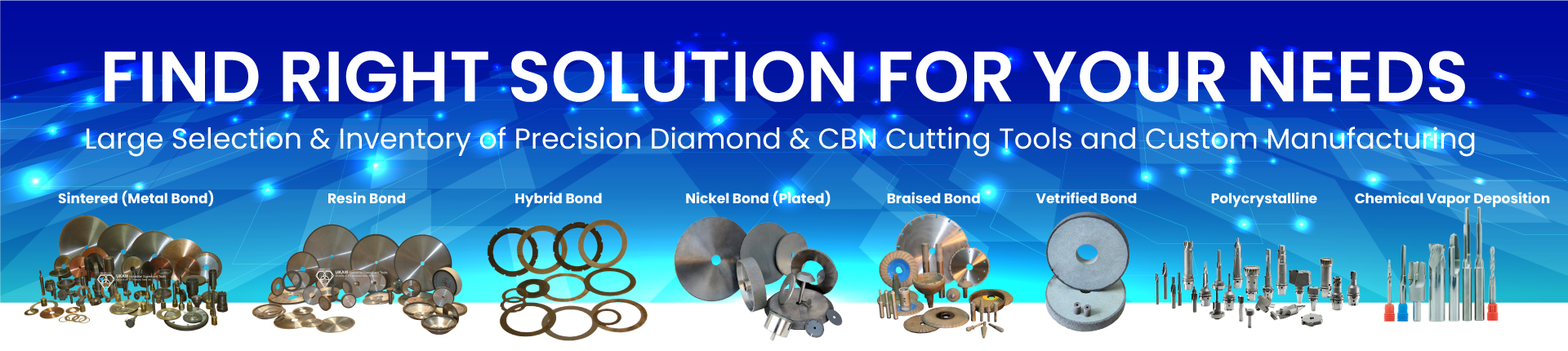
ARE YOU USING RIGHT TOOLS
FOR YOUR APPLICATION?
LET US
HELP YOU
HAVING ISSUES WITH
YOUR CURRENT TOOLS?
Knowledge Center
How to Selecting Right Diamond Tools for your application
How to properly use Diamond Tools
Why use diamond
Diamond vs CBN (cubic boron nitride) Tools
What is Diamond Mesh Size and how to select best one for your application
What is Diamond Concentration and which to use for your application
Diamond Tool Coolants Why, How, When & Where to Use
Choosing The Correct Diamond Bond Type
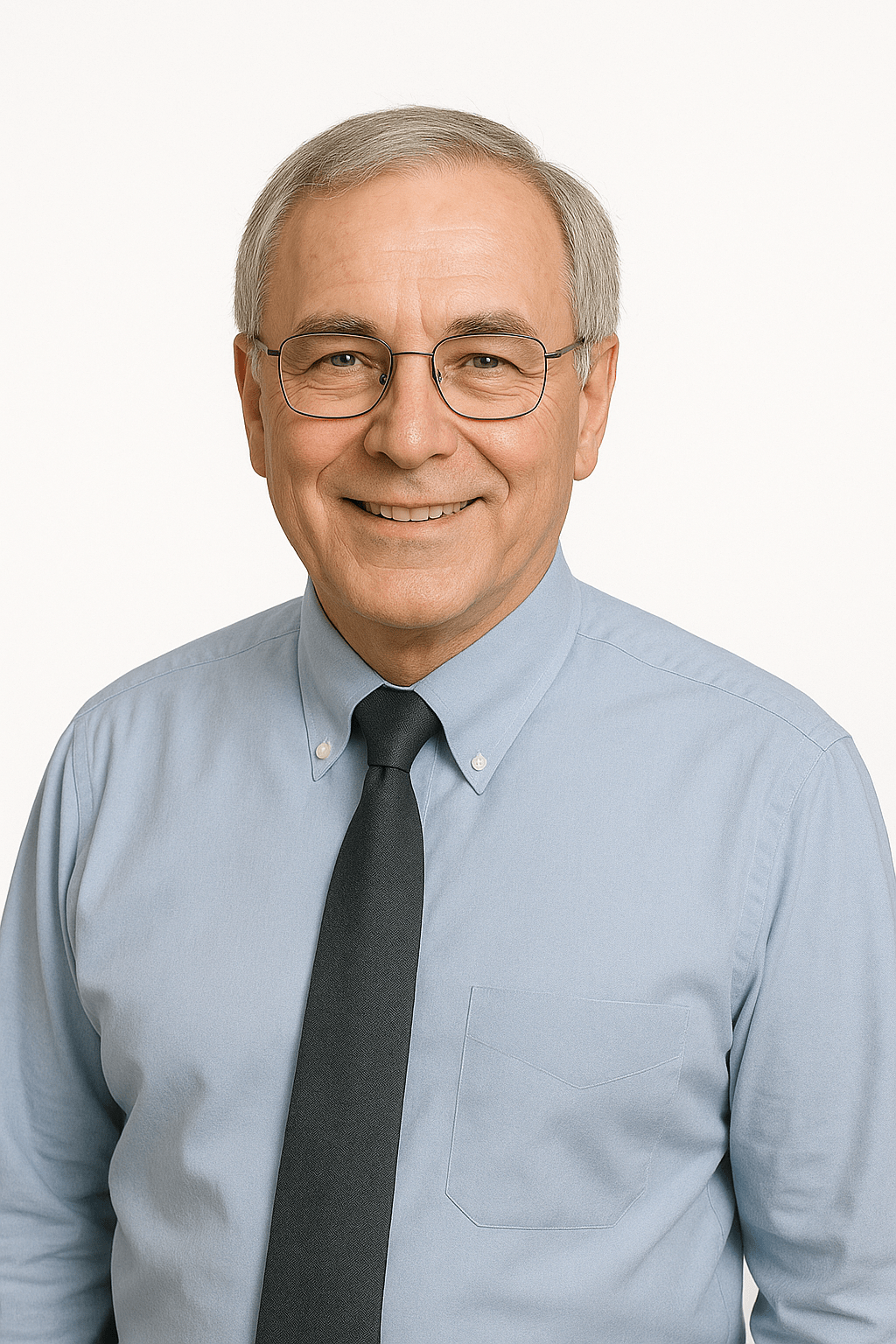
Alexander Schneider is a senior applications engineer and leading authority in the industrial diamond tooling industry, with over 35 years of hands-on experience in the development, application, and optimization of ultra-thin and high-precision diamond blades, diamond core drills, and diamond and CBN grinding wheels. His work spans a wide range of advanced materials including ceramics, glass, composites, semiconductors, and high-performance metals.
Throughout his career, he has collaborated with leading R&D institutions, national laboratories, and high-tech manufacturing companies across Europe, North America, and Asia, providing technical expertise and tailored solutions for demanding cutting and surface preparation applications.
Mr. Schneider has played a pivotal role in advancing precision cutting, sectioning, dicing, and grinding technologies used in research, production, and failure analysis. He is widely respected for his ability to optimize tool design and cutting parameters to meet exacting industry standards—balancing factors such as cut quality, blade life, material integrity, and process consistency.
As an author, Mr. Schneider is known for delivering practical, application-focused insights that translate complex technical challenges into clear, actionable strategies. His articles and technical guides serve as trusted resources for engineers, researchers, and manufacturers seeking to improve precision, reduce process variability, and enhance tool performance in critical applications.