Table of Contents
ToggleDiamond band saw blades are used for cutting large variety of materials from ultra hard ceramics to glass and composite materials. This article covers all critical usage recommendations and best practices for diamond band saw blades, providing operators with the insights needed to maximize blade performance and extend machine longevity. We will explore daily maintenance routines, operational techniques, and safety protocols essential for optimal use of these high-performance blades. By following these guidelines, operators can improve and optimize their diamond band saw blade performance.
Share this Article with Friend or Colleague
Material Suitability
Before beginning any cutting operation, it is crucial to ensure that the diamond blade selected is explicitly designed for the type of material you intend to cut. Materials vary widely in their properties; for instance, glass, ceramics, and metals differ significantly in hardness and abrasiveness. These differences necessitate the use of blades with specific diamond grit sizes and bonding matrices that are tailored to each material's unique characteristics.
For example, cutting glass typically requires a blade with a fine diamond grit and a smooth, continuous rim to reduce chipping and achieve a clean cut. Ceramics, being harder and more brittle, might need a blade with a medium grit and a more robust bond to handle the material's resistance without cracking it. Metals, on the other hand, could require blades with a coarse grit and a strong metallic bond to efficiently cut through the material without rapid wear.
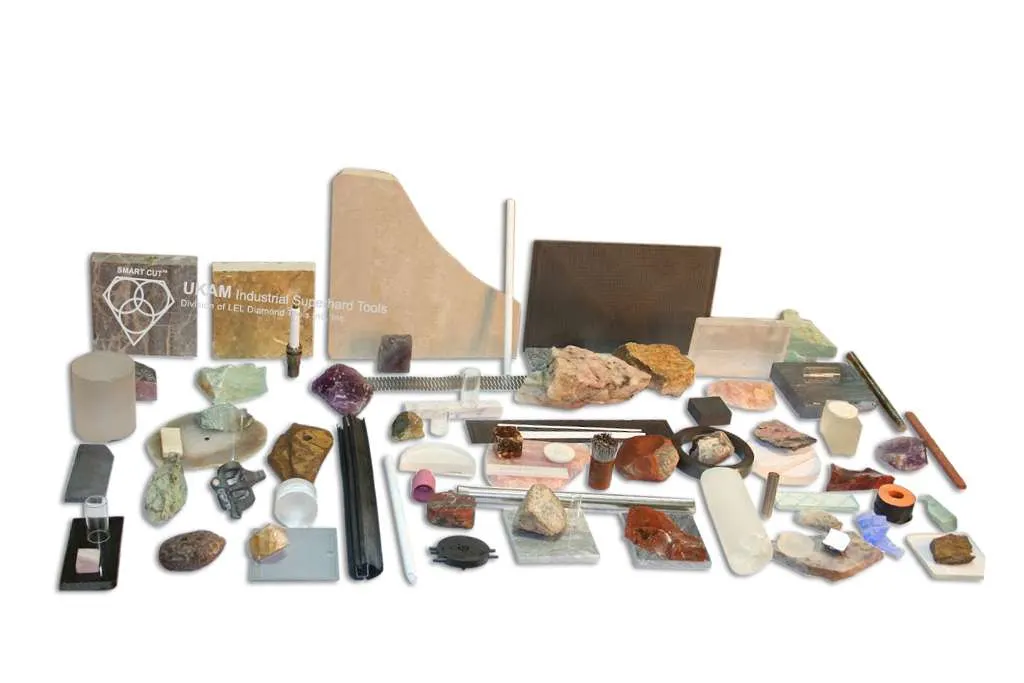
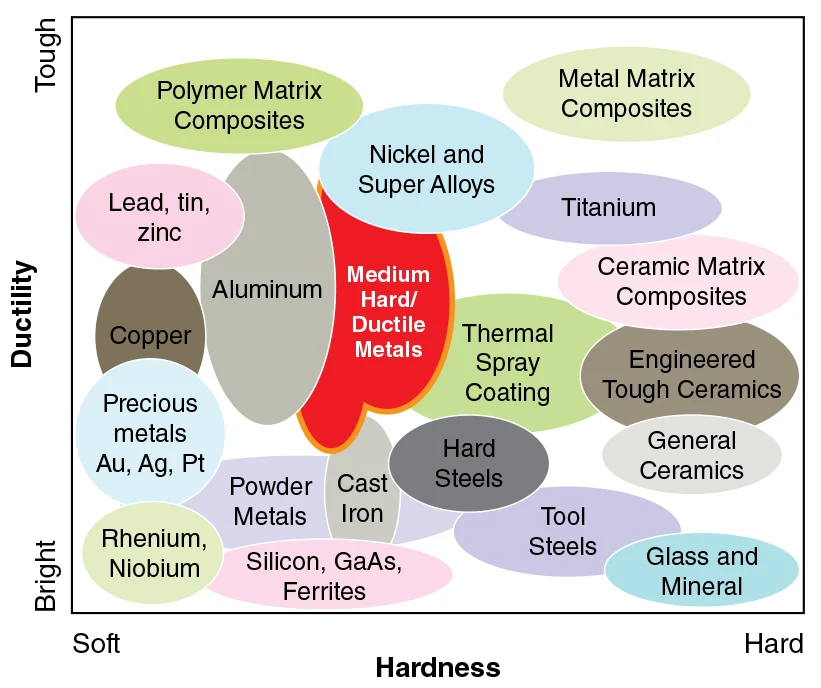
Selecting the wrong type of blade not only leads to suboptimal cutting performance but can also escalate the wear on the blade, thereby shortening its lifespan and increasing your costs. Furthermore, using an inappropriate blade can cause damage to the material, such as excessive chipping, cracking, or even complete breakage, which could compromise the integrity of the finished product.
In addition to the immediate physical and financial risks, there are also safety concerns. Incorrect blade selection can lead to unexpected blade failures, where fragments might detach at high speeds, posing severe risks to the operator and bystanders. Therefore, it is advisable to consult with blade manufacturers or specialists who can recommend the proper blade type based on the specific cutting needs and material characteristics.
Understanding the interaction between the diamond band saw blade and the material it is intended to cut not only optimizes the cutting process but also enhances safety protocols, ensuring that operations are both efficient and safe. Always prioritize acquiring blades from manufacturers who can provide support and recommendations for detailed specifications and usage guidelines tailored to diverse materials and applications.
Installation Accuracy
Proper installation of the diamond blade is crucial for ensuring safe and effective operation. The process begins with cleaning both the blade and the machine surfaces to remove any debris that could affect the blade’s alignment. Once cleaned, the blade should be mounted carefully, ensuring it is correctly seated in the guides and on the wheels of the band saw.
It is essential to check that the blade is perfectly perpendicular to the cutting table and parallel to the direction of feed, as misalignment can lead to inaccurate cuts and increased wear on both the blade and the machine. Tensioning the blade according to the manufacturer’s specifications is equally critical. Both under-tensioning and over-tensioning can be detrimental; the former may cause the blade to wander or slip, while the latter can stress the blade and lead to premature breakage. If available, using a tension gauge can help set the correct tension accurately.
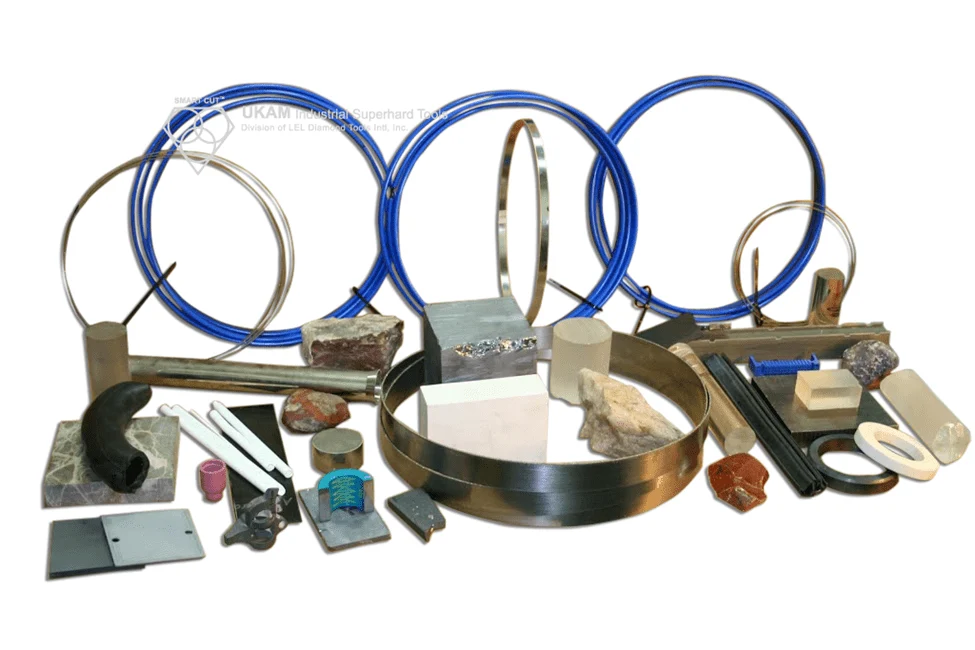
Before each use, a visual inspection of the blade should be performed to ensure there are no signs of wear or damage such as cracks, missing segments, or unusual wear patterns. Conducting a brief test run by making a shallow cut in a scrap piece of material allows for observing the blade in action and making any necessary adjustments before proceeding with more critical work.
Incorporate checks of blade alignment and tension into the regular maintenance routine. This helps in the early detection of issues that could lead to serious problems if left unaddressed. Keeping a log of maintenance activities, noting any changes in blade performance, adjustments made, and replacement of parts can help track the blade’s lifespan and optimize maintenance schedules.
Common issues such as blade drift, uneven wear, or excessive noise and vibration during operation are indicators of potential problems with the installation. In such cases, it's important to reevaluate the alignment, tension, and condition of the blade and machine components.
Optimal Cutting Speed
Adjusting the cutting speed to match the specific characteristics of the material and the specifications of the diamond blade is crucial for achieving the best results. Materials differ in their hardness and abrasiveness, which should guide the speed settings to optimize cutting efficiency and minimize damage.
High speeds may be suitable for softer, less abrasive materials, allowing for quick cuts without significant blade wear. However, when cutting harder, more abrasive materials, high speeds can generate excessive heat. This not only risks damaging the blade through segment loss or warping but can also affect the material's integrity by introducing thermal stresses that may cause cracks or other structural changes.
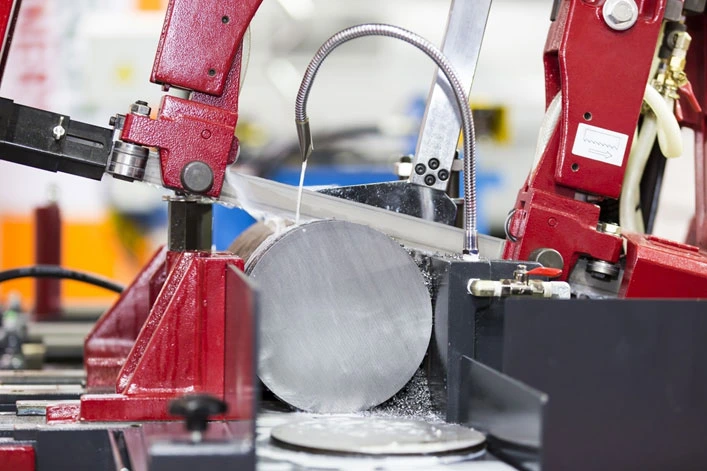
Conversely, a cutting speed that is too slow may seem safer, but it can be just as problematic. Slow speeds can lead to a range of inefficiencies such as increased time for cutting, higher energy consumption, and even accelerated blade wear due to prolonged contact with the material. This can also lead to increased operational costs and reduced productivity.
It is essential to find a balance where the blade can perform efficiently without compromising the quality of the cut or the physical state of the material. This balance can typically be achieved by starting with the manufacturer’s recommended speed settings for your blade and material type, then adjusting based on the outcomes observed during initial cuts.
Moreover, the choice of wet or dry cutting plays a role in determining the appropriate speed. Wet cutting, which involves the use of water or another coolant, generally allows for higher speeds since the coolant helps to manage heat generation and remove debris. In dry cutting scenarios, lower speeds might be necessary to manage heat buildup more effectively.
To ensure precision and safety, regularly consult the blade manufacturer’s guidelines or seek advice from a professional when setting up new materials or blade types. Implementing a methodical approach to testing and adjusting speeds can also be beneficial. By conducting controlled tests on sample materials, you can observe how different speeds affect blade performance and material properties, allowing for more informed adjustments.
The optimal RPM (Revolutions Per Minute) for diamond band saw blades can vary greatly depending on a variety of critical factors, including the material type, blade diameter, material hardness, and the blade’s specific design. Here are some expanded guidelines to help determine the best speed for your cutting needs:
Material Type: The nature of the material being cut is a primary consideration when setting blade speeds. Softer materials, such as certain ceramics or glass, can often be cut at higher speeds due to their lower resistance to cutting. This allows for quicker cuts without significant wear on the blade. In contrast, harder materials like quartz or granite demand slower speeds. High speeds on such hard materials can lead to excessive heat generation and potential damage to both the blade and the material.
Blade Diameter: The diameter of the blade plays a crucial role in determining the appropriate RPM. Larger blades require lower RPMs because the outer edge of the blade moves faster than the inner parts, covering more distance per revolution. Operating at lower RPMs compensates for this increased speed at the edge, helping to manage heat and reduce the risk of damage.
Manufacturer’s Recommendations: It is essential to adhere to the manufacturer's guidelines when deciding on RPM settings. These recommendations are derived from comprehensive testing and are tailored to maximize both the performance and the lifespan of the blade. Ignoring these guidelines can lead to suboptimal cutting results and might also void warranties or lead to safety issues.
Cooling Considerations: Effective cooling is vital, especially at higher speeds. Faster blade speeds generate more friction and heat, which can be detrimental unless properly managed. A robust cooling system, such as a water coolant setup, can enable higher speeds by dissipating heat and flushing away debris from the cut. Without adequate cooling, it is prudent to opt for lower RPMs to prevent overheating, which can warp the blade and damage the material.
Application Specifics: Consider the specifics of the cutting task, such as the thickness of the material and the desired quality of the cut. Thicker materials and cuts requiring high precision might necessitate adjustments to the blade speed. Fine-tuning the RPM based on the actual cutting experience and observing the outcomes can lead to more refined and effective settings.
For achieving very precise cuts, opting for a slower RPM can be beneficial as it allows for greater control over the cutting process. On the other hand, using a higher RPM than recommended can lead to increased blade wear and tear, reducing the lifespan of the blade. Conversely, setting the speed too low can result in inefficient cutting and place unnecessary strain on the saw.
Certain specialized applications might have specific RPM needs, especially when cutting very dense or abrasive materials, where a lower RPM can help minimize blade wear. It's crucial to ensure that the RPMs you select are within the operational range of your saw, as operating a saw at an unsuitable RPM can be dangerous and potentially damage the saw.
Experienced users often have the knowledge to safely and effectively adjust the RPMs based on their understanding of the material and cutting process. However, sometimes finding the optimal RPM requires experimentation—starting at a lower speed and gradually increasing it, all while closely monitoring the cutting performance and the condition of the blade. This approach allows for fine-tuning the process to achieve the best results without compromising the equipment or the quality of the cut.
Using Coolants
Using the right coolant is essential when operating diamond band saw blades, enhancing the cutting process, extending blade life, and ensuring safety. Water, often used for cutting stone, glass, or tile, efficiently absorbs heat, making it a popular choice. For metals, however, water-soluble coolants or cutting oils are preferred as they reduce friction and effectively remove cutting debris.
It’s crucial to mix water-soluble coolant at the right concentration. An overly diluted mixture diminishes its effectiveness, while an overly concentrated mixture can be wasteful and harmful to both the blade and the workpiece. Applying the coolant continuously and directly at the point of contact between the blade and the material maximizes its effectiveness in reducing heat and wear.
Coolant plays a pivotal role in preventing both the blade and the material from overheating, which can cause damage and pose safety hazards. To maintain its effectiveness, the coolant should be regularly cleaned and replaced to avoid contamination that could damage the blade.
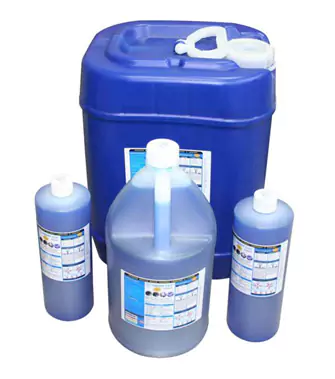
Environmental considerations are also important; some coolants require specific disposal methods to minimize their environmental impact. Additionally, using water-based coolant necessitates adding a rust inhibitor to prevent corrosion on your equipment.
Maintaining the coolant distribution system is critical. Ensure that nozzles and hoses are clear of clogs and correctly positioned to deliver coolant efficiently. For applications not designed for dry cutting, it’s essential to use coolant, as dry cutting can significantly shorten the life of the blade and degrade its performance.
In warmer conditions, the coolant's temperature can increase, reducing its cooling capacity. Implement strategies to maintain a lower coolant temperature to ensure optimal performance. Always handle coolants with care in well-ventilated areas and wear appropriate protective gear to avoid contact with skin and eyes. Some coolants may emit harmful vapors or irritate the skin, necessitating precautions.
Systems that allow for the recycling and filtration of the coolant are not only cost-effective but also support environmental sustainability. Adjusting the pressure and volume of the coolant flow depending on the material being cut and the specifics of the cutting operation is necessary, as different materials and speeds may require adjustments to achieve optimal cutting conditions.
To achieve the best outcomes, it is vital to ensure that the coolant used is fully compatible with the material being cut. Incompatibility can lead to adverse reactions that may affect the cutting process or damage the material. Periodically reviewing the compatibility of coolants with various materials and adjusting accordingly is crucial for maintaining efficiency and safety.
Over time, coolants can degrade in quality or become contaminated with material residues, which can impede their performance. Regularly inspecting and replacing old coolant can prevent this issue, ensuring that the blade operates under optimal conditions. Keeping detailed records of coolant changes, types used, and the conditions under which they were used can help in predicting the performance of coolants and scheduling maintenance more accurately.
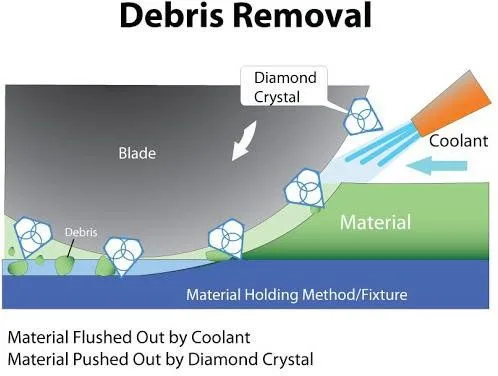
For operations in environmentally sensitive areas, choosing coolants with low environmental impact and ensuring proper disposal according to local regulations are key steps in maintaining responsible practices. In addition, educating all personnel on the proper handling and disposal of coolants is essential to avoid environmental damage and to comply with regulatory requirements.
Ensuring that all equipment, especially coolant pumps, hoses, and nozzles, are regularly checked for wear and function can prevent failures that may interrupt the cutting process or lead to accidents. Moreover, equipping coolant systems with filters can extend the life of the coolant and reduce the frequency of replacements.
it’s important to establish a clear protocol for handling and monitoring the system. This includes training all operators on the specific characteristics of different coolants and the proper techniques for applying and maintaining them during cutting operations. Such training ensures that each operator understands how to optimize coolant use for different materials and recognizes the signs of coolant failure or inefficiency.
At the same time, implementing a system for regular audits and checks on the coolant system can help identify potential issues before they lead to significant problems or equipment damage. These checks should include verifying the correct alignment and positioning of coolant nozzles to ensure that the coolant is applied directly to the cutting zone for maximum effect. Regular inspections can also help in adjusting coolant flow rates and pressures as needed based on ongoing observations and the results of past cutting operations.
Incorporating advanced sensors and automation in the coolant system can provide real-time data on coolant flow, temperature, and quality, enabling more precise control over the cutting environment. This technology can help to optimize coolant usage, reduce waste, and ensure consistent performance across varying operating conditions.
Additionally, considering the integration of environmentally friendly coolant options, such as biodegradable or recyclable coolants, can reduce the environmental footprint of your operations. These sustainable options often provide comparable performance to traditional coolants while aligning with broader environmental compliance and corporate responsibility goals.
Diamond Blade Feed Rates
When operating a diamond band saw, setting the appropriate feed rate is essential to enhance both the precision of the cut and the longevity of the blade. The hardness of the material significantly influences the optimal feed rate; softer materials can tolerate faster rates, whereas harder materials, like granite, require a slower speed to avoid damaging the blade. Each blade's manufacturer specifications provide guidance on the suitable feed rate, ensuring compatibility with various materials and cutting conditions.
The material's thickness also affects how fast or slow the blade should move; thicker materials need a more measured approach to maintain cut consistency and prevent blade deflection or breakage. Additionally, the complexity of the cut influences the feed rate—straight cuts can be made faster than intricate or curved cuts, which demand greater precision to preserve the detail without compromising the blade's integrity.
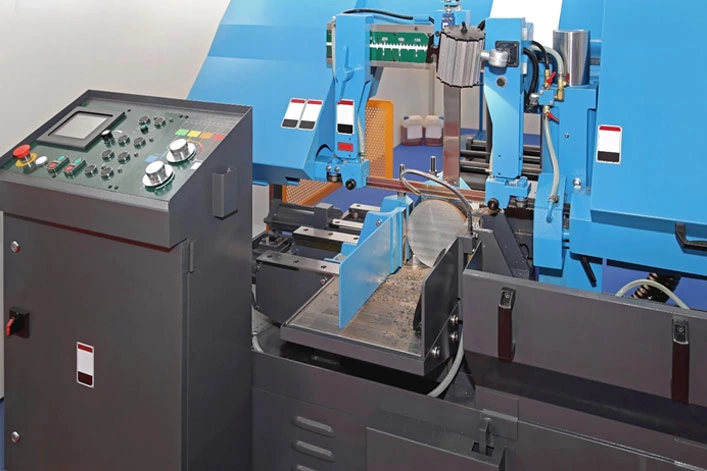
The condition of the blade is another crucial factor; newer blades can typically handle higher speeds, but as they wear, it may be necessary to adjust the feed rate to maintain efficiency. Effective cooling and lubrication can slightly increase the allowable feed rate by reducing the risks of overheating and burning the material.
Ensuring the feed rate matches the capabilities of the cutting equipment is vital. Overloading the machine can result in suboptimal outcomes and potential damage. Real-time feedback, such as the sound of the blade or the appearance of the cut surface, can indicate whether adjustments are needed—chattering or a rough cut surface often suggests the feed rate is too high.
Experienced operators play a key role in setting the feed rate, utilizing their knowledge of the equipment and materials to make precise adjustments. A cautious approach is particularly important for materials that are prone to chipping or fracturing, where a slower feed rate can help avoid damage.
Finding the ideal feed rate usually involves some experimentation—starting conservatively and gradually increasing the speed while monitoring the blade’s performance and the quality of the cut. Safety should always be the priority, ensuring that the chosen feed rate does not compromise control or create hazardous conditions.
Maintaining a consistent feed rate throughout the cutting process is crucial for achieving smooth, even cuts. This consistency prevents issues such as blade wandering or irregularities in the cut. Different materials and cutting requirements might also call for adjustments in blade width and cutting techniques, like employing a "step cutting" method for thicker materials to alleviate stress on the blade.
Regular blade maintenance, including proper tensioning, cleaning, and alignment, along with the use of suitable coolants and cutting speeds, supports optimal blade performance and longevity. Training and experience are invaluable, enabling operators to effectively navigate and adapt to various cutting scenarios, ultimately enhancing both the efficiency and safety of the cutting process.
Usage Recommendations
When operating a diamond band saw, paying attention to unusual noises or vibrations is crucial as they can indicate potential issues with the blade or equipment. If appropriate, using blade stabilizers can help reduce vibrations and improve cutting precision. It's important to ensure the material is properly supported both before and after the cut to avoid unnecessary blade stress or deflection. Applying force to the blade should be gentle and consistent; abrupt force can damage the blade and affect cutting quality.
Keeping the blade path clear by regularly cleaning guides and wheels helps maintain optimal performance. Periodic assessments by professionals can ensure that both your equipment and blades are in top condition. Ensuring all operators are well-versed in emergency procedures is vital for safety in case of blade breakage or equipment failure.
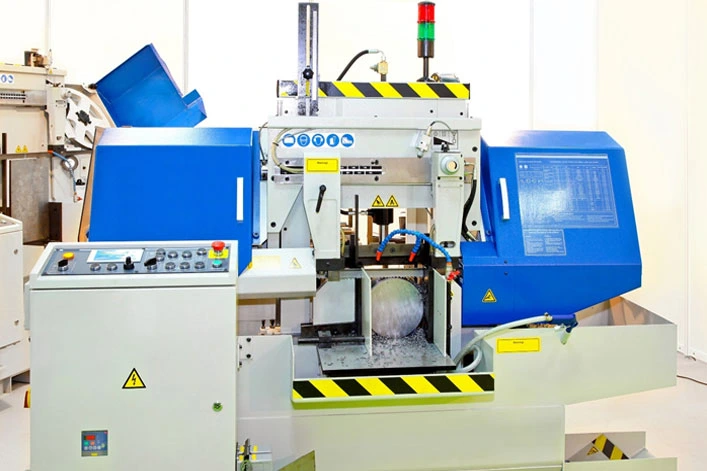
The saw machine should be suitable for the type of diamond band saw blade being used, taking into account factors like power, speed, and size. Monitoring the blade alignment during use is essential, especially when cutting tougher materials, to prevent shifting. If possible, rotate the blade usage to promote even wear, extending the blade's life.
Avoid twisting the blade off the material at the end of a cut to prevent damage. Blades that are beyond their useful life should be decommissioned responsibly, adhering to safety and environmental guidelines. The blade’s running direction should match the saw’s indicated direction; reversing the blade can lead to underperformance and damage.
Before cutting, inspect the material for any defects or foreign objects that might damage the blade. Regular lubrication of the saw’s moving parts is necessary to ensure smooth operation and reduce wear. Choosing a blade with a diamond grit size suitable for the material being cut will optimize performance. Provide new operators with comprehensive safety and operational training, including practical demonstrations and supervised practice sessions.
Do not exceed the blade’s maximum depth of cut as overextending the blade can lead to damage and unsafe conditions. Be aware of environmental factors like humidity and temperature, which can affect both the material and the blade. Maintain a regular preventive maintenance schedule for both the saw and the blades to ensure longevity and performance. Lastly, ensure that the emergency stop feature is easily accessible during operation and recognize that even the highest quality blades have limitations and are not indestructible.
Encourage operators to optimize the use of cutting fluids and power settings not only to achieve better cutting results but also to reduce energy consumption and operational costs. This includes strategic planning of cutting sequences to minimize material wastage. Discuss the importance of using environmentally friendly coolants and the recycling of used blades and materials whenever possible, highlighting how sustainable practices can be integrated into the cutting process to align with broader environmental goals and regulations.
Introduce more sophisticated methods for monitoring blade and machine performance, such as the use of sensors and digital tools that can predict blade wear and automate maintenance reminders. This technology-driven approach can significantly enhance precision and predictability in operations.
Beyond using stabilizers, recommend installing anti-vibration mounts and sound-dampening materials around the sawing area to improve operator comfort and comply with workplace safety regulations regarding noise levels. Emphasize the importance of ergonomic tools and workstations to prevent operator fatigue and injury, discussing how proper ergonomics can improve operator performance and safety, especially during long or complex cutting operations.
Encourage a culture of safety and efficiency where operators are trained to communicate effectively, especially in team settings where multiple personnel interact with the sawing equipment. Promoting a team-oriented approach can enhance both safety and productivity.
Techniques for Initiating the Cut to Reduce Material Chipping and Enhance Cut Quality
Initiating the cut properly is pivotal in diamond band saw operations, as it significantly influences the longevity of the blade and the quality of the finish. A careful start is essential to minimize material waste and achieve a superior finish. Starting slowly is advisable; a controlled and stable cut line should be established at a lower feed rate, which can be gradually increased once the blade has settled into a clear cutting path. This methodical approach prevents the blade from becoming overloaded and significantly reduces the risk of chipping.
Alignment of the blade also plays a critical role. It should be positioned perpendicular to the material surface to ensure even penetration and minimal stress on the blade edges. For materials that are thicker or more brittle, making a shallow pilot cut can provide a more effective guide for the remainder of the cutting process.
The application of coolants should not be overlooked. Generous and appropriate use of coolants not only reduces heat buildup, which can cause premature wear and material damage, but also assists in flushing away cutting debris. This keeps the cutting path clear and minimizes the risk of blade jamming.
Finally, selecting the correct blade according to the material's needs is crucial. The blade should have a diamond grit size and concentration that is suitable for the material being cut. Typically, finer grits are preferable for materials prone to chipping, ensuring the cut quality is optimized while the blade's integrity is maintained.
How to Handle Complex Cuts (e.g., Curves and Intricate Shapes)
Cutting complex shapes demands meticulous planning and precise adjustments to the saw settings. When cutting curves, it is beneficial to reduce the blade speed to enhance control and accuracy. This careful adjustment helps prevent the blade from binding and minimizes deviations from the intended path.
For intricate cuts, especially tight curves and corners, thinner blades are more advantageous. Their increased flexibility allows for easier navigation through complex patterns without risking breakage or accuracy loss. It is also crucial to ensure that the blade tension is correctly adjusted according to the blade's thickness and the radius of the cuts being made.
Using a template or a jig can greatly aid in maintaining consistency throughout the cutting process, particularly for repetitive cuts or complex geometric patterns. This technique helps in preserving the design integrity and ensures uniformity across multiple pieces.
For exceptionally intricate designs, employing incremental cutting strategies is advisable. By making gradual, incremental cuts, the material is shaped slowly, minimizing stress on the blade and preventing material fracture. This technique requires patience but results in a more precise and finely crafted final product.
Monitoring the Cutting Process for Consistent Performance and Blade Health
Consistent monitoring of the cutting process is crucial for maintaining optimal blade performance and extending the lifespan of diamond band saw blades. This vigilance ensures that any potential issues are identified early, thereby preventing damage and maintaining high cut quality throughout the process.
A thorough visual inspection of the blade should be conducted regularly. Operators need to check for signs of wear such as uneven tooth wear, missing diamonds, or deviations in the blade path. Identifying these signs early can help in taking corrective actions that prevent further damage and maintain the quality of cuts.
It is also important to listen for changes in the sound produced during the cutting process. Any variation in the noise level or type can indicate potential problems such as blade binding, material obstruction, or inappropriate blade speeds. Being attuned to such auditory cues can provide early warnings that might not be visually apparent.
Monitoring the cutting force required to push the material through the blade is another critical aspect. An increase in the force needed can indicate several issues such as blade dulling, insufficient coolant flow, or incorrect speed settings. Addressing these issues promptly can enhance the cutting efficiency and prevent undue strain on the blade and the machine.
Taking regular breaks during extended cutting sessions is essential to prevent blade overheating and to clear any accumulated debris. These pauses allow the blade to cool down and help maintain its sharpness, thus preventing thermal damage that could compromise the blade's structural integrity and cutting capability.
Finally, a post-cut inspection should be an integral part of the cutting process. After each cut, inspecting the finished edges and the overall condition of the blade can provide insights into the effectiveness of the current cutting parameters and whether any adjustments are needed. Signs of material chipping or irregular wear patterns on the blade can indicate the need for process refinement or blade replacement.
Maintenance and Care
Proper maintenance and care are pivotal in maximizing the lifespan and performance of diamond band saw blades. Adhering to a rigorous maintenance routine not only extends the operational life of the blades but also ensures they deliver optimal cutting results consistently.
One of the fundamental steps in blade maintenance is cleaning the blade after each use. Residual debris and cutting byproducts can adhere to the blade and create build-up, which may lead to increased wear and tear or even blade malfunction. By cleaning the blade thoroughly after use, operators can prevent build-up and keep the blade in prime cutting condition. This involves removing any particles lodged between the diamond segments or the blade body and ensuring that no residual cutting fluid or material fragments are left on the blade.
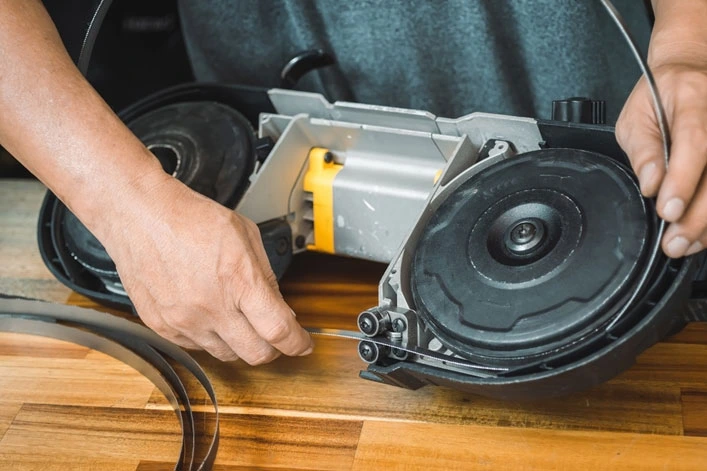
Regular maintenance checks are essential to ensure that the blade operates at peak efficiency. These checks should include adjustments to the blade tension and realignment of the blade within the saw. Proper tension is crucial for effective cutting; too little tension can lead to inaccurate cuts or increased blade wear, while too much tension may cause blade breakage.
Realignment ensures that the blade tracks correctly through the material, providing straight and precise cuts. Regular checks allow for timely corrections that prevent more severe issues and maintain the blade's cutting accuracy.
Knowing when to replace your blade is crucial for maintaining cutting performance and safety. Signs of wear and performance degradation include visible wear on the diamond edges, a decrease in cutting speed or efficiency, increased material wastage due to chipping, and unusual noise or vibrations during operation. These indicators suggest that the blade may no longer be able to perform its task effectively and should be replaced to avoid compromising the quality of cuts and to maintain operational safety.
Diamond Band Saw Machine Maintenance
Proper mounting and usage of diamond band saw blades are critical for ensuring maximum productivity and extending the life of both the blade and the machine. Here are detailed recommendations and daily maintenance steps to follow:
Guide Blocks: Regularly check the guide blocks for wear and regrind them as needed to maintain precision. Properly setting the guides with a clearance of 0.001" to 0.0015" between the band and the blocks is crucial for achieving straight cuts. This clearance helps prevent the blade from rubbing against the guides, which can cause premature wear or blade deviation.
Backup Bearings: These should also be checked periodically for wear. Worn bearings can affect the blade's alignment and the quality of cuts, leading to inaccuracies and increased blade wear.
Upper Guideposts: Position the upper guideposts as close to the workpiece as possible. This minimizes the exposed length of the blade during cutting, which reduces blade deflections and increases cut accuracy.
Upper Wheel Slide Assembly: Since this area significantly affects band tensioning, it must be kept clean to ensure consistent blade performance. Flush this area with coolant at least once per day to remove debris and prevent build-up that could affect the blade's tension.
Lower Wheel Area: Like the upper wheel slide assembly, flush the lower wheel area with coolant daily. This helps maintain the cleanliness of the wheels, ensuring smooth blade operation and reducing potential tracking issues.
Tires: The grooves in the tires must be kept clean to prevent hydroplaning and maintain proper blade tracking. Dirty or worn tires can cause the blade to track improperly, leading to uneven wear or potential blade failure. Check the tires for cleanliness and integrity whenever installing a new band saw blade.
Overall Cleanliness: Daily wiping down of the machine not only keeps it clean but also serves as a reminder to check and maintain all crucial components. Regular cleaning prevents the accumulation of residues that can affect the machine's operation and the blade's performance.
Operator Training: Educating operators on the proper setup and maintenance of the diamond band saw is vital. Comprehensive training should include techniques for mounting, tensioning, and aligning blades, as well as on-going care practices. Keeping accurate records of the performance and maintenance of each diamond band saw blade can help predict blade life and optimize replacement schedules.
Adhering to these detailed maintenance practices ensures that your diamond band saw machine operates at peak efficiency, maximizing the lifespan of the blades and enhancing overall productivity.
Safety Considerations
Safety is paramount in any operation involving diamond band saw blades, as these tools present various hazards if not handled with care. Ensuring safety not only protects the operators but also enhances the efficiency and longevity of the equipment.
Personal Protective Equipment (PPE) is essential to safeguard operators from potential hazards associated with cutting operations. The required PPE includes safety goggles or face shields to protect against flying particles and splinters that can result from cutting processes. Hearing protection is also crucial due to the high noise levels produced by the saws. Additionally, operators should wear cut-resistant gloves to protect their hands from sharp edges and debris, as well as sturdy footwear to guard against heavy material falling on the feet. Depending on the material being cut and the environment, respiratory protection may be necessary to prevent inhalation of harmful dust particles.
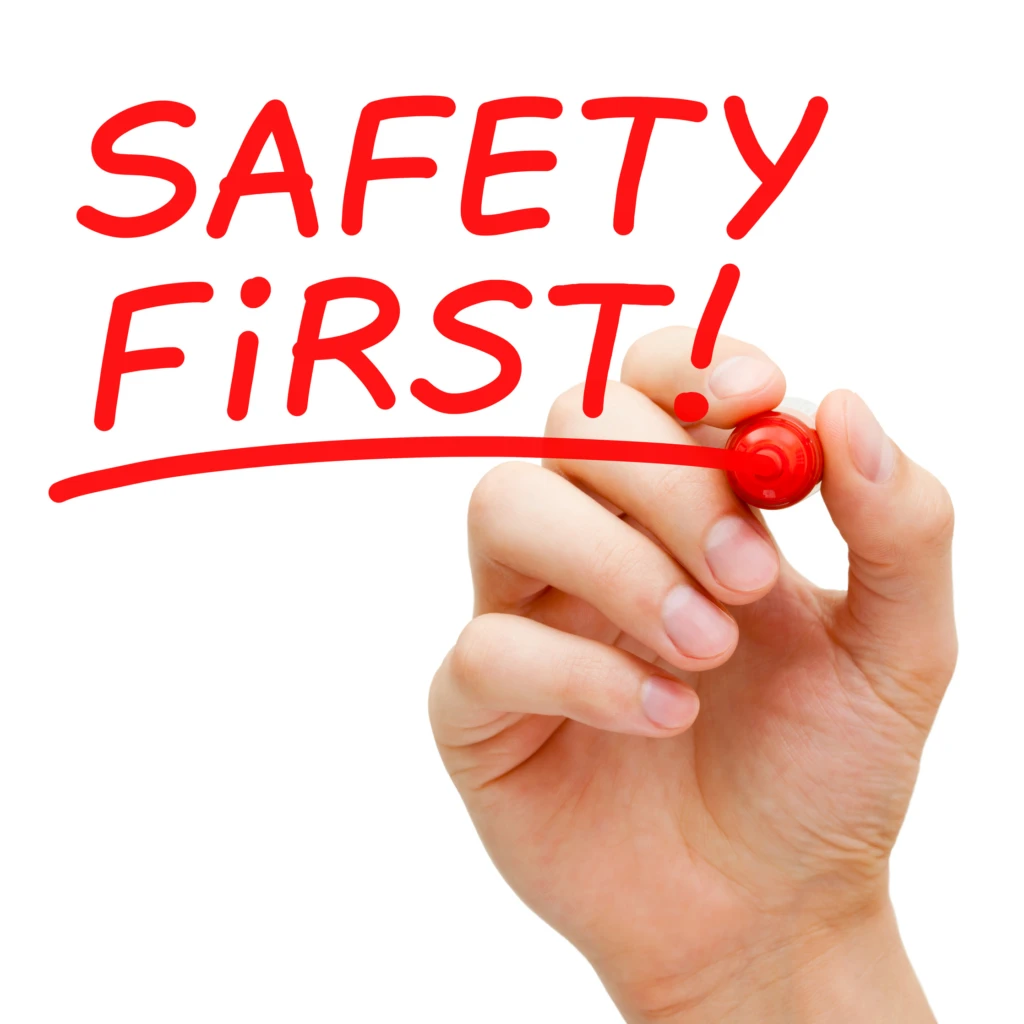
Safety protocols form the backbone of accident and injury prevention while using diamond band saw blades. It is crucial that all operators are trained on the specific model of saw they will be using, including understanding its particular safety features and emergency shut-off procedures. Regular safety drills and reviews can help reinforce safe handling practices.
Before any cutting task, inspect the saw and blade for signs of damage or wear, and ensure that all safety guards are in place and functioning correctly. During operation, keep hands and other body parts away from the moving blade. Work areas should be kept clean and well-lit to avoid slips or trips that could lead to accidents.
It's also important to establish a clear protocol for dealing with emergencies, including immediate steps to shut down equipment safely and administer first aid if needed. Signage reminding operators of safety practices and the location of emergency stops and first aid kits should be visibly displayed around the working area.
Step By Step Installation Guide
Detailed setup procedure for diamond band saw blades formatted into a table for clear and concise reference:
Step |
Procedure |
Details and Recommendations |
---|---|---|
1 |
Install Blade |
Place the new band saw blade over the machine’s wheels and through the guides. |
2 |
Adjust Guides |
Set machine guides to .001" - .0015" over the width of the diamond band saw blade to minimize friction. |
3 |
Attach Tension Gauge |
Attach a tension gauge to the blade in its intended operational position. |
4 |
Tension Adjustment |
Zero out the gauge and adjust the tension to 1.5 units. Keep tension as low as possible while ensuring straight cuts. |
5 |
Initial Blade Tracking |
Run the blade slowly to ensure proper tracking on the tires. |
6 |
Retension |
Release and then re-tension the blade to 1.5 units at the beginning of each shift. |
7 |
Check Blade Position |
Ensure the blade does not touch the backup bearings to avoid premature wear on the backing material. |
8 |
Set Initial Feed Rate |
Start with a cutting rate of four square inches per minute. Keep records to adjust based on blade performance. |
9 |
Adjust Band Speed |
Set the band speed to 1500-2500 surface feet per minute. Record each blade's performance for future optimization. |
10 |
Optimize Table Feed |
Adjust feed to allow diamonds to cut freely without overfeeding, preventing excessive rubbing against backup bearings. |
11 |
Reduce Speed Before Stopping |
Slowly reduce the blade speed before stopping to minimize startup shock. |
12 |
Remove Tension After Use |
Remove tension from the blade when not in use to reduce stress and extend blade life. |
13 |
Dress the Blade |
Periodically dress the blade to clean, sharpen, and renew the diamonds, enhancing cutting efficiency. |
14 |
Weekly Blade Inversion |
Invert the blade weekly to distribute wear evenly and improve lifespan. |
Additional |
Utilization Recommendation |
Use on saws with 26″ wheels or larger for optimal performance and reduced blade fatigue. |
1. Install the Blade
Begin by installing the new diamond band saw blade onto the machine. Carefully place the blade over the machine’s wheels and through the guides. Ensure that the blade is correctly oriented, with the cutting edge facing the right direction. Wear protective gloves while handling the blade, as its sharp edges can cause injury. Take your time to ensure that the blade sits smoothly on the wheels without any twists or kinks, which can lead to improper tracking and performance issues during cutting operations.
2. Adjust the Guides
Once the blade is installed, adjust the machine guides to maintain a clearance of approximately 0.001" to 0.0015" over the width of the diamond band saw blade. Proper guide adjustment minimizes friction and prevents the blade from wandering during the cut. It’s important to clean the guides regularly, as debris buildup can interfere with blade positioning and lead to premature wear. If the blade moves excessively during cutting, it may be necessary to recheck and readjust the guides.
3. Attach a Tension Gauge
After adjusting the guides, attach a tension gauge to the blade in its operational position. This gauge ensures the correct blade tension, which is critical for cutting accuracy and extending the blade's lifespan. Some machines have built-in tension gauges, but if your machine does not, an external gauge can be used. Make sure the gauge is securely positioned according to the machine or gauge manufacturer's specifications. Proper tensioning will prevent the blade from loosening or creating uneven cuts.
4. Adjust Blade Tension
With the tension gauge in place, zero it out and adjust the blade tension to 1.5 units. Tension is a delicate balance: too much tension puts unnecessary stress on the blade and machine components, while too little tension can cause the blade to slip, leading to misaligned cuts and excessive wear. Aim for the lowest possible tension while ensuring straight, accurate cuts. After adjusting the tension, run the machine at low speed to verify that the blade maintains its tension and does not wander. If necessary, make small incremental adjustments.
5. Verify Initial Blade Tracking
Once tension is set, run the blade slowly to check its tracking on the machine’s wheels or tires. Proper tracking is critical to ensuring the blade remains centered on the wheels throughout the cutting process. If the blade shifts or moves laterally, stop the machine and make necessary adjustments to the wheel alignment or tire tension. Any significant movement or noise during this phase may indicate that the blade is not properly seated or the wheels are misaligned.
6. Retension at the Start of Each Shift
At the beginning of each cutting shift, release and then re-tension the blade to the 1.5 unit setting. Blades tend to lose tension over time due to the stresses of cutting, so it's important to recheck and retension at the start of each session. Failing to do so could result in inconsistent cuts, blade slippage, or even blade breakage. Always release tension at the end of the shift to reduce stress on both the blade and the machine, extending the life of both components.
7. Check Blade Position Relative to Backup Bearings
During setup, ensure that the blade is positioned just in front of the backup bearings and is not making direct contact. If the blade rubs against the bearings, it can lead to excessive friction, heat buildup, and premature wear of the blade backing material. Backup bearings are meant to support the blade, but they should not serve as the primary contact point. Regularly check for any contact and make slight adjustments to the bearings or blade position if necessary.
8. Set the Initial Feed Rate
For your first cuts, start with a moderate feed rate, typically around four square inches of material per minute. This conservative approach ensures that the blade cuts through the material cleanly without applying excessive force. Keep a record of the feed rate and monitor the blade’s performance. Adjust the feed rate based on factors like material hardness, blade performance, and desired cut quality. Overfeeding can lead to premature wear, blade binding, or excessive chipping.
9. Adjust Band Speed
The optimal speed for diamond band saw blades typically ranges between 1,500 and 2,500 surface feet per minute (SFM). However, the ideal speed depends on the material being cut and the specific blade used. Start within this range and experiment with different speeds to determine the best balance between cutting efficiency and blade wear. Keep a log of each blade’s performance, as this data will help you optimize future cuts and extend the blade's life.
10. Optimize Table Feed for Smooth Cuts
Adjust the table feed so that the diamonds on the blade cut freely without excessive force. Overfeeding can cause the diamonds to rub against the material, leading to inefficient cuts, blade damage, and potential overheating. On the other hand, underfeeding can lead to slow cutting speeds and reduced productivity. The key is to allow the blade to work at its natural cutting pace without excessive pressure or resistance from the material.
11. Reduce Speed Before Stopping the Machine
When stopping the machine, gradually reduce the blade speed before powering it down completely. This helps prevent sudden startup shock when restarting the machine. Rapid changes in speed can cause stress on both the blade and the machine components, potentially leading to blade breakage or wheel misalignment over time. Always aim for a smooth and controlled shutdown process.
12. Remove Tension After Each Use
When the machine is not in use, always remove tension from the blade. Leaving the blade under tension when idle can cause the blade to stretch and weaken over time. This simple step extends the life of both the blade and the machine by reducing unnecessary stress. Make it a habit to remove tension at the end of each cutting session or shift.
13. Periodically Dress the Blade
Over time, the diamonds on the blade can become dull or clogged with material debris. Periodically dressing the blade will clean and sharpen the diamonds, renewing their cutting effectiveness. Blade dressing is especially important for maintaining consistent cutting quality and prolonging the blade’s usable life. Follow manufacturer guidelines for dressing intervals based on usage and material types.
14. Invert the Blade Weekly
To ensure even wear and maximize the lifespan of the diamond band saw blade, invert the blade on the machine once per week. Regular inversion distributes wear more evenly along the blade’s length, reducing localized stress points and extending the blade’s overall life. This simple maintenance step helps you get more cutting time out of each blade and ensures more consistent cutting performance.
Problem |
Possible Causes |
Solutions |
---|---|---|
Blade Breakage |
|
|
Blade Dulling Quickly |
|
|
Inaccurate Cuts |
|
|
Excessive Vibration |
|
|
Difficulty in Starting the Cut |
|
|
Excessive Noise |
|
|
Uneven Wear on Blade |
|
|
Uneven Cut Surface |
|
|
Excessive Blade Wear |
|
|
Saw Not Cutting Straight |
|
|
Frequent Blade Slippage |
|
|
Coolant Issues |
|
|
Increased Power Consumption |
|
|
Difficulty in Blade Installation |
|
|
Blade Deviates from Cut Line |
|
|
Rapid Tooth Strip Off |
|
|
Blade Binding |
|
|
Irregular Tooth Wear |
|
|
Slow Cutting Speed |
|
|
Noise or Chatter During Cutting |
|
|
Difficulty in Controlling Cut Direction |
|
|
Excessive Coolant Spatter |
|
|
Motor Overheating |
|
|
Problem |
Possible Causes |
Solutions |
Reduced Cutting Precision |
|
|
Frequent Overheating of Blade or Saw |
|
|
Increased Material Waste |
|
|
Blade Becomes Stuck in Material |
|
|
Difficulty in Blade Tracking |
|
|
Inconsistent Blade Life |
|
|
Excessive Noise During Start-up |
|
|
Difficulty in Adjusting Blade Tension |
|
|
Problem |
Possible Causes |
Solutions |
Frequent Resetting of Circuit Breaker |
|
|
Blade Falling Off the Wheels |
|
|
Inefficient Cutting of Curves |
|
|
Vibration in the Saw |
|
|
Difficulty in Maintaining Cut Line |
|
|
Excessive Dust and Debris Accumulation |
|
|
Difficulty in Blade Alignment |
|
|
Blade Chipping or Cracking |
|
|
Blade Loses Tension During Cutting |
|
|
Material Burn Marks |
|
|
Blade Produces Rough Cut |
|
|
Saw Struggles to Start Cutting |
|
|
Inconsistent Blade Movement |
|
|
Difficulty in Changing Blades |
|
|
Excessive Wear on Blade Back |
|
|
Intermittent Cutting Issues |
|
|
Saw Stops Mid-Cut |
|
|
Blade Wandering During Cut |
|
|
Excessive Kerf Width |
|
|
Coolant Leakage or Spillage |
|
|
Blade Corrosion or Rusting |
|
|
Motor Vibration or Noise |
|
|
Difficulty in Maintaining Constant Speed |
|
|
Blade Teeth Breaking Off |
|
|
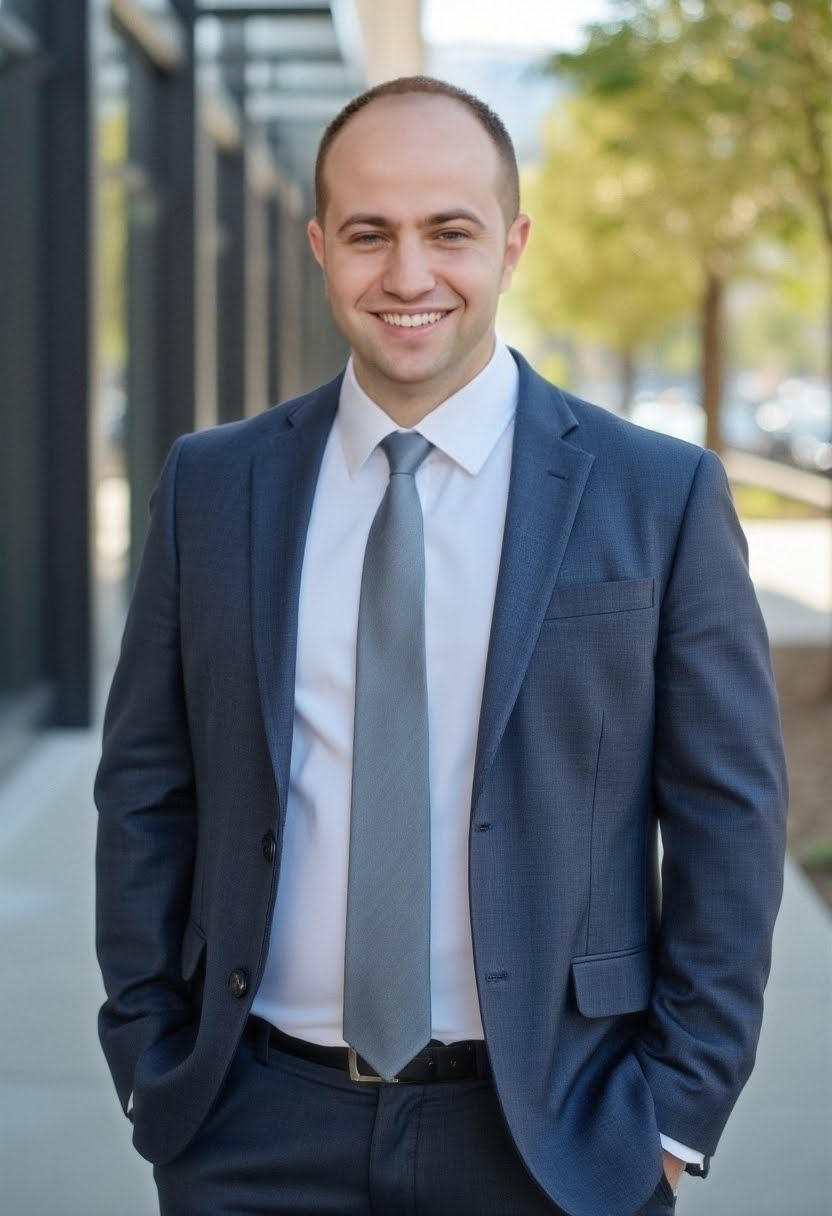
Brian is an experienced professional in the field of precision cutting tools, with over 27 years of experience in technical support. Over the years, he has helped engineers, manufacturers, researchers, and contractors find the right solutions for working with advanced and hard-to-cut materials. He’s passionate about bridging technical knowledge with real-world applications to improve efficiency and accuracy.
As an author, Brian Farberov writes extensively on diamond tool design, application engineering, return on investment strategies, and process optimization, combining technical depth with a strong understanding of customer needs and market dynamics.
ARE YOU USING DIAMOND BAND SAW BLADES
FOR YOUR APPLICATION?
LET US
HELP YOU
HAVING ISSUES WITH
YOUR CURRENT DIAMOND BAND SAW BLADES?
Knowledge Center
Selecting the Right Diamond Band Saw blade for your Application
Diamond Band Saw Blades Usage Recommendations & Best Practices
The Comprehensive Guide to the Processes of Silicon Wafers Production
Diamond Tool Coolants Why, How, When & Where to Use
Silicon Fabrication Guide
What is Diamond Concentration and which to use for your application
What is Diamond Mesh Size and how to select best one for your application
Why use diamond
How to Selecting Right Diamond Tools for your application
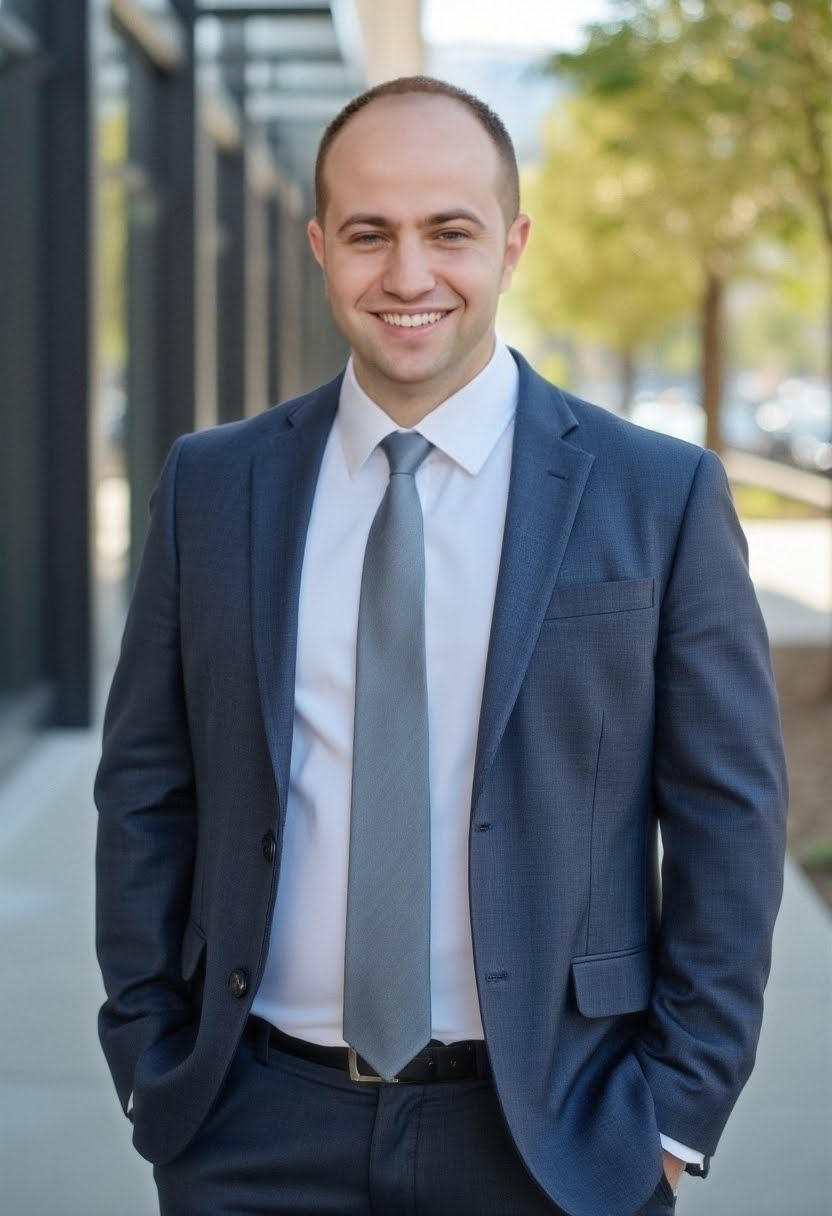
Brian is an experienced professional in the field of precision cutting tools, with over 27 years of experience in technical support. Over the years, he has helped engineers, manufacturers, researchers, and contractors find the right solutions for working with advanced and hard-to-cut materials. He’s passionate about bridging technical knowledge with real-world applications to improve efficiency and accuracy.
As an author, Brian Farberov writes extensively on diamond tool design, application engineering, return on investment strategies, and process optimization, combining technical depth with a strong understanding of customer needs and market dynamics.