Selecting the right silicon carbide paper for metallographic sample preparation is important for achieving accurate and reliable results in material analysis. The grinding and polishing process plays a fundamental role in preparing specimens for microscopic examination, and the choice of abrasive paper directly impacts surface quality, material removal efficiency, and overall workflow effectiveness. Silicon carbide paper is widely used in metallography due to its hardness, sharp cutting ability, and availability in a range of grit sizes suitable for various stages of sample preparation. This guide explores the key factors to consider when selecting silicon carbide paper, including grit progression, backing types, wet vs. dry grinding, and application-specific recommendations to ensure optimal results for different materials and metallographic techniques.
Why use silicon carbide paper for metallography?
Silicon carbide paper is widely used in metallography primarily due to its exceptional hardness, which ranks second only to diamonds. This characteristic makes it particularly effective for grinding and polishing hard metals and alloys, as well as other hard materials such as ceramics and glass. Silicon carbide's ability to remove material efficiently without significant wear ensures that it remains effective over multiple uses, providing both cost efficiency and consistent performance.
Metallography
Feature |
Description |
---|---|
Hardness |
Exceptionally hard, second only to diamond, making it effective for grinding hard metals, alloys, ceramics, and glass. |
Thermal Properties |
High thermal conductivity helps dissipate heat, reducing the risk of thermal damage, warping, or microstructural alterations. |
Wet and Dry Grinding |
Can be used for both wet and dry grinding; wet grinding minimizes dust, overheating, and improves sample preservation. |
Fine Finish Capability |
Produces very smooth surfaces, essential for high-contrast microscopic analysis and accurate microstructure examination. |
Grit Size Availability |
Available in a wide range of grits from very coarse to ultra-fine, allowing for stepwise refinement of the sample surface. |
Material Compatibility |
Compatible with various materials, including hard and soft metals, ceramics, and composites, making it highly versatile. |
Cost-Effectiveness |
More economical than diamond abrasives while still providing durability and effective material removal for routine use. |
Another key advantage of silicon carbide is its excellent thermal properties. It possesses high thermal conductivity that helps dissipate heat effectively, reducing the risk of thermal damage to the sample. Such damage could include warping or alterations in the microstructure that might skew examination results. Silicon carbide paper can be used for both wet and dry grinding. Wet grinding minimizes dust, cools the sample, and reduces overheating risks, which is crucial for maintaining the metallurgical properties of the sample. Dry grinding, however, is useful for quick jobs or in situations where water is not desirable.
Silicon carbide is also known for its ability to produce fine finishes. It is especially valued for the final polishing stages of sample preparation, where it produces a very smooth surface necessary for detailed and high-contrast microscopic analysis. This ensures that the true microstructure of the material is accurately revealed without interference from surface imperfections.
The availability of silicon carbide paper in a broad range of grit sizes—from very coarse to ultra-fine—allows for stepwise refinement of the sample surface. This graded approach is crucial for achieving the best possible finish, as each subsequent grit size erases the scratches from the coarser previous step until the desired smoothness is reached.
Moreover, silicon carbide paper is compatible with a wide array of materials, including softer metals. This versatility makes it an invaluable tool in laboratories that handle diverse types of samples, enhancing its utility in multi-material testing environments. Despite its high performance, silicon carbide paper is relatively economical compared to other abrasive materials like diamond. This cost-effectiveness, combined with its durability and effectiveness, makes it a preferred choice for routine sample preparation tasks in both academic and industrial metallurgical laboratories.
What Type of silicon carbide paper is used for metallography?
The selection of the right type of silicon carbide paper, specifically C grade, for metallography and sample preparation is crucial due to its unique properties and the specific requirements of the processes involved in material analysis. Using the correct grade ensures the effectiveness, accuracy, and efficiency of the sample preparation phase, which is vital for achieving reliable analytical results.
C grade silicon carbide is designed for consistency and uniformity in its abrasive properties, which is essential for preparing samples where reproducible results are critical. Other grades may not provide the same level of uniformity, potentially leading to sample variability that could affect the metallurgical analysis. This grade is particularly effective for harder materials common in metallurgy, such as metals and alloys. It has the hardness necessary to abrade these materials efficiently without causing excessive damage or alteration to the sample surface.
Furthermore, C grade papers typically come with a waterproof backing, which is ideal for wet grinding—a common practice in metallography. Wet grinding helps to prevent overheating of the sample, reduces the generation of airborne particles, and enhances the removal of material from the sample surface. The availability of C grade silicon carbide paper in a wide range of grit sizes allows for precise step-wise progression from coarser to finer grits, critical for achieving a smooth and defect-free surface necessary for microscopic examination.
Compared to other grades, C grade silicon carbide paper is more durable and has a longer lifespan. This reduces the need for frequent replacements and ensures a consistent abrasion rate throughout its use, making it more cost-effective and reliable for laboratory operations. Using the correct grade of abrasive paper also minimizes the risk of contamination during sample preparation. C grade papers are engineered to resist disintegration and minimize the embedding of abrasive particles into the sample, which could lead to inaccurate results and analyses.
Many industrial and international standards for metallurgical testing specify the use of certain types of abrasive materials, including C grade silicon carbide paper, to ensure standardization across tests and labs. Compliance with these standards is essential for labs intending to certify their results for industrial and academic purposes.
Thickness of paper
The thickness of silicon carbide paper used for metallography significantly influences both the performance during sample preparation and the overall outcomes of the metallurgical analysis. Typically, this thickness can vary depending on the backing material and the manufacturer but generally falls within the range of 0.8 mm to 1.2 mm. This measurement includes both the abrasive layer and the backing, which is often waterproof to accommodate wet grinding processes.
Thicker papers tend to be more durable and are capable of withstanding intensive grinding and polishing tasks without tearing, making them suitable for the initial coarse grinding stages where significant material removal is required. Conversely, thinner papers are usually preferred for finer grits. They offer greater flexibility and conform better to the sample surface, which is crucial during the final polishing stages to achieve a high-quality finish without introducing new surface defects.
The choice of backing material also impacts the thickness and performance of the abrasive paper. Paper backings are common and provide a good balance of durability and flexibility but are generally thinner and less durable than other types. Cloth or polyester backings are thicker and more robust, making them appropriate for heavy-duty applications or where the same sheet needs to be used repeatedly.
When selecting silicon carbide paper for metallography, the thickness should be chosen based on the specific requirements of the sample preparation process. For initial material removal, thicker, more durable papers are preferred to withstand the pressures and wear associated with reducing the sample size and removing major surface imperfections. For final polishing stages, thinner, more flexible papers are beneficial for achieving a uniform and smooth surface necessary for detailed microscopic examination.
Silicon Carbide Paper Diameters
Silicon carbide paper is available in various diameters to accommodate different types of equipment and sample sizes. The choice of diameter often depends on the polishing or grinding machine being used, as well as the scale of the work being performed. Here are the most common diameters of silicon carbide paper used in metallography:
-
200 mm (8 inches) - This size is widely used in many standard manual and automatic polishing machines. It's large enough to handle a variety of sample sizes and is a common choice in metallurgical laboratories for its versatility.
-
250 mm (10 inches) - Also common, this slightly larger disk provides a greater surface area, which can be beneficial for processing multiple samples simultaneously or for larger individual samples.
-
300 mm (12 inches) - Used in larger equipment, these discs are suitable for extensive polishing sessions or for larger, more cumbersome samples that require a broader grinding or polishing surface.
-
Other Sizes - While the above are the most commonly used, silicon carbide papers can also be found in smaller diameters, such as 100 mm (4 inches) or 150 mm (6 inches), which are suitable for handheld devices or smaller polishing machines. These smaller sizes are often used for precision work or for samples that are small and delicate.
The availability of these different diameters ensures that there is a suitable option for virtually any metallographic analysis scenario, from small, precise laboratory studies to larger-scale industrial applications. When selecting the diameter, it's important to consider the size of the equipment's platen and the size and number of samples that will typically be processed. Larger diameters offer more efficient usage of time and resources when dealing with bigger or multiple samples, whereas smaller diameters can provide more control and precision for detailed work.
How do silicon carbide discs compare to other abrasive types such as zirconia discs
Silicon carbide and zirconia are both commonly used abrasive materials in metallography for grinding and polishing metal samples, each offering distinct characteristics and benefits. Silicon carbide is known for its extreme hardness, ranking just below diamond. This allows it to effectively grind very hard materials. It also boasts excellent thermal properties, which help dissipate heat, reducing the risk of thermal damage during grinding and polishing. Silicon carbide cuts at high speeds, although it may wear out more quickly than zirconia when used on very tough materials. It is available in a wide range of grit sizes, suitable for everything from rough grinding to fine polishing, and is generally less expensive than zirconia, making it a cost-effective choice.
Zirconia alumina, on the other hand, is slightly less hard than silicon carbide but has high fracture toughness, making it particularly effective on tough materials. Zirconia discs are known for their durability and long life, especially when grinding tough materials. They do not wear down as quickly as silicon carbide, maintaining a consistent removal rate over a longer period. However, zirconia may not cut as quickly as silicon carbide and is typically more expensive. It is often available in coarser grits, making it excellent for initial stages of metallographic preparations but may not offer the same range of fine grits for polishing.
In terms of material compatibility, silicon carbide is versatile across various materials, making it a suitable choice in multi-material labs. Zirconia excels in situations where the material is particularly tough, like certain alloys and composites. For applications requiring very fine finishes, silicon carbide’s availability in ultra-fine grits makes it superior. The choice between silicon carbide paper and zirconia discs often comes down to balancing cost with abrasive life expectancy. Silicon carbide might be more cost-effective upfront but could require more frequent changes than zirconia, which, although more expensive, may offer greater durability and longer life.
Table comparing the key attributes of Silicon Carbide and Zirconia as abrasives used in metallography
Attribute |
Silicon Carbide |
Zirconia |
---|---|---|
Hardness |
Extremely high, second only to diamond |
Very high but less than silicon carbide |
Thermal Stability |
Excellent thermal properties, good heat dissipation |
Good thermal properties |
Cutting Speed |
High cutting speed, but may wear faster on tough materials |
Consistent removal rate, slower than silicon carbide |
Grit Availability |
Wide range from coarse to ultra-fine grits |
Typically available in coarser grits |
Economic Efficiency |
Generally less expensive, cost-effective |
More expensive but offers longer lifespan |
Versatility |
Effective across various materials |
Especially effective on tough materials like alloys and composites |
Durability |
Good but less than zirconia |
High durability and long life |
Cost |
Less expensive |
More expensive |
Finishing Needs |
Available in ultra-fine grits for superior finishes |
May not provide the same level of fine finish |
Material Compatibility |
Universally applicable across various materials |
Best for tough materials |
Silicon Carbide Discs vs Diamond Discs
Silicon carbide and diamond discs are two prominent abrasive options in metallography, each well-suited to specific types of materials and applications. Silicon carbide is extremely hard, ranked just below diamond, making it highly effective for grinding a variety of hard materials. It features excellent thermal properties that help dissipate heat effectively, reducing the risk of thermal damage during grinding and polishing. Although it offers high cutting speed, silicon carbide may wear out more quickly when used on particularly tough materials, yet it remains a cost-effective choice due to its lower price and versatility across a broad range of materials.
Diamond discs, on the other hand, are the hardest materials available and provide the most efficient performance for grinding extremely hard and wear-resistant materials. They excel in heat dissipation, allowing for the fastest material removal rates without causing significant thermal damage. Diamond discs are incredibly durable and long-lasting, making them the most expensive option, yet their longevity and efficiency justify the investment. They are exceptional for achieving both coarse and fine finishes and are particularly ideal for very hard materials such as ceramics and hard metals.
Choosing between silicon carbide and diamond discs primarily depends on the material hardness, required precision, budget constraints, and the desired durability of the abrasive. Each type of disc offers distinct advantages that can significantly influence the efficiency and outcome of the material analysis process.
Feature |
Silicon Carbide Discs |
Diamond Discs |
---|---|---|
Hardness |
Extremely hard, ranked just below diamond |
The hardest material available, superior to silicon carbide |
Thermal Stability |
Excellent heat dissipation, reducing thermal damage |
Exceptional heat dissipation, minimizing thermal damage |
Cutting Speed |
High cutting speed but wears faster on tough materials |
Fastest material removal rate, highly efficient |
Durability |
Moderate durability, wears out faster on very hard materials |
Extremely durable and long-lasting |
Material Compatibility |
Versatile, suitable for a wide range of materials |
Ideal for extremely hard materials like ceramics and hard metals |
Cost |
Lower cost, cost-effective for standard applications |
Most expensive but cost-effective due to longevity |
Surface Finish Capability |
Good for both coarse and fine finishes but limited lifespan |
Excellent for both coarse and ultra-fine finishes |
Best Applications |
General grinding and polishing of various materials, including metals, ceramics, and composites |
Best for grinding and polishing extremely hard materials such as ceramics, glass, and hard metals |
Silicon Carbide Discs Life & Wear Rate
The durability and wear rate of silicon carbide discs are crucial considerations for their selection and use in metallography, impacting operational costs and workflow efficiency. Silicon carbide's hardness makes it a generally durable option for grinding, but its lifespan varies based on factors like grit size, backing material, and manufacturing quality. Coarser grits are more durable as they are less prone to clogging, while discs with rigid or cloth backings withstand higher pressures and more intense use better than those with paper backings.
The wear rate of these discs depends on the material being ground, with harder materials accelerating wear more than softer ones. Grinding pressure also affects wear rate; higher pressures cause more aggressive abrasion, which can wear down both the material and the disc itself. Additionally, using coolants, particularly in wet grinding, can reduce wear by lubricating the grinding interface, thereby lowering friction and the resultant heat.
For effective planning and budgeting, understanding the expected lifespan of the discs in relation to the grinding tasks is essential. Labs can estimate how often they will need to replace the discs by considering the types of materials worked and the grinding conditions. Investing in higher-quality, more durable discs might cost more upfront but can decrease the overall cost per use by lasting longer. Managing a well-organized inventory of various grit sizes and types also helps in controlling costs and ensuring availability, minimizing downtime and maintaining consistent quality in surface finishes.
Silicon Carbide Discs Cost / Performance Ratio
When choosing silicon carbide discs for metallography, it's important to weigh the cost against the performance and longevity offered. Higher-priced discs typically feature superior abrasive grain quality and durable backings which, despite the initial cost, enhance efficiency and extend lifespan, reducing overall expenses. For instance, discs with cloth backings, though more expensive, can handle tougher tasks and last longer, offering greater long-term value.
Premium silicon carbide discs deliver more consistent scratch patterns, crucial for precise finishes in fine polishing tasks. This consistency reduces the time and effort needed to achieve desired surfaces. On the other hand, economical discs, suitable for rough grinding or frequent replacement scenarios, can offer savings despite their shorter lifespan and variability.
The decision between high-end and budget-friendly discs should consider the hardness of the materials, the precision required, and budget constraints. In environments where frequent disc changes or downtime are costly, investing in more durable discs may prove more economical over time.
Understanding & Selecting right Silicon Carbide Paper grit size
Selecting the appropriate grit size of silicon carbide paper is essential for achieving desired results in sample preparation. The choice of grit size should be based on the material hardness, the amount of material to be removed, and the desired final finish. For harder materials or when a significant amount of material needs to be removed, start with coarser grits such as 80-120 grit. This will allow effective material removal without damaging the sample. As the surface becomes smoother, switch to finer grits to refine the surface incrementally up to ultra-fine grits of 1000-4000 for applications requiring a high polish. Always progress through grits gradually, ensuring each step completely removes the scratches from the previous one.
U.S. Industrial Grit |
European FEPA P-Grading |
Micron Grading |
---|---|---|
60 |
60 |
260 |
80 |
80 |
200 |
100 |
100 |
165 |
120 |
120 |
125 |
150 |
180 |
100 |
180 |
220 |
80 |
220 |
280 |
68 |
240 |
320 |
52 |
280 |
360 |
46 |
320 |
400 |
40 |
360 |
500 |
35 |
400 |
600 |
30 |
600 |
800 |
25 |
800 |
1000 |
22 |
1200 |
1200 |
18 |
- |
2400 |
15 |
- |
4000 |
12 |
- |
- |
10 |
- |
- |
9 |
- |
- |
6 |
- |
- |
5 |
The grit size of abrasive materials such as silicon carbide is categorized under different standards around the world, which are crucial for ensuring consistency and effectiveness in grinding and polishing applications.
In the United States, grit sizes are standardized by the American National Standards Institute (ANSI) using the CAMI system. This system ranges from coarse (like 24 or 36 grit) to very fine (up to 600 grit or more), with lower numbers indicating coarser abrasives that remove more material.
Europe follows the Federation of European Producers of Abrasives (FEPA) system, denoted as "P" for coated abrasives and "F" for bonded ones. FEPA sizes are slightly finer than their ANSI equivalents and extend into the thousands for micro-finishing applications.
Japan uses the Japanese Industrial Standards (JIS), which are similar to the FEPA system but can vary slightly, especially in finer grits. Other regions might adopt these standards or develop their own, such as China and other Asian countries, which sometimes use ISO standards similar to FEPA but with variations in coarser grits.
Understanding these different standards is crucial when selecting abrasives for metallography. The choice of grit size can significantly impact the material removal rate, the surface finish, and the effectiveness of the preparation process, facilitating global communication and material procurement.
Table comparing the grit sizes of silicon carbide paper used in metallography under different international standards:
Standard |
Coarse Range |
Medium Range |
Fine Range |
Ultra-Fine Range |
---|---|---|---|---|
ANSI/CAMI (USA) |
24 to 60 grit |
80 to 220 grit |
240 to 600 grit |
Above 600 grit |
FEPA (Europe) |
P24 to P60 |
P80 to P220 |
P240 to P600 |
P1000 and above |
JIS (Japan) |
24 to 60 grit |
80 to 220 grit |
240 to 600 grit |
Above 600 grit |
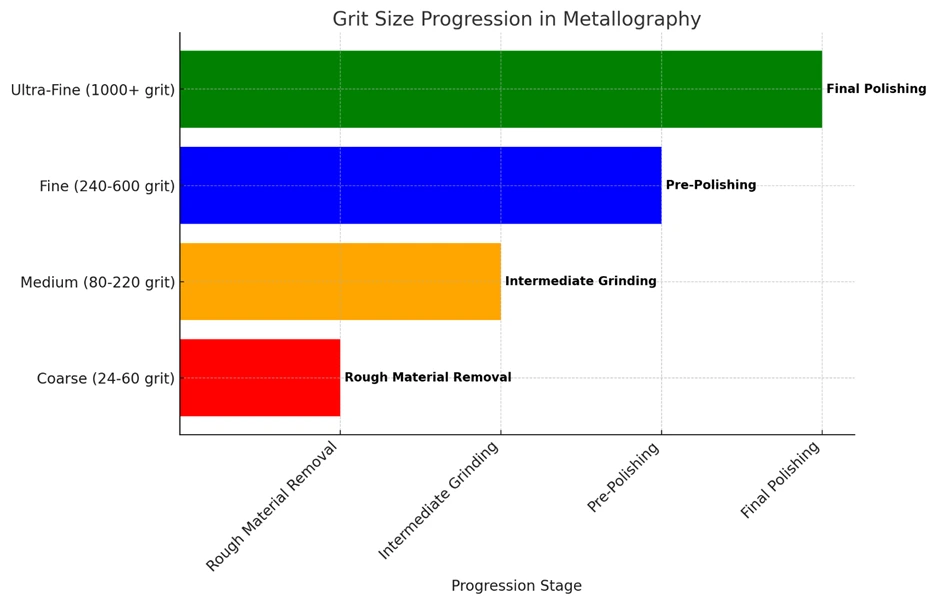
-
Coarse (24-60 grit): Used for rough material removal, ideal for initially reducing material size and removing large imperfections.
-
Medium (80-220 grit): Continues to refine the surface, preparing it for finer polishing by smoothing out scratches from the coarse grit.
-
Fine (240-600 grit): Used for pre-polishing to further refine the surface and prepare it for the final polishing stage.
-
Ultra-Fine (1000+ grit): Applied in the final polishing stage to achieve a mirror-like finish necessary for detailed microscopic analysis.
Backing Type
Silicon carbide discs come with various types of backings, each designed to meet specific needs in metallography. Here's a detailed look at the features and benefits of different backing types:
Plain-Backed (Non-Adhesive) discs require mechanical fastening to the grinder or polisher. This type is more flexible, making it suitable for contours and delicate surfaces. It's less convenient for quick changes because it requires manual fastening, but it's generally less expensive and can be reused with new fastening, making it easier to recycle.
PSA (Pressure Sensitive Adhesive) discs are self-adhesive and stick directly to the grinding or polishing tool. These offer high durability and are very convenient for quick changes, ideal for automated machines. However, they are more expensive due to the adhesive layer and are typically single-use as the adhesive may weaken after removal, making them the least easy to recycle.
Foil or Polyester Plastic Backing discs also typically come with a self-adhesive layer but boast the highest durability among the types. These are the least flexible but very durable, making them perfect for high-stress environments and precision tasks. They are the most expensive due to the high-quality backing material used and also tend to be single-use due to adhesive wear.
Tri-tab PSA discs enhance the features of regular PSA discs by adding easy-tab removal. This design makes them highly convenient for quick changes in fast-paced or automated environments. They provide high durability and are slightly more expensive than regular PSA discs. Like other PSA discs, they are typically single-use and easier to remove but still share the recycling challenges of adhesive-backed products.
Feature/Backing Type |
Plain-Backed (Non-Adhesive) |
PSA (Pressure Sensitive Adhesive) |
Foil or Polyester Plastic Backing |
Tri-tab PSA |
---|---|---|---|---|
Adhesion Method |
Requires mechanical fastening |
Self-adhesive, sticks directly |
Typically self-adhesive |
Self-adhesive with easy-tab removal |
Ease of Use |
Less convenient for quick changes |
Very convenient for quick changes |
Very convenient for quick changes |
Enhanced convenience with easy tabs |
Flexibility |
More flexible, good for contours |
Less flexible than plain-backed |
Least flexible, very durable |
Less flexible than plain-backed |
Durability |
Moderate durability |
High durability |
Highest durability |
High durability |
Common Applications |
Hand sanding, delicate surfaces |
Automated machines, quick swaps |
High-stress environments, precision tasks |
Quick change environments, automated machines |
Surface Suitability |
Suitable for varied surfaces |
Best for flat surfaces |
Best for hard, flat surfaces |
Best for flat surfaces |
Cost |
Generally less expensive |
More expensive due to adhesive |
Most expensive due to material |
Slightly more expensive than regular PSA due to tabs |
Removability/Reusability |
Can be reused with new fastening |
Single use, as adhesive may weaken |
Single use, as adhesive may weaken |
Easier to remove, single use |
Environmental Considerations |
Easier to recycle |
Least easy to recycle |
Less easy to recycle |
Less easy to recycle |
Each backing type offers unique advantages. For example, while plain-backed discs are suitable for varied surfaces and reusable, the Tri-tab PSA discs stand out for their ease of use in environments requiring frequent disc changes. The choice between these backings depends on the specific requirements of the metallographic application, including factors such as the need for flexibility, durability, cost considerations, and environmental impact.
The backing material impacts the flexibility, durability, and usability of silicon carbide paper. Paper backings are best suited for general use and contour polishing where flexibility is needed to conform to various sample shapes. They are typically lighter and less expensive but may wear out quicker under heavy use. Cloth backings are ideal for flat and high-pressure applications, offering greater durability and tear resistance, making them more suitable for prolonged use or for tough materials. For precision applications where minimal thickness variation is crucial, such as in semiconductor or optical materials, polyester backings are the superior choice due to their exceptional durability and uniformity.
In metallography, waterproof paper backing for silicon carbide paper is the most commonly used due to its versatility and effectiveness in both dry and wet grinding applications. Waterproof paper is especially favored because it is specifically treated to resist water, making it ideal for wet grinding, a preferred method in metallography. This technique helps keep the sample cool, minimizes dust, and can improve the surface finish by reducing grinding and polishing artifacts.
This type of backing is made from paper that is treated with a water-resistant chemical or coated to prevent degradation when exposed to moisture. Despite its durability against water, it remains flexible, allowing it to conform well to various material contours during polishing or grinding.
Waterproof paper backings are available in two main adhesion types: plain-backed, which requires mechanical attachment to the tool, and pressure-sensitive adhesive (PSA), which has a self-adhesive layer for quick changes. The adhesive used in PSA versions is also water-resistant, ensuring it maintains its properties during wet operations.
Although not as durable as cloth or polyester backings, waterproof paper provides sufficient durability for most standard metallographic applications, balancing flexibility and strength to enable effective grinding and polishing without tearing. It is also more cost-effective than the more durable alternatives, making it a popular choice for routine sample preparation tasks in both academic and industrial settings. Additionally, waterproof paper is excellent for fine grit applications, crucial for achieving a high-quality finish necessary for detailed microscopic analysis. This combination of performance, cost-effectiveness, and compatibility with wet conditions makes waterproof paper a go-to choice for many professionals in the field.
How to Cross-reference Silicon Carbide Paper & Compare to different Manufacturers/Suppliers
Selecting the right silicon carbide paper can be challenging, especially when comparing different manufacturers' specifications and item numbers. To ensure you get the best match for your metallographic sample preparation process, we have created a detailed cross-reference guide to help you compare our silicon carbide paper with equivalent products from other leading manufacturers.
Each silicon carbide paper is identified based on key specifications, including grit size, backing type, disc or sheet size, adhesion method, and whether it is designed for wet or dry applications. By matching these parameters, you can confidently select the appropriate alternative to competitor brands while ensuring consistent performance and quality.
Our silicon carbide paper is carefully cross-referenced with products from manufacturers such as Buehler, Struers, LECO, Allied High Tech, & many others. We compare grit sizes, backing materials, and application types to ensure that you receive the best alternative without compromising on performance. In many cases, our products offer improved durability, better heat resistance, and enhanced adhesion compared to other brands.
To make the selection process easier, we provide a cross-reference table listing our product codes alongside equivalent competitor item numbers. This allows you to quickly find the corresponding product based on your current specifications. If you are unsure which silicon carbide paper best suits your application, our team is available to assist you with technical recommendations.
Comparison Table for 8" Diameter
SMART CUT® Silicon Carbide Discs-Plain Backing to Buehler, Struers, & Lco
Grit Size |
Our Item Number |
Buehler Item No |
Struers Item No |
LECO Item No |
---|---|---|---|---|
60 grit |
30-08-0060 |
PAPZO-60 |
810-217-300 |
|
80 grit |
PAPZO-80 |
|||
120 grit |
30-08-0120 |
PAPZO-120 |
810-219-300 |
|
240 grit |
30-08-0240 |
810-223-300 |
||
400 grit |
30-08-0400 |
810-227-300 |
||
600 grit |
6053002 |
30-08-0600 |
810-229-300 |
|
800 grit |
6053004 |
30-08-0800 |
4040-0010 |
810-035-100 |
1000 grit |
6053006 |
30-08-1000 |
4040-0011 |
|
1200 grit |
6053008 |
30-08-1200 |
4040-0012 |
810-036-100 |
Comparison Table for 10" Diameter
Silicon Carbide Discs-Plain Backing to Buehler, Struers, & Lco
Grit Size |
Our Item Number |
Buehler Item No |
Struers Item No |
LECO Item No |
---|---|---|---|---|
60 grit |
30-10-0060 |
PAPZI-60 |
812-374-300 |
|
120 grit |
30-10-0120 |
PAPZI-120 |
812-375-300 |
|
240 grit |
30-10-0240 |
812-377-300 |
||
400 grit |
30-10-0400 |
812-379-300 |
||
600 grit |
6055002 |
30-10-0600 |
812-380-300 |
|
800 grit |
6055004 |
30-10-0800 |
4040-0071 |
812-217-200 |
1000 grit |
6055006 |
30-10-1000 |
4040-0072 |
|
1200 grit |
6055008 |
30-10-1200 |
4040-0073 |
812-219-200 |
Comparison Table for 12" Diameter
Silicon Carbide Discs-Plain Backing to Buehler, Struers, & Lco
Grit Size |
Our Item Number |
Buehler Item No |
Struers Item No |
LECO Item No |
---|---|---|---|---|
60 grit |
30-12-0060 |
PAPZU-600 |
810-291-300 |
|
120 grit |
30-12-0120 |
PAPZE-120 |
810-292-300 |
|
240 grit |
30-12-0240 |
810-294-300 |
||
400 grit |
30-12-0400 |
810-296-300 |
||
600 grit |
6057002 |
30-12-0600 |
810-297-300 |
|
800 grit |
6057004 |
30-12-0800 |
4040-0034 |
|
1000 grit |
6057006 |
30-12-1000 |
4040-0035 |
|
1200 grit |
6057008 |
30-12-1200 |
4040-0036 |
Comparison Table for 8" Diameter
Silicon Carbide Discs-PSA Adhesive Backing
Grit Size |
Our Item Number |
Buehler Item No |
Struers Item No |
LECO Item No |
---|---|---|---|---|
60 grit |
6052001 |
30-08-0060 |
PAPZO-60 |
810-259-300 |
80 grit |
PAPZO-80 |
|||
120 grit |
6052003 |
30-08-0120 |
PAPZO-120 |
810-261-300 |
240 grit |
6052006 |
30-08-0240 |
PAPZO-240 |
810-265-300 |
400 grit |
6052010 |
30-08-0400 |
810-269-300 |
|
600 grit |
30-08-0600 |
810-034-500 |
||
800 grit |
30-08-0800 |
810-033-100 |
||
1000 grit |
30-08-1000 |
|||
1200 grit |
30-08-1200 |
810-034-100 |
Comparison Table for 10" Diameter
Silicon Carbide Discs-PSA Adhesive Backing
Grit Size |
Our Item Number |
Buehler Item No |
Struers Item No |
LECO Item No |
---|---|---|---|---|
60 grit |
6054001 |
30-10-0060 |
PAPZI-60 |
812-367-300 |
80 grit |
PAPZI-80 |
|||
120 grit |
6054003 |
30-10-0120 |
PAPZI-120 |
812-368-300 |
240 grit |
6054006 |
30-10-0240 |
812-370-300 |
|
400 grit |
6054010 |
30-10-0400 |
812-372-300 |
|
600 grit |
30-10-0600 |
812-373-300 |
||
800 grit |
30-10-0800 |
|||
1000 grit |
30-10-1000 |
|||
1200 grit |
30-10-1200 |
Comparison Table for 12" Diameter
Silicon Carbide Discs-PSA Adhesive Backing
Grit Size |
Our Item Number |
Buehler Item No |
Struers Item No |
LECO Item No |
---|---|---|---|---|
60 grit |
6056001 |
30-12-0060 |
PAPZU-600 |
810-245-300 |
120 grit |
6056003 |
30-12-0120 |
PAPZE-120 |
810-247-300 |
240 grit |
6056006 |
30-12-0240 |
PAPZE-240 |
810-251-300 |
400 grit |
6056010 |
30-12-0400 |
810-255-300 |
|
600 grit |
6057002 |
30-12-0600 |
810-257-300 |
|
800 grit |
6057004 |
30-12-0800 |
||
1000 grit |
6057006 |
30-12-1000 |
||
1200 grit |
6057008 |
30-12-1200 |
Switching to our silicon carbide paper ensures high-quality results while maintaining cost efficiency. Whether you require waterproof paper for wet grinding, PSA-backed discs for quick changes, or polyester-backed options for high-stress applications, we provide direct alternatives to competitor products with the added benefit of superior performance. If you need further assistance in identifying the right product, contact us, and we will help you find the perfect match for your needs.