The production of silicon wafers, an essential component in semiconductor manufacturing, involves several intricate steps to ensure precision and quality. This article explores the detailed processes depicted in the provided illustration, covering both monocrystalline and multicrystalline silicon wafers.
Monocrystalline Silicon Ingot Formation
The journey begins with the formation of the monocrystalline silicon ingot, typically produced using the Czochralski (CZ) method. This process involves melting high-purity silicon and carefully drawing a single crystal seed to form a large, cylindrical ingot of monocrystalline silicon.
Cutting for Top and Tail - The next step is to cut the top and tail of the ingot. This step ensures that any impurities or defects that may have accumulated at the ends during the crystal growth are removed, providing a uniform starting material for subsequent processes.
Squaring - Once the top and tail are cut, the ingot undergoes a squaring process. Here, the cylindrical ingot is shaped into a square or rectangular cross-section. This transformation facilitates easier handling and further processing, optimizing the ingot for the wafering process.
Silicon Block Formation - After squaring, the silicon is cut into blocks. These silicon blocks are more manageable units that can be precisely processed into wafers.
Cropping - The silicon blocks then go through cropping, where they are cut into smaller, more uniform pieces. This step is crucial for ensuring consistency in the size and shape of the wafers produced.
Outer Diameter (OD) Grinding - To achieve the required thickness and surface finish, the wafers undergo OD grinding. This process ensures that the wafers are uniformly thin and smooth, which is essential for subsequent semiconductor device fabrication.
Chamfering - Chamfering the edges of the wafers is done to prevent chipping and breakage during handling and processing. This step involves beveling the edges to create a more durable and resilient wafer.
Face Grinding Wafering - Wafering involves slicing the cropped silicon blocks into thin wafers using diamond wire saws or other precision cutting tools. This step is critical, as the thickness and flatness of the wafers must be controlled meticulously to meet industry standards.
Final Product: Monocrystalline Silicon Wafer - The final product of this series of processes is the monocrystalline silicon wafer, ready for further processing in semiconductor manufacturing.
Multicrystalline Silicon Ingot Formation
The production of multicrystalline silicon wafers starts with the formation of multicrystalline silicon ingots. These are typically produced using the casting method, where molten silicon is poured into a mold and allowed to solidify, forming a polycrystalline structure.
Squaring - Similar to the monocrystalline process, the multicrystalline ingot is squared to create a manageable and uniform block for further processing.
Block Formation - The squared ingot is then cut into smaller blocks, preparing them for the cropping and wafering processes.
Cropping - Cropping involves cutting the blocks into smaller, more uniform pieces, ensuring consistency in the subsequent wafering process.
Wafering - The cropped blocks are sliced into thin wafers using precision cutting tools. This step is critical to ensure the wafers meet the required thickness and flatness specifications.
Outer Diameter (OD) Grinding - OD grinding is employed to achieve the precise thickness and surface finish necessary for high-quality wafers.
Chamfering - Chamfering the wafer edges prevents damage during handling and processing, ensuring the integrity of the wafers.
Final Product: Multicrystalline Silicon Wafer - The final product is a multicrystalline silicon wafer, ready for use in various semiconductor applications.
Cutting for Top and Tail
The cutting of the top and tail of the silicon ingot is a critical process in the production of high-quality silicon wafers. This step, often overlooked in its complexity, plays a vital role in ensuring the integrity and uniformity of the final product. Let's delve deeper into why this step is necessary, the techniques used, and its impact on subsequent processes.
Impurity Removal - During the crystal growth process, impurities tend to accumulate at the ends of the silicon ingot. These impurities can originate from several sources, including the initial raw materials, the crucible used in the growth process, and the environment in which the ingot is grown. By cutting off the top and tail of the ingot, manufacturers can remove these impurity-laden sections, thereby ensuring that the remaining ingot is of the highest purity.
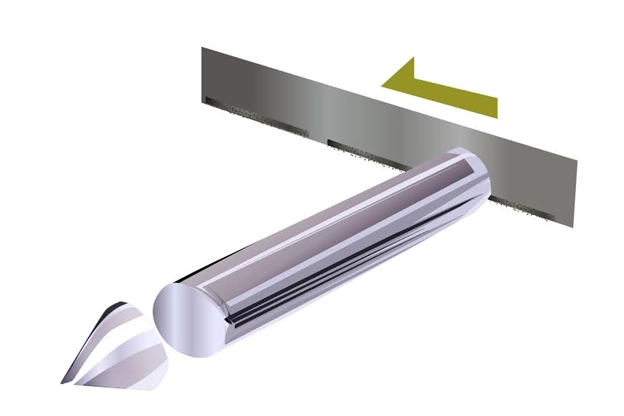
Defect Elimination - Defects such as dislocations, grain boundaries, and other crystallographic imperfections are often more prevalent at the extremities of the ingot. These defects can compromise the mechanical strength and electronic properties of the wafers. By eliminating the top and tail sections, manufacturers can minimize the presence of these defects in the final product, leading to wafers with better performance characteristics.
Uniform Starting Material - The removal of the top and tail also helps in achieving a uniform starting material for subsequent processes. This uniformity is crucial for maintaining consistency in the wafering process, which directly impacts the quality and yield of the final wafers. A uniform ingot ensures that the wafers sliced from it will have consistent properties, which is essential for high-precision applications in the semiconductor industry.
Inside Diameter Diamond Blades - One of the most common tools used for cutting the top and tail of silicon ingots is the diamond blade. Diamond blades are renowned for their hardness and precision, making them ideal for cutting through the tough, crystalline structure of silicon. These blades can be configured to cut at various depths and speeds, ensuring a clean and precise cut that minimizes damage to the ingot.
Diamond Wire Saws - Wire saws are another popular method for cutting silicon ingots. These saws use a thin wire embedded with diamond abrasives to slice through the silicon. The wire saw method is particularly advantageous for its ability to produce very thin cuts with minimal kerf loss (the amount of material removed during the cutting process). This precision helps in maximizing the usable material from each ingot.
Diamond Band Saw Blades - One of the key advantages of using diamond band saw blades for silicon cutting is their ability to provide high precision cuts. This is crucial for applications where accuracy is critical, such as in the semiconductor and photovoltaic industries. Additionally, diamond blades minimize chipping and cracking, thereby maintaining the integrity of the material. They also produce a smooth surface finish, which reduces the need for extensive post-processing. Furthermore, diamond band saw blades have a longer lifespan compared to conventional blades when cutting hard and brittle materials like silicon.
Cutting Method |
Precision |
Chipping/Cracking |
Surface Finish |
Blade Life |
Cutting Speed |
Cooling Requirement |
Maintenance |
Best Applications |
---|---|---|---|---|---|---|---|---|
Diamond Band Saw Blade |
High |
Minimal |
Smooth |
Long |
Moderate |
High |
Regular blade and equipment maintenance |
Semiconductor, photovoltaic industries |
Diamond Wire Saw |
Very High |
Very Minimal |
Very Smooth |
Long |
Slow to Moderate |
High |
Frequent wire inspection and replacement |
Advanced ceramics, semiconductor wafer slicing |
Laser Cutting |
High |
Minimal to Moderate |
Very Smooth |
N/A |
Fast |
Moderate (air cooling) |
Regular calibration and maintenance of laser |
Precision machining, intricate patterns |
Outside Diameter Diamond Blades |
Moderate |
Moderate to High |
Moderate |
Short |
Fast |
Low |
Frequent blade replacement |
General rough cutting, lower precision applications |
Waterjet Cutting |
Moderate to High |
Minimal |
Smooth |
N/A |
Moderate to Fast |
Very High (water and abrasive) |
Regular nozzle and pump maintenance |
Complex shapes, versatile materials |
ID Diamond Cutting Blade |
Very High |
Very Minimal |
Very Smooth |
Long |
Slow to Moderate |
High |
Regular inspection and dressing of the blade |
Semiconductor wafer slicing, high-precision applications |
Squaring
Squaring is a crucial step in the preparation of ingots for the wafering process, particularly in industries dealing with semiconductors, solar cells, and various advanced materials. After the top and tail of the ingot are removed—a process that eliminates irregularities and potential contaminants—the ingot is transformed from its original cylindrical shape into a square or rectangular cross-section. This section delves deeper into the significance, methods, and considerations involved in the squaring process.
The primary purpose of squaring is to prepare the ingot for efficient and precise slicing in the subsequent wafering stages. A square or rectangular cross-section provides several advantages:
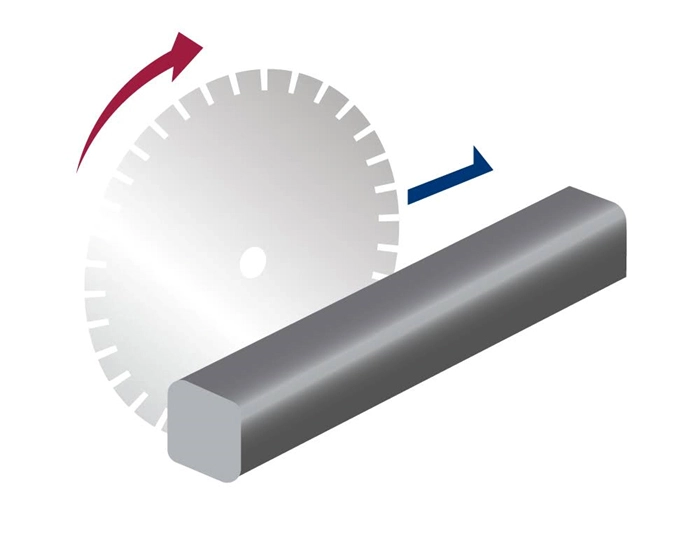
-
Uniformity and Consistency: Squared ingots ensure that wafers are produced with consistent dimensions and properties, which is critical for the high standards required in semiconductor manufacturing and photovoltaic applications.
-
Optimal Use of Material: By converting the cylindrical ingot into a squared shape, manufacturers can maximize the use of the material, reducing waste and improving the yield of valuable wafers.
-
Enhanced Handling and Mounting: Squared ingots are easier to handle, align, and mount on slicing equipment, which reduces the risk of errors during the cutting process.
Several techniques can be employed for squaring ingots, each utilizing distinct tools and technologies. Band sawing involves using a band saw equipped with diamond-impregnated blades to shape the ingot. This method is particularly favored for its ability to handle large ingots and its relatively low operational cost. Wire sawing is preferred for materials that require a high level of precision and minimal material loss. This technique employs a wire coated with abrasive particles to slice through the ingot, delivering high accuracy and smooth surfaces. An advancement of traditional wire sawing, multi-wire sawing, uses multiple wires simultaneously, significantly increasing both the throughput and efficiency of the squaring process.
When squaring ingots, it's crucial to manage several factors carefully to ensure optimal results. The choice of blade, whether for band sawing or wire sawing, is critical. Factors such as the blade’s material, grit size, and concentration must be matched to the ingot’s composition and the desired cut quality. Parameters like cutting speed, feed rate, and coolant flow must be optimized to minimize defects such as chipping and thermal damage, which can adversely affect the wafer's quality. Proper handling and precise alignment of the ingot before squaring are essential to avoid misalignments that can lead to material wastage and non-uniform wafers.
Silicon Block Formation
Silicon block formation is a crucial intermediate step in semiconductor manufacturing, occurring right after the squaring of the silicon ingot. This phase involves cutting the squared ingot into smaller, more manageable units known as silicon blocks. These blocks serve as the precursors to silicon wafers, which are essential components in the production of semiconductor devices.
Once the ingot has been squared, ensuring uniformity and structural integrity, it undergoes the block formation stage. Here, the large squared ingot is segmented into blocks using highly precise and controlled cutting techniques. Precision wire sawing, which employs a wire saw that operates with a thin, diamond-coated wire, is favored for its ability to make clean, precise cuts with minimal material loss. For larger ingots, ID sawing (Internal Diameter Sawing) is often used. This technique utilizes a large circular blade to slice through the silicon, maintaining consistent thickness throughout the block.
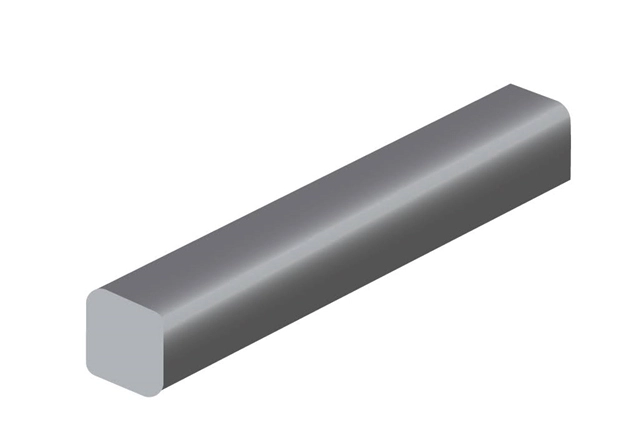
The transformation of squared ingots into smaller blocks enhances manageability. By reducing the size of the silicon from large ingots to smaller blocks, manufacturers can handle and process the material more efficiently. Smaller blocks are easier to manipulate, inspect, and transport, facilitating smoother operations throughout the manufacturing process. Additionally, smaller blocks allow for more precise control during the wafering process, crucial for ensuring that the wafers are uniform and meet the strict thickness and flatness specifications required for high-quality semiconductor devices.
However, despite its advantages, silicon block formation presents certain challenges. Maintaining the dimensional accuracy of each block is critical; any deviation in size can lead to significant issues during the wafering phase, affecting the uniformity and quality of the final wafers. The cutting process must also be meticulously controlled to avoid introducing defects such as cracks or impurities into the silicon, as these defects can propagate during subsequent processing stages, compromising the quality of the wafers. Additionally, each cut into the silicon ingot potentially results in material loss. Optimizing the cutting process to minimize waste is crucial, especially given the high cost of pure silicon.
Cropping
After silicon blocks are formed, they proceed to the cropping stage, where they are cut into smaller, more uniform pieces. This step is crucial in the wafer production process, as it ensures consistency in the size and shape of the wafers that are eventually produced. Cropping is typically done using precision cutting tools that can accurately measure and slice the silicon blocks to required specifications.
The main goal of cropping is to refine the block dimensions further, making them perfectly suited for the next stages of wafer processing. This involves cutting the blocks into precisely measured, smaller sections, which facilitates better handling and more efficient processing in subsequent manufacturing steps. Ensuring uniformity at this stage is essential because variations in the size and shape of these pieces can lead to inconsistencies during wafer fabrication, affecting the overall quality and performance of the semiconductor devices they become part of.
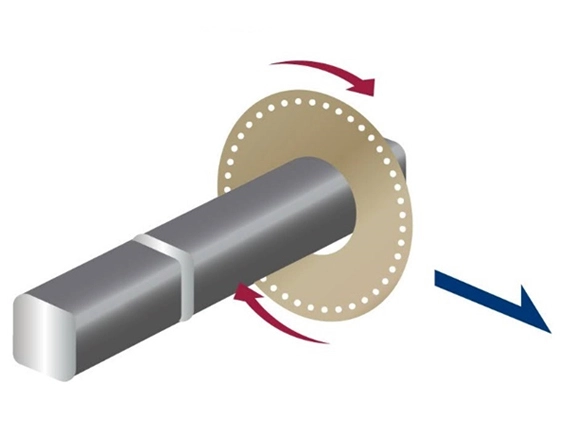
Cropping also serves to remove any irregular edges or defects that might have been introduced during the block formation stage. By doing this, manufacturers can improve the yield of high-quality wafers, as only the best parts of the silicon blocks are taken forward for further processing. This step is also strategic for minimizing waste—by accurately sizing the pieces, the amount of silicon discarded during later stages can be reduced.
However, cropping is not without its challenges. It requires extremely precise machinery and skilled handling to ensure that each piece meets the stringent standards required for semiconductor manufacturing. The equipment used must be regularly maintained and calibrated to avoid any deviations that could compromise the integrity of the wafers.
Outer Diameter (OD) Grinding
Outer Diameter (OD) Grinding is a critical process in the manufacturing of silicon wafers, focusing on achieving the required thickness and a high-quality surface finish. This stage is essential for ensuring that the wafers are not only uniformly thin but also exhibit smooth surfaces, qualities that are crucial for the high precision required in semiconductor device fabrication.
During OD grinding, the edges and outer surfaces of the wafers are meticulously ground to precise specifications using specialized grinding machines. These machines, equipped with diamond grinding wheels or other abrasive materials designed for silicon, carefully handle the wafers to avoid introducing any physical stress or damage that could lead to defects. The grinding process is meticulously controlled to achieve the exact thickness necessary for the functionality of semiconductor devices, as even minor deviations can affect the electrical properties.
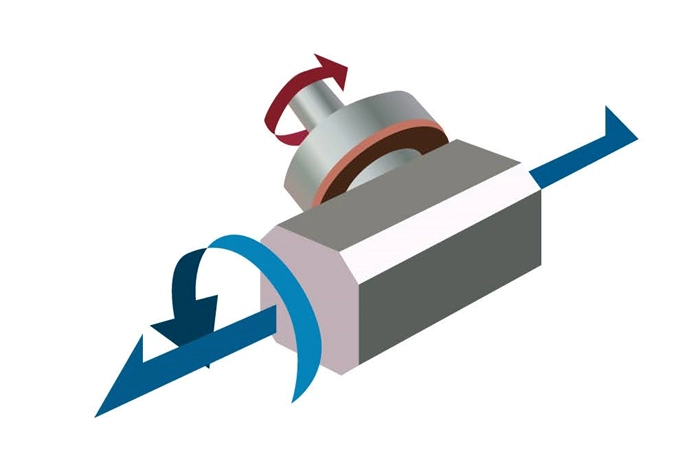
A smooth surface is necessary to ensure good adhesion of thin films and other materials in subsequent processing steps such as deposition and etching. Surface irregularities can lead to defects in these layers, compromising the performance of the final semiconductor devices. OD grinding also shapes the edges of the wafers to specific profiles, important for handling and mounting the wafers in various equipment throughout the manufacturing process. Properly profiled edges reduce the risk of chipping and breakage, which are critical for maintaining the integrity of the wafers during processing.
The precision of OD grinding impacts not just the performance but also the yield of semiconductor manufacturing processes. The grinding must be carefully controlled to ensure that all wafers meet the stringent requirements for thickness and smoothness. This involves continuous monitoring and adjustment of the grinding parameters, including the speed of the grinding wheel, the pressure applied to the wafers, and the use of appropriate cooling or lubricating fluids to minimize thermal damage.
Moreover, the equipment used for OD grinding must be maintained at a high level of operational readiness. Regular calibration and maintenance are required to ensure that the grinding wheels are in good condition and that the machinery is capable of performing the necessary precise movements and adjustments.
Wafering
Wafering is the process of slicing cropped silicon blocks into thin wafers, a critical step in the production of semiconductor devices. This stage uses advanced cutting technologies such as diamond wire saws or other precision cutting tools to achieve the required dimensions and properties of the silicon wafers. The quality of wafering directly influences the performance and reliability of the final semiconductor products, making it a highly controlled and precise operation.
The primary goal during wafering is to produce wafers that are not only thin but also have uniform thickness and exceptional flatness across their entire surface. These characteristics are vital because even minor deviations can lead to significant variations in the electrical properties of semiconductor devices. The process begins with mounting the silicon blocks onto the wafering machine. Here, either a single wire strung in a series of loops, known as a slurry saw, or a diamond-impregnated wire is used to cut the blocks into wafers.
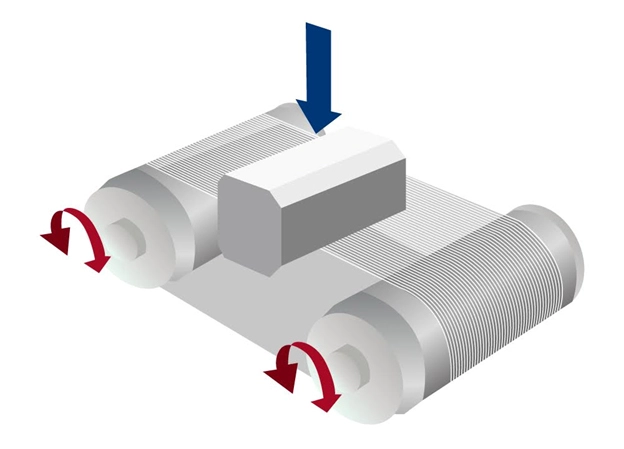
Diamond wire saws, in particular, have become the preferred tool for wafering due to their ability to cut with high precision while minimizing material waste. The diamond-coated wire slices through the silicon with a controlled application of tension and speed, which helps maintain the integrity of the silicon crystals and avoids damage like cracks or chips.
Control over the wafering process is maintained through several critical parameters:
-
Speed of the wire: Adjusting the speed can help control the rate of cutting and reduce thermal damage to the wafers.
-
Tension on the wire: Proper tension ensures that the wire does not sag or break, which can affect the consistency of the cut.
-
Coolant flow: The use of coolants not only reduces the heat generated during cutting but also helps in flushing away any debris, which could otherwise scratch the wafer surface.
After the wafers are sliced, they undergo inspection and cleaning. Any wafers that do not meet the stringent criteria for thickness and flatness are either reprocessed or discarded. This stage is crucial for ensuring that only the highest quality wafers proceed to the next phases of semiconductor manufacturing, such as doping, etching, and layer deposition.
The precision and efficiency of the wafering process also have a significant impact on the overall yield and cost-effectiveness of semiconductor production. Advances in wafering technology continue to focus on increasing the throughput and reducing the kerf loss (the width of material removed during the cutting process), which helps maximize the number of wafers produced from each silicon block.
Chamfering
Chamfering is a vital step in the manufacturing of silicon wafers, serving as a critical measure to enhance the durability and handling resilience of the wafers. This process involves beveling the edges of the wafers, which helps to prevent chipping and breakage during subsequent handling and processing steps. Chamfering not only increases the mechanical strength of the wafers but also significantly reduces the risk of damage that can occur from routine handling or when the wafers undergo various semiconductor fabrication processes.
The chamfering process is executed using specialized equipment that precisely grinds the edges of the wafers to create a beveled profile. This beveling is typically done at a 45-degree angle, although the exact angle and width of the chamfer can vary depending on the specifications required for particular applications. The goal is to remove any sharp edges and to create a uniform, smooth perimeter that can withstand stress without fracturing.
Several techniques are employed for chamfering, including:
-
1. Mechanical Grinding: This is the most common method, where mechanical grinders equipped with diamond-tipped wheels are used to shave off the sharp edges of the wafers. This method is highly effective and can be adjusted for different chamfer sizes.
-
2. Laser Chamfering: For applications requiring high precision and minimal physical contact, laser chamfering can be used. This method involves using a focused laser beam to melt and reshape the wafer’s edge. It's particularly useful for very thin or delicate wafers where mechanical stress needs to be minimized.
-
3. Chemical Etching: In some cases, chemical etching processes are used to chamfer the edges. This involves exposing the wafer edges to chemical agents that selectively remove material, rounding off the edges. This method is less common but can be advantageous for certain types of semiconductor materials.
Chamfering not only enhances the structural integrity of the wafers but also plays a significant role in improving the overall yield of the semiconductor manufacturing process. Wafers with chamfered edges are less likely to cause cross-contamination with debris from chips or cracks, thereby maintaining the cleanliness and purity required in semiconductor environments.
Monocrystalline Silicon Wafer – Final Product
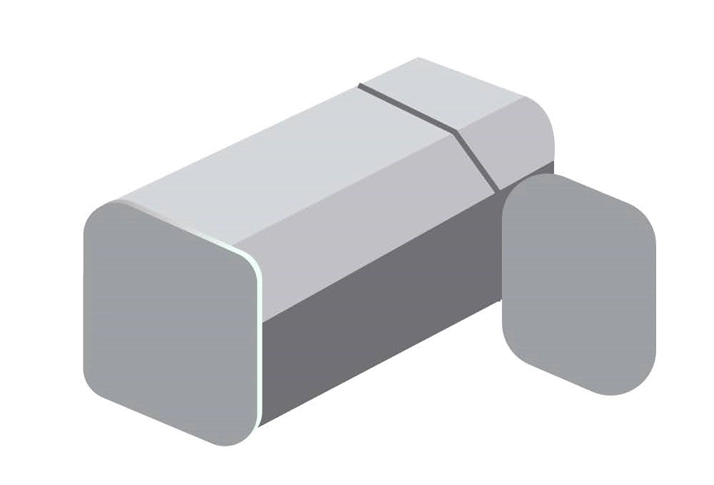
Multicrystalline Silicon Ingot Formation
Squaring
Squaring the multicrystalline ingot is a critical preparatory step in the fabrication of multicrystalline silicon wafers, which are extensively used in photovoltaic cells and various semiconductor applications. This process is analogous to the squaring of monocrystalline silicon, designed to convert the irregularly shaped multicrystalline ingot into a more uniform, manageable block, facilitating subsequent processing steps.
Multicrystalline silicon ingots, typically cast in rectangular molds, often emerge with rounded corners and uneven edges that need to be trimmed to optimize the use of silicon and improve handling efficiency. The squaring process involves cutting these ingots with precision tools to achieve a more standardized geometric form—typically a square or rectangular prism. This shape is not only easier to handle and process but also maximizes the yield of usable wafers by minimizing the amount of silicon that must be removed in later stages.
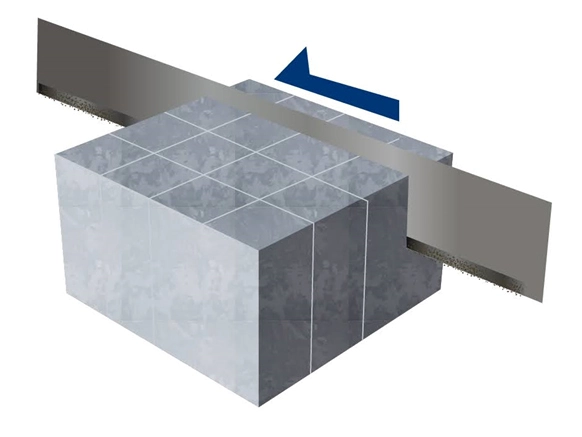
The squaring of multicrystalline ingots usually employs wire saws, which use a web of thin wires coated with an abrasive compound, such as silicon carbide or diamonds. These saws are capable of making clean, straight cuts and are highly efficient for processing multiple ingots simultaneously, which is crucial for scaling up production.
-
Enhanced Material Utilization: By transforming the ingot into a squared block, the process significantly reduces silicon wastage. The uniform shape allows for more efficient layout and cutting patterns when the wafers are subsequently sliced, maximizing the number of wafers obtained per ingot.
-
Improved Processing Efficiency: Squared ingots can be easily stacked, stored, and transported, reducing logistical challenges. Additionally, their uniform shape facilitates automated processing in later stages, enhancing the overall efficiency of the wafer production line.
-
Quality Consistency: While multicrystalline silicon does not possess the same level of crystallographic uniformity as monocrystalline silicon, squaring helps in maintaining as much consistency as possible. A uniform block ensures consistent heat distribution during subsequent thermal processes, which is vital for maintaining quality across the batch.
Block Formation
Despite its benefits, squaring multicrystalline silicon presents certain challenges. The inherent structural irregularities of multicrystalline silicon, such as grain boundaries and crystallographic misalignments, can cause differential resistance to cutting tools, potentially leading to microcracks or particle generation. Additionally, the abrasive nature of the cutting process can introduce surface imperfections that must be carefully managed to avoid impact on the wafer's performance.
Block formation is a crucial intermediary stage in the production of silicon wafers, serving as the transition from large squared ingots to the smaller, more manageable units required for detailed processing. This step involves cutting the squared ingot into smaller, standardized blocks, which are subsequently cropped and wafered into the thin silicon slices used in semiconductor devices and photovoltaic cells.
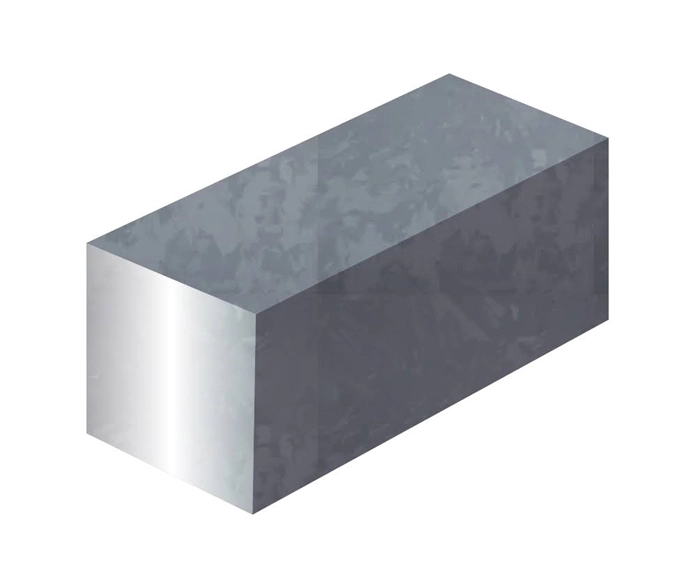
Following the squaring of the ingot, which standardizes its external dimensions and removes any peripheral material inconsistencies, the block formation process begins. This stage uses precise cutting technologies to segment the squared ingot into blocks. These blocks are designed to be of a size that optimizes handling, storage, and subsequent processing steps.
The cutting is typically done using wire saws or band saws. Wire saws are especially prevalent due to their ability to make clean, precise cuts with minimal material loss. These saws use a continuous loop of wire coated with abrasive particles, such as diamond grit, which slices through the silicon ingot. The process is carefully controlled to ensure uniformity in block size, which is crucial for the consistency of the wafers produced in later stages.
-
Standardization of Raw Material: By cutting the ingot into uniform blocks, manufacturers can standardize the starting material for the wafering process. This standardization is critical for automated mass production, allowing for consistent settings on machines in the cropping and wafering stages.
-
Optimized Material Use: Block formation is strategically planned to maximize the yield from each ingot. The dimensions of each block are calculated to minimize waste during the wafering process, thereby enhancing the overall efficiency of silicon utilization.
-
Improved Handling and Processing: Smaller blocks are easier to handle and process than large ingots. This ease of handling reduces the risk of damage during transport and processing, which is crucial for maintaining the integrity of the silicon, a material that is inherently brittle and prone to cracking under stress.
Despite its benefits, block formation presents several challenges. Precision in cutting is paramount; any deviation can lead to significant material waste or the production of non-uniform wafers, which would be unsuitable for high-quality semiconductor applications. Additionally, the mechanical stress induced during cutting must be meticulously managed to prevent the introduction of microcracks or other defects into the silicon blocks. These defects can propagate during subsequent processing, severely impacting the quality of the final wafers.
Cropping
Cropping is a critical stage in the preparation of silicon blocks for the wafering process, where these blocks are cut into smaller, more uniform pieces. This step is essential for ensuring that the dimensions and properties of the final wafers are consistent, which is vital for the high standards required in semiconductor manufacturing.
The cropping process involves slicing the pre-formed silicon blocks into thinner, more manageable slices that will be further refined into wafers. This step is typically conducted using precision cutting tools such as wire saws or blade saws, which can maintain high accuracy and minimize material loss. These tools are crucial for maintaining the integrity of the silicon, as any irregularities introduced during cropping can propagate flaws into the subsequent layers of semiconductor device fabrication.
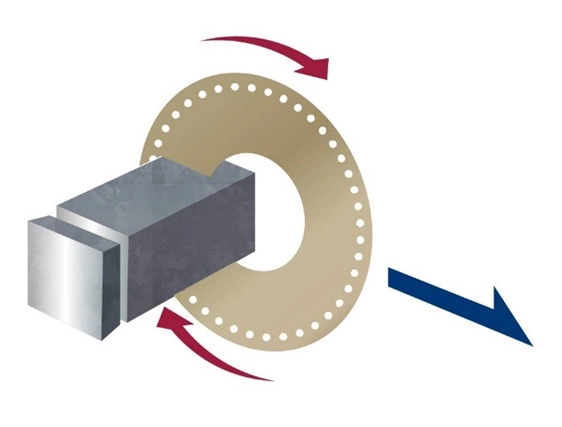
Wire saws, for instance, use a thin wire embedded with abrasive particles to cut through the silicon blocks. This method is favored for its ability to produce smooth, straight cuts while reducing the kerf loss—the amount of material wasted due to the cut. ID Blade saws, on the other hand, might be used for their speed and efficiency in processing larger volumes of material.
-
Uniformity and Precision: By ensuring that each piece is cut to precise specifications, cropping aids in the uniformity of the wafers produced. Uniform wafers are crucial for the semiconductor industry, where variations in thickness or flatness can lead to significant performance issues in electronic devices.
-
Material Efficiency: Cropping is designed to maximize the number of viable wafers that can be produced from each block. By optimizing the dimensions of each cropped piece, manufacturers can reduce waste and increase the overall yield of the production process.
-
Process Consistency: Consistent cropping practices help standardize the subsequent processing stages, including polishing and etching, ensuring that these processes can be conducted under uniform conditions to produce high-quality wafers.
Cropping presents several challenges that manufacturers must address to maintain the quality of the silicon wafers:
-
Control of Defects: The cropping process must be carefully controlled to avoid introducing defects such as cracks, chips, or microfractures into the silicon. Such defects can undermine the structural integrity of the wafers and render them unsuitable for high-precision applications.
-
Dimensional Accuracy: Maintaining dimensional accuracy is crucial, as any deviations can affect the alignment and layering processes in semiconductor manufacturing, potentially leading to defective electronic components.
-
Equipment Precision: The precision of the cropping equipment is fundamental. Wear and tear on blades or wires can lead to inconsistent cuts. Regular maintenance and calibration of equipment are necessary to ensure ongoing accuracy and efficiency.
Outer Diameter (OD) Grinding
Outer Diameter (OD) Grinding is a critical finishing process in the manufacturing of silicon wafers, where the wafers are ground to achieve precise dimensions, thickness, and surface smoothness. This process is essential for ensuring that the wafers meet the exact specifications required for high-quality semiconductor device fabrication.
OD grinding involves the use of specialized grinding machines that are equipped with abrasive wheels or belts designed specifically for silicon material. These tools are used to finely grind the outer diameter of the wafer, bringing it to the desired thickness and ensuring that the edges are perfectly round and smooth. This is particularly important for the uniformity of the wafers, which in turn, affects the consistency of device performance across the wafer.
The grinding process is carefully calibrated to achieve a high degree of surface finish and flatness, minimizing surface irregularities that can impact the functionality of semiconductor devices. Precise control over the grinding parameters, including the speed of the grinding wheel, the pressure applied, and the cooling methods used, is crucial to prevent damage such as cracking, warping, or the introduction of micro-abrasions that could lead to wafer breakage during subsequent processing steps.
-
Thickness Control: One of the primary goals of OD grinding is to achieve uniform wafer thickness. Uniform thickness is critical for processes like photolithography and etching, where depth precision is necessary for pattern accuracy and functionality of semiconductor circuits.
-
Improved Surface Quality: OD grinding helps in achieving a mirror-like surface finish that is essential for high-performance semiconductor applications. A smoother surface reduces scattering of light and electrons, which is crucial for the efficient function of devices like sensors and optical components.
-
Edge Integrity: The process also involves ensuring that the edges of the wafers are smooth and free from defects. Properly ground edges reduce the risk of chipping and cracking during handling and processing, thereby increasing the yield of usable wafers.
Despite its advantages, OD grinding presents several challenges that must be carefully managed:
-
Thermal Damage: The grinding process generates significant heat, which can affect the structural integrity of the silicon if not properly managed. Effective cooling systems are essential to dissipate heat and prevent thermal damage, such as slip dislocations or warping.
-
Material Removal Rate: Balancing the rate of material removal is critical. Removing too much material too quickly can lead to defects, while too slow a rate can be inefficient and economically non-viable.
-
Equipment Precision: The precision of the grinding equipment is vital. Wear and tear on the grinding wheels or belts can lead to inconsistencies in wafer thickness or surface finish. Regular maintenance and calibration of equipment are necessary to ensure ongoing accuracy.
Chamfering
Chamfering is a vital process in the production of silicon wafers, specifically designed to modify the edges of the wafers to prevent damage during handling, processing, and subsequent device fabrication. The process involves creating a beveled edge around the wafer, which helps to mitigate the risk of edge chipping and cracking, common issues that can significantly impair the quality and functionality of semiconductor devices.
The primary purpose of chamfering is to enhance the mechanical stability of silicon wafers by reducing stress concentrations at the edges, which are particularly vulnerable during loading and unloading operations. The chamfered edges are less likely to catch on or scrape against equipment and other wafers, thereby reducing the incidence of mechanical failures and yield losses.
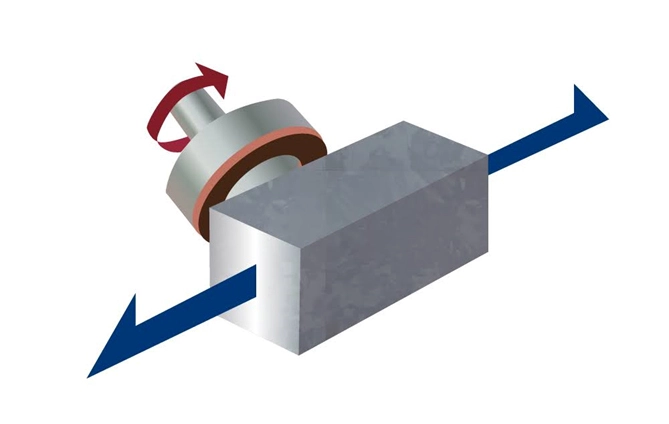
-
Increased Handling Safety: Chamfered edges make the wafers safer to handle. This is crucial in environments where manual handling of wafers is necessary, as it minimizes the risk of injury to personnel from sharp edges.
-
Enhanced Durability: By smoothing the wafer edges, chamfering reduces the likelihood of edge defects that can propagate into larger cracks during high-temperature processes such as oxidation and deposition.
-
Improved Process Integration: Many semiconductor manufacturing processes, such as lithography and etching, require precise alignment and uniform exposure. Chamfered edges contribute to better alignment and loading of wafers into process equipment, ensuring consistent processing across the entire wafer surface.
Chamfering can be achieved through various methods, each suited to different production scales and wafer specifications:
-
Mechanical Grinding: This is the most commonly used method for chamfering, where grinding wheels or belts are used to bevel the wafer edges. This technique is appreciated for its speed and ability to handle large batches of wafers.
-
Laser Chamfering: For high precision requirements, laser chamfering offers a contactless method to achieve a clean and controlled edge profile. This method is particularly useful for very thin or fragile wafers where mechanical stress needs to be minimized.
-
Chemical Etching: Chamfering can also be performed using chemical etching techniques, which remove material from the wafer edges by chemical action. This method is less common but can be advantageous for certain material types or when a very specific edge profile is required.
Despite its benefits, chamfering must be carefully controlled to avoid introducing new defects:
-
Process Control: The chamfering process parameters such as speed, pressure, and temperature must be meticulously managed to ensure consistent edge quality across all wafers.
-
Material Removal Accuracy: Excessive material removal can weaken the wafer's structural integrity, while insufficient chamfering might not effectively reduce the risk of edge damage.
-
Integration with Other Processes: Chamfering must be seamlessly integrated into the wafer fabrication workflow to prevent bottlenecks and ensure that the edge profiles are compatible with subsequent processing steps.
Face grinding
Face grinding is a critical process in the preparation of multicrystalline silicon wafers, where the flat surfaces or "faces" of the wafers are finely ground to achieve desired thickness uniformity and surface smoothness. This process is especially important for multicrystalline silicon, which inherently contains grain boundaries and other microstructural irregularities due to its casting process. These characteristics pose unique challenges and require specific attention during grinding to ensure high-quality wafers suitable for photovoltaic cells and certain types of semiconductor devices.
Process Overview
In face grinding, multicrystalline silicon blocks or wafers are mounted on a chuck or carrier, which holds them securely during the grinding process.
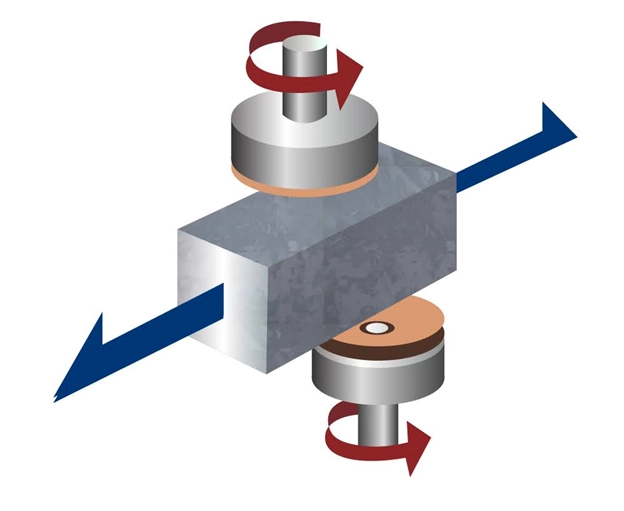
Grinding wheels or large abrasive belts, which can be coated with diamond or other high-hardness materials, are used to abrade the surface of the silicon. This not only smooths the surface but also removes excess material to bring the wafer to its target thickness.
The process involves several key steps:
-
Rough Grinding: This initial phase removes the majority of the material. It is performed under controlled conditions to quickly reduce thickness without inducing too much stress or sub-surface damage.
-
Fine Grinding: Following rough grinding, fine grinding uses finer abrasives to achieve a smoother surface and tighter thickness tolerances. This step is crucial for ensuring the functional quality of the wafers.
Importance of Face Grinding
-
Surface Uniformity: Face grinding helps to create a uniform surface free from irregularities and defects, which is essential for multicrystalline wafers. Uniform surfaces ensure consistent electrical properties across the wafer, which is crucial for the efficiency of solar cells and the reliability of semiconductor devices.
-
Thickness Accuracy: Precise control of wafer thickness is vital for subsequent processing steps, such as doping and metallization in solar cell manufacturing. Thickness uniformity across a wafer ensures even reaction rates and depths during these processes.
-
Reduced Subsurface Damage: Properly executed face grinding minimizes subsurface damage, which can otherwise lead to weakened wafers and increased breakage rates during handling and further processing.
Challenges in Face Grinding of Multicrystalline Silicon
-
Material Hardness Variation: The varying hardness and abrasiveness of the different crystal grains in multicrystalline silicon can lead to non-uniform material removal rates during grinding, posing challenges in achieving surface uniformity.
-
Stress Management: The grinding process introduces mechanical stresses that can exacerbate the formation of microcracks, particularly along grain boundaries. Managing these stresses through careful control of grinding parameters is essential.
-
Heat Dissipation: Like other abrasive processes, face grinding generates significant heat. Inadequate heat management can lead to thermal damage, affecting the electrical properties and mechanical strength of the wafers.
Wafering
Wafering is the critical process in semiconductor manufacturing where cropped silicon blocks are transformed into thin, flat wafers, ready for subsequent electronic device fabrication. This stage involves slicing the blocks with high precision to ensure that the resulting wafers meet stringent thickness and flatness specifications crucial for the functionality and reliability of semiconductor devices.
During wafering, the cropped silicon blocks are loaded into specialized cutting machines equipped with precision tools, such as diamond wire saws. These saws utilize a thin, diamond-coated wire that slices through the silicon with minimal material waste and high accuracy. The process is meticulously controlled to ensure uniformity across all wafers produced, with each wafer being measured to verify that it meets the precise thickness and flatness required.
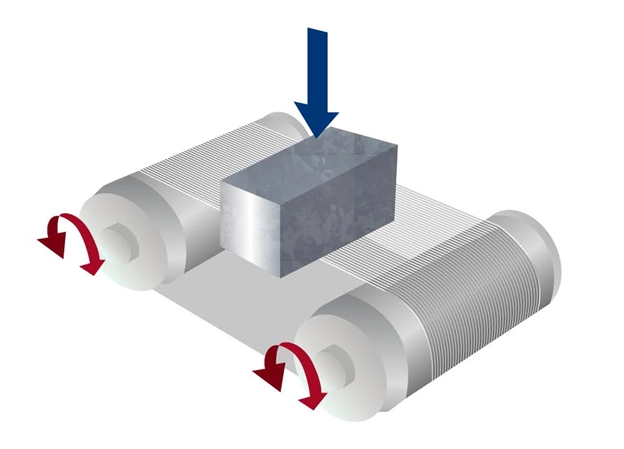
The choice of cutting tool and technique is dictated by the need to minimize damage to the silicon material. Diamond wire saws, for example, offer advantages in terms of speed and efficiency and are particularly effective at reducing the occurrence of kerf loss—the silicon wasted as sawdust during the cutting process. This is not only economically beneficial but also critical for sustainable manufacturing practices.
The exacting standards required in wafering are due to the direct impact that wafer uniformity has on the semiconductor manufacturing process:
-
Thickness Consistency: Variations in wafer thickness can lead to problems in subsequent processing steps such as lithography and etching, where uniformity is crucial for patterning and layering accuracy.
-
Surface Flatness: The flatness of wafers affects the ability to uniformly deposit thin films and other materials on their surfaces. Any irregularities can lead to uneven layer thicknesses, which can impede the electrical performance of the finished semiconductor devices.
-
Structural Integrity: Maintaining the structural integrity of wafers during cutting is essential to prevent defects such as microcracks or warping, which could lead to failures during device assembly or operation.
Despite advances in technology, wafering presents several challenges that must be managed to maintain high-quality output:
-
Material Quality: The inherent qualities of the silicon material, such as crystal orientation and purity, can affect how it behaves during the cutting process. Inconsistencies in the material can lead to variations in cutting performance and wafer quality.
-
Tool Wear: The precision tools used in wafering undergo wear and tear, which can affect their performance. Regular monitoring and replacement of these tools are necessary to maintain the quality of the cuts.
-
Process Control: The need for precise control over cutting speed, wire tension, and coolant flow is critical. Any deviations can cause fluctuations in wafer thickness and flatness, leading to batch inconsistencies.
Monocrystalline Silicon Wafer – Final Product
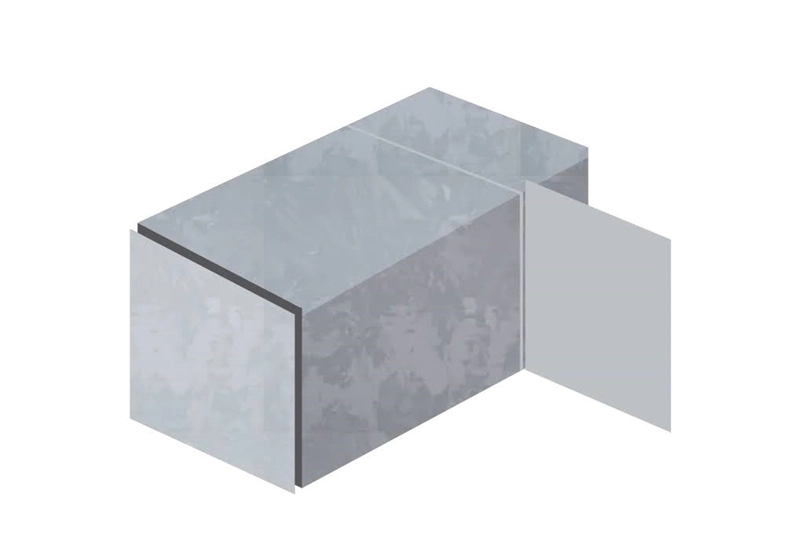