Table of Contents
ToggleCutting is a foundational step in the lapidary process, and the choice of diamond Lapidary blade significantly influences subsequent stages. While the market offers a plethora of blades for lapidary work, their performance and quality and level of consistency can vary widely.
The key to optimal performance is choosing a “high Quality Diamond Lapidary Blade” that is most optimal for your needs and application.
Share this Article with Friend or Colleague
Imagine you're planning a trip from point A to point B. Any car can theoretically make the journey, but the choice of vehicle greatly influences the experience. A compact car might be fuel-efficient and perfect for city driving, but it may struggle on rough terrain. Conversely, an SUV might handle off-road conditions with ease but be more costly to fuel and maintain. Similarly, a sports car offers speed and style but might not be the best choice for a family trip. Each car has its strengths and weaknesses, depending on the journey and your specific needs.
This analogy mirrors the selection process for diamond lapidary blades. Just as any car can get you to your destination, any diamond blade can cut material. However, the effectiveness and efficiency of the cut depend on choosing the right blade for the job. Some blades are designed for quick, rough cuts, akin to the sports car's speed but might lack the finesse for delicate work. Others offer precision and a smooth finish, similar to the reliability and comfort of a family sedan, making them ideal for more intricate lapidary tasks. Then there are blades built for durability and tough materials, much like an SUV's robustness for challenging conditions.
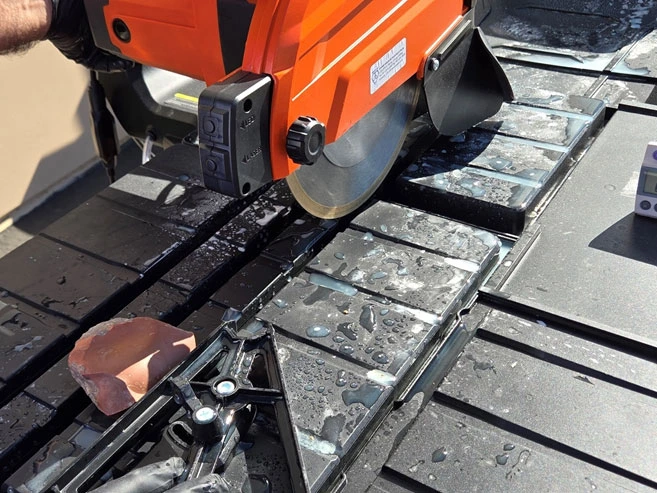
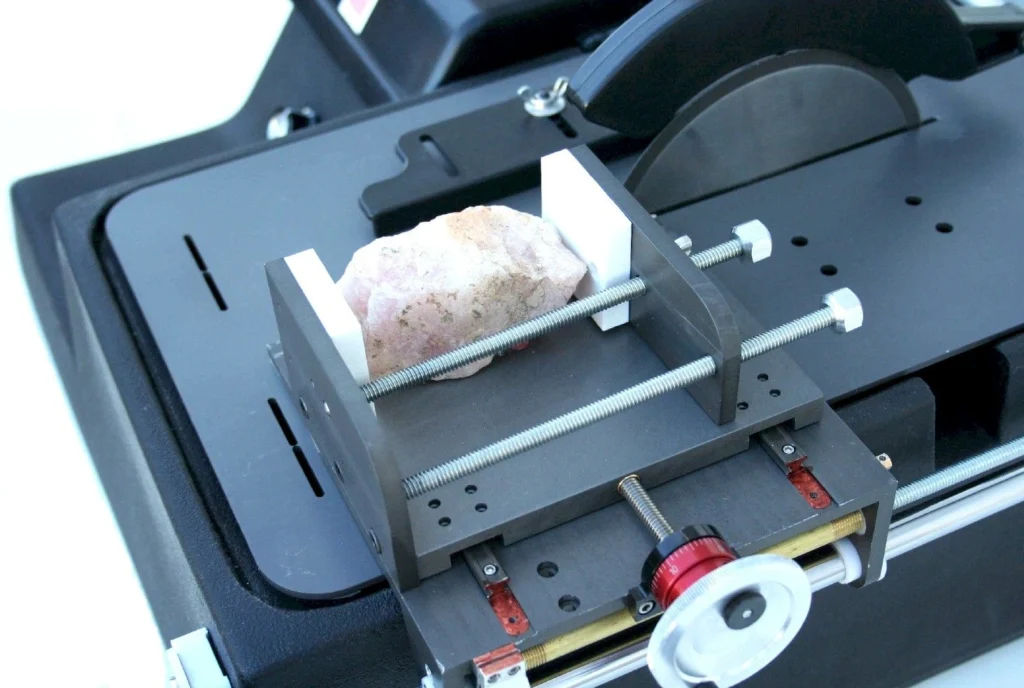
Just as you'd choose an SUV for off-road adventures or a compact car for urban errands, selecting a diamond blade involves considering the material you are cutting, the desired quality of the finish, and how often you will use the blade. The right choice leads to efficient, effective cutting, minimizing waste and saving time—just as the right car can make your journey more enjoyable, cost-effective, and suited to your needs.
Just as with cars, the world of diamond lapidary blades sees a wide spectrum of manufacturers, each offering products with varying levels of quality, performance, and sophistication. Drawing a parallel to the automotive industry, where the difference between an entry-level Chinese car and a high-end American or European luxury vehicle is stark, similar disparities exist among blade producers. These differences manifest in the design, mechanics, and composition of the products they offer.
In the automotive world, luxury vehicles are celebrated for their advanced engineering, superior materials, and meticulous attention to detail. These cars offer enhanced performance, durability, and a host of refined features that cater to the discerning driver's needs. They are the result of years of research and development, leveraging cutting-edge technologies and high-quality materials to achieve excellence in every aspect, from safety and comfort to efficiency and power.
Likewise, high-quality diamond lapidary blades are products of advanced technology and precision engineering. Top-tier manufacturers invest significantly in research and development to discover innovative ways to enhance blade performance. They use premium synthetic diamonds with optimal hardness and thermal stability, ensuring that the blade cuts effectively and lasts longer. The bond matrix that holds these diamonds is meticulously formulated to balance wear rate with cutting efficiency, allowing for consistent exposure of sharp diamond crystals. This is specially important when cutting ultra hard materials harder then 8.0 on mohes scale of hardness. This is where you can really tell the difference between blades.
The craftsmanship involved in creating such blades also mirrors the luxury car manufacturing process. Just as luxury cars are assembled with a keen eye for detail and strict quality control standards, leading diamond blade manufacturers employ precision manufacturing techniques to ensure every blade meets high standards of quality and consistency. This includes ensuring uniform diamond distribution, optimizing blade geometry for stability and precision, and incorporating features like advanced cooling systems to prevent overheating and extend the blade's lifespan.
High-quality diamond lapidary blades stand out due to their superior features, design, craftsmanship, and reliability. The mark of an exceptional blade is found in a combination of factors that contribute to its efficiency in cutting, longevity, and the ability to achieve fine finishes with minimal waste.
To discover which blade works best for your needs, we recommend try a few and see how they perform. However, you can also look for signs of a high-quality blade, such as the type of diamonds used, how those diamonds are placed & distributed through the blade, tolerances on kerf thickness, side relief, diamond depth/height, type of steel core used, and other features. These features help make cutting faster, freer, easier more precise, minimize heat generation, improve cut quality and consistency. Bottom line: Using the “Right High Quality Blade for your Application” will help you save time and money.
Diamond Quality and Size
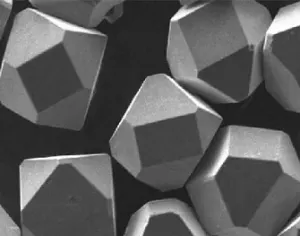
High-Quality Diamonds:
The cornerstone of an exceptional diamond lapidary blade lies in the caliber of the diamonds embedded within its matrix. These diamonds are not just any ordinary stones; they are high-grade, synthetic diamonds engineered to exhibit unparalleled hardness and exceptional thermal stability. This superior quality ensures that the blade can withstand the rigors of cutting through the toughest materials without succumbing to premature wear or loss of cutting efficiency. Moreover, the uniformity in the quality of these diamonds ensures consistent performance across the blade's lifespan, a crucial factor in achieving precise cuts time after time. Find Out More>>>
Advanced Synthetic Diamond Production
The quality of diamonds incorporated into these blades is not just a matter of selecting the hardest available stones; it involves a sophisticated evaluation of several critical attributes that influence how the blade performs under various cutting conditions. Here are additional facets of diamond quality that underscore its importance:
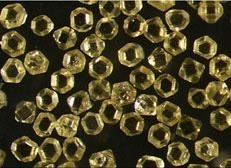
-
Controlled Synthesis for Specific Properties: Modern synthetic diamond production has evolved to control the crystalline growth process precisely, tailoring diamonds to exhibit specific properties such as exceptional hardness, fracture toughness, and thermal stability. This level of control ensures that the diamonds used in lapidary blades are not only incredibly hard but also possess the resilience needed to withstand the stresses of cutting without fracturing.
-
Technological Innovations in Diamond Coating: A number of our diamond lapidary blades utilize diamonds that have been coated with different coatings such as titanium or other metals to enhance their bond to the matrix and improve heat dissipation during cutting. This coating technology significantly extends the life of the diamond particles, allowing them to maintain their cutting edge longer than uncoated diamonds.
Diamond Grading and Selection
Proper quality control of diamond particles and other raw materials prior to manufacturing will help determine the consistency of the final product. Some of important quality control steps diamond crystals used in the lapidary blade manufacturing process include:
Microscopic Grading for Uniformity and Quality:
Each diamond destined for use in a premium diamond lapidary blade undergoes microscopic examination to ensure it meets stringent criteria for size, shape, and quality. This meticulous selection process guarantees the uniformity of the diamonds throughout the blade, which is crucial for consistent cutting performance and longevity.
Impurity Control for Enhanced Performance:
The presence of impurities within synthetic diamonds can adversely affect their performance. Advanced purification processes are employed during diamond synthesis to minimize these impurities, ensuring that the diamonds offer the highest level of performance and durability. The purity of the diamonds not only affects their cutting efficiency but also influences the blade's overall lifespan.
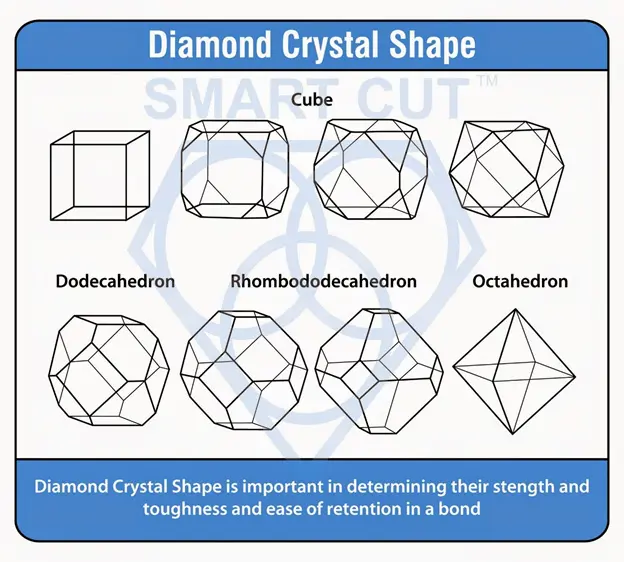
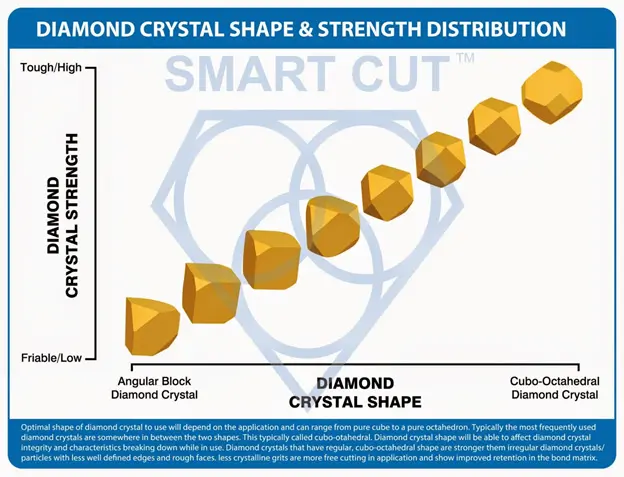
Optimal Diamond Size and Distribution
The effectiveness of a diamond lapidary blade is significantly influenced by the grit size of the diamonds, which must be carefully selected based on the specific cutting application.
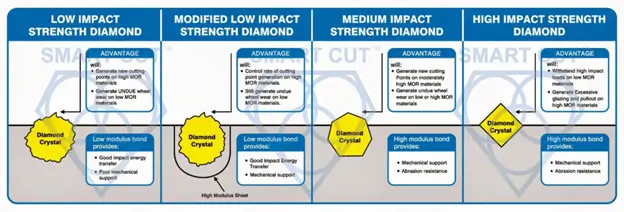
The grit size impacts not only the cutting speed but also the finish quality of the material being cut. Fine grit diamonds, often used in blades designed for cutting gemstones or other delicate materials, ensure a smooth, precise cut with minimal surface damage. Conversely, blades intended for more aggressive material removal may incorporate coarser grit diamonds, which can cut more quickly through harder materials. Find Out More About Diamond Grit Size>>>
Right Diamond Grit Size for Material Hardness Being Cut:
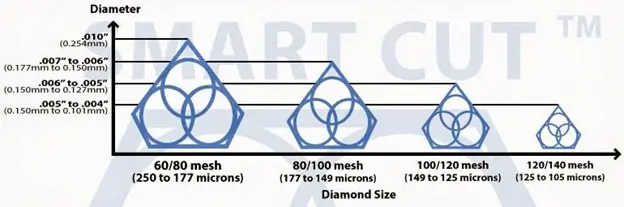
The optimal size of diamonds embedded in a lapidary blade is intricately matched with the hardness and abrasiveness of the material to be cut. For instance, cutting softer materials like limestone or marble may require larger diamond particles to prevent excessive blade wear, whereas harder materials like granite or sapphire necessitate finer diamonds for precise and smooth cutting. This precise matching ensures that the blade operates efficiently, maximizing both cutting speed and the quality of the finish.
Uniform Distribution Across the Blade:
The diamonds within the cutting edge (bond matrix) of the blade should be distributed uniformly to ensure consistent cutting performance across the entire blade surface. This uniformity is critical for maintaining steady cutting rates, preventing hotspots that can lead to premature blade wear, and ensuring that each portion of the blade contributes equally to the cutting process.
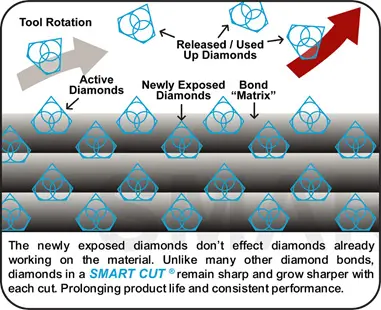
Strategic Placement for Maximum Efficiency:
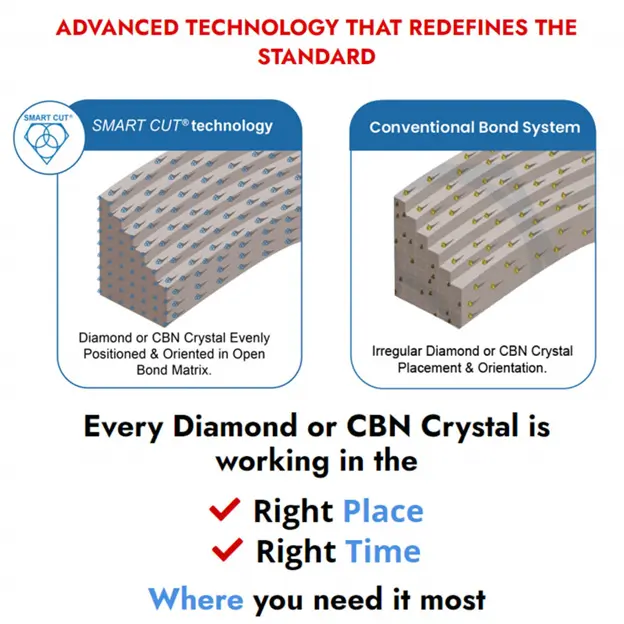
Beyond uniform distribution, the strategic placement of diamonds—based on advanced computational models—optimizes the cutting action for specific materials and cutting conditions. This might include concentrating diamonds in areas subjected to higher wear or dispersing them differently across the diamond edge designed for different cutting phases (e.g., initial entry, through-cutting, and exit).
Diamond Concentration
Optimizing Concentration:
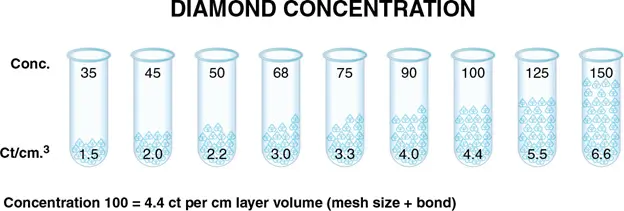
Optimizing diamond concentration in a lapidary blade is a delicate art that significantly influences both the blade's cutting performance and life span. This optimal balance is important because it directly impacts the blade's efficiency, heat management, cost-effectiveness, and adaptability to various materials. A superior diamond lapidary blade maintains an optimal diamond concentration that balances cutting efficiency with blade lifespan. Too high a concentration can reduce cutting speed, while too low can wear the blade out quickly.
Optimal diamond concentration ensures that there are sufficient cutting surfaces to interact efficiently with the material being cut. It allows for an even distribution of wear across the blade, extending its usable life. Moreover, the right concentration prevents overcrowding of diamonds, which can impede heat dissipation and debris removal—key factors in maintaining the blade's performance. Conversely, adequate spacing facilitated by balanced concentration promotes effective cooling and debris clearance, preventing overheating and the buildup of cutting residue.
From an economic standpoint, diamond concentration must also be considered to ensure that the blade remains cost-effective for its intended application. High diamond concentrations, while potentially enhancing the blade's cutting capabilities, increase the manufacturing cost due to the greater volume of diamond material used. Therefore, finding a balance in diamond concentration is essential not only for optimizing performance but also for ensuring the blade is economically viable, offering the best return on investment.
The hardness and abrasiveness of the material being cut further dictate the optimal concentration of diamonds. Harder materials may necessitate a denser concentration to maintain effective cutting, whereas softer materials might be better served with a blade that features a lower concentration, thus adapting the blade for optimal performance across various cutting scenarios.
Matrix Composition and Bond Hardness
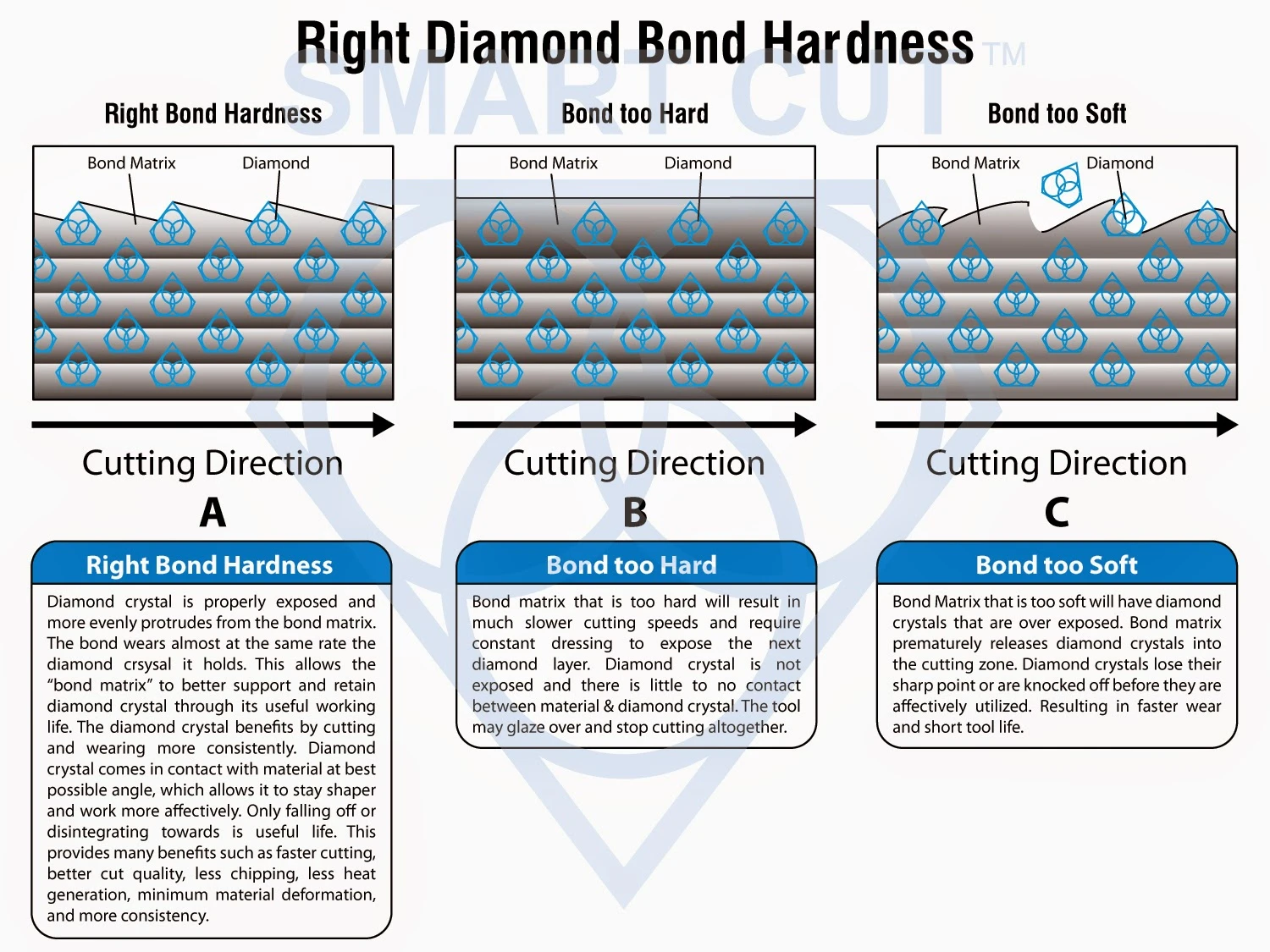
The composition and hardness of the matrix, or bond, that secures the diamonds in place are central to a diamond lapidary blade's performance. This bond is not a one-size-fits-all solution; it requires meticulous engineering to match the cutting task at hand. Expanding on the initial explanation, here are more insights into how matrix composition and bond hardness play pivotal roles in the functionality of a diamond lapidary blade:
Advanced Bond Matrix Composition/Formulation
The matrix composition is a sophisticated blend of metal powders and other materials engineered to achieve the desired hardness and wear characteristics. This blend determines how well the bond can support the diamonds, allowing them to protrude at the ideal height for cutting, while also controlling how quickly the bond wears away to expose new, sharp diamonds. The composition often includes metals such as cobalt, nickel, and bronze, which are selected for their ability to adhere to diamonds and withstand the thermal and mechanical stresses of cutting. Find Out More>>>
In addition to metal powders, modern matrix formulations may incorporate special additives and compounds designed to enhance the bond's performance. These can improve everything from the bond's wear resistance and thermal conductivity to its ability to adhere to the diamond particles. The precise composition is often proprietary, the result of extensive research and development efforts aimed at optimizing the cutting performance for specific materials.
Customizing Bond Hardness
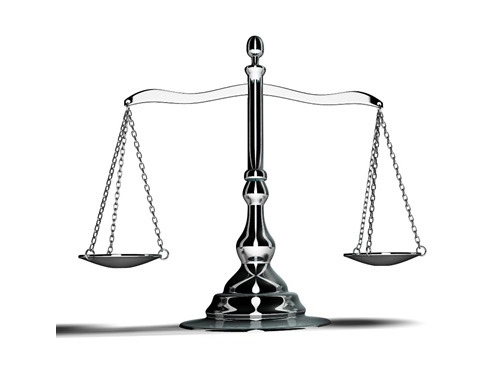
Customizing the bond hardness is a critical aspect of blade design, allowing blades to be produced for cutting a wide range of materials. Harder materials like agate and jasper typically require a softer bond. This softer bond wears away more readily, ensuring that dull diamonds are replaced with sharp ones in a timely manner, maintaining cutting efficiency. On the other hand, softer materials like marble or limestone are best cut with a blade that has a harder bond. A harder bond wears down more slowly, preventing the rapid exposure of new diamonds, which could lead to excessive blade wear and material loss.
This tailored approach to bond hardness is crucial for balancing cutting speed with blade lifespan. A bond that is too hard for the material can lead to glazing of the blade, where diamonds become over-polished and lose their cutting effectiveness. Conversely, a bond that is too soft may wear down too quickly, leading to premature blade replacement and increased operating costs.
Dynamic Exposure for Consistent Cutting (Open Bond Design)
The ultimate goal of tailoring the matrix composition and bond hardness is to achieve dynamic diamond exposure. This ensures that as the outer layer of diamonds wears down and loses its cutting edge, new, sharp diamonds are exposed at just the right time to take over the cutting task. This dynamic process is key to maintaining consistent cutting performance throughout the blade's lifespan. It allows the blade to adapt to changing cutting conditions and material properties, ensuring optimal performance from the first cut to the last.
Bond Matrix Composition:
Advanced diamond lapidary blades may use a composite matrix with varying hardness or wear characteristics throughout the blade's depth, adapting to different materials or stages of wear. The matrix composition of a diamond lapidary blade is akin to the meticulously crafted recipe of a gourmet dish, where the blend of ingredients, their quality, and the chef's expertise in combining them determine the final outcome's success. In the realm of diamond blades, the matrix—the material in which the diamond particles are embedded—plays a crucial role in the blade's performance, much like the foundational ingredients of a signature dish.
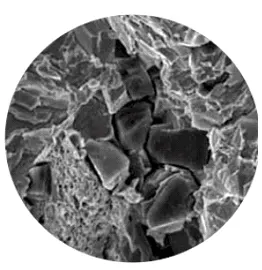
Superior Quality Lapidary Blades leverage a composite bond matrix, which, through its varying hardness and wear characteristics at different depths, is engineered to adeptly adapt to diverse materials and their respective cutting stages, much as a chef adjusts a recipe to achieve the perfect balance of flavors.
Bond Formulations as Culinary Recipes
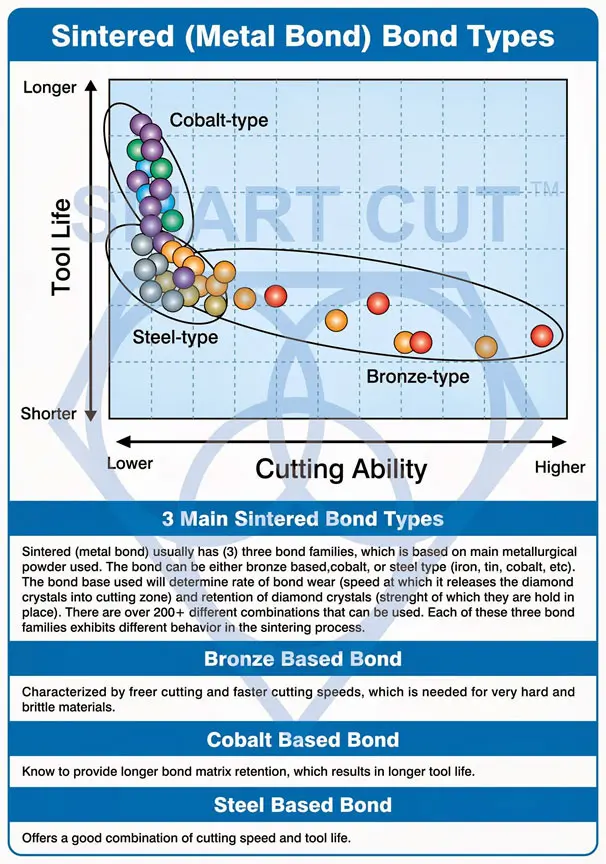
Just as every chef has their unique interpretation of a recipe, adding secret ingredients and employing specific techniques to create a standout dish, diamond blade manufacturers have their proprietary bond formulations. These formulations determine how well the blade can cut through various materials and how long it will last. The "secret ingredients" in a blade's matrix—whether they be specific types of metal powders, bonding agents, or other additives—are closely guarded trade secrets. These unique blends are what set one manufacturer's blade apart from another, much like the secret sauce that makes one restaurant's dish unforgettable compared to others.
The Role of Quality and Consistency
The quality and consistency of the ingredients used in both cooking and blade manufacturing cannot be overstated. Just as a chef sources the best possible ingredients to ensure each dish meets a high standard, manufacturers of diamond lapidary blades select premium raw materials. The uniformity of the diamond grit, the purity of the bonding metals, and the precision in the mixture contribute to a blade that cuts reliably, maintains its integrity, and reduces the need for frequent replacements.
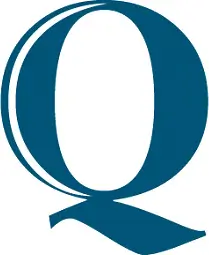
Equipment and Techniques
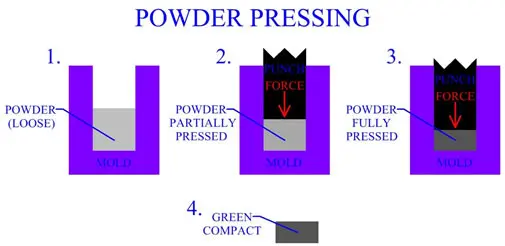
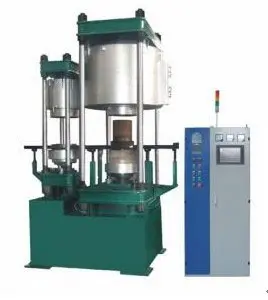
The analogy extends to the equipment and techniques used in the preparation process. In cooking, the choice of oven, the cookware, and even the cooking temperature can significantly impact a dish's quality. Similarly, the manufacturing equipment and processes—such as sintering temperatures and pressing techniques—play a pivotal role in how well the components of a diamond blade bond together. Advanced manufacturing technologies enable the creation of blades that are not only durable and effective but also tailored to specific cutting tasks.
Guarded Recipes and Competitive Edge
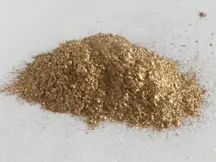
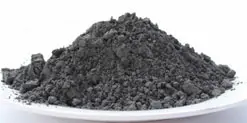
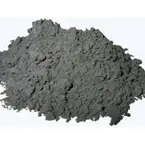
Just as a restaurant might keep its signature recipe a secret to maintain a competitive edge, the specific formulations and processes used to create advanced diamond lapidary blades are often proprietary. These "recipes" are developed through extensive research and development, refined over years of testing and customer feedback. The unique characteristics provided by these formulations are what make a blade from one manufacturer perform distinctly better in certain applications than those from another.
In essence, the matrix composition of a diamond lapidary blade is much more than a simple mix of materials—it's a carefully crafted recipe that defines the blade's identity and performance. Like the culinary masterpieces that stand out in the gastronomic world, high-quality diamond blades are distinguished by their unique formulations, the expertise with which they are created, and the precise application for which they are intended. These blades represent the culmination of science, art, and craftsmanship, offering users a tool that is unmatched in its ability to cut, endure, and excel.
Blade Thickness and Tension
Blade Kerf Thickness:
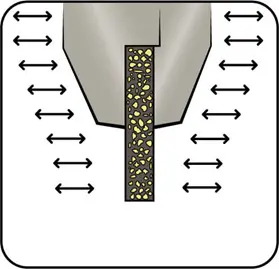
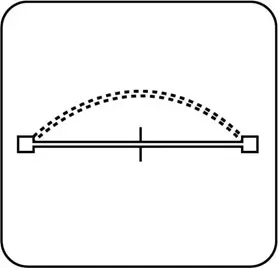
Ultra-thin blades represent one of the most desired blades in the world of lapidary cutting, specially for precious gemstones. These blades are tailored for lapidary artists and professionals who require most minimum loss of material possible and demand the utmost accuracy and efficiency. These blades are engineered to minimize the kerf—the width of the cut made by the blade—thereby reducing the amount of material lost during the cutting process. This feature is particularly valuable in lapidary work, where every millimeter of precious or semi-precious stone matters, and the goal is often to maximize the yield from raw materials.
Enhanced Precision and Control
The reduced thickness of ultra-thin lapidary blades offers enhanced precision and control, allowing for intricate cuts and shapes that would be challenging or impossible with thicker blades. This level of control is crucial for detailed work, such as creating complex jewelry designs or executing precise inlays that require tight tolerances and smooth edges.
Increased Material Yield and Cost Efficiency
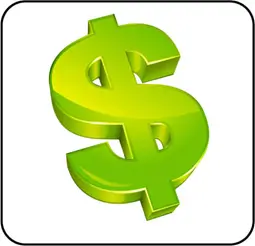
By minimizing material loss, ultra-thin blades contribute significantly to increased material yield. This efficiency is especially important in the lapidary field, where the materials being cut can be rare and costly. The ability to conserve more of these materials not only reduces waste but also enhances the overall cost-effectiveness of projects, allowing for a greater number of finished pieces from a given amount of raw lapidary material.
1. Reduced Stress on Materials
Ultra-thin lapidary blades exert less pressure on the material being cut, reducing the risk of cracks, chips, and other forms of damage that can occur during the cutting process. This gentle approach is particularly beneficial when working with delicate or brittle materials that are prone to fracturing under stress, ensuring that the integrity of the stone is preserved.
2. Energy Efficiency
The slender profile of ultra-thin lapidary blades also translates to lower energy consumption during cutting. Less material resistance means the cutting equipment can operate more efficiently, requiring less power to achieve the desired cuts. This energy efficiency not only reduces operational costs but also contributes to a more environmentally friendly cutting process.
3. Application Versatility
While ultra-thin lapidary blades are known for their precision and minimum kerf thickness, they also offer versatility across a range of lapidary applications. Whether cutting gemstones for jewelry, slicing minerals for collection, or shaping lapidary materials for decorative pieces, these blades can adapt to the specific requirements of each task, providing clean, precise cuts across a variety of materials.
Correct Blade Tension:
Tension testing is a critical aspect of the quality assurance process for diamond lapidary blades, ensuring that each blade maintains its flatness and stability under the operational stresses of cutting. This testing process is not merely a routine check but a rigorous evaluation that guarantees the blade's reliability and performance. Blades that have undergone and passed tension testing are distinguished by their ability to deliver precision cuts with minimal deviation or wobble, attributes that are essential for professionals demanding the highest standards of workmanship. This section delves deeper into the significance of tension testing and its impact on blade performance.
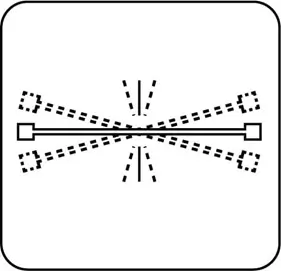
1. The Importance of Tension Testing
Tension testing involves applying forces to the blade to simulate the stresses it will encounter during use. This test assesses the blade's structural integrity, ensuring it can withstand the demands of cutting without bending, warping, or vibrating excessively. A blade that remains flat and stable under these conditions is less likely to produce inaccurate cuts or suffer from premature wear.
2. Impact on Cutting Accuracy
The stability of a blade directly influences its cutting accuracy. A lapidary blade that maintains its tension and does not wobble can make cleaner, more precise cuts. This precision is especially crucial when working with materials that require tight tolerances or when executing intricate designs. The assurance of a tension-tested blade gives operators confidence, allowing them to focus on the craftsmanship of their work rather than the reliability of their equipment.
Durability and Longevity
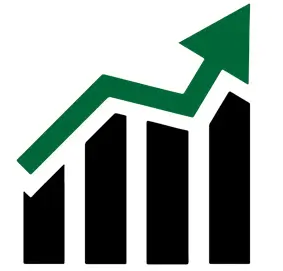
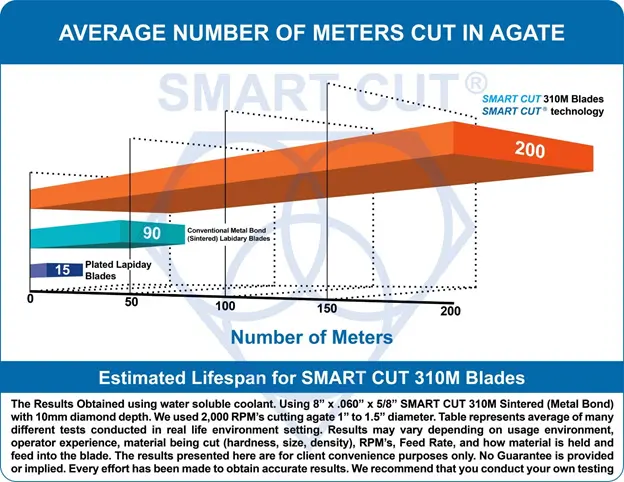
Longer Lifespan
The durability and longevity of a lapidary blade are indeed significantly influenced by the depth or height of the diamonds embedded within its matrix. This dimension is more than a mere measurement; it's a critical design feature that directly impacts the blade's ability to perform over time and through various cutting tasks. Understanding the relationship between diamond depth and a blade's enduring performance can offer insights into the intricate balance of design considerations that define a high-quality lapidary blade.
Durability and Longevity
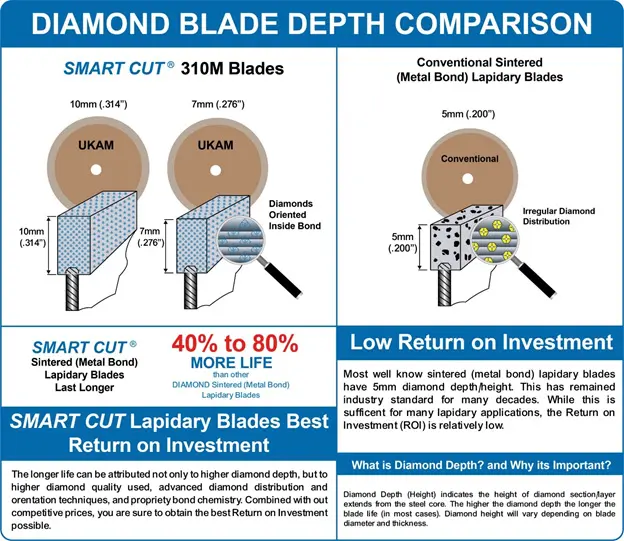
Diamond depth, or the height of the diamond segments from the blade's base, plays a pivotal role in determining how long a blade can maintain its cutting efficiency before needing replacement or resharpening. Deeper diamond segments mean that there is more diamond material available to be gradually worn down through the cutting process, extending the blade's useful life. As the outermost layer of diamonds wears away and becomes dulled, new, sharp diamonds are exposed, ready to continue the cutting task. This continuous renewal process ensures consistent performance, even as the blade ages.
Improved Cutting Performance
Beyond longevity, higher diamond depth/height can also enhance the overall cutting performance. With more diamond material available, the blade can maintain optimal cutting speeds and precision over a longer period. This is particularly beneficial when cutting through tough or abrasive materials, where a shallow diamond layer might quickly wear down, leading to a decrease in cutting efficiency and the need for more frequent blade changes.
Cost-Effectiveness
While blades with deeper diamond segments might initially cost more due to the greater amount of diamond material used in their construction, their extended lifespan often translates to improved cost-effectiveness over time. By reducing the frequency of blade replacements and the downtime associated with blade changes, these blades offer long-term savings and increased productivity, making them a wise investment for serious lapidary work.
Considerations for Material Types
The optimal diamond depth can vary depending on the types of materials being cut. Harder materials, which cause more wear on the blade, might benefit from deeper diamond segments for extended life. In contrast, softer materials might not require as much diamond depth, as the wear on the blade is less intense. Understanding the specific needs of the material being cut can help in selecting a blade with the appropriate diamond depth for both efficiency and longevity.
Balancing Design Factors
Diamond Depth should be carefully balanced with other blade design factors, such as bond hardness and diamond concentration, to create a well-rounded tool. A blade with deep diamond depth but an inappropriate bond for the material being cut might not offer the expected performance improvements. Similarly, the distribution and quality of the diamond particles within those segments are crucial for ensuring that the blade cuts effectively at all depths.
Tolerance on Blade Kerf Thickness
tolerance on the blade kerf thickness is a critical aspect when considering the precision and efficiency of lapidary blades. The kerf refers to the width of the cut made by the blade, and its tolerance indicates how much variation is allowed in that width. High-quality lapidary blades are engineered with tight tolerances on kerf thickness to ensure consistent and accurate cuts across various materials.
Maintaining strict tolerance on kerf thickness is essential for several reasons:
1. Precision Cutting
Tight tolerance ensures that each cut is as accurate as possible, crucial for intricate designs and patterns in lapidary work where every millimeter counts. This precision directly affects the fit and finish of the final piece, especially in jewelry making or inlay work.
2. Material Conservation
With minimal variation in kerf thickness, there's less waste of valuable material. This is particularly important in lapidary where the materials being cut, such as gemstones, can be rare and expensive. Tight tolerance on kerf thickness means more efficient use of these materials.
3. Consistency Across Cuts
Lapidary Blades with consistent kerf thickness produce more uniform cuts, which is vital when working on projects that require multiple pieces to fit together perfectly. Consistency ensures that parts are interchangeable and fit together seamlessly without additional adjustment or material removal.
4. Reduced Blade Stress
Variations in kerf thickness can lead to uneven stress distribution on the blade during cutting, potentially causing blade warp or premature wear. Tight tolerance helps distribute stress evenly, extending the life of the blade.
Blade Side Runout
Side run-out in diamond lapidary blades, particularly the difference in thickness between the diamond kerf and the steel core, plays a crucial role in determining the blade's cutting precision and overall performance. A significant variance here can lead to bending or flexing of the blade during use, impacting the accuracy and straightness of cuts. This precision is vital in lapidary work, where each cut needs to be exact for the final piece to come together perfectly.
The balance between the kerf and core thickness is key not only for ensuring the blade cuts accurately but also for maintaining its stability and reducing vibrations during operation. When the core is too thin compared to the cutting edge, it can cause the blade to wobble, leading to inconsistent cuts, increased material waste, and potentially faster wear and tear on the blade itself.
Compatibility with Cutting Equipment
1. Universal Compatibility across just about any Equipment:
Great Diamond Lapidary Blades are designed to fit a wide range of cutting machines, They should easily integrate with both high-speed professional lapidary equipment and smaller, benchtop models used by hobbyists.
Understanding the types of equipment these blades are compatible with can help users select the right blade for their specific requirements.
2. Lapidary Saws
Lapidary saws, including trim saws and slab saws, are fundamental tools in the cutting and shaping of gemstones. These saws can vary significantly in size and functionality:
-
Trim Saws: These are smaller saws used for fine cuts and trimming small pieces. They typically operate at higher RPMs for precision work. Diamond lapidary blades designed for trim saws are engineered for detailed and delicate cutting tasks, ensuring minimal material loss and smooth finishes.
-
Slab Saws: Larger than trim saws, slab saws are used to cut larger pieces of rough into slabs. These saws generally operate at lower RPMs compared to trim saws, requiring blades that can handle larger, thicker pieces without overheating or causing undue wear on the blade or the material.
Both types of saws can come in single or variable speed models, necessitating blades that can perform efficiently across a range of speeds. A blade's ability to maintain precision and minimal vibration at varying speeds is crucial for the versatility and quality of the cuts.
3. Other Cutting Equipment
Diamond lapidary blades are also compatible with a wider array of cutting tools beyond traditional lapidary equipment:
-
Tile Saws: Often used in masonry and tile work, these saws require blades that can deliver clean cuts through ceramic, porcelain, and stone. Diamond blades for tile saws are designed to operate effectively at the specific RPMs of tile saws, which can vary but typically are lower than those of lapidary saws to prevent chipping and cracking of the material.
-
Drop Saws: Commonly used in construction for cutting wood, metal, and sometimes stone, drop saws can benefit from specialized diamond blades when used for hard, abrasive materials. Blades for these saws need to withstand the impact and force associated with drop saw operations.
4. Adaptability to Different RPMs
The operational RPM (revolutions per minute) is a critical factor in the compatibility of diamond lapidary blades with various equipment. Blades are often designed to accommodate a range of RPMs to ensure:
-
Optimal Performance: Ensuring the blade can cut efficiently and with the desired finish across different materials and thicknesses.
-
Versatility: Allowing users to use the same blade on different machines, reducing the need for multiple, specific blades.
-
Safety and Durability: Operating within an optimal RPM range minimizes the risk of blade damage or failure, enhancing safety for the user and longevity of the blade.
A significant factor enhancing the compatibility of diamond lapidary blades with a wide range of equipment is the ability to customize the blade's inside diameter, also known as the arbor size. This customization ensures that the blades can be adapted to fit virtually any piece of equipment, further extending their versatility and utility across various applications. Here’s how this adaptability impacts users and their equipment:
Customizable Arbor Size
The arbor size of a blade determines the size of the saw's spindle with which the blade can be compatible. By offering the capability to alter the inside diameter of the blade, to anything the client requires same day for any quantity, we can cater to the specific needs of different machines, whether they are part of a sophisticated lapidary setup, a standard tile saw, or more specialized equipment. This flexibility is particularly beneficial for users who operate multiple types of saws or have unique equipment with non-standard arbor sizes. It ensures that high-quality diamond blades are not limited to a select few but are accessible to a broader range of users and applications.
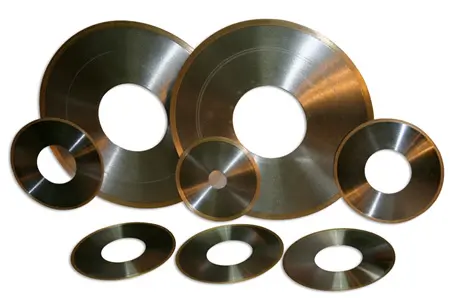
Bushings for Any Size
To further enhance this adaptability, we provide bushings that can adjust the blade’s arbor size to fit any equipment. Bushings are essentially adapters that reduce the diameter of the blade's hole to match the spindle size of the saw more precisely. This solution not only broadens the compatibility of diamond lapidary blades but also ensures a snug, secure fit, which is crucial for safe operation and optimal cutting performance.
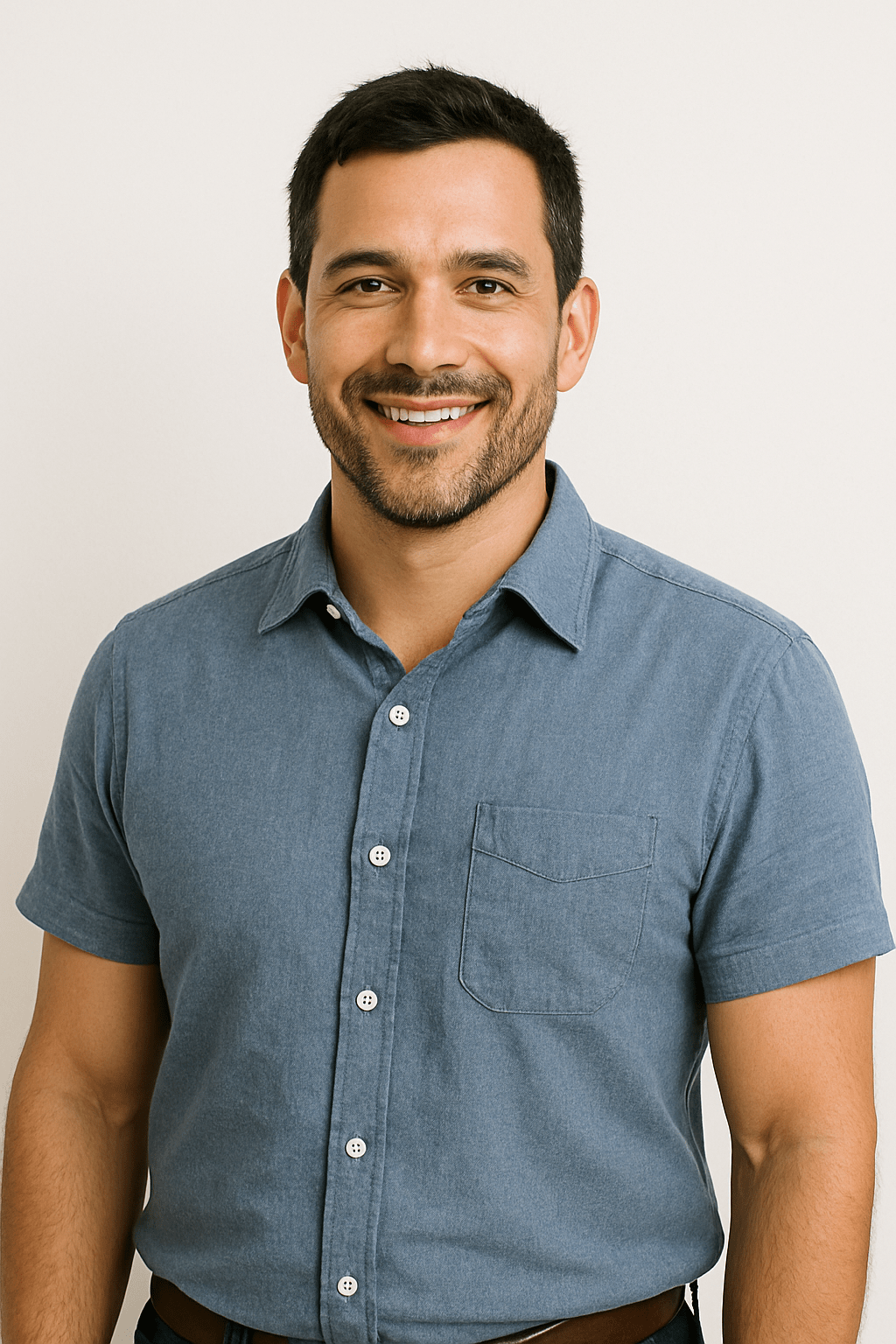
Carlos Sanchez is a senior technical specialist and field applications trainer with more than 17 years of experience in the use and optimization of industrial diamond tools, including ultra-thin diamond blades, core drills, and CBN grinding wheels. With a foundation in industrial engineering and technical operations, Mr. Sanchez has worked extensively with manufacturers and laboratories around the world, providing hands-on support and practical training for a wide range of cutting, grinding, and sample preparation applications.
Fluent in both English and Spanish, Carlos is known for his ability to translate complex tooling concepts into clear, actionable procedures for engineers, technicians, and production staff. His approach emphasizes real-world process improvement, tool longevity, and operator education—ensuring clients get the most out of their diamond tooling investments.
As an author, Mr. Sanchez shares field-tested insights on tool performance optimization, defect prevention, training methodologies, and troubleshooting common cutting issues.
ARE YOU USING RIGHT LAPIDARY BLADES
FOR YOUR APPLICATION?
LET US
HELP YOU
HAVING ISSUES WITH
YOUR CURRENT LAPIDARY BLADES?
Knowledge Center
How to Properly Use Diamond Lapidary Blades
Signs of a High Quality Diamond Lapidary Blade
What Makes a Great Diamond Lapidary Blade
Mastering the Art of Lapidary cutting
Evaluating & Comparing Diamond Blades
How to Improve & Optimize Your Diamond Sawing Operation
Troubleshooting Diamond Sawing Problems
How to properly use Diamond Tools
How to Selecting Right Diamond Tools for your application
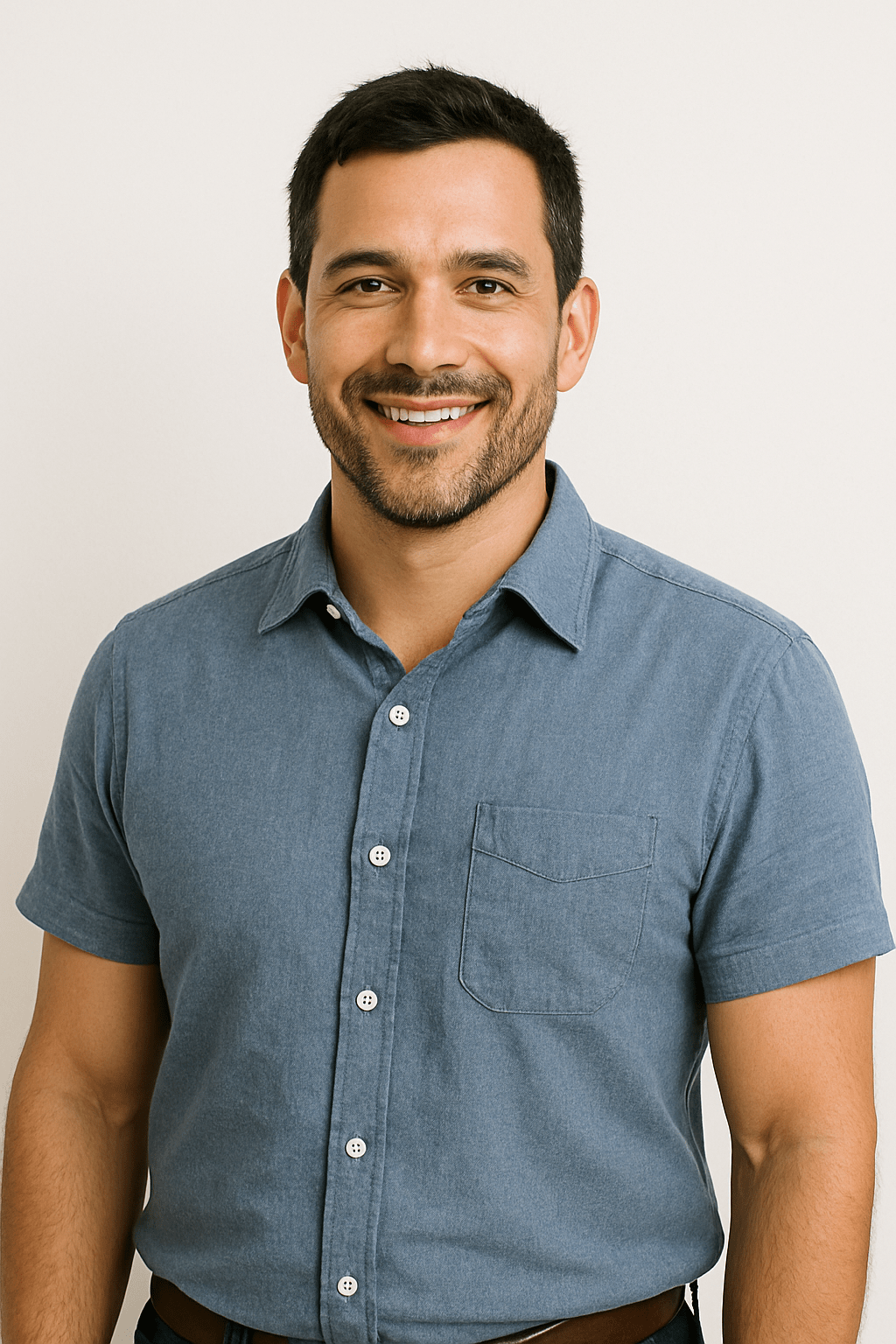
Carlos Sanchez is a senior technical specialist and field applications trainer with more than 17 years of experience in the use and optimization of industrial diamond tools, including ultra-thin diamond blades, core drills, and CBN grinding wheels. With a foundation in industrial engineering and technical operations, Mr. Sanchez has worked extensively with manufacturers and laboratories around the world, providing hands-on support and practical training for a wide range of cutting, grinding, and sample preparation applications.
Fluent in both English and Spanish, Carlos is known for his ability to translate complex tooling concepts into clear, actionable procedures for engineers, technicians, and production staff. His approach emphasizes real-world process improvement, tool longevity, and operator education—ensuring clients get the most out of their diamond tooling investments.
As an author, Mr. Sanchez shares field-tested insights on tool performance optimization, defect prevention, training methodologies, and troubleshooting common cutting issues.