Table of Contents
ToggleWhen evaluating diamond and cubic boron nitride (CBN) cutting blades, it’s crucial to consider key performance metrics and criteria. Different applications have varying goals, making it important to understand these factors to determine a blade’s effectiveness and impact on result quality. There are many metrics that are important in optimizing your cutting operation to ultimate level of efficiency. In this article we will focus on the main top 5 Key metrics include surface finish, blade life, cost, and consistency. For example, cutting optical glass prioritizes surface finish and cut quality, while cutting tiles and construction materials emphasizes cutting speed and cost. These criteria help differentiate blades and identify the best solution for specific applications. Here we will explain each of these main performance metrics and show different methods that these can be measured and calculated. Understanding and measuring these metrics is essential for improving and optimizing performance.
Key Top 5 Performance Metrics for Evaluating Diamond & CBN Blades
-
Cutting Speed: How quickly a diamond or cbn blade can complete a cut without sacrificing quality. Faster speeds can increase throughput but must not surface finish, cut quality and chipping and integrity of material.
-
Surface Finish: The quality of the surface after cutting is crucial. A finer finish reduces the need for subsequent grinding and polishing, thereby saving time and preserving the material's characteristics. Minimizing chipping and other forms of cut-induced damage is crucial for maintaining excelling surface finish quality.
-
Blade Life: This refers to how long a diamond or cbn blade can maintain its cutting effectiveness before it needs to be replaced. A longer blade life reduces downtime and the cost of consumables.
-
Cost per Cut: Considers the total cost of using the diamond and cbn blade divided by the number of cuts it can make before it is deemed ineffective. This metric helps in assessing the economic efficiency of the blade over its lifespan.
-
Consistency: The ability of the diamond or cbn blade to consistently produce quality cuts throughout its life span. Inconsistency can lead to wasted material and unreliable results.
14 Other Important Diamond & CBN Performance Metrics
Below are other important diamond & cbn performance metrics that we will discuss in another article
-
Required Force: A blade that requires less force to cut through materials is preferable as it minimizes potential sample damage and operator fatigue.
-
Heat Dissipation: Effective heat management improves cut quality and increases blade’s life. Blades that dissipate heat efficiently perform better in demanding conditions.
-
Material Compatibility: A blade's ability to handle different types of materials effectively without degradation is essential, especially when working with a variety of materials
-
Wear Resistance: Resistance to wear and tear defines how well a blade holds up under regular use, impacting its longevity and reliability.
-
Vibration: Lower vibration levels indicate a more stable cut, improve cut quality and cut consistency
-
Amount of Material Deformation: It’s essential to minimize deformation during cutting to ensure that the true microstructure of the material and material/part reliability
-
Secondary Grinding and Polishing Steps Required: Blades that produce cleaner cuts reduce the need for secondary finishing operations.
-
Thermal Stability: Assesses the blade's ability to maintain its properties and performance at varying temperatures. Blades with high thermal stability perform consistently across a range of operational conditions, which is crucial when working with thermally sensitive materials.
-
Blade Flexibility: Evaluates the blade's ability to flex without breaking, particularly when making intricate cuts or when operating under variable loads. This is important for ensuring the blade's reliability in complex cutting scenarios.
-
Recovery Time: The time it takes for a blade to return to optimal performance after dressing or any form of maintenance. Faster recovery can significantly reduce downtime
-
Edge Durability: Measures how long the cutting edge remains effective before it dulls. Durable edges reduce the frequency of blade replacements and maintenance.
-
Impact Resistance: Evaluates the blade's ability to withstand sudden stresses or impacts without cracking or chipping. This is particularly relevant for cutting hard, brittle materials.
-
Profile Retention: Measures how well a blade maintains its original profile and cutting characteristics over its lifespan. High profile retention reduces the need for frequent adjustments and recalibrations.
-
Blade Stiffness: A measurement of the rigidity of the blade. Stiffer blades are less prone to wobbling and can provide more precise cuts, especially important in high-precision applications.
Top 5 Diamond & CBN Performance Metrics
Metric |
Description |
Implications |
Operational Impact and |
---|---|---|---|
Cutting Speed |
Measures the speed at which a blade can complete a cut without compromising the quality, surface finish, and integrity of the m |
Increases throughput but may compromise cut quality if too high. |
Speed vs. Quality: Higher speeds can reduce blade life and worsen surface finish, requiring a balance to maintain cut integrity and operational efficiency. |
Surface Finish |
Assesses the quality of the surface post-cut. A finer finish reduces subsequent processing needs, preserving the material's characteristics. |
A finer finish reduces need for additional processing, saving time and resources. |
Influenced by Cutting Speed and Blade Sharpness: Optimal speeds and well-maintained blades ensure better finishes, reducing post-process work. |
Blade Life |
Indicates how long a blade can remain effective before replacement. |
Longer blade life reduces replacement frequency and associated costs. |
Affects Cost per Cut and Consistency: Prolonging blade life reduces overall operational costs and maintains consistency in production outputs. |
Cost per Cut |
Reflects the total cost of using the blade divided by the number of cuts it can perform before becoming ineffective. |
Directly impacts budgeting and financial planning in operations. |
Dependent on Blade Life and Cutting Conditions: Optimizing blade life and operational parameters reduces cost per cut, enhancing economic efficiency. |
Consistency |
The blade's ability to consistently produce reliable and high-quality cuts throughout its lifespan. |
Ensures reliable production outcomes and minimizes material waste. |
Relies on All Metrics: Maintaining consistent cutting conditions, speed, and blade maintenance is crucial for achieving reliable and predictable results. |
Cutting Speed for Diamond and CBN Cutting Blades
Cutting speed is a crucial performance metric when selecting Diamond and CBN blades. It refers to the rate at which the blade can cut through the material. This metric is important for several reasons. Higher cutting speeds can significantly enhance productivity by reducing the time required for each cut. This is particularly beneficial in high-volume cutting environments where time efficiency translates directly into cost savings. Optimal cutting speed ensures that the diamond or cbn blade operates within its designed parameters, leading to efficient material removal without causing excessive wear or damage to the blade. This balance helps maintain the blade's integrity and extends its usable life.
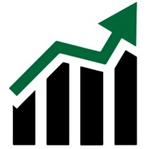
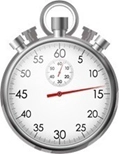
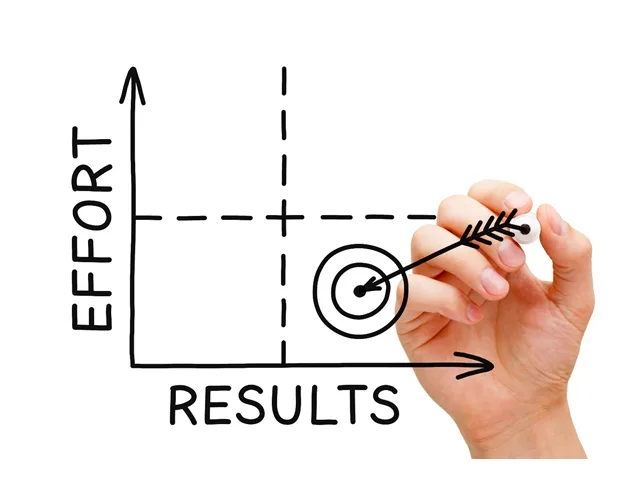
Different materials require different cutting speeds for optimal results. For example, harder materials like ceramics or superalloys may necessitate slower cutting speeds to prevent blade overheating and ensure a smooth finish, whereas softer materials can be cut at higher speeds. Cutting speed directly affects the amount of heat generated during the cutting process. Higher speeds can lead to increased heat, which needs to be managed to prevent damage to both the blade and the material. Proper cooling systems and blade design can mitigate these effects, allowing for higher operational speeds without compromising quality.
The speed at which a blade cuts can influence the surface finish of the material. Too fast a speed may cause rough edges or increased chipping, while too slow a speed can result in inefficient cutting and potential material deformation. Achieving the right balance ensures a high-quality surface finish appropriate for the specific application. Operating a blade at its optimal cutting speed reduces unnecessary wear and tear. Blades used at inappropriate speeds may experience accelerated degradation, leading to more frequent replacements and increased operational costs.
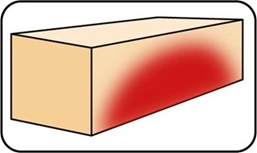
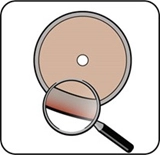
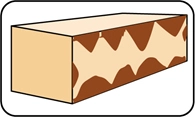
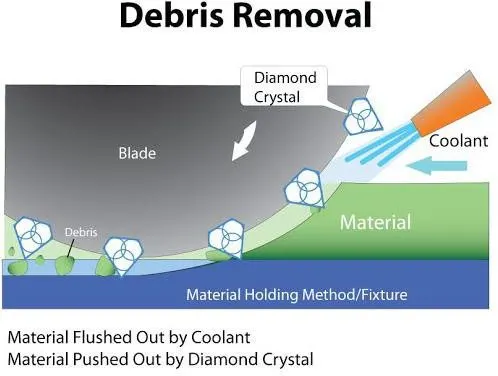
Optimizing Cutting Speed
To optimize cutting speed, several factors must be considered:
Material Hardness and Thickness
The hardness and thickness of the material being cut dictate the need for appropriate speeds to ensure precision without causing unnecessary damage or deformation.
Blade Specifications
The blade's diameter, bond type, kerf thickness, diamond size, concentration, and bond hardness all influence the ideal cutting speed. For instance:
Surface Finish (Cut Quality & Chipping Level)
Cut quality and the level of chipping are critical performance indicators for diamond and CBN cutting blades across a wide range of applications, The accuracy of the cut can significantly impact the usability and integrity of the material being processed. High-quality cuts are characterized by their cleanliness and minimal finishing required post-cutting, whereas chipping involves small fragments of the material breaking away during the cutting process, compromising the integrity and dimensions of the final product.
-
Diameter and Bond Type: Larger diameter blades and harder bonds may require slower speeds.
-
Kerf Thickness: Thinner kerf blades can operate at higher speeds but may need more frequent dressing.
-
Diamond Size and Concentration: Optimal speeds vary with diamond size and concentration; finer diamonds typically allow for smoother finishes at lower speeds.
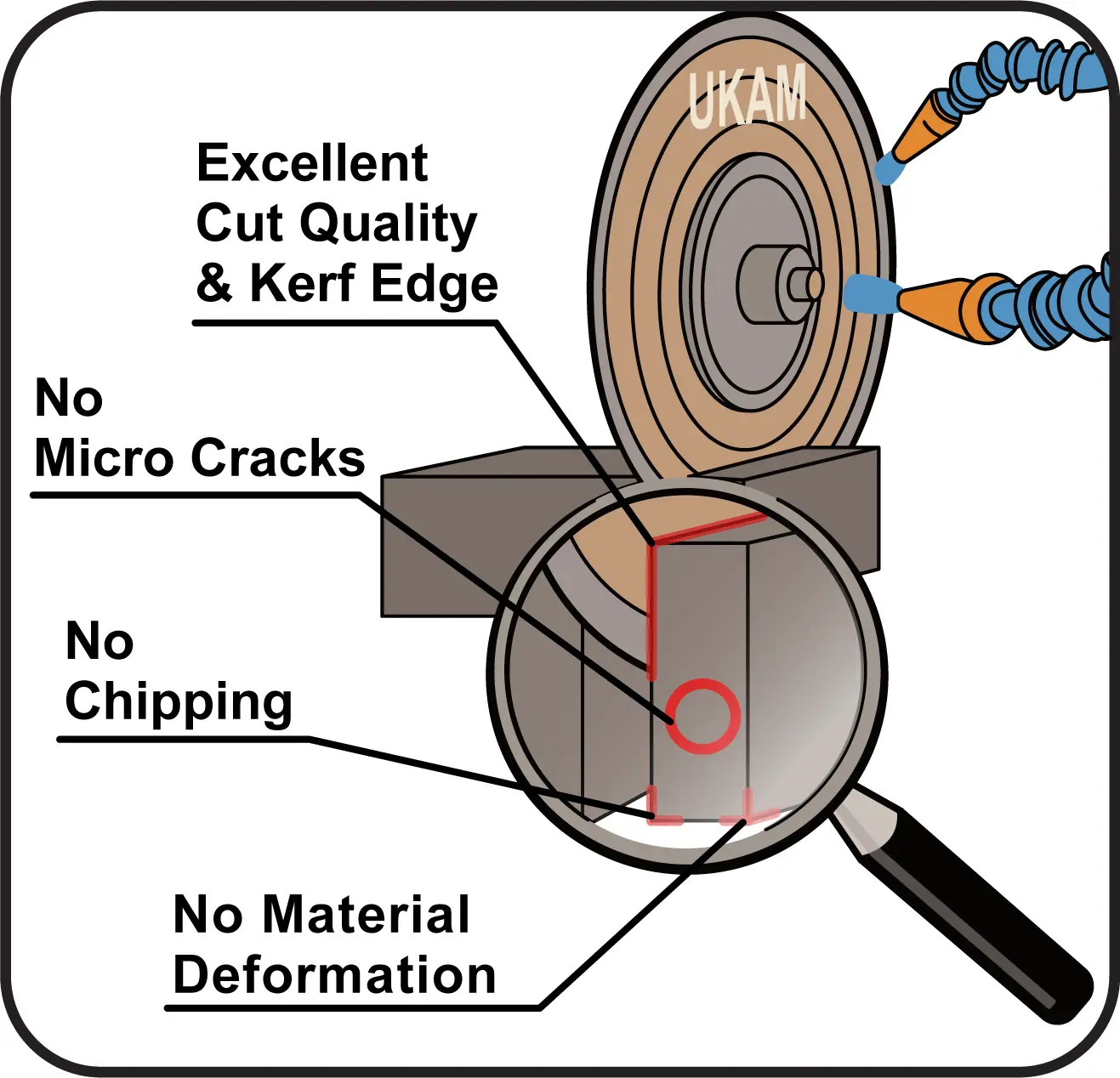
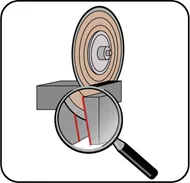
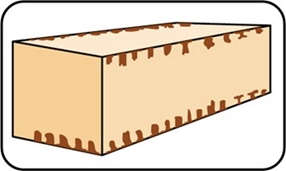
Cut Quality - Cut quality refers to the smoothness and precision of the cut surfaces, which should be free from irregularities and deformations. High-quality cuts are typically characterized by their cleanliness and the minimal finishing required post-cutting. Achieving optimal cut quality is essential for ensuring that the material meets the required specifications and performance standards.
Good cut quality is the absence of significant scratches, pits, or rough textures. The integrity of the material at the edges is maintained, minimizing chips and cracks. This is crucial for materials prone to fracturing or delaminating. Additionally, the dimensions of the cut should closely match the specified measurements to ensure that the component fits into its intended design without further modification. High Quality quality diamond & cbn blades and cutting processes should also not cause significant thermal damage to the work material, which can alter its properties and structural integrity.
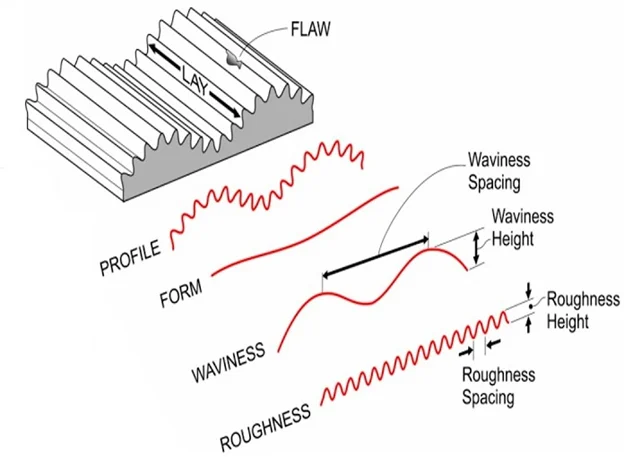
Chipping - Chipping during the cutting process with diamond and cubic boron nitride (CBN) cut-off blades is a significant concern, as it directly impacts the integrity and dimensions of the final product. This phenomenon occurs when small fragments of material break away from the material during cutting, potentially leading to defects and diminished performance. The issue is especially critical in applications requiring high precision and aesthetic quality, where even minor imperfections can render a component unsuitable for use.
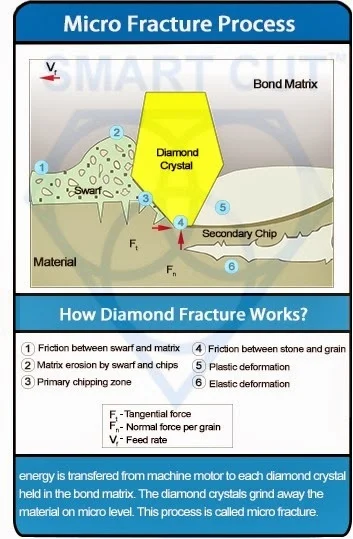
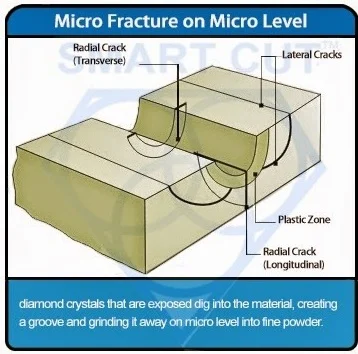
The occurrence of chipping is primarily influenced by the interaction between the blade and the material at a microscopic level. As the blade makes contact with the material, it may induce micro-cracks that can propagate through the material under the stress of cutting, leading to the detachment of small chips. This is more pronounced in materials that are inherently brittle or have low fracture toughness, such as ceramics, glass, and some hard metals.
Chipping not only affects the quality of the cut but also contributes to material waste. In industries like electronics, aerospace, and precision engineering, where the dimensions and integrity of components are crucial, chipping can compromise the functionality of the entire system. For instance, in semiconductor manufacturing, even microscopic chips can affect the performance of a chip or lead to failure during service.
Factors Influencing Cut Quality and Chipping
Blade Design and Maintenance
-
Exposed Diamond Crystals: Blades with exposed diamond crystals tend to cause less chipping and usually produce better cut quality with minimal chipping.
-
Regular Maintenance and Dressing: Keeping the blade sharp and effective through regular maintenance and dressing is vital for maintaining high cut quality.
-
Diamond Specifications: The type of diamond used, its size, concentration, and the bond hardness are significant factors. Finer diamond sizes generally provide higher cut quality with minimal chipping.
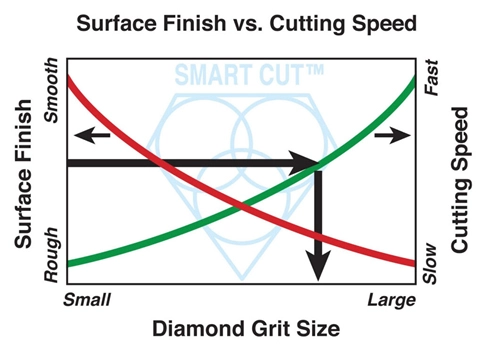
Cutting Speed - The speed at which the blade cuts through the material impacts both chipping and overall cut quality. Cutting too fast may lead to increased chipping, while cutting too slowly can cause unwanted friction and potential burn marks on the material. Different materials react differently; hard, brittle materials are more prone to chipping and require blades designed to handle such challenges.
Cooling and Lubrication - Proper cooling and lubrication are essential for reducing thermal stress on both the material and the cutting blade. This minimizes thermal expansion, which can lead to chipping and cracks. Coolants help remove debris from the cut, maintaining a clear path for the blade and improving overall cut quality.
1. Surface Roughness (Ra)
Surface roughness (Ra) is a common parameter used to quantify the smoothness of a surface. It is typically measured in micrometers (um) and can be calculated as the average deviation of the surface profile from the mean line over a specified length.
Ra = (1/L) ∫ y(x)dx
Where:
-
L is the length of the surface profile measurement.
-
y(x) is the vertical deviation of the surface from the mean line at position x.
2. Maximum Roughness Depth (Rz)
Maximum roughness depth (Rz) is another parameter used to measure the roughness of a surface. It is defined as the average height difference between the five highest peaks and the five deepest valleys over the evaluation length.
where

-
Pi are the heights of the five highest peaks.
-
Vi are the depths of the five deepest valleys.
Find out More: How to measure surface finish roughness >>>
3. Chipping Level (C)
Chipping level can be assessed by measuring the number and size of chips along the cut edge. One approach to quantifying chipping level is to use a chip density metric, which can be expressed as the total chipped area divided by the length of the cut.
Chipping Level (C) = Total Chipped Area / Length of Cut
Where:
-
Total Chipped Area is the sum of the areas of all chips along the cut edge.
-
Length of Cut is the total length of the cut edge.
Example Calculation for Surface Finish and Chipping Level
Let's consider a practical example where you need to calculate the surface roughness (Ra) and chipping level (C) for a Diamond or CBN cutting blade.
1. Surface Roughness (Ra):
-
Assume the surface profile length L is 10 mm.
-
Vertical deviations y(x) at different positions are recorded.
-
Calculate the average absolute deviation from the mean line.
If the recorded deviations are [0.2, 0.3, 0.1, 0.4, 0.2] µm, the Ra can be calculated as:
Ra = (0.2 + 0.3 + 0.1 + 0.4 + 0.2) / 10 = 1.2 / 10 = 0.12 µm
2. Chipping Level (C):
-
Assume the total chipped area is measured as 0.5 mm².
-
The length of the cut is 50 mm.
The chipping level can be calculated as:
Chipping Level (C) = 0.5 mm² / 50 mm = 0.01 mm
Example of Cut Quality and Chipping Measurements
Measurements for Each Blade – Table of Comparison (Resin Bond Diamond Cut off Blades)
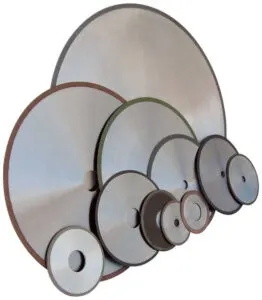
Blade |
Diameter (mm) |
Bond Type |
Diamond Grit Size |
Diamond Concentration (%) |
Surface Roughness Measurements (µm) |
Average Surface Roughness (Ra) (µm) |
Total Chipped Area (mm²) |
Length of Cut (mm) |
Chipping Level (C) (mm) |
---|---|---|---|---|---|---|---|---|---|
Blade A |
150 |
Resin |
120 |
100% |
[0.22, 0.25, 0.20, 0.24, 0.23] |
0.228 |
0.4 |
50 |
0.008 |
Blade B |
150 |
Resin |
200 |
75% |
[0.18, 0.21, 0.19, 0.22, 0.20] |
0.2 |
0.3 |
50 |
0.006 |
Blade C |
150 |
Resin |
150 |
50% |
[0.26, 0.29, 0.25, 0.28,0.27] |
0.27 |
0.5 |
50 |
0.01 |
Blade D |
150 |
Resin |
100 |
125% |
[0.24, 0.27, 0.23, 0.26, 0.25] |
0.25 |
0.35 |
50 |
0.007 |
-
Total Chipped Area (mm²): 0.35
-
Length of Cut (mm): 50
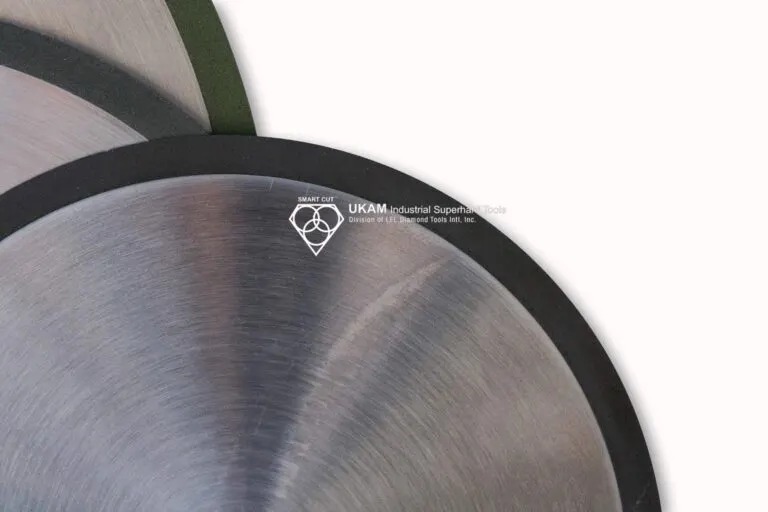
Average Surface Roughness
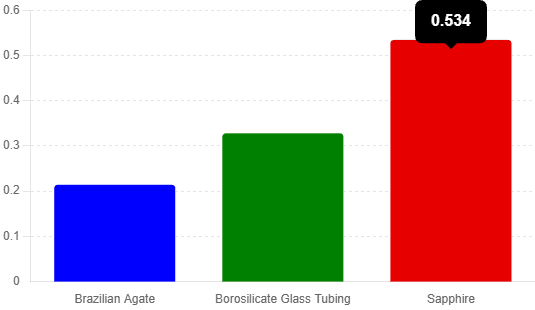
Chipping Level (C)
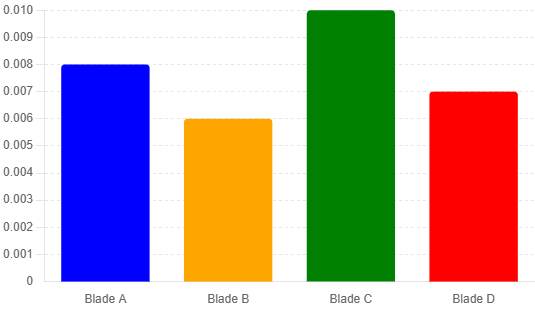
Blade Life for Diamond and CBN Cutting Blades
Blade life, in the context of diamond and CBN cutting blades, refers to the duration a blade can maintain its cutting effectiveness before requiring replacement. This metric is crucial as it directly impacts operational efficiency, cost of consumables, and overall productivity. A longer blade life translates to fewer blade replacements, reduced downtime, and lower costs associated with purchasing new blades and performing related maintenance.
Factors Influencing Blade Life
Quality of Raw Materials
-
Diamond Type and Quality: The type and quality of diamond used significantly affect blade life. High-quality diamonds are more durable and resistant to wear.
-
Diamond Grit Size: The size of the diamond grit influences the blade's cutting efficiency and longevity. Coarser grits may wear down faster, while finer grits can provide a longer blade life under appropriate conditions.
-
Diamond Concentration: Higher diamond concentration can enhance the blade's cutting performance and durability.
Blade Design
-
Core Material: The type of core material, whether steel or fully impregnated with diamond, impacts the blade's structural integrity and longevity.
-
Bond Type: The bond type, such as sintered, resin, or nickel bond, affects how well the diamonds are held in place and how the blade wears over time.
-
Diamond Depth/Height: Blades with greater diamond depth/height generally have a longer life as they contain more abrasive material.
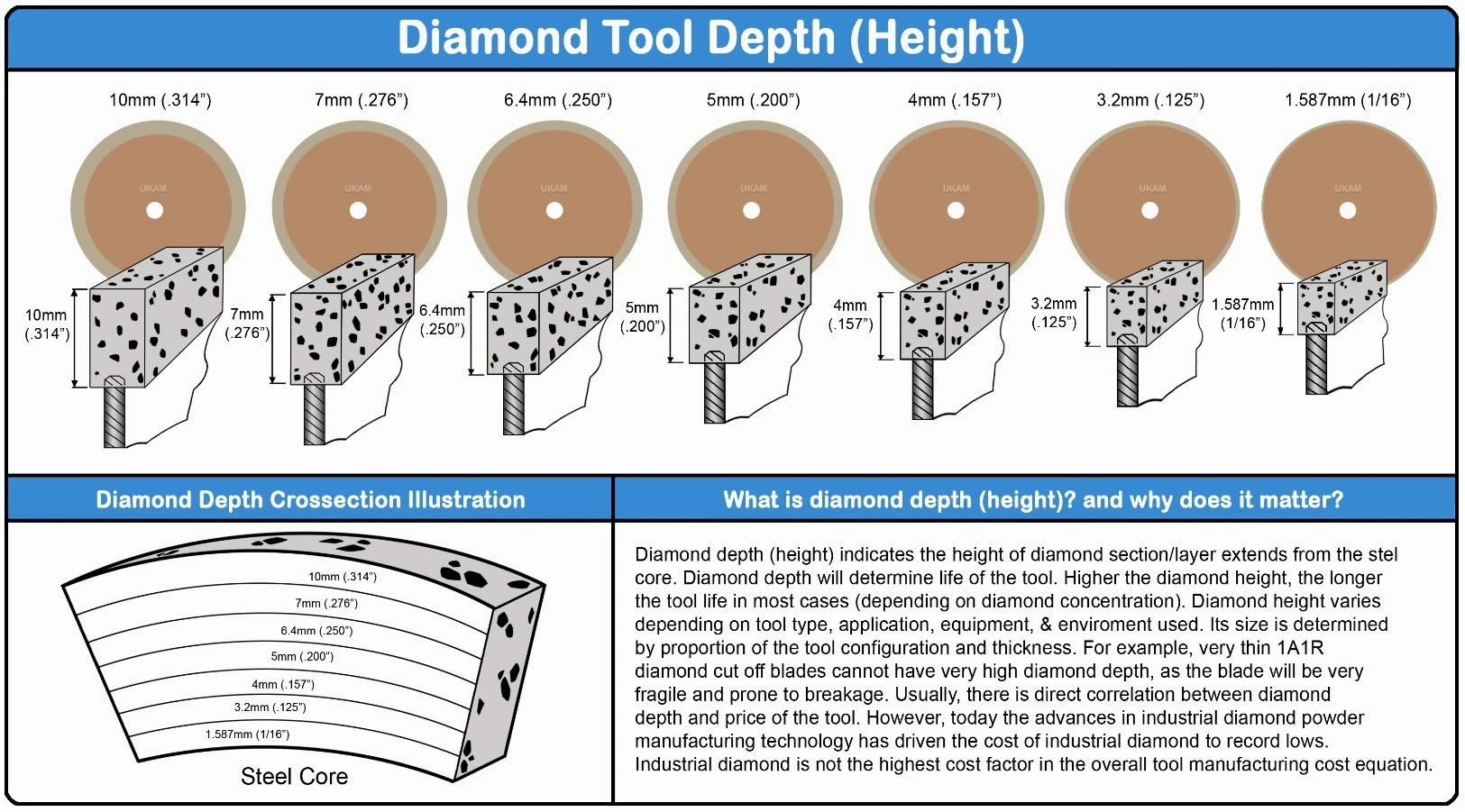
Operational Conditions
-
RPM and Feed Rates: The rotational speed and feed rate at which the blade operates can influence its wear. Optimal settings can maximize blade life.
-
Coolant Types: The type of coolant used helps in reducing heat and friction, thereby extending the blade's life.
-
Cutting Machine Type: The compatibility of the blade with the cutting machine and its settings is crucial for maximizing blade longevity.
Application-Specific Factors
-
Material Being Cut: The hardness and abrasiveness of the material being cut affect the rate of blade wear. Matching the right blade to the material is essential.
-
Cutting Equipment and Settings: Using the correct cutting equipment and settings tailored to the specific blade and material ensures optimal performance and extends blade life.
Improving Blade Life
High-quality diamond & cbn cutting blades are manufactured using higher quality materials, with higher diamond depth and concentration, manufactured using advanced technology and stringent quality control methods, tend to have longer lifespans. The design of the blade, including factors such as kerf thickness and bond matrix type, also contributes to its longevity.
-
Consistent High-Technology Manufacturing: Blades produced with advanced manufacturing techniques and rigorous quality control are more consistent in performance and durability.
-
Regular Maintenance and Proper Usage: Maintaining the blade and using it according to the recommended guidelines ensures that it performs efficiently for a longer period.
To calculate the blade life for Diamond and CBN cutting blades, you can use the following equation:
Blade Life = Total Cutting Distance / Wear Rate
Where:
-
Total Cutting Distance is the total length of material that the blade can cut before it becomes ineffective.
-
Wear Rate is the rate at which the blade wears down per unit of cutting distance.
Here's a more detailed breakdown of the equation components:
-
Total Cutting Distance: This is the cumulative length or amount of material that the blade can effectively cut over its lifespan.
-
Wear Rate: This is a measure of how quickly the blade material degrades or wears out during the cutting process. It is typically expressed in units such as millimeters of blade wear per meter of material cut.
Therefore, the equation can be expressed as:
Blade Life = Total Cutting Distance (meters) / Wear Rate (millimeters per meter)
Alternatively, if the blade life is expressed in terms of the number of cuts:
Blade Life (Number of Cuts) = Total Cutting Distance / Average Cutting Distance per Cut
Where:
-
Total Cutting Distance is as defined above.
-
Average Cutting Distance per Cut is the average length of material cut in each individual
Cost per Cut
Cost per cut is a vital performance metric that assesses the economic efficiency of a cutting blade over its lifespan. It involves calculating the total cost of using the blade, including its purchase price, maintenance expenses, and any associated operational costs, and then dividing this by the number of cuts the blade can make before it is deemed ineffective. This metric provides a clear picture of the overall value and cost-effectiveness of the blade in practical applications.
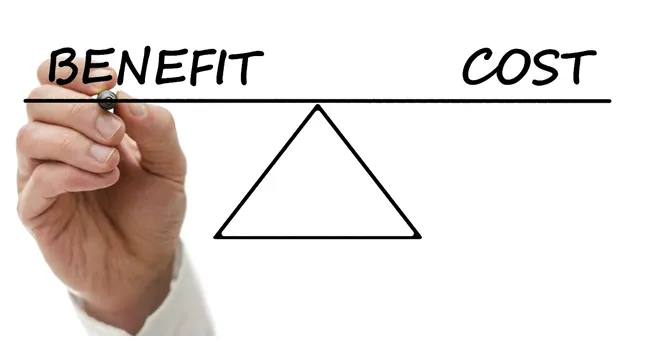
To fully understand the cost per cut, several factors must be considered. Firstly, the initial purchase price of the blade is a primary component. While some blades may have a higher upfront cost, they might offer longer life and superior performance, ultimately reducing the cost per cut. Conversely, cheaper blades might wear out quickly, leading to higher replacement costs and increased downtime, which can drive up the overall cost per cut.
Maintenance expenses also play a significant role. Regular maintenance, such as sharpening or dressing the blade, can prolong its life and maintain cutting efficiency. However, these activities come with costs that must be factored into the overall economic assessment. Blades that require frequent maintenance or special handling can have a higher cost per cut compared to those designed for longer periods of uninterrupted use.
Operational costs include factors such as energy consumption and labor. Efficient blades that cut faster and with less resistance may reduce energy usage and labor time, contributing to a lower cost per cut. Additionally, blades that minimize material wastage by producing cleaner cuts can add to the economic efficiency, as less material is lost during the cutting process.
Another critical aspect is the blade's lifespan, which is the number of effective cuts it can perform before needing replacement. Blades with a longer lifespan naturally have a lower cost per cut, as the initial and ongoing costs are spread over a greater number of cuts. This makes understanding the durability and wear characteristics of a blade essential when calculating its cost efficiency.
How to Calculate Cost Per Cut
To calculate the cost per cut for a Diamond or CBN blade, you can use the following equation:
Cost per Cut = Total Cost of Blade / Total Number of Cuts
Where:
-
Total Cost of Blade includes the purchase price, maintenance expenses, and any associated operational costs.
-
Total Number of Cuts is the total number of effective cuts the blade can make before it is deemed ineffective.
Here's a more detailed breakdown of the equation:
Total Cost of Blade = Purchase Price + Maintenance Expenses + Operational Costs
Therefore, the equation can be expanded to:
Cost per Cut = (Purchase Price + Maintenance Expenses + Operational Costs) / Total Number of Cuts
Example of Calculation:
Specification |
Blade A (Brazilian Agate) |
Blade B (Borosilicate Glass Tubing) |
Blade C (Sapphire) |
---|---|---|---|
Blade Diameter |
8” (200mm) |
8” (200mm) |
8” (200mm) |
Bond Type |
Sintered (Metal Bond) |
Sintered (Metal Bond) |
Sintered (Metal Bond) |
Kerf Thickness |
.040” (1.0mm) |
.040” (1.0mm) |
.040” (1.0mm) |
Diamond Grit Size |
Coarse |
Fine |
Medium |
Concentration |
Low |
High |
High |
Cutting Speed |
2000 RPM |
1500 RPM |
1200 RPM |
Coolant Used |
Water soluble coolant |
Water soluble coolant |
Oil-based coolant |
Purchase Price |
$64.00 |
$175.00 |
$194.00 |
Maintenance Expenses |
$50 |
$40 |
$60 |
Operational Costs |
$100 |
$80 |
$120 |
Total Number of Cuts |
1000 |
900 |
700 |
Cost per Cut |
$0.214 |
$0.3278 |
$0.5343 |
Cost Per Cut Calculation
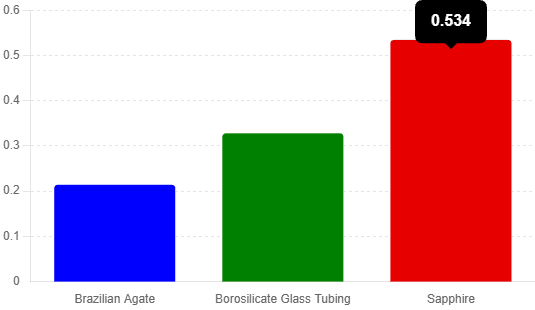
Diamond & CBN Cutting Blade Economics
"Diamond Cutting Economics" illustrates the relationship between the cutting rate of diamond blades and the various costs associated with the cutting process. Here's an explanation of the different components shown in the graph:
Cutting Rate (cm²/min): Displayed on the x-axis, this represents the speed at which the cutting process is carried out, measured in square centimeters per minute. The cutting rate is a crucial factor in production efficiency.
Cutting Cost ($/m²): Shown on the y-axis, this metric indicates the cost of cutting material per square meter. It combines all relevant costs into a single measure to assess the overall economic efficiency of the cutting operation.
Total Cost (Red Line): This curve shows the overall cost per unit area of material cut as the cutting rate increases. Initially, the total cost decreases as the cutting rate increases, due to more efficient use of resources (e.g., labor and overhead are spread over more units of output). However, beyond a certain point, the cost begins to increase, possibly due to factors like accelerated blade wear or the need for more frequent blade replacements.
Minimum Cost (Dotted Line): This line marks the optimal point where the total cost per unit area reaches its minimum. It represents the most cost-effective cutting rate, balancing speed and cost efficiency. The graph indicates that this optimal point occurs at a cutting rate of around 1500 cm²/min.
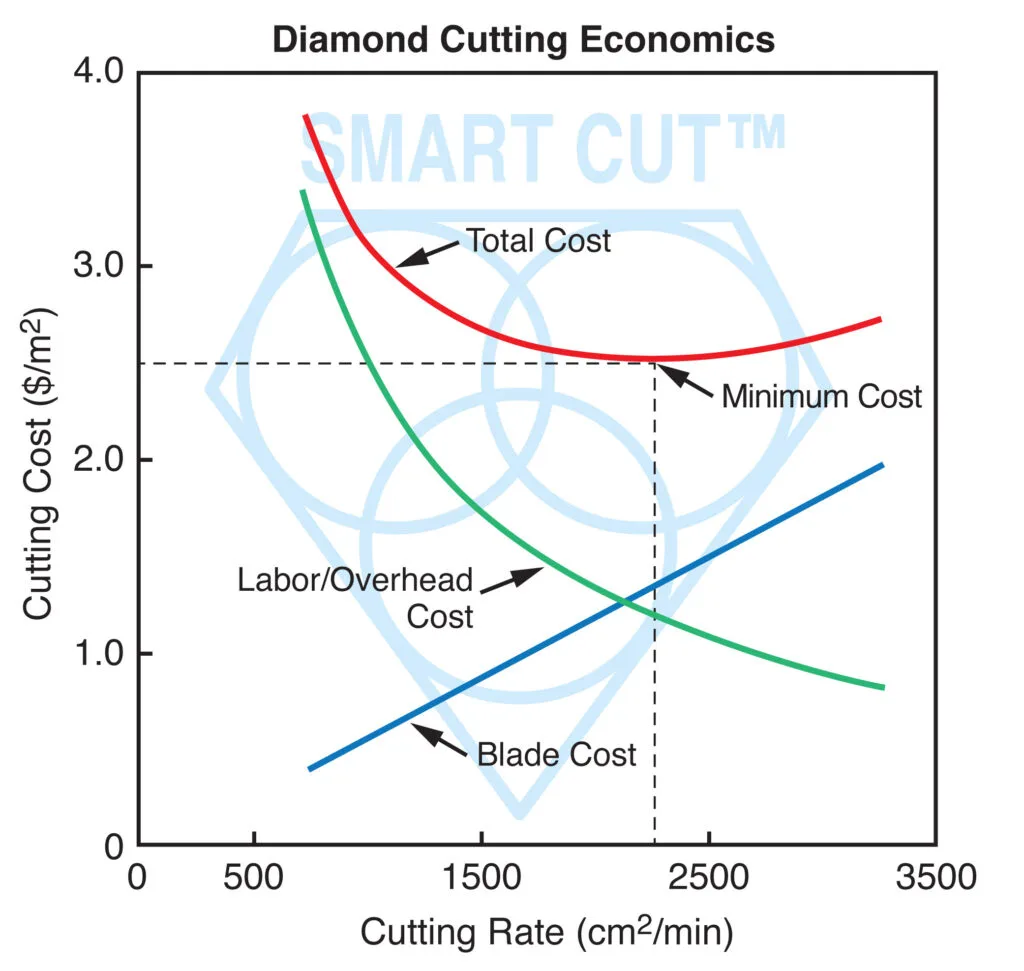
Labor/Overhead Cost (Light Blue Lines): These curves represent the labor and overhead costs associated with the cutting process. As the cutting rate increases, these costs per unit area typically decrease because the fixed costs (like labor salaries and facility overheads) are amortized over a larger output. The graph shows multiple scenarios or calculations for labor and overhead, indicated by the multiple light blue lines, possibly under different assumptions or conditions.
Blade Cost (Green Line): This line illustrates how the cost of the blade per unit area decreases as the cutting rate increases, initially. However, after a certain rate, the cost starts to increase again, suggesting that at higher speeds, the blade may wear out faster.
Diamond & CBN Cutting Blade Cost Metrics
Blade |
Cutting Rate (cm²/min) |
Cutting Cost ($/m²) |
Total Cost (per unit area cut) |
Minimum Cost |
Labor/Overhead Cost |
Blade Cost |
---|---|---|---|---|---|---|
A |
High (2000 RPM) |
Low ($0.214) |
$214 (100 cuts × $0.214) |
Mid-range |
Low* |
Low* |
B |
Mid (1500 RPM) |
Mid ($0.3278) |
$295.02 (900 cuts × $0.3278) |
Optimal |
Mid* |
Mid* |
C |
Low (1200 RPM |
High ($0.5343) |
$374.01 (700 cuts × $0.5343) |
High |
High* |
High* |
Assumptions and Estimations:
Cutting Rate (cm²/min): The cutting rate in cm²/min would be influenced by the RPM and material type. Since higher RPM generally suggests a higher cutting rate, we could assume Blade A > Blade B > Blade C in terms of cutting rate.
Cutting Cost ($/m²): To convert cost per cut to cost per m², we would need to know the surface area cut per operation, which depends on the depth and width of the cut besides the material. Without specific data, we assume a direct relationship with the cost per cut.
Total Cost: Directly taken from your data on cost per cut as a proxy for total cost effectiveness per unit area. This is an assumption for visualization purposes.
Minimum Cost: The optimal point in cost efficiency per unit area. Since Blade B operates at 1500 RPM, close to the 1500 cm²/min optimal cutting rate identified, we could assume its operational parameters may align closest to the minimum cost.
Labor/Overhead Cost and Blade Cost: These would typically scale inversely with the number of cuts and cutting rate, spreading fixed costs over more output. Higher RPM might suggest lower per unit costs due to increased production rate, but exact figures require more detailed operational data.
Cost per Cut for Each Blade: This bar graph illustrates the cost per cut for each blade, showing that Blade C is the most expensive per cut, followed by Blade B and Blade A.
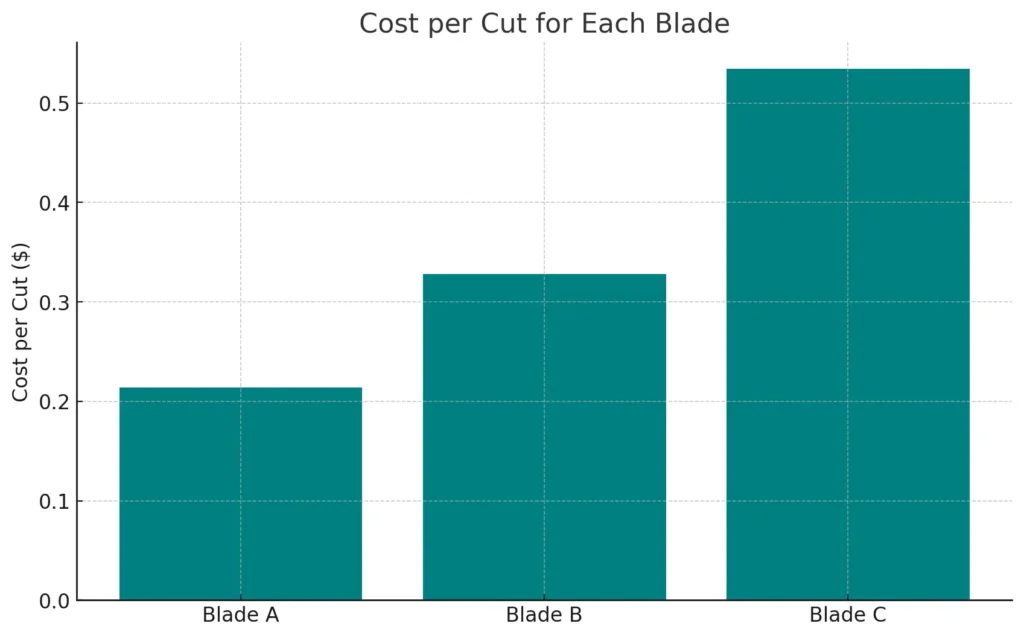
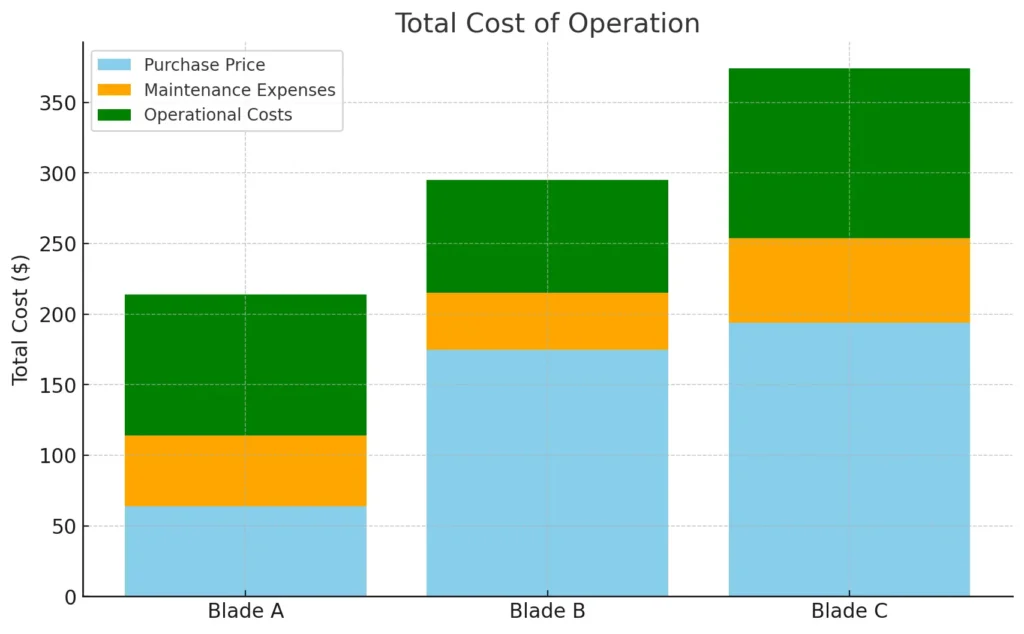
Total Cost of Operation: This stacked bar graph displays the total costs broken down into purchase price, maintenance expenses, and operational costs. Blade C has the highest total cost, reflecting its higher purchase and maintenance expenses.
Total Number of Cuts by Blade: The bar graph shows the total number of cuts achievable by each blade, with Blade A performing the most cuts.
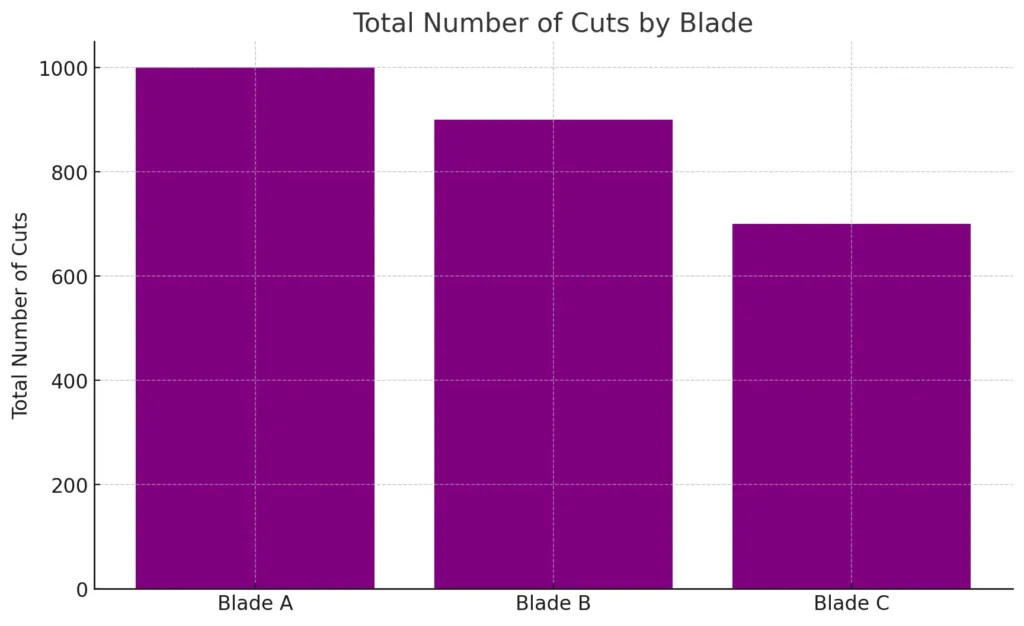
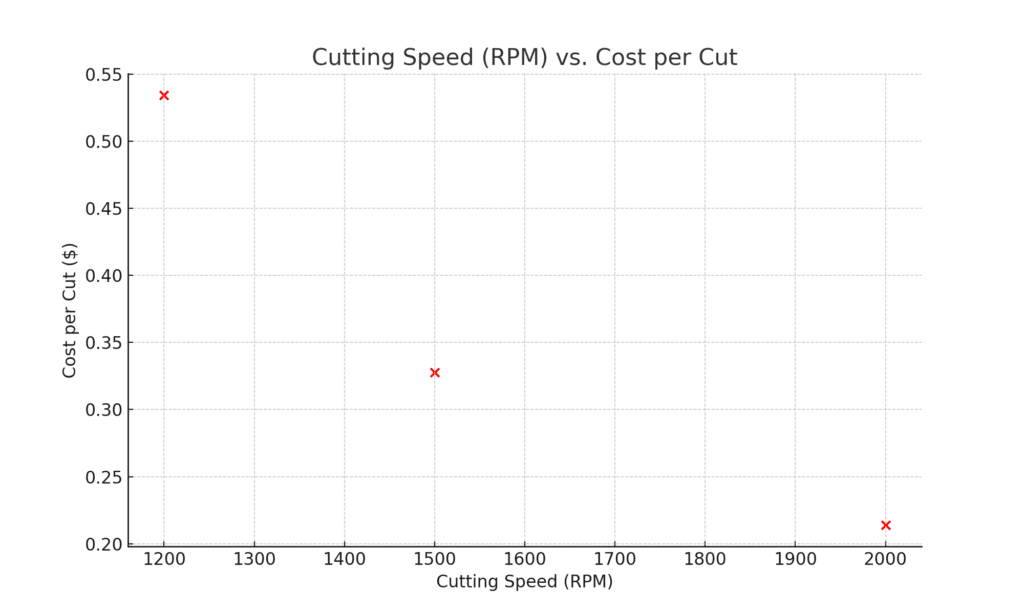
Cutting Speed (RPM) vs. Cost per Cut: The scatter plot correlates the cutting speed with the cost per cut for each blade, suggesting that higher speeds (Blade A) do not necessarily correspond to lower costs per cut.
Comparison of Cutting Cost Per Square Meter: This bar graph estimates the total cost effectiveness in cutting per square meter, calculated simply by multiplying the cost per cut by the total number of cuts.
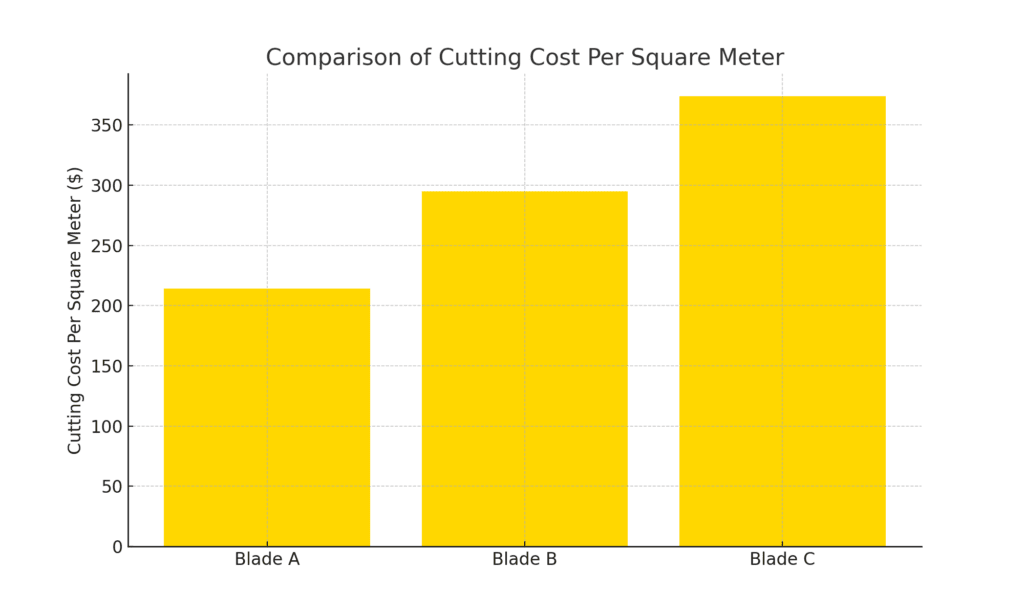
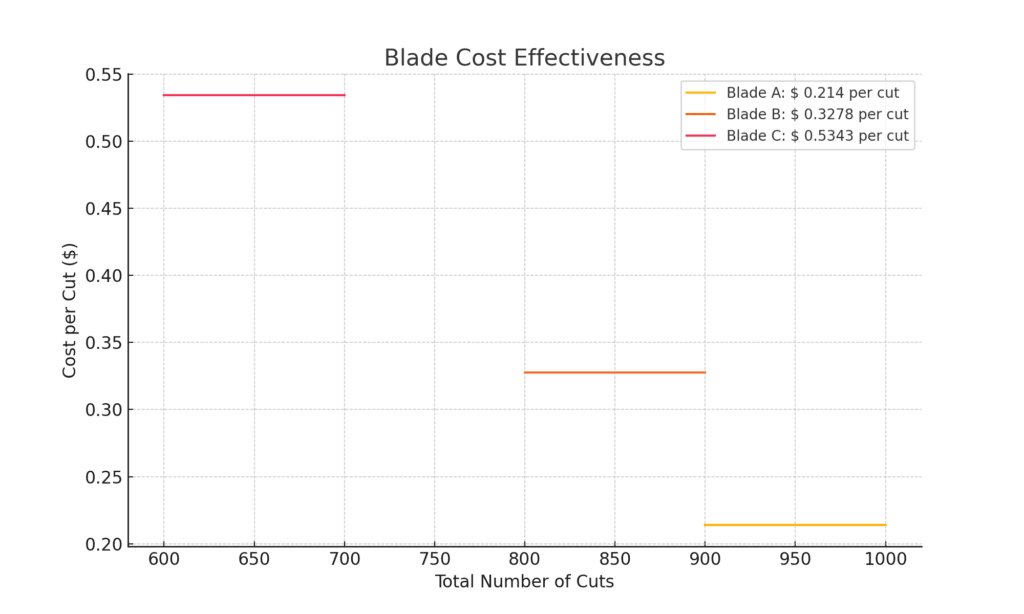
Blade Cost Effectiveness: The line graph plots the cost per cut against the total number of cuts, showing how the cost effectiveness varies across the blade lifecycle.
Consistency in Performance
Consistency is a fundamental performance metric for Diamond and CBN cutting blades, reflecting their ability to produce high-quality cuts consistently throughout their lifespan. This consistency is critical for maintaining operational efficiency and ensuring reliable results across different cutting operations. Inconsistent blade performance can lead to significant issues such as wasted material and unreliable results, especially in precision industries like electronics, optics, and advanced ceramics, where it can compromise the quality and functionality of the final product.
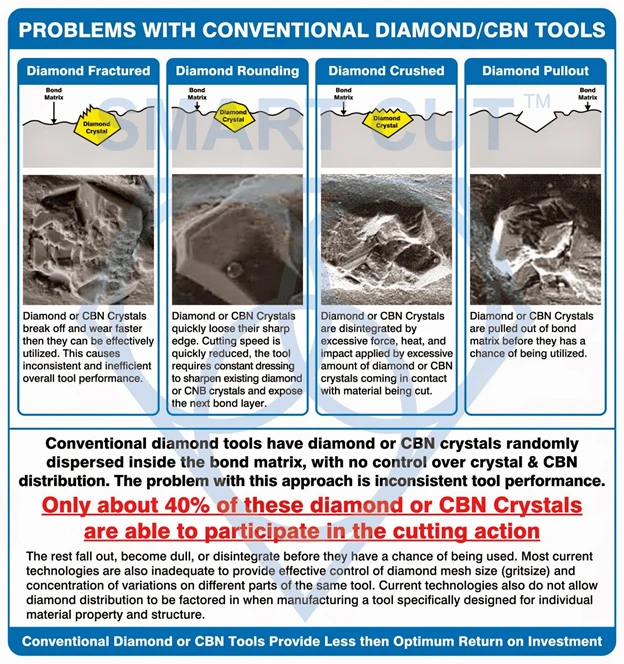
Consistent blade performance is essential for operational efficiency, reducing the need for frequent adjustments and calibrations, thus minimizing downtime and maximizing productivity. In high-volume cutting environments, this ensures that each cut meets the required specifications, reducing the likelihood of defective products and rework. Inconsistent blades can lead to increased costs due to material waste and higher labor costs for inspecting and correcting cuts. Consistent blades maintain uniform quality, optimizing material usage and labor efficiency.
A consistent blade contributes to process stability, crucial for maintaining production schedules and meeting delivery timelines. It ensures that subsequent processes, such as assembly, polishing, or inspection, can proceed without interruption. This stability is particularly important in industries with tight production timelines and high standards for quality control
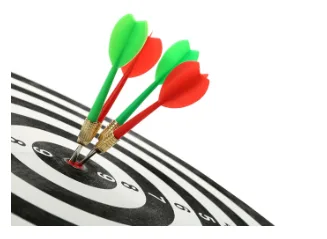
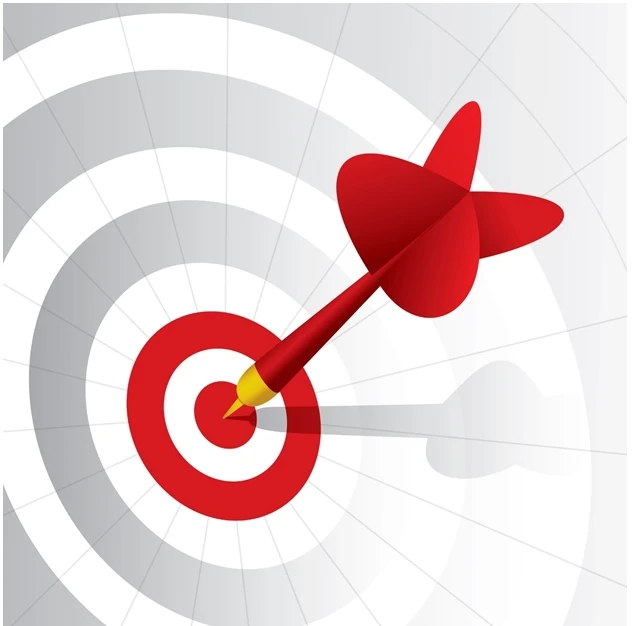
Measuring consistency involves regular monitoring and analysis of cutting performance over time, focusing on indicators like uniformity of cut dimensions, rate of blade wear, and frequency of defects or errors.
This involves examining the quality of the cuts for smoothness, straightness, and minimal chipping or rough edges. Consistent blades maintain these qualities throughout their lifespan, even with extended use.
Another indicator of consistency is the blades performance across various materials. For example, a consistent diamond & cbn blade should deliver similar results, whether cutting different types of materials or varying thicknesses. Monitoring how quickly a blade wears down can also reveal its consistency; a blade that maintains its shape and diamond crystal exposure is more consistent, while rapid or uneven wear suggests inconsistency.
The frequency of adjustments and maintenance can signal inconsistency. Blades that require frequent dressing, re-sharpening, or recalibration are often less consistent. Operator feedback is also helpful; experienced operators can detect changes in performance, like increased vibration or wobbly cuts, which may indicate inconsistency.
Using consistency testing tools, such as those that measure cut straightness and surface roughness, can provide more precise data on a diamond and cbn cutting blades performance. By combining these observations, you can determine if a blade is consistently delivering high-quality and repeatable results, which is crucial for reliable and consistent results. A consistent diamond and cbn blade leads to fewer operational disruptions, reduced waste, and ultimately, more efficient and cost-effective cutting processes.
There are many methods and calculations to measure diamond & cbn blade consistency. One popular method involves using consistency index show below:
Consistency Index (CI)
The Consistency Index can be calculated using the standard deviation of a set of measurements related to cut quality, such as cut width, depth, or surface roughness, over a series of cuts.
CI = (σ / μ) x 100
Where:
-
σ is the standard deviation of the measured cut quality parameter (e.g., cut width, depth, or surface roughness).
-
μ is the mean (average) of the measured cut quality parameter.
-
The result is multiplied by 100 to express the Consistency Index as a percentage.
Steps to Calculate Consistency Index:
1 Measure Cut Quality Parameters: Collect a set of measurements for a specific cut quality parameter (e.g., surface roughness or cut width) over a series of cuts. For example, measure the surface roughness (Ra) in micrometers (µm) for 10 consecutive cuts.
2. Calculate the Mean (μ):
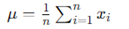
where n is the number of cuts and xi are the individual measurements.
2. Calculate the Standard Deviation (σ):

3. Compute the Consistency Index (CI):
CI = (σ / μ) x 100
A Consistency Index (CI) of 12.3% indicates that the variation in the surface roughness measurements is relatively low, suggesting that the blade produces consistent cuts.
Example Calculation
Let's assume we have measured the surface roughness (Ra) for 10 cuts with the following values in micrometers (µm): [0.12, 0.13, 0.11, 0.14, 0.13, 0.12, 0.15, 0.12, 0.11, 0.13].
1. Calculate the Mean (μ):
μ = (0.12 + 0.13 + 0.11 + 0.14 + 0.13 + 0.12 + 0.15 + 0.12 + 0.11 + 0.13) / 10 = 0.126 µm
2. Calculate the Standard Deviation (σ):
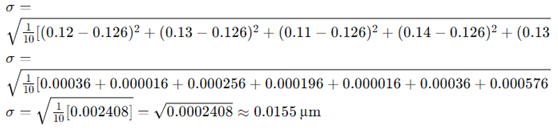
3. Compute the Consistency Index (CI):
CI = (0.0155 / 0.126) x 100 ≈ 12.3%
A Consistency Index (CI) of 12.3% indicates that the variation in the surface roughness measurements is relatively low, suggesting that the blade produces consistent cuts.
Example Showing the Calculation of Consistency Measurement Parameters
Table showing Different Consistency Measurement Parameters
Material Type |
Consistency Index (CI) |
Mean (μ) |
Standard Deviation (σ) |
Measurement Parameter |
Range of Measurements |
---|---|---|---|---|---|
Surface Roughness (Example Calculation) |
12.3% |
0.126 μm |
0.0155 μm |
Surface Roughness (Ra) |
0.11 - 0.15 μm |
Ceramics Cutting |
4.04% |
Data not provided |
Data not provided |
Surface Roughness |
0.210 - 0.240 μm |
Hardened Steel Cutting |
2.18% |
Data not provided |
Data not provided |
Cut Width |
0.440 - 0.470 mm |
Silicon Wafers Cutting |
20.42% |
Data not provided |
Data not provided |
Chipping Level |
2.0 - 3.0 chips/mm |
Composite Materials Cutting |
4.67% |
Data not provided |
Data not provided |
Surface Roughness |
0.1400 - 0.1600 μm |
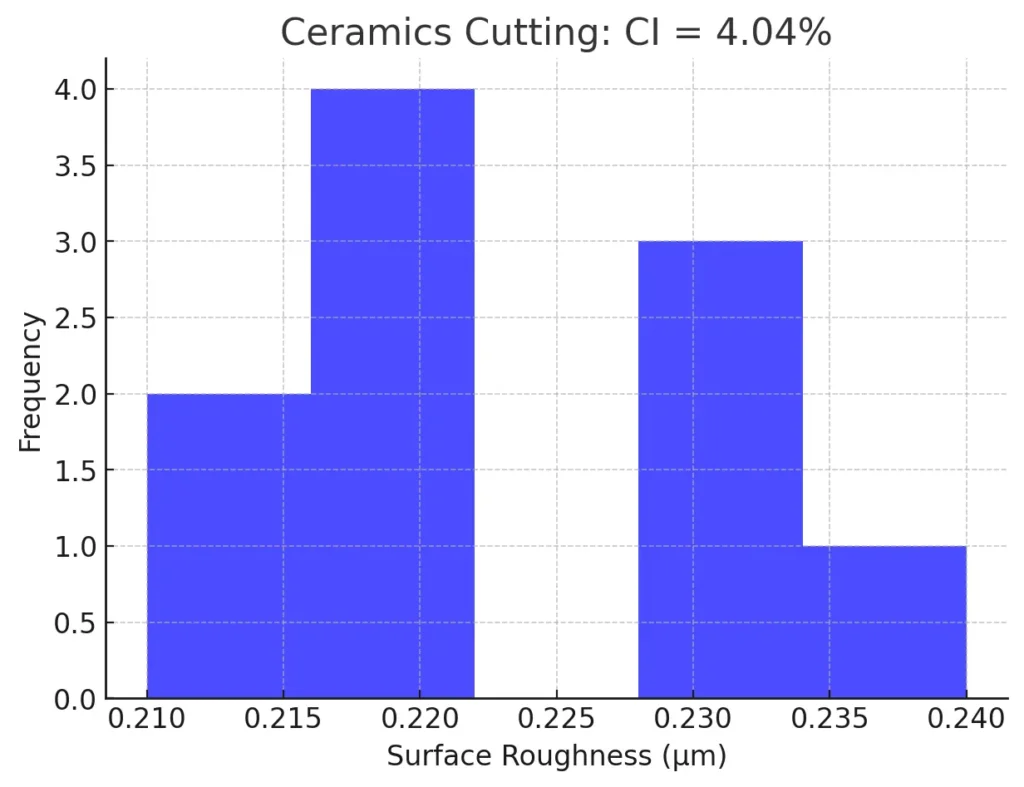
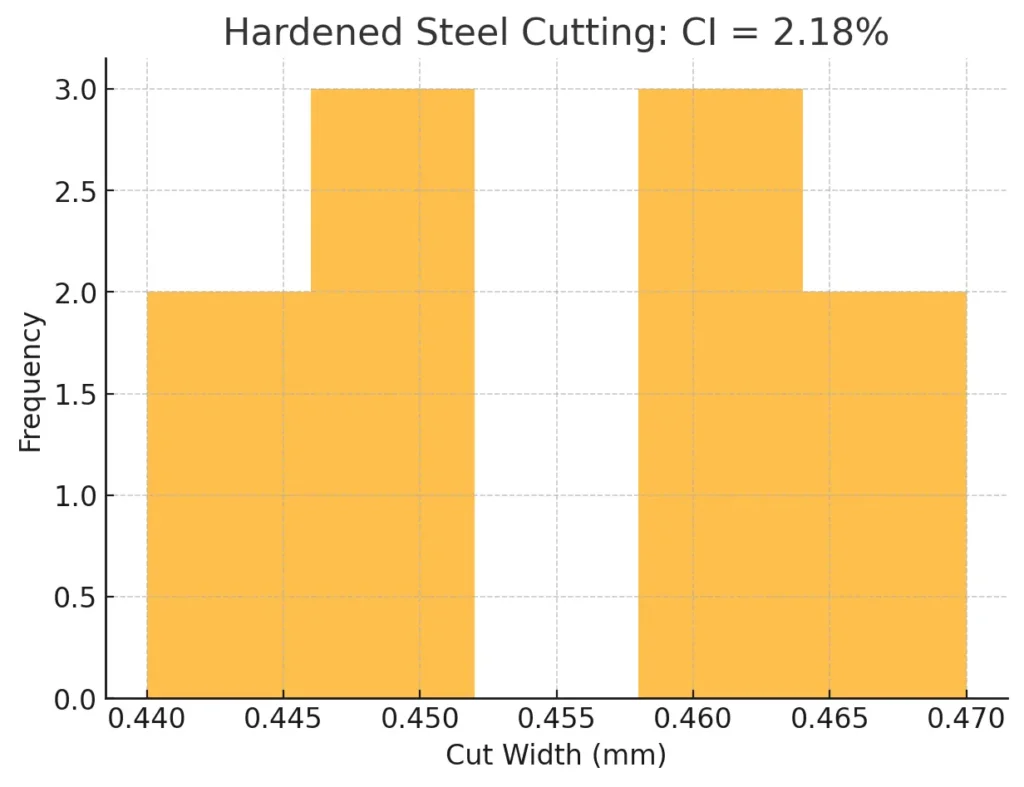
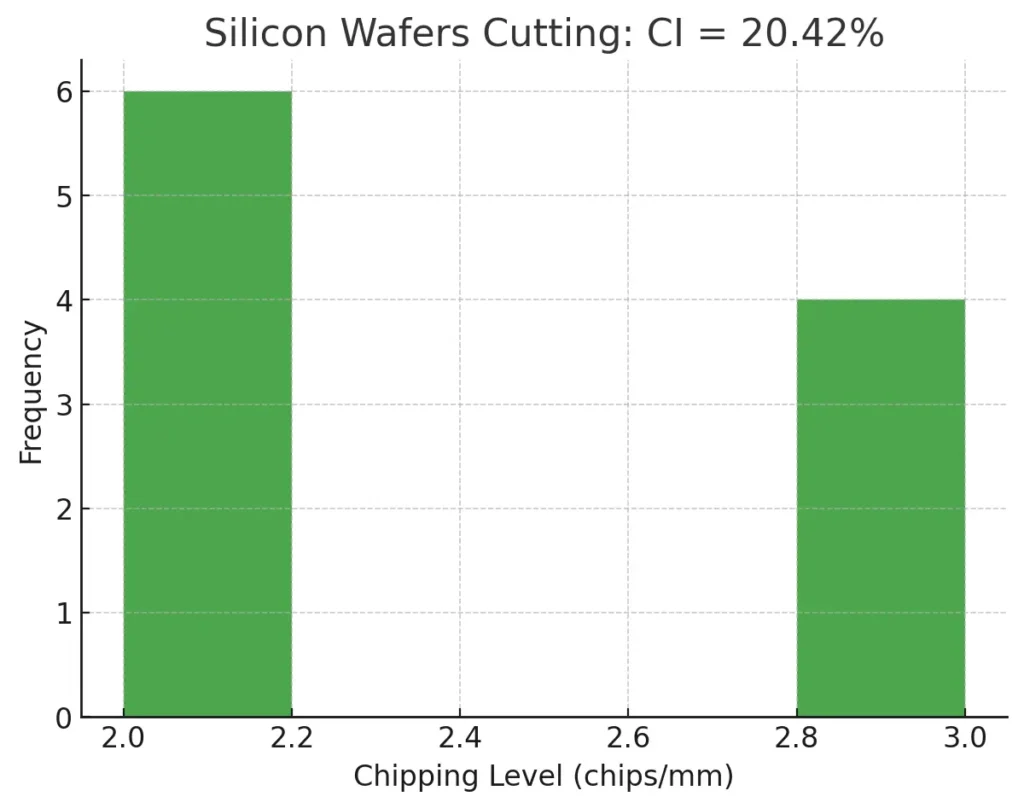
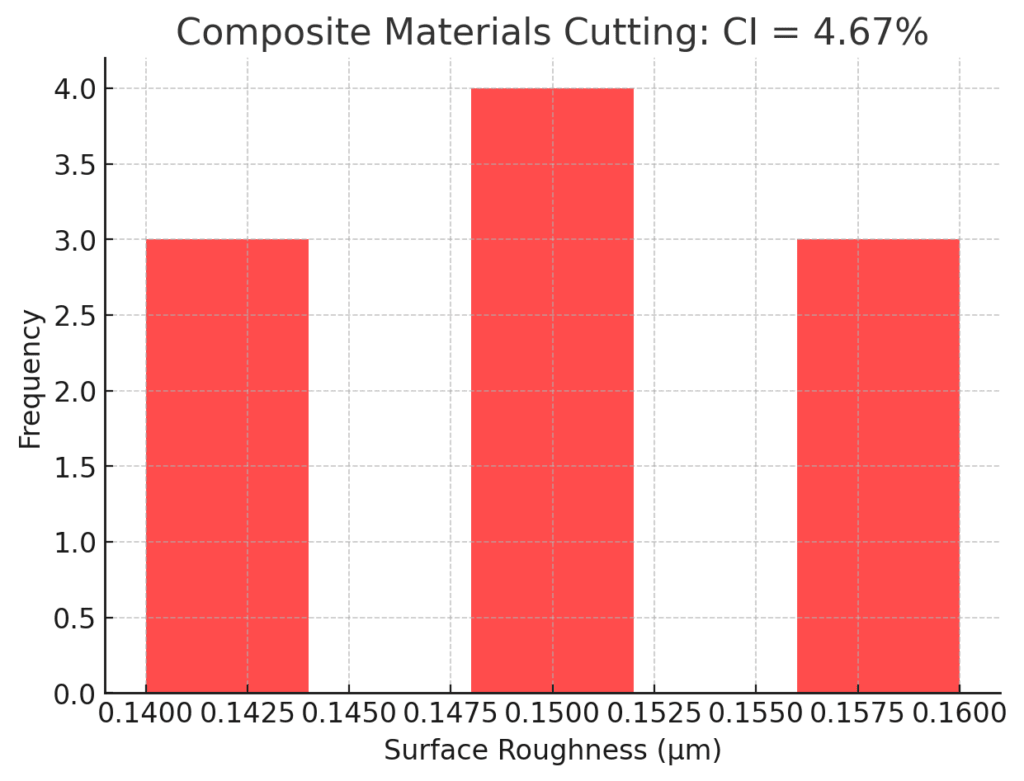
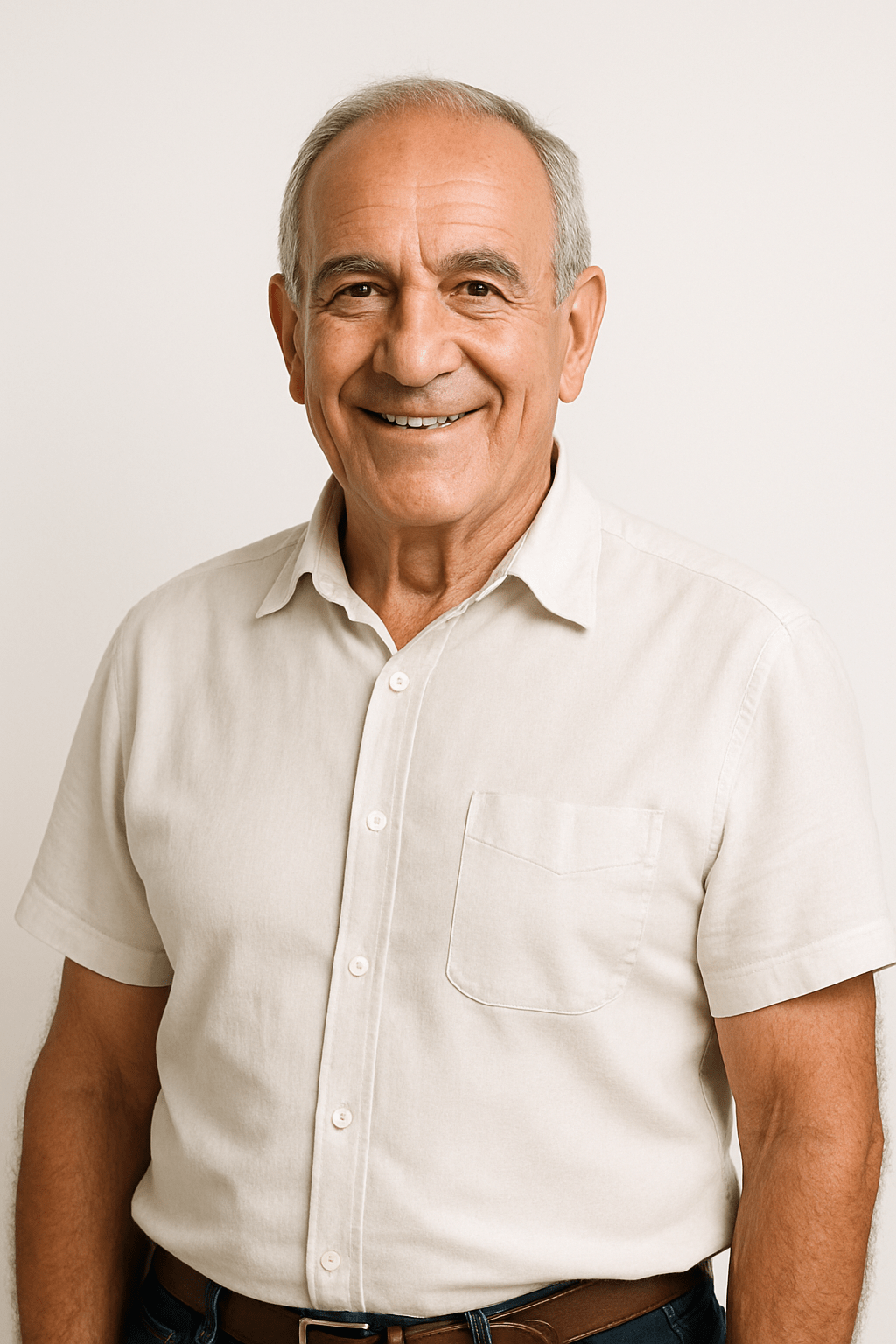
Leon Meyer is a veteran manufacturing engineer and technical consultant with over 50 years of experience in the development, implementation, and troubleshooting of industrial diamond tooling systems. Having spent his career at the intersection of tool design, precision manufacturing, and production engineering, Mr. Meyer is widely regarded as one of the most experienced voices in the application of ultra-thin diamond blades, sintered core drills, and CBN grinding wheels across heavy industry, advanced materials, and research sectors.
Known for his pragmatic, no-nonsense approach, Leon has advised manufacturers across the United States, Europe, and East Asia—helping streamline cutting processes, extend tool life, and solve complex issues related to material breakage, chipping, and tolerance drift. His expertise has directly contributed to improved production efficiency in industries ranging from aerospace alloys and technical ceramics to optics, composites, and high-nickel superalloys.
As an author, Mr. Meyer brings a lifetime of field knowledge to his writing, with a focus on real-world problem solving, cost-performance optimization, and tool reliability under demanding conditions.
ARE YOU USING RIGHT DIAMOND & CBN BLADES
FOR YOUR APPLICATION?
LET US
HELP YOU
HAVING ISSUES WITH
YOUR CURRENT DIAMOND & CBN BLADES?
Knowledge Center
Select right Diamond Blade for your application
How to Properly Use Precision Diamond & CBN Blades
Precision & Ultra Thin Diamond Blade Guide
How to Improve & Optimize Your Diamond Sawing Operation
Evaluating & Comparing Diamond Blades
Diamond & CBN Cutting Blade Performance Metrics that you Should Know
Total Cost of Ownership & Why its Important
Understanding Tradeoffs- Searching for Perfect Diamond & CBN Blade
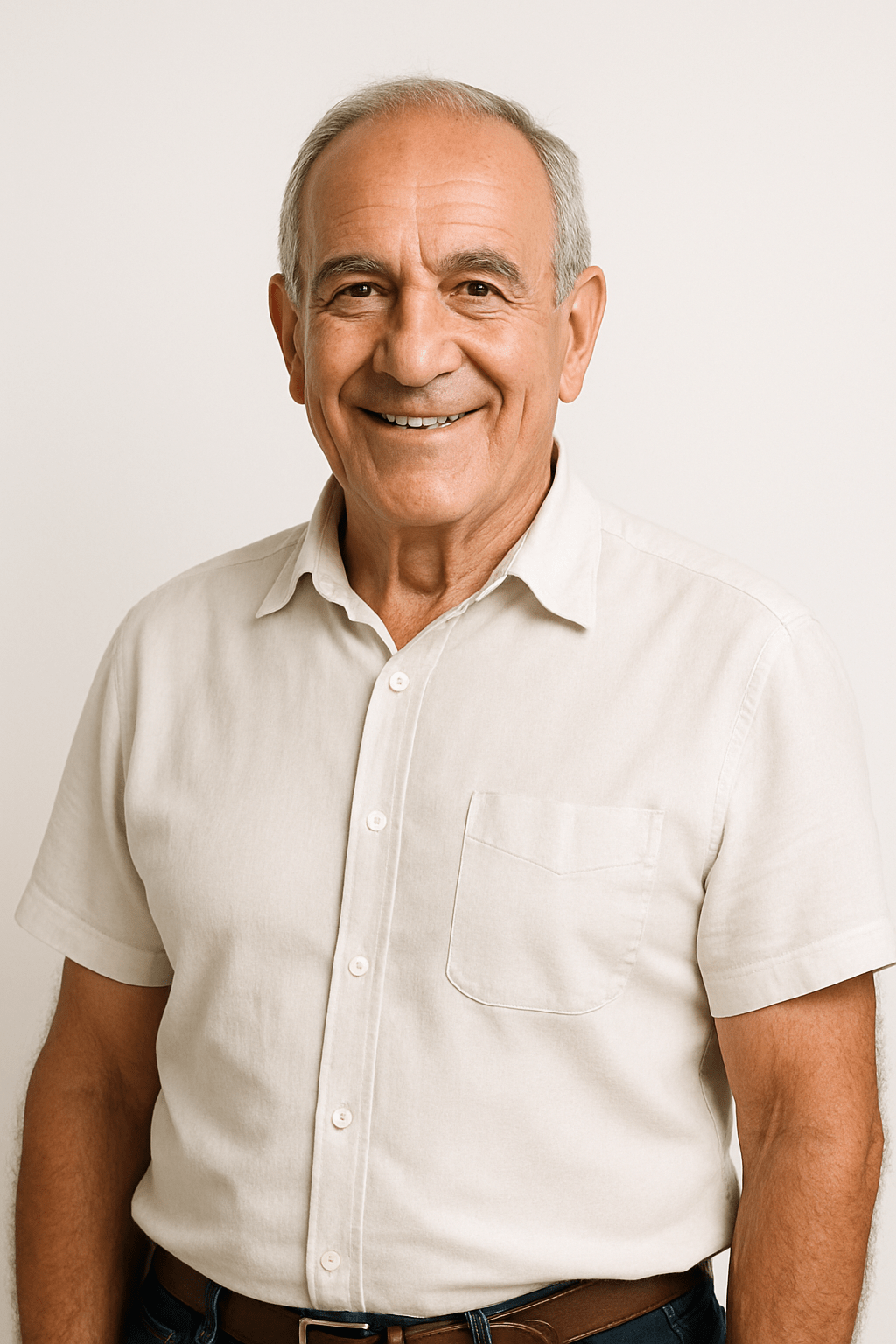
Leon Meyer is a veteran manufacturing engineer and technical consultant with over 50 years of experience in the development, implementation, and troubleshooting of industrial diamond tooling systems. Having spent his career at the intersection of tool design, precision manufacturing, and production engineering, Mr. Meyer is widely regarded as one of the most experienced voices in the application of ultra-thin diamond blades, sintered core drills, and CBN grinding wheels across heavy industry, advanced materials, and research sectors.
Known for his pragmatic, no-nonsense approach, Leon has advised manufacturers across the United States, Europe, and East Asia—helping streamline cutting processes, extend tool life, and solve complex issues related to material breakage, chipping, and tolerance drift. His expertise has directly contributed to improved production efficiency in industries ranging from aerospace alloys and technical ceramics to optics, composites, and high-nickel superalloys.
As an author, Mr. Meyer brings a lifetime of field knowledge to his writing, with a focus on real-world problem solving, cost-performance optimization, and tool reliability under demanding conditions.