Table of Contents
ToggleGetting the best results when using lapidary blades is not only skill but also about using the right blade for the application. When we talk about a good blade for lapidary application, we are really looking at how it cuts. The best blades cut through large range of lapidary materials ranging from hard as sapphire to soft as glass fast, easy, smoothly, and keep on doing it without needing too much upkeep such as dressing.
A good diamond lapidary blade leaves clues. But with so many blades out there, how do you choose the best one?
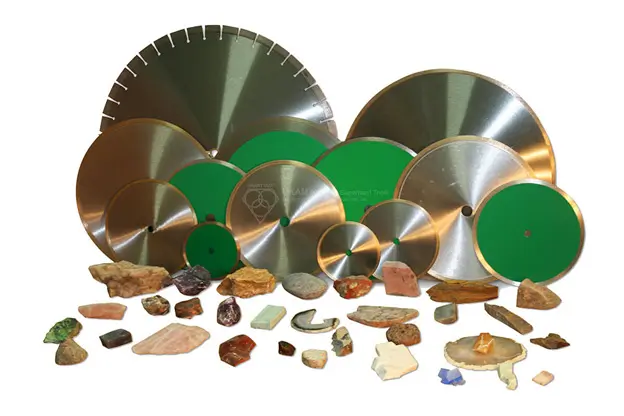
This article explores the critical attributes & performance metrics that set a high-quality diamond lapidary blade apart from the rest, focusing on visual, measurable, and audible criteria, as well as the tangible results these blades deliver.
When comparing diamond blades for cutting lapidary materials some of the main evaluation and comparison criteria involves: how fast it cuts, how smooth the cut is, how long the blade lasts, how often you need to dress the blade, and how consistent the cutting speed and cut quality.
Most Important variables in order of important for cutting lapidary materials
- Cutting Speed
- Surface Finish
- Blade Life
- Frequency of Dressing
- Consistency
Emphasis in determining a quality lapidary blade will be on both audible / sensory feedback and performance metrics
AUDIBLE & SENSORY FEEDBACK
-
cutting sound
-
vibration
PERFORMANCE METRICKS
-
straightness of the cut
-
required force
-
cutting speed
-
dressing frequency
-
heat dissipation
-
material compatibility
-
cut quality / chipping level
-
durability and longevity
-
wear resistance
-
consistency in performance
Audible and Sensory Feedback
Sounds and vibrations a blade emits during cutting provide invaluable real-time insights into its performance. This feedback helps operators immediately understand how well the blade is interacting with the material, allowing for adjustments on the fly to optimize the cut.
Cutting Sound
The sound a diamond lapidary blade makes during operation is an insightful gauge of its performance, providing real-time feedback that goes beyond mere noise. A superior blade is marked by its ability to operate consistently with a low-noise profile, indicating a smooth, uniform cut. This steady sound isn't just a sign of quality; it's a multifaceted diagnostic tool that operators can rely on to assess both the blade's condition and the effectiveness of the cutting process.
A consistent acoustic signature means that the blade is cutting as expected, without encountering any unforeseen issues. When the sound changes, becoming higher-pitched or fluctuating in volume, it often signals potential problems. These auditory cues might suggest anything from irregularities in the material being cut to uneven wear or damage to the blade itself. Understanding these nuances allows for adjustments on the fly, ensuring optimal cutting conditions and extending the blade's life.
Moreover, the interaction between the blade and different materials can lead to variations in the sound produced. Recognizing these variations can help operators tailor their approach to each material, improve efficiency and overall performance. Additionally, design innovations aimed at reducing vibration not only contribute to a blade's cutting stability but also minimize its noise output, creating a more comfortable and safer working environment.
Here are various sounds and what they might indicate about the blade's performance and condition when cutting different lapidary materials:
1. Consistent, Low Hum or Whirring
Indication: This sound typically indicates that the blade is in good condition and is cutting the material smoothly and efficiently. A consistent, low-level noise suggests that there are no significant obstacles or issues affecting the cutting process, and the blade is operating as expected.
2. High-Pitched Squealing or Screeching
Indication: A high-pitched noise can signal several potential issues. It might indicate that the blade is encountering a harder-than-expected area within the material, possibly due to variations in mineral composition. This sound can also suggest that the blade is dulling and struggling to cut through the material efficiently, or that the blade is not adequately lubricated.
3. Irregular, Fluctuating Sounds
Indication: Changes in the sound level or pattern, such as intermittent cutting sounds, might suggest irregularities in the material, such as cracks, voids, or inclusions. These irregularities can cause the blade to momentarily lose contact with the material or encounter varying resistance, leading to fluctuations in the sound.
4. Grinding or Gritty Sounds
Indication: A gritty or grinding noise may indicate that the blade is encountering abrasive materials within the gemstone, possibly wearing the blade unevenly. It could also suggest the presence of debris or foreign particles between the blade and the material, which could damage the blade or affect the quality of the cut.
5. Banging or Clunking
Indication: These sounds are less common but could occur if the blade momentarily binds in the cut or if there is a mechanical issue with the cutting equipment. Such sounds warrant immediate attention to prevent damage to both the blade and the material.
Each type of material has unique characteristics that can influence these sounds, helping you understand what's happening during the cutting process and adjust your techniques accordingly.
For hard stones like quartz, sapphire, or ruby, a consistent low hum indicates a smooth cut. If you start hearing high-pitched squealing, it could mean the blade is struggling, possibly due to the material's hardness or a dull blade. Ensuring the blade is designed for these hard gemstones can mitigate this issue.
On the other hand, softer stones like opal may produce irregular, fluctuating sounds due to varied hardness within the stone itself. This isn't always cause for concern but does necessitate a gentle cutting approach. A grinding sound in these cases might reveal the presence of sand or other abrasives, indicating the need for extra caution.
Porous stones such as turquoise might exhibit a steady hum with occasional fluctuations, reflecting transitions between areas of different hardness. This variability requires careful attention to avoid damaging the material.
Materials like agate and jasper, known for their uniformity, should produce a consistent sound during cutting. A deviation from this consistency, especially a high-pitched squeal, could signal a mismatch between the blade and the material's density or a need for additional cooling lubricant to reduce friction.
Emeralds and other stones with known inclusions present a unique challenge, as hitting an inclusion can change the sound unexpectedly. These fluctuations serve as a warning to proceed with care to prevent damage to both the stone and the blade.
Vibration
When using a diamond lapidary blade, the sensation of vibration under your fingertips is more than just feedback—it's a direct line to understanding the blade's performance and potential issues. Ideally, this vibration should be barely noticeable, ensuring that the blade is cutting smoothly and accurately. Excessive vibration, however, is a telltale sign of problems that could range from blade misalignment to uneven wear, each impacting the blade's ability to deliver a precise cut. It's an aspect that intertwines closely with the user's comfort, the blade's condition, and the overall safety of the cutting operation.
In the world of precision cutting, the quest to minimize vibration begins at the manufacturing stage. Precision is key, from ensuring the diamonds are uniformly distributed within the bond matrix to balancing the blade to eliminate uneven rotation. These manufacturing details are crucial for a blade's performance, affecting not only its cutting efficiency but also how it feels in use.
But the responsibility doesn't rest solely on manufacturing. Regular maintenance and careful inspection of both the blade and cutting equipment play pivotal roles in keeping vibration to a minimum. Keeping an eye out for wear, ensuring the blade is correctly mounted, and maintaining the equipment in top condition can all contribute to a smoother cutting experience.
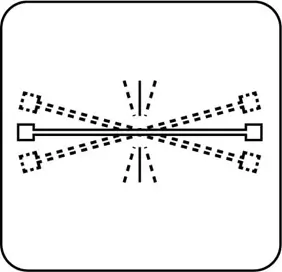
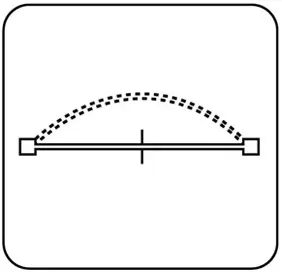
Performance Metrics
Performance Metrics for a superior lapidary blade include: straightness of the cut, the minimal force required for operation, the efficiency of cutting speed, frequency of dressing, exceptional heat dissipation, unparalleled material compatibility, superior cut quality with minimal chipping, outstanding durability and longevity, and robust wear resistance. Lets examine each one in more detail
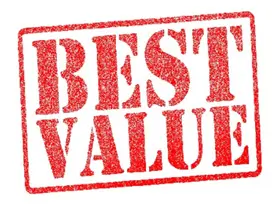
Straightness of the Cut
Measuring the straightness of the cut provides insight into the blade's accuracy. A high-quality blade produces very straight cuts, indicative of its precision and the even distribution of diamond particles.
The straightness of the cut is a critical metric for evaluating the performance of a diamond lapidary blade, serving as a clear indicator of its precision and the quality of its construction. When a blade achieves a perfectly straight cut, it's a testament not only to the precision engineering behind its design but also to the meticulous attention to detail in the distribution of diamond particles within the matrix. Expanding on this concept reveals the multi-dimensional aspects of what makes a blade perform at such an optimal level.
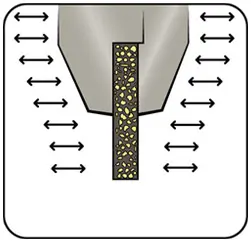
The foundation of a blade's ability to produce straight cuts lies in the precision engineering of the blade itself. This encompasses everything from the geometric accuracy of the blade's design to the quality of materials used in its construction. High-quality blades are designed with an emphasis on symmetry and balance, ensuring that each rotation of the blade moves through the material with minimal deviation.
An even distribution of diamond particles across the blade's surface is crucial for maintaining a consistent cutting edge. Variations in diamond distribution can lead to uneven wear on the blade, which in turn can cause the blade to veer off course during a cut. Manufacturers of high-quality Diamond Blades employ advanced techniques to embed diamond particles uniformly, ensuring that the blade maintains its cutting path with precision.
The stiffness of the blade also plays a significant role in its ability to cut straight lines. A blade that is too flexible may bend or warp under pressure, leading to curved or uneven cuts. Conversely, a blade engineered for optimal stiffness will resist bending forces, maintaining a straight cutting path even under stress. Additionally, effective vibration control mechanisms are integral to preventing deviations, as excessive vibration can also lead to inaccuracies in the cut.
Required Force
The amount of force required to penetrate material during cutting operations is a crucial determinant of a diamond lapidary blade's efficiency. Superior blades are engineered to cut through materials with minimal force, a feature that underscores their advanced design and the quality of materials used in their construction. This efficiency not only enhances the user experience but also has significant implications for the overall cutting process. Delving deeper into this aspect reveals the nuanced benefits of using blades that are optimized for low-force cutting.
In lapidary work, cutting through precious gemstones and minerals with precision and care requires a deep understanding of how much force a diamond lapidary blade needs to apply. The hardness, structural characteristics, and even the potential inclusions within each type of lapidary material dictate the necessary force for cutting. The goal is always to optimize this force to enhance the cutting process, ensuring that the integrity of these valuable stones is preserved and that the lapidary artists can work safely and comfortably.
Superior lapidary blades are designed to adapt their cutting force to the unique requirements of each material. Hard gemstones like sapphires or rubies demand blades that can apply a slightly higher force without causing any damage, thanks to the blade's design and the quality of the diamonds it contains. Softer stones, such as opals or turquoises, need blades that can make clean cuts with minimal force to avoid any chipping or cracking. This precision in controlling the cutting force is crucial, especially when working with materials that are prone to cleavage, like emeralds. A blade that requires less force to cut reduces the stress on the stone, thereby lowering the chances of creating cracks or splits. This is particularly important for maximizing the yield from each precious stone, considering their value and rarity.
The benefits of using blades that require less force extend beyond material preservation to include ergonomic advantages for the lapidary artist. High-force cutting can lead to increased physical strain and elevate the risk of accidents, including slippage or loss of control. Conversely, blades designed for efficient, low-force cutting minimize the physical demands on the operator. This not only lessens fatigue and reduces the risk of injuries but also allows for longer periods of focused, precise work. Such ergonomic considerations are crucial for maintaining high safety standards and ensuring the quality of the lapidary work.
Adapting the cutting force for different lapidary materials isn't just about the hardness of the materials but also involves understanding their internal structures and potential vulnerabilities. Advanced lapidary blades, part of systems with adjustable speed and feed rate controls, give operators the flexibility to tailor the cutting process to the specific needs of each material. This careful adjustment of force is vital for achieving clean cuts without compromising the material's integrity or the operator's safety.
Cutting Speed
The most universal standard would be how effective and consistently the blade removes the material being cut. This can be determined by measuring amount of material the blade is able to cut within certain amount of time without the need to dress the blade
A notable feature of exceptional blades is their ability to maintain high cutting speeds without bogging down, ensuring efficient and fast and freer cutting speed.
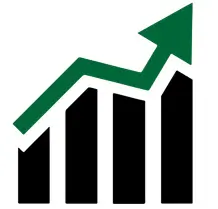
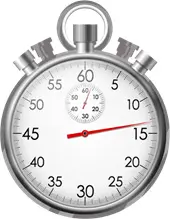
The cutting speed of a diamond lapidary blade is a critical attribute that directly impacts the efficiency and productivity of cutting operations. Exceptional blades stand out for their ability to maintain high cutting speeds, slicing through materials swiftly without bogging down or losing momentum. This capability not only facilitates the quick completion of tasks but also reflects the advanced engineering and superior material quality of the blade. Delving further into this feature reveals several key aspects that contribute to the high-performance standards of these blades.
The core of fast and freer diamond lapidary cutting blade lies in its material composition. Using high-grade, synthetic diamonds that are not only incredibly hard but also exceptionally durable. These diamonds are embedded in a carefully formulated bond matrix that is designed to wear at a rate that continuously exposes sharp diamond edges. This design ensures that the blade remains efficient over time, capable of maintaining high cutting speeds even as it wears.
Optimized Diamond Grit and Distribution
The size of the diamond grit and its distribution across the blade play pivotal roles in determining cutting speed. Finely tuned to match the specific cutting application, the grit size affects how quickly and smoothly the blade can cut through material. A well-distributed diamond coating ensures consistent cutting ability across the blade's surface, preventing hot spots or uneven wear that could slow down the cutting process.
Blade Geometry and Diamond Edge Design
The physical design of the blade, including its geometry and diamond edge configuration, is optimized for speed. Narrower blades with specific segment designs can reduce resistance as they cut, allowing for faster movement through the material. Moreover, some blades have diamond edge with special cut-outs or slots that facilitate debris removal and cooling, further enhancing the blade's ability to cut quickly and efficiently.
Reduced Heat Generation
Maintaining high cutting speeds is also a matter of managing heat buildup. Excessive heat can slow down the cutting process, damage the material being cut, and wear down the blade itself. Exceptional blades are designed to dissipate heat effectively, often through integrated cooling technologies or materials within the blade that conduct heat away from the cutting zone. This heat management ensures that the blade can sustain high speeds without adverse effects on its performance or lifespan.
Dressing Frequency
The frequency with which a diamond lapidary blade requires dressing is a subtle yet profound indicator of its overall quality and durability. Dressing, the process designed to refresh the blade's cutting surface by removing worn material and exposing new diamond crystals, is essential for maintaining optimal cutting performance.
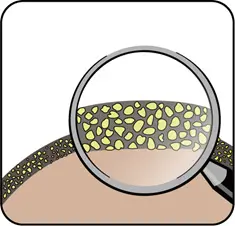
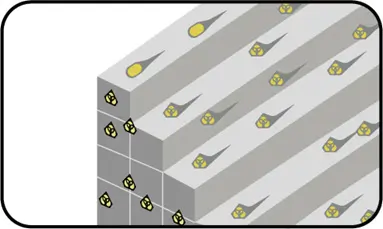
High-Quality Diamond Crystals
The quality of the diamond grit used in a blade directly affects its longevity and performance. Superior blades utilize high-quality, synthetic diamonds with properties tailored for durability and consistent performance. These diamonds are less prone to fracturing and pulling out from the bond, ensuring that the blade remains sharp and effective for longer periods, thus reducing the need for frequent dressing.
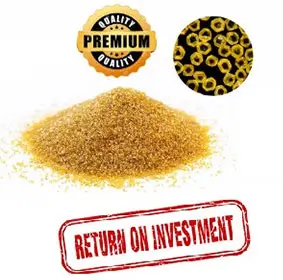
However, the need for frequent dressing can signal a blade's premature wear, reflecting on the bonding matrix's quality and the durability of the diamond grit. Superior blades distinguish themselves by demanding less frequent dressing, a characteristic that speaks volumes about the craftsmanship and technology behind them. Expanding on this, there are several critical elements that contribute to reducing the need for dressing and enhancing a blade's longevity.
Advanced Bond Matrix
The bonding matrix that holds the diamond grit in place is crucial for the blade's longevity. Advanced bonding technologies ensure that the diamonds are held firmly, yet allow for the gradual wear necessary to expose fresh, sharp diamond particles. This delicate balance is achieved through years of research and development, resulting in a bond that degrades at the optimal rate, minimizing the need for dressing.
Precision Engineering and Manufacturing
The way a blade is engineered and manufactured also plays a significant role in its dressing frequency. Blades designed with precision and manufactured under strict quality control conditions ensure uniform distribution of diamond grit and consistent bond quality. This uniformity prevents uneven wear patterns that could necessitate more frequent dressing, thereby extending the blade's useful life.
Customized Blade Design
Blades designed for specific materials or cutting conditions can also influence the frequency of dressing required. By matching the blade's characteristics—such as diamond size, concentration, and bond hardness—to the specific application, you can optimize performance and durability. Such customization minimizes the blade's stress under operational conditions, thereby reducing the need for frequent dressing.
Operational Factors
The operational conditions under which the blade is used can also impact the need for dressing. Correct usage, appropriate cutting speeds, and adequate cooling can all help to reduce wear and extend the blade's lifespan. Educating users on best practices for blade operation can thus directly contribute to minimizing the frequency of dressing required.
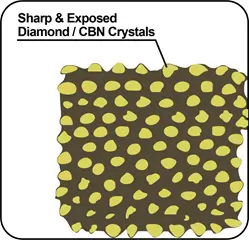
Heat Dissipation
Efficient heat dissipation plays a pivotal role in the performance and longevity of a diamond lapidary blade. As these blades slice through materials, the friction generated can lead to significant heat buildup. Without proper management, this heat can compromise the blade's structural integrity and cutting efficiency. A blade that effectively dissipates heat maintains its cool even under intense operation, safeguarding against potential warping or degradation of the diamond cutting edge.
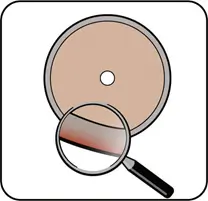
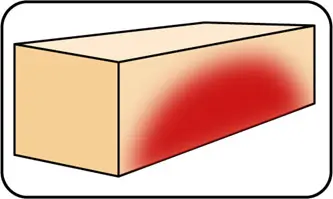
This characteristic is a hallmark of superior blade design and construction, underscoring the importance of thermal management in the engineering of diamond lapidary tools.
Advanced Materials for Heat Management
The choice of materials in the blade bond formulations is crucial for heat dissipation. high-performance Lapidary blades incorporate materials known for their thermal conductivity properties, facilitating the rapid transfer of heat away from the cutting zone. Additionally, the diamond grit and bonding matrix are selected not only for their cutting rate but also for their ability to withstand and dissipate heat, ensuring that the blade remains cool and effective throughout its operation.
Blade Design Innovations
Innovations in blade design have significantly enhanced heat dissipation capabilities. Features such as integrated cooling channels or segments designed with specific geometries can help direct heat away from the core of the blade. Moreover, certain blade designs optimize coolant and airflow around the blade during operation, enhancing the natural cooling effect and reducing the temperature of the cutting surface.
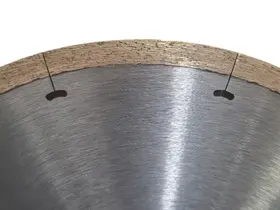
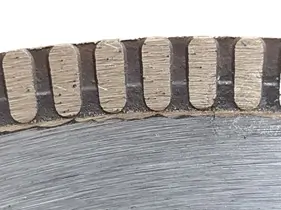
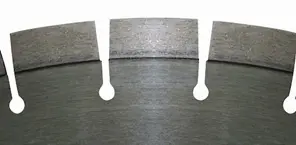
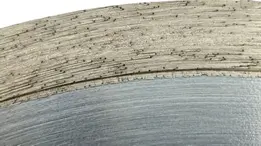
Operational Practices for Heat Reduction
Beyond blade design and materials, operational practices play a critical role in managing heat generation. Proper cutting speed, adequate pressure, and the use of appropriate cooling fluids can all contribute to minimizing heat buildup. Training for operators to understand these dynamics is crucial, ensuring that the blades are used in a manner that promotes efficient heat dissipation.
The Impact of Heat Management on Blade Life
Effective heat management extends beyond maintaining cutting efficiency; it significantly impacts the overall life of the blade. By preventing excessive heat buildup, you can ensure that the diamonds remain securely bonded and that the blade retains its shape and structural integrity. This directly translates to fewer blade replacements, reduced operational costs, and a lower environmental impact due to decreased waste.

Material Compatibility
Material compatibility is one of the main features of a superior diamond lapidary blades, underscoring their versatility and efficiency in a wide array of cutting tasks. These blades are meticulously engineered to adapt to various materials, from the hardest gemstones to the most delicate rocks, demonstrating a level of performance that transcends the limitations of more specialized tools. The ability of a blade to seamlessly transition between different material types without the need for constant adjustments or blade changes is a testament to the advanced engineering and thoughtful design that go into creation of diamond lapidary blades. This versatility not only streamlines the workflow but also significantly enhances operational efficiency.
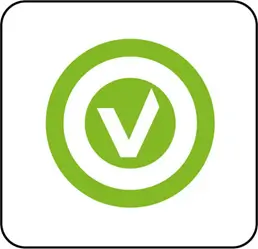
Material compatibility is one of the main features of a superior diamond lapidary blades, underscoring their versatility and efficiency in a wide array of cutting tasks. These blades are meticulously engineered to adapt to various materials, from the hardest gemstones to the most delicate rocks, demonstrating a level of performance that transcends the limitations of more specialized tools. The ability of a blade to seamlessly transition between different material types without the need for constant adjustments or blade changes is a testament to the advanced engineering and thoughtful design that go into creation of diamond lapidary blades. This versatility not only streamlines the workflow but also significantly enhances operational efficiency.
The development of versatile diamond lapidary blades involves extensive testing across a spectrum of materials. This rigorous testing ensures that the blades can handle the unique challenges posed by different lapidary materials, such as varying levels of hardness, abrasiveness, and even thermal sensitivity. By understanding how a blade interacts with diverse materials, we are able to fine-tune the diamond grit size, bond hardness, and blade geometry to produce blades that provide consistent performance, regardless of the material being cut.
Advanced Diamond Technology
The versatility of these blades is largely attributed to advances in diamond technology. Modern manufacturing techniques allow for the production of synthetic diamonds with tailored properties, such as size, shape, and strength, making it possible to design blades that are highly adaptable. The precise arrangement of these diamond particles within the blade's matrix further enhances its ability to cut through a wide range of materials with ease.
Optimized Bond Formulas
The bond matrix that holds the diamond particles in place is another critical factor in a blade's material compatibility. Optimized bond formulas are developed to provide the perfect balance between holding the diamonds securely and allowing them to be exposed at the right rate for cutting different materials. This balance ensures that the blade remains sharp and effective, whether cutting through soft marble or hard granite, minimizing the need for frequent blade changes.
Workflow Efficiency and Cost Effectiveness
The ability to use a single blade for multiple materials significantly boosts workflow efficiency. It reduces downtime associated with blade changes, lowers the inventory of specialized blades that must be kept on hand, and minimizes the learning curve for operators. Furthermore, this versatility makes the blade more cost-effective over its lifespan, offering savings in both time and resources.
Cut Quality / Chipping Level
The quality of the cut, particularly the smoothness of the edges, is a critical measure of a diamond lapidary blade's performance. High Quality Lapidary Blades are distinguished by their ability to produce chip-free edges, a feature that significantly elevates the precision and finish of the cut. This capability not only enhances the aesthetic appeal of the material being cut but also streamlines the fabrication process by reducing, or in some cases eliminating, the need for secondary finishing operations.
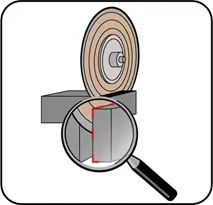
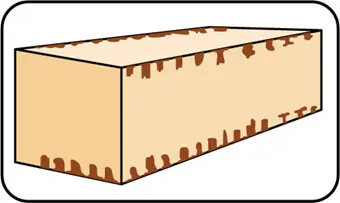
Precision Diamond Arrangement (SMART CUT technology)
The arrangement of diamonds on the blade plays a pivotal role in achieving chip-free edges. Superior blades use advanced technology to distribute the diamonds evenly across the diamond cutting surface. This even distribution ensures that each part of the diamond crystal inside the bond matrix contributes equally to the cut, reducing the chances of chipping and ensuring a smoother finish. Advanced manufacturing techniques allow for the optimization of diamond placement, enhancing the blade's cutting precision.
Bond Matrix Innovation
The bond matrix that secures the diamonds to the blade is engineered to complement the cutting action, providing just the right amount of hold versus release of the diamond particles. A bond that's too hard may not expose new diamonds quickly enough, leading to dull cuts that can cause chipping. Conversely, a bond that's too soft might release diamonds too rapidly, diminishing the blade's effectiveness. The ideal bond matrix is tailored to release diamonds at an optimal rate, maintaining the sharpness of the cut and ensuring chip-free edges.
Durability and Longevity
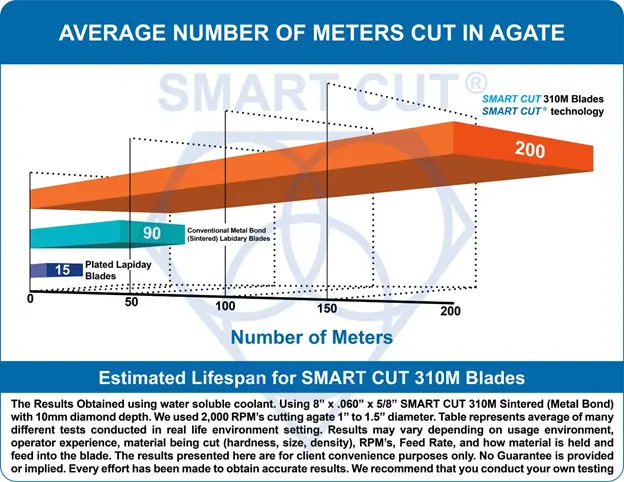
Durability and longevity are fundamental attributes that define the overall value and effectiveness of a diamond lapidary blade. These qualities are not merely about a blade's resistance to physical wear but encompass a broader spectrum of performance characteristics, including the blade's ability to maintain its cutting precision, speed, and efficiency over time. Superior blades are designed with an emphasis on enduring the rigors of extensive use without significant degradation, making them not only more cost-effective but also reliable for consistent, high-quality work. Exploring the factors contributing to a blade's durability and longevity sheds light on the technological prowess and meticulous attention to detail involved in its creation.
High-Quality Materials
The foundation of a durable blade lies in the quality of the materials used in its manufacturing process. Premium diamond lapidary blades utilize high-grade synthetic diamonds known for their exceptional hardness and thermal stability. These diamonds are embedded in a bond matrix composed of carefully selected materials that balance toughness with wear resistance, ensuring that the blade can withstand prolonged use without losing its effectiveness.
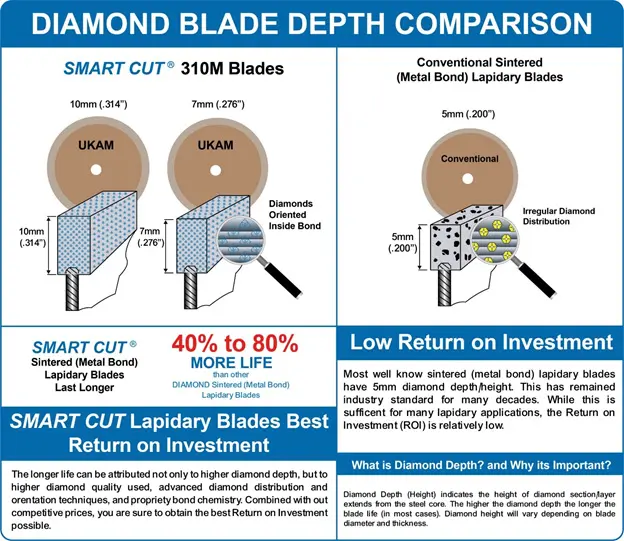
Wear Resistance
Wear resistance is a critical attribute that directly impacts the longevity and cost-effectiveness of a diamond lapidary blade. A blade that can withstand the rigors of rigorous use without significant degradation in its cutting capabilities not only ensures consistent performance but also provides greater value over its lifespan. High-quality blades are distinguished by their ability to retain their cutting edge and diameter over extended periods, demonstrating resilience against the wear and tear that typically accompanies intensive cutting tasks.
The wear resistance of a diamond lapidary blade is largely a function of the engineering and bond matrix composition that go into its design. Using high-grade, synthetic diamonds with properties optimized for toughness and thermal resistance, ensuring that the cutting edges remain sharp and effective through repeated use. The bonding matrix that holds these diamonds in place is also crucial; it must be hard enough to keep the diamonds exposed but wear down at a rate that continuously reveals new, sharp diamond edges. This balance is achieved through sophisticated material formulations and manufacturing processes that ensure the longevity of the cutting edge.
Consistency in Performance
A hallmark for an excellent lapidary blades is the consistency of its performance across large spectrum of lapidary materials. This is what makes a blade stand out from all the rest. Having the right bond formulation, right bond hardness, and right diamond type will make sure the diamond particles exposed in the lapidary blade bond matrix at every point in which it comes in contact with the material. This uniform distribution of diamonds within the blade allows for consistent cutting speed, crucial for maintaining precision and efficiency in every pass.
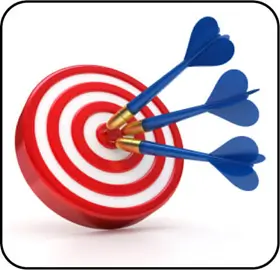
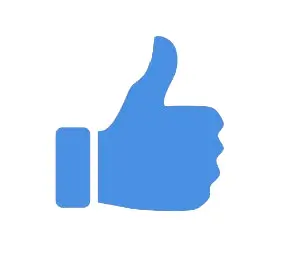
A high-quality blade also offers freer cutting capabilities, reducing the resistance encountered when slicing through different lapidary materials. This not only enhances the blade's lifespan by minimizing wear but also ensures that the cut quality remains
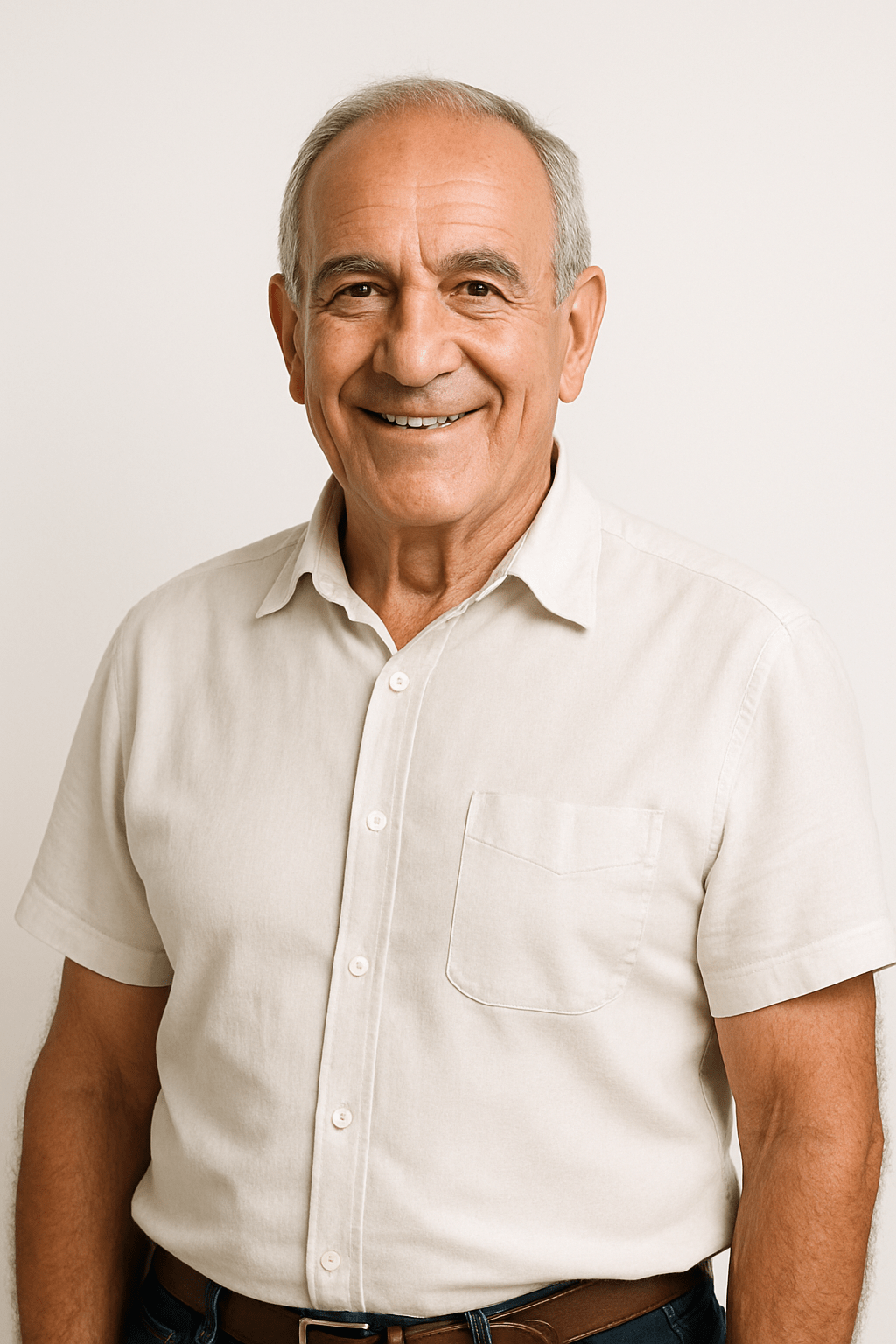
Leon Meyer is a veteran manufacturing engineer and technical consultant with over 50 years of experience in the development, implementation, and troubleshooting of industrial diamond tooling systems. Having spent his career at the intersection of tool design, precision manufacturing, and production engineering, Mr. Meyer is widely regarded as one of the most experienced voices in the application of ultra-thin diamond blades, sintered core drills, and CBN grinding wheels across heavy industry, advanced materials, and research sectors.
Known for his pragmatic, no-nonsense approach, Leon has advised manufacturers across the United States, Europe, and East Asia—helping streamline cutting processes, extend tool life, and solve complex issues related to material breakage, chipping, and tolerance drift. His expertise has directly contributed to improved production efficiency in industries ranging from aerospace alloys and technical ceramics to optics, composites, and high-nickel superalloys.
As an author, Mr. Meyer brings a lifetime of field knowledge to his writing, with a focus on real-world problem solving, cost-performance optimization, and tool reliability under demanding conditions.
ARE YOU USING RIGHT LAPIDARY BLADES
FOR YOUR APPLICATION?
LET US
HELP YOU
HAVING ISSUES WITH
YOUR CURRENT LAPIDARY BLADES?
Knowledge Center
How to Properly Use Diamond Lapidary Blades
Signs of a High Quality Diamond Lapidary Blade
What Makes a Great Diamond Lapidary Blade
Mastering the Art of Lapidary cutting
Evaluating & Comparing Diamond Blades
How to Improve & Optimize Your Diamond Sawing Operation
Troubleshooting Diamond Sawing Problems
How to properly use Diamond Tools
How to Selecting Right Diamond Tools for your application
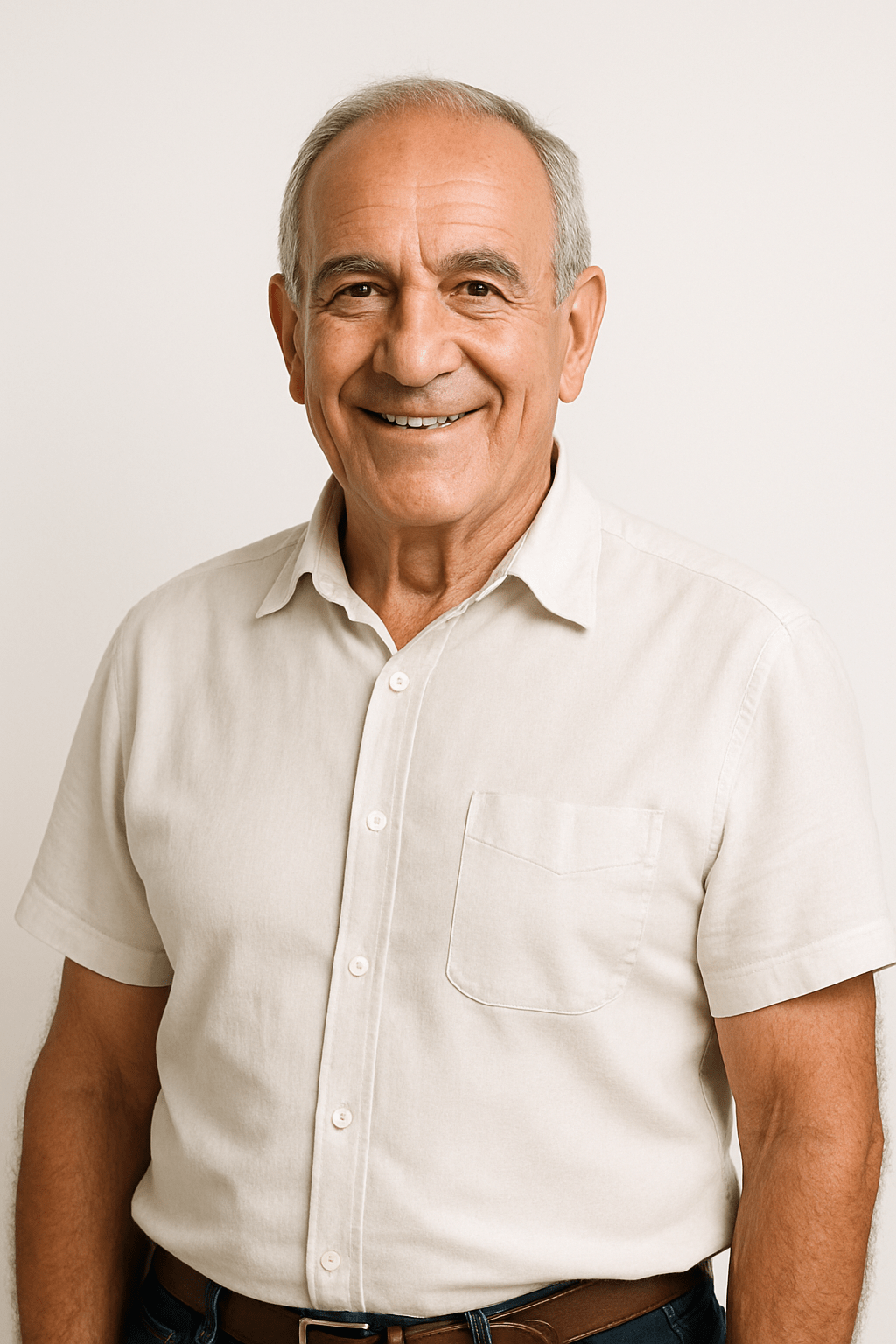
Leon Meyer is a veteran manufacturing engineer and technical consultant with over 50 years of experience in the development, implementation, and troubleshooting of industrial diamond tooling systems. Having spent his career at the intersection of tool design, precision manufacturing, and production engineering, Mr. Meyer is widely regarded as one of the most experienced voices in the application of ultra-thin diamond blades, sintered core drills, and CBN grinding wheels across heavy industry, advanced materials, and research sectors.
Known for his pragmatic, no-nonsense approach, Leon has advised manufacturers across the United States, Europe, and East Asia—helping streamline cutting processes, extend tool life, and solve complex issues related to material breakage, chipping, and tolerance drift. His expertise has directly contributed to improved production efficiency in industries ranging from aerospace alloys and technical ceramics to optics, composites, and high-nickel superalloys.
As an author, Mr. Meyer brings a lifetime of field knowledge to his writing, with a focus on real-world problem solving, cost-performance optimization, and tool reliability under demanding conditions.