Table of Contents
ToggleSAMPLE / MATERIAL CLAMPING / FIXTURING
Properly securing the material in place is one of the first and most important steps in the sectioning process. The function of the chuck or holding fixture is to keep the sample or material firmly in place, preventing it from moving during sectioning / cutting. Various sample chucks and holding fixtures are available for a wide range of sectioning saws to accommodate all types of material shapes and geometries. It is very important to use the right mounting media for your specific sample. The choice of chuck for your application will depend on the initial sample or material dimensions, desired cut depth, and material properties such as hardness, brittleness, and shape or geometry.
Using the correct chuck is crucial because improper clamping can lead to several issues. For instance, occasional chipping at the bottom of the cut can be a challenge. This problem arises when the back side of the material does not have firm support at the cutting area, creating a higher chipping rate when the blade exits the cut. Ensuring firm support throughout the material's length can help mitigate this issue.
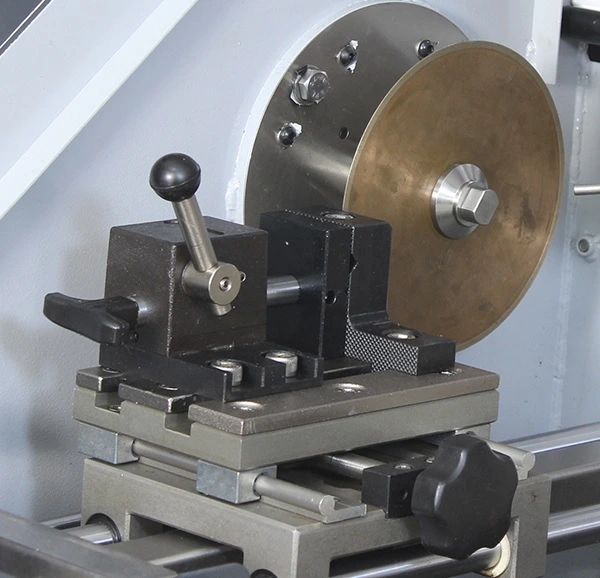
The sample must not move while being sectioned. Movement of the sample can damage the material or the blade and can prevent obtaining a planar section. However, the sample must also not be over-tightened. Over-tightening can damage the chuck or the sample itself. For example, brittle materials such as those in the glass and refractory families can fracture if over-tightened. On the other hand, harder and denser materials such as silicon carbide can cause dents in the chuck if excessive force is applied. Dents or nicks in the chuck will affect subsequent samples sectioned in the same chuck, causing damage and potential cracks.
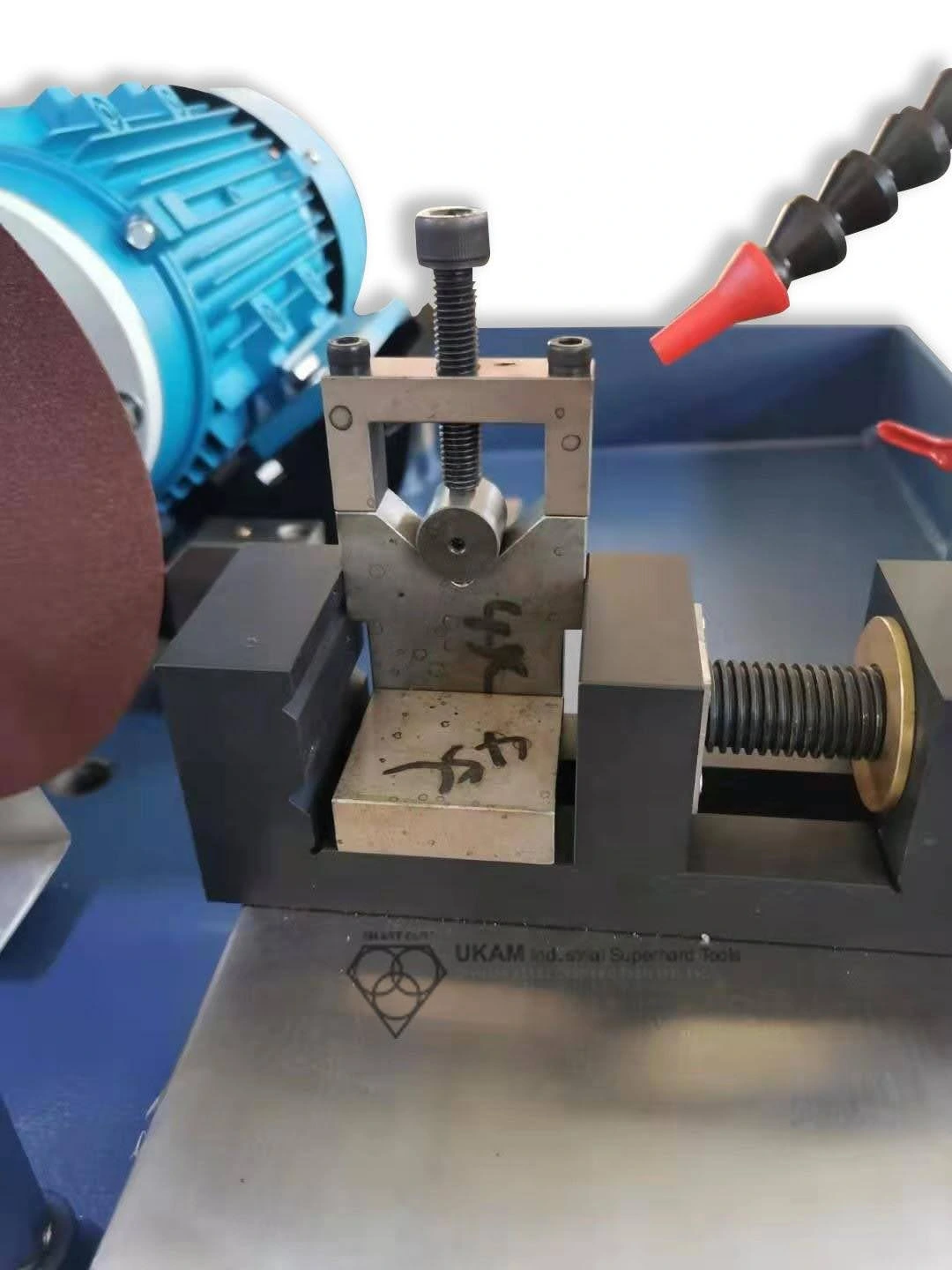
The choice of chuck or holding fixture must account for the specific characteristics of the sample. For irregularly shaped samples, custom fixtures might be necessary to ensure even clamping pressure and stability during cutting. For cylindrical samples, v-blocks or collet chucks can provide the necessary support and alignment.
In addition to selecting the right chuck, using proper padding and cushioning materials can help protect both the sample and the chuck from damage. Padding materials such as rubber or foam can distribute clamping forces more evenly and reduce the risk of damage to brittle samples. This approach also helps to minimize the introduction of nicks and dents in the chuck, preserving its integrity and performance over time.
Effective clamping also involves considering the dynamics of the cutting process. During cutting, vibrations and forces exerted on the sample can cause movement if the clamping is not secure. Utilizing fixtures that can dampen vibrations or distribute forces more evenly can improve the stability of the sample and enhance the quality of the cut.
The position and orientation of the sample in the chuck can also influence the cut quality. Ensuring that the sample is aligned correctly with the cutting plane can help achieve more accurate and consistent sections. For materials that are prone to deformation under clamping pressure, supporting the sample at multiple points can help maintain its shape and prevent warping.
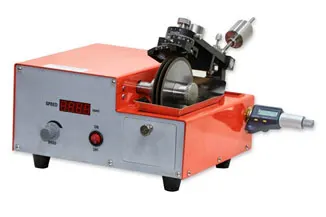
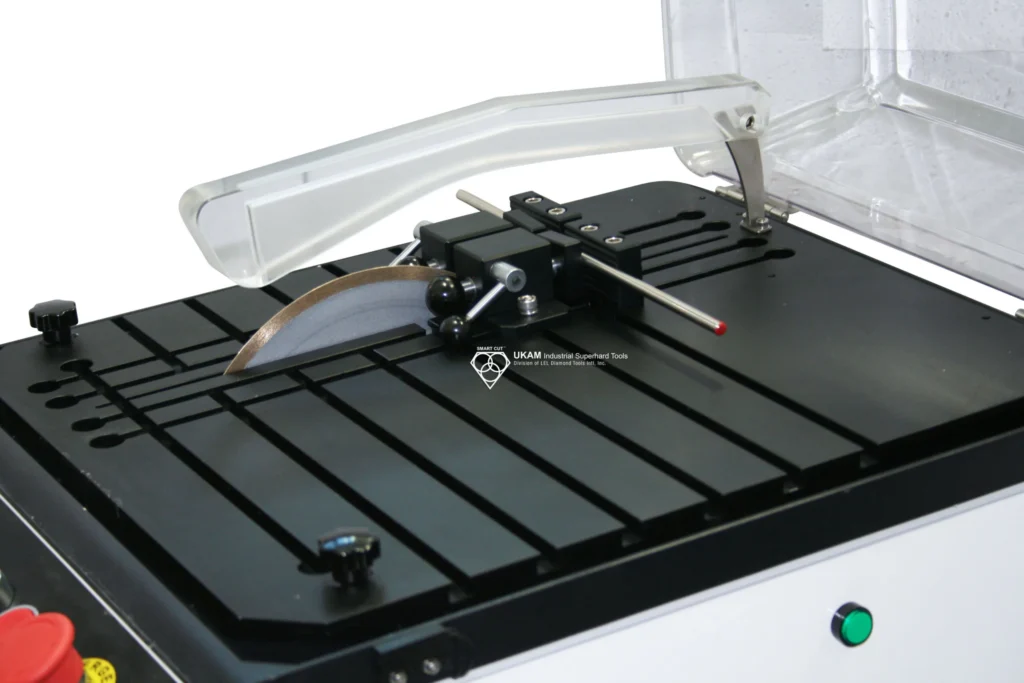
Types of chucks / holding fixtures
The choice of chuck or holding fixture must account for the specific characteristics of the sample to ensure optimal clamping and cutting performance. Different materials and geometries require tailored approaches to secure them effectively during the sectioning process. Additionally, different types of saws—low and high-speed saws, medium-speed sectioning/wafering saws, and metallographic abrasive cutters for larger diameters—require specific chucks designed for their operational characteristics.
For irregularly shaped samples, standard chucks may not provide the necessary stability and even clamping pressure. Custom fixtures might be necessary in these cases to ensure the sample is held securely without causing deformation or damage. Custom fixtures can be designed to match the unique contours and dimensions of the sample, providing a more tailored fit that enhances stability during cutting. These fixtures often include adjustable components that can adapt to different sample sizes and shapes, offering flexibility and precision.
For cylindrical samples, v-blocks or collet chucks are ideal choices as they provide the necessary support and alignment. V-blocks offer a stable base by cradling the cylindrical sample in a V-shaped groove, ensuring it remains aligned with the cutting plane. Collet chucks, on the other hand, grip the sample evenly around its circumference, distributing clamping pressure uniformly and preventing slippage during the cutting process. Both of these fixtures help maintain the sample's position and orientation, which is critical for achieving accurate and repeatable cuts.
different saw types necessitate specific chucks to ensure optimal performance, stability, and safety during the cutting process. The choice of chuck is influenced by the type of saw, the material being cut, and the specific requirements of the application.
Low-Speed Saws:
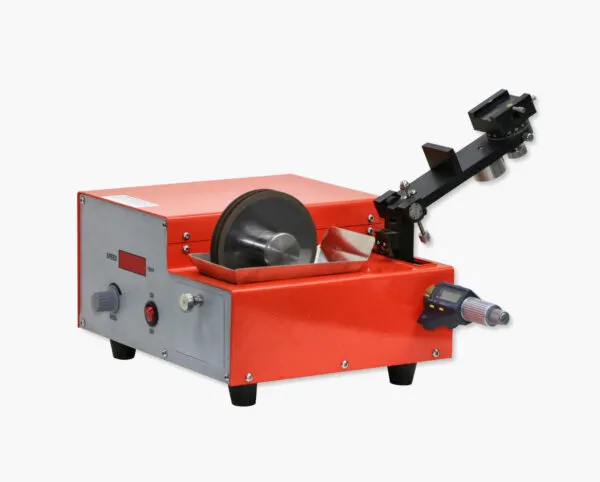
SMART CUT® 4005
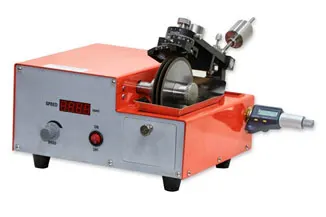
SMART CUT® 6005
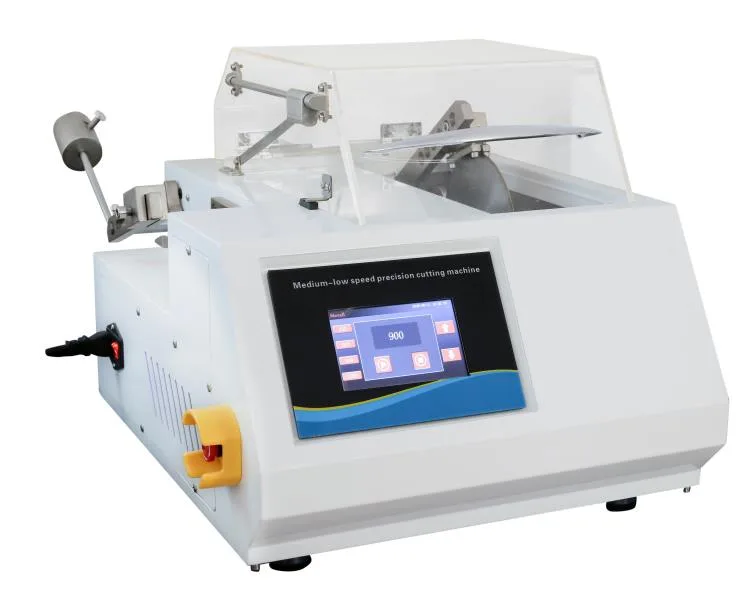
SMART CUT® 6040
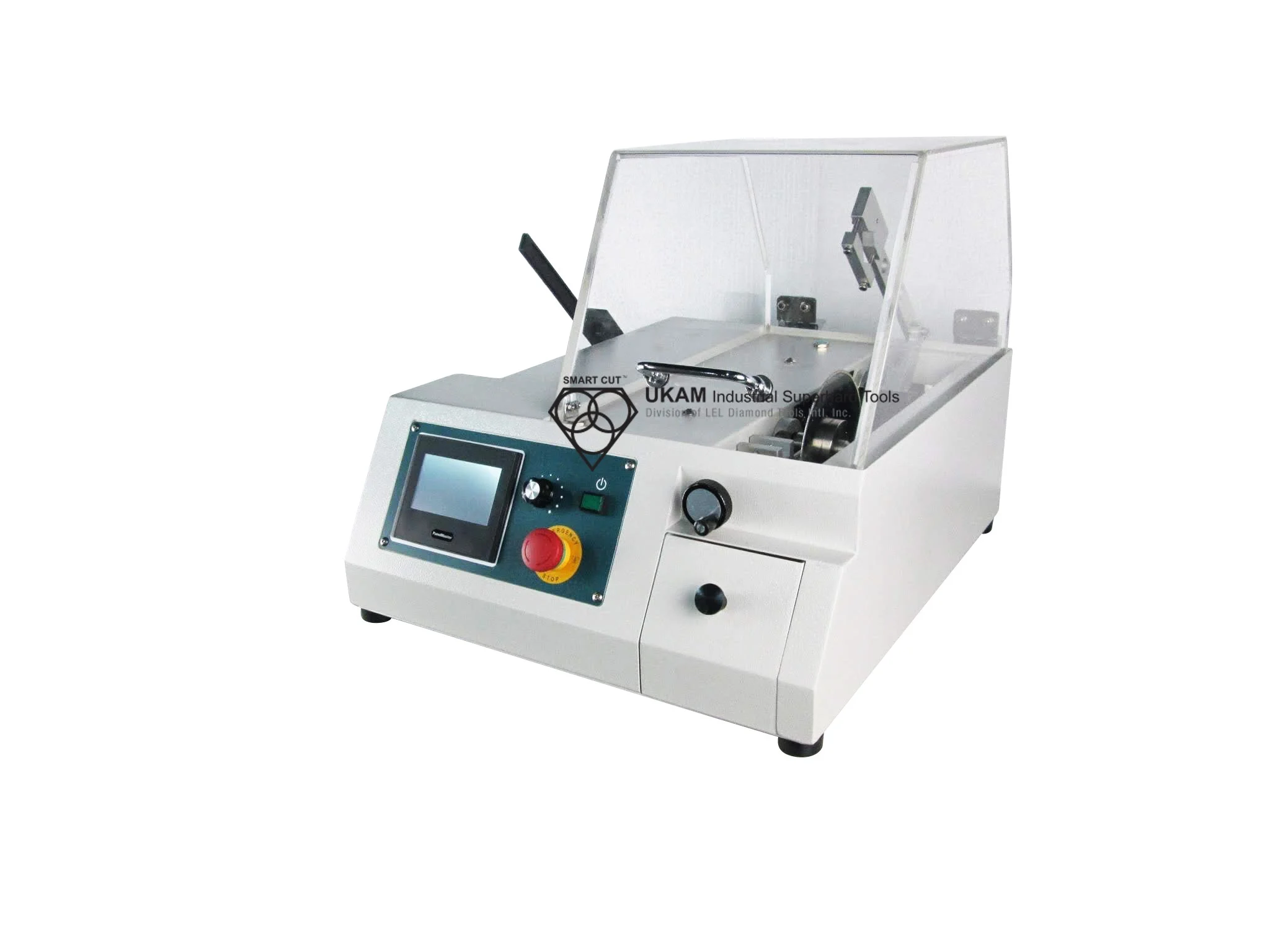
SMART CUT® 6035
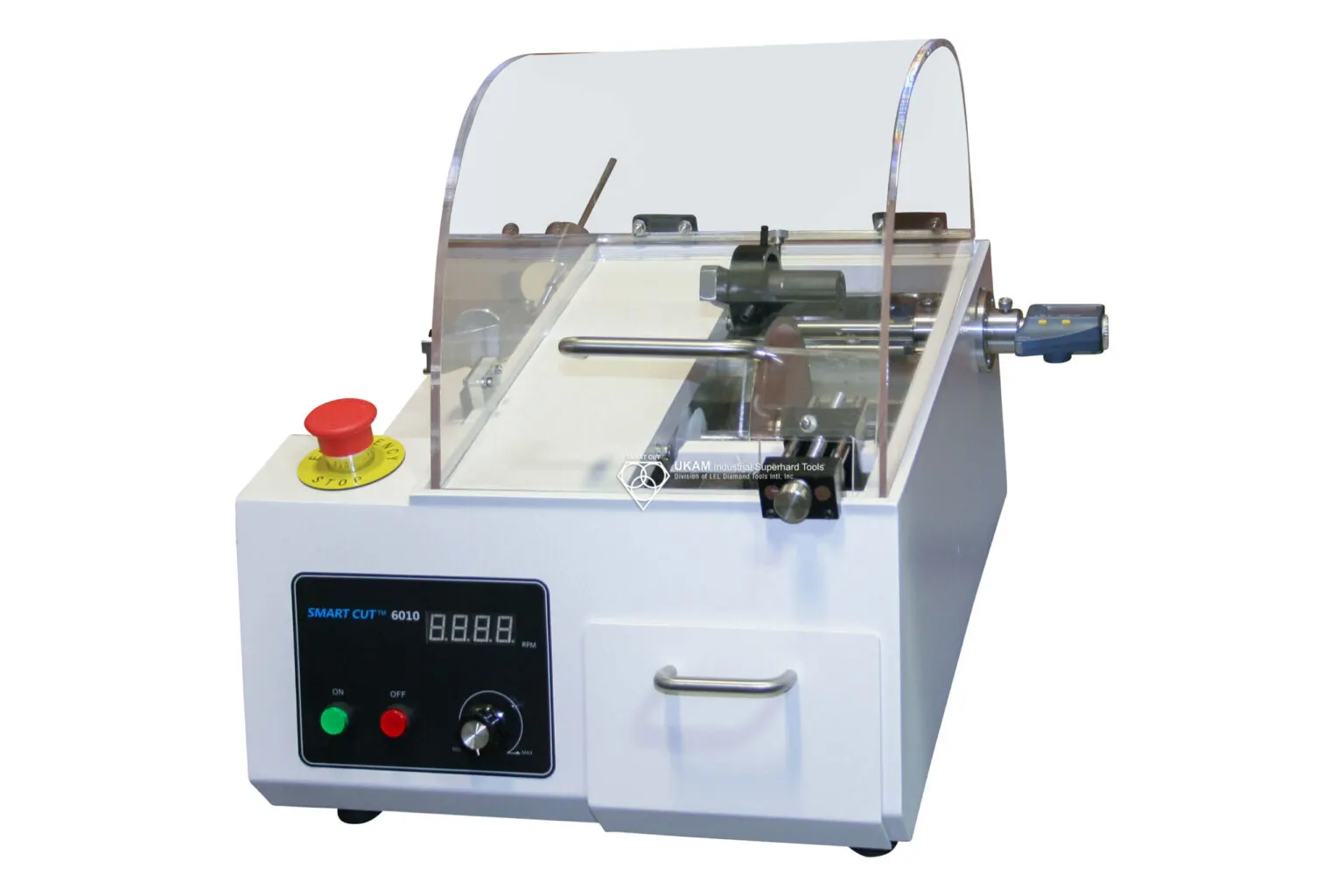
SMART CUT® 6010
These saws are designed for delicate materials that require gentle handling to avoid damage. Chucks for low-speed saws often incorporate cushioning materials and adjustable grips to securely hold the sample without exerting excessive force. This setup is crucial for brittle materials such as ceramics, glass, and thin wafers, where even slight pressure can cause fractures or other forms of damage. The cushioning materials help distribute the clamping force evenly, protecting the integrity of both the sample and the chuck. Adjustable grips allow for precise positioning, ensuring that the sample remains stable and aligned during the cutting process.
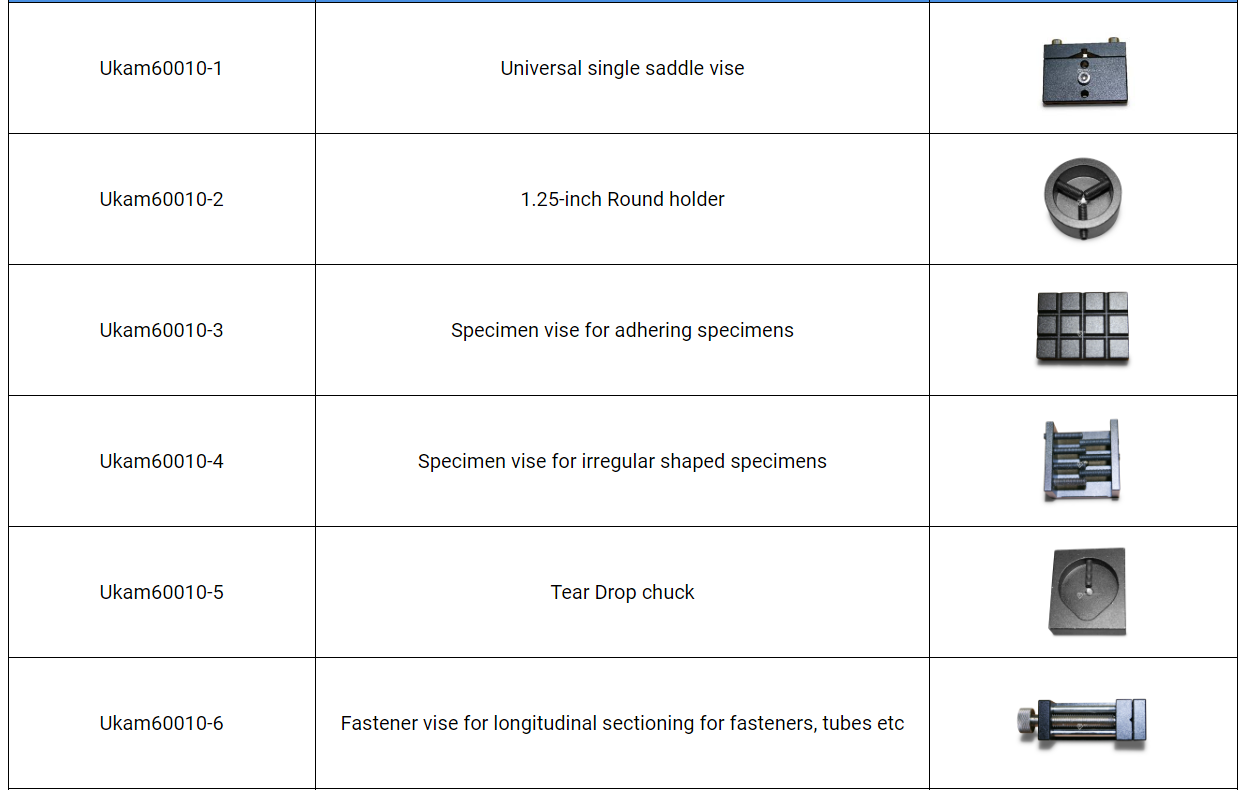
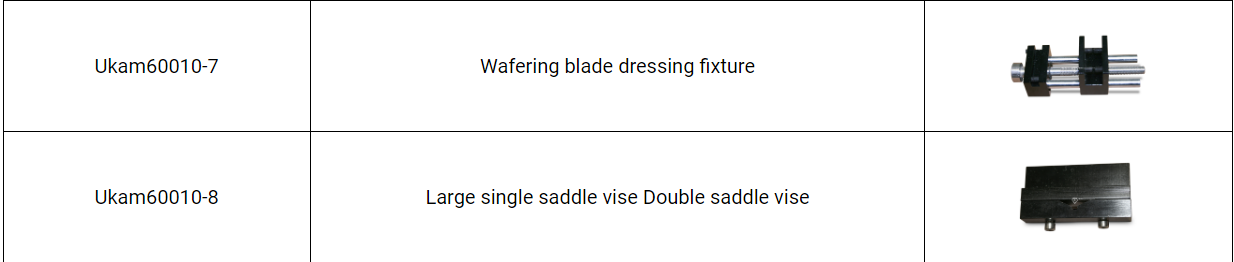
High-Speed Saws:
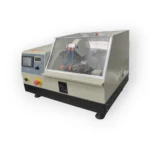
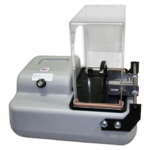
SMART CUT® 4002 XP
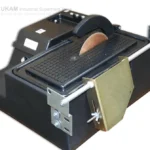
SMART CUT® 6001 XP
High-speed saws are used for harder materials that can withstand greater forces and higher cutting speeds. Chucks for high-speed saws are typically more robust and capable of applying higher clamping forces to ensure the sample remains stable during rapid cutting. Materials like metals and dense composites are commonly processed with high-speed saws, requiring chucks that can maintain firm, consistent pressure to prevent movement and ensure precision. These chucks often feature heavy-duty construction and may include additional supports to manage the increased stress and vibrations associated with high-speed operations.
Medium-Speed Sectioning/Wafering Saws:
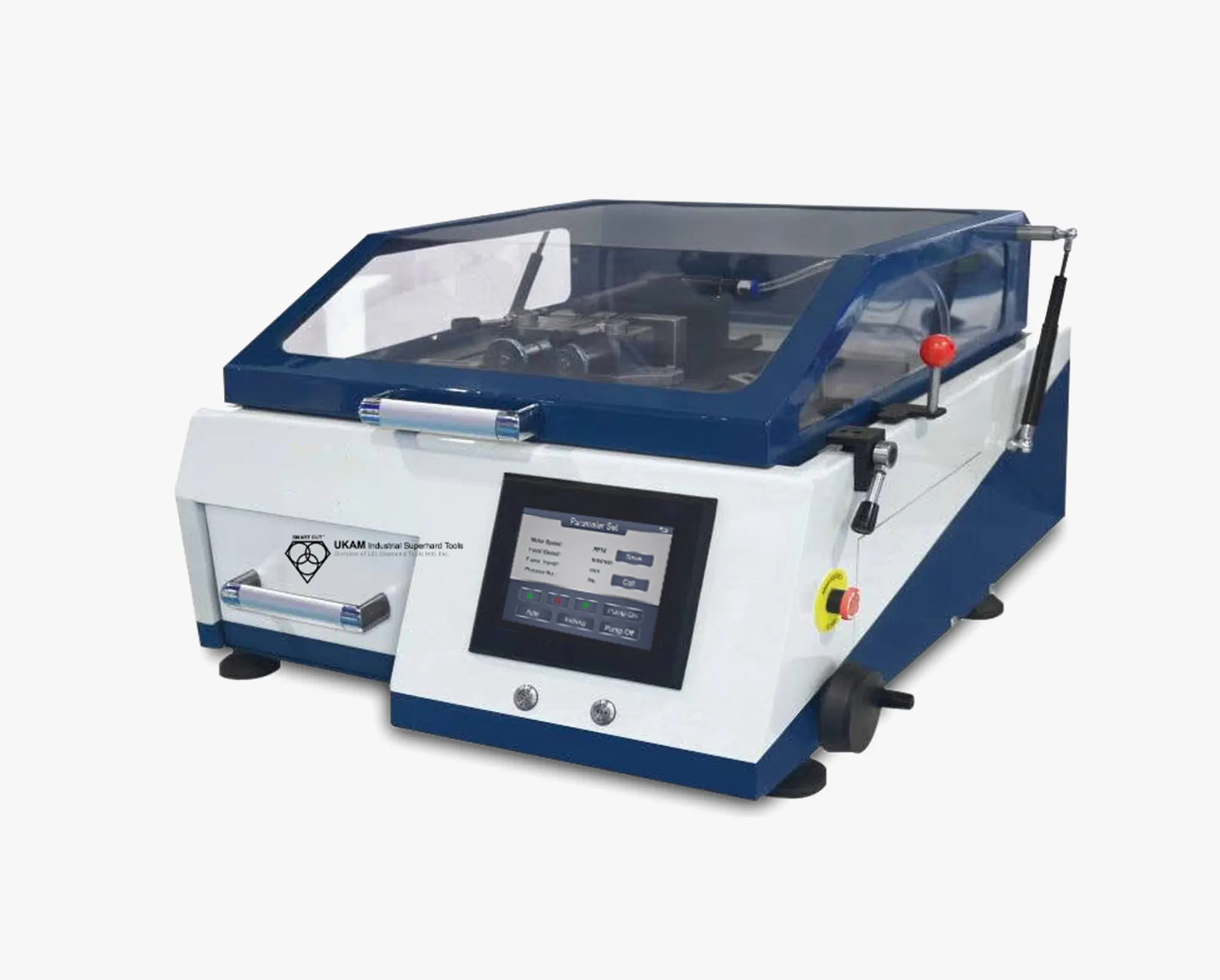
SMART CUT® 6018
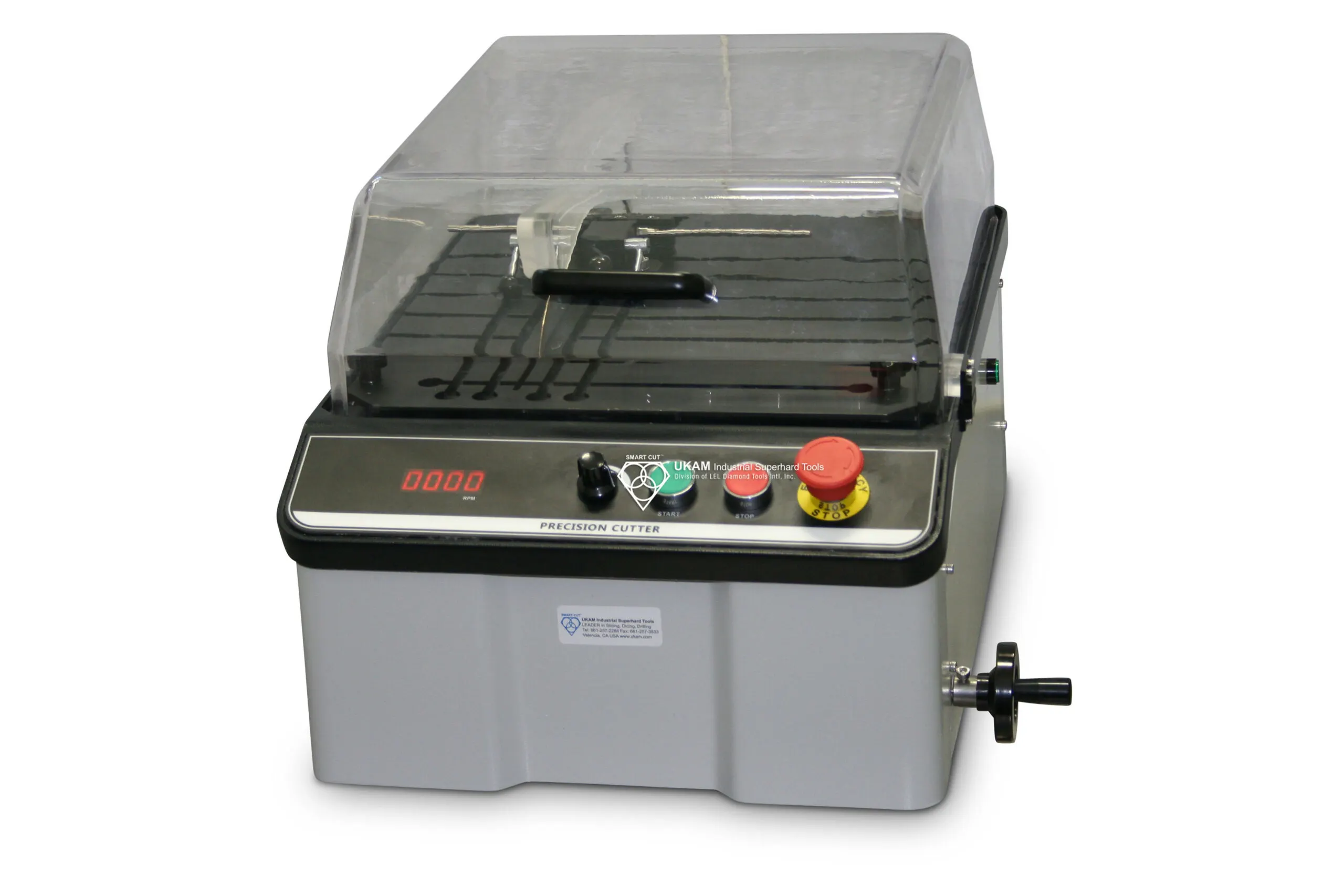
SMART CUT® 6025-Manual Low & high Speed Sectioning Saw
These versatile saws handle a wide range of materials and cutting conditions. Chucks for medium-speed saws need to be adaptable, providing secure clamping for various sample shapes and sizes. These chucks often include modular components that can be adjusted or swapped out to accommodate different materials. For example, a medium-speed saw might need to switch between holding a small, delicate sample and a larger, more robust one. The modular design allows for quick and easy adjustments, enhancing the saw's flexibility and efficiency. This adaptability is particularly useful in research and development settings, where a variety of materials and sample geometries are often encountered.
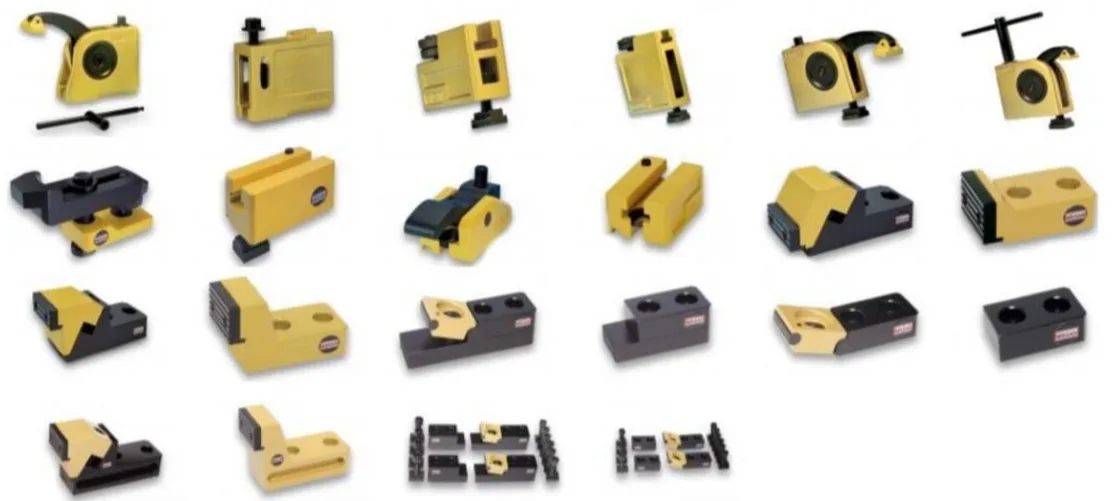
Metallographic Abrasive Cutters:
Designed for larger diameter samples, metallographic abrasive cutters typically operate at medium to high speeds. The chucks used in these machines need to handle significant forces while maintaining precise alignment. They are often equipped with heavy-duty clamps and support structures to manage the larger, heavier samples typically processed in metallographic studies. The robust construction of these chucks ensures that they can withstand the high forces generated during cutting without compromising stability or accuracy. Additionally, these chucks may feature enhanced clamping mechanisms to prevent slippage and ensure that the sample remains securely in place throughout the cutting process.
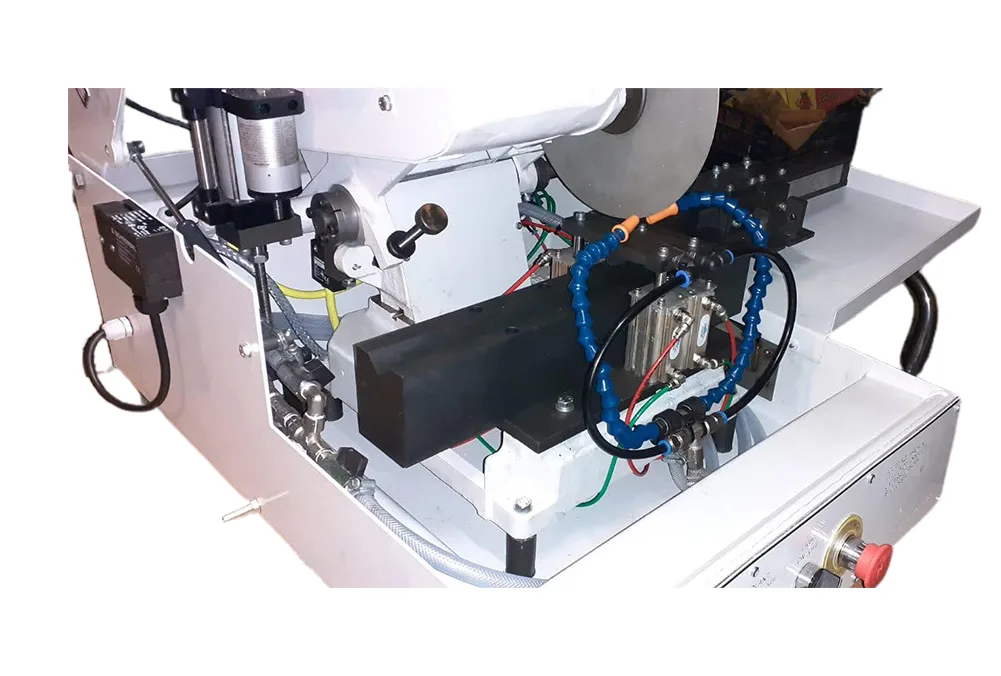
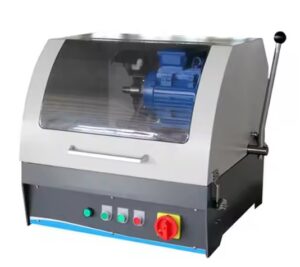
The type of padding and cushioning materials used in the chuck can also be adjusted based on the sample and saw type. Soft rubber or foam padding is ideal for delicate samples, while harder, more durable padding materials are better suited for high-speed operations and harder materials.
In addition to the sample's shape, the material's hardness and brittleness must be considered when selecting a chuck or holding fixture. Brittle materials, such as ceramics or glass, require gentle clamping to avoid inducing fractures. In these cases, fixtures with soft, cushioning materials or inserts can help distribute the pressure more evenly and reduce the risk of damage. Harder materials, like metals and dense composites, can withstand more substantial clamping forces, but it is still important to avoid excessive pressure that could deform the sample or the chuck itself.
Temperature sensitivity of the material is another critical factor. Some materials may expand or contract significantly with temperature changes, which can affect their stability in the chuck. Fixtures designed with thermal compensation features can help maintain secure clamping even as the sample's dimensions change with temperature fluctuations. These fixtures might use materials with low thermal expansion coefficients or incorporate adjustable elements that can be fine-tuned during the cutting process.
The surface finish and cleanliness of both the sample and the chuck also play a role in achieving a secure hold. Any contaminants or irregularities on the clamping surfaces can reduce friction and lead to slippage. Ensuring that both the sample and the chuck are clean and free of debris helps maintain a firm grip. In some cases, surface treatments or coatings on the chuck can enhance grip and reduce wear over time.
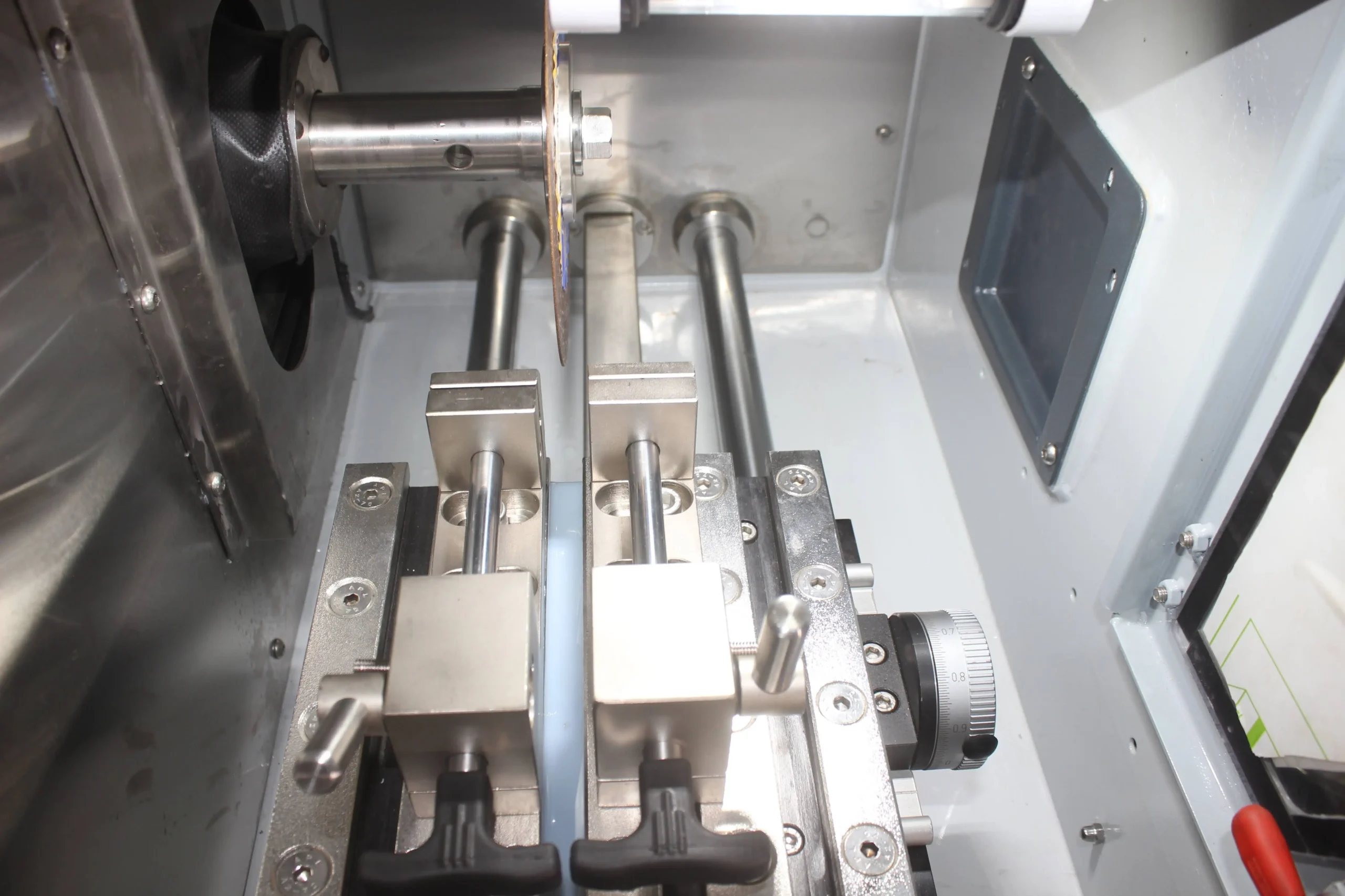
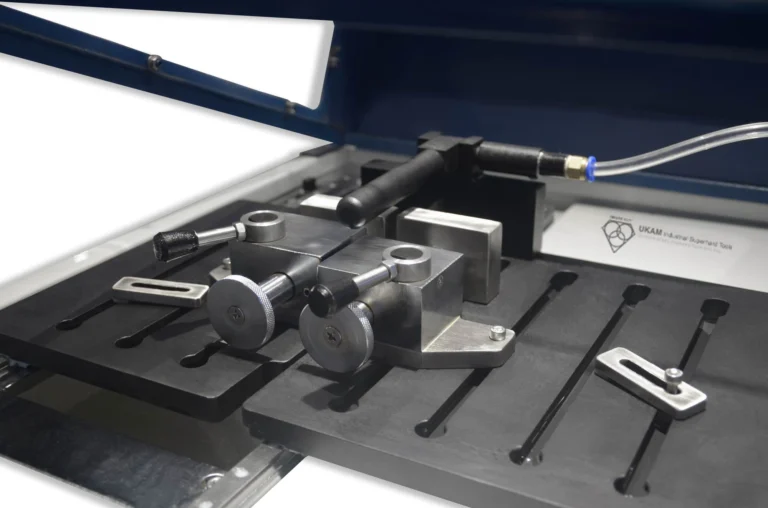
Automation and precision in clamping are increasingly important in advanced metallography and sample preparation. Automated clamping systems can provide consistent pressure and alignment, reducing variability introduced by manual adjustments. These systems often include sensors and feedback mechanisms that monitor the clamping force and make real-time adjustments to maintain optimal conditions. This level of control is especially valuable for high-throughput environments where consistency and efficiency are paramount.
Fixtures designed for quick and easy adjustment can improve workflow efficiency. Modular systems that allow for rapid swapping of different fixtures or the adjustment of clamping points can save time and reduce the risk of error. This flexibility is particularly beneficial in research settings where a wide variety of samples may need to be processed quickly and accurately.
CHUCK POSITIONING / ALIGNMENT
The positioning and alignment of the sample chuck are critical to ensuring the success of the sectioning process in metallography and sample preparation. Properly securing the sample chuck to the load arm and ensuring the correct positioning and angle of the sample can significantly impact cut quality, material deformation, and the overall efficiency of the cutting operation.
The sample chuck should be securely attached to the load arm. For most applications, this is done on the right-hand side of the load arm. However, for longer samples, mounting on the left-hand side of the load arm can provide extra clearance and minimize the possibility of the sample coming into contact with the saw hood. Improper mounting of the chuck or sample can cause damage to both the sample and the wafering blade.
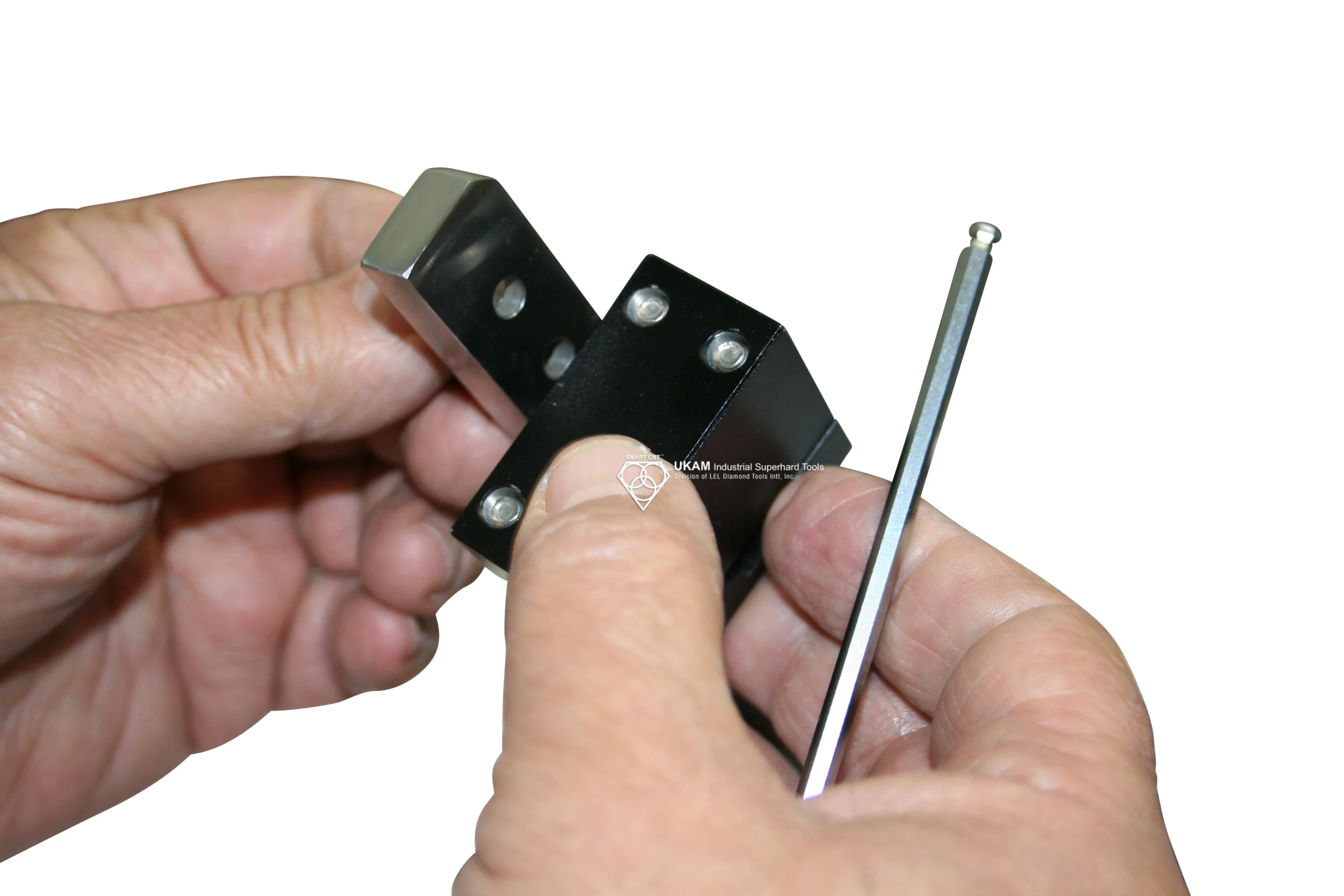
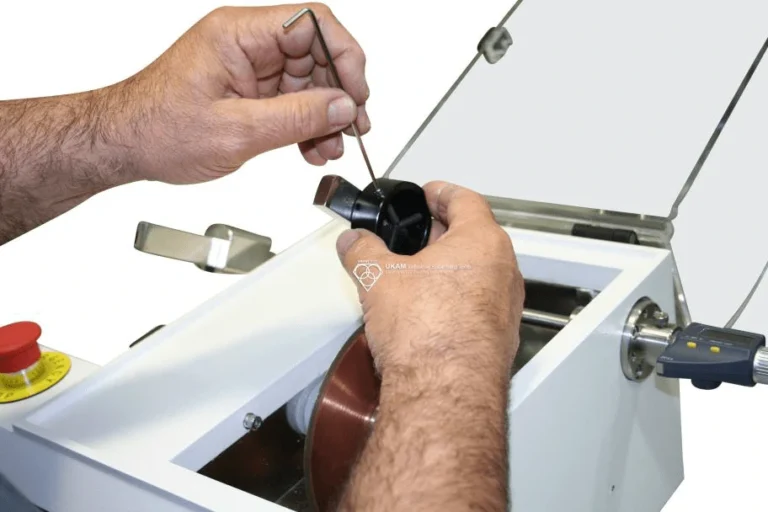
Positioning the sample and its angle where it contacts the cutting blade play an essential role in determining the cut quality and minimizing material deformation. Additionally, these factors can affect the time it takes to complete the cut or section. For optimal results, position and align the sample so that the smallest section or angle comes into contact with the blade first. This approach ensures that the sample is cut faster compared to when the widest dimension of the sample contacts the blade initially.
This alignment is especially critical for materials and samples with varying compositions and properties. For example, coated specimens should be positioned so that the coated side is cut first. This helps avoid excessive damage to the coating, which typically has different material properties than the underlying material. Cutting through the coating first reduces the risk of delamination or excessive wear on the coating, preserving the integrity of both the coating and the substrate.
Samples and materials should be aligned with the blade in a way that ensures the sample chuck does not touch the blade support flanges. During the sectioning operation, if you find that the sample chuck is touching the blade flanges, the chuck should be attached to a different position on the saw load arm. Depending on the design and configuration of your saw, this may not always be feasible. An alternative solution is to reposition the sample within the chuck to ensure there is proper clearance between the chuck and the blade flange. This adjustment helps prevent potential damage to the blade and ensures a smoother cutting process.
Proper alignment also involves ensuring that the sample is parallel to the cutting blade. Misalignment can lead to uneven cuts, increased wear on the blade, and potential damage to the sample. Use alignment tools or guides to check and adjust the sample's position before starting the cut. This practice is especially important when working with brittle or delicate materials, where even minor misalignments can lead to significant issues.
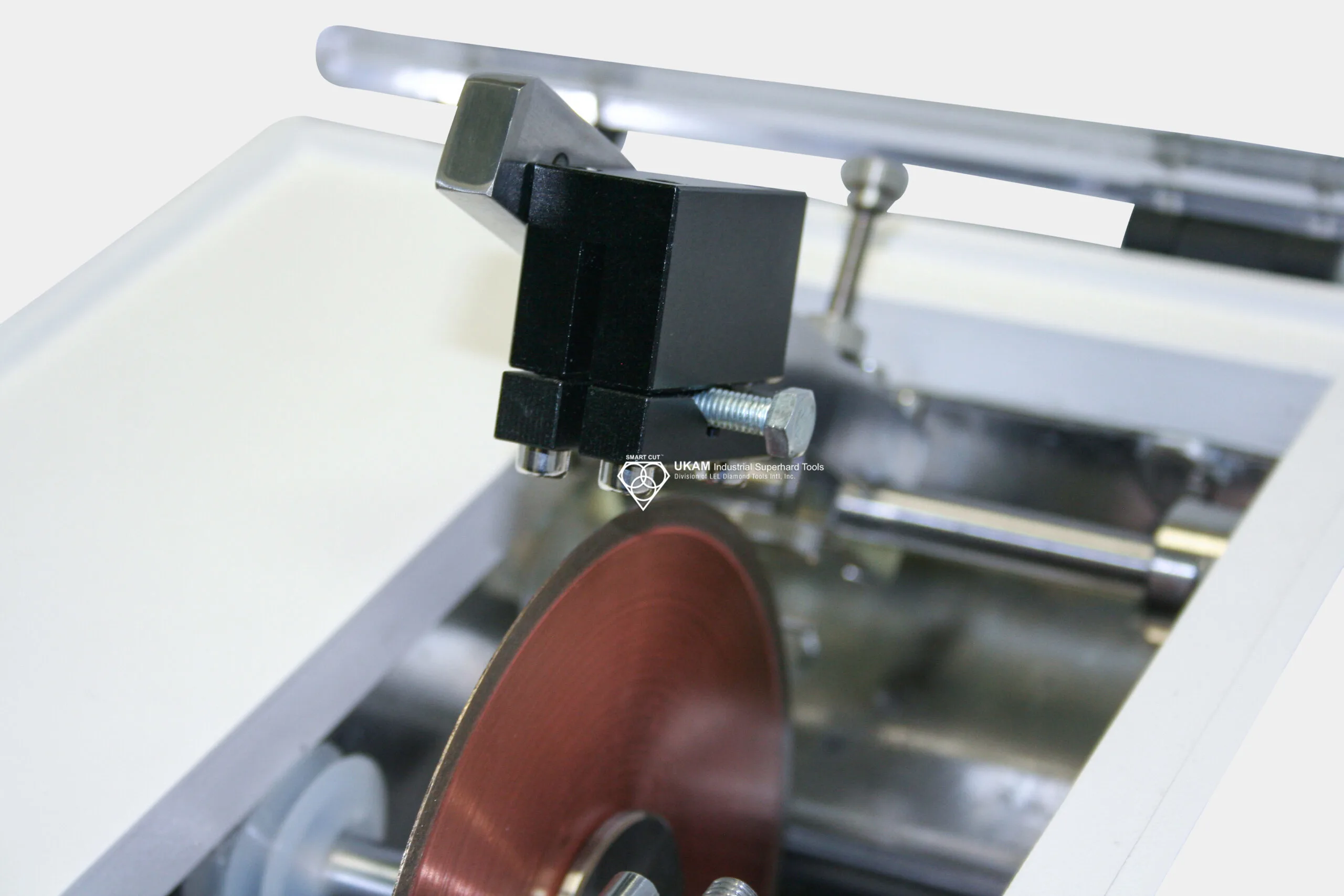
In addition to positioning and alignment, consider the force and pressure applied during the cutting process. Uniform pressure distribution across the sample helps in achieving a clean and precise cut. Adjust the load arm and chuck settings to ensure that the pressure is evenly applied and does not vary significantly during the cutting process.
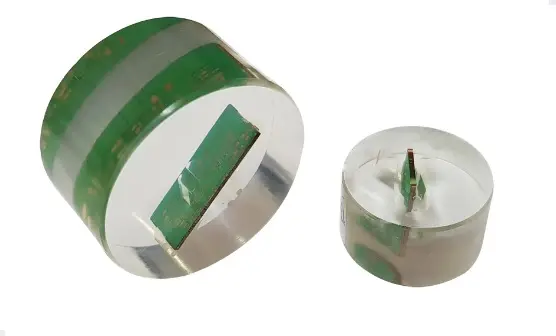
EPOXY SAMPLE MOUNTING
Epoxy sample mounting is a crucial technique for securing samples that are too small or delicate to be clamped or fixtured directly, enhancing the precision and safety of the cutting process. By stabilizing the sample within a hardened matrix, this method significantly reduces movement and vibration during cutting, which is essential for achieving clean and precise cuts, particularly with materials prone to movement or chipping.
When a sample is embedded in epoxy, it is shielded from the direct stress and potential damage of the cutting process. This protection is particularly important for fragile or brittle samples that might otherwise suffer from the physical forces of cutting. Moreover, epoxy mounting ensures that the sample can be presented consistently throughout the cutting process, which is beneficial for irregularly shaped or very small samples, providing a uniform base that facilitates easier handling and more accurate cuts.
The procedure for epoxy sample mounting involves several key steps. First, the sample and mold must be prepared by thoroughly cleaning the sample to remove any impurities that could interfere with the epoxy's adhesion. The mold should be selected to fit the sample snugly without too much excess space. Next, the epoxy resin and hardener should be mixed according to manufacturer specifications to ensure optimal performance. The mixture should be poured into the mold carefully to avoid introducing air bubbles, which can compromise the integrity of the mount.
Once the epoxy is poured, it needs to be allowed to cure fully, which can take several hours to overnight, depending on the type of epoxy used. After curing, the sample embedded in the epoxy block can be removed from the mold and mounted in the cutting machine for sectioning.
It is important to avoid air bubbles in the mixture as they can weaken the mount and affect the quality of the cut. The curing conditions should be controlled to avoid premature hardening or incomplete curing. Proper curing is essential for achieving a stable and durable mount. Safety measures should also be observed when handling epoxy resins and hardeners, using appropriate safety equipment and working in well-ventilated areas to avoid exposure to potentially harmful fumes.
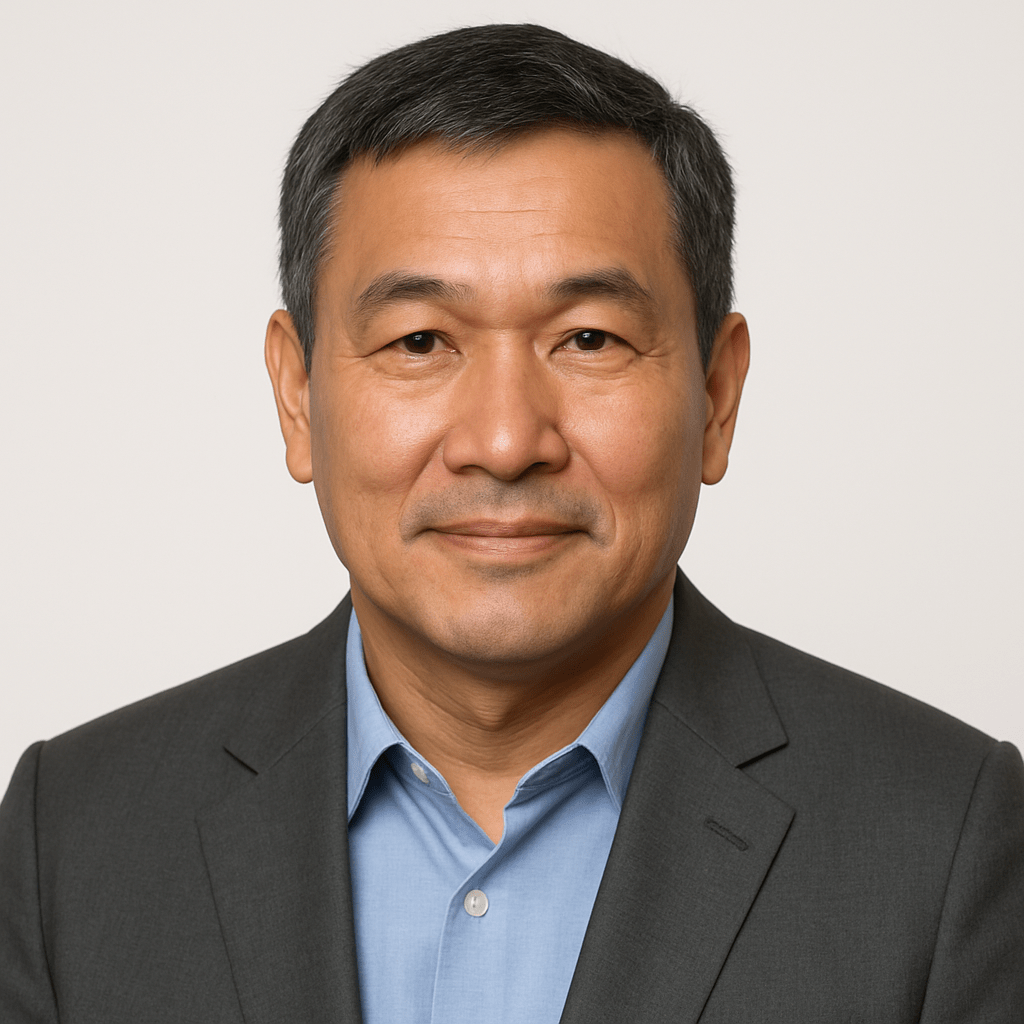
Ayan Sadyk is a materials scientist and process engineer with over two decades of experience in the industrial diamond tooling sector. His expertise lies in integrating ultra-thin diamond blades, CBN wheels, and advanced cutting systems into precision manufacturing workflows for applications in optics, semiconductors, and technical ceramics.
With a background in materials behavior and surface integrity, Mr. Sadyk brings a data-driven, application-specific approach to cutting and grinding process development. He has worked closely with manufacturers and R&D facilities across Eastern Europe, North America, and the Middle East, helping optimize tool life, surface finish, and process stability.
As an author, he focuses on bridging materials science with tooling innovation—writing on topics such as blade wear mechanisms, thermal effects in hard material sectioning, and adaptive process design.
ARE YOU USING RIGHT DIAMOND & CBN BLADES
FOR YOUR APPLICATION?
LET US
HELP YOU
HAVING ISSUES WITH
YOUR CURRENT DIAMOND & CBN BLADES?
Knowledge Center
Select right Diamond Blade for your application
How to Properly Use Precision Diamond & CBN Blades
Precision & Ultra Thin Diamond Blade Guide
How to Improve & Optimize Your Diamond Sawing Operation
Evaluating & Comparing Diamond Blades
Diamond & CBN Cutting Blade Performance Metrics that you Should Know
Total Cost of Ownership & Why its Important
Understanding Tradeoffs- Searching for Perfect Diamond & CBN Blade
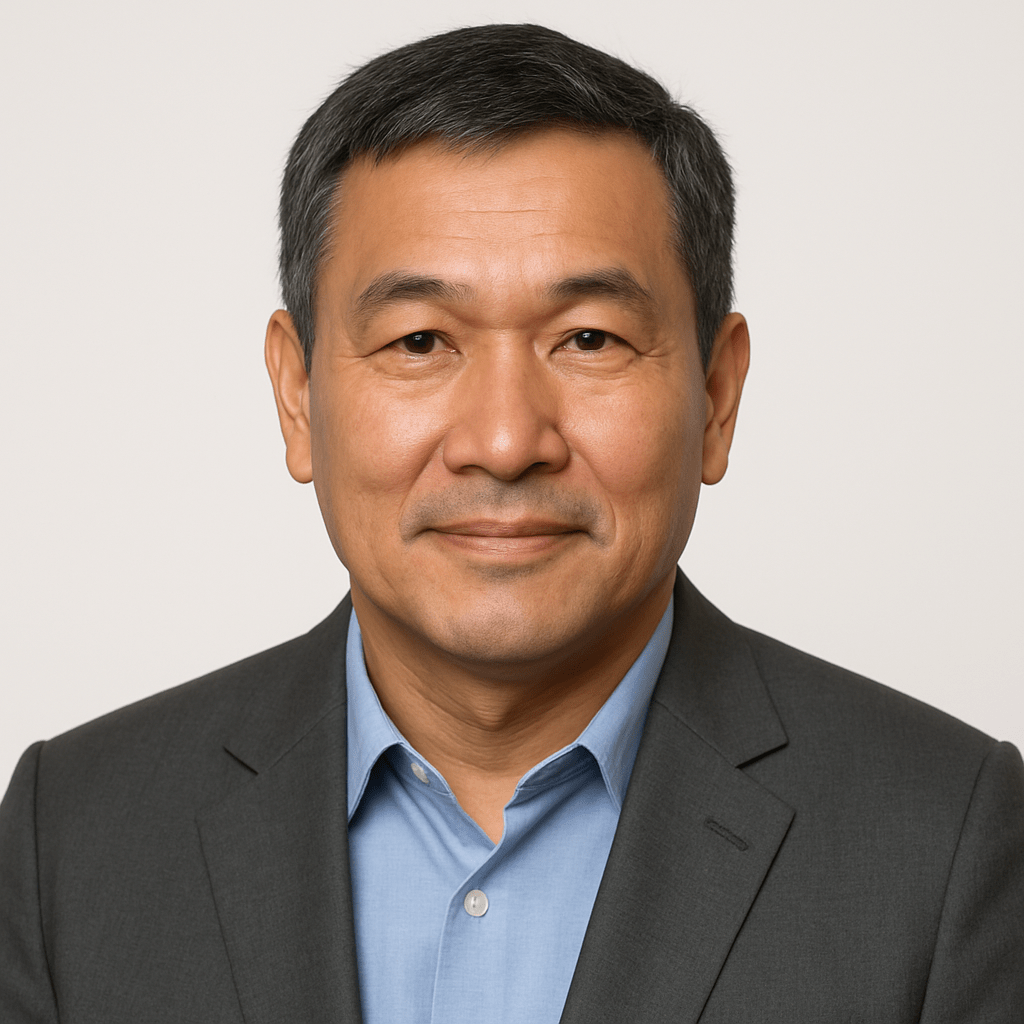
Ayan Sadyk is a materials scientist and process engineer with over two decades of experience in the industrial diamond tooling sector. His expertise lies in integrating ultra-thin diamond blades, CBN wheels, and advanced cutting systems into precision manufacturing workflows for applications in optics, semiconductors, and technical ceramics.
With a background in materials behavior and surface integrity, Mr. Sadyk brings a data-driven, application-specific approach to cutting and grinding process development. He has worked closely with manufacturers and R&D facilities across Eastern Europe, North America, and the Middle East, helping optimize tool life, surface finish, and process stability.
As an author, he focuses on bridging materials science with tooling innovation—writing on topics such as blade wear mechanisms, thermal effects in hard material sectioning, and adaptive process design.