-
0 items in quote
No products in the Quote Basket.
SMART CUT® XP
Water Soluble Dicing Coolant / Lubricant / Surfactant
SMART CUT® XP Water Soluble Dicing Coolant added to deionized (DI) water reduces surface tension flowing from saws injection system and is carried directly of dicing blade.
This reduces material thermal stress, edge damage, and internal cracking, assuring long-term integrity of material being processed. Since SMART CUT® XP Dicing Coolant is a coolant and lubricant, and Surfactant both the dicing blade and substrate / wafer / package benefit.
SMART CUT® XP Dicing Coolant/Lubricant is a specially formulated low-foaming dicing and sawing coolant/lubricant designed for precision applications involving wafers with integrated circuits, MEMS devices, and IC packaging. This aqueous-based synthetic formulation enhances the dicing process by ensuring superior cleanliness of the die or package after dicing while preventing corrosion and oxidation on exposed metals. It eliminates electrostatic discharge, which can be generated during the rotation of the dicing blade, protecting delicate components from damage.
DESCRIPTION
SPECIFICATIONS
FREQUENTLY ASKED QUESTIONS
INDUSTRIES USED IN
ACCESSORIES
USAGE RECOMMENDATION
DESCRIPTION
By effectively lubricating and cleaning the blade’s diamond matrix, SMART CUT® XP ensures the blade cuts freely and wears evenly, extending its lifespan and maintaining optimal cutting performance. As wafer sizes increase and dicing cycles lengthen, the role of an advanced lubricant like SMART CUT® XP becomes even more critical in maintaining efficiency and precision.
Stream of SMART CUT® XP Dicing Coolant/Lubricant added to deionized (DI) water reduces material thermal stress, edge damage, and internal cracking, assuring long-term integrity of material being cut. Since SMART CUT Dicing Coolant is both coolant and lubricant, both the dicing blade and material benefit.
As a coolant, SMART CUT® XP KOOL reduces heat caused by friction. As a lubricant, SMART CUT® XP KOOL lowers friction and surface tension, which increases swarf dispersion.
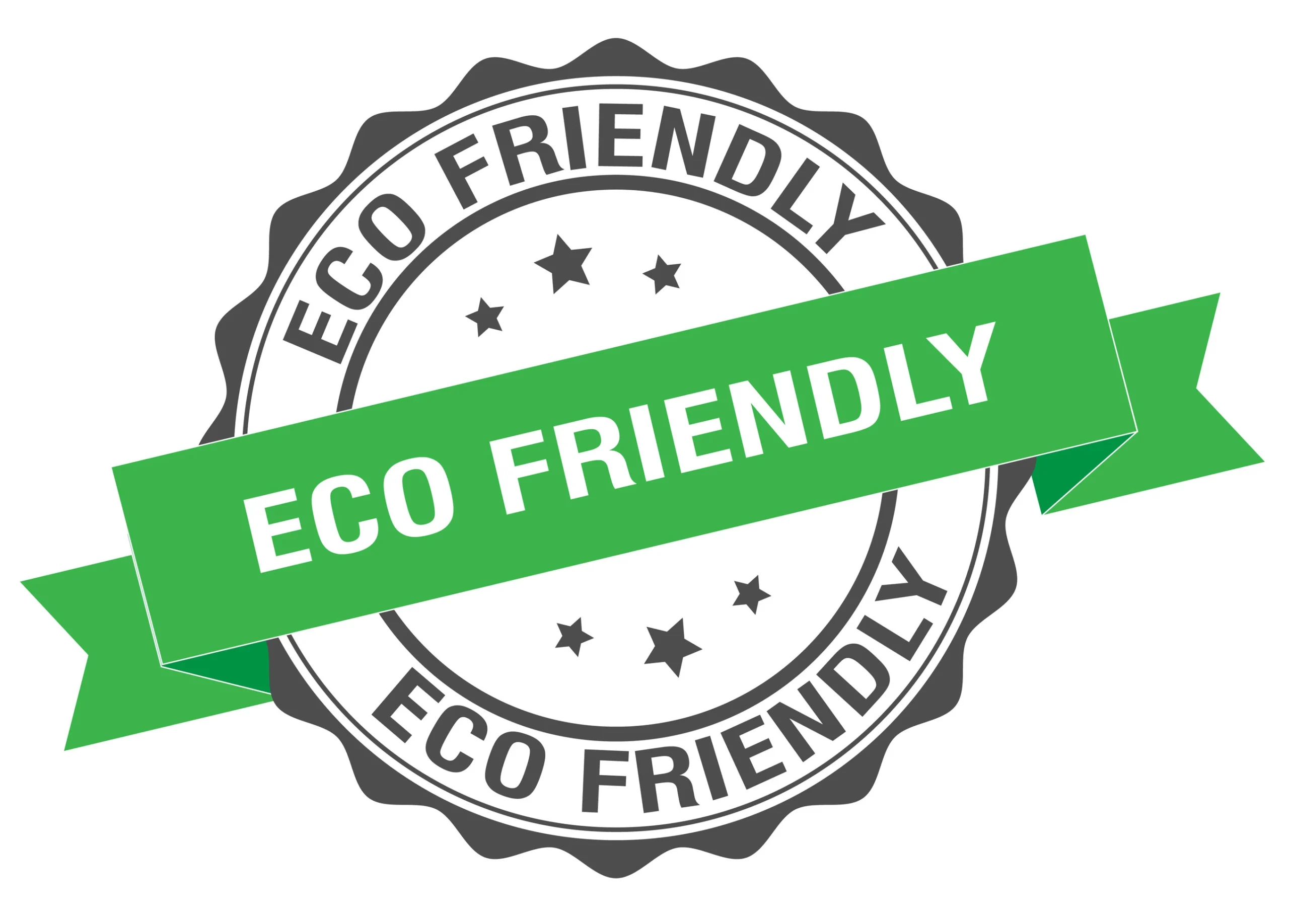
SMART CUT® XP Dicing Coolant/Lubricant contains no nitrides, phosphates, chromates, phenols, heavy metal salts, Petroleum oils, chlorine or phosphorus. Do not add inorganic nitrates, nitrites, or organic-nitro compounds.
Advanced in technology require smaller devices. As the size of devices decrease, the size of wafers overall have increased. This creates additional challenges for package and wafer manufacturers to increase production output and speed, while reducing product cost. SMART CUT® XP water soluble coolant/lubricant has been specifically formulated for this purpose.
In dicing, the wafer is mounted in a frame and placed under the saw. The blades rotates at 30K–60K RPM to cut a slot through the space between the die (known as a street) while using a dicing fluid/water mixture. Once all the die are singulated, the frame is rinsed or cleaned and the individual die are removed for packaging.
As wafers become larger and thicker, the time it takes to dice them into individual die increases. Subsequently, extended exposure to coolant during a dicing process increases the risk of corrosion and the formation of oxide, making bonding more difficult and device failure more prevalent. Thicker wafers and narrower streets can lead to chipping and cracking especially when using harder, thinner blades, resulting in device failure and decreased yield. Kerf material generated during dicing can stick to the bond pads making for difficult packaging/cleaning downstream. The use of a specialized dicing fluid, at economical dilution ratios of The mix ratio for SMART CUT® XP is between 0.10% and 0.25% coolant with DI water., will inhibit corrosion, keep the die clean, extend wheel life and decrease chipping and cracking for a dramatic increase in yield. Using SMART CUT® XP water soluble dicing fluid also eliminates the need for a CO2 injector and protects against electrostatic discharge (ESD).
SMART CUT® XP minimizes foaming issues that can interfere with the cutting process. Its economical usage, requiring only a low concentration when mixed with deionized water, makes it a cost-effective solution for manufacturers. The formulation is completely biodegradable, safe, and non-toxic, making it easy to implement in any facility while ensuring environmental responsibility.

With its ability to support longer dicing cycles, maintain blade integrity, and provide superior surface cleanliness, SMART CUT® XP is an essential component in achieving high-quality, defect-free cuts in advanced semiconductor and electronic packaging applications.
SPECIFICATIONS
- pH: 6.5
- Conductivity: 0.3 mS
- Specific Gravity: 1.01
- Formulation: Aqueous-based synthetic lubricant
- Concentration for Use: 0.10% – 0.25% in deionized (DI) water
- Foam Characteristics: Low-foaming, designed for high-pressure saw coolant spray nozzles
- Environmental & Safety Features: Biodegradable, non-toxic, and non-corrosive
- Packaging Options: Available in 5-gallon pails and 55-gallon drums
- Application Method: Recommended for use with an injection pump system for precise dosing
- Appearance: Clear liquid
- Solubility: Fully miscible with deionized (DI) water
- Dilution Ratio: 1 part coolant to 399–999 parts water (0.10% – 0.25%)
- Cooling Efficiency: Optimized for high thermal conductivity, reducing heat buildup and thermal stress
- Blade Compatibility: Suitable for all types of diamond and CBN dicing blades, ensuring consistent lubrication and extended blade life
- Material Compatibility: Safe for use with silicon wafers, compound semiconductors, MEMS, IC packaging materials, glass, ceramics, and other advanced substrates
- Filtration System Compatibility: Works with standard filtration setups, including fine mesh and ultra-filtration systems, without causing clogging or residue buildup
- Residue-Free Performance: Does not leave films, deposits, or staining on dicing surfaces or equipment
- Shelf Life: Stable under normal storage conditions; recommended to be stored in a cool, dry environment
FREQUENTLY ASKED QUESTIONS
No. SMART CUT Dicing Coolant was specifically designed and developed for semiconductor industry. While soaps leave residues and an cause contamination, SMART CUT Dicing Coolant rinses free, without concern of sodium’s and other ingredients that may contaminate delicate circuitry. Yes proper filtration will not affect SMART CUT Dicing Coolant performance. SMART CUT Dicing Coolant is homogeneous mixture that will not settle during storage. Shelf life is indefinite. However as will al materials we suggest rotation your inventory. A standard metering pump, commercially available can be retrofitted into the dicing saw water lines. Optimum dilution rates are best determined in house. Every application and customer preference is different. For best results we recommend 100:1 dilution ration. Some customers have used higher dilution ratios, with good success. SMART CUT Dicing Coolant is compatible with all semiconductor materials such as silicon, GaAs, Inp, or ceramic wafers. As well as majority of semiconductor packages used today such QFN and BGA, and many others. Excessive concentration of coolant is detrimental to material and waste of resources. Most internal water supplies of most organizations measure approximately seventy dynes of surface tension. When dicing and back grinding wafers and packages the dynes should be targeted for the forty five to fifty range. Coolants can only lower surface tension to a specific amount. Therefore adding more coolant concentration will only cause excessive foaming and residual build up on the wafer. Also some microelectronic packages and semiconductor wafers have copper present in the package or the photo mask operation. High concentration of coolant will react with the copper, and oxidation process can develop. General oxidation problems will arise on the bon pads. However, the proper amount of coolant as recommended by coolant manufacturer, will pose no oxidation problems. To avoid undesired die bonding problems, the sure to thoroughly rinse the water after the dicing procedure is complete. Again the use of a quality coolant will assist in wafer cleaning and removal of the slurry film build up. Additionally it is recommended to consult with the die bonding engineers to receive feedback on the consistency of their process. Sometimes the inability to standardize die bonding parameters and capillaries can be attributed to dirty wafers, specifically dirty bond pads. SMART CUT® Water Soluble Dicing Coolant is a coolant and lubricant solution designed for dicing applications. It is added to deionized (DI) water to reduce surface tension, decrease thermal stress, and minimize edge damage and internal cracking during the dicing process. SMART CUT® Dicing Coolant reduces material thermal stress, edge damage, and internal cracking, helping to maintain the long-term integrity of the material. It acts as both a coolant, lowering friction and heat, and a lubricant, improving swarf dispersion. Yes, SMART CUT® Dicing Coolant is formulated with operator-friendly additives that do not irritate the skin, eyes, or nasal passages. It also contains biocides and fungicides to prevent bacterial and fungal growth in the coolant system. Yes, SMART CUT® Dicing Coolant is compatible with all filtration systems and can be used with various types of dicing blades, including diamond blades, to improve performance and blade life. The coolant helps reduce surface tension and increases swarf dispersion, which helps prevent heat buildup and internal cracking. It also protects the material from corrosion and minimizes the risk of bonding issues or device failure. By lowering friction and thermal stress, SMART CUT® Dicing Coolant ensures that the dicing blade runs cooler, which reduces fatigue and blade wear. This prevents chipping, cracking, and other edge damage that could affect material yield. SMART CUT® Dicing Coolant is recommended to be mixed with water at a dilution ratio of 100 parts water to 1 part coolant (100:1). Yes, SMART CUT® Dicing Coolant can eliminate the need for a CO2 injector while still providing protection against electrostatic discharge (ESD). SMART CUT® Dicing Coolant helps maintain precise tolerances by dissipating heat at the point of contact between the dicing blade and the material, preventing thermal deformations that could affect the blade and material. Yes, SMART CUT® Dicing Coolant is suitable for recycling, especially in large central systems, thanks to its biocides and fungicides that control the growth of bacteria and fungi. SMART CUT® Dicing Coolant is widely used in semiconductor, package, and wafer manufacturing industries, particularly in applications involving dicing of thin, hard materials such as wafers and substrates. No, SMART CUT® Dicing Coolant does not leave a sticky or hard-to-remove residue on the material or equipment. The residue is easily dissolved in water, ensuring a clean and efficient operation. SMART CUT® Dicing Coolant is safe to handle and dispose of, following normal disposal guidelines for non-hazardous waste. It should be stored in a cool, dry area away from direct sunlight and extreme temperatures. SMART CUT® Dicing Coolant is superior due to its combination of lubrication and cooling properties, which work together to extend blade life, reduce edge damage, and improve material yield. Unlike many other coolants, it also provides corrosion protection and is safe for both the operator and the environment. Yes, SMART CUT® Dicing Coolant is versatile and effective in both high-speed (30K–60K RPM) and low-speed dicing applications. It helps reduce heat and friction, providing excellent lubrication and cooling in various cutting conditions. SMART CUT® Dicing Coolant is formulated to protect sensitive materials from damage during the cutting process. It minimizes thermal stress, reduces the risk of cracking, and prevents material degradation, making it ideal for processing delicate materials like advanced ceramics, semiconductors, and wafers. SMART CUT® Dicing Coolant should be stored in a cool, dry area away from direct sunlight and extreme temperatures. Proper storage conditions will help maintain its stability and performance over time. It should be kept in tightly sealed containers to avoid contamination. The effectiveness of SMART CUT® Dicing Coolant can be monitored by checking its clarity, color, and viscosity. If the coolant becomes discolored, cloudy, or too thick, it may need to be replaced. Additionally, if performance such as cooling efficiency or lubrication diminishes, it’s time for a change. Yes, SMART CUT® Dicing Coolant is compatible with both manual and automated dicing machines. Its superior lubrication and cooling properties ensure optimal performance, whether you are operating small manual systems or large, high-speed automated machines. Yes, SMART CUT® Dicing Coolant can help reduce maintenance costs by preventing corrosion and wear on dicing blades and machinery. Its formulation reduces friction, lowering the likelihood of breakdowns and costly repairs, which leads to more efficient operation and reduced downtime. SMART CUT® Dicing Coolant helps improve the cleanliness of the work environment by dispersing swarf more effectively, preventing accumulation on blades and in the machine. This reduces the need for extensive cleaning and maintenance of the work area and equipment. SMART CUT® Dicing Coolant is specifically formulated for cutting applications, such as dicing and wafer singulation. While it is not designed for polishing, its lubrication and cooling properties may provide temporary benefits in certain polishing processes, but it is recommended to use a separate coolant designed for polishing for optimal results. SMART CUT® Dicing Coolant offers several advantages over petroleum-based coolants, including being more environmentally friendly, non-corrosive, and safe to handle. It also provides better lubrication and cooling performance without leaving harmful residues or causing contamination. No, SMART CUT® Dicing Coolant is compatible with all filtration systems. It is designed to perform optimally with existing filtration systems, ensuring that any contaminants such as swarf or dirt are removed efficiently without affecting coolant performance. While SMART CUT® Dicing Coolant is primarily designed for use with diamond dicing blades, its lubricating and cooling properties can also be beneficial for other types of cutting tools, such as those used in grinding or sawing, provided the materials being cut are suitable for this type of coolant. SMART CUT® Dicing Coolant helps preserve the true microstructure of materials by reducing thermal stress during the cutting process. This results in fewer distortions and defects in the material’s microstructure, leading to higher-quality cuts and better overall performance. SMART CUT® Dicing Coolant does not have a strict expiration date, but its performance can degrade over time due to contamination or prolonged exposure to high temperatures. Regular maintenance, monitoring, and replacing the coolant when necessary will ensure consistent performance. SMART CUT® Dicing Coolant is specifically designed for wet cutting applications, where it is mixed with water to provide cooling and lubrication. It is not suitable for dry cutting applications, where no coolant is used, as it depends on the presence of water to deliver its benefits. SMART CUT® Dicing Coolant is formulated to perform under extreme cutting conditions, such as high-speed dicing or when cutting harder materials. Its ability to reduce friction and dissipate heat allows it to maintain stable performance and help protect both the blade and the material from damage. Using too much or too little SMART CUT® Dicing Coolant can negatively impact its performance. Too little coolant may lead to insufficient lubrication and cooling, while too much can result in excessive foam or residue buildup. It is important to use the recommended dilution ratio (100:1) for optimal results. SMART CUT® Dicing Coolant helps protect against electrostatic discharge (ESD) by preventing the buildup of static electricity during the dicing process. Its ability to bond with water molecules and provide lubrication reduces the chances of ESD-related damage to sensitive materials and devices. Yes, SMART CUT® Dicing Coolant is designed to be compatible with a wide range of saws and cutting machines, including both manual and automated systems. It works effectively with diamond, metal, and other types of blades used for dicing and cutting applications. Yes, SMART CUT® Dicing Coolant performs well in high-speed dicing applications, including those operating at speeds of 30K-60K RPM. It helps manage the increased heat and friction generated at high speeds, ensuring that the cutting process remains efficient and the material remains protected. Yes, SMART CUT® Dicing Coolant helps reduce microcracking by lowering the temperature at the cutting interface and minimizing thermal stress. The improved lubrication also ensures a smoother cut, which reduces the risk of cracks forming within the material. SMART CUT® Dicing Coolant is specifically formulated to perform well with hard, brittle materials. It improves lubrication and cooling, which reduces blade wear and helps maintain sharpness, thus ensuring longer blade life and more precise cuts. SMART CUT® Dicing Coolant is environmentally friendly and can be safely disposed of by following local environmental and waste disposal regulations. It is biodegradable and does not contain hazardous substances such as petroleum oils, heavy metals, or chlorides, making disposal less problematic compared to traditional coolants. No, SMART CUT® Dicing Coolant is free of nitrides, phosphates, chromates, phenols, heavy metals, petroleum oils, chlorine, and phosphorus. This makes it safer for both operators and the environment compared to many other industrial coolants. SMART CUT® Dicing Coolant is formulated to perform effectively in a range of temperatures. In extremely low temperatures, however, the coolant may thicken or freeze. It is recommended to store the coolant at room temperature to ensure optimal performance. Yes, SMART CUT® Dicing Coolant helps prevent the formation of heat-affected zones (HAZ) by efficiently dissipating heat during the cutting process. This ensures that the material’s integrity is maintained and reduces the risk of heat-induced damage. The correct concentration for SMART CUT® Dicing Coolant is a dilution ratio of 100 parts water to 1 part coolant (100:1). If unsure, you can perform tests on the coolant’s performance in your specific application and adjust the concentration as needed. Consult the manufacturer’s guidelines for specific recommendations. SMART CUT® Dicing Coolant has a long shelf life when stored under proper conditions, such as in a cool, dry place and in tightly sealed containers. However, it is recommended to use the coolant within 1-2 years of purchase for optimal performance. Yes, SMART CUT® Dicing Coolant can be used in cutting various hard materials such as glass and ceramics, in addition to wafers and semiconductors. Its cooling and lubricating properties make it suitable for cutting a wide range of materials without damaging the substrate. Yes, SMART CUT® Dicing Coolant is designed to reduce thermal stress and cracking, which improves yield in high-precision dicing applications. By providing better cooling and lubrication, it helps maintain the integrity of the material and the dicing blade, leading to higher-quality cuts and fewer defects. Yes, regular maintenance is necessary to ensure that the coolant system remains clean and operates efficiently. It’s important to monitor the coolant’s concentration, check for contamination, and replace it when necessary to maintain its optimal performance. Yes, SMART CUT® Dicing Coolant is ideal for applications that require fine tolerances. By reducing heat at the point of contact between the blade and material, it prevents deformations, helping maintain precise cutting dimensions and achieving high-quality results. Yes, SMART CUT® Dicing Coolant is compatible with closed-loop recycling systems, making it an environmentally sustainable option for large-scale manufacturing environments. It can be filtered and reused, helping to reduce waste and improve overall system efficiency. SMART CUT® Dicing Coolant improves cutting speed by reducing friction and heat buildup, allowing the blade to cut through materials more efficiently. This not only speeds up the process but also reduces wear on the blade, extending its lifespan and maintaining optimal cutting performance. No, SMART CUT® Dicing Coolant is non-staining, meaning it does not affect the color or appearance of the material. It is safe for use with sensitive materials, including those with light or transparent finishes, and helps maintain the material’s integrity. Yes, SMART CUT® Dicing Coolant is formulated to be stable in all water conditions, including hard water with high mineral content. Its performance is not significantly affected by hard water ions, making it suitable for a wide range of applications. By providing superior lubrication and cooling, SMART CUT® Dicing Coolant reduces friction between the blade and the material, lowering the temperature of the blade and preventing excessive wear. This helps reduce blade fatigue, leading to longer blade life and more consistent cutting performance.
INDUSTRIES USED IN
- 1 (one) Quart Bottles
- 1 (one) Gallon Bottles
- 5 (five) Gallon Pails
- 55 Gallon Drums
ACCESSORIES
Tab Content
USAGE RECOMMENDATION
1. Chemical Metering Pump:
There are many types of chemical metering pumps used for injecting small metered amounts of chemicals into industrial processes. The type most commonly used for feeding SMART CUT® DICING COOLANT/SURFICANT Series products are “solenoid diaphragm metering pumps” with adjustable stroke and frequency. A typical pump is shown below:
The pump should be capable of injecting SMART CUT® DICING COOLANT/SURFICANT Series products at a dilution of between 200:1 – 500:1, into a flow of up to 10 liters per minute of saw water per saw. This would mean for a 10 liter flow, the pump should be capable of injecting 50ml/minute into the saw water line for a dilution ratio of 200 parts water to 1 part SMART CUT® DICING COOLANT/SURFICANT Series product.
The frequency of the stroke and the length of the stroke should be adjusted for output and optimum injection for maximum chemical dissolution in the saw water line prior to use.
Typical solenoid diaphragm metering pumps that would meet the specification for a single saw are:/p>
- Neptune Pumps, Series PZiA
- Pulsatron Pumps, Series D, Series E, Series MP
- LMI Milton Roy Pumps, Series C
However, users should choose a pump that best suits the equipment and configuration in use.
2. Back Pressure Control Valve:
When line pressure (saw water feed line) is under 20 psi, atmospheric or erratic, inaccurate feed can result. A back-pressure control valve provides constant pressure for the discharge check assembly on the metering pump to operate properly. These back-pressure valves also provide anti-siphoning protection.
3. Calibration Cylinders:
Calibration cylinders should be installed on the suction end of the pump to insure that the pump is properly calibrated to start and to provide an easy method of checking flow periodically. Some pumps are now equipped with automatic flow calibration attached to the pump for ease of use and installation.
4. Injection Valve:
SMART CUT® DICING COOLANT/SURFICANT Series products should be injected into the saw water line via an injection valve comparable to the size of the tubing. Most metering pumps include an injection valve that also functions as a back-pressure valve/check valve.
5. Static Mixer:
A static mixing line approximately 30 cm should be installed after the injection quill to also insure complete mixing of SMART CUT® DICING COOLANT/SURFICANT Series products with the saw water prior to use.




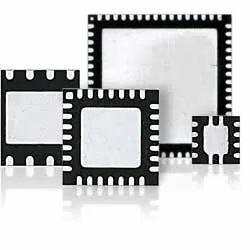




SMART CUT® Dicing Fluid
Available in 4 Different Formulas to Fit Most Dicing Applications
XP-1 is a general-purpose dicing fluid within the SMART CUT® range, designed to reduce debris, improve tool life, and prevent corrosion, while ensuring smooth cutting and protecting sensitive materials from ESD.
XP-2 enhances lubrication for demanding applications, offering superior cutting speeds, tool longevity, and advanced cleaning capabilities for tough materials like SiC and sapphire.
XP-3 is ideal for high-pressure systems, offering consistent cooling performance without foam buildup.
XP-4 specifically protects electrostatic-sensitive components by eliminating ESD, reducing defects, and extending tool life during the dicing process.
SMART CUT Coolant (General Materials Formula) - versatile, general-purpose coolant, used for dicing ultra hard and brittle materials such as ceramics, optics, quartz, silicon, and other hard materials.
Why Work With Us?
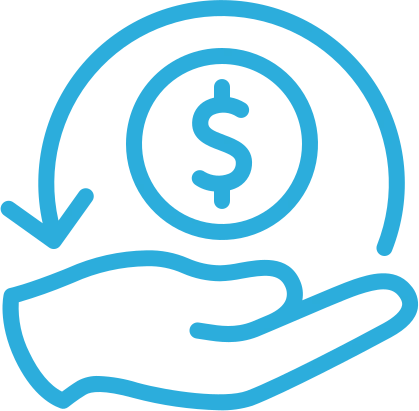
Best Return
on Investment
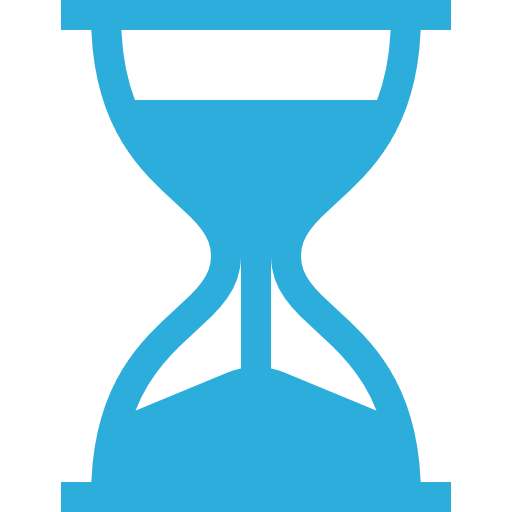
Attractive Cost of
Ownership
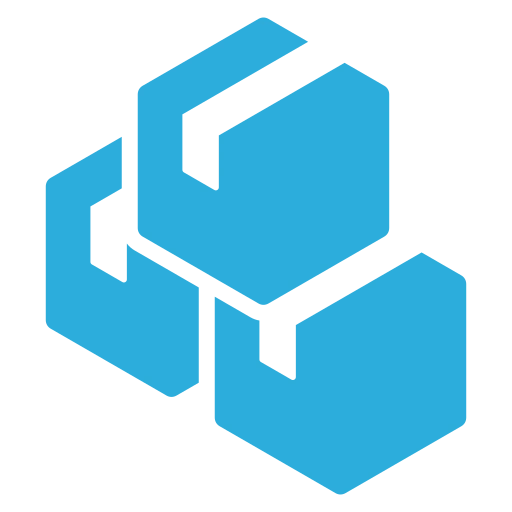
Thousands of Diamond & CBN Blades in stock
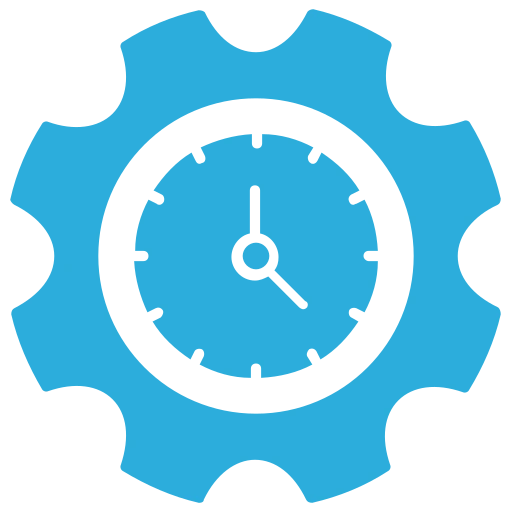
Custom Manufacturer with Fast Lead times
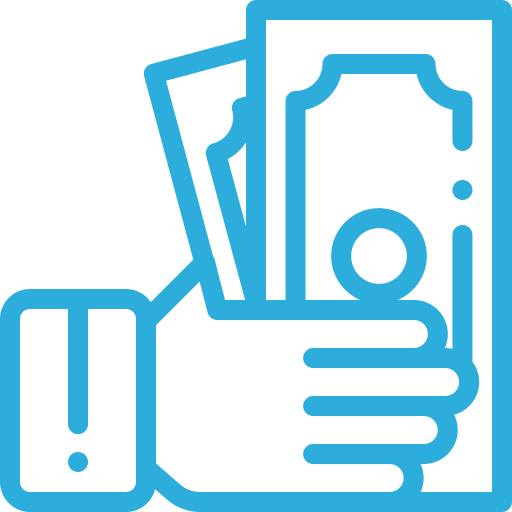
Unmatched
Prices in North America
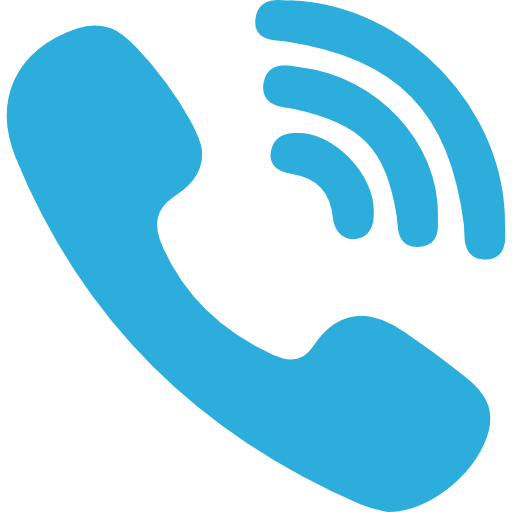
Unmatched Experience & Technical Support
Features
- Ensures superior cleanliness of the die or package after dicing, reducing post-processing requirements.
- Prevents corrosion and oxidation on exposed metals, protecting delicate electronic components.
- Eliminates electrostatic discharge during dicing, reducing the risk of component damage.
- Lubricates and cleans the blade’s diamond matrix, ensuring free cutting and even wear over its lifespan.
- Designed for high-pressure saw coolant spray nozzles, minimizing foaming issues that can disrupt the process.
- Supports extended dicing cycles for larger and more complex wafers, improving overall efficiency.
- Requires only a low concentration when mixed with DI water, making it cost-effective.
- Completely biodegradable, making it environmentally friendly and easy to dispose of safely.
- Safe and non-toxic, ensuring a hazard-free working environment for operators.
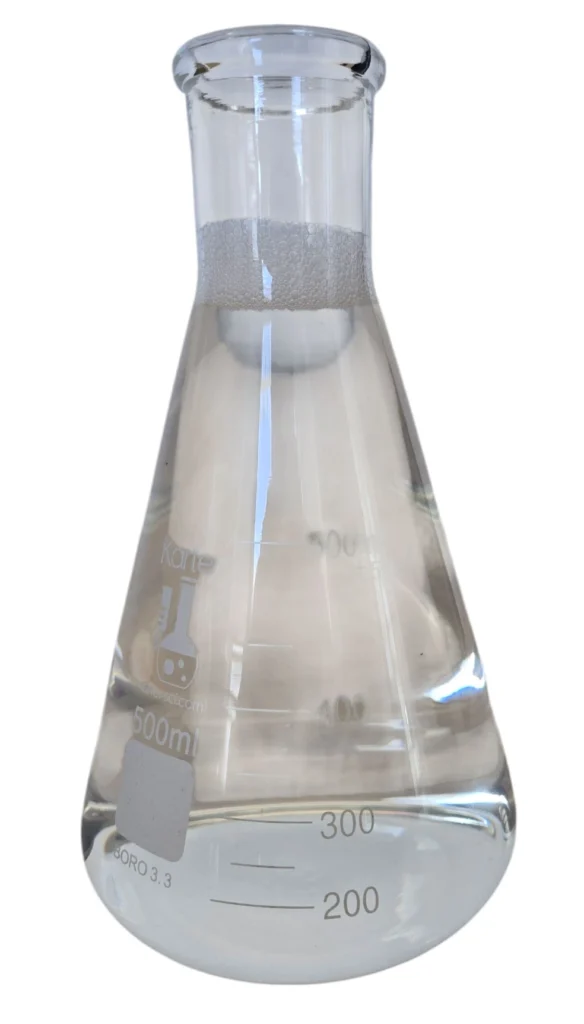

Advantages
- Improve Cutting Speed, Yield, & Efficiency – Enhances material removal rates, reducing cycle times and increasing overall production efficiency.
- Improved Cut Quality – Minimizes defects, edge chipping, and micro-cracks, leading to higher yield and reduced material waste.
- Longer Blade Life – Reduces blade wear by optimizing lubrication, lowering replacement costs and improving cost efficiency.
- Superior Cooling Performance – Effectively dissipates heat, preventing thermal damage to wafers and maintaining dimensional accuracy.
- Non-Staining – Does not leave residue or discoloration on wafers or packages, ensuring clean and uncontaminated surfaces.
- Preserve Material True Microstructure – Prevents unwanted changes in material properties, maintaining structural integrity and original composition.
- Non-Corrosive – Safe for all machine components and materials, preventing damage to equipment and delicate substrates.
- Compatible with All Filtration Systems – Works seamlessly with both standard and high-efficiency filtration systems without causing clogging or requiring special maintenance.
- No Foam – Specifically formulated for use in high-pressure saw coolant spray nozzles, ensuring uninterrupted coolant flow and preventing foaming issues.
- Reduce Chipping and Thermal Stress – Provides stable lubrication and cooling to prevent heat buildup, reducing stress fractures and surface defects.
- Reduce Material Micro-Cracking & Edge Damage – Minimizes stress-induced fractures, ensuring smoother edges and reducing scrap rates.
- Better Material Compatibility – Works efficiently with a variety of materials, including delicate semiconductor wafers, IC packages, and MEMS devices.
- Lower Operational Costs – Requires minimal concentration, reducing coolant consumption while maintaining performance.
- Safer Work Environment – Non-toxic and biodegradable, eliminating risks associated with hazardous chemicals and improving workplace safety.
- Easier Waste Disposal – Being completely biodegradable, it meets environmental regulations and simplifies disposal procedures.
- Scalability for High-Volume Production – Supports extended dicing cycles without performance degradation, making it suitable for high-throughput manufacturing.
SMART CUT® XP-1: Standard Dicing Fluid

XP-1 is the standard water-soluble dicing coolant formulated to meet the needs of most dicing applications and backgrinding applications. This specially-formulated chemical product combines detergent, coolant, lubricant, and corrosion inhibitor functions. It helps reduce debris during the dicing process, improves tool life, and ensures smooth cutting with minimal tool wear. The product acts as a detergent to reduce saw debris, simplifying or eliminating the need for post-process cleaning. Additionally, it helps reduce heat and stress on the die or package, while keeping blades free-cutting, improving cutting speed and tool life. The corrosion inhibitors prevent oxide formation and corrosion on exposed metal pads, improving bonding and connectivity. Furthermore, XP-1 adds conductivity to DI water, eliminating the risk of electrostatic discharge (ESD) during the dicing process, making it ideal for sensitive materials. With its low Chemical Oxygen Demand (COD), XP-1 is an environmentally friendly option that contributes to sustainability and safer disposal.
Application:
XP-1 is suitable for general-purpose dicing of materials such as semiconductors, ceramics, glass, and precision tasks. It is ideal for routine use in high-precision applications where cooling, lubrication, and corrosion prevention are critical.
Features:
- Debris Reduction: Acts as a detergent to reduce saw debris, making post-process cleaning simpler or unnecessary.
- Cooling & Lubrication: Reduces heat and stress on die or package while keeping blades free-cutting, which improves cutting speed and tool life.
- Corrosion Prevention: Contains corrosion inhibitors that prevent oxide formation and corrosion on exposed metal pads, improving bonding and connectivity.
- Electrostatic Discharge (ESD) Prevention: Adds conductivity to DI water to eliminate the risk of electrostatic discharge (ESD) during the dicing process, ideal for sensitive materials.
- Environmental Impact: XP-1 has the lowest Chemical Oxygen Demand (COD) among commercially available dicing lubricants, contributing to sustainability and safer disposal.
SMART CUT® XP-2: High Lubricity Dicing Fluid
XP-2 is a next-generation version designed for more demanding applications that require enhanced lubricity and improved cleaning capabilities. It provides superior lubrication, reduces friction, and maintains cutting blade performance even under high load or high-speed conditions. XP-2 also contains an effective corrosion inhibitor to minimize oxide formation. The high lubricity of XP-2 reduces friction and heat during high-speed or high-load cutting, allowing for faster cutting speeds and extended tool life. The enhanced surfactants in the product improve the removal of cutting debris, especially in challenging materials like bonded wafers, sapphire, and SiC. Effective corrosion inhibition prevents oxide growth and protects metal pads, improving device bonding and connectivity. XP-2 also helps eliminate ESD effects by adding conductivity to DI water, ensuring the protection of sensitive components during the cutting process. With a low COD value, XP-2 is an environmentally friendly choice, contributing to safer disposal.
Application:
XP-2 is perfect for high-speed dicing and back-grinding of tough materials like advanced ceramics and SiC. It is also ideal for dicing operations that require increased lubrication for smoother cuts and reduced defects, as well as applications that demand advanced cleaning capabilities and improved lubrication.

Features:
- High Lubricity: Reduces friction and heat during high-speed or high-load cutting, allowing for faster cutting speeds and extended tool life.
- Improved Cleaning: Enhanced surfactants improve the removal of cutting debris, especially in challenging materials like bonded wafers, sapphire, and SiC.
- Corrosion Protection: Effective corrosion inhibition prevents oxide growth and protects metal pads, improving device bonding and connectivity.
- ESD Control: Helps eliminate ESD effects by adding conductivity to DI water, protecting sensitive components during the cutting process.
- Environmental Friendly: Low COD value for better environmental compatibility and safer disposal.
SMART CUT® XP-3: Low-Foaming Dicing Fluid
XP-3 is formulated to be low-foaming, making it ideal for use in high-pressure dicing systems or systems that utilize atomizing nozzles. It reduces foam buildup, ensuring consistent flow, cooling performance, and minimizing contamination during the cutting process. The low foaming characteristics of XP-3 prevent foam formation in high-pressure or atomizing nozzle systems, ensuring optimal coolant performance without disrupting the cutting process. The surfactants in XP-3 improve the suspension of debris, reducing the risk of re-adherence to the material surface. In addition, XP-3 includes corrosion inhibitors that protect metal surfaces, preventing oxide buildup and reducing bonding issues. It also adds conductivity to the DI water supply to prevent electrostatic buildup, protecting sensitive devices during dicing. The product is biodegradable with a low COD value, making it an eco-friendly choice compared to other lubricants.
Application:
XP-3 is ideal for back-grinding and high-pressure dicing systems that use atomizing or high-pressure nozzles. It is also perfect for low-foam applications in precision dicing of microelectronics and MEMS devices and works well in cleanroom environments or sensitive processes where foam buildup could impact precision.
Features:
- Low Foaming: Prevents foam formation in high-pressure or atomizing nozzle systems, ensuring optimal coolant performance without disrupting the cutting process.
- Enhanced Dispersion: Surfactants improve the suspension of debris, reducing the risk of re-adherence to the material surface.
- Corrosion Resistance: Includes corrosion inhibitors that protect metal surfaces, preventing oxide buildup and reducing bonding issues.
- ESD Prevention: Adds conductivity to the DI water supply to prevent electrostatic buildup, protecting sensitive devices during dicing.
- Sustainability: Biodegradable with a low COD value, making it a more eco-friendly choice compared to other lubricants.
SMART CUT® XP-4: Electrostatic Discharge Sensitive Dicing Fluid
XP-4 is designed specifically to eliminate electrostatic discharge (ESD) effects during the dicing process, ensuring that sensitive materials such as semiconductors and MEMS devices are protected from static damage. This product combines the benefits of cooling, lubrication, corrosion inhibition, and ESD protection in one formula. XP-4 prevents electrostatic discharge, ensuring no shift in threshold voltage after dicing, thus protecting sensitive electronic components. It helps reduce friction and heat during cutting while keeping the blade free-cutting, extending tool life and increasing cutting efficiency. Additionally, XP-4 prevents oxide formation and corrosion on metal pads, which is crucial for maintaining the integrity of connections and device performance. The product’s low COD value ensures it is biodegradable and safer for disposal. XP-4 also reduces defects like chipping, cracking, and de-lamination by maintaining an organic micro-layer cushion between the blade, matrix, and material.
Application:
XP-4 is ideal for dicing electrostatic-sensitive devices such as semiconductors and MEMS. It is used in applications where ESD could lead to irreversible damage, particularly in cleanroom and high-tech manufacturing settings. XP-4 is also suitable for dicing processes that require high lubrication and effective cooling.
Features:
- Eliminates ESD Effects: Specifically formulated to prevent electrostatic discharge, XP-4 ensures no shift in threshold voltage after dicing, protecting sensitive electronic components.
- Superior Lubrication & Cooling: Helps reduce friction and heat while keeping the blade free-cutting, extending tool life and increasing cutting efficiency.
- Corrosion Resistance: Prevents oxide formation and corrosion on metal pads, which is crucial for maintaining the integrity of connections and device performance.
- Environmentally Friendly: The low COD value ensures that the product is biodegradable and safer for disposal.
SMART CUT® Water Soluble Coolant (General Materials Formula)

SMART CUT® Water Soluble Coolant (General Materials Formula) is specifically designed for use in dicing applications. It helps to effectively manage heat during the dicing process, which is critical for preventing thermal stress, cracking, and edge damage to sensitive materials. By reducing friction between the dicing blade and the material, it ensures smoother cuts, extending the life of the dicing and improving cut quality. This coolant also improves cutting efficiency by providing both cooling and lubrication, which leads to more efficient dicing and fewer tool changes.
Application:
The coolant is highly effective for a range of materials commonly used in dicing, including ceramics, optics, quartz, silicon, composites, and metals. For dicing applications, the coolant should be mixed with deionized (DI) water in a dilution ratio of 1:20 to 1:50, depending on the material being cut. For harder materials like silicon carbide (SiC), a ratio closer to 1:50 is recommended, while for ultra-hard materials like sapphire, a ratio of 1:20 ensures optimal performance.
Features:
- Effective Cooling: Reduces heat and prevents thermal stress, cracking, and damage.
- Lubrication: Reduces friction for smoother cuts and improved blade life.
- Versatile Compatibility: Suitable for large variety of ultra hard and bittle materials such as ceramics, optics, quartz, silicon, composites, and metals.
- Improved Cutting Efficiency: Enhances performance and reduces blade wear.
- Surface Finish Enhancement: Provides a smoother, more precise cut.
- Improves Blade Life: Increases blade life and reduces downtime.
- Environmentally Friendly: Bio-resistant and safe for operators.
Dicing Fluid Comparison Table
Aspect |
XP-1 |
XP-2 |
XP-3 |
XP-4 |
---|---|---|---|---|
Description |
Standard dicing fluid for most applications. |
High lubricity fluid designed for increased lubrication. |
Low-foaming fluid for applications where foaming is problematic. |
Designed for applications sensitive to electrostatic discharge. |
Applications |
General dicing of semiconductors, ceramics, glass, and precision tasks. |
Heavy load/high-speed cutting, precision slicing of tough materials like advanced ceramics, and for operations requiring enhanced lubrication. |
Ideal for high-pressure dicing or areas where foam buildup may disrupt the cutting process. Used in cleanroom environments and sensitive operations. |
Used in applications where electrostatic discharge (ESD) can harm components like semiconductors, MEMS, and microelectronics. |
Best For |
General-purpose, routine dicing applications. |
High-speed, high-load, and high-precision cutting. |
Foam-sensitive, high-pressure dicing operations. |
Electrostatic-sensitive materials like semiconductors, microelectronics, and MEMS. |
Lubricity |
Standard |
High |
Moderate |
Standard |
Foaming |
Low |
Low |
Very Low |
Low |
Electrostatic Sensitivity |
No |
No |
No |
Yes |
Recommended Materials |
Common materials like ceramics, glass, semiconductors, and thin metals. |
Tougher materials such as advanced ceramics, composites, and metals. |
Thin-film electronics, microelectronics, and delicate substrates. |
ESD-sensitive materials like semiconductors, ICs, MEMS, and sensitive electronics. |
Cutting Speed |
Moderate |
High |
Moderate |
Moderate |
Blade Wear |
Moderate |
Low |
Moderate |
Moderate |
Cooling Efficiency |
Good |
Excellent |
Good |
Good |
Application Example
Comparing Rates of Oxide Formation
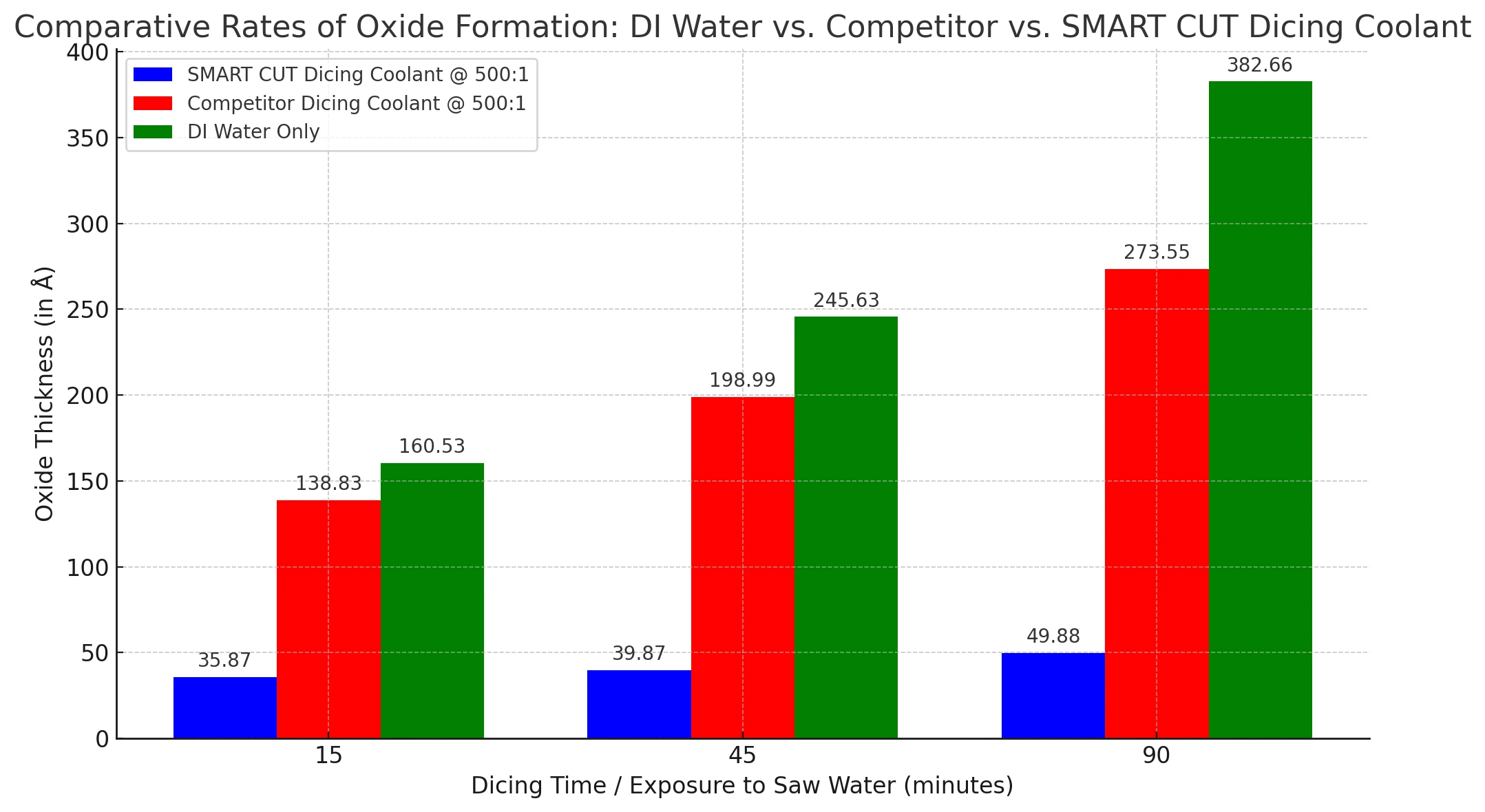
Dicing Time / Exposure to Saw Water (minutes) |
Oxide Thickness (in Å): SMART CUT Dicing Coolant @ 500:1 |
Oxide Thickness (in Å): Competitor Dicing Coolant @ 500:1 |
Oxide Thickness (in Å): DI Water Only |
---|---|---|---|
15 minutes |
35.87 |
138.83 |
160.53 |
45 minutes |
39.87 |
198.99 |
245.63 |
90 minutes |
49.88 |
273.55 |
382.66 |
SMART CUT® XP Dicing Coolant helps Semiconductor Package & Wafer Manufacturers

Reduces Surface Tension - by 25-40 dynes/cm2. SMART CUT KOOL allows more water into the material kerf / pores, dissipating heat generated by friction.
Bonds Water Molecules - into the kerf and to the diamond dicing blade, allowing better swarf dispersion and lubrication.
Prevent Swarf Accumulation - on the diamond dicing blade and in Back and frontside edges, minimizing chipping and internal cracking.
Extend Blade Life - by up to 30%. The lubricated dicing blade runs cooler, reducing fatigue and blade wear.
Improve Material Yield and Reliability - from the reduced amount of chipping, cracking and consequent edge damage.
Eliminate Additional Material Processing . Depending on the application and your objectives, SMART CUT Dicing Coolant frequently eliminates and minimizes secondary and subsequent material processing.
Improved Die Tolerances - Many of today's demanding package singulation and wafering dicing operations require very high precision tolerance. SMART CUT™ Dicing Coolant promotes attainment of close tolerances by removing heat generated at the point of contact between the dicing blade and substrate/wafer. Heat can cause deformations in both the blade and material that results in the loss of tolerance. When the generation of heat and its subsequent removal by a coolant is momentarily interrupted any coolant product will adversely affect the performance of a tool and therefore ruin a tolerance specification.
TOP 10 REASONS Why SMART CUT® XP Coolant is SUPERIOR

- Operator Sensitivity- SMART CUT KOOL is formulated with operator friendly additives that will not irritate skin (dermatitis), nasal passages, or eyes.
- Bio-resistance. SMART CUT KOOL is formulated with biocides and fungicides to biologically control the growth of bacteria, fungi, and mold in the coolant system. The bio-resistance will determine its suitability for recycling in large central systems.
- Corrosion Protection- SMART CUT KOOL is formulated with corrosion inhibitors, which provide protection to machinery and the substrate. The protection needed will be determined by the customers requirements. With proper concentration, no corrosion should occur on the machinery.
- Hard Water Stability- SMART CUT KOOL should be stable in all water conditions. Hard water ions react with coolant additives and reduce the effectiveness of the coolant solution.
- Mixability. Concentrate SMART CUT KOOL should mix easily or .bloom. into the water. Any difficulty in mixing will not be tolerated by the customer.
- Foam- All water based coolants can potentially foam. SMART CUT KOOL is formulated with defoamers to prevent foaming under most conditions. The proper selection of coolant concentration will help alleviate potential problems.
- Residue- SMART CUT KOOL will not leave a .hard-to-remove. residue on the surface of the machine or substrates. As the water in the coolant. evaporates organic residue will be left on the machines. This residue should not be sticky and should be easily re-dissolved in water.
- Oxidative Stability- High temperatures and pressures will cause changes in the composition of the coolant, such as fragmentation or polymerization of the additives in the coolant formulation. This can decrease the performance of the coolant and create difficult to remove deposits.
- Emulsion Stability. Concentrate SMART CUT KOOL mixes easily with water and should not separate or create an invert on the surface of the coolant mixture. Customers currently using soluble oils may be experiencing particular difficulties with this problem.
- Tramp Oil Rejection- SMART CUT KOOL should reject the tramp oils and way lubricants, which may contaminate the sump. Other coolants which do not reject tramp oils are prone to attack by bacteria and fungal organisms.
Case Study: Dicing Silicon Wafers
Material: Silicon wafer
Blade: Nickel bond hubless blade
Blade Specifications: 3” (100 mm) diameter × 0.008” (0.203 mm) thickness × 40 mm arbor, 320 grit diamond
Spindle RPM: 30,000 RPM
Feed Speed: 40 mm/s
Objective:
Evaluate the impact of SMART CUT® XP Dicing Coolant / Lubricant on blade longevity and cutting efficiency compared to using only deionized (DI) water.
Results:
- Blade life increased by 48% when using SMART CUT XP Dicing Coolant / Lubricant at a 0.20% concentration compared to DI water alone.
- More consistent cutting performance maintained over extended operation, reducing blade wear rate.
- Lower diamond matrix wear resulted in improved cutting consistency over the entire blade lifespan.
Conclusion:
Using SMART CUT® XP Dicing Coolant / Lubricant significantly extended blade longevity, reduced tool wear, and improved cost efficiency in high-volume silicon wafer dicing applications.
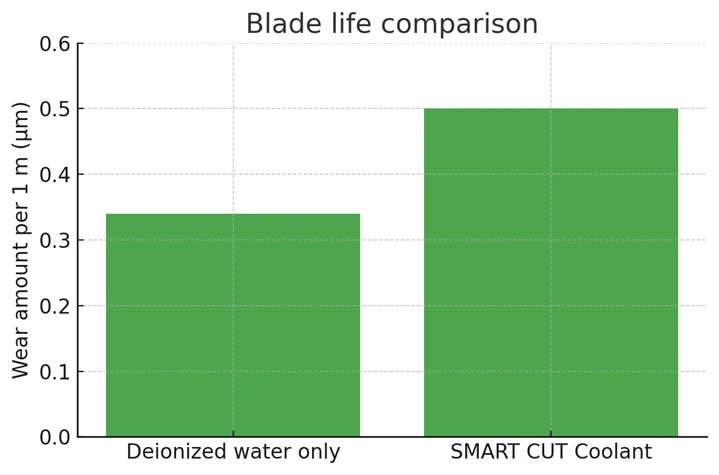
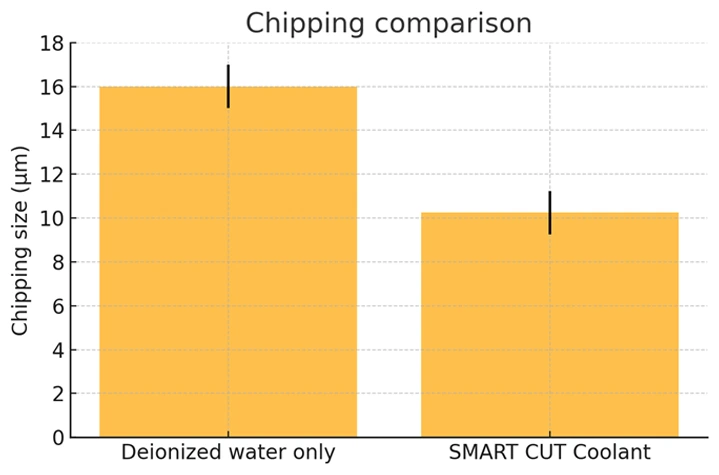
Thermal Stress and Micro-Cracking Reduction in Ceramic Substrate Dicing
Material: Alumina (Al₂O₃) ceramic substrate
Blade: Metal bond dicing blade
Blade Specifications: 4.6” (118 mm) diameter × 0.020” (0.50 mm) thickness × 3.5” (88.9 mm) arbor, 270 grit diamond
Spindle RPM: 6,000 - 8,000 RPM
Feed Speed: 8 - 12 mm/s
Objective:
Determine whether SMART CUT® XP Dicing Coolant / Lubricant reduces thermal stress and micro-cracking during ceramic dicing.
Results:
- Micro-cracking reduced by 38%, improving mechanical strength and final product integrity.
- Lower thermal stress, preventing structural damage in the ceramic and maintaining material properties.
- Blade wear reduced, ensuring longer blade life and consistent cutting performance over extended production runs.
Conclusion:
The use of SMART CUT® XP Dicing Coolant / Lubricant significantly improved cut quality, reduced stress fractures, and enhanced process efficiency for brittle ceramic materials, making it a valuable solution for precision dicing operations.
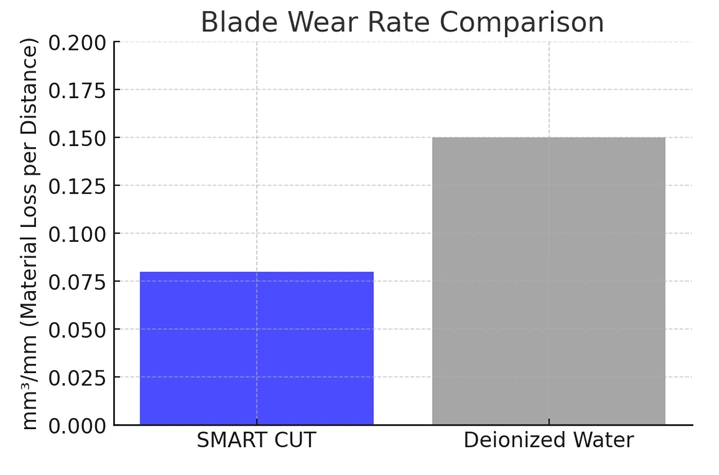
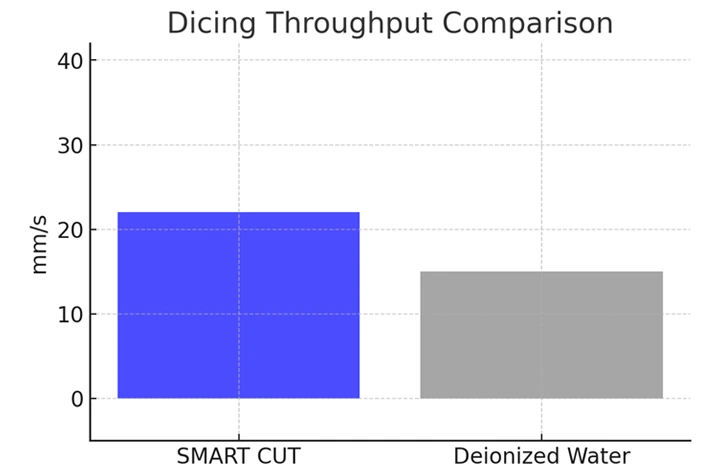
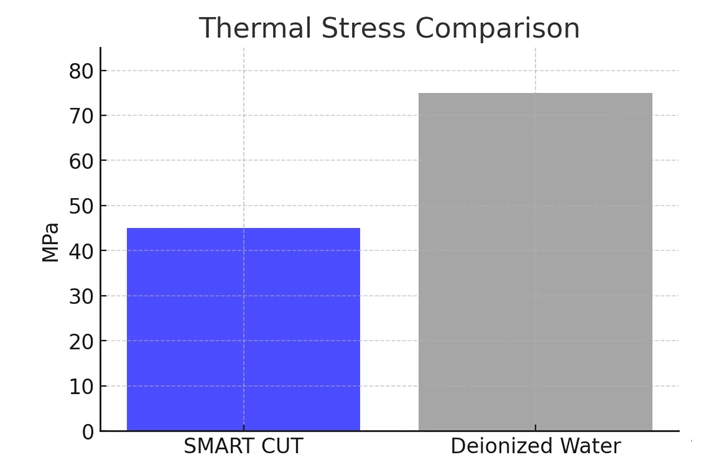
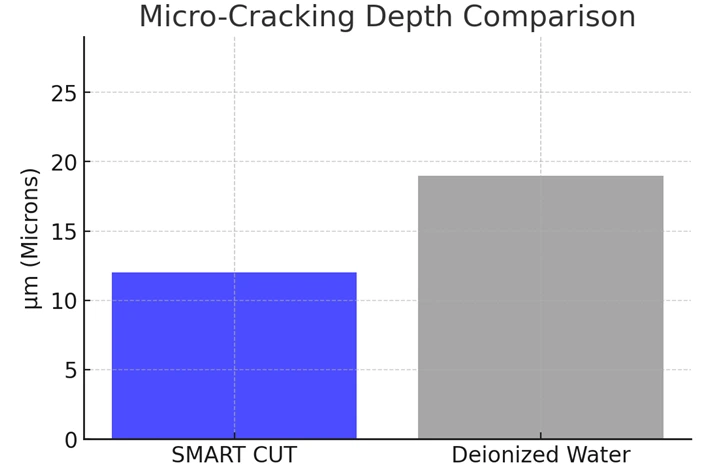
Related Products
SMART CUT® Water Soluble Coolant
(General Materials Formula)
High-Performance Fully Synthetic Coolant & Lubricant for Diamond Slicing, Dicing, Drilling, and Grinding & Machining of Ceramics, Glass, Optics, Quartz, Silicon, and Other Hard & Brittle Materials
SMART CUT® Water Soluble Coolant (General Materials Formula) is a fully synthetic, non-oily, and non-foaming coolant and lubricant engineered to meet the rigorous demands of slicing, dicing, drilling, sectioning, wafering, grinding, and polishing operations involving hard and brittle materials. This advanced formula has been specifically developed for use with ceramics, precision optics, quartz, silicon, sapphire, and other materials commonly found in semiconductor, photonics, and materials research applications.SMART CUT® Mineral Oil
SMART CUT® Mineral Oil is recommended for cutting, drilling, grinding and machining larger variety of materials such as:
- Materials with High Metallic Content
- Advanced Ceramics
- Precious & Semi Precious Stone
- Many Other Ultra Hard Materials
SMART CUT® HD Synthetic Low IFT Coolant/Lubricant For Diamond Wire Sawing Silicon
SMART CUT® is a synthetic coolant specifically designed for the cutting of semiconductor materials, including sapphire, silicon, germanium, single-crystal SiC, and II-VI crystals. This coolant offers excellent cut rates and imparts outstanding surface finishes with reduced warp and total thickness variation (TTV). It is ideal for diamond abrasive cropping, squaring, and wafering of silicon ingots using ID, band, and wire saws. SMART CUT® HD-2B can also be used as a non-re-circulating edge grinding coolant or lubricant for silicon wafers and ingots.
Recently Viewed Products
ARE YOU USING RIGHT Dicing Coolant/ Lubricant
FOR YOUR APPLICATION?
LET US
HELP YOU
HAVING ISSUES WITH
YOUR CURRENT Dicing Coolant/ Lubricant?
Knowledge Center
02
Jun
Diamond Tool Coolants Why, How, When & Where to Use
Coolant is one of the most overlooked variables in the overall diamond or cbn tool machining process. Effective and proper use of coolant and recalculating coolant system will pay off in terms of improved surface...
02
Jun
Dicing Blade Operations Recommendations
Share this Article with Friend or Colleague
Selecting the right dicing blade parameters often involves a trial and error process, many aspects of which can be mitigated through experience and a deep understanding of how...
02
Jun
Optimizing Dicing Blade Performance
There are many variables that affect dicing blade performance. Each variable of the dicing process is only of the many components of a larger dicing system (equation). Changing one component or variable of...
- Unmatched Selection For Many Applications
- Superior Quality & Consistency
- Immediate Worldwide Delivery
- Technical Support & Expertise
- American Based Manufacturer
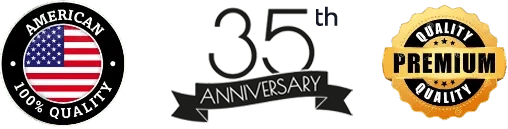

- Different Product
- Different Technology
- Different Company
- Expect MORE from your tools
Let Us HELP You!
Subscribe To Our Newsletter
Signup for email offers, updates, and more
Contact Us
- 25205 & 25201 Avenue Tibbits Valencia CA 91355 USA
-
Phone : (661) 257-2288
FAX : (661) 257 -3833 - lel@ukam.com
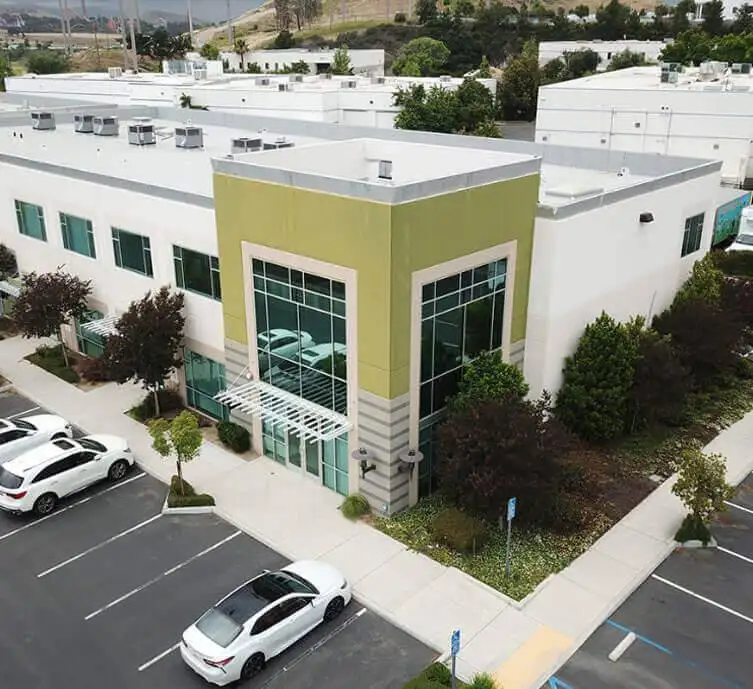
UKAM Industrial Superhard Tools is a U.S. High Technology, Specialty Diamond Tool & Equipment manufacturer. We specialize in producing ultra thin, high precision cutting blades, precision cutting machines diamond drills, diamond micro tools, standard & custom advanced industrial diamond tools and consumables.
- 25205 & 25201 Avenue Tibbits Valencia CA 91355 USA
-
Phone : (661) 257-2288
FAX : (661) 257 -3833 - lel@ukam.com
- 25205 & 25201 Avenue Tibbits Valencia CA 91355 USA
-
Phone : (661) 257-2288
FAX : (661) 257 -3833 - lel@ukam.com
DIAMOND TOOLS BY BOND
EQUIPMENT
KNOWLEDGE CENTER
OUR PRODUCTS
COMPANY
CUSTOMER SERVICE
Shipping Methods


Safe & Secure Payments

© Copyright 1990-2025. UKAM Industrial Superhard Tools – Terms of Use