-
0 items in quote
No products in the Quote Basket.
SMART CUT® Water Soluble Coolant
(General Materials Formula)
High-Performance Fully Synthetic Coolant & Lubricant for Diamond Slicing, Dicing, Drilling, and Grinding & Machining of Ceramics, Glass, Optics, Quartz, Silicon, and Other Hard & Brittle Materials
SMART CUT® Water Soluble Coolant (General Materials Formula) is a fully synthetic, non-oily, and non-foaming coolant and lubricant engineered to meet the rigorous demands of slicing, dicing, drilling, sectioning, wafering, grinding, and polishing operations involving hard and brittle materials. This advanced formula has been specifically developed for use with ceramics, precision optics, quartz, silicon, sapphire, and other materials commonly found in semiconductor, photonics, and materials research applications.
DESCRIPTION
SPECIFICATION
FREQUENTLY ASKED QUESTIONS
INDUSTRIES USED IN
ACCESSORIES
USAGE RECOMMENDATION
DESCRIPTION
This unique water-based coolant significantly enhances overall process efficiency by providing exceptional cooling and lubrication directly at the point of contact between the diamond tool and the workpiece. Its superior thermal transfer properties help dissipate heat rapidly, preventing thermal cracking, micro-fractures, and material deformation. By minimizing heat generation and tool-to-workpiece friction, SMART CUT® coolant improves cutting speed, enhances edge and surface quality, and extends the service life of diamond blades, drills, and grinding wheels.
Operator- and environmentally-friendly, SMART CUT® Water Soluble Coolant contains no oils, silicones, or volatile organic compounds (VOCs). It is non-toxic, biodegradable, and completely water-soluble, making it ideal for use in clean rooms, research laboratories, and production environments where safety and cleanliness are critical. Unlike traditional oil-based coolants, it leaves no sticky residues and rinses off easily with water, reducing cleanup time and keeping equipment and work surfaces clean.
The non-foaming nature of this coolant makes it especially well-suited for high-speed and automated equipment, ensuring consistent fluid flow and uninterrupted machining operations. It maintains stable operating conditions even under demanding loads, and is compatible with virtually all types of precision diamond machining equipment, including low-speed saws, dicing saws, CNC systems, wafering machines, and high-speed polishing and grinding equipment.
Designed to deliver measurable improvements in productivity and performance, SMART CUT® Water Soluble Coolant can improve cutting, drilling, grinding, & machining performance by 10% to 50% or more, depending on the material being processed, the type of tooling used, and the condition of the previous coolant. These improvements can include faster cutting speeds, reduced chipping and subsurface damage, longer tool life, and greater consistency across batches and setups.
Plain water evaporates at 212 F. Often temperature in your cutting zone reaches as much as 500 degrees F. Often water evaporates, before it has a chance of affectively cooling the diamond wheel and material being drilled. Resulting in shorter Diamond Wheel Life, Material Damage or micro cracks associated with overheating. Water may cool your diamond & cbn tools, yet provide poor lubrication properties needed for optimum slicing, dicing, drilling, grinding & polishing results Premium water soluble synthetic coolant. SMART CUT® General Materials Formula is designed for large variety of materials and applications. Such as Glass, Natural & Semi Precious Stone, Composites, Semiconductor, Metals, Hard Tool Steels, Ceramics, Porcelain and many others. SMART CUT® General materials formula will benefit users in all industries and applications. SMART CUT® water soluble coolant reduces material thermal stress, edge damage, internal cracking, increases tool life, provides better cut quality, preserves the material microstructure, assures long-term integrity of the material being cut and more. As a coolant SMART CUT® reduces heat caused by friction. As a lubricant SMART CUT® lowers friction and surface tension, which increases swarf dispersion.
How it Works
Stream of SMART CUT® coolant added to deionized (DI) water reduces material thermal stress, edge damage, and internal cracking, assuring long-term integrity of material being drilled. Since SMART CUT® is a coolant and lubricant, both the diamond tools and material benefit. Stream of SMART CUT® coolant added to deionized (DI) water reduces material thermal stress, edge damage, and internal cracking, assuring long-term integrity of material being processed. Since SMART CUT® is a coolant and lubricant, both the diamond tools and material benefit. Usage Recommendations >>>
Sizes Available
- 1 Quart
- 1 gallon bottles
- 5 gallon pails
- 55 gallon drums
Mix Ratio:
Application | Range Ratio |
---|---|
Slicing | 1:20 to 1:50 |
Millig | 1:50 to 1:100 |
Drilling | 1:20 to 1:50 |
Grinding | 1:30 to 1:50 |
Material Hardness | Recommended Ratio |
---|---|
Soft Materials | 1:75 |
Hard Materials | 1:50 |
Very Hard Materials | 1:30 |
Utra Hard Materials | 1:20 |
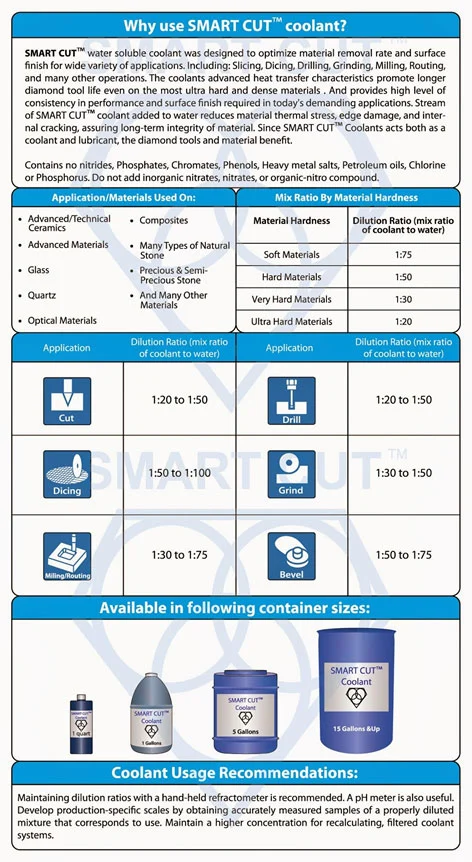
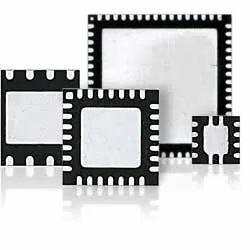

SPECIFICATION
PRODUCT SPECIFICATIONS:
- Appearance: Blue liquid
- Odor: Slight ammoniacal
- pH Value: 9.8
- Specific Gravity: 1.025
- Solubility: Soluble in water
- VOC Content: Less than 0.21%
- Packaging: 1 quart, 1 gallon, 5 gallon, 55 gallon
- Shelf Life: 2 years
Hazard Identification:
- Hazard Classification: Not classified as hazardous under the 2012 OSHA Hazard Communication Standard (29 CFR 1910.1200). However, it should be noted that the coolant may cause slight transient eye irritation and prolonged or repeated exposure could cause skin irritation.
Handling and Storage:
- Handling: Handle in accordance with good industrial hygiene and safety practice. Avoid contact with skin and eyes. Keep container tightly closed when not in use.
- Storage: Store in a cool, dry, and well-ventilated place. Protect from freezing and excessive heat. Keep away from incompatible materials.
Safety Information:
- Eye Contact: In case of contact, rinse immediately with plenty of water for at least 15 minutes.
- Skin Contact: Wash with soap and water; use hand cream to treat any irritation.
- Inhalation: If inhaled, move to fresh air and seek medical attention if symptoms persist.
- Ingestion: Do not induce vomiting; drink water or milk and seek medical attention immediately.
Storage Recommendations:
- Keep Container Tightly Closed: To prevent contamination and evaporation, it’s essential to keep the coolant
container tightly closed when not in use. This practice helps preserve the concentration and properties of the coolant. - Store in a Cool, Dry, and Well-Ventilated Place: The storage area should be cool to prevent the coolant from degrading due to heat. It should also be dry to avoid moisture ingress, which can dilute the coolant and reduce its effectiveness. Adequate ventilation is necessary to dissipate any vapors or gases that might be emitted from the coolant.
- Protect from Freezing and Extreme Heat: The coolant should be protected from freezing temperatures, which could affect its chemical structure and performance. Similarly, it should not be stored in areas where it could be exposed to extreme heat, which might cause degradation or increase the risk of release of hazardous decomposition products.
- Keep Away from Incompatible Materials: As stated in the SDS, the coolant should not be stored near strong oxidizers, strong reducing agents, or nitrosating agents. Contact with incompatible materials could lead to dangerous reactions or degrade the coolant.
- Follow Local Regulations: Always follow local, regional, national, and international regulations regarding the storage of chemicals. This ensures compliance with safety standards and environmental protections.
FREQUENTLY ASKED QUESTIONS
SMART CUT® water soluble coolant is specifically designed to be used at a number of different concentrations. Each material and application will have an ideal concentration. The concentration will affect sump life, tool life, and surface finish. Here are some examples of different applications and their corresponding concentrations. Maintaining proper concentration is essential to obtain optimum results, specially in production setting. Based on our experience, close to 80% of the coolant issues reported by clients are directly or indirectly attributable to poor concentration control. Concentration control is difficult to achieve when the coolant is manually mixed in small batches and is virtually impossible to maintain when untrained operators mix coolant. The Systems Equipment Division carries a complete line of automatic proportioning equipment to maintain accurate coolant concentration control. (Fluid Mixers) The refractometer factor is used in determining concentration of a metalworking fluid. Each Master Chemical product has a refractive index factor for determining concentration. Consult the Data and Information Sheet for product specific refractive index factors. Multiply the refractive index (refractometer reading) by the refractometer factor and the result is the concentration of the working solution in percent. (The factor for most emulsion fluids is 1.0 so that the refractive index is the fluid concentration.) An unpleasant coolant smell is most likely attributed to anaerobic bacteria. Bacteria produce waste products, which often contain sulfur and exude the “rotten-egg” smell. Bacteria are major contributors to coolant failure. They chemically alter coolants and destroy the lubricants and corrosion inhibitors in the process. They also pass off corrosive acids and salts into the coolant, which can lead to low pH and corrosion problems. The bacterial growth can be minimized by: Oftentimes, “cover-ups” which are perfumes, can be used to mask odors but they are not a cure and their use can lead to more serious fluid problems later. Most coolants exhibit colors and odors that result from the chemicals from which they are blended. But sometimes metal cutting fluid manufacturers use dyes and colorants to give them an aesthetic appeal. They are also helpful in identification of products for companies which use a number of different products. Machine operators sometimes use color intensity as an indication of coolant concentration. Color intensity is not a good indicator of concentration as tramp oil can absorb the dyes used, and some work materials (such as cast iron) can “mask” the dye. Even with dyed coolants it is necessary to check fluid concentration properly periodically. Residue is the material left behind on the machine and workpieces after the water evaporates from the coolant solution. Residues should never interfere with the smooth and proper machine tool function but more importantly the residue should enhance the machine’s operation. Residues may be classified as: For optimum machine tool functioning, oily, non-gummy residues are preferable. If a residue is hard, gummy or crystalline, it can cause a machine’s moving parts to “stick” or “freeze” and may cause a machine malfunction. A moderate crystalline film may be tolerated on certain types of surface grinders but such a residue could cause a major problem on a 5-axis machining center. In other words, the type of machine must be considered when selecting a fluid because the type of residue may dramatically affect the machine function. SMART CUT™ Water Soluble Coolant is a synthetic coolant formulated for use in cutting, grinding, and machining operations. It is effective for cooling and lubricating a wide range of materials, including metals, ceramics, and composites. This coolant is ideal for applications like milling, drilling, and grinding, helping to enhance cutting efficiency, protect tools, and improve surface finish quality. The mixing ratio depends on the material being cut and the type of operation: For light-duty cutting: Mix 1 part coolant to 20 parts water. For more intense cutting or grinding: Mix 1 part coolant to 10 parts water. Be sure to mix thoroughly and test the concentration using a refractometer to ensure the correct mix for your specific needs. While the SDS doesn’t specify an exact shelf life, SMART CUT™ should be stored under recommended conditions—cool, dry, and sealed containers. If properly stored, it should maintain its effectiveness for an extended period. Avoid prolonged exposure to high temperatures or freezing conditions, which could impact the product’s stability. Yes, this coolant is compatible with a wide range of cutting, grinding, and machining equipment, including CNC machines, band saws, lathes, and surface grinders. It works well with different materials, from metals and composites to ceramics, ensuring versatility in various industrial applications. The coolant is a blue liquid with a slight ammoniacal odor, which is typical for water-soluble coolants. It is designed to be non-intrusive and safe to handle in a well-ventilated environment. Yes, SMART CUT™ is biodegradable and formulated to minimize environmental impact. It is safer for disposal compared to oil-based coolants, provided local disposal regulations are followed. The biodegradable nature of the coolant makes it a more sustainable choice for industries looking to reduce their environmental footprint. Yes, SMART CUT™ Water Soluble Coolant can be effectively filtered to maintain its performance and extend its service life. Implementing a filtration system helps remove contaminants such as metal particles, tramp oils, and other debris, ensuring optimal machining conditions. For optimal results, it’s advisable to consult with coolant manufacturers or filtration system providers to design a filtration solution tailored to your specific machining operations and coolant type. SMART CUT™ Water Soluble Coolant is formulated to provide effective cooling and lubrication across various machining operations. Compared to other water-soluble coolants, SMART CUT™ offers enhanced corrosion protection, improved tool life, and better surface finishes. Its formulation ensures effective cooling and lubrication across different materials and cutting conditions. Not all coolants are the same. Where there may be many coolant options, metalworking coolants are primarily formulated for metals and may not be effective for machining hard and brittle materials like ceramics, glass, composites, semiconductors, and precious stones. These materials often require specialized coolants or lubricants tailored to their unique properties. For instance, when slicing, grinding, drilling glass, ceramics, and other brittle materials, the choice of coolant significantly influences the effectiveness of the fabrication process. The coolant should efficiently remove heat, provide sufficient lubricity, and effectively remove waste material from the grinding zone, all while maintaining optimal material removal rates and surface finish quality. Conventional coolants often lack the ability to efficiently remove heat from the cutting area, leading to overheating, tool wear, and poor surface finishes. They can also cause material contamination, poor lubrication, and inconsistent tool performance, especially when working with hard and brittle materials. Additionally, conventional coolants may require additional secondary operations to correct material damage or imperfections. Yes, SMART CUT® Coolant is fully compatible with most filtration systems, ensuring that it can be used efficiently in systems designed for water-soluble coolants without the need for significant adjustments or additional components. SMART CUT® Coolant requires minimal maintenance. It is formulated to prevent bacterial growth and avoid foaming, which can disrupt cooling efficiency. Regular monitoring of the coolant’s dilution ratio is recommended to ensure optimal performance. Periodic cleaning of the filtration system may also be necessary to maintain the coolant’s effectiveness. Yes, SMART CUT® Coolant can help reduce machining costs in the long term. By extending tool life, improving cutting efficiency, reducing downtime, and eliminating secondary operations, SMART CUT® Coolant provides significant cost savings for manufacturers. SMART CUT® Coolant is specifically formulated to perform effectively in high-speed machining operations. By maintaining cooling and lubrication properties under extreme cutting conditions, it helps reduce heat buildup and friction, which are common problems at high speeds. This leads to better tool life, improved surface finish, and faster, more efficient cutting. Yes, SMART CUT® Coolant reduces material thermal stress and edge damage by maintaining an optimal cutting temperature. It helps prevent chipping, microcracking, and material deformation, which is crucial when working with brittle materials like ceramics, glass, and precious stones. SMART CUT® Coolant is designed for wet cutting operations. While it can be used in near-dry or minimal coolant conditions, it is most effective when used in conjunction with deionized water, ensuring consistent cooling and lubrication for the material and the cutting tools. SMART CUT® Coolant is highly effective in machining composite materials, as it reduces heat buildup and prevents material softening, which can lead to fiber damage. Its excellent lubrication and cooling properties allow for smoother cuts and higher precision, which is critical when working with materials like carbon fiber and fiberglass. Yes, SMART CUT® Coolant is ideal for cutting precious stones such as diamonds, opals, and other semi-precious materials. Its ability to reduce thermal stress and prevent material cracking ensures that the stones retain their integrity and surface finish during the cutting process. SMART CUT® Coolant is effective within a wide temperature range, maintaining its properties even under extreme heat conditions. It is designed to perform well in temperatures as high as 500°F in the cutting zone, preventing tool overheating and material damage during high-speed or high-pressure operations. Yes, SMART CUT® Coolant contains corrosion inhibitors that provide excellent protection for both cutting tools and machinery. This helps prevent rust and corrosion from forming on tools, cutting equipment, and machinery, thereby prolonging their lifespan and reducing maintenance costs. While SMART CUT® Coolant is highly effective on its own, it is generally not recommended to mix it with other coolants or lubricants, as this could compromise its performance. It is best to use SMART CUT® Coolant as a standalone solution for optimal results. If needed, consult the manufacturer for recommendations on mixing or blending with other products. SMART CUT® Coolant helps maintain a consistent machining process by stabilizing the cutting temperature and reducing friction during operation. This leads to more predictable outcomes, with fewer variations in cut quality, material deformation, or tool wear. The coolant’s ability to improve temperature control ensures that every cut maintains the desired precision and surface finish. By providing effective cooling and lubrication, SMART CUT® Coolant reduces the thermal stresses that cause material deformation. Its ability to maintain a stable temperature at the cutting zone prevents the material from expanding or contracting due to heat, ensuring that delicate or high-precision workpieces retain their shape and integrity throughout the machining process. SMART CUT® Coolant is an eco-friendly solution, free from harmful chemicals like nitrates, phosphates, and chlorinated compounds. It is biodegradable and non-toxic, reducing its environmental impact. Additionally, its ability to extend tool life and reduce coolant waste makes it a more sustainable and cost-effective option in the long term. SMART CUT® Coolant works effectively when you observe smoother cutting, longer tool life, minimal material damage, and improved surface finish quality. If you’re experiencing reduced tool wear, fewer secondary operations, and more consistent results, it’s a good sign that the coolant is performing optimally. Regularly checking the coolant’s dilution and cleanliness will also help maintain its effectiveness. SMART CUT® Coolant is safe to use on most types of diamond saws, grinders, CNC machines, and other machining equipment. It is compatible with a wide range of filtration systems and doesn’t cause corrosion or buildup on machines. However, always ensure that the coolant is used at the recommended dilution ratios for best results. If you notice any issues with the coolant’s performance, such as poor cooling or lubrication, check the dilution ratio to ensure it is within the recommended range for your specific operation. It’s also important to monitor for contamination, which can occur over time. If necessary, contact the manufacturer for support or advice on troubleshooting specific problems. Yes, SMART CUT® Coolant is highly effective for high-precision wafering operations. Its ability to provide consistent cooling and lubrication, as well as its capability to prevent microcracking and thermal distortion, makes it an excellent choice for applications where ultra-tight tolerances are required, such as in semiconductor manufacturing. Yes, SMART CUT® Coolant is highly effective in automated systems, ensuring smooth and consistent coolant delivery during automated cutting, grinding, and slicing operations. It maintains the required lubrication and cooling properties without the need for manual intervention, helping increase throughput and reduce operator involvement. SMART CUT® Coolant minimizes microcracking by reducing thermal stresses at the cutting zone. Its cooling properties help maintain a stable temperature during the cutting process, preventing material expansion and contraction that could lead to cracks. This is particularly important for brittle materials like ceramics, glass, and gemstones. Using SMART CUT® Coolant instead of plain water provides substantial performance improvements. The coolant’s ability to bond with water molecules allows for better swarf removal, superior cooling, and lubrication. This helps in reducing friction, extending tool life, and maintaining a consistent cutting temperature, resulting in higher-quality cuts, fewer tool changes, and reduced risk of material damage. No, SMART CUT® Coolant does not leave hard-to-remove residues on the material or machinery. Its formulation is designed to minimize residue buildup, ensuring that any organic residue left behind is easily cleaned and won’t harm the workpiece or the machine components. SMART CUT® Coolant helps improve cutting accuracy by maintaining consistent tool temperatures, preventing overheating, and reducing tool wear. These factors are critical in high-precision applications like semiconductor wafering, thin section cutting, and diamond sawing, where even slight temperature fluctuations or material deformations can lead to dimensional inaccuracies. Yes, SMART CUT® Coolant is designed to work effectively with all types of diamond tools, including diamond drills, slicing blades, wafering blades, and other precision cutting tools. It improves the performance and longevity of these tools by providing efficient cooling and reducing friction during cutting. Yes, SMART CUT® Coolant is highly effective in polishing operations. Its lubrication properties reduce friction, allowing for smoother and more controlled polishing of materials, while also preventing overheating, which can cause surface damage. It helps achieve a high-quality, fine finish with less material waste. SMART CUT® Coolant should be stored at room temperature, ideally between 50°F and 85°F (10°C to 30°C). It should be kept in a cool, dry place, away from direct sunlight and extreme temperatures, to maintain its stability and effectiveness over time. Yes, SMART CUT® Coolant is versatile and can be used with both hard and soft materials. Whether you’re cutting tough ceramics, soft metals, or composite materials, SMART CUT® Coolant’s unique formulation provides optimal cooling and lubrication, ensuring high-quality results across a wide range of material types. SMART CUT® Coolant increases cutting speed by improving lubrication and cooling, which reduces friction and heat buildup. This results in more efficient cutting, allowing operators to achieve higher speeds without compromising tool life, material quality, or cutting precision. No, SMART CUT® Coolant does not require special handling or equipment. It is compatible with standard filtration and coolant systems used in most machining setups. However, it is important to follow the recommended dilution ratios to ensure optimal performance and maximize the coolant’s benefits. SMART CUT® Coolant is designed to work independently for optimal performance. It is generally not recommended to mix SMART CUT® with other cutting fluids as it may reduce its efficiency. However, if you need to blend with another product, it’s advised to consult the manufacturer to ensure compatibility and avoid compromising the coolant’s performance. SMART CUT® Coolant benefits a wide variety of cutting operations, including: Diamond blade cutting Grinding and polishing Dicing and slicing of thin sections Drilling and boring of hard materials Wafering and precision machining It is especially beneficial in high-precision, high-speed, and high-pressure applications. Yes, SMART CUT® Coolant improves surface finish quality by reducing friction and heat generation, which helps in preventing tool marks, material chipping, and surface imperfections. Its superior lubrication properties contribute to a smooth, polished surface, which is essential in high-quality, precision cutting operations. Yes, SMART CUT® Coolant is effective for grinding operations, including both surface and cylindrical grinding. It helps prevent tool wear, reduces the risk of thermal damage, and ensures smooth, efficient grinding with minimal swarf accumulation. The coolant’s ability to reduce friction and heat buildup leads to higher efficiency and longer tool life during grinding. SMART CUT® Coolant is ideal for high-precision cutting due to its ability to maintain stable cutting temperatures, improve lubrication, and prevent material deformation or cracking. These factors are crucial for industries that require ultra-tight tolerances and clean cuts, such as semiconductor manufacturing, optics, and precision materials cutting. SMART CUT® Coolant has a pleasant scent that enhances the working environment by reducing the unpleasant odors often associated with traditional cutting fluids. It is designed to be non-toxic and non-irritating, ensuring a more comfortable and safer environment for operators. If you notice any issues such as poor cooling, increased tool wear, or decreased cutting efficiency, check the dilution ratio to ensure it aligns with the recommended specifications for your application. Ensure that the coolant is clean and free from contaminants. If problems persist, consider contacting the manufacturer for further troubleshooting support. By preventing cracking, chipping, and thermal damage, SMART CUT® Coolant ensures that more material is usable, improving yield. It reduces material waste caused by cutting defects, which is particularly beneficial for high-cost materials and precision applications where material loss is a concern. Yes, SMART CUT® Coolant is safe for use on a wide range of machinery, including CNC machines, precision cutting equipment, grinding machines, and diamond saws. It is compatible with most filtration systems and does not cause corrosion or damage to machine components when used as directed. SMART CUT® Coolant improves productivity by extending tool life, increasing cutting speeds, and reducing downtime caused by tool changes. It also enhances surface finish quality, reducing the need for additional post-processing steps. These factors contribute to more efficient and faster machining operations. SMART CUT® Coolant is designed to maintain its effectiveness over extended periods, reducing the need for frequent replenishment. As long as the dilution ratio is maintained and the coolant is kept clean, it can last for a significant amount of time without the need for frequent changes. Yes, SMART CUT® Coolant helps prevent material from sticking to the tool. Its lubrication properties reduce friction, ensuring that the material and tool remain separated during the cutting or grinding process. This is particularly important in high-speed operations where material adhesion can cause tool clogging or surface defects. Store SMART CUT™ in a cool, dry, and well-ventilated area, away from direct sunlight and sources of heat. The container should be kept tightly closed when not in use to prevent contamination. Avoid storing the coolant near incompatible materials like strong oxidizers, reducing agents, or nitrites, as these could lead to dangerous reactions or degrade the coolant. SMART CUT™ is non-flammable and non-hazardous under normal conditions. However, as with any chemical product, it’s important to follow safety guidelines. Always wear appropriate personal protective equipment (PPE) such as gloves and goggles to prevent skin or eye contact, especially during mixing or handling. Eye Contact: Rinse immediately with plenty of water for at least 15 minutes. If irritation persists, seek medical attention. Skin Contact: Wash with soap and water. Apply hand cream afterward to keep the skin moisturized. If irritation continues, remove contaminated clothing and seek medical advice. Inhalation: Move to fresh air. If symptoms such as coughing or shortness of breath persist, seek medical help. Ingestion: Drink water or milk immediately, but do not induce vomiting unless directed by medical personnel. Seek immediate medical attention. Store SMART CUT™ at a moderate temperature, typically between 10°C (50°F) and 30°C (86°F). Avoid freezing conditions as well as exposure to extreme heat, which can cause the product to degrade or evaporate, reducing its effectiveness. The coolant’s superior lubrication properties reduce friction between the cutting tool and the workpiece, which minimizes wear on the tool and enhances its performance. By keeping tools cool and preventing overheating, SMART CUT™ ensures longer tool life and improves overall cutting efficiency. Yes, SMART CUT™ can be recycled or reused by filtering out contaminants such as metal shavings, dirt, and other debris. Many industrial facilities use coolant recycling systems to extend the life of the coolant, making it more cost-effective and environmentally friendly. However, regular testing is necessary to ensure it maintains the correct concentration and effectiveness. In case of a spill, absorb the coolant with inert materials such as sand or sawdust. Once absorbed, place the waste material in a suitable container for disposal. Avoid allowing the coolant to enter drains or waterways, as it could lead to environmental contamination. Always clean up spills promptly and follow local waste disposal regulations. The primary chemical component in SMART CUT™ is triethanolamine (less than 20%). While generally safe under normal use, prolonged skin contact or inhalation of the mist should be avoided. Always follow the safety guidelines provided in the SDS and use personal protective equipment (PPE) to minimize exposure. The coolant should be replaced when it becomes contaminated or when its performance drops. Regular testing for concentration, pH levels, and contamination can help determine when to replace the coolant. Typically, coolant should be replaced if it starts to show signs of discoloration, odor, or if it becomes too thick or contaminated. SMART CUT™ offers superior cooling and lubrication performance compared to traditional oil-based coolants. Its biodegradable nature, low VOC content, and effective corrosion inhibition make it an environmentally friendly and efficient choice for both high-performance cutting operations and regular maintenance tasks. To ensure that SMART CUT™ is performing effectively, regularly monitor the coolant’s pH, concentration, and cleanliness. Use a refractometer to measure the coolant concentration and make adjustments if necessary. If the coolant becomes too contaminated or the concentration is off, tool performance and cut quality will degrade. Yes, SMART CUT™ is suitable for cutting and machining a variety of metals, including aluminum. Its superior lubrication and cooling properties make it effective for aluminum, preventing overheating and tool wear during cutting and grinding operations. Coolant should be replaced when it becomes too contaminated or when its cooling and lubrication properties start to deteriorate. Regular testing for concentration and pH will help you determine when it’s time to replace the coolant. Additionally, if the coolant begins to smell, becomes discolored, or the mixture has been used for an extended period, it’s time to change it. Yes, to maintain its effectiveness, it’s important to regularly filter out contaminants such as metal particles and debris. Using a filtration system can help prolong the life of the coolant and ensure it continues to provide optimal performance during machining operations. Yes, SMART CUT™ is compatible with CNC machines. It works well in a wide range of automated cutting, grinding, and milling operations, providing both effective cooling and lubrication. Its use in CNC machines can enhance precision, tool life, and surface quality during high-speed machining. Used coolant should be disposed of according to local regulations and environmental guidelines. In many cases, it can be recycled or reconditioned. It’s essential to consult local authorities for proper disposal methods to minimize environmental impact. It’s not recommended to mix SMART CUT™ with other coolants, especially if they are of different types (e.g., oil-based or synthetic). Mixing coolants can lead to incompatible chemical reactions that may reduce the coolant’s effectiveness or cause other unwanted effects. Always use SMART CUT™ as specified by the manufacturer. SMART CUT™ is designed to improve the surface finish of materials by reducing friction and heat during cutting processes. Properly mixed coolant will help to achieve a smoother cut and prevent defects such as burning, discoloration, or rough finishes. Yes, SMART CUT™ is effective for use with hard metals like titanium, stainless steel, and other alloys. Its cooling and lubrication properties help manage the heat generated during cutting, which is especially important when machining harder materials that are prone to overheating. Absolutely. SMART CUT™ is well-suited for grinding applications, providing excellent cooling and lubrication during grinding processes, reducing tool wear, and improving the quality of the surface finish. If you find that the concentration is either too high or too low, you can adjust it easily by adding more coolant concentrate or water, respectively. Always stir the mixture thoroughly after adjusting the concentration to ensure an even distribution of the coolant in the mixture. Then, test again using a refractometer to verify the correct concentration. It’s recommended to use soft, clean water for mixing SMART CUT™ to avoid any negative effects from hard water, such as the formation of scale and deposits in the system. Hard water can reduce the performance of the coolant and potentially cause damage to the cooling system over time. Yes, SMART CUT™ is versatile and suitable for various machining operations, including milling, drilling, grinding, slicing, dicing, polishing. Its formulation ensures effective cooling and lubrication across different materials and cutting conditions. The optimal dilution ratio depends on the specific machining operation and material being processed. For general applications, a 5% solution (1 part coolant to 19 parts water) is commonly used. However, for heavy-duty operations or specific materials, a higher concentration may be beneficial. It’s advisable to consult the manufacturer’s guidelines or conduct trials to determine the best ratio for your needs. While SMART CUT™ is designed to be compatible with various water qualities, using soft or deionized water is recommended to prevent mineral deposits and scale formation. Hard water can lead to reduced coolant performance and potential damage to equipment over time. Used coolant should be managed according to local environmental regulations. Generally, it can be filtered to remove contaminants and then disposed of as non-hazardous waste. Some facilities opt to recycle the coolant to extend its usability. Always ensure compliance with local laws regarding disposal. SMART CUT™ contains triethanolamine as a primary ingredient. While generally safe under normal usage conditions, prolonged skin contact or inhalation of the mist should be avoided. Always follow safety guidelines and use personal protective equipment (PPE) to minimize exposure. Regular monitoring of the coolant’s concentration, pH level, and cleanliness is essential. Using a refractometer can help maintain the correct concentration. Additionally, observing the quality of the machined surface and the condition of cutting tools can provide insights into the coolant’s performance. Yes, SMART CUT™ is formulated to be effective with a wide range of metals, including ferrous and non-ferrous materials. Its corrosion inhibitors help protect against rust and oxidation, ensuring longevity and performance across different metal types. Absolutely. SMART CUT™ is designed to perform well under high-speed machining conditions, providing effective cooling and lubrication to prevent overheating and reduce tool wear. When mixing, add the coolant concentrate to water to prevent splashing and ensure proper dilution. Use appropriate PPE, such as gloves and safety goggles, to avoid skin and eye contact. Ensure the work area is well-ventilated to prevent inhalation of any mist. If skin irritation occurs, wash the affected area with soap and water. Apply hand cream to moisturize the skin. If irritation persists, discontinue use and consult a healthcare professional. Prolonged or repeated exposure may lead to skin sensitization in some individuals.
When water miscible coolants are used in machining and grinding operations the volume of fluid in the coolant sump decreases due to the physical loss of the fluid (fluid is carried off on chips and parts) and water evaporates because it absorbs heat generated in the machining or grinding operation. Proper operation requires that the fluid level is maintained at some minimum level and so “makeup fluid” must be added to replenish coolant carried out on chips and parts. Since the loss of water by evaporation causes the fluid in the sump to increase in concentration the “makeup fluid” will always be mixed at the same concentration less that of the recommended operating concentration. For example, if an emulsion coolant is to be run at 5% volume to water then the “makeup” concentration for that fluid will generally be 2.5-3.0%. Check your product data and information sheets for recommended working and “makeup” concentrations.
Mixing is crucial to maintaining stability in cutting and grinding fluids. Proper mixing instructions are available on all Master Chemical Data and Information Sheets. For optimum performance and maximum life, coolant concentrates should be mixed with chemically pure water produced by deionization or reverse osmosis. It is a general rule that concentrates should be added to the water last and mixed thoroughly. One way to remember the proper sequence of addition is to remember “O.I.L.”, meaning “oil in last”. Special mixing devices and proportioners like the UNIMIX™ and Master Mix™, which automate the mixing process and minimize the waste of concentrate, are available from Master Chemical. (Fluid Mixers)
INDUSTRIES USED IN
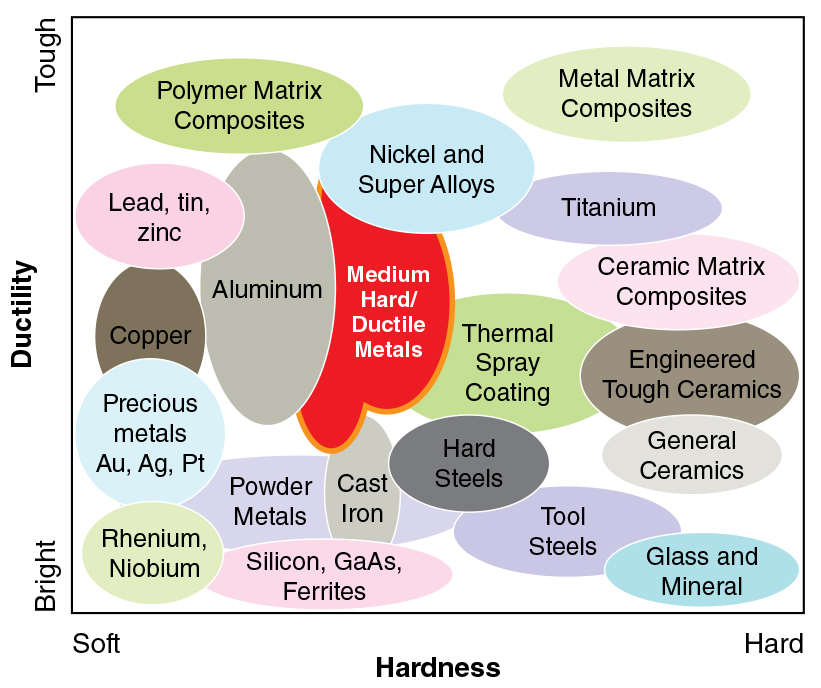
INDUSTRIES USED IN:
- Advanced Ceramics
- Composites
- Glass
- Geology
- Quartz
- Materials Research
- Medical Devices
- Metallography
- Photonics / Optics
- Semiconductor
FERROUS & NON-FERROUS METALS:
- Plain Carbon Steels
- Electronic Packages
- stainless Steels Plastics
- Tool Steels Fasteners
- Aluminum Refractories
- Copper Base Alloys Integrated Circuits
- Magnesium Thermal Spray Coatings
- Titanium Metal Matrix Composites
- Biomedical Wafers
- Petrographic
ACCESSORIES
Tab Content
USAGE RECOMMENDATION
SMART CUT® Water Soluble Coolant Usage Recommendations
Showing 1 – -1 of 4 results Showing all 4 results Showing the single result No results found
Sort by Price low to high
Filters Sort results
Reset Apply
Image | Item No. | Name | Price | Quantity | Add to cart |
---|---|---|---|---|---|
$34.81 | Max: Min: 1 Step: 1 | ||||
$99.81 | Max: Min: 1 Step: 1 | ||||
$317.41 | Max: Min: 1 Step: 1 | ||||
$1,745.00 | Max: Min: 1 Step: 1 |
Advantage
-
Reduce Surface Tension
-
Improve Output & Reliability
-
Improve Surface Finish Quality
-
Increase Tool Life
-
Preserve Material Micro Structure
-
Reduce Thermal Stress
-
Reduce Chipping
-
Reduce Edge Damage
-
Reduce & Minimize Micro Cracking
-
Reduce Heat Transfer
-
Improve Process Consistency
-
Eliminate Secondary Processing Operations
-
Improve Tolerances
-
Minimize Swarf Accumulation
-
Assure Long Term Integrity of Material
-
Lowers Friction
-
Improve Tolerances
Benefits
-
Wetting agents and increased lubricity allow high speed operation and high production yields.
-
Excellent Corrosion Inhibition even at lower than the recommended dilutions
-
None foaming
-
Mixes with hard or soft water
-
Not irritating to skin or eyes
-
Enhances surface finish
-
Effective in Preventing Odor-Causing Microbiological Growths
-
Pleasantly Scented
-
Bonds Water Molecules
-
User & Environment Friendly
-
None Staining
-
None Foaming
-
Compatible with all Filtration Systems
-
Non Corrosive
-
Economical with High Dilution Ratios
-
Universal Application can be used for most materials & applications
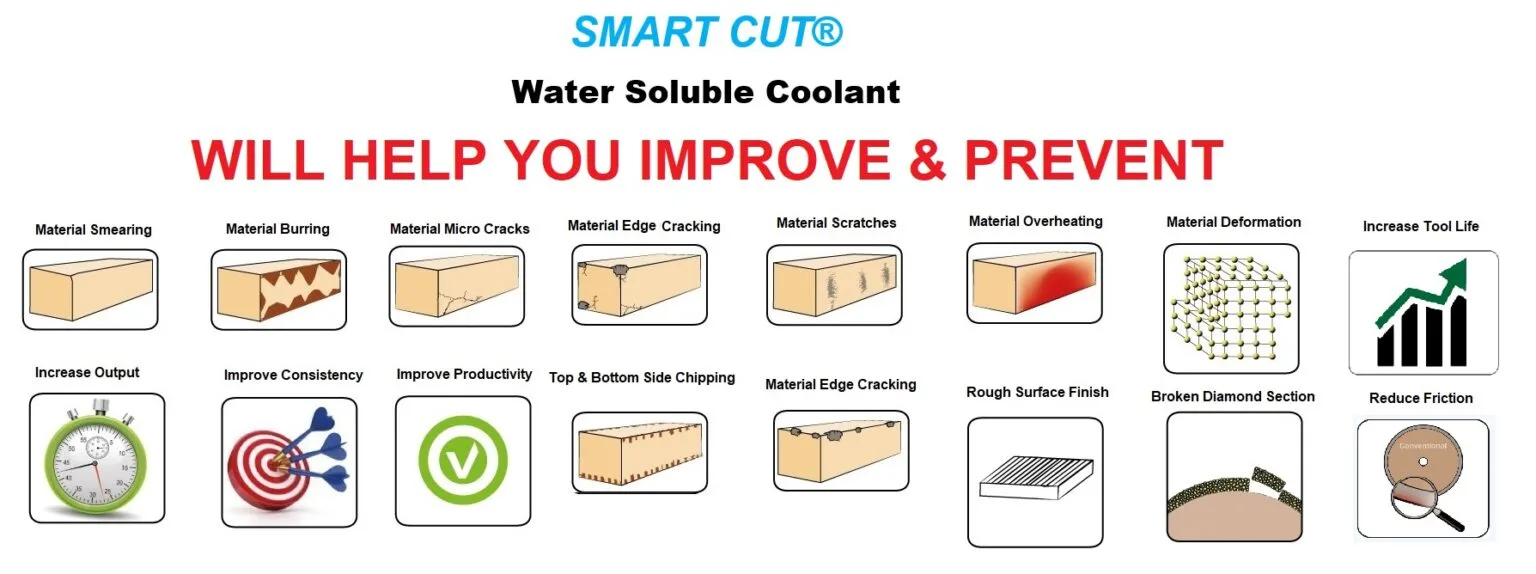
IMPROVE OVERALL PERFORMANCE BY 30%
Try SMART CUT® Coolent Today and see the difference it can make for your application
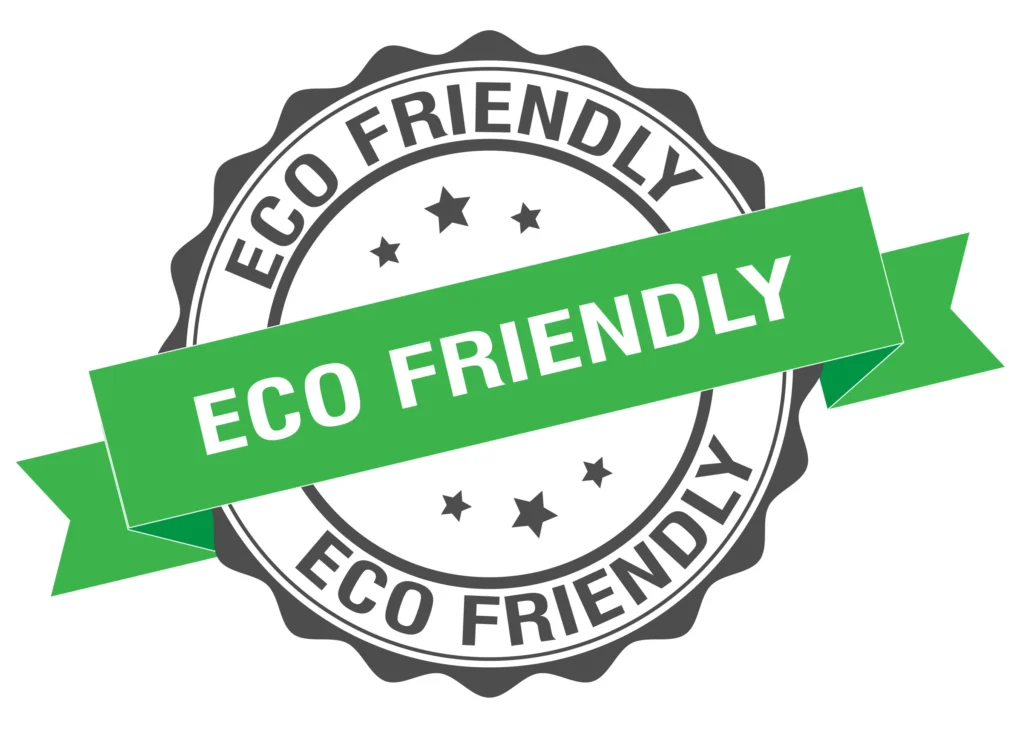
Green & Environmental Friedly Coolant

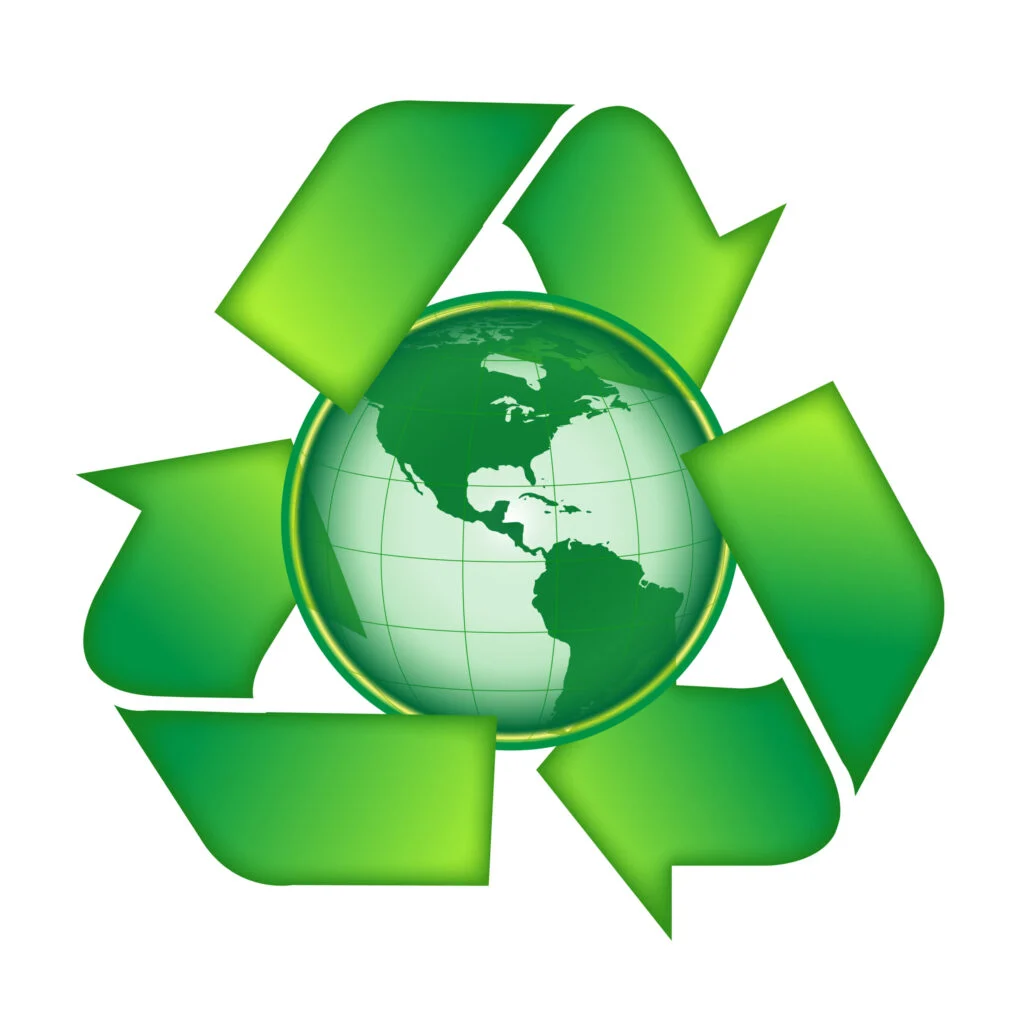
NOTE: contains no nitrides, phosphates, chromates, phenols, heavy metal salts, Petroleum oils, chlorine or phosphorus. Do not add inorganic nitrates, nitrites, or organic-nitro compounds.
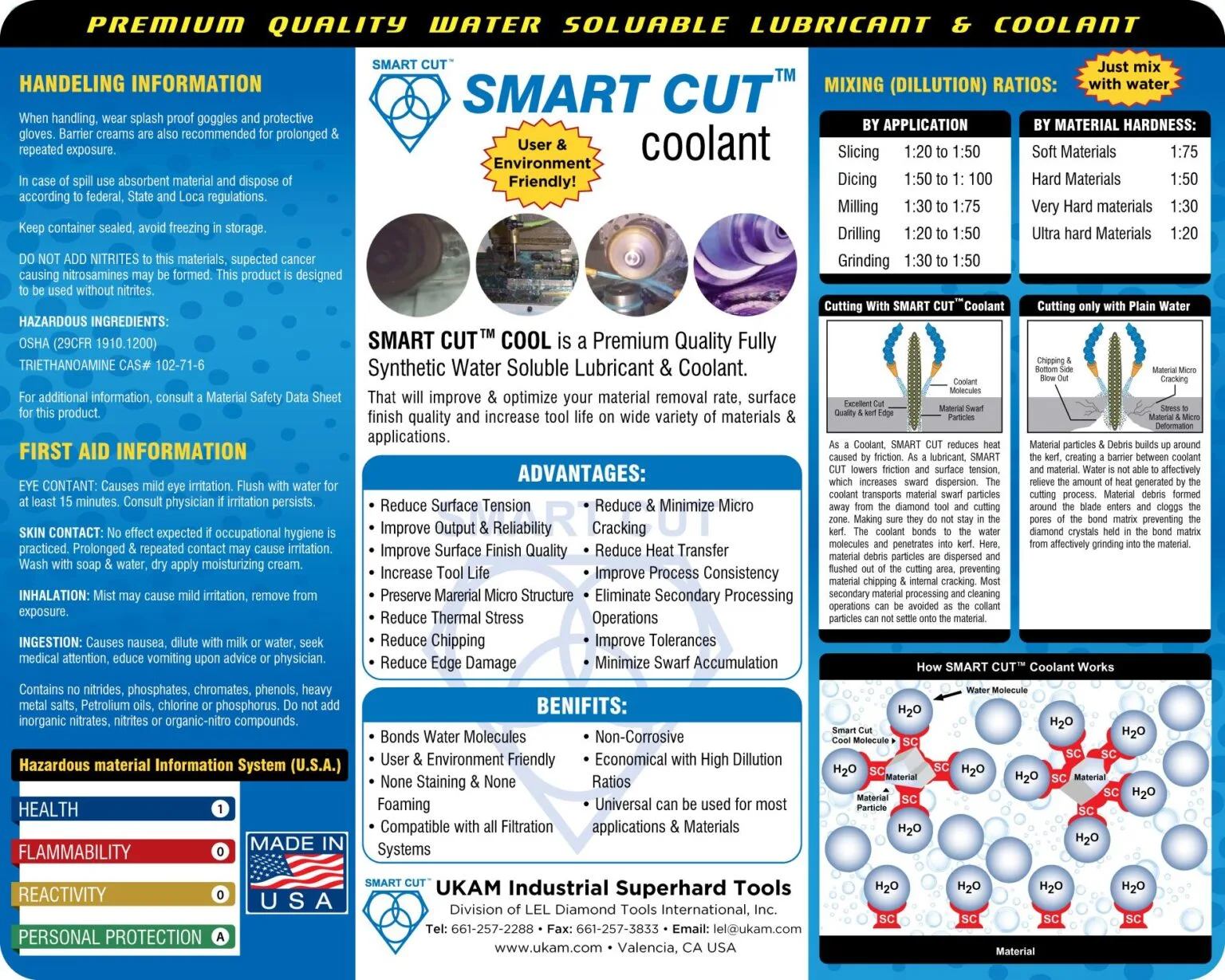
SMART CUT® Coolant Applications
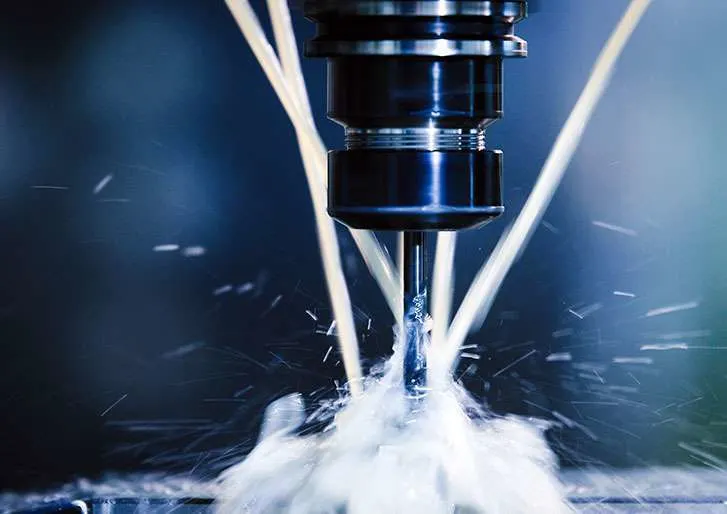
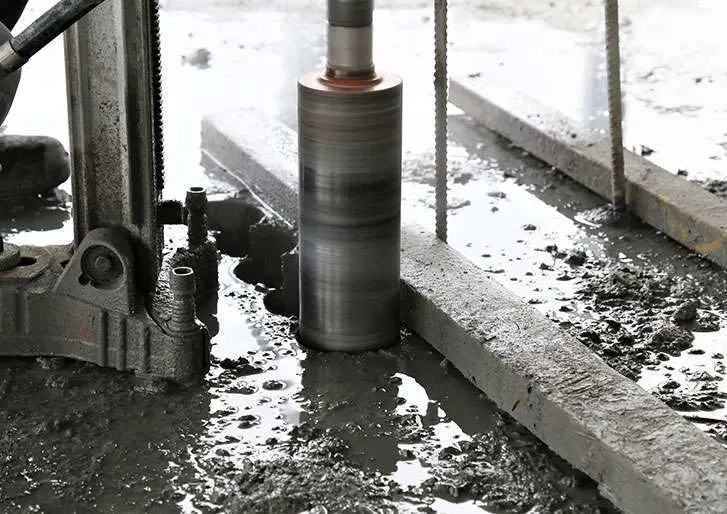
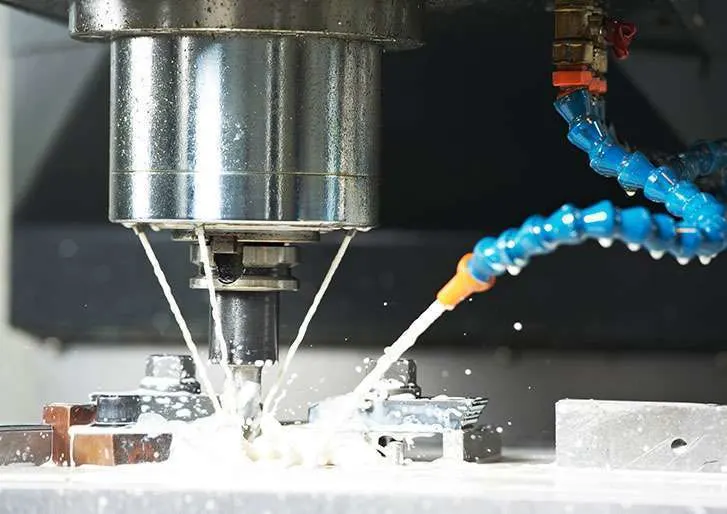
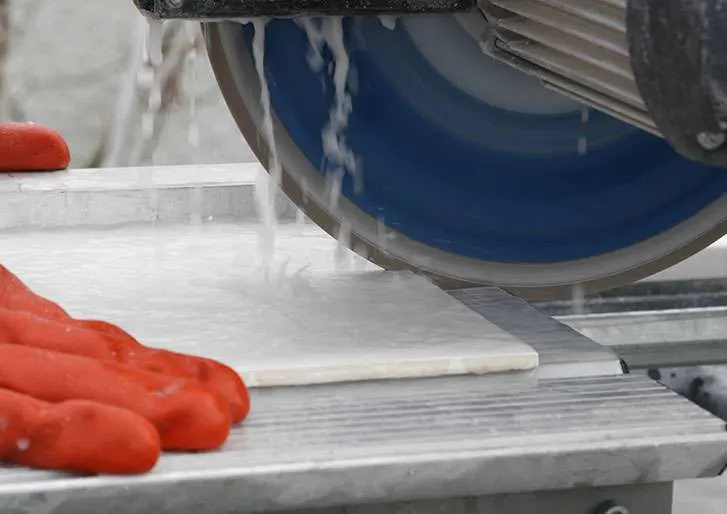

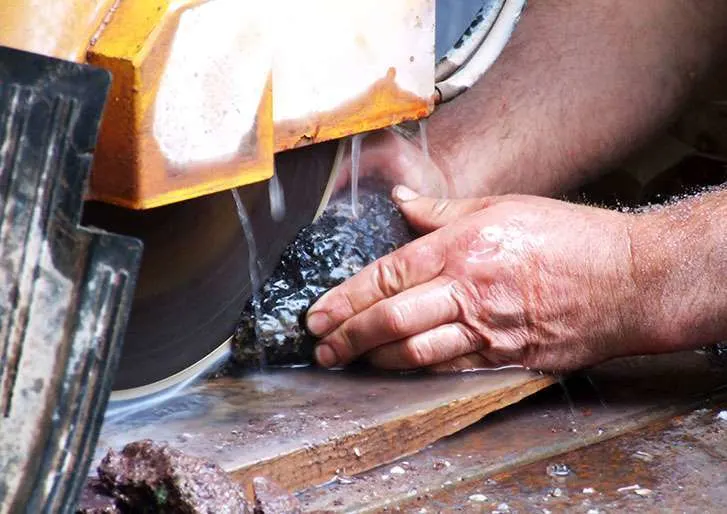
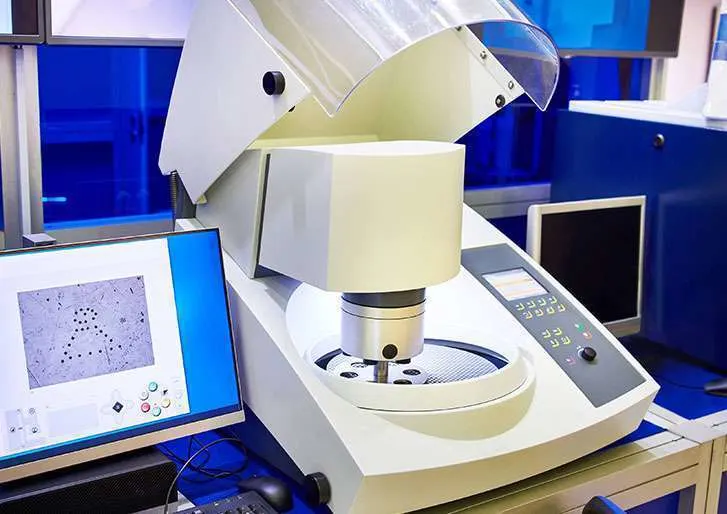
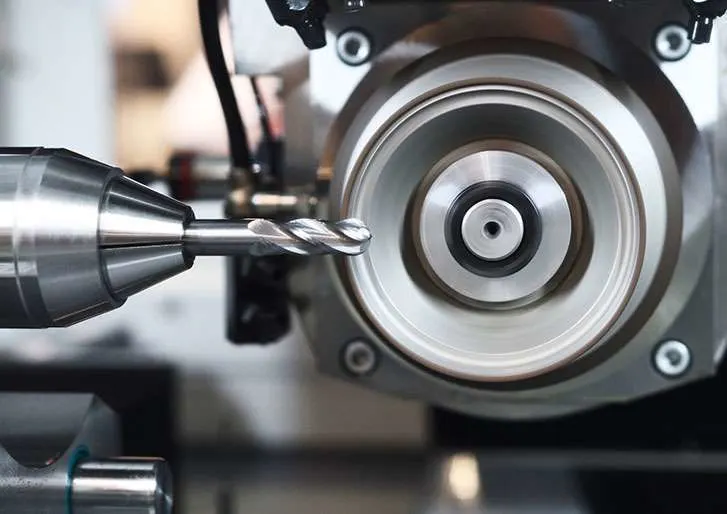

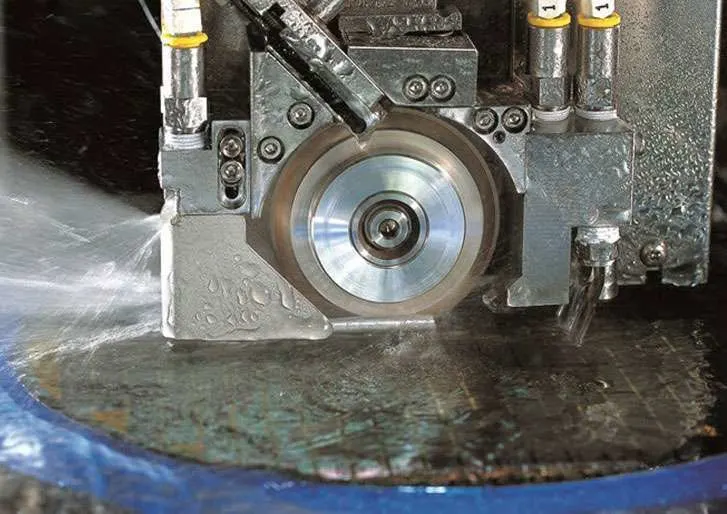
SMART CUT® Coolant Materials Used On
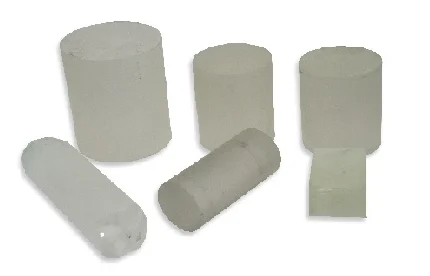
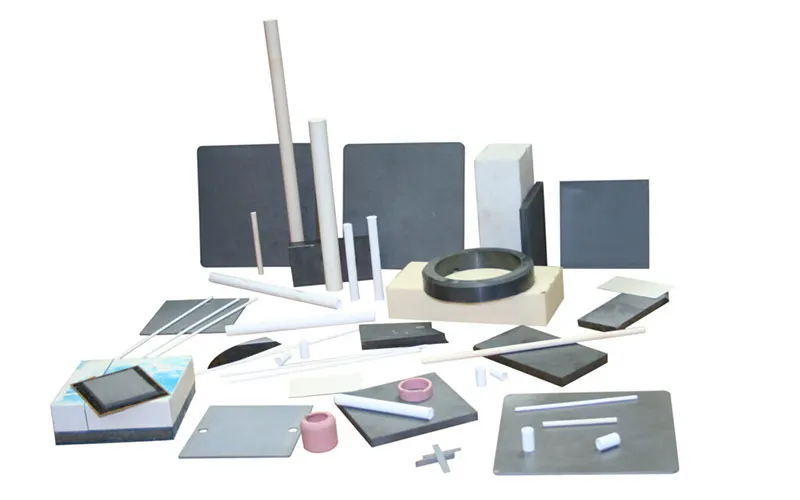

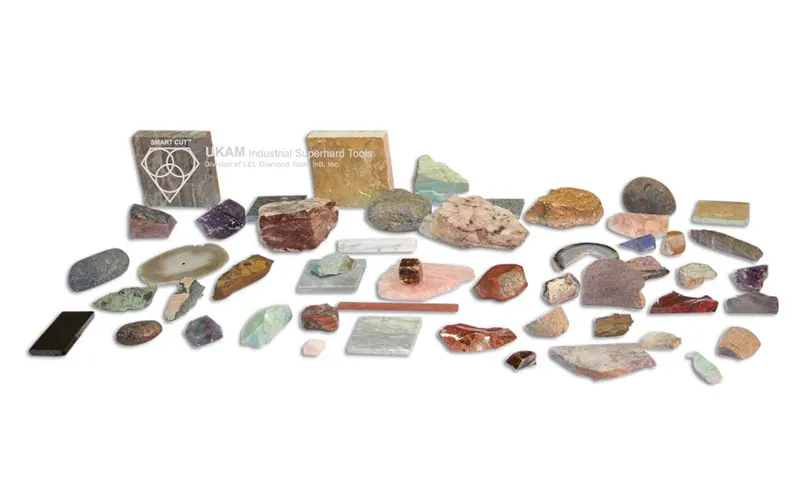
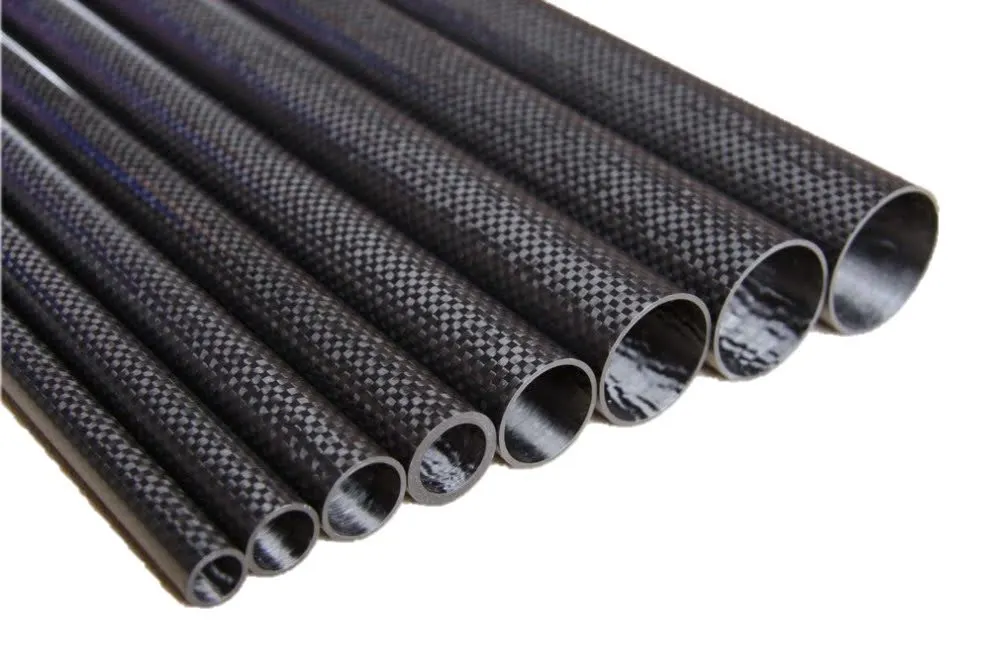
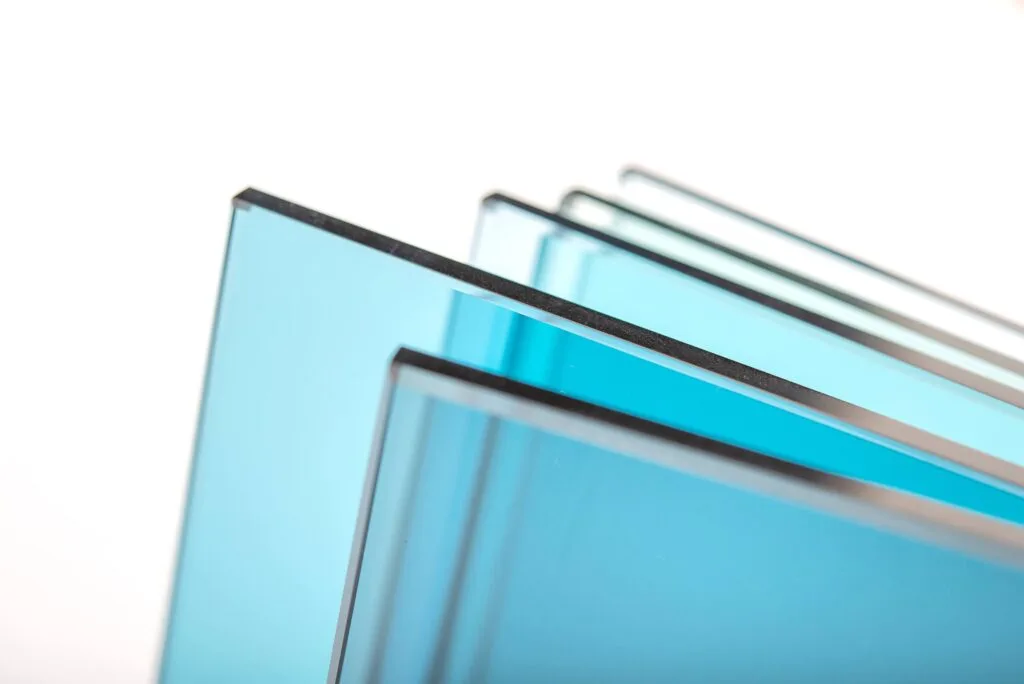
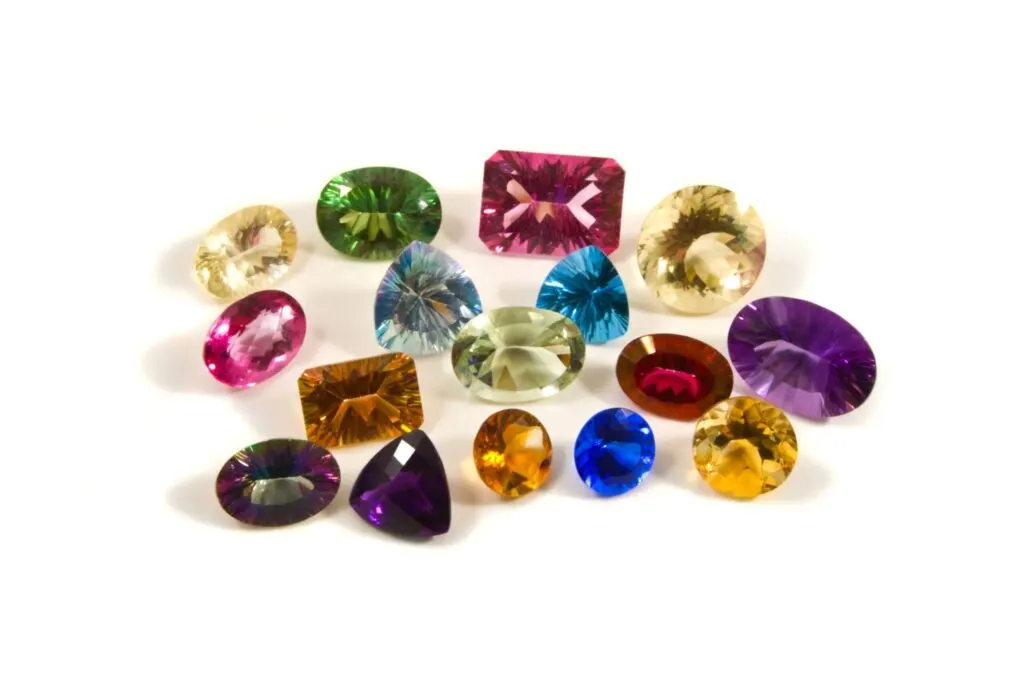
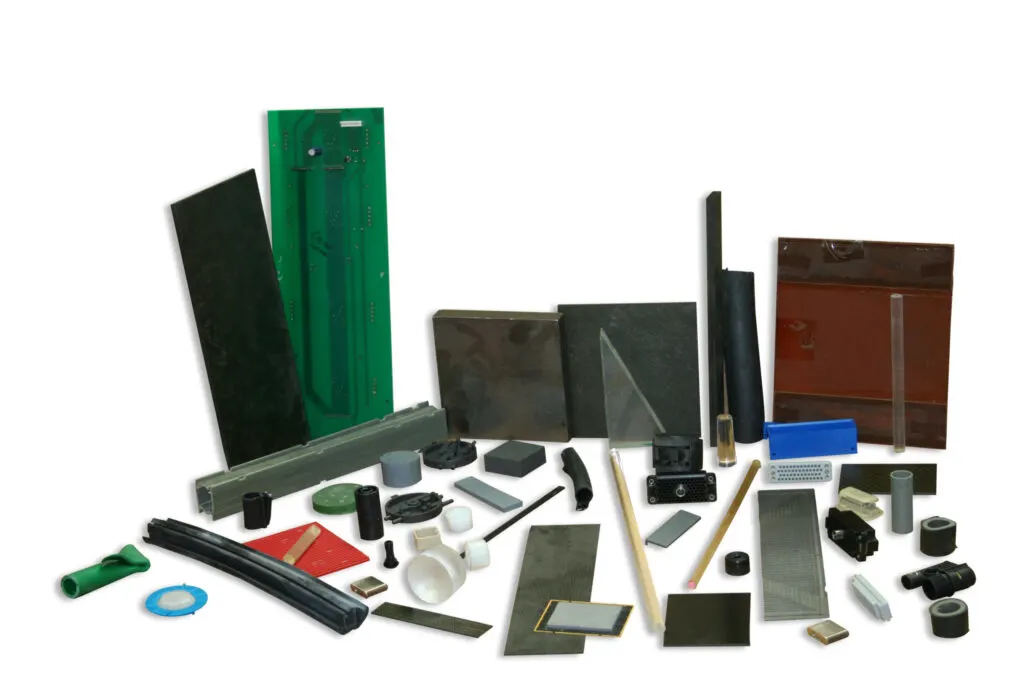
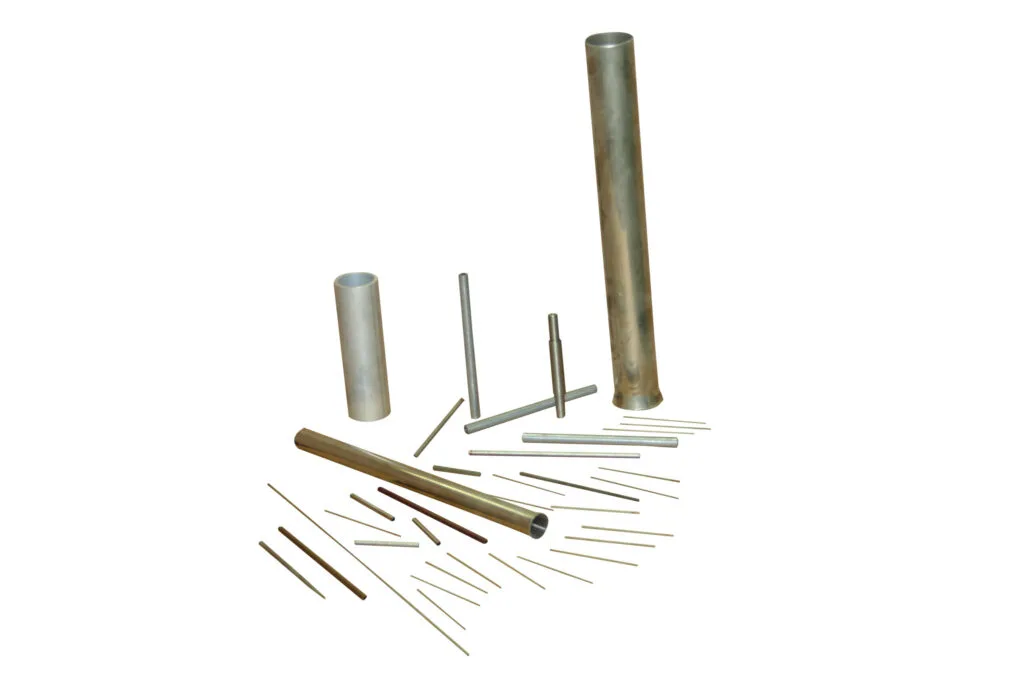
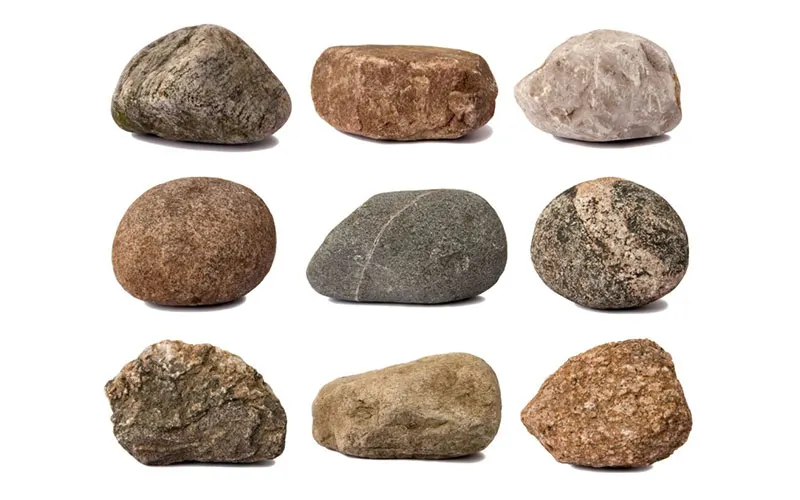
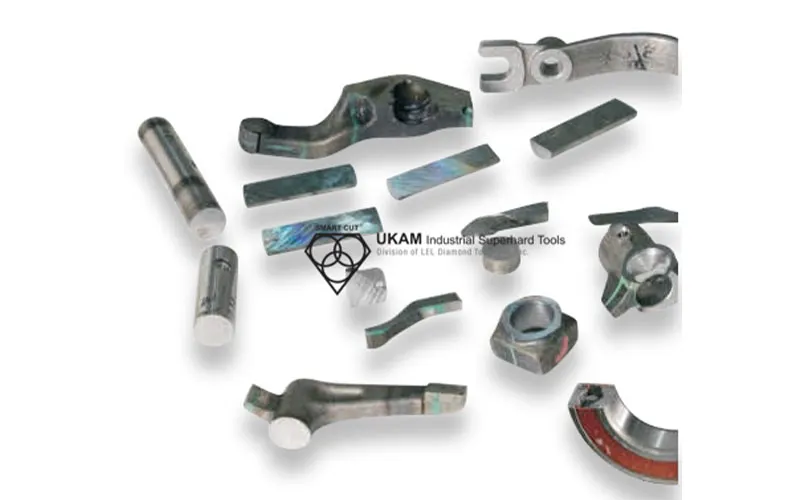
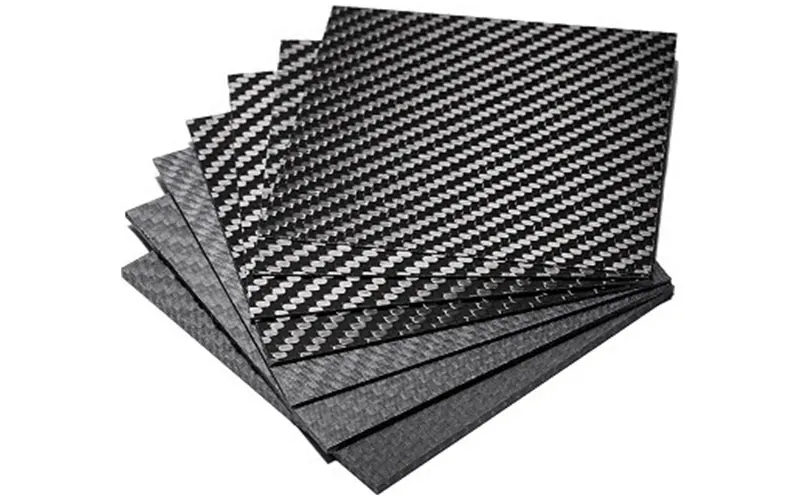
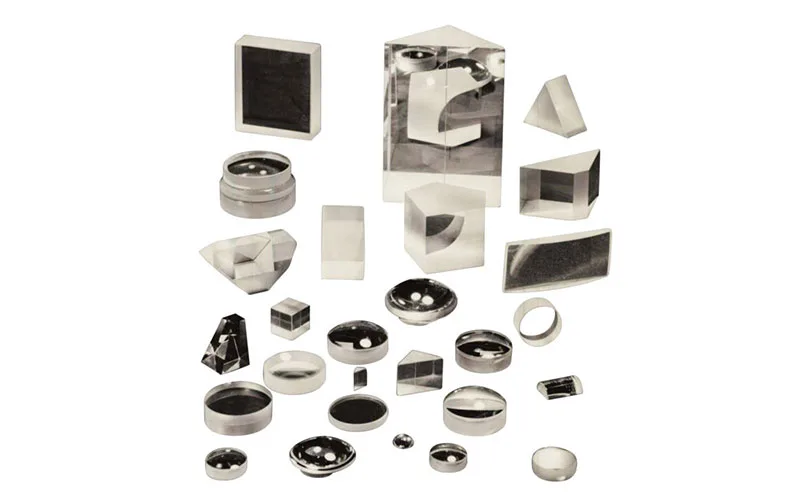
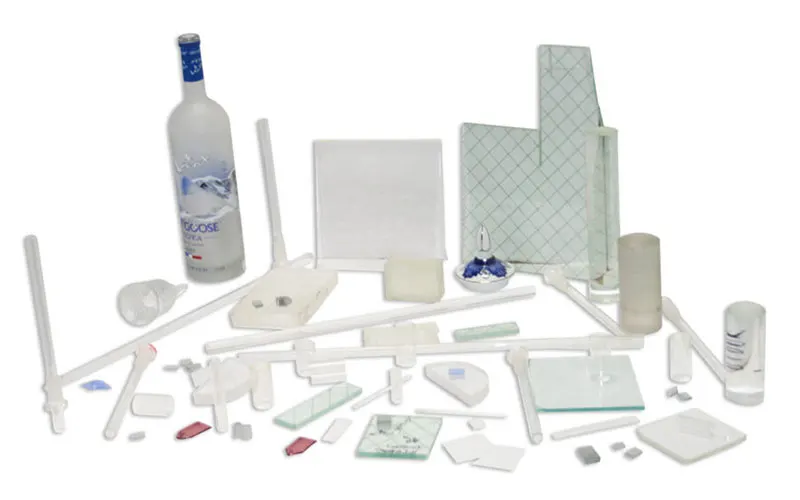
Why use Coolants?
Coolants increase productivity and the quality of material preserve true material micro structure, & minimize material deformation. Coolants increase the time interval between tooling changes. This saves you money by reducing the number of tool or die changes needed. Tooling changes require the shut down of the production lines, therefore less tooling changes will increase productivity. Modern coolants must fulfill two primary functions: cooling and lubrication. Both of these functions are important, but their relative importance depends on the type of operation and material being processed. Find out more >>>
Cooling
Prior to modern high-speed equipment, cooling from a lubricant was not needed. The slow cutting speeds did not generate much heat. The straight lubricants were able to transfer enough heat to avoid damage to the parts and tools. However, modern equipment operates at high speeds. This high speed movement creates tremendous amounts of heat which must be removed by the coolant. Failure to remove the heat and chips in the contact zone, between the cutting tool and the part will shorten tool life and increase the number of tool changes as well as reduce the tolerances of tooling and part because of thermal expansion. Find out more >>>
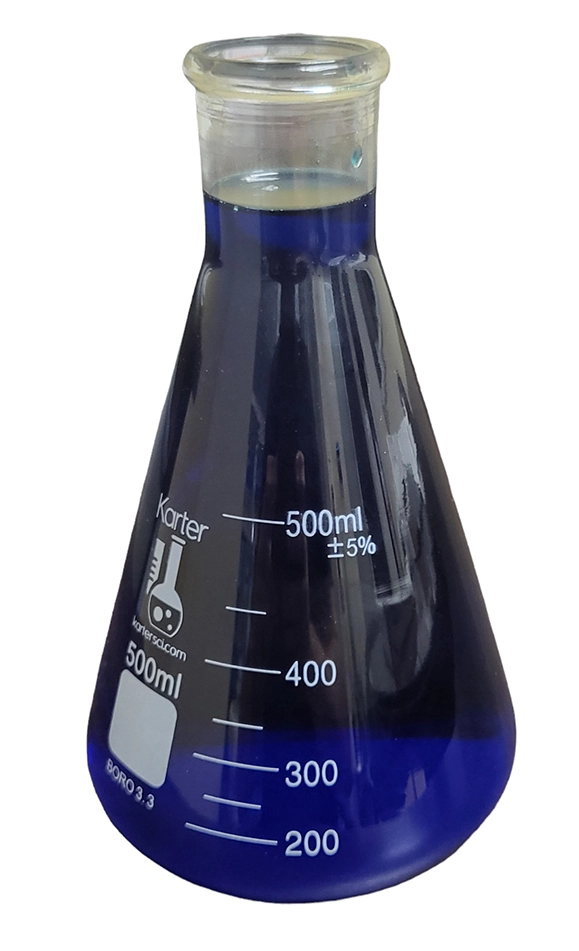
Lubrication
Lubrication provided by the coolant reduces the friction between the tool and material / substrate. The coolant prevents the substrate from sticking to the tool and will increase the surface finish. Some companies are trying to eliminate coolants, which inevitably increase the amount of money spent on tooling and lost production. But some companies feel that this is worth the cost benefit of maintaining the coolant systems and the work associated with the coolants. These companies are in the minority.
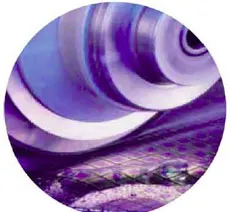
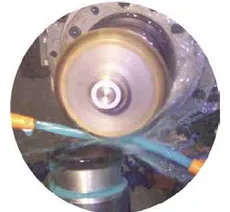
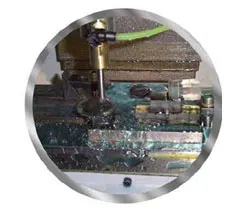
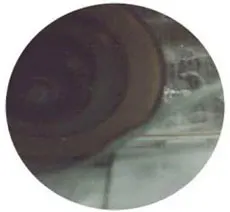
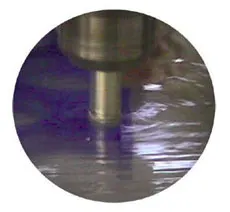
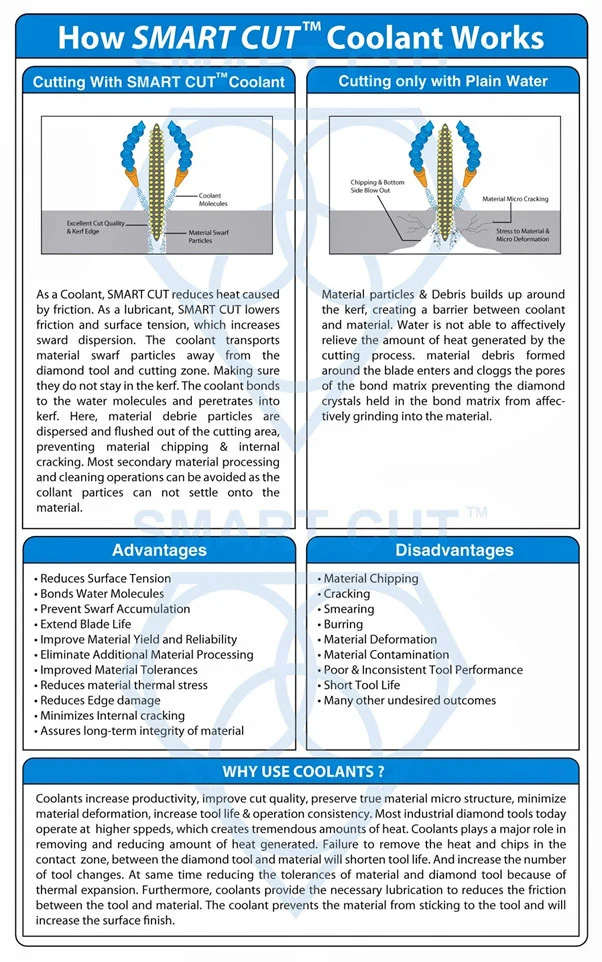
SMART CUT® Coolants Helps Manufacturers and R & D Labs
-
Reduces Surface Tension - by 25-40 dynes/cm2. SMART CUT® Coolant allows more water into the material kerf / pores, dissipating heat generated by friction.
-
Bonds Water Molecules - into the kerf and to the diamond tool, allowing better swarf dispersion and lubrication.
-
Prevent Swarf Accumulation - on the diamond tool and in Back and frontside edges, minimizing chipping and internal cracking.
-
Extend Diamond & CBN Blade, Drill, Wheel, & Tool Life - by up to 30%. The lubricated blade / diamond tool runs cooler, reducing metal fatigue and blade / diamond tool wear.
-
Improve Material Yield and Reliability - from the reduced amount of chipping, cracking and consequent edge damage.
-
Eliminate Additional Material Processing - Depending on the application and your objectives, SMART CUT® Coolant frequently eliminates and minimizes secondary and subsequent material processing.
-
Improved Machining Tolerances - Many of today’s demanding advanced material applications provide challenges to advanced material manufacturers and R & D facilities. Obtaining tolerances less than a millionths of an inch, is not uncommon. SMART CUT® Coolant promotes attainment of close tolerances by removing heat generated at the point of contact between the tool and work piece. Heat can cause deformations in both the tool and work piece that results in the loss of tolerance. When the generation of heat and its subsequent removal by a coolant is momentarily interrupted any coolant product will adversely affect the performance of a tool and therefore ruin a tolerance specification.
TOP 10 REASONS Why SMART CUT® Coolant is SUPERIOR
1. Operator Sensitivity - SMART CUT® Coolant is formulated with operator friendly additives that will not irritate skin (dermatitis), nasal passages, or eyes.
2. Bio-resistance - SMART CUT® Coolant is formulated with biocides and fungicides to biologically control the growth of bacteria, fungi, and mold in the coolant system. The bio-resistance will determine its suitability for recycling in large central systems.
3. Corrosion Protection - SMART CUT® Coolant is formulated with corrosion inhibitors, which provide protection to machinery and the substrate. The protection needed will be determined by the customers requirements. With proper concentration, no corrosion should occur on the machinery.
4. Hard Water Stability - SMART CUT® Coolant should be stable in all water conditions. Hard water ions react with coolant additives and reduce the effectiveness of the coolant solution.
5. Mixability -Concentrate SMART CUT® Coolant should mix easily or .bloom. into the water. Any difficulty in mixing will not be tolerated by the customer.
6. Foam -All water based coolants can potentially foam SMART CUT® Coolant is formulated with defoamers to prevent foaming under most conditions. The proper selection of coolant concentration will help alleviate potential problems.
7. Residue -All water based coolants can potentially foam SMART CUT® Coolant will not leave a .hard-to-remove. residue on the surface of the machine or substrates. As the water in the coolant. evaporates organic residue will be left on the machines. This residue should not be sticky and should be easily re-dissolved in water.
8. Oxidative Stability - High temperatures and pressures will cause changes in the composition of the coolant, such as fragmentation or polymerization of the additives in the coolant formulation. This can decrease the performance of the coolant and create difficult to remove deposits.
9. Emulsion Stability - Concentrate SMART CUT® Coolant mixes easily with water and should not separate or create an invert on the surface of the coolant mixture. Customers currently using soluble oils may be experiencing particular difficulties with this problem.
10. Tramp Oil Rejection - SMART CUT® Coolant should reject the tramp oils and way lubricants, which may contaminate the sump. Other coolants which do not reject tramp oils are prone to attack by bacteria and fungal organisms.
How does SMART CUT® Coolant Compare to Conventional Coolants?
Property/Feature |
SMART CUT® Coolant |
Conventional Coolants |
---|---|---|
Formulation |
Fully synthetic, water-soluble coolant, formulated for a wide range of materials like ceramics, glass, composites, and semiconductors. |
Typically mineral oil-based or emulsions, primarily formulated for metals. |
Cooling Efficiency |
Superior cooling properties, reduces thermal stress and edge damage, effectively removing heat from the cutting zone. |
Cooling efficiency may be limited, especially for hard, brittle, or precision materials. |
Lubrication |
Provides both lubrication and cooling, reducing friction, improving tool life, and enhancing surface finish quality. |
Often provides cooling only, may not offer adequate lubrication for hard materials, leading to higher tool wear. |
Tool Life Extension |
Increases tool life by up to 30% through superior lubrication and cooling, preventing excessive tool wear. |
Tool life may be shorter due to insufficient lubrication, leading to faster wear and more frequent tool replacements. |
Surface Finish Quality |
Improves surface finish by reducing friction, preventing chipping and cracking. |
Surface finish may suffer due to higher friction and inadequate cooling. |
Operator Safety |
Non-irritating to skin, eyes, and respiratory system, offering a safer working environment. |
May cause skin, eye, or respiratory irritation, especially over long-term exposure. |
Bio-resistance |
Formulated with biocides to prevent microbial growth (bacteria, fungi, mold), ensuring coolant cleanliness. |
Typically lacks bio-resistance, leading to microbial growth in the system over time, affecting coolant quality and performance. |
Corrosion Protection |
Excellent corrosion inhibitors that protect both tools and machinery. |
Often provides limited corrosion protection, requiring regular maintenance to prevent rust and corrosion. |
Foam Formation |
Designed with defoamers to prevent foaming under high-speed cutting conditions. |
Can foam excessively, especially in high-speed or high-feed operations, reducing cooling efficiency. |
Residue Formation |
Leaves minimal residue that can be easily cleaned without damaging the workpiece or machinery. |
May leave sticky or hard-to-remove residue on the workpiece, tools, and machinery. |
Emulsion Stability |
Highly stable emulsion, preventing separation or inversion in the coolant mixture. |
Emulsion stability can be an issue, with potential separation or poor mixing in the system. |
Hard Water Stability |
Remains stable even in hard water conditions, ensuring consistent performance across different environments. |
May lose effectiveness in hard water, leading to reduced performance and the need for frequent coolant replacement. |
Mixability |
Easily mixes with water without forming clumps or separation, ensuring smooth and consistent performance. |
May have difficulty mixing with water, resulting in poor emulsion quality and inconsistent performance. |
Environmental Impact |
Environmentally friendly, non-toxic, and biodegradable, reducing the environmental footprint. |
Often contains harmful chemicals (e.g., chlorine, phosphates) that can have negative environmental effects. |
Wetting Properties |
Low surface tension (25-40 dynes/cm²) improves wetting of the material, enhancing cooling and lubrication. |
May have higher surface tension, leading to less efficient cooling and lubrication, particularly on hard materials. |
Toxicity |
Non-toxic, not irritating, and safe for long-term use with minimal health risks. |
Potentially toxic or harmful, with skin irritation and respiratory concerns, especially in confined spaces. |
Swarf Dispersion |
Improved swarf dispersion, preventing swarf accumulation on tools and reducing the risk of chipping or internal cracking. |
May struggle with swarf dispersion, leading to clogged tools and poor cutting efficiency. |
Tolerances and Precision |
Promotes high precision and tight tolerances by preventing thermal distortion and ensuring consistent cooling. |
May struggle to maintain tight tolerances due to inadequate cooling and lubrication, leading to tool deflection and material deformation. |
Oxidative Stability |
Maintains stability under high temperatures and pressures, ensuring reliable performance in extreme conditions. |
May degrade under high temperatures, leading to poor performance and the formation of undesirable deposits. |
Ease of Maintenance |
Minimal maintenance required, easy to clean and dispose of without leaving harmful residues. |
Requires frequent maintenance to prevent microbial growth, foaming, and residue build-up. |
Performance in High-Speed Operations |
Optimized for high-speed cutting and grinding, maintaining performance under rapid and intense operations. |
May underperform in high-speed operations, resulting in tool wear, overheating, and reduced efficiency. |
Cost-Effectiveness |
High dilution ratios (up to 1:75) make it cost-effective in the long term, providing significant productivity gains. |
Often requires more frequent replacement and higher operational costs, leading to inefficiencies. |
Operator Comfort |
Pleasantly scented and does not cause unpleasant odors, improving the working environment. |
Often produces unpleasant odors, contributing to a less comfortable working environment. |
Staining |
Non-staining formulation that does not leave marks or discoloration on materials or equipment. |
May stain materials or machinery, leading to additional cleaning efforts and potential damage to workpieces. |
Compatibility with Filtration Systems |
Fully compatible with all filtration systems, improving the longevity and cleanliness of the coolant system. |
May not be compatible with all filtration systems, leading to more frequent maintenance and system issues. |
Cooling and Lubrication Duality |
Offers both cooling and lubrication in a single solution, ensuring optimal performance for cutting, grinding, and drilling operations. |
Often requires a combination of different products (e.g., separate coolants and lubricants) to achieve both effects, increasing complexity and cost. |
Compatibility with Multi-Stage Machining |
Effective across multiple machining stages, ensuring consistent results throughout the process. |
May require coolant changes or modifications between different stages of machining, which can affect consistency and increase costs. |
Heat Transfer Efficiency |
High heat transfer efficiency, maintaining the cutting zone temperature within optimal ranges for precision cutting. |
Less efficient at transferring heat, especially in high-speed or high-pressure conditions, leading to thermal expansion or material distortion. |
Handling of High Material Hardness |
Specifically formulated to manage high material hardness (e.g., ceramics, composites), ensuring smooth cutting with minimal tool wear. |
Struggles with harder materials, often resulting in more rapid tool wear and decreased cutting efficiency. |
Formulation for Precision Operations |
Optimized for precision cutting applications, maintaining tool sharpness and reducing the risk of dimensional inaccuracies. |
Often less effective in precision operations, where minor temperature fluctuations or friction can affect the final dimensions of the workpiece. |
Additive Integration |
Easily integrates with additional SMART CUT products for a customized solution that suits specific applications, such as diamond wire sawing. |
Typically less adaptable to customization, as most conventional coolants are designed as one-size-fits-all solutions. |
Shelf Life Stability |
Long shelf life without degradation, ensuring consistency in coolant properties throughout extended use. |
Shorter shelf life and more frequent degradation, requiring more frequent replacement or replenishment. |
Machining Speed |
Suitable for high-speed cutting and grinding operations, maintaining optimal performance without overheating. |
May require slower machining speeds to avoid overheating or excessive tool wear, reducing overall productivity. |
Chemical Additives |
Contains no harmful chemical additives like nitrates, nitrites, or phosphates, ensuring cleaner and safer operations. |
May contain chemicals like nitrates, phosphates, or chlorine that can be harmful to operators and the environment. |
Consistency in Application |
Maintains consistent performance across various cutting processes and materials, ensuring uniform results and reduced material waste. |
Performance may vary depending on material types, cutting conditions, and machine settings, leading to inconsistent results. |
Flexibility in Application |
Versatile in a wide range of applications, from slicing delicate ceramics to heavy-duty metal cutting. |
Often limited to specific applications or materials, reducing flexibility in diverse machining environments. |
Compatibility with CNC Systems |
Highly compatible with CNC systems, providing consistent cooling and lubrication during automated, high-precision machining. |
May not be as effective in automated or CNC machining, especially under high-speed or high-precision conditions, leading to potential overheating or tool wear. |
Optimization for Fine Cuts |
Perfect for fine cuts with minimal edge damage, ensuring high precision without microcracking or thermal distortion. |
Fine cuts may suffer from thermal damage, poor surface finish, or higher chances of microcracking, especially with brittle materials. |
Cost Over Time |
Offers long-term cost savings by extending tool life, increasing productivity, and reducing the frequency of coolant replacements. |
Higher long-term costs due to more frequent tool replacements, coolant changes, and potential production slowdowns due to cooling inefficiency. |
Ease of Disposal |
Easy disposal due to its environmentally friendly, biodegradable composition, requiring minimal special handling. |
Disposal may require special treatment due to harmful chemical contents, contributing to higher disposal costs and potential environmental hazards. |
Environmental Safety |
Safe for the environment with no hazardous chemicals, reducing the ecological footprint of the machining operation. |
May introduce environmental risks due to the presence of hazardous chemicals and the difficulty in recycling or disposing of the coolant properly. |
Odor Control |
Pleasantly scented, reducing odors that may cause discomfort in the workplace. |
Often produces unpleasant odors, which may affect both operator comfort and the work environment. |
Concentration Flexibility |
Offers flexible dilution ratios (e.g., 1:20 for drilling, 1:30 for grinding), allowing operators to adjust based on specific needs. |
Less flexible with dilution ratios, often requiring strict adherence to a specific formula or concentration, which may not optimize performance across different tasks. |
Recycling Compatibility |
Compatible with recycling systems, minimizing waste and contributing to more sustainable machining practices. |
May not be suitable for recycling systems, often requiring disposal after use, contributing to higher operational waste. |
Impact on Material Properties |
Preserves the material’s microstructure and long-term integrity by reducing thermal stress and preventing cracking. |
Higher chances of material deformation, cracking, or thermal damage due to inadequate cooling and lubrication. |
Reaction to Extreme Thermal Fluctuations |
Maintains its properties across a wide range of temperatures, ensuring stable performance during rapid thermal changes. |
Performance may degrade under extreme temperature fluctuations, affecting both the coolant and tool effectiveness. |
Adaptation to Cutting Tool Changes |
Remains effective with frequent tool changes in high-volume applications, maintaining consistent cooling and lubrication performance. |
May require adjustments or coolant replacement after each tool change, leading to downtime and reduced efficiency. |
Influence on Swarf Removal |
Optimizes swarf removal by reducing the adhesion of material chips to tools and surfaces, enhancing machining efficiency. |
Swarf may accumulate on the cutting tool, reducing efficiency and leading to tool clogging or poor surface finishes. |
Optimal Performance Across Machine Types |
Provides consistent performance across different types of machinery, from manual to fully automated systems. |
May not provide reliable performance across all machines, particularly in automated systems or high-speed machines. |
Reduced Need for Material Secondary Finishing Operations |
Reduces or eliminates the need for post-processing (e.g., grinding or polishing) due to its excellent cutting precision and surface finish quality. |
Typically requires additional post-processing operations to correct defects caused by poor cutting or excessive tool wear. |
Impact on Cutting Efficiency in High-Velocity Operations |
Facilitates efficient cutting at high velocities, maintaining a smooth cutting action without loss of precision or tool life. |
Struggles to maintain cutting efficiency at high velocities, often leading to heat build-up, tool wear, and slower operations. |
Longevity in Continuous Use |
Designed to withstand continuous use over extended periods, maintaining high performance without degradation or loss of effectiveness. |
Often loses effectiveness after prolonged use, requiring more frequent coolant changes and resulting in decreased overall efficiency. |
Minimizing Cutting Force |
Reduces cutting forces by minimizing friction, allowing for lower power consumption and extended tool life. |
May lead to higher cutting forces, requiring more energy and potentially causing premature tool failure. |
Ability to Handle Fine Detail Work |
Excels in handling delicate or fine detail work, ensuring precision without causing damage to the material or tool. |
Less suited for fine detail work, where tool pressure and heat may cause material damage or loss of precision. |
Machine Component Maintenance |
Minimizes wear and tear on machine components by ensuring efficient heat transfer and reducing the need for frequent cleaning or lubrication. |
Contributes to higher maintenance requirements, as coolant inefficiencies can lead to additional stress on machine components. |
Viscosity Stability at Different Temperatures |
Stays consistent across temperature variations, maintaining optimal viscosity for cooling and lubrication, which is especially beneficial in varying operational conditions. |
Viscosity can change with temperature fluctuations, leading to inconsistent performance, which may require adjustments during machining. |
Resilience in High-Duty Cutting Operations |
Maintains excellent performance in high-duty operations such as continuous grinding or slicing of challenging materials. |
Struggles to perform in high-duty operations, leading to tool wear and reduced cutting efficiency, especially in tough materials. |
Suitability for Smaller Workpieces |
Ideal for smaller, precision workpieces, providing fine control and minimizing material deformation. |
May not perform well with smaller workpieces due to the risk of overheating, causing material deformation or poor finish. |
Effect on Workpiece Finish |
Improves the overall quality and smoothness of the workpiece finish, reducing the need for additional finishing steps. |
Often leaves rough finishes or tool marks on the workpiece, necessitating secondary finishing processes. |
Related Products
SMART CUT® Mineral Oil
SMART CUT® Mineral Oil is recommended for cutting, drilling, grinding and machining larger variety of materials such as:
- Materials with High Metallic Content
- Advanced Ceramics
- Precious & Semi Precious Stone
- Many Other Ultra Hard Materials
SMART CUT® HD Synthetic Low IFT Coolant/Lubricant For Diamond Wire Sawing Silicon
SMART CUT® is a synthetic coolant specifically designed for the cutting of semiconductor materials, including sapphire, silicon, germanium, single-crystal SiC, and II-VI crystals. This coolant offers excellent cut rates and imparts outstanding surface finishes with reduced warp and total thickness variation (TTV). It is ideal for diamond abrasive cropping, squaring, and wafering of silicon ingots using ID, band, and wire saws. SMART CUT® HD-2B can also be used as a non-re-circulating edge grinding coolant or lubricant for silicon wafers and ingots.
SMART CUT® Water Soluble Dicing Coolant
SMART CUT® XP Water Soluble Dicing Coolant added to deionized (DI) water reduces surface tension flowing from saws injection system and is carried directly of dicing blade.
This reduces material thermal stress, edge damage, and internal cracking, assuring long-term integrity of material being processed. Since SMART CUT® XP Dicing Coolant is a coolant and lubricant, and Surfactant both the dicing blade and substrate / wafer / package benefit.
SMART CUT® XP Dicing Coolant/Lubricant is a specially formulated low-foaming dicing and sawing coolant/lubricant designed for precision applications involving wafers with integrated circuits, MEMS devices, and IC packaging. This aqueous-based synthetic formulation enhances the dicing process by ensuring superior cleanliness of the die or package after dicing while preventing corrosion and oxidation on exposed metals. It eliminates electrostatic discharge, which can be generated during the rotation of the dicing blade, protecting delicate components from damage.
Recently Viewed Products
ARE YOU USING RIGHT Coolant
FOR YOUR APPLICATION?
LET US
HELP YOU
HAVING ISSUES WITH
YOUR CURRENT Coolant?
Knowledge Center
02
Jun
How to properly use Diamond Tools
UKAM Industrial Superhard Tools manufactures precision diamond tools for a large variety of applications, materials, and industries.
Share this Article with Friend or Colleague
Metal Bonded Diamond Tools are “impregnated” with diamonds. This means that selected...
02
Jun
Why use diamond
Diamond is the hardest material known to man kind. When used on diamond/tools, diamond grinds away material on micro (nano) level. Due to its hardness Diamond will work all types of materials from...
02
Jun
Diamond vs CBN (cubic boron nitride) Tools
Cubic Boron Nitride (CBN) is a synthetic material that is renowned for its exceptional hardness and high thermal stability. It is composed of boron and nitrogen atoms arranged in a crystal lattice structure, similar to...
02
Jun
What is Diamond Mesh Size and how to select best one for your application
Diamond grit size can be defined as the size of the diamond particles used in the bond matrix. The larger the diamond particles (grit size) the faster the tool will cut.
Share this Article with Friend or...
02
Jun
What is Diamond Concentration and which to use for your application
Diamond concentration is measured based on the volume of diamond within a section of the tool. It is typically defined as Concentration 100, which equates to 4.4 carats per cubic centimeter of the diamond layer...
02
Jun
Diamond Tool Coolants Why, How, When & Where to Use
Coolant is one of the most overlooked variables in the overall diamond or cbn tool machining process. Effective and proper use of coolant and recalculating coolant system will pay off in terms of improved surface...
02
Jun
SMART CUT® Water Soluble Coolant Usage Recommendations
Mixing Ratios, Process, Best Practices, & Optimization
This usage guide will cover most aspects of coolant use, including mixing ratios, the mixing process, best practices, and optimization strategies. We will start by discussing the proper mixing...
17
May
Choosing The Correct Diamond Bond Type
Selecting the appropriate diamond bond type for specific applications is crucial for several reasons. Diamond bond type directly affects the tool's performance, efficiency, and longevity. Different bond types determine how well a tool can withstand...
- Unmatched Selection For Many Applications
- Superior Quality & Consistency
- Immediate Worldwide Delivery
- Technical Support & Expertise
- American Based Manufacturer
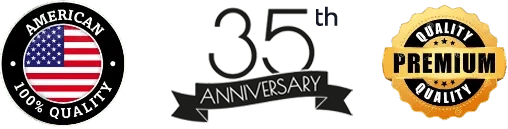

- Different Product
- Different Technology
- Different Company
- Expect MORE from your tools
Let Us HELP You!
Subscribe To Our Newsletter
Signup for email offers, updates, and more
Contact Us
- 25205 & 25201 Avenue Tibbits Valencia CA 91355 USA
-
Phone : (661) 257-2288
FAX : (661) 257 -3833 - lel@ukam.com
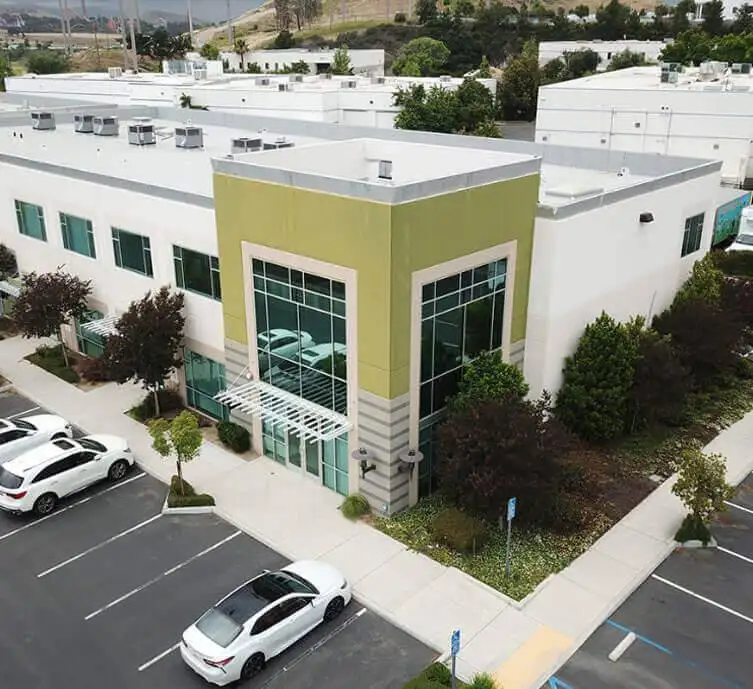
UKAM Industrial Superhard Tools is a U.S. High Technology, Specialty Diamond Tool & Equipment manufacturer. We specialize in producing ultra thin, high precision cutting blades, precision cutting machines diamond drills, diamond micro tools, standard & custom advanced industrial diamond tools and consumables.
- 25205 & 25201 Avenue Tibbits Valencia CA 91355 USA
-
Phone : (661) 257-2288
FAX : (661) 257 -3833 - lel@ukam.com
- 25205 & 25201 Avenue Tibbits Valencia CA 91355 USA
-
Phone : (661) 257-2288
FAX : (661) 257 -3833 - lel@ukam.com
DIAMOND TOOLS BY BOND
EQUIPMENT
KNOWLEDGE CENTER
OUR PRODUCTS
COMPANY
CUSTOMER SERVICE
Shipping Methods


Safe & Secure Payments

© Copyright 1990-2025. UKAM Industrial Superhard Tools – Terms of Use