-
0 items in quote
No products in the Quote Basket.
Resin Bond Diamond Discs for Grinding & Polishing Machines
SMART CUT® diamond discs are specialized tools designed for grinding and sculpting glass, jewelry, stones, ceramics, composites, optics, metals and other hard, dense and brittle materials. These discs are usually produced with either a metal or resin bond and with diamonds impregnated inside. These particles inside the bond matrix provide exceptional abrasion, enabling the discs to efficiently and rapidly grind and shape large variety of materials. They can be produced with or without grooves, and customizing the diameter, size, and all specifications of these wheels can be done with usually no minimum order quantities.
Description
Specifications
Frequently Asked Questions
Industries Used In
Accessories
Recommendations
Description
Tab Content
Specifications
- Bond Type: Sintered (Metal Bond) or Resin Bond
- Abrasive Type: Diamond or CBN (cubic boron nitride)
- Thickness: 20mm to 100mm
- Inside Diameter: 1/2″ (12.7mm) to 5″ (125mm)
- Diamond Grit Size: 60 mesh to 3 microns
Frequently Asked Questions
SMART CUT diamond discs are specialized tools designed for precision grinding and sculpting a wide range of materials, including glass, jewelry, stones, ceramics, composites, optics, metals, and other hard, dense, and brittle materials. These discs are available with either a metal or resin bond and contain embedded diamond particles that provide exceptional abrasion, allowing for efficient and rapid material removal and shaping.
SMART CUT diamond discs offer several advantages over traditional tools. They provide exceptional precision and efficiency, resulting in finer finishes and faster material removal. The embedded diamond particles ensure consistent performance and extended tool life, making them a preferred choice for professionals.
Metal bond diamond discs are known for their durability and are ideal for heavy-duty grinding and shaping tasks. Resin bond diamond discs, like the 1A2 Resin Diamond Grinding Disc, offer versatility and precision, making them suitable for a wide range of materials and applications. The choice between the two depends on your specific needs and the material you are working with.
Yes, SMART CUT diamond discs can be customized to meet your exact specifications, including diameter, size, and other wheel characteristics. This customization can often be done without the need for minimum order quantities, providing flexibility to tailor the tool to your unique applications.
Yes, SMART CUT diamond discs can be produced both with and without grooves, depending on your requirements and preferences. Grooves can help with coolant distribution and debris removal during the grinding process.
Yes, SMART CUT diamond discs can be used for both wet and dry grinding and sculpting. They are versatile tools that adapt to your preferred method, depending on the material and your specific project needs.
The cost of SMART CUT diamond discs is competitive, considering their exceptional performance and customization options. While there may be cheaper alternatives, the quality and precision these discs offer make them a valuable investment for professionals and those seeking top-tier results.
SMART CUT diamond discs provide superior abrasion, allowing for efficient and rapid material removal and shaping. They offer precision, durability, and flexibility, making them essential tools for achieving fine finishes and intricate designs in various hard and brittle materials.
Absolutely, SMART CUT diamond discs are versatile tools that excel in lapidary work. Whether you need to cut, shape, or polish gemstones, these discs offer the precision and durability required for achieving stunning results in jewelry and lapidary projects.
SMART CUT diamond discs are well-suited for working with composite materials. Their ability to efficiently grind and shape composites makes them valuable tools in industries such as aerospace and manufacturing, where composite materials are commonly used.
Yes, SMART CUT diamond discs are designed for consistent performance and extended tool life. The embedded diamond particles ensure that the discs maintain their abrasion capabilities throughout their use, resulting in reliable and long-lasting performance.
When using SMART CUT diamond discs, it’s essential to wear appropriate personal protective equipment, such as safety glasses, gloves, and a dust mask if dry grinding. Additionally, ensure that your work area is well-ventilated, and follow the manufacturer’s recommendations for tool usage and maintenance.
Yes, SMART CUT diamond discs cater to both professionals and hobbyists. Their versatility, precision, and customization options make them accessible and valuable tools for a wide range of users, from experienced professionals to DIY enthusiasts.
SMART CUT diamond discs can be used with both handheld tools and machinery, depending on the specific disc and your project requirements. This adaptability allows for greater flexibility in various work settings.
The lead time for customizing SMART CUT diamond discs can vary depending on your specific customization requests and the manufacturer’s production schedule. It is advisable to inquire about lead times when placing your order to ensure timely delivery for your project.
To extend the life of SMART CUT diamond discs, it’s essential to regularly clean them by brushing off debris and residues after each use. Proper storage in a dry and clean environment can also help prevent contamination and maintain the tool’s performance.
Frequently Asked Questions (FAQ) – Proper Usage and Optimization of SMART CUT Diamond Discs
The ideal RPM for SMART CUT diamond discs depends on the specific disc type and the material you are working with. It’s crucial to consult the manufacturer’s recommendations for the recommended RPM range to achieve the best results. Using the correct RPM ensures both safety and optimal performance.
SMART CUT diamond discs are versatile and can be used with various types of machinery, including bench grinders, lapidary machines, angle grinders, and more. However, it’s essential to ensure that the disc is compatible with your specific machine and that you follow the manufacturer’s guidelines for mounting and operation.
The choice of coolant depends on the material you are working with. Water is a common coolant for most applications, but for certain materials like ceramics or glass, specialized coolants or lubricants may be more effective. Always use the recommended coolant or lubricant to prevent overheating and extend the life of the diamond disc.
The amount of pressure to apply varies depending on the material, the machine, and the specific task. In general, it’s best to start with light to moderate pressure and adjust as needed. Excessive pressure can lead to premature wear and overheating, while too little pressure may result in inefficient grinding. Experiment and find the right balance for your application.
Dressing SMART CUT diamond discs involves removing any glazed or clogged diamond particles that can reduce their cutting efficiency. This can be done using a dressing stick or a dressing tool. Optimizing surface finish often involves adjusting factors like RPM, pressure, and coolant flow to achieve the desired results. Consult the manufacturer’s recommendations and be prepared to experiment to achieve the best finish for your specific application.
Yes, adjusting the machine speed (RPM) can have a significant impact on both performance and speed. Higher speeds may result in faster material removal but could generate more heat. Lower speeds might provide finer finishes but require more time. It’s essential to strike a balance by experimenting with RPM settings to achieve your desired results.
Safety is paramount when using diamond discs. Always wear appropriate personal protective equipment, such as safety glasses, gloves, and a dust mask if dry grinding. Ensure proper ventilation in your workspace and follow the manufacturer’s safety guidelines for the specific disc and machine you are using.
To extend the life of your diamond discs, use the correct RPM, apply the appropriate pressure, and use the recommended coolant or lubricant. Regularly dress the disc to remove glazing and maintain cutting efficiency. Proper storage and handling also contribute to longer disc life.
Yes, technique plays a crucial role in optimizing results. Maintain a consistent and steady hand when working with the diamond disc, and move it evenly across the material’s surface. Avoid excessive lateral pressure, as it can lead to uneven wear on the disc. Experiment with different angles and passes to achieve the desired finish and material removal rate.
Yes, SMART CUT diamond discs are versatile enough to handle both rough grinding and fine polishing tasks. You can adjust factors such as RPM, pressure, and coolant flow to transition from coarse to fine work smoothly. This versatility makes them valuable tools for achieving a range of surface finishes.
To control heat buildup, use an appropriate coolant or lubricant as recommended for your material. Ensure that your machine’s RPM is within the recommended range. If you notice excessive heat, reduce pressure, increase coolant flow, or lower the RPM to maintain a cooler operating temperature.
A decrease in performance can be a sign of disc wear or glazing. To address this, consider dressing the disc to remove glazing and expose fresh diamond particles. If the disc is significantly worn, it may need replacement. Regular maintenance and proper usage can help prolong the life of your diamond discs.
Yes, SMART CUT diamond discs are versatile enough to handle intricate and detailed work. Their precision and fine abrasive qualities make them suitable for achieving intricate designs and precise cuts, whether you’re working on jewelry, glass art, or other intricate projects.
The choice of grit or mesh size depends on the material and the desired finish. Coarser grits are suitable for rapid material removal, while finer grits are better for achieving a polished surface. Consult the manufacturer’s recommendations and consider the specific requirements of your project when selecting the appropriate grit or mesh size.
SMART CUT diamond discs can be used on curved or irregular surfaces, but they are most commonly associated with flat work. Achieving consistent results on curved surfaces may require adjustments to technique and pressure to maintain contact between the disc and the workpiece.
Yes, SMART CUT diamond discs are well-suited for beveling or chamfering edges on materials like glass and ceramics. Their precision and fine abrasive qualities allow for the creation of precise angles and edges, enhancing the overall finish of your workpiece.
To achieve a mirror-like finish, start with a coarser grit or mesh size to remove any imperfections or scratches from the surface. Gradually progress to finer grits, using a slow and steady approach. Use an appropriate coolant to prevent overheating, and adjust RPM and pressure for optimal control and a flawless mirror finish.
SMART CUT diamond discs are suitable for glass engraving and intricate etching work. Their precision and fine abrasives allow for detailed designs and patterns to be created on glass surfaces. Ensure proper technique and control to achieve the desired results
Dressing SMART CUT diamond discs can help maintain their cutting performance. Use a dressing stick or tool provided by the manufacturer and follow their guidelines for proper dressing techniques. Regular dressing removes glazed particles and exposes fresh diamond abrasives, ensuring consistent and efficient cutting.
Yes, SMART CUT diamond discs can be used for projects involving delicate or fragile materials like stained glass restoration. Their precision and controlled material removal make them suitable for such tasks. Ensure a light touch and adjust RPM, pressure, and coolant flow to minimize the risk of damage to fragile surfaces.
SMART CUT diamond discs are well-suited for lapidary work, including intricate facet cutting on gemstones. Their precision and fine abrasives enable lapidary artists to achieve detailed and precise facets, enhancing the brilliance of gemstones.
Store SMART CUT diamond discs in a dry and clean environment, away from dust and contaminants. Proper storage helps prevent disc contamination and ensures they maintain their cutting efficiency over time. Avoid exposing them to extreme temperature fluctuations.
Yes, SMART CUT diamond discs are suitable for intricate profiling tasks, allowing you to create custom shapes and contours with precision. Their fine abrasives and versatility make them valuable tools for achieving complex designs in various materials.
Yes, you can achieve matte or textured finishes on materials like metals or glass using SMART CUT diamond discs. To do so, experiment with lower RPM, light pressure, and coarser grits to create the desired texture or matte appearance. Adjust your technique to control the level of texture.
SMART CUT diamond discs are effective for regrinding and repairing damaged surfaces on materials like ceramics and composites. Their precision and abrasion capabilities allow for controlled material removal, making them suitable for restoring surfaces to their intended condition.
Yes, SMART CUT diamond discs can be used for both dry and wet grinding and sculpting, depending on your preferences and material requirements. Using water or an appropriate coolant can help control dust, reduce heat buildup, and extend the life of the disc.
SMART CUT diamond discs are adaptable and can be used on irregularly-shaped workpieces, including free-form sculptures and custom jewelry designs. Their precision allows for intricate work on various shapes and contours, making them valuable tools for artistic and creative projects.
SMART CUT diamond discs may have a break-in period during initial usage. It is recommended to start with lighter grinding or sculpting tasks to allow the diamond abrasives to expose themselves gradually. After this break-in period, you can progressively tackle more challenging projects with improved performance.
Yes, SMART CUT diamond discs are excellent for reconditioning or refurbishing older pieces of glass or jewelry. Their ability to efficiently remove imperfections and reshape surfaces makes them valuable for restoring the luster and quality of older items.
Achieving the best balance between speed and precision involves fine-tuning factors like RPM, pressure, and coolant flow. Start with lower RPM and pressure for precision work, and gradually increase as needed for faster material removal. Experiment and adjust to find the optimal balance for your specific project.
SMART CUT diamond discs are suitable for applications that require consistent and uniform material thickness. Their precision and fine abrasives allow you to achieve accurate and even thickness in materials like glass and ceramics, making them valuable for creating precise panels or tiles.
To prevent chipping or damage to the edge of SMART CUT diamond discs, avoid making direct contact with hard surfaces or applying excessive lateral pressure. Maintain a controlled and even approach when grinding or sculpting near edges to ensure the disc remains intact and functional.
Yes, SMART CUT diamond discs can be used to achieve specific surface finishes, including satin or frosted appearances, on materials like glass or metal. Experiment with different grits and techniques to control the level of texture and finish, allowing you to achieve your desired aesthetic results.
Cleaning and maintaining SMART CUT diamond discs is essential for their longevity and performance. After each use, brush off debris and residues from the disc’s surface. Store them in a dry and clean environment, away from contaminants. Regularly dress the disc to remove glazing and expose fresh diamond particles for consistent performance.
Yes, SMART CUT diamond discs are suitable for tasks that require intricate detailing, including engraving initials or patterns on jewelry pieces. Their precision allows for fine and delicate work, making them valuable for adding intricate designs to jewelry and other small objects.
Common mistakes to avoid include applying excessive pressure, using the wrong RPM, not using an appropriate coolant or lubricant, and neglecting proper safety precautions. Overheating, uneven wear, and safety hazards can result from these errors. Always follow manufacturer recommendations and guidelines to prevent mistakes and achieve the best outcomes.
To minimize disc clogging during extended use, use an appropriate coolant or lubricant to control dust and debris. Regularly brush or clean the disc’s surface to remove accumulated particles. Adjust coolant flow and RPM as needed to maintain efficient material removal and prevent clogging.
Yes, SMART CUT diamond discs are well-suited for tasks that involve creating precise angles or bevels, such as beveled glass edges or metal chamfers. Their precision and fine abrasives allow for controlled material removal, enabling you to achieve accurate and well-defined angles and bevels.
When using SMART CUT diamond discs for extended periods, ensure adequate ventilation to disperse dust and fumes. Consider using personal protective equipment like a dust mask and eye protection. Take regular breaks to prevent operator fatigue and discomfort. Additionally, maintain proper ergonomics to minimize strain during prolonged use.
To achieve a high-gloss or mirror-like finish on materials like acrylic or plastic using SMART CUT diamond discs, progressively use finer grits or mesh sizes. Start with coarser grits to remove imperfections and scratches and gradually move to finer grits. Maintain consistent pressure and use an appropriate coolant to prevent overheating for a flawless finish.
SMART CUT diamond discs are versatile and can be used for sculpting 3D objects or creating intricate relief patterns in materials like wood or stone. Their precision and fine abrasives allow for detailed and creative work, making them suitable for sculptors and artisans.
To prevent accidental damage or breakage during storage or transport, store SMART CUT diamond discs in their original protective packaging or use appropriate storage containers. Avoid stacking heavy objects on top of them and handle them with care to prevent chips or fractures. Proper storage and handling can extend the life of your diamond discs.
Yes, SMART CUT diamond discs can be used for restoring or refinishing antique or vintage pieces, including fine china and decorative glassware. Their precision and controlled material removal capabilities make them valuable tools for bringing older items back to their original luster and quality.
To ensure that SMART CUT diamond discs maintain their flatness and true shape, store them in a flat and stable position, and avoid exposing them to excessive pressure or uneven loads during storage. Regularly inspect the disc’s surface for signs of wear or unevenness and address any issues promptly to maintain consistent results.
To achieve an even and uniform surface finish on large-scale projects, consider using a consistent and overlapping pattern when moving the diamond disc across the workpiece. Maintain a steady pace and pressure to ensure even material removal. For large projects, using machinery with variable speed control can help achieve the desired finish efficiently.
Yes, SMART CUT diamond discs are suitable for edge profiling and contouring on materials like granite or marble for architectural applications. Their precision allows for detailed edge work, creating custom profiles and contours to meet specific architectural design requirements.
When working with highly abrasive materials, use a high-quality SMART CUT diamond disc designed for such applications. Ensure that the RPM, pressure, and coolant/lubricant are optimized for the material to prevent excessive wear. Dress the disc regularly to expose fresh diamond abrasives and maintain cutting efficiency.
SMART CUT diamond discs are well-suited for intricate inlay work or creating mosaics on materials like ceramic tiles or semiprecious stones. Their precision and fine abrasives allow for detailed and artistic designs, making them valuable for crafting custom patterns and inlays.
For precision drilling or creating holes, use SMART CUT diamond core bits or drills designed for such tasks. Follow the manufacturer’s guidelines for speed, pressure, and coolant/lubricant usage to achieve clean and accurate holes. Proper tool selection is crucial for achieving precise results.
Yes, SMART CUT diamond discs are suitable for projects that require intricate texturing or engraving on materials like natural stone or porcelain. Their precision and controlled material removal capabilities make them ideal for creating detailed texturing and engraving designs on a variety of surfaces.
Yes, SMART CUT diamond discs are suitable for restoring or refurbishing historic architectural details, including ornate stone carvings or decorative metalwork. Their precision and fine abrasives allow for intricate and delicate work, making them valuable tools for preserving and revitalizing historical structures.
Proper alignment of SMART CUT diamond discs is essential to ensure even wear and consistent performance. Follow the manufacturer’s instructions for mounting and aligning the disc on your machinery. Ensure that it is securely fastened and balanced to prevent uneven wear and vibrations during operation.
Yes, SMART CUT diamond discs are compatible with automated CNC (Computer Numerical Control) machines for high-precision tasks, including engraving intricate designs on metals or glass. CNC machines provide precise control, allowing for accurate and repeatable results in complex applications.
Disc wobbling or vibration can indicate issues with disc alignment or balance. If you experience these problems, stop the machine immediately and inspect the disc for any irregularities or damage. Correct any alignment or balance issues before resuming operation to ensure safe and smooth usage.
Yes, SMART CUT diamond discs can be used for restoring or repairing fine art sculptures, such as marble or stone statues, without damaging the original artwork. Their precision and controlled material removal capabilities make them valuable tools for art restoration, allowing for the careful preservation of valuable sculptures.
To maintain a consistent and even material thickness, ensure that the SMART CUT diamond disc is aligned and mounted correctly on the machinery. Use a steady and controlled motion when cutting or grinding to avoid variations in thickness. Regularly check the workpiece for uniformity during the process to achieve precise results.
Yes, SMART CUT diamond discs can be used for creating custom or specialty bevels on glass or mirror surfaces for decorative or functional purposes. Their precision and controlled material removal capabilities allow for the creation of intricate and customized bevel designs to meet specific project requirements.
When transporting SMART CUT diamond discs, use suitable protective packaging to prevent damage. Ensure they are securely stored to avoid shifting or impact during transit. Proper handling and storage during transportation will help ensure they arrive at the project site in optimal condition.
Absolutely! The 1A2 Resin Diamond Grinding Disc is excellent for sharpening a variety of tools, including knives, scissors, and precision instruments. The diamond abrasives ensure a sharp and long-lasting edge.
Yes, this grinding disc is ideal for shaping and polishing diamonds. Its precision diamond abrasives enable you to achieve exquisite facets and a brilliant finish on diamonds, making it a valuable tool for jewelry professionals.
Yes, this grinding disc is designed to be user-friendly and suitable for both beginners and experienced professionals. Its ease of use allows you to achieve professional-level results with minimal effort.
No, the 1A2 Resin Diamond Grinding Disc features a premium resin bond that provides excellent heat resistance. You can use it for extended periods without worrying about overheating, ensuring consistent performance.
This disc is crafted for durability and engineered to withstand continuous use across various materials. Its lifespan depends on usage frequency and intensity, but with proper care, it should provide long-lasting performance.
Yes, this grinding disc is compatible with most lapidary and grinding machines. It is designed to be easily integrated into your existing equipment, making it a convenient choice for professionals and hobbyists alike.
The flat disc design ensures even and consistent material removal, making it ideal for creating flat surfaces, facets, and precise angles on your workpieces. It eliminates the risk of uneven surfaces and helps you achieve professional-quality results.
While this disc can be used for dry grinding and polishing, it is often recommended to use it with water or a suitable coolant, especially when working with materials like glass and ceramics. Using water or coolant helps control dust and keeps the disc and workpiece cool during operation.
To maintain the disc’s performance, regularly clean it by brushing off debris and residues after each use. Store it in a dry and clean environment to prevent contamination. Proper maintenance will ensure consistent and reliable results.
Industries Used In
Tab Content
Accessories
Tab Content
Recommendations
Tab Content
Advantages:
- Maximum Performance: These discs are engineered for maximum efficiency. The combination of industrial-grade diamonds and specialized bonding materials ensures that you can complete your projects quickly and with precision.
- Long Life: The high-quality diamond coating on the discs means they have a longer lifespan compared to conventional grinding tools. This can result in cost savings over time as replacements are less frequent.
- Universal Application: These discs can be used on a wide range of materials, making them a versatile addition to any workshop or toolbox. From delicate jewelry work to heavy-duty industrial applications, they have you covered.
- Consistency: Achieving consistent results is crucial in many industries. These discs provide uniform grinding and shaping, ensuring that your finished products meet high-quality standards
Applications:
- Glasswork: Perfect for precision grinding and shaping glass pieces for art, architecture, or practical use.
- Jewelry Making: Ideal for creating intricate jewelry designs, shaping gemstones, and polishing metals.
- Stone Sculpting: Used by sculptors and stone artisans to shape and carve hard stones into beautiful sculptures.
- Ceramics: Essential for precision work in ceramics, ensuring smooth edges and precise shapes.
- Industrial Use: Suitable for various industrial applications, including tool and die production, metalworking, and more.
Features:
- Exceptional Hardness: These discs are coated with industrial-grade diamonds, which are significantly harder than the materials they are designed to grind. This exceptional hardness ensures efficient material removal and long-lasting performance.
- Precision and Consistency: The use of diamonds as the abrasive material ensures precise and consistent grinding or shaping results. This is crucial for applications such as jewelry making, glasswork, and stone sculpting, where accuracy is paramount.
- Versatility: These discs can be used on a wide range of materials, including glass, jewelry, stones, ceramics, and more. This versatility makes them valuable tools for professionals across various industries.
- High Abrasion Resistance: The industrial-grade diamonds provide a high level of abrasion resistance, meaning the discs maintain their cutting efficiency over extended periods. This reduces the need for frequent replacements and saves on operating costs.
- Customization: These discs come in various sizes and can be supplied with or without grooves, allowing users to choose the best fit for their specific projects and requirements. Customization ensures maximum flexibility in applications.
- Efficiency: The combination of hardness and abrasion resistance results in efficient material removal. This means faster work completion, which can increase productivity and save time.
- Longevity: Due to their durability and resistance to wear, these discs have a longer lifespan compared to conventional grinding tools. This translates to cost savings in the long run.
- Uniform Results: These discs provide consistent and uniform grinding or shaping results, ensuring that the finished products meet high-quality standards. This is crucial in industries where precision and uniformity are essential.
- Reduced Heat Generation: Depending on the specific application, these discs can generate less heat during the grinding process compared to other abrasive tools. This can be advantageous for materials that are sensitive to temperature changes.
- Safety: When used correctly and with proper safety precautions, these discs offer a safer grinding and shaping solution compared to some traditional methods that may involve more hazardous materials.
- Wide Range of Applications: From delicate jewelry work to heavy-duty industrial tasks, these discs can be applied in various settings, making them versatile and adaptable tools.
- Improved Surface Finish: Resin-bonded discs, in particular, can provide a smoother finish, which is beneficial in applications where aesthetics and surface quality are crucial.
About Sintered (Metal Bond)
Sintered (metal bonded) diamond tools have multiple layers of diamonds impregnated inside the metal matrix. Diamonds are furnaces sintered in a matrix made of iron, cobalt, nickel, bronze, copper, tungsten, alloys of these powders or other metals in various combinations. Metal bonded diamond tools are “impregnated” with diamonds. This means that selected diamonds are mixed and sintered with specific metal alloys to achieve the best cutting performance possible on any materials such as sapphire, advanced ceramics, optics, glass, granite, tile and etc. The metal bond surrounding the diamonds must wear away to continuously keep re-exposing the diamonds for the diamond tool to continue cutting. Sintered (metal bonded) diamond tools are recommended for machining hard materials from 45 to 75 on rockwell scale (5 to 9.5 on mohe’s scale of hardness).
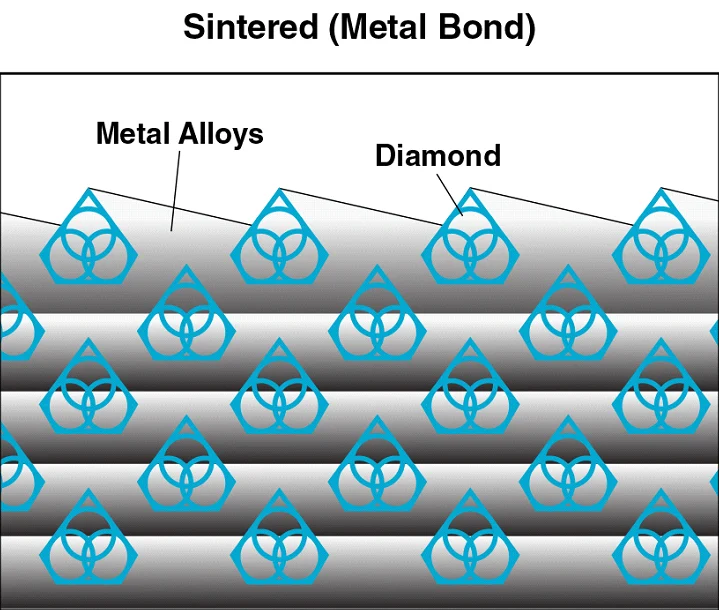
How SMART CUT® Bond Works?
Step 1
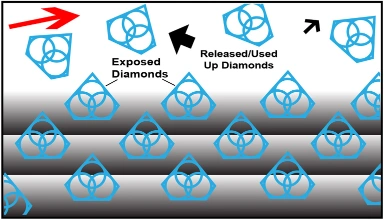
Sharpest And Finest Quality Diamonds
The newly exposed diamonds don’t effect diamonds already working on the material. Unlike many other diamond bonds, diamonds in a SMART CUT® Bond remains sharp and grow sharper with each cut, prolonging product life and consistent performance.
Step 2
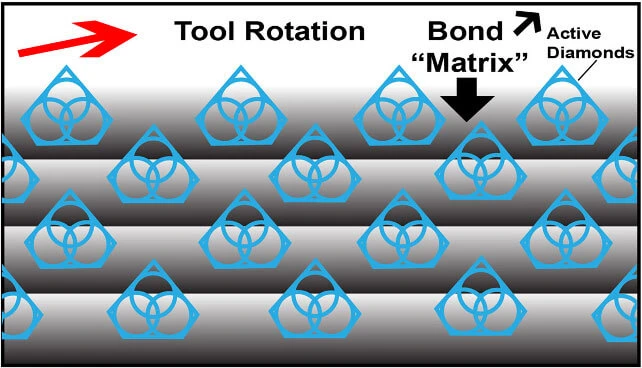
Diamonds or CBN Crystals
Diamonds or CBN Crystals are activated only at the exposed layer. As Bond Matrix layer begin to wear out, diamonds in a new Bond Matrix layer are immediately activated, substituting the already used up diamond layer. The SMART CUT® Diamond Hybrid Bond makes sure every diamond is in the right place and at the right time, working where you need it most.
Step 3
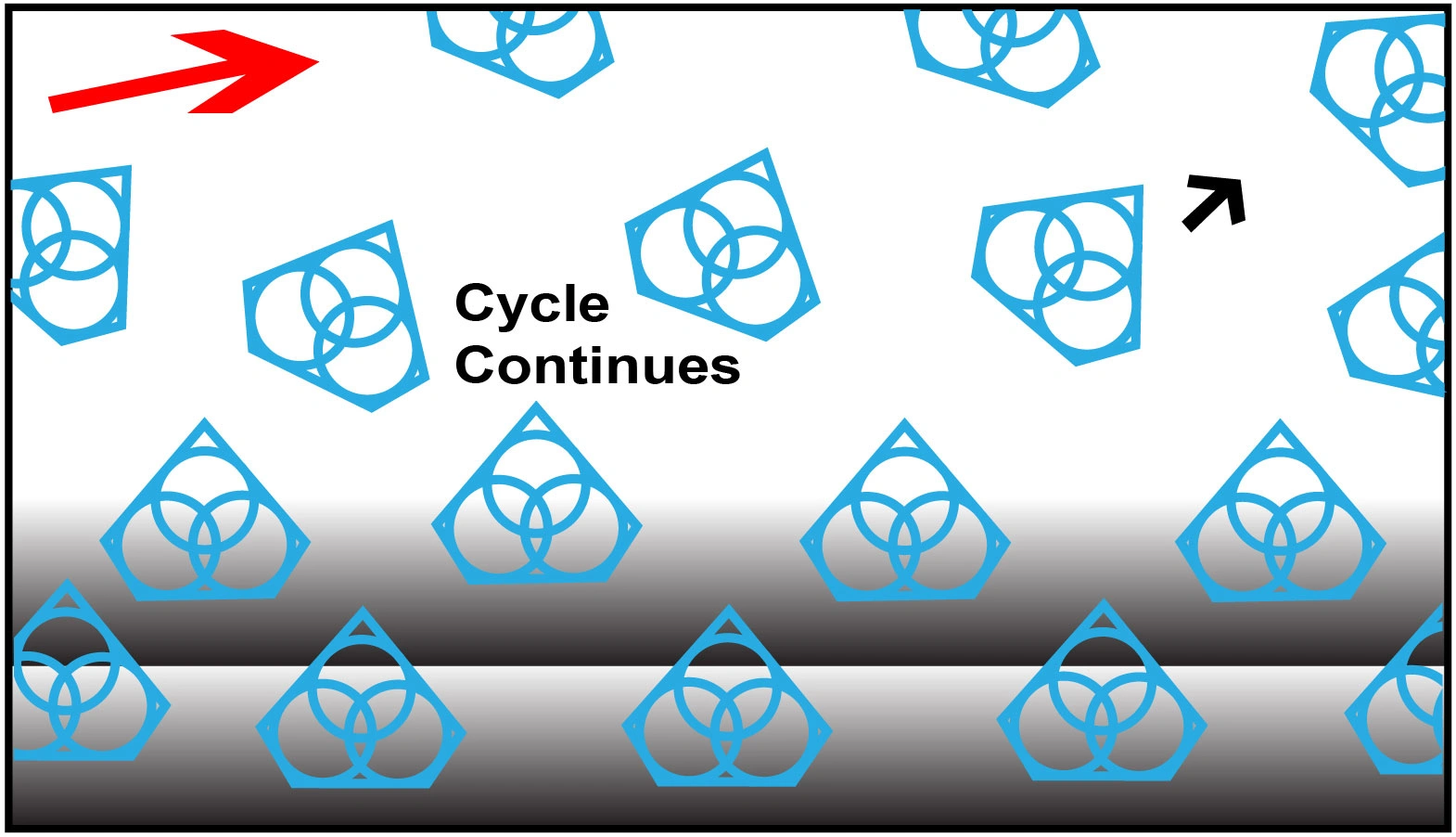
Advanced Formulated Open Diamond Bond Design
This advanced formulated open diamond bond design insures minimal chipping, fast cut, constant speed of cut, minimal cutting noise, and most important of all, consistent performance.
Longer
Life
In most cases tools manufactured utilizing SMART CUT® technology, will outlast other conventional material (sintered), resin, and nickel bonded diamond & CBN tools. SMART CUT® diamond & CBN tools are more sturdy than tools manufactured with conventional technologies. They are capable to retain their form and bond configuration all the way through the tools life.
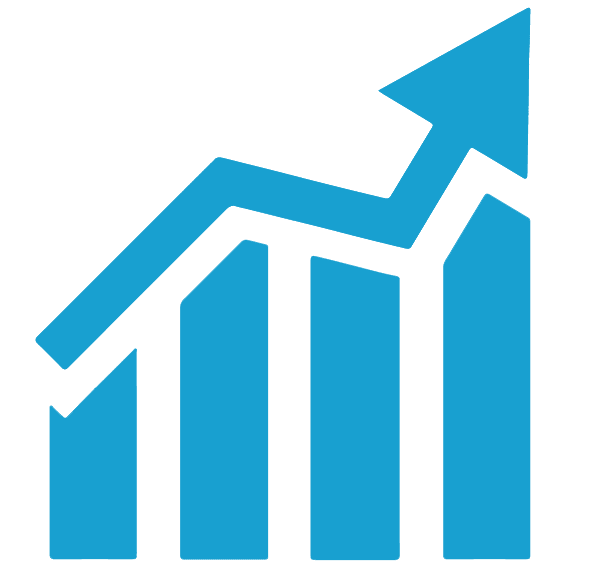
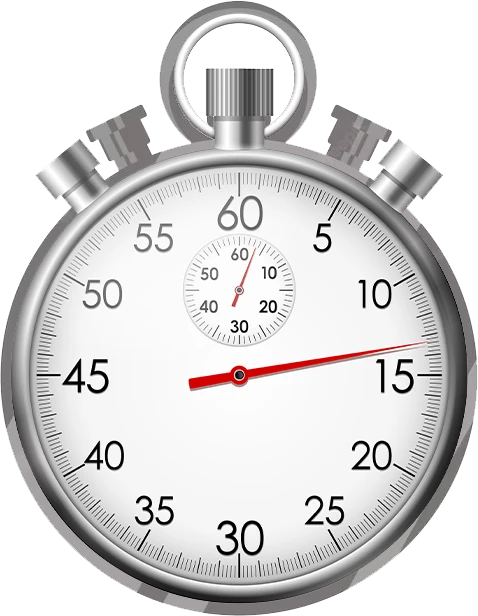
Faster
Cutting Action
Diamond & CBN tools made utilizing SMART CUT® technology are much more aggressive than your conventional tools. They can cut faster, while still leaving behind a smooth finish free of material deformation.
More
Consistent Performance
SMART CUT® Sintered (Metal Bond) Tools have diamonds crystals oriented and evenly positioned inside bond matrix. Unlike Many Other Tool Types, they wear evenly, and are known for their consistency. You will get consistent cutting speed, and overall consistent performance, with minimum amount of dressing even on the hardest to cut materials
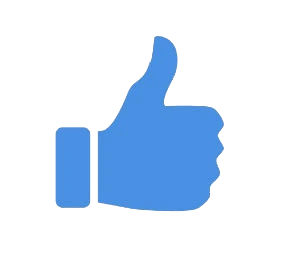
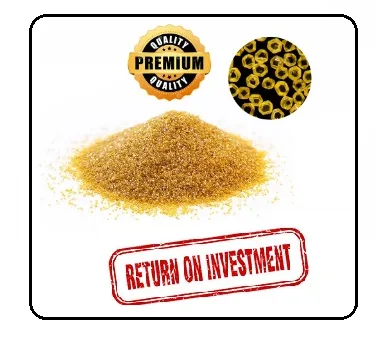
Manufactured Using
The Highest Quality Raw Materials
Only the highest quality synthetic diamonds and raw materials are used in the manufacturing process. The highest quality standards and product consistency is maintained, using sophisticated inspection and measurement equipment.
Best
Performance & Value on the Market
SMART CUT® Sintered (Metal Bond) Diamond Tools are the best investment you can make! Although they may cost more than some Sintered (Metal Bond) Tools. They will more than pay for themselves in terms of overall performance and provide best Return on Investment.
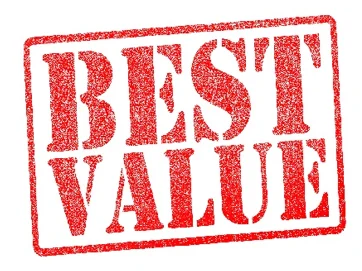
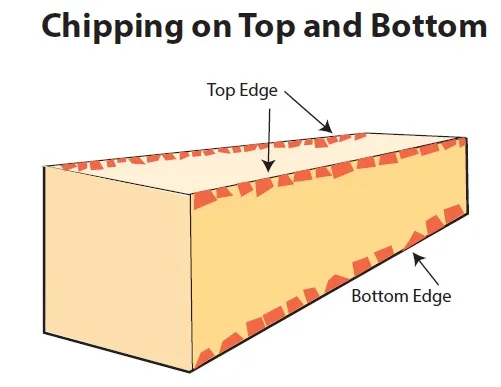
Minimize Chipping &
Improve Surface Finish
SMART CUT® Sintered (Metal Bond) Tools have diamonds oriented and evenly distributed in a bond matrix. Providing faster, freer cutting action with minimum heat generation. This translates in improved surface finish and minimum chipping.
Why Choose Us?
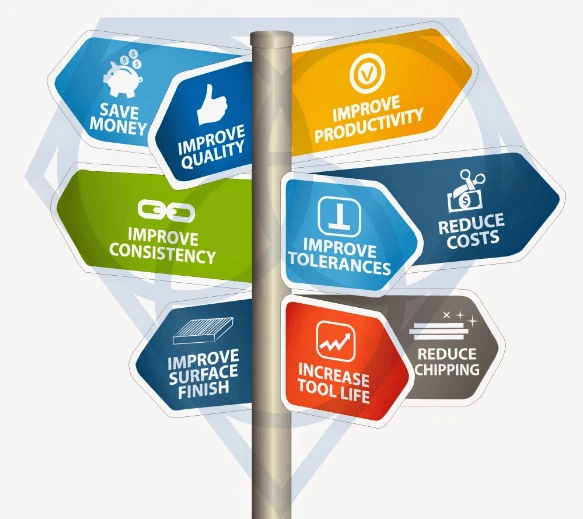
- Unmatched Selection For Many Applications
- Unmatched Technical Support & Expertise
- Superior Quality & Consistency
- Super Technology & innovation
- Immediate Worldwide Delivery
- American Based Manufacturer
-
Custom
Manufacturing - Better Value manufacturer Direct Price
Related Products
SMART CUT® Metal Bond Diamond Discs for Large Grinding / Polishing Machines
SMART CUT® Resin Bond Diamond Polishing Discs
Resin Bond Diamond Discs
Resin Bond Discs are designed removal of material/sample scratches, chips. high spots, & as well as pre-polishing on a larger variety of materials. Using a propriety technique, a high concentration of premium diamond is loaded onto each disc to provide an extremely aggressive grinding rate yet leaves an exceptionally smooth surface finish. Each disc is color coded to easily determine the diamond size of the disc. These resin bond diamond discs are guaranteed to out-perform many cloth polishing discs using loose conventional abrasive or diamond compound/slurry finishing systems. Depending on the application and process these discs on average will last for 100-200 parts/samples & maintain consistent level of performance. These are perfect for hard materials such as metals, ceramics, refractories, cement, geological rocks, glass, optics, composites, and many other materials 35 and up Rockwell C scale of hardness. All discs come with a 3M pressure-sensitive adhesive backing that bonds to backing plates, or with magnetic backing to attach to steel plates. Must be used with coolant. Not recommended for heavy stock material removal
DIAMOND LAPS
UKAM Industrial Superhard Tools manufactures & offers a large variety of diamond laps & polishing discs. Below you will find information, specifications & prices on all laps & polishing discs we offer for this application. Contact us for volume pricing. We can also produce any custom diamond wheel per your specification. Contact us Today for Free Quote!
Recently Viewed Products
ARE YOU USING RIGHT TOOLS
FOR YOUR APPLICATION?
LET US
HELP YOU
HAVING ISSUES WITH
YOUR CURRENT TOOLS?
Knowledge Center
02
Jun
How to properly use Diamond Tools
UKAM Industrial Superhard Tools manufactures precision diamond tools for a large variety of applications, materials, and industries.
Share this Article with Friend or Colleague
Metal Bonded Diamond Tools are “impregnated” with diamonds. This means that selected...
02
Jun
Why use diamond
Diamond is the hardest material known to man kind. When used on diamond/tools, diamond grinds away material on micro (nano) level. Due to its hardness Diamond will work all types of materials from...
02
Jun
Diamond vs CBN (cubic boron nitride) Tools
Cubic Boron Nitride (CBN) is a synthetic material that is renowned for its exceptional hardness and high thermal stability. It is composed of boron and nitrogen atoms arranged in a crystal lattice structure, similar to...
02
Jun
What is Diamond Mesh Size and how to select best one for your application
Diamond grit size can be defined as the size of the diamond particles used in the bond matrix. The larger the diamond particles (grit size) the faster the tool will cut.
Share this Article with Friend or...
02
Jun
What is Diamond Concentration and which to use for your application
Diamond concentration is measured based on the volume of diamond within a section of the tool. It is typically defined as Concentration 100, which equates to 4.4 carats per cubic centimeter of the diamond layer...
02
Jun
Diamond Tool Coolants Why, How, When & Where to Use
Coolant is one of the most overlooked variables in the overall diamond or cbn tool machining process. Effective and proper use of coolant and recalculating coolant system will pay off in terms of improved surface...
18
Jul
Get to Know the Diamond Tool Bond Types and Which to use for your application
The indication of this premature loss of diamond is deep pocket left behind. The presence of many pockets means the diamond is wasted without being used. Each diamond must protrude high to cut fast with...
17
May
Get to Know the Diamond Tool Bond Types and Which to use for your application
Selecting the appropriate diamond bond type for specific applications is crucial for several reasons. Diamond bond type directly affects the tool's performance, efficiency, and longevity. Different bond types determine how well a tool can withstand...
- Unmatched Selection For Many Applications
- Superior Quality & Consistency
- Immediate Worldwide Delivery
- Technical Support & Expertise
- American Based Manufacturer
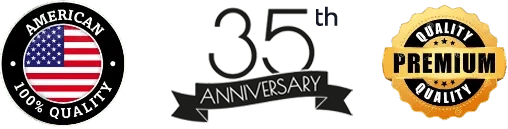

- Different Product
- Different Technology
- Different Company
- Expect MORE from your tools
Let Us HELP You!
Subscribe To Our Newsletter
Signup for email offers, updates, and more
Contact Us
- 25205 & 25201 Avenue Tibbits Valencia CA 91355 USA
-
Phone : (661) 257-2288
FAX : (661) 257 -3833 - lel@ukam.com
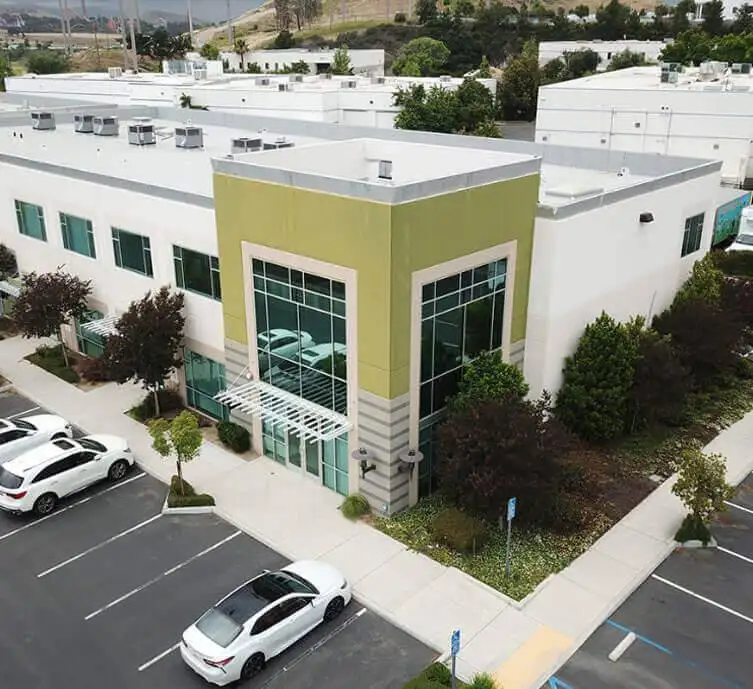
UKAM Industrial Superhard Tools is a U.S. High Technology, Specialty Diamond Tool & Equipment manufacturer. We specialize in producing ultra thin, high precision cutting blades, precision cutting machines diamond drills, diamond micro tools, standard & custom advanced industrial diamond tools and consumables.
- 25205 & 25201 Avenue Tibbits Valencia CA 91355 USA
-
Phone : (661) 257-2288
FAX : (661) 257 -3833 - lel@ukam.com
- 25205 & 25201 Avenue Tibbits Valencia CA 91355 USA
-
Phone : (661) 257-2288
FAX : (661) 257 -3833 - lel@ukam.com
DIAMOND TOOLS BY BOND
EQUIPMENT
KNOWLEDGE CENTER
OUR PRODUCTS
COMPANY
CUSTOMER SERVICE
Shipping Methods


Safe & Secure Payments

© Copyright 1990-2025. UKAM Industrial Superhard Tools – Terms of Use