-
0 items in quote
No products in the Quote Basket.
Dressing Sticks For Precision Diamond & CBN Tools
Diamond Tools must be used with diamonds exposed properly through frequent dressing. Otherwise, the diamond tool will glaze over. They will begin to tear rather than grind which is very destructive. Tearing caused from unexposed diamonds creates friction. This causes uneven wear and heat cracks in the diamond tool as well as material being machined. Resulting in premature diamond tool wear, blade tensioning problems, and will eventually destroy the diamond tool. The more a diamond tool is dress the cooler it will drill or cut. Everything you wanted to know about dressing Diamond & CBN Tools
SMART CUT® Dressing Sticks are expertly designed to help you clean, sharpen, and condition your diamond blades, grinding wheels, and other diamond tooling, ensuring optimal performance and extended tool life. Available from stock in many different dimensions, abrasive types, grit size, and bond harnesses to fit most requirements. Manufactured in the USA with premium-grade materials, these dressing sticks are an essential accessory for any industry relying on precise cutting, drilling, grinding, & operations. Custom specifications can be produced upon request with fast lead times & small minimum order quantities.
DESCRIPTION
SPECIFICATIONS
FREQUENTLY ASKED QUESTIONS
INDUSTRIES USED IN
ACCESSORIES
USAGE RECOMMENDATION
DESCRIPTION
Advantage
- Material Quality: Made with high-purity, abrasive materials that provide just the right hardness to effectively dress diamond tools without causing damage.
- Versatility: Suitable for a wide range of diamond and CBN tools. Whether you are dressing a grinding wheel or refreshing the edge of a cutting blade, our sticks are designed to meet your needs.
- Precision Performance: Regular use of our dressing sticks helps to expose fresh diamond particles, maintaining the sharpness and efficiency of your tools.
- Customization: Available in various grit sizes and dimensions to match the specific requirements of your diamond tools and machinery.
- Enhanced Tool Efficiency: Maintains the cutting/grinding efficiency of diamond tools, reducing downtime and increasing productivity.
- Cost-Effective: Extends the life of your diamond tools, thus reducing the need for frequent replacements and lowering operational costs.
- Improved Quality: Ensures consistent quality in precision cutting and grinding tasks, essential for manufacturing and research environments where precision is paramount.
SPECIFICATIONS
Specifications of Dressing Sticks for Diamond and CBN Wheels
Dressing sticks are essential for cleaning, sharpening, and opening up diamond and CBN grinding wheels. Their specifications vary based on grit size, bond type, dimensions, and material composition. Below is a comprehensive breakdown:
- Composition of Dressing Sticks
- Aluminum Oxide (Al₂O₃) – Common for dressing CBN wheels.
- Silicon Carbide (SiC) – Preferred for dressing diamond wheels due to its hardness.
- Boron Carbide (B₄C) – Used for very fine precision dressing applications.
- Grit Size
- Coarse (80 – 120 grit) → Removes large amounts of bond material; for opening up wheels.
- Medium (150 – 240 grit) → Balances material removal and finish.
- Fine (280 – 600 grit) → Used for precise finishing and minimal material loss.
✅ Recommended Grit Based on Wheel Grit Size:
Dressing Stick Grit | Wheel Grit Size |
80 – 120 | 60 – 100 |
150 – 220 | 120 – 200 |
320 – 600 | 220 – 600 |
- Bond Type
- Soft Bond – Breaks down quickly; effective for exposing new diamonds.
- Medium Bond – Balanced wear rate for general applications.
- Hard Bond – Longer-lasting but requires more pressure to dress the wheel.
- Dimensions
Dressing sticks come in various sizes, depending on application and compatibility with the wheel being dressed.
Common Sizes (L x W x H in inches):
- 6″ x 1″ x 1″ (Most common size for precision wheels)
- 8″ x 1″ x 1″ (For larger diameter wheels)
- 4″ x 1/2″ x 1/2″ (Smaller wheels or fine dressing)
- Other custom sizes available
✅ Choosing the Right Size:
- The length should be at least 50% of the wheel’s diameter.
- A wider dressing stick is preferable for larger diameter wheels.
- Applications
- Resin Bond Diamond & CBN Wheels → Use Silicon Carbide or Aluminum Oxide (150 – 320 grit).
- Metal Bond Diamond Wheels → Use Silicon Carbide (120 – 220 grit); harder bonds may require Boron Carbide.
- Vitrified CBN Wheels → Use Aluminum Oxide (220 – 400 grit).
- Electroplated Diamond & CBN Wheels → Typically do not require dressing; but if needed, use fine-grit silicon carbide.
FREQUENTLY ASKED QUESTIONS
Dressing Diamond Tools is crucial to ensure the diamonds are exposed properly. Without frequent dressing, the tool will glaze over, leading to tearing instead of grinding. This tearing is not only destructive to the material being machined but also wears down the tool rapidly and causes heat cracks in the diamond tool. Poorly dressed Diamond Tools tend to push the material rather than cut it. This results in high loads, increased cutting temperatures, and reduced cut quality. It can also lead to tool breakage. Signs that indicate your Diamond Tool needs dressing include: Yes, the more frequently a Diamond Tool is dressed, the cooler it will drill or cut. This can lead to prolonged tool life, as it minimizes uneven wear and the risk of heat cracks. There is no one-size-fits-all answer to this. The frequency of dressing depends on various factors like the bond type, tool type, bond hardness, diamond grit size, tool concentration, and application factors such as material hardness, density, porosity, cut depth, equipment used, coolant used, and RPMs. When diamonds aren’t properly exposed, the tool tends to tear rather than grind. This tearing action, combined with friction, can generate sparks in the cutting zone. Yes, Diamond Tools that are not dressed correctly experience increased cutting temperatures and high loads, leading to poor cut quality. This strain can cause the tool to break. While there are no specific universal guidelines, the best approach depends on various factors related to the tool and its application. It’s essential to consider the unique requirements of each situation and adjust dressing practices accordingly. Properly dressed Diamond Tools can penetrate materials more easily, ensuring cleaner cuts. Conversely, poorly dressed tools tend to push materials, reducing cut quality. Not necessarily. The technique may vary based on the bond type, tool type, and other variables. It’s essential to understand the specifics of your Diamond Tool and its application to dress it correctly. When a Diamond Tool is not dressed correctly, the unexposed diamonds cause the tool to tear rather than grind the material. This tearing action creates friction which, in turn, generates excessive heat. This heat can cause the material to burn, especially if there’s inadequate cooling or lubrication. Coolant aids in reducing the cutting temperature and heat generated during the machining process. It helps in cooling the tool and the workpiece, preventing burns, and facilitating smoother cuts. Additionally, it assists in removing the material swarf or debris away from the cutting zone. Harder materials tend to wear down the Diamond Tool faster, which may necessitate more frequent dressing to keep the diamonds properly exposed. Conversely, softer materials might not demand dressing as often. Yes, materials with complex shapes or geometries may cause uneven wear on the Diamond Tool, which might require more frequent dressing to ensure consistent performance across the entire tool surface. Operating Diamond Tools at higher RPMs can lead to increased wear and heat generation. This could mean that tools running at higher speeds might need more frequent dressing compared to those operating at lower RPMs. There isn’t a single universally recommended tool for dressing Diamond Tools, as it often depends on the specific Diamond Tool in use and its application. However, diamond dressing sticks, rotary dressers, and stationary dressing tools are some commonly used options. A tool with a higher diamond concentration might be more resistant to wear, possibly reducing the frequency of dressing. However, it’s still crucial to monitor performance and dress as necessary. Yes, if a Diamond Tool has been poorly dressed, it can often be redressed to expose the diamonds properly, provided there’s enough of the diamond layer left on the tool. A harder bond might hold the diamonds more securely, leading to less frequent dressing needs, while a softer bond might release diamonds more readily. Similarly, a finer diamond grit size might wear out faster than a coarser one, affecting dressing frequency. There’s no strict maximum limit. However, as the tool gets dressed repeatedly, the depth of the diamond layer reduces. Once the diamonds are nearly worn out, the tool will need replacement. Sparks often indicate excessive friction and heat generation during the cutting process, which might be due to insufficiently exposed diamonds. It suggests the tool is tearing rather than grinding, leading to metal-to-metal contact or extreme friction between the tool and material. Yes, a well-dressed Diamond Tool ensures consistent and smooth cuts, leading to better surface finishes on the material. A poorly dressed tool can cause tearing, resulting in a rougher finish. Definitely. The right coolant aids in heat dissipation and prevents material from adhering to the tool. Using an unsuitable coolant may not offer the desired cooling effects, leading to faster tool wear and the need for more frequent dressing. If diamonds are being released from the tool too quickly (leading to fast tool wear), the bond might be too soft. Conversely, if the diamonds are hardly getting exposed, resulting in the tool glazing over, the bond might be too hard. A deeper cut exerts more force on the Diamond Tool, potentially causing faster wear. As such, tools used for deeper cuts might require more frequent dressing than those used for shallow cuts. Yes, visual signs can include a shiny or glazed-over surface, uneven wear patterns, or visible loss of diamond particles on the tool’s surface. Using an undressed Diamond Tool can lead to various issues, including poor material finishes, increased chances of material breakage, tool overheating, and reduced tool lifespan. Yes, synthetic diamonds typically have consistent properties and might wear uniformly. Natural diamonds, with their inherent variability, might have uneven wear patterns, possibly affecting dressing frequency. It’s essential to monitor each tool’s performance and dress accordingly. Dressing can be both manual and automated, depending on the equipment and setup. Some advanced machining centers have automated dressing cycles to maintain tool performance consistently. Using excessive force can lead to premature wear of the dressing tool and might also damage the Diamond Tool by dislodging diamonds or causing microfractures in the bond. Yes, over-dressing refers to the removal of too much of the bond material, which may lead to premature diamond particle exposure and subsequent loss. Over-dressing can lead to a shorter tool lifespan and reduced cutting efficiency. Absolutely. Harder and more abrasive materials can cause faster wear on the Diamond Tool, necessitating more frequent dressing. Conversely, softer materials might not require dressing as often. Yes, the type of tool (e.g., grinding wheel, saw blade, drill bit) can influence the dressing technique. It’s crucial to follow manufacturer recommendations or seek expert advice for the specific tool in question. Higher RPMs can lead to increased friction and heat generation. If a Diamond Tool is operated at consistently high speeds without adequate coolant or dressing, it might require dressing more often due to the accelerated wear and heat effects. Not always. The type of dresser suitable for a particular Diamond Tool can vary based on the tool’s bond hardness, diamond grit size, and other factors. It’s essential to use a dresser compatible with your specific Diamond Tool to ensure effective dressing and tool longevity. Potentially. Older tools, especially if stored in adverse conditions or used irregularly, might have altered bond properties or diamond exposure. This can affect their dressing needs. Higher diamond concentration means more diamonds are embedded in the bond. Tools with high diamond concentration might require less frequent dressing as there’s a higher chance of exposed diamonds even as some wear out. However, the bond hardness and other factors also play a role. Signs might include excessive tool wear, difficulty in dressing, poor material finishes, or decreased cutting efficiency. If in doubt, consult with the tool manufacturer or an expert in the field. Yes, correct and timely dressing can extend the tool’s lifespan by ensuring consistent diamond exposure, reducing friction and heat, and preventing excessive tool wear or damage. There isn’t a universal number, as it varies based on the tool’s construction, application, and the dressing process. However, once the diamond particles become sparse or the tool can’t perform efficiently even after dressing, it might be time to consider replacement. Coolants help dissipate heat, reduce friction, and flush away material debris during cutting. The type and concentration of coolant can influence how the tool interacts with the material, potentially affecting wear rates and thus the dressing frequency. Inadequate coolant can increase the need for dressing due to elevated friction and heat. Larger tools, with more surface area, might distribute wear more uniformly, potentially influencing dressing frequency. However, application specifics, like material cut and depth of cut, play a significant role irrespective of tool size. Yes. Poorly dressed tools can increase vibrations, create irregular cutting forces, and produce excessive heat, all of which can be detrimental to your equipment over time. Some mistakes include: Storing tools in damp or corrosive environments can affect the bond and possibly lead to diamond degradation. Proper storage ensures the tool remains in optimal condition and might require less dressing when used next. While many Diamond Tools benefit from dressing, some might not require it based on their specific application or design. However, tools used for grinding or cutting generally need dressing to maintain efficiency. Extremes in temperature and high humidity can affect the bond matrix and the diamonds. Such conditions might either make the bond too soft or too brittle, impacting the wear rate and, by extension, the dressing frequency. Yes, there are automated dressing systems, especially for industrial-scale applications. Automated systems ensure consistent dressing, reduce human error, and might extend tool life. However, they can be more expensive than manual methods and might not be suitable for all tool types. In many cases, yes. If a tool has been inadequately dressed but is not damaged beyond repair, proper re-dressing can revive its performance. However, if the tool has lost a significant amount of diamonds or its structure is compromised, re-dressing might not be feasible. Absolutely. Always wear appropriate personal protective equipment (PPE), like safety glasses and gloves. Ensure the equipment is turned off and unplugged when adjusting or fitting a dresser. Avoid applying excessive force, and always follow manufacturer’s guidelines and best practices. Dressing sticks are tools used to clean, sharpen, and true the surface of grinding wheels. They ensure optimal performance and longevity of abrasive wheels. For dressing diamond wheels, you should typically opt for a softer dressing stick, such as one made from aluminum oxide. Silicon carbide dressing sticks are often recommended for CBN wheels. The coarser the grit of your wheel, the coarser your dressing stick should be, and vice versa. Matching the grit size of the stick to the wheel ensures effective dressing. Yes, for rough grinding, coarser dressing sticks are typically used, whereas precision grinding may require a finer dressing stick. Dressing sticks come in various shapes, including square, rectangle, or round. Custom shapes can also be made for specific applications. Signs include slow cutting, material or tool burning, chipping or cracking of material, and sparks coming from the cutting zone. No. The selection depends on various factors like the wheel’s type, grit size, bond hardness, application, and the desired finish. Manufacturer recommendations are an excellent starting point, but it’s also wise to test different dressing sticks to determine the best fit for your specific application. Yes, some dressing sticks are designed for automated or semi-automated systems, while others are more suitable for manual dressing. As materials and technologies evolve, newer and more efficient dressing sticks may emerge. Stay updated and periodically review your dressing stick choices to ensure optimal performance. Yes, dressing sticks can be reused until they are worn down to a size that’s impractical or unsafe to handle. Ensure the stick is in good condition before each use. The dressing speed is influenced by the wheel size, the type of grinding machine, and the stick material. Typically, dressing at a slower speed can yield better results, but you may need to experiment to determine the best speed for your specific situation. A wheel with a higher concentration of abrasive grains may require more frequent dressing than one with a lower concentration, as a densely packed wheel can glaze over faster. Yes. Truing is the process of making the wheel run true or concentric with the grinding axis. Dressing is the act of removing the top layer of the wheel to expose fresh abrasive grains. Both are essential for the efficient operation of a grinding wheel. While traditional dressing sticks are not particularly harmful, there are emerging eco-friendly options that reduce environmental impact through sustainable sourcing and manufacturing processes. Dressing sticks should be stored in a cool, dry place away from direct sunlight and extreme temperatures. Proper storage extends their shelf life. Yes, many manufacturers offer customization options in terms of size, grit, and material to cater to specific requirements. Always wear protective eyewear, maintain a firm grip, and ensure the machine is turned off when manually dressing a wheel. Avoid applying excessive force, which can lead to breakage. While dressing sticks are versatile, it’s crucial to ensure compatibility with your grinding machine. Check your machine’s manual or consult the manufacturer. If dressing doesn’t improve the wheel’s performance, it might be worn out or damaged. In such cases, it’s best to replace the wheel.
⦁ Slow cutting speed
⦁ The tool doesn’t cut at all
⦁ The material or the tool starts to burn
⦁ Chipping or cracking of the material being cut
⦁ Sparks emerging from the cutting zone
⦁ The tool is not cutting true or straightSigns that indicate your Diamond Tool needs dressing include:
⦁ Slow cutting speed
⦁ The tool doesn’t cut at all
⦁ The material or the tool starts to burn
⦁ Chipping or cracking of the material being cut
⦁ Sparks emerging from the cutting zone
⦁ The tool is not cutting true or straight
We hope this FAQ helps you understand the importance of dressing Diamond Tools and how to identify when your tool needs dressing. Proper maintenance ensures longevity and high performance of your Diamond Tool.
Remember, the key to maximizing the performance and lifespan of your Diamond Tool lies in understanding its specific needs and ensuring proper maintenance. Regular dressing, tailored to the tool’s unique requirements, plays a pivotal role in this process.
It’s essential to maintain a balance between proactive tool care and efficient material processing to ensure optimal performance and longevity of your Diamond Tools. Always monitor tool behavior and adjust your dressing frequency based on observed performance.
Understanding the nuances of Diamond Tool dressing is crucial for optimal tool performance and maximizing return on investment. Always ensure you’re aligned with best practices and regularly monitor tool behavior.
⦁ Not dressing frequently enough, leading to glazing.
⦁ Over-dressing, causing premature diamond loss.
⦁ Using the wrong dresser type for the tool.
⦁ Dressing at incorrect angles or pressures.
Remember, the proper maintenance and dressing of abrasive wheels play a significant role in the quality of the finish and the longevity of both the wheel and the dressing tool. Always choose wisely!
INDUSTRIES USED IN
Tab Content
ACCESSORIES
Tab Content
USAGE RECOMMENDATION
Tab Content
Showing 1 – -1 of 4 results Showing all 4 results Showing the single result No results found
Sort by Price low to high
Filters Sort results
Reset Apply
Image | Name | Description | Price | Quantity | Add to cart |
---|---|---|---|---|---|
1.0" x 1.0" x 6.0" Black Recommended for use in Diamond Tools 150 Grit Size (mesh size) or finer. | $15.39 | Max: Min: 1 Step: 1 | |||
1.0" x 1.0" x 6.0" Black Recommended for coarser grits found in segment wheels, core drills, or Blanchard grinding. Excellent performance on 120 grit tools. | $15.99 | Max: Min: 1 Step: 1 | |||
2.0" x 2.0" x 6.0" Black Recommended for use in Diamond Tools 150 Grit Size (mesh size) or finer. | $39.47 | Max: Min: 1 Step: 1 | |||
2.0" x 2.0" x 6.0" Black Recommended for coarser grits found in segment wheels, core drills, or Blanchard grinding. Excellent performance on 120 grit tools. | $39.47 | Max: Min: 1 Step: 1 |
Showing 1 – -1 of 3 results Showing all 3 results Showing the single result No results found
Sort by
Filters Sort results
Reset Apply
Image | Name | Description | Price | Quantity | Add to cart |
---|---|---|---|---|---|
UKAMDRST10 A-100 Soft | Recommended for coarser grits found in segment wheels, core drills, or Blanchard grinding. Excellent performance on 120 grit tools. | $8.65 | Max: Min: 1 Step: 1 | ||
UKAMDRST11 A-100 Soft | Recommended for coarser grits found in segment wheels, core drills, or Blanchard grinding. Excellent performance on 120 grit tools. | $15.99 | Max: Min: 1 Step: 1 | ||
UKAMDRST13 A-100 Soft | For use on diamond tools 150 to 220 Grit Size. | $8.65 | Max: Min: 1 Step: 1 |
It is important for the diamonds to be well protruded and exposed in order to easily penetrate into the material.
Diamond Tools that are poorly dressed will tend to push the material, creating high loads, high cutting temperature/heat, and poor cut quality. This can also cause tool breakage. There are no specific recommendations or guidelines on when or how often a diamond tool should be dressed. How frequently and when to dress will depend on large variety of variable such as bond type, type of tool, bond hardness, diamond grit size, concentration of the tool. As well as application factors such as material (hardness, density, porosity, material diameter and shape/geometry) cut depth, equipment and coolant used, rpm's.
Sign a Diamond Tools Needs Dressing
-
Slow Cutting
-
Not Cutting
-
Material or Tool starts to Burn
-
Chipping or Cracking of Material
-
Sparks Coming from Cutting Zone
-
Tool not Cutting True
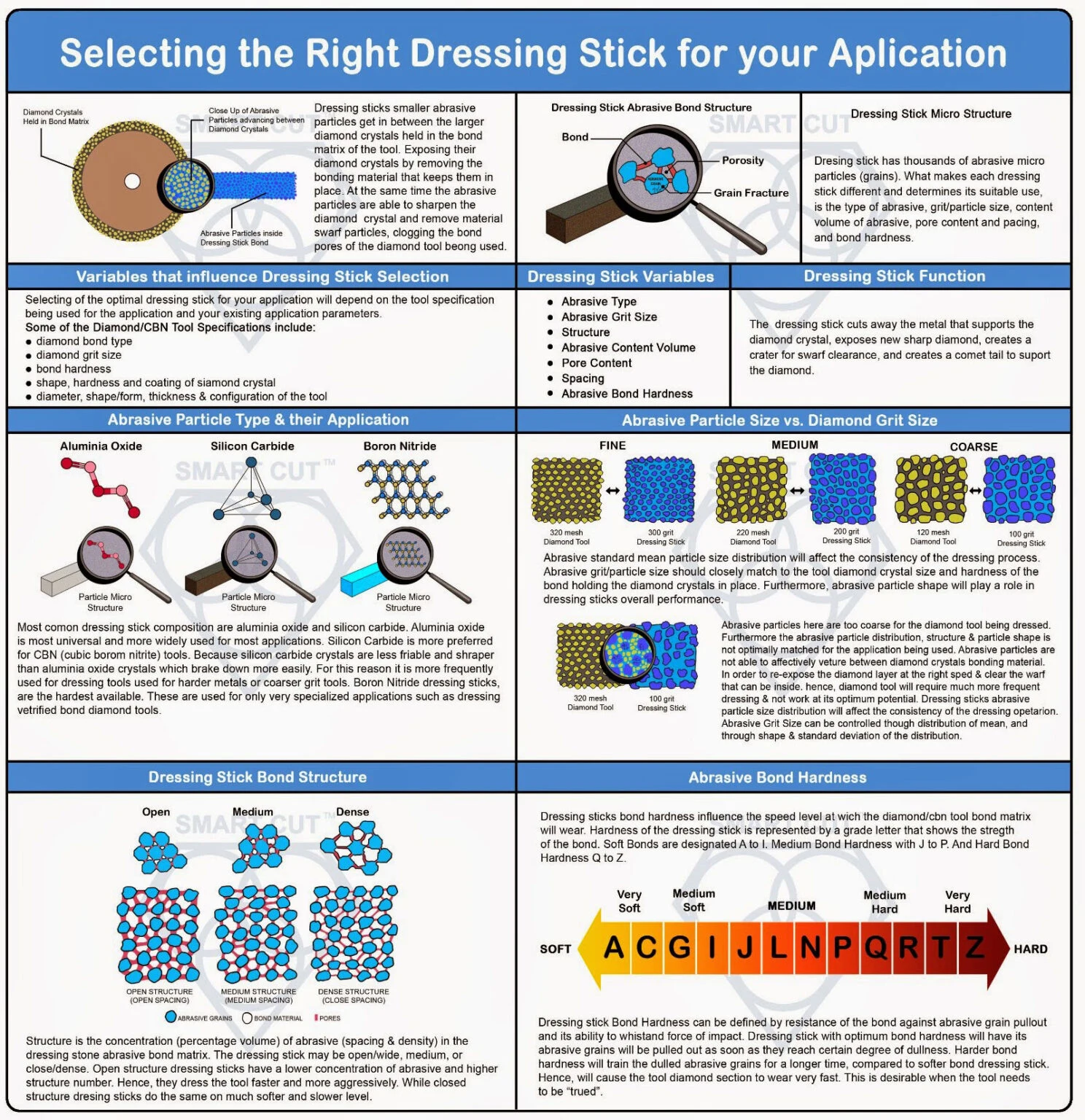
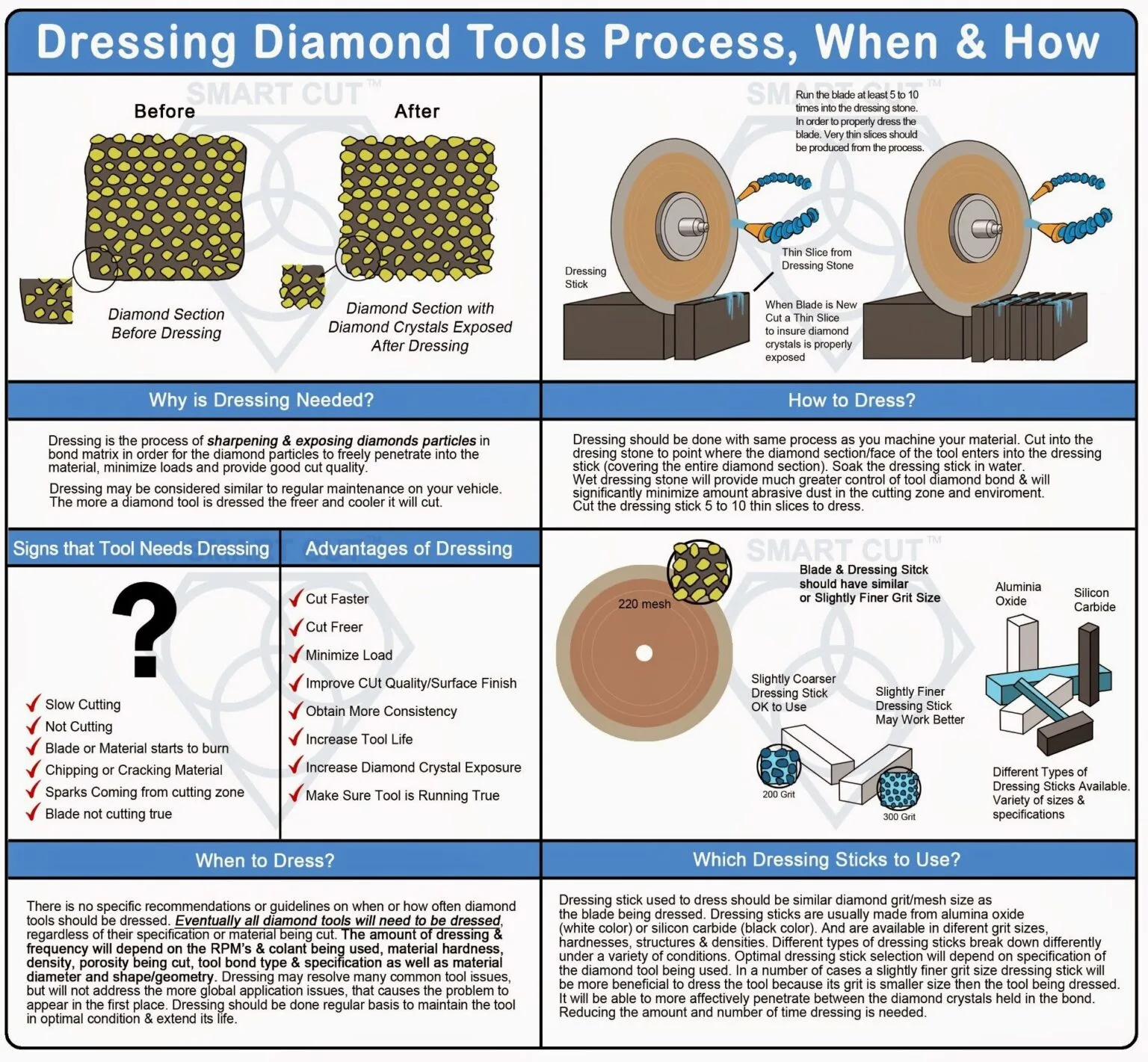
Related Products
SMART CUT® Water Soluble Coolant
(General Materials Formula)
High-Performance Fully Synthetic Coolant & Lubricant for Diamond Slicing, Dicing, Drilling, and Grinding & Machining of Ceramics, Glass, Optics, Quartz, Silicon, and Other Hard & Brittle Materials
SMART CUT® Water Soluble Coolant (General Materials Formula) is a fully synthetic, non-oily, and non-foaming coolant and lubricant engineered to meet the rigorous demands of slicing, dicing, drilling, sectioning, wafering, grinding, and polishing operations involving hard and brittle materials. This advanced formula has been specifically developed for use with ceramics, precision optics, quartz, silicon, sapphire, and other materials commonly found in semiconductor, photonics, and materials research applications.SMART CUT® Mineral Oil
SMART CUT® Mineral Oil is recommended for cutting, drilling, grinding and machining larger variety of materials such as:
- Materials with High Metallic Content
- Advanced Ceramics
- Precious & Semi Precious Stone
- Many Other Ultra Hard Materials
SMART CUT® HD Synthetic Low IFT Coolant/Lubricant For Diamond Wire Sawing Silicon
SMART CUT® is a synthetic coolant specifically designed for the cutting of semiconductor materials, including sapphire, silicon, germanium, single-crystal SiC, and II-VI crystals. This coolant offers excellent cut rates and imparts outstanding surface finishes with reduced warp and total thickness variation (TTV). It is ideal for diamond abrasive cropping, squaring, and wafering of silicon ingots using ID, band, and wire saws. SMART CUT® HD-2B can also be used as a non-re-circulating edge grinding coolant or lubricant for silicon wafers and ingots.
SMART CUT® Water Soluble Dicing Coolant
SMART CUT® XP Water Soluble Dicing Coolant added to deionized (DI) water reduces surface tension flowing from saws injection system and is carried directly of dicing blade.
This reduces material thermal stress, edge damage, and internal cracking, assuring long-term integrity of material being processed. Since SMART CUT® XP Dicing Coolant is a coolant and lubricant, and Surfactant both the dicing blade and substrate / wafer / package benefit.
SMART CUT® XP Dicing Coolant/Lubricant is a specially formulated low-foaming dicing and sawing coolant/lubricant designed for precision applications involving wafers with integrated circuits, MEMS devices, and IC packaging. This aqueous-based synthetic formulation enhances the dicing process by ensuring superior cleanliness of the die or package after dicing while preventing corrosion and oxidation on exposed metals. It eliminates electrostatic discharge, which can be generated during the rotation of the dicing blade, protecting delicate components from damage.
Recently Viewed Products
ARE YOU USING RIGHT TOOLS
FOR YOUR APPLICATION?
LET US
HELP YOU
HAVING ISSUES WITH
YOUR CURRENT TOOLS?
Knowledge Center
02
Jun
How to properly use Diamond Tools
UKAM Industrial Superhard Tools manufactures precision diamond tools for a large variety of applications, materials, and industries.
Share this Article with Friend or Colleague
Metal Bonded Diamond Tools are “impregnated” with diamonds. This means that selected...
02
Jun
Why use diamond
Diamond is the hardest material known to man kind. When used on diamond/tools, diamond grinds away material on micro (nano) level. Due to its hardness Diamond will work all types of materials from...
02
Jun
Diamond vs CBN (cubic boron nitride) Tools
Cubic Boron Nitride (CBN) is a synthetic material that is renowned for its exceptional hardness and high thermal stability. It is composed of boron and nitrogen atoms arranged in a crystal lattice structure, similar to...
02
Jun
What is Diamond Mesh Size and how to select best one for your application
Diamond grit size can be defined as the size of the diamond particles used in the bond matrix. The larger the diamond particles (grit size) the faster the tool will cut.
Share this Article with Friend or...
02
Jun
What is Diamond Concentration and which to use for your application
Diamond concentration is measured based on the volume of diamond within a section of the tool. It is typically defined as Concentration 100, which equates to 4.4 carats per cubic centimeter of the diamond layer...
02
Jun
Diamond Tool Coolants Why, How, When & Where to Use
Coolant is one of the most overlooked variables in the overall diamond or cbn tool machining process. Effective and proper use of coolant and recalculating coolant system will pay off in terms of improved surface...
18
Jul
Get to Know the Diamond Tool Bond Types and Which to use for your application
The indication of this premature loss of diamond is deep pocket left behind. The presence of many pockets means the diamond is wasted without being used. Each diamond must protrude high to cut fast with...
17
May
Get to Know the Diamond Tool Bond Types and Which to use for your application
Selecting the appropriate diamond bond type for specific applications is crucial for several reasons. Diamond bond type directly affects the tool's performance, efficiency, and longevity. Different bond types determine how well a tool can withstand...
- Unmatched Selection For Many Applications
- Superior Quality & Consistency
- Immediate Worldwide Delivery
- Technical Support & Expertise
- American Based Manufacturer
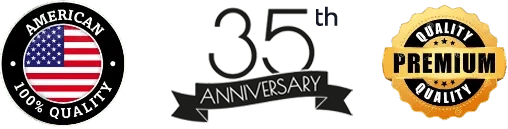

- Different Product
- Different Technology
- Different Company
- Expect MORE from your tools
Let Us HELP You!
Subscribe To Our Newsletter
Signup for email offers, updates, and more
Contact Us
- 25205 & 25201 Avenue Tibbits Valencia CA 91355 USA
-
Phone : (661) 257-2288
FAX : (661) 257 -3833 - lel@ukam.com
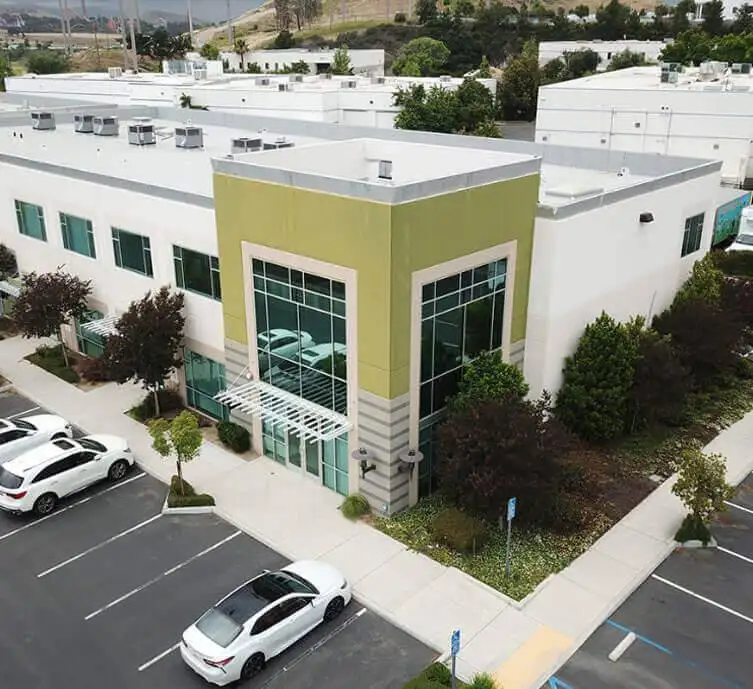
UKAM Industrial Superhard Tools is a U.S. High Technology, Specialty Diamond Tool & Equipment manufacturer. We specialize in producing ultra thin, high precision cutting blades, precision cutting machines diamond drills, diamond micro tools, standard & custom advanced industrial diamond tools and consumables.
- 25205 & 25201 Avenue Tibbits Valencia CA 91355 USA
-
Phone : (661) 257-2288
FAX : (661) 257 -3833 - lel@ukam.com
- 25205 & 25201 Avenue Tibbits Valencia CA 91355 USA
-
Phone : (661) 257-2288
FAX : (661) 257 -3833 - lel@ukam.com
DIAMOND TOOLS BY BOND
EQUIPMENT
KNOWLEDGE CENTER
OUR PRODUCTS
COMPANY
CUSTOMER SERVICE
Shipping Methods


Safe & Secure Payments

© Copyright 1990-2025. UKAM Industrial Superhard Tools – Terms of Use