Table of Contents
ToggleProper testing procedures and methodologies must be set up and used to obtain accurate as well as repeatable testing results. This article will discuss several simple procedures which have been used under actual field conditions, verifying their feasibility for testing diamond cut off wheels.
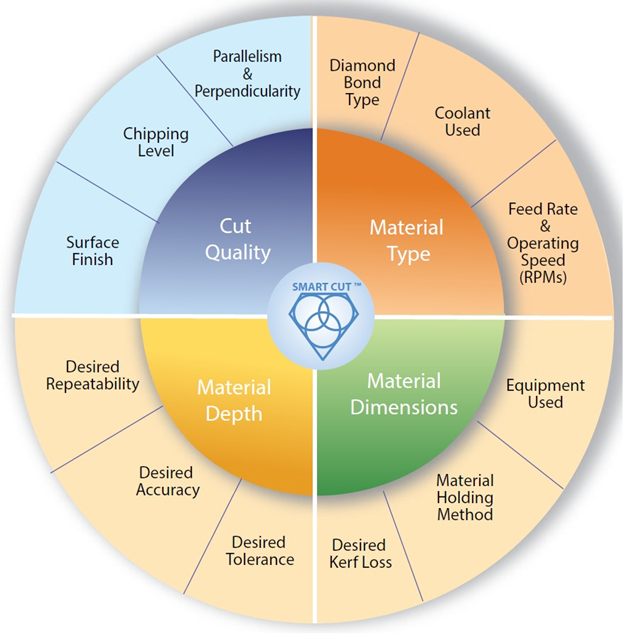
There are many variables that affect diamond blade performance and cost. It’s in the end users best interest to understand these variables and setup some standard for their diamond blade cutting operation and test evaluations. Following proper diamond blade testing procedures and testing methodology will help end user answer numerous questions concerning diamond blade life, rate of cut, straightness of cut, and quality of surface finish related to material being cut. Allowing the end user to understand, evaluate and compare cutting costs. As well as evaluate performance of diamond blade with a different specification being used and compare against a diamond blade supplied by a different manufacturer.
Proper testing procedures and methodologies must be set up and used to obtain accurate as well as repeatable testing results. This article will discuss several simple procedures which have been used under actual field conditions, verifying their feasibility for testing diamond cut off wheels.
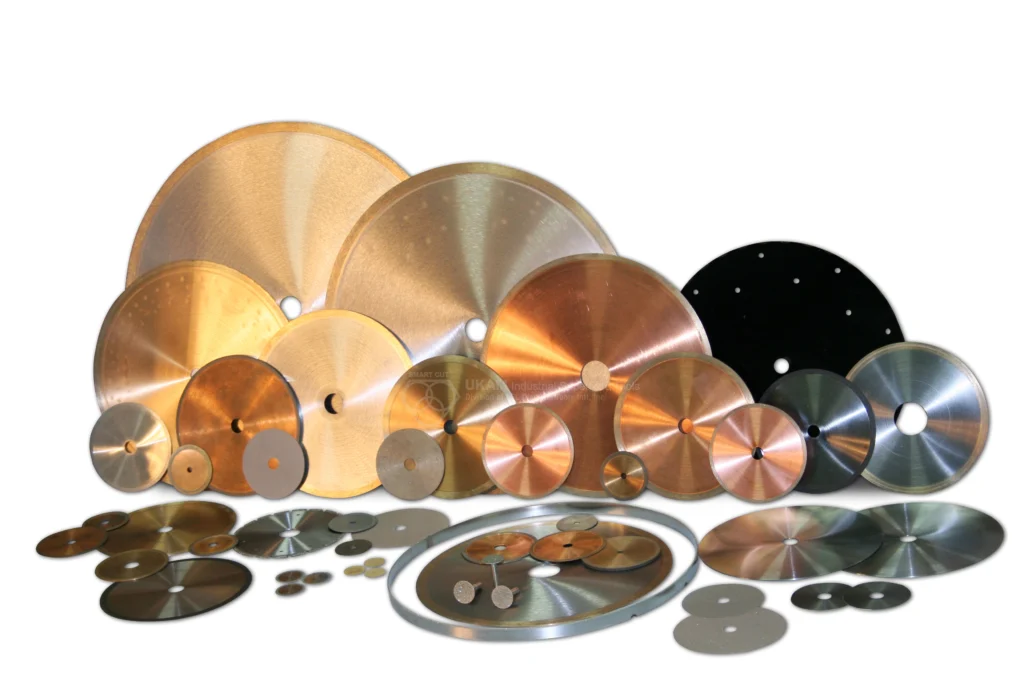
Here are some of the most important variable factors that affect diamond blade performance and which should be considered in any test evaluation.
- Material being cut
- Cutting machine used
- Peripheral speed (SFPM) of the blade
- Operator and their experience
- Feed rate
- Depth of Cut
- Coolant used and its application
All diamond blade manufacturers do a certain amount of testing of their own products. In order to improve existing products, develop new products, compare against competition and etc. Each blade manufacturer typically uses their own methodology and hence different manufacturers may produce various results.
In this article we will attempt to provide some standardization in constructing testing procedures. In general, the procedures set up and results obtained within the manufacturers facilities will tend toward ideal conditions and results. These results cannot necessarily be duplicated in the customers facility. Their operating conditions undoubtedly will vary considerably from those within the manufacturers plant. However, it must be realized that the final test of a product is under the customers conditions and within their facilities. This is known as “field performance”.
Generally most diamond blade manufacturers are in best position to engineer diamond blade tests. Equipped with proper equipment which is in reasonably good condition, operators who are familiar with the correct use of diamond blades, the adequate use and proper application of coolant, controlled speeds and feeds, adequate mounting of material to be cut, as well as other recommended conditions for the use of diamond cut off wheels. Under these controlled conditions the results obtained within the manufacturers facilities naturally tend toward the ideal.
It is the experience of the diamond blade manufacturer that it is practically impossible to obtain two identical cutting wheels no matter how carefully the duplicate is made. Under strictly controlled laboratory test conditions, supposedly identical cutting wheels can give cutting efficiencies which vary by ten percent. Not only between the blades themselves, but between various consecutive tests with the same diamond blade. Nevertheless, controlled test conditions can point out consistent differences in a product and invaluable to both manufacturer and end user. For the user they point up what results in the way of greater production and lower costs he could expect if their operating conditions were improved. For the manufacturer, this presents an opportunity to make new developments to improve their products, to produce a more consistent product and to compare their products with their competition with similar specifications or intended uses.
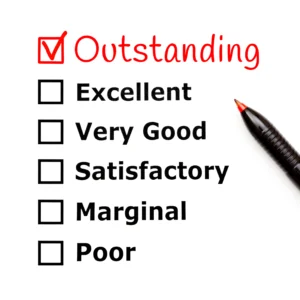
There is no universally perfect test procedures. However, any test procedure must be able to duplicate results and to simulate the field application and to make it possible to correlate these results with what may be expected in actual applications. The testing procedure does not have to be elaborate, but should be capable of providing complete information in order to properly evaluate test results in light of customer requirements.
What is the blade life? the rate of cut? the quality of finish? the types of materials cut. Why did the blade perform as it did? Answers to such questions are needed in order provide a point of departure for any future changes.
A test program must consider the amount of time and money available as well as the exactness of results required to meet customer objectives. Customers requirements must always be kept in mind when conducting tests.
Generalizations and estimates can be made, however the results may not fit the field conditions. One client may wish a fast cutting blade without too much regard to wheel life, surface finish or chipping of material. Another customer may be more interested in slower cutting blade with a longer blade life and fair finish.
In predicting diamond wheel performance it is important to take into account the rate of wear of the diamond blade in relation to amount of material cut, cutting time required and the power consumption. These factors are essential so that all of the cost factors, including not only blade cost, but labor and overhead costs as well, can be compared for different types of diamond cut off wheels.
Some important factors to consider in conducting comparative diamond blade tests
- Material being cut
- Matrix holding the diamond
- Size, type and amount of diamond particles
- Feed rate
- Operator
- Peripheral speed (SFPM) of the blade
- Condition of the machine
- Application of coolant
- Depth of cut
- Driving power
in setting up test process for use “in plant” which can also be used “in field” for the determination of diamond cut wheel wear or wheel life and cutting rate of the listed variables.
Item 2 and 3 will not be considered since, normally this information is known only to the manufacturer. Also, in general since “in field” tests are concerned mainly with testing one blade against another under similar conditions for a specific application, all the variables except 2 and 3 should be analyzed and considered.
MATERIAL BEING CUT
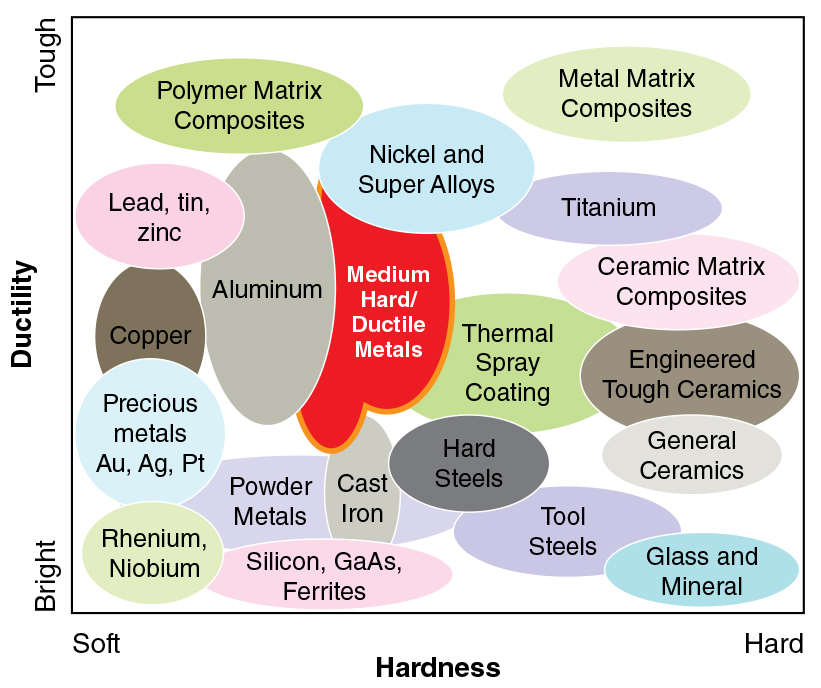
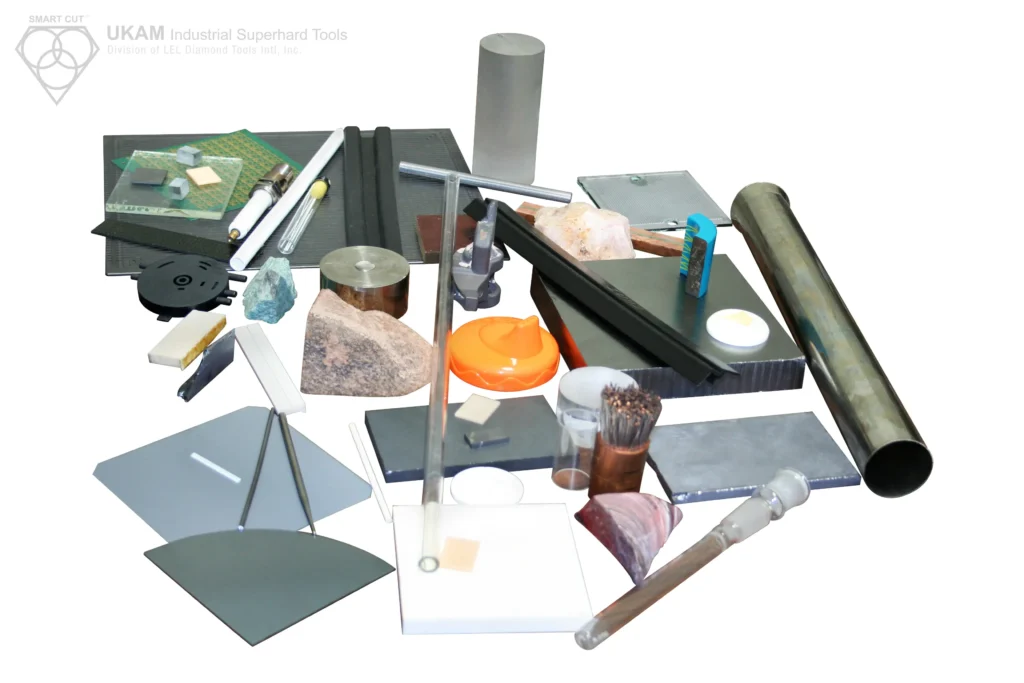
When testing diamond & CBN blades, the hardness and structural characteristics of the materials being used are crucial to evaluating the blade's performance accurately. There is no one-size-fits-all diamond blade that can handle all types of materials, particularly non-metallic, hard, and brittle ones, which necessitates having blades tailored for specific groups or types of materials.
For valid and reliable blade testing, the consistency of the materials used is very important. Utilizing materials that are uniform in terms of structure and hardness ensures that any observed variations in blade performance are due to the blades' capabilities, not inconsistencies in the test materials. Variations in material characteristics such as grain size, density, or hardness can dramatically alter how a blade performs. These factors can change the blade's wear rate, cutting speed, and the quality of the cut, skewing the results and potentially misleading the evaluation of the blade’s effectiveness.
To manage the diversity in materials typically encountered in such tests, developing a logical weighting system is essential. This system assesses the impact of each material's unique properties on the blade's cutting ability. By quantifying these impacts, the evaluation criteria can be adjusted to reflect the true performance of the blades across various materials. This system helps standardize results and ensures a balanced and fair assessment of blade performance, accounting for differences in material hardness and abrasiveness which would otherwise complicate direct comparisons.
In practice, selecting materials for blade testing involves choosing samples that closely resemble the intended real-world applications of the blade while ensuring that these samples do not vary significantly among themselves in terms of key properties. To ensure that the test results are reliable and consistent, the materials used should be as standardized as possible. This means that each test piece should have uniform characteristics within a specific tolerance. Properties like hardness, density, and internal structure must be consistent to avoid introducing variability in the test outcomes. For example, if testing a blade's performance on granite, the granite used should all be of the same type, sourced from the same quarry, or at least have very similar mineral compositions and grain sizes.
Before testing, it’s advantageous to measure and document the physical and mechanical properties of the materials. Techniques such as Mohs hardness testing, density measurements, and even microscopic structural analysis can provide detailed insights into the materials' characteristics. This data can be used to correlate the blade's performance with specific material properties, enhancing the understanding of why certain blades perform better with certain materials.
Maintaining comprehensive records of the materials tested, along with their properties and how different blades performed on them, can be is an excellent approach. These records allows for a systematic review of past tests and can help predict blade performance in future applications. It also serves as a reference that can streamline the material selection process for new blade tests, ensuring consistency and reliability in ongoing research and development efforts.
Conditioning the materials to a standardized state before testing is another critical step. This may involve ensuring that the materials are free from surface impurities, are cut or prepared to uniform dimensions, and are conditioned to a consistent moisture content or temperature. These steps help mitigate external variables that could affect the cutting process.
When multiple materials are tested, grouping them logically according to their properties—like grouping all soft materials together, all abrasive materials together, etc.—can provide clearer insights into blade performance across different categories. Additionally, sequencing the tests from less challenging to more challenging materials can help in assessing the blade's wear and degradation over time.
FEED RATE
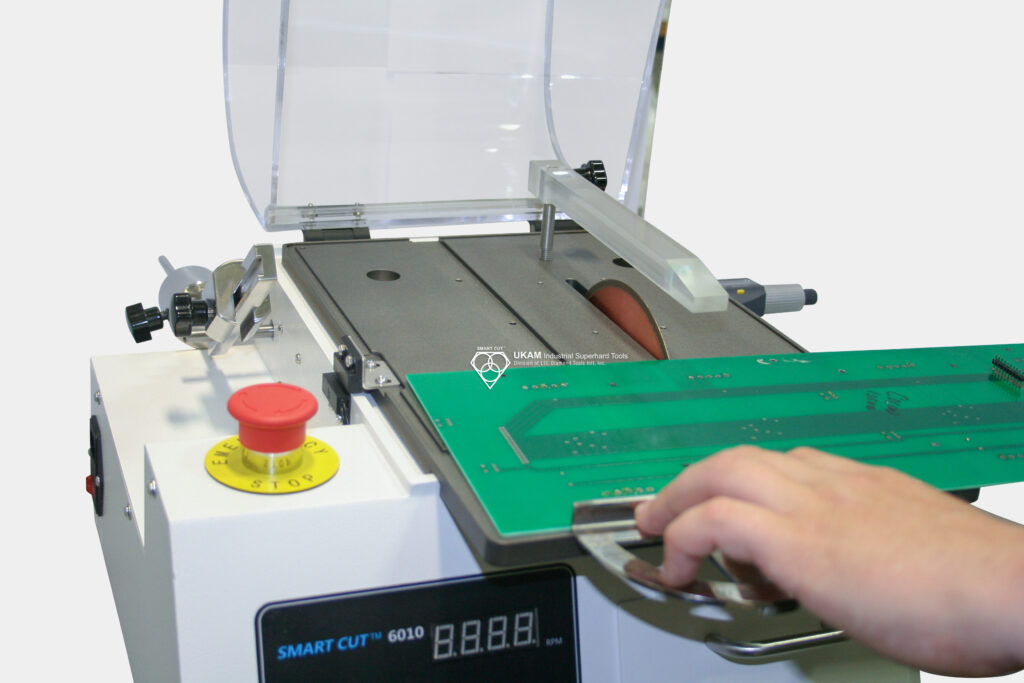

The feed rate or the speed at which the diamond blade moves through the material being cut, has a very pronounced affect on the cutting results. The speed at which the diamond or cbn blade moves through the material, known as the feed rate, is important in determining both the quality and efficiency of the cutting process. It is closely related the depth of cut, the structure and the hardness of the material being cut and the blade specification. Never force the diamond blade beyond its cutting ability. This will only result in a glazed diamond blade, poor cutting and shortened blade life. For any accurate comparison of results, the feed rate must be the same for all tests which are designated for the same purpose.
Achieving an optimal feed rate is key to maximizing cutting performance while avoiding undue stress on the blade. Pushing the blade to cut faster than its design allows can cause several issues, with blade glazing being the most prevalent. This occurs when the diamond edges overheat and become rounded due to inadequate cutting action, reducing the blade's efficiency, diminishing cut quality, and shortening the blade's lifespan.
For precise evaluations, maintaining a uniform feed rate is crucial, particularly in comparative testing. Ensuring consistent feed rates across all tests allows for uniform cutting conditions, facilitating fair comparisons between different blades or materials. Adjusting the feed rate to suit the material being cut can significantly improve the cutting process. Harder materials typically require a slower feed rate to prevent excessive wear or damage, whereas softer materials might handle faster rates, enhancing productivity without sacrificing cut quality.
The specifications of the blade should also guide the setting of the feed rate. Blades designed for specific materials or cut types might need tailored feed rates to optimize their performance. For example, blades with higher diamond concentrations or particular bond hardnesses might perform optimally at different speeds.
Experimentation, guided by manufacturer recommendations, is often the best method to determine the ideal feed rate for a particular application. Starting with a lower feed rate and gradually increasing it while monitoring the blade's performance and wear can pinpoint the most effective rate for each situation. This method ensures efficient operation, prolonging the blade's useful life and yielding high-quality cuts.
Thus, a consistent feed rate is vital for accurately evaluating diamond blades as it directly impacts test reliability and result validity. It influences crucial performance indicators such as cut quality and blade life. Uniform feed rates are essential for methodological consistency, eliminating variables that could distort the data, thus helping to develop solid performance benchmarks and informed usage recommendations.
PERIPHERAL SPEED OF THE BLADE
Peripheral speed, or surface feet per minute (SFPM), is crucial in determining the performance and longevity of diamond and CBN blades. This speed is calculated based on the blade's diameter and the revolutions per minute (RPM) at which it operates. Maintaining consistent peripheral speed is essential during comparative tests to ensure uniform conditions, allowing for accurate comparisons between different blades or materials. Fluctuations in SFPM can lead to inconsistent cutting results, complicating the evaluation of blade performance.
The cutting ability and lifespan of a diamond or CBN blade are closely related to the peripheral speed and the material being cut.
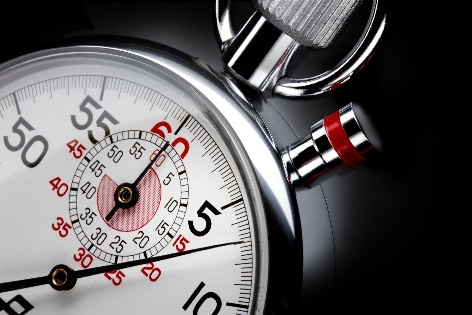
When the speed is too high for certain hard, brittle materials, the blade may become glazed and dull prematurely. This "glazing" effect occurs when the diamond edges round off due to excessive heat and insufficient cutting action, reducing cutting efficiency and shortening blade life.
Identifying the ideal SFPM for a material ensures the blade operates at maximum efficiency, reducing the cost per cut by minimizing wear and enhancing the cutting rate for faster, cleaner cuts. Below are some general SFPM recommendations for various materials:
- Ceramics typically require an SFPM range of 4,500 to 6,000.
- Glass should be cut at an SFPM between 3,500 and 5,000.
- Quartz can be optimally cut at speeds from 4,500 to 6,500 SFPM.
- Silicon Carbide often needs an SFPM between 5,000 and 7,000.
- For composite materials, an SFPM range of 4,000 to 5,500 is suitable.
In practice, the optimal SFPM for specific cutting tasks can vary based on factors like material hardness and abrasiveness, desired cut quality, and the type of blade used. Adjustments might be necessary based on empirical observations and cutting trials to find the most effective speed for each situation.
The following example shows graphically the affect of varying the peripheral speed (SFPM):
Blade diameter – 14” diameter
Cutting fed rate – 6 ft/mn
Dept of cut – ¼”
Type of material cut – hard granite
Peripheral Speed Blade Life
7,000 SFPM 74,320 sq in
11,000 SFPM 53,937 sq in
in this cutting application can be seen the affect of varying the peripheral speed of the diamond blade on cutting efficiency. When the speed was kept within the recommended operation conditions, about 38% greater blade life was obtained. In other words, we have reduced our blade cutting costs about 28%.
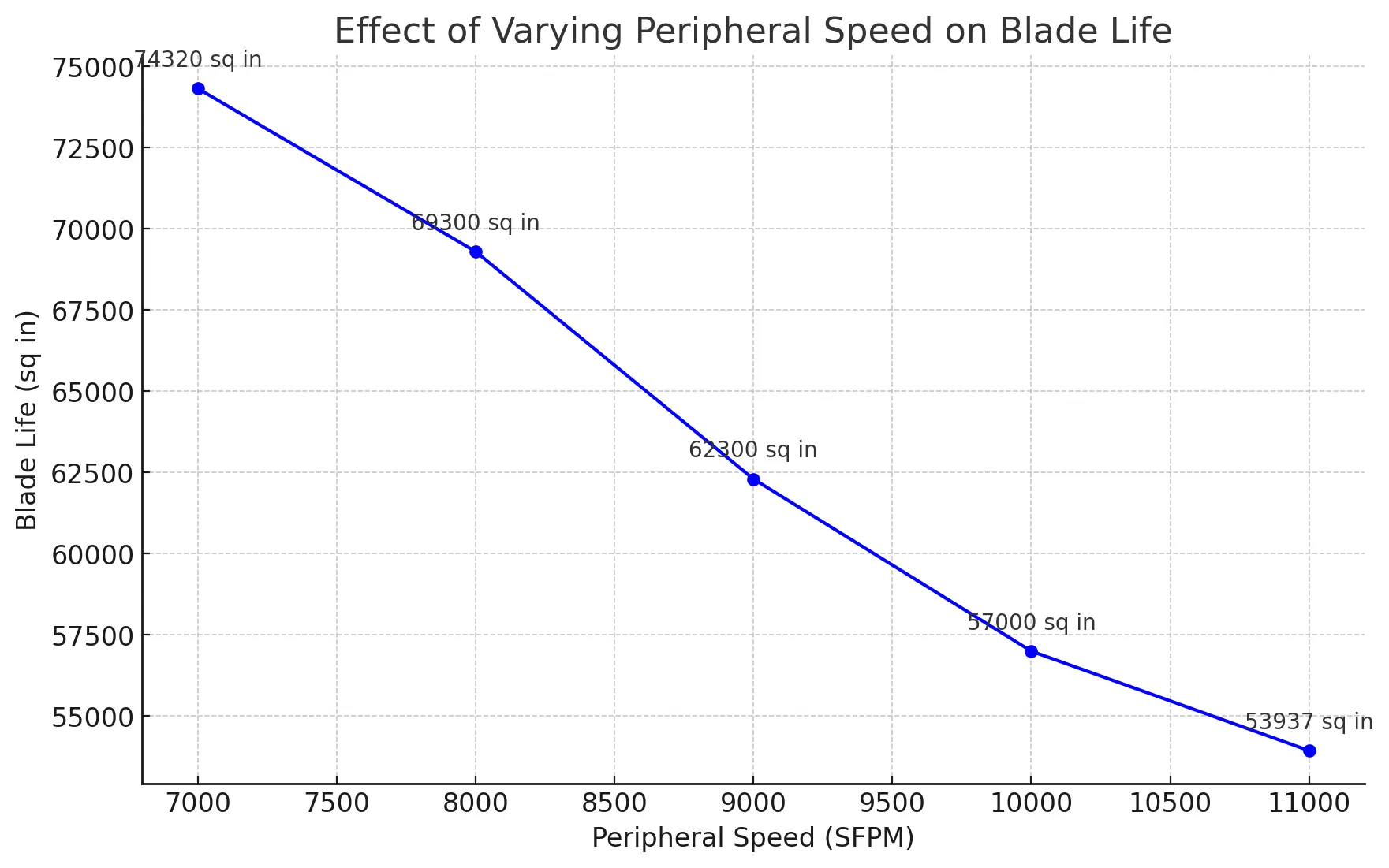
Blade Life vs. Cutting Cost:
This graph illustrates the relationship between blade life and cutting cost. As blade life increases, the cutting cost decreases. The annotations indicate the cost associated with each blade life point.
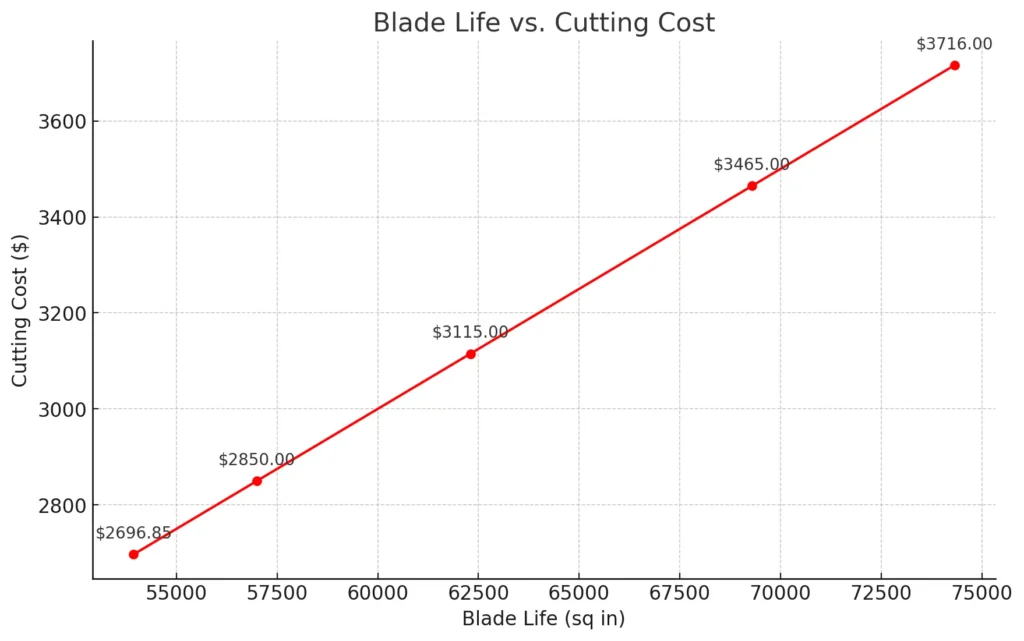
Effect of Varying Peripheral Speed on Blade Life:
This graph shows how blade life (in square inches) decreases as the peripheral speed (in SFPM) increases. Key points are annotated to highlight the specific blade life at given speeds.
Selecting the Right Cutting Equipment / Machine for Testing
Selecting the right cutting equipment for the application is a critical part of the diamond or cbn blade evaluation process. The compatibility of the cutting equipment with the diamond or cbn blade not only affects the efficiency and quality of the cut but also impacts the longevity and performance of the blade. Here’s a detailed look at why choosing the right equipment is essential and how it influences the testing and use of diamond blades.
1. Equipment Compatibility: The cutting equipment must be suitable for the type and size of diamond blade being used. For instance, different blades are designed for varying speeds, materials, and cutting actions. Using a blade on incompatible equipment can lead to inefficient cutting, increased wear on the blade, and potentially hazardous situations.
2. Power and Performance: The power output of the cutting equipment needs to match the requirements of the diamond blade. Insufficient power can cause the blade to operate under suboptimal conditions, which might lead to poor cutting performance and excessive blade wear. Conversely, too much power can lead to overly rapid wear or even damage to the blade and the material being cut.
3. Precision Control: Equipment with advanced control features allows for more precise adjustments in speed, feed rate, and cutting pressure. These controls are crucial for fine-tuning the cutting process to achieve optimal results with different materials, from soft stones to hard metals and ceramics. Precision in controlling these parameters helps in minimizing material waste, achieving cleaner cuts, and extending the blade’s lifespan.
4. Stability and Rigidity: The structural stability of the cutting equipment influences the accuracy of the cut. Equipment that lacks rigidity can vibrate excessively, leading to irregular cuts and uneven wear on the blade. Stable and rigid equipment provides a consistent platform for the blade to perform as expected, ensuring uniform cuts and reducing the risk of blade breakage.
5. Safety Features: Safety is paramount when operating high-speed cutting equipment with diamond blades. The right equipment should include safety features such as blade guards, emergency stops, and other protective mechanisms to safeguard the operator and prevent accidents.
6. Maintenance and Support: Equipment that is easier to maintain and supported by reliable technical service can enhance the overall performance of diamond blades. Regular maintenance ensures that the equipment remains in optimal condition, which is essential for consistent cutting performance. Availability of parts and technical support also plays a role in keeping the equipment running smoothly.
7. Cost-Efficiency: Finally, the cost-effectiveness of the equipment should be considered. Equipment that is energy-efficient, durable, and requires less frequent replacements or repairs can reduce the overall operating costs, making the cutting process more economical in the long run.
Condition of Cutting Machine
Standardized testing equipment is crucial for obtaining accurate and reliable results when evaluating diamond and CBN blades. The success of these tests largely hinges on using equipment that consistently performs well across all testing sessions. Consistency ensures that the machinery operates under the same parameters for each test, confirming that any changes in results are due to the blades themselves, rather than fluctuations in equipment performance.
Regular calibration is vital to maintain this precision. It involves adjusting the equipment to match standard specifications and validating these adjustments against a known reference. This step guarantees that measurements of RPM, feed rates, and other critical metrics are precise, thereby providing dependable data for analysis.
Maintaining the equipment is also essential for reliability. Well-maintained machinery is less prone to mechanical failures that could skew the results. Routine maintenance should include inspecting for wear and tear, replacing any worn-out parts, and ensuring that all components are clean and functional.
When selecting standardized testing equipment, it's important to choose machines capable of meeting the stringent demands of blade testing. This includes equipment with precise control settings for adjusting cutting speeds and feed rates, crucial for replicating exact test conditions consistently, which is key for effective comparative analysis.
Moreover, the machines should be durable enough to endure the stress and strain of repeated cuts, especially when dealing with hard, abrasive materials. Such robustness ensures that the equipment can withstand the rigorous demands of continuous testing without compromising performance or safety.
To further reduce the risk of operator error—a significant factor that could affect test outcomes—machines should have user-friendly interfaces. These interfaces should be intuitive, allowing operators to easily make accurate setups and adjustments. The simpler it is to operate the testing equipment, the more reliable the test results will be, as there is less chance for human error.
Ensuring that the cutting machine is in excellent condition is also important during the testing process. A poorly maintained machine can greatly distort test results. Mechanical issues like worn bearings, a deteriorated shaft, a loose rolling table or blade carriage, slack belts, and dirty flanges and centers can negatively impact the cutting process. These issues may lead to a poor finish on the material being cut, diminished blade life, and other undesirable outcomes.
For example, poor bearings and shaft conditions can cause vibrations and instability during cutting, leading to uneven cuts and increased blade wear. A loose rolling table or blade carriage can result in cuts that stray from the intended path, affecting the precision necessary for effective material sectioning. Loose belts might cause inconsistent blade speeds and torque, impacting the blade’s cutting efficiency and consistency. Similarly, dirty flanges and centers can disrupt the blade's alignment and the even distribution of forces along the blade, further degrading cut quality and blade integrity.
To address these issues, the cutting machine should be inspected and serviced daily, including tightening any loose components, cleaning flanges and centers, and checking for any signs of wear or damage that could affect performance. Depending on how frequently and intensely the machine is used, a complete overhaul every two months, or more often if necessary, is advisable. This overhaul should involve a thorough inspection and replacement of worn parts, recalibration of the machine, and any necessary adjustments to ensure optimal performance.
Adhering to a strict maintenance schedule and keeping the machine in top condition minimizes the impact of machine-related variables on test results. This meticulous approach is essential for conducting fair and accurate evaluations of diamond blades, allowing the data to accurately reflect the blades' performance under optimal conditions. This not only supports the development of reliable cutting solutions but also helps maintain consistent production quality in practical applications.
APPLICATION OF COOLANT
In almost all diamond blade cutting applications some for of coolant must be used. Cases when coolant cannot be used regardless of reason are special and will not be considered in this article. Main purpose of coolant is to keep the diamond blade cool so it will not wrap and cool the localized points of heating resulting from each diamond particle machining or grinding the material being cut. A coolant is also used to clean away the swarf and to lubricant both the diamond particles and material work piece. Improper use or application of coolant will result in greatly shortened blade life, poor cut surfaces and damaged pieces.

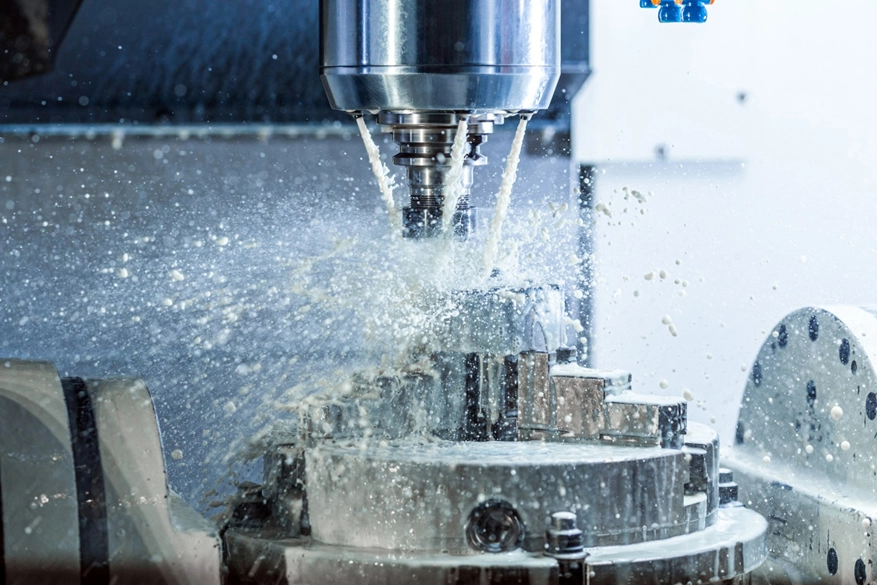
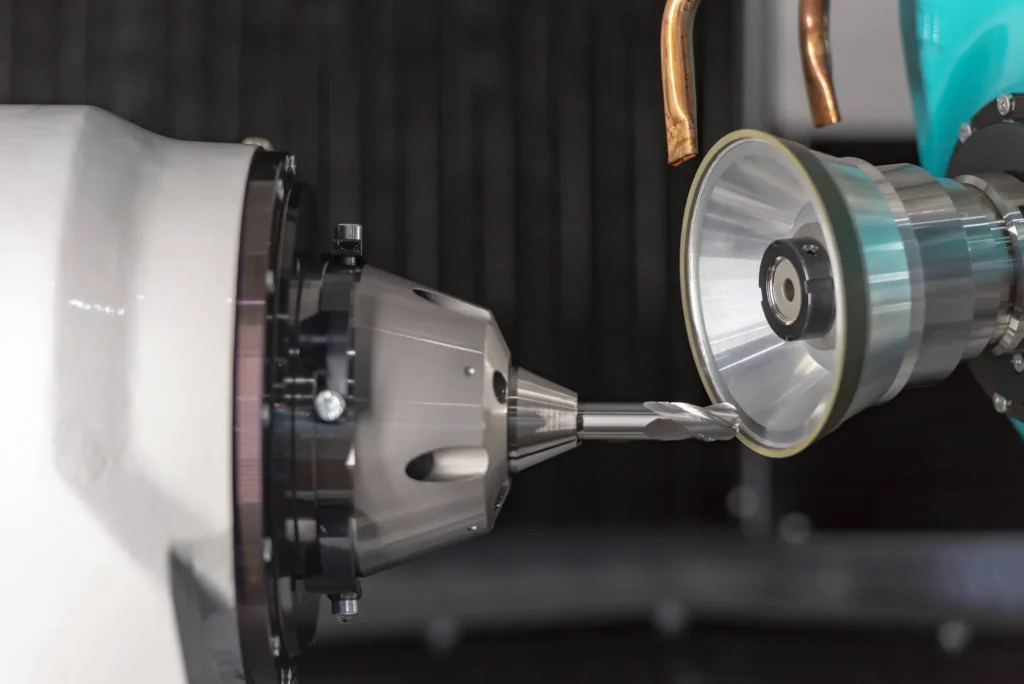

The mere presence of coolant around the blade does not necessarily indicate that the coolant is being properly directed. For these reasons it is most essential to have an adequate supply of coolant under sufficient pressure to overcome any envelope of air surrounding the diamond blade caused by its rotation. Great care must also be taken to put the coolant on the blade and in the kerf in a proper manner so as to assure that the cutting surfaces are kept wet at all times.
There are many types of coolant application systems – some quite elaborate yet ineffective; others highly praised as ideal systems are found to be grossly inadequate under actual cutting conditions. One of the most simple systems the one used in this presentation is one that simulates a turning fork and consists to two perforated pipes extending along the sides of the blade into the center and connected to common pipe at the outer end and fastened to the blade guard. The flow of coolant is directed downward at approximately at 30 degree angle to the rotating blade. With the flow applied in this manner, jets of coolant will penetrate the air envelopes surrounding the rotating blade and cling to the surface of the diamond blade instead of bouncing off.
The coolant will then spiral to the periphery of the blade in a thin wheel, wetting the cutting surface and reaching the bottom of the kerf.

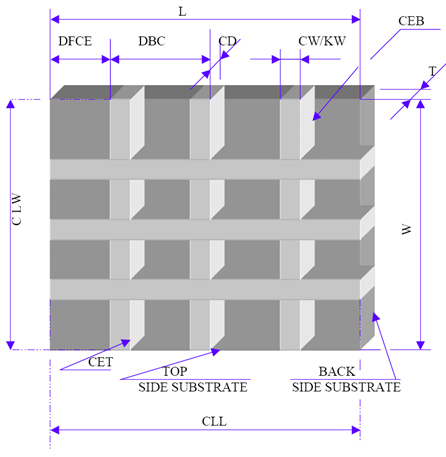
DEPTH OF CUT
The depth of cut significantly affects both the performance and longevity of diamond & cbn blades, similar to the impact of feed rate. It dictates how efficiently and effectively a blade can cut through various materials. For softer materials such as stone or loosely bonded, open-structured materials, it's often possible to make the full depth of cut in one pass. This method allows for quicker cuts without significantly compromising the integrity of the blade or the quality of the cut.
However, harder, denser materials like many types of granite and fine-grained alumina, referred to as alundum, require a more cautious approach known as step cutting. In this method, the total depth is achieved through multiple incremental passes. Cutting too deeply in a single pass can overload the blade, leading to blade glazing where the diamonds on the blade's edge become overheated and rounded off due to excessive friction and insufficient cooling. This results in a loss of cutting ability and poor performance.
To prevent these issues, it's crucial to establish and maintain an appropriate depth of cut tailored to each specific material and application. This optimal depth varies based on the material's hardness and abrasiveness, the type of diamond blade used, and the cutting equipment's capabilities.
For less dense materials, taking full advantage of the blade’s cutting depth capability can maximize efficiency, as long as the blade's specifications and the machine's power can handle such depth without undue wear. On the other hand, for hard materials, a step cutting strategy should be employed to manage stress on the blade and the material effectively. This involves making several passes, each slightly deeper than the last, to reach the desired total depth, thus distributing mechanical stress and heat generation more evenly and preserving the blade’s sharpness and structural integrity.
Regular adjustments to the depth of cut may be necessary based on real-time assessments of blade performance and material response. If signs of blade glazing or performance degradation are observed, reducing the depth of each pass can help mitigate these issues.
OPERATOR
As everyone is aware, the operator of the machinery can either “make” or “break” the performance of any diamond or cbn blade. The skill and experience of the operator play a critical role in maximizing the performance, Whether the machinery is operated manually or automatically, the capability of the operator can significantly influence the results of the cutting process. Some operators have a natural proficiency and experience that allow them to extract maximum efficiency from any diamond and cbn, while others may not achieve such optimal results.

For accurate comparative tests, it is crucial to use the same operator for all evaluations. This ensures consistency and controls the human variable, allowing the focus to remain strictly on the performance of the diamond and CBN blades.
Operators often begin their tasks with diamond and cbn blades without adequate training or with misconceptions that lead to errors during the setup phase, including the omission of critical steps. When problems arise, there is a tendency to hastily address the symptoms without identifying and tackling the underlying causes. This reactive approach can lead to frustration and, unfortunately, operators might unfairly blame the diamond or CBN blades being used. In many cases, what is perceived as a significant issue can often be resolved by simply adhering to fundamental best practices.
Training and operator experience are essential for maximizing the return on investment in diamond and CBN blades. Well-trained operators are less likely to make setup errors or overlook important steps, leading to fewer mistakes and higher efficiency. When issues arise, properly trained operators can identify the root causes rather than just addressing the immediate symptoms. This significantly improves the performance of the diamond & cbn blades and extends their lifespan, improving productivity and reducing waste.
At the same time, a deep understanding of the specific diamond or cbn blade specifications and cutting techniques involved is critical. Operators who are well-informed about the properties of diamond and CBN blades, and how best to utilize them, can optimize cutting processes, further improving efficiency and profitability. Ensuring that operators are comprehensively trained and have a thorough understanding of diamond and cbn variables and their cause and affect factors is an important step towards for achieving optimal performance for just about in any cutting application.
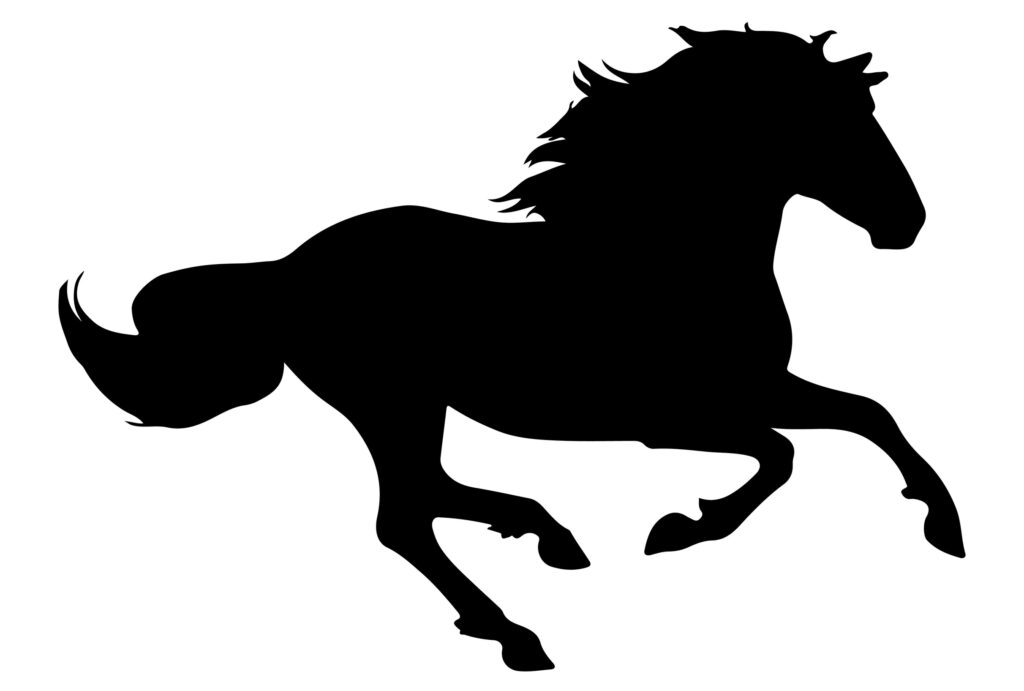
DRIVING POWER
The driving power, often referred to as the horsepower (HP) of the cutting machine, plays a critical role in the performance of diamond & cbn blades. Maintaining a constant peripheral speed throughout the cutting process is crucial for optimal blade performance. This consistency is largely dependent on the machine's ability to sustain a consistent RPM, which in turn is influenced by the horsepower available to drive the shaft.
Fluctuations in machine power during the cutting period can lead to variations in blade / cutting wheel speed, measured in surface feet per minute (SFPM). These fluctuations adversely affect the life and efficiency of the diamond or cbn blade. A drop in RPM due to insufficient driving power can cause the blade to operate at lower speeds than needed, resulting in poor cutting performance and increased wear on the blade.
To ensure a constant RPM, it is essential that the cutting machine is equipped with sufficient horsepower. This requirement is particularly critical when cutting harder or denser materials, which can place additional load on the blade and the machine. Adequate horsepower ensures that the blade can maintain the necessary speed to cut effectively through the material without the risk of the machine bogging down.
In setting up a testing procedure to evaluate the performance of diamond or cn blades / cutting wheels, understanding the relationship between the machine’s horsepower and the blades / wheels operational efficiency is key. A well-designed test should account for the horsepower required to maintain constant SFPM, thereby providing realistic insights into the blades / wheels performance across various conditions.
This test should also help determine the economic aspects of using a particular blade by measuring the blade’s lifespan in relation to its ability to maintain consistent cutting speeds. The data collected can then be used to calculate the cost per cut, taking into account the lifespan of the blade and the operational efficiency provided by the adequate horsepower of the cutting machine.
PROCEDURE FOR TESTING DIAMOND CUT OFF BLADES
Each material / application will require different testing procedures and methodology. Testing conditions, equipment and desired results will vary with each group.
Before we outline the specific testing procedures for each material or application, it is crucial to describe one piece of equipment that is common to all testing setups.
Measuring the wear on the blade is critical to determine its durability and efficiency without pushing it to the point of destruction. In many instances, it is not practical or economical to completely wear out the diamond or cbn blade to gather the necessary data. Therefore, we utilize a method where we measure the wear at specific intervals, recording the difference between the initial diameter of the blade and its diameter after use. These measurements are taken using tools such as vernier calipers or tubular micrometers.
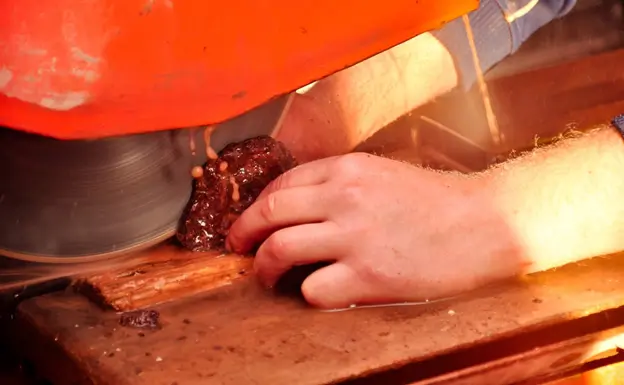
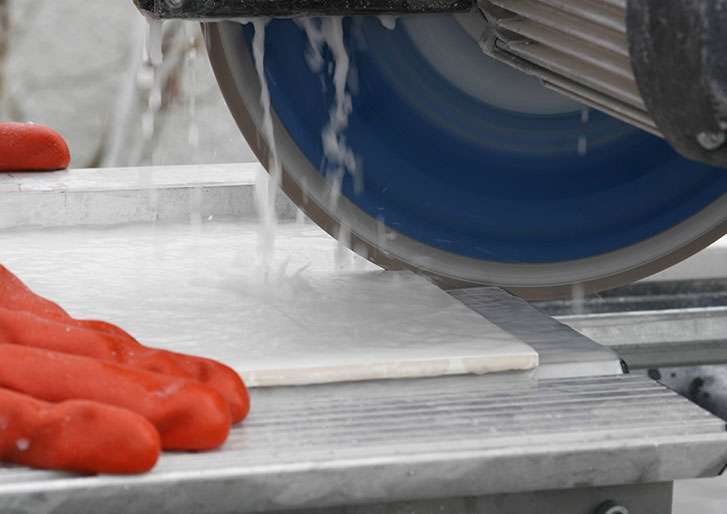
To ensure that the wear rate is reasonably uniform across the diamond blade’s usable life, we extrapolate this data to project the theoretical lifespan of the blade. However, to verify these projections, it is often necessary to conduct full lifespan tests where a blade is used until it is no longer functional.
The testing environment also plays a significant role in accurately determining blade life and performance. For example, maintaining a controlled temperature and humidity in the testing area helps mimic the
conditions under which the blades will be used in real-world applications. This environmental control is essential to ensure that our test results are replicable and relevant to our customers’ needs.
Furthermore, it is important to monitor the speed and feed rates during the tests. These parameters should be adjusted according to the material being cut to simulate actual usage conditions as closely as possible. By varying these rates, we can better understand how the blade performs under different stresses and identify the optimal conditions for each type of material.
During the testing process, we also pay close attention to the quality of the cut. This includes assessing the smoothness of the cut surfaces, the amount of material loss due to the cutting process, and any potential damage to the material. These factors are crucial for understanding the blade’s efficiency and the potential impact on the final product.
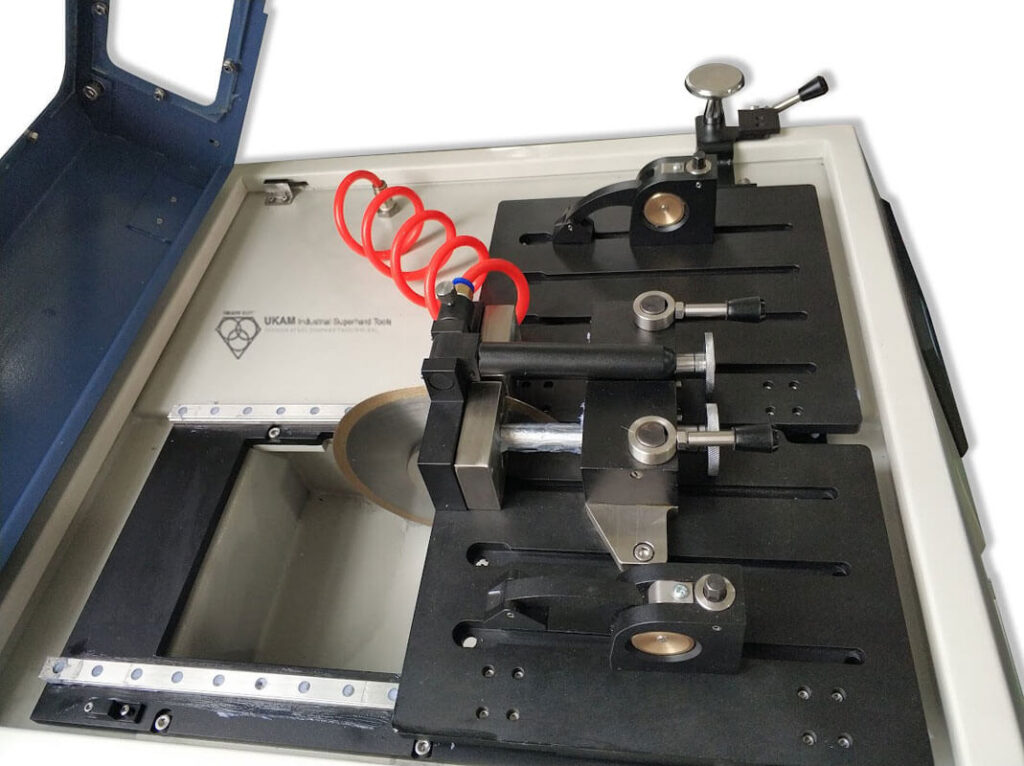
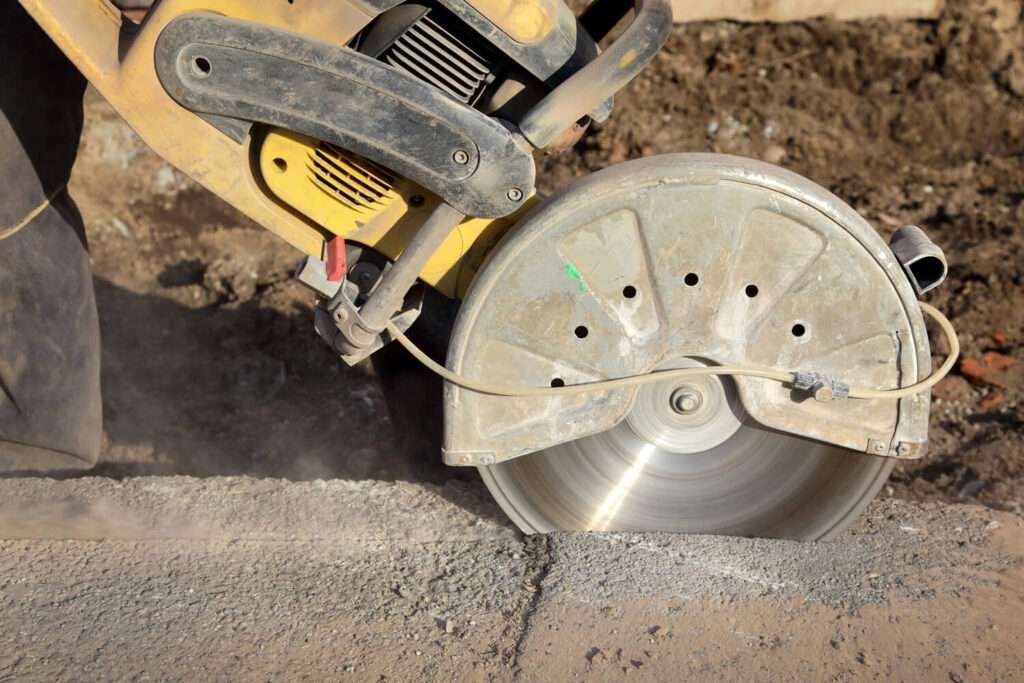
In addition to technical measurements, it is equally important to gather subjective feedback from the operators who perform the tests. Their insights into the blade’s handling, any vibrations felt during cutting, and the ease of operation provide valuable information that complements the quantitative data collected.
By integrating both objective data and subjective feedback, we can provide comprehensive insights into our diamond cut-off blades‘ performance. This thorough testing ensures that we continue to deliver products that meet the high standards of precision and durability required by our clients in various industries.
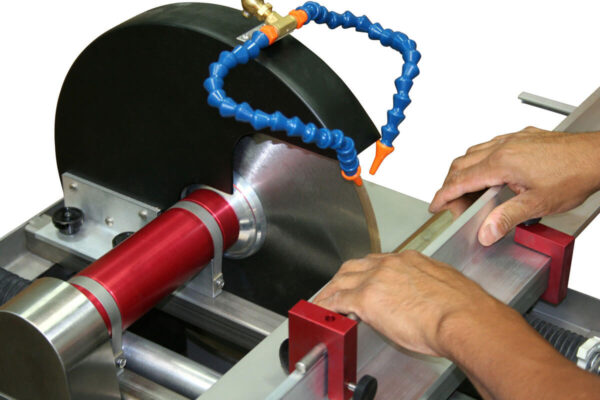
Key Performance Metrics for Diamond & Blades
All diamond and CBN blades can cut materials, but their performance can vary greatly between different blade specifications. Even blades that seem identical might perform differently when sourced from various manufacturers or suppliers, showing significant variations in effectiveness.
These differences make it crucial to understand the specific capabilities and limitations of each blade. Key performance metrics are essential for determining how well a diamond or CBN blade can handle the demands of different materials and applications. These metrics reflect not only the physical and mechanical properties of the blades but also affect their overall productivity and cost-effectiveness. By understanding and optimizing these metrics, you can choose the best blade for your needs, improving your overall return on investment.
Below, we discuss some of the most important metrics to consider when evaluating, comparing, and testing diamond and CBN blades.
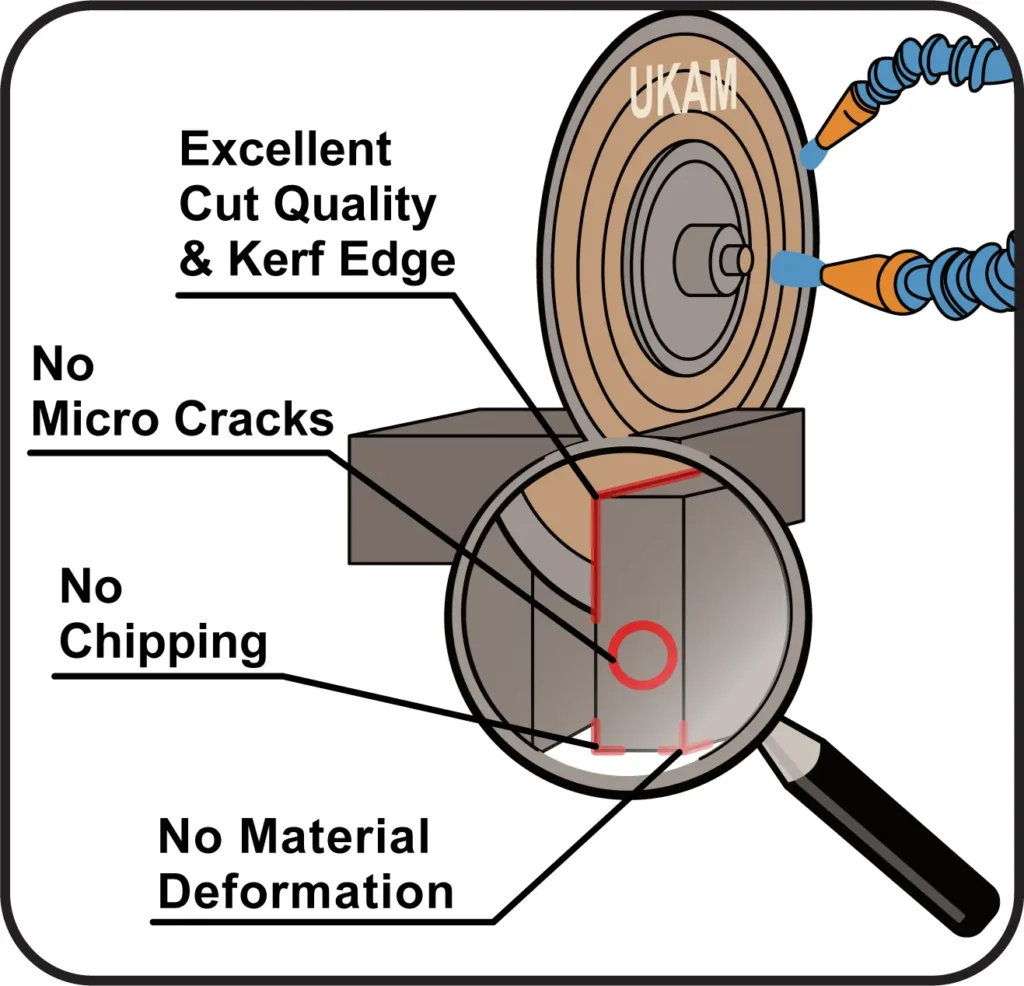
Find Out More >>>
-
Cutting Speed: How quickly a diamond blade can complete a cut without sacrificing quality. Faster speeds can increase throughput but must not compromise the integrity of the sample.
-
Surface Finish: The quality of the surface after cutting is crucial. A finer finish reduces the need for subsequent grinding and polishing, thereby saving time and preserving the material's characteristics. Minimizing chipping and other forms of cut-induced damage is crucial for maintaining the structural integrity of the sample.
-
Blade Life: This refers to how long a blade can maintain its cutting effectiveness before it needs to be replaced. A longer blade life reduces downtime and the cost of consumables.
-
Consistency: The ability of the blade to consistently produce quality cuts throughout its life span. Inconsistency can lead to wasted material and unreliable results.
-
Required Force: A blade that requires less force to cut through materials is preferable as it minimizes potential sample damage and operator fatigue.
-
Required Force: A blade that requires less force to cut through materials is preferable as it minimizes potential sample damage and operator fatigue.
-
Heat Dissipation: Effective heat management prevents sample damage and preserves the blade’s life. Blades that dissipate heat efficiently perform better in demanding conditions.
-
Material Compatibility: A blade's ability to handle different types of materials effectively without degradation is essential, especially when working with a variety of samples.
-
Wear Resistance: Resistance to wear and tear defines how well a blade holds up under regular use, impacting its longevity and reliability.
-
Vibration: Lower vibration levels indicate a more stable cut, enhancing the precision and quality of the sample.
-
Amount of Material Deformation: It’s essential to minimize deformation during cutting to ensure that the true microstructure of the material is preserved for accurate analysis.
-
Secondary Grinding and Polishing Steps Required: Blades that produce cleaner cuts reduce the need for extensive secondary processing, thereby enhancing overall efficiency and sample quality.
-
Thermal Stability: Assesses the blade's ability to maintain its properties and performance at varying temperatures. Blades with high thermal stability perform consistently across a range of operational conditions, which is crucial when working with thermally sensitive materials.
-
Blade Flexibility: Evaluates the blade's ability to flex without breaking, particularly when making intricate cuts or when operating under variable loads. This is important for ensuring the blade's reliability in complex cutting scenarios.
-
Recovery Time: The time it takes for a blade to return to optimal performance after dressing or any form of maintenance. Faster recovery can significantly reduce downtime.
-
Edge Durability: Measures how long the cutting edge remains effective before it dulls. Durable edges reduce the frequency of blade replacements and maintenance.
-
Startup Performance: Assesses how quickly and effectively a blade reaches its optimal cutting performance from startup. This can be crucial in production environments where time and quick setup are valued.
-
Cost per Cut: Considers the total cost of using the blade divided by the number of cuts it can make before it is deemed ineffective. This metric helps in assessing the economic efficiency of the blade over its lifespan.
-
Impact Resistance: Evaluates the blade's ability to withstand sudden stresses or impacts without cracking or chipping. This is particularly relevant for cutting hard, brittle materials.
-
Profile Retention: Measures how well a blade maintains its original profile and cutting characteristics over its lifespan. High profile retention reduces the need for frequent adjustments and recalibrations.
-
Blade Stiffness:, A measurement of the rigidity of the blade. Stiffer blades are less prone to wobbling and can provide more precise cuts, especially important in high-precision applications.
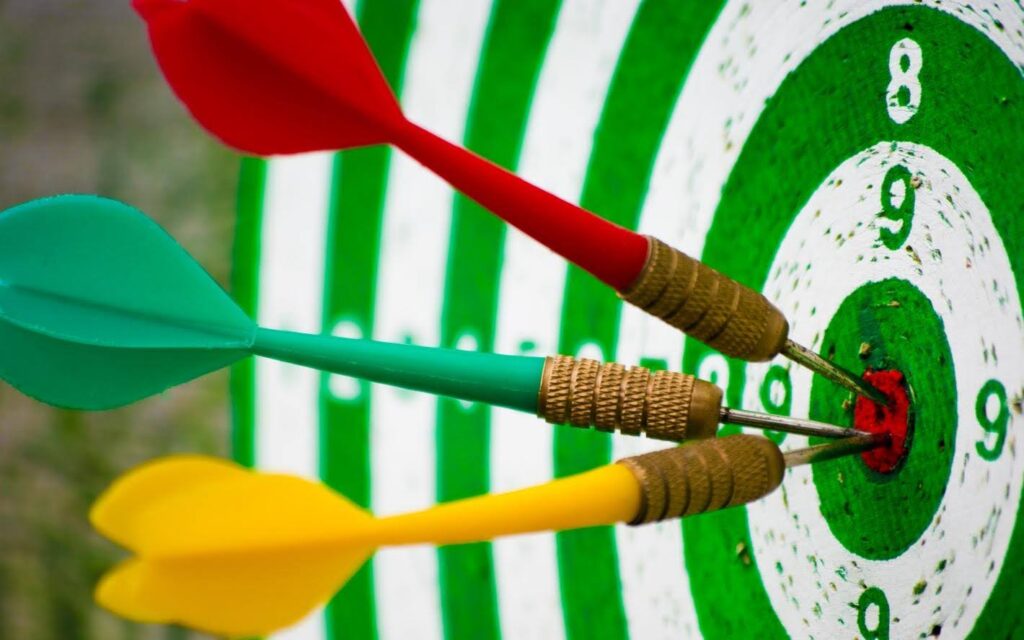
Improving Accuracy of Test Results
Performing multiple tests under the same conditions is crucial when evaluating diamond & cbn blades to ensure the reliability and accuracy of results. Known as repeat testing, this approach significantly enhances the statistical significance of the data by providing a robust set of results from which to draw conclusions.
Repeat testing allows for a more comprehensive analysis of a diamond & cbn blade's performance. By running the same tests multiple times, it's possible to collect enough data to identify patterns and trends that might not be apparent from a single test. This is especially important when the blade’s performance could be influenced by subtle variations in the material composition or slight differences in machine calibration.
Repeat testing allows for a more comprehensive analysis of a diamond & cbn blade's performance. By running the same tests multiple times, it's possible to collect enough data to identify patterns and trends that might not be apparent from a single test. This is especially important when the blade’s performance could be influenced by subtle variations in the material composition or slight differences in machine calibration.
One of the key benefits of repeat testing is its ability to average out anomalies. In any experiment, there can be outliers—data points that significantly deviate from the rest due to random errors or unforeseen factors. Conducting multiple tests reduces the impact of these outliers on the final results, as averaging the outcomes can smooth out these irregularities, providing a more accurate representation of the blade's typical performance.
Outliers can skew results significantly, particularly if the sample size is small. In the context of diamond and cbn blade testing, an outlier might occur due to an atypical piece of material or a temporary lapse in equipment performance. Repeat testing minimizes the undue influence of these outliers by incorporating more data points, ensuring that the final results reflect standard operating conditions rather than exceptional or flawed scenarios.
Additionally, repeat testing is critical for confirming the reproducibility of a blade’s performance. If a blade consistently produces similar results across multiple tests, it demonstrates that the blade's quality and capabilities are reliably reproducible. This consistency is crucial for manufacturers who need to ensure that every blade produced meets quality standards.
Furthermore, repeat testing enhances the predictive accuracy regarding how the blade will perform in real-world conditions. By testing across a range of controlled scenarios that might simulate different operational environments, it helps predict the blade’s durability and efficiency, which are vital for users who rely on these tools for precision and cost-efficiency in their projects.
Example of Improving Accuracy of Test Results:
The following example shows graphically the affect of varying the peripheral speed (SFPM):
Blade diameter – 14” diameter
Cutting fed rate – 6 ft/mn
Depth of cut – ¼”
Type of material cut – hard granite
Peripheral Speed Blade Life
7,000 SFPM 74,320 sq in
11,000 SFPM 53,937 sq in
in this cutting application can be seen the affect of varying the peripheral speed of the diamond blade on cutting efficiency. When the speed was kept within the recommended operation conditions, about 38% greater blade life was obtained. In other words, we have reduced our blade cutting costs about 28%.
Here's the table displaying the test results for blade life at different peripheral speeds across multiple tests:
Test Number |
7,000 SFPM (sq in) |
11,000 SFPM (sq in) |
---|---|---|
Initial |
74,320 |
53,937 |
Repeat 1 |
75,000 |
54,000 |
Repeat 2 |
74,500 |
53,500 |
Repeat 3 |
73,800 |
54,200 |
Repeat 4 |
74,100 |
53,800 |
Repeat 5 |
74,000 |
53,600 |
To provide a comprehensive statistical analysis based on your data for blade life at two different peripheral speeds (7,000 SFPM and 11,000 SFPM), let's break down the calculations into several key statistics and tests:
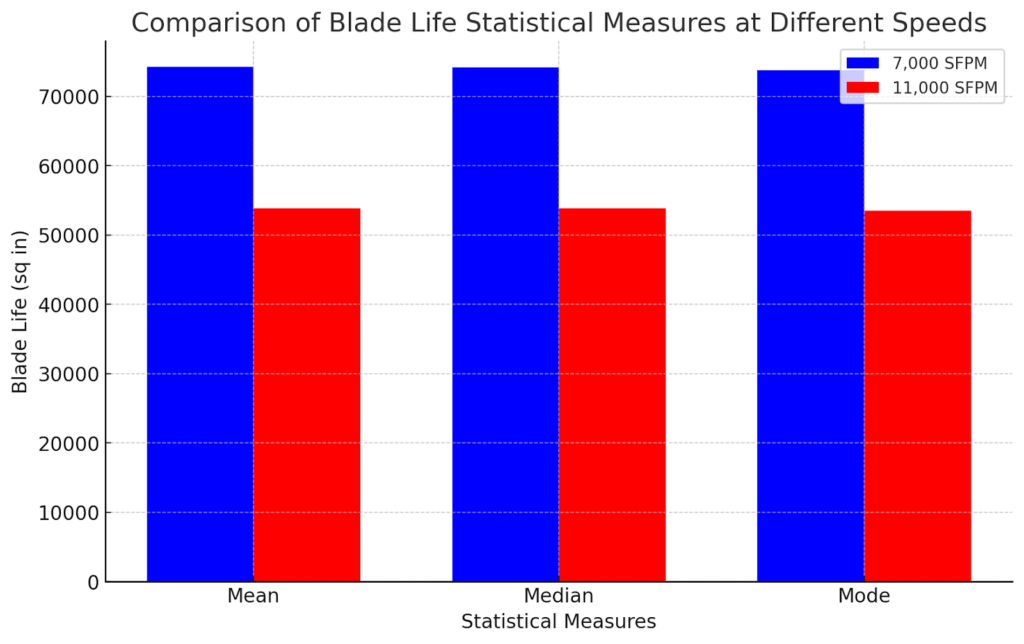
1. Average, Mean, Median, and Mode
These terms (except for the mode) are typically used interchangeably in common usage to describe the central tendency of data. The "average" and "mean" are the same, calculated as the sum of all values divided by the number of values. The "median" is the middle value when the data points are arranged in order. The "mode" is the value that appears most frequently in a data set.
Here are the computed statistical results for the blade life at the two different peripheral speeds:
For 7,000 SFPM:
- Mean (Average) Blade Life: 74,287 sq in
- Median Blade Life: 74,210 sq in
- Mode Blade Life: 73,800 sq in (least value since all others are unique)
For 11,000 SFPM:
- Mean (Average) Blade Life: 53,840 sq in
- Median Blade Life: 53,869 sq in
- Mode Blade Life: 53,500 sq in (least value since all others are unique)
2. T-test
A t-test can be used to compare the means of blade life at the two different speeds to see if there is a statistically significant difference between them. This test assumes that the data for both conditions are normally distributed.
T-test Results:
- T-statistic: 100.22
- P-value: Very close to zero (2.396 x 10^-16)
The t-test results indicate a highly significant difference in blade life between the two speeds, with the p-value being practically zero. This suggests that the difference in blade life at 7,000 SFPM compared to 11,000 SFPM is not due to random chance and is statistically significant.
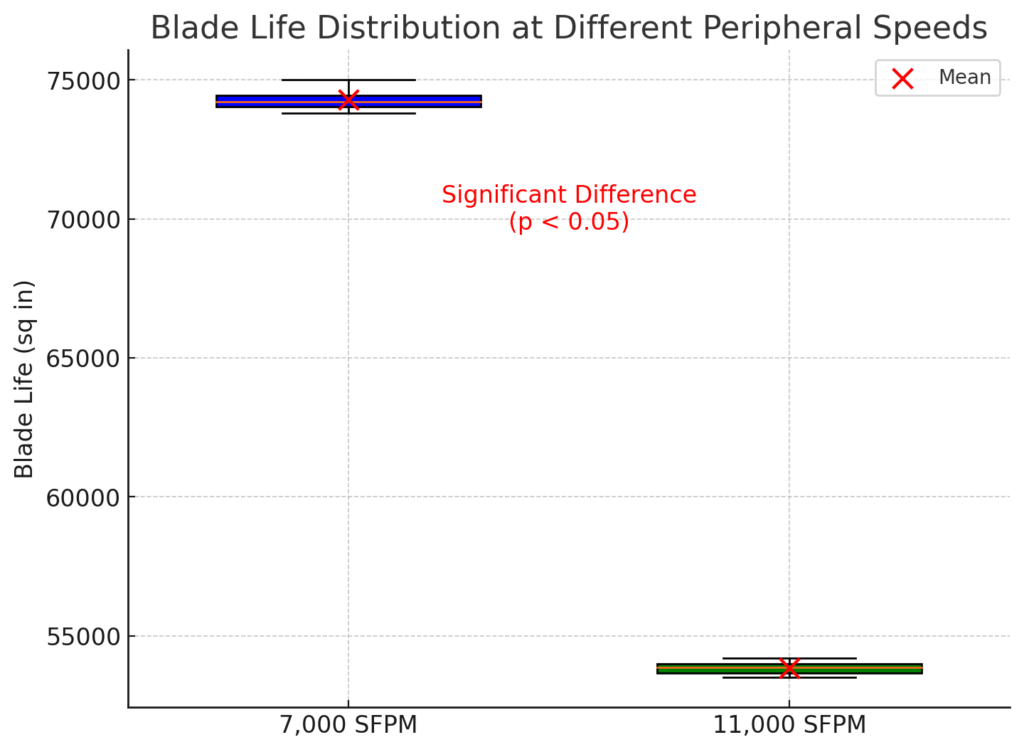
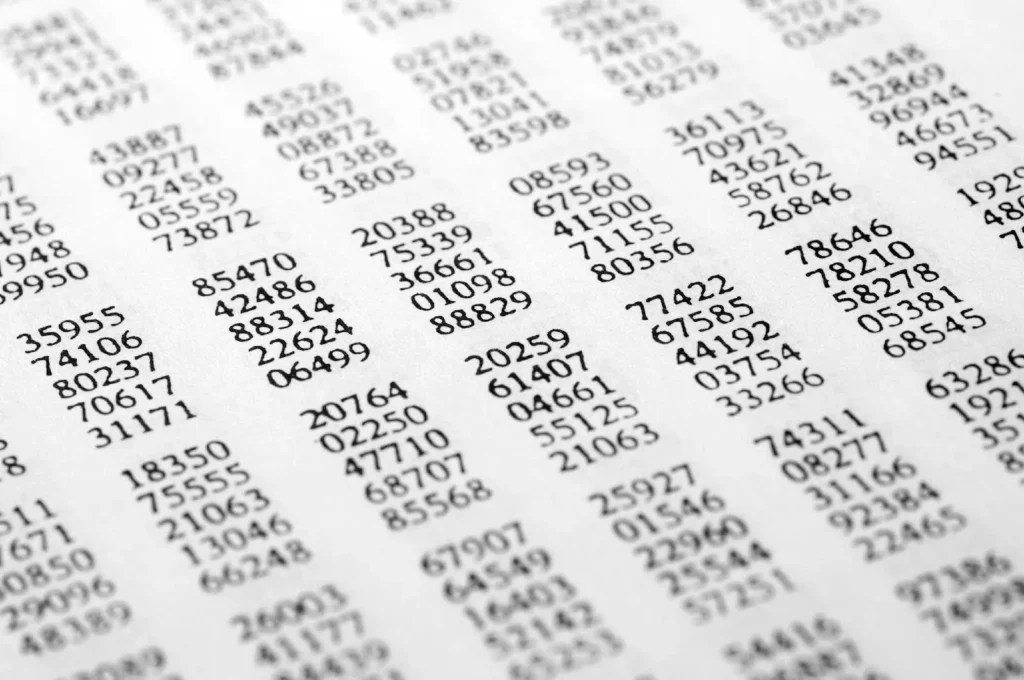
Randomization in Testing Process
Introducing randomization in the selection of blades and test sequences is crucial for eliminating bias and ensuring objective test results in diamond blade evaluations. Randomization prevents any unconscious biases in the choice of blades, ensuring that each blade has an equal chance of being tested. This method helps avoid selection bias and maintains the integrity of the test results.
Randomizing the sequence in which blades are tested is also important to avoid the impact of the order of testing on the results, particularly as blades might degrade slightly over time. This approach ensures that results are not skewed by blades being tested later in their lifecycle, where prior use might affect performance.
By mitigating the impact of confounding variables and distributing external influences evenly across the test samples, randomization enhances the reliability of the conclusions drawn from the data. It also adds statistical rigor to the testing process, allowing for accurate inferences about the blade's performance across a general population of similar products.
Implementing randomization can be done using random number generators to determine the order of blade selection and testing sequences. This method not only supports the development of high-quality diamond and cbn blades but also builds confidence among manufacturers and users in the product's consistency and reliability.
Measuring Results
This enables the detection of subtle differences and improvements in using different blades and processes. Utilizing high-precision instruments like micrometers, calipers, and optical systems helps accurately assess cut depth, cut quality, and blade wear. These tools provide precise, repeatable measurements essential for comparing the minute variations in blade performance.
Advancements in digital measurement technologies and software for data analysis improve the efficiency and accuracy of these tests. They allow for quick data collection and sophisticated analysis, crucial for identifying performance patterns and conducting thorough quality control.
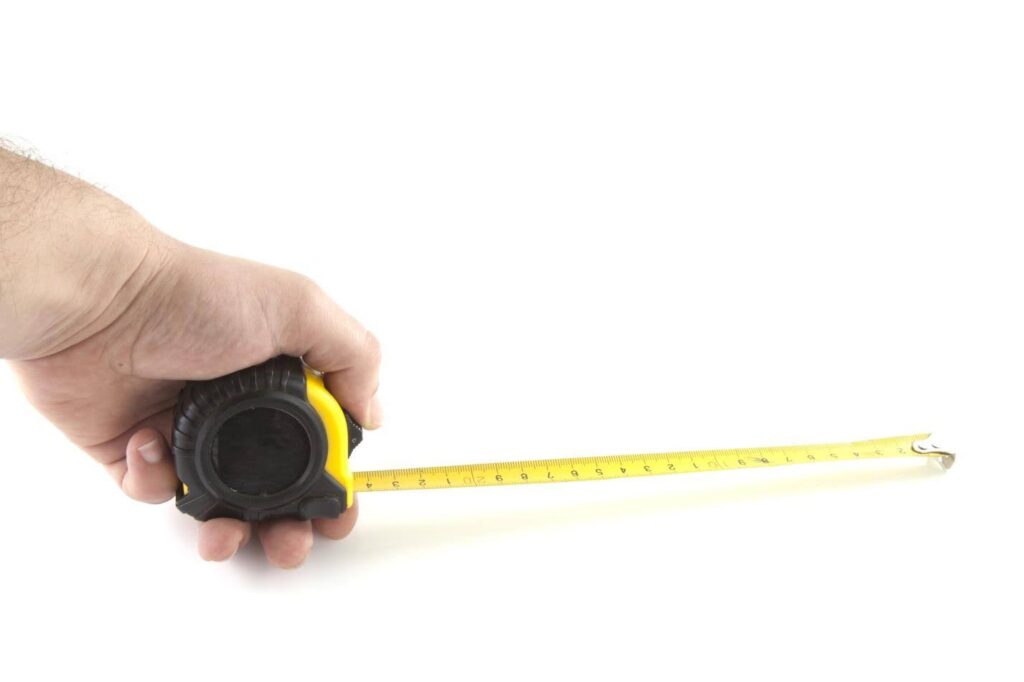
To ensure consistent and comparable test results, standardizing measurement procedures is necessary. This includes regular calibration of instruments and adherence to consistent measurement protocols across different testing setups. Integrating these precise measurement tools and practices helps maintain high standards in blade quality and supports ongoing improvements in diamond blade technology.
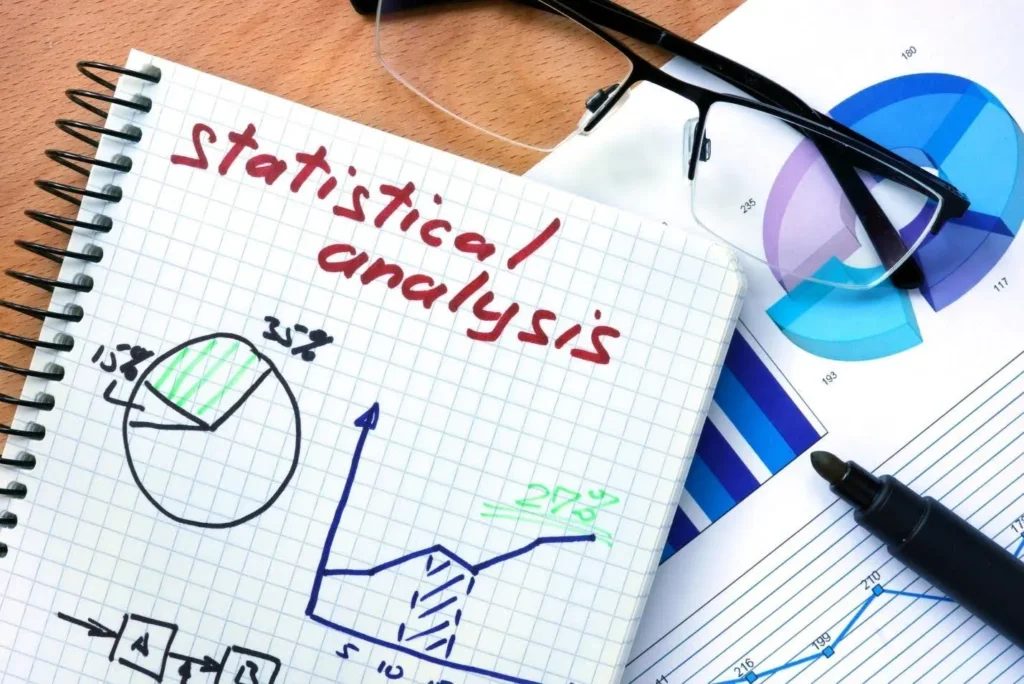
Statistical Testing Analysis
Statistical analysis is essential in evaluating diamond blade performance during tests. It uses simple averages (mean) and medians to summarize how a blade typically performs. Averages provide a general idea, while medians show the middle point of data, helping to mitigate the impact of unusually high or low values that could skew the average.
Standard deviation is another important measure, indicating how much a blade’s performance varies from one test to another. A smaller standard deviation suggests that the blade's performance is more consistent and predictable, which is beneficial for both manufacturers and users.
The analysis also involves examining trends over time or under different conditions and testing claims, such as whether a new blade design lasts longer than an older one. Techniques like regression analysis help to understand the effects of various factors like blade material or speed on performance, and hypothesis testing methods like t-tests allow checking if performance differences are significant or just by chance.
Graphs and charts are also used to make the data more digestible. They visually highlight patterns, outliers, and trends, making it easier for everyone to understand the results, even those without a technical background.
Overall, statistical analysis helps quantify how diamond blades perform under different testing conditions, ensuring that improvements to the blades are based on solid data. This method makes the testing process more dependable and the results more straightforward and trustworthy.
Example of Statistical Testing Analysis:
The following example shows graphically the affect of varying the peripheral speed (SFPM):
Blade diameter – 14” diameter
Cutting fed rate – 6 ft/mn
Dept of cut – ¼”
Type of material cut – hard granite
Peripheral Speed Blade Life
7,000 SFPM 74,320 sq in
11,000 SFPM 53,937 sq in
in this cutting application can be seen the affect of varying the peripheral speed of the diamond blade on cutting efficiency. When the speed was kept within the recommended operation conditions, about 38% greater blade life was obtained. In other words, we have reduced our blade cutting costs about 28%.
Here's the table displaying the test results for blade life at different peripheral speeds across multiple tests:
Test Number |
7,000 SFPM (sq in) |
11,000 SFPM (sq in) |
---|---|---|
Initial |
74,320 |
53,937 |
Repeat 1 |
75,000 |
54,000 |
Repeat 2 |
74,500 |
53,500 |
Repeat 3 |
73,800 |
54,200 |
Repeat 4 |
74,100 |
53,800 |
Repeat 5 |
74,000 |
53,600 |
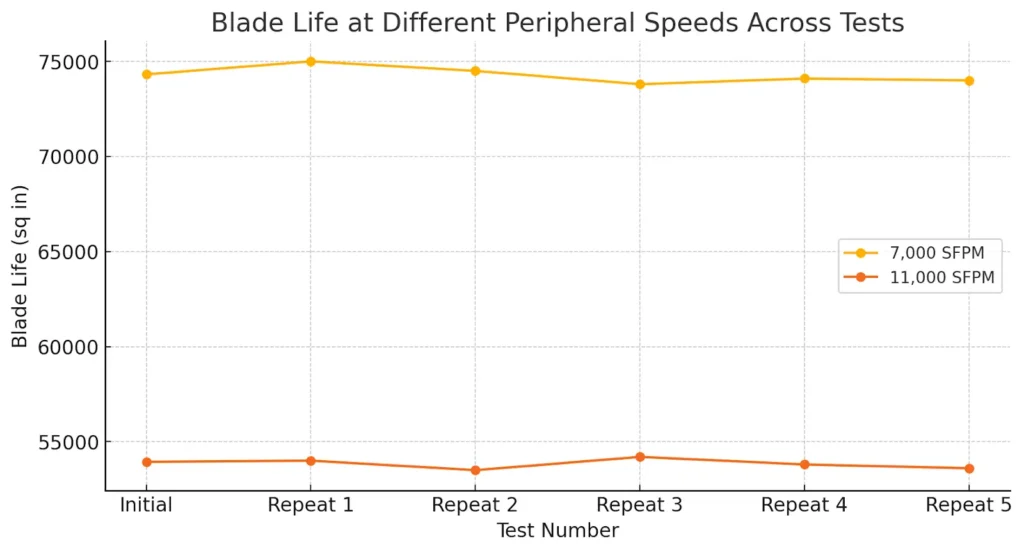
The accompanying graph plots these results, showing blade life at 7,000 SFPM and 11,000 SFPM across the initial and five repeat tests. The graph illustrates that blade life at 7,000 SFPM consistently exceeds that at 11,000 SFPM across all tests, confirming the initial findings with repeat testing. This visual representation helps in easily seeing the trend and consistency in blade performance at different speeds, supporting the conclusion that lower peripheral speeds lead to increased blade life.
Average Blade Life at Different Peripheral Speeds
Here's the bar chart showing the average blade life at two different peripheral speeds, 7,000 SFPM and 11,000 SFPM. The chart clearly illustrates that the average blade life at 7,000 SFPM is significantly higher than at 11,000 SFPM, reinforcing the benefits of operating at a lower speed for enhanced blade longevity.
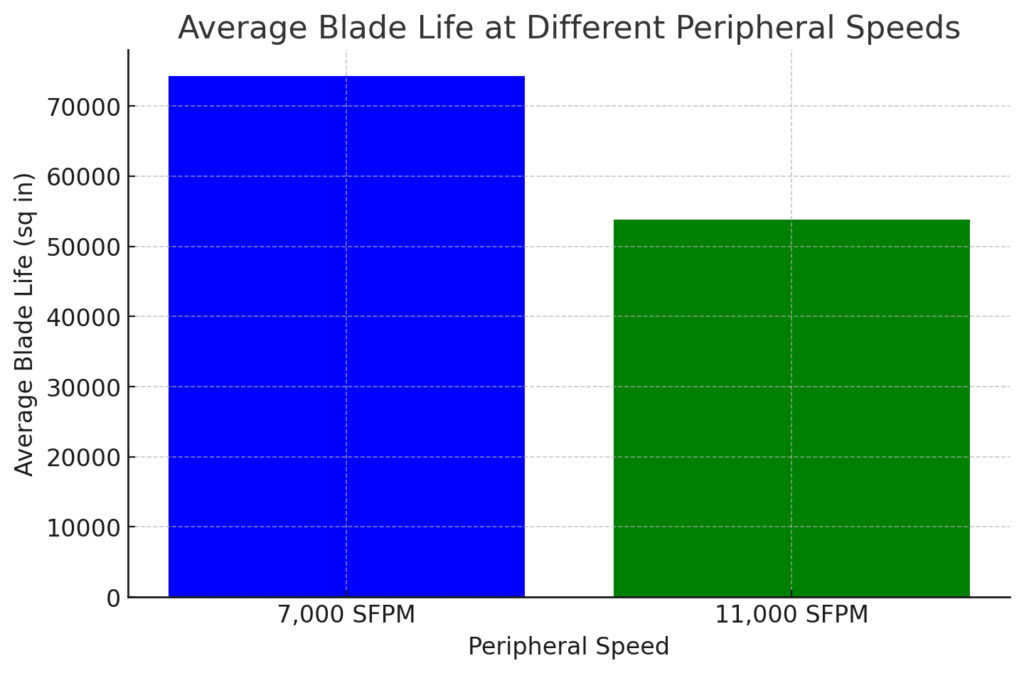
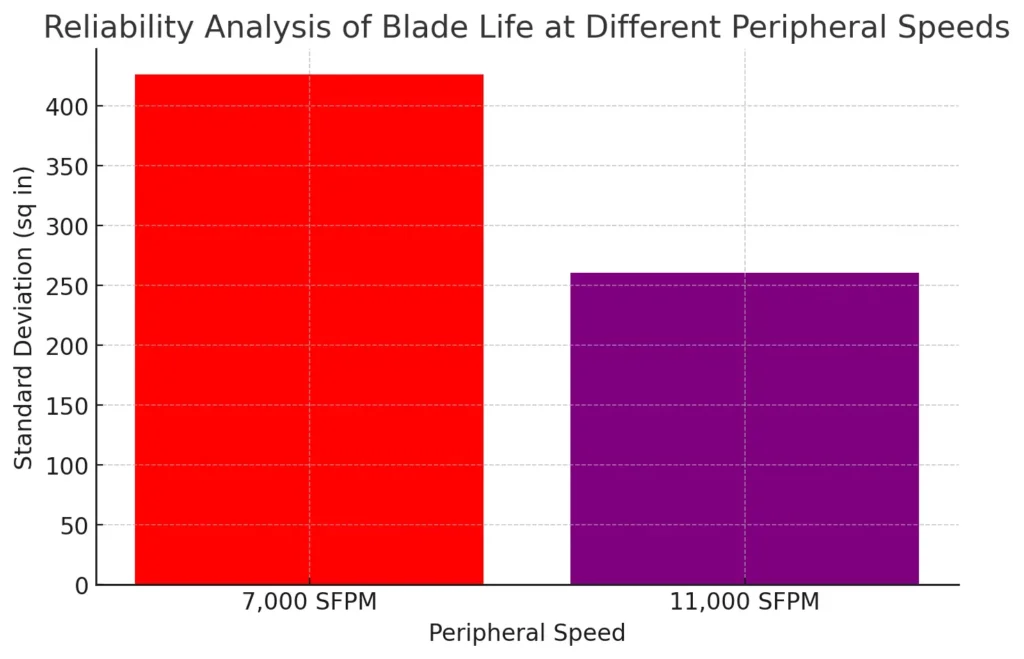
Here's the bar chart illustrating the reliability analysis of blade life at different peripheral speeds, based on the standard deviation of the results. The chart shows the standard deviation for blade life at 7,000 SFPM and 11,000 SFPM. A lower standard deviation indicates more consistent results, and as shown, both speeds demonstrate variability in blade life, which is a key aspect of understanding the reliability of the blade under different operating conditions. This graph is critical for assessing how predictably a blade performs, with lower variability generally preferred for consistent performance.
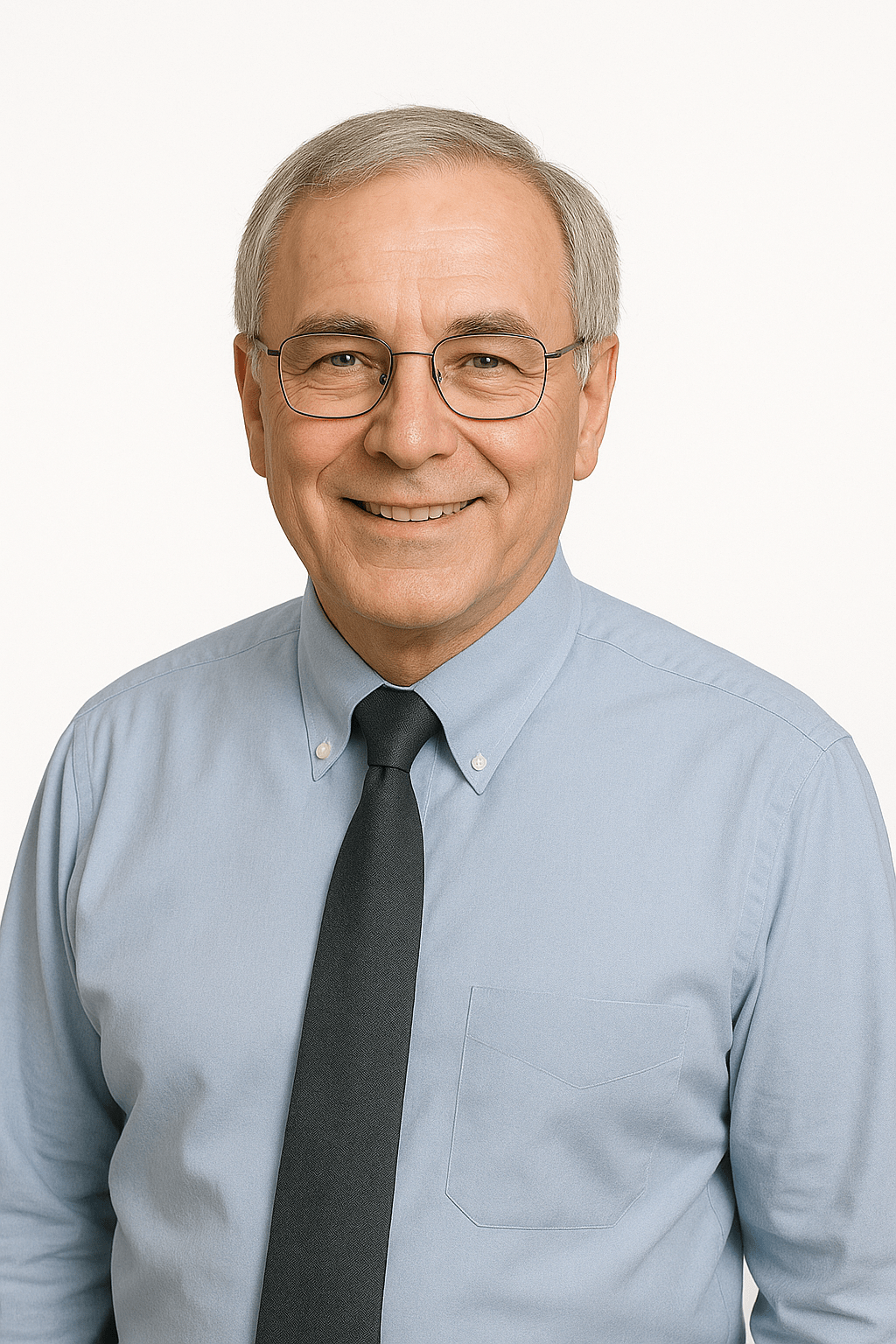
Alexander Schneider is a senior applications engineer and leading authority in the industrial diamond tooling industry, with over 35 years of hands-on experience in the development, application, and optimization of ultra-thin and high-precision diamond blades, diamond core drills, and diamond and CBN grinding wheels. His work spans a wide range of advanced materials including ceramics, glass, composites, semiconductors, and high-performance metals.
Throughout his career, he has collaborated with leading R&D institutions, national laboratories, and high-tech manufacturing companies across Europe, North America, and Asia, providing technical expertise and tailored solutions for demanding cutting and surface preparation applications.
Mr. Schneider has played a pivotal role in advancing precision cutting, sectioning, dicing, and grinding technologies used in research, production, and failure analysis. He is widely respected for his ability to optimize tool design and cutting parameters to meet exacting industry standards—balancing factors such as cut quality, blade life, material integrity, and process consistency.
As an author, Mr. Schneider is known for delivering practical, application-focused insights that translate complex technical challenges into clear, actionable strategies. His articles and technical guides serve as trusted resources for engineers, researchers, and manufacturers seeking to improve precision, reduce process variability, and enhance tool performance in critical applications.
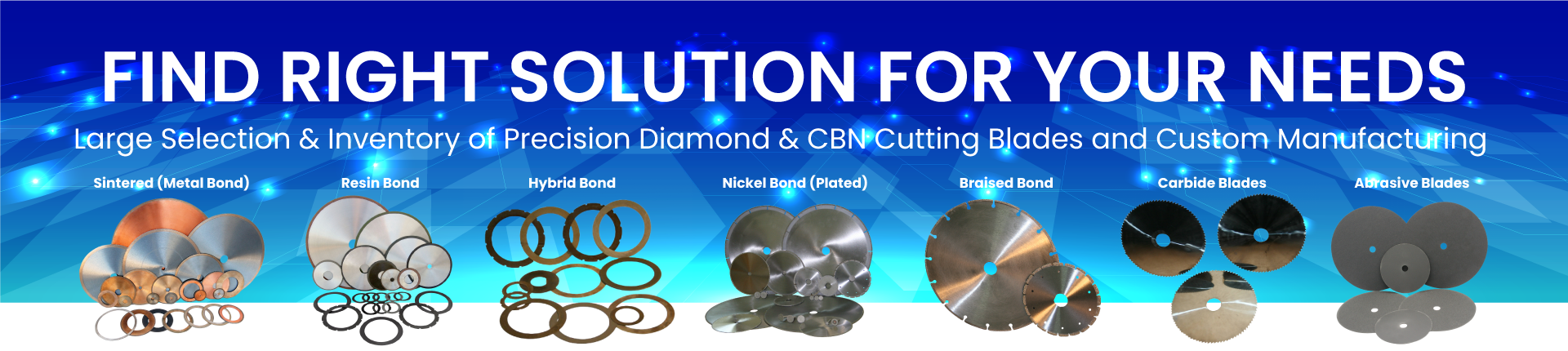
ARE YOU USING RIGHT DIAMOND & CBN BLADES
FOR YOUR APPLICATION?
LET US
HELP YOU
HAVING ISSUES WITH
YOUR CURRENT DIAMOND & CBN BLADES?
Knowledge Center
Select right Diamond Blade for your application
How to Properly Use Precision Diamond & CBN Blades
Precision & Ultra Thin Diamond Blade Guide
How to Improve & Optimize Your Diamond Sawing Operation
Top 5 Diamond & CBN Cutting Blade Performance Metrics
Diamond & CBN Cutting Blade Performance Metrics that you Should Know
Total Cost of Ownership & Why its Important
Understanding Tradeoffs- Searching for Perfect Diamond & CBN Blade
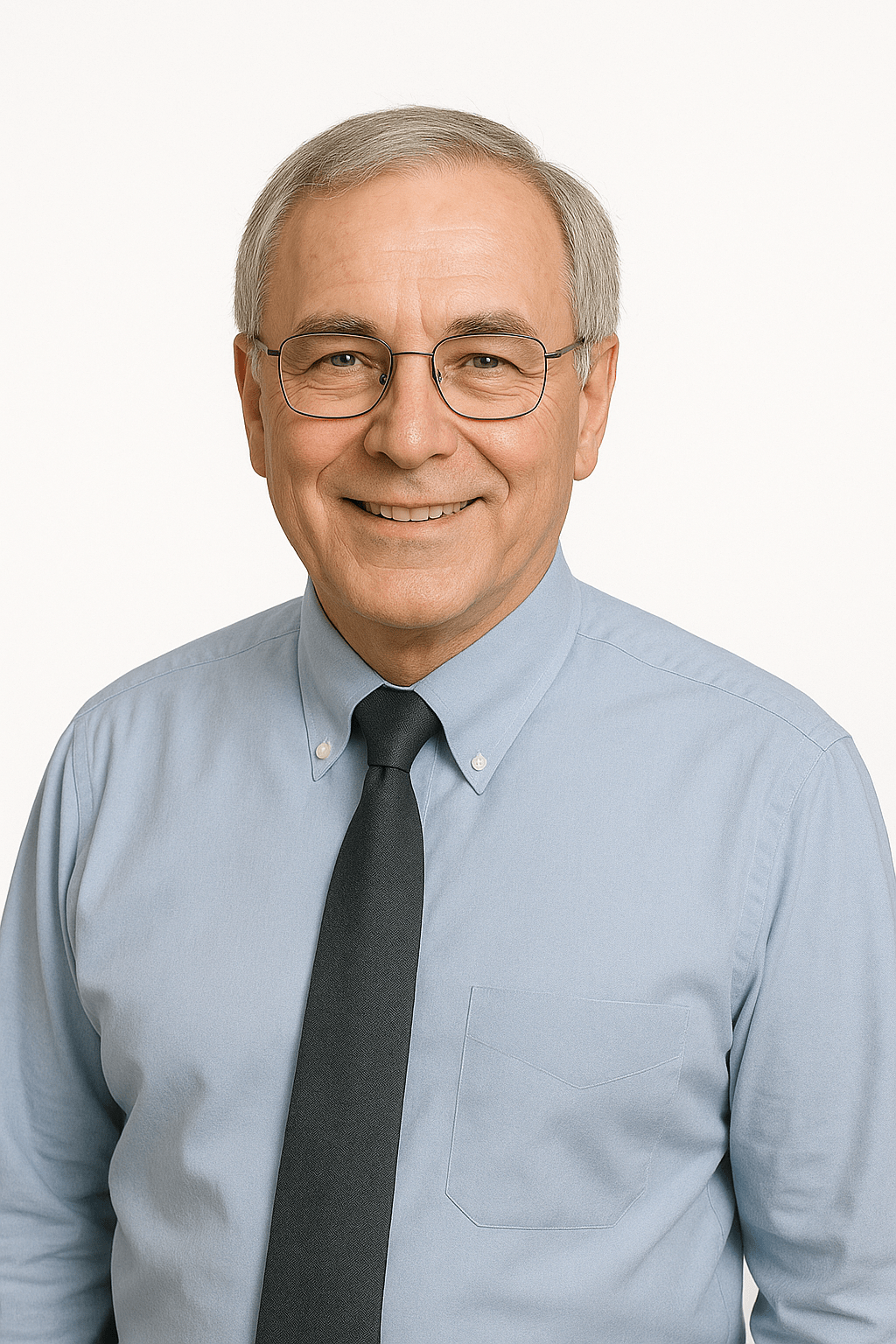
Alexander Schneider is a senior applications engineer and leading authority in the industrial diamond tooling industry, with over 35 years of hands-on experience in the development, application, and optimization of ultra-thin and high-precision diamond blades, diamond core drills, and diamond and CBN grinding wheels. His work spans a wide range of advanced materials including ceramics, glass, composites, semiconductors, and high-performance metals.
Throughout his career, he has collaborated with leading R&D institutions, national laboratories, and high-tech manufacturing companies across Europe, North America, and Asia, providing technical expertise and tailored solutions for demanding cutting and surface preparation applications.
Mr. Schneider has played a pivotal role in advancing precision cutting, sectioning, dicing, and grinding technologies used in research, production, and failure analysis. He is widely respected for his ability to optimize tool design and cutting parameters to meet exacting industry standards—balancing factors such as cut quality, blade life, material integrity, and process consistency.
As an author, Mr. Schneider is known for delivering practical, application-focused insights that translate complex technical challenges into clear, actionable strategies. His articles and technical guides serve as trusted resources for engineers, researchers, and manufacturers seeking to improve precision, reduce process variability, and enhance tool performance in critical applications.