Table of Contents
ToggleUnderstanding the wear mechanisms of diamond crystals is essential for optimizing cutting performance in terms of both cutting ratio and speed. Diamond crystal loss, which primarily occurs through micro chipping rather than fracturing or pullout, is crucial for maximizing efficiency and reducing tool degradation. This fine balance aims to preserve the cutting edge by minimizing the severe impacts that lead to crystal degradation.
Share this Article with Friend or Colleague
Selecting the Appropriate Diamond Crystals for Your Application
When optimizing the performance of diamond tools, the selection of diamond crystals or particles plays a crucial role. This choice largely depends on the material to be cut, as different materials vary in hardness and abrasiveness, impacting both wear and efficiency of the diamond crystals.
The selection process involves considering the material hardness since harder materials require diamonds with greater mechanical strength to cut effectively without suffering premature wear or damage. The market offers a diverse array of both natural and synthetic diamond crystals, each engineered to meet specific demands.
Natural diamonds are often preferred for their lasting sharpness and durability, ideal where longevity and precision are paramount.
Synthetic diamonds, produced through methods like high-pressure high-temperature synthesis or chemical vapor deposition, can be tailored to show specific properties such as improved thermal stability and predictable wear patterns, making them suitable for repetitive industrial tasks.
The mechanical strength of a diamond is crucial as it determines the ability to resist crushing and maintain an edge under intense conditions. Thermal stability is also vital, especially in applications that generate significant heat or involve high-speed cutting, ensuring diamonds can withstand thermal stresses without degrading. Additionally, the bond retention characteristic of a diamond, which refers to its capacity to adhere to the tool’s bond matrix, whether metal, resin, or ceramic, affects overall tool performance and durability.
Table that outlines key characteristics of diamond crystals, their descriptions, and the importance of each characteristic in industrial applications:
Characteristic |
Description |
Importance |
---|---|---|
Mechanical Strength |
Higher strength diamonds are necessary for cutting tougher materials to prevent shattering and ensure clean cuts. |
Essential for cutting hard, tough materials without failure, ensuring durability and precision in cuts. |
Thermal Stability |
Diamonds should resist changes in shape, size, and strength under high temperatures, crucial in high-speed cutting operations that generate substantial heat. |
Critical for operations where tools are subjected to high temperatures, preventing degradation and loss of cutting capability. |
Bond Retention |
Diamonds must maintain a strong bond with the tool matrix to prolong tool life and ensure consistent performance. Tailored synthetic diamonds for specific bonds like metal, resin, or vitrified can significantly enhance tool efficiency. |
Vital for achieving prolonged tool life and consistent cutting performance, especially in tools designed for specific applications. |
Choosing the right diamond also involves strategic considerations beyond simply matching crystal properties with material characteristics. This includes analyzing the cutting equipment, cutting speed, desired finish, and operational costs. While stronger, more durable diamonds may perform better, they also come with a higher price tag, requiring a balance between cost and performance needs. Investing in higher-quality diamonds can also lead to long-term savings by reducing tool changeovers and downtime. Furthermore, environmental factors such as the presence of coolants, ambient temperature, and humidity can influence diamond choice, as these elements can affect the thermal and mechanical stresses experienced by the tool.
Importance of Diamond Crystal Shape in Tool Performance
The shape of the diamond crystal significantly influences the consistency and quality of industrial diamond tools. Optimal crystal shapes vary according to specific applications, ranging from pure cubes to perfect octahedrons, with many crystals exhibiting a cubo-octahedral form—a hybrid shape that optimizes both sharpness and durability.
Typically, diamond crystals form in geometries that blend cubic and octahedral traits:
-
Cubic faces often appear square or rectangular.
-
Octahedral faces exhibit triangular or hexagonal shapes.
-
Occasionally, rhombohedral faces may be present, appearing rectangular or rhombohedral—a rarity in synthetic diamonds due to their growth conditions but common in natural diamonds.
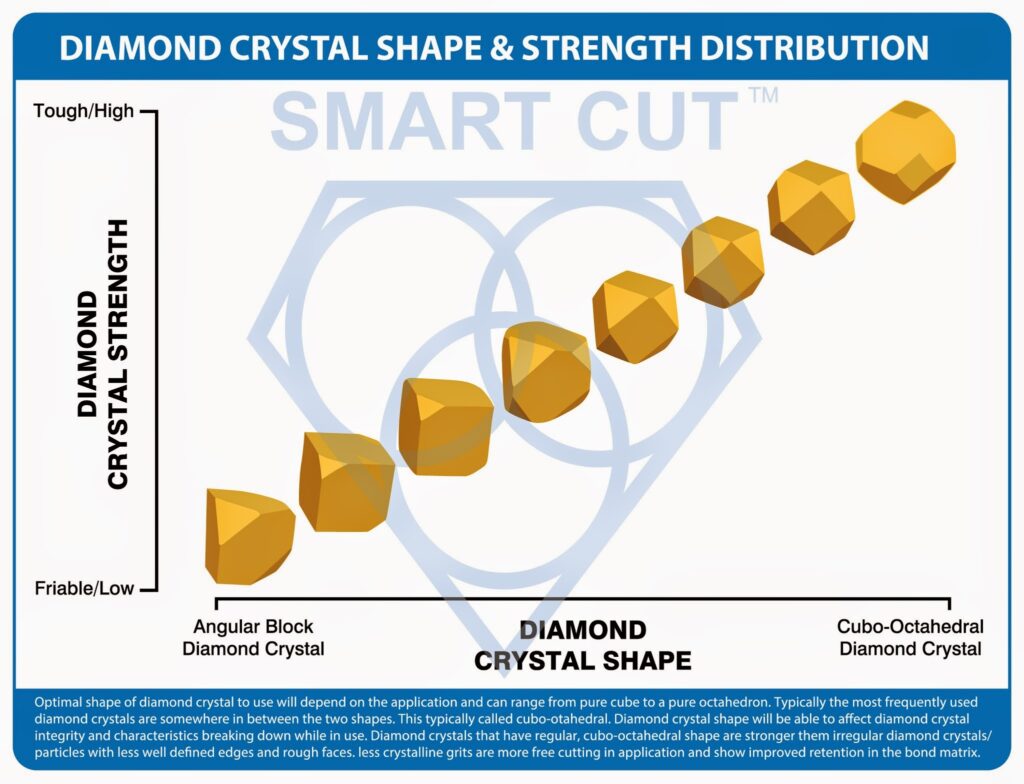
Table outlining the characteristics and key benefits of three different diamond crystal shapes:
Diamond Crystal Shape |
Description |
Key Benefits |
---|---|---|
Dodecahedron |
A dodecahedron diamond crystal has many facets, providing a balance between cutting efficiency and durability. Its multiple surfaces help distribute wear more evenly, enhancing the lifespan of the diamond in abrasive applications. |
Balanced cutting efficiency and durability, even wear distribution, enhanced lifespan |
Rhombododecahedron |
This complex shape combines aspects of both cubic and octahedral forms, offering a good compromise between strength and available cutting edges. It is versatile for various cutting applications due to its increased point strength and improved retention within the bond matrix. |
Combines strength and cutting edge availability, versatile in application, improved retention |
Octahedron |
The octahedron is one of the most effective shapes for cutting applications due to its pointed ends and sharp edges. This shape allows for excellent penetration and cutting speed, making it ideal for high-precision tasks. Its structure also tends to expose new sharp edges as it wears, which can help maintain cutting effectiveness over time. |
Excellent penetration and cutting speed, ideal for high-precision tasks, self-sharpening |
The growth environment of synthetic diamonds, particularly the temperature and catalysts used (such as Fe, Co, Ni, or other alloys), heavily influences their shape. Despite aiming for uniformity, synthetic processes often yield diamonds with irregular shapes, rough surfaces, and even metal inclusions or other defects. Each diamond crystal nucleates and grows uniquely within the synthesis chamber, contributing to these variabilities.
Consistently controlling the diamond shape is vital for maintaining product quality. Diamonds with a regular, cubo-octahedral shape tend to exhibit stronger structural integrity and more uniform wear characteristics. Their blocky, sharply edged forms offer enhanced resistance to fracturing, enabling more efficient material removal with fewer forces required. These crystals are particularly suitable for tougher, more durable bond families like sintered (metal) bonds.
In contrast, diamonds with more irregular and angular shapes provide better retention within softer, more brittle bond matrices such as resin bonds. These particles are typically used in less demanding applications and are favored for their free-cutting properties.
Angular Diamond vs Blocky Diamond Crystal
Angular diamond crystals are particularly valued for their sharp, precise edges which make them the preferred choice for precision applications requiring meticulous attention to detail. The defining feature of these crystals is their angular geometry, which provides several sharp points and edges that make precise and clean cuts possible. This ability to achieve high levels of precision is essential in industries where detail is paramount, such as fine jewelry making, precision engineering, and intricate component fabrication in electronics.
The effectiveness of angular diamond crystals in material removal is another key benefit. Their sharp angles cut efficiently into hard materials, removing small, precise amounts of material with each pass. This not only ensures accuracy but also reduces waste, which is critical when working with expensive or delicate materials.
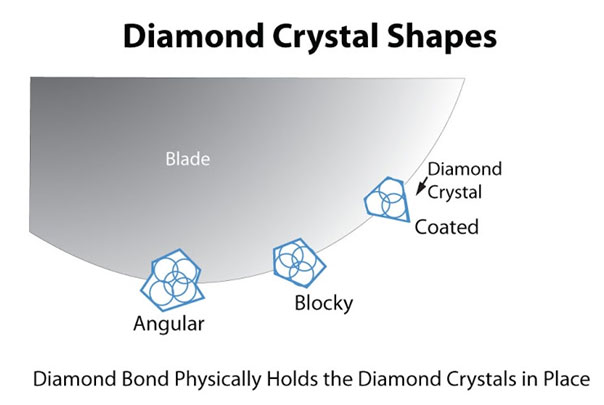
For example, in the electronics industry, angular diamonds are used to cut intricate patterns into silicon wafers without causing damage to the delicate structures.
Moreover, angular diamond crystals excel in tasks such as detailed engraving, where the ability to control cut depth and precision is necessary. Engraving with these crystals allows for intricate designs on hard surfaces such as metals and gemstones, which can significantly enhance the aesthetic and value of the product. Similarly, in the field of restorative dentistry, angular diamond crystals are used to shape dental ceramics, allowing for precise modifications and a perfect fit.
Additionally, the crafting of complex shapes in materials like aerospace composites or synthetic sapphires is another area where angular diamond crystals shine. Their precision enables manufacturers to achieve the exact geometries required for components that must meet stringent specifications for performance and safety.
Blocky diamond crystals are engineered to be inherently robust, making them the optimal choice for heavy-duty cutting operations that demand both strength and durability. These crystals have a somewhat subdued angular structure, which enhances their resilience against breakage and allows them to withstand substantial wear and impact. This quality makes them particularly effective for industries engaged in rigorous cutting activities, such as construction and mining, where they routinely cut through highly abrasive materials like concrete and granite.
The design of blocky diamond crystals focuses on maximizing their life span and maintaining their performance over extended periods of intense usage. This attribute is crucial in applications such as the production of automotive and aerospace components, where precision and reliability are just as critical as the toughness of the cutting tool. The durability of blocky crystals means that tools equipped with them require fewer replacements and less frequent maintenance, which translates into uninterrupted workflows and reduced operational costs.
Additionally, the broad application range of blocky diamond crystals extends to manufacturing processes involving metals and advanced engineered materials. These crystals can handle the demands of cutting through tough metals like titanium and stainless steel, which are prevalent in machine part fabrication and shipbuilding. Their ability to maintain structural integrity at high cutting speeds and under significant physical stress makes them invaluable in settings that prioritize throughput and efficiency.
In terms of economic benefits, the longevity and robustness of blocky diamond crystals contribute directly to lowering the total cost of ownership of cutting tools. By reducing the need for frequent tool changes and minimizing downtime for repairs, these crystals provide a cost-effective solution for businesses aiming to optimize their production lines for high yield and minimal interruption.
The functionality of the diamond bond is also crucial, as highlighted in the illustration. The bond's primary role is to securely hold the diamond crystals to the blade, ensuring they remain in place throughout the cutting process. The effectiveness of this bond is paramount as it directly impacts the blade's performance by efficiently transferring the force from the machine into cutting power at the diamond tips. A strong bond minimizes the risk of crystal detachment, which can lead to inconsistent cuts and potential damage to both the tool and the material.
Understanding the different shapes of diamond crystals and the importance of a strong diamond bond can significantly influence the selection of cutting tools. Choosing the right type of crystal and ensuring it is properly bonded to the blade is key to maximizing cutting efficiency and extending the tool's operational life.
Comparison table that outlines the key characteristics, suitable applications, advantages, and the importance of bonding for angular and blocky diamond crystals:
Diamond Crystal Type |
Characteristics |
Suitable Applications |
Advantages |
Bond Importance |
---|---|---|---|---|
Angular |
Sharp, precise edges; ideal for detailed and intricate cutting. |
Detailed engraving, crafting complex shapes in harder materials. |
Allows for fine, meticulous work with exact cuts. |
Requires strong bonding to prevent crystal detachment and ensure precision. |
Blocky |
Robust, durable, less angular; built to endure significant wear and impact. |
Cutting a variety of materials like stones and tough metals. |
Ensures consistent performance under challenging conditions, reduces blade replacements. |
Strong bond crucial for maintaining crystal integrity and cutting power. |
Evaluating Diamond Crystal Quality: You Usually Get What You Pay For
The quality of synthetic diamonds plays a pivotal role in the performance and longevity of diamond tools in industrial applications, impacting everything from cutting efficiency to tool life. Here’s a closer look at how different qualities of synthetic diamonds cater to various needs:
High-Quality Synthetic Diamonds
High-quality synthetic diamonds are specially made to handle tough conditions in industries where strong performance and durability are essential. These diamonds are mainly used in settings that require sturdy bonds, like those found in sintered (metal bonds). They're perfect for cutting hard materials such as quartz, sapphire, and advanced ceramics, which are challenging for lesser quality diamonds.
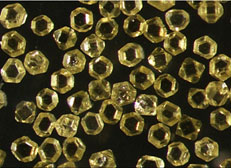
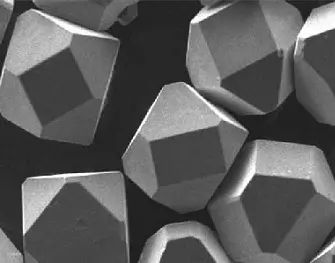
The shape of these diamonds is carefully designed with octahedral, blocky forms to maximize cutting efficiency. This design provides multiple sharp edges that make for precise and clean cuts, which is particularly important in industries like electronics, where exact cuts are needed for things like silicon wafers or glass screens.
These diamonds can also withstand very high temperatures and pressures, which is crucial for maintaining performance in environments where cutting generates a lot of heat. Their ability to hold up under such conditions prevents them from breaking down and losing efficiency, a common problem with lower quality diamonds.
One of the best features of high-quality synthetic diamonds is their self-sharpening ability. As the diamond gets used, it naturally exposes new, sharp edges, which keeps the cutting tool working well without needing to replace it often. This not only helps keep costs down by extending the life of the diamond tools but also keeps machines running longer without interruption, boosting productivity.
This makes high-quality synthetic diamonds a top choice in fields where reliability and precision are key. They are indispensable in areas such as aerospace engineering, where they might be used to machine important components, or in medical device manufacturing, where accurate cuts are critical.
Advantages of High Quality Diamond
-
Usually used for harder bonds such as Sintered (metal bond)
-
Used for harder & more challenging applications
-
Strongest diamond crystal
-
lasts longer
-
capable of withstanding higher temperature & pressure
-
Octahedral Shape (more blocky shape)
-
Higher Termostability
-
More sharper points and better edge definition
-
Minimum number of inclusions or defects on surface
-
Self Sharpening Characteristics
Medium Quality Synthetic Diamonds
Medium quality synthetic diamonds serve as an excellent middle ground between performance and cost, making them versatile and well-suited for a variety of applications that don't push the limits of what diamond tools can handle. These diamonds have a mix of crystal shapes—some blocky and some irregular. This variety in shape helps them strike a balance between being tough enough to last and aggressive enough to cut effectively. They're great for cutting softer types of stones, various metals, and composite materials, and they do so at speeds that keep production moving along smoothly.
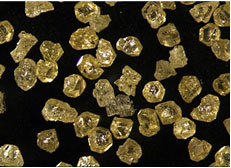
The durability of medium quality diamonds means they perform reliably over time, which is essential for manufacturers who need their tools to last but can’t justify the expense of the highest grade diamonds. Additionally, these diamonds handle heat pretty well. They have moderate thermostability, which means they can withstand typical manufacturing temperatures without losing their effectiveness too quickly. This makes them a go-to choice in environments that are tough on tools but not extremely so—like general machining or fabricating operations where extreme temperatures and pressures aren’t a constant challenge.
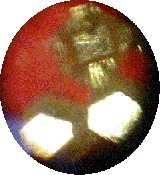
Medium quality diamonds are particularly valued in settings where cost considerations are as important as performance. They offer a reliable, cost-effective option that helps keep production costs down without sacrificing too much in terms of tool life or quality of output. This makes them ideal for smaller shops or less intensive applications, where every dollar saved on tools can make a big difference to the bottom line.
In short, these diamonds are a practical choice for many businesses. They provide good performance where it’s needed most, without the high costs associated with the top-tier synthetic diamonds. For many manufacturers, this level of quality meets their needs perfectly, balancing cost, performance, and durability in a way that supports efficient and effective production.
Advantages of Medium Quality Diamond
-
combination of blocky and irregular shape crystal
-
suitable for electroplated and resin bond tools
-
Medium Thermostability
-
Good Cutting Speed
-
Good Crystal Shape and Strength
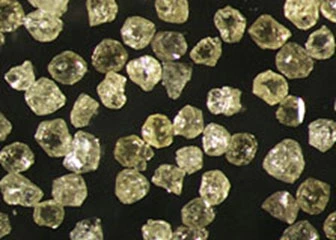
Low-Quality Synthetic Diamonds
At the more affordable end of the spectrum, low-quality synthetic diamonds are tailored for situations where the finest precision and fastest cutting speeds are not crucial priorities. These diamonds typically have irregular and weaker shapes, which tend to wear out more quickly and cut at slower rates. As a result, they are most suitable for consumer-grade tools used in basic cutting and grinding tasks where high performance is not a necessity.
The reduced durability of these diamonds means they're often incorporated into tools designed for less demanding, non-industrial applications, like DIY home projects or light craft work. The advantage here is cost: low-quality synthetic diamonds significantly lower the price of the tools, making them accessible to hobbyists and casual users who may not benefit from investing in more robust, professional-grade equipment.
Another characteristic of these diamonds is their lower thermal stability. This limits their effectiveness to environments where heat generation is minimal. They are not suited for heavy-duty machining or other high-heat applications as they are prone to quicker degradation and loss of cutting edges under such conditions. Instead, these diamonds are better suited to operations that require less intensity and generate less heat, ensuring that the diamonds can perform adequately over their expected lifespan.
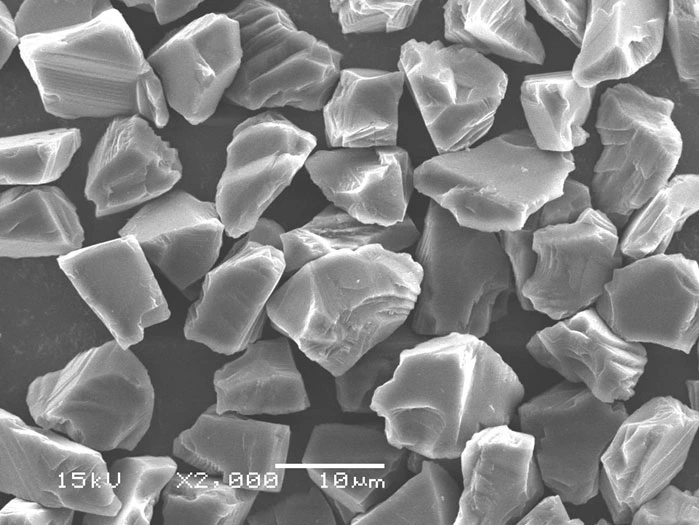
Low-quality diamonds are typically embedded in softer, faster-wearing bond matrices like resin bonds. Resin bonds are less durable than metal bonds but are cheaper and sufficient for light applications. This makes low-quality diamonds a popular choice in the manufacturing of low-cost tools where the price is a more significant concern than long-term performance.
Advantages of Low Quality Diamond
-
Weaker crystals wear irregular shape
-
shorter life and lower cutting rates
-
Lower thermal stability
-
jagged points break causing waster wear
-
Used softer and faster wearing bonds such as Resin Bond
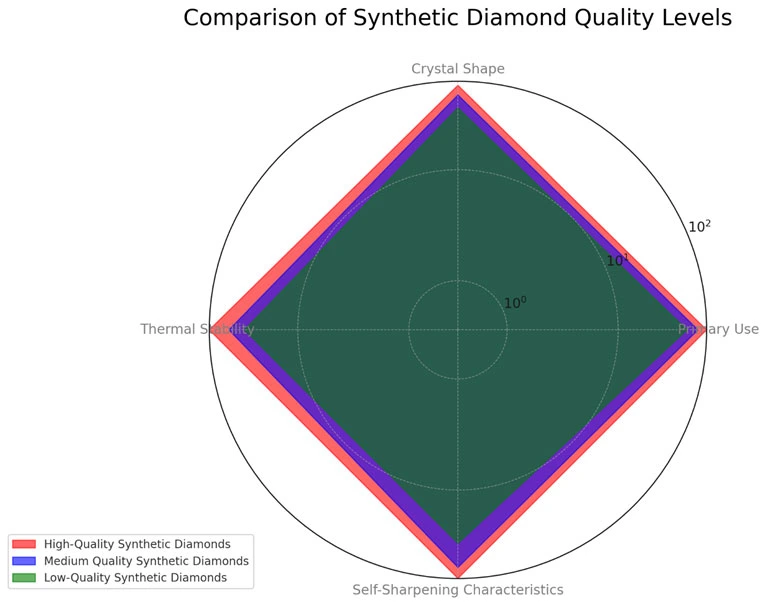
Table for the different quality levels of synthetic diamonds, highlighting their characteristics and typical applications:
Quality Level |
Primary Use |
Crystal Shape |
Thermal Stability |
Self-Sharpening Characteristics |
---|---|---|---|---|
High-Quality Synthetic Diamonds |
Harder, more challenging applications and stronger bonds such as sintered (metal bond) |
Octahedral shapes with more blocky configurations, providing sharper points and better edge definition |
High thermostability with minimal inclusions or defects |
Possess self-sharpening characteristics, contributing to longer lifespan and consistent performance |
Medium Quality Synthetic Diamonds |
Versatile for various tooling applications including electroplated and resin bond tools |
Balance between blocky and irregular shapes |
Moderate thermostability |
Good cutting speed and satisfactory crystal shape and strength |
Low-Quality Synthetic Diamonds |
Softer and faster-wearing bond matrices such as resin bonds |
Weaker, more irregular shapes |
Lower thermal stability |
Jagged points prone to breakage, resulting in faster wear |
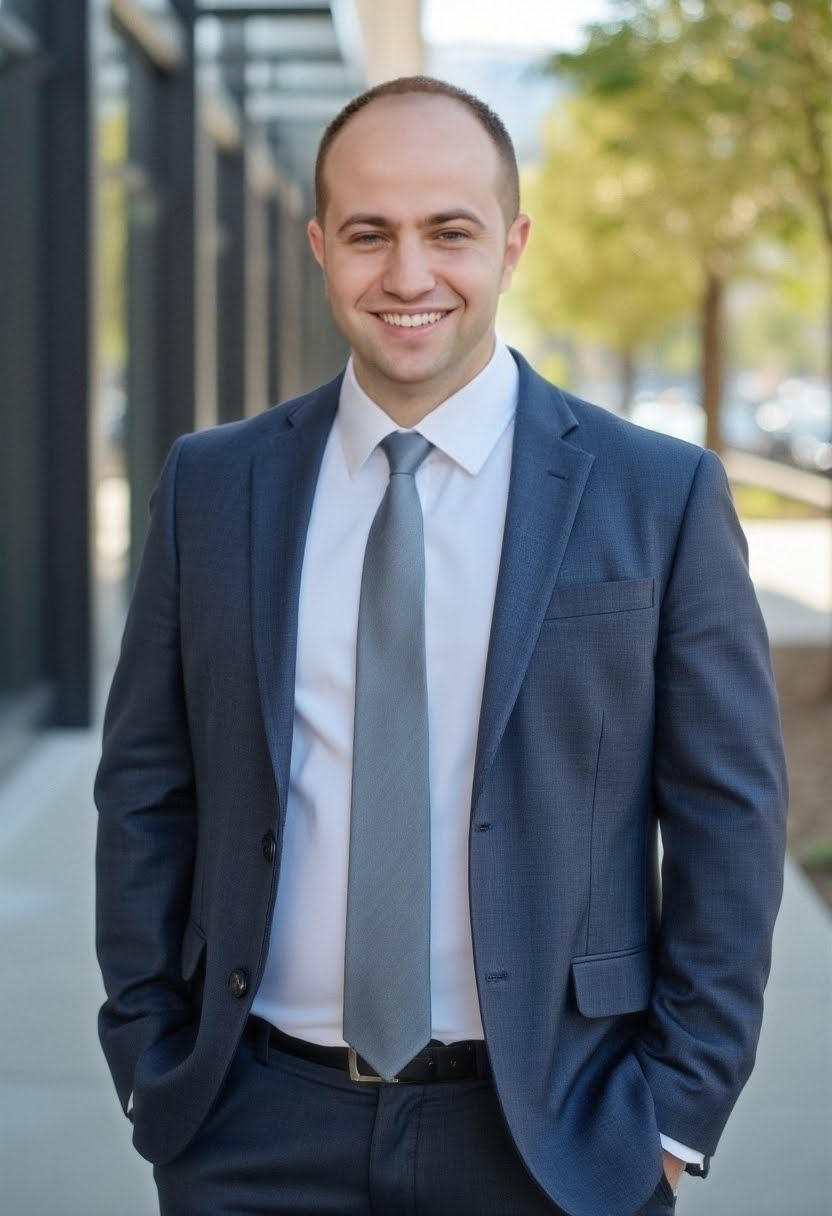
Brian is an experienced professional in the field of precision cutting tools, with over 27 years of experience in technical support. Over the years, he has helped engineers, manufacturers, researchers, and contractors find the right solutions for working with advanced and hard-to-cut materials. He’s passionate about bridging technical knowledge with real-world applications to improve efficiency and accuracy.
As an author, Brian Farberov writes extensively on diamond tool design, application engineering, return on investment strategies, and process optimization, combining technical depth with a strong understanding of customer needs and market dynamics.
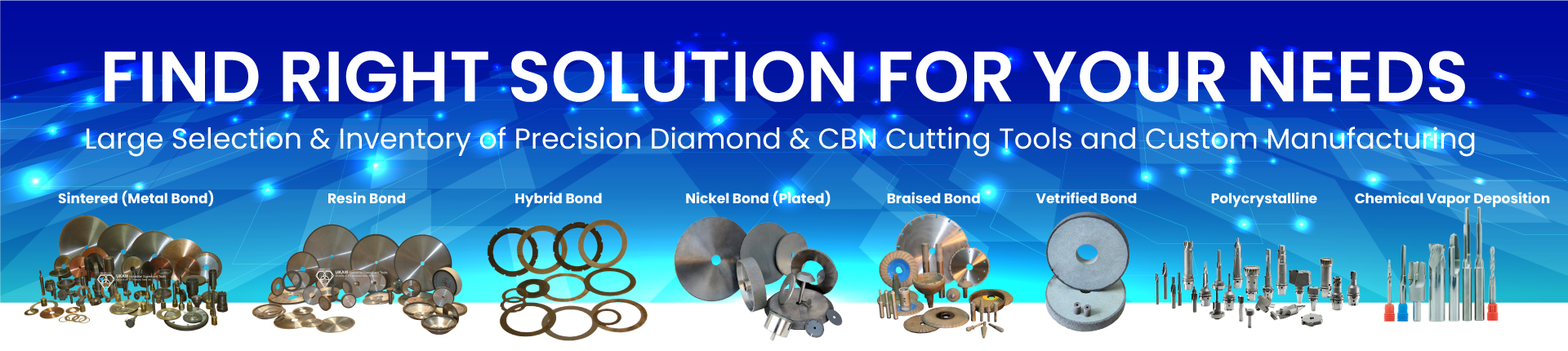
ARE YOU USING RIGHT TOOLS
FOR YOUR APPLICATION?
LET US
HELP YOU
HAVING ISSUES WITH
YOUR CURRENT TOOLS?
Knowledge Center
How to Selecting Right Diamond Tools for your application
How to properly use Diamond Tools
Why use diamond
Diamond vs CBN (cubic boron nitride) Tools
What is Diamond Mesh Size and how to select best one for your application
What is Diamond Concentration and which to use for your application
Diamond Tool Coolants Why, How, When & Where to Use
Choosing The Correct Diamond Bond Type
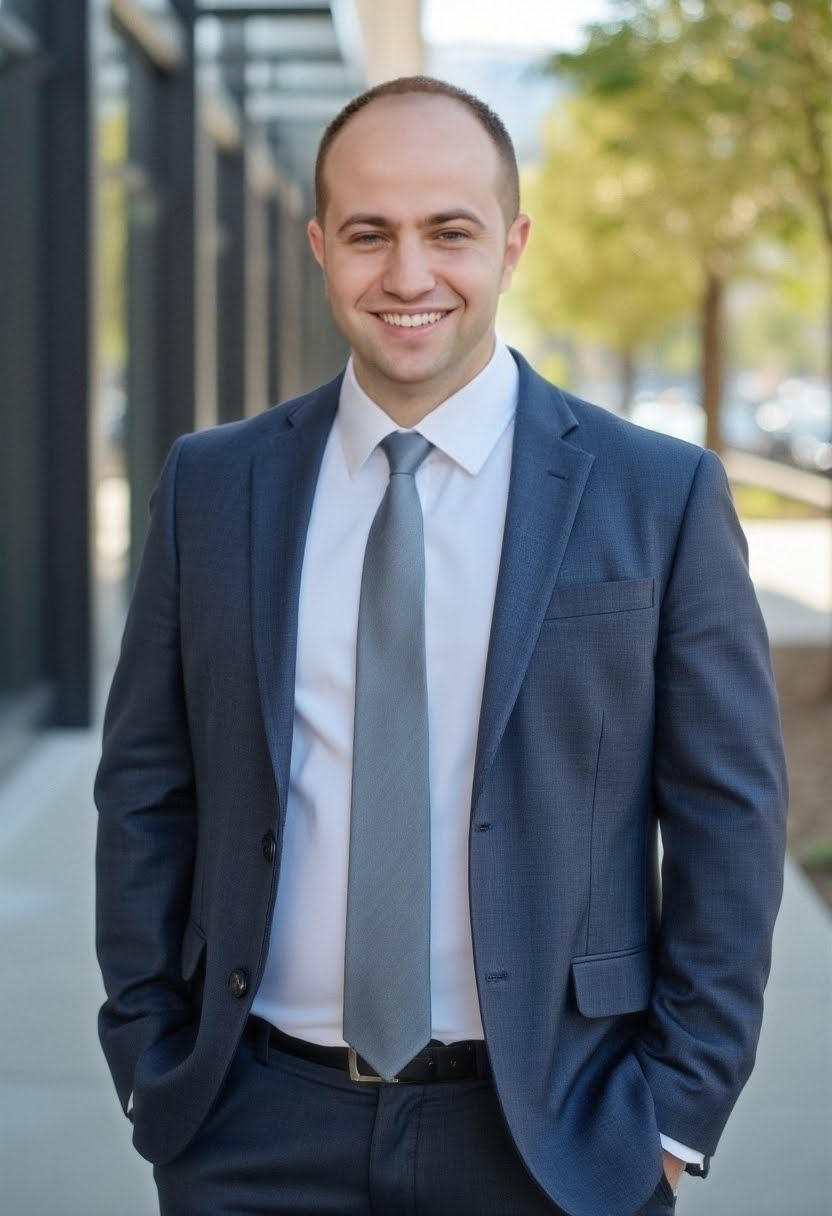
Brian is an experienced professional in the field of precision cutting tools, with over 27 years of experience in technical support. Over the years, he has helped engineers, manufacturers, researchers, and contractors find the right solutions for working with advanced and hard-to-cut materials. He’s passionate about bridging technical knowledge with real-world applications to improve efficiency and accuracy.
As an author, Brian Farberov writes extensively on diamond tool design, application engineering, return on investment strategies, and process optimization, combining technical depth with a strong understanding of customer needs and market dynamics.