Table of Contents
ToggleThe diamonds impregnated inside the bond matrix of the diamond & tool, are what actually participate in cutting action. No matter what equipment and process you are using. You will not be able to obtain the material surface finish, and precision tolerances you need, if the diamond & cbn crystals you are using is not right for your application.
There are significant differences in diamond crystal types, specifications, and performance. This article examines the critical relationship between the quality of diamond crystals and their performance in various applications. We will discuss using not only higher quality diamond type, but also matching right diamond specification for the particular type of tool and material/application and process can lead to significant advantages, including enhanced cutting precision, reduced tool wear, and overall cost savings. The goal of this article is to help users understand the various specifications of the diamond crystals that are used in producing the tools that they use.
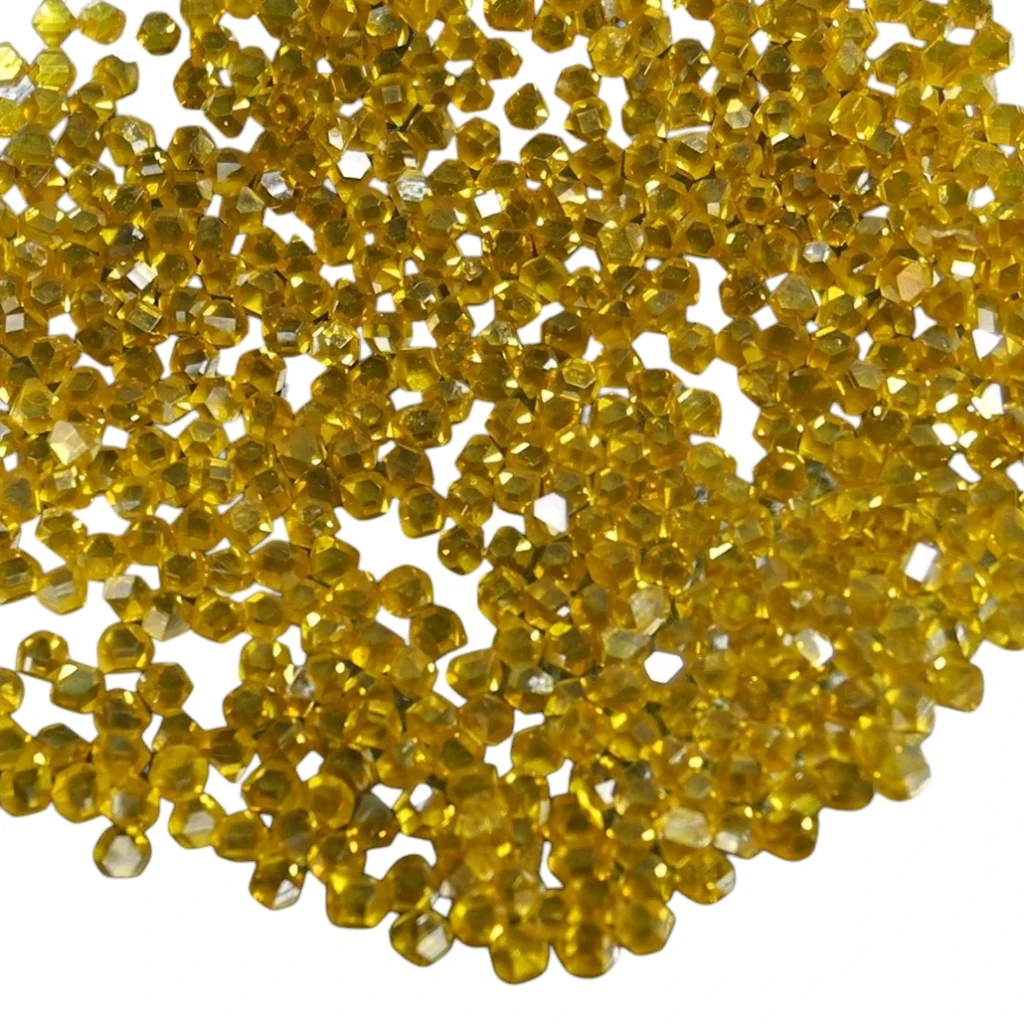
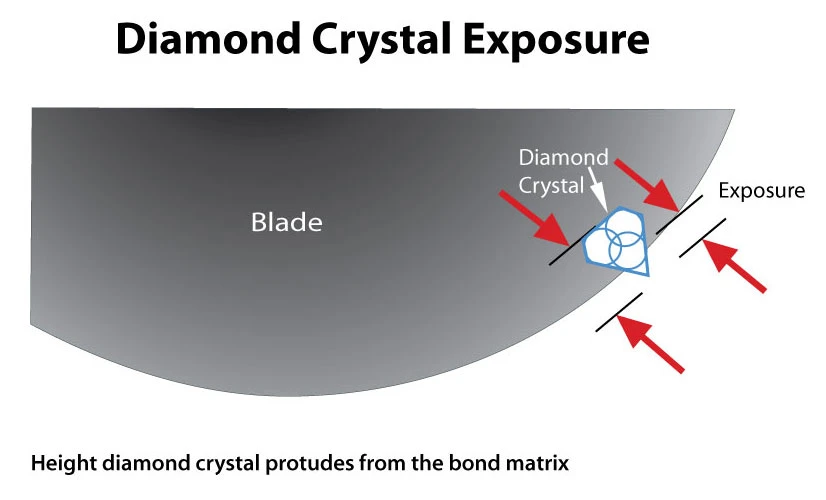
Diamond Crystal Exposure
Diamond crystal exposure, or protrusion, significantly affects the tool's cutting performance and material removal rate. The height to which a diamond crystal protrudes from the bond matrix influences how deeply each crystal can cut into the material, directly impacting the efficiency and speed of the cutting process. Greater diamond exposure generally means a more aggressive cut, as the diamond crystals have more surface area to interact with the material, allowing for faster removal rates. However, the effectiveness of this protrusion depends on the available horsepower and force applied during the cutting operation, as insufficient power can lead to inadequate performance or even tool damage.
Larger diamond crystals, combined with greater protrusion, enhance the material removal rate, making the cutting process more efficient for softer materials. This is because the larger surface area and greater contact with the workpiece allow the tool to break down and remove more material per pass. Consequently, for softer or less dense materials, such as asphalt, concrete, or certain composites, using larger diamond crystals maximizes removal efficiency while maintaining tool stability.
In contrast, when cutting harder materials, smaller diamond crystals are typically preferred. These smaller crystals produce a finer, more controlled cut and are better able to penetrate the harder material without causing excessive stress on the tool or material. Their reduced protrusion prevents the tool from becoming overly aggressive, which could lead to breakage, chipping, or overheating. For materials like ceramics, glass, or certain metals, where precision and surface quality are critical, smaller diamond crystals are effective in maintaining cutting accuracy and surface integrity.
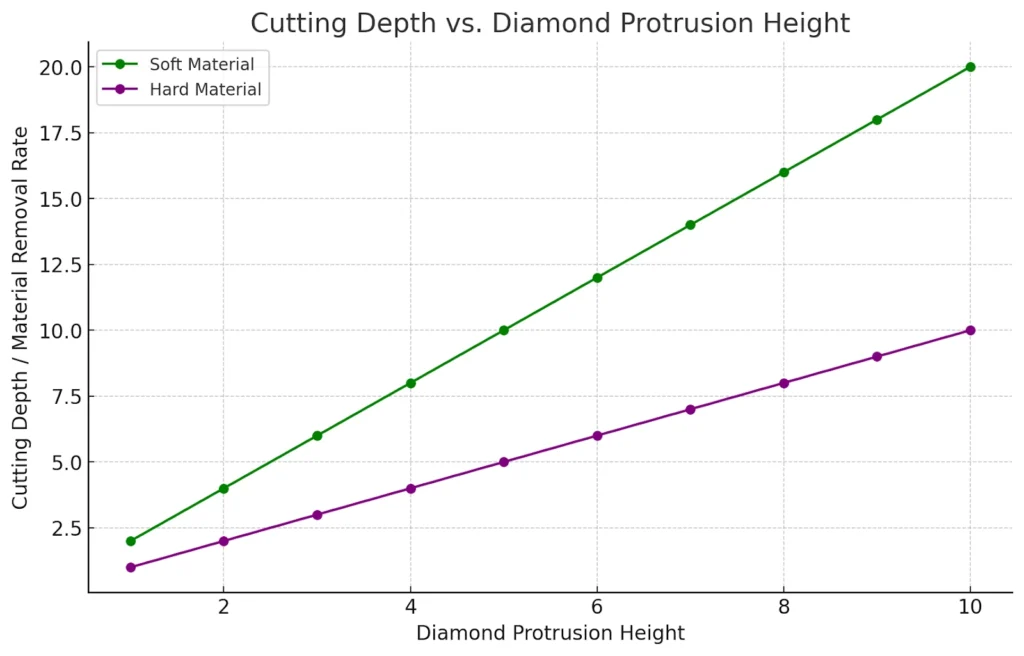
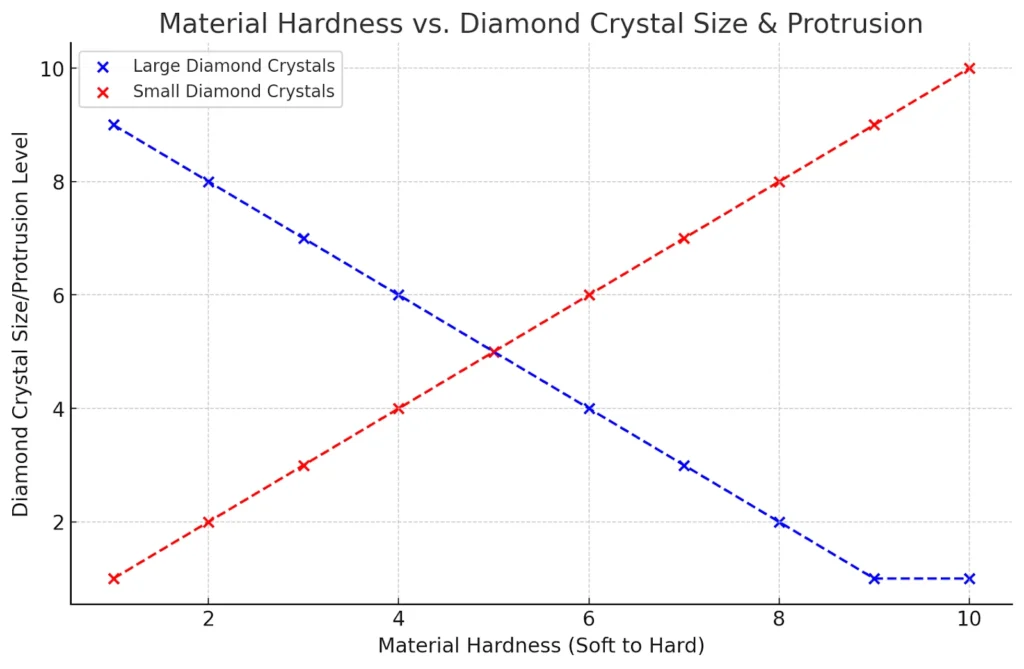
The balance of diamond exposure is also influenced by the bond matrix's ability to retain the diamond crystals. A bond that holds the diamonds too tightly can limit protrusion and cutting depth, reducing material removal rates. Conversely, a bond that allows too much protrusion may lead to premature diamond loss, as the crystals can break or dislodge under high cutting forces. Therefore, matching the bond wear rate with the desired level of diamond exposure is crucial to optimizing tool performance and achieving the best balance between cutting speed, tool life, and surface finish.
DIAMOND IMPACT STRENGTH
Diamond crystal impact strength plays a critical role in determining the effectiveness of diamond tools for various applications. It directly influences the tool’s ability to handle impact forces while cutting, grinding, or drilling materials of different hardness. A crystal with high impact strength can maintain its cutting action in very hard and dense materials, such as sapphire, without shattering or losing its cutting edges prematurely. In contrast, weaker diamond crystals are best suited for cutting softer materials like glass, where high strength is not required, and the risk of crystal damage is minimal.
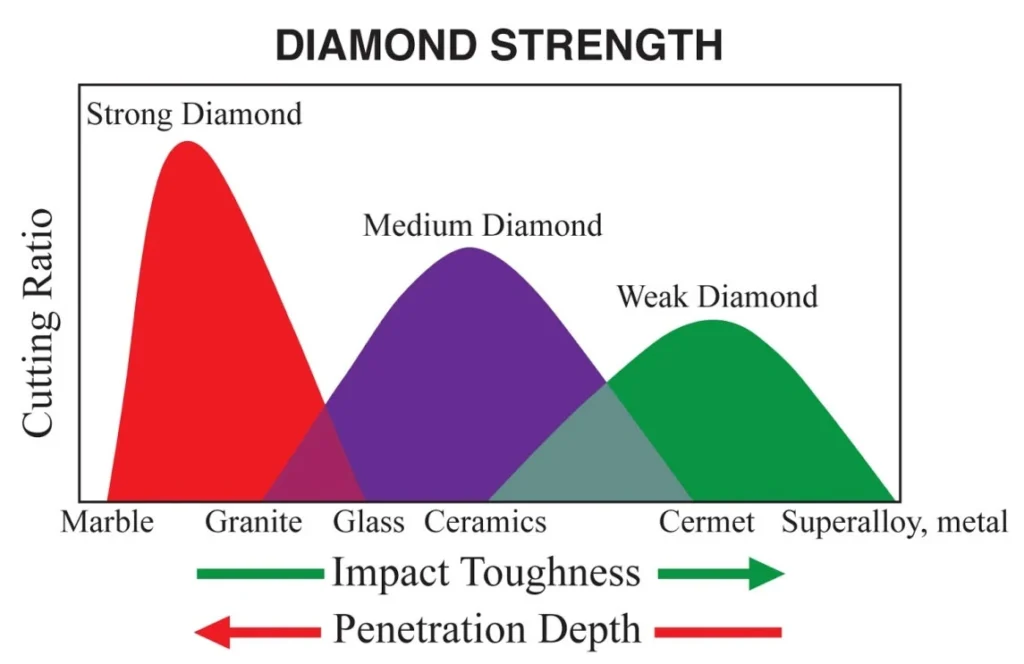
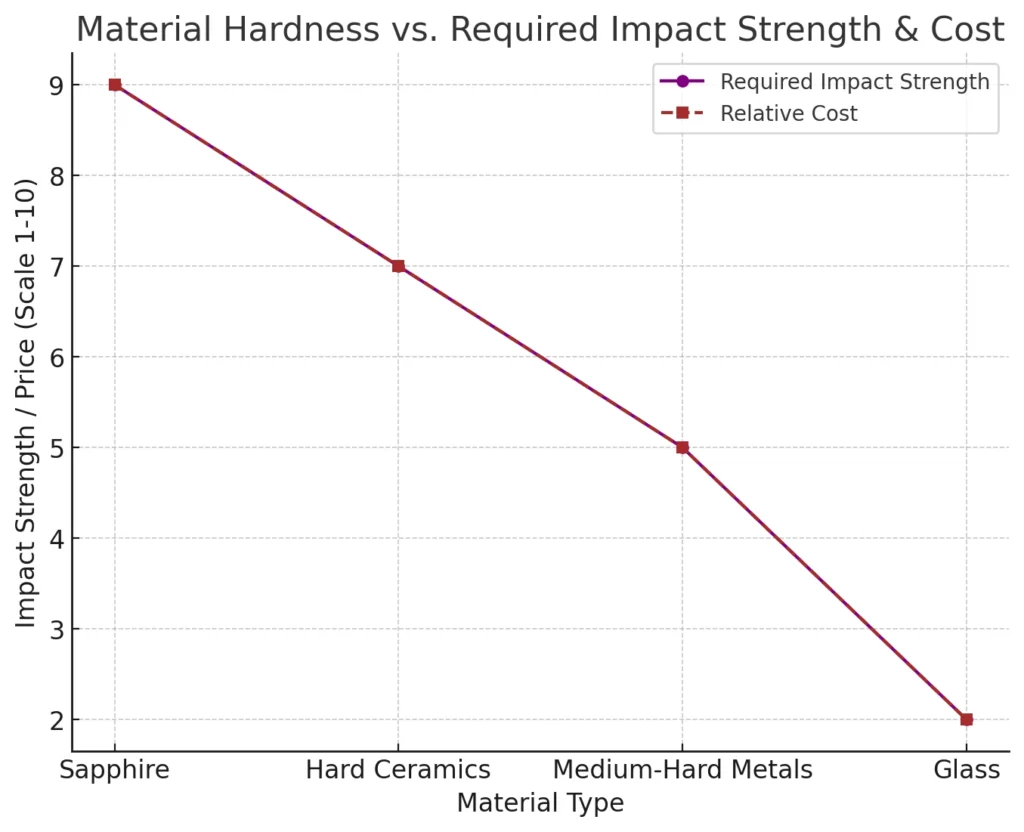
The relationship between impact strength and the cost of industrial diamond crystals is also significant. Stronger crystals, due to their enhanced durability and cutting efficiency, come at a higher price. However, it is crucial to balance the impact strength with the application needs, as overly strong crystals are not always ideal. For some materials, high impact strength does not necessarily translate to better performance, and in some cases, it may even hinder the cutting process by preventing the self-renewal of sharp cutting edges, thus reducing the tool's overall.
Impact strength is primarily determined by the external integrity of the diamond crystal, which includes factors like shape, surface smoothness, and structural quality. Euhedral crystals, which have well-formed crystallographic faces and regular geometric shapes, exhibit high impact strength compared to crystals with irregular or rough surfaces. Similarly, blocky crystals have better resistance to impact forces than elongated or needle-like crystals, as the compact shape allows for a more uniform distribution of cutting forces and prevents breakage.
Temperature is another critical factor influencing the impact strength of diamond crystals. Exposure to high temperatures can reduce impact strength by weakening the crystal structure, making it more prone to breakage. This reduction in impact strength due to temperature is often tied to the thermal stability (thermostability) of the diamond. High thermostability helps retain the integrity of the diamond crystal under heat generated by high-speed cutting, grinding, or drilling operations.
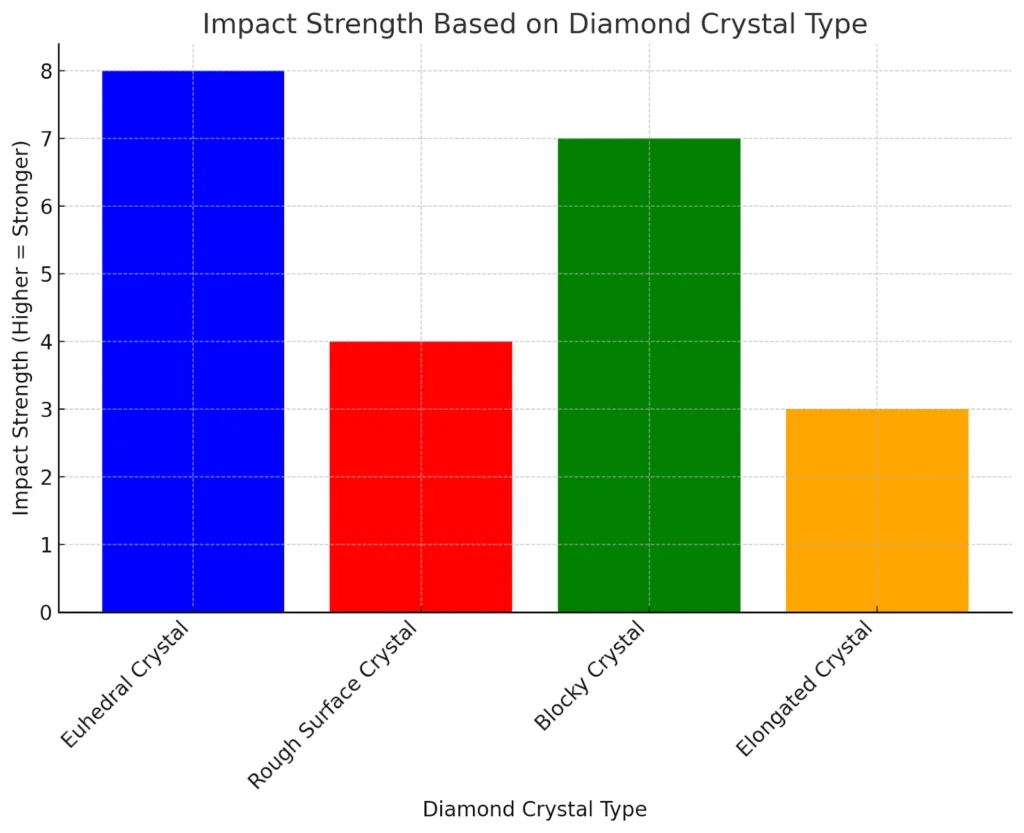
The impact strength of diamond crystals is quantitatively measured using the Toughness Index (TI). This metric assesses the diamond’s ability to resist fracturing under force, providing a benchmark for determining the suitability of a crystal for various applications. A higher TI indicates a greater ability to withstand impact and is generally favored for cutting harder, more abrasive materials. Conversely, a lower TI suggests the crystal is better suited for softer materials where high impact forces are not encountered, and a self-renewing cutting edge is desired for optimal performance.
In practice, choosing the right diamond crystal for a specific application involves a careful balance of impact strength, cutting requirements, and cost. For applications involving ultra-hard materials like ceramics or superalloys, diamonds with higher impact strength are beneficial to maintain efficient cutting and tool longevity. For softer materials requiring precision or delicate handling, weaker diamonds with lower impact strength and a higher rate of micro-chipping may be more appropriate to ensure continuous sharpness and reduce the risk of glazing or tool overheating.
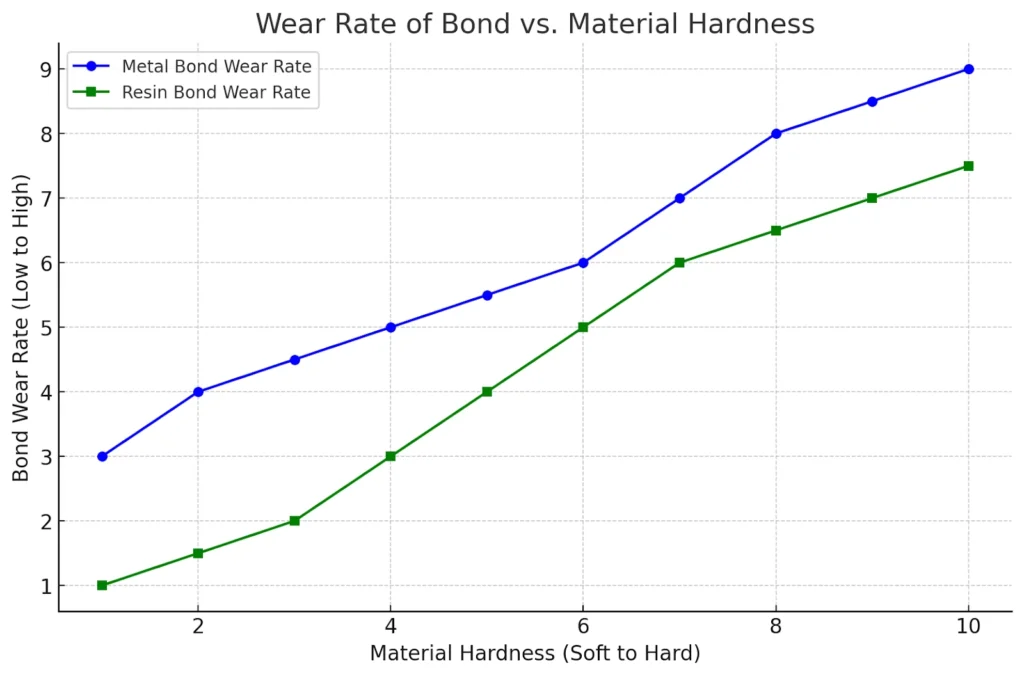
BOND WEAR RESISTANCE
The wear resistance of the bond matrix is a critical factor in the performance and longevity of diamond tools. This wear resistance must align closely with the abrasiveness of the material being cut to achieve efficient cutting and prevent premature diamond loss. The bond matrix is responsible for holding the diamond crystals in place, allowing them to cut effectively while ensuring they are sufficiently exposed without falling out too early. A balance is essential: if the bond is too soft, it wears down faster than the diamond crystals, leading to premature pull-out of the diamonds. On the other hand, if the bond is too hard and wear-resistant, it may hold the diamond crystals so tightly that they are unable to renew their cutting edges, leading to glazing over and a loss of cutting efficiency.
When cutting hard, dense, and brittle materials, such as ceramics, stone, or certain metals, the bond matrix typically wears down slowly. This is due to the minimal amount of material debris generated during the cutting process, which often appears as a fine powder. Such materials do not provide enough abrasive action to break down the bond quickly, which can result in the diamond crystals becoming polished or "glazed." In this state, the diamond is no longer cutting effectively because the worn surfaces of the crystals are no longer sharp, leading to increased friction, heat generation, and reduced cutting speed. For these applications, a softer bond is often preferred to ensure that the diamond crystals remain sufficiently exposed and can renew their sharp cutting edges through micro-chipping.
Conversely, when cutting softer, gummy, gritty, or open-textured materials like asphalt, concrete, or some composites, the bond matrix experiences a faster wear rate. The cutting process produces a large quantity of coarse, blocky debris that is more abrasive to the bond. This aggressive material removal action can quickly break down the bond matrix, exposing new diamond crystals for continuous cutting. However, if the bond is too soft, it will erode too quickly, leading to premature loss of the diamond crystals before they have been fully utilized, reducing tool life and efficiency. In these cases, a harder bond with greater wear resistance is necessary to match the abrasiveness of the material, prolonging tool life and ensuring consistent performance.
Matching Bond Wear to Material Properties
Optimizing bond wear resistance involves carefully matching the bond’s characteristics to the material being cut and the cutting conditions. The goal is to achieve a balanced wear rate between the diamond crystals and the bond matrix. This ensures that as the diamonds are worn down from cutting, the bond also wears at a controlled rate, allowing fresh diamonds to protrude and renew their cutting action without premature loss. Several key considerations influence this balance:
The choice between a soft or hard bond depends on the abrasiveness of the material. A soft bond wears down faster, exposing more diamonds and renewing cutting edges quickly, which is ideal for hard and dense materials where glazing is a concern. A hard bond provides greater wear resistance and is suitable for soft, abrasive materials that would otherwise erode a softer bond too quickly.
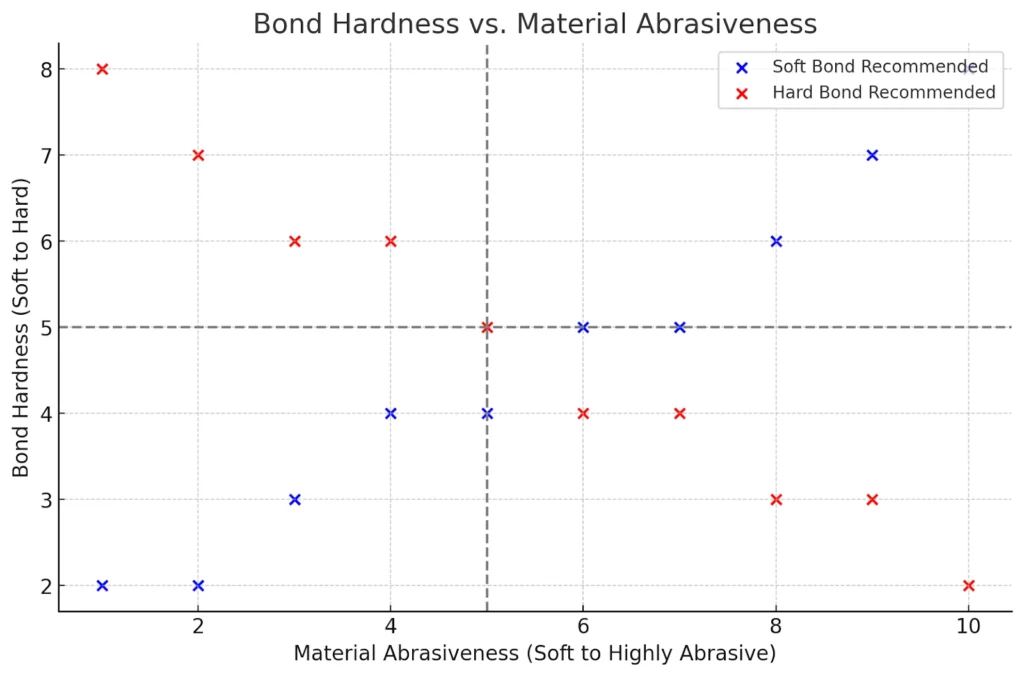
Bond Composition and Structure: The materials used to create the bond matrix—often metals, resins, or ceramics—determine its wear properties. The structure and density of the bond also play a role in how it wears down in response to the cutting action. For example, metal bonds tend to be more wear-resistant and are used for demanding applications, while resin bonds can be softer and are often used for smoother finishes or delicate materials.
Material Debris and Cutting Behavior: The type and size of debris generated during cutting significantly affect bond wear. Hard, brittle materials produce fine powder-like debris that does not aggressively wear down the bond, requiring the bond to be softer to maintain efficient cutting. On the other hand, soft, gritty, or gummy materials produce larger, coarser debris that quickly erodes the bond matrix, necessitating a harder, wear-resistant bond to withstand the abrasive action.
Cutting Parameters and Environment: Cutting speed (RPM), pressure, coolant use, and feed rate also impact bond wear. Higher speeds and greater cutting pressures can accelerate bond wear, particularly if the material is highly abrasive. Adequate coolant flow helps to reduce heat buildup, which can soften the bond and accelerate wear. Therefore, optimizing these parameters is crucial for achieving the desired wear balance and extending tool life.
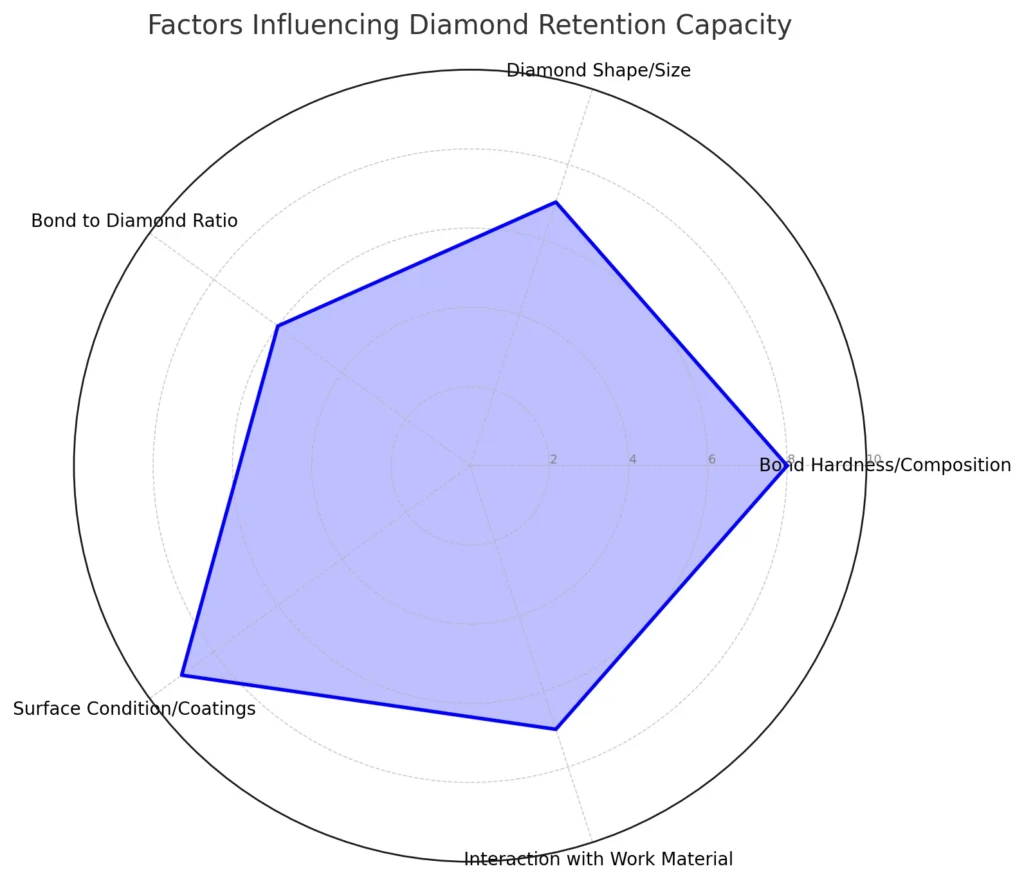
DIAMOND CRYSTAL WEAR MECHANISM
Diamond retention capacity is a critical function of the bond matrix, second only to the diamond's ability to cut effectively. The primary role of the bond matrix is to securely anchor diamond crystals within the tool, ensuring they remain stable and effective throughout the cutting, drilling, or grinding process. The ability to retain diamond crystals properly directly influences the tool's performance, efficiency, and longevity.
An optimal bond matrix is designed to hold diamond crystals firmly in place while simultaneously allowing controlled exposure to maintain the cutting action. The matrix must strike a careful balance between securely gripping the diamond and gradually releasing it as the crystal becomes worn or dull. If the bond matrix does not retain the diamond effectively, premature pull-out or loss of the diamond can occur, leading to reduced cutting efficiency and shorter tool life. On the other hand, if the bond is too tight or does not wear properly, it can prevent sufficient diamond exposure, causing the tool to glaze over and significantly reduce cutting performance.
Key Factors Influencing Diamond Retention
1. Bond Hardness and Composition: The composition of the bond matrix greatly affects its retention capacity. Metal, resin, and vitrified bonds each have different retention properties. Harder bonds provide a firmer grip on the diamond, which is essential for high-impact cutting applications involving harder materials. Softer bonds are designed to wear down at a rate that allows continuous exposure of fresh diamonds. The choice of bond depends on the specific cutting requirements, material properties, and desired tool life.
2. Diamond Crystal Shape and Size: The shape and size of diamond crystals influence how well they are retained in the bond matrix. Coarser diamonds with well-defined crystal faces provide more surface area for the bond to grip, improving retention. Irregular or angular-shaped diamonds are often better retained because their structure creates a mechanical lock with the bond matrix. Fine diamond grits, used for precise or delicate cutting, require a bond that can securely hold the small crystals without premature loss while still exposing them adequately for effective cutting.
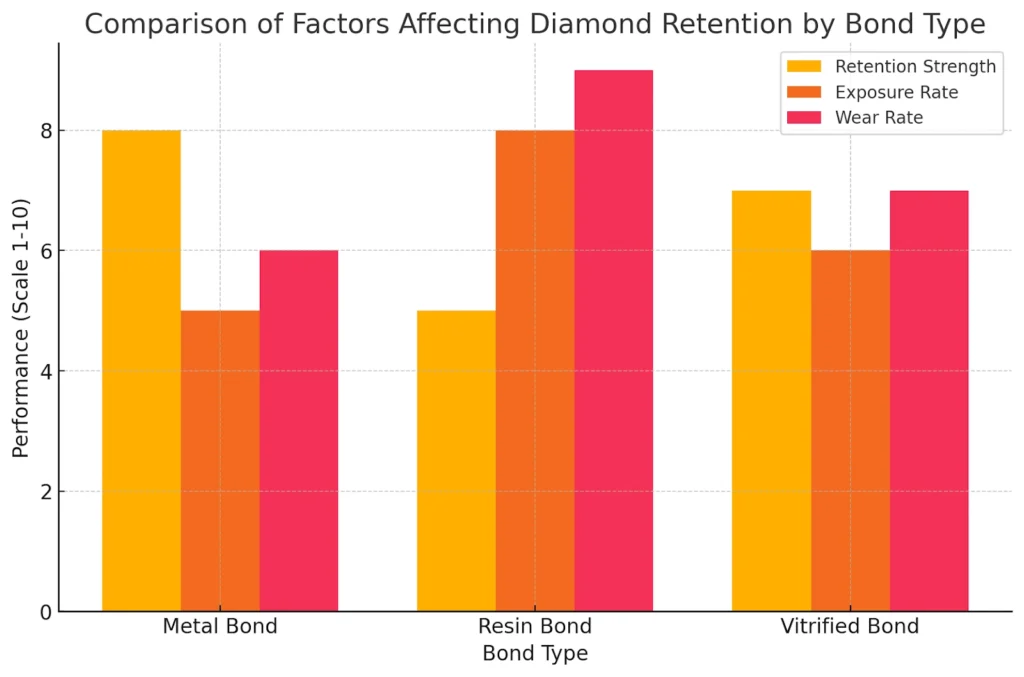
3. Bond to Diamond Ratio (Concentration): The concentration of diamonds within the bond matrix is a crucial factor in retention capacity. A high concentration of diamonds increases cutting efficiency, but it also requires the bond to manage the retention of many individual crystals effectively. A lower concentration means fewer diamonds in the matrix, which can improve retention but may reduce cutting speed. Achieving the optimal diamond concentration depends on the desired balance between cutting efficiency, tool life, and material type.
4. Surface Condition and Coatings: The surface condition of the diamond crystal plays a significant role in its retention. Diamond crystals with rougher surfaces or coatings, such as titanium, chromium, or other carbides, improve the bond’s ability to grip the diamond. The coating creates an intermediary layer that enhances adhesion to the bond and increases retention strength, reducing the likelihood of premature diamond loss. Smooth or highly polished diamond crystals may not bond as effectively, leading to quicker dislodgement under cutting forces.
5. Interaction with Work Material: The properties of the material being cut impact the bond’s ability to retain diamonds. Hard, dense materials exert high localized pressures on the diamond, potentially causing dislodgement if the bond is not strong enough. Conversely, softer materials create more abrasive wear on the bond itself, requiring a balance that allows for sufficient wear without premature diamond pull-out. Understanding the interplay between the work material and the bond matrix helps in designing tools with the right retention capacity.
DIAMOND STRENGTH
If a tough diamond crystal is used to cut hard material will either be broken or it will be knocked off the bond matrix, depending on bond matrix hardness in comparison to diamond crystal.
An overly strong diamond crystal will either be broken or lost, but an overly wear diamond crystal will be disintegrated too fast. For this reason diamond crystal strength must be adjusted to suit the impart force in such a way that micro chipping is the dominant mode of wear and occurs more slowly.
Diamond crystal wear mechanism is dependent on diamond strength. In order to optimize the cutting performance in both cutting ration and cutting speed, diamond crystal loss must be turned to micro chipping at the expensive of smashing and pullout/micro fracture.
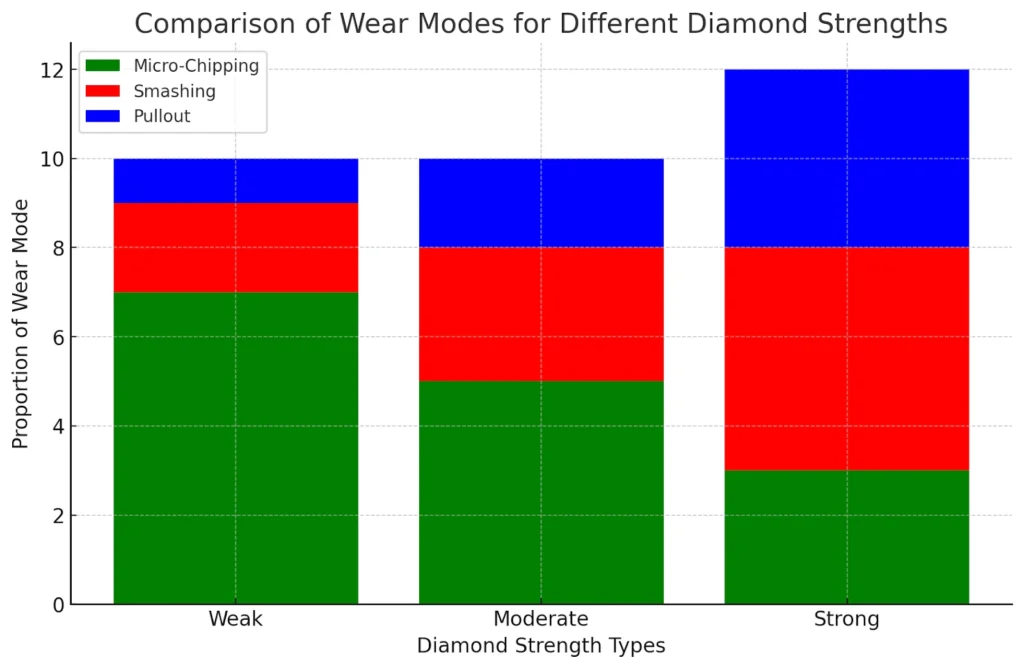
IF a diamond that is friable is embedded in a cushion like a resin bond matrix and used to cut very hard material. Friable diamond will provide best level of performance at smaller cutting depth. With deeper cutting depth the diamond crystal will be smashed quickly, yet with smaller cutting depth this diamond will stay sharp by forming microchips gradually. In this matter the shaper diamond crystals can penetrate the hard material and cut it in most efficient mater, by utilizing electrical energy. Diamond friability will increase with increasing toughness of the material. Here is each diamond crystal can cover a certain range of toughness. Diamond crystal will develop a wear flat and become too dull to penetrate
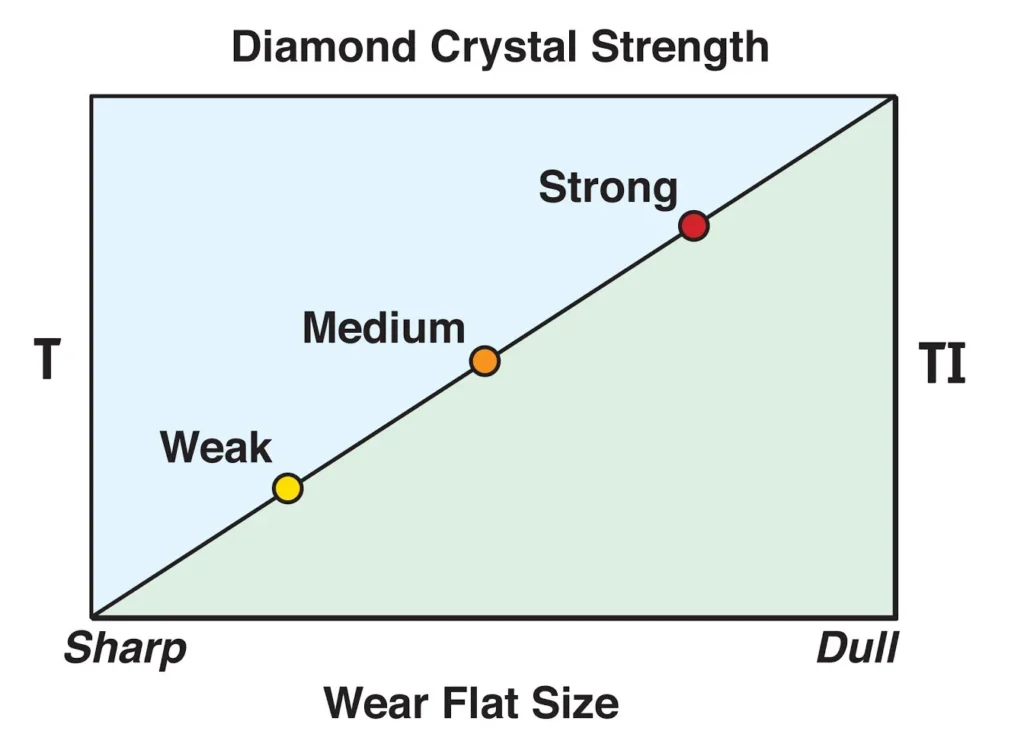
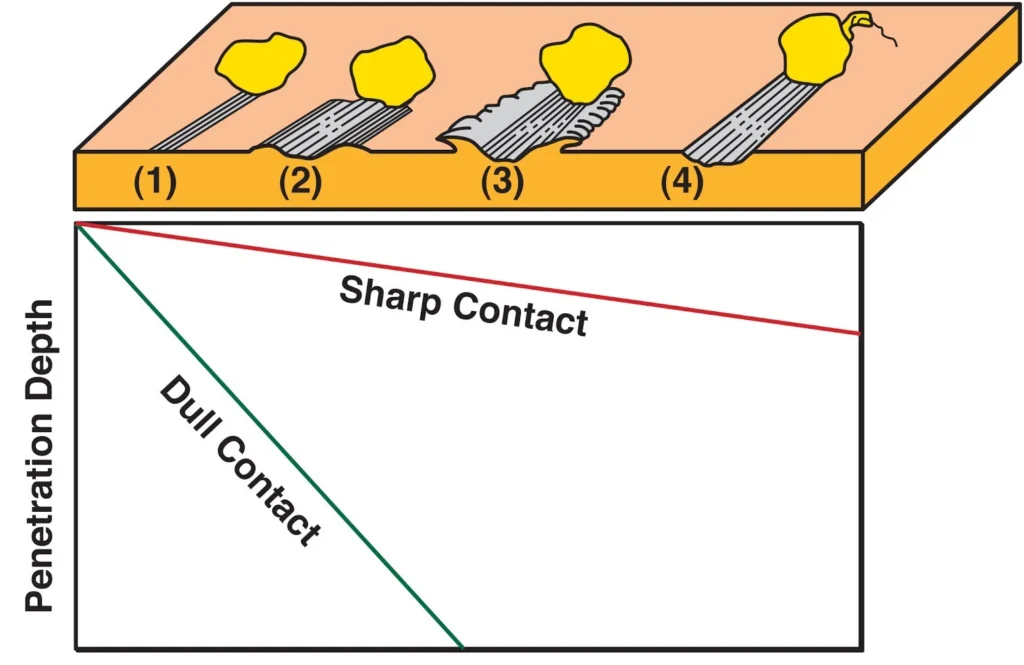
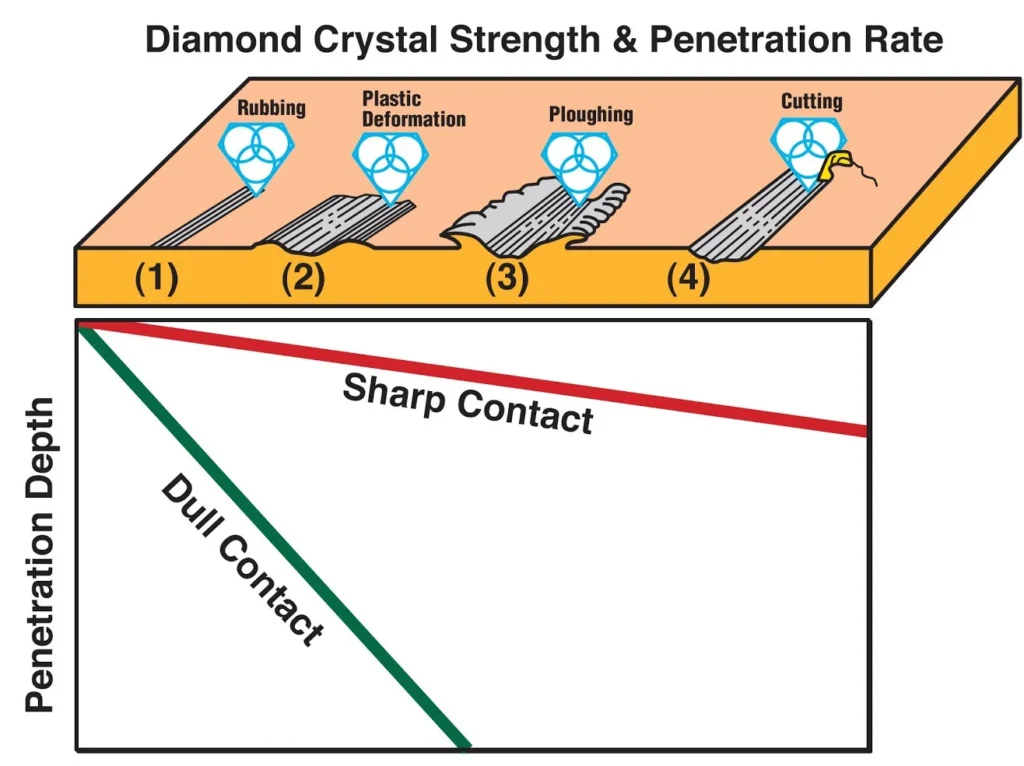
Diamond crystal penetration depth will determine its level of functionality and utilization, and hence the level of the diamond tool performance. The optimal diamond crystal penetration depth is to allow the diamond crystal to microchip gradually. However the penetration depth will depend on the properties of both diamond crystal and material being cut. Diamond crystal penetration depth will be shallow with weaker diamond, specially when working with very hard material such as advanced ceramics, and deeper with strong diamond crystal when cutting through softer materials such as glass or tile.
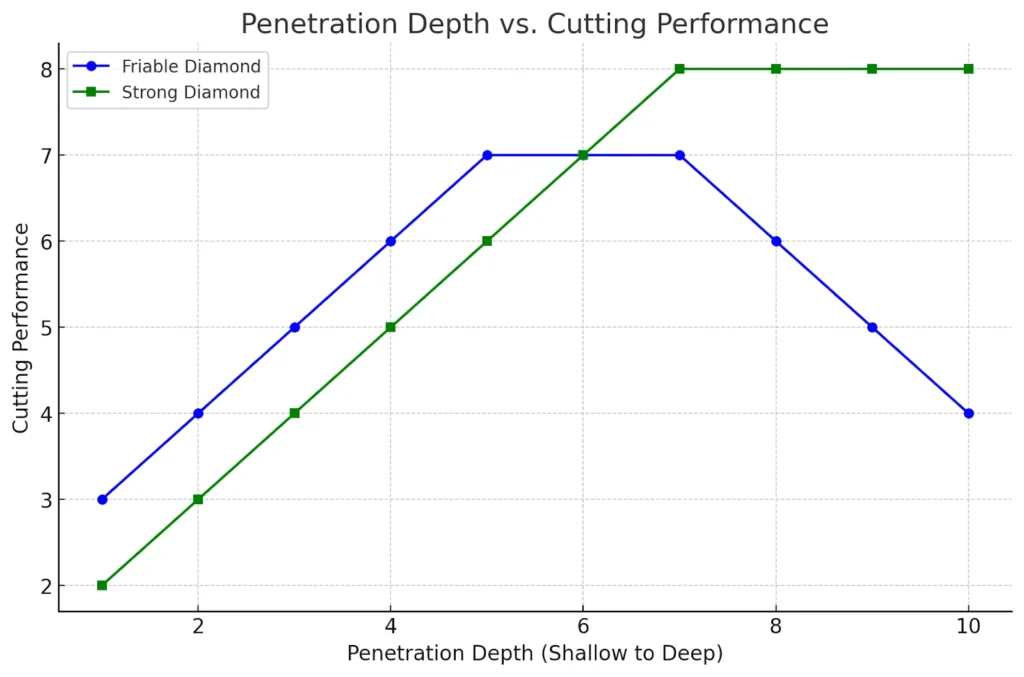
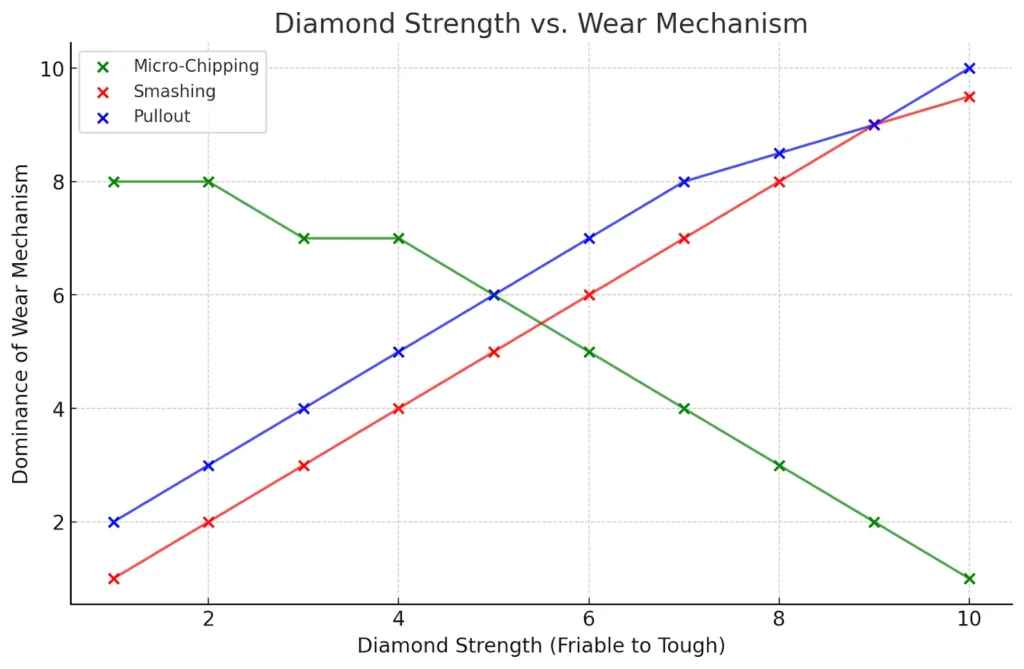
Diamond is the hardest material known to man kind. So it can be used to cut into any type of material. Diamond crystal can cut into any Soft and brittle materials such as glass or soft stone, without being broken or pulled out. On the contrary for hard and dense materials the diamond crystal must sharpen itself by forming smaller microchips. This will reduce the contact pressure between diamond crystal and material, allowing diamond crystal to penetrate freely.
DIAMOND CRYSTAL WEAR MECHANISM
The capability of the diamond crystal to penetrate into the material, will depend on the contact pressure (feed rate) amount of force applied. With higher amount of force applied the diamond crystal will increase its penetration depth. At first the material at point of contact will be deformed, then gradually broken. This is the definition of diamond grinding action. The rate at which the diamond crystal penetrates will increase rapidly with the development of the wear flats.
A sharp diamond crystal can cut easily, however diamond crystal with large wear flat faces, will increase amount of resistance force between the material it comes in contact.
The challenge in this scenario is the kinetic energy will be distributed more towards heat generation then to cutting the material. As a result not only the grinding sped will be reduced, but the diamond crystal may fail due to large impact force at high temperature. A diamond crystal that is too strong will either be broken or lost but a very weak diamond crystal will be smashed quickly. For this reason diamond strength must be tailored to suit the impart force to the extent where micro chipping is the dominant mode of wear in a controlled matter.
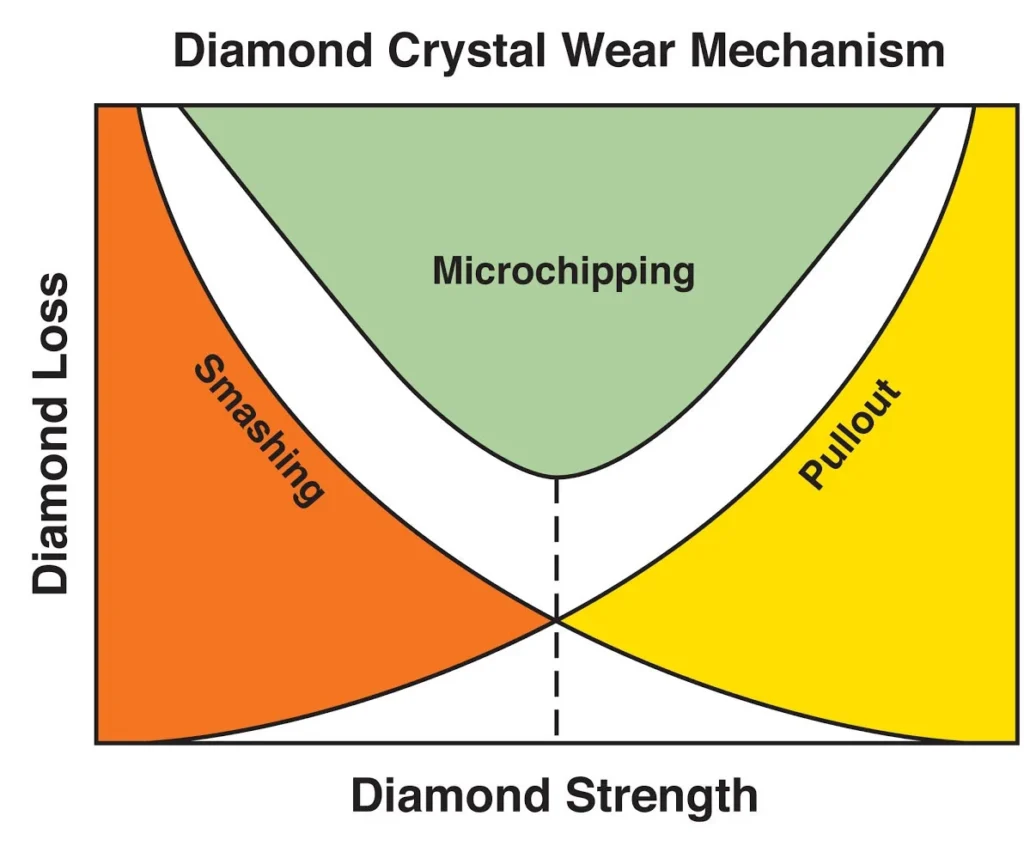
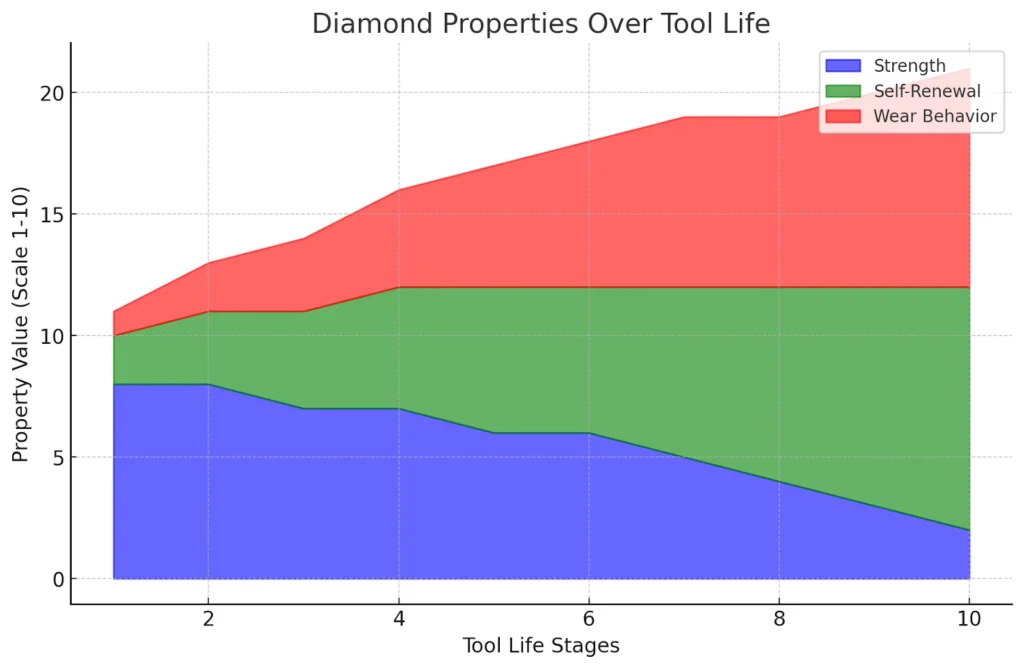
DIAMOND CRYSTAL SELECTION
Diamond crystal strength is a balance between durability and self-renewal. The diamond must be strong enough to withstand the impact forces of cutting but not so strong that it resists micro-chipping. Micro-chipping is the ideal wear mechanism, as it allows the diamond to maintain sharp cutting edges. If the diamond is too strong, it develops a smooth wear flat, which reduces cutting efficiency. Conversely, if it is too weak, it breaks down too quickly. Therefore, optimal diamond strength must allow for controlled micro-chipping after the diamond has worn down.
Industrial diamond crystals typically have imperfections like surface roughness, metal inclusions, and micro-fractures. While these defects can weaken the diamond’s thermal stability, they play a crucial role in enhancing cutting efficiency. Specifically, metal inclusions can encourage self-sharpening by increasing contact forces between the diamond and the work material. This controlled distribution of defects allows the diamond to form sharp edges through micro-chipping, which is particularly important when cutting ultra-hard, dense materials.
The bond matrix and cutting conditions must match the diamond’s properties to support efficient chipping without premature loss. This ensures that the diamond is optimally retained within the tool, allowing it to cut effectively for the duration of its life. By maintaining a careful balance between diamond strength, defect management, and proper wear behavior, tools can achieve maximum efficiency, extended life, and reliable performance across various industrial applications, from heavy-duty sawing to precision grinding.
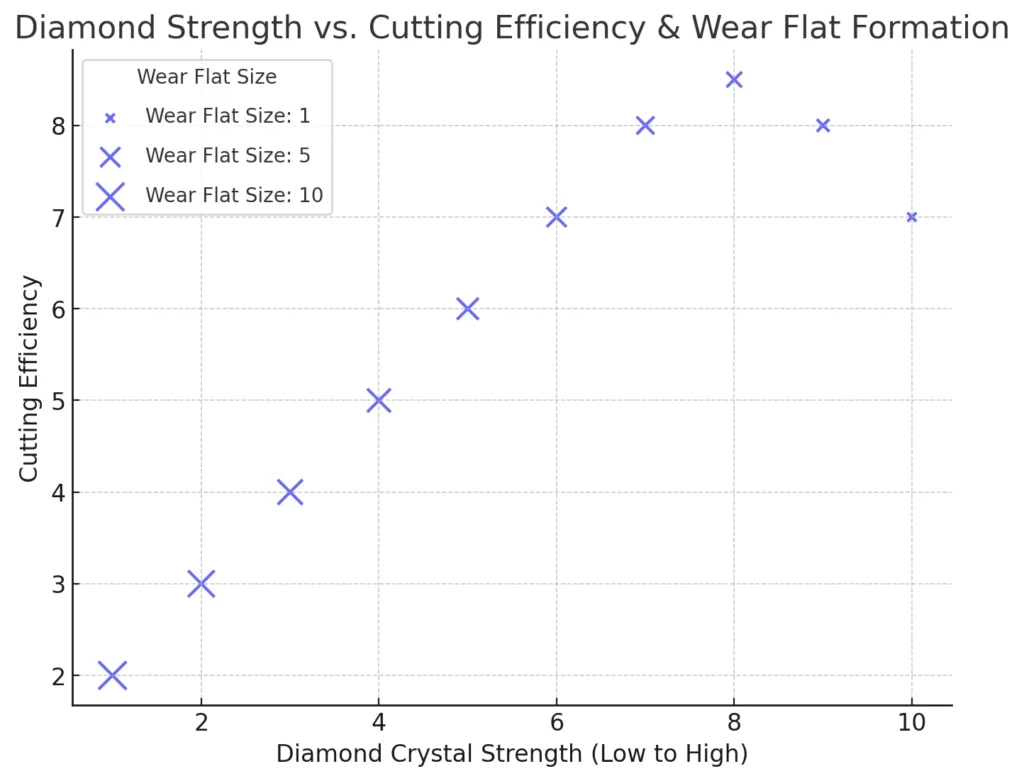
Diamond crystal surface condition
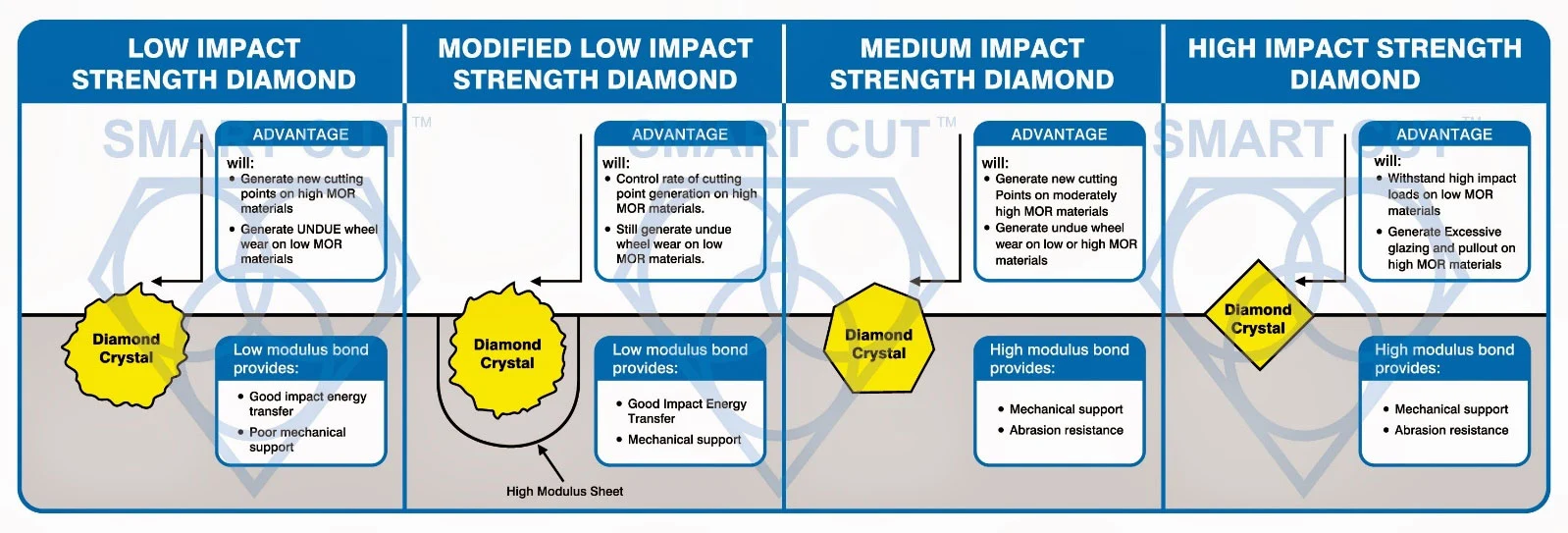
Typically the diamond crystals used for industrial diamond tool application have many different types of defects such as surface roughness, metal inclusions, and micro fractures. In many cases, the less defined the diamond crystal form, the more metal inclusions and other defects in can have. These types of diamond crystals are weaker and are less thermally stable. As metal inclusions present in the diamond crystal can waken it at high temperatures. Not always is this an undesirable outcome. In some cases properly controlled distribution of metal inclusions can be used to create sharp cutting edges that are formed by increasing contact force with the material due to the dullness of the cutting tip. This shelf sharpening characteristic is very important for a number of applications, specially for ultra hard and dens materials.
DIAMOND GRIT SIZES
Both natural and synthetic (man made) diamond are classified into two board bands of grit sizes. These are frequently called "saw" and "wheel" grits. Each grit size can be narrowed down to a band, which is defined by tow sieve aperture sizes (top and bottom).. Many diamond grit sizes are also characterized by particle per carat count. This guarantees the number of particles per carat to straight tolerance for each mesh size, helping insure high degree of consistency.
different industries, applications and types of tools used different diamond grit sizes. Below is an application example relative to grit size range:
20/30 Mesh
Diamond sawing and drilling of very abrasive materials. Such as sandstone, concrete, asphalt. Drilling of Reinforced concrete, frame sawing of abrasive sandstone
30/40 mesh
Diamond sawing and drilling of stone, concrete, reinforced concrete and asphalt. Frame sawing of abrasive sandstone
40/50 Mesh
Diamond sawing, drilling and milling of stone (granite, diorite, gabbro, less abrasive sandstone, limestone, dolomite, marble), concrete and refractoriness; wire sawing of stone and construction materials; calibrating of stone slabs
50/60 Mesh
Diamond sawing, drilling and milling of stone (granite, diorite, gabbro, less abrasive sandstone, limestone, dolomite, marble), concrete and refractoriness; wire sawing of stone and construction materials; calibrating of stone slabs
60/80 Mesh
Diamond sawing, drilling and milling of glass, calibrating of ceramic tiles Coarser diamond grit sizes typically protrude more for supporting bond matrix so they can cut into the material faster. This results in greater clearance and enables easier swarf ejection when larger material has to be removed per tool revolution.
80/100 Mesh
80/100 mesh is commonly used for cutting lapidary materials and various types of glass, such as soda-lime and borosilicate glass. The coarser grit size allows for fast cutting speeds and efficient material removal. It provides greater clearance, facilitating easier swarf ejection when working with thicker materials. This grit size is often used for applications that require rapid cutting and aggressive stock removal, making it ideal for rough-cutting operations where surface finish is not the primary concern.
100/120 Mesh
This grit size is also suitable for lapidary materials and glass cutting, offering a slightly finer cut compared to 80/100 mesh. It maintains a balance between cutting speed and surface quality, allowing for a better finish while still providing efficient cutting performance. It is commonly used in applications requiring controlled cutting of glass, ceramics, and similar hard materials where both speed and surface quality are considerations.
140/170 Mesh
140/170 mesh grit is designed for cutting and milling advanced ceramics. The finer grit size compared to 100/120 mesh provides a smoother surface finish and is particularly useful for materials that require precise cuts and minimal chipping. This grit is suitable for a range of advanced ceramics, including alumina, zirconia, and silicon carbide, which are typically used in high-tech industries like electronics, aerospace, and medical devices.
180/200 Mesh
This mesh size is slightly finer than 140/170 mesh and is used for similar applications. It provides a smoother finish while maintaining efficient cutting capabilities. The smaller grit size is effective for precision operations in cutting advanced ceramics and materials requiring greater control over the surface finish. It is often used in applications where a clean cut with minimal chipping and an accurate surface profile is required.
200/230 Mesh
The 200/230 grit size is suitable for precise cutting and milling of advanced ceramics, as well as applications in glass where a finer finish is needed. This size is excellent for finishing operations or cutting delicate materials that require a high degree of accuracy and minimal surface damage. It is also used in wire sawing of hard materials and can provide a controlled cut with a smoother surface than coarser grits.
220 Mesh
220 mesh is particularly effective for cutting optical glass and fine ceramics. Its finer particle size allows for a high-quality surface finish with minimal damage to the edges or surface of the workpiece. This grit is crucial in applications where surface integrity is paramount, such as in optics manufacturing, where precision and smoothness are critical. It ensures a delicate and controlled cut, reducing chipping and improving the overall quality of the finished product.
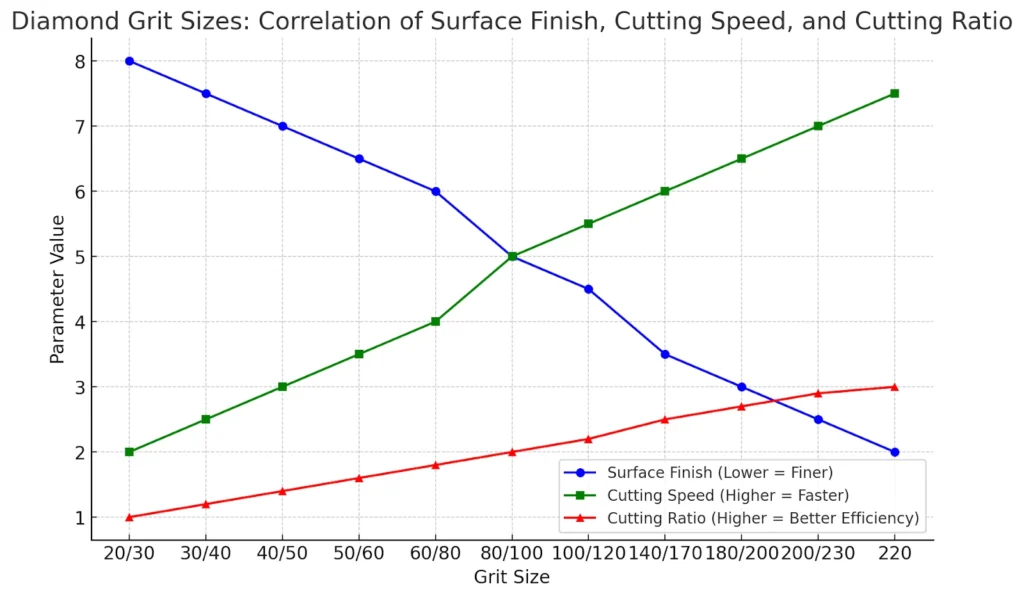
Grit Size |
Applications |
---|---|
20/30 Mesh |
Diamond sawing and drilling of very abrasive materials (sandstone, concrete, asphalt). Drilling of reinforced concrete, frame sawing of abrasive sandstone. |
30/40 Mesh |
Diamond sawing and drilling of stone, concrete, reinforced concrete, and asphalt. Frame sawing of abrasive sandstone. |
40/50 Mesh |
Diamond sawing, drilling, and milling of stone (granite, diorite, gabbro, less abrasive sandstone, limestone, dolomite, marble), concrete, and refractories. Wire sawing of stone and construction materials; calibrating of stone slabs. |
50/60 Mesh |
Diamond sawing, drilling, and milling of stone (granite, diorite, gabbro, less abrasive sandstone, limestone, dolomite, marble), concrete, and refractories. Wire sawing of stone and construction materials; calibrating of stone slabs. |
60/80 Mesh |
Diamond sawing, drilling, and milling of glass; calibrating of ceramic tiles. |
80/100 Mesh |
Cutting lapidary materials and glass (soda-lime, borosilicate). Fast cutting speeds, efficient material removal, good swarf ejection. Ideal for rough-cutting operations. |
100/120 Mesh |
Lapidary materials and glass cutting, offering finer cuts with balance between speed and surface quality. Used for controlled cutting of glass, ceramics, and hard materials. |
140/170 Mesh |
Designed for cutting and milling advanced ceramics (alumina, zirconia, silicon carbide). Provides smoother surface finish, useful for precise cuts with minimal chipping. |
180/200 Mesh |
Finer than 140/170 mesh, used for precision cutting of advanced ceramics. Offers smooth finish and controlled cutting for clean, accurate profiles. |
200/230 Mesh |
Suitable for precise cutting and milling of advanced ceramics and glass. Ideal for finishing operations requiring high accuracy and minimal surface damage. |
220 Mesh |
Effective for cutting optical glass and fine ceramics. Ensures high-quality surface finish with minimal damage. Used in optics manufacturing for precision cuts. |
Coarser diamond grit sizes typically protrude more for supporting bond matrix so they can cut into the material faster. This results in greater clearance and enables easier swarf ejection when larger material has to be removed per tool revolution. Diamond grit size selecting is a compromise between cutting speed (quantity) and surface finish (quality). Optimum results will be found where maximum material cutting rate at minimal acceptable surface finish.
Diamond grit size selecting is a compromise between cutting speed (quantity) and surface finish (quality). Optimum results will be found where maximum material cutting rate at minimal acceptable surface finish.
For a number of applications, optimum results cannot be achieved within a single step. In this case two or several steps will be needed. First material will be ground, and then polished by finer diamond grit sizes until desired surface finish has been achieved. Coarser diamond grit sizes also tend to last longer.
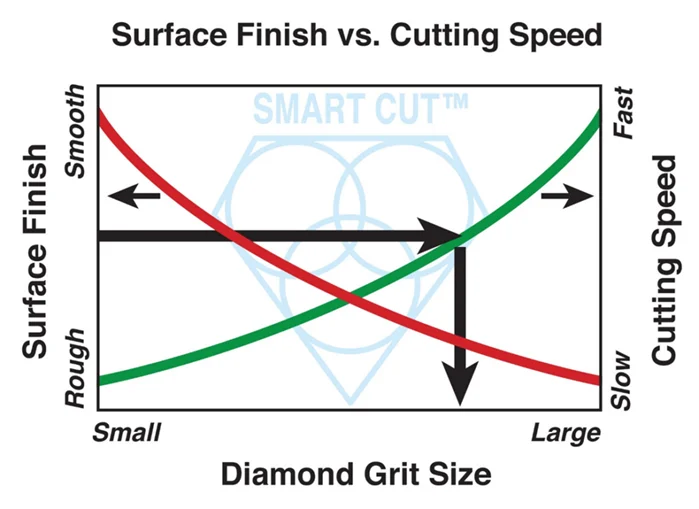
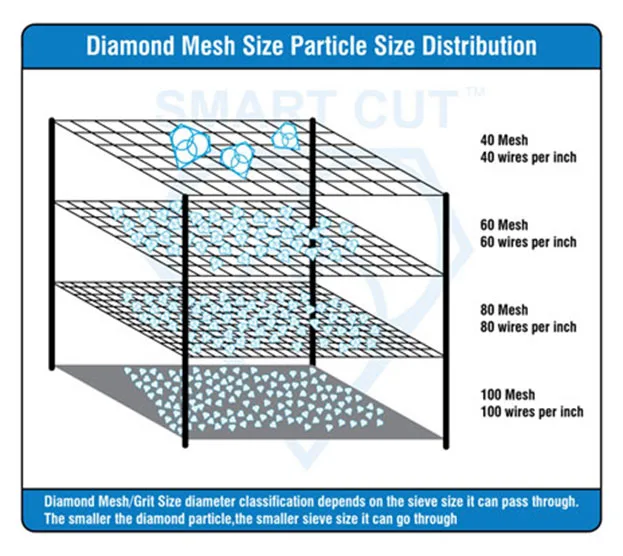
How Diamond Grit Size is Classified
Diamond Crystal is first classified by size. To determine each crystals size, sieving process is implemented. A sieve is made from cross weaving of metal wires (usually stainless steel) that have very consistent shape and size square holes. Diamond crystals are bounced around these holes within pre determined amount of time in order to separate them in two patches. Those that passed the sieve (went through) and those that were left behind on the screen.
The sieve holes are determined by specification set forth by either American or European standard. American use ANSI (American Nation Standards Institute) Specifications, and their European counterparts following FEPA. The American system sets the standard for sieving based on number of holes per inch of screen wire, this is what is referred to as mesh size.
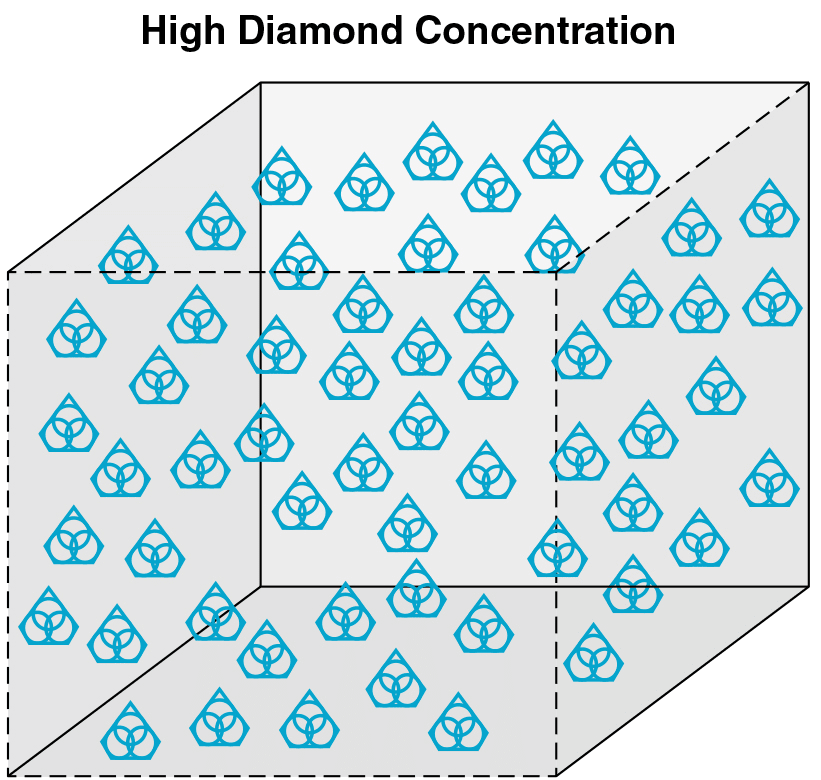
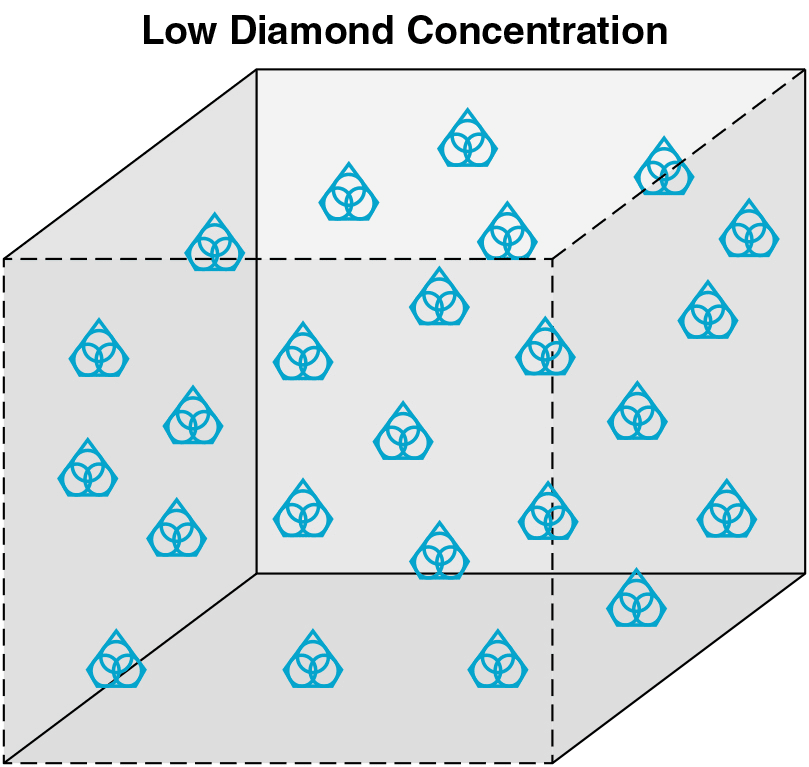
In many applications the life of the diamond tool is primarily controlled by amount of diamond crystal in the bon matrix. This amount is called “diamond concentration”. Diamond concentration can be defined as volume fraction of diamond crystal in bond matrix. Hence, the higher the diamond concentration a diamond tool has, the longer its life time. The trade off is slower cutting speeds, due close spacing of diamond crystals in the bond. The level of the diamond crystal exposure is reduced as well, possibly causing rubbing of bond matrix against material being cut. This side effect causes increase in temperature and burning of material or tool, or often both.
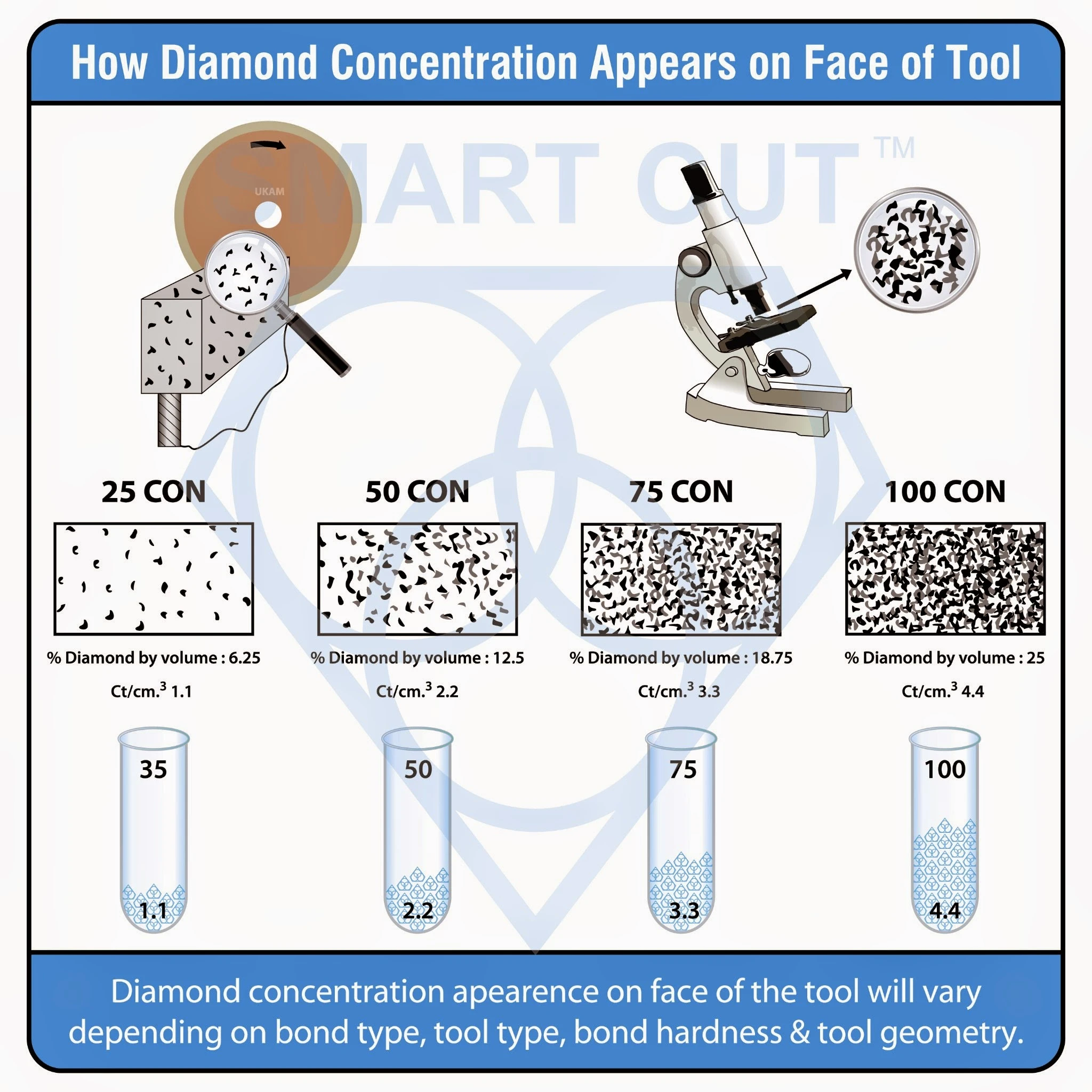
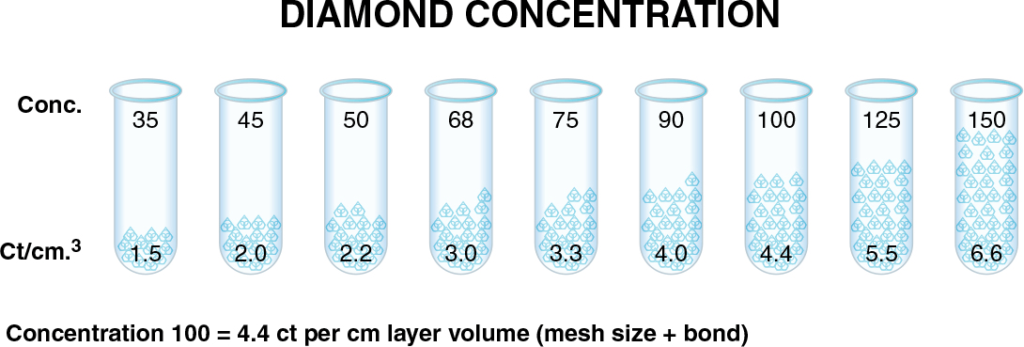
“Diamond concentration is determined by the slowest cutting speed that is acceptable for achieving certain objective”
low diamond concentration typically makes the diamond crystals highly vulnerable because of the increased impact force on the over exposed diamond crystal. As a result the diamond crystal is used too fast, causing the cutting speed to drop below acceptable level quickly. For this reason there is optimum diamond concentration to use in correlation to each diamond grit size.
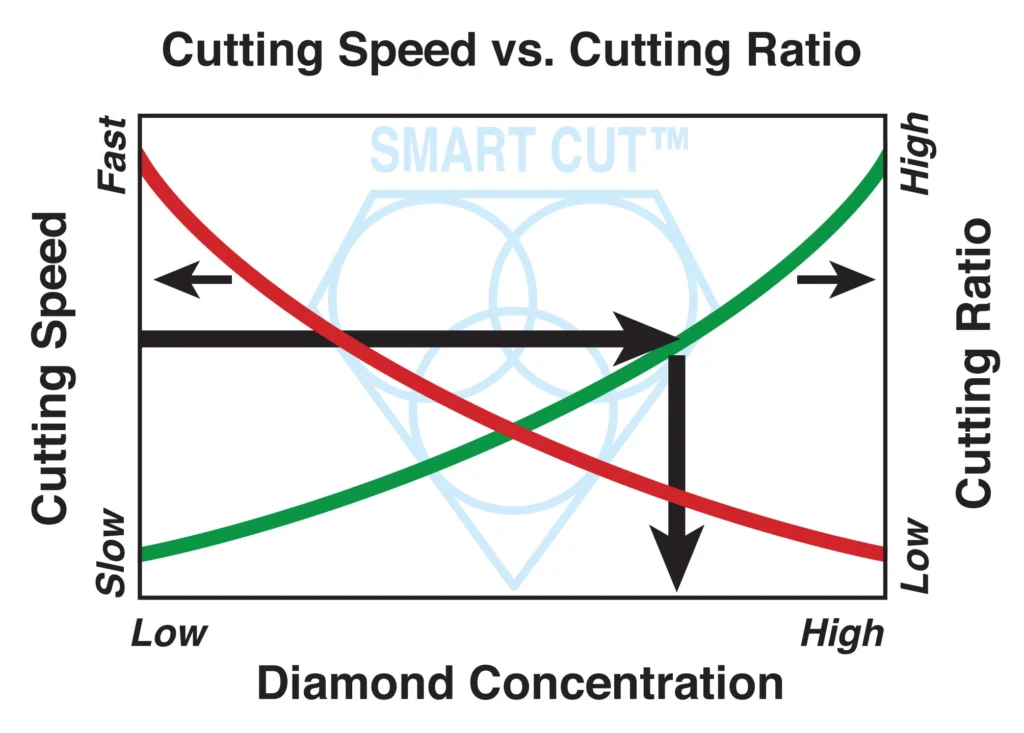
Achieving Optimum Diamond Tool Performance
Achieving optimum diamond tool performance requires a balance between efficiency, cost-effectiveness, and ease of application. The performance of a diamond tool is evaluated based on key factors such as cutting speed, tool life, and power consumption. These factors must work harmoniously to ensure that the diamond tool delivers high-quality results in the most cost-effective manner. However, it is not only the diamond tool itself that determines performance; the equipment and processes used must also align with the necessary cutting parameters to achieve the best results.
Several factors influence diamond tool performance, including diamond crystal strength, bond matrix hardness, and the properties of the material being cut. The diamond crystal's strength plays a pivotal role in determining the mode of wear or fracture. A diamond crystal that forms a "wear flat" (a smooth, polished surface on the diamond) during cutting is likely too strong for the application or the cutting conditions are too mild, leading to inefficient cutting.
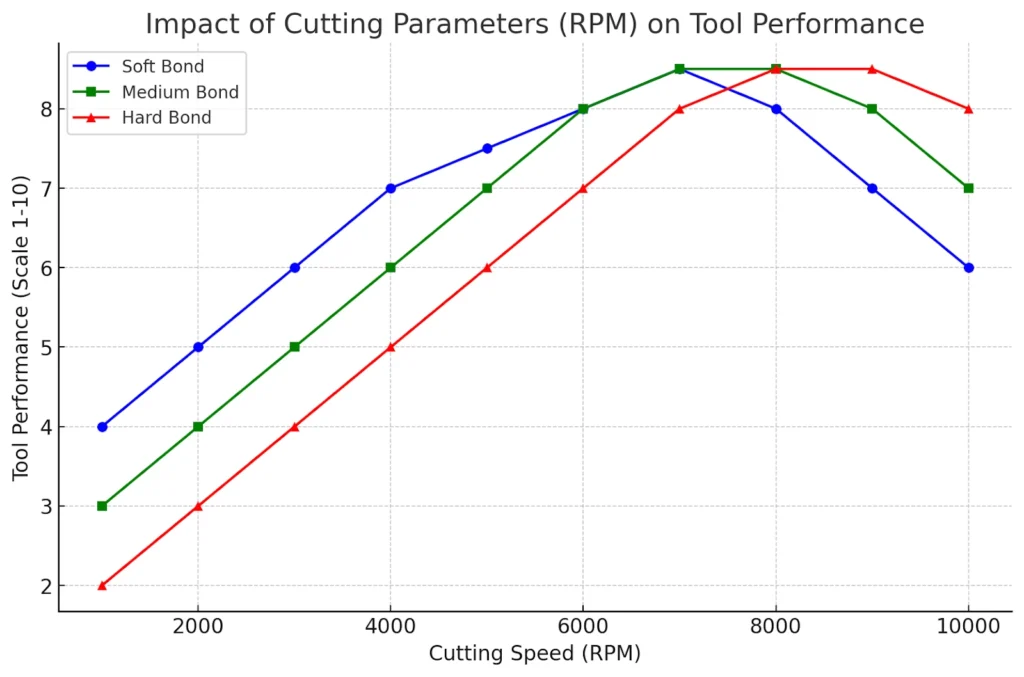
This lack of renewal in cutting edges results in increased friction, heat, and inefficient material removal. On the other hand, if the diamond crystal shatters easily, the diamond is too weak or the operational conditions are overly aggressive, leading to rapid breakdown and tool failure.
The optimal wear mode for diamond crystals is micro-chipping. In micro-chipping, the diamond crystal undergoes tiny fractures that renew the cutting edge, creating a sharp, jagged surface capable of efficiently removing material. This self-sharpening effect ensures that the cutting process remains aggressive and effective, allowing the tool to maintain high cutting speeds and produce cleaner, more precise cuts throughout its lifespan. Achieving this optimal wear mode requires proper balance between diamond strength, bond hardness, and process parameters.
Factors Influencing Optimum Performance
1. Diamond Crystal Strength and Fracture Behavior: The strength of the diamond crystal should match the demands of the application. If the diamond is too strong, it won’t micro-chip, resulting in reduced cutting efficiency. If it’s too weak, it will break down too rapidly, reducing tool life. Ideally, the diamond should have enough strength to cut through the material but not so much that it doesn’t micro-chip and renew its cutting edges. Understanding the wear behavior allows for adjustment of tool properties or cutting conditions to maintain optimal cutting performance.
2. Bond Matrix Hardness: The bond matrix holds the diamond crystals in place and supports their cutting action. The hardness of the bond matrix must be appropriate for the material being cut and the type of diamond used. A bond that is too hard may hold onto the diamond particles too long, preventing proper exposure of fresh crystals, while a bond that is too soft may release diamonds prematurely, resulting in inefficient cutting and reduced tool life. For optimum performance, the bond matrix should wear at a rate that exposes new diamonds as needed while retaining those in use to maximize cutting efficiency.
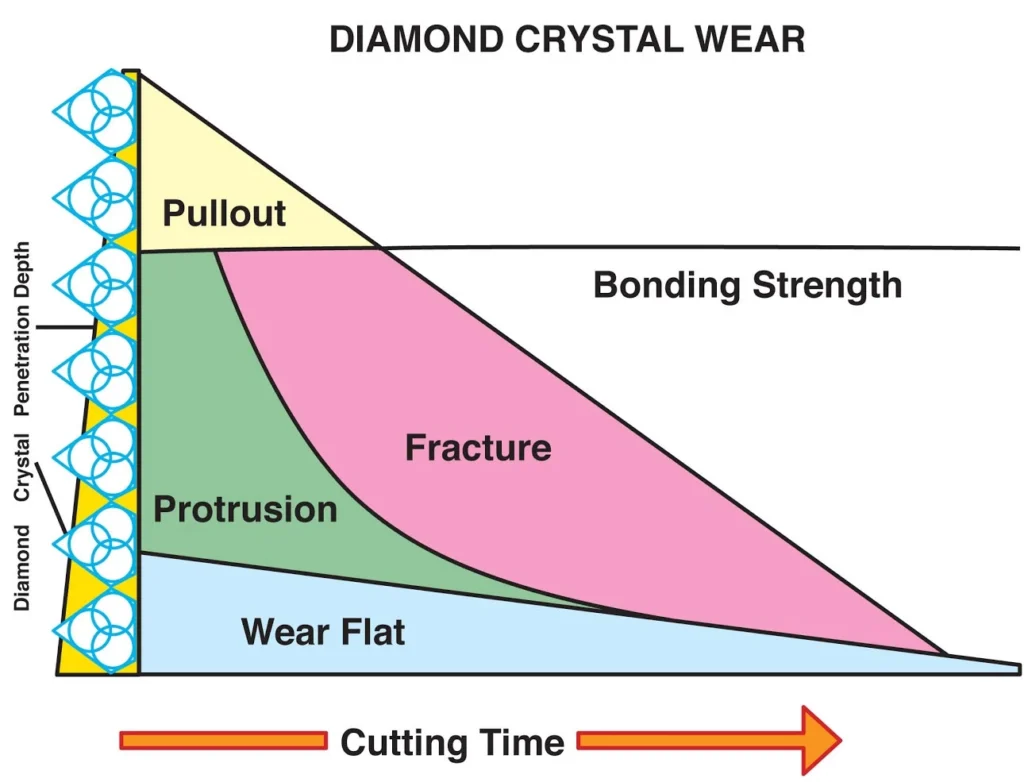
3. Material Hardness and Properties: The properties of the material being cut greatly influence diamond tool performance. Harder materials require diamond crystals with higher strength, but the cutting parameters, such as speed, feed rate, and depth of cut, must also be adjusted to prevent excessive tool wear. In contrast, softer materials may require a different bond composition to avoid rapid diamond loss or smearing, ensuring that the tool operates efficiently without sacrificing cut quality or tool life.
4. Cutting Parameters and Equipment Compatibility: Optimum diamond tool performance is not solely a function of the tool itself; it also depends on using the right equipment and cutting parameters. Machine stability, RPM, feed rate, coolant flow, and pressure must all be tailored to support the diamond tool’s characteristics. For example, higher RPMs are typically more suitable for smaller diamond grit sizes, while coarser grits may require lower speeds but greater force to achieve the right balance between cutting speed and tool wear. Coolant is also crucial to manage heat buildup and maintain tool integrity.
5. Power Consumption and Efficiency: The power consumed by the equipment during cutting directly impacts overall efficiency and cost. Properly tuned cutting parameters reduce unnecessary power usage by ensuring that the tool operates at peak efficiency. Overly aggressive settings can lead to higher power consumption, excessive heat, and tool degradation, while too mild settings may fail to utilize the tool effectively, resulting in longer cycle times and reduced productivity. Monitoring and adjusting power requirements are essential for achieving optimal tool performance.
6. Tool Life vs. Cutting Speed Trade-off: Tool life and cutting speed often have an inverse relationship. Increasing the cutting speed may improve productivity but can also lead to accelerated tool wear and reduced life if not balanced with appropriate diamond strength and bond composition. Conversely, focusing on longer tool life may require slower cutting speeds and more conservative parameters. The goal is to find a balance where the tool provides a high material removal rate without sacrificing its operational longevity.
Optimizing Wear and Efficiency
To achieve the best performance, diamond tools must be used in a way that encourages optimal wear patterns, particularly micro-chipping of diamond crystals. This allows the cutting edges to remain sharp throughout the tool’s life, ensuring maximum cutting efficiency, consistent material removal, and a balance between speed and tool longevity. Regular monitoring of the tool’s condition, cutting performance, and wear patterns can help determine when adjustments to parameters are needed to maintain optimal performance.
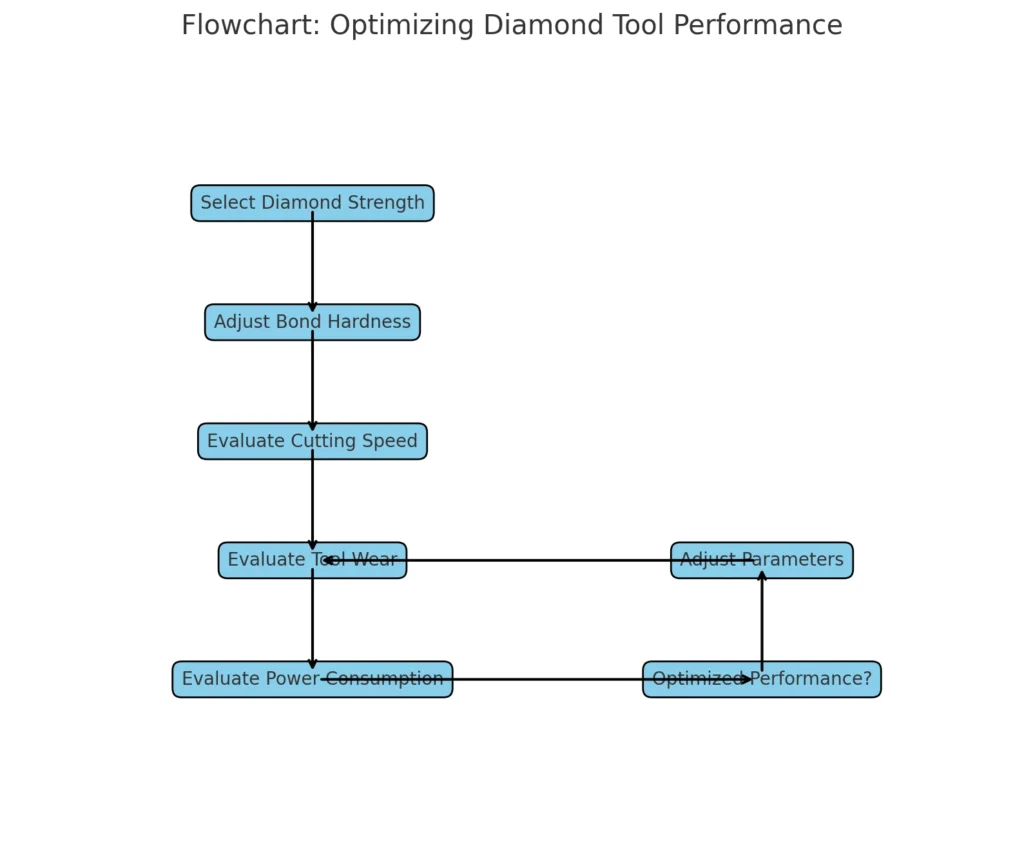
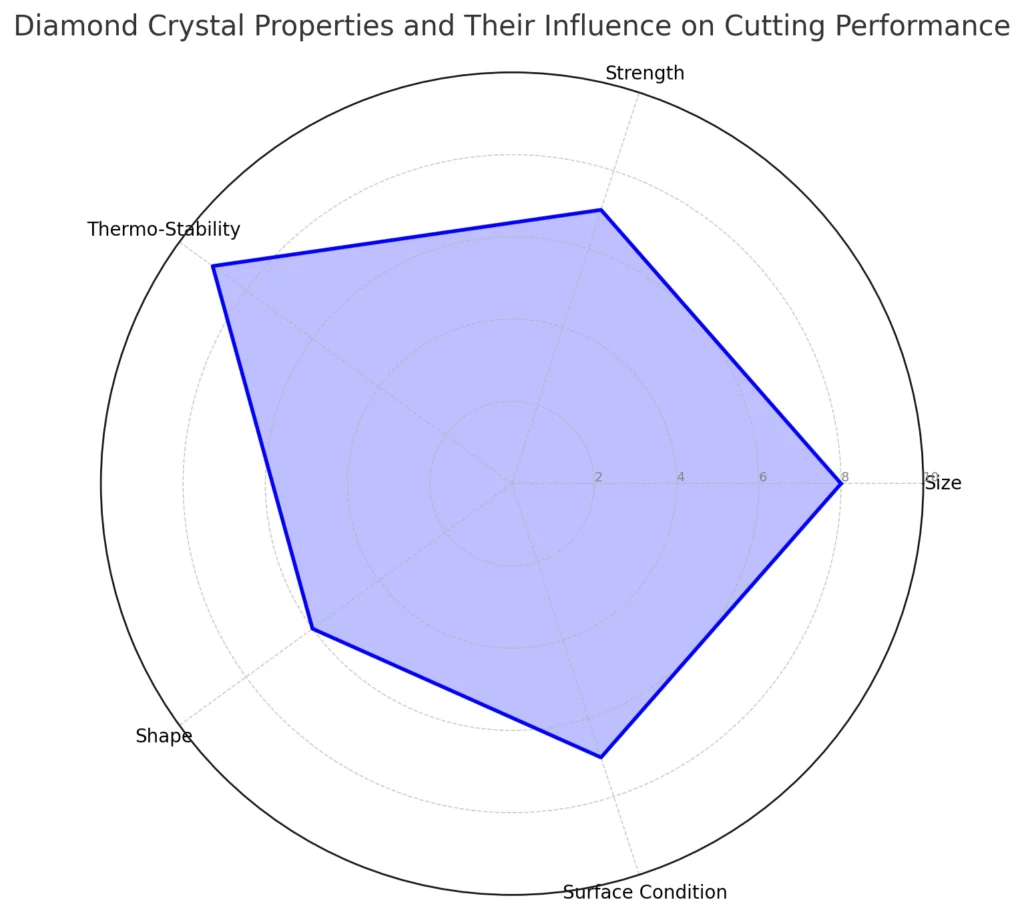
DIAMOND CRYSTAL PROPERTIES
Diamond crystals used in industrial applications are generally very small, typically less than 1mm in size, and are often barely visible to the naked eye. Most of these crystals have rough surfaces due to the presence of flaws, impurities, and varying internal structures, which are characteristic of industrial diamonds. Despite these imperfections, industrial diamond crystals are highly valuable due to their hardness and unique cutting properties.
Among industrial diamond grades, coarse saw-grade diamond crystals stand out for their large size, with grit sizes ranging from 20 to 50 mesh (approximately 1mm to 0.25mm). These crystals exhibit the highest degree of perfection possible for industrial-grade diamonds. They are often euthedral in shape, featuring well-defined crystallographic faces, and they have interiors with minimal defects or inclusions. The advantage of coarse saw-grade diamonds lies in their ability to cut at high speeds and break materials using brute force. Their size and structure allow for aggressive cutting action, making them suitable for heavy-duty applications requiring rapid material removal.
In contrast, smaller-sized diamond crystals operate differently. These crystals work by scratching the surface of the material gradually, relying on their hardness rather than toughness. They penetrate the material through abrasion rather than brute force, making them suitable for precision cutting or for applications where a fine surface finish is required. As a result, the choice between large and small diamond crystals depends on the balance between cutting speed, material removal rate, and desired surface quality.
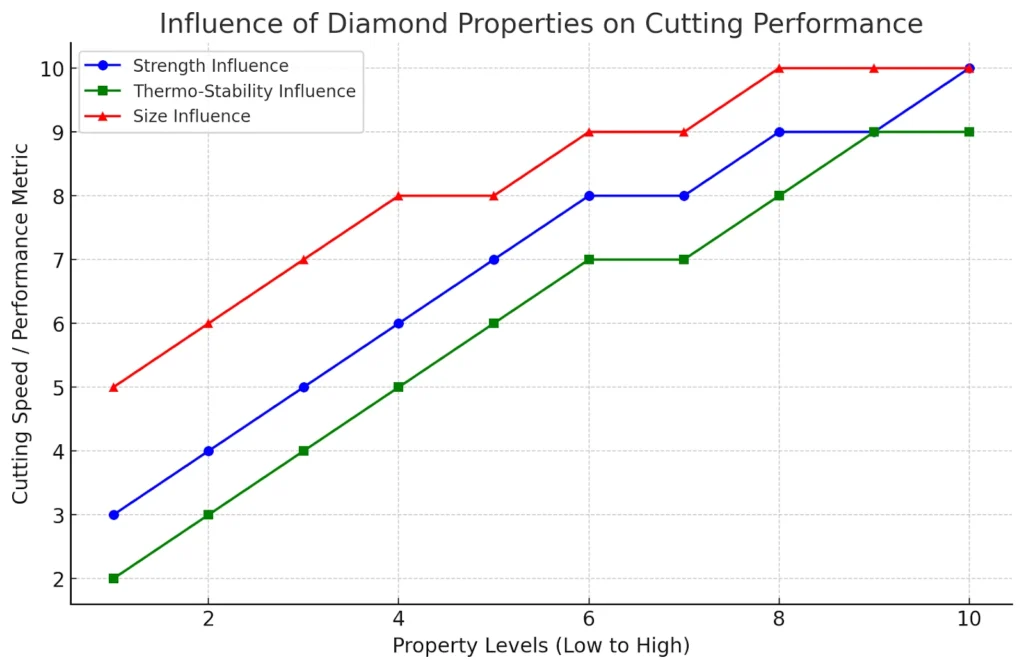
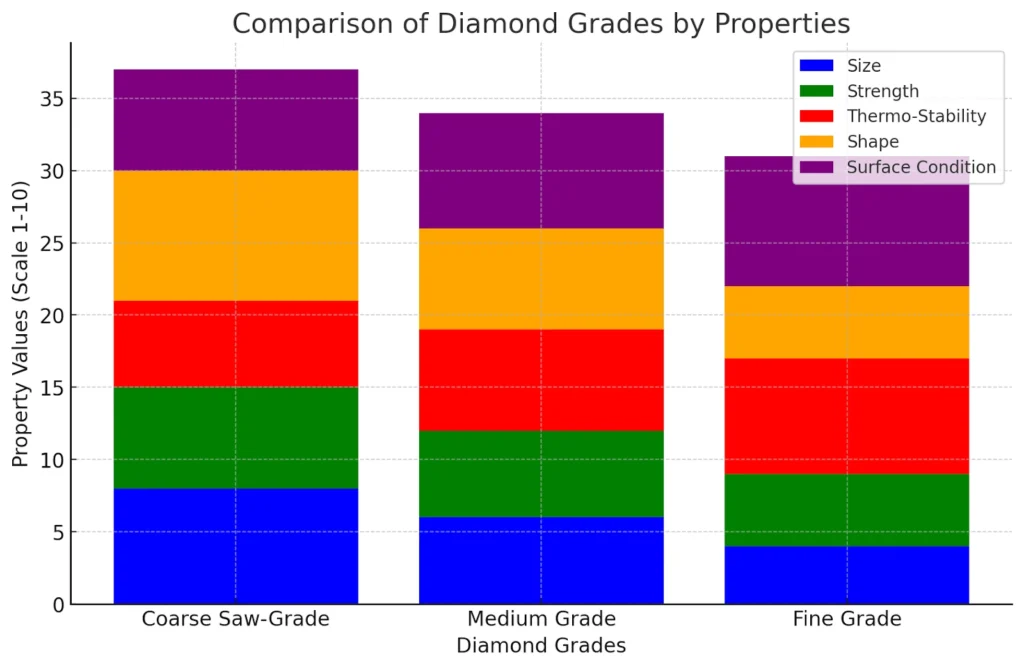
Industrial diamonds are available in a wide range of grades and prices, which reflect differences in size, strength, and overall quality. While all industrial diamond manufacturers can produce lower-grade diamonds with reduced strength and small sizes, only a select few have the capability to produce high-grade, high-performance diamonds with superior cutting characteristics.
Several key properties influence the performance of diamond crystals in cutting and grinding applications:
Diamond Crystal Size
The size of the diamond crystal is one of the most critical factors in determining a tool’s cutting speed and the roughness of the surface finish produced. Larger crystals, such as those found in coarse saw-grade diamonds, enable faster cutting and rougher finishes, while smaller crystals provide finer finishes and more controlled cutting action. Tools designed for high material removal rates and aggressive cutting typically use larger diamond grit sizes.
Diamond Crystal Strength
Strength is a defining factor in a diamond’s ability to cut through various materials. It determines the range of materials that can be processed and the appropriate cutting parameters, such as speed (RPM) and load. Stronger diamonds withstand higher forces without breaking or disintegrating, making them suitable for cutting harder and more abrasive materials. High-strength diamonds enable longer tool life and the ability to maintain cutting efficiency under demanding conditions.
Diamond Crystal Thermo-Stability
Thermo-stability refers to the diamond’s ability to maintain its structural integrity under elevated temperatures. This property is crucial in determining the processing temperatures the diamond can handle and the type of tools in which it can be used. High thermo-stability ensures that the diamond remains effective even when cutting or grinding at high temperatures, reducing the risk of thermal degradation. This stability also influences the aggressiveness of the cut, allowing for deeper penetration without causing the diamond to lose its cutting ability or fracture prematurely.
Diamond Crystal Shape
The shape of the diamond crystal plays a vital role in cutting speed and resistance to the material being processed. Crystals with sharp, well-defined edges provide efficient cutting and enhance material removal, especially in aggressive cutting applications. The more uniform and regular the shape, the better the cutting efficiency and the more consistent the performance. Conversely, irregular or rounded diamond crystals may reduce cutting speed but provide a more controlled cutting action, which is beneficial for precision operations and applications requiring minimal chipping or damage to the material.
Natural Diamond
Natural diamonds are evaluated based on the “Four Cs”: Carat, Color, Clarity, and Cut. These factors significantly influence the value, quality, and appearance of the diamond.
-
Carat: This refers to the weight of the diamond. One carat is equivalent to 200 milligrams. Larger diamonds are rare and typically more valuable, though smaller diamonds can still be valuable depending on their other characteristics.
-
Color: The color of a natural diamond ranges from colorless to various shades of yellow and brown. The most highly valued diamonds are completely colorless, while those with noticeable color tints (especially yellow) are generally less valuable. Fancy-colored diamonds (e.g., pink, blue) can be very valuable due to their rarity.
-
Clarity: This describes the presence of internal or external imperfections (inclusions and blemishes) in the diamond. Diamonds with fewer inclusions are more valuable, as they allow light to pass through more effectively, enhancing brilliance and sparkle. Clarity is graded on a scale ranging from "Flawless" to "Included."
-
Cut Charm: The cut quality of a diamond affects its brilliance and sparkle. A well-cut diamond reflects light beautifully, creating a charm that enhances its visual appeal. The cut includes aspects such as symmetry, polish, and proportion, all contributing to the overall charm and shine of the diamond. A poorly cut diamond, regardless of its carat weight or clarity, may appear dull or less impressive
Synthetic Diamond
Synthetic or lab-grown diamonds are evaluated based on different parameters more related to their industrial and practical use, focusing on qualities like Size, Strength, Stability, Shape, and Surface.
-
Size: Unlike natural diamonds, synthetic diamonds can be manufactured to precise sizes and shapes based on application requirements. This consistency in size is crucial for industrial applications, ensuring uniformity in cutting, grinding, or other operations where the diamond is used.
-
Strength: Synthetic diamonds are often chosen for their enhanced mechanical strength. They are designed to withstand high-impact cutting, abrasion, and pressure without chipping or fracturing. The crystal structure and quality can be controlled during the manufacturing process to achieve the desired strength.
-
Stability: Stability in synthetic diamonds refers to their thermal and chemical resistance. These diamonds can endure extreme temperatures and exposure to harsh chemicals without degrading or losing their cutting effectiveness, making them suitable for applications in high-temperature environments and materials processing.
-
Shape: Synthetic diamonds can be engineered in a variety of shapes, from blocky to elongated crystals, depending on the intended use. The shape directly impacts how the diamond interacts with the material being cut or ground. For instance, blocky shapes may be favored for toughness and durability, while more angular shapes are chosen for aggressive cutting and grinding.
-
Surface: The surface condition of a synthetic diamond is crucial for its bonding to tools and overall cutting performance. The surface can be coated or treated to enhance adhesion to the bond matrix of the tool, improving tool life and efficiency. Smooth surfaces ensure efficient cutting, while rough or coated surfaces enhance the diamond's retention in the matrix, especially in demanding applications.
Criteria |
Natural Diamond |
Synthetic Diamond |
---|---|---|
Carat/Size |
Weight measured in carats, rarity increases with size |
Manufactured to precise sizes for specific industrial applications |
Color |
Ranges from colorless to yellow or brown; rare colors highly valued |
Usually clear or uniform in color; tailored to industrial needs |
Clarity |
Graded on a scale from flawless to included; fewer inclusions add value |
Engineered to have minimal inclusions for optimal performance |
Cut Charm/Shape |
A well-cut diamond enhances brilliance and charm |
Designed shapes for specific use; blocky or angular for efficiency |
Strength |
Typically less controlled in strength as compared to synthetics |
Engineered for high strength and impact resistance |
Stability |
Stability varies naturally; some can endure high temperatures and chemicals |
High stability against thermal and chemical exposure |
Surface |
Natural surfaces are polished but can have imperfections |
Surface can be treated or coated to improve tool bonding and performance |
DIAMOND CRYSTAL COATINGS
Diamond crystal coatings play a significant role in enhancing the performance of diamond tools across a variety of applications. By applying specific coatings to diamond crystals, their retention within the bond matrix is improved, ultimately influencing the tool’s cutting efficiency, speed, and longevity. Coated diamond crystals not only have enhanced retention but also demonstrate a higher protrusion ratio, which allows for more effective engagement with the work material, thus providing a faster cutting speed.
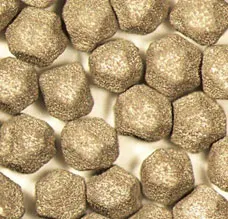
Studies have shown that coatings can extend the lifespan of diamond crystals by at least one-third compared to uncoated diamonds. This increased retention results from the coating’s ability to better anchor the diamond crystal within the bond matrix. The coating acts as a transitional layer, improving adhesion between the diamond and the bond material and reducing premature diamond loss during cutting operations. This enables the diamond crystals to be used to their full potential before being dislodged, enhancing the tool’s overall performance and cost-efficiency.
The coatings applied to diamond crystals typically consist of carbide-forming material components, such as titanium (Ti), chromium (Cr), tungsten (W), and silicon (Si). These carbide-forming elements have a high affinity for carbon and are capable of creating strong carbide bonds with the diamond crystal at its surface. This bond formation improves the crystal’s grip within the bond matrix, effectively strengthening the diamond’s attachment and allowing for more aggressive cutting.
There are several methods for applying coatings to diamond crystals, each with its own set of advantages and limitations. Common techniques include:
-
Vapor Deposition: This method involves applying the coating material onto the diamond surface in a vapor phase. Techniques such as Chemical Vapor Deposition (CVD) or Physical Vapor Deposition (PVD) allow for the uniform distribution of the coating material across the diamond crystal. Vapor deposition provides good control over coating thickness and adhesion properties, making it suitable for fine-tuning performance attributes. However, this method can be more expensive and time-consuming compared to others.
-
Chemical Reaction: This process relies on a controlled chemical reaction to bond the coating material to the diamond surface. The coatings are typically formed through chemical interactions between the diamond and reactive gases or liquids. This method can be efficient for creating specific coating compositions but may require precise conditions to achieve consistent results.
-
Diffusion in Fused Salt Bath: In this method, the diamond crystals are submerged in a molten salt bath containing the desired coating elements. These elements diffuse onto the diamond surface, creating a strong bond. This technique can be advantageous for applying coatings over larger surface areas and for bulk processing of diamond crystals. However, controlling the uniformity and thickness of the coating can be more challenging compared to vapor deposition methods.
Each of these coating techniques influences the performance of diamond tools differently. For instance, coatings applied via vapor deposition tend to provide more consistent and predictable performance due to their precise application, but they may come at a higher cost. Chemical reaction coatings are effective but require meticulous control over the reaction environment to ensure even coating. The fused salt bath diffusion method is cost-effective for larger batches, though it may lack the uniformity seen in vapor deposition techniques.
The choice of coating and application method depends largely on the specific cutting or grinding application, the properties of the work material, and the desired balance between tool life and cutting performance. For example, tools used for abrasive materials such as concrete or stone may benefit from thicker coatings to enhance retention and durability, while tools used for precision cutting of ceramics or glass may require thin, uniform coatings to maintain surface finish quality.
DIAMOND TAILS
Diamond tails play a critical role in the cutting efficiency and durability of diamond tools. A diamond tail is a structure that extends from the diamond crystal and enhances how securely the crystal is held within the bond matrix. This feature significantly impacts the longevity of the diamond particles and the overall tool performance.
The tail acts as a support and shield for the diamond crystal, anchoring it firmly into the bond. This secure hold prevents premature dislodgement or loss of the diamond. When a diamond tool is in use, the bond matrix wears down gradually to expose new diamond particles. Without a properly formed tail, the diamonds may loosen, fall out too soon, or be dislodged before they have been used to their full potential. The tail ensures that the diamond remains effective throughout its lifespan, maximizing cutting efficiency and extending the tool’s usability.
The direction of cutting is crucial for maintaining the integrity of the diamond tail. When the tool is used in the intended direction, the tail supports the diamond, ensuring a stable cut and gradual wear of the bond. This proper usage allows for consistent exposure of the diamond and efficient cutting. However, cutting in the opposite direction to the tail’s alignment can erode the tail prematurely, causing the diamond crystal to become overexposed. As a result, the diamond becomes unstable and more prone to dislodgement when it contacts the work material. This not only shortens the tool’s lifespan but also leads to inefficient cutting, increased tool wear, and potentially damaging the surface finish of the material.
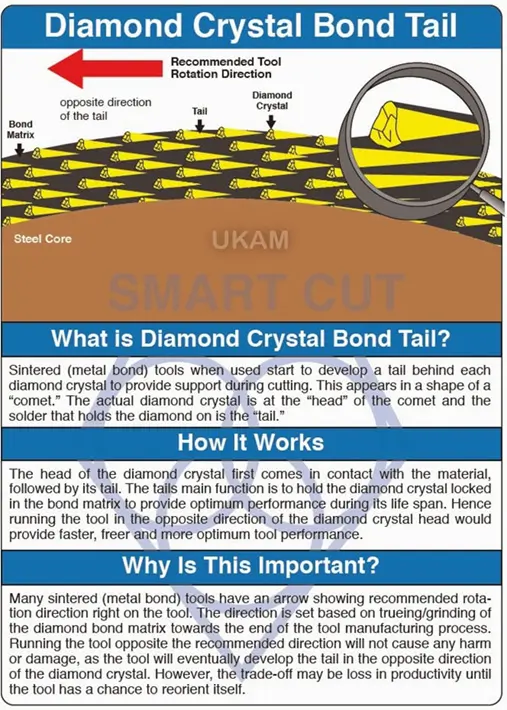
To achieve optimal performance, it is crucial to ensure that the diamond tool cuts in the correct direction relative to the tail. Proper alignment maximizes diamond usage by keeping it securely held within the bond for a longer duration, providing a sustained cutting action and minimizing waste. It also allows for steady wear and exposure of diamond particles, leading to a more predictable and uniform cut. By preventing premature loss of diamond particles, the tool’s lifespan is extended, offering cost-efficiency and reducing the need for frequent replacements.
If a diamond tool is used improperly by cutting against the tail’s intended alignment, it can lead to visible signs of damage. Rapid wear of the bond matrix, overexposed diamonds that break off quickly, inconsistent cutting behavior, rough finishes, or damaged workpieces are common outcomes of incorrect usage. This also reduces the overall life of the tool and increases the need for dressing.
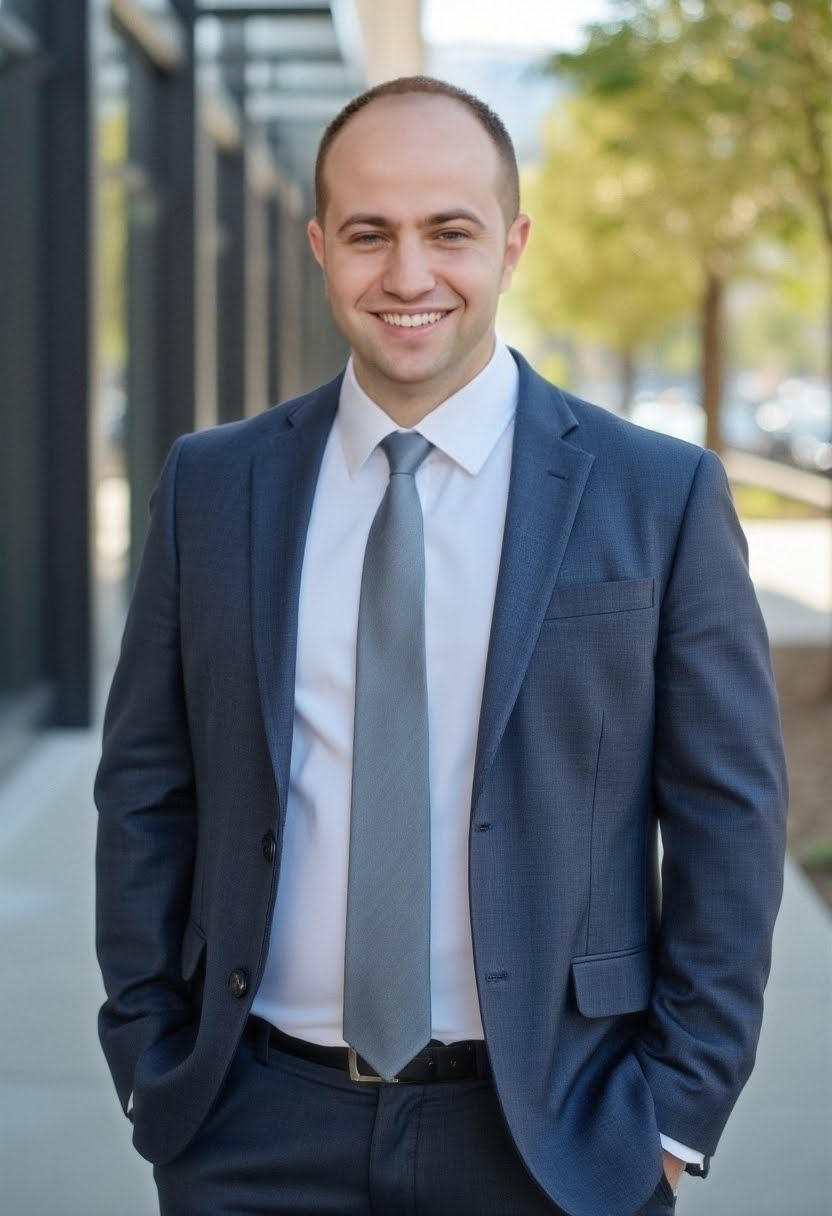
Brian is an experienced professional in the field of precision cutting tools, with over 27 years of experience in technical support. Over the years, he has helped engineers, manufacturers, researchers, and contractors find the right solutions for working with advanced and hard-to-cut materials. He’s passionate about bridging technical knowledge with real-world applications to improve efficiency and accuracy.
As an author, Brian Farberov writes extensively on diamond tool design, application engineering, return on investment strategies, and process optimization, combining technical depth with a strong understanding of customer needs and market dynamics.
ARE YOU USING RIGHT TOOLS
FOR YOUR APPLICATION?
LET US
HELP YOU
HAVING ISSUES WITH
YOUR CURRENT TOOLS?
Knowledge Center
How to Selecting Right Diamond Tools for your application
How to properly use Diamond Tools
Why use diamond
Diamond vs CBN (cubic boron nitride) Tools
What is Diamond Mesh Size and how to select best one for your application
What is Diamond Concentration and which to use for your application
Diamond Tool Coolants Why, How, When & Where to Use
Get to Know the Diamond Tool Bond Types and Which to use for your application
Choosing The Correct Diamond Bond Type
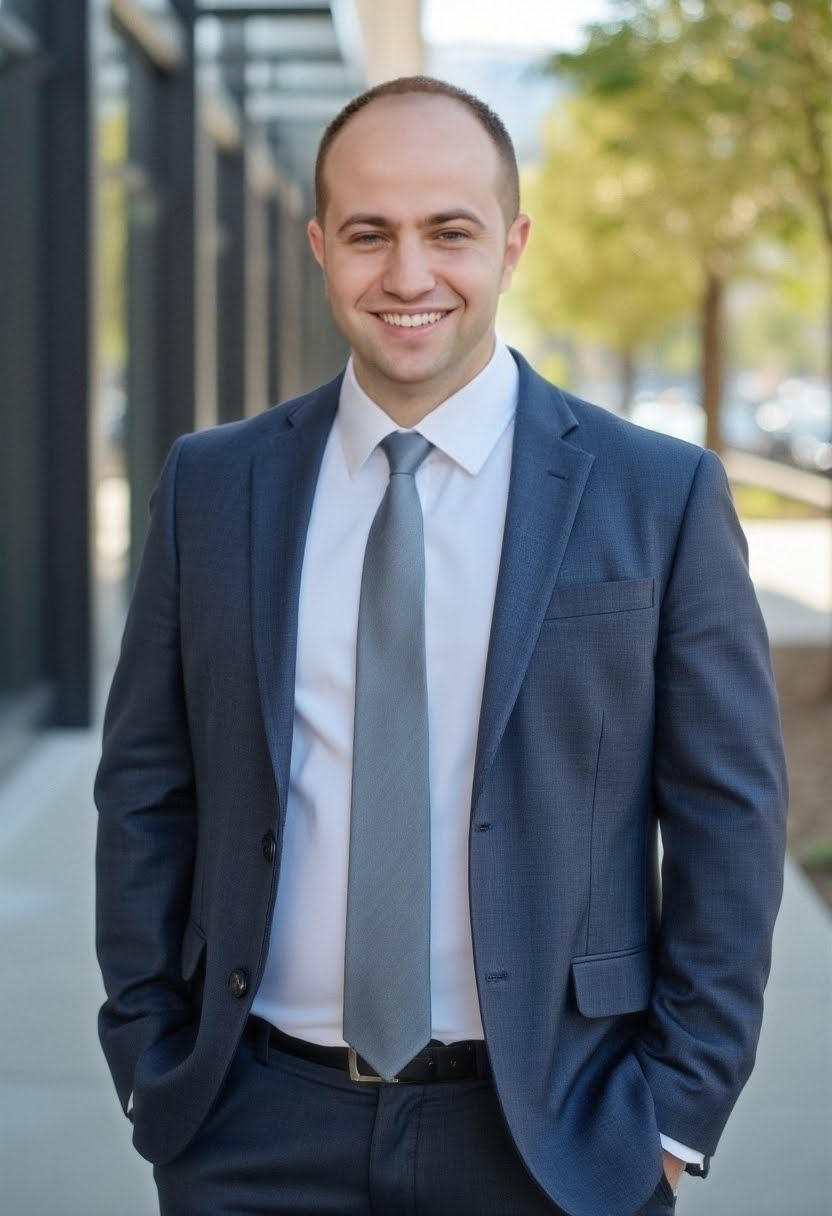
Brian is an experienced professional in the field of precision cutting tools, with over 27 years of experience in technical support. Over the years, he has helped engineers, manufacturers, researchers, and contractors find the right solutions for working with advanced and hard-to-cut materials. He’s passionate about bridging technical knowledge with real-world applications to improve efficiency and accuracy.
As an author, Brian Farberov writes extensively on diamond tool design, application engineering, return on investment strategies, and process optimization, combining technical depth with a strong understanding of customer needs and market dynamics.