Table of Contents
ToggleSelecting the appropriate diamond bond type for specific applications is crucial for several reasons. Diamond bond type directly affects the tool's performance, efficiency, and longevity. Different bond types determine how well a tool can withstand the rigors of various machining tasks, especially in the context of material hardness, abrasiveness, and the desired precision of the final product. The right bond type ensures that the diamond remains effectively embedded in the tool, providing consistent performance and maximizing the cutting or grinding capabilities. Incorrect bond selection can lead to rapid wear and tear, increased tool replacement costs, and poor quality finishes, ultimately affecting productivity and increasing operational costs.
What is Bond Matrix?
The bond is the agent that keeps the diamond or CBN (cubic boron nitride) crystals in place. Its a matrix that consists of various powders (whether metal, phenolic resin or ceramic). Its job is to release the diamond crystals it hold in a controlled rate to obtain the clients desired objectives. Whether its best surface finish quality, fast cutting speed (certain yield), and long life (economics/return on investment).
The diamond itself does the actual cutting. Bond matrix function is to retain and expose diamond. These two goals can often contradict and even interfere with each other. However, choice of the right bond grading assures that the diamond grit will be held until the maximum cutting value has been obtained.
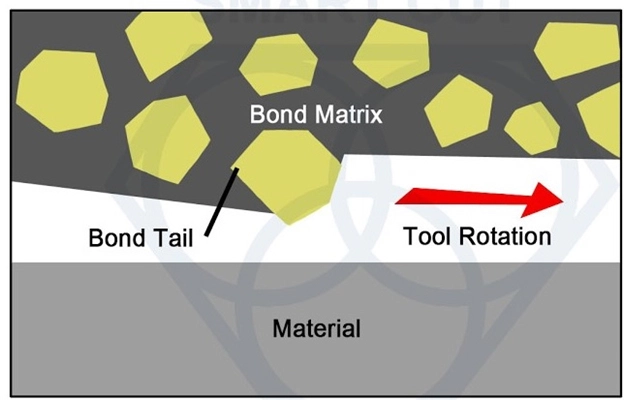
If its too hard, dull diamonds will be held tool long resulting in glazing of the tool which means slow cutting and loss in productivity. For example a hard bond matrix can retain diamond crystals by burying them. If the bond is too soft, the bond matrix will lose diamond crystals by overly exposing them, resulting in premature loss and hence short tool life.
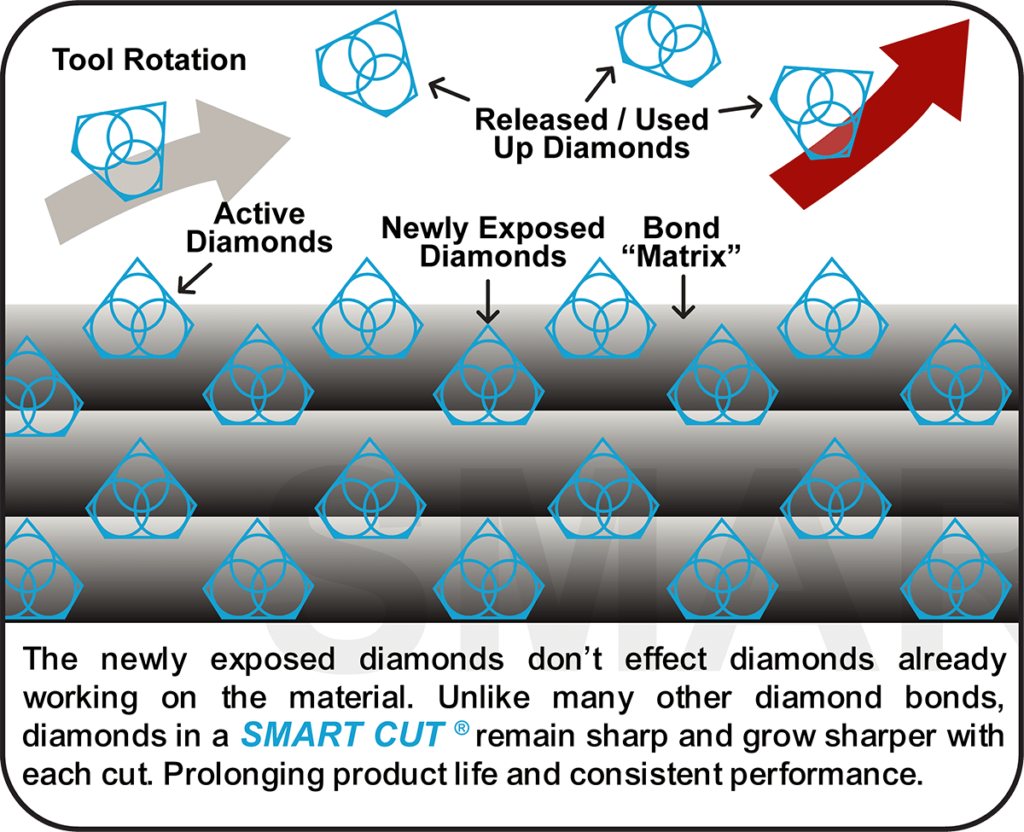
The indication of this premature loss of diamond is deep pocket left behind. The presence of many pockets means the diamond is wasted without being used. Each diamond must protrude high to cut fast with low resistance. In order to cut efficiently not only diamond must be strong enough to withstand the impact, but also it should be adhered in the matrix firmly. Penetration into the material must be deep enough to allow the micro chipping, but shallow enough to prevent diamond shattering.
In order to keep distinct difference between these two goals the diamond is frequently coated or brazed in order to improve its retention so the matrix wear rate can be independently adjusted to allow the diamond to protrude properly.
Function of Bond Matrix in Diamond Tools
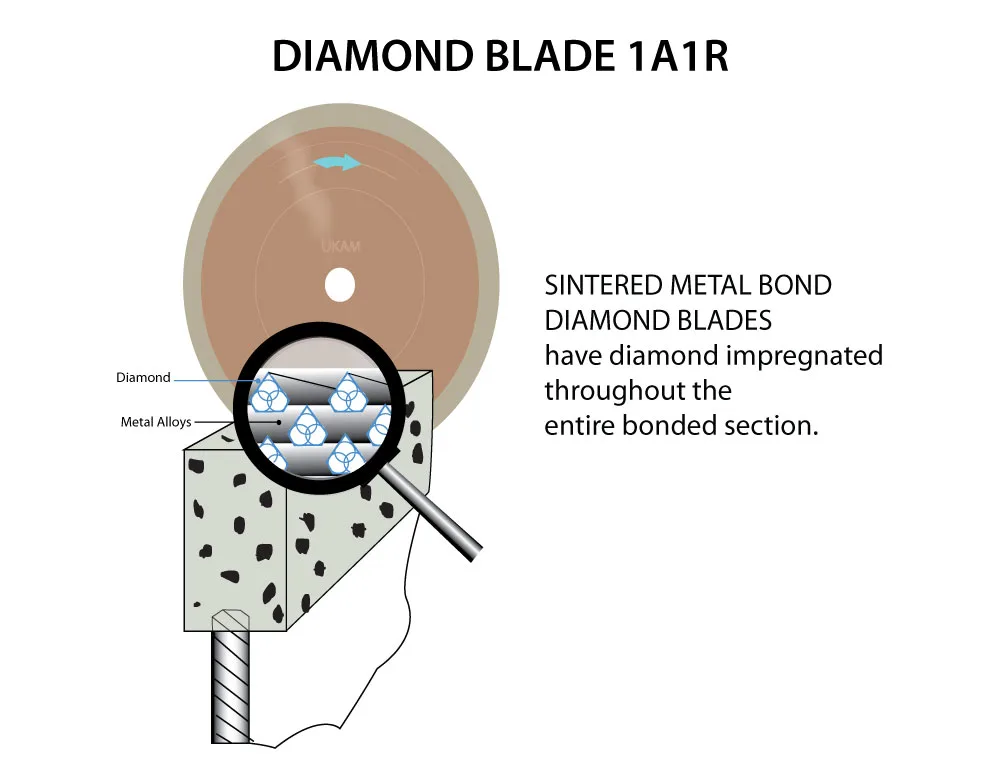
1. Diamond Crystal Retention Without Premature Pullouts
-
Purpose: The primary function of the bond matrix is to hold the diamond crystals securely in place during the cutting or grinding process. The bond needs to be strong enough to avoid premature pullouts of diamonds, which can lead to inefficient tool performance and uneven wear.
-
Mechanism: The bond matrix grips the diamonds through mechanical interlocking and chemical bonds, depending on the material of the bond and the coating on the diamonds. This retention must balance the strength and wear rate to ensure that diamonds are held firmly until they are worn to a point where they no longer cut effectively.
2. Controlled Bond Erosion for Diamond Exposure
-
Purpose: As the diamonds at the surface of the tool become dull, the bond must erode at a controlled rate to expose new, sharp diamonds. This controlled erosion is essential for maintaining the cutting efficiency of the tool over its lifetime.
-
Mechanism: The bond matrix is designed to wear away at a specific rate, which depends on the bond material and the operational conditions. This wear rate should match the diamond erosion rate to ensure that new cutting surfaces are exposed just as the old ones become worn out.
3. Strength for Optimal Energy Transfer
-
Purpose:The bond matrix must provide sufficient structural strength to withstand the forces exerted during machining. It should effectively transfer energy from the spindle of the machine to the material being worked on, maximizing the tool's cutting or grinding power.
-
Mechanism: The integrity of the bond affects how well it can transfer and distribute mechanical stress across the tool. A well-designed bond matrix will be able to handle the dynamic stresses of high-speed cutting and grinding without cracking or breaking.
Diamond & cbn bonds can be further classified based on if its single or multiple layered. A single layer bond is a coating with only one layer of diamond crystal attached to steel body. Once that layer of diamond crystal is worn, the tool is finished. Multiple layered bond has usually hundreds of bond layers impregnated in the bond matrix, when one layer of crystal wears, looses its sharp point, disintegrates and falls out. A new layer of fresh diamond crystal protrudes and starts working in the cutting zone, taking its place.
The choice between single-layer and multiple-layer diamond bonds depends largely on the specific requirements of the application, including the expected tool life, the nature of the material being processed, and economic considerations. Single-layer bonds offer precision and cost-effectiveness for smaller, detailed tasks, whereas multiple-layer bonds provide durability and sustained performance for extensive and demanding cutting operations.
Single-Layer vs. Multiple-Layer
Single-Layer Bonds
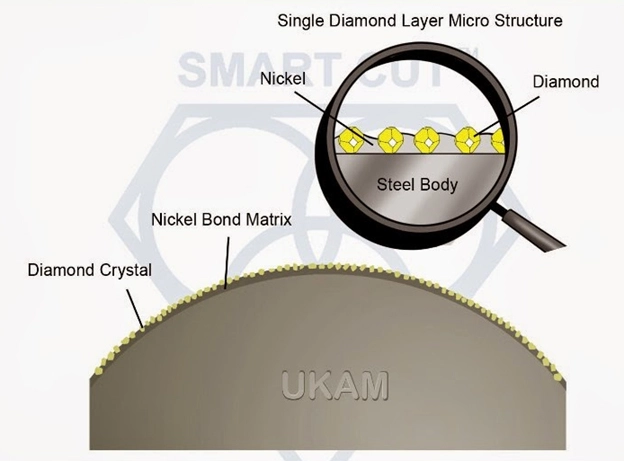
Structure and Composition: In single-layer bonds, a single layer of diamond crystals is electroplated or brazed onto a metal substrate, typically steel. The diamonds are held in place by a metal layer that coats the base. There are no additional layers of diamonds beneath the surface.
Operational Characteristics: The performance of single-layer tools is directly linked to the exposed diamonds. Once these diamonds are worn down or fall out, the tool’s effectiveness diminishes, and it cannot be used further unless re-coated.
Applications: Single-layer diamond tools are often used for specialized applications where precision and control are paramount. They are ideal for intricate cutting, detailing, and finishing work, particularly in materials like ceramics and composites where minimal tool pressure is required.
Advantages: Provides high precision due to the uniform exposure of diamond particles. It is also cost-effective for small or intricate tasks where a controlled cut is more important than tool life.
Limitations: The major drawback is the shorter lifespan compared to multiple-layer tools. Once the diamond layer is worn, the tool must be replaced or re-coated, making it less suitable for heavy-duty or large-volume applications.
Multiple-Layer Bonds
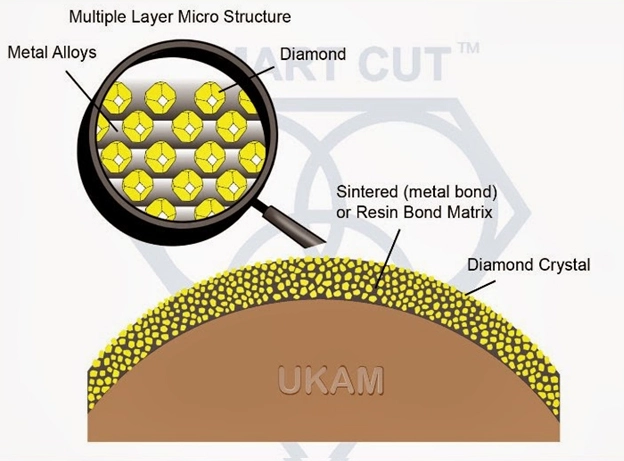
Structure and Composition: Multiple-layer bonds contain several layers of diamond crystals embedded within a bond matrix, typically made from metal, resin, or vitrified materials. As the outer layer of diamonds wears out, new layers of sharp diamonds are exposed, continually renewing the tool’s cutting surface.
Operational Characteristics: These tools are designed for longevity and continuous use. The depth of the diamond layers can vary, often containing hundreds of layers, allowing for extensive use over time. As diamonds on the outer layer become dull and disintegrate, fresh, sharp diamonds from the underlying layers protrude to maintain cutting efficiency.
Applications: Multiple-layer diamond tools are extensively used in heavy-duty applications such as grinding concrete, cutting hard stones, or in any operation where prolonged tool use is necessary.
Advantages: Extended tool life and enhanced durability make these tools more cost-effective for large-scale and intensive cutting operations. The continuous exposure of new diamonds minimizes downtime due to tool changes and maintenance.
Limitations: The initial cost of multiple-layer tools can be higher due to the complexity of their manufacturing process. Additionally, the cutting performance may slightly vary as new layers are exposed, requiring adjustments in operating parameters.
Factors Influencing Bond Type Selection: Material Characteristics
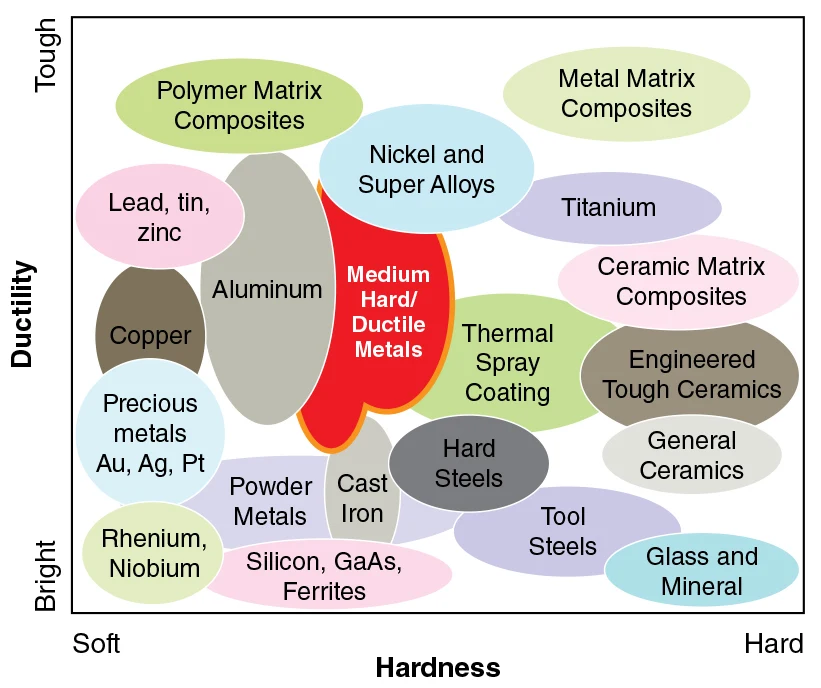
When selecting the appropriate diamond bond type for machining, understanding the characteristics of the material to be processed is crucial. The hardness and abrasiveness of the material directly impact the bond choice. Hard materials like tungsten carbide or hardened steels require a robust bond such as metal or vitrified, which holds the diamonds firmly to avoid premature wear and ensures the longevity of the tool. Conversely, softer and more abrasive materials, such as certain ceramics and composites, demand a bond that allows for quicker diamond exposure and more frequent renewal of the cutting surface, making resin bonds a suitable choice due to their balance between wear resistance and diamond replenishment.
Moreover, the thermal and chemical properties of the material significantly influence the selection of the diamond bond. Materials that generate considerable heat during machining or those that are chemically reactive with carbon, such as titanium and nickel-based alloys, necessitate bonds that can withstand high temperatures and resist chemical attack.
For instance, vitrified bonds are valued for their thermal stability, which helps prevent damage to both the tool and workpiece from excessive heat. Metal bonds are advantageous in scenarios where high thermal conductivity is essential for dissipating heat efficiently, thereby protecting the diamond grits from thermal degradation.
In environments involving chemically reactive materials, opting for chemically inert bonds like certain specialized metal or resin formulations is essential. These bonds prevent the chemical degradation of the diamonds, extending the tool’s operational life. Additionally, in conditions where the machining environment itself may be corrosive, selecting bonds that incorporate corrosion-resistant materials or protective coatings can further enhance the durability and effectiveness of the diamond tool.
Desired Outcomes: Influence of Diamond Bond Type on Machining Results
When selecting a diamond bond type, the desired outcomes in terms of surface finish, precision, and material removal rate are fundamental considerations. Each bond type offers different characteristics that can significantly influence the final results of the machining process. Understanding these outcomes helps tailor the tooling to meet specific operational goals efficiently.
Clients come from many different industries and organization types and sizes. The desired output/yield objectives will vary depending if the application is prototyping/R & D or high volume production operation. Furthermore different clients require different tolerance ranges, surface finish quality, chipping level, tool life, tool cost, and level of consistency. Its not uncommon for different clients to select different tool specification and bond for same application. While the material type and equipment used may have limited the range of choices available.
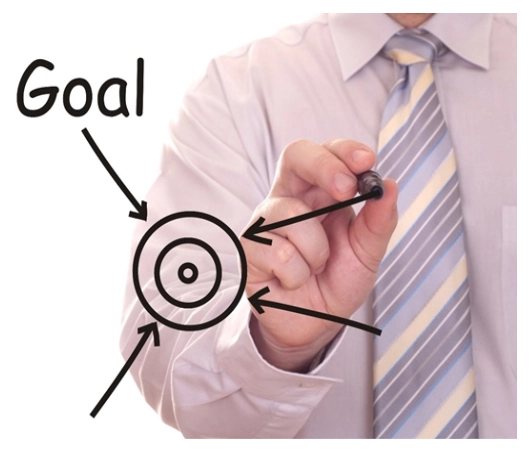
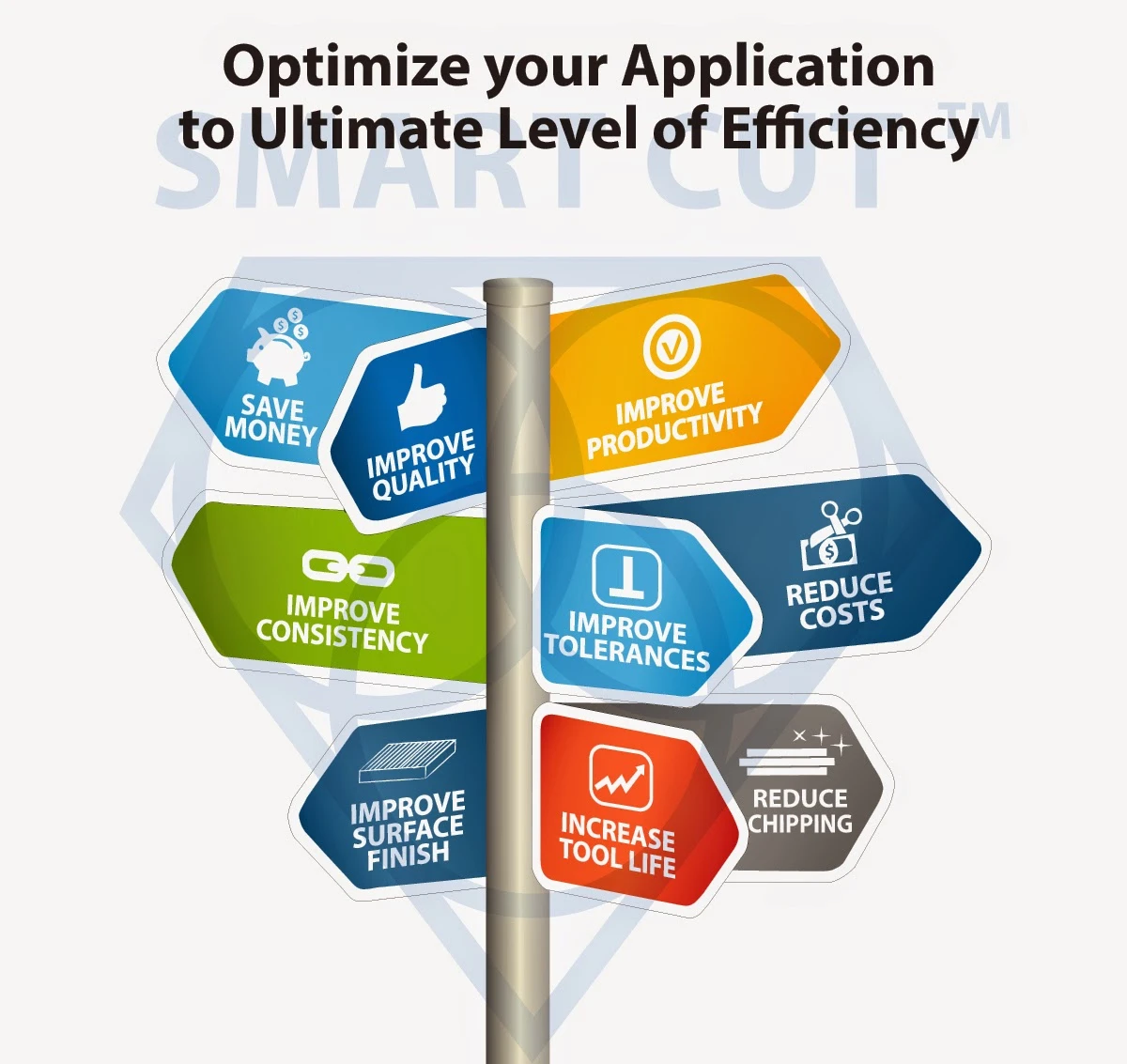
Surface Finish and Precision
The bond type directly affects the surface finish and the precision of the machining operation. For example, resin bonds are renowned for their ability to deliver a smoother finish, which makes them particularly suitable for applications where aesthetic quality and precise dimensional tolerances are critical. Resin bonds are softer compared to metal bonds, allowing the diamond particles to release more readily. This characteristic results in a finer finish, as new, sharp diamonds are exposed more consistently, ensuring that the cut remains clean and precise.
Applications that benefit from resin bonds include precision engineering tasks, such as machining components for medical devices or intricate aerospace parts, where even minor deviations in surface quality or dimensions can compromise the functionality of the finished product. Additionally, the smoother finish provided by resin bonds reduces the need for post-process finishing, which can save both time and money.
Material Removal Rate
The material removal rate (MRR) is a crucial factor in many machining operations, particularly in rough machining and bulk material removal scenarios. Some bonds are specifically engineered to maximize MRR, enhancing overall operational efficiency. Metal bonds, for instance, are typically harder and more wear-resistant, which allows them to maintain a high level of cutting aggressiveness over a longer period. This durability makes metal bonds ideal for high-load conditions where significant material needs to be removed quickly, such as in the construction and stonework industries.
Metal bonds are less likely to wear down or release diamond particles prematurely, which means they can sustain a high MRR for the duration of their use. This characteristic is particularly valuable in applications like cutting concrete or shaping hard stone, where prolonged, aggressive cutting action is required. By maintaining a consistent MRR, metal-bonded tools can help reduce cycle times and increase productivity, making them a cost-effective choice for heavy-duty machining tasks.
Machine Compatibility: Selecting Diamond Bond Types Based on Equipment Specifications
The compatibility between the diamond tool and the machine used is crucial for optimizing tool performance and ensuring longevity. Different machines have varying characteristics that influence which diamond bond type is most appropriate. Understanding these factors can greatly enhance tool efficiency and durability.
Tool Holding and Machine Power
The nature of the tool holding and the power of the machine are critical factors in selecting the right diamond bond. Machines with robust tool holding mechanisms and higher power capacities can effectively utilize harder bond types, such as metal bonds, which are denser and more durable. These bonds are less prone to fracturing under high loads, making them ideal for powerful machines that can exert considerable force without causing tool failure.
Conversely, lighter-duty machines, which typically operate with less power and might have less rigid tool holding capabilities, are better suited to softer bond types, such as resin bonds. These bonds can provide the necessary cutting action without the need for excessive force, reducing the risk of tool breakage and ensuring smoother operation. Using a bond that is too hard for a given machine might lead to inefficient tool use, higher wear and tear, and potentially shortened tool life.
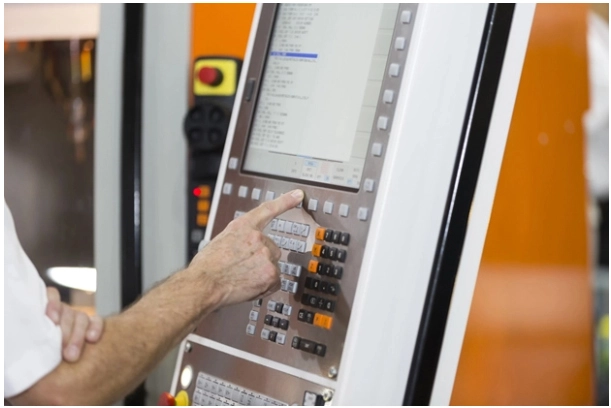
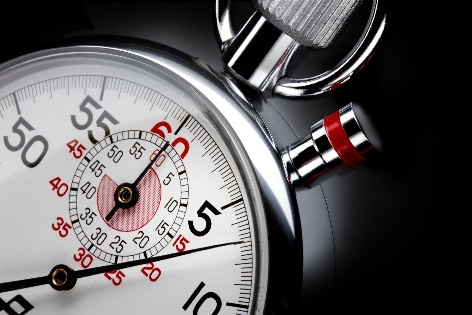
Operational Speeds
Operational speeds significantly impact the choice of diamond bond type due to the differing abilities of bond types to handle the forces generated at high speeds. High-speed operations generate more centrifugal force and heat, which can stress the tool. Bonds that can handle such stresses — typically metal or specially formulated vitrified bonds — are necessary to prevent premature wear and tool degradation.
For machines operating at high speeds, choosing a bond that offers excellent thermal conductivity and stability is crucial. Metal bonds, for example, are effective at dissipating heat and maintaining structural integrity under high-speed conditions. This capability ensures that the diamond crystals are retained securely, and the bond does not break down rapidly, thus maintaining tool effectiveness and extending lifespan.
In lower-speed applications, the selection can afford to prioritize other factors such as the finish quality or material removal rate over the bond’s ability to handle high speeds and temperatures. In such scenarios, resin or softer vitrified bonds may be appropriate, providing efficient performance without the need for high-speed durability.
Cost Efficiency: Evaluating the Economic Impact of Diamond Bond Choices
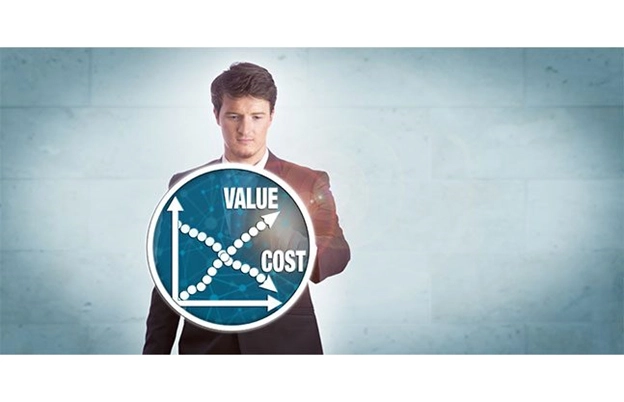
When selecting diamond & cbn tools, cost efficiency is a critical factor that encompasses not only the initial purchase price but also the broader implications of operational lifespan and maintenance requirements. A thorough analysis of these costs can help manufacturers make economically sound decisions that optimize both performance and budget.
Initial Cost vs. Operational Lifespan
The initial cost of diamond bonds can vary significantly based on the type of bond and its intended application. While some diamond bonds may carry a higher upfront cost, their potential for an extended operational life can make them more economical over the long term. For instance, metal and vitrified bonds typically cost more than resin bonds due to their robust construction and the complex manufacturing processes involved. However, their durability under harsh conditions means that tools equipped with these bonds require fewer replacements and can continue to operate efficiently for longer periods, reducing the overall cost per usage hour.
This extended lifespan not only amortizes the initial higher cost but also contributes to greater production continuity, reducing downtime that would otherwise be spent on tool changes and adjustments. For industries where equipment downtime equates to significant production losses, investing in more durable bonds can result in substantial economic benefits.
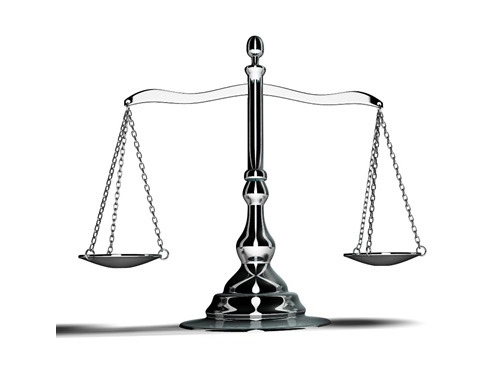
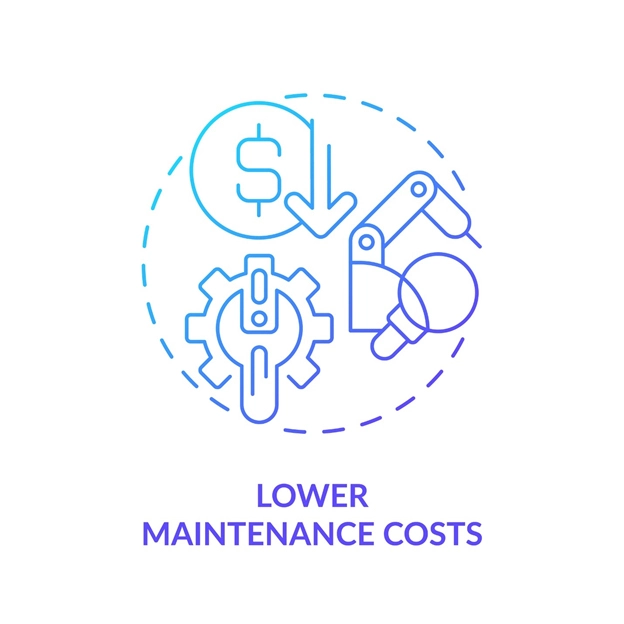
Maintenance and Replacement Costs
The frequency and cost of maintenance and replacements are heavily influenced by the choice of diamond bond. Bonds that wear out more quickly, such as some types of resin bonds, may initially be less expensive but can lead to higher long-term costs due to the need for more frequent replacements. This not only increases direct costs related to purchasing new tools but also adds indirect costs associated with machine downtime and labor for replacing worn tools.
Moreover, the cost of maintenance can vary with the type of bond. Metal and vitrified bonds, for example, might require specific maintenance procedures to maximize their lifespan, such as periodic dressing or specific cooling techniques to prevent overheating. While these procedures have associated costs, they are often justified by the significantly longer tool life and enhanced performance they provide.
Strategic Considerations for Cost Efficiency
To optimize cost efficiency when selecting diamond bonds, manufacturers should consider the following strategies:
-
Assess Total Cost of Ownership: Include all costs associated with the tool over its lifetime, not just the initial purchase price. This assessment should factor in maintenance, replacements, and any potential downtime costs.
-
Match Bond Type to Application Needs: Choose a bond type that aligns with the specific requirements of the application to ensure optimal performance. Over-specifying can lead to unnecessary costs, while under-specifying can result in frequent tool failures and replacements.
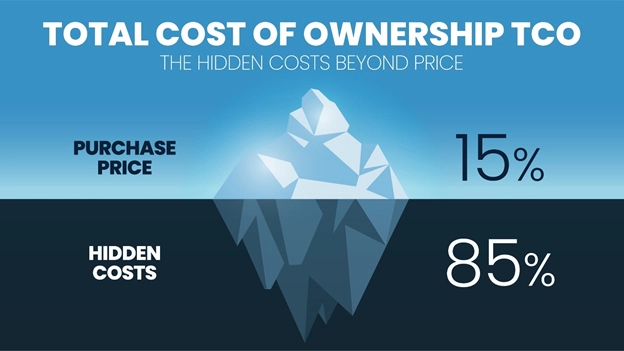
-
Assess Total Cost of Ownership: Include all costs associated with the tool over its lifetime, not just the initial purchase price. This assessment should factor in maintenance, replacements, and any potential downtime costs.
-
Match Bond Type to Application Needs: Choose a bond type that aligns with the specific requirements of the application to ensure optimal performance. Over-specifying can lead to unnecessary costs, while under-specifying can result in frequent tool failures and replacements.
-
Plan for Long-Term Savings: Opt for higher-quality, durable bonds if the application warrants it, focusing on long-term savings rather than just the upfront cost. This is particularly important for high-volume or critical machining operations where downtime has a major impact on productivity.
Selecting the right Bond Hardness
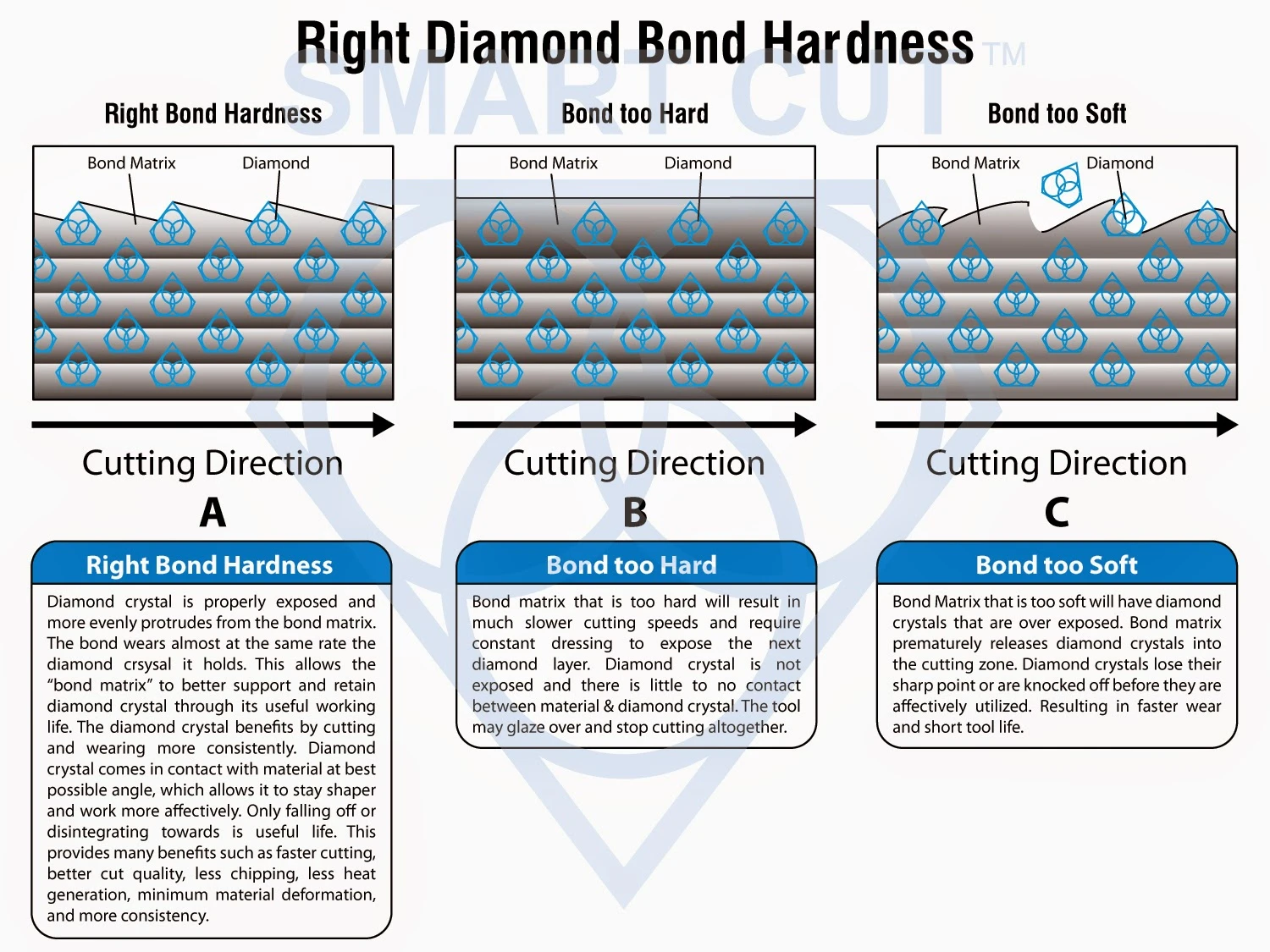
Right Bond Hardness
Diamond crystal is properly exposed and more evenly protrudes from the bond matrix. The bond wears almost at the same rate as the diamond crystal it holds. This allows the "bond matrix" to better support and retain and diamond crystal through its useful working life. the diamond crystal benefits by cutting and wearing more consistently. Diamond crystal comes in contact with material at best possible angle, which allows it to stay sharper and work more affectively. Only falling off or disintegrating towards its useful life. this provides many benefits such as faster cutting, better cut quality, less chipping, less heat generation, minimum material deformation, and more consistency.
Bond too Hard
Bond matrix that is too hard will result in much slower cutting speeds and require constant dressing to expose the next diamond layer. diamond crystal is not exposed and there is little to no contact between material and diamond crystal. The tool may glaze over and stop cutting altogether.
Bond too Soft
Bond matrix that is too soft will have diamond crystals that are over exposed. Bond matrix prematurely releases diamond crystals into the cutting zone. Diamond crystals lose their sharp point or are knocked off. Before they are affectively utilized. Resulting in faster wear and short tool life.
Find out more about selecting right bond hardness for your application>>>
Diamond & CBN Bond Types Available
The selection of a bond type for diamond and CBN tools is a crucial aspect that directly influences their performance and suitability for specific applications. The following bond types are commonly used in the production of diamond tools:
-
Sintered (metal bond)
-
Resin Bond
-
Electroplated (nickel bond)
-
Vitrified Bond
-
Brazed Bond
-
Hybrid Bond
Each bond is manufactured through unique technological processes, utilizing various bonding materials, additives, and types of diamond crystals. Consequently, every bond type has its distinct properties, strengths, and weaknesses, making it more or less suitable for certain applications. The choice of bond type depends on several factors, including the client’s objectives, the material being processed, the equipment used, and the overall operational environment. Therefore, collaboration between the client and the diamond tool manufacturer is crucial to ensure that the bond type and its characteristics are optimally matched to the specific application.
The client must provide detailed information about their needs, materials, and equipment, while the manufacturer uses their expertise and analytical experience from previous projects to determine the optimal tool parameters. These parameters include diamond grit size, concentration, bond hardness, and more. However, it is essential to recognize that tools with the same specification can behave drastically differently depending on the bond type used. What works well for one bond type might be entirely unsuitable for another.
For instance, a 120-mesh resin bond diamond cut-off wheel may offer an ideal combination of cutting speed and surface finish for glass or ceramic tubing. However, the same 120-mesh grit in a sintered (metal bond) wheel would produce excessive chipping, reducing cut quality. To match the surface finish and chipping level of a resin bond wheel, a metal bond wheel would typically require a finer grit size (such as 600-mesh) and a higher diamond concentration. Even then, it would be challenging to achieve the same surface finish and cutting speed provided by the resin bond. This is akin to comparing apples to oranges—while both are fruits, they differ significantly in characteristics and suitability for specific needs.
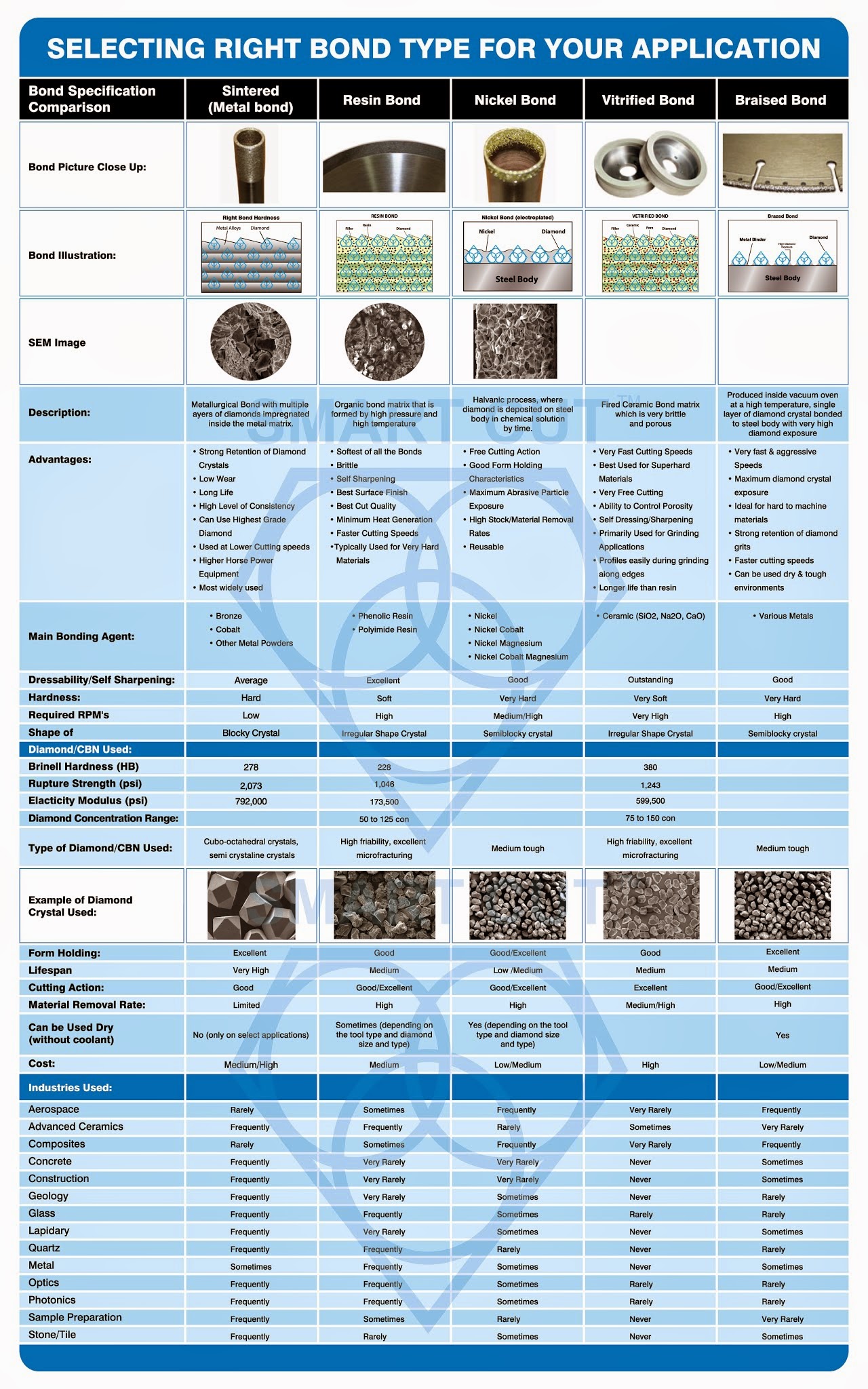
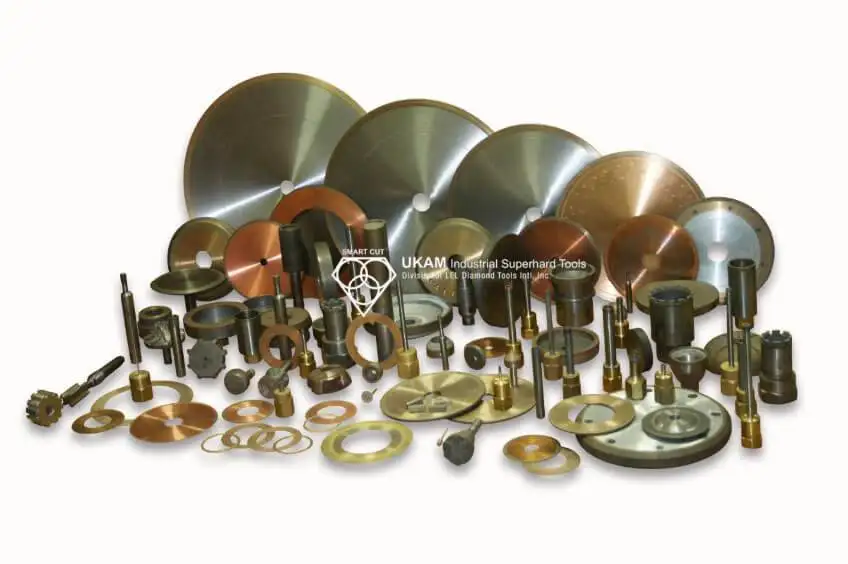
Diamond Tools
Sintered (Metal Bond)
UKAM Industrial manufactures and offers many types and forms of sintered (meta bond) diamond & cbn tools. Such as diamond wheels used for grinding, diamond cut off wheels use for cutting, dicing blades for singulation, diamond slotting wheels, drills, core drills, forming tools etc. Complex tool shapes can be made, Large variety of Diamond & CBN grit sizes from 300 to 3 microns can be used to achieve the clients desired surface finish, cutting speed, tool life and consistency. Diameters from small as .020″ (.5mm) to large as 20″ (500mm). Custom Tool specifications in this bond can be produced per your specification and requirements with short lead time.
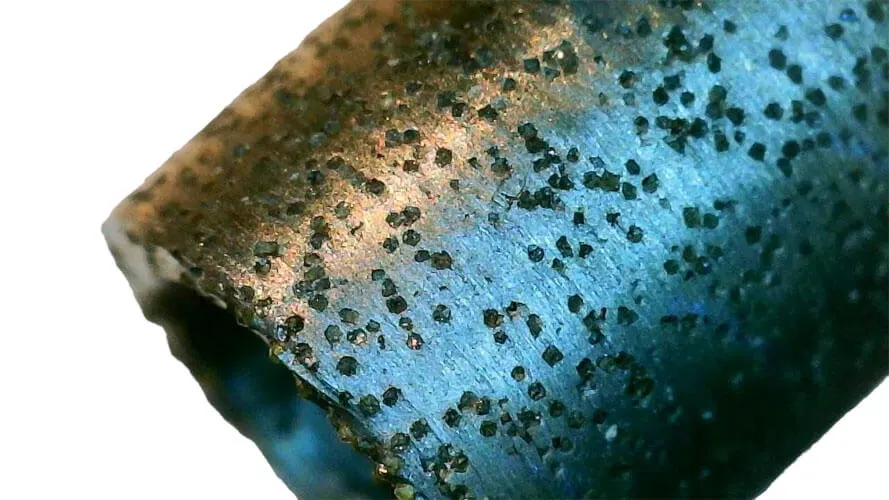
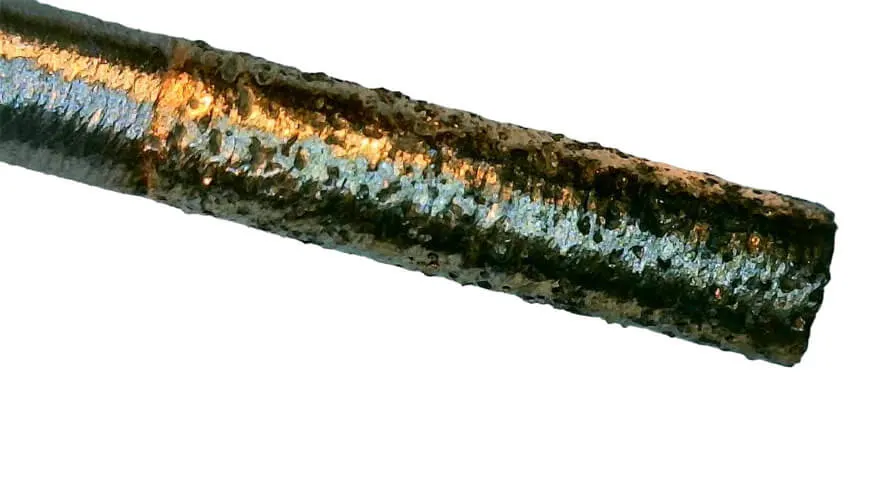
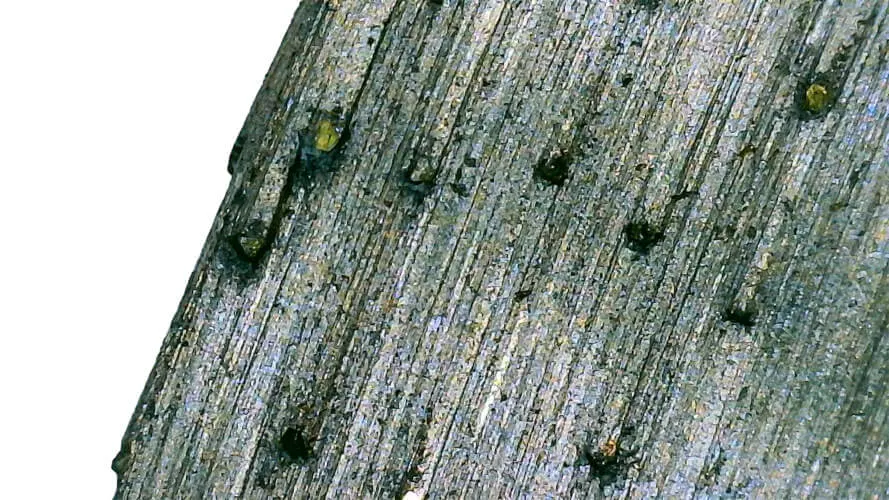
About Sintered (Metal Bond)
Sintered (metal bonded) diamond tools have multiple layers of diamonds impregnated inside the metal matrix. Diamonds are furnaces sintered in a matrix made of iron, cobalt, nickel, bronze, copper, tungsten, alloys of these powders or other metals in various combinations. Metal bonded diamond tools are “impregnated” with diamonds. This means that selected diamonds are mixed and sintered with specific metal alloys to achieve the best cutting performance possible on any materials such as sapphire, advanced ceramics, optics, glass, granite, tile and etc. The metal bond surrounding the diamonds must wear away to continuously keep re-exposing the diamonds for the diamond tool to continue cutting. Sintered (metal bonded) diamond tools are recommended for machining hard materials from 45 to 75 on rockwell scale (5 to 9.5 on mohe’s scale of hardness).
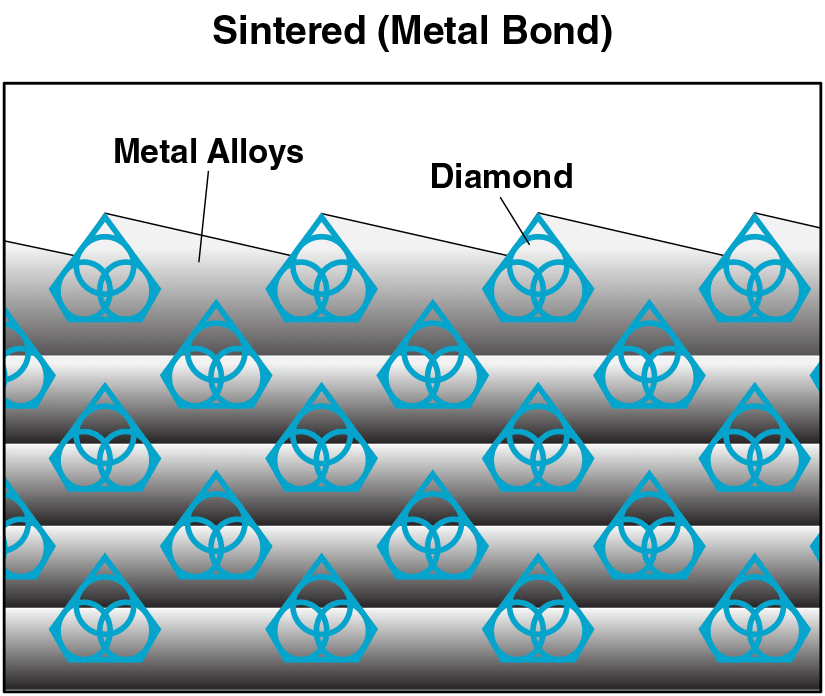
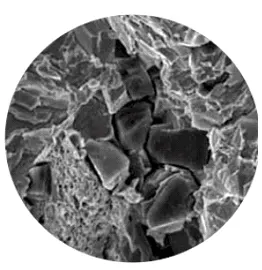
SEM Image of Sintered (Metal Bond) Materix
Application of
Sintered (metal bond) Tools
Sintered (Metal bond) diamond tools utilize various metallurgical powders to firmly keep the diamond crystals in place, with minimum wear. The compacted materials are then hot pressed or sintered to full density. Heating rate, applied pressure, sintering temperature and holding time, are all controlled according to the matrix composition. This means that selected diamonds are mixed and sintered with specific metal alloys to achieve the best cutting performance possible large variety of materials. This bond type can utilize the highest quality and grade industrial diamonds (strong and blocky shape) monocrystaline particles. For this reason this bond family requires higher horsepower equipment and lower cutting speeds. Compared to their resin bond, nickel bond, braised bond, and vitrified bond counterparts. Sintered (Metal bond) is the strongest of all the bond families. Offering the longest life, greatest variety of specifications and fields of use available. While its not the optimum solution for all applications, Its one of the most widely used bond across most industries today.
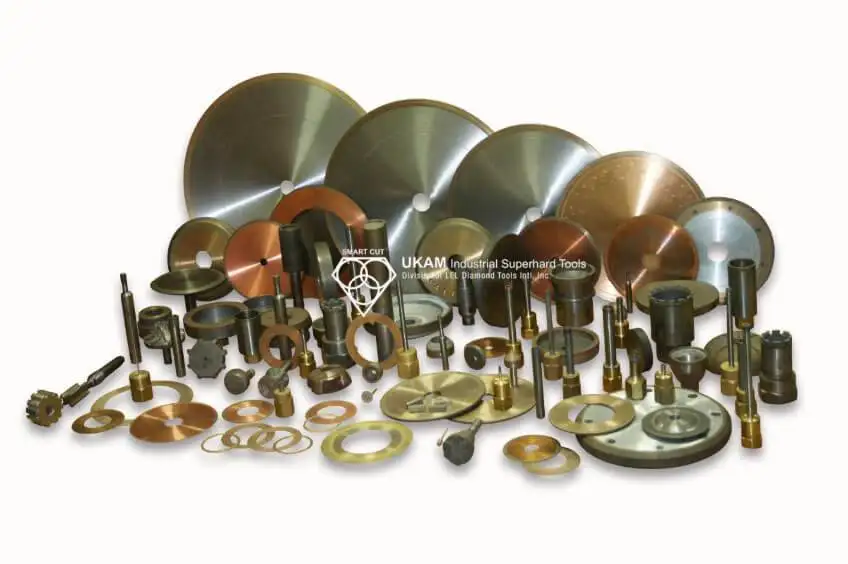
Diamond & CBN Tools
Resin Bond
UKAM Industrial Resin Bond Diamond & CBN diamond tools are manufactured with advanced molding process. Available in a large variety of diamond, thicknesses, arbor/mandrel sizes, geometries, diamond sizes, diamond concentrations, and bond harnesses. Over a hundred resin bond formulations are available using hundreds of various fillers, diamond coatings, resins, molding pressures, curing cycles & temperatures. We have a stock program that includes most popular resin bond tool specifications for various industries and custom manufacture based on your requirements.
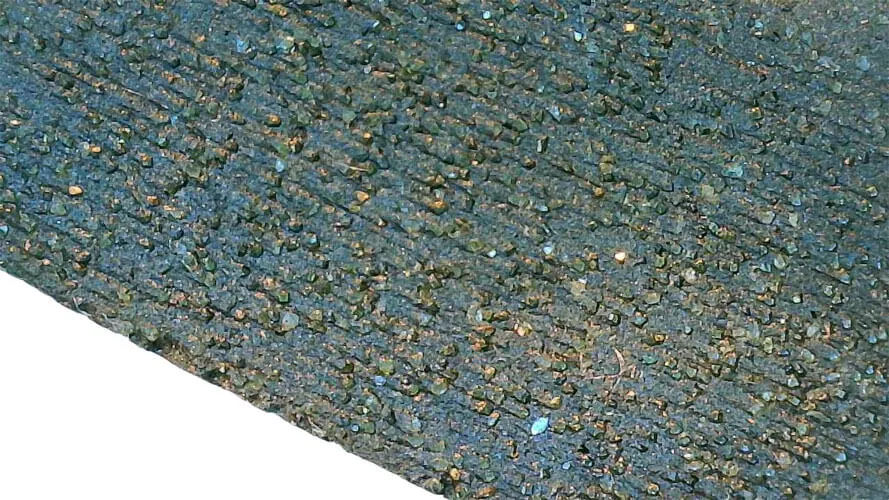
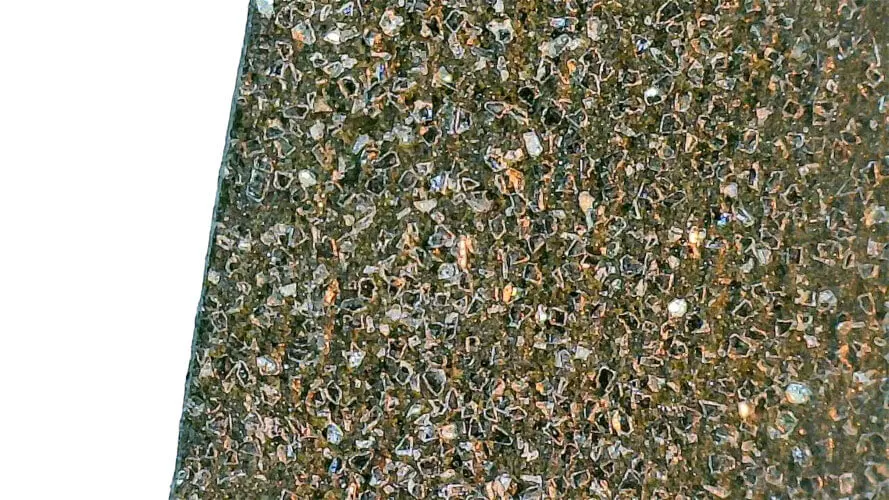
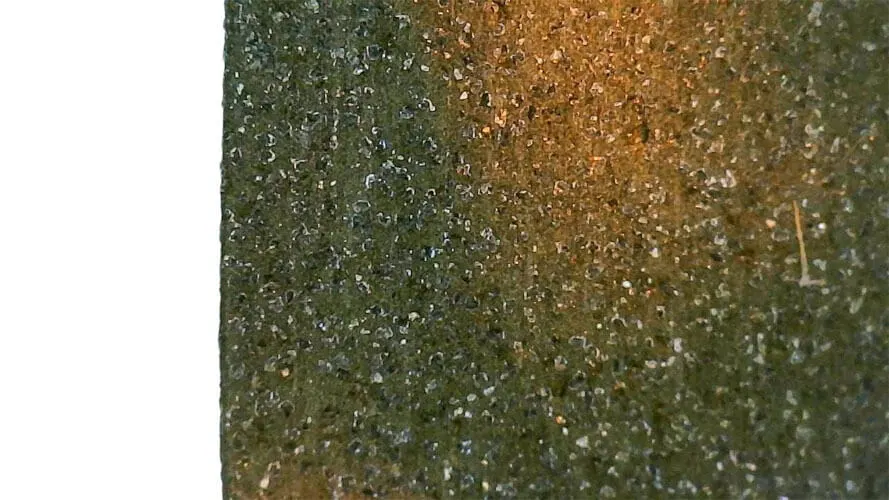
Application of
Resin Bond Tools
Recommended cutting, grinding and polishing hard, brittle or delicate materials including ceramics, glass tubing, optical glass, carbides, composites, silicon, magnetic materials, thermal spray alloys and exotic metals where low heat generation or improved surface finish is desired. Must be used at higher speeds. CBN, Resin bond Tools are recommended for cutting and grinding hard steels above Rc 60 at high speeds.
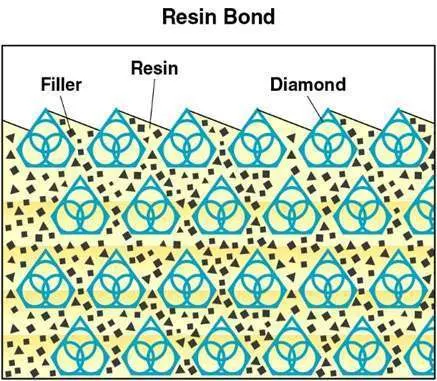
Advantages of
Resin Bond Diamond Tools
- Unmatched Cut Quality (eliminates secondary finishing operations)
- Faster & Freer Speed
- Less Heat Generation than other bond types
- Less Stress to material than other bond types
- Can be used dry (without coolant) when needed
- Can withstand Higher Temperature than sintered (metal bond) tools
- Perfect for fragile and delicate materials
- Minimize Chipping
- Improve Surface Finish
- Minimize Material Deformation
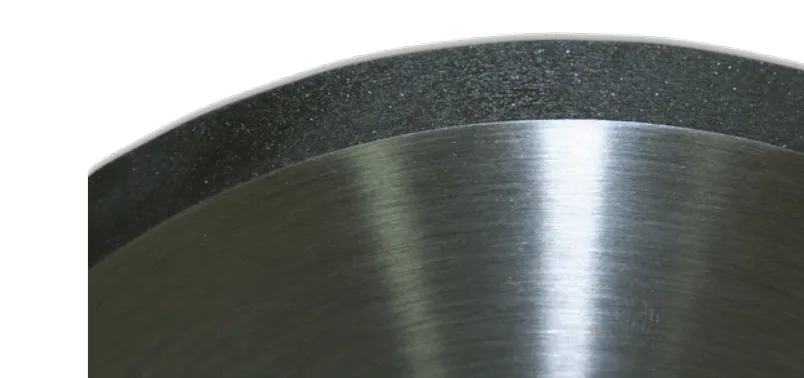
About Resin Bond
Its hardness, wear, heat resistance, diamond crystal retention and lubrication is controlled by use of various fillers organic and inorganic (usually ceramic or other metallic powders). Resin bond is low on Youn’s modulus, this gives it the free cutting characteristics for which this bond family is known. These properties is what gives this bond the fast cutting speeds, superior surface finish, and minimal chipping. Resin bond diamond tools are used at higher speeds, the most other bond families.
Resin bond diamond tools have shorter wheel life because the bond is much softer and brittle, and hence is not able to hold the diamond crystals in place as strong as its sintered (metal bond) counterpart.
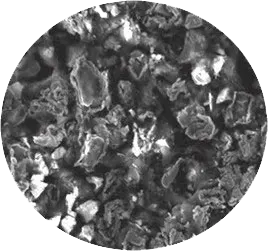
Diamond & CBN Tools
Hybrid Bond
UKAM Industrial manufactures and offers many types and forms of Hybrid bond diamond tools. Such as diamond wheels used for grinding, diamond cut off wheels use for cutting, dicing blades for singulation, diamond slotting wheels, etc. Complex tool shapes can be made,
Large variety of Diamond & CBN grit sizes from 250 to 3 microns can be used to achieve the clients desired surface finish, cutting speed, tool life and consistency. Diameters from small as .080″ to large as 20″ (500mm). Custom Tool specifications in this bond can be produced per your specification and requirements with short lead time
Application of
Hybrid Bond Tools
Hybrid bond diamond and CBN tools find extensive utility in a wide range of applications including cutting, slicing, dicing, grinding, polishing, milling, slotting, beveling, and numerous others, where both resin bond and sintered (metal bond) diamond tools are conventionally employed. These versatile tools offer remarkable adaptability across various industries.
Hybrid Bond Tools excel in grinding carbide and HSS tools, ensuring precision and efficiency in tool manufacturing. They are also indispensable in the manufacturing of electronic devices, particularly for slicing and dicing blades such as the delicate and slender 1 A8 blades, whether in single blade or multi-blade configurations. Additionally, when it comes to achieving a mirror finish on read-write head sliders, which are composed of hard and brittle materials like alumina titanium carbide (Al2O. TiC), a two-step process involving a metal-bonded tool and subsequent polishing step with a resin-bonded tool is commonly employed. However, with the advent of hybrid bond blades specifically designed for this purpose, both the slicing and polishing operations can be seamlessly executed in a single operation, streamlining the manufacturing process.
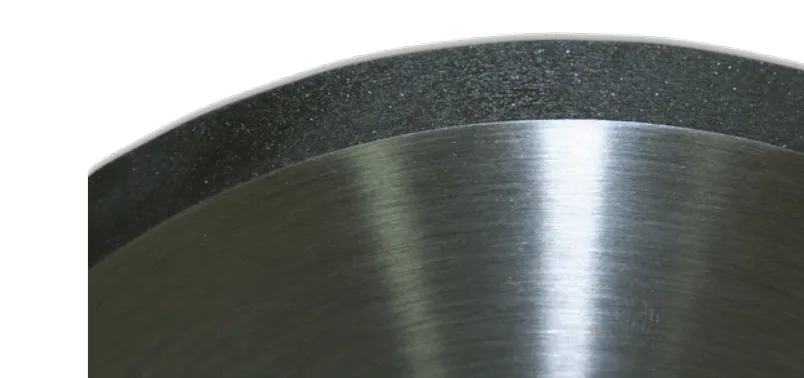
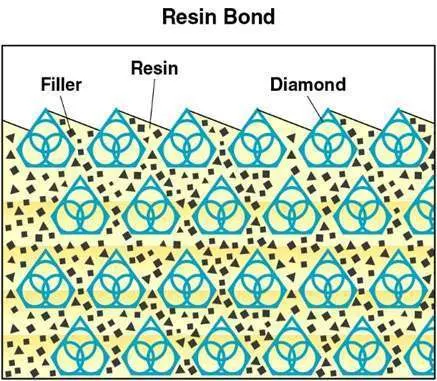
Advantages of
Hybrid Bond Tools
- Longer tool life
- Minimum chipping
- Improved surface finish
- Better edge retention
- More consistent performance
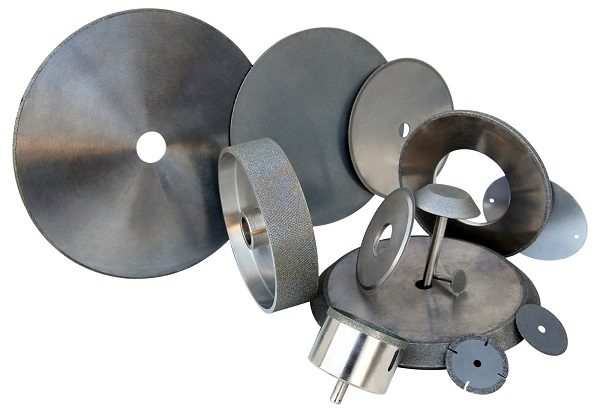
Electroplated (Nickel Bond)
Diamond & CBN Tools
UKAM Industrial Superhard Tools manufactures Precision Electroplated Diamond Products from 0.5 microns to 20 grit (diamond mesh size) in Synthetic, Natural Diamond or CBN (cubic boron nitride). For a large variety of applications, materials, and industries.
We have a stock program that includes most popular electroplated specifications for various industries and custom manufacture based on your requirements.
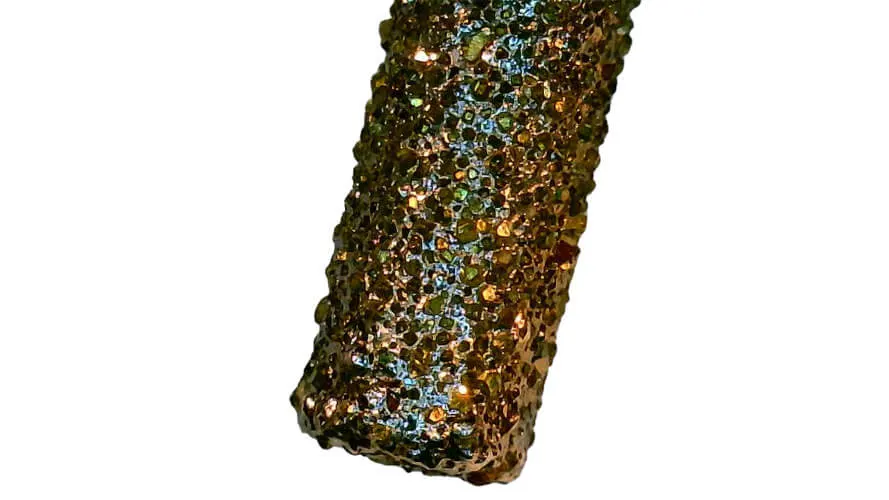
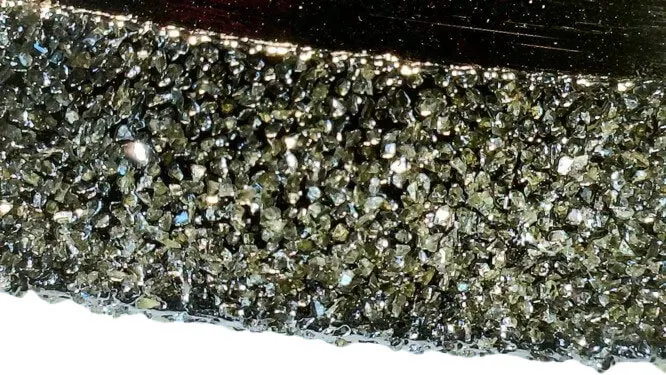
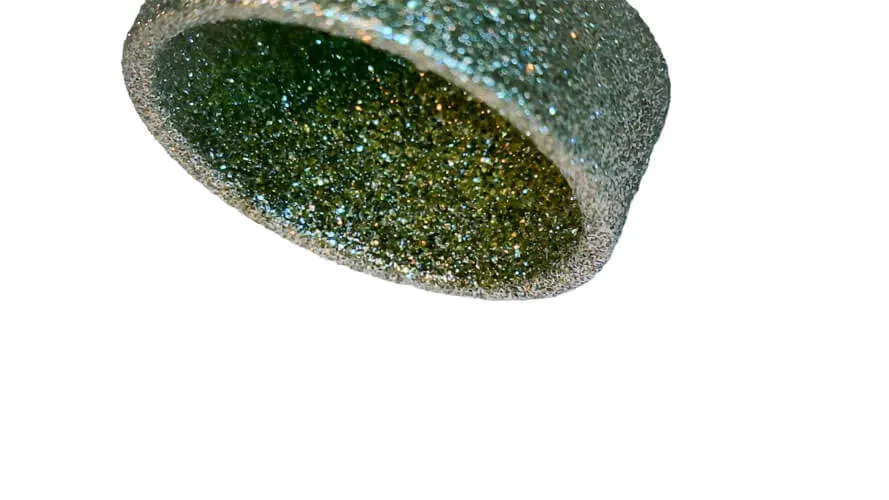
Tools can produce just about any type or shape of electroplated tools, from print supplied by you, or we will plate a blank your provide
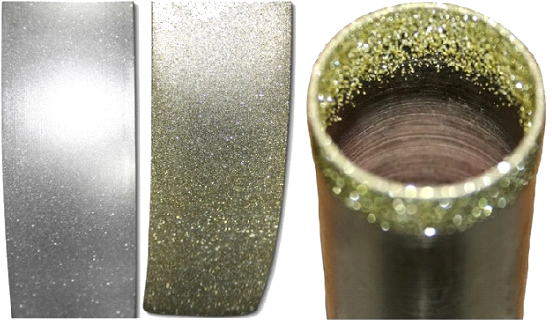
Advantages of Electroplated Diamond Tools:
- Free Cutting Action - better removal rates and less thermal damage to the part
- Good Form Holding Characteristics - -hold simple and intricate forms for the entire life of the tool or wheel, from first grind to last.
- Maximum Abrasive Particle Exposure
- High Stock/Material Removal Rates - Lower long term cost with the potential reduction or elimination of time associated with set-up, dressing and tool changes.
- Reusable - striped & replated with potential savings of 25% over new electroplated products.
About Nickel Bond
(Electroplated) Tools
Electroplated (nickel bond) diamond products usually have a single layer of diamonds, held by a tough durable nickel alloy. Nickel is frequently used as a base for plating diamond. Because of its excellent strength, toughness and flexibility during the plating process. Electroplated diamond products are able to retain their original shape and dimensions thought their working life. Unlike sintered (meal bond) or resin bond diamond products, where diamond particles are buried in bond and held together by metal or resin binder deep inside.
Electroplating allows diamond particles to protrude from the bond matrix, providing a free, faster cutting action with minimum heat generation.
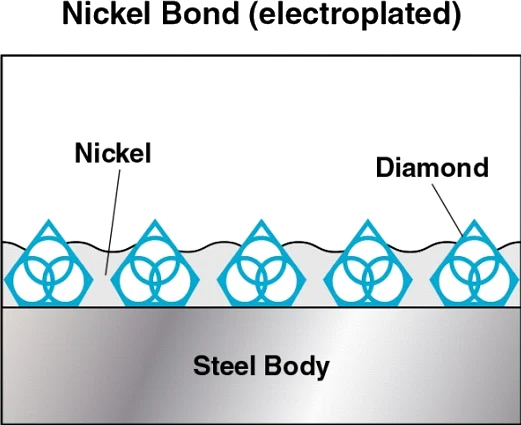
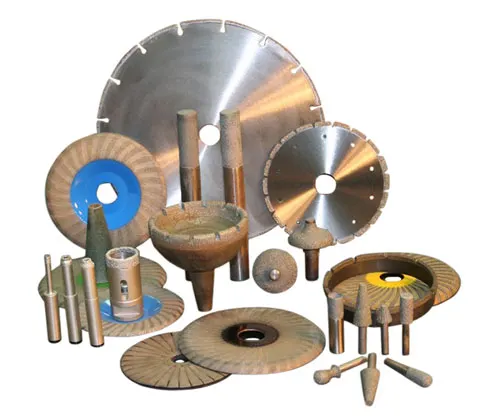
Diamond & CBN Tools
Braised Bond
UKAM Industrial manufactures and offers all types and forms of braised bond diamond tools. Such as diamond wheels used for grinding, diamond cut off wheels use for cutting, diamond core drills and bits used for drilling, reaming and milling. Diamond router bits, carving points and form tools used for shaping and forming. Complex tool shapes can be made,
Large variety of Diamond & CBN grit sizes from 40 to 1,200 mesh can be used to achieve the clients desired surface finish, cutting speed, tool life and consistency. Diameters from small as .080" to large as 30". Popular specifications that are used across many different applications are kept in stock as part of our standard stock program. Custom Tool specifications in this bond can be produced per your specification and requirements with short lead time.
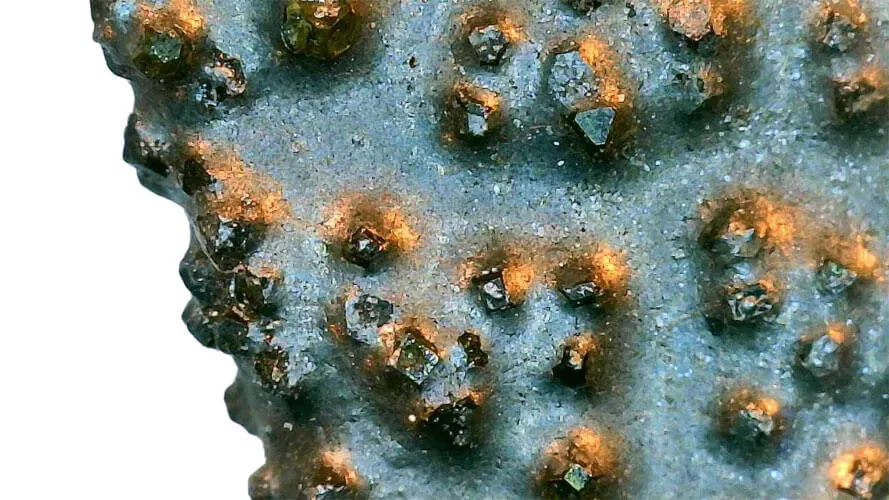
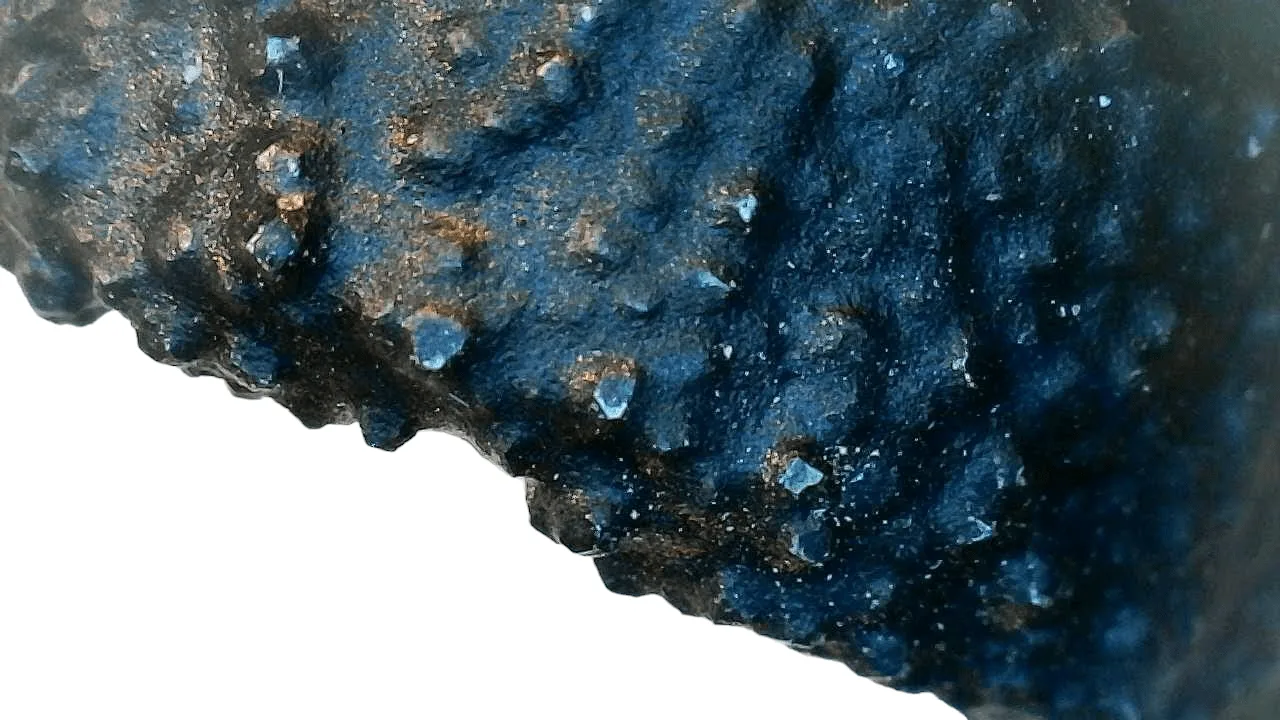
Application of Brazed Bond Tools
Brazed Bond Diamond Tools are perfect for machining tough-to-cut materials where fast stock removal and deep cuts are required. Including applications such as: non-metallic materials such as graphite epoxy, FRP, graphite, fiberglass, friction material, honeycomb and other composites.
Examples of Industries Used in
- Ophthalmic Lens
- Composites
- Construction
- Quartz
- Carbide
- Silicon
- Granite / Marble
- Fired and pre-fired Ceramics
- Plastics Industry
- Glass
- Graphite
- Ceramics (pre fired & post fired)
About Brazed Bond
Brazed Diamond Tools are produced using and process that creates a fusion between the diamonds and the metal bond. While they may appear similar to electroplated (nickel bond) diamond tools. They are produced utilizing completely different process. Brazed Bond Diamond Tools are produced inside vacuum oven at a high temperature, single layer of diamond crystal bonded to steel body with very high diamond exposure. Not only does it promote high diamond exposure, but it also eliminates the loss of diamond particles through pull-out. The diamond section will not strip or peel from the steel body. This translates into multiple benefits, including: aggressive tools that last longer, cut faster, run cooler and load less, providing increased productivity and part consistency.

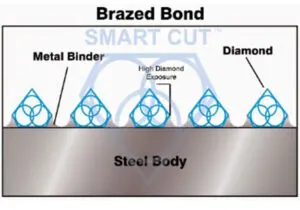
Advantages of
Brazed Bond Diamond Tools
- Very fast & aggressive cutting speed
- Maximum diamond crystal exposure
- Ideal for hard to machine materials
- Strong retention of diamond grits
- Can be used at faster cutting speeds
- Can be used dry and tough environments
- Less Required Power
- Capability to Retain Form
- Minimizing & Often Eliminating Need for Dressing
- Ability to Strip and re-plate the tool (re-use)
- Lower Cost
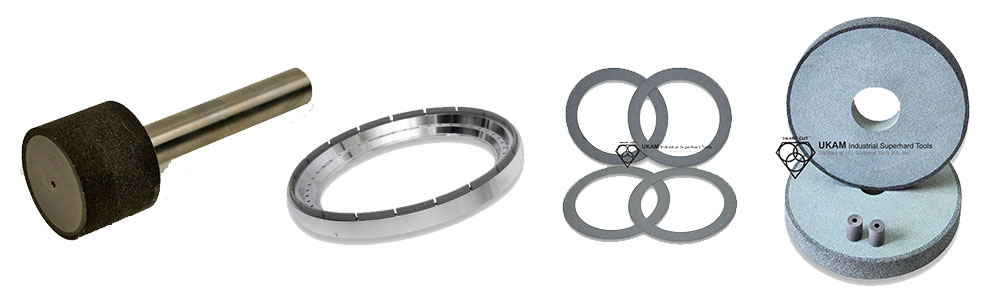
Vitrified Bond
Diamond & CBN Tools
UKAM Industrial offers large variety of vitrified diamond & CBN Tools for many different applications. Vitrified bond tools are produced in a large variety of diamond, thicknesses, arbor/mandrel sizes, geometries, diamond sizes, diamond concentrations, and harnesses. High precision tolerances can be maintained. All vitrified bond tools are made to order.
Application of
Vitrified Bond Tools
Automotive parts grinding, Paper Manufacturing Industry, Bearing Industry, Aerospace industry, Turbine Industry, Grinding of PCD and PCBN, Profile grinding of TC threading plates, OD grinding of Printing Rolls, Shafts and Rods, Flat grinding of Ceramic components, Flat, OD and ID grinding operations of various parts, Grinding of Camshafts and Crankshafts, Finishing of turbine parts
Advantages of
Vitrified Bond Diamond Tools
- Very fast cutting speeds
- Best used for superhard materials
- Very free cutting
- Ability to control prosity
- Self dressing/sharping
- Primarily used for grinding applications
- Profile easily during grinding along edges
- Longer life than resin bond diamond tools
About Vetrified Bond
Vitrified Bond is a Fired Ceramic Bond matrix, which is very brittle and porous. Also known as ceramic bond. Based on fusible glasses combined with fillers and abrasive grains. Offers durability of sintered (metal bond), along with free cutting action of resin bond. Vitrified bond has higher bonding strength then resin bond. Vitrified bond diamond tools are free cutting, produce good surface roughness, have good wear resistance and retain straightness and form very well.
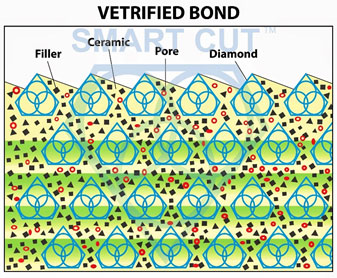
Diamond & CBN Bond Type Characteristics
The retention of diamond and CBN crystals is crucial for cutting tool performance. Brazed and Sintered bonds excel in retaining these crystals for heavy-duty tasks, while Nickel bonds also provide strong retention suitable for robust applications. Vitrified bonds balance retention with cooling for high-speed operations, whereas Resin bonds, ideal for softer materials, offer the least crystal retention, focusing on flexibility and smooth finishes.
Retention of Diamond/CBN Crystals
The ability of a bond to retain diamond or CBN crystals during the cutting process is crucial, especially for applications where durability and cutting precision are key. Among the various bond types, Brazed and Sintered (Metal) bonds are the top performers when it comes to retaining crystals. The strong retention characteristic of these bonds makes them ideal for heavy-duty applications such as cutting hard materials, where the longevity of the cutting edge is important to avoid frequent tool changes. These bonds are engineered to hold onto abrasive crystals even during high-intensity cutting operations, ensuring consistent cutting performance and prolonging the life of the tool.
Nickel bonds also exhibit commendable retention, benefiting from the galvanic process in which diamond or CBN particles are mechanically held. This ensures that the abrasive grains stay firmly in place, making it suitable for tasks that demand strong retention without compromising on cutting efficiency.
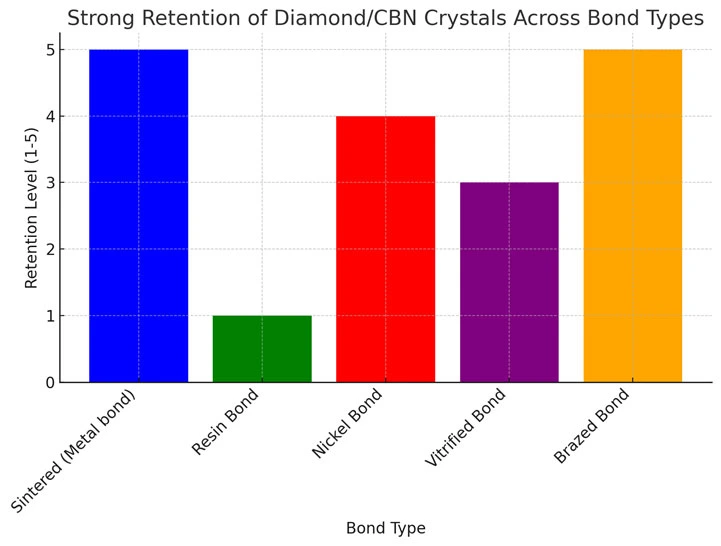
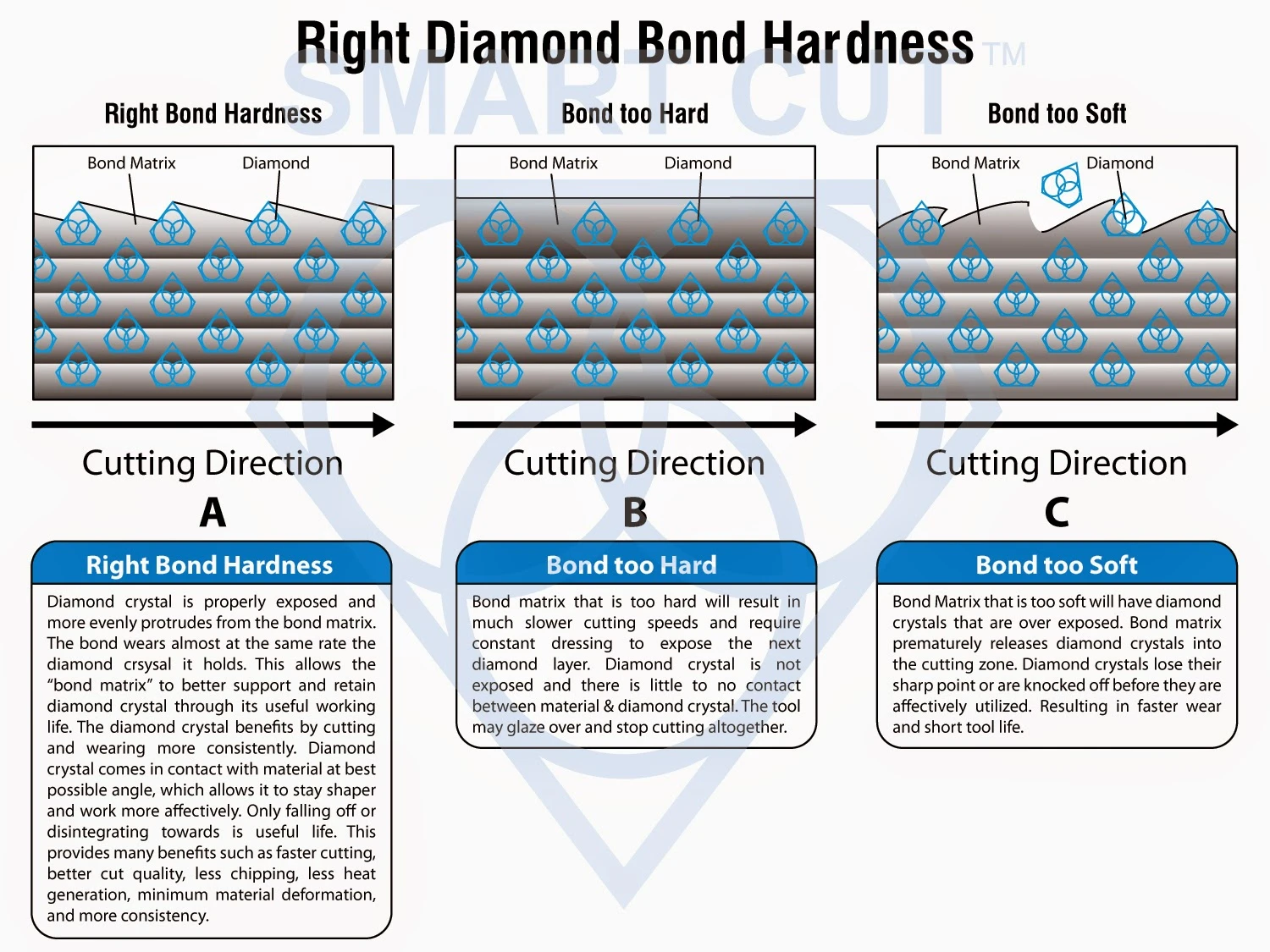
Vitrified bonds, on the other hand, offer a balanced performance in terms of retention. While they are designed for rapid cutting and high porosity, which promotes cooling and material clearance, their retention capability is slightly lower compared to metal bonds, but sufficient for many high-speed operations.
At the lower end of the spectrum, Resin bonds provide the least retention of diamond and CBN particles. Resin bonds are typically used in applications where softer materials are involved, or where a smoother finish is more important than strong abrasive retention. Due to the more flexible nature of resin, the bond wears down faster, and the retention of abrasive particles is reduced, making it suitable for short, precise cutting tasks rather than prolonged heavy-duty operations.
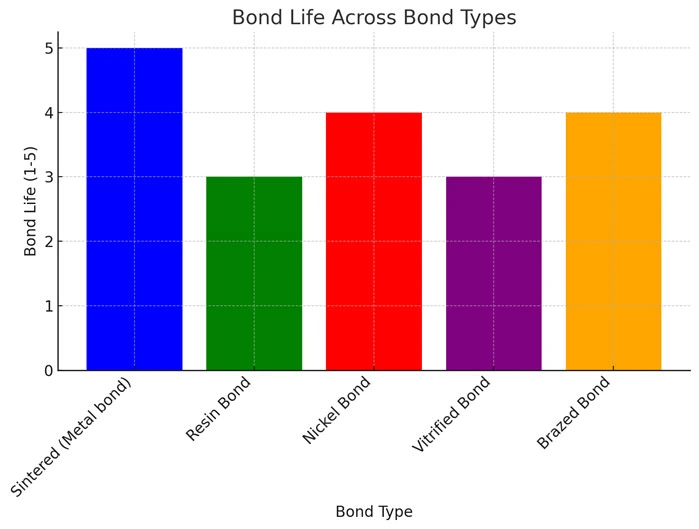
Bond Life
Bond life plays a significant role in determining the overall cost-effectiveness and efficiency of a diamond or CBN tool. Sintered (Metal) and Brazed bonds are known for their exceptional durability, offering the longest bond life among the available options. These bonds are particularly favored in industries where tools are subjected to high levels of stress and where a long operational life is critical. Sintered bonds, in particular, are built to last, with their robust structure providing wear resistance and maintaining cutting efficiency over long periods. This makes them a go-to option for applications involving the cutting of dense and abrasive materials, such as ceramics or metals.
Brazed bonds share similar longevity with Sintered bonds. Their durability is coupled with the ability to perform high-speed cuts, making them a preferred choice for applications that require a combination of speed and tool life. Nickel bonds offer slightly less longevity but are still highly durable.
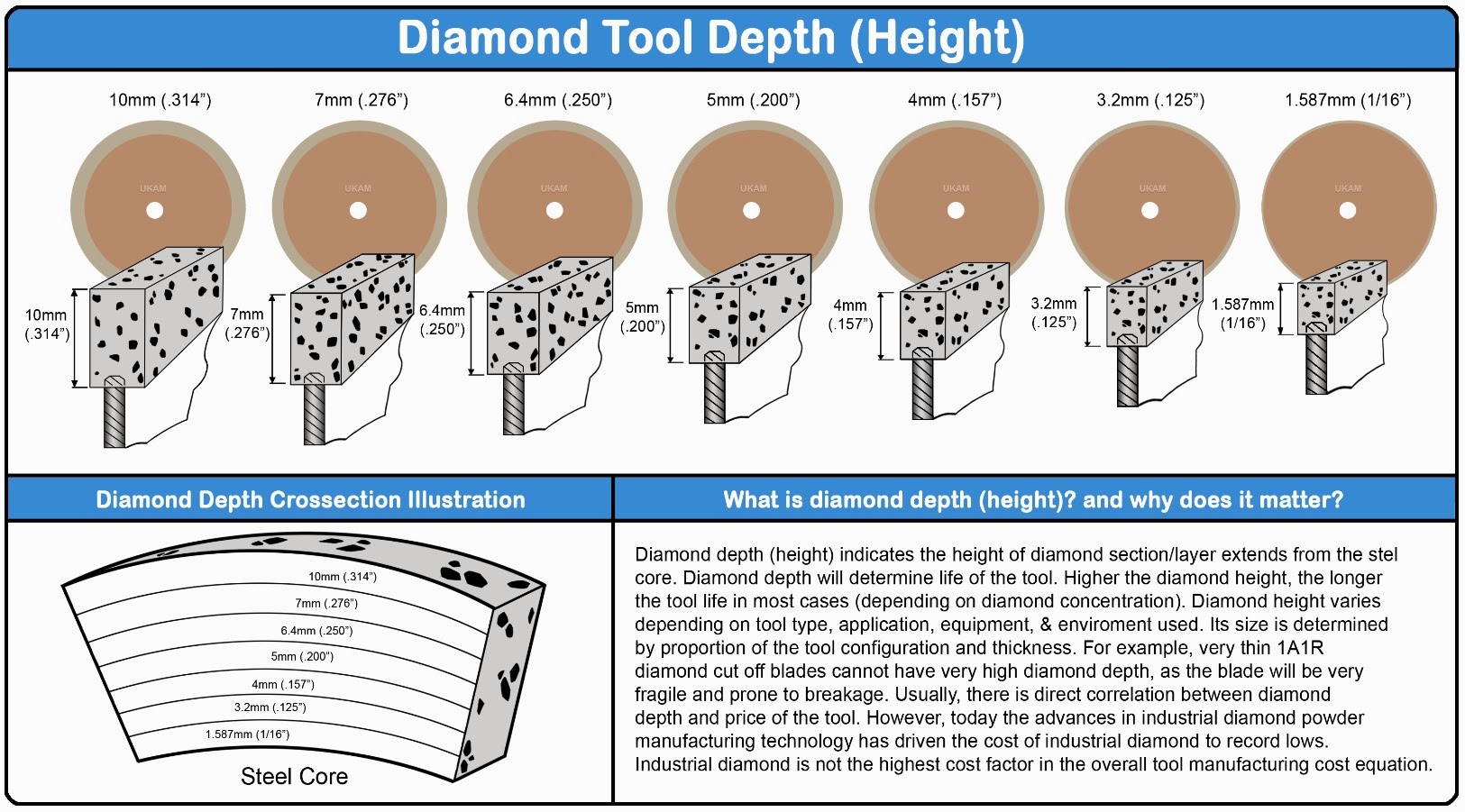
Nickel bonds provide a good balance between long bond life and cutting performance, particularly for specialized applications such as cutting composites or glass, where toughness and longevity are both important.
On the other hand, Vitrified and Resin bonds offer shorter bond lives. Vitrified bonds are known for their cutting speed and porosity, which makes them ideal for applications requiring high material removal rates. However, this focus on speed comes at the expense of bond life. Vitrified bonds are more brittle, and while they cut fast, they tend to wear down quicker. Resin bonds, being softer and more flexible, also have shorter lifespans. They are more suitable for applications where frequent tool changes are acceptable, and precision is more important than tool longevity, such as in the cutting of softer materials or in fine-detail work.
Surface Finish
Achieving a smooth and high-quality surface finish is critical in industries such as optics, electronics, and advanced ceramics, where the precision of the cut directly impacts the quality of the final product. Resin bonds are unmatched in their ability to provide the best surface finish, making them ideal for applications where a chip-free and clean cut is essential. The softness of the resin bond allows for a gentle cutting action, minimizing damage to the material and producing a smoother surface. This makes Resin bonds particularly suitable for cutting softer, more delicate materials such as certain composites or glass, where a fine finish is paramount.
Nickel and Vitrified bonds also perform well in providing a high-quality surface finish. These bonds are often chosen for applications where a balance between cutting speed and surface quality is required. Nickel bonds, due to their ability to expose sharp diamond or CBN particles consistently, ensure that the cutting edges remain efficient throughout the process, resulting in a smooth cut.
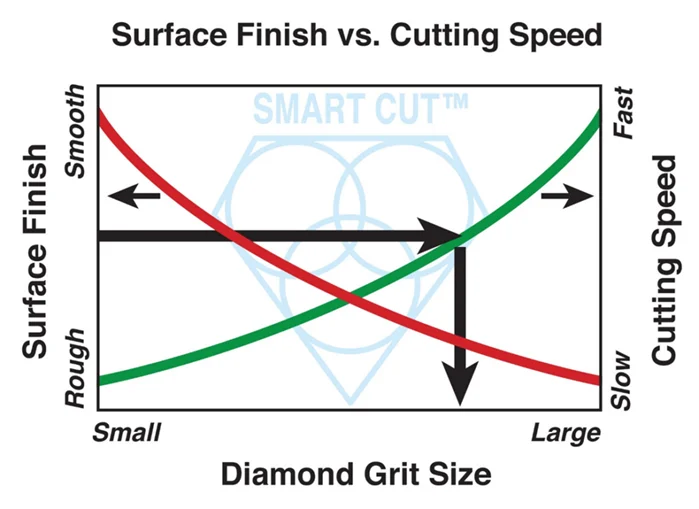
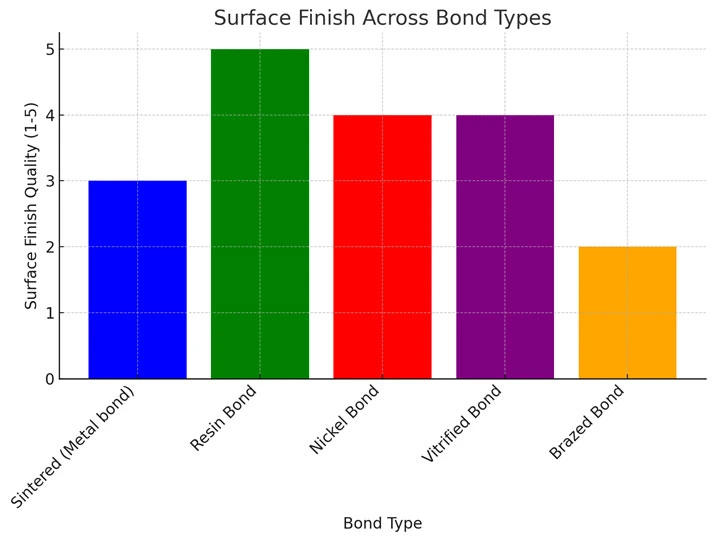
Vitrified bonds, while primarily designed for speed, offer good surface quality as well, thanks to the bond’s porosity, which helps in cooling the cutting edge and removing debris from the cut surface.
Sintered (Metal) and Brazed bonds, while excellent in terms of durability and cutting speed, are not typically selected for applications that demand a high-quality surface finish. These bonds are more focused on robust material removal, and as a result, the cuts they produce tend to be rougher compared to Resin or Nickel bonds. This makes them more suited for rough cutting operations where surface finish is not a primary concern.
Diamond/CBN Particle Exposure
The exposure of diamond or CBN particles during cutting operations directly influences the cutting speed and efficiency of a tool. Brazed and Nickel bonds stand out as the leaders in maximizing particle exposure. This characteristic allows for faster cutting speeds, as the cutting particles are more exposed to the material being processed, thereby increasing the material removal rate. Brazed bonds, in particular, are known for their aggressive cutting action, making them ideal for high-speed applications involving hard materials like metals and stone. Nickel bonds, with their galvanic construction, offer excellent particle exposure, which contributes to efficient cutting in applications like composites or geology.
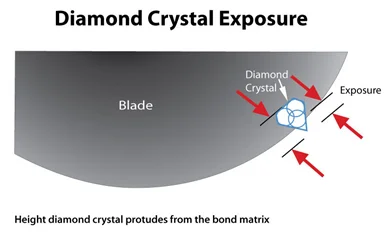
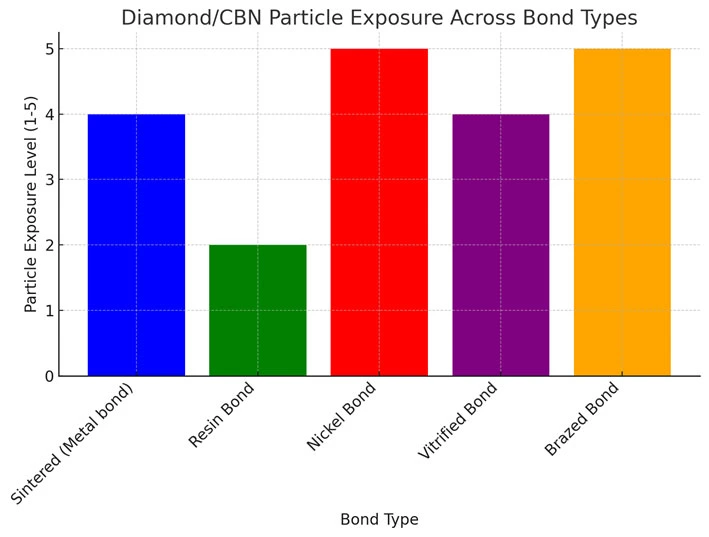
Vitrified and Sintered (Metal) bonds provide moderate particle exposure. In Sintered bonds, the diamond or CBN particles are embedded in the bond matrix, which wears down at a slower pace. This controlled wear helps in maintaining consistent exposure of new cutting particles, offering a steady cutting performance, though at a slower rate than Brazed or Nickel bonds. Vitrified bonds, while faster in terms of cutting speed, offer a similar level of particle exposure, providing a good balance between speed and exposure.
Resin bonds, however, have the lowest level of particle exposure. This is because Resin bonds are designed for more delicate and precise applications, where aggressive cutting is not required. The lower exposure of particles ensures a smoother, more controlled cut, making Resin bonds ideal for precision tasks rather than fast material removal.
Cutting Speeds
Cutting speed is a critical factor in productivity, especially in industries where high-volume production or rapid material processing is necessary. Brazed, Vitrified, and Resin bonds are all known for their ability to operate at high cutting speeds. Brazed bonds, with their excellent particle exposure and durability, are particularly well-suited for aggressive, high-speed cutting tasks, making them a favorite for tough materials like metals, stone, or construction materials. Vitrified bonds, designed for high-speed operations, offer fast cutting thanks to their porous structure, which allows for better cooling and debris removal during the cutting process. This makes Vitrified bonds ideal for applications where speed is critical, such as in sample preparation or advanced ceramics.
Resin bonds, while providing high cutting speeds, are more specialized for applications requiring precision and clean cuts. They work well at high speeds in softer materials where surface finish is more important than durability.
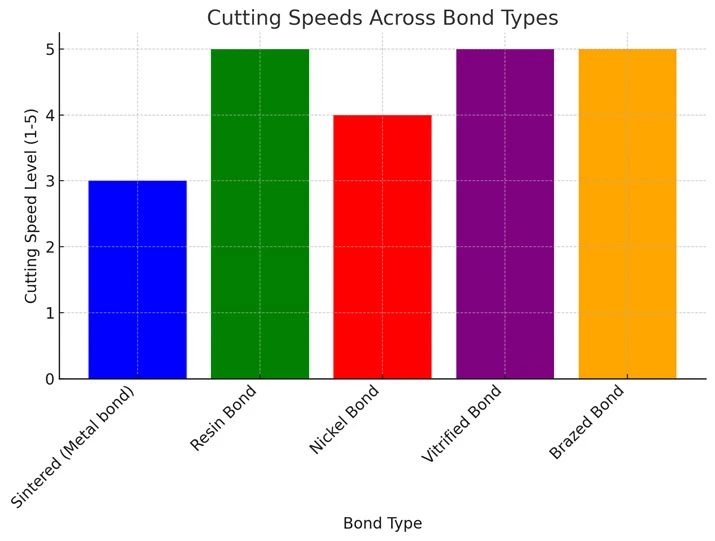
Nickel bonds, though slightly slower than Brazed or Vitrified bonds, still offer commendable cutting speeds, particularly in specialized applications like cutting composites or glass. The strength of the Nickel bond allows for consistent cutting without frequent tool changes. Sintered (Metal) bonds, on the other hand, provide the slowest cutting speeds among the bond types. While they excel in durability and longevity, their slower cutting speed makes them more suitable for applications where robustness and precision over long durations are more important than quick material removal.
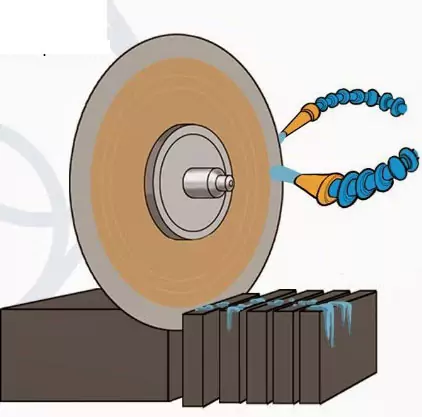
Dressing Frequency
Dressing frequency is crucial for maintaining the efficiency of diamond and CBN tools. The need to dress depends on the bond type, the material being processed, and the desired cutting performance. Each bond type has its own characteristics, affecting how frequently dressing is required.
Sintered (Metal) bonds are among the most durable, requiring infrequent dressing due to their tough metal matrix that wears down slowly. This slow wear allows steady exposure of fresh abrasive particles, making these bonds excellent for long-term, high-stress applications. However, when they do require dressing, it often needs to be done with strong tools to break through the metal structure.
Resin bonds wear down faster than metal bonds and expose new abrasive particles more readily, which reduces the need for frequent dressing.
However, they can become loaded with material debris, especially when cutting softer materials, requiring occasional light dressing to clean the bond and maintain cutting efficiency. Compared to metal and vitrified bonds, resin bonds have moderate dressing needs, but the process is generally quick and straightforward.
Nickel bonds, due to their electroplated construction, do not need frequent dressing and are designed for precision applications. Their wear tends to be controlled, maintaining sharp cutting edges over time. However, debris can build up on the bond layer, requiring occasional mild dressing to restore the tool's performance without damaging the bond.
Vitrified bonds require more frequent dressing compared to other bonds due to their porous, glass-like structure, which wears down faster, especially in high-speed applications. Although the bond is designed for efficient cooling and material removal, the brittle nature of vitrified bonds means that dressing is necessary to maintain sharpness and porosity. Fortunately, the dressing process is often quick and easy.
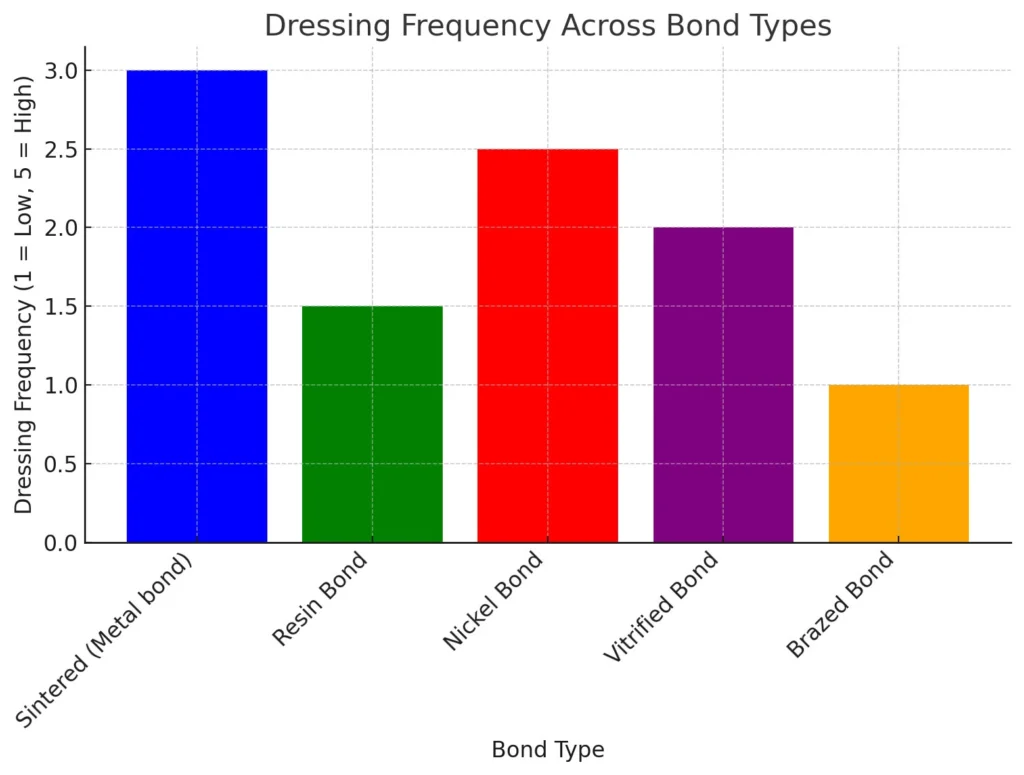
Brazed bonds have a strong crystal retention design, exposing abrasive particles fully for aggressive cutting and requiring minimal dressing. These bonds are structured for high-speed, long-duration cutting, and the dressing is mainly for cleaning rather than restoring sharpness, allowing consistent performance over extended use.
When comparing dressing frequencies, sintered (metal) and brazed bonds require the least maintenance, while nickel bonds need periodic touch-ups for debris buildup. Vitrified bonds need more frequent dressing due to their faster wear, and resin bonds, while self-sharpening, still require occasional dressing to maintain surface finish and prevent loading.
Comparing Cost
The cost of diamond and CBN tools varies significantly by bond type, with each offering a balance between cost, performance, and durability. Sintered (Metal Bond) tools are generally the least expensive due to their simpler manufacturing process and durable matrix, making them cost-effective for many applications. Electroplated (Nickel Bond) tools come next in cost, offering precise particle retention and strong performance at a moderate price.
Brazed Bond tools are slightly more expensive due to their high crystal exposure and aggressive cutting ability, which makes them suitable for demanding tasks. Resin and hybrid bonds are higher in cost, largely due to their self-sharpening properties, surface finish quality, and adaptability to various materials. Vitrified Bond tools are the most expensive because of their ceramic-like structure, which provides superior cutting speed, porosity, and precision, making them ideal for high-end, high-speed applications.
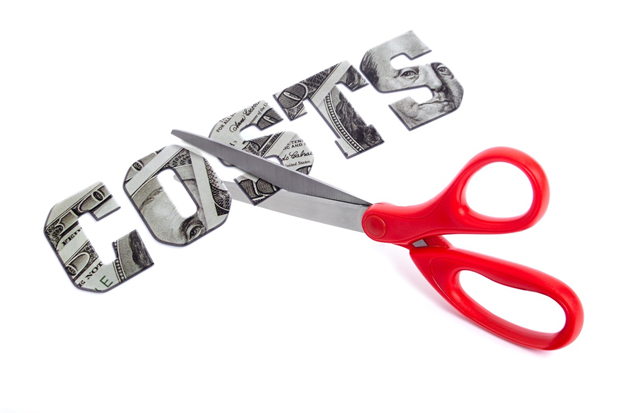
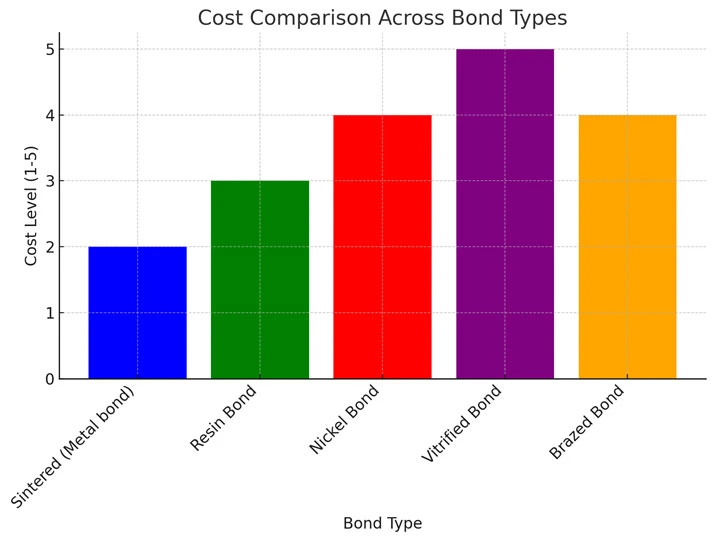
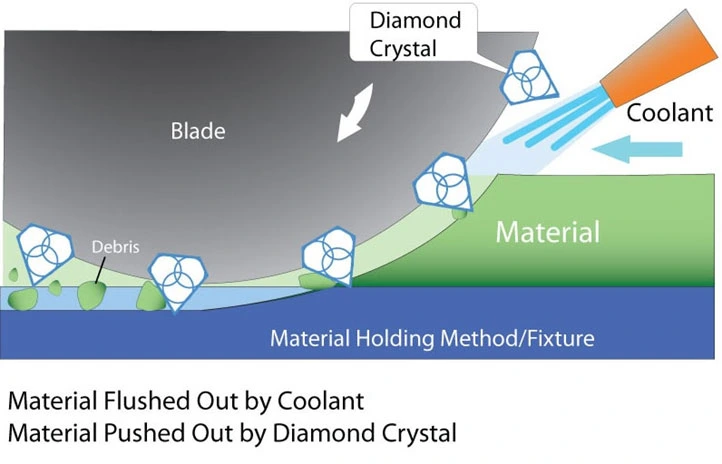
Coolant Use
Coolant plays a crucial role in diamond tool operations, essential for minimizing heat generation, enhancing cutting efficiency, and extending tool life. The need for coolant varies significantly across different bond types used in diamond tools, each responding differently based on its material composition and the specific requirements of the cutting process.
Sintered (Metal Bond) tools are frequently employed in cutting hard materials, where the use of coolant is often essential. The coolant helps dissipate heat efficiently, thereby prolonging the tool life. While the necessity for coolant might not be constant across all applications, its use in scenarios that demand minimal heat generation can dramatically boost both performance and durability of the tools. Sintered bonds, with their robust structures, are particularly suited to benefit from coolant applications that enhance their cutting capabilities while preventing premature wear.
Resin Bond tools derive significant advantages from coolant usage. These tools are designed to handle various thermal loads efficiently. However, applying coolant can fine-tune the cutting conditions, significantly reducing the risk of thermal damage and ensuring a superior finish. Consistent application of coolant is recommended to preserve the integrity of the bond and maintain high-quality cuts. This is particularly important in precision cutting operations where the quality of the finish is critical.
Nickel Bond tools generally require less coolant than other types, thanks to the inherent thermal properties of nickel which allow these tools to manage heat generation effectively. These tools are characterized by a higher level of diamond protrusion and exposure, which facilitates better cutting action. However, using a controlled amount of coolant is beneficial as it enhances the cutting process and prevents the bond from clogging, especially when dealing with materials that produce substantial debris.
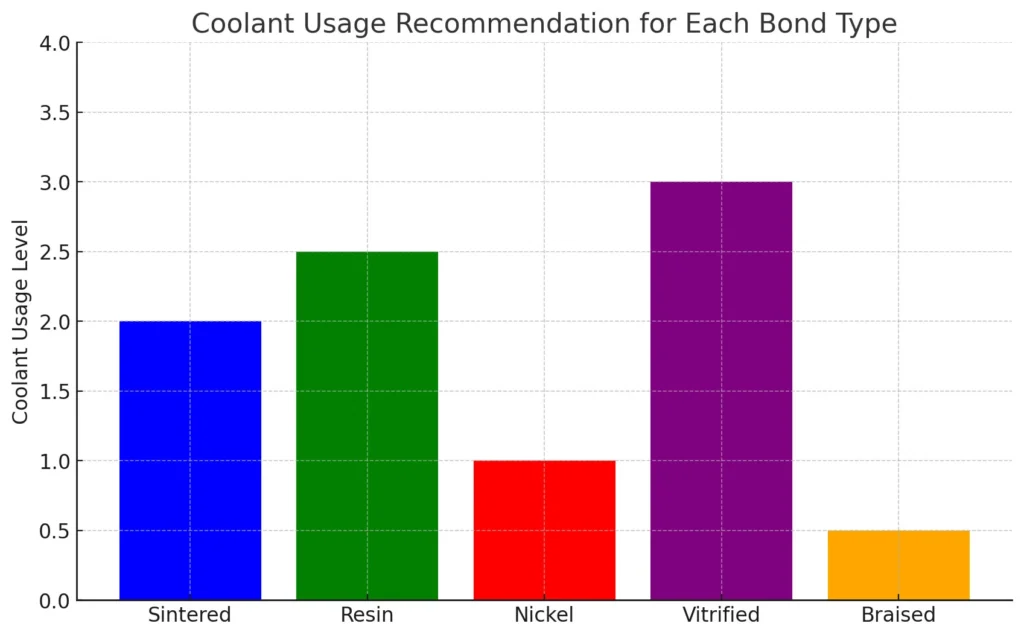
Vitrified Bond tools necessitate a consistent application of coolant due to their inherently porous structure. This characteristic is advantageous as it aids in maintaining optimal temperatures and efficiently clears out swarf, thereby preventing overheating and potential thermal damage. A regular flow of coolant is essential to fully exploit the capabilities of vitrified bonded tools, maximizing their performance and durability.
Braised Bond tools require the least amount of coolant, primarily due to their robust nature and high thermal conductivity. This bond type also features the highest diamond exposure ratio, enhancing its cutting capabilities. Nonetheless, in precision applications or when processing heat-sensitive materials, a minimal application of coolant is advantageous. It helps minimize any potential thermal effects and enhances the cutting quality, ensuring precise and clean cuts.
Application Across Various Industries
Diamond and CBN tools find applications across a diverse range of industries, with each industry favoring specific bond types that align with its unique requirements. In this overview, we will explore how different bond types are preferred based on their distinct attributes and how they perform in various applications. This analysis helps us uncover valuable insights into the appropriateness and efficacy of each bond type within distinct industry sectors, highlighting why certain bonds are more suitable for particular tasks than others.
Sintered (Metal Bond) bonds are extensively used in a variety of industries due to their strong retention of diamond crystals, offering high durability and efficiency. These bonds are particularly favored in fields such as geology, construction, and lapidary where abrasive tools are essential for processing hard materials.
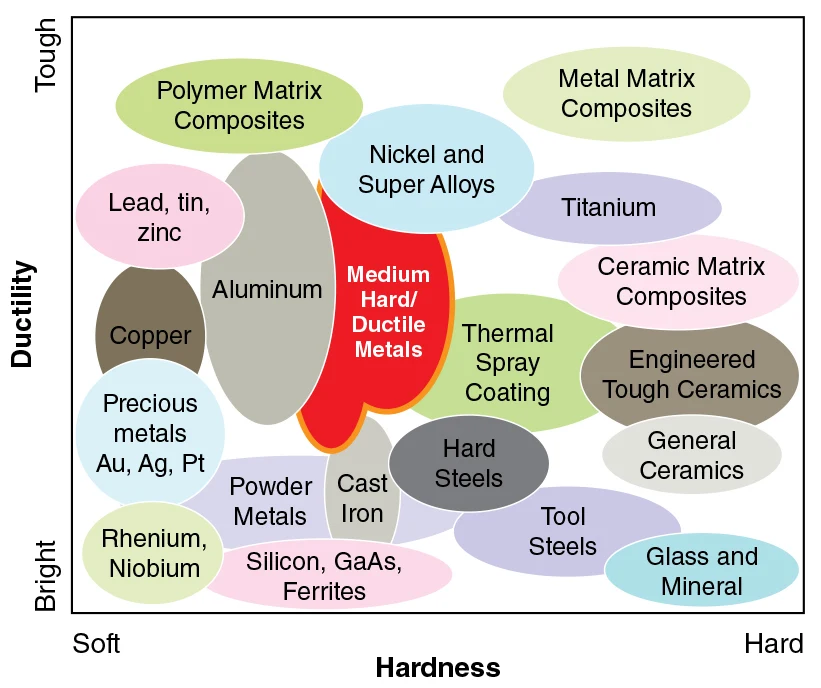
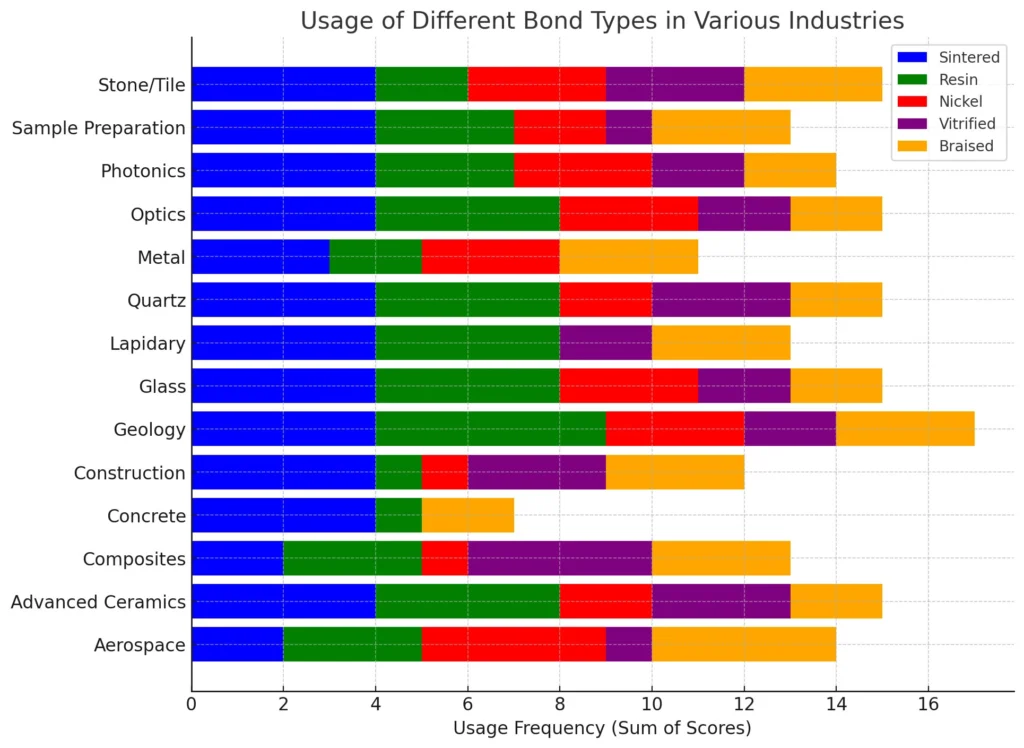
Resin Bond tools are appreciated for their softness and self-sharpening characteristics, making them ideal for precision applications that require a smooth finish. Industries like optics and photonics extensively utilize resin bonds to achieve high-quality surface finishes. They are also popular in handling advanced ceramics and composites, showcasing their versatility in specialized applications.
Nickel Bond tools are moderately used across several sectors, with significant applications in aerospace and photonics. These bonds are chosen for their precision and material integrity, essential for cutting high-strength materials where precision is critical.
Vitrified Bond tools are particularly valued in the metal and advanced ceramics industries for their fast cutting speeds and ability to effectively manage cooling and debris removal through controlled porosity. Their properties make them suitable for high-stakes environments that demand precision and efficiency.
Braised Bond tools, though less frequently used, are preferred in specific industries such as aerospace and stone/tile. These bonds are selected for their extreme durability and capability to perform under tough conditions, underscoring their utility in challenging environments.
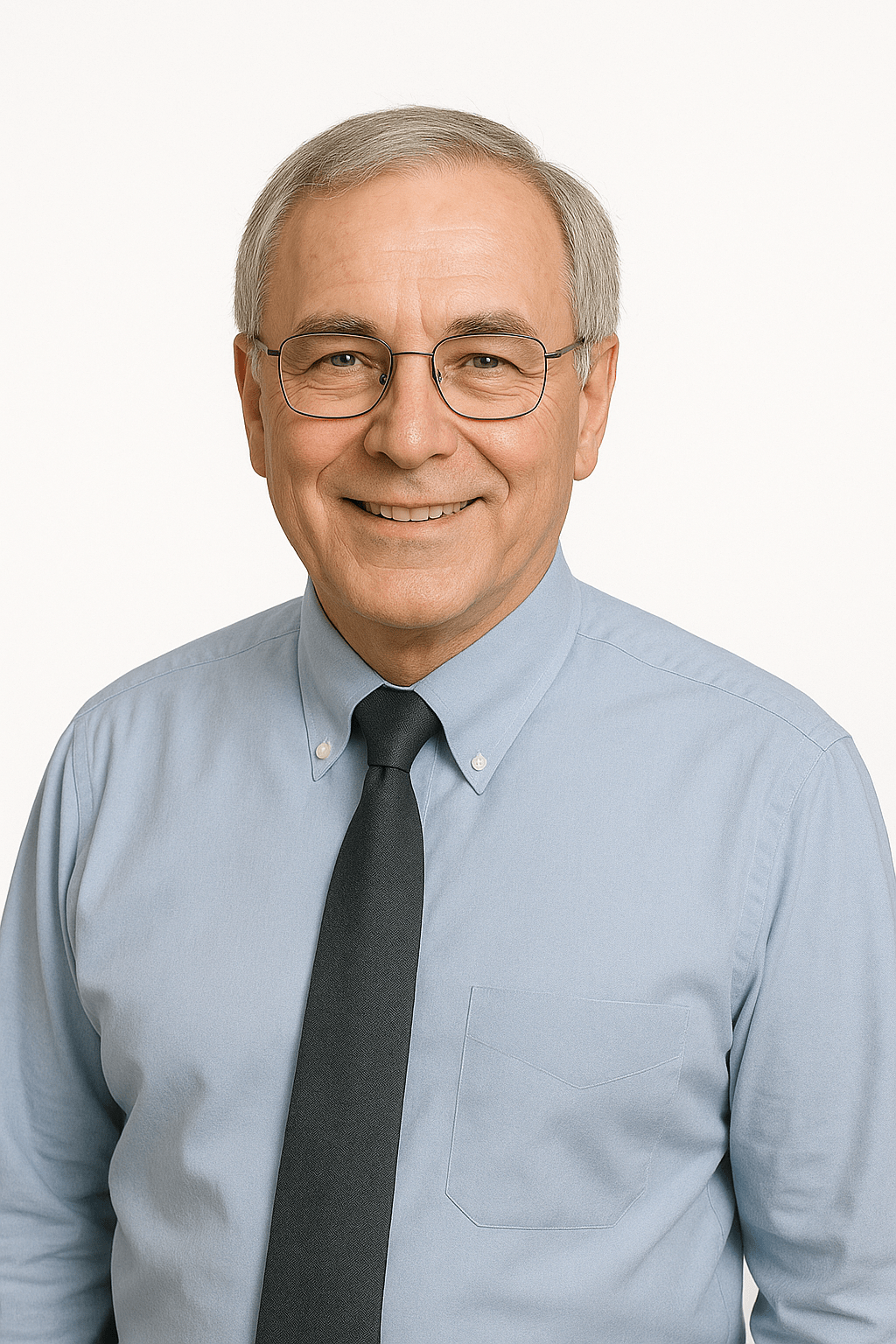
Alexander Schneider is a senior applications engineer and leading authority in the industrial diamond tooling industry, with over 35 years of hands-on experience in the development, application, and optimization of ultra-thin and high-precision diamond blades, diamond core drills, and diamond and CBN grinding wheels. His work spans a wide range of advanced materials including ceramics, glass, composites, semiconductors, and high-performance metals.
Throughout his career, he has collaborated with leading R&D institutions, national laboratories, and high-tech manufacturing companies across Europe, North America, and Asia, providing technical expertise and tailored solutions for demanding cutting and surface preparation applications.
Mr. Schneider has played a pivotal role in advancing precision cutting, sectioning, dicing, and grinding technologies used in research, production, and failure analysis. He is widely respected for his ability to optimize tool design and cutting parameters to meet exacting industry standards—balancing factors such as cut quality, blade life, material integrity, and process consistency.
As an author, Mr. Schneider is known for delivering practical, application-focused insights that translate complex technical challenges into clear, actionable strategies. His articles and technical guides serve as trusted resources for engineers, researchers, and manufacturers seeking to improve precision, reduce process variability, and enhance tool performance in critical applications.
ARE YOU USING RIGHT TOOLS
FOR YOUR APPLICATION?
LET US
HELP YOU
HAVING ISSUES WITH
YOUR CURRENT TOOLS?
Knowledge Center
How to Selecting Right Diamond Tools for your application
How to properly use Diamond Tools
Why use diamond
Diamond vs CBN (cubic boron nitride) Tools
What is Diamond Mesh Size and how to select best one for your application
What is Diamond Concentration and which to use for your application
Diamond Tool Coolants Why, How, When & Where to Use
Get to Know the Diamond Tool Bond Types and Which to use for your application
Get to Know the Diamond Tool Bond Types and Which to use for your application
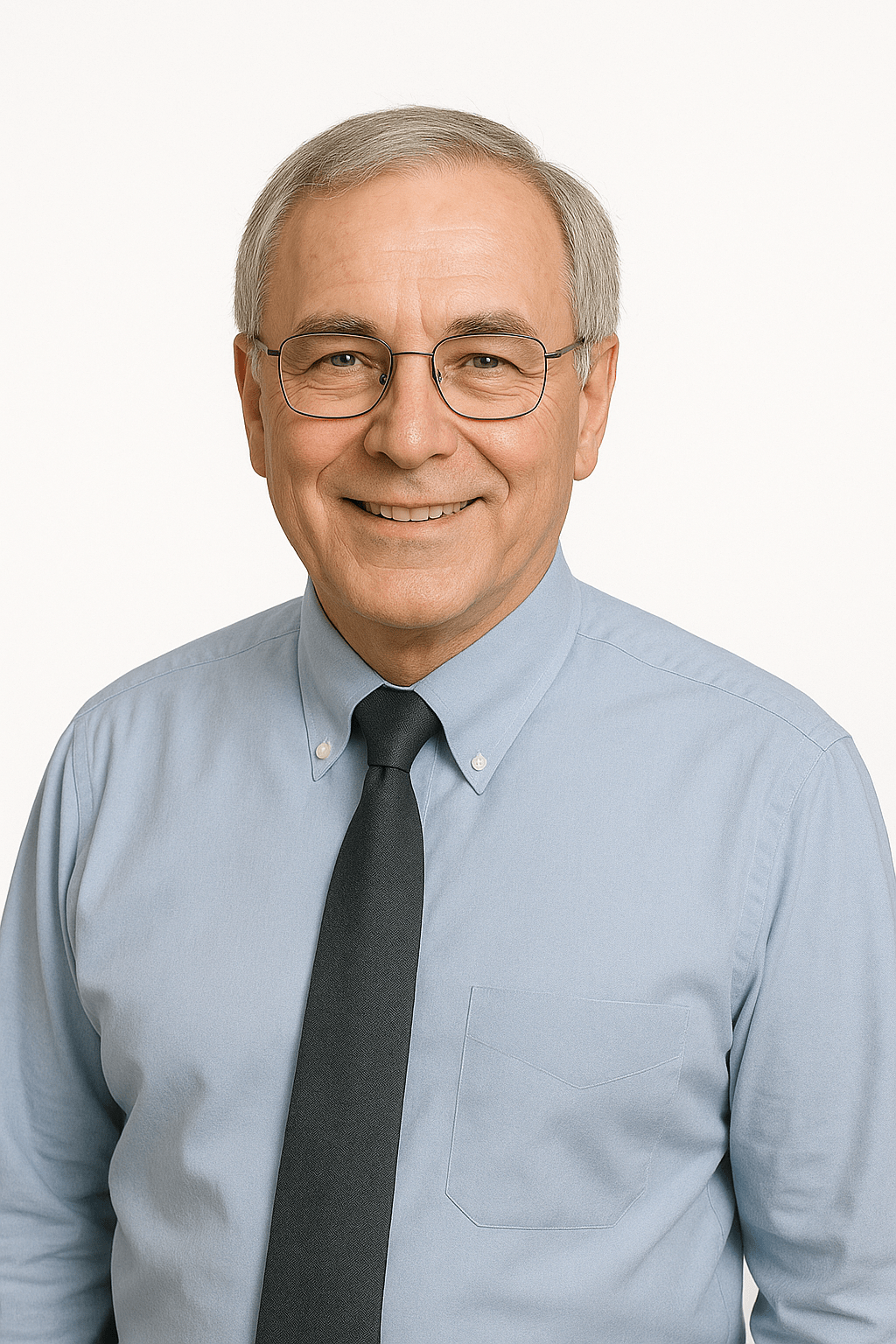
Alexander Schneider is a senior applications engineer and leading authority in the industrial diamond tooling industry, with over 35 years of hands-on experience in the development, application, and optimization of ultra-thin and high-precision diamond blades, diamond core drills, and diamond and CBN grinding wheels. His work spans a wide range of advanced materials including ceramics, glass, composites, semiconductors, and high-performance metals.
Throughout his career, he has collaborated with leading R&D institutions, national laboratories, and high-tech manufacturing companies across Europe, North America, and Asia, providing technical expertise and tailored solutions for demanding cutting and surface preparation applications.
Mr. Schneider has played a pivotal role in advancing precision cutting, sectioning, dicing, and grinding technologies used in research, production, and failure analysis. He is widely respected for his ability to optimize tool design and cutting parameters to meet exacting industry standards—balancing factors such as cut quality, blade life, material integrity, and process consistency.
As an author, Mr. Schneider is known for delivering practical, application-focused insights that translate complex technical challenges into clear, actionable strategies. His articles and technical guides serve as trusted resources for engineers, researchers, and manufacturers seeking to improve precision, reduce process variability, and enhance tool performance in critical applications.