Selecting the right RPM (revolutions per minute) when using industrial diamond tools is a critical factor in achieving optimal results for a variety of applications. Whether you're slicing, dicing, drilling, grinding, or polishing, the RPM of your machine plays a pivotal role in the performance and longevity of both the tool and the material being worked on.
This comprehensive guide, spanning nine parts, provides a detailed exploration of RPM selection for industrial diamond tools. With this extensive knowledge, operators are well-equipped to make informed decisions and achieve exceptional performance in their machining operations. By understanding and optimizing these factors, operators can achieve optimal results, enhance product quality, and improve overall process efficiency.
This guide to help you understand the factors that influence RPM selection and how it fits into the broader machining equation.
Why Selecting the Right RPM’s for your application is important?
During the process of cutting or grinding using specialized equipment, the surface speed can reach remarkable velocities, with speeds of up to 30 meters per second achievable when employing high-speed machinery. To put this into perspective, such speeds surpass those typically observed on most highways where cars travel.
The cutting action itself is facilitated by numerous diamond particles embedded within the bond matrix of the cutting tool. As the tool interacts with the workpiece material, these diamond particles scratch away small chips, gradually shaping the material into the desired form.
The configuration of the diamond tool, including factors such as the number of cutting edges determined by the quantity or concentration of diamond particles, constitutes its fundamental structure, which is further enhanced by the composition of the bond matrix. Additionally, the size of the diamond particles directly influences the size of the chips that can be produced during the cutting process. Furthermore, the overall thickness or diameter of the tool, comprising both the diamond particles and the matrix, dictates the width of the resulting cut.
It is essential to emphasize that the careful selection of appropriate tools, in conjunction with considerations such as feed rate, cutting speed, and depth of cut, will ultimately govern the efficiency and effectiveness of the machining process.
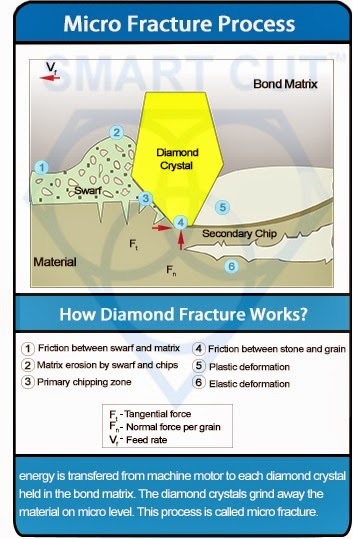
An important aspect to consider when dealing with diamond tools is the behavior of diamond crystals at different speeds. At very high speeds, diamond crystals may fracture, potentially leading to premature tool failure. Conversely, at very slow speeds, diamond crystals may dislodge or fall out of the tool, compromising cutting performance. Therefore, selecting an optimum surface speed or RPM is crucial to balance these two potential disadvantages and ensure optimal tool performance and longevity.
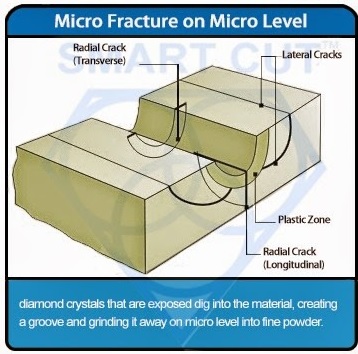
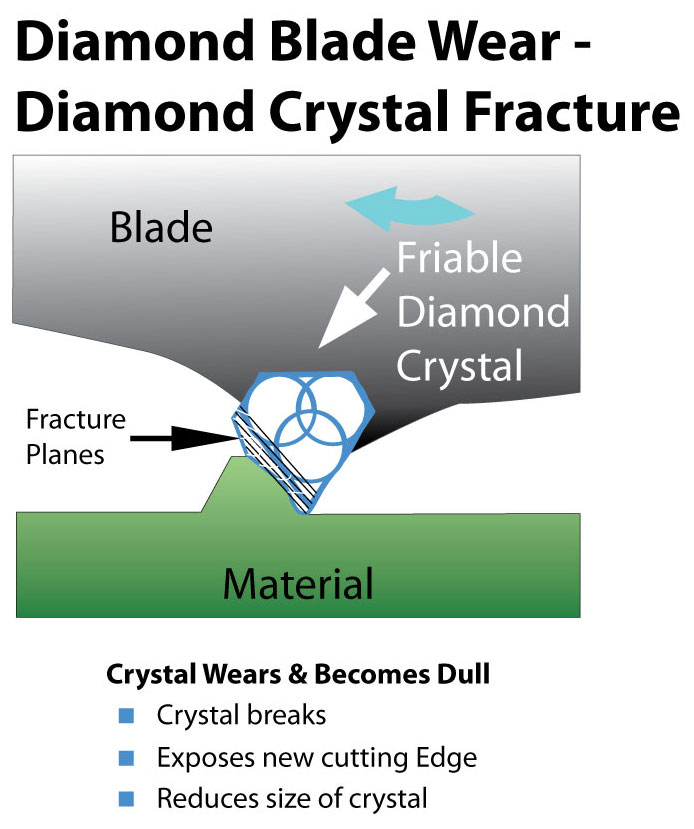
Diamond & CBN Tool Variables correlation with RPM’s
The table below illustrates the correlations between RPM and different variables or attributes in industrial diamond tool usage:
Attribute |
Correlation with RPM |
Effect |
---|---|---|
Tool Diameter |
Inversely Correlated |
Larger tool diameters require lower RPMs to maintain cutting speed. |
Cutting Speed |
Directly Correlated |
Higher RPMs increase cutting speed. |
Feed Rate |
Directly Correlated |
Higher RPMs increase feed rate for a given feed per tooth. |
Material Hardness |
Inversely Correlated |
Harder materials require lower RPMs to prevent tool wear. |
Material Brittleness |
Inversely Correlated |
Brittle materials require lower RPMs to prevent cracking. |
Thermal Conductivity |
Directly Correlated |
Materials with high thermal conductivity can handle higher RPMs. |
Tool Wear |
Directly Correlated |
Higher RPMs increase tool wear due to friction and heat. |
Surface Finish |
Directly Correlated |
Higher RPMs generally improve surface finish. |
Surface Roughness |
Inversely Correlated |
Higher RPMs reduce surface roughness. |
Cutting Force |
Inversely Correlated |
Higher RPMs reduce cutting force due to increased cutting speed. |
Chip Formation |
Directly Correlated |
Higher RPMs generally produce continuous chips. |
Vibration |
Directly Correlated |
Higher RPMs increase the risk of vibration or chatter. |
Tool Deflection |
Directly Correlated |
Higher RPMs increase the risk of tool deflection. |
Thermal Damage |
Directly Correlated |
Higher RPMs increase the risk of thermal damage. |
Cycle Time |
Inversely Correlated |
Higher RPMs generally reduce cycle time. |
Productivity |
Directly Correlated |
Higher RPMs generally increase productivity. |
Diamond & CBN Tool Variables and their affect on RPM’s
Variable/Factor |
Description |
Impact on RPM |
---|---|---|
Material Hardness |
The resistance of the material to indentation, scratching, abrasion, or deformation. |
Harder materials require lower RPMs to prevent wear. |
Material Brittleness |
The tendency of the material to fracture or shatter under stress. |
Brittle materials require lower RPMs to prevent damage. |
Material Ductility |
The ability of the material to deform plastically without fracturing. |
Ductile materials may allow for higher RPMs in some cases. |
Material Thermal Conductivity |
The rate at which heat is transferred through the material. |
Low thermal conductivity materials require lower RPMs. |
Tool Diameter |
The size of the tool's cutting or grinding surface. |
Larger diameters typically require lower RPMs. |
Tool Type |
The specific type and design of the cutting or grinding tool. |
Different tool types have specific RPM requirements. |
Tool Geometry |
The shape and structure of the tool, including grit size and bond type. |
Tool geometry influences optimal RPM for efficiency. |
Coolant Application |
The method and amount of coolant or cutting fluid used during machining. |
Coolant application may allow for higher RPMs. |
Material Handling |
How materials are secured, positioned, or moved during machining. |
Proper handling ensures stable RPM operation. |
Machining Parameters |
Other machining parameters such as feed rate and depth of cut. |
RPM must be balanced with other parameters for efficiency. |
Material Composition |
The chemical makeup of the material, including alloys or composite materials. |
Different compositions may require varying RPM ranges. |
Surface Finish Required |
The desired quality of the surface finish, ranging from rough to mirror-like. |
Finer finishes may require lower RPMs for precision. |
Tool Material |
The material from which the cutting or grinding tool is made, such as steel or diamond. |
Tool material influences RPM tolerance and wear rate. |
Workpiece Size |
The dimensions of the workpiece being machined, including length, width, and thickness. |
Larger workpieces may require lower RPMs for stability. |
Machining Operation |
The specific machining process being performed, such as cutting, drilling, or grinding. |
Each operation may have different RPM requirements. |
Machine Rigidity |
The stiffness and stability of the machining equipment, including machine tools and fixtures. |
More rigid machines can handle higher RPMs with less vibration. |
Tool Wear Resistance |
The ability of the cutting tool to resist wear and maintain sharpness over time. |
Higher wear resistance may allow for higher RPMs. |
Machining Environment |
The conditions in which machining takes place, including temperature and humidity. |
Extreme environments may require adjustments to RPM. |
Tool Sharpness |
The sharpness of the cutting edge or abrasive particles on the tool surface. |
Sharp tools may allow for higher RPMs for efficient cutting. |
Cutting Tool Stability |
The stability and rigidity of the cutting tool during machining operations. |
Stable tools can withstand higher RPMs without vibration. |
Workpiece Material Temperature |
The temperature of the workpiece material during machining, which affects thermal conductivity. |
Elevated temperatures may require lower RPMs to prevent overheating. |
Machining Tolerance |
The allowable deviation from specified dimensions in the machined part. |
Tight tolerances may require lower RPMs for precision. |
Understanding the Machining Equation
Before diving into the specifics, it's important to understand the machining equation that governs the relationship between speed, feed rate, and the material being processed. The basic equation is as follows:
Cutting Speed (V)=𝜋×Diameter (D)×RPMCutting Speed (V)=π×Diameter (D)×RPM
Feed Rate (F)=Feed per Tooth (f)×Number of Teeth (N)×RPMFeed Rate (F)=Feed per Tooth (f)×Number of Teeth (N)×RPM
These equations demonstrate how the cutting speed and feed rate are directly influenced by the RPM of the machine. Therefore, selecting the correct RPM is crucial for achieving the desired cutting or grinding performance.
RPM and Material Removal Rate
Material removal rate (MRR) is a key factor influenced by RPM in various machining processes. The MRR is generally defined as:
MRR=Feed Rate×Depth of Cut×Width of CutMRR=Feed Rate×Depth of Cut×Width of Cut
In this context, RPM influences the feed rate, which in turn affects the overall MRR. An optimal RPM ensures that the MRR is balanced with tool wear and surface finish requirements.
RPM and Cutting Speed Calculation
A crucial aspect of selecting the appropriate RPM is calculating the optimal cutting speed for a given application. The cutting speed is typically expressed in surface feet per minute (SFM) or meters per minute (MPM), and it varies based on the material and tool being used. The formula for calculating RPM from cutting speed is:
RPM=(Cutting Speed×12)(𝜋×Diameter)RPM=(π×Diameter)(Cutting Speed×12)
RPM=(Cutting Speed×1000)(𝜋×Diameter)RPM=(π×Diameter)(Cutting Speed×1000)
Depending on the measurement system, where:
-
Cutting Speed is expressed in surface feet per minute (SFM) or meters per minute (MPM)
-
Diameter is the diameter of the tool or workpiece in inches or millimeters.
This formula helps determine the optimal RPM based on the material and tool geometry.
Influence of Material Properties on RPM Selection
Selecting the optimal RPM for industrial diamond tool usage involves carefully considering the properties of the material being machined. The interplay between RPM and material properties significantly impacts the performance, quality, and efficiency of the machining process. Key material properties that affect RPM include hardness, brittleness, ductility, and thermal conductivity.
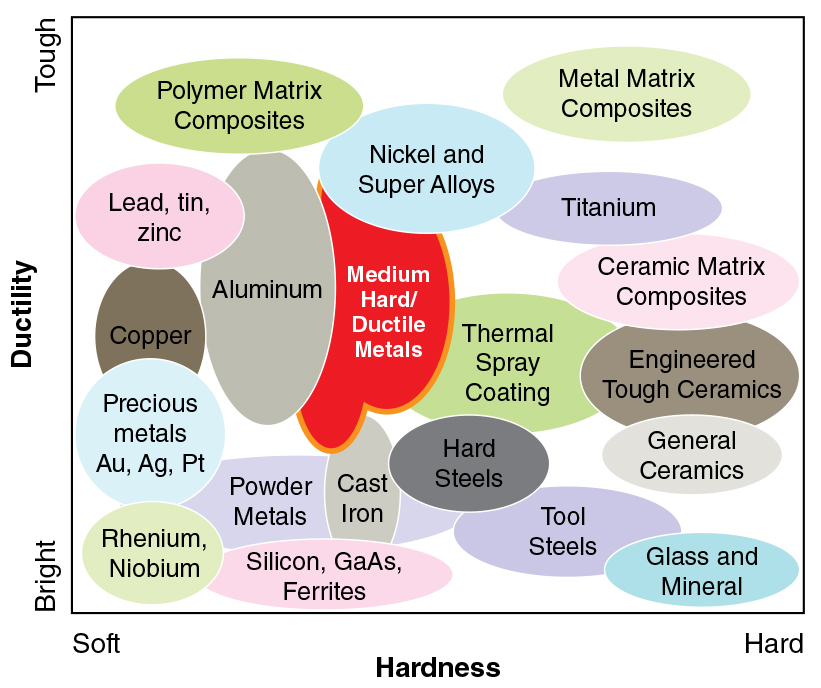
1. Hardness
Material hardness is a crucial factor in determining the appropriate RPM for machining. Hard materials such as hardened steel, ceramics, and hardened alloys are resistant to indentation and deformation, which means they require slower cutting speeds to avoid rapid tool wear and thermal damage. For hard materials, lower RPMs are recommended, typically ranging from 500 to 2,000 RPM, depending on the specific application and tool geometry. These hard materials are often used in cutting tools, dies, and precision components, where maintaining dimensional accuracy and surface finish is critical. On the other hand, softer materials like aluminum, copper, and plastics are more malleable and can be machined at higher speeds. However, soft materials can be prone to surface damage if the RPM is too high. For soft materials, higher RPMs, ranging from 2,000 to 10,000 RPM or more, are typically used, depending on the desired surface finish and cutting conditions. Soft materials are commonly used in applications where lightweight or electrical conductivity is important, such as in aerospace or electronics.
2. Brittleness
Brittle materials are sensitive to impact and can easily crack or chip during machining. Examples of brittle materials include glass, silicon, and certain ceramics. These materials lack ductility and tend to fracture under mechanical stress. Lower RPMs minimize cutting forces and prevent cracking or chipping. For brittle materials, lower RPMs, typically between 500 to 3,000 RPM, are recommended to ensure clean, precise cuts. Brittle materials are often used in optical components, semiconductors, and decorative applications, where surface integrity and edge quality are crucial.
3. Ductility
Ductile materials can undergo significant plastic deformation before fracturing, affecting their machining behavior. Examples of ductile materials include aluminum, copper, and certain steels. These materials can be machined at higher speeds but may require lower RPMs for finishing operations to prevent distortion or surface defects. For roughing, higher RPMs of 2,000 to 10,000 RPM or more can be used, while finishing operations benefit from lower RPMs, typically between 500 to 3,000 RPM. Ductile materials are
common in structural components, electrical conductors, and automotive parts, where flexibility and formability are advantageous.
4. Thermal Conductivity
Thermal conductivity affects how heat is dissipated during machining, influencing the optimal RPM. Materials with low thermal conductivity, such as titanium, stainless steel, and certain composites, do not dissipate heat well, increasing the risk of thermal damage to both the tool and the workpiece at high RPMs. For materials with low thermal conductivity, lower RPMs, typically between 500 to 2,000 RPM, are recommended to prevent overheating. These materials are often used in aerospace, medical, and high-temperature applications, where thermal resistance or specific mechanical properties are needed. In contrast, materials with high thermal conductivity, such as copper, aluminum, and diamond, dissipate heat efficiently, allowing for higher RPMs and faster cutting speeds without the risk of thermal damage. For materials with high thermal conductivity, higher RPMs, typically between 2,000 to 10,000 RPM or more, can be used, depending on the application. These materials are commonly used in heat sinks, electrical components, and thermal management systems, where efficient heat dissipation is crucial.
Influence of Material Properties on RPM Selection
Material Property |
Characteristics |
Optimal RPM Range (Approx.) |
Applications |
---|---|---|---|
Hardness |
|
|
|
Brittleness |
|
|
|
Ductility |
|
|
|
Thermal Conductivity |
|
|
|
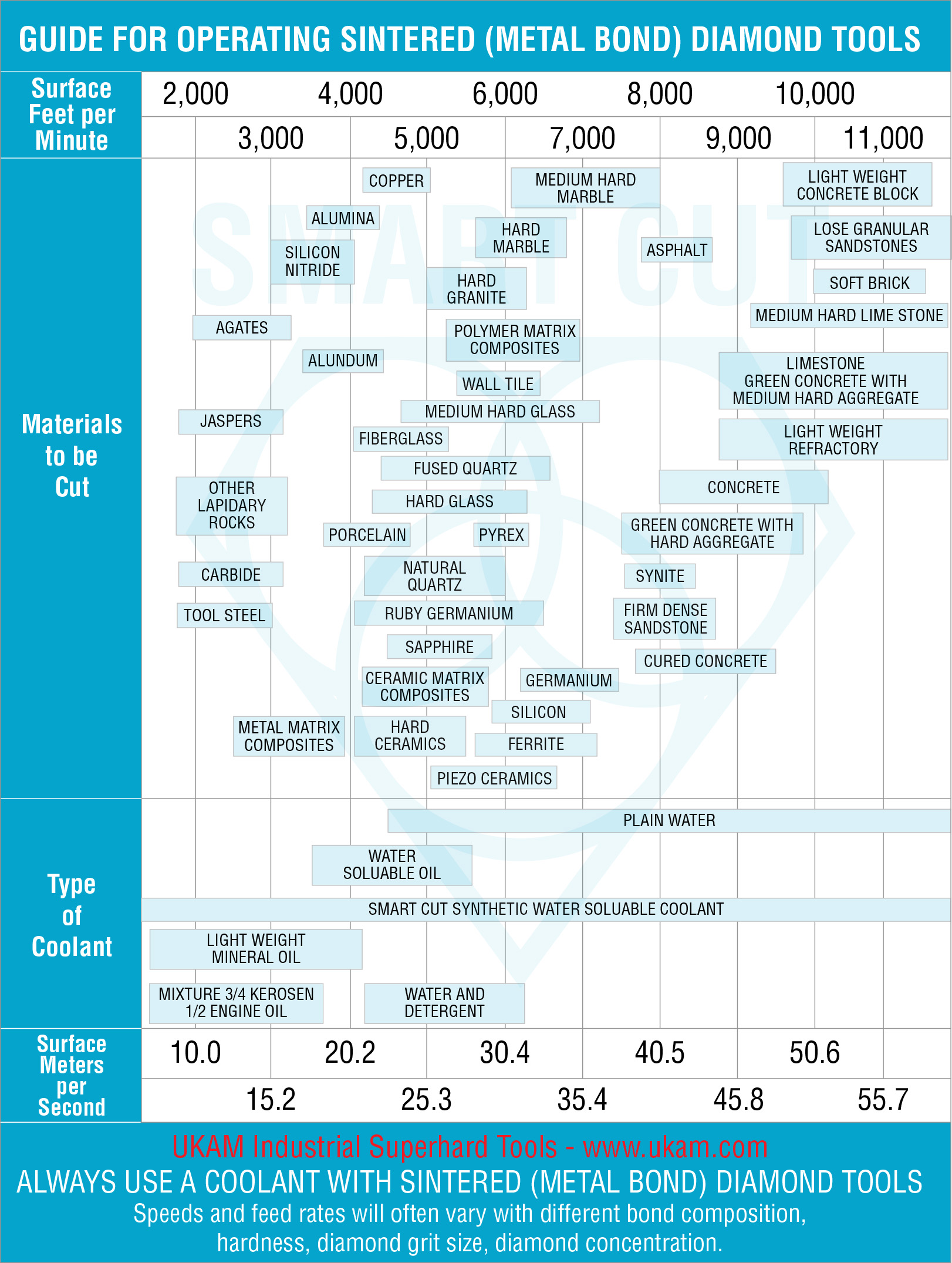
Material Type and How it Affects RPM Selection
The choice of RPM during industrial diamond tool usage is influenced by a variety of factors, including the type of material being machined. Each material has distinct characteristics and hardness levels that affect the optimal cutting speed. Below are examples of different material types and their corresponding RPM considerations.
Metals
Metals span a broad spectrum of hardness levels and characteristics, influencing their optimal machining speeds.
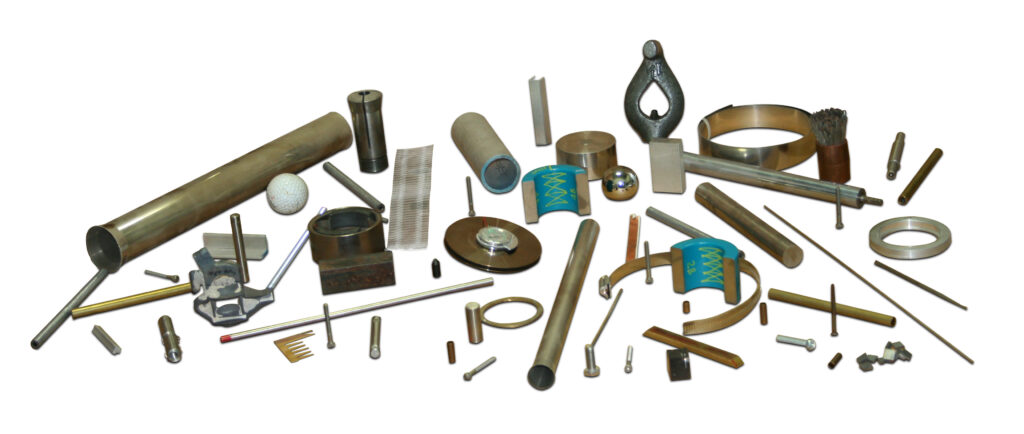
Harder Metals:
-
Stainless Steel: This metal has a high hardness and is prone to work hardening. Slower RPMs are required to prevent overheating and rapid tool wear. Cutting speeds between 50 to 200 SFM are ideal, which translates to lower RPMs, depending on the tool diameter.
-
Titanium: Known for its high strength and low thermal conductivity, titanium requires slower RPMs to prevent thermal damage. Optimal cutting speeds range between 50 to 150 SFM.
-
Hardened Steel: This category includes tool steels and case-hardened materials. Lower RPMs are necessary, with cutting speeds typically between 30 to 100 SFM to maintain tool life and surface quality.
Softer Metals:
-
Aluminum: This lightweight and ductile metal allows for higher RPMs. Cutting speeds between 200 to 1,000 SFM are common, facilitating efficient material removal and smooth surface finishes.
-
Copper: Similar to aluminum, copper is soft and ductile but tends to adhere to cutting tools. RPMs should be moderate, with cutting speeds between 100 to 500 SFM to balance material removal and tool wear.
-
Brass: Brass is softer and easier to machine than most metals, with cutting speeds typically between 200 to 800 SFM. Higher RPMs can be used, but care must be taken to avoid excessive heat buildup.
Ceramics
Ceramics are challenging to machine due to their hardness and brittleness.
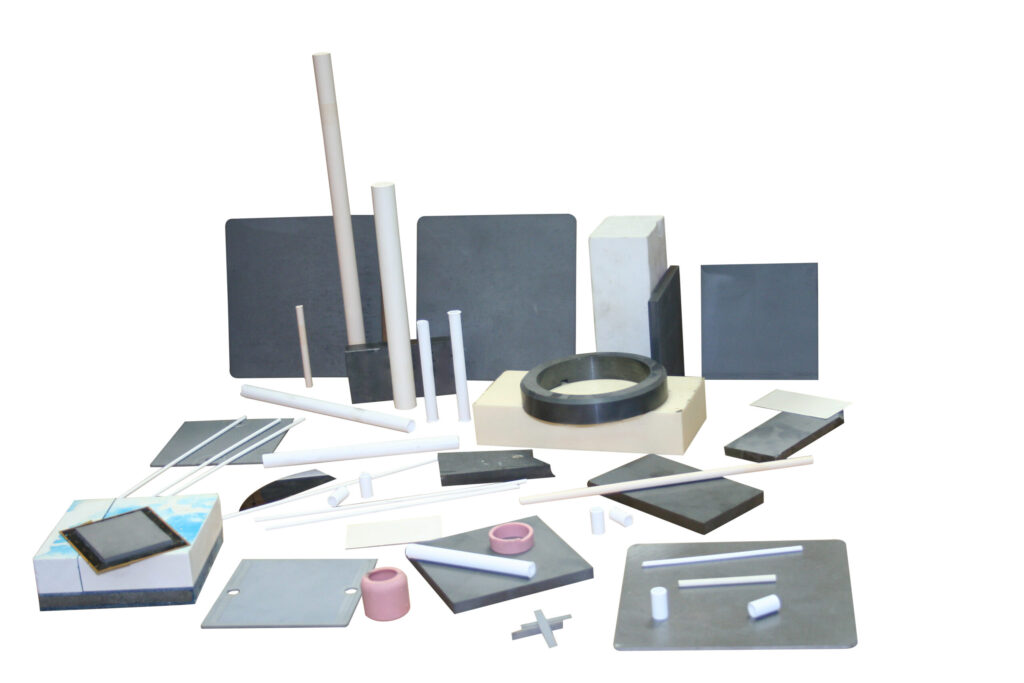
Technical Ceramics:
-
Aluminum: This common engineering ceramic is extremely hard and requires low RPMs to avoid cracking. Cutting speeds should generally be between 50 to 300 SFM.
-
Silicon Carbide: Known for its extreme hardness, silicon carbide requires careful handling. Optimal cutting speeds are typically between 50 to 200 SFM to minimize thermal stress and tool wear.
-
Zirconia: This tough ceramic is often used in high-wear applications. Lower RPMs, with cutting speeds between 50 to 150 SFM, are recommended to prevent surface damage and chipping.
Traditional Ceramics:
-
Porcelain: Used in tiles and sanitary ware, porcelain requires low RPMs for cutting or drilling. Cutting speeds between 50 to 200 SFM are ideal for clean, precise results.
-
Earthenware: This porous ceramic is relatively easy to machine but can crack easily. Lower RPMs, with cutting speeds between 50 to 100 SFM, are recommended for safe machining.
Composites
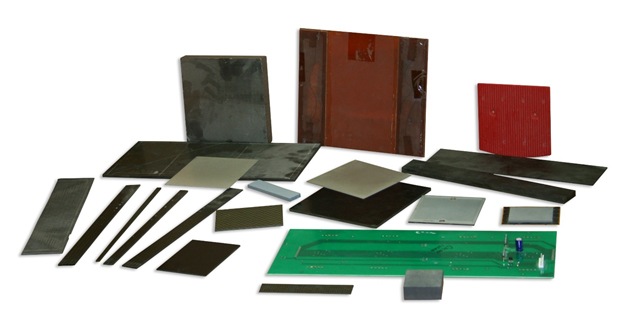
Composites combine different materials, resulting in unique machining challenges.
Fiber Composites:
-
Carbon Fiber Reinforced Polymer (CFRP): This lightweight composite requires balanced RPMs to avoid delamination. Cutting speeds typically range between 100 to 500 SFM for efficient machining.
-
Fiberglass: This versatile material is also prone to delamination. Optimal cutting speeds are between 100 to 400 SFM, with moderate RPMs to prevent fiber damage.
Laminate Composites:
-
Laminated Glass: This safety glass requires lower RPMs for cutting. Cutting speeds between 50 to 150 SFM are recommended to prevent edge cracking and maintain clarity.
-
Metal-Polymer Laminates: These materials require moderate RPMs to balance the properties of both constituents. Cutting speeds between 100 to 300 SFM are ideal for clean cuts and minimal delamination.
Glass
Glass is brittle and transparent, requiring careful handling during machining.
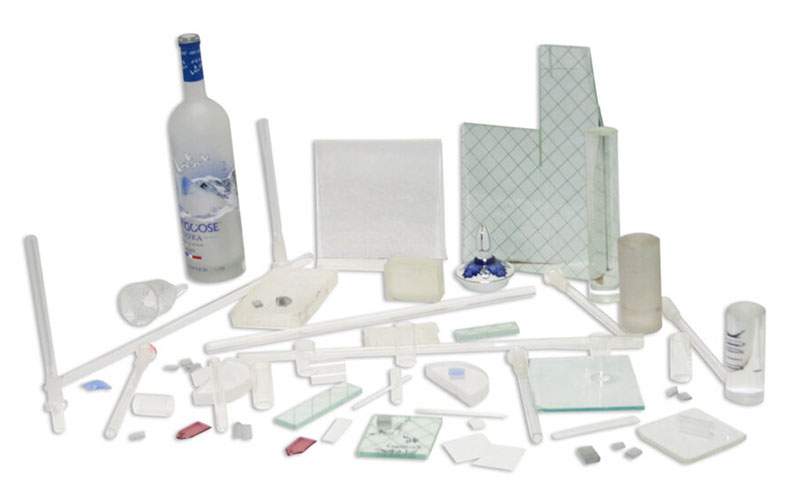
Optical Glass:
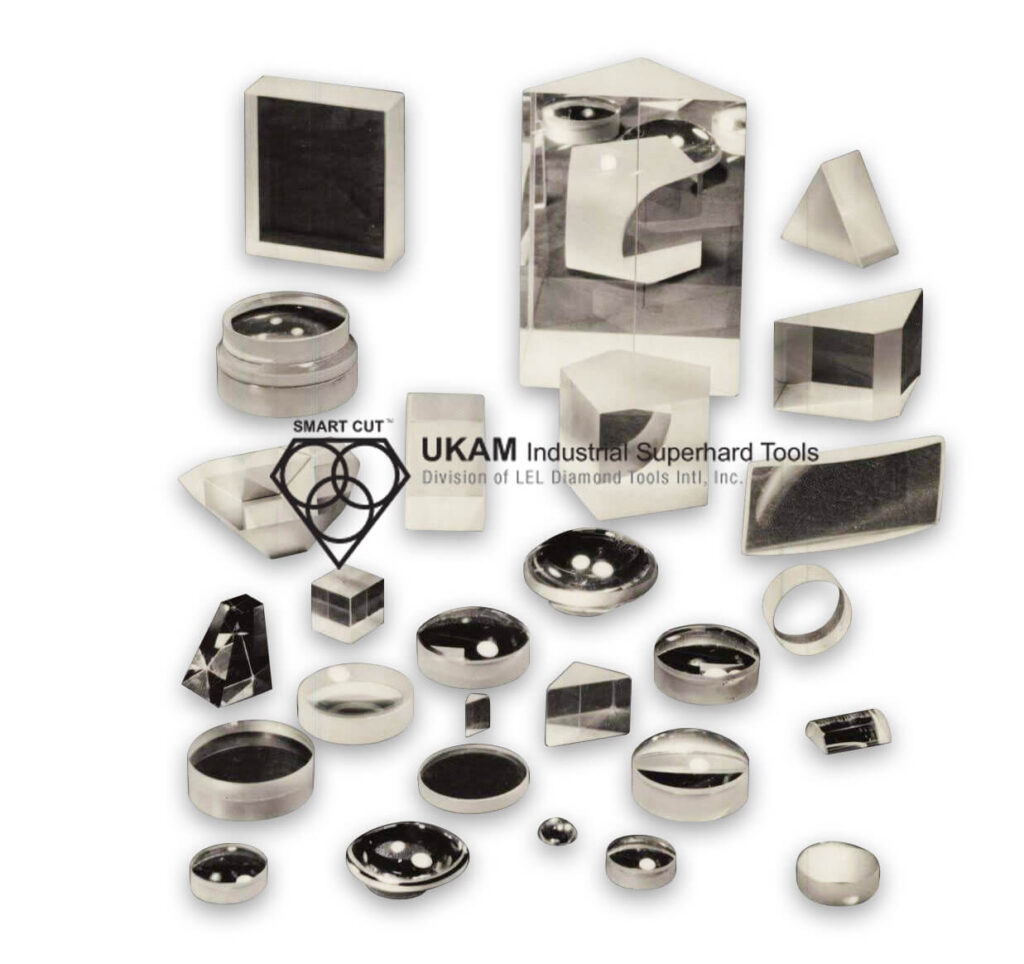
-
BK7: This common optical glass requires very low RPMs for precision cutting. Cutting speeds typically range between 50 to 200 SFM for smooth, defect-free edges.
-
Fused Silica: This highly pure glass is challenging to machine due to its hardness and brittleness. Lower RPMs, with cutting speeds between 50 to 150 SFM, are recommended to prevent cracking.
Industrial Glass
-
Soda-Lime Glass: This common glass is easier to machine but still prone to chipping. Optimal cutting speeds are typically between 100 to 300 SFM, with moderate RPMs to balance cutting efficiency and edge quality.
-
Borosilicate Glass: Known for its thermal resistance, borosilicate glass requires careful handling during machining. Lower RPMs, with cutting speeds between 50 to 200 SFM, are recommended for safe and precise cutting.
Lapidary Materials
Lapidary materials, used in the art of cutting, grinding, and polishing stones and gems, require specific RPMs to achieve desired results.
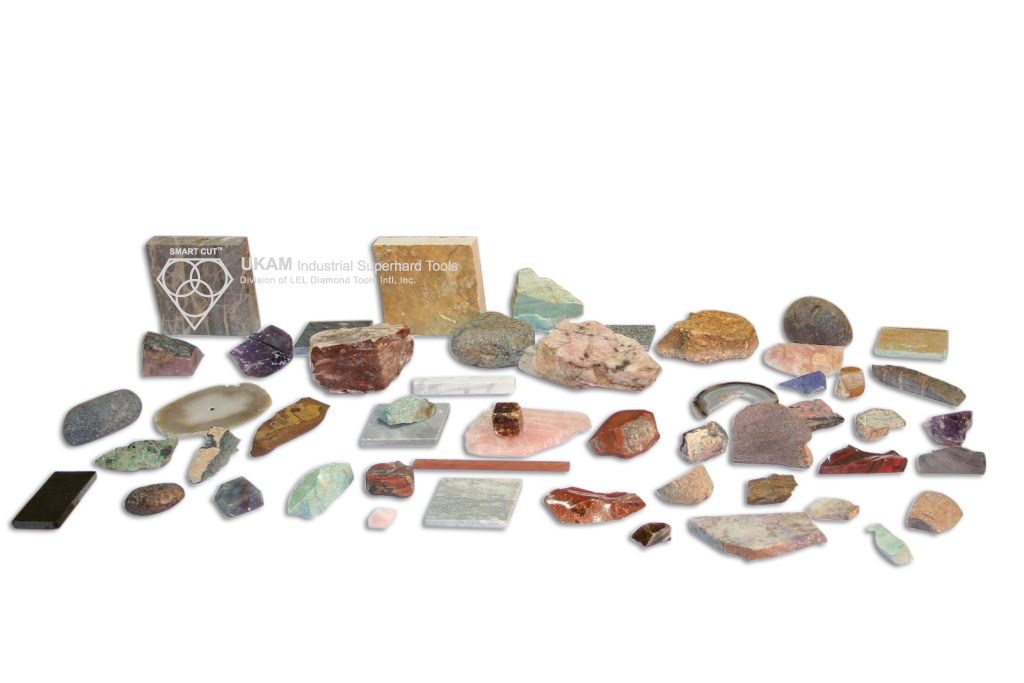
Precious Gemstones:
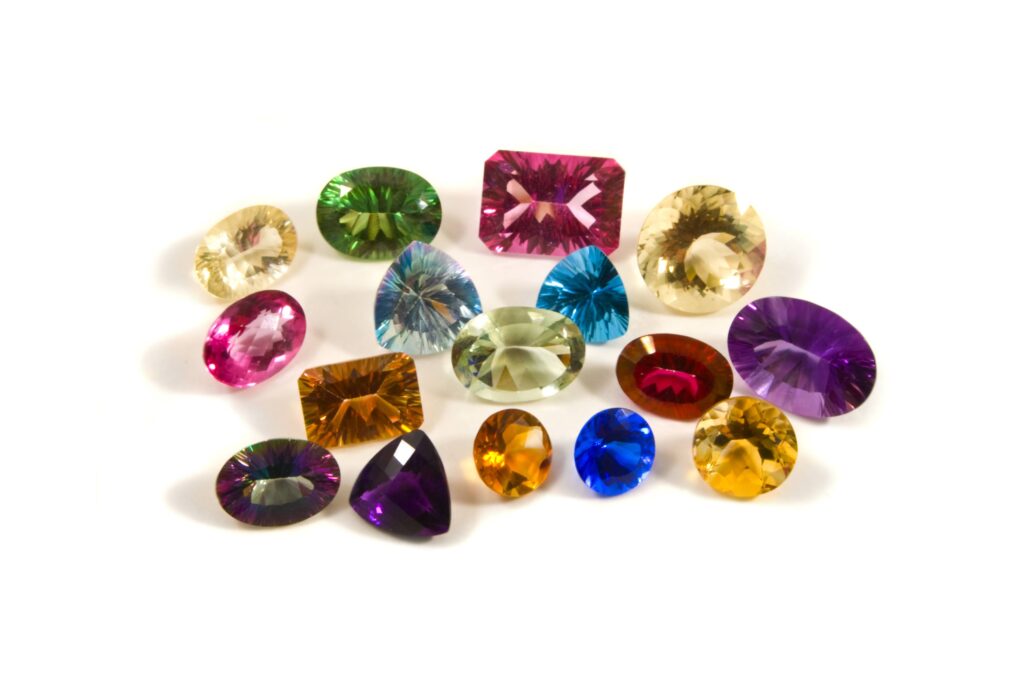
-
Diamond: Being the hardest material, diamond requires slower RPMs to prevent thermal damage and achieve a high-quality polish. Cutting speeds typically range between 50 to 300 SFM, depending on the specific operation and tool geometry.
-
Ruby and Sapphire: These corundum minerals are also very hard and benefit from lower RPMs. Optimal cutting speeds are usually between 50 to 200 SFM for precision cutting and polishing.
Semi-Precious Gemstones:
-
Quartz: Quartz is commonly used in lapidary work and requires moderate RPMs to prevent chipping and achieve a smooth finish. Cutting speeds generally range from 100 to 400 SFM.
-
Agate: This banded form of chalcedony is relatively hard but brittle, necessitating lower RPMs for safe cutting and shaping. Cutting speeds between 50 to 300 SFM are ideal for controlled machining.
Natural Stone
Natural stone materials vary widely in hardness and structure, impacting their optimal RPM for cutting, grinding, and polishing.
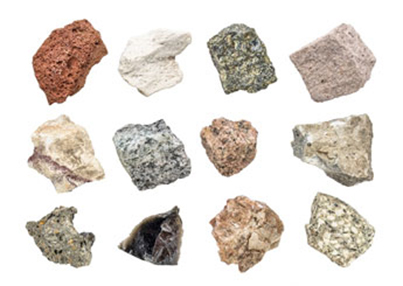
-
Granite: Granite is hard and durable, often used for countertops and monuments. Lower RPMs are necessary to prevent cracking and chipping, with cutting speeds typically between 50 to 300 SFM.
-
Marble: Marble is softer and more brittle, requiring lower RPMs to avoid thermal damage and achieve a high-quality finish. Cutting speeds generally range from 50 to 200 SFM.
-
Slate: Slate is a fine-grained, layered stone that benefits from moderate RPMs for cutting and shaping. Optimal cutting speeds are typically between 100 to 400 SFM.
-
Limestone: Limestone is relatively soft and easy to machine but can chip easily. Lower RPMs, with cutting speeds between 50 to 150 SFM, are recommended for clean cuts and smooth surfaces.
Plastics and Polymers
Plastics and polymers are generally soft but can exhibit varied properties that affect RPM selection.
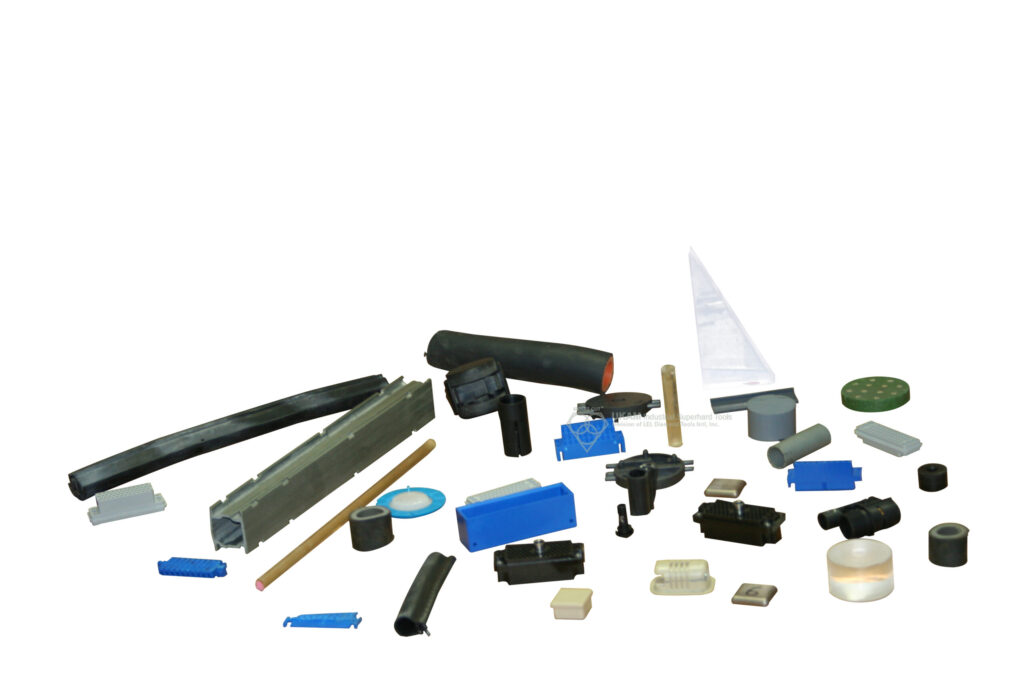
-
Acrylic: Acrylic is a transparent plastic that benefits from moderate RPMs for clean cuts and polished edges. Cutting speeds between 200 to 1,000 SFM are typically recommended, depending on the desired surface finish.
-
Polycarbonate: This strong and impact-resistant plastic can be machined at higher RPMs, with cutting speeds generally between 300 to 1,500 SFM for efficient material removal.
-
Polyethylene: Polyethylene is soft and prone to melting, requiring lower RPMs to prevent thermal damage and achieve smooth surfaces. Optimal cutting speeds are typically between 100 to 500 SFM.
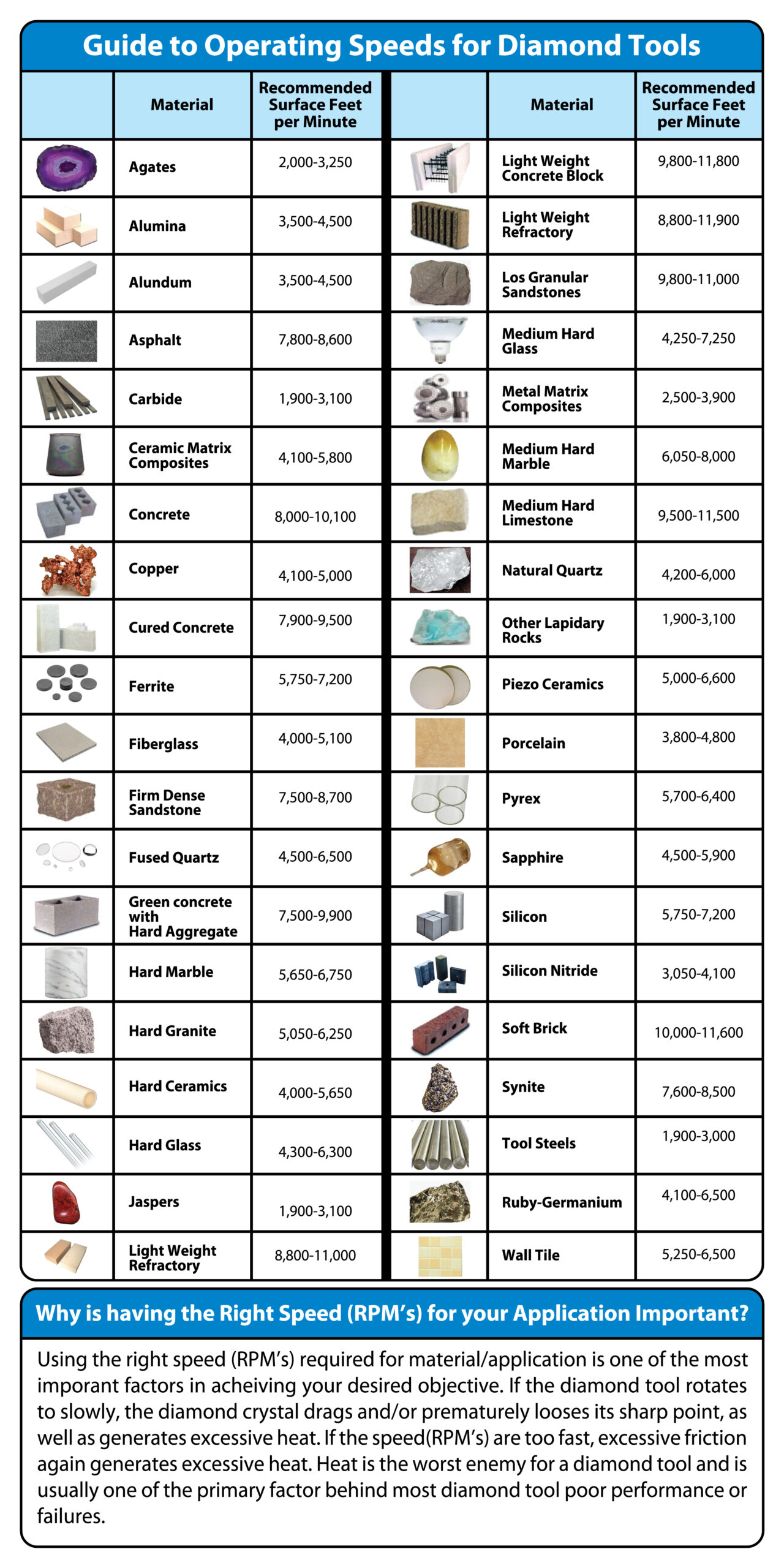
Diamond & CBN Tool Type and RPM Selection
The type of diamond tool used plays a critical role in determining the appropriate RPM for efficient and effective machining operations. Different tools have specific characteristics and operational requirements that dictate their optimal RPM. Below, the influence of tool type on RPM selection is explored.
Diamond Blades
Diamond blades are commonly used for cutting a variety of materials and come in ultra-thin and high-precision designs. These blades require specific RPM ranges to prevent warping or damage.
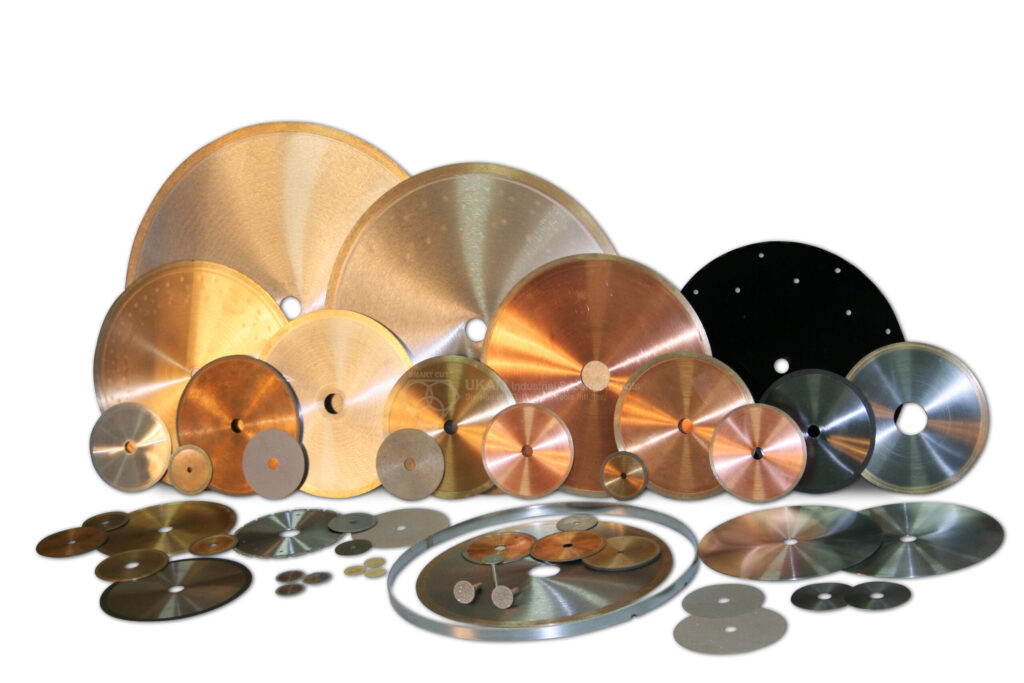
Ultra-thin diamond blades are used for precision cutting in applications such as semiconductor manufacturing, optics, and advanced materials. These blades operate best at lower RPMs, typically between 1,000 to 3,000 RPM, depending on the diameter and material being cut. The lower RPMs prevent blade deflection, minimize thermal stress, and ensure clean cuts.
Segmented diamond blades are used for cutting concrete, masonry, and other tough materials. The segmented design enhances cooling and debris removal, allowing segmented blades to handle higher RPMs, typically between 4,000 to 9,000 RPM, depending on the blade diameter and material hardness. The higher RPMs facilitate fast cutting while maintaining blade durability.
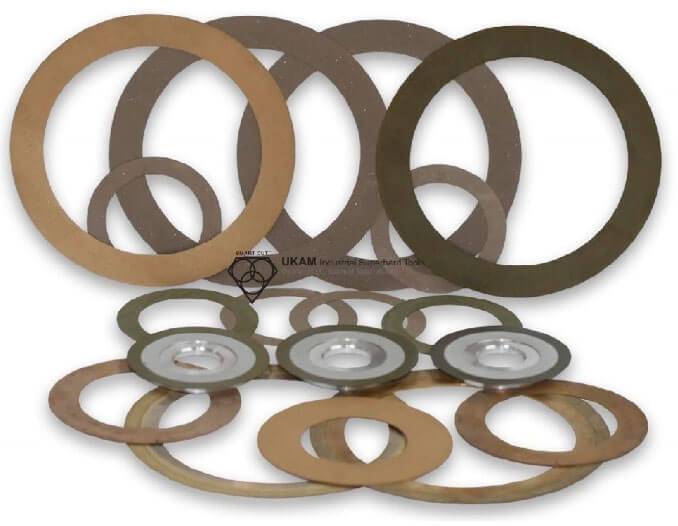
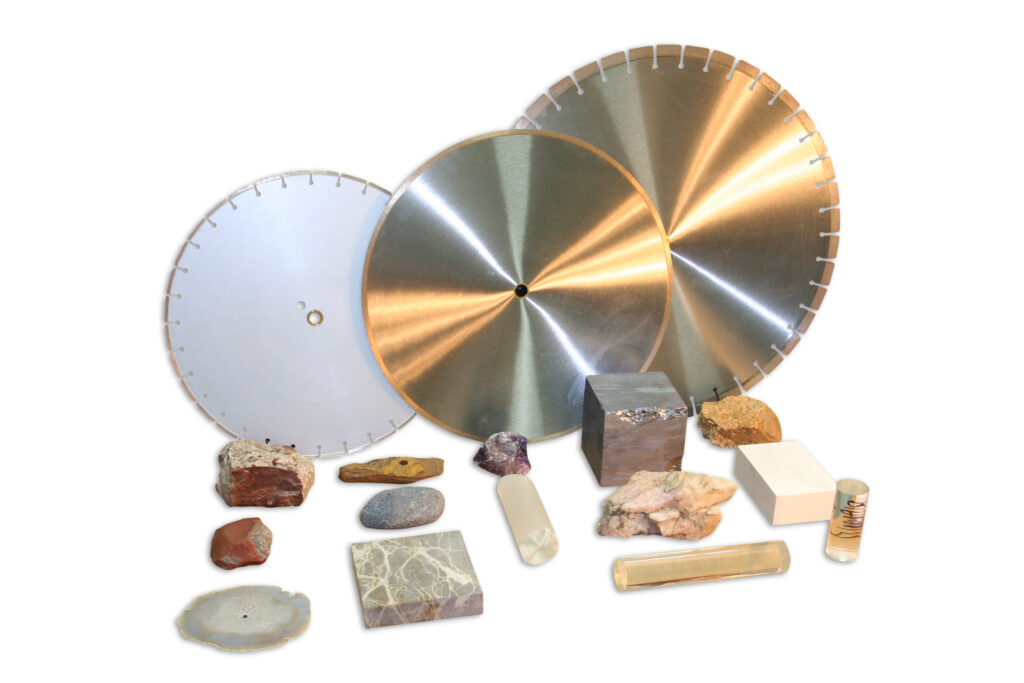
Continuous rim diamond blades are used for smooth, precise cutting of tiles, ceramics, glass, and other hard and brittle materials. The continuous rim ensures a clean finish, and these blades benefit from moderate RPMs, typically between 2,000 to 5,000 RPM, depending on the material and desired edge quality. The continuous rim minimizes chipping and produces clean edges.
Diamond Core Drills
Diamond core drills are used for drilling holes in materials like glass, ceramics, and masonry. These tools benefit from lower RPMs to maintain structural integrity and achieve precise results.
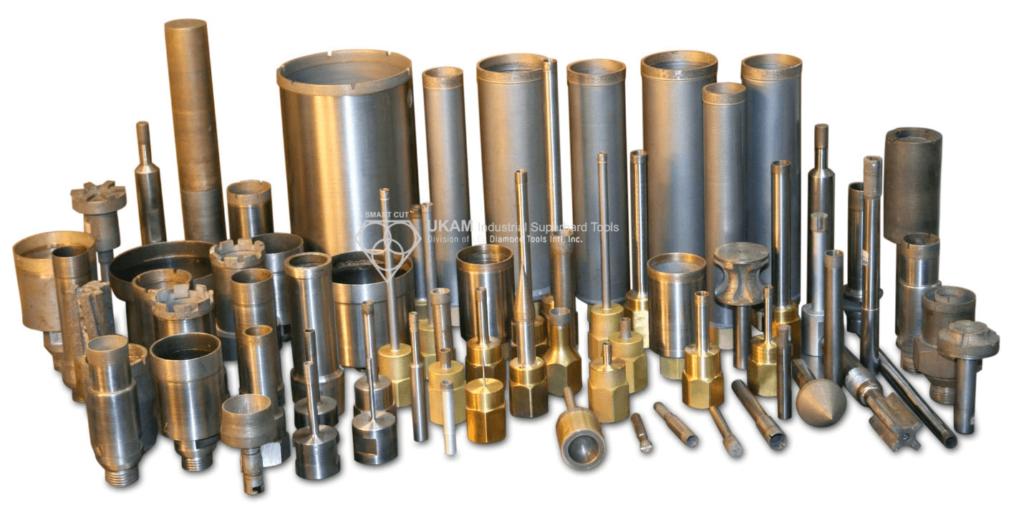
Thin-wall diamond core drills are used for precision drilling in applications such as laboratory glassware, optical components, and ceramic tiles. These drills operate best at lower RPMs, typically between 500 to 1,500 RPM, depending on the diameter and material being drilled. The lower RPMs minimize thermal stress and prevent cracking or chipping.
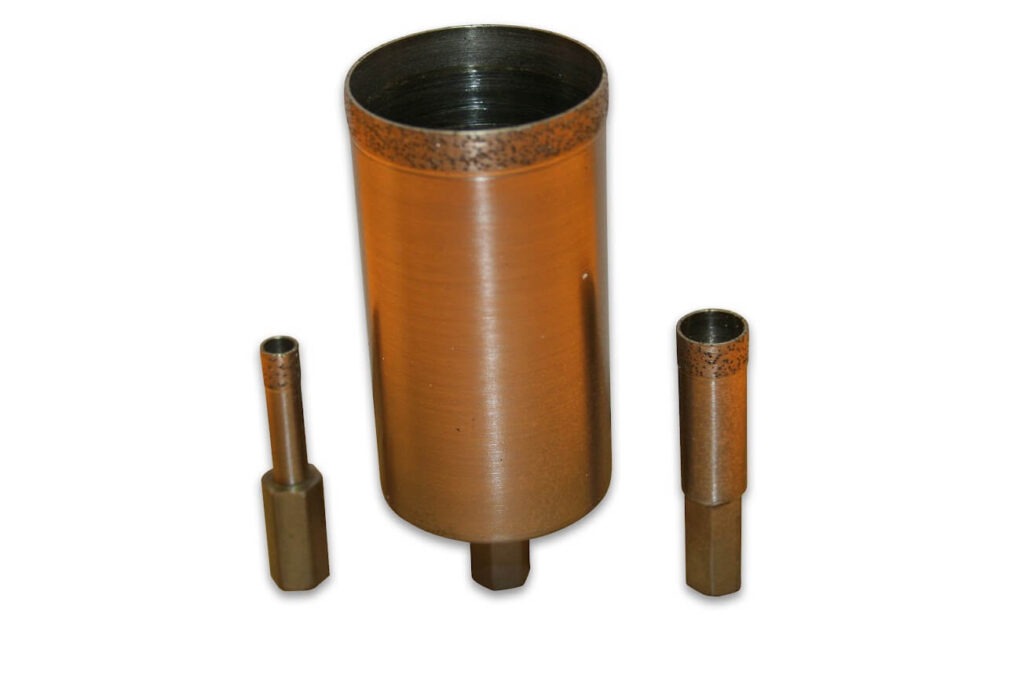
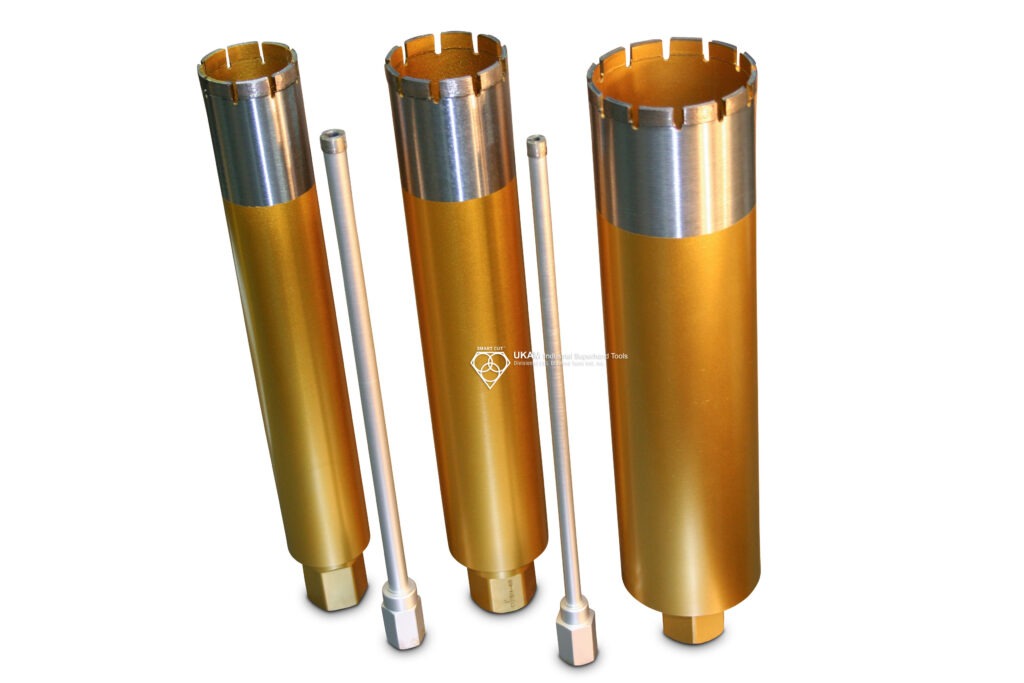
Heavy-duty diamond core drills are used for larger holes in concrete, stone, and similar materials. These heavy-duty drills benefit from moderate RPMs, typically between 400 to 1,000 RPM, depending on the diameter and material hardness. The moderate RPMs provide sufficient power while preventing tool wear or damage.
Diamond Grinding Wheels
Diamond grinding wheels are used for material removal and surface finishing. The bond type and grit size influence the optimal RPM for grinding.
Resin-bonded diamond wheels are used for general-purpose grinding and finishing of materials like carbide, ceramics, and composites. These wheels typically operate at moderate RPMs, generally between 3,000 to 6,000 RPM, depending on the wheel diameter and material hardness. The moderate RPMs balance material removal with surface finish.
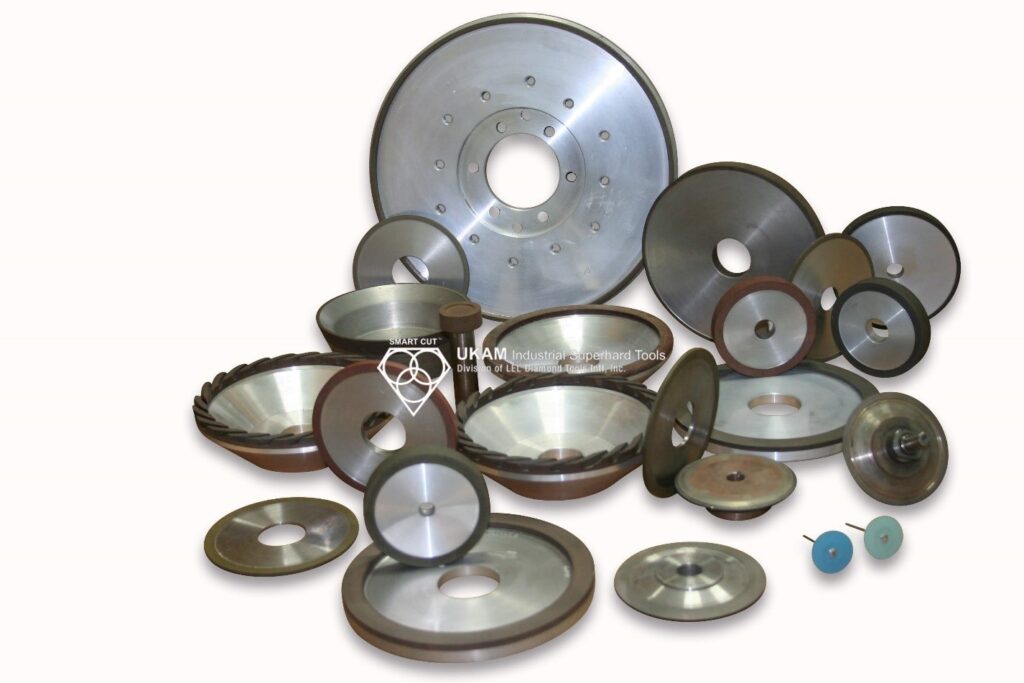
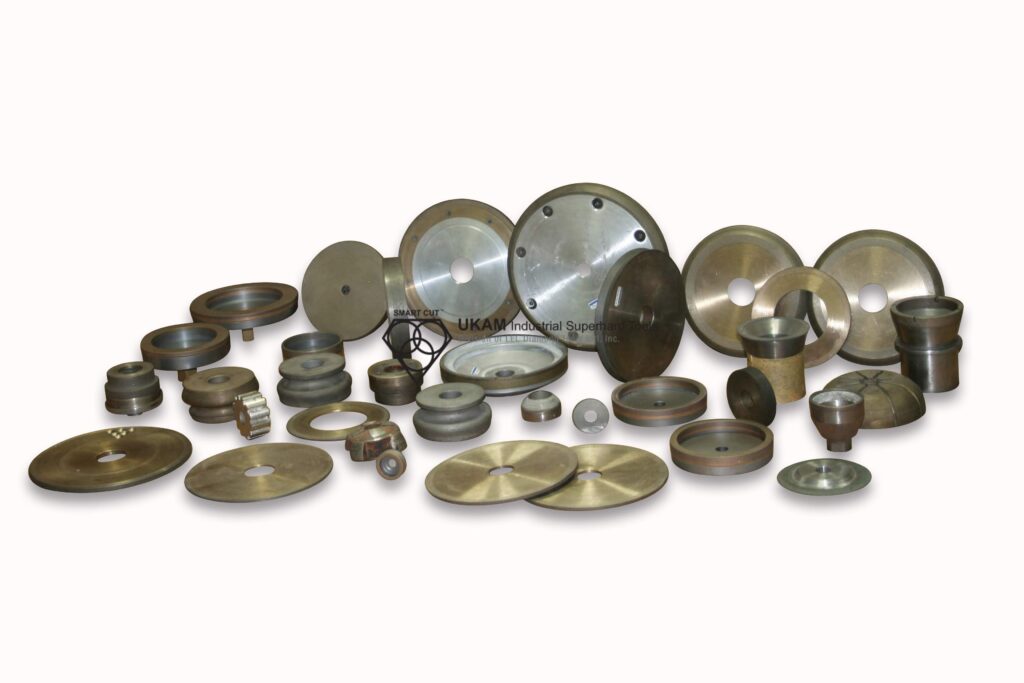
Metal-bonded diamond wheels are used for heavy-duty grinding of hard materials like glass, stone, and hardened steels. These wheels benefit from higher RPMs, typically between 4,000 to 8,000 RPM, depending on the wheel diameter and material. The higher RPMs facilitate aggressive material removal while maintaining wheel integrity.
Vitrified-bonded diamond wheels are used for precision grinding of hard materials such as ceramics and semiconductor wafers. These wheels typically operate at lower RPMs, generally between 1,000 to 4,000 RPM, depending on the wheel diameter and material. The lower RPMs prevent thermal damage and maintain dimensional accuracy.
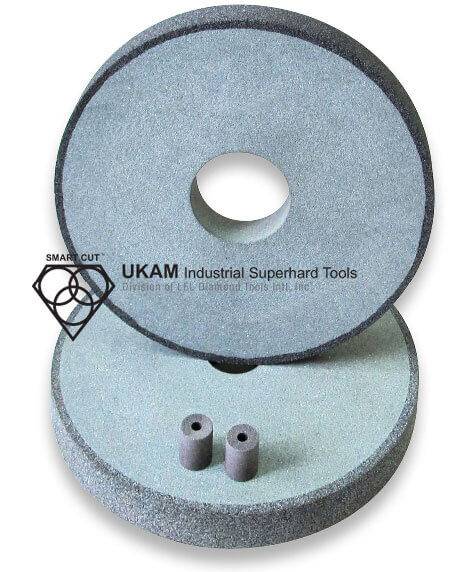
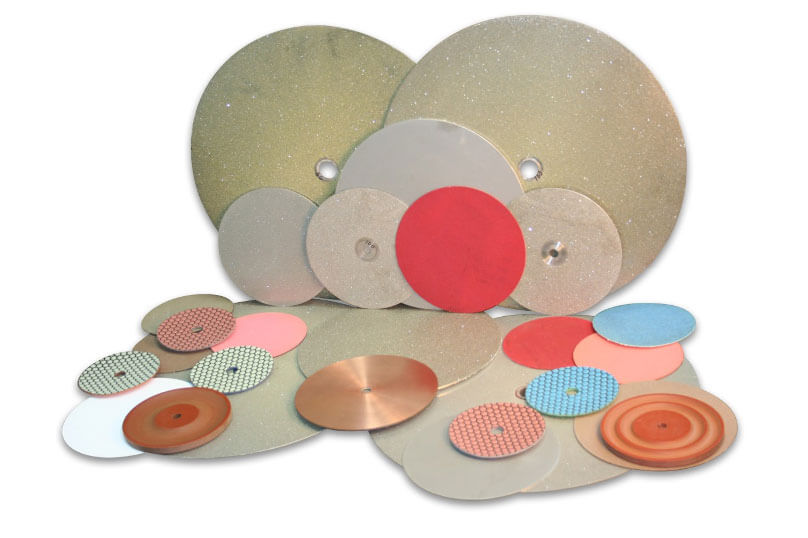
Diamond Polishing Discs
Diamond polishing discs are used for surface finishing and require lower RPMs to avoid heat buildup and ensure a smooth finish.
Flexible diamond polishing discs are used for polishing metals, stones, and composites, offering flexibility and fine control. These discs benefit from lower RPMs, typically between 1,000 to 3,000 RPM, depending on the material and desired finish. The lower RPMs prevent overheating and produce a high-quality polish.
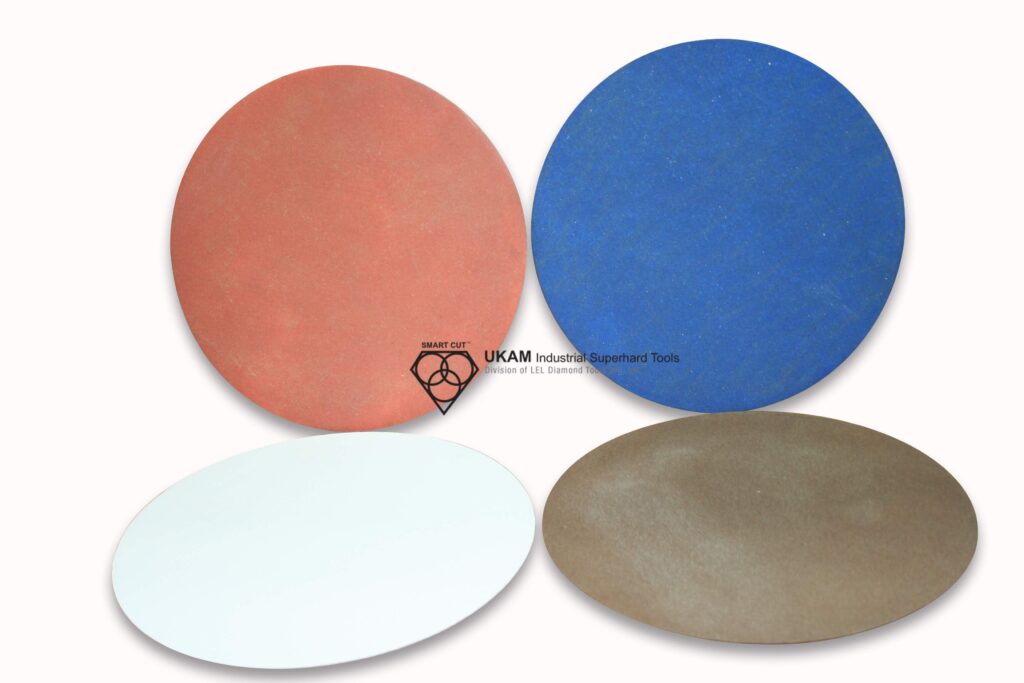
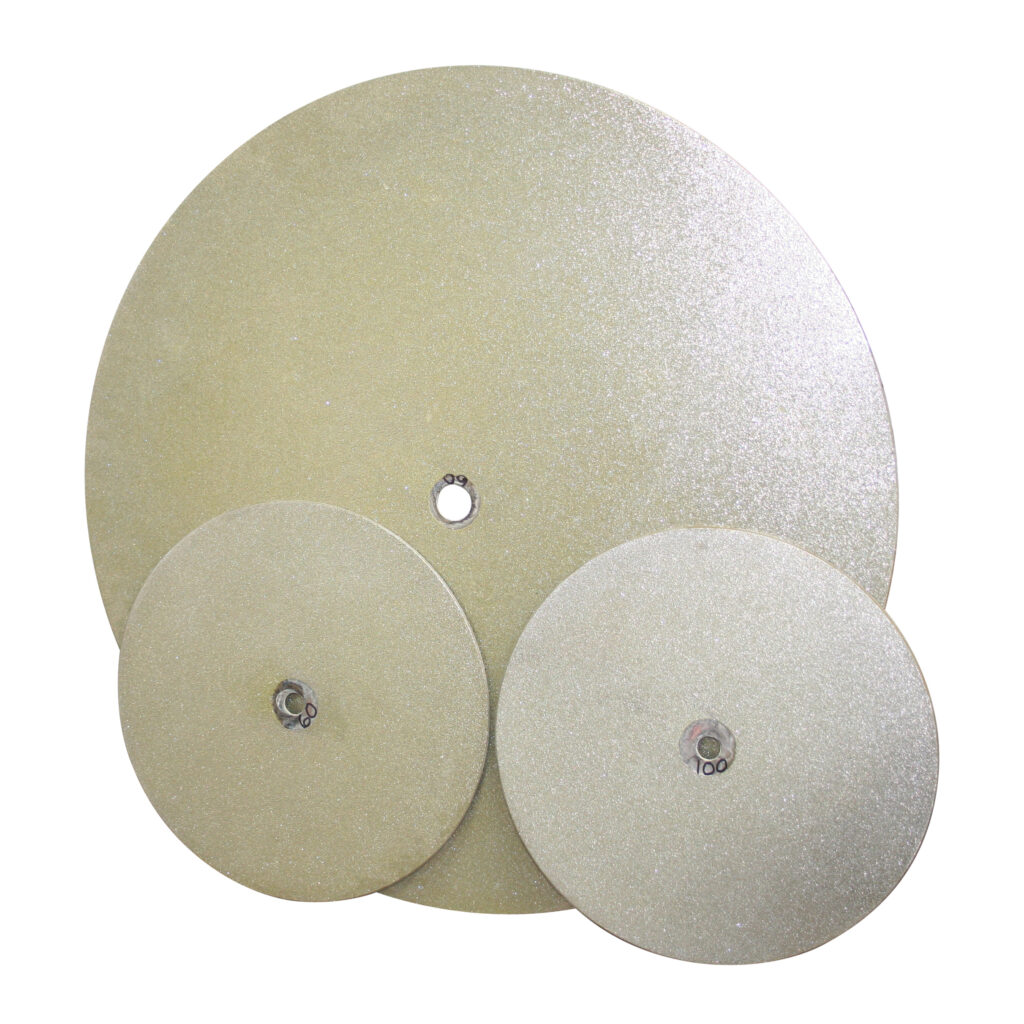
Rigid diamond polishing discs are used for polishing harder materials such as glass and ceramics, providing precise and consistent polishing. These discs also benefit from lower RPMs, generally between 500 to 2,000 RPM, depending on the material and surface requirements. The lower RPMs ensure a uniform finish and prevent surface defects.
Diamond & CBN Tool Diameter and RPM Selection
Tool diameter plays a significant role in determining the optimal RPM for machining operations involving industrial diamond tools. The relationship between tool diameter and RPM is crucial for achieving the desired cutting speed and maintaining efficient, high-quality machining.
Relationship Between Tool Diameter and RPM
The cutting speed or surface speed of a tool is expressed in surface feet per minute (SFM) or meters per minute (MPM) and is calculated using the following equation:
Cutting Speed (V)=𝜋×Diameter (D)×RPMCutting Speed (V)=π×Diameter (D)×RPM
From this equation, it is clear that for a given cutting speed, the RPM must decrease as the diameter of the tool increases. Conversely, smaller diameter tools can be rotated at higher RPMs to achieve the same cutting speed.
Impact of Tool Diameter on Cutting Speed
Larger diameter tools have a greater cutting surface, which means they cover more distance per revolution. To maintain an appropriate cutting speed, the RPM must be adjusted accordingly:
1. Large Diameter Tools:
Examples: Large saw blades, grinding wheels, or core drills.

Optimal RPM: Large diameter tools typically operate at lower RPMs to achieve suitable cutting speeds. For example, a large grinding wheel with a diameter of 10 inches may operate between 500 to 1,500 RPM, depending on the material and application.
Considerations: Lower RPMs for larger tools help prevent excessive centrifugal forces, which can lead to tool warping or failure. Additionally, lower RPMs reduce thermal damage and maintain tool stability.
2. Small Diameter Tools:
Examples: Small burrs, micro-drills, or fine grinding wheels.
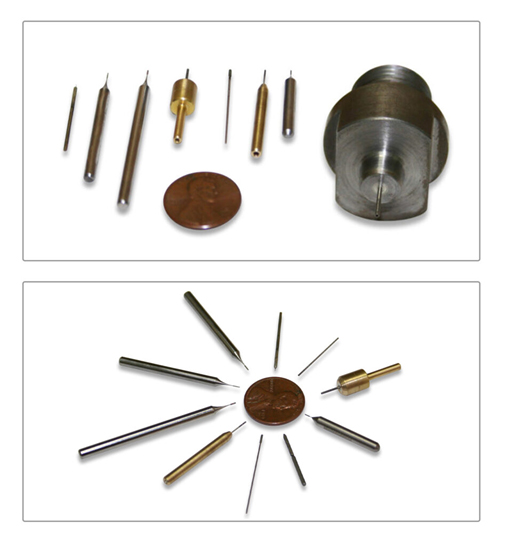
Optimal RPM: Small diameter tools can be operated at higher RPMs to maintain effective cutting speeds. For example, a small micro-drill with a diameter of 1 millimeter may operate between 10,000 to 50,000 RPM, depending on the material and application.
Considerations: Higher RPMs for smaller tools facilitate efficient material removal and improved surface finish. However, care must be taken to avoid excessive tool wear or breakage due to high rotational speeds.
Cutting Environment
The cutting environment, including the presence of coolants or lubrication, impacts the choice of RPM:
-
Wet Cutting: Using coolants allows for higher RPMs as it helps dissipate heat.
-
Dry Cutting: Lower RPMs are necessary to prevent overheating in dry cutting conditions.
Effects of Incorrect RPM
Operating at incorrect RPMs can have several detrimental effects on both the tool and the workpiece:
Diamond Tool Wear and Damage
Diamond tools, while exceptionally hard and durable, are not immune to wear and damage. The choice of RPM during usage is a critical factor in the longevity and effectiveness of diamond tools. Operating at incorrect RPMs can result in various issues, including overheating, bond breakdown, and tool warping. Below, we explore these issues in detail.
1. Overheating
Overheating is one of the primary causes of diamond tool wear and damage. High RPMs can cause excessive heat buildup, leading to thermal damage or even catastrophic failure of the diamond tool.
During high-speed machining, friction between the tool and the workpiece generates significant heat. If the RPM is too high, this heat can quickly accumulate, especially in materials with low thermal conductivity or when cutting fluids are not effectively used.
Excessive heat can degrade the diamond particles, leading to dulling or even fracturing of the diamonds. It can also damage the tool's bond, resulting in bond breakdown or loosening of the diamond particles. In extreme cases, overheating can cause the tool to fail catastrophically. This failure might involve cracking, shattering, or rapid degradation of the tool, posing risks to both the machine and operator.
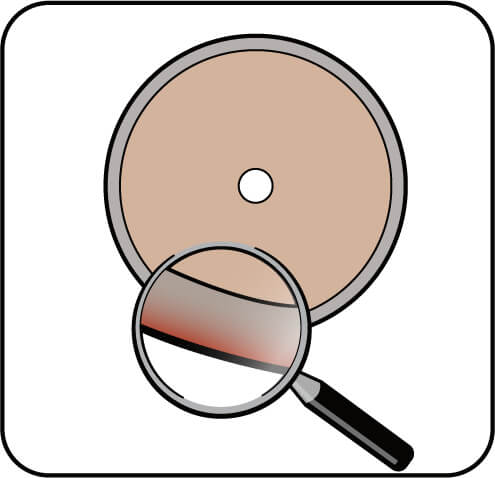
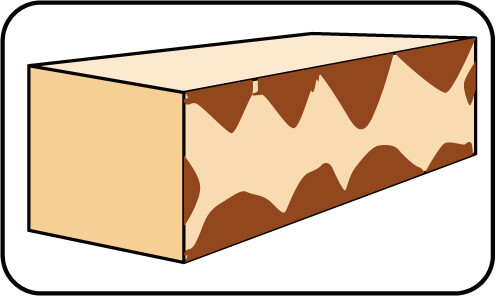
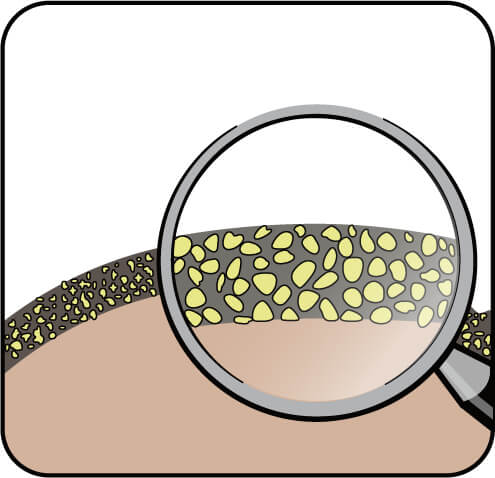
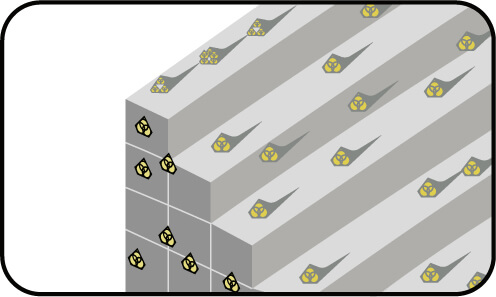
2. Bond Breakdown
The bond holding the diamond particles in place is crucial for tool performance. Incorrect RPMs can cause this bond to break down prematurely, reducing tool life and effectiveness.
Diamond tools use various bond types, including resin, metal, and vitrified bonds. Each bond type has an optimal RPM range, and operating outside this range can cause the bond to weaken or fail. High RPMs can cause excessive wear or breakdown of the bond, especially if the tool overheats or experiences excessive mechanical stresses.
This wear reduces tool life and can result in uneven cutting or grinding. Maintaining bond integrity is crucial for consistent tool performance. Premature bond breakdown leads to uneven tool wear, degraded surface finish, and increased risk of tool failure.
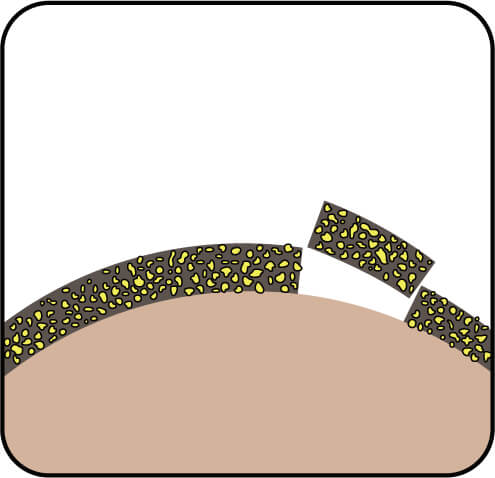
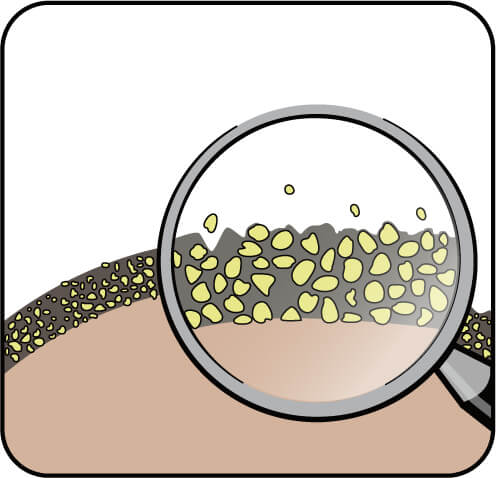
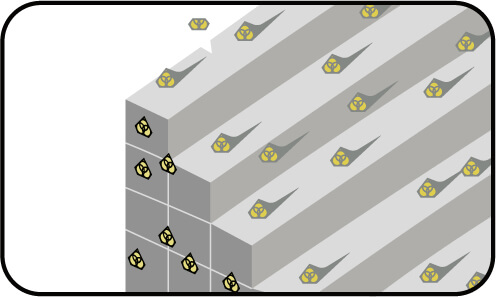
3. Tool Warping
Tool warping is a particular concern for ultra-thin diamond blades and other delicate tools. High RPMs can create centrifugal forces that warp or distort the tool, affecting performance and accuracy. As RPM increases, centrifugal forces act on the tool. For ultra-thin blades or small diameter tools, these forces can cause the tool to warp or deform, leading to inaccurate cuts or damage.
High RPMs can also cause uneven thermal expansion in the tool, particularly if overheating occurs. This thermal expansion can warp or distort the tool, affecting dimensional accuracy and surface finish. Maintaining structural integrity is crucial for ultra-thin or precision diamond tools. Warping not only affects performance but also increases the risk of tool failure or breakage.
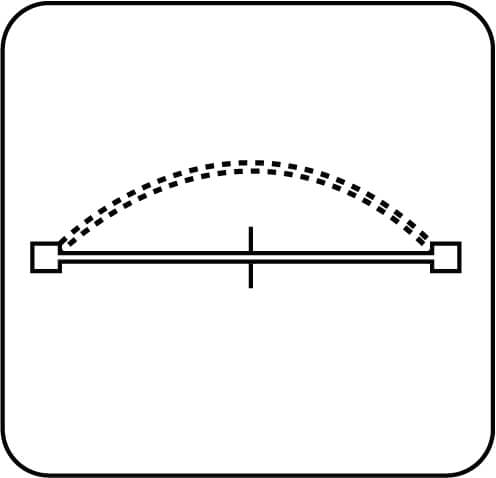
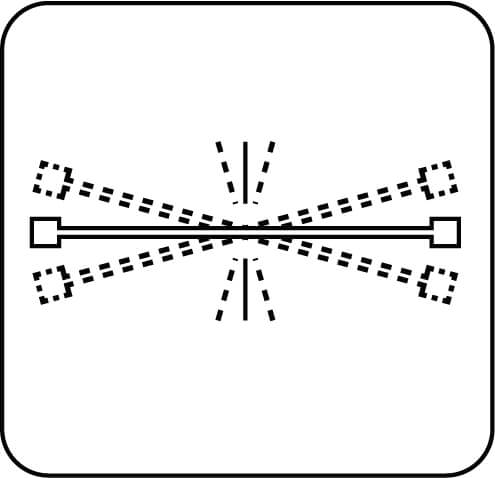
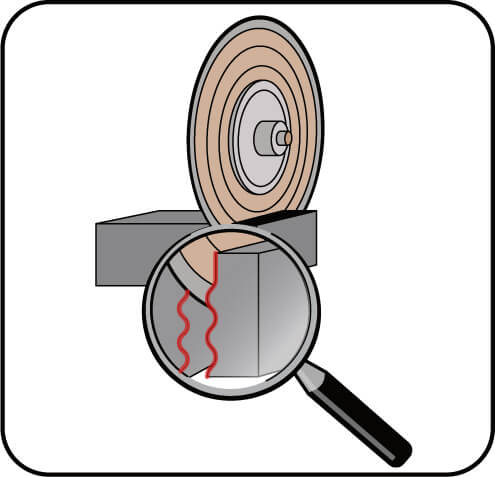
Material Damage Due to Incorrect RPM
Selecting the appropriate RPM is crucial for maintaining the integrity of the material being machined. When RPMs are too high or too low, the resulting issues can lead to material damage, adversely impacting the quality and usability of the final product. The main types of material damage include cracking or chipping, surface burns, and dimensional inaccuracies.
1. Cracking or Chipping
Cracking or chipping occurs when brittle materials like glass and ceramics are processed at high RPMs. The increased cutting forces generated by high RPMs can create stress concentrations in these materials, causing them to fracture.
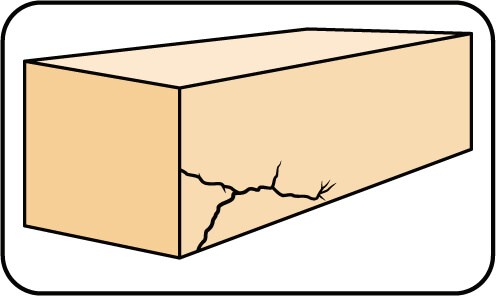
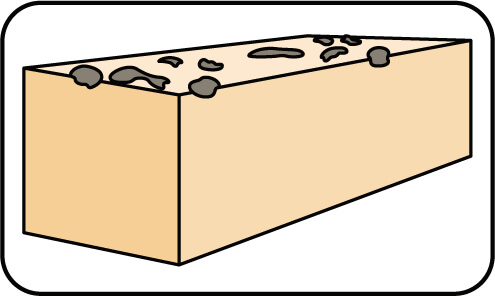
Cracking typically happens when the material is subjected to excessive mechanical or thermal stress. High RPMs increase the cutting forces, which can induce tensile stresses in brittle materials, leading to cracking. This is particularly problematic for materials like silicon wafers, glass sheets, and ceramic tiles, where even minor cracks can render the component unusable.
Chipping occurs when small pieces break off the edge of the material during cutting or grinding. High RPMs can increase the impact forces at the cutting edge, resulting in chipping, which affects both the structural integrity and aesthetic quality of the material. This is common in precision optical components, ceramic substrates, and delicate glassware, where edge quality is critical.
2. Surface Burns
Surface burns or discoloration can occur when metals and other materials are cut or ground at inappropriate RPMs.
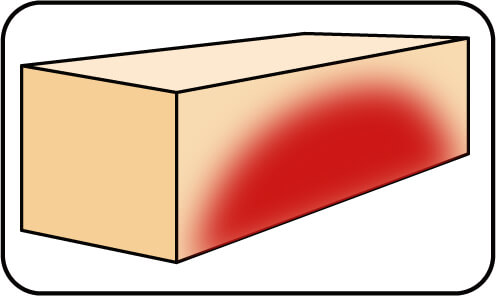
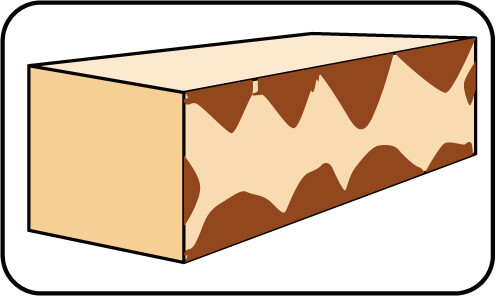
This problem arises from excessive heat generation during machining. Surface burns are typically caused by excessive friction and heat, which can occur when the RPM is too high for the material being processed. The heat generated can oxidize the surface, leaving unsightly marks or altering the material's properties. For example, stainless steel can develop blue or black discoloration due to oxidation, while aluminum can become pitted or damaged.
Discoloration is a visual indication of thermal damage and can affect the appearance and functionality of the finished part. Incorrect RPMs, especially when cutting or grinding metals, can cause surface discoloration, which may compromise the aesthetic quality of components used in decorative or high-visibility applications.
3. Dimensional Inaccuracies
Dimensional inaccuracies occur when incorrect RPMs lead to poor control over the cutting or grinding process, affecting the size, shape, or tolerance of the finished part.
Incorrect RPMs can result in uneven material removal, thermal distortion, or tool deflection, all of which can affect the dimensional accuracy of the part. This is particularly problematic for precision components, such as bearings, gears, or medical implants, where tight tolerances are crucial.
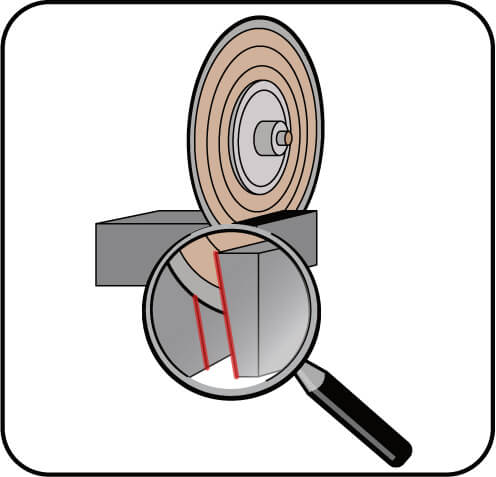
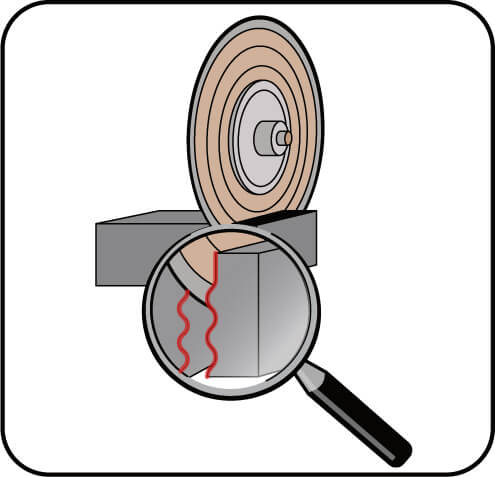
Out-of-roundness is another issue that can arise in operations like drilling or grinding, where incorrect RPMs can lead to out-of-round holes or cylindrical parts. High RPMs can cause tool chatter or vibration, resulting in non-circular or inconsistent dimensions. This issue affects components like bushings, shafts, or tubing, where roundness is essential for proper function. Warping or bowing can also result from incorrect RPMs, as thermal distortion or mechanical stress can lead to warped or bowed parts. This is especially common when machining thin or delicate materials, such as electronic substrates, optical lenses, or metal sheets, where flatness and dimensional stability are crucial.
How to Select the Right RPM’s for your application
Selecting the appropriate RPM for a given application is crucial for achieving optimal machining performance. The following strategies offer a structured approach to RPM selection, ensuring efficiency, quality, and tool longevity.
1. Consult Manufacturer Recommendations
To select the correct RPM, it's important to follow the specific RPM ranges provided by the tool manufacturer. These recommendations are based on extensive testing and should be your primary reference point when determining RPMs. The manufacturer's guidance accounts for the tool's design, material, and intended application, offering a safe and effective starting point for most operations. Additionally, the tool specifications often include specific parameters, such as maximum and minimum RPMs, which help prevent damage or excessive wear. By aligning with these recommendations, you ensure the tool operates within its designed capabilities.
2. Use Machining Guidelines
Various machining handbooks and guides offer RPM ranges for different materials and applications, providing a solid starting point for RPM selection, particularly when working with new or unfamiliar materials. These guidelines are often based on industry standards and best practices, offering reliable RPM ranges for common materials and operations. They categorize RPMs based on material properties, such as hardness, brittleness, or ductility, and also consider the type of operation, such as roughing, finishing, or drilling. This tailored approach ensures appropriate RPMs for specific materials and tasks.
3. Adjust Based on Application
Practical considerations, such as the need for fine finishes or aggressive material removal, also influence RPM selection. Generally, higher RPMs yield smoother finishes, while lower RPMs allow for more controlled material removal. For example, applications requiring fine surface finishes, such as precision components or decorative parts, benefit from higher RPMs to produce smooth, polished surfaces. On the other hand, applications requiring aggressive material removal, such as roughing or heavy grinding, benefit from lower RPMs for controlled and efficient cutting. The specific application context, such as machining delicate parts or removing large amounts of material, should guide adjustments to meet desired outcomes.
4. Monitor Tool Performance
Regularly monitoring tool performance during operation is crucial for maintaining optimal RPMs. Observing signs of overheating, unusual noises, or visible damage can indicate incorrect RPMs, requiring adjustment. Monitoring the tool's temperature helps identify overheating, which indicates excessively high RPMs or insufficient cooling. Unusual noises or excessive vibration often signal incorrect RPMs, misalignment, or tool imbalance, requiring adjustments or troubleshooting. Visible signs of tool wear or damage, such as chipped edges or dulled surfaces, suggest inappropriate RPMs or cutting conditions, prompting reevaluation and adjustment.
5. Use Variable Speed Control
Modern machinery often includes variable speed control, which allows for fine-tuning of RPMs during operation. This feature is particularly useful when experimenting with different materials or adjusting for tool wear over time. Variable speed control enables incremental adjustments to RPMs, allowing precise optimization for specific materials, tools, or applications. Some advanced machines offer adaptive control, automatically adjusting RPMs based on real-time feedback, such as cutting forces, temperature, or tool condition. The flexibility of variable speed control supports diverse operations, enabling quick adaptation to changing conditions, material properties, or operational requirements.
Surface Finish and RPM
The RPM, or revolutions per minute, directly affects the surface finish of a machined material. The relationship between RPM and surface finish is complex and varies depending on the material, tool, and machining conditions.
1. High RPMs for Smoother Finishes
In general, higher RPMs result in smoother finishes. When the RPM is increased, the cutting edge of the tool engages with the material more frequently. This frequent engagement leads to the formation of finer chips, which in turn produces smoother surfaces.
Higher RPMs also reduce the size of the tool marks left on the material surface, which enhances the surface finish. This is especially relevant for finishing operations where a polished or refined surface is desired. For example, in turning operations, a higher RPM can result in a finer finish, as the tool makes smaller, more frequent passes over the material. Similarly, in grinding and polishing applications, increasing the RPM can lead to a better surface finish by reducing the roughness of the machined surface.
2. Low RPMs for Rougher Finishes
Conversely, lower RPMs may produce rougher surfaces. This is because the cutting edge engages with the material less frequently, leading to larger chips and more pronounced tool marks. Low RPMs are often used for roughing operations, where the goal is to remove material quickly rather than achieve a fine finish.
Rough finishes created at low RPMs may be beneficial in certain applications where adhesion or bonding is required, as the rough surface can provide better mechanical interlocking. For example, in adhesive bonding, a rougher surface may enhance the bond strength between the material and the adhesive.
3. Tool Chatter and Vibration
However, excessively high RPMs can cause tool chatter or vibration, which negatively impacts the surface finish. Tool chatter occurs when the tool vibrates uncontrollably against the material, leading to an uneven and often scalloped surface. This chatter is typically caused by resonance between the tool and the workpiece, which can be exacerbated by high RPMs.
Vibration can also be introduced from other sources, such as machine misalignment, imbalanced tools, or improper workholding. When vibration occurs, the resulting surface finish is often characterized by irregular patterns or waviness, detracting from the desired smoothness.
4. The Sweet Spot for RPM
Finding the sweet spot for RPM is crucial for achieving the desired surface quality. The sweet spot is the RPM range where the cutting conditions are optimal for both material removal and surface finish. This range varies based on factors such as the material being machined, the tool geometry, and the machining operation.
For example, in milling operations, the sweet spot for RPM may depend on the diameter of the milling cutter, the feed rate, and the type of material being milled. In grinding operations, the sweet spot may depend on the type of grinding wheel, the speed of the wheel, and the material being ground.
5. Balancing Surface Finish with Other Factors
When selecting the optimal RPM for surface finish, it is important to balance it with other factors such as material removal rate, tool life, and machining efficiency. For example, while higher RPMs may improve surface finish, they may also increase tool wear or reduce material removal rates. Similarly, while lower RPMs may produce rougher surfaces, they may increase tool life or improve material removal rates.
By carefully balancing these factors, operators can select the optimal RPM that achieves the desired surface quality while also meeting other machining requirements.
Cutting Fluids and RPM
Cutting fluids or coolants play a critical role in many machining operations, particularly those involving industrial diamond tools. These fluids serve several essential functions during machining, such as cooling, lubrication, and debris removal, which all influence the optimal RPM for a given operation.
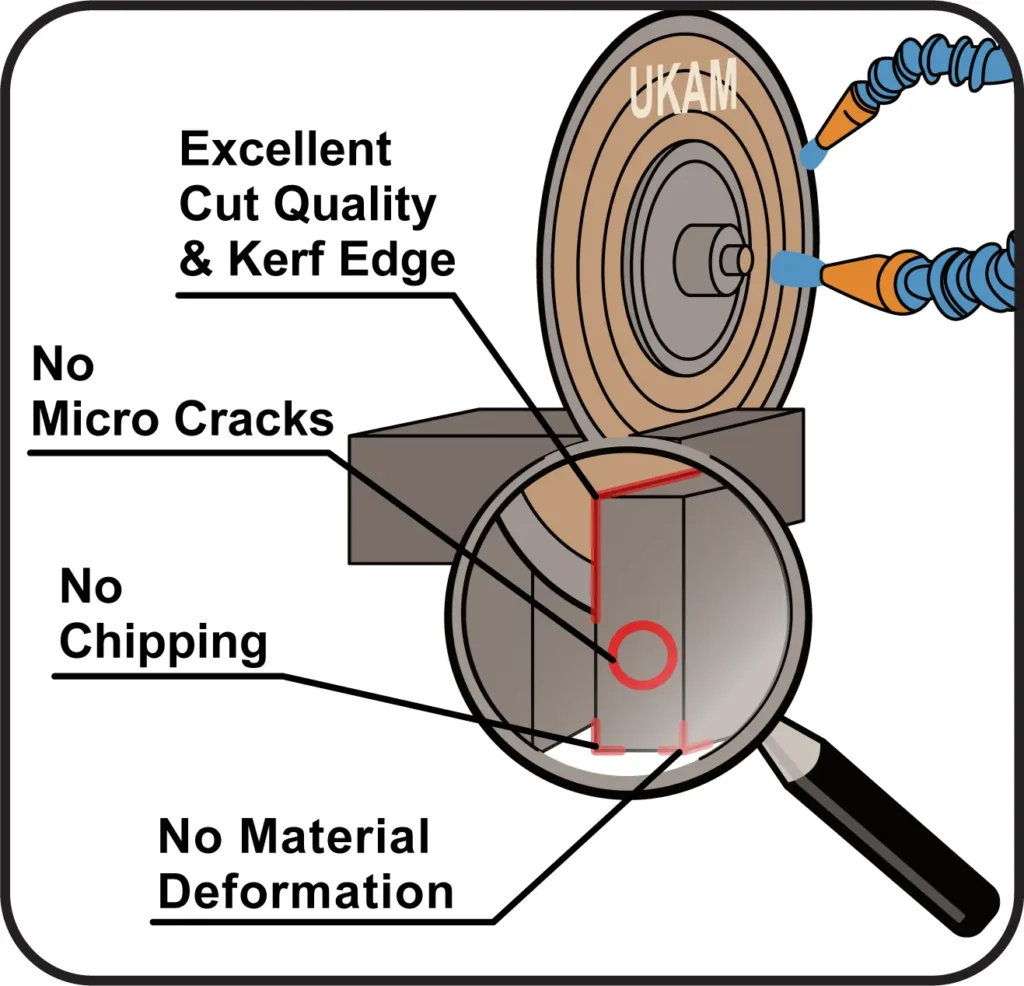
1. Cooling the Tool and Workpiece
Cutting fluids primarily serve to cool the tool and workpiece during cutting or grinding, which helps prevent thermal damage to both the tool and the material being machined. High temperatures can degrade the diamond particles, weaken the tool bond, and damage the workpiece surface. By cooling the tool and workpiece, cutting fluids allow for higher RPMs without overheating. This is especially important in applications like precision grinding, where maintaining a stable temperature is crucial for achieving tight tolerances and preventing material distortion. Lower temperatures also contribute to longer tool life, as excessive heat can accelerate tool wear and lead to premature failure. Using cutting fluids effectively allows operators to maintain optimal RPMs while protecting the tool from thermal damage.
2. Lubricating
Cutting fluids also act as lubricants, reducing friction between the tool and the material, which is crucial for maintaining smooth cutting or grinding operations. Reducing friction minimizes the cutting forces and heat generated during machining, which allows for higher RPMs, as the reduced friction helps maintain stable cutting conditions and prevents excessive tool wear. Additionally, lubrication improves the surface finish of the machined material, as lower friction results in smoother cuts and less risk of scratching or gouging the surface. Higher RPMs, combined with effective lubrication, can enhance the quality of the finished part.
3. Flushing Away Debris
Another important function of cutting fluids is to flush away chips or swarf, maintaining a clean cutting surface. Accumulated debris can interfere with the cutting process, leading to uneven cuts, increased tool wear, or even tool breakage. Cutting fluids help remove debris, allowing for higher RPMs and more efficient material removal. Clearing away chips or swarf also improves surface quality, as trapped debris can scratch or damage the material surface. Proper debris removal, in conjunction with appropriate RPMs, ensures clean and precise machining.
4. Adjusting RPM with Cutting Fluid Type and Amount
The RPM should be adjusted based on the type and amount of cutting fluid used. Wet cutting uses a generous amount of cutting fluid to cool and lubricate the tool and workpiece, allowing for higher RPMs, as the improved cooling and lubrication prevent overheating and reduce cutting forces. Wet cutting is commonly used in applications like grinding, drilling, or sawing, where maintaining a stable temperature and clean surface is crucial.
Dry cutting, which does not use cutting fluids and relies solely on air cooling, requires lower RPMs to prevent overheating, as there is no fluid to dissipate the heat or lubricate the cutting surface. Dry cutting is often used in situations where using cutting fluids is impractical or unnecessary, such as in some woodworking or metalworking applications.
Different cooling methods, such as mist or flood cooling, also affect the optimal RPM. Mist cooling uses a fine spray of cutting fluid, which provides some cooling and lubrication but may not be sufficient for high-speed operations. Flood cooling involves a large volume of fluid, providing excellent cooling and lubrication, allowing for higher RPMs in demanding applications.
Diamond Tool Geometry and RPM
The geometry of a diamond tool plays a crucial role in determining the optimal RPM for machining. Key factors to consider include grit size, tool shape, and bond type, as each of these factors directly influences the tool’s performance, material removal rate, and surface finish.
1. Grit Size
The grit size of a diamond tool refers to the size of the abrasive particles embedded in the tool. This directly impacts the tool’s cutting ability and the surface finish of the material being machined.
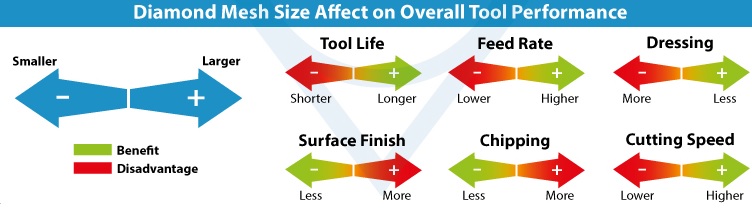
Coarse Grit: Coarse grit diamond tools have larger abrasive particles, making them suitable for high material removal rates (MRR). These tools require lower RPMs to maintain surface integrity, as higher RPMs can generate excessive heat and cause surface damage. Coarse grit tools are ideal for rough grinding or cutting applications where a smooth finish is not the primary concern.
Fine Grit: Fine grit diamond tools have smaller abrasive particles, making them suitable for achieving fine finishes. These tools can operate at higher RPMs, as the smaller particles generate less heat and allow for precise material removal. Fine grit tools are commonly used for finishing operations, such as polishing or precision grinding, where achieving a smooth surface is crucial.
2. Tool Shape
The shape of the diamond tool also affects the optimal RPM, as different shapes are designed for specific applications and cutting conditions.
Flat Blades: Flat diamond blades are commonly used for slicing or dicing materials. These blades benefit from balanced RPMs to prevent warping or chipping. If the RPM is too high, the blade can warp due to centrifugal forces, while too low an RPM can result in uneven cuts or chipping. Flat blades are often used in applications such as wafer slicing or precision cutting of glass and ceramics.
Core Drills: Diamond core drills are hollow tools used for drilling holes in materials like glass, ceramics, and concrete. These tools require lower RPMs to maintain structural integrity and prevent binding. Core drills can overheat or fracture if operated at excessively high RPMs, particularly when drilling brittle materials or thin-walled components.
3. Bond Type
The bond type of a diamond tool refers to the material that holds the diamond particles in place. The bond type impacts the tool’s durability, flexibility, and optimal RPM.
Resin Bond: Resin bond diamond tools are flexible and suitable for medium RPMs. The resin bond provides cushioning, which helps absorb vibrations and prevents tool chatter. These tools are ideal for applications such as grinding and polishing, where a smooth finish and controlled material removal are important.
Metal Bond: Metal bond diamond tools are durable and suitable for high RPMs, especially in demanding grinding applications. The metal bond provides strength and wear resistance, allowing the tool to operate at higher speeds without breaking down. These tools are commonly used in applications such as heavy-duty grinding or cutting of hard materials.
Vitrified Bond: Vitrified bond diamond tools are brittle and suitable for lower RPMs to prevent bond failure. The vitrified bond is typically made of glass or ceramic, which can fracture under high stress or heat. These tools are ideal for precision grinding or finishing applications, where maintaining dimensional accuracy and surface quality is crucial.
RPM and Diamond & CBN Tool Life
The lifespan of diamond tools is significantly influenced by the chosen RPM. Operating at incorrect RPMs can accelerate wear and reduce tool life. Several key factors play a role in determining how RPM impacts tool wear, performance, and longevity.
1. Thermal Damage
High RPMs increase the risk of thermal damage to diamond tools. The friction generated during high-speed machining can cause excessive heat buildup, which degrades the diamond particles or weakens the bond holding them in place. Thermal damage can manifest in several ways:
-
Diamond Degradation: Excessive heat can cause the diamond particles to soften, fracture, or even vaporize. This degradation reduces the tool's cutting effectiveness and shortens its lifespan. In applications such as grinding or high-speed cutting, managing RPM to control heat is crucial for maintaining diamond integrity.
-
Bond Failure: The bond holding the diamond particles in place is also susceptible to thermal damage. High temperatures can weaken the bond, causing the diamonds to dislodge or the tool to lose its structural integrity. Bond failure is particularly problematic in tools with resin or vitrified bonds, which are more sensitive to thermal stress.
To prevent thermal damage, operators should use appropriate coolants or cutting fluids and avoid excessive RPMs, especially when machining hard or brittle materials.
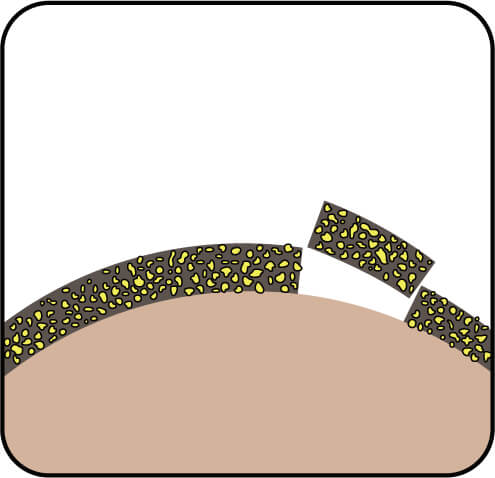
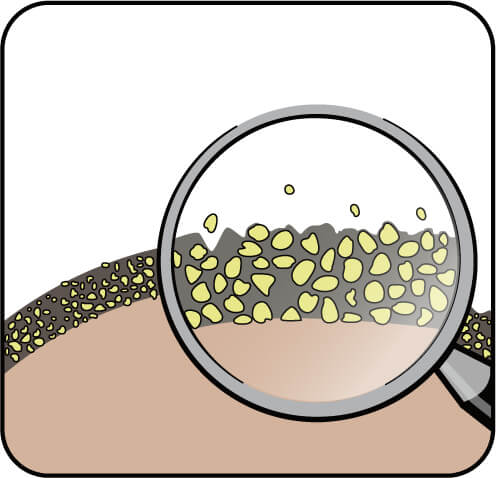
-
Inadequate Cutting Speed: Operating at low RPMs may produce inadequate cutting speeds, reducing the tool's effectiveness and increasing wear. This is particularly problematic when machining hard materials, as the tool may struggle to penetrate or remove material efficiently, leading to excessive friction and wear.
-
Tool Dulling: As the diamond particles wear down, the tool becomes dull and less effective at cutting or grinding. This dulling not only reduces tool life but also affects the quality of the machined surface. Maintaining adequate RPMs helps ensure efficient cutting speeds and reduces abrasive wear.
2. Mechanical Stress
Excessive RPMs can induce mechanical stresses in diamond tools, leading to breakage or deformation. Mechanical stress is a common issue when operating ultra-thin blades, small-diameter tools, or delicate grinding wheels at high speeds:
-
Tool Breakage: High RPMs can generate significant centrifugal forces, which may exceed the tool's structural limits and cause it to break. This is particularly problematic for thin or brittle tools, such as diamond saw blades or core drills, which may fracture or shatter under excessive mechanical stress.
-
Tool Deformation: High RPMs can also cause tool deformation, such as warping or bending. This deformation affects the tool's cutting accuracy and can lead to uneven wear or poor surface finish. For example, ultra-thin diamond blades may warp if operated at excessively high RPMs, resulting in inaccurate or damaged cuts.
To minimize mechanical stress, operators should ensure that the RPM aligns with the tool's design specifications and avoid pushing the tool beyond its structural limits.
3. Abrasive Wear
Lower RPMs may result in inadequate cutting speeds, leading to increased abrasive wear and tool dulling. Abrasive wear occurs when the diamond particles or cutting edges gradually wear down due to friction and material contact:
-
Inadequate Cutting Speed: Operating at low RPMs may produce inadequate cutting speeds, reducing the tool's effectiveness and increasing wear. This is particularly problematic when machining hard materials, as the tool may struggle to penetrate or remove material efficiently, leading to excessive friction and wear.
-
Tool Dulling: As the diamond particles wear down, the tool becomes dull and less effective at cutting or grinding. This dulling not only reduces tool life but also affects the quality of the machined surface. Maintaining adequate RPMs helps ensure efficient cutting speeds and reduces abrasive wear.
To mitigate abrasive wear, operators should select an RPM that matches the material being machined and the tool's capabilities, ensuring efficient cutting and minimizing friction.

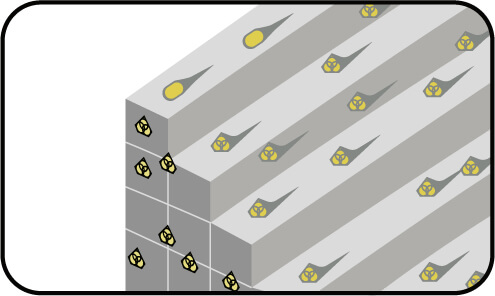
Maximizing Diamond & CBN Tool Life with Correct RPM
By selecting the correct RPM, operators can maximize the lifespan of diamond tools and reduce operational costs. Proper RPM selection helps balance thermal damage, mechanical stress, and abrasive wear, extending tool life and improving performance:
-
Optimize Cutting Speed: Ensuring the RPM provides an optimal cutting speed for the material and tool helps minimize abrasive wear and improve cutting efficiency.
-
Use Appropriate Coolants: Proper cooling helps prevent thermal damage and extends tool life, especially during high-speed or high-temperature operations.
-
Monitor Tool Condition: Regular monitoring of tool wear, surface finish, and cutting forces helps identify signs of thermal or mechanical damage, allowing operators to adjust RPMs and extend tool life.
Balancing RPM with Other Parameters
The RPM, or revolutions per minute, is one of several key parameters that affect machining performance. Achieving optimal machining results requires balancing RPM with other important factors, such as feed rate, depth of cut, and tool path.
1. Feed Rate
Feed rate refers to the speed at which the material moves through the cutting area. It determines how much material is removed per revolution of the cutting tool and must be balanced with RPM to prevent overloading or underutilizing the tool.
-
Balancing Feed Rate and RPM: The correct combination of feed rate and RPM ensures efficient cutting and prevents issues like tool chatter or poor surface finish. If the feed rate is too high relative to RPM, the cutting tool may become overloaded, leading to excessive tool wear or breakage. Conversely, if the feed rate is too low, the tool may be underutilized, resulting in inefficient material removal and potential rubbing or burnishing rather than cutting.
-
Optimizing Feed Rate:The optimal feed rate depends on the tool type, material, and desired surface finish. For example, roughing operations typically use higher feed rates to maximize material removal, while finishing operations use lower feed rates for improved surface quality. The feed rate should be carefully adjusted to align with the selected RPM and the specific machining application.
-
Monitor Tool Condition: Regular monitoring of tool wear, surface finish, and cutting forces helps identify signs of thermal or mechanical damage, allowing operators to adjust RPMs and extend tool life.
2. Depth of Cut
Depth of cut refers to the thickness of the material being removed during each pass of the cutting tool. It determines the amount of material engaged with the tool and affects the required RPM.
-
Balancing Depth of Cut and RPM: The correct balance of depth of cut and RPM helps prevent excessive tool load and ensures consistent material removal. Higher RPMs typically allow for shallower depths of cut, as increased cutting speed reduces the load on the tool. However, if the depth of cut is too large, even high RPMs may not be sufficient to prevent tool overload or deflection.
-
Optimizing Depth of Cut:The optimal depth of cut depends on the tool, material, and machining operation. Roughing operations typically use larger depths of cut to maximize material removal, while finishing operations use shallower depths of cut for improved surface quality. The depth of cut should be adjusted to match the selected RPM and ensure efficient and safe machining.
-
Monitor Tool Condition: Regular monitoring of tool wear, surface finish, and cutting forces helps identify signs of thermal or mechanical damage, allowing operators to adjust RPMs and extend tool life.
3. Tool Path
Tool path refers to the direction and pattern of tool movement during machining. The RPM should be adjusted to accommodate changes in tool path, such as during cornering or contouring.
-
Balancing Tool Path and RPM: The correct combination of tool path and RPM ensures smooth and accurate machining, especially during complex movements. When the tool path involves sharp corners or tight contours, the RPM should be reduced to maintain control and prevent excessive tool or material stresses. Conversely, during straight or simple tool paths, higher RPMs can be used to maximize cutting speed and efficiency.
-
Optimizing Tool Path:The optimal tool path depends on the geometry of the part, the tool type, and the desired outcome. Complex shapes or intricate features may require lower RPMs to maintain accuracy, while simple or repetitive shapes may benefit from higher RPMs for faster machining. The tool path should be carefully planned and adjusted to align with the selected RPM and ensure optimal performance.
Balancing RPM with Cost Considerations
Selecting the correct RPM for machining operations has significant financial implications. By optimizing the RPM, operators can reduce costs, improve efficiency, and enhance overall operational effectiveness. Here are key ways in which RPM selection affects costs in machining operations:
1. Reduce Tool Costs
Proper RPM selection is crucial for extending tool life, which in turn reduces the frequency of tool replacements and associated costs. This is particularly important for expensive diamond tools, which are often used in specialized or precision applications.
When the RPM is too high, excessive heat and mechanical stress can accelerate tool wear, leading to premature failure or damage. This not only increases tool replacement costs but also disrupts production schedules. Conversely, when the RPM is too low, it can lead to ineffective cutting or grinding, resulting in increased abrasive wear and shorter tool life. By selecting the correct RPM, operators can protect their investment in high-quality tools and minimize unnecessary expenses.
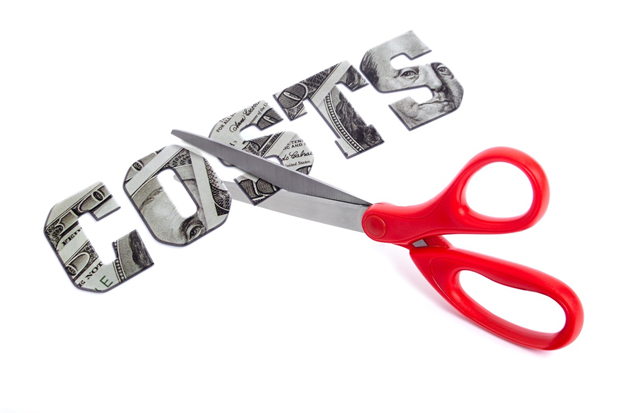
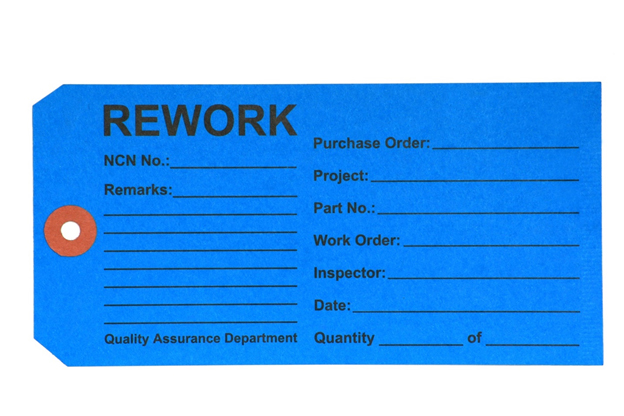
2. Minimize Scrap and Rework
Incorrect RPMs can result in defective parts that must be scrapped or reworked, incurring additional costs. This is particularly relevant in precision machining or high-value manufacturing, where product quality and consistency are critical.
When the RPM is not optimized, it can lead to issues such as poor surface finish, dimensional inaccuracies, or material damage, which render parts unusable or require costly rework. By ensuring the correct RPM, operators can improve product quality, minimize waste, and enhance customer satisfaction. This not only reduces direct costs associated with scrap or rework but also prevents indirect costs related to delays, quality complaints, or lost business opportunities.
3. Improve Efficiency
Optimal RPMs maximize material removal rates and minimize cycle times, improving overall efficiency and reducing production costs. This is especially beneficial for high-volume or high-throughput operations, where small improvements in cycle time can lead to significant cost savings.
By adjusting the RPM to match the material, tool, and machining conditions, operators can achieve faster and more efficient material removal, reducing the time and resources required for each part. This enhances productivity, reduces labor costs, and increases capacity, allowing operators to meet demand more effectively and improve profitability.
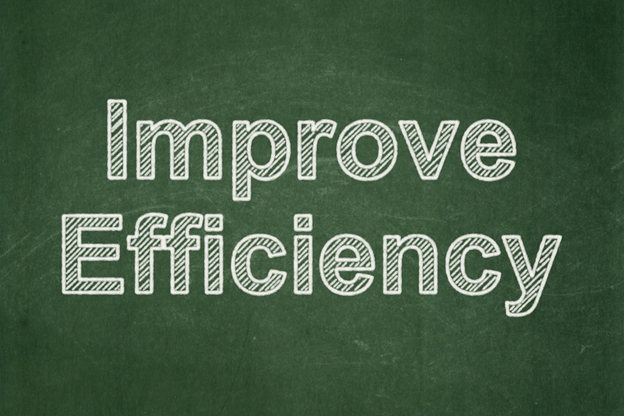
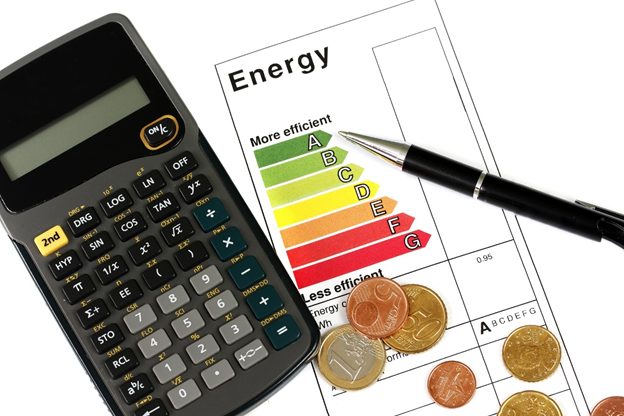
4. Energy Savings
Running at excessively high RPMs consumes more energy and increases operational costs. By selecting the appropriate RPM, operators can reduce energy consumption and lower utility bills, which is particularly important for energy-intensive machining operations.
Excessive RPMs can lead to increased friction, heat, and mechanical resistance, all of which require additional energy to overcome. In contrast, operating at the optimal RPM minimizes unnecessary energy use, reducing both direct energy costs and the associated environmental impact. This is especially important in today’s business environment, where energy efficiency and sustainability are increasingly valued by customers, regulators, and stakeholders.
RPM and Diamond & CBN Tool Runout
Tool runout refers to the deviation of the tool's rotating axis from its ideal path, which can result in uneven cutting or grinding. Runout occurs when the cutting edge or abrasive surface of the tool does not remain perfectly concentric with the axis of rotation, leading to irregular cutting forces and poor surface finishes. High RPMs can exacerbate runout issues, leading to increased tool wear, vibration, and compromised machining quality.
Flood Cooling
Flood cooling involves applying a large volume of coolant to the cutting area, effectively dissipating heat and reducing tool wear. This method is particularly useful for higher RPMs, especially in grinding applications where excessive heat can damage the tool or workpiece. Flood cooling helps maintain optimal temperatures and provides lubrication, allowing for efficient material removal at higher speeds. This method is ideal for applications where maintaining a consistent temperature and reducing friction are crucial for achieving high-quality results and prolonging tool life.
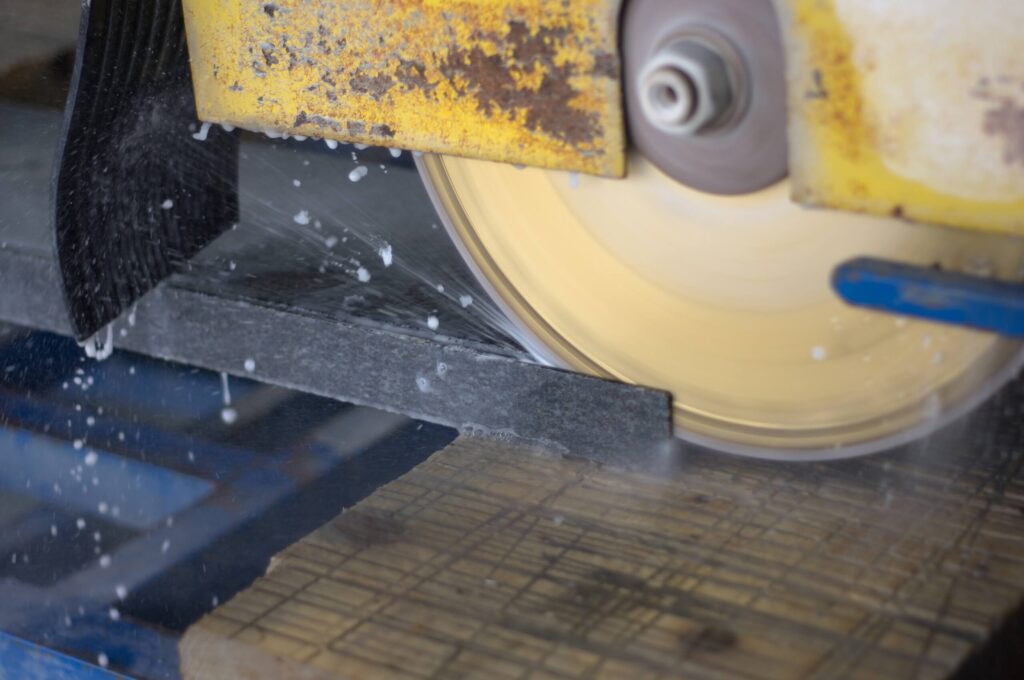
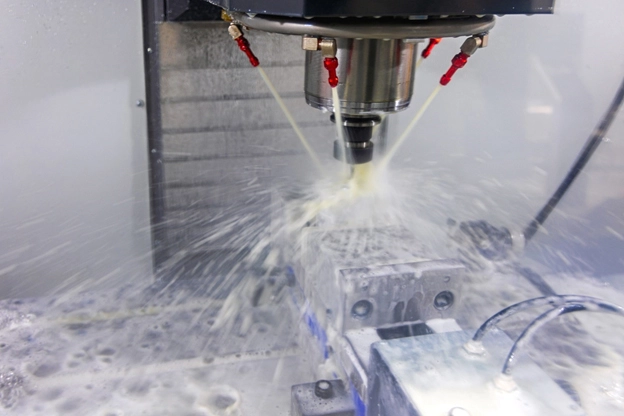
Mist Cooling
Mist cooling uses a fine spray of coolant to lubricate and cool the cutting area. This method is suitable for high-RPM operations, such as micro-machining or light grinding, where excessive fluid could interfere with precision. Mist cooling provides adequate cooling and lubrication without overwhelming the work area, making it ideal for delicate or detailed machining. The fine mist helps to keep the tool and workpiece cool while allowing for precise control over the machining process. This method is often used in applications where high RPMs are necessary for fine finishes or intricate work.
Dry Cutting
Dry cutting is typically limited to applications where coolant is impractical or unnecessary. In dry cutting, lower RPMs are recommended to prevent overheating and tool damage. This method is often used in materials that are sensitive to moisture or where the use of coolants could contaminate the workpiece. Dry cutting relies on air or the natural cooling properties of the material to manage heat, making it less effective for high-speed operations. However, it is suitable for certain applications where wet cutting is not feasible, and it requires careful control of the RPM to avoid thermal damage and ensure consistent machining.
Case Studies in RPM Optimization
To illustrate the importance of RPM selection, consider the following case studies:
Wafer Slicing
-
Application: Slicing silicon wafers for semiconductor manufacturing.
-
Issue: Excessive RPMs caused micro-cracks and reduced wafer yield.
-
Solution: Reducing the RPM to 2,000 improved wafer quality and increased yield.
In semiconductor manufacturing, precision is crucial, and micro-cracks can lead to significant losses. The solution involved reducing the RPM to prevent excessive forces on the brittle silicon, resulting in improved quality and yield.
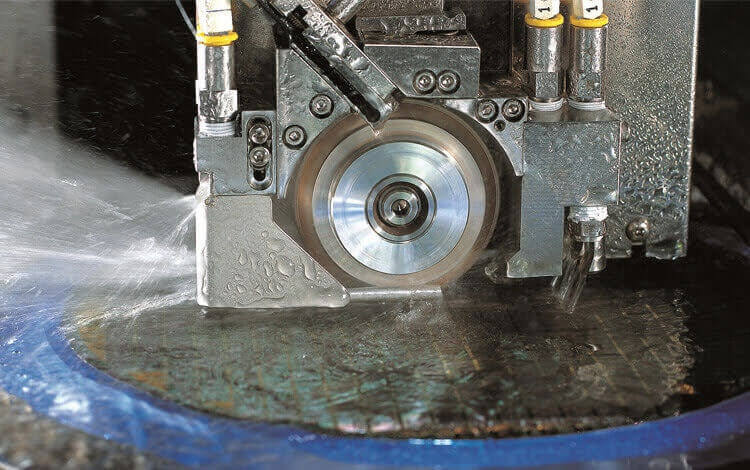

Precision Grinding
-
Application: Grinding hardened steel components for automotive applications.
-
Issue: High RPMs caused overheating and surface burns.
-
Solution: Adjusting the RPM to 5,000 improved surface finish and extended tool life.
In this automotive application, overheating caused surface defects and shortened tool life. By lowering the RPM, the grinding process became more controlled, leading to better surface quality and longer-lasting tools.
Glass Polishing
-
Application: Polishing optical glass for lenses.
-
Issue: Low RPMs resulted in inadequate polishing and poor surface quality.
-
Solution: Increasing the RPM to 1,500 achieved a flawless finish and improved optical clarity.
For optical glass, a smooth finish is essential for clear optics. The initial low RPMs did not provide sufficient polishing action, but increasing the RPM provided the necessary speed to achieve a flawless, clear finish.
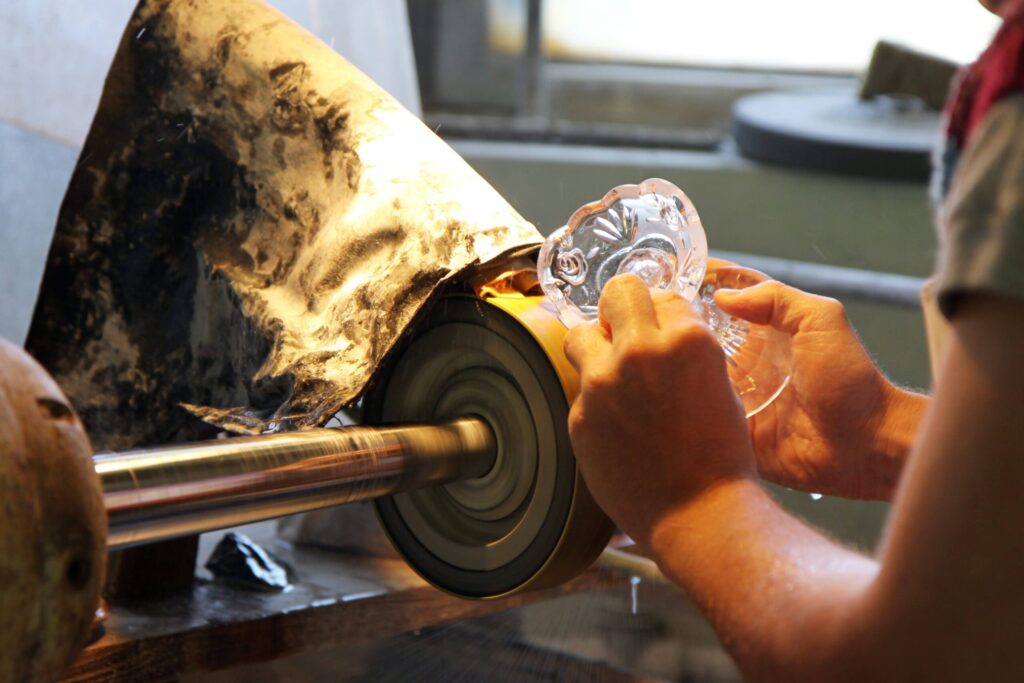
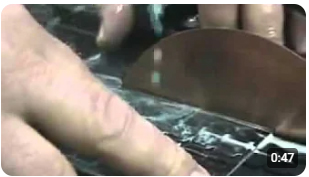
Precision Glass Cutting
-
Application: Cutting optical glass for lenses.
-
Issue: High RPMs caused edge chipping and surface defects.
-
Solution: Lowering the RPM to 2,500 reduced chipping, resulting in cleaner cuts and higher-quality lenses.
High RPMs can damage brittle materials like glass, leading to poor quality. Lowering the RPM provided a more controlled cutting process, resulting in better-quality lenses.
Ceramic Tile Drilling
-
Application:Drilling holes in ceramic tiles for fixtures.
-
Issue: Excessive RPMs led to cracked tiles and wasted materials.
-
Solution: Reducing the RPM to 1,000 allowed for clean, accurate drilling without damaging the tiles.
Ceramic tiles are prone to cracking under excessive drilling speeds. By reducing the RPM, the drilling process became more controlled, preventing damage and waste.
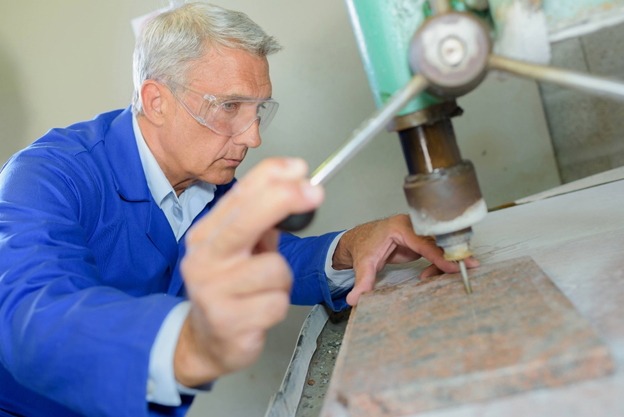
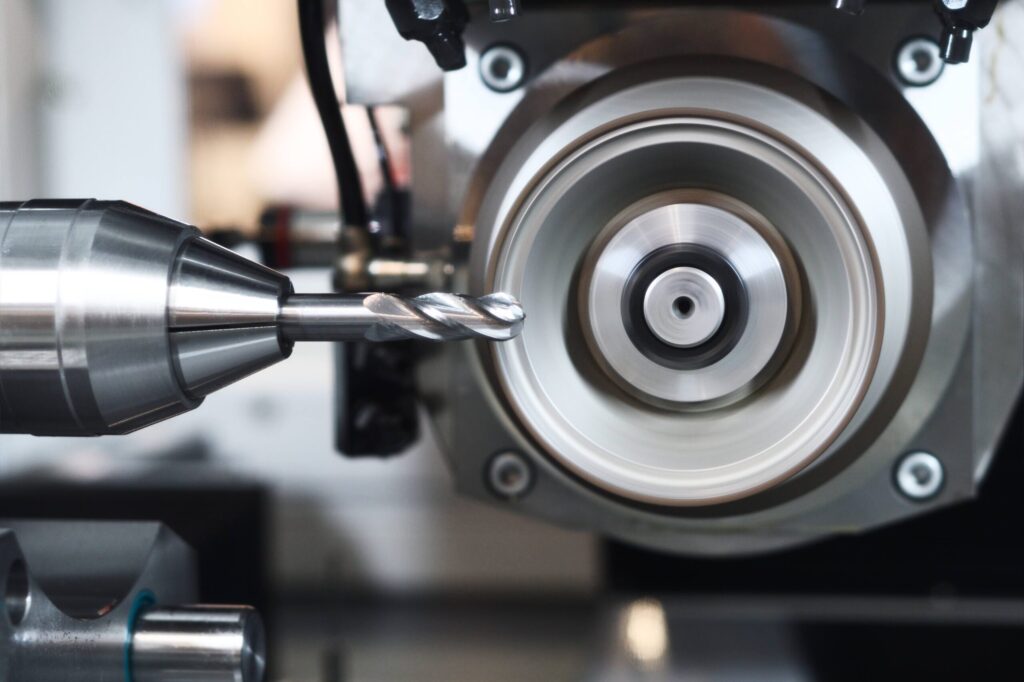
Metal Grinding
-
Application:Grinding hardened steel components.
-
Issue: High RPMs caused overheating and surface burns.
-
Solution: Adjusting the RPM to 5,500 reduced heat buildup, resulting in improved surface finish and longer tool life.
Overheating is a common issue in metal grinding, leading to poor finishes and reduced tool life. Lowering the RPM mitigated heat buildup, enhancing surface quality and extending tool lifespan.