Performance of Diamond or CBN Tools is not solely dependent on the diamond grit itself but also on the bond matrix that holds the diamonds in place. The bond matrix serves a dual function: retaining and exposing the diamond grit, which directly impacts the efficiency and effectiveness of the cutting process.
The hardness of this bond, categorized from very soft to very hard, plays a critical role in determining how well the tool performs across various parameters. This article explores the importance of selecting the right bond hardness for different applications and examines the factors influencing this decision. By understanding the relationship between bond hardness and key performance attributes such as cutting speed, feed rate, dressing frequency, and tool life, users can make informed choices to optimize their cutting processes.
In the following sections, we delve into the categorization of bond hardness, the function of the bond matrix, and the factors influencing its performance. We also discuss the correlation between bond hardness and overall tool performance, providing a comprehensive guide for selecting the appropriate diamond tool bond hardness for various precision cutting applications.
Bond Matrix Function
The primary function of the bond matrix in a diamond tool is to retain and expose the diamond grit, which is integral to the cutting action. The bond acts as a binder that holds the diamond particles in place, allowing them to cut into the material. The diamond particles gradually wear down as they cut, and when they become dull, the bond releases them to expose fresh, sharp diamond particles.
The goal is to hold the diamond crystals tightly in place and to release the diamond crystals (wear) at pace compatible with their loss. The wear rate/resistance of the bond matrix has to be in correlation with abrasiveness of material being cut, in order to achieve the most optimum ratio. So that height diamond crystals protrudes insufficiently nor they are lost or dislodges before they have a chance of being used to their full potential. A bond matrix that is too โsoftโ for the application will wear at rate much faster then the diamond crystal/particles themselves. Resulting in premature diamond pullout and ineffectiveness in tool performance associated with this issue. Bond hardness that is too hard, would wear more slowly then diamond crystal breaks down, causing diamond crystal to glaze over, hence to stop working effectively.
Wear Mechanism and Diamond Exposure
As the diamond particles cut into the material, they gradually wear down. The rate at which they wear depends on several factors, including the hardness of the material being cut and the bond matrix's properties. When the diamonds become dull, the bond matrix must release them to expose fresh, sharp diamond particles, ensuring continued cutting efficiency. The balance between diamond retention and exposure is crucial for optimal cutting performance.
Matrix Hardness and Diamond Retention
The hardness of the bond matrix determines how tightly it holds onto the diamond particles. As the hardness of the bond is increased, its diamond retention capabilities increase as well. However the trade off is slower cutting speed. Life of the diamond or cbn tool is usually increased with hardness of its bond matrix. On the other hand a harder bond matrix will retain the diamonds for longer periods, making it suitable for cutting softer materials. In contrast, a softer bond matrix releases diamonds more quickly, which is advantageous when cutting harder materials. The key is to match the matrix hardness with the application requirements to achieve the desired cutting performance.
Bonds are designated on their scale of hardness from Soft, Medium, and Hard. There are dozens of variations and classification schemes based on bond degree of hardness or softness. Using diamond tools or cbn with optimum bond hardness for your application is important to successful precision diamond sawing operation. Bond matrix that is too soft for the material being cut will release diamond particles faster than needed, resulting in faster wear and shorter diamond blade life. On other hand bond matrix that is too hard will result in much slower cutting speeds and require constant dressing to expose the next diamond layer. As rule of thumb, harder materials such as sapphire and alumina generally require a softer bond. Whereas softer and more brittle materials require a harder bond.
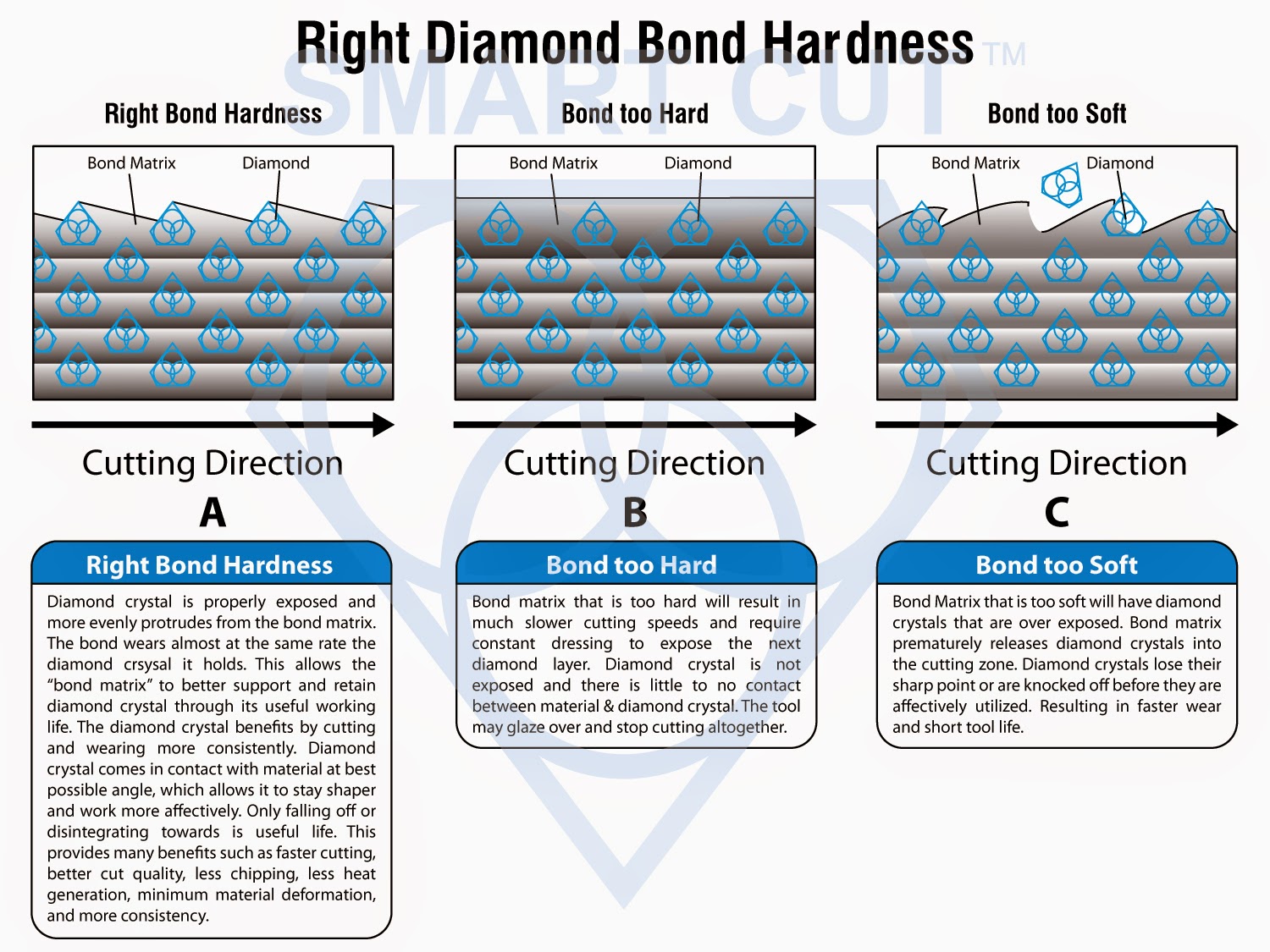
Right Bond Hardness
The bond matrix is properly exposed, and the diamond crystals evenly protrude from the bond matrix. The bond wears at almost the same rate as the diamond crystals it holds, allowing the bond matrix to support and retain the diamond crystal throughout its useful working life. The cutting direction is indicated, showing the tool's movement. The text associated with this section explains that when the bond hardness is correct, the diamond crystal is properly exposed and more evenly protrudes from the bond matrix. The bond wears almost at the same rate as the diamond crystal it holds. This allows the bond matrix to better support and retain the diamond crystal throughout its useful working life. The diamond crystal benefits by cutting and wearing more consistently. The diamond crystal comes in contact with the material at the best possible angle, which allows it to stay sharper and work more effectively, only falling off or disintegrating towards the end of its useful life. This provides several benefits, such as faster cutting, better cut quality, less chipping, less heat generation, minimum material deformation, and more consistency.
Bond too Hard
Bond matrix is harder than the diamond crystal, resulting in less exposure. The bond requires constant dressing to expose the next diamond layer. The diamond crystal is barely exposed, leading to minimal contact between the material and the diamond crystal, causing the tool to glaze over and stop cutting altogether. The cutting direction is indicated. The text explains that a bond matrix that is too hard will result in much slower cutting speeds and require constant dressing to expose the next diamond layer. In this case, the diamond crystal is not properly exposed, and there is little to no contact between the material and the diamond crystal. Consequently, the tool may glaze over and stop cutting altogether.
Bond too Soft
Bond matrix is softer than the diamond crystal, leading to overexposure. The diamond crystals prematurely release into the cutting zone, losing their sharpness or getting knocked off before they are effectively utilized. This results in a faster wear rate and shorter tool life. The cutting direction is again indicated. The accompanying text states that a bond matrix that is too soft will have diamond crystals that are overexposed. In this case, the bond matrix prematurely releases diamond crystals into the cutting zone. The diamond crystals lose their sharp points or are knocked off before they are effectively utilized, leading to faster wear and shorter tool life.
Matrix Composition and Performance
The composition of the bond matrix affects its performance characteristics. Bond matrices can be made from various materials, such as metal, resin, or a hybrid of both. Each type of bond matrix has unique properties that make it suitable for different cutting applications.
-
Metal Bond Matrix: This type of matrix is harder and provides aggressive cutting. It's ideal for applications where fast cutting is required, such as in concrete or stone cutting.
-
Resin Bond Matrix: This matrix is softer and offers precision cutting. It's suitable for applications where a smooth finish is required, such as in ceramics or glass cutting.
-
Hybrid Bond Matrix:This combines properties of both metal and resin bonds, providing a balance between aggressive and precision cutting.
Dynamic Behavior of the Bond Matrix
The bond matrix is not static during the cutting process. As the tool operates, the matrix undergoes changes to facilitate efficient cutting. The matrix wears away at a controlled rate, ensuring that the diamond particles are exposed and utilized effectively. This dynamic behavior is essential for maintaining a consistent cutting performance throughout the tool's life.
Categorization of Bond Hardness
The bond hardness of a diamond tool is typically categorized on a scale from very soft to very hard, labeled from B (very soft) to Z (very hard). The optimal bond hardness ensures that the diamond crystals are retained just long enough to facilitate efficient cutting, but are also released at the right time to expose fresh cutting edges. This delicate balance is crucial for effective cutting.
Understanding the Bond Hardness Scale
The bond hardness scale helps users select the appropriate tool for their application. The scale is divided as follows:
-
B, C These are very soft bonds. They are suitable for cutting very hard materials where rapid diamond exposure is needed, such as in ceramics or certain types of stone.
-
G, I: These are medium soft bonds, useful for hard materials but with a slightly slower rate of diamond exposure.
-
J, L, N: These represent medium hardness bonds. They are versatile and can be used for a range of materials, from hard to soft.
-
P, Q: These are medium hard bonds, suitable for medium-hard to hard materials.
-
R, T: These are hard bonds, appropriate for softer materials where slower diamond exposure is desired.
-
Z: This is a very hard bond, ideal for very soft materials where minimal diamond exposure is needed.
Choosing the Right Bond Hardness
Selecting the right bond hardness depends on the material being cut and the desired performance characteristics. For example, when cutting very hard materials like ceramics or glass, a softer bond is preferable to ensure efficient diamond exposure. Conversely, when cutting softer materials like wood or aluminum, a harder bond is suitable to prevent excessive diamond loss.
Applications of Different Bond Harnesses
-
Very Soft Bonds (B, C): Ideal for materials like ceramics, carbide, and certain stones. The rapid diamond exposure prevents glazing and ensures efficient cutting.
-
Medium Soft Bonds (G, I): Suitable for hard materials that require a slower rate of diamond exposure.
-
Medium Bonds (J, L, N): Versatile and effective for a range of materials, including metals and composites.
-
Medium Hard Bonds (P, Q): Best for medium-hard to hard materials like steels and alloys.
-
Hard Bonds (R, T): Suitable for softer materials where minimal diamond exposure is desired.
-
Very Hard Bond (Z): Ideal for soft materials like wood or plastic where diamond retention is critical.
Influence of Bond Hardness on Cutting Efficiency
The hardness of the bond affects how quickly the diamonds are released and how effectively the tool performs. A softer bond will release diamonds more quickly, which is advantageous when cutting hard materials but can result in excessive wear when cutting softer materials. Conversely, a harder bond will hold onto the diamonds longer, which is beneficial for softer materials but can cause glazing and reduced cutting efficiency when cutting harder materials.
Balancing Bond Matrix Function with Application Requirements
Choosing the appropriate bond hardness is critical for maintaining the tool's effectiveness. An overly soft bond will prematurely release diamond crystals, leading to increased wear and a shortened tool life. Conversely, an excessively hard bond can hold onto dull diamonds, causing glazing and reduced productivity. The key is to align the bond hardness with the application's requirements to achieve the desired cutting performance.
Factors Influencing Bond Matrix Function in Diamond Tools
The bond matrix in diamond tools plays a critical role in the cutting process by retaining and exposing the diamond grit. The effectiveness of the bond matrix is influenced by several factors, including the type of bond, the type of tool, the equipment used, the RPMs, the coolant used, and the clientโs desired output. Understanding these factors helps in selecting the optimal bond hardness for specific applications.
Type of Bond
The type of bond used in diamond tools varies depending on the application:
-
Metal Bond: This bond type is made from metallic powders and is highly durable. It's ideal for aggressive cutting applications where longevity is essential, such as grinding hard materials. Metal bonds typically have a longer tool life but may require more frequent dressing.
-
Resin Bond: Resin bonds are softer and offer a smoother finish, making them suitable for precision cutting and polishing applications. These bonds are generally used for softer materials and provide rapid diamond exposure, which enhances cutting efficiency but may shorten tool life.
-
Electroplated Bond: In this bond type, diamonds are electroplated onto a metal substrate. The bond is typically single-layered and offers precise cutting or shaping. It's useful for fine or intricate cutting operations but has a limited lifespan since it cannot be redressed.
-
Vitrified Bond: This bond type uses a glass-like material to hold the diamonds in place. It offers a combination of hardness and precision, making it ideal for high-precision cutting or grinding applications.
-
Hybrid Bond: Hybrid bonds combine elements of metal and resin bonds, offering a balance of hardness and cutting precision. They are versatile and can be tailored to suit various materials and applications.
Type of Tool
The type of tool being used also influences the bond matrix function:
-
Aggressive Cutting Tools: Tools designed for aggressive cutting, such as grinding wheels or heavy-duty saw blades, generally require harder bonds to ensure durability and longevity.
-
Precision Cutting Tools: Tools designed for precision cutting, such as fine saw blades or micro drills, typically use softer bonds to allow rapid diamond exposure and maintain sharpness.
-
Shaping and Polishing Tools: For shaping and polishing applications, the bond hardness should align with the desired surface finish. Softer bonds allow for smoother finishes, while harder bonds provide more aggressive material removal.
Equipment Used
The equipment used for the cutting operation affects the optimal bond hardness:
-
High-Speed Equipment: Equipment operating at high RPMs typically benefits from softer bonds, as the rapid rotation exposes fresh diamond grit more effectively.
-
Low-Speed Equipment: Lower-speed equipment might perform better with harder bonds, as the reduced rotation allows for controlled exposure of the diamond grit.
RPMs Used
The rotational speed of the tool is a key factor in determining bond hardness:
-
Higher RPMs: Higher rotational speeds benefit from harder bonds, as the increased speed helps maintain the diamond exposure rate and prevents premature wear.
-
Lower RPMs: Lower rotational speeds require softer bonds, as the slower speed allows for efficient diamond exposure without excessive glazing or dulling.
Coolant Used
The type and amount of coolant used during cutting influence bond matrix function:
-
Effective Cooling: Using effective cooling can allow for harder bonds, as the coolant prevents overheating and maintains cutting efficiency.
-
Inadequate Cooling: Inadequate cooling may necessitate softer bonds to avoid overheating and ensure efficient cutting. The cooling medium should match the application to optimize performance.
Clientโs Desired Output
The client's desired output plays a significant role in selecting the optimal bond hardness:
-
Cutting Speed: If the client desires high cutting speed, softer bonds may be preferred to rapidly expose fresh diamond grit.
-
Surface Finish: For a smooth surface finish, softer bonds are generally better, as they allow for rapid diamond exposure and minimize surface roughness.
-
Tool Life: If tool life is a priority, harder bonds may be more suitable, as they retain the diamond grit longer and provide extended tool use.
Variables or attributes that can influence the choice of bond hardness in diamond tools:
Factor |
Softer Bond |
Harder Bond |
---|---|---|
Type of Bond |
- Resin Bond |
- Metal Bond |
- Electroplated Bond |
- Vitrified Bond |
|
Type of Tool |
- Precision Cutting Tools |
- Aggressive Cutting Tools |
- Polishing and Shaping Tools |
||
Equipment Used |
- High-Speed Equipment |
- Low-Speed Equipment |
RPMs Used |
- Lower RPMs |
- Higher RPMs |
Coolant Used |
- Inadequate Cooling |
- Effective Cooling |
Clientโs Output |
- Smooth Surface Finish |
- Long Tool Life |
- High Cutting Speed |
- Rougher Surface Finish |
|
Material Hardness |
- Harder Materials |
- Softer Materials |
Material Abrasiveness |
- High Abrasiveness |
- Low Abrasiveness |
Cutting Depth |
- Shallow Cuts |
- Deep Cuts |
Cutting Speed |
- Lower Speed |
- Higher Speed |
Tool Cost |
- Lower Cost |
- Higher Cost |
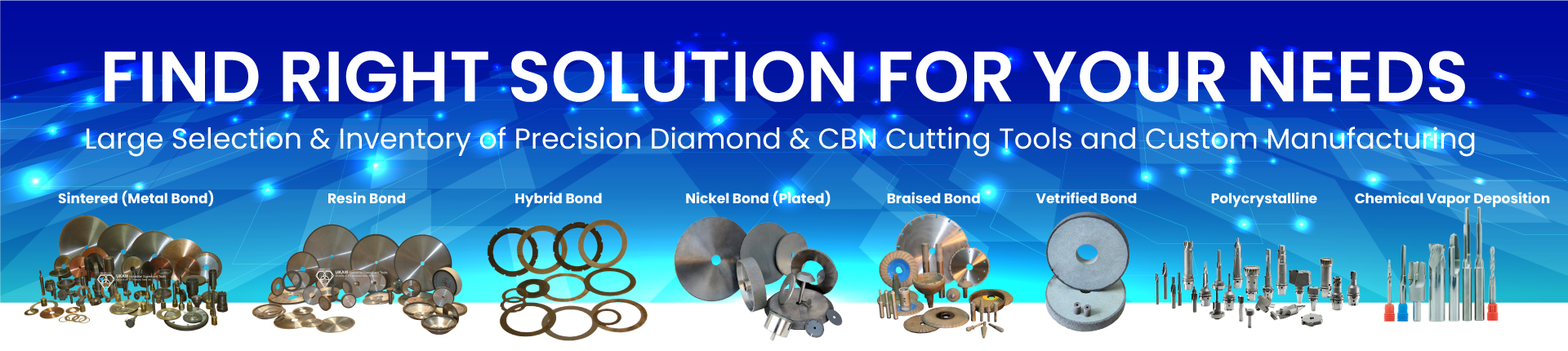