Proper selection of SMART CUT® Metallographic / Metallurgical Polishing Cloths and Pads is important to achieving best results in metallography and sample preparation. These products are specially designed for precision, durability, and compatibility with various abrasive materials. Follow these steps to choose the right polishing solution for your specific application:
Understand Types of Polishing Cloths/Pads
Different types of cloths and pads cater to specific polishing requirements, considering factors like the material under preparation, the polishing stage, and the quality of finish needed. Here is a detailed exploration of the most common types of polishing cloths and pads, highlighting their properties and optimal uses.
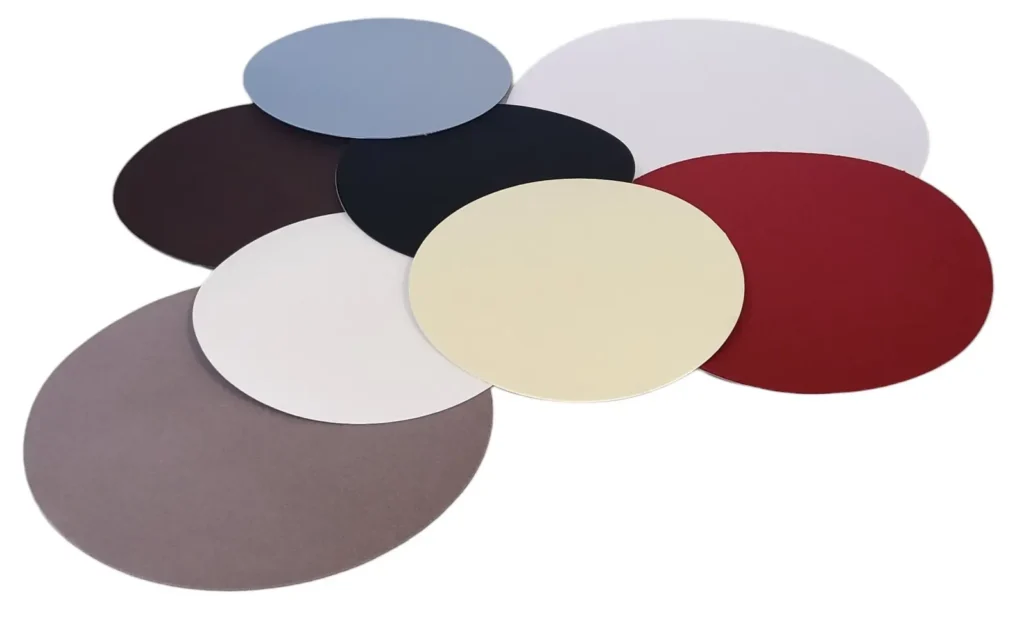
A. Non-Woven Synthetic Cloths
Non-woven synthetic cloths consist of synthetic fibers that are bonded, not woven, to create a robust and flexible polishing surface. These cloths are designed with varying levels of hardness and abrasiveness, enhancing their resistance to tearing and suitability for high-pressure applications. Ideal for rough and intermediate polishing stages, non-woven cloths effectively remove scratches and level surfaces. They are particularly beneficial for polishing harder materials such as steel, titanium, and ceramics, and are frequently employed with coarse abrasives like diamond or alumina.
B. Woven Cloths
Constructed from tightly interwoven fibers, woven cloths include materials like silk, nylon, or polyester. These cloths offer a smoother, more consistent surface than non-woven varieties, making them preferable for obtaining a high-quality, scratch-free finish. Silk cloths, characterized by their softness and fineness, are particularly suitable for the final polishing of softer metals such as aluminum and copper. Nylon, known for its durability and moderate abrasiveness, is apt for intermediate polishing of medium-hard materials. Polyester cloths, due to their versatility, are widely utilized in both intermediate and final polishing stages and are compatible with fine abrasive particles like colloidal silica or oxide slurries.
C. Composite Pads
Composite pads are crafted by amalgamating different materials such as synthetic fibers, foams, and incorporated abrasives. These pads offer an optimal blend of hardness, flexibility, and abrasive action, ensuring reliable performance across various polishing phases. Commonly utilized in automated polishing systems, composite pads facilitate consistent outcomes and are versatile enough for polishing metals, ceramics, and composites during both intermediate and final stages.
D. Specialty Cloths/Pads
Engineered for particular applications, specialty cloths and pads may include embedded abrasives or diamond particles to provide a precise and consistent polishing action. Available in a range of grit sizes and hardness levels, these cloths are tailored for processing challenging materials like superalloys or hardened steels. Their application is crucial in achieving exact and repeatable outcomes, making them indispensable in high-precision metallography, particularly within research and industrial environments where consistency is paramount.
E. Foam and Felt Pads
Foam and felt pads are distinguished by their softness and compressibility, which allow for a more delicate polishing action. These pads vary in density and thickness and are typically paired with fine abrasives or polishing suspensions. Primarily utilized in the final polishing stages, foam and felt pads excel in removing fine scratches and achieving a mirror-like finish on softer materials such as aluminum, magnesium, and copper. Their application is crucial in producing a high-luster surface without introducing additional surface imperfections.
Comparison table of various types of polishing cloths and pads used in metallography, highlighting their properties, optimal uses, and ideal applications:
Type |
Material |
Ideal for Stage |
Surface Finish |
Ideal Materials |
Common Abrasives Used |
---|---|---|---|---|---|
Non-Woven Synthetic Cloths |
Synthetic fibers bonded (not woven) |
Rough and intermediate |
Effective at removing scratches, leveling surfaces |
Hard materials (steel, titanium, ceramics) |
Coarse (diamond, alumina) |
Woven Cloths |
Silk, nylon, polyester (tightly woven) |
Intermediate and final |
Smooth, consistent, high-quality, scratch-free |
Soft metals (aluminum, copper); medium-hard materials |
Fine (colloidal silica, oxide slurries) |
Composite Pads |
Synthetic fibers, foams, abrasives |
Both intermediate and final stages |
Consistent performance across different stages |
Metals, ceramics, composites |
Varies widely, suited to material |
Specialty Cloths/Pads |
Various materials, often with embedded abrasives |
Specific applications, exact requirements |
Controlled, consistent, precise for challenging materials |
Superalloys, hardened steels |
Specific to material and application |
Foam and Felt Pads |
Foam, felt |
Final polishing stages |
Mirror-like finish, removes fine scratches |
Soft materials (aluminum, magnesium, copper) |
Fine abrasives or polishing suspensions |
Understand Your Application Needs
Selecting the right polishing cloth or pad starts with a thorough understanding of your application requirements, including the type of material being processed and the desired analysis results.
You may establish the material type based on the properties of the material you need to work with. Metals, for instance, come in different hardnesses and compositions, so the polishing cloth has to be able to accommodate these variations. For harder metals, you need firm and durable cloths/pads to effectively navigate the abrasion process, whilst softer metals require these softer cloth/pads to prevent sample distortion or over-polishing. For ceramic or composite materials, non-metallic or composite polishing pads are used to prevent compromising of the material, or for a composite with its own complex geometry. Also, for soft materials, softer pads are required that should not damage the softer surface; for hard materials, tough pads will be along which can endure a higher level of abrasive forces.
The choice of cloth/pad also depends on the analysis needs. A polish pad that has been designed as part of an engineered process for the final stage on metal surfaces is particularly important if generating a mirror reflective surface at this level is the goal. These cloths/pads can be used in conjunction with ultra-fine abrasives to achieve a perfect finish. However, applications that only need a plane, flat surface are able to use polishing cloth/pads for coarse or intermediate levels. In cases where the sample has some underlying structure that must be retained (in order to study grain boundaries, microstructural features in metallography, etc.), it is important to choose pads that cause the fewest damage to the structure. It keeps the sample intact and prepared for clear, thorough analysis.
Match the Cloth/Pad to the Polishing Stage & Desired Finish
Polishing is typically a multi-stage process, and the selection of the appropriate cloth or pad for each stage is critical to achieving the desired results. Each stage requires a cloth or pad with specific characteristics to ensure optimal material removal, surface refinement, and finishing.
Coarse Polishing
The first step in polishing is the aggressive removal of material to level the surface and remove defects. Strong, tough polishing pads are needed for this step. To do this, the pads need to be able to handle the high forces seen in this process and be compatible with abrasives that have a much coarser size, like diamond suspensions or larger grit particles. Their sturdy construction guarantees the efficient removal of excess material while preserving a consistent surface profile.
Intermediate Polishing
The intermediate stage focuses on refining and preparing the surface after the rough polishing stage for final finishing. A medium-hardness polishing cloth is ideal to achieve this, balancing material removal with surface smoothing. These cloths work best with medium-grit abrasives or fine diamond pastes, providing the precision needed to transition the sample from a rough state to a more refined one.
Final Polishing
A key step in the process is the final polishing stage of the surface, to make a smooth, polished reflection. This is where a soft, high-performance polishing cloth/pad is most suited, as it excels at delivering exceptional fine finishing. The cloths work perfectly with sub-micron abrasives or colloidal silica to produce a scratch-free finish, bringing out the features of the sample. This step is especially crucial for applications involving microscopy, as only a pristine surface will expose fine material morphology.
Comparison table for different stages of polishing, outlining the focus, cloth/pad types, abrasive compatibility, key benefits, and typical applications for each stage:
Polishing Stage |
Focus |
Cloth/Pad Type |
Abrasive Compatibility |
Key Benefits |
Typical Applications |
---|---|---|---|---|---|
Coarse Polishing |
Aggressive removal of material to level surface and remove defects. |
Strong, tough polishing pads |
Coarser abrasives like diamond suspensions or larger grit particles |
Efficient removal of excess material, maintains uniform surface profile |
Suitable for materials like steel, titanium, ceramics |
Intermediate Polishing |
Refining and preparing the surface for final finishing. |
Medium-hardness polishing cloth |
Medium-grit abrasives or fine diamond pastes |
Balances material removal with surface smoothing |
Used for a variety of metals and hard materials |
Final Polishing |
Achieving a smooth, polished reflection suitable for microscopic examination. |
Soft, high-performance polishing cloth/pad |
Sub-micron abrasives or colloidal silica |
Delivers exceptional fine finishing, ensures scratch-free surface |
Critical for applications involving microscopy or high-precision requirements |
Desired Surface Finish
The desired surface finish is another crucial factor that guides the polishing process. Different applications require varying levels of surface quality, ranging from scratch-free to mirror-like finishes. For example:
-
Scratch-Free Finish: Achieving a scratch-free surface is essential for accurate microstructural analysis. This typically involves multiple polishing stages, starting with coarse abrasives to remove deep scratches and progressing to finer abrasives for a smooth finish.
-
Mirror-Like Finish: A mirror-like finish is often required for aesthetic purposes or high-precision applications. This level of finish is achieved through final polishing stages using fine abrasives and soft pads, such as foam or felt, to produce a highly reflective surface.
-
Intermediate Finish: For some applications, an intermediate finish may be sufficient. This involves balancing material removal and surface quality, often using medium-grit abrasives and woven cloths.
Consider Abrasive Compatibility
The performance of a polishing cloth or pad is directly influenced by its compatibility with the abrasive materials used during the polishing process. SMART CUT® Polishing Cloths are specifically engineered to work with a wide range of abrasive materials, ensuring flexibility and reliability across different applications. Selecting a cloth or pad that complements your abrasive is important in order to optimal results and preserve the integrity of your sample.
Diamond Abrasives
Diamond abrasives are widely recognized for their exceptional hardness and precision, making them ideal for cutting and polishing various materials. When using diamond abrasives, it is crucial to select a polishing cloth that can handle their aggressive nature while ensuring even distribution across the surface. SMART CUT® cloths designed for diamond abrasives deliver consistent performance, enabling precise material removal and superior surface finishes. They are particularly effective for hard materials like metals, ceramics, and composites that require detailed polishing.
Colloidal Silica
For applications requiring ultra-fine polishing and a mirror-like reflective finish, colloidal silica is an excellent abrasive choice. Its chemical-mechanical polishing properties enable it to create a flawless surface without causing material damage or deformation. SMART CUT® soft polishing cloths are perfectly compatible with colloidal silica, allowing users to achieve a scratch-free, highly reflective finish ideal for microscopic examination and high-precision applications.
Other Abrasives
Different applications may call for various types of abrasives, including aluminum oxide, silicon carbide, or other specialized materials. To achieve the best results, the polishing pad must match the abrasive's grit size, chemical composition, and intended use. For example, coarse abrasives work well with firm cloth / pads during initial material removal, while finer abrasives require softer cloth / pads for final finishing. Selecting the right combination ensures effective polishing and minimizes the risk of uneven surfaces or sample damage.
Consideration of Abrasive Grit Size
When selecting a polishing cloth or pad, one crucial factor to consider is the abrasive grit size. The grit size of the abrasive particles used in conjunction with the polishing tool significantly affects the material removal rate, the surface finish, and the overall efficiency of the polishing process. Understanding how to match the abrasive grit size with the appropriate polishing cloth or pad can lead to improved outcomes and more efficient operations.
Impact of Abrasive Grit Size
The coarser the grit size, the faster the rate at which material is removed from the workpiece. Coarse grits are ideal for the initial stages of polishing where significant material removal is necessary to eliminate surface defects and prepare the material for finer finishing. Conversely, finer grits are used in the latter stages to achieve a smooth, refined surface.
The grit size directly influences the quality of the finish. Larger grit sizes can leave visible scratches or marks on the surface, which are acceptable in early polishing stages but undesirable in final finishes. Finer grits, while slower at removing material, produce a much smoother and more aesthetically pleasing surface finish.
Using the correct grit size for a specific polishing cloth or pad can optimize the efficiency of the process and minimize wear on the tool. Incorrect grit sizes can lead to increased cloth or pad wear, higher replacement costs, and potentially damaged workpieces.
Matching Abrasive Grit Size with Polishing Cloths/Pads
Coarse Grits: When using coarse abrasives, select polishing cloths or pads that are durable and designed to handle high abrasion without tearing or wearing down quickly. These pads often have stronger bonding and thicker naps to manage the aggressive nature of large grit particles.
Fine Grits: For finer abrasives, choose cloths or pads that are softer and have a tighter weave or smoother surface. These characteristics help in distributing the fine abrasive particles evenly and gently over the surface, which is crucial for achieving high-quality finishes without scratches.
Hybrid Approaches: In some cases, a combination of different grit sizes may be required throughout the polishing process. Selecting a range of cloths or pads that can work effectively with varying grit sizes allows for flexibility and adaptability in multi-stage polishing operations.
Best Practices for Abrasive Grit Selection
To effectively match the abrasive grit size with the polishing cloth or pad, consider the following best practices:
-
Assess the Initial Condition of the Material: Determine the amount of material that needs to be removed and the desired final finish to select the starting grit size.
-
Step Down Gradually: Use progressively finer grit sizes as you move through the polishing stages to gradually refine the surface without introducing new scratches.
-
Test Different Combinations: Experimentation can be key in finding the optimal combination of abrasive grit size and polishing cloth or pad, especially for new materials or unusual applications.
Polishing Cloth / Pad Lubricant Compatibility
In the realm of polishing, the choice of lubricant plays a pivotal role in determining the efficiency and quality of the process. Lubricants like RedLube or GreenLube are specially formulated to complement specific types of polishing cloths and pads, enhancing their performance and longevity. Understanding how these lubricants interact with polishing tools can help professionals achieve superior results.
Importance of Lubricant Compatibility
The compatibility between a lubricant and a polishing cloth or pad is crucial for several reasons. Firstly, the right lubricant ensures that the abrasive particles in the polishing process are effectively suspended and distributed. This uniform distribution is key to achieving a consistent and smooth finish on the material being polished. Secondly, lubricants can prevent the overheating of both the workpiece and the polishing tool, which is essential for maintaining the integrity of the material's surface and extending the life of the polishing cloth.
Enhancing Polishing Efficiency
Using a compatible lubricant like RedLube or GreenLube can significantly enhance the polishing efficiency. These lubricants are designed to reduce friction between the polishing cloth and the material, facilitating a smoother polishing action. This reduced friction not only speeds up the polishing process but also minimizes the effort required to achieve the desired finish. Efficient lubrication thus leads to a quicker attainment of results without compromising the quality of the surface.
Improving Polishing Quality
The quality of the polishing outcome is directly influenced by the type of lubricant used. Lubricants that are compatible with the polishing cloth or pad ensure that the material is not removed too aggressively, which can prevent scratches and other surface defects. Additionally, these lubricants help in achieving a finer finish by allowing for a more refined interaction between the abrasive particles and the material surface. The end result is a smoother and more visually appealing surface finish.
Extending Cloth Life
The longevity of polishing cloths and pads is significantly enhanced by the use of appropriate lubricants. Lubricants help to reduce wear and tear on the cloths by providing a protective layer that absorbs some of the mechanical stresses involved in the polishing process. This protective effect not only preserves the physical integrity of the polishing cloth but also maintains its effectiveness over longer periods, reducing the need for frequent replacements and thus lowering operational costs.
Best Practices for Lubricant Use
To maximize the benefits of lubricants in polishing processes, it is important to:
-
Select the correct lubricant based on the material of the cloth or pad and the type of material being polished.
-
Apply the lubricant evenly across the surface of the cloth or pad to ensure consistent performance throughout the polishing process.
-
Regularly replenish the lubricant during long polishing sessions to maintain its effectiveness and prevent drying out, which can lead to increased friction and potential damage to both the cloth and the workpiece.
Understanding Cloth/Pad Hardness and Resilience
When selecting a polishing cloth or pad, it is crucial to understand the properties of hardness and resilience, as these characteristics significantly influence the effectiveness of the polishing process. They affect material removal rates, surface finish quality, and the longevity of the polishing tool. Here are some example of how polishing cloths/pads can be classified:
Hard and Rigid: These are suitable for initial rough polishing where aggressive material removal is needed. Examples include HGN Weave (PLAN) and Metal Mesh, which are designed for hard materials and high abrasion resistance.
Soft and Flexible: Ideal for final polishing stages, these cloths provide a gentle polish that is necessary for achieving a high-quality finish without damaging the material. Examples include Brown Final Polishing Cloth and SMART CUT Nylon Polishing Pad.
Here’s a closer look at how cloth or pad hardness and resilience affect the selection process and the best practices for choosing the right one for specific applications.
Cloth/Pad Hardness: Hardness refers to the ability of the polishing cloth or pad to resist surface deformation or penetration by abrasive particles. Harder cloths are more durable and suitable for aggressive polishing actions where substantial material removal is required. Hard cloths are typically used on hard materials such as metals, ceramics, and mineral samples, efficiently removing material without being quickly worn down. They are particularly effective during the initial stages of polishing to remove defects and surface irregularities.
It is essential to select a polishing cloth or pad that is suitably hard relative to the material being polished. A cloth that is too soft for a hard material may lead to inadequate polishing and excessive wear. Hard pads are generally preferred in earlier polishing stages for their ability to level surfaces quickly and remove deeper scratches or imperfections.
Cloth/Pad Resilience: Resilience is the ability of a polishing cloth or pad to recover its original form or position after deformation. This property is crucial for maintaining consistent contact with the surface during prolonged or intense polishing sessions. Resilient cloths are beneficial for final polishing stages, where a gentle yet consistent action is needed to achieve a high-quality finish without introducing new surface defects.
More resilient cloths should be chosen when polishing delicate or intricate surfaces where the cloth needs to adapt to the contours of the material. Cloths with higher resilience are also preferable in applications requiring repeated use over long periods, as they maintain their effectiveness and shape, ensuring consistent results.
To ensure the best match for your polishing needs, it's important to align the cloth hardness with the type of material you are working on: hard pads for hard materials during rough polishing stages and softer, more resilient pads for softer materials or final polishing stages. Additionally, consider environmental factors such as heat or chemicals, which might affect the durability and performance of the polishing cloth or pad. Sometimes, the ideal cloth or pad is found through experimentation—testing different hardness and resilience levels to determine which provides the best finish for a specific material. Lastly, consulting technical support team can provide valuable guidance on the suitability of various cloth/pad types for different materials and stages, aiding in making an informed choice.
Selecting the Right Polishing Cloth / Pad Backing/Mounting
The choice of backing or mounting system for a polishing pad is an important consideration, as it ensures compatibility with your equipment and provides the stability needed for efficient polishing. Proper backing selection not only enhances ease of use but also ensures consistent and repeatable results.
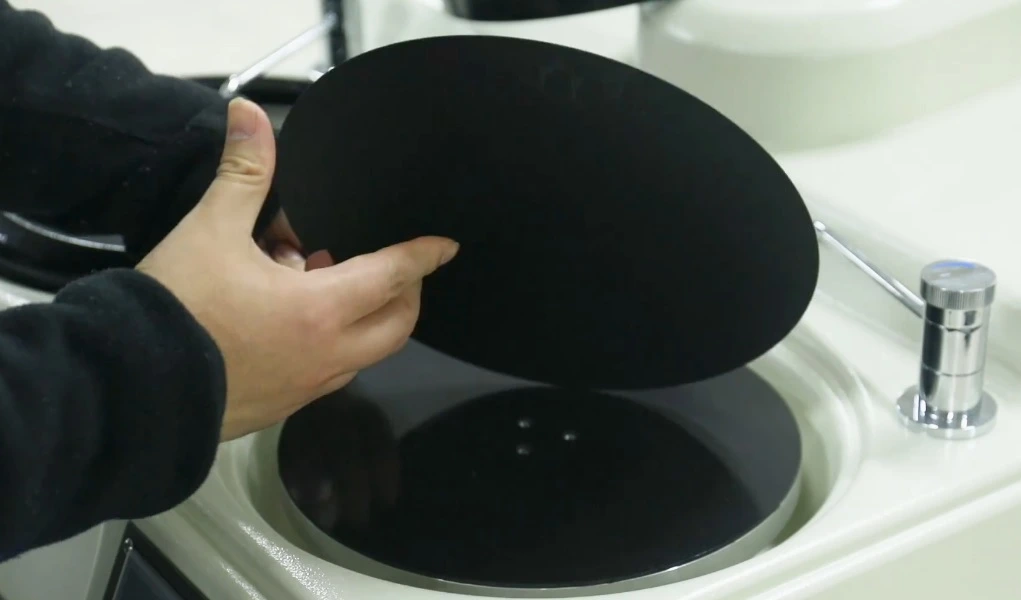
Adhesive Backing
Adhesive-backed polishing cloth/pads are a popular option for many applications. They are equipped with a peel-and-stick layer that allows quick and secure attachment to the platen or polishing plate. This option is ideal for users who prioritize ease of setup and need a reliable hold during polishing. Adhesive-backed pads are especially suited for single-use or short-term applications, as they are typically disposed of after the polishing session. To ensure smooth removal, check for adhesive pads designed to leave minimal residue.
Magnetic Backing
Magnetic-backed polishing cloth/pads offer greater flexibility and convenience for applications requiring frequent pad changes. These pads are equipped with a magnetic layer that securely attaches to a compatible magnetic base plate. This system allows users to quickly swap pads between different polishing stages or materials without the need for adhesives, saving time and effort. Magnetic backings are particularly beneficial in multi-stage polishing workflows or high-throughput environments where efficiency is key.
Plain Backing
Plain-backed polishing pads are designed for use with platen systems that utilize alternative attachment methods, such as clamping rings or double-sided tape. This option provides maximum versatility, as users can customize their mounting solution based on specific equipment or application requirements. Plain backing is often chosen when flexibility in mounting is needed, or for specialized polishing setups.
Key Considerations for Backing Selection
- Compatibility with Equipment: Ensure the backing system matches the platen or mounting system of your polishing machine.
- Ease of Use: Consider how frequently you need to change pads and whether a magnetic or adhesive solution would improve efficiency.
- Application Requirements: For long-term use and repeatable polishing tasks, magnetic systems may offer better performance. For single-use applications, adhesive-backed pads provide a cost-effective solution.
- Stability and Precision: The backing must provide a stable surface during polishing to ensure uniform pressure distribution and consistent results.
Comparison table for different types of polishing cloth/pad backing/mounting systems, outlining their characteristics, ideal applications, benefits, and considerations:
Backing Type |
Description |
Ideal for |
Benefits |
Considerations |
---|---|---|---|---|
Adhesive Backing |
Equipped with a peel-and-stick layer for quick, secure attachment to platen or polishing plate. |
Users who prioritize ease of setup and need reliable hold during polishing. |
Quick setup, secure attachment, ideal for single-use or short-term applications. |
Typically disposed after use; check for minimal residue designs. |
Magnetic Backing |
Features a magnetic layer that securely attaches to a compatible magnetic base plate. |
Applications requiring frequent pad changes, such as multi-stage polishing workflows. |
Facilitates quick pad swaps, saves time and effort, beneficial in high-throughput environments. |
Requires a compatible magnetic base plate for effective use. |
Plain Backing |
Designed for use with systems utilizing clamping rings or double-sided tape. |
Maximum versatility in mounting based on specific equipment or application needs. |
Allows customization of mounting solutions, suited for specialized polishing setups. |
Flexible in use but may require additional accessories for mounting. |
Evaluate Durability and Reusability
When selecting metallographic / metallurgical polishing cloths or pads, it is essential to consider their durability and reusability in relation to your workflow and application demands. These factors significantly impact the cost-effectiveness and efficiency of the polishing process.
In high-throughput environments, where large volumes of samples are prepared regularly, durability becomes a critical factor. We recommend polishing cloths/pads engineered for long-term use, as these are designed to maintain consistent performance over extended periods without significant wear or degradation. Durable cloths/pads not only reduce the frequency of replacements but also ensure reliability across multiple polishing cycles, making them ideal for laboratories and facilities with heavy workloads.
For applications where only a few samples are being prepared, single-use or less durable polishing cloths may be more appropriate. These cost-effective options are suitable for situations where the cloth's longevity is not as critical, such as occasional sample preparation or one-time polishing tasks. By choosing pads designed for limited use, you can minimize expenses without compromising the quality of the polished surface.
Assess Polishing Cloth/Pad Size
When selecting polishing pads for your equipment, carefully assessing the size and mounting requirements is crucial for compatibility with your polishing machinery and for optimal performance results. Here’s how you can make informed choices regarding pad size and mounting needs:
Choosing the Right polishing cloth / Pad Size
The size of the polishing pad is important as it must correspond to the dimensions of the equipment being used. Common polishing cloth / pad sizes in the industry include 8 inches, 10 inches, and 12 inches in diameter. Selecting the correct size ensures that the pad covers the appropriate surface area of the material being polished without overhang or insufficient coverage, which is essential for achieving an even polish and preventing potential damage to both the sample and the equipment.
Equipment Compatibility: The size of the polishing pad must match the platen or base of the polishing machine. A perfectly fitting pad reduces the risk of slippage and uneven wear, securing it properly during use.
Surface Coverage: A properly sized pad covers the entire surface area that needs to be polished without extending beyond the edge of the platen. This uniform coverage is vital for ensuring that the entire sample is uniformly treated. Overhanging pads can snag or tear, which could lead to potential damage to the pad, the sample, or the equipment.
Efficiency and Uniformity: The right-sized pad ensures efficient use of abrasives and a consistent application of pressure across the sample's surface. This uniformity is crucial for achieving a smooth and consistent finish, especially in precision applications.
Common Sizes and Their Applications
8-inch Diameter: These smaller pads are optimal for laboratory settings where precision and control are crucial. They are particularly suitable for smaller or more delicate samples requiring detailed work.
10-inch Diameter: Offering a balance between size and control, 10-inch pads are commonly used in both research and industrial environments. This size adapts well to a broad range of materials and sample sizes.
12-inch Diameter: Larger pads are typically employed for industrial-scale polishing tasks. They are effective for handling large or multiple samples simultaneously, which enhances throughput in high-volume settings.
Consider the size of the material being polished. Larger samples might require bigger pads to effectively cover the surface area without multiple passes. Also, plan for replacement and compatibility by ensuring that replacement pads are readily available in the selected size. Using standard sizes can simplify sourcing and replacing pads as needed.
Factor in Environmental and Safety Considerations
When setting up a polishing operation, integrating environmental and safety considerations into your planning is essential for achieving optimal results and maintaining a safe workspace. Here’s how you can effectively manage these factors:
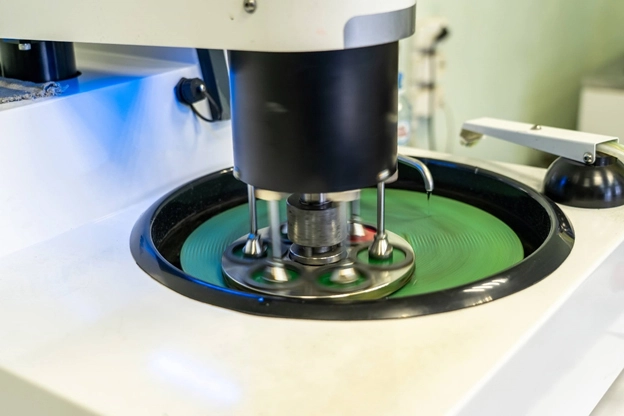
Maintaining a Controlled Work Environment
The performance of polishing processes can be significantly affected by the work environment, particularly the temperature and humidity levels. Consistent temperature helps ensure that the physical properties of the polishing pads and abrasives remain stable, which is important for achieving uniform results. Similarly, controlling humidity is important as excessive moisture can affect the adhesion of abrasives on the polishing pads and may lead to inconsistent abrasion or clumping of polishing media. For this reason, maintaining a controlled environment with stable temperature and humidity levels is crucial for optimizing the quality and consistency of your polishing results.
Ensuring Adequate Ventilation
Safety is important in any operational setting, and this is especially true when working with abrasives during the polishing process. Some abrasives can generate dust and other particulates that, if inhaled, can be harmful to health. To mitigate these risks, proper ventilation is necessary. Using an effective ventilation systems ensures that airborne particles are efficiently extracted from the work area, maintaining clean air and reducing the risk of respiratory issues for operators. This not only adheres to health and safety regulations but also creates a more comfortable and sustainable working environment.
Safety Measures
In addition to maintaining a controlled environment and ensuring adequate ventilation, it's important to implement strategic safety measures such as:
-
Regular monitoring of environmental conditions using humidity and temperature sensors to ensure they remain within optimal ranges.
-
Installation of high-efficiency particulate air (HEPA) filters or similar systems in ventilation equipment to capture fine abrasive particles effectively.
-
Conducting routine safety audits and training for all personnel on the proper handling of materials and equipment, emphasizing the importance of personal protective equipment (PPE) such as masks, goggles, and gloves.
Test and Adjust as Needed
Choosing the right polishing cloth or pad for metallography / metallurgy can significantly affect the quality of your sample preparation. If you are uncertain about which product best meets your needs, a methodical approach to testing and adjustment can guide you to the most effective solution. Here’s how to proceed:
Try Different Polishing Cloth / Pad Specifications
When you are not sure what polishing cloth/pad specification to pick, starting with a trial pack can be an excellent strategy. We can usually provide trial packs that include a variety of cloths or pads, allowing you to experiment with different types before committing to a bulk purchase. This approach lets you directly assess the impact of each type on your specific application. We can cross reference any competitor product specification or item number if needed.
Monitor and Adjust
Once you begin using a particular cloth or pad, closely monitor its performance during the polishing process. Pay attention to how well it removes scratches, its durability, and the quality of the finish it produces on different materials. If the results do not meet your expectations or the specifics of your application, adjust your approach by trying a different type of pad or altering the parameters of your polishing process, such as speed and pressure.
The key to optimizing your sample preparation is iterative testing and adjustment. This process involves:
-
Assessing the effectiveness of each cloth or pad under various conditions.
-
Adjusting your methodology based on the outcomes and observations.
-
Repeating the process if necessary to fine-tune the results.