Table of Contents
ToggleDiamond is the hardest material known to man kind. When used on diamond/tools, diamond grinds away material on micro (nano) level. Due to its hardness Diamond will work all types of materials from hardness of 40 on Rockwell scale and up. Diamond will machine hardest material, including those materials that other conventional types of abrasives, carbide and high speed steel will not. This capability allows diamond tools to machine an extensive range of materials, from metals and composites to ceramics and advanced polymers, which are often difficult or impossible to machine with traditional tools.
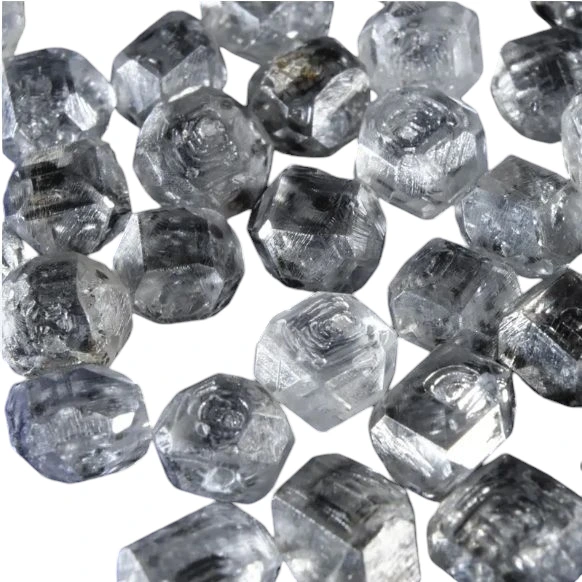
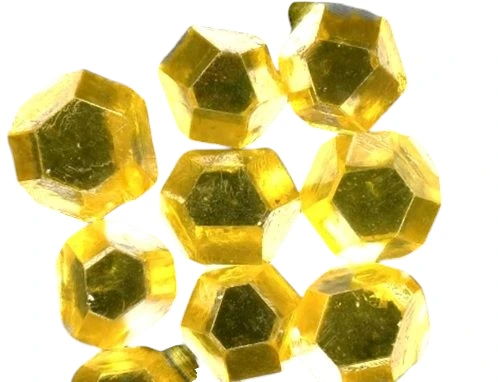
Diamond tools excel where conventional materials, such as carbide, high-speed steel, or abrasives like aluminum oxide and silicon carbide, fall short. Diamond’s hardness enables it to remove material at the micro or even nano level, delivering levels of precision that are impossible to achieve with other abrasives. Additionally, diamond’s unique thermal conductivity and wear resistance allow it to endure the high temperatures and stresses encountered in high-demand industrial applications, sustaining performance even in the most challenging environments.
This article explores why diamond is not just a choice but a necessity for industries working with materials at the forefront of hardness, toughness, and complexity. From enhanced return on investment to the unmatched ability to handle a wide range of materials, diamond tools provide a compelling solution for achieving the highest standards of quality, efficiency, and longevity in cutting, grinding, and polishing applications.
Share this Article with Friend or Colleague
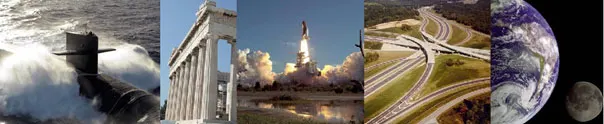
Furthermore Diamond and CBN have unmatched properties by any other material. Including conventional abrasives such as aluminum oxide and silicon carbide. Diamonds is the perfect material to be used as an abrasive cutting agent due to its unmatchable high wear resistance, thermal conductivity, and ability to whistand extreme heat (up to 1100°C ). Its strength and efficiency when used on cutting tools application can provide the best ROI (Return on Investment) Possible.
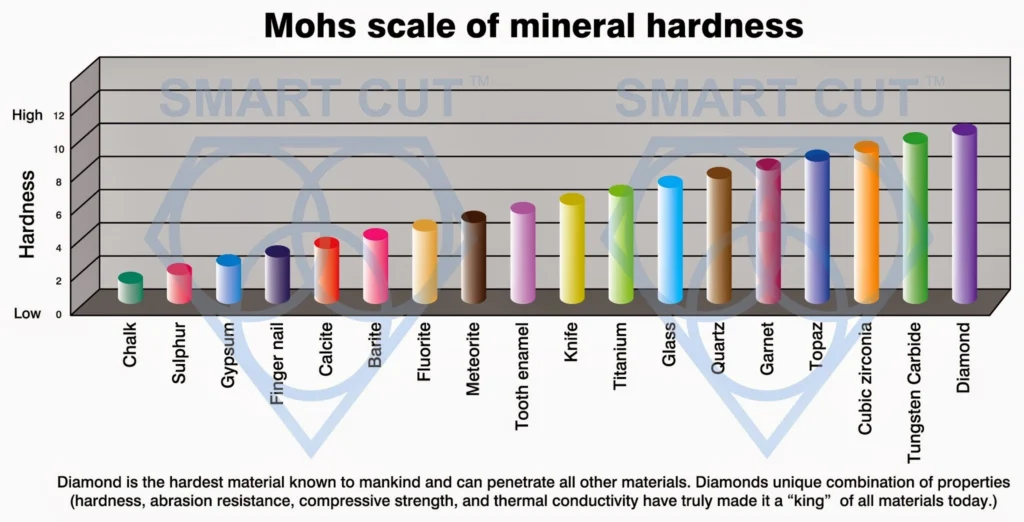
Diamond Can Provide the following Advantages for tool making applications:
-
Produce more product (yield)
-
Hold much higher tolerances
-
accuracy, and repeatability
-
Reduce Labor
-
Reduce Cost
-
Improve Productivity
-
Improve Surface Finish Quality
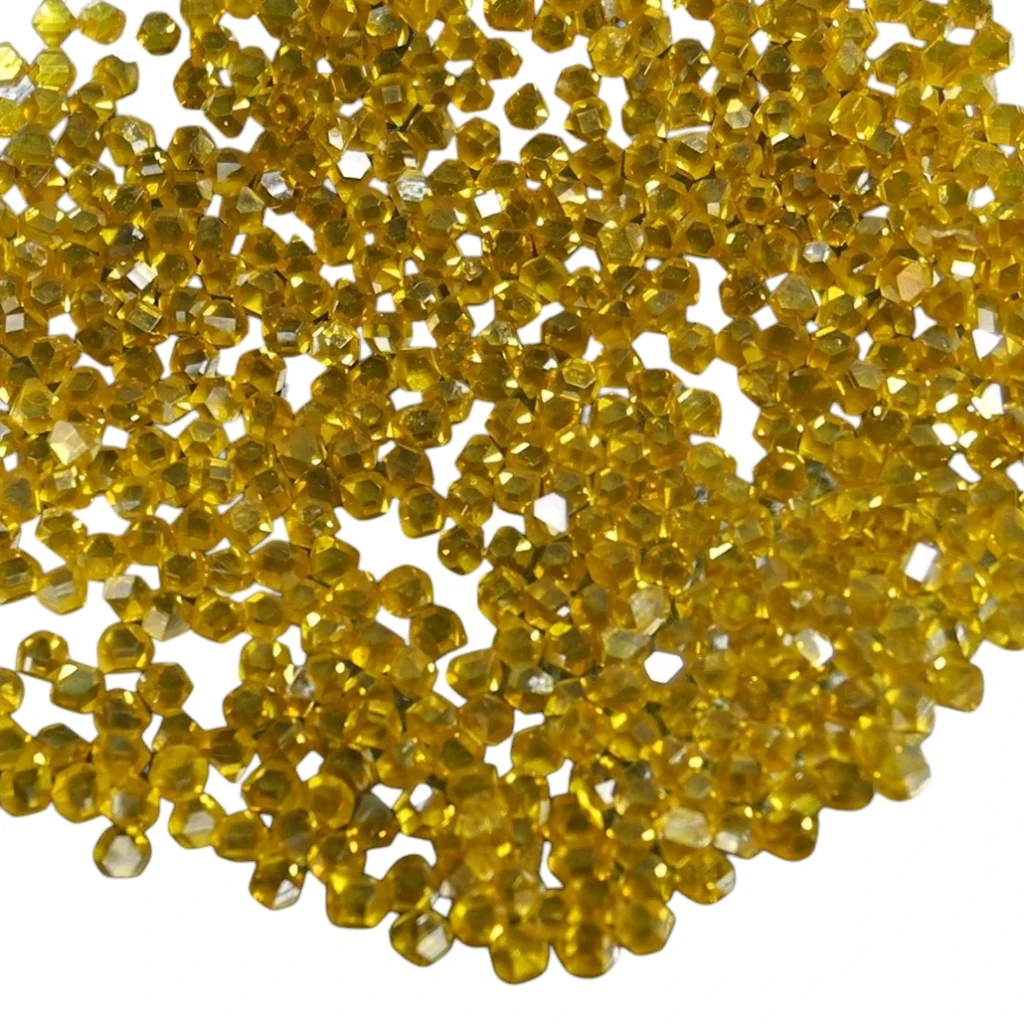
Diamonds unique combination of properties (hardness, abrasion resistance, compressive strength, and thermal conductivity have truly made it a "kind" of all materials today.
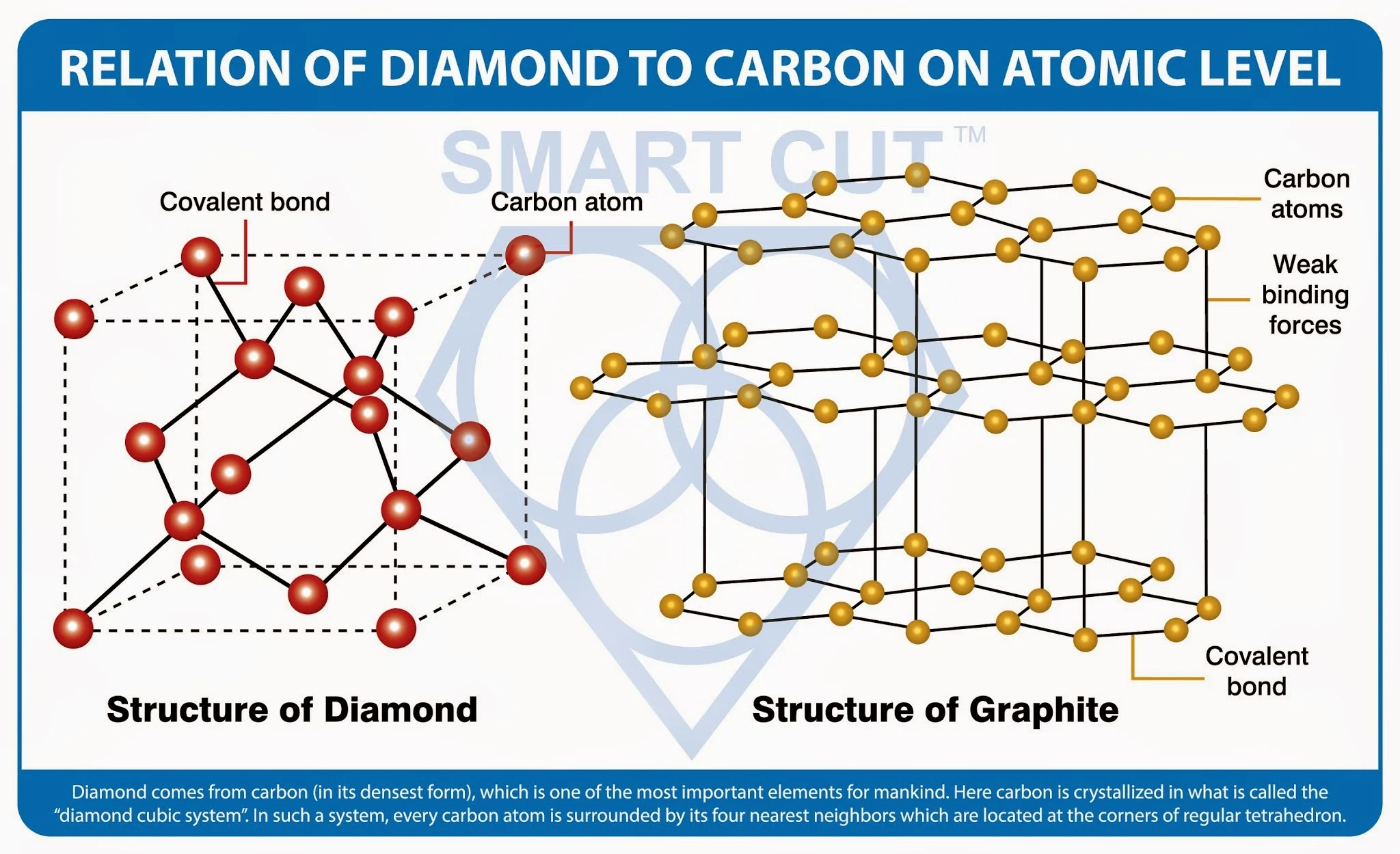
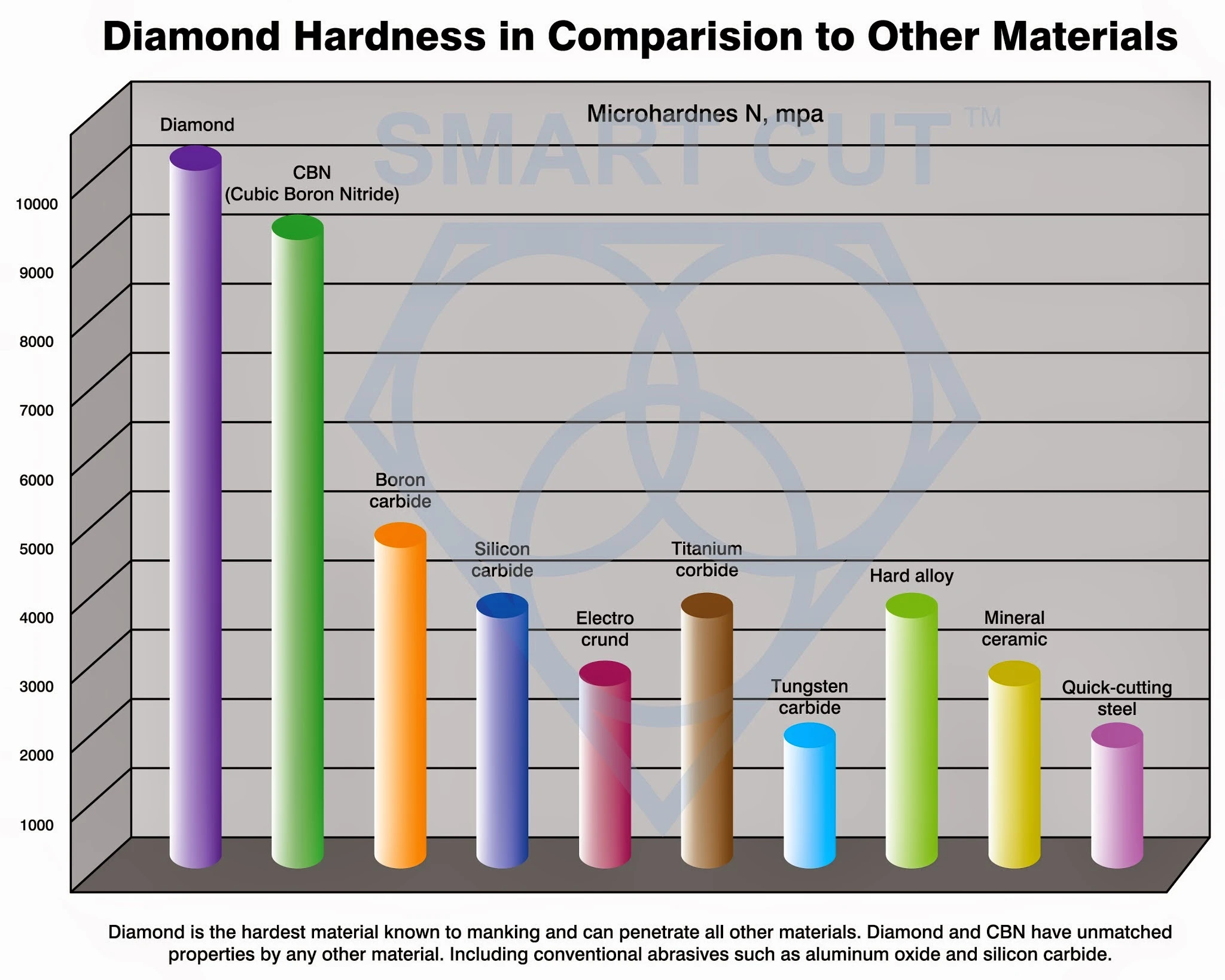
Diamond Hardness Comparison to Other Materials
Diamond comes from carbon, which is one of the most important elements for mankind. When paired with other elements its is the base of all life on earth. Coal and graphite are other most common elements found on earth. All of these elements are composed of same atoms, but structured in a different form. The differences in their atom arrangement can explain the different properties and forms of carbon.
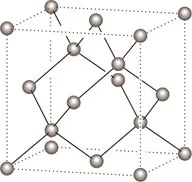
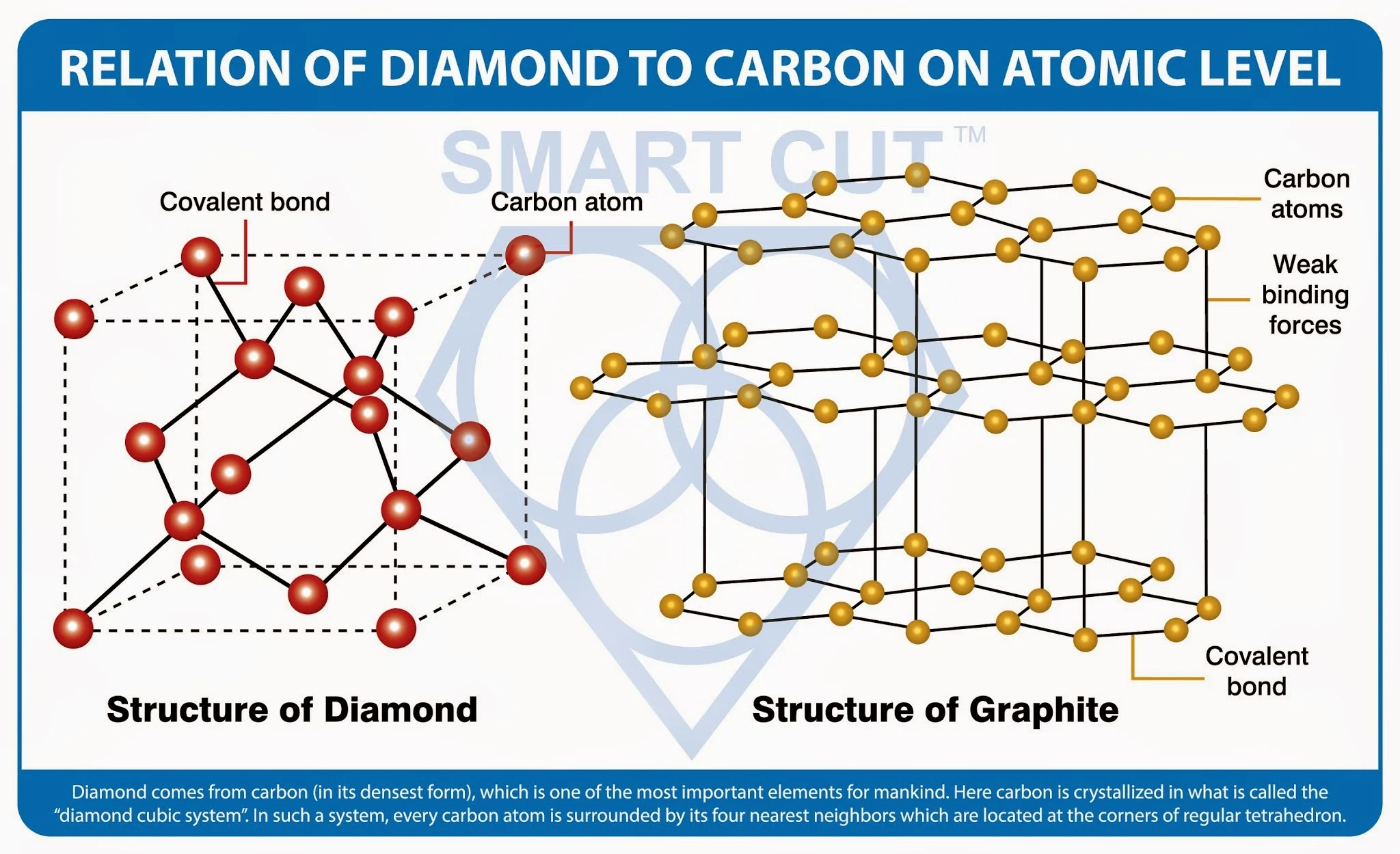
Diamond is carbon in its densest from, crystallized in what is called the "diamond cubic system". In such a system, every carbon atom is surrounded by its four nearest neighbors which are located at the corners of regular tetrahedron.
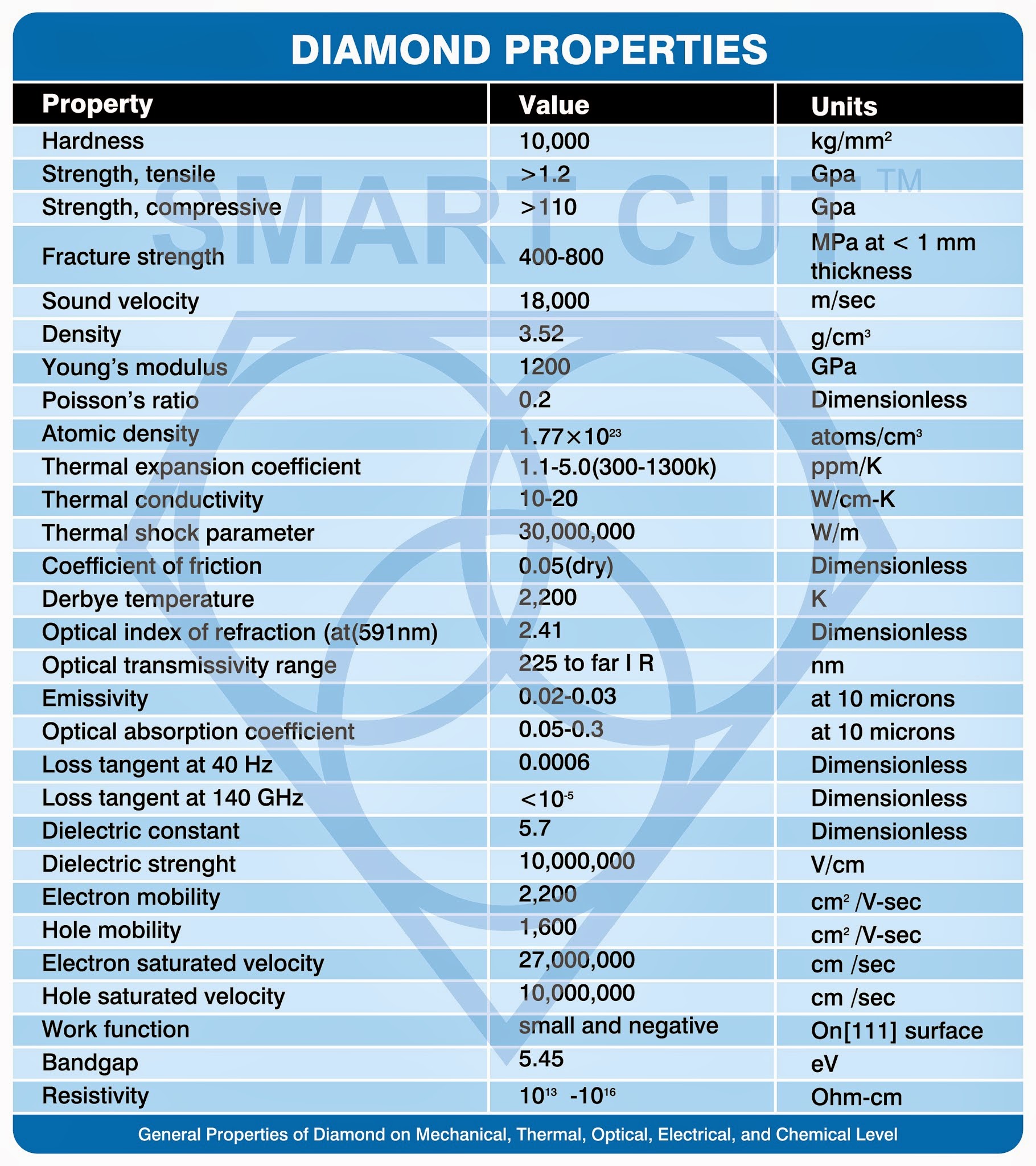
Diamond's Application Outside of Jewelry Industry:
Mechanical Applications - abrasive and wear resistant coatings for cutting tools such as drills, saws, knives, glass cutting and wire dies
Optical Applications - lenses, windows for high power lasers and diffractive optical elements
Thermal Applications - heatsinks for power transistors and semiconductor laser arrays
Detector Applications: sold blind photo detectors, radiation hard and or chemically inert detectors
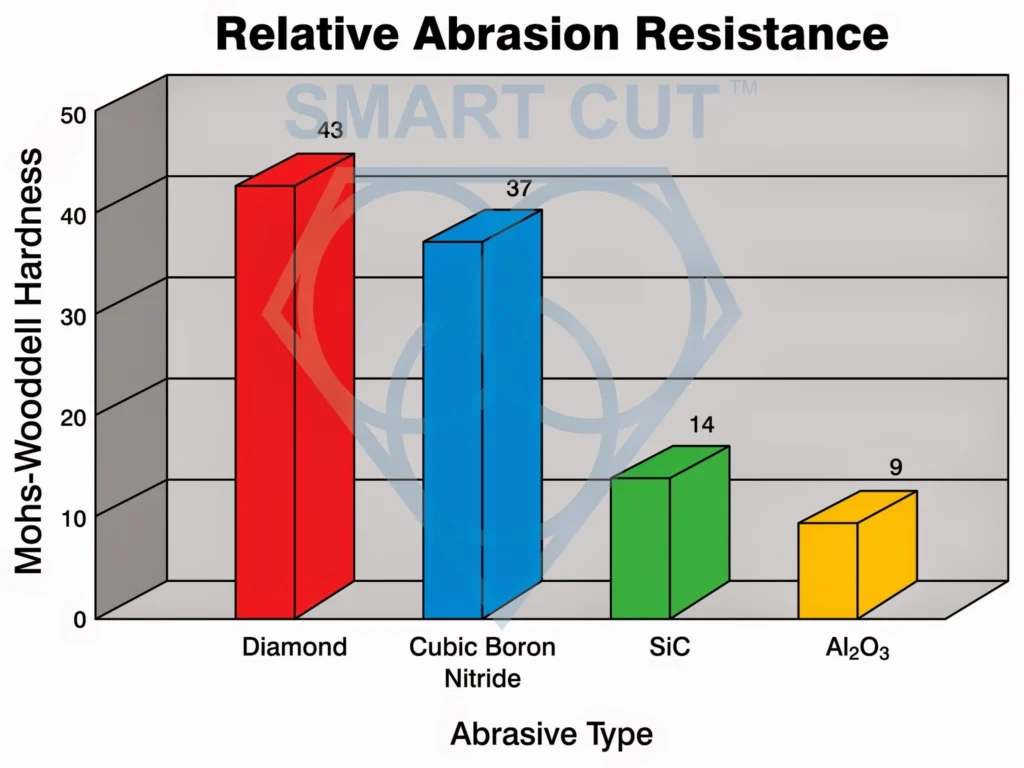
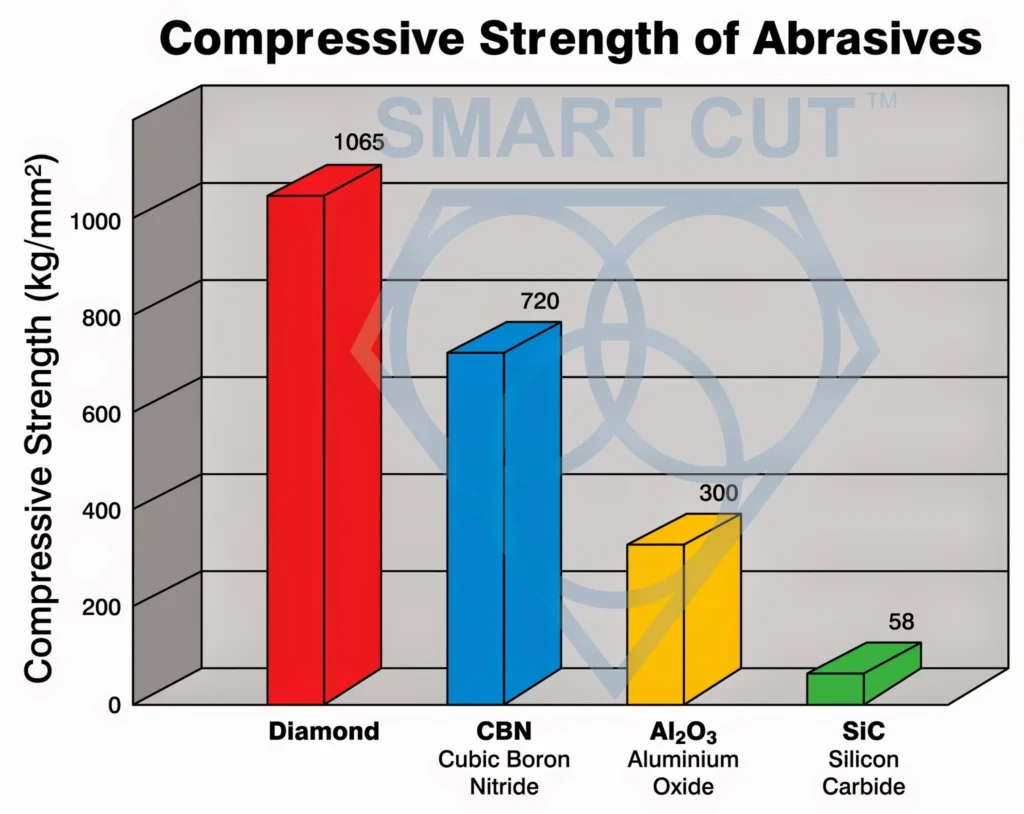
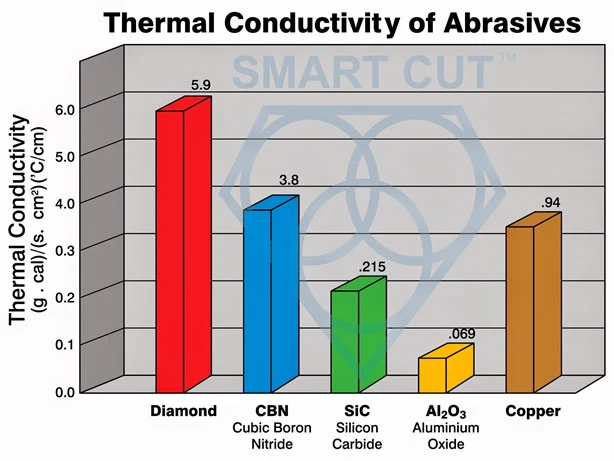
Diamonds hardness is one of the key reasons of its white implementation as cutting agent in tool industry. Here diamond is used as an abrasive/cutting agent. Diamond of specific size, shape, and friability (fracturability) is used to grind, saw, or drill various hard materials. Diamond is bonded to edge of a tool such as surface of grinding wheel, cutting saw, or tip of a drill. Typical bonding agents are phenolic resins, metals, and vitreous substances.
Essentially diamond is a form of mineral. Similar to that of granite, marble, coal, quartz and other rock materials that we are familiar with. What has been a popular test to determine whether what is represented is diamond is genuine, would be to scratch glass. Obviously more sophisticates tests are available for this purpose. Such as X ray diffraction, acid dissolution and hardness, among many others.
How Diamond is Formed
The large majority of natural diamonds are formed from volcanic rocks, called kimberlite and lamproite, that are derived from 150 to 200 km below the Earth’s surface. Diamond is formed out of carbon under high temperature and high pressure conditions. Once diamond is formed it retains its properties when cooled and brought to one atmosphere. In order to form synthetic conditions under which is diamond is formed in nature (earths crust) must be replicated.
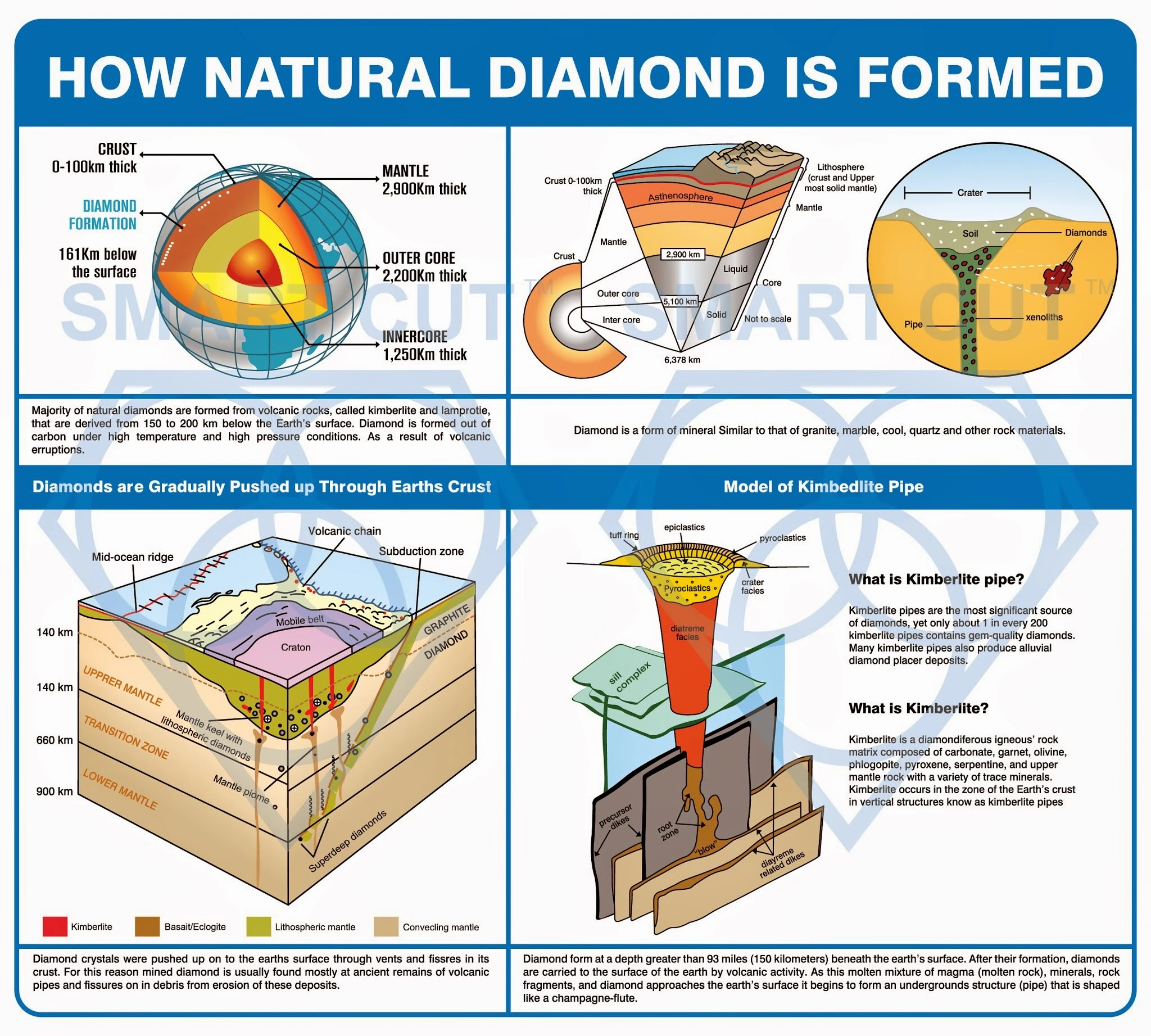
Where deep in the interior of the earth, high pressure and high temperatures were combined to turn carbon into diamond (as result of volcanic eruptions). After formation some of the diamond crystals were pushed up on to the earths surface through vents and fissures in its crust.
For this reason mined diamond is usually found mostly at ancient remains of volcanic pipes and fissures on in debris from erosion of these deposits. Diamonds are found on every continent except for Europe and Antarctica. Through history diamond has been recognized as symbol of great value, beauty and permanence. However the most significant and important property of diamond is its incredible hardness as the hardest material know to mankind.

Natural Industrial Diamond Powder
Natural diamond used in industry in smaller crystal sizes is frequently called as "bort" and as industrial diamond in larger crystal sizes. Its value/price is usually measured in size and quality. With only clear, transparent and inclusion free diamond used for jewelry purposes. For industrial/tool making applications diamond is purchased by weight, with carat being standard form of measurement and in certain mesh size
The shape and strength of diamond crystal is considered in determining its suitability for given application. Over 80% of the diamonds mined today are classified as industrial diamond (not sufficient enough to be used for jewelry). Yet it represents only a small portion of annual world sales. This diamond was fragmented into a coarse powder and use as abrasive to produce cutting tools. Its appearance is similar to grayish white sand. Natural diamond when crushed does not break up into uniformed form crystals in shape and strength. Hence hen when sorted by size, its performance as cutting agent/abrasive in tools has a degree of variability and inconsistency as its physical characteristics are restricted to those formed in nature.

Natural diamond grows predominantly in an octahedral form that provides several sharp points optimal for single point diamond tools. It is also found in long stone form, created by the partial dissolution of the octahedral form using in dressing tools. Long stone shapes are also produced by crushing and ball milling diamond fragments. Crushing and milling introduces flaws that significantly reduce strength and life of the diamond crystal.
Twinned diamond stones called maacles also occur regularly in nature. These are typically triangular in shape. The tinned zone down the center of the triangle is the most wear resistant surface known. Maacles are used for sharpening chisesla s well as for reinforments in the most demand form roll applications. Natural diamond crystals used for tool industry is derived from crystals considered unsuitable for jewelry due to flaws, inclusions, and defects. Before use diamond is crushed and fultered through a series of mesh nets. The particles obtained have random shapes, sharp cutting edges and high strength or low friability. Often they can be spottedby their yellow color, which is caused by nitrogen atoms dispersed in the lattice. Shape of the diamond crystals can be octahedral, dodecahedral or hexahedral. The characteristic shape of good quality natural stones is octahedral, but the toughest stone shape iscubo octahedral
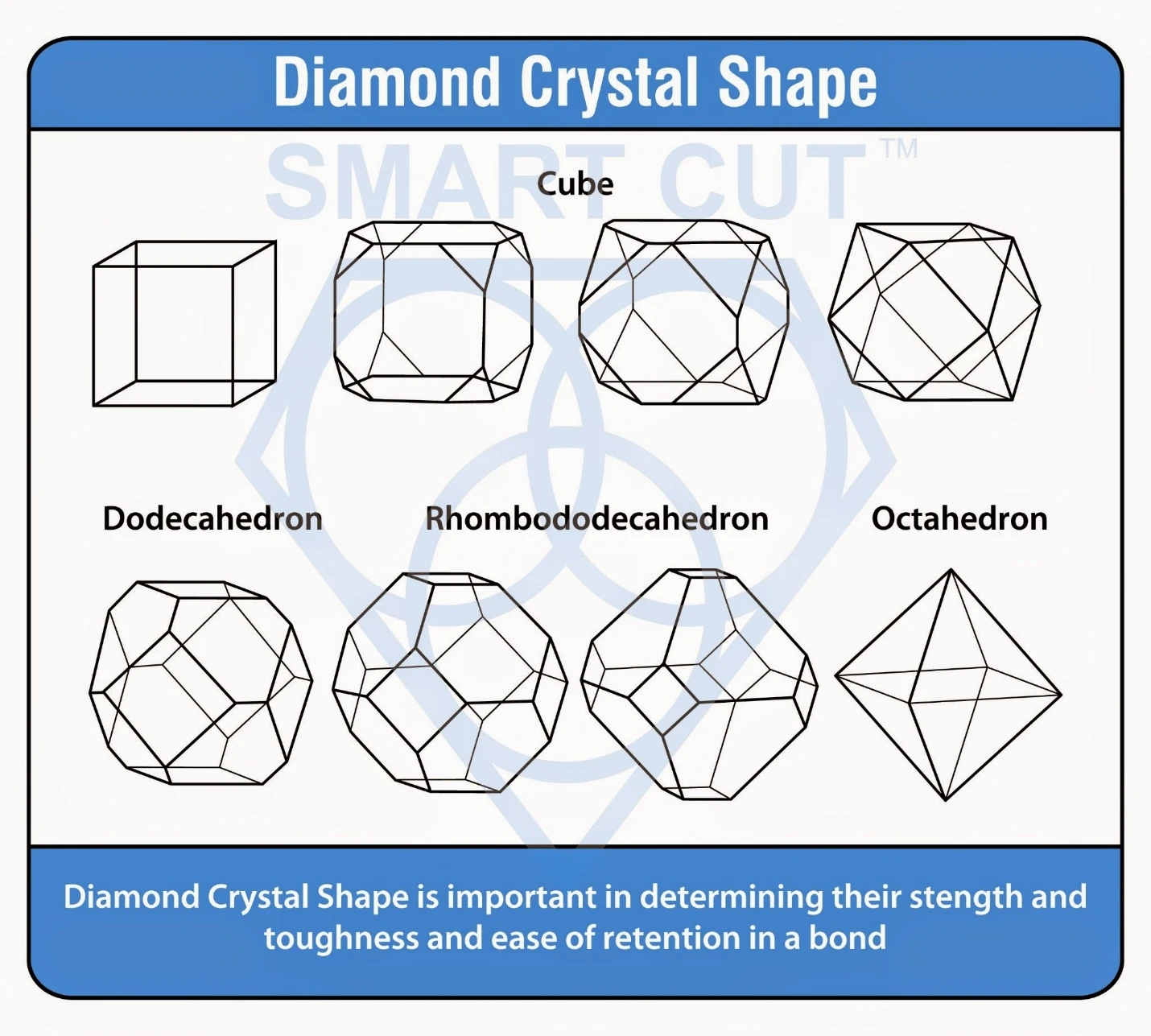
Natural Diamond Crystal Common Shapes
despite the dramatic growth of synthetic diamond. Demand for natural diamond has not declined. In fact the cost of natural diamond has increased, specially for higher quality stones. some of the lower quality stones that used to be used for industrial applications such as single point tools are now more frequently used for jewelry applications. Once germ quality diamonds considered to small for jewelry purposes, are now being processed by low wage third world countries such as India, driving the price up. The quality of natural diamond depends on reliability of the diamond source and ability to sort diamonds according to requirements. Highest quality diamond stones used for industrial application are as mined virgin material. Lower quality stones are most frequently processed by either crushing and/or ball milling or even reclaimed from old form rolls or tools
Synthetic Diamond Crystal
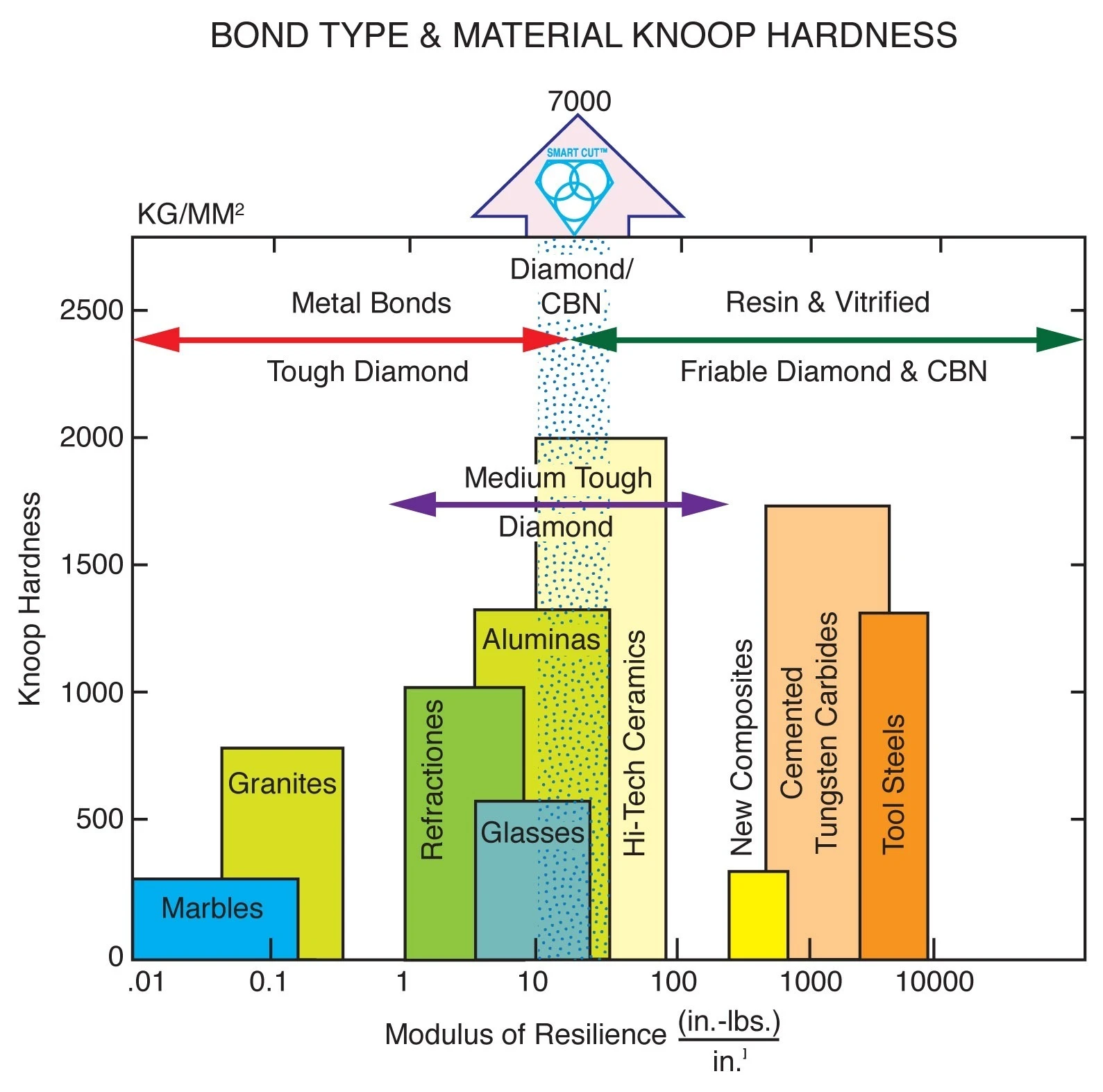
The first synthetic (man made) diamond produced was in February 1955 by General Electric Laboratory. the next challenge faced was producing diamond with right properties for specific application/material. In order to achieve this objective its necessary to select the right graphite, proper solvent catalyst, have the right conditions for pressure, temperature and time.
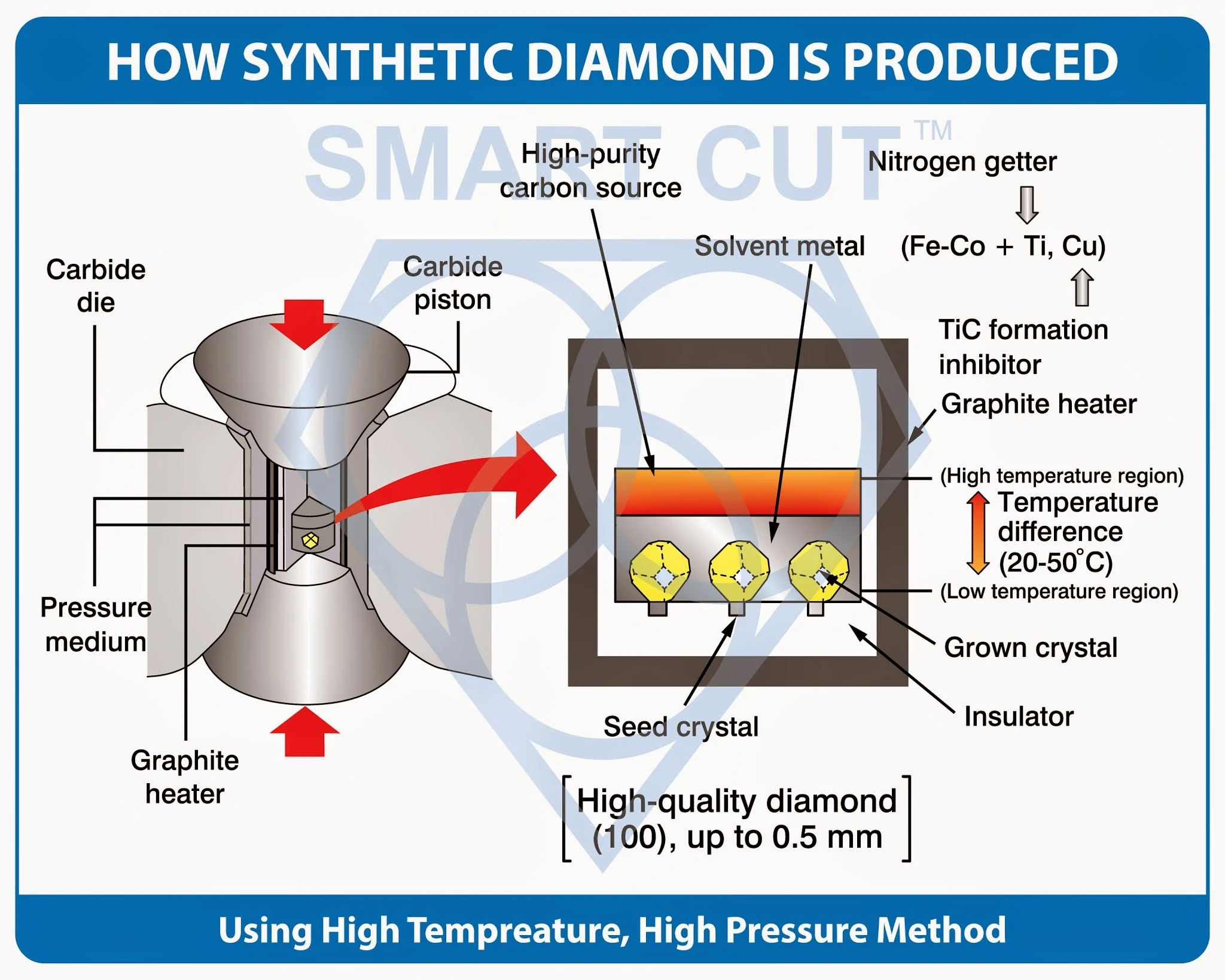
Synthetic vs Natural diamond Crystal
synthetic diamond is the most widely use diamond crystal for tool cutting applications. Proven to significantly outperform natural diamond in majority of applications.
natural diamond crystals made by crushing minded diamond, are free from metallic inclusions and as result have excellent thermal stability properties. Natural diamond particles are typically able to retain the original mechanical strength even up to 1400 C when synthetic diamond crystals start to loose strength after 800 degrees Celsius. Natural diamond crystals have excellent bond retention characteristics which translate into many re-entrant surfaces. The irregularity sometimes found in natural diamond can reduce mechanical strength, which may be advantageous in more challenging applications. These tougher applications usually require the use of more tougher diamond, which are better able to whistand higher impact force.
Although the hardness of diamond for both synthetic and natural may be similar or same. There are other factors that affect performance when used for industrial cutting tools. These factors are friability and consistency. Friability is the ability of diamond to fracture under stress (shape and surface of individual crystal and toughness of the crystal). Factors that can be controlled for natural diamond: sizing, sorting, and treating to improve uniformity and consistency. Yet physical characteristics as created by nature are outside human control. Natural diamonds come from different sources and geographical areas and have different characteristics, mainly different shapes and organic contaminants.
Their limited availability in consistent form and properties makes them less attractive option for today's demanding applications requiring high rate of repeatability. The opposite is true for synthetic diamond. As almost all properties and characteristics can be specifically "tailored" to each individual and unique application. The main advantage of synthetic diamonds is their controlled manufacturing process. Both the diamond tool maker and the client can rest assured the diamond crystal they use today, will be available with exact same shape and characteristics tomorrow and many years later.
Synthetic diamond is usually produced with aid of cobalt or nickel base alloys as a catalyst/solvent in the diamond synthesis crystals of different internal structure can be obtained. Cobalt grades are distinct by the presence of metal inclusion arrays. Nickel grade synthetic diamond on the other hand are uniformly distributed through the particle. This is the type of diamond crystal that exhibits excellent transparency and cosmetic appearance and higher ability to retain mechanical strength after processing at higher temperatures. Below is an example of how diamond is tailored for each application requirement:
Comparison table between natural diamond and synthetic (man-made) diamond, focusing on their characteristics relevant to industrial tool applications:
Feature |
Natural Diamond |
Synthetic (Man-Made) Diamond |
---|---|---|
Origin |
Formed naturally over millions of years under high-pressure, high-temperature conditions within the Earth |
Produced artificially using High Pressure High Temperature (HPHT) or Chemical Vapor Deposition (CVD) methods |
Purity and Consistency |
Varies; can contain inclusions or impurities that may affect tool performance |
High purity and consistency; engineered to be nearly flawless with controlled properties |
Cost |
Typically higher due to rarity and extraction costs |
Generally lower cost due to controlled manufacturing processes |
Availability |
Limited by natural deposits and mining availability |
Readily available, as it can be produced on demand |
Hardness |
Extremely hard, generally around 10 on the Mohs scale but may vary slightly due to natural imperfections |
Comparable hardness to natural diamond, but consistency in hardness is often higher due to controlled crystal growth |
Thermal Conductivity |
High thermal conductivity, but may vary depending on impurities |
Consistently high thermal conductivity, often engineered for specific industrial applications |
Size and Shape Control |
Limited; natural diamonds must be cut and shaped, which can lead to variations |
Fully customizable during synthesis, allowing for tailored shapes and sizes ideal for specific tool applications |
Environmental Impact |
Higher environmental impact due to mining operations and resource extraction |
Lower impact with controlled, sustainable production environments |
Wear Resistance |
High wear resistance but can vary depending on natural impurities and inclusions |
Engineered for optimal wear resistance; consistent quality enhances durability |
Applications |
Often used in high-value applications where natural diamond properties are specifically required (e.g., gemstones, limited tooling) |
Widely used in industrial applications (cutting, grinding, drilling) where consistency and customizability are crucial |
Crystal Structure |
Typically octahedral or cubic, with natural imperfections |
Primarily cubic or tailored for specific structural requirements, resulting in optimal performance |
Lifespan in Tools |
Long-lasting but may vary due to natural imperfections |
Generally more durable in tools due to engineered consistency and minimal impurities |
Industrial Suitability |
Suitable for high-precision applications but limited by natural availability |
Preferred for industrial tools due to customizable properties, cost-efficiency, and consistent performance |
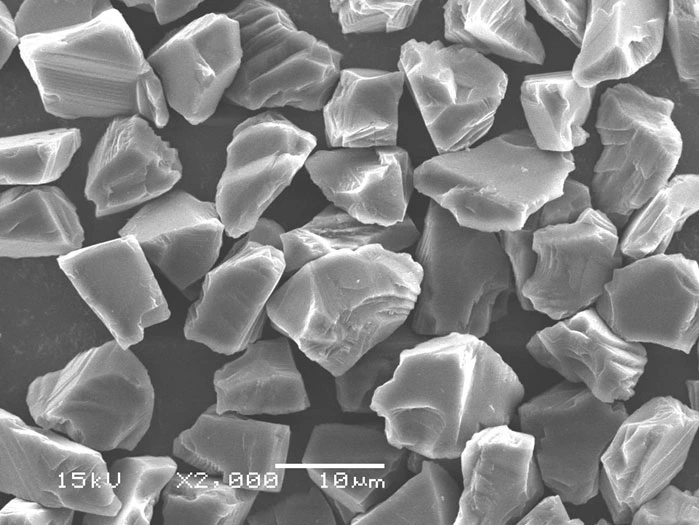
Resin Bond and Vitrified Bond Diamond Tools
shape and friability of diamond crystal is very important for these bond families. Most common man made (synthetic) diamond crystals used for these applications are called RVG and RVG-W diamond. These diamond crystals are elongated and irregular, with rough surfaces to make sure they are held firmly in place.
So that diamond crystals break down gradually over time at a controlled rate (not being torn out of the bond). This is know as friability. During their cutting action chips are broken off each crystal, crated new sharp cutting faces. This results in self sharpening effect which is need for the bond types to work affectively.
Sintered (metal bond) Diamond Tools
this bond family requires high strength diamond crystal. Lower degree of friability is more desirable. As this is a much harder bond family compared to resin bond, the diamond crystal used must be much tougher. Here each crystal has distinctive blocky shape which gives it strength.
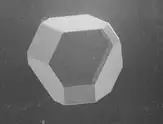
For sawing/cutting purposes similar diamond of diamond crystal is used that is even more stronger and larger. this type of diamond produced as a sing grown diamond. Here the crystal surfaces are smooth and regular with no ragged surfaces to reduce the crystals strength. and cine shape contributes to strength each crystal approximates a cubo otahedron for greatest resistance to fracturing.
Synthetic Diamond Type and their Uses
synthetic diamond can be achieved through several technological process. Two main process widely used today is high pressure high temperature synthesis (HPHT) and Chemical Vapor Deposition (CVD).
High Pressure, High Temperature Diamond
Catalytic high pressure, high temperature method most widely used today for diamond synthesis because of its relative lower cost. Amount of industrial diamond produced using this method is at least four (4) times higher then the amount of mined natural diamond used in cutting tools industry. Although its wide popularity, this method has some weaknesses in variability of production (with many crystal defects and impurities. Diamond crystal typically produced with this method is yellow color, which comes from relatively high nitrogen concentration.
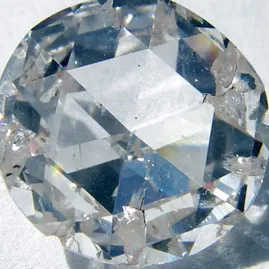
CVD (Chemical Vapor Deposition) Diamond
this method first developed in 1980's creates a carbon plasma on top of substrate onto which the carbon atoms deposit to form diamond. The advantage of this method is its possible to grow cBD diamond under high purity conditions, producing fewer defects and impurities
Here is why diamond is catching on in the cutting tools industry:
-
Diamond crystal is able to maintains its sharp cutting edges almost unchanged through its useful life span. This translates into improved tolerances, consistency, reliability, and reducing and often eliminating scrap
-
Significantly Increased Tool Life. Diamond is frequently able to outlast conventional tools by as much as 100 times. In most applications life span of diamond & cbn tooling is 10 to 100 times all other tools
-
Increased level of automation and demand for output at reduced cost has made diamond or cbn the only practical choice in almost any field/industry. As only diamond has the characteristics needed to address the growing challenges faced today at the right price.
-
New Generation Materials being developed today are much harder and have more variety in composition. Creating problems and challenges that can only be solved by application of diamond tools
-
More people from many industries and walks of life are discovering that diamond tools can perform the same jobs faster, better, easier, and more economically.
Diamond is the Material of the Future
diamond properties and characteristics will make its use more common in more complex technologies to finding its way into our everyday lives. its just a matter of time. Human societies and first civilizations depended on metal for use to make swords, spears, tools, and construction structures. At the beginning of industrial revolution, emphasis on metal was replaced by use of plastics. In modern time our society has placed greater emphasis o use of Silicon material. as its all around us in use in computers, electronics and technology. Diamond is next stage of evolution and will dominate as the main material used around us as we approach the future.
What Diamond Crystal/Particles to Use for your Application?
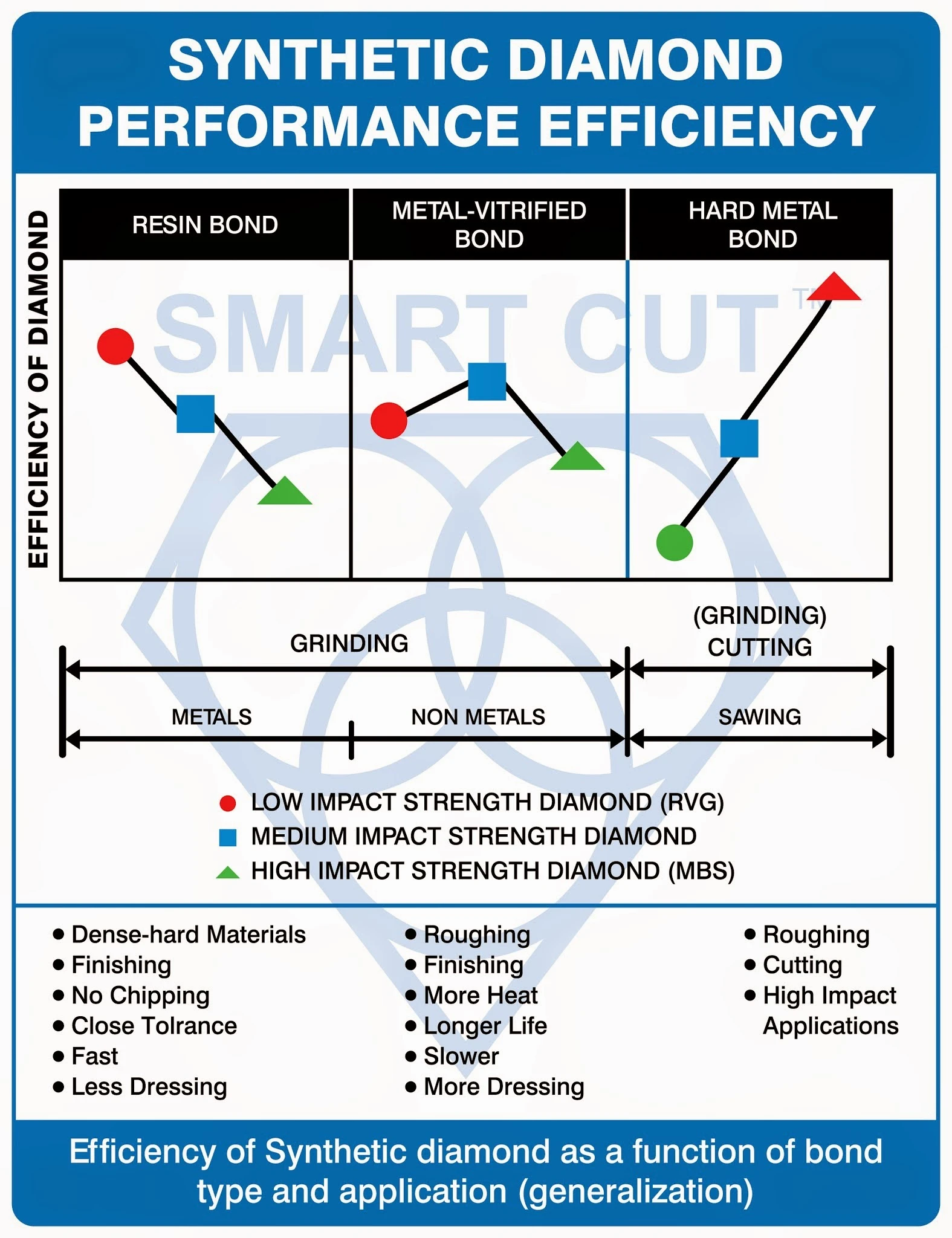
The material being cut will determine the type of diamond crystal will be used for the application. The harder the material the stronger diamond crystal has to be used. There is a wide range of natural and synthetic diamond crystals that can be used for any given application. Each one with different mechanical strengths, thermal stability and bond retention characteristics. The manufacturer must select the right diamond based on previous experience or input from the operator in the field. This decision is based, in part, on the tool's design, bond properties, material to be cut and machine power. These factors must be balanced by the selection of diamond grade and concentration that will provide the operator with optimum performance at a suitable cost.
CBN (Cubic Boron Nitride) Crysal

Cubic boron nitride (CBN) is the second hardest material after synthetic diamond and is synthesised from hexagonal boron nitride under conditions similar to those used to produce synthetic diamond from graphite. The desirable characteristics of an abrasive include high hardness, strength, abrasion resistance, and thermal and chemical resistance, and an ability to maintain sharp cutting edges during use. These characteristics exceed the values of conventional abrasives, such as silicon carbide and aluminum oxide. In particular, the properties of high thermal stability and chemical resistance make it suitable for machining ferrous materials, an area where synthetic diamond abrasives are not normally employed.
Hardness is a crucial property of any abrasive. However, most abrasives suffer a loss in hardness at the elevated temperatures experienced during application. One of the physical advantages of CBN compared to conventional abrasives is that, in addition to being harder at ambient temperature, it maintains this hardness over a wide temperature range.
CBN abrasives provide higher productivity and dramatically longer tool lives compared to conventional abrasives when grinding, honing and fine finishing hardened ferrous materials and difficult to machine alloys. CBN is firmly established in ‘tool and cutter’ grinding and in mass production grinding operations in the automotive, general engineering and aerospace industries. Application examples include camshafts, crankshafts, fuel injectors, transmission parts, gears, CV joints, power steering pump parts and compressor parts. Some of the many advantages of CBN include improved surface finishes and the production of more favourable compressive residual surface stresses.

APPLICATION COMPARISON DIAMOND VS CBN (CUBIC BORON NITRIDE)
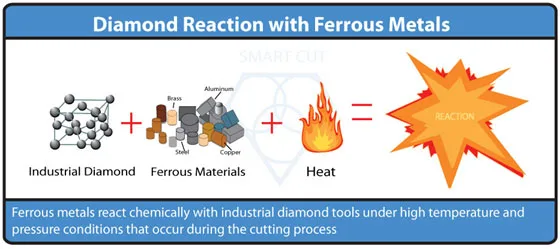
How Do Diamond & CBN Tools Compare to Other Tool Types
Diamond tools with traditional materials like carbide, high-speed steel, and common abrasives such as aluminum oxide and silicon carbide, several distinctive advantages of diamond tools emerge. Conventional tools, while widely adopted in various industries, have inherent limitations in terms of longevity and cutting precision. For example, carbide tools, though durable and resistant to moderate levels of heat, cannot achieve the same level of hardness as diamond. This disparity is especially evident when carbide is applied to ultra-hard materials, where it tends to wear more quickly and underperforms in high-tolerance applications requiring continuous, intensive use.
High-speed steel (HSS), frequently used in general machining, performs adequately on softer materials but is unsuitable for ultra-hard materials due to its comparatively low abrasion resistance and hardness. HSS tools are limited in their ability to achieve the fine precision and durability that diamond can offer, making them less viable in high-precision machining applications.
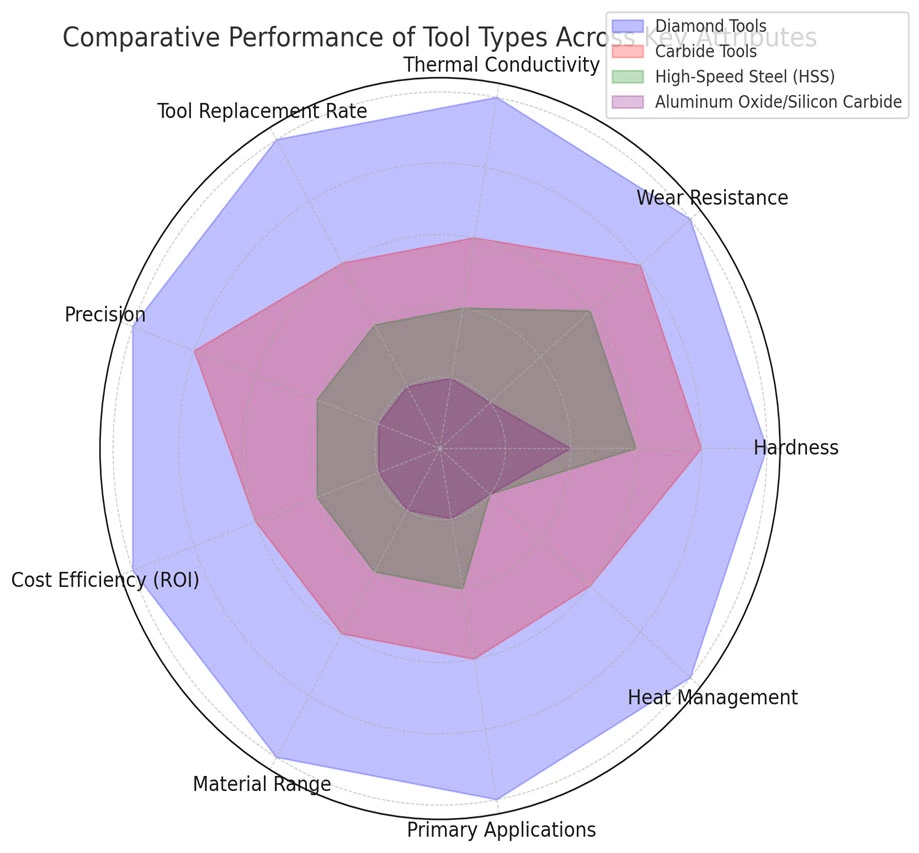
For softer metals, abrasives like aluminum oxide and silicon carbide provide effective grinding and finishing capabilities, but these materials degrade swiftly when applied to harder surfaces. Moreover, these abrasives cannot achieve the precision levels needed in fields like electronics and optics, where minimal tolerance for material damage and high fidelity in cutting and finishing are crucial.
Diamond tools, by contrast, offer a combination of precision, durability, and cost-efficiency that is unmatched by these conventional materials. With diamond, industries benefit from extended tool life and superior precision, which contribute to a lower cost per cut over time. This not only mitigates the initial expense but also boosts the overall productivity of machining operations, as fewer replacements and repairs are needed.
The return on investment (ROI) for diamond tools, though associated with a higher upfront cost, is considerably advantageous in the long term. The extended lifespan of diamond tools results in reduced replacement expenses, as these tools maintain their sharpness and effectiveness far longer than their conventional counterparts. Additionally, diamond’s ability to dissipate heat efficiently and resist wear minimizes downtime, thereby accelerating production cycles and increasing throughput. The precision of diamond tools further ensures minimal material loss, particularly valuable when working with high-cost materials such as advanced ceramics or semiconductor components.
Table of Comparison Between Diamond Tools, Carbide Tools, High Speed Steel and Abrasive Tools
Feature |
Diamond Tools |
Carbide Tools |
High-Speed Steel (HSS) |
Aluminum Oxide/Silicon Carbide Abrasives |
---|---|---|---|---|
Hardness |
Extreme hardness (10 on Mohs); ideal for ultra-hard materials; enables micro/nano-level cutting |
High hardness; effective on metals and hard materials but wears on super-hard materials |
Moderate hardness; suitable for softer materials, wears quickly on hard materials |
Moderate hardness; best for softer metals, quickly degrades on hard materials |
Wear Resistance |
Exceptional; retains shape and sharpness for extensive periods |
Good; moderate wear rate, especially on harder materials |
Moderate; wears quickly when machining hard materials |
Low wear resistance; degrades rapidly under demanding conditions |
Thermal Conductivity |
High; dissipates heat effectively, avoiding overheating up to ~1100°C |
Moderate; retains heat under prolonged use, leading to potential wear |
Low; prone to heat buildup, limiting high-temperature applications |
Low; retains heat and can cause tool degradation in extended use |
Tool Replacement Rate |
Low; longevity reduces the need for frequent replacements |
Moderate; requires periodic replacement, especially under high-demand usage |
High; frequent sharpening needed for effectiveness |
High; wears down quickly, requiring frequent replacements |
Precision |
Superior precision; enables nano-level abrasion and minimal material loss |
Moderate; capable of high precision but lacks nano-level accuracy |
Lower precision; suitable for general machining |
Low; lacks precision for fine or high-tolerance applications |
Cost Efficiency (ROI) |
High, due to durability, precision, and efficiency despite higher upfront cost |
Moderate; cheaper initially but needs more frequent replacements |
Low-to-moderate; low initial cost but lower efficiency and durability |
Low; affordable but quickly consumed, making frequent purchases necessary |
Material Range |
Extensive; suitable for ultra-hard materials (e.g., ceramics, composites) and dense alloys |
Limited; performs well on metals and some hard materials but not ultra-hard |
Limited; best on general metals, unsuitable for high-hardness applications |
Limited; generally suitable for soft metals and surface finishing |
Primary Applications |
Ideal for precision machining (electronics, optics, ceramics, high-hardness materials) |
Best for general machining, metalworking, and milling |
Suitable for general machining of soft metals and alloys |
Suitable for basic polishing, grinding of softer metals, surface prep |
Heat Management |
Excellent; maintains cool operation, prevents tool and material damage |
Moderate; prone to heat buildup with extended use |
Poor; can deform or damage material under high temperatures |
Poor; generally unsuitable for high-heat applications |
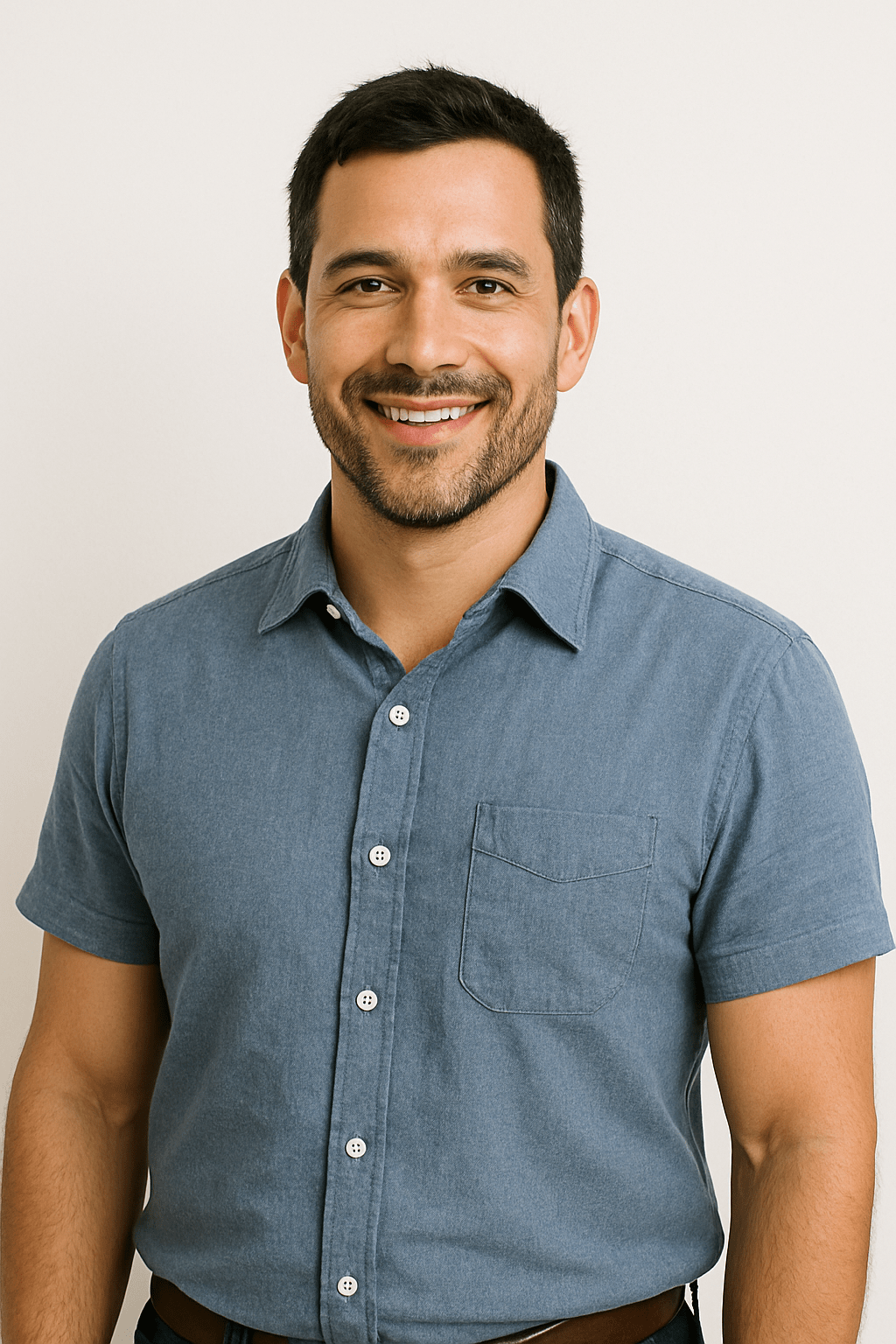
Carlos Sanchez is a senior technical specialist and field applications trainer with more than 17 years of experience in the use and optimization of industrial diamond tools, including ultra-thin diamond blades, core drills, and CBN grinding wheels. With a foundation in industrial engineering and technical operations, Mr. Sanchez has worked extensively with manufacturers and laboratories around the world, providing hands-on support and practical training for a wide range of cutting, grinding, and sample preparation applications.
Fluent in both English and Spanish, Carlos is known for his ability to translate complex tooling concepts into clear, actionable procedures for engineers, technicians, and production staff. His approach emphasizes real-world process improvement, tool longevity, and operator education—ensuring clients get the most out of their diamond tooling investments.
As an author, Mr. Sanchez shares field-tested insights on tool performance optimization, defect prevention, training methodologies, and troubleshooting common cutting issues.
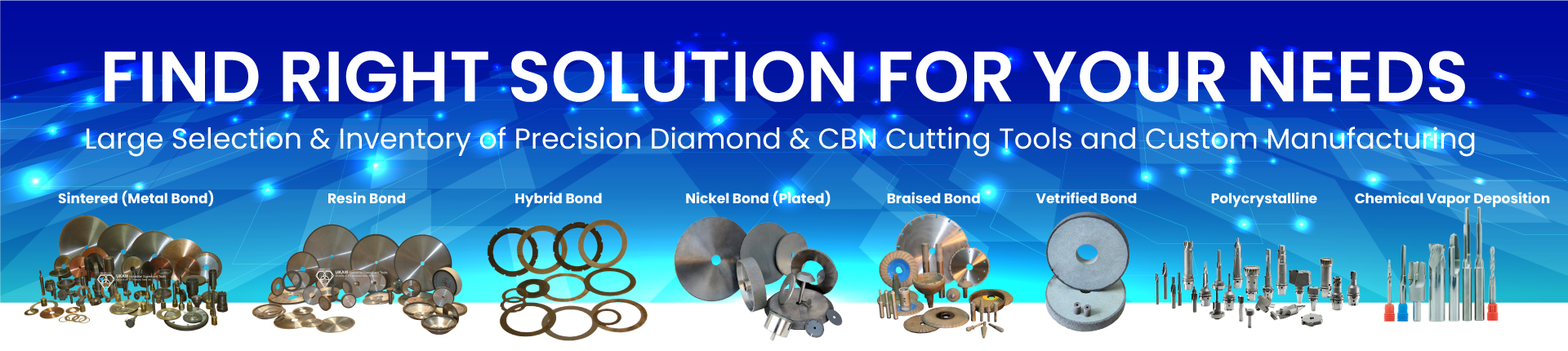
ARE YOU USING RIGHT TOOLS
FOR YOUR APPLICATION?
LET US
HELP YOU
HAVING ISSUES WITH
YOUR CURRENT TOOLS?
Knowledge Center
How to Selecting Right Diamond Tools for your application
How to properly use Diamond Tools
Why use diamond
Diamond vs CBN (cubic boron nitride) Tools
What is Diamond Mesh Size and how to select best one for your application
What is Diamond Concentration and which to use for your application
Diamond Tool Coolants Why, How, When & Where to Use
Get to Know the Diamond Tool Bond Types and Which to use for your application
Get to Know the Diamond Tool Bond Types and Which to use for your application
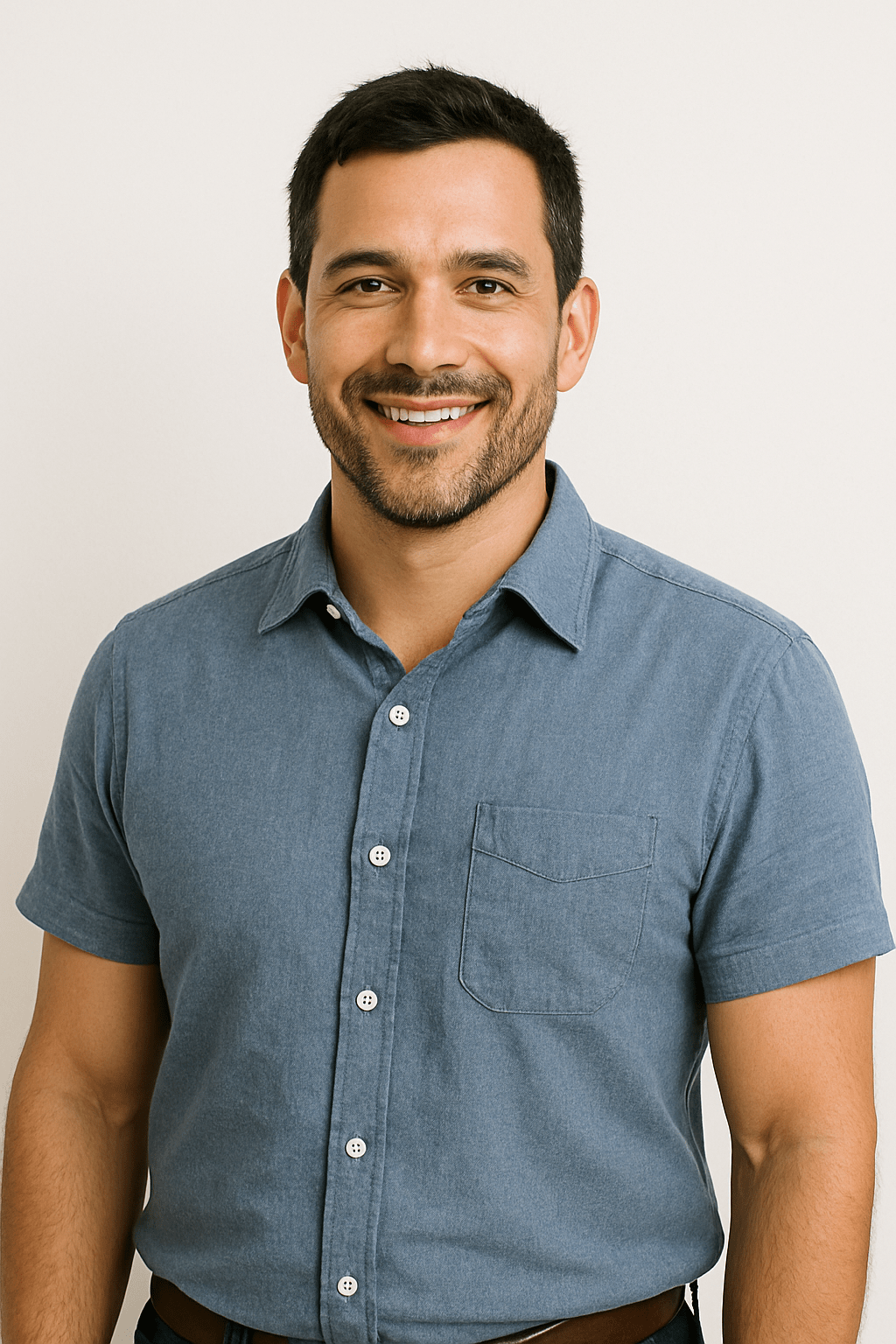
Carlos Sanchez is a senior technical specialist and field applications trainer with more than 17 years of experience in the use and optimization of industrial diamond tools, including ultra-thin diamond blades, core drills, and CBN grinding wheels. With a foundation in industrial engineering and technical operations, Mr. Sanchez has worked extensively with manufacturers and laboratories around the world, providing hands-on support and practical training for a wide range of cutting, grinding, and sample preparation applications.
Fluent in both English and Spanish, Carlos is known for his ability to translate complex tooling concepts into clear, actionable procedures for engineers, technicians, and production staff. His approach emphasizes real-world process improvement, tool longevity, and operator education—ensuring clients get the most out of their diamond tooling investments.
As an author, Mr. Sanchez shares field-tested insights on tool performance optimization, defect prevention, training methodologies, and troubleshooting common cutting issues.