Table of Contents
ToggleCVD (Chemical Vapor Deposition) diamond coating is an advanced technique used to significantly enhance the performance of cutting tools. This process is conducted in a vacuum chamber, where tools, typically made from carbide, are exposed to extremely high temperatures. A hot filament system heats tungsten or other refractory wires until they glow, providing the necessary energy to break down carbon-containing gases like methane, which are introduced into the chamber.
Share this Article with Friend or Colleague
As the temperature rises, these gases decompose, freeing carbon atoms that migrate and re-bond in a crystalline structure. This results in a layer of pure diamond forming atom by atom on the tool's surface. Over time, this leads to a continuous diamond coating, which can be up to 20 microns thick depending on the application and tooling requirements.
The primary benefit of CVD diamond-coated tools is their vastly extended operational life. The diamond coating imparts exceptional hardness and wear resistance, allowing the tools to maintain their cutting edge and dimensional stability far longer than uncoated tools. In practice, carbide tools with a CVD diamond coating can last between 10 to 50 times longer than their uncoated counterparts, depending on the machining conditions and materials processed.
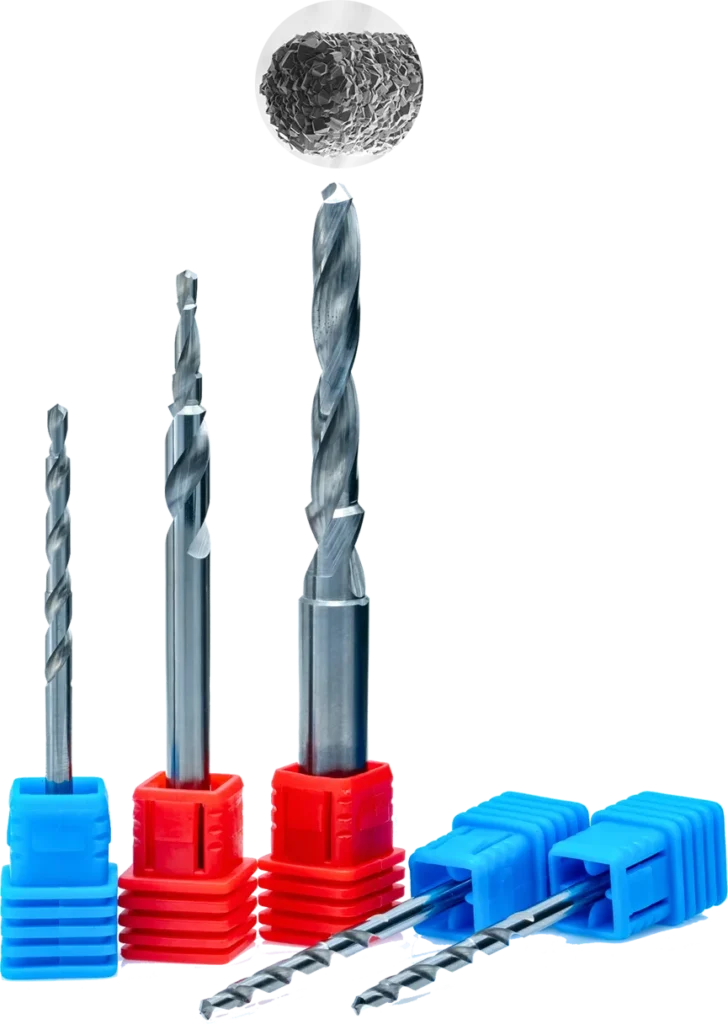
How CVD (Chemical Vapor Deposition) Diamond Works
Besides longevity, CVD diamond coatings also enhance the performance of cutting tools by reducing friction and improving heat dissipation. This allows for higher cutting speeds and more aggressive machining operations, leading to more efficient material removal rates and improved surface finishes on machined parts.
While the initial cost of CVD diamond-coated tools may be higher, the longer lifespan and reduced maintenance demands quickly compensate for the upfront expense. Additionally, the decreased frequency of tool changes minimizes downtime, boosting overall productivity. The versatility of CVD diamond coatings means they can be applied to a wide range of tool geometries and types, making them ideal for industries such as aerospace, automotive, and electronics manufacturing, where precision and tool durability are paramount.
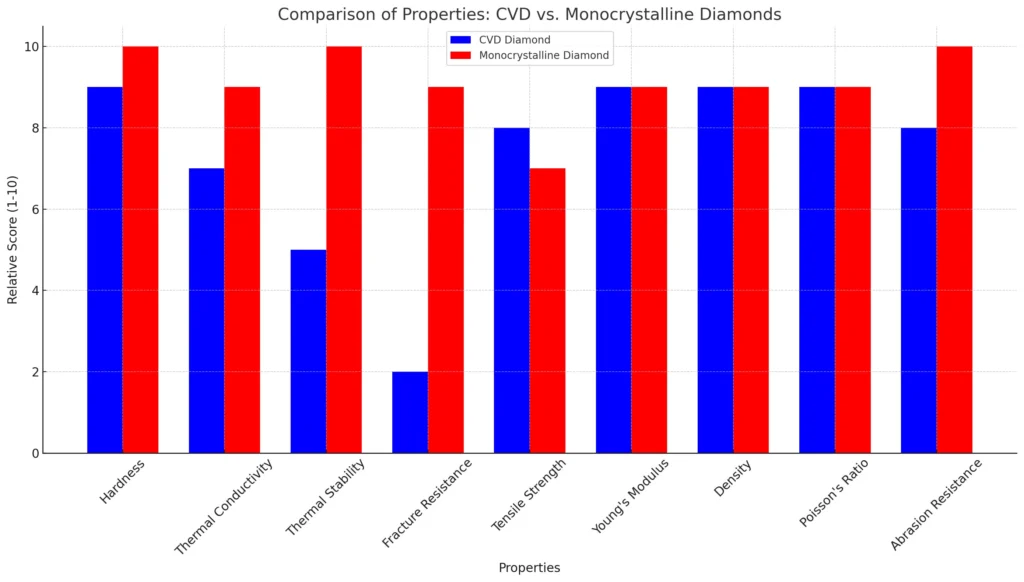
Characteristics and Advantages of CVD Diamond Coatings
Thickness and Uniformity: The thickness of the diamond films can vary typically from 4 to 40 microns, depending on the diameter of the tool and the specific requirements of the application. This variation allows for customized coating solutions tailored to different machining needs.
Purity and Bonding: The diamond films produced are of high purity and consist entirely of crystalline diamond with no binders. This purity is crucial for the film's effectiveness, as it ensures that the properties of diamond, such as extreme hardness and thermal conductivity, are fully imparted to the tool.
Mechanical and Chemical Bonding: One of the distinctive features of CVD diamond coatings is that they are both mechanically and chemically bonded to the tool surface. This dual bonding mechanism enhances the adhesion of the coating, significantly increasing the tool's lifespan by providing exceptional wear resistance and reducing the likelihood of coating delamination under intense operational conditions.
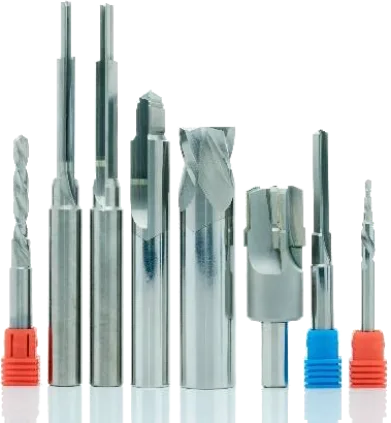
Microstructure Control: The process of diamond crystal growth is meticulously controlled during deposition to produce a diamond film with a microstructure that is optimally suited for the intended machining application. This control over the microstructure is essential for maximizing the performance benefits of the diamond coating, such as improved cutting speed, precision, and reduced heat generation during machining.
Properties of CVD Diamond coatings
Detailed comparison of properties between CVD diamond and Monocrystalline diamond:
Property |
CVD Diamond |
Monocrystalline Diamond |
---|---|---|
Hardness |
10,000 kg/mm² |
Approx. 200 GPa |
Thermal Conductivity (W/mK) |
1800 - 2200 |
3300 (up to 41,000 at 104 K) |
Thermal Stability (°C) |
Up to 700°C |
Up to 2500°C under high pressure |
Fracture Resistance (MPa m^1/2) |
Not specifically reported |
Up to 26.6 |
Tensile Strength (GPa) |
Up to 750 (for thin films) |
Up to 125 (in nanostructures) |
Young's Modulus (GPa) |
1050 |
1050 |
Density (g/cm³) |
3,515 |
3,515 |
Poisson's Ratio |
0.1 |
0.1 |
Abrasion Resistance |
High |
Very High |
The properties of CVD (Chemical Vapor Deposition) diamond and Monocrystalline diamond vary significantly across various parameters, influencing their applications in a range of industries. Here is a detailed comparison between the two types of diamonds based on their physical and mechanical properties.
Hardness
CVD diamond exhibits a hardness of approximately 10,000 kg/mm². In contrast, Monocrystalline diamond is notably harder, with a hardness value of around 200 GPa. This difference makes Monocrystalline diamond one of the hardest materials available, suitable for applications requiring extreme wear resistance and cutting capabilities.
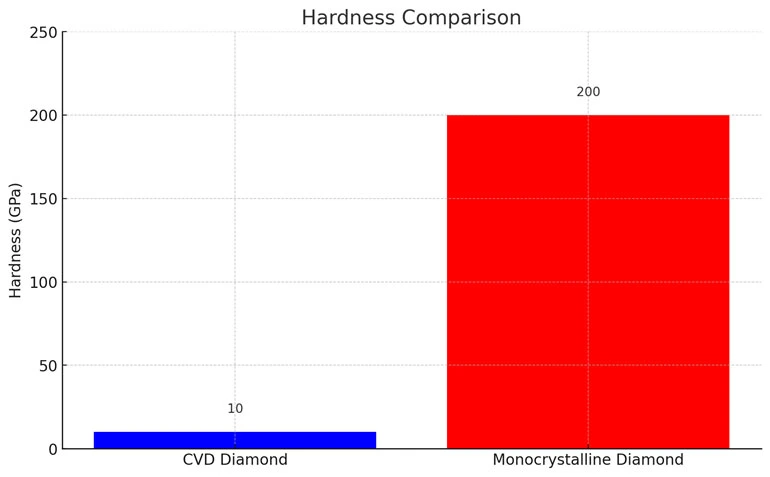
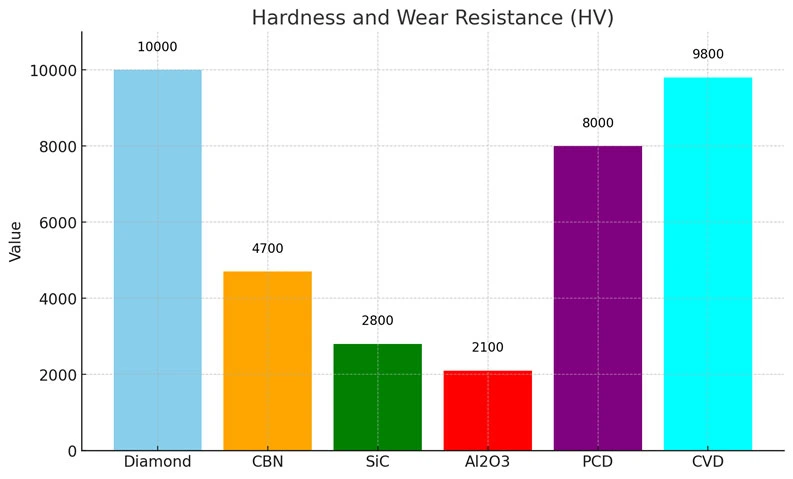
Thermal Conductivity
Thermal conductivity plays a crucial role in applications involving heat dissipation, such as electronics. CVD diamond has a thermal conductivity ranging between 1800 to 2200 W/mK. However, Monocrystalline diamond significantly outperforms this, with thermal conductivity values reaching up to 3300 W/mK, and even potentially 41,000 W/mK at extremely low temperatures (104 K). This makes Monocrystalline diamond an excellent material for managing heat in high-performance systems.
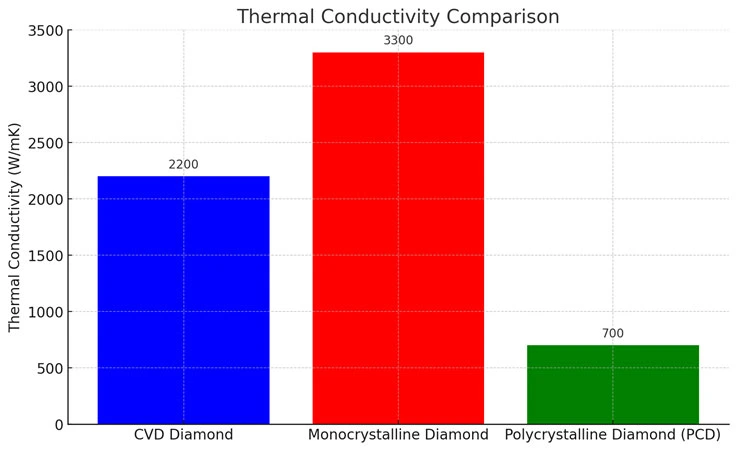
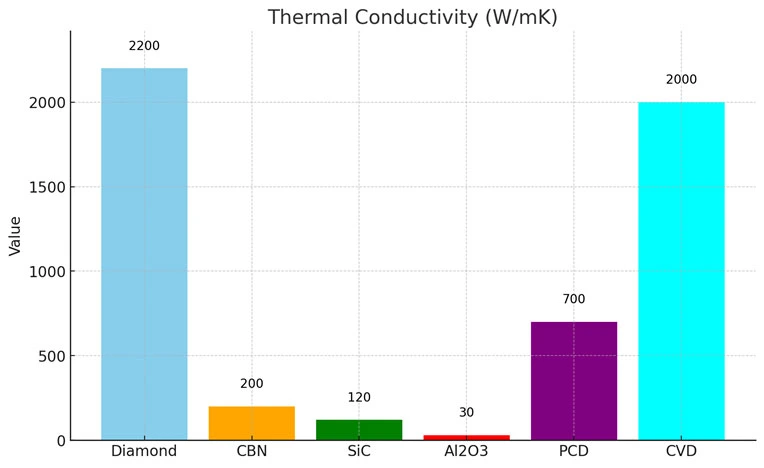
Thermal Stability
Thermal stability is essential for maintaining structural integrity under high-temperature conditions. CVD diamond remains stable up to temperatures of around 700°C. Monocrystalline diamond, on the other hand, can withstand much higher temperatures, up to 2500°C, especially when under high pressure. This makes Monocrystalline diamond the preferred choice for applications involving extreme thermal environments.
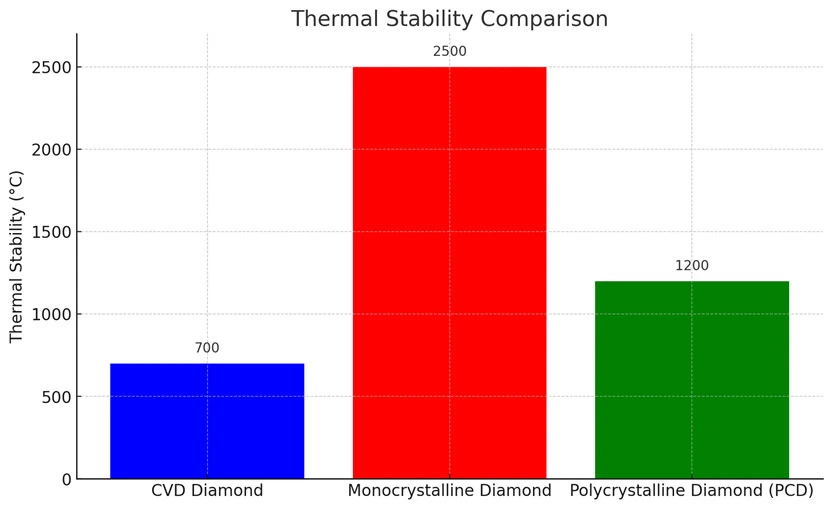
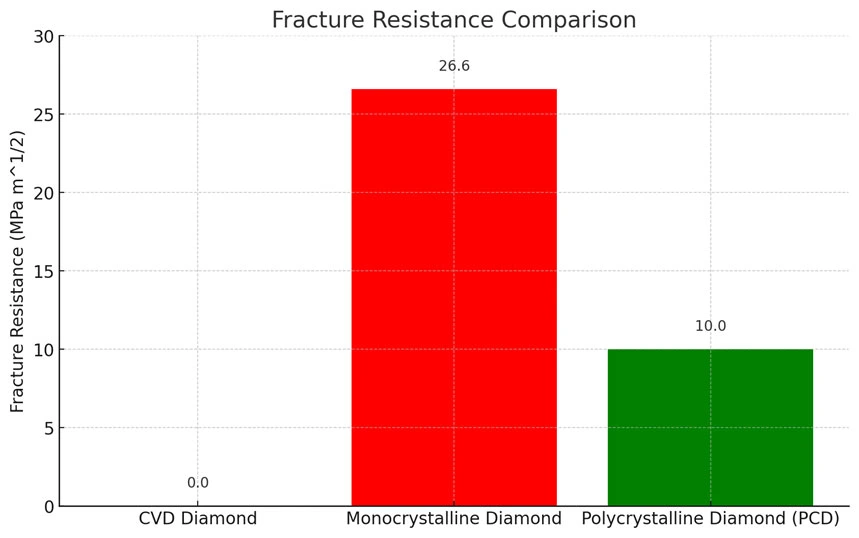
Fracture Resistance
Fracture resistance is an important measure of a material's toughness and its ability to resist cracking. While there is no specific data on CVD diamond's fracture resistance, Monocrystalline diamond has a fracture resistance of up to 26.6 MPa m^1/2. This high resistance contributes to its durability and performance under stress.
Tensile Strength
CVD diamond demonstrates high tensile strength, reaching up to 750 GPa for thin films. For Monocrystalline diamond, tensile strength can go up to 125 GPa, especially in nanostructures. While both types of diamonds offer significant tensile strength, the precise form and structure of the material play a role in determining its performance.
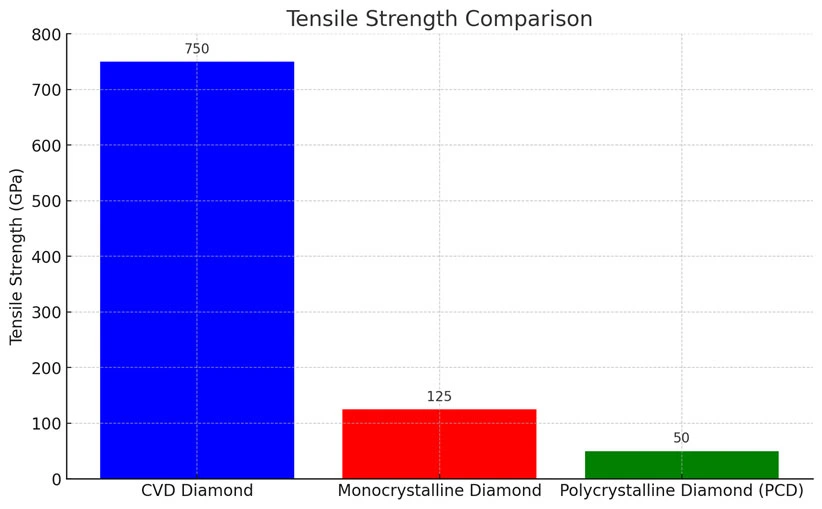
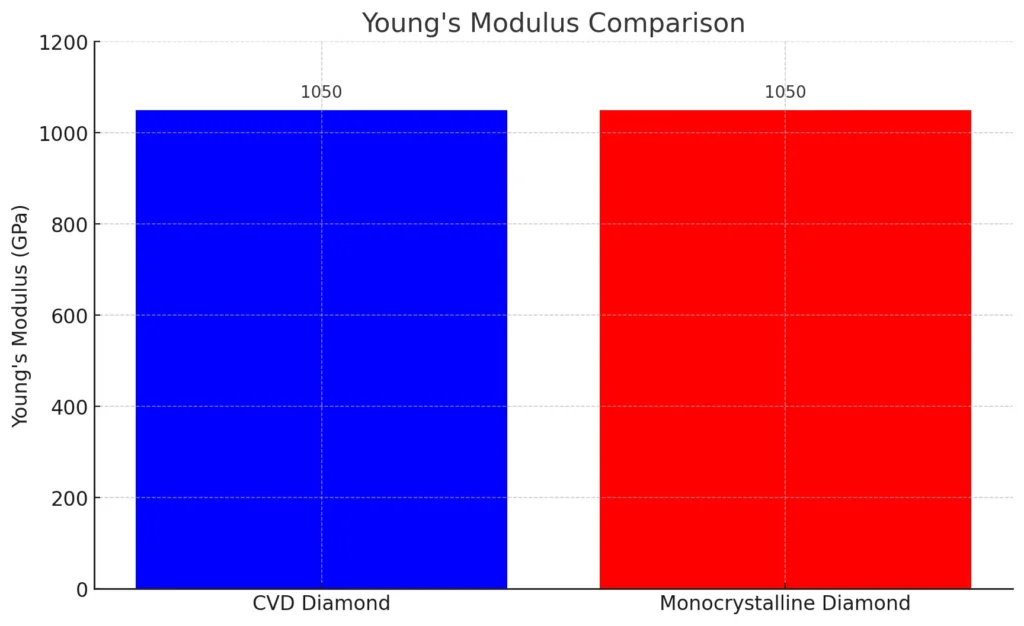
Young's Modulus
Both CVD and Monocrystalline diamonds share a similar Young’s modulus, around 1050 GPa. This indicates their extremely high stiffness and rigidity, which makes them both suitable for applications where minimal deformation is required under mechanical stress.
Density
The density of both CVD and Monocrystalline diamonds is identical, at approximately 3.515 g/cm³. This high density contributes to their overall mechanical properties and durability in applications requiring compact and strong materials.
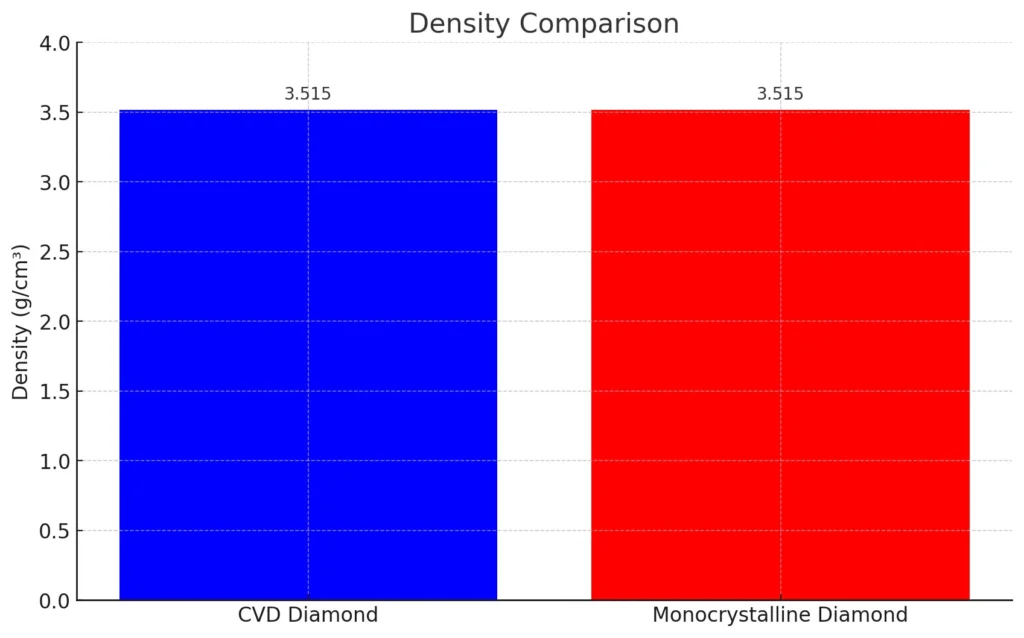
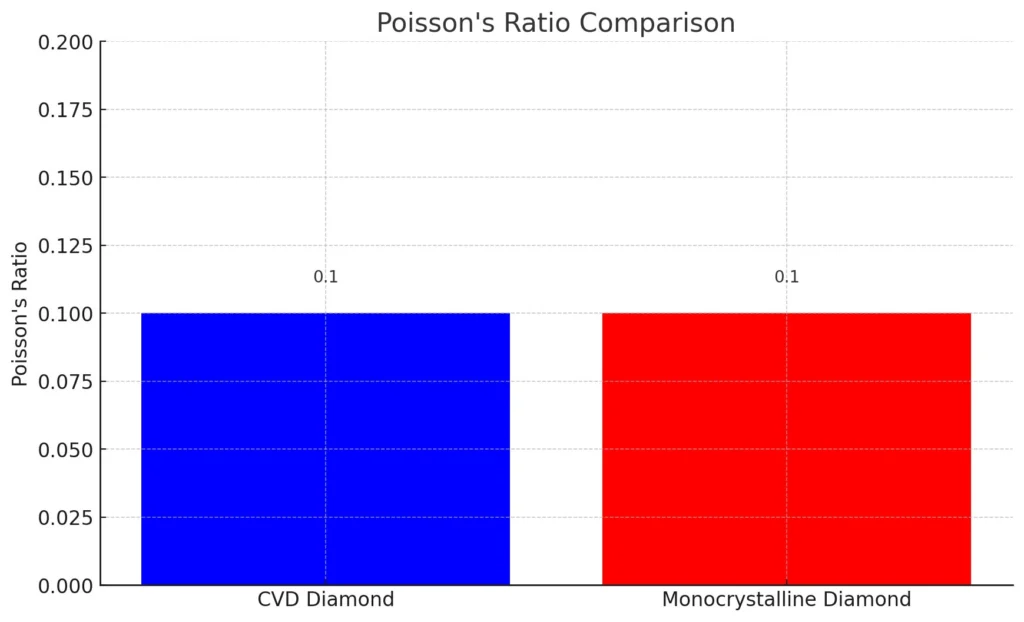
Poisson's Ratio
The Poisson’s ratio, which measures the material's tendency to expand in directions perpendicular to the direction of compression, is 0.1 for both CVD and Monocrystalline diamonds. This similarity suggests that both materials have similar dimensional responses to mechanical stress.
Abrasion resistance is critical for cutting, grinding, and wear-related applications. CVD diamond has a high abrasion resistance, making it suitable for numerous industrial applications. However, Monocrystalline diamond boasts very high abrasion resistance, making it more suitable for demanding applications where extreme wear resistance is required.
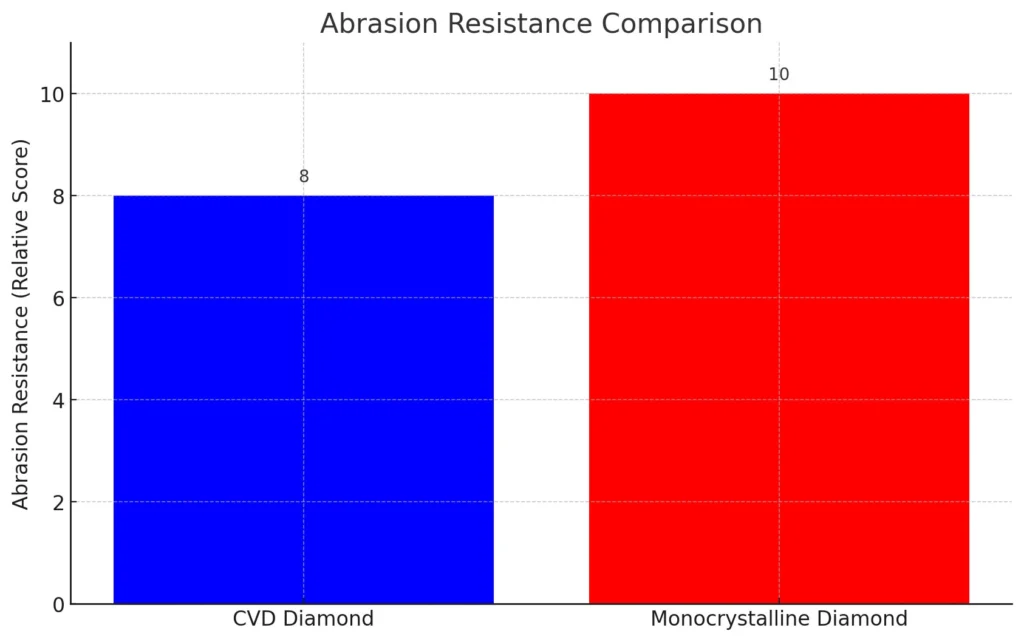
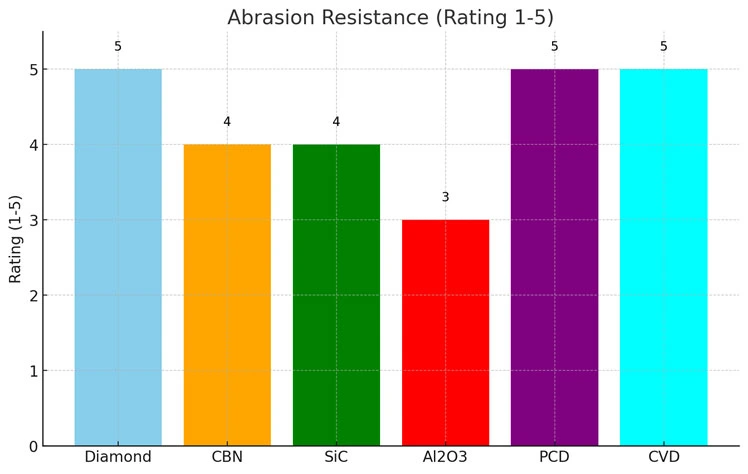
Chemical Inertness
Both CVD (Chemical Vapor Deposition) diamond and Monocrystalline diamond exhibit high levels of chemical inertness, making them highly resistant to reactions with acids, alkalis, and other corrosive substances. This inertness is a crucial property for applications in harsh chemical environments, such as cutting, drilling, and machining materials that are exposed to corrosive agents. Monocrystalline diamond typically exhibits a slightly higher level of chemical stability, contributing to its durability in aggressive chemical processes. CVD diamond, while also chemically inert, provides a practical and cost-effective option for applications where high resistance to chemical erosion is necessary, ensuring prolonged tool life and consistent performance. These properties make both types of diamonds ideal for industries like chemical processing, mining, and biomedical applications, where exposure to aggressive substances is common.
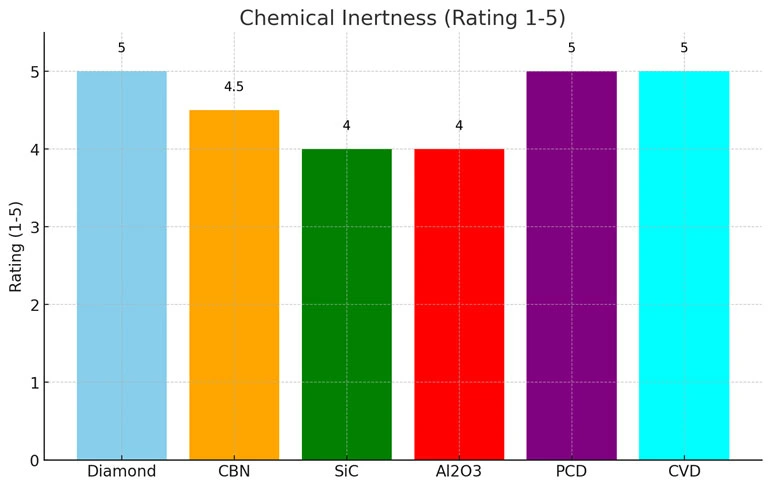
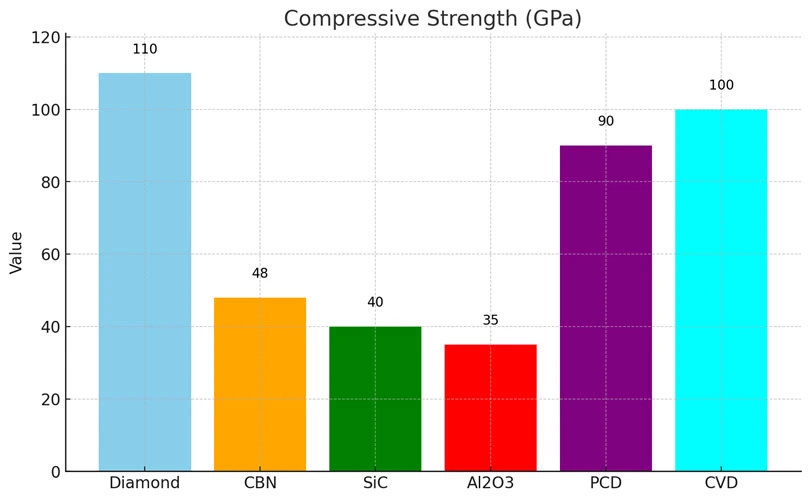
Compress Strength
Compressive strength is the capacity of a material to withstand compressive forces without breaking or deforming. Monocrystalline diamond has an extremely high compressive strength, which can exceed 110 GPa, making it one of the strongest known materials. This high compressive strength allows Monocrystalline diamond to maintain its structural integrity under intense pressure, making it an excellent choice for high-stress applications such as high-precision cutting, deep drilling, and other demanding machining operations.
CVD diamond also exhibits significant compressive strength, though slightly lower than Monocrystalline diamond. The formation of diamond layers in CVD-coated tools provides a strong and durable structure that can handle substantial pressure without fracturing.
While its compressive strength may not match the level of Monocrystalline diamond, CVD diamond offers a balance of strength and flexibility, allowing it to be used effectively in a wide variety of industrial and manufacturing applications.
Applications of CVD Diamond Coatings
CVD diamond coatings are particularly beneficial in industries that require tools to maintain sharpness and integrity under harsh conditions, including aerospace machining, automotive components manufacturing, and the production of composite materials. The enhanced durability and performance of diamond-coated tools lead to increased productivity, reduced downtime due to tool changes, and overall cost efficiency in manufacturing processes.
Benefits of CVD diamond coatings for a range of materials and applications, illustrating how these coatings enhance performance and durability across various industrial sectors:
Application |
Material/Use |
Benefits of CVD Diamond Coatings |
---|---|---|
Graphite Machining |
Graphite |
Reduces tool wear, increases efficiency, maintains precision, crucial for high-quality end products. |
PCB Manufacturing |
Printed Circuit Boards (PCB) |
Enhances wear resistance of drills and routers, leads to more consistent hole quality and diameter, essential for high electronics standards. |
Composite Materials |
GFRP & CFRP |
Produces cleaner cuts with fewer passes, withstands abrasiveness, leads to smoother finishes, extends tool life. |
Semiconductor Drilling |
Gallium & Silicon Wafers |
Reduces microcracks and chips during drilling, increases yield of usable chips, reduces material waste. |
Microelectronic Components |
Microelectronic Devices |
Ensures high levels of precision needed for microfabrication, contributes to reliability and performance of electronic devices. |
Micro Circuit Substrates |
Micro Circuit Substrates |
Maintains exacting standards of precision over prolonged use, prevents wear that could alter tool shape and effectiveness. |
Thin High-Density Ceramics |
Ceramics |
Maintains tool integrity, minimizes the risk of cracking and damage during machining, exceptional wear resistance and reduced friction. |
Hard Metal Alloys |
Tungsten Carbide, Titanium Alloys |
Enhances machining capabilities, provides durable, wear-resistant surface, suitable for aerospace and automotive industries. |
Ceramic Materials |
Ceramics |
Offers benefits similar to metal machining, allows for precision machining without causing damage or deformation. |
Exotic Materials Machining |
Nickel-based Superalloys, Intermetallic Compounds |
Used for processing high-performance materials, enhances tool longevity where conventional tools would wear out quickly. |
Electrodes and Electrical Contacts |
Electrodes and Contacts |
Provides excellent electrical insulation, resistance to erosion, crucial for high power or high-frequency electrical applications. |
Decorative Applications |
Jewelry |
Coats less expensive materials with a durable layer of diamond, offers aesthetic appeal and scratch resistance. |
Optoelectronics and Photonics |
Laser Windows, Lenses |
Enhances durability and performance of optical components in harsh environments, leverages diamond's transparency and thermal conductivity. |
Biomedical Applications |
Surgical Instruments, Prosthetic Devices |
Ensures longevity and resistance to sterilization processes, suitable for various biomedical applications. |
Wear-Resistant Coatings |
Mechanical Seals, Pumps |
Reduces maintenance needs, extends operational life of systems handling abrasive or corrosive fluids. |
Advantages of CVD Diamond Tools
CVD diamond-coated tools offer several advantages that make them superior to uncoated tools or tools with alternative coatings. One of the primary benefits is their extended operational life. The diamond coating provides exceptional hardness and wear resistance, allowing the tools to maintain their cutting edge and perform efficiently for much longer periods. This longevity translates to fewer tool replacements and reduced operational costs over time.
In addition to durability, these diamond-coated tools enhance performance and efficiency in machining operations. The diamond layer on the tool enables higher speeds and feed rates while maintaining cut quality. This ability to perform faster machining without compromising precision significantly improves production efficiency and can lead to higher throughput in industrial applications. Furthermore, the reduction in wear also means that the tools can sustain aggressive cutting parameters, which would quickly degrade uncoated alternatives.
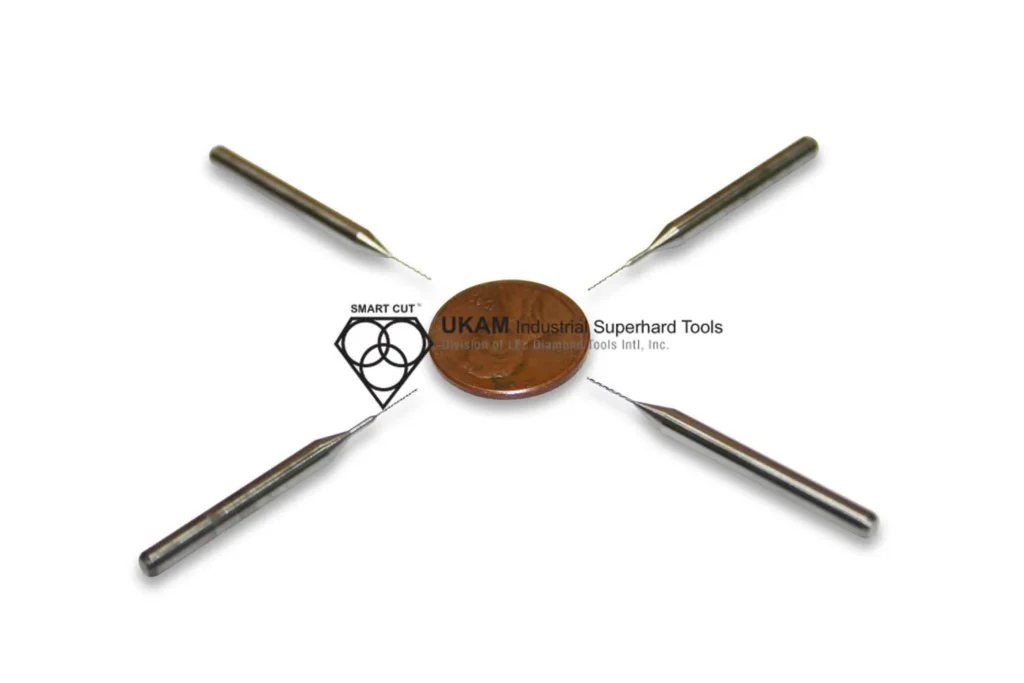
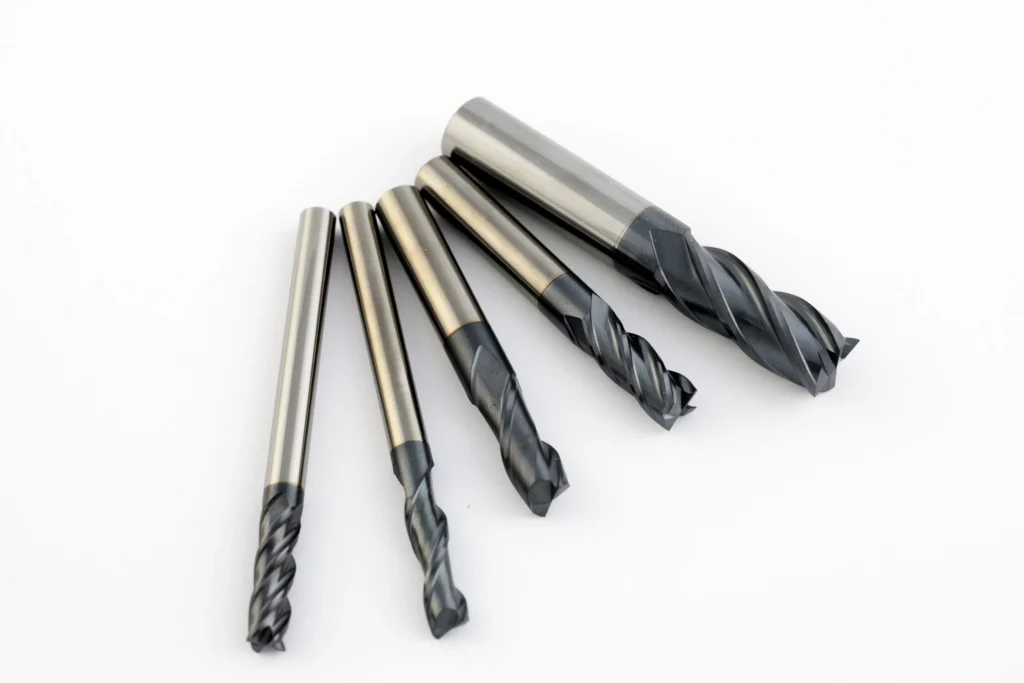
The cost-effectiveness of CVD diamond-coated tools is another major advantage. Since these tools last much longer, they reduce the need for frequent replacements, lowering the overall tooling costs. This extended tool life also leads to a decrease in downtime associated with tool changes, maintenance, and adjustments, thereby boosting productivity. Over the life of the tool, the initial investment in CVD diamond coatings is often offset by the cost savings from reduced replacement needs and increased uptime.
Consistency and precision in production are also key benefits of using CVD diamond-coated tools. The diamond coating ensures that the tools maintain a sharp and stable cutting edge throughout their operational life, which is crucial for high-quality production outcomes. As a result, products are manufactured with consistent precision, reducing defects and ensuring that final components meet stringent quality standards.
How Does CVD Diamond Tools Compare to Other Types of Tools (including conventional diamond tools, PCD diamond tools, abrasive tools, and carbide tools)
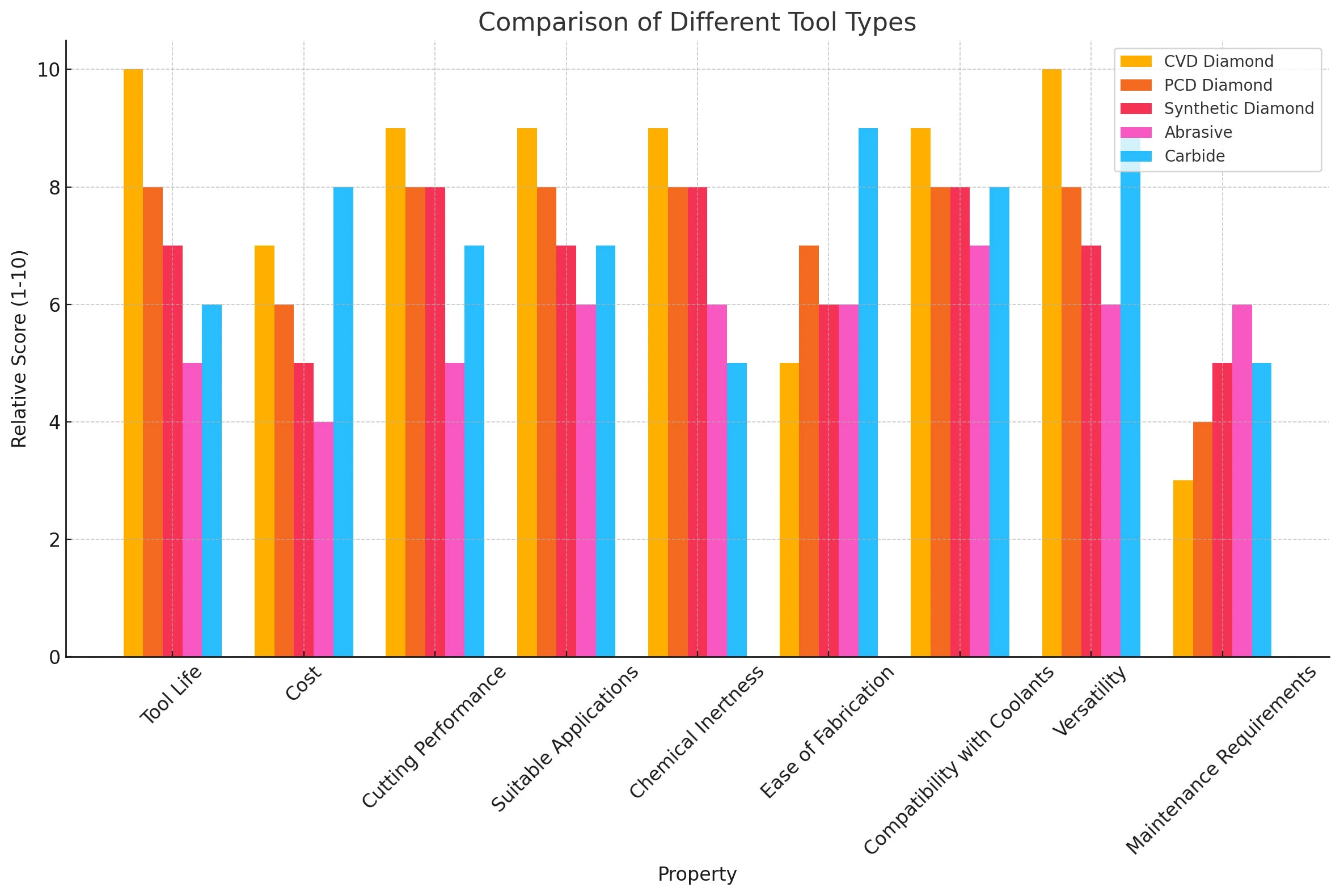
CVD diamond-coated tools have an impressive tool life, lasting up to 50 times longer than uncoated tools and minimizing replacements. PCD tools also offer durability but may wear out faster on very hard materials. Synthetic diamond tools perform well in cutting, grinding, and polishing but have a shorter lifespan under extreme conditions. Abrasive tools typically have a moderate to short lifespan, while carbide tools offer decent longevity, although they generally fall short compared to diamond-coated options.
In terms of cost, CVD diamond tools have a high initial expense, balanced by their durability. PCD tools are slightly less costly than CVD tools, while synthetic diamond tools, though expensive, are more affordable than natural diamonds. Abrasive tools are moderately priced, and carbide tools are the most cost-effective, offering a good balance of affordability and performance.
CVD diamond tools deliver superior cutting precision and finish. PCD tools excel in non-ferrous materials and ceramics, while synthetic diamond tools handle hard and brittle materials effectively. Abrasive tools provide moderate performance depending on their material, and carbide tools perform well across ferrous and non-ferrous materials.
In terms of applications, CVD diamond tools are versatile for precision machining of ceramics, composites, glass, and electronics. PCD tools are best for non-ferrous metals and ceramics, and synthetic diamond tools are ideal for cutting hard metals and gemstones. Abrasive tools are suitable for grinding and polishing, while carbide tools work well for both ferrous and non-ferrous machining.
CVD diamond tools exhibit high chemical inertness, resisting acids and alkalis effectively. PCD tools have good resistance but slightly less than CVD. Synthetic diamond tools are similarly inert, while the chemical resistance of abrasive tools varies. Carbide tools offer moderate chemical resistance.
Fabrication of CVD diamond tools is moderately complex due to the specialized coating process. PCD tools are easier to produce with sintering, and synthetic diamond tools require precision in synthesis. Abrasive tools have a moderate fabrication process, while carbide tools are easy to manufacture and widely available.
CVD diamond tools are compatible with most machining coolants, enhancing tool life. PCD tools perform well with standard coolants, as do synthetic diamond tools in cutting and grinding. Abrasive tools generally work well with coolants to reduce heat, and carbide tools are compatible with standard machining fluids.
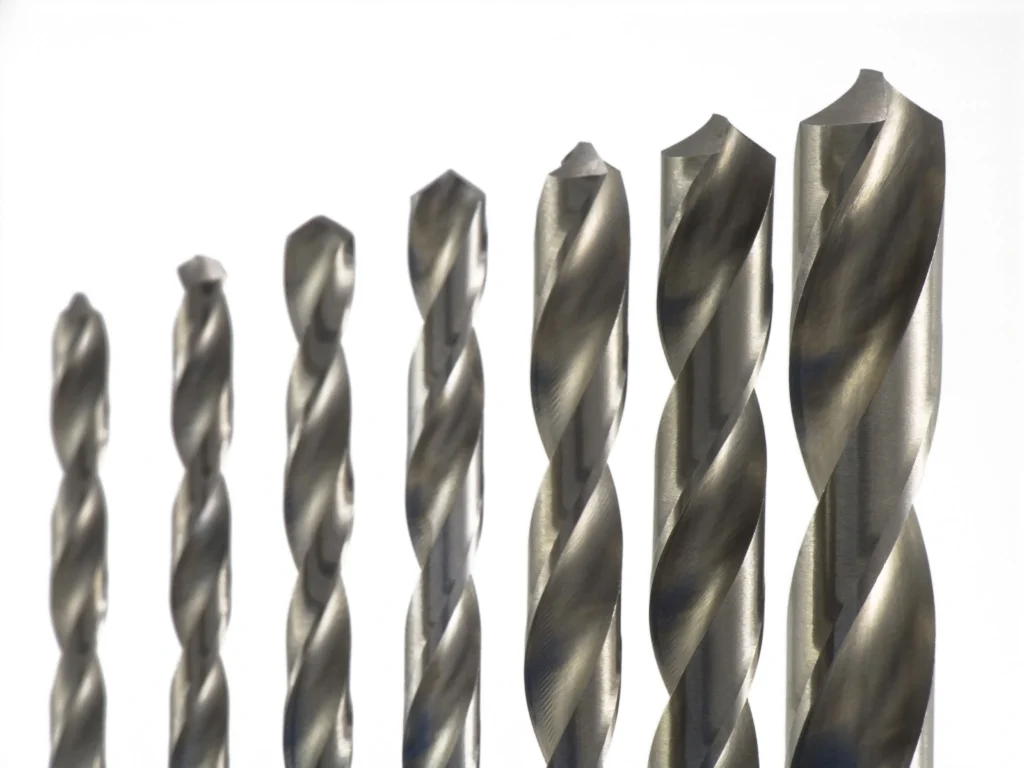
In versatility, CVD diamond tools can handle a wide range of materials, from ceramics to electronics. PCD tools work best with non-ferrous metals and composites, while synthetic diamond tools are versatile for cutting and grinding hard materials. Abrasive tools are adaptable for grinding and polishing, and carbide tools are widely applicable across different machining processes.
Maintenance for CVD diamond tools is minimal, thanks to their durability. PCD tools require low to moderate upkeep, while synthetic diamond tools need more attention, particularly for improper use. Abrasive tools often need more frequent replacements, and carbide tools have moderate maintenance needs, offering a good balance between durability and versatility.
Selecting the Right CVD Diamond Tools for your Application
When selecting the right CVD diamond tool for an application, it’s important to consider the specific requirements of the material being machined, the design of the tool, and the cost-performance balance.
Material Properties
When choosing a CVD diamond tool, understanding the properties of the work material is fundamental. The hardness and abrasiveness are especially crucial because they directly influence tool wear, cutting performance, and the quality of the final product. Materials like ceramics, composites, glass, and even certain metals demand tools that can withstand intense cutting forces without degrading quickly. CVD diamond tools are specifically designed for such demanding applications, offering high wear resistance, exceptional hardness, and the ability to maintain sharp cutting edges for extended periods.
Ceramics, for example, are highly brittle but incredibly hard, making them difficult to machine without cracking or chipping. A CVD diamond-coated tool, with its exceptional hardness and thermal stability, provides the necessary precision and durability to cut ceramics cleanly, minimizing tool wear and improving the surface finish. Similarly, composites such as carbon fiber-reinforced polymers (CFRP) or glass fiber-reinforced polymers (GFRP) are highly abrasive due to their fiber structure.
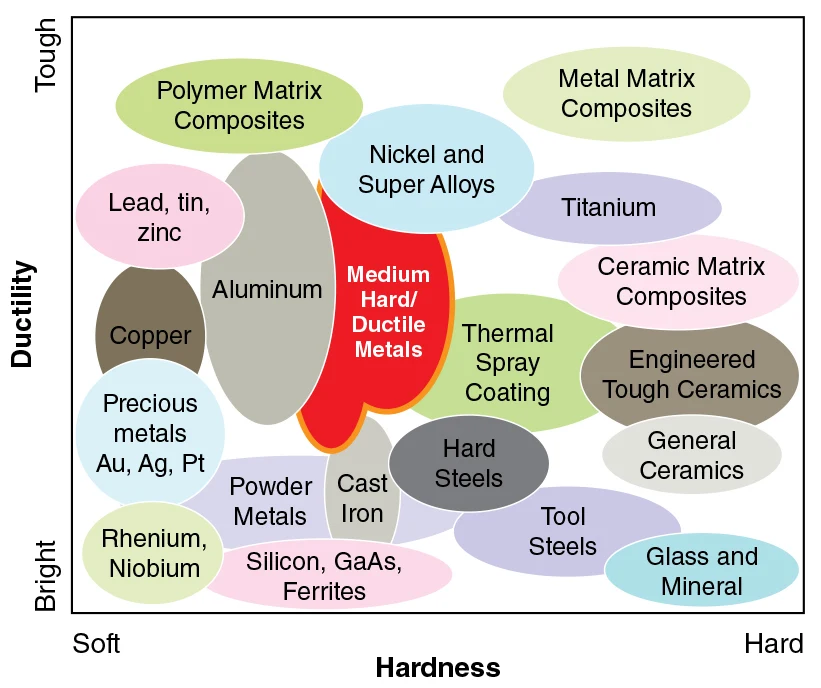
Using CVD diamond-coated tools significantly reduces edge rounding and breakage during cutting, resulting in cleaner cuts and prolonged tool life.
Glass is another material that benefits from CVD diamond tooling. The hardness of the diamond allows for smooth, precise cuts, which is essential when working with glass to avoid fractures or surface damage. This is particularly important in applications like optics or decorative glassware, where maintaining high precision and aesthetic quality is critical.
On the other hand, softer materials like certain plastics, wood, or aluminum alloys do not necessarily require the extreme hardness provided by a CVD diamond tool. For these materials, the high cost of CVD diamond tools may not be justified, as other more economical tool coatings (e.g., PCD or carbide) can achieve comparable results without the added expense. The key is to match the material’s properties with a tool that has the appropriate balance of hardness, toughness, and resistance to wear and heat.
The abrasiveness of the material is another determining factor in tool selection. Highly abrasive materials quickly wear down traditional tool coatings, leading to loss of edge sharpness and poor surface finishes. CVD diamond coatings are engineered to resist such wear, making them suitable for machining abrasive materials like stone, cemented carbides, and high-strength composites. The low coefficient of friction of the diamond coating also reduces cutting forces and heat generation, which helps maintain tool performance and enhances tool life.
Tool Geometry & Design
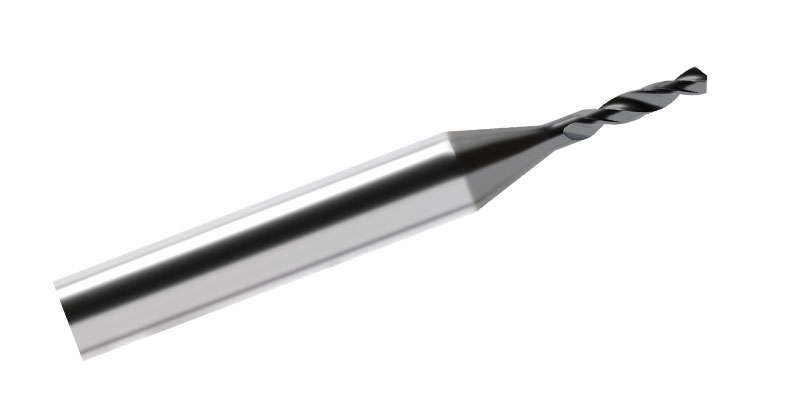
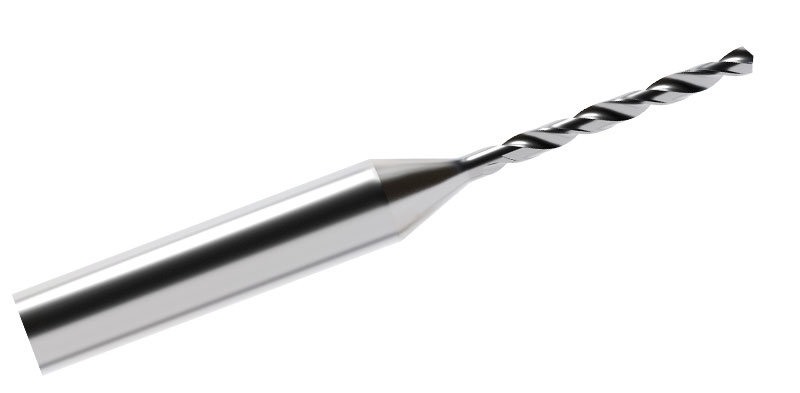
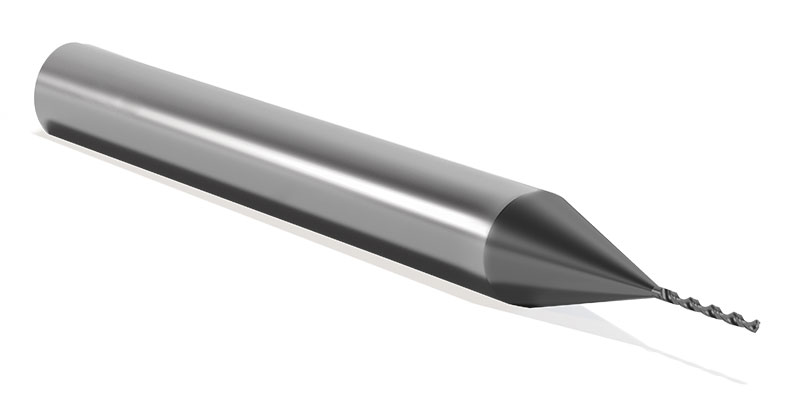
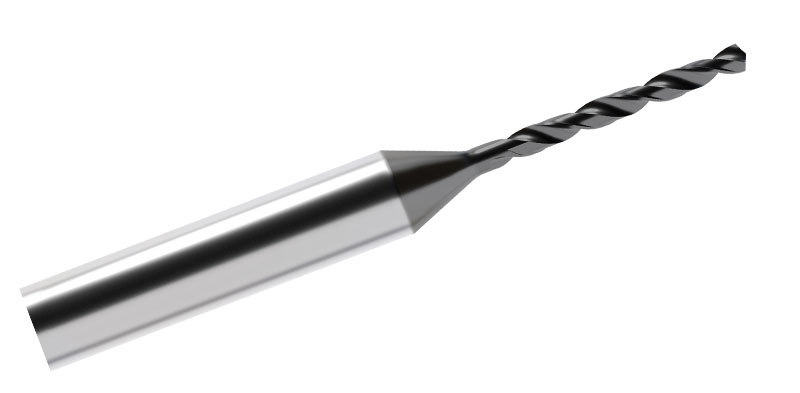
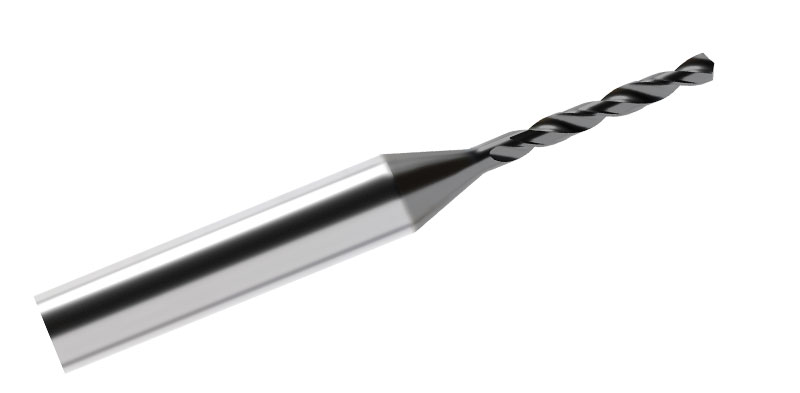
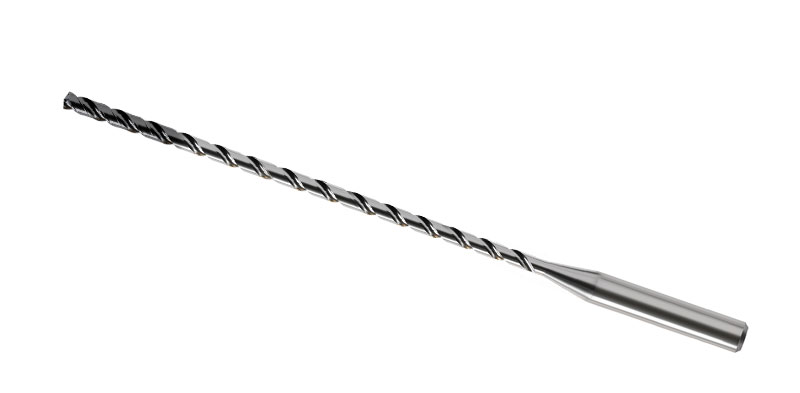
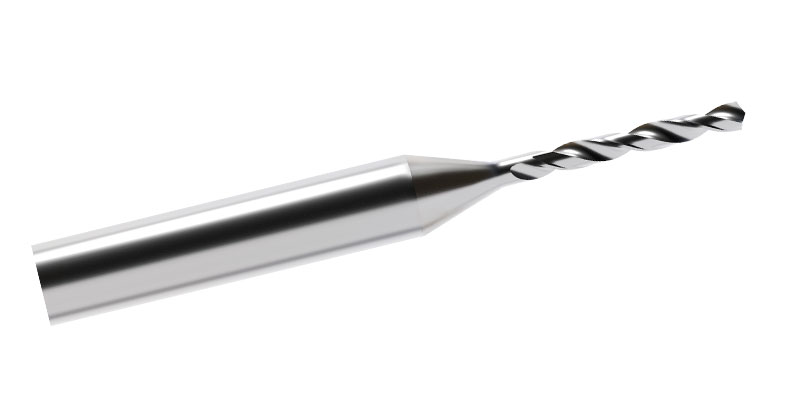
The geometry and design of CVD diamond tools significantly influence their performance and effectiveness in various applications. One key aspect is the thickness of the diamond coating itself. A thicker diamond coating provides greater durability and resistance to wear, which can be beneficial when machining hard or abrasive materials. This thicker layer helps extend tool life by providing a robust barrier between the tool substrate and the workpiece. However, the downside to this added durability is a potential loss of precision. The increased thickness can affect the sharpness of the cutting edges, which may be critical for applications requiring high levels of accuracy and fine surface finishes.
On the other hand, a thinner CVD diamond coating maintains a sharper edge, making the tool more suitable for applications where precise cuts are necessary. This allows for higher-quality surface finishes and cleaner edges, particularly in delicate or fine-detail work. However, the trade-off is that a thinner coating may wear down faster, especially when used on highly abrasive materials. Thus, finding the right balance in coating thickness is essential, and it depends largely on the material being cut and the desired cutting quality.
Tool geometry is equally important in maximizing the benefits of a CVD diamond coating. The shape of the cutting edge, rake angles, clearance angles, and the overall tool profile directly influence how efficiently the tool can remove material while minimizing wear and chipping. For example, a positive rake angle can reduce cutting forces and improve chip evacuation, which is beneficial when working with softer or more ductile materials. Conversely, a negative rake angle provides more support to the cutting edge, enhancing durability when machining harder materials.
Flute design is another critical factor. The number of flutes, their size, and their shape can impact the tool’s ability to clear chips effectively during machining. Proper chip evacuation is crucial for maintaining cutting efficiency and preventing tool wear or damage. A tool with fewer but larger flutes might be better suited for aggressive material removal, while a tool with more flutes and finer geometry might be more appropriate for precision finishing work.
The overall tool design should also consider the workpiece material and the specific application. For instance, in milling, the helix angle of the tool can impact how smoothly the tool engages with the workpiece. A high helix angle can provide a smoother cutting action, which is desirable for delicate or flexible materials. However, a lower helix angle provides a more aggressive cut, which may be necessary for hard materials.
To maximize the benefits of the CVD diamond coating, the tool geometry must be optimized to ensure that it aligns with the coating's properties and the demands of the cutting process. This means taking into account factors such as cutting speed, feed rates, depth of cut, and workpiece material. By doing so, the tool will not only perform efficiently but also maintain its cutting edge longer, ensuring consistent quality and productivity in machining operations.
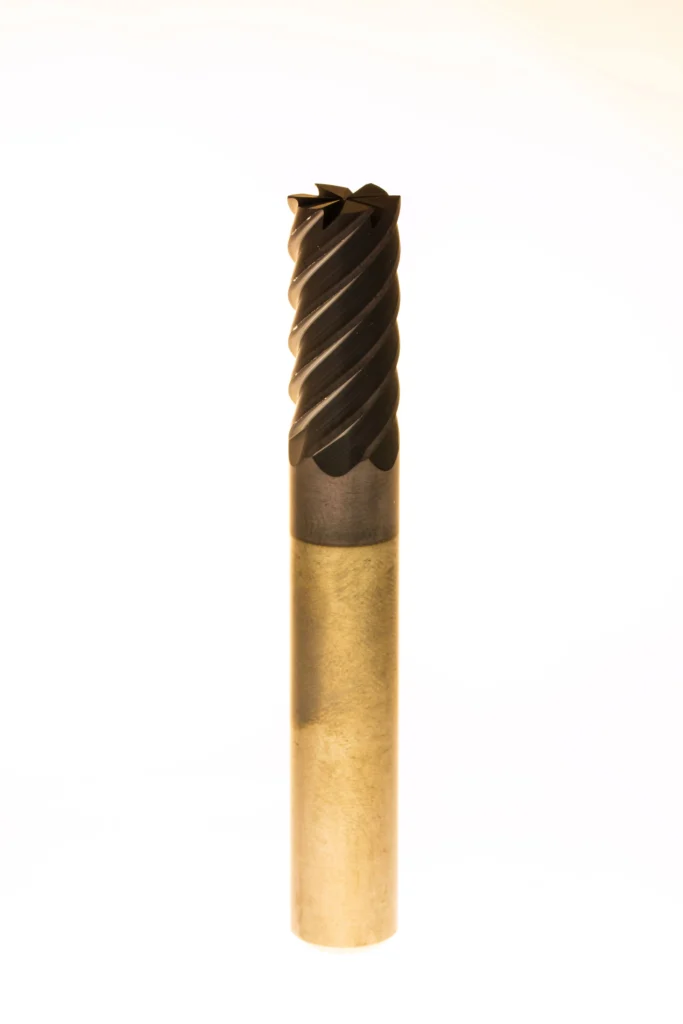
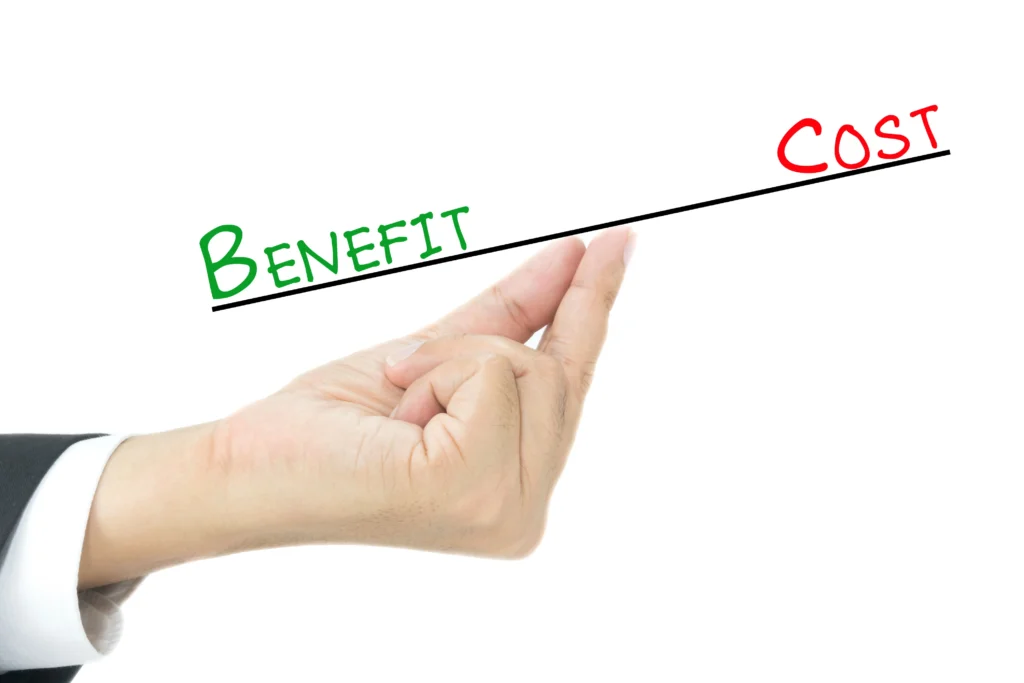
Cost
When considering the cost of CVD diamond-coated tools, it's crucial to strike a balance between the upfront investment and the tool's performance and longevity. While these tools typically come with a higher initial cost compared to uncoated or other coated alternatives, their extended lifespan often makes them more economical over time. The high wear resistance and durability of CVD diamond-coated tools mean fewer replacements, reduced downtime, and increased efficiency, especially in high-volume or precision-critical operations.
In applications where precise machining, minimal tool wear, and high production rates are necessary, the cost-effectiveness of CVD diamond tools becomes apparent. Their ability to maintain sharpness and cut quality over a long period not only ensures consistent product quality but also reduces overall tool costs.
The need for fewer replacements and less frequent tool changes translates to significant cost savings in production and maintenance, making these tools a wise investment for demanding applications.
However, the suitability of CVD diamond tools should be evaluated based on the specific demands of the application. For less demanding operations, where the materials being processed are softer or the required precision is lower, the cost-benefit advantage of CVD diamond coatings may not be as pronounced. In such cases, alternative tools like carbide or PCD (Polycrystalline Diamond) tools could provide adequate performance at a lower upfront cost. Conducting a detailed cost-benefit analysis, considering factors like tool life, material properties, production volume, and precision requirements, can help determine whether the investment in CVD diamond-coated tools will offer the best value or if another tool option may better align with both the technical and budgetary needs of the operation.
CVD Micro Tools (Micro Drills, End Mills, Routers)
CVD micro drills are specialized tools designed for precision drilling in hard and brittle materials. They are available in a wide range of sizes, from diameters as small as 0.05mm to 6mm, and come with standard shank sizes of 3mm and 3.2mm. To accommodate different drilling needs, these drills also offer varying head lengths starting from 0.5mm and include a variety of flute designs to match specific application requirements. CVD micro drills are ideal for producing micro-holes in challenging materials like sapphire, high-density ceramics, micro-circuit substrates, glass, silicon, and various types of wafers and tubes.
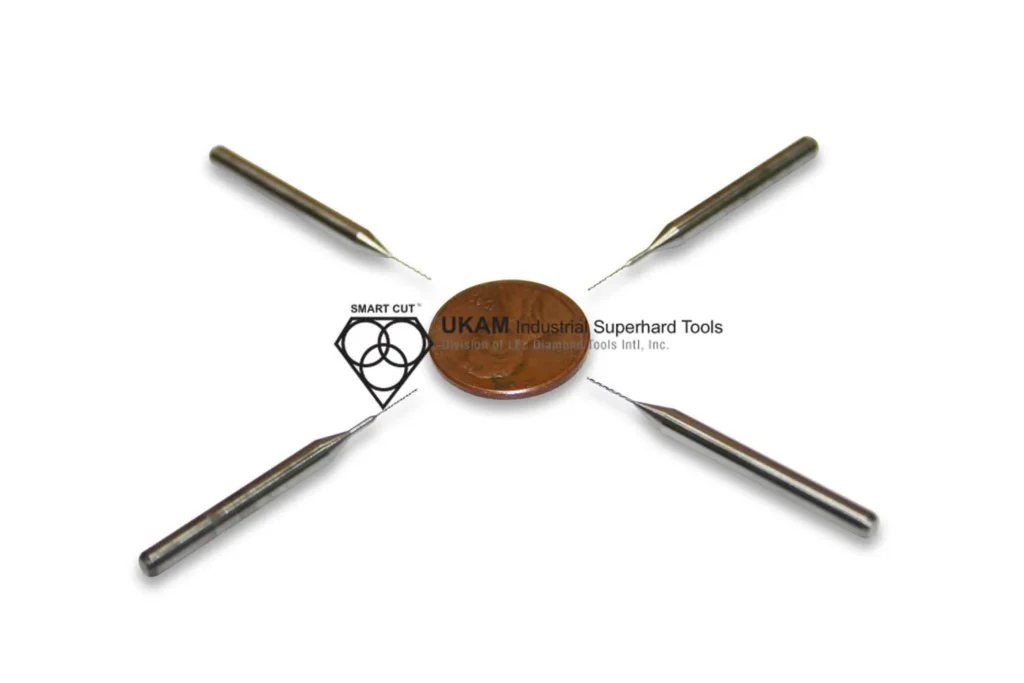
These drills are made with a tungsten carbide substrate coated with a microcrystalline CVD diamond layer consisting of evenly distributed diamond particles sized between 3-6 microns. This diamond coating enhances the performance and lifespan of the carbide drills significantly—up to 12 to 20 times longer than non-coated tools. This not only ensures a cleaner, more precise cut but also reduces operational downtime, as fewer tool changes are required throughout the drilling process.

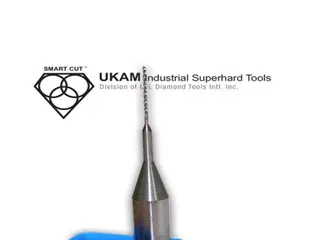
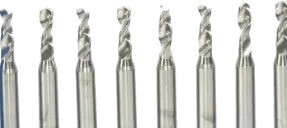
CVD micro tools and end mills are also offered in various geometries, sizes, flute designs, head lengths, and coatings to suit diverse machining needs. These micro tools are particularly well-suited for creating complex geometries and small features with high precision, such as drilling small holes, machining tiny pockets, and forming intricate ribs and channels. Their precision and tight tolerance capabilities make them invaluable for applications requiring detailed and fine-feature work.
In addition to micro drills and end mills, small CVD routers and tooling are also available, specifically designed for routing operations that involve removing material to produce grooves, channels, or profiles. These routers are commonly used across a variety of industries where precise cuts and detailed designs are required. The CVD diamond coating on these small routers enhances their wear resistance and extends tool life significantly, making them highly efficient for intricate machining tasks. Like the micro drills, CVD routers feature a diamond layer on a tungsten carbide substrate, which drastically increases the durability of the tool and minimizes downtime caused by frequent tool replacements.
Recommended RPM’s for CVD Diamond Tools
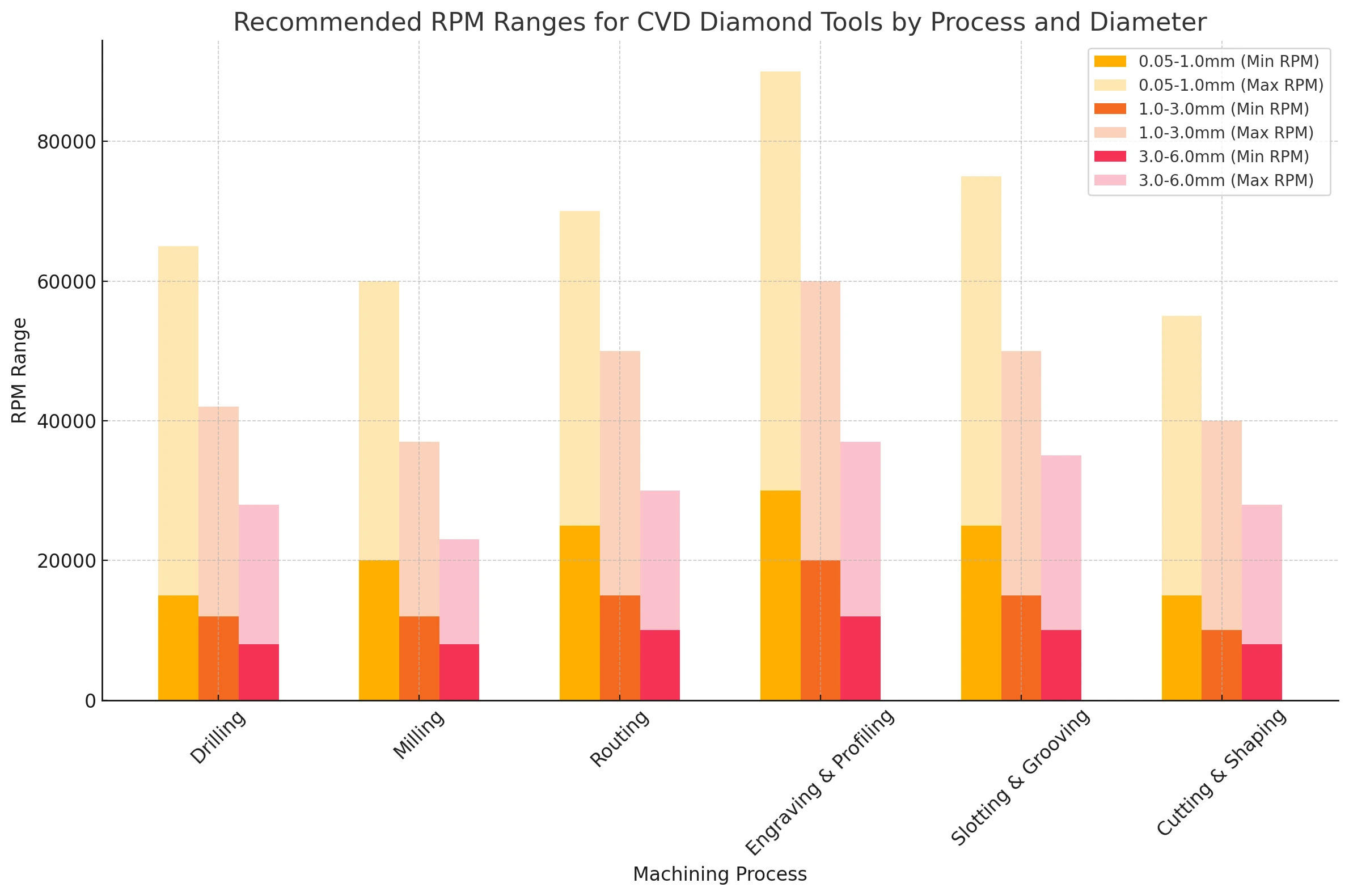
Recommended RPMs for various machining processes using CVD diamond tools based on tool diameter and material type:
Machining Process |
Material |
Tool Diameter (mm) |
Recommended RPM Range |
Notes |
---|---|---|---|---|
Drilling |
Hard/brittle materials (ceramics, glass, silicon, sapphire) |
|
|
|
Milling |
High-density ceramics, composites (GFRP/CFRP), graphite |
|
|
|
Routing |
PCB boards, composites, ceramics |
|
|
|
Engraving & Profiling |
Quartz, ceramics, glass, silicon wafers |
|
|
|
Slotting & Grooving |
Silicon, ceramics, composites |
|
|
|
Cutting & Shaping Hard Materials |
Sapphire, gemstones, ceramics, alloys |
|
|
|
Recommended RPM’s Range for CVD Diamond Tools
Material |
Min SFM (Surface Feet per Minute) |
Max SFM (Surface Feet per Minute) |
---|---|---|
Aluminum |
2000 |
6000 |
Aluminum (5-8% Si) |
1800 |
5000 |
Aluminum (8-12% Si) |
1500 |
4500 |
Aluminum (14-18% Si) |
1200 |
3500 |
Copper |
1500 |
4000 |
Brass |
1500 |
4500 |
Bronze |
1000 |
3500 |
Carbon Composites |
2500 |
5500 |
Glass Fiber |
1800 |
4000 |
Graphite |
2500 |
6000 |
Sintered Carbide |
600 |
1500 |
High Aluminum Ceramics |
800 |
2000 |
Silicon |
500 |
1200 |
Wood & Composites |
3000 |
8000 |
Carbon |
1000 |
2500 |
Titanium Alloys |
600 |
1200 |
Stainless Steel |
500 |
1000 |
Zinc Alloys |
1500 |
3500 |
Nickel-based Alloys |
500 |
1000 |
Magnesium Alloys |
2000 |
6000 |
Composite Laminates |
2000 |
5000 |
Molybdenum |
500 |
800 |
Inconel |
400 |
700 |
Hardened Steel |
400 |
800 |
Zirconium Alloys |
700 |
1200 |
Superalloys (General) |
400 |
900 |
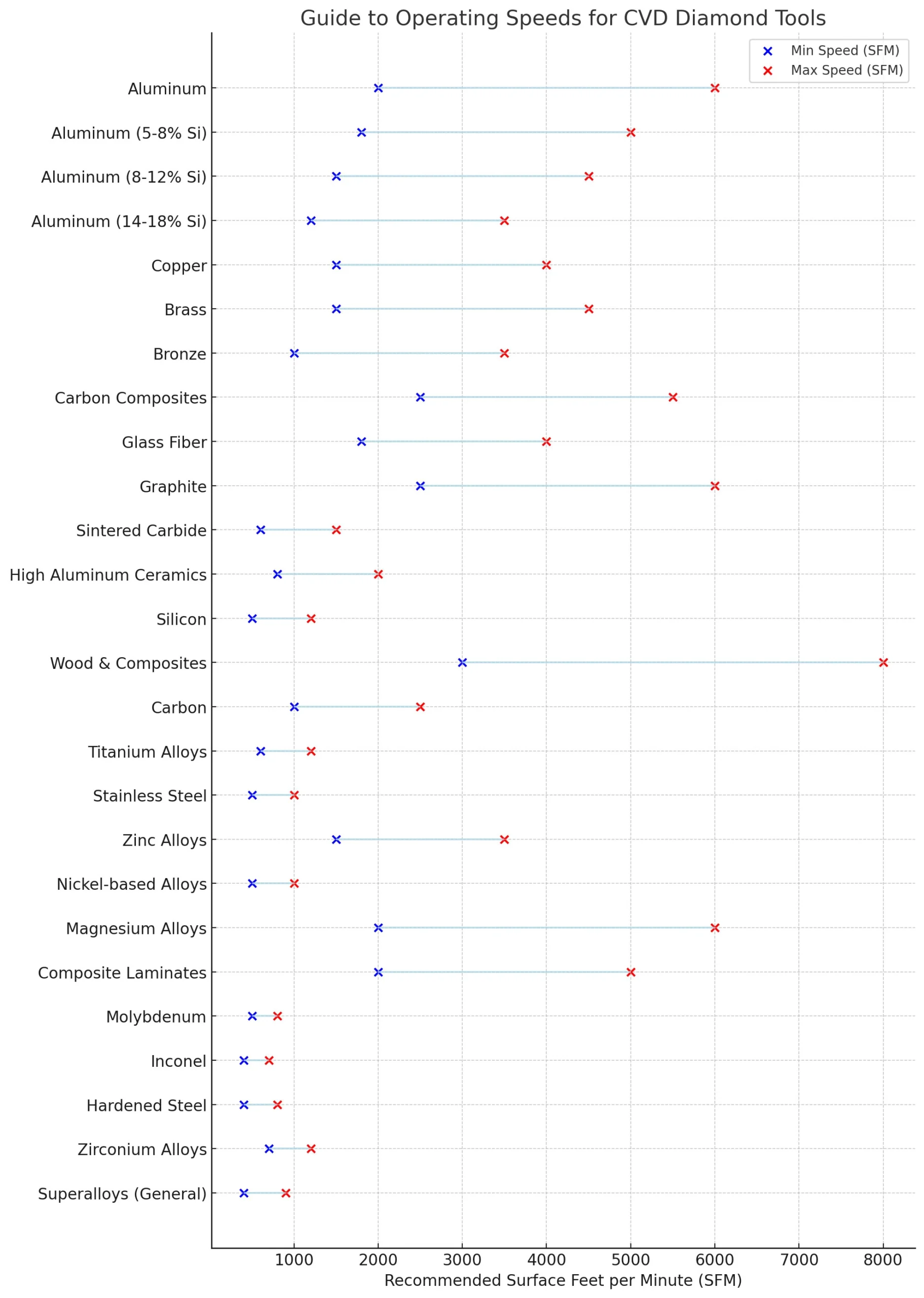
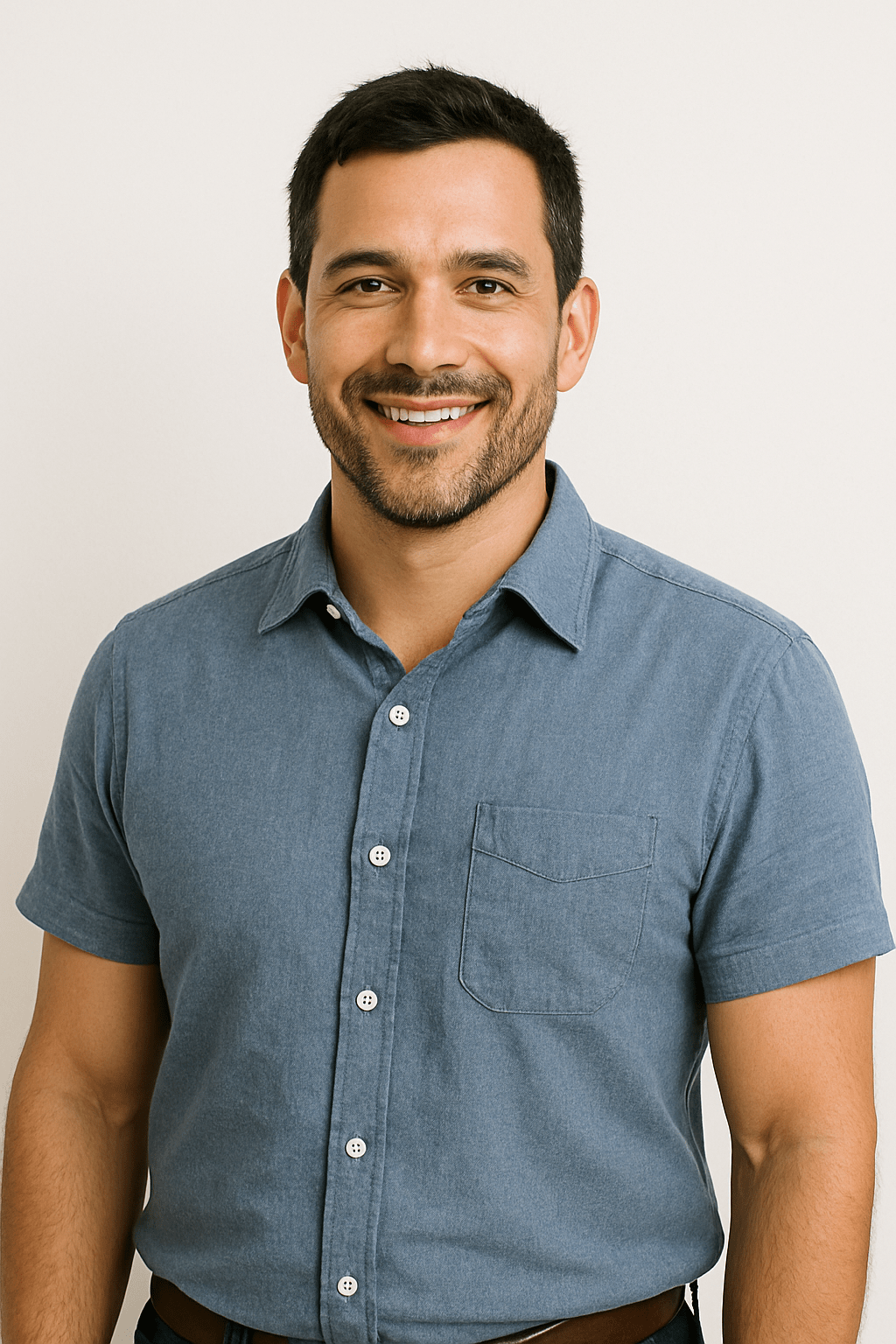
Carlos Sanchez is a senior technical specialist and field applications trainer with more than 17 years of experience in the use and optimization of industrial diamond tools, including ultra-thin diamond blades, core drills, and CBN grinding wheels. With a foundation in industrial engineering and technical operations, Mr. Sanchez has worked extensively with manufacturers and laboratories around the world, providing hands-on support and practical training for a wide range of cutting, grinding, and sample preparation applications.
Fluent in both English and Spanish, Carlos is known for his ability to translate complex tooling concepts into clear, actionable procedures for engineers, technicians, and production staff. His approach emphasizes real-world process improvement, tool longevity, and operator education—ensuring clients get the most out of their diamond tooling investments.
As an author, Mr. Sanchez shares field-tested insights on tool performance optimization, defect prevention, training methodologies, and troubleshooting common cutting issues.
ARE YOU USING RIGHT TOOLS
FOR YOUR APPLICATION?
LET US
HELP YOU
HAVING ISSUES WITH
YOUR CURRENT TOOLS?
Knowledge Center
How to Selecting Right Diamond Tools for your application
How to properly use Diamond Tools
Why use diamond
Diamond vs CBN (cubic boron nitride) Tools
What is Diamond Mesh Size and how to select best one for your application
What is Diamond Concentration and which to use for your application
Diamond Tool Coolants Why, How, When & Where to Use
Get to Know the Diamond Tool Bond Types and Which to use for your application
Get to Know the Diamond Tool Bond Types and Which to use for your application
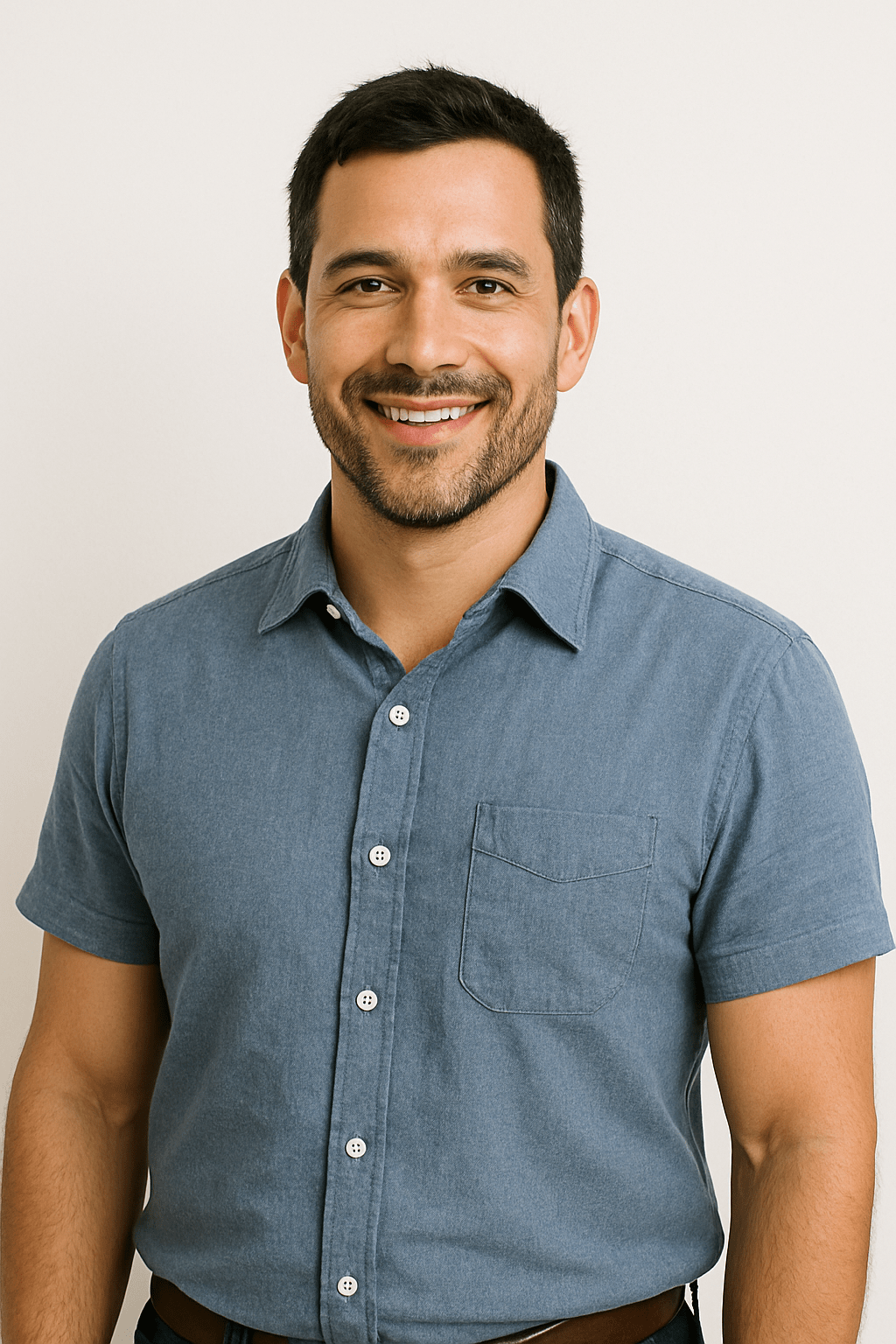
Carlos Sanchez is a senior technical specialist and field applications trainer with more than 17 years of experience in the use and optimization of industrial diamond tools, including ultra-thin diamond blades, core drills, and CBN grinding wheels. With a foundation in industrial engineering and technical operations, Mr. Sanchez has worked extensively with manufacturers and laboratories around the world, providing hands-on support and practical training for a wide range of cutting, grinding, and sample preparation applications.
Fluent in both English and Spanish, Carlos is known for his ability to translate complex tooling concepts into clear, actionable procedures for engineers, technicians, and production staff. His approach emphasizes real-world process improvement, tool longevity, and operator education—ensuring clients get the most out of their diamond tooling investments.
As an author, Mr. Sanchez shares field-tested insights on tool performance optimization, defect prevention, training methodologies, and troubleshooting common cutting issues.