Table of Contents
ToggleIn the world of manufacturing, precision and efficiency are paramount. Among the various processes that contribute to achieving these objectives in abrasive grinding operations, truing and dressing stand out as critical steps. These processes are fundamental to maintaining the performance, longevity, and accuracy of grinding wheels. Truing and dressing, while often mentioned together, serve distinct purposes and are essential for different reasons.
Share this Article with Friend or Colleague
Truing is the process of reshaping the grinding wheel to ensure it is concentric and uniform. This procedure not only corrects any geometric inaccuracies but also restores the true running conditions of the wheel, making it essential for precision machining. The primary goal of truing is to create a wheel that runs true with no vibration, which can otherwise lead to defects in the workpiece and reduce the life of the grinding machinery.
Dressing, on the other hand, involves removing the old abrasive grains from the surface of the grinding wheel, exposing new, sharp grains and clearing away clogged material. This rejuvenation of the wheel's surface is crucial for effective material removal, as it directly impacts the cutting efficiency and the quality of the finish on the workpiece. Dressing also helps in maintaining the wheel’s cutting ability and extends its lifespan by refreshing its surface.
Both truing and dressing are integral to the grinding process, each serving to enhance the wheel's performance in different ways. While truing ensures the wheel runs smoothly without any wobble, dressing sharpens the wheel and clears away debris that could interfere with grinding operations. Understanding these processes and the tools involved is essential for anyone involved in the machining and metalworking industries, as it directly impacts the quality of the products being manufactured.
This article will delve deeper into the tools and techniques used in truing and dressing, highlight the latest advancements in the field, and discuss how to choose the right tools for specific grinding tasks. Our goal is to equip practitioners and enthusiasts with the knowledge to optimize their grinding operations for better efficiency and precision.
Understanding Truing and Dressing
Truing and dressing, though often mentioned in tandem, perform distinct functions in the maintenance of abrasive grinding wheels, each tailored to enhance the wheel’s performance in different ways. Understanding the specific purposes and outcomes of truing and dressing is crucial for optimizing the precision and effectiveness of grinding operations.
Truing: Restoring Wheel Geometry
Truing is essential for restoring or creating the desired geometric shape of the grinding wheel. Whether a wheel is newly mounted or has deformed from previous use, it may not be perfectly round. Truing corrects these imperfections, removing material from the wheel’s surface to achieve a uniform diameter and an even surface. This process is vital for ensuring the wheel runs true with minimal vibration, thereby preventing the creation of out-of-round conditions on the workpiece and establishing a precise geometric form that directly impacts the shape of the finished product. Truing tools typically include diamond-tipped cutters or abrasive sticks, selected based on the wheel’s material and the complexity of the required profile.
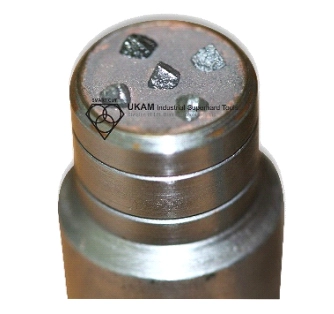
Dressing: Enhancing Wheel Surface Condition
Dressing focuses on refreshing the cutting surface of a grinding wheel. Over time, wheels can become glazed or loaded with particles that clog the cutting surface. Dressing removes these particles and exposes fresh abrasive grains, thereby optimizing the wheel’s cutting efficiency. This process is crucial for maintaining effective material removal and achieving a high-quality finish on the workpiece. Dressing tools range from single-point dressers for light cleaning to multi-point and rotary dressers designed for deeper cuts into the wheel’s surface, with each type suited to different wheel conditions and desired finishes.
Importance of Regular Maintenance
Regular maintenance through truing and dressing extends the life of grinding wheels and maintains the quality of grinding operations. Neglecting these processes can lead to diminished efficiency, increased operational costs due to frequent wheel replacements, and compromised quality of finishes and geometries on the workpiece. By integrating consistent truing and dressing routines, grinding wheels are kept in optimal condition, leading to more precise workpieces and efficient operations. This foundational understanding is critical as we explore the various tools used for truing and dressing, ensuring each grinding task is paired with the appropriate tool to maintain peak performance.
Comparison table that outlines the distinct functions, tools, and outcomes of truing and dressing processes in maintaining abrasive grinding wheels:
Aspect |
Truing |
Dressing |
---|---|---|
Purpose |
Restores or creates the desired geometric shape of the grinding wheel. |
Refreshes the cutting surface of the grinding wheel. |
Key Function |
Corrects imperfections and ensures the wheel runs true with minimal vibration, enhancing the wheel's geometric accuracy and preventing out-of-round conditions on the workpiece. |
Removes clogged particles and exposes fresh abrasive grains, optimizing the wheel’s cutting efficiency for effective material removal and achieving a high-quality finish on the workpiece. |
Tools Used |
Typically includes diamond-tipped cutters or abrasive sticks, chosen based on the wheel’s material and the complexity of the required profile. |
Ranges from single-point dressers for light cleaning to multi-point and rotary dressers designed for deeper cuts into the wheel’s surface, each suited to different wheel conditions and desired finishes. |
Outcome |
Establishes a precise geometric form on the wheel that directly impacts the shape of the finished product. |
Maintains effective material removal capabilities and surface finish quality. |
Importance of Maintenance |
Regular truing is essential to maintain the structural integrity and functional precision of the grinding wheel, preventing premature wear and ensuring the longevity of the wheel. |
Regular dressing is crucial for sustaining the wheel's efficiency in material removal and quality of finish, preventing the wheel from becoming inefficient due to clogging or glazing. |
Impact of Neglect |
Neglecting truing can lead to increased vibration, reduced accuracy in grinding operations, and potential damage to both the grinding wheel and the workpiece. |
Failing to regularly dress the wheels can result in diminished cutting efficiency, increased operational costs from more frequent wheel replacements, and compromised quality of finishes and geometries on the workpiece. |
Strategic Tool Selection for Truing and Dressing
Selecting the right truing and dressing tool is crucial for optimal grinding performance, requiring a thorough understanding of the grinding wheel’s specifications, the desired profile, and the quality of the diamond used in the tool. Here’s an expanded look at these key considerations:
Wheel Specifications
The characteristics of the diamond & cbn grinding wheel, including its size, bond type, and abrasive material, dictate the appropriate diamond tool size, typically measured in carats. Larger wheels demand larger diamonds due to their extensive surface area and the prolonged contact during dressing. The bond type of the wheel, such as vitrified, resin, or metal, influences how the dressing tool interacts with the wheel. For example, vitrified bonds are hard and brittle and may require diamonds with different properties compared to more wear-resistant metal bonds. Additionally, the type of abrasive material, like aluminum oxide, silicon carbide, or ceramic, determines the toughness required from the diamond, as harder materials necessitate diamonds that can endure greater levels of resistance and abrasion.
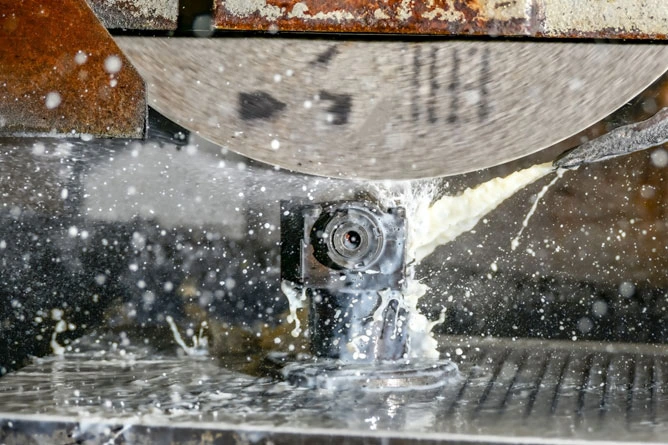
Required Profile
The choice of tool is also influenced by the specific form or profile required on the wheel. Simple profiles can be adequately managed with single-point diamond dressers or simple form dressers, which are versatile for general-purpose grinding and are easily adjustable. More intricate profiles necessitate the use of multi-point or impregnated dressers, as well as profile and blade dressers, which provide better precision and are suitable for creating specific geometric configurations on the grinding wheel. For highly specialized applications, custom-made tools with engineered points, such as cone or chisel tips, may be necessary. These tools are designed to achieve precise radii or angles on the grinding wheel, tailored to specific manufacturing requirements.
Diamond Quality
The longevity and effectiveness of a dressing tool significantly depend on the quality of the diamond. Higher quality diamonds typically have fewer inclusions and offer superior structural integrity, which makes them more durable and capable of maintaining sharpness over extended periods. The geometry of the diamond, including its size and the number of points, impacts its dressing capabilities. For instance, multi-point diamonds distribute wear more evenly, extending the tool's lifespan. The method by which diamonds are set in the tool, such as sintering, brazing, or electroplating, also affects the diamond's exposure and the tool's overall performance in material removal and surface finish.

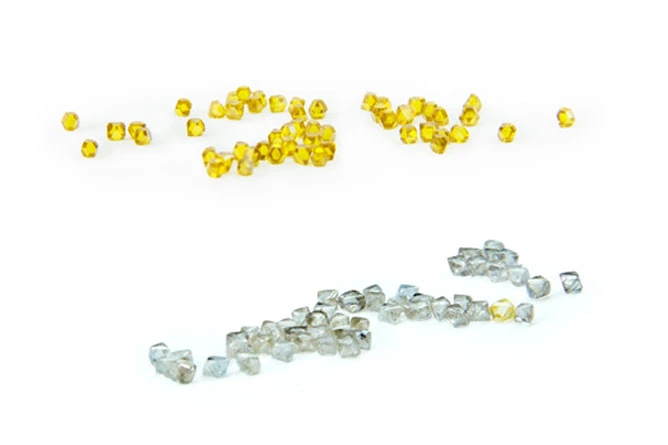
Tools for Different Needs in Truing and Dressing Applications
The selection of truing and dressing tools is driven by the specific needs of the grinding operation, with various tools optimized for different tasks. Each tool type is designed to cater to particular challenges presented by the grinding wheel's material, size, and desired finish.
Single Point Tools
Single point tools are the quintessential choice for achieving basic forms and are predominantly utilized in tool rooms. These tools are straightforward in their design and function, featuring a single diamond point that is used to dress the wheel. They are highly effective for simple, routine maintenance tasks on the grinding wheel, such as minor touch-ups and smoothing operations. The simplicity of single point tools makes them a popular choice for standard grinding operations, offering precision and ease of use with minimal setup.
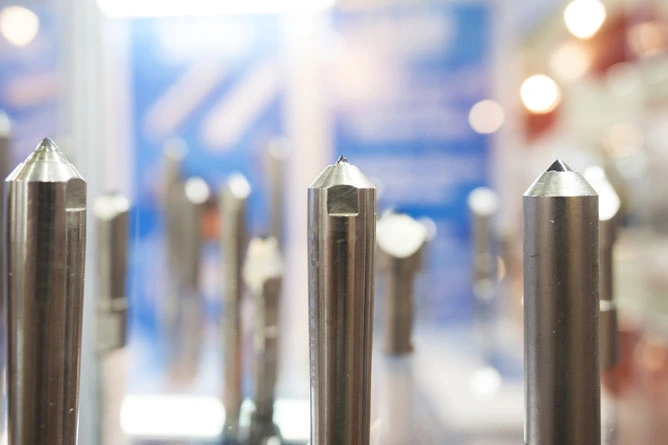
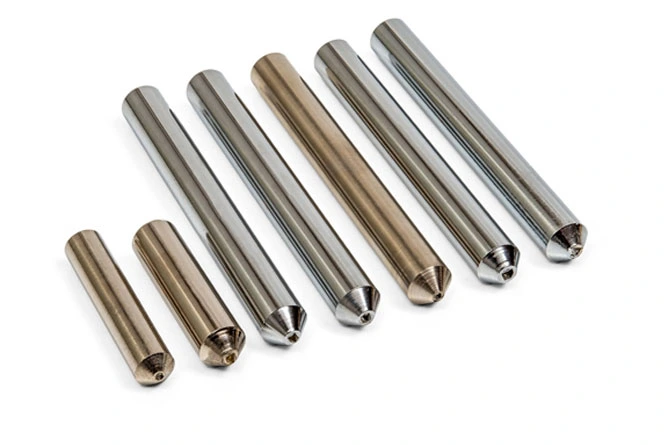
Cone and Chisel Point Tools
Cone and chisel point tools are engineered for more complex and precise applications, making them particularly suitable for CNC machine setups. These tools often require custom fabrication to meet specific grinding profiles. Cone points are typically used for intricate detail work on harder materials, whereas chisel points provide the precision needed for creating specific, complex forms on the grinding wheel. Their design allows for precision truing of the wheel, catering to detailed and precise grinding operations, especially those required in high-tech industries.
Cluster and Multi-Point Tools
Cluster and multi-point tools are designed for efficiency and speed, particularly useful for dressing large diameter wheels. These tools feature multiple diamond points embedded in a single tool body, allowing for faster dressing action as more surface area is covered in a single pass. This design is particularly beneficial for quickly refreshing the wheel and removing larger amounts of material, making them ideal for applications where frequent reconditioning of the wheel is necessary. Cluster tools are valuable in industrial settings where time and efficiency are critical, reducing downtime between dressing cycles.
Blade and Fliesen Tools
Blade and Fliesen tools are tailored for handling intricate profiles on large wheels. These tools offer a controlled, uniform contact area that makes them especially suitable for complex shapes and precise profile maintenance. Blade tools typically consist of a flat, thin diamond blade that provides a broad surface for truing, ideal for large wheels that require careful attention to detail. Fliesen tools, similarly, are used to achieve precise geometrical truing and are often utilized in applications demanding high precision, such as in the ceramic and glass industries.
Table of comparison for the various tools used in truing and dressing applications, highlighting their primary uses, design features, and typical applications:
Tool Type |
Primary Use |
Design Features |
Typical Applications |
---|---|---|---|
Single Point Tools |
Basic form achievement and routine maintenance |
Features a single diamond point for dressing the wheel |
Tool rooms, simple grinding operations |
Cone and Chisel Point Tools |
Complex and precise truing |
Engineered for detailed work; cone points for intricate details, chisel points for complex forms |
CNC setups, high-tech industries requiring detailed truing |
Cluster and Multi-Point Tools |
Efficient dressing of large diameter wheels |
Multiple diamond points embedded in a single tool body for covering more surface area in one pass |
Industrial settings where quick wheel refreshing is necessary |
Blade and Fliesen Tools |
Handling intricate profiles on large wheels |
Blade tools feature a flat, thin diamond blade; Fliesen tools are used for precise geometrical truing |
Applications demanding high precision such as in ceramic and glass industries |
Selecting the Right Tool
Choosing the appropriate truing and dressing tool is a pivotal decision in the grinding process that significantly impacts the efficiency, effectiveness, and outcome of the operations. The selection is driven by several critical factors, including the specific characteristics of the grinding wheel, the desired outcome for the workpiece, and the type of grinding machine in use. This section explores how these elements influence tool selection and offers guidance on matching tool capabilities with grinding requirements.
Assessing Wheel Specifications
The first step in selecting a truing or dressing tool is to thoroughly assess the specifications of the grinding wheel. Factors such as the wheel's size, bond type, and abrasive material are foundational in determining the suitable tool:
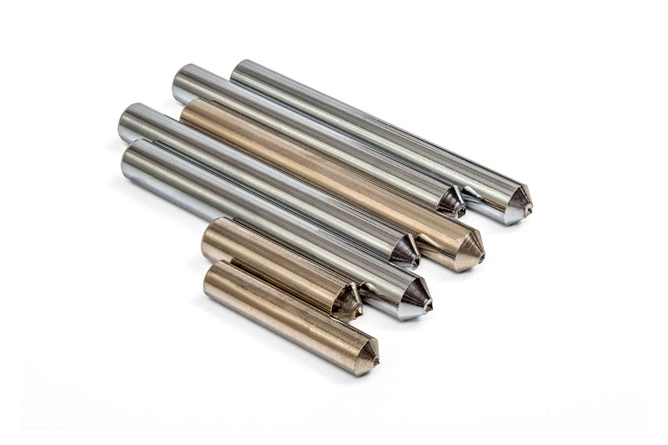
-
Size of the Wheel: Larger wheels require tools with larger, more robust diamonds or multiple diamond points to handle the increased surface area and the extended contact time during truing and dressing.
-
Bond Type: The bond of the grinding wheel (e.g., vitrified, resin, metal) dictates the hardness and wear resistance of the wheel, influencing the choice of the truing and dressing tool. Different tools are designed to interact optimally with different bond types to maintain the integrity of the wheel while achieving the desired modification.
-
Abrasive Material: The material of the abrasive grains (such as aluminum oxide, silicon carbide, or ceramic) determines the toughness and durability needed from the diamond in the truing or dressing tool. Harder abrasive materials require diamonds that can withstand more significant resistance and offer longer wear life.
Desired Outcome for the Workpiece
The intended finish and dimensional accuracy of the workpiece also play a crucial role in tool selection. Depending on whether the operation requires a high precision profile or a specific surface finish, the tool must be chosen accordingly:
-
Precision Truing: Operations that require high precision in the wheel's profile for intricate designs or critical dimensions need tools that offer fine control, such as single-point diamond dressers or precision-formed tools.
-
Surface Finish: If the priority is achieving a specific surface finish, tools designed to expose new grains or smooth the wheel's surface, such as multi-point dressers or rotary dressers, may be more appropriate.
Compatibility with Grinding Machine
The type of grinding machine—whether a simple bench grinder or a complex CNC machine—affects the choice of truing and dressing tool. Each machine type has different capabilities and limitations, which must be considered to select a tool that can operate effectively within those constraints:
-
Tool Room Grinders: For less complex machines, simple and versatile tools like single-point dressers are often sufficient.
-
CNC Machines: More sophisticated machinery may require equally sophisticated tools that offer greater precision and automation compatibility, such as CNC-specific dressers or advanced rotary tools.
Maintenance and Care of Truing and Dressing Tools
Proper maintenance and care of truing and dressing tools are critical for maximizing their lifespan and maintaining their effectiveness in grinding operations. Regular upkeep ensures consistent performance and prevents premature wear and potential damage to both the tools and the grinding wheels.
Routine Inspection and Cleaning
Regular inspection and cleaning are fundamental for keeping truing and dressing tools in optimal condition. After each use, it's advisable to remove debris and metal particles that may have accumulated on the tool using a soft brush or compressed air. This helps maintain the tool's effectiveness. Tools should be inspected for signs of wear or damage, such as chips or unusual wear patterns on the diamond points, before and after each use.
Proper Usage Techniques
Using truing and dressing tools according to their design specifications is essential to avoid undue stress and wear. Tools should be operated within the speed recommendations to prevent excessive heat buildup, which can lead to damage. Additionally, tools should be used strictly for their intended applications to avoid ineffective truing or dressing and to preserve their operational life.

Correct Installation and Alignment
Ensuring correct installation and alignment of truing and dressing tools can significantly impact their performance and longevity. Tools must be correctly aligned with the grinding wheel to prevent uneven wear and potential damage to both the tool and the wheel. Secure mounting is also critical; a tool that is not securely mounted may lead to inaccurate truing or dressing, increasing the risk of wheel damage.
Storage Conditions
The environment in which truing and dressing tools are stored can significantly affect their longevity and performance. Tools should be stored in a dry, clean environment to prevent corrosion and contamination from moisture and dust. It's also important to store tools in a way that prevents them from coming into contact with each other, as this can cause chips and other damages, particularly to the delicate diamond tips.
Handling and Transportation
Careful handling and transportation are vital to maintaining the integrity of truing and dressing tools. Tools should be handled carefully to avoid impacts or drops that could chip the diamond. When transporting tools, especially frequently or over distances, using protective cases is recommended to safeguard them.
Periodic Maintenance and Servicing
For tools designed for long-term use, periodic servicing is necessary to restore them to their original condition. Resharpening or relapping tools with multiple diamond points can expose new cutting surfaces, extending the tool’s useful life. For complex or expensive tools, professional assessment and servicing can ensure optimal performance and extend their operational life.
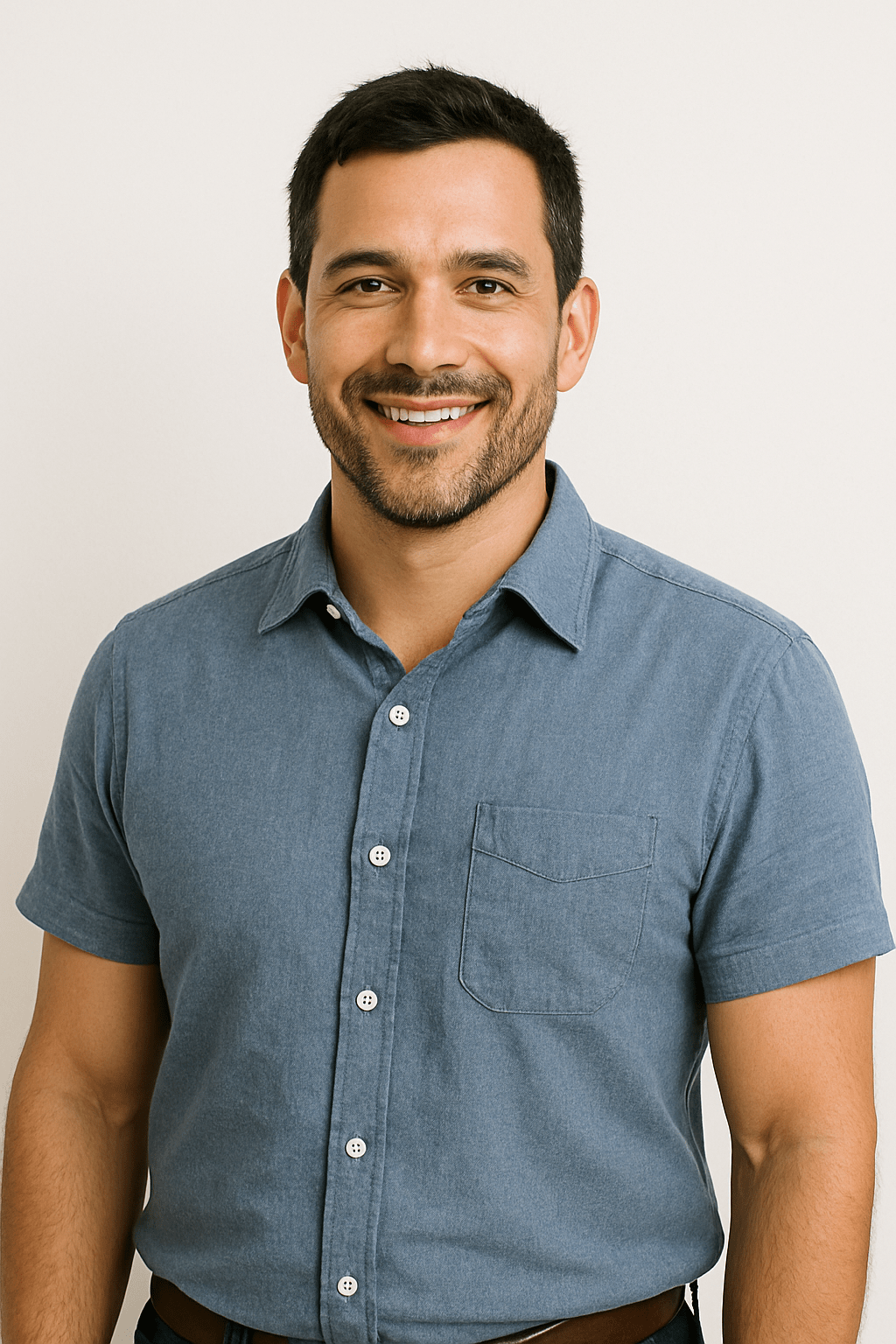
Carlos Sanchez is a senior technical specialist and field applications trainer with more than 17 years of experience in the use and optimization of industrial diamond tools, including ultra-thin diamond blades, core drills, and CBN grinding wheels. With a foundation in industrial engineering and technical operations, Mr. Sanchez has worked extensively with manufacturers and laboratories around the world, providing hands-on support and practical training for a wide range of cutting, grinding, and sample preparation applications.
Fluent in both English and Spanish, Carlos is known for his ability to translate complex tooling concepts into clear, actionable procedures for engineers, technicians, and production staff. His approach emphasizes real-world process improvement, tool longevity, and operator education—ensuring clients get the most out of their diamond tooling investments.
As an author, Mr. Sanchez shares field-tested insights on tool performance optimization, defect prevention, training methodologies, and troubleshooting common cutting issues.
ARE YOU USING RIGHT TOOLS
FOR YOUR APPLICATION?
LET US
HELP YOU
HAVING ISSUES WITH
YOUR CURRENT TOOLS?
Knowledge Center
How to Selecting Right Diamond Tools for your application
How to properly use Diamond Tools
Why use diamond
Diamond vs CBN (cubic boron nitride) Tools
What is Diamond Mesh Size and how to select best one for your application
What is Diamond Concentration and which to use for your application
Diamond Tool Coolants Why, How, When & Where to Use
Choosing The Correct Diamond Bond Type
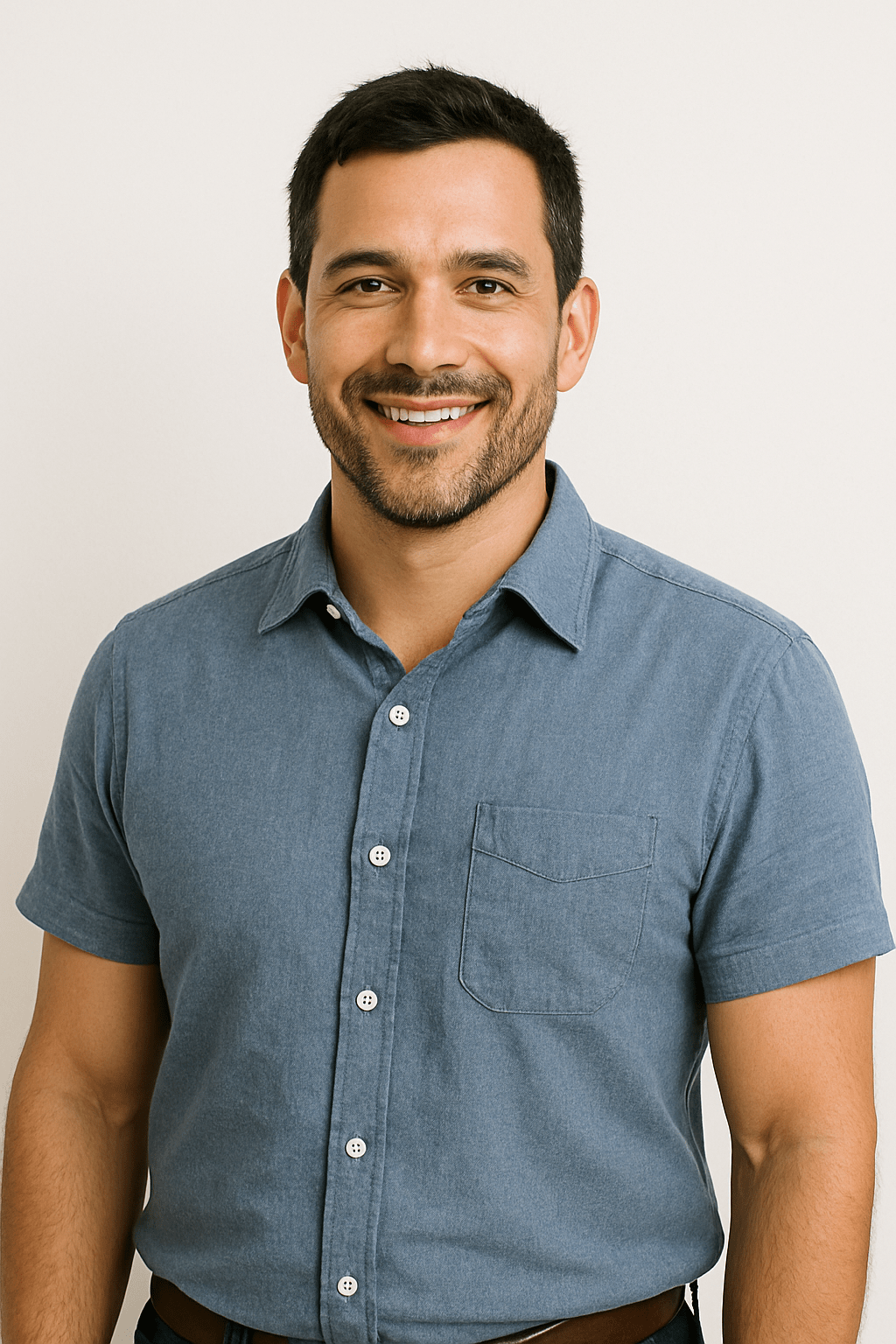
Carlos Sanchez is a senior technical specialist and field applications trainer with more than 17 years of experience in the use and optimization of industrial diamond tools, including ultra-thin diamond blades, core drills, and CBN grinding wheels. With a foundation in industrial engineering and technical operations, Mr. Sanchez has worked extensively with manufacturers and laboratories around the world, providing hands-on support and practical training for a wide range of cutting, grinding, and sample preparation applications.
Fluent in both English and Spanish, Carlos is known for his ability to translate complex tooling concepts into clear, actionable procedures for engineers, technicians, and production staff. His approach emphasizes real-world process improvement, tool longevity, and operator education—ensuring clients get the most out of their diamond tooling investments.
As an author, Mr. Sanchez shares field-tested insights on tool performance optimization, defect prevention, training methodologies, and troubleshooting common cutting issues.