-
0 items in quote
No products in the Quote Basket.
SMART CUT® Miniature Sintered Turbo Type Diamond Wheels Mounted on a Mandrel
SMART CUT® Miniature sintered turbo type diamond wheels mounted on a mandrel are used for cutting, engraving, and carving of large variety of materials. Available from 15mm to 85mm Diameter, with various kerf thicknesses, and shank/mandrel diameters.
DESCRIPTION
SPECIFICATIONS
ADVANTAGES
FAQ
INDUSTRIES USED IN
ACCESSORIES
USAGE RECOMMENDATION
DESCRIPTION
- Cutting: These wheels are designed to make precise cuts in hard materials such as granite, marble, and concrete. Their small size allows for detailed and intricate cutting, which is essential in custom fabrication of stone products.
- Engraving: They are used for engraving designs and patterns into stone surfaces. This is particularly useful in the monument and decorative stone industry, where intricate designs and lettering are required.
- Carving: These tools are also ideal for carving shapes and forms into stone. This can range from artistic sculptures to functional architectural elements like moldings and columns.
SPECIFICATIONS
- Application:designed for cutting, engraving and carving granite, marble, concrete, sandstone, and many other similar materials
- Bond Type: Sintered (Metal bond)
- Edge Type: Turbo Type
- Outside Diameter: 30mm to 60mm
- Kerf Thickness: 1mm to 2mm
- Shank Diameter: 6.4mm (1/4″)
- Equipment Used On: Rotary Hand Piece, Hand Held Drill, Drill Press, CNC Machine, Routers, & Others
ADVANTAGES
- Easy to Use: Due to their small size from 15mm to 85mm diameter, these wheels allow for very precise cuts, engravings, and carvings. This is crucial in applications requiring intricate detailing, such as in artistic stone carving or precision engineering.
- Long Life: Sintered diamond, known for its extreme hardness, ensures that these wheels are very durable. They can withstand the rigors of cutting hard materials like granite and marble without significant wear, leading to a longer lifespan.
- Turbo Type Design Provides Faster & Freer Cutting: Turbo type design provides efficient material removal rates. This allows for quicker processing of hard materials compared to non-diamond abrasive wheels.
- Universal Application: These wheels can be used on a variety of hard materials, including granite, marble, concrete, and sandstone. This versatility makes them valuable in diverse industries, from construction and masonry to artistic sculpture.
- Reduced Heat Generation: The design of turbo type wheels often allows for better heat dissipation. This is important in preventing heat damage to both the tool and the material being worked on.
- Improved Surface Finish: These wheels can achieve a smoother finish on the material surface, reducing the need for additional finishing processes.
- Compatibility with Different Equipment: Being mounted on a mandrel, they can be easily attached to various types of equipment, increasing their usability across different machines and setups.
- Affordable: Although the initial investment might be higher compared to standard abrasive wheels, the long-term durability and efficiency of diamond wheels can lead to lower costs over time due to less frequent replacement needs and faster working speeds.
FAQ
These are specialized tools used for precise cutting, engraving, and carving on hard materials like granite, marble, and concrete. They consist of diamond wheels mounted on a mandrel, available in diameters from 15mm to 85mm, with varying kerf thicknesses and shank diameters.
- Cutting: Ideal for making precise cuts in hard materials, particularly useful in custom fabrication of stone products.
- Engraving: Used for engraving designs and patterns on stone surfaces, especially in the monument and decorative stone industry.
- Carving: Suitable for artistic sculptures and functional architectural elements like moldings and columns.
- Outside Diameters: 15mm, 25mm, 30mm, 40mm, 50mm, 60mm, 70mm, 85mm.
- Shank Diameter: 6.4mm (1/4″). Other specifications are available upon request.
- Easy to Use: Ideal for precise cuts, engravings, and carvings.
- Long Life: Made of durable sintered diamond.
- Efficient Cutting: Turbo type design for faster and freer cutting.
- Universal Application: Versatile for various hard materials.
- Reduced Heat Generation: Better heat dissipation.
- Improved Surface Finish: Achieves a smoother finish.
- Compatibility: Easily attachable to different equipment.
- Affordable: Long-term cost-effectiveness due to durability and efficiency.
- Application: Designed for cutting, engraving, and carving hard materials.
- Bond Type: Sintered (Metal bond).
- Edge Type: Turbo Type.
- Outside Diameter: 30mm to 60mm.
- Kerf Thickness: 1mm to 2mm.
- Shank Diameter: 6.4mm (1/4″).
- Equipment Used On: Rotary Hand Piece, Hand Held Drill, Drill Press, CNC Machine, Routers, & others.
They are ideal for industries like construction, masonry, and artistic sculpture. They can be attached to rotary hand pieces, drills, CNC machines, and more.
The Turbo Type design allows for faster material removal rates, which leads to quicker processing and efficiency when working with hard materials.
Yes, their small size and precise design make them perfect for detailed and intricate work, such as in artistic stone carving or precision engineering tasks.
SMART CUT Diamond Wheels offer several advantages over non-diamond abrasive wheels:
- Durability: Diamond is one of the hardest materials, making these wheels more durable and resistant to wear.
- Precision: They provide more precise cuts, essential for detailed work.
- Efficiency: Faster cutting speeds and better material removal rates.
- Surface Finish: They achieve a smoother finish, often reducing the need for additional finishing.
While primarily designed for hard materials like granite, marble, concrete, and sandstone, they may be suitable for other materials. However, it’s essential to check the compatibility of the material with the wheel specifications.
Yes, the wheels are designed for easy installation and replacement. They can be quickly mounted on or detached from the mandrel, fitting various types of equipment.
Safety is crucial when using these wheels. Always wear protective gear, including eye protection, gloves, and a dust mask. Ensure that the tool is securely mounted and operated within the recommended speed limits.
The lifespan varies depending on usage, material hardness, and frequency of use. However, due to their sintered diamond construction, they generally last longer than standard abrasive wheels.
Yes, using water or coolants can help reduce dust and heat buildup, which is especially beneficial when working with heat-sensitive materials.
The shank diameter (6.4mm or 1/4″) is a common size that fits many types of equipment, making these wheels versatile for different setups.
While specialized training is not always required, a basic understanding of the equipment and safety procedures is essential. Users with experience in handling similar cutting, engraving, or carving tools will find it easier to adapt.
The variety of kerf thicknesses available allows users to select the appropriate wheel for their specific cutting needs, whether they require a fine, precise cut or a wider groove for more substantial material removal.
While extremely versatile, the effectiveness of these wheels can vary depending on the material hardness and the complexity of the cut. Extremely intricate designs may require additional tools or specialized wheels.
Yes, these wheels are typically suitable for both wet and dry cutting. Wet cutting is preferable for reducing dust and extending the wheel’s life.
The turbo type edge design enhances the cutting efficiency by providing a better balance between speed and precision, which is particularly useful for tough materials like granite and concrete.
The sintered (metal bond) type holds the diamond particles strongly, providing a balance between wear rate and sharpness. This bond type is known for its durability and longevity, especially when cutting harder materials.
Choosing the right wheel depends on the material being worked on and the desired outcome. Larger diameters and thicker kerfs are typically used for more significant, less detailed work, while smaller diameters and thinner kerfs are for finer, more detailed work.
The choice of shank diameter (6.4mm or 1/4″ in this case) should match the collet size of the equipment being used. A correct match ensures stable and safe operation, as well as optimal performance of the wheel.
Typically, diamond wheels come in various grit sizes, catering to different levels of finish and material removal rates. The choice of grit size will depend on the specific application and desired outcome.
It’s crucial to follow the manufacturer’s guidelines for optimal speed settings. Using the wheel at a correct speed ensures safety, efficiency, and prolongs the life of the wheel.
Yes, these wheels are compatible with CNC machines, provided they fit the machine’s specifications, particularly the shank diameter.
A thinner kerf typically allows for more precise cuts but may reduce cutting speed and be less suitable for thicker materials. A thicker kerf increases material removal rate but might reduce precision.
Balancing speed and finish quality involves selecting the right wheel type and grit size, adjusting the cutting speed, and sometimes using a combination of rough and fine wheels for initial cutting and finishing.
To extend their life, use the wheels within recommended speed and pressure limits, avoid overheating, use appropriate coolants, and store them correctly when not in use.
Water is the most common coolant, but other coolants designed for stone or hard material cutting can also be used. The choice of coolant may depend on the material being cut and the specific requirements of the process.
Customization of the wheel specifications is possible, there may be a small minimum order quantity Special orders can typically be made for specific diameters, kerf thicknesses, and bond types.
Wheel wear can affect the precision and efficiency of the cuts. Signs of significant wear or damage indicate it’s time to replace the wheel. Regular inspections are recommended to assess wear.
While primarily designed for use with powered equipment, in some cases, they can be used manually. However, this requires great care and might not provide the same level of precision or efficiency.
The hardness and abrasiveness of the material dictate the choice of wheel. Harder materials require wheels with stronger bonds and possibly coarser grit, while softer materials can be cut with finer grit wheels.
First-time users should start with basic projects, follow all safety guidelines, and familiarize themselves with the tool’s operation and handling. Practicing on scrap material before moving on to actual projects is also advisable.
Under continuous use, these wheels maintain performance but may require more frequent checks for heat buildup and wear. Adequate cooling and proper operating speeds are important in such conditions.
Common mistakes include using the wrong wheel type for the material, operating at incorrect speeds, applying excessive pressure, and neglecting safety precautions.
The skill level can significantly impact the precision and quality of the work. Experienced users can achieve better results and are more adept at handling complex tasks.
These wheels are widely used in industries like masonry, construction, and sculpting. Beginners should be aware of the specific demands and standards of these industries to ensure appropriate use of the wheels.
The angle at which the wheel contacts the material can significantly affect the quality of the cut. The correct angle ensures efficient cutting and minimizes the risk of chipping or damage to the material or the wheel.
While primarily designed for cutting and shaping, with the right specifications (like grit size and wheel type), they can be used for both roughing and finishing works. However, finer finishes might require additional tools or processes.
Generally, compatibility is determined by the shank diameter and the equipment’s collet size. As long as these match, there should be no brand-specific compatibility issues.
Larger diameters generally allow for cutting larger areas or deeper cuts, while smaller diameters are better for detailed or intricate work. The choice of diameter should match the scale and detail of the project.
The procedure involves safely removing the worn-out wheel from the mandrel and replacing it with a new one, ensuring it’s securely fastened. Always follow the equipment’s manual for specific instructions.
Quality diamond wheels typically produce less noise and vibration compared to conventional abrasive wheels. However, this can also depend on the equipment used and the material being worked on.
The right pressure depends on the material’s hardness and the wheel’s specifications. Generally, it’s advisable to start with lighter pressure and increase as needed, avoiding excessive force that can damage the wheel or the material.
Operating speed can greatly influence the cutting efficiency and the lifespan of the wheel. Using the manufacturer-recommended speed ensures optimal performance and safety.
The thickness of the wheel determines the maximum depth of cut that can be achieved. Thicker wheels can make deeper cuts and can be used for grinding, but they might reduce the level of detail and precision.
To prevent overheating, users should use appropriate coolants, take regular breaks during prolonged use, and avoid excessive pressure and speed that can generate excessive heat.
This can be done by cutting into a dressing stone several times to wear away metal layer to expose the diamond and sharpen the diamond crystals
The wheel’s speed rating should always match or exceed the maximum RPM of the equipment it’s used on. Using a wheel at speeds higher than its rating can be dangerous and lead to wheel failure.
These wheels are primarily designed for hard, non-metallic materials like granite and marble. Cutting metals requires different types of diamond wheels specifically designed for metalworking.
Dispose of worn-out diamond wheels according to local regulations and guidelines. They should not be thrown in regular waste due to the metal and diamond content.
A common misconception is that diamond wheels can cut any material. While they are extremely hard and versatile, they are primarily designed for specific types of materials and applications.
Sintered bond, involving the fusion of diamond particles with a metal matrix, provides a strong bond that holds up well against the rigors of cutting hard materials. This results in a longer-lasting wheel compared to other bonds like resin or electroplated bonds, especially under heavy use.
Uneven wear can indicate issues with the equipment or improper use. Users should check the equipment’s alignment and ensure that the wheel is being used at the correct angle and pressure. If the issue persists, consulting a professional is advisable.
Yes, these wheels can be used at different angles to achieve various cutting depths and profiles. However, users must ensure that the wheel and the equipment can safely handle the desired angle.
The diameter of the wheel influences the types of equipment it can be used with. Larger diameters are typically used with more powerful equipment, while smaller diameters are suited for handheld or precision tools.
These wheels are particularly advantageous in industries where precision cutting of hard materials is crucial, such as in stone masonry, monument building, sculpture, and in certain types of construction and renovation work.
Extreme temperatures can affect the metal bond and the overall integrity of the wheel. It’s advisable to use these wheels within a moderate temperature range and avoid exposing them to extreme heat or cold.
- Frequent use, especially under heavy load or on very hard materials, can shorten the wheel’s lifespan. Proper maintenance and using the wheel within its specified limits can help maximize its lifespan.
INDUSTRIES USED IN
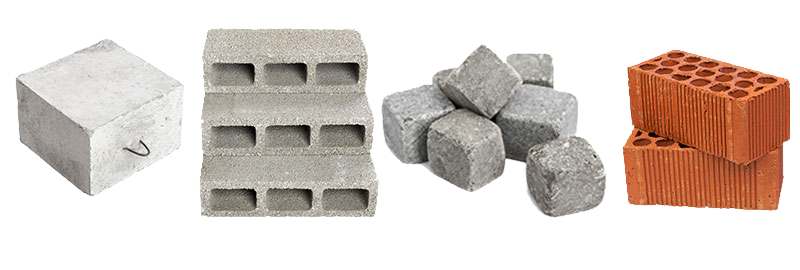
Concrete & Construction
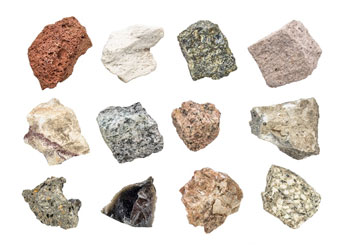
Natural Stone
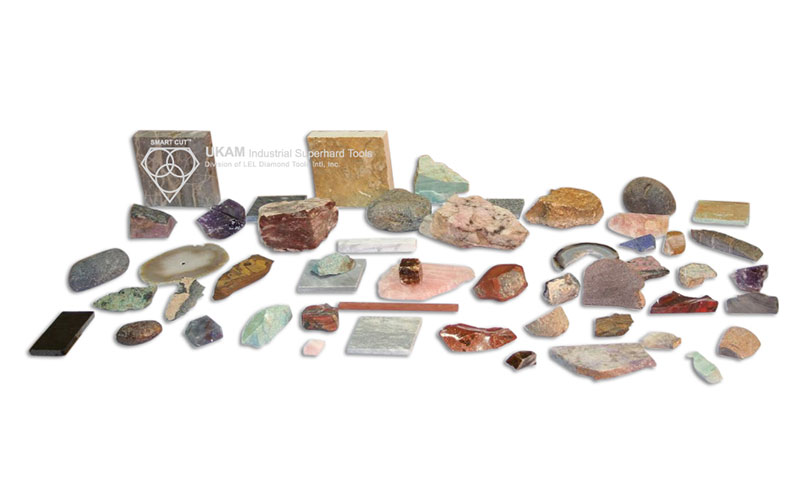
Lapidary
ACCESSORIES
Tab Contant
USAGE RECOMMENDATION
Tab Contant
Outside Diameters Available: | Shank Diameter |
15mm, 25mm, 30mm, 40mm, 50mm, 60mm, 70mm, 85mm | 6.4mm (1/4″) |
*other specifications are available upon request
About Sintered (Metal Bond)
Sintered (Metal Bond) diamond tools have multiple layers of diamonds impregnated inside the metal matrix. Diamonds are furnaces sintered in a matrix made of iron, cobalt, nickel, bronze, copper, tungsten, alloys of these powders or other metals in various combinations. Metal bonded diamond tools are “impregnated” with diamonds. This means that selected diamonds are mixed and sintered with specific metal alloys to achieve the best cutting performance possible on any materials such as sapphire, advanced ceramics, optics, glass, granite, tile and etc. The metal bond surrounding the diamonds must wear away to continuously keep re-exposing the diamonds for the diamond tool to continue cutting. Sintered (metal bonded) diamond tools are recommended for machining hard materials from 45 to 75 on rockwell scale (5 to 9.5 on mohe’s scale of hardness).
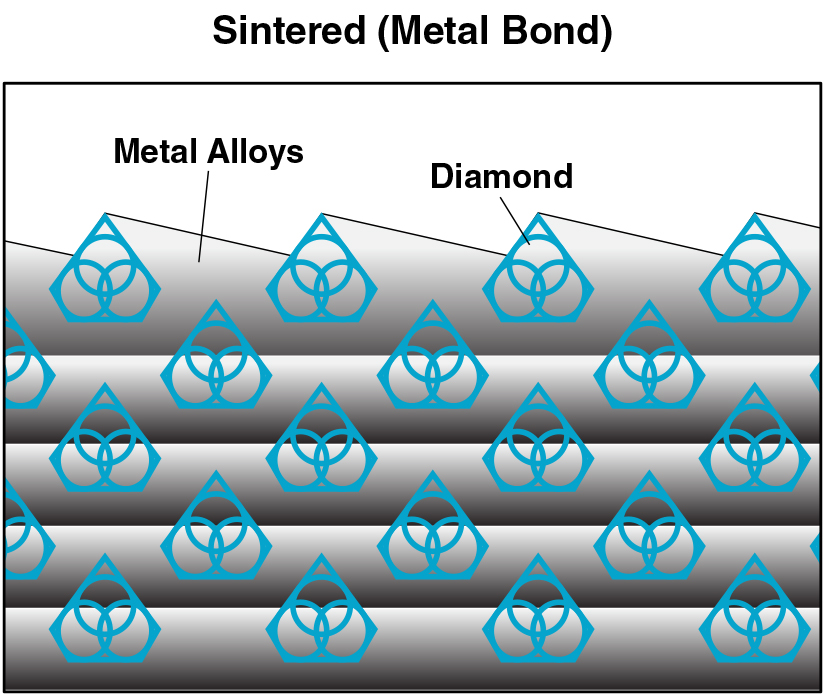
How SMART CUT ® Bond Works?
Step 1
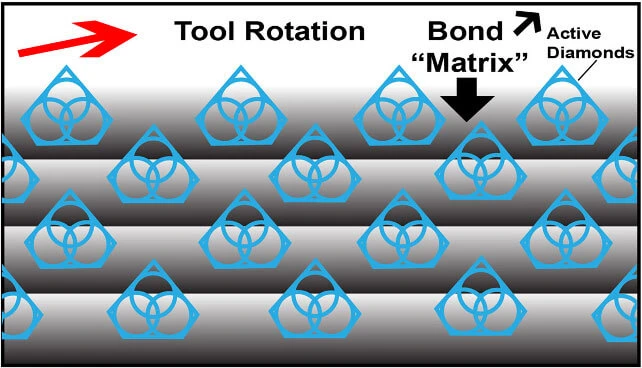
Diamonds or CBN Crystals
Diamonds or CBN Crystals are activated only at the exposed layer. As Bond Matrix layer begin to wear out, diamonds in a new Bond Matrix layer are immediately activated, substituting the already used up diamond layer. The SMART CUT® Diamond Hybrid Bond makes sure every diamond is in the right place and at the right time, working where you need it most.
Step 2
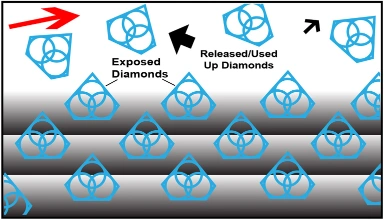
Sharpest And Finest Quality Diamonds
The newly exposed diamonds don’t effect diamonds already working on the material. Unlike many other diamond bonds, diamonds in a SMART CUT® Bond remains sharp and grow sharper with each cut, prolonging product life and consistent performance.
Step 3
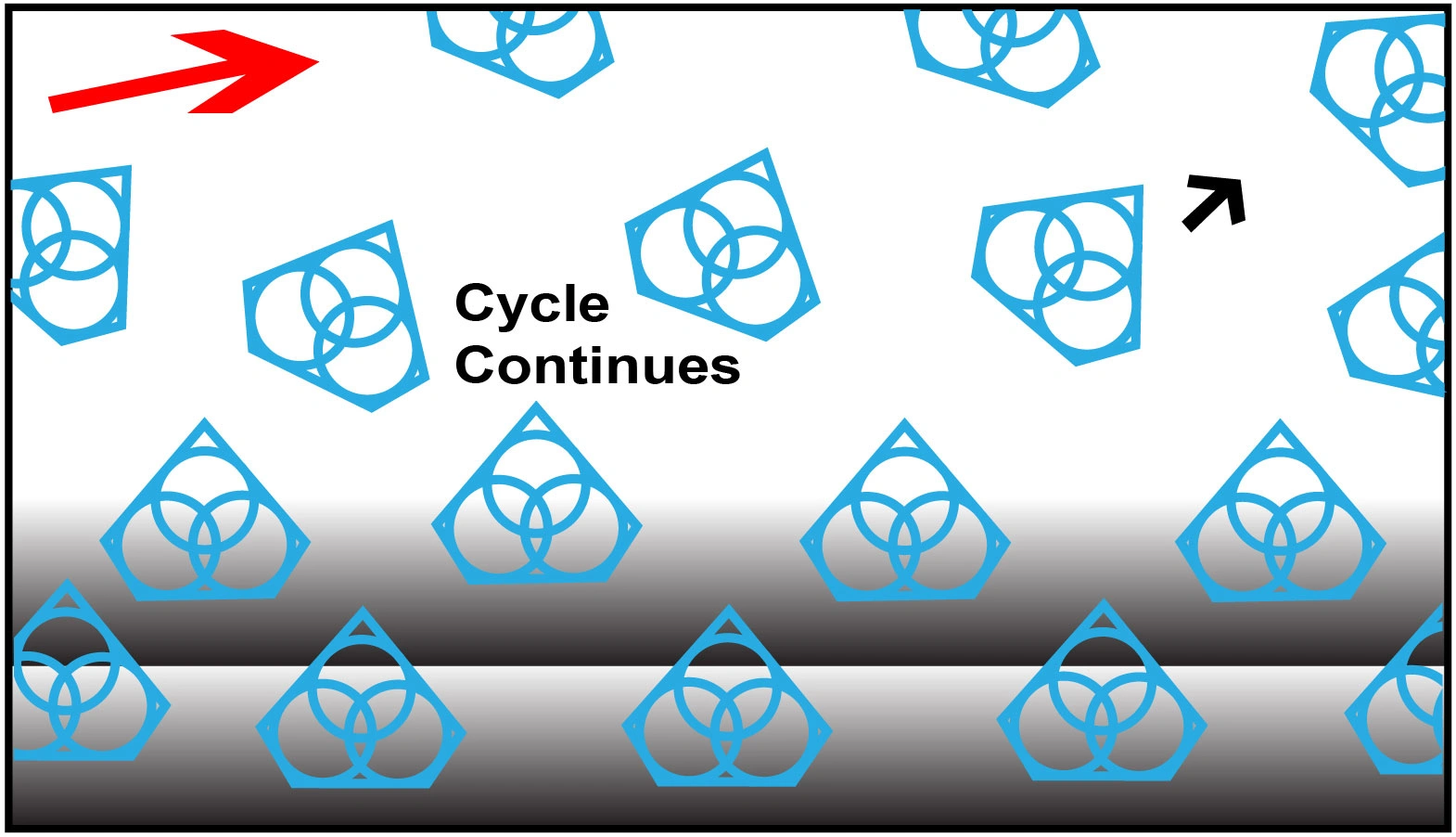
Advanced Formulated Open Diamond Bond Design
This advanced formulated open diamond bond design insures minimal chipping, fast cut, constant speed of cut, minimal cutting noise, and most important of all, consistent performance.
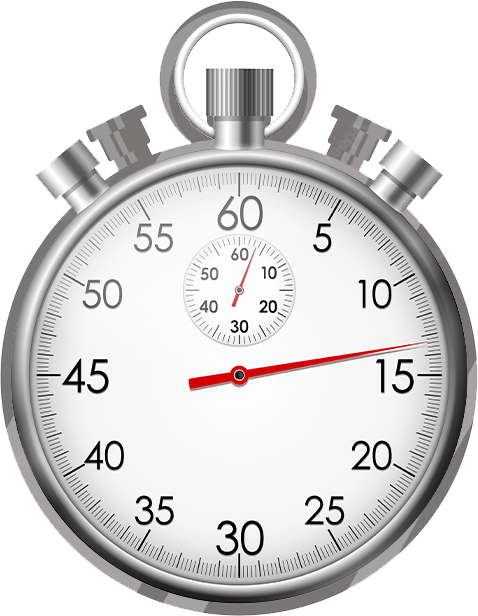
Faster & Freer Action
Diamond drills made utilizing SMART CUT technology are much more aggressive than your conventional drills. They can drill faster, while still leaving behind a smooth finish free of material deformation.
Longer Life
In most cases tools manufactured utilizing SMART CUT technology, will outlast other conventional Diamond Core Bits SMART CUT diamond & CBN tools are more sturdy than tools manufactured with conventional technologies. They are capable to retain their form and bond configuration all the way through the tools life.
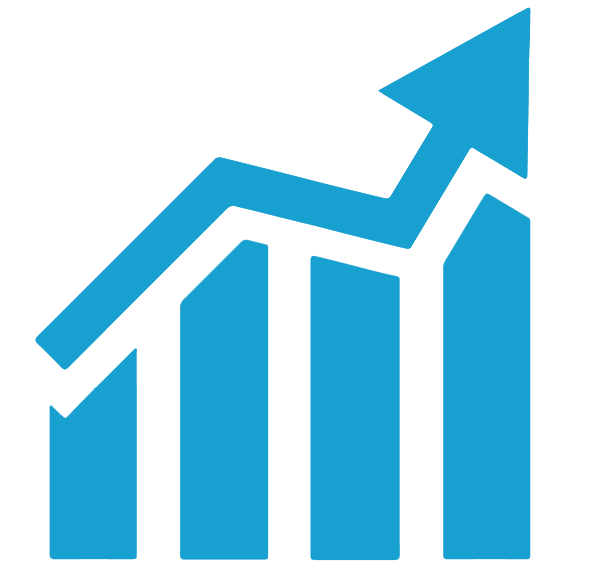
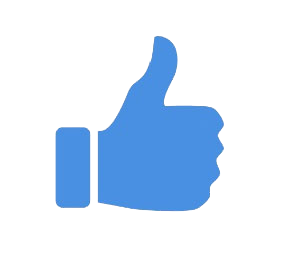
More Consistent Performance
SMART CUT Diamond Core Bits are produced using advanced technology Unlike Many Other Core Bits they wear evenly, and are known for their consistency. You will get consistent cutting speed, and overall consistent performance, with minimum amount of dressing even on the hardest to cut materials
Manufactured Using The Highest Quality Raw Materials
Only the highest quality synthetic diamonds and raw materials are used in the manufacturing process. The highest quality standards and product consistency is maintained, using sophisticated inspection and measurement equipment.
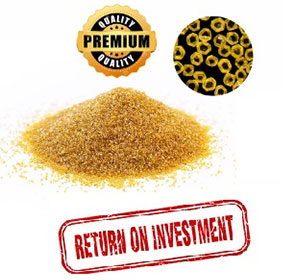

Best Performance & Value on the Market
SMART CUT® Dry Diamond Core Bits are the best investment you can make! Although they may cost more than Dry Diamond Core Bits They will more than pay for themselves in terms of overall performance and provide best Return on Investment.
Diamond Miniature Blade / Wheel
Selection Variables
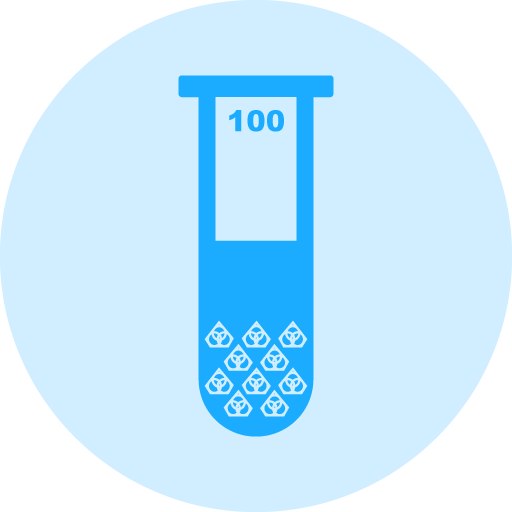
Diamond Concentration :
Diamond Concentration is still a factor in determining the life and cutting speed of your Diamond Blade. Higher diamond concentration is recommended and usually used for cutting softer and more abrasive types of materials. However, the trade off is significantly slower cutting speed. Low diamond concentration is recommended and widely used for cutting ultra hard and brittle materials.
Low Diamond Concentration - Typically low concentration wafering blades should be for cutting ultra hard and brittle materials such as ceramics and glass. In Low Concentration Wafering Blades, diamond works by fracture process. Pressure on each diamond crystal/particle is higher which provides enough stress to chip off small flakes in the cut.
High Diamond Concentration - High concentration diamond wafering blades are recommended for cutting metals, plastics and polymers. In this application, materials cut by a plowing mechanism. In this applications diamond plough through the material, work hardened strips of materials become brittle and break off. The greater number of diamond by volume, the quicker the cutting action will be. Increasing the number of diamond s also lowers the per unit force. For metals where it is possible to induce deep deformation layers, a lower per unit force is desirable to reduce the deformation during the cut.
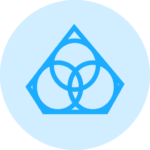
Diamond Particle/Grit size -
Diamond Mesh Size plays a major role in determining your cutting speed, cut quality/surface finish, level of chipping you will obtain, and material microstructure damage you will obtain. Diamond Mesh size does have considerable effect on cutting speed. Coarse Diamonds are larger than finer diamonds and will cut faster. However, the tradeoff is increase in material micro damage. If you are cutting fragile, more delicate materials then finer mesh size diamond wafering blades are recommended.
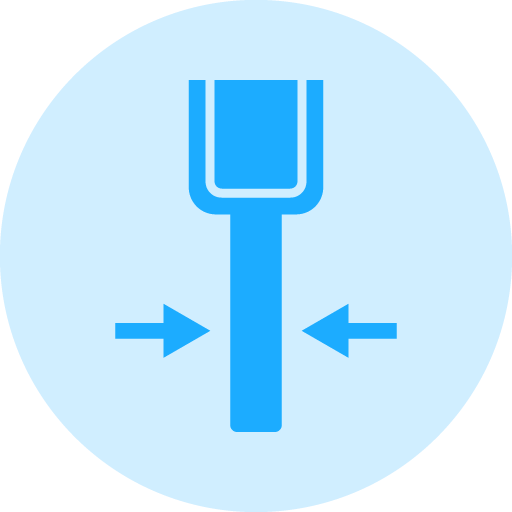
Blade Thickness :
Diamond blade thickness typically ranges from .006” to .040” (1mm). Thinner and thicker Diamond & CBN Blades are available, frequently from stock upon request. Kef thickness typically increases with blade diameter (in proportion to diameter of the blade). Kerf is the amount of material removed from the material/sample due to the thickness of blade passing though the material/sample. Blade thickness is important for users requiring most minimal amount of material loss during sectioning. For example if the user requires precision position of the cutting plane relative to the detail on the sample (IC circuit for example), a thinner and smaller diameter blade would be best for this application. Blades ranging from 3” to 5” (75mm to 125mm) in diameter and thickness .006” to .015” (0.2mm to 0.4mm) would be bet suited for this purpose. There are large variety of factors that will contribute to optimal blade thickness for your material/application Including your desired cutting speed, load/feed rate, material diameter, thickness, hardness, density, and shape. As well as skill & experience of the operator. Thicker wafering blades are more stiff and can whistand higher loads/feed rates. Another advantage of thicker kerf blades is they are more forgiving to operator error and abuse. Thicker kerf blade are recommended for use in environment where large number of individuals will be sharing and using same equipment. Perfect for less experienced and novice saw operators, such as in University laboratory.
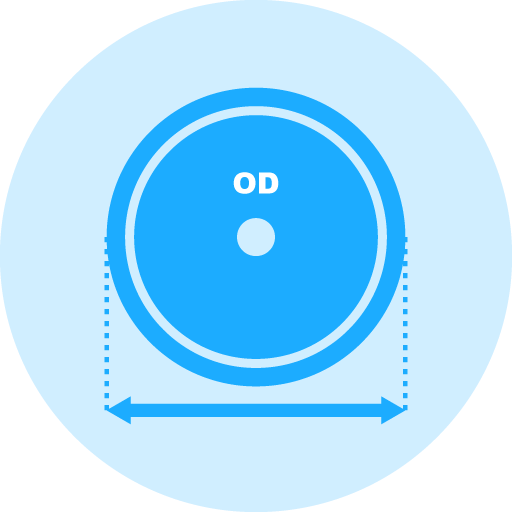
Blade Outside Diameter :
Typically blade diameters range form 1” (25.4mm) to 3” (75mm). Blade diameter should be selected based on material diameter and thickness being cut. Smaller diameter wafering blades are thinner than the larger diameter blades and are more prone to bending and warping. Although large diameter blades are thicker, they are typically used for cutting larger and heavier samples at higher loads and speeds than smaller blades.
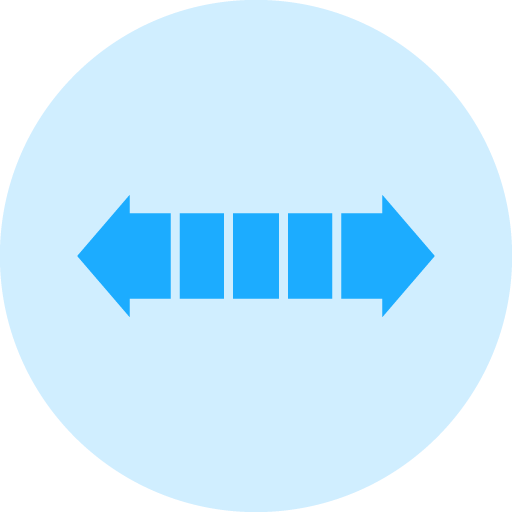
Bond Hardness :
Ability of the bond matrix to hold diamonds. As the hardness of the bond is increased, its diamond retention capabilities increase as well. However the trade off is slower cutting speed. Life of the diamond blade is usually increased with hardness of its bond matrix. Bonds are designated on their scale of hardness from Soft, Medium, and Hard. There are dozens of variations and classification schemes based on bond degree of hardness or softness. Using diamond blades with optimum bond hardness for your application is important to successful precision diamond sawing operation. Bond matrix that is too soft for the material being cut will release diamond particles faster than needed, resulting in faster wear and shorter diamond blade life. On other hand bond matrix that is too hard will result in much slower cutting speeds and require constant dressing to expose the next diamond layer. As rule of thumb, harder materials such as sapphire and alumina generally require a softer bond. Whereas softer and more brittle materials require a harder bond.
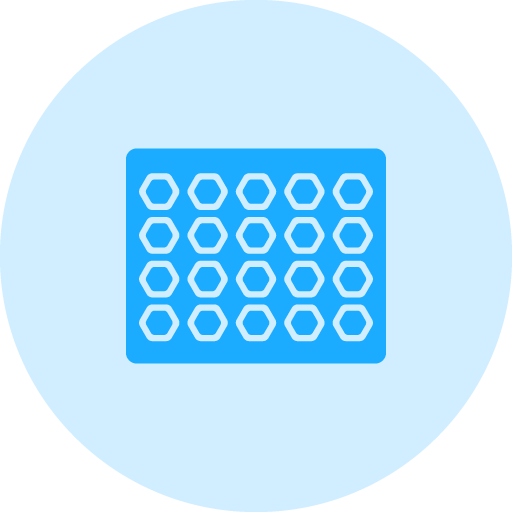
Bond Type :
Metal bonding offers long life and durability, while resin bonding creates less heat, provides better surface finish and is well suited for cutting hard, delicate or brittle materials.
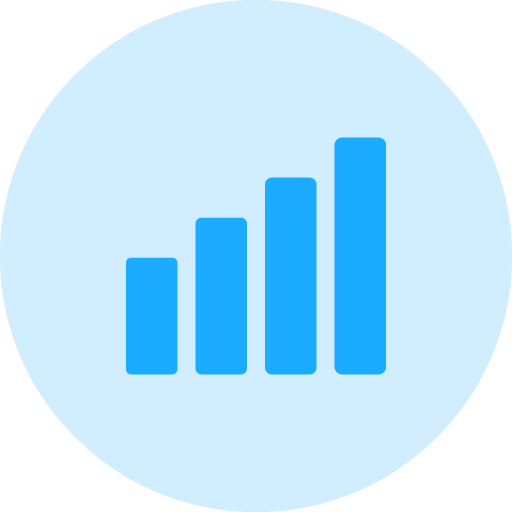
Feed Rates :
Load/Feed Rate applied to blades typically vary from 10-1000 grams. Generally, harder specimens are cut at higher loads and speeds (e.g. ceramics and minerals) and more brittle specimens are cut at lower loads and speeds (e.g. electronic silicon substrates). The Speeds/RPM’s you are using, shape/geometry of the specimen, and how the specimen is being clamped/hold in place will affect the load that can be used for your application.
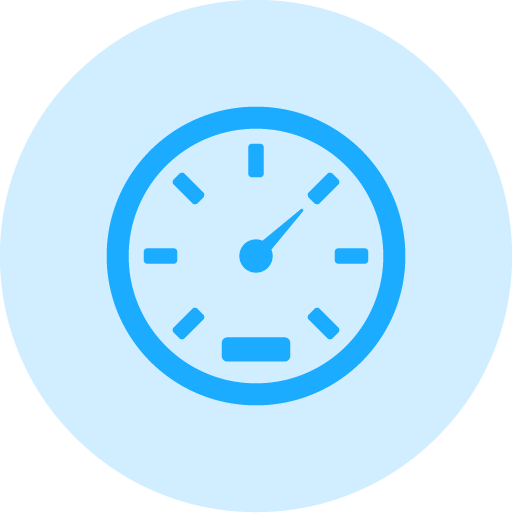
Blade Speeds/RPM’s :
Most blades are used between 10,000 to 35,000 RPM’s Typically harder and more denser materials such as Silicon Carbide, are cut at higher RPM’s/speeds Where more brittle materials such as silicon wafers and gallium arsenide are cutting at lower RPM’s. These minature diamond & cbn blades are used on high speed machines such as Dremel, Foredom, Proxxon, High Speed Grinders and Spidles. These have many different speed setting to select best one for your particular application.
Why Choose SMART CUT® Miniature Diamond & CBN Wheels / Blades
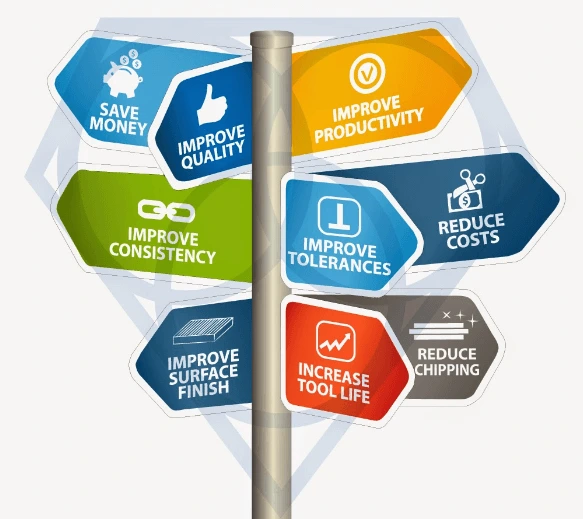
- Unmatched Selection For Many Applications
- Unmatched Technical Support & Expertise
- Superior Quality & Consistency
- Super Technology & innovation
- Immediate Worldwide Delivery
- American Based Manufacturer
-
Custom
Manufacturing - Better Value manufacturer Direct Price
Related Products
Miniature Diamond Cut Off Blades, Electroplated (Nickel Bond)
Used on Dremel, Fordedom Hand Pieces, Die Grinders, and other cutting machines. Use for cutting, slotting, and grooving of large spectrum of materials. Ranging from ultra hard & brittle materials (such as Al203, sapphire, etc), Ultra Hard Metals, Glass, Composites. Hundreds of Sintered (metal bond), Miniature Diamond Cut Off Blades are available in stock in all diameters, thicknesses, inside diameters, specifications (grit sizes, concentrations, shapes, radiuses, etc).
MINIATURE DIAMOND CUT OFF BLADES, SINTERED (METAL BOND)
Used on Dremel, Fordedom Hand Pieces, Die Grinders, and other cutting machines. Use for cutting, slotting, and grooving of large spectrum of materials. Ranging from ultra hard & brittle materials (such as Al203, sapphire, etc), Ultra Hard Metals, Glass, Composites. Hundreds of Sintered (metal bond), Miniature Diamond Cut Off Blades are available in stock in all diameters, thicknesses, inside diameters, specifications (grit sizes, concentrations, shapes, radiuses, etc).
Diamond Slitting Wheels (Plated)
Recently Viewed Products
ARE YOU USING RIGHT DIAMOND & CBN BLADES
FOR YOUR APPLICATION?
LET US
HELP YOU
HAVING ISSUES WITH
YOUR CURRENT DIAMOND & CBN BLADES?
Knowledge Center
02
Jun
How to Properly Use Precision Diamond & CBN Blades
The diamond blade itself is only a small factor in your cutting operation. Successful diamond sawing is both an art & science. Requiring proper use and understanding of the right: RPM's, Coolants, Equipment, Dressing Devices, Accessories...
02
Jun
Precision & Ultra Thin Diamond Blade Guide
Diamond and CBN blades are available in an extensive array of varieties, each differing in bond types, manufacturing methods, and design specifics. Ultra Thin & High Precision Diamond Blades are particularly versatile, applicable...
02
Jun
How to Improve & Optimize Your Diamond Sawing Operation
There are numerous variables that affect the performance of diamond and CBN cutting blades. Understanding these variables will help end users select the right diamond blade specifications for their applications and optimize their...
02
Jun
Evaluating & Comparing Diamond Blades
Share this Article with Friend or Colleague
Proper testing procedures and methodologies must be set up and used to obtain accurate as well as repeatable testing results. This article will discuss several simple procedures which...
31
Jul
Top 5 Diamond & CBN Cutting Blade Performance Metrics
Share this Article with Friend or Colleague
When evaluating diamond and cubic boron nitride (CBN) cutting blades, it's crucial to consider key performance metrics and criteria. Different applications have varying goals, making it...
01
Aug
Diamond & CBN Cutting Blade Performance Metrics that you Should Know
Share this Article with Friend or Colleague
When evaluating diamond and cubic boron nitride (CBN) cutting blades, it's crucial to consider key performance metrics and criteria. Different applications have varying goals, making it important to...
02
Aug
Total Cost of Ownership & Why its Important
Share this Article with Friend or Colleague
Diamond and CBN cutting blades are available in a myriad of specifications, with virtually limitless options. The industry is saturated with numerous manufacturers, each professing to offer the...
05
Aug
Understanding Tradeoffs- Searching for Perfect Diamond & CBN Blade
Share this Article with Friend or Colleague
Choosing the right blade diamond or cbn blade can significantly impact efficiency, cost, and quality. However, this is not simple and clear cut process. Selecting the optimal blade...
- Unmatched Selection For Many Applications
- Superior Quality & Consistency
- Immediate Worldwide Delivery
- Technical Support & Expertise
- American Based Manufacturer
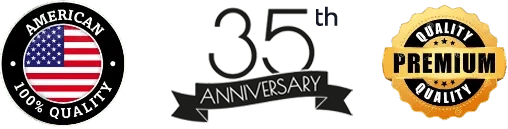

- Different Product
- Different Technology
- Different Company
- Expect MORE from your tools
Let Us HELP You!
Subscribe To Our Newsletter
Signup for email offers, updates, and more
Contact Us
- 25205 & 25201 Avenue Tibbits Valencia CA 91355 USA
-
Phone : (661) 257-2288
FAX : (661) 257 -3833 - lel@ukam.com
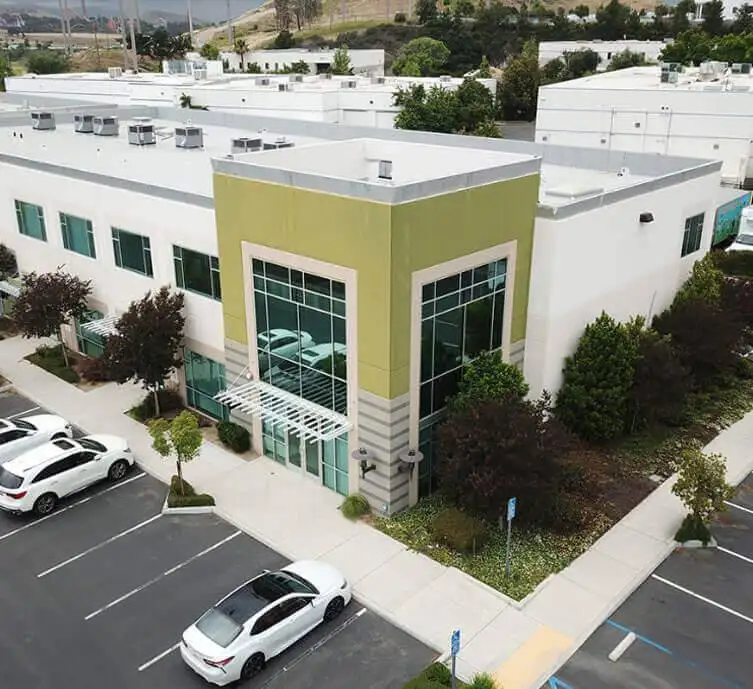
UKAM Industrial Superhard Tools is a U.S. High Technology, Specialty Diamond Tool & Equipment manufacturer. We specialize in producing ultra thin, high precision cutting blades, precision cutting machines diamond drills, diamond micro tools, standard & custom advanced industrial diamond tools and consumables.
- 25205 & 25201 Avenue Tibbits Valencia CA 91355 USA
-
Phone : (661) 257-2288
FAX : (661) 257 -3833 - lel@ukam.com
- 25205 & 25201 Avenue Tibbits Valencia CA 91355 USA
-
Phone : (661) 257-2288
FAX : (661) 257 -3833 - lel@ukam.com
DIAMOND TOOLS BY BOND
EQUIPMENT
KNOWLEDGE CENTER
OUR PRODUCTS
COMPANY
CUSTOMER SERVICE
Shipping Methods


Safe & Secure Payments

© Copyright 1990-2025. UKAM Industrial Superhard Tools – Terms of Use