-
0 items in quote
No products in the Quote Basket.
SMART CUT® Fine Grinding
(Fixed Abrasive) Plates & Double Disc Grinding Wheels
SMART CUT® Fine Grinding (Fixed Abrasive) Plates is the ultimate solution for achieving unparalleled precision and exceptional surface quality in your machining processes. These cutting-edge plates are designed to revolutionize your fine grinding operations by replacing traditional lapping processes, making them ideal for parts demanding impeccable parallelism and precise dimensional control.
Used on double and single-sided fine grinding, flat-honing & converted lapping machines for precision stock removal of flat workpieces. Especially suitable for hard to grind materials. Typically used on many famous brand name equipment such as:
- Stahli
- Peter Wolters
- Lapmaster
- Speed Fam
- Many Others
Description
Specifications
Frequently Asked Questions
Industries Used In
Accessories
Recommendations
Description
Double Disc Grinding or Lapping
Double disc grinding or lapping is used to achieve parallelism and flatness on both sides of the silicon wafers simultaneously. In this process, two opposing grinding or lapping discs remove material from both faces of the wafer. This method is highly efficient for mass production as it allows high throughput with excellent control over thickness and flatness. Lapping, while similar to grinding, uses loose abrasive particles between the wafers and rotating discs, focusing on achieving a superior finish and removing any surface imperfections.
Specifications
- Plate Diameter: 450mm (17 inches) to over 1000mm (40 inches). Popular Outside Diameters: 450mm, 600mm, 800mm, 1000mm, and larger
- Plate Inside Diameter: 50.8mm (2 inches) or 76.2mm (3 inches) & many others
- Plate Thickness: 3mm to 15mm
- Abrasive Grit Size: 300 to 3 microns
- Plate Material: metal alloys, ceramics, or composite
- Plate Hardness: HRC 40 to HRC 70
- Plate Flatness and Parallelism Tolerances: 1 micron
- Mounting Configuration: bolt holes, threaded inserts, or other attachment features
- Bond Type: Sintered (Metal Bond), Resin Bond, Hybrid Bond, Vitrified Bond, Electroplated (Nickel Bond)
- Diamond Patterns Available: Rectangular, Circular, Triangular, Waffle, Spiral, Concentric Ring, Grid Patterns, Segmented, Multi Segment Configuration, Hexagon, Full Faced, Custom Shapes
- Equipment Used On: Stahli, Peter Wolters, Lapmaster, Speed Fam, & Many Others
Frequently Asked Questions
Fine Grinding Plates are specialized abrasive tools used on grinding machines to precision-machine workpieces. They consist of abrasive grains bonded to a plate. The abrasive grains remove material from the workpiece, resulting in a smooth and precise surface finish.
Fine Grinding Plates are commonly used for applications that require high parallelism, close dimensional control, and fine surface finishes. Typical applications include optics, ceramics, metals, semiconductor wafers, and precision components.
Selecting the right plate involves considering factors such as workpiece material, required surface finish, plate type, grit size, bond type, and plate diameter. Consult with the manufacturer or supplier for guidance.
Fine Grinding Plates offer advantages such as precise control over surface finish, minimal subsurface damage, and the ability to achieve high parallelism and dimensional accuracy without the need for additional lapping processes.
Fine Grinding Plates come in various sizes, typically ranging from 450mm (17 inches) to over 1000mm (40 inches) in diameter. They can have different shapes, abrasive patterns, and bond types to suit various applications.
The recommended operating RPM varies depending on the plate type, workpiece material, and desired results. Typically, the range is between 500 and 3,000 RPM. Consult the manufacturer’s guidelines for specific recommendations.
Water-soluble coolants are commonly used due to their effectiveness in controlling heat. However, the choice of coolant depends on the workpiece material and specific requirements. Consult the manufacturer or coolant supplier for recommendations.
Yes, regular maintenance is essential to ensure optimal performance. This may include plate dressing, inspection, and cleaning. Follow the manufacturer’s maintenance guidelines for best results.
Yes, some manufacturers offer customization options, including plate diameter, bond type, abrasive grit size, and even custom shapes or patterns to match unique application requirements.
Yes, safety is important. Operators should follow safety protocols, wear appropriate personal protective equipment (PPE), and be trained in the safe operation of grinding machines.
Fine Grinding Plates can be used on a wide range of materials, including metals, ceramics, glass, semiconductor materials, and composites. The choice of plate and parameters depends on the material.
Yes, Fine Grinding Plates are often used as a replacement for lapping processes, offering advantages such as improved efficiency and reduced processing time.
Fine Grinding Plates are designed for precision machining and surface finishing, offering advantages like high parallelism and close dimensional control. Conventional grinding wheels may be more suitable for material removal and less demanding surface finish requirements.
Fine Grinding Plates can be used on standard grinding machines with appropriate spindle compatibility. However, some applications may benefit from machines optimized for fine grinding processes.
While Fine Grinding Plates are often used with water-soluble coolants for wet grinding, dry grinding may also be feasible in some cases. Consult the manufacturer’s recommendations for guidance on wet or dry grinding.
The achievable dimensional tolerances depend on various factors, including workpiece material, plate type, machine setup, and operator skill. Fine Grinding Plates can achieve tight tolerances when used correctly.
The size and weight of workpieces that can be processed with Fine Grinding Plates depend on the capacity and capabilities of the grinding machine being used. Consult the machine’s specifications for size and weight limitations.
Yes, Fine Grinding Plates are often used in batch processing and high-volume production. They can offer efficiency and consistency in producing multiple identical components.
The lifespan of Fine Grinding Plates varies depending on factors like material being processed, grinding parameters, and maintenance. Proper plate maintenance, dressing, and careful usage can extend their lifespan.
Yes, operators may need training and experience to optimize the use of Fine Grinding Plates. Operator skill and familiarity with the process are essential for achieving consistent and high-quality results.
Fine Grinding Plates are generally used for flat or near-flat surface grinding. For curved surfaces or complex geometries, specialized tools or processes may be required.
Proper disposal of grinding waste, including used abrasive material and coolants, is important to comply with environmental regulations. Implement waste management practices in accordance with local laws.
The generation of dust and airborne particles can vary depending on the workpiece material and grinding parameters. Implement dust extraction and filtration systems as needed to maintain a clean and safe working environment.
Fine Grinding Plates are primarily designed for external surface grinding. For internal grinding, specialized tools and processes, such as internal grinding wheels, are typically employed.
The plate diameter affects the grinding area and the surface speed at the grinding contact point. Larger diameter plates are often used for larger workpieces and can provide improved material removal rates.
When grinding thin or fragile workpieces, it’s important to use appropriate fixturing and support to prevent workpiece deformation or breakage. Consult the manufacturer’s recommendations for best practices.
Yes, Fine Grinding Plates can be used for a wide range of materials, including both ferrous (e.g., steel) and non-ferrous materials (e.g., aluminum, copper, ceramics). Plate selection and grinding parameters may vary based on material type.
Yes, Fine Grinding Plates can be used to achieve mirror-like surface finishes when combined with the appropriate grit size and plate type. However, achieving such finishes may require additional steps and care in the process.
While Fine Grinding Plates excel in precision and surface finish, they are not typically used for heavy stock removal tasks. Coarser grinding methods, such as conventional grinding wheels, are better suited for such applications.
Dressing is recommended to maintain the sharpness of abrasive grains on Fine Grinding Plates. Some plates have built-in dressing mechanisms, while external dressing tools may be used. Dressing is typically performed when the plate’s cutting efficiency diminishes.
The bond type affects the retention and spacing of abrasive grains on the plate. Different bond types provide varying levels of grain retention and wear resistance. The choice of bond type depends on the application and material being ground.
Yes, operators should follow safety protocols, wear appropriate PPE, and be aware of potential hazards associated with grinding operations. Proper training and adherence to safety guidelines are crucial.
Fine Grinding Plates are primarily designed for flat or near-flat surface grinding. While they can accommodate slightly contoured surfaces, specialized tools may be needed for highly contoured workpieces.
The lifespan of coolant can vary depending on factors such as usage, concentration, and maintenance. Regularly monitor the coolant’s condition and replace or replenish it according to the manufacturer’s recommendations.
When grinding thin workpieces, be cautious about excessive pressure, which can cause distortion. Proper fixturing and support are crucial to maintain workpiece integrity.
Yes, Fine Grinding Plates are versatile and can be used for both batch processing and single-piece machining. They offer efficiency and precision in various production scenarios.
Yes, Fine Grinding Plates are versatile and can be used for both batch processing and single-piece machining. They offer efficiency and precision in various production scenarios.
Fine Grinding Plates are available in various types to suit specific applications and material requirements. Some common types include:
- Diamond Plates: Ideal for grinding hard and brittle materials like ceramics, silicon carbide, and diamond.
- CBN Plates: Suitable for grinding hard and tough materials like tool steels and carbides.
- Aluminum Oxide Plates: Used for general-purpose grinding on a wide range of materials, including metals, plastics, and composites.
- Silicon Carbide Plates: Effective for grinding softer materials like glass, ceramics, and composites.
Fine Grinding Plates are available in a range of grit sizes, from coarse to fine, to achieve different surface finishes. The choice of grit size depends on the desired surface finish and the material being ground.
- Coarse Grit (60-120): Used for rough grinding to remove large amounts of material and create a preliminary surface finish.
- Medium Grit (180-320): Suitable for intermediate grinding to refine the surface finish and prepare for finer polishing.
- Fine Grit (400-600): Used for precision grinding to achieve a high-quality surface finish with minimal material removal.
- Ultrafine Grit (800-1200): Ideal for optical-grade polishing, creating a mirror-like surface finish.
Fine Grinding Plates employ various bonding types to adhere the abrasive grains to the plate’s surface. Each bonding type offers distinct characteristics and is suitable for specific applications.
- Vitrified Bond: A strong and durable bond commonly used for general-purpose grinding and applications requiring high wear resistance.
- Resin Bond: A flexible bond suitable for precision grinding and applications where minimal workpiece distortion is critical.
- Metal Bond: A highly durable bond ideal for grinding hard and abrasive materials, providing exceptional wear resistance.
The optimal operating parameters for Fine Grinding Plates depend on the specific application, material being ground, and desired surface finish. However, some general guidelines include:
- Rotational Speed: Typically ranging from 50 to 1000 RPM, depending on the plate size and workpiece dimensions.
- Grinding Pressure: Typically ranging from 1 to 100 psi, depending on the material hardness and surface finish requirements.
- Coolant: Coolant is often used to prevent overheating and maintain abrasive sharpness.
Always follow proper safety precautions when using Fine Grinding Plates:
- Wear appropriate safety gear: Wear safety glasses, gloves, and respiratory protection when operating grinding machines.
- Securely mount the plate: Ensure the plate is properly mounted to the grinding machine to prevent vibration and accidents.
- Use proper grinding techniques: Follow recommended grinding techniques to avoid workpiece damage and ensure operator safety.
- Maintain the machine and plates: Regularly inspect and maintain the grinding machine and plates to ensure optimal performance and safety.
Fine Grinding Plates offer several environmental advantages over traditional grinding methods:
- Reduced Coolant Consumption: Fixed abrasive technology requires less coolant compared to loose abrasive methods, minimizing wastewater generation.
- Extended Abrasive Life: Longer-lasting abrasive bonds reduce the frequency of abrasive replacements, minimizing waste disposal.
- Energy Efficiency: Efficient grinding processes minimize energy consumption, contributing to a smaller environmental footprint.
Yes, Fine Grinding Plates can be integrated into automated or robotic grinding systems for consistent and repeatable machining processes.
Depending on local regulations, used Fine Grinding Plates may be considered industrial waste. Dispose of them in accordance with applicable environmental laws and guidelines.
The reconditioning or re-sharpening of Fine Grinding Plates may be possible in some cases, depending on their design and condition. Consult with the manufacturer or a specialized service provider for guidance.
Challenges in fine grinding can include achieving tight tolerances, controlling heat generation, maintaining consistent surface finishes, and managing abrasive wear. Troubleshooting and process optimization may be necessary to address these challenges.
Yes, some Fine Grinding Plates come with automated dressing mechanisms that help maintain the sharpness of abrasive grains. These mechanisms can be integrated into the grinding system for convenience.
When grinding brittle materials, it’s important to use lower pressure and ensure proper workpiece support to prevent chipping or breakage. Additionally, selecting the right plate and coolant is critical for minimizing thermal stress.
While Fine Grinding Plates can improve surface finish and precision, they are primarily designed for flat or slightly contoured surfaces. Removing deep defects or machining highly irregular shapes may require additional steps or specialized tools.
Changing Fine Grinding Plates involves proper machine shutdown, safety precautions, and careful handling of the tool. Follow the manufacturer’s instructions for plate replacement to ensure safety and proper installation.
In some cases, a single Fine Grinding Plate may be used for both roughing and finishing by adjusting parameters like pressure and grit size. However, it’s essential to carefully control these parameters to achieve the desired results.
Yes, Fine Grinding Plates can be employed to achieve specific roughness values (Ra) by selecting the appropriate plate and adjusting grinding parameters. Consult the manufacturer or supplier for guidance on achieving desired surface finishes.
Fine Grinding Plates are often used for machining exotic materials like sapphire and advanced ceramics. However, the choice of plate and grinding parameters should be tailored to the specific material properties and requirements.
Proper balancing is crucial to prevent vibrations and uneven wear. Follow the manufacturer’s recommendations for balancing procedures, and periodically check and adjust the plate’s balance as needed.
Yes, Fine Grinding Plates are suitable for large-scale production runs, especially when precision and surface finish are critical. They can help maintain consistency in quality across a large volume of workpieces.
Safety precautions include wearing appropriate personal protective equipment (PPE), ensuring machine safety interlocks are functional, and following safety guidelines for machine operation. Proper training is essential for operators.
Achieving flatness and parallelism requires proper machine setup, workpiece fixturing, and control of grinding parameters. Consult the manufacturer’s recommendations and consider using measuring equipment to verify results.
Yes, Fine Grinding Plates can be adapted for both single-sided and double-sided grinding processes, depending on the machine setup and requirements of the application.
To control heat generation, use an appropriate coolant/lubricant, ensure consistent pressure, and control grinding parameters such as speed and feed rate. Monitoring temperature during grinding can also help manage heat.
Yes, Fine Grinding Plates can be used for grinding non-metallic materials, including plastics and composites. Choose the appropriate plate type and abrasive grit size for the specific material and application.
Cleaning Fine Grinding Plates involves removing debris and coolant residues. Follow the manufacturer’s maintenance recommendations, which may include regular cleaning, inspection, and dressing as needed.
Yes, Fine Grinding Plates are commonly used for precision optics manufacturing. They can help achieve the required surface quality and accuracy for optical components.
What is the typical lead time for ordering custom Fine Grinding Plates with specific specifications?
Lead times for custom Fine Grinding Plates can vary depending on the manufacturer and the complexity of the customization. It’s advisable to inquire with the manufacturer regarding lead times for specific orders.
To minimize subsurface damage, use finer grit sizes, lower pressure, and appropriate coolant/lubricant. Additionally, consider post-grinding processes like polishing or chemical etching for further damage reduction.
While Fine Grinding Plates excel in finishing applications, they can also achieve moderate material removal rates when using coarser grit sizes and appropriate pressure. However, for heavy material removal, other grinding methods may be more suitable.
Fine Grinding Plates are not typically used for sharpening cutting tools or blades, as their primary function is surface finishing and precision machining. Sharpening tools often require specialized abrasive materials and equipment.
Repurposing worn Fine Grinding Plates for alternative applications may be possible depending on their condition and design. Consult with the manufacturer or a specialist for guidance on repurposing options.
Fine Grinding Plates can be used for machining CFRP materials, but it’s important to select the appropriate plate type, grit size, and grinding parameters to prevent delamination and achieve desired surface finish.
When grinding heat-sensitive materials, use lower speeds, reduce pressure, and choose a coolant that minimizes thermal effects. Monitoring temperature during grinding is crucial to prevent material damage.
Achieving tight thickness tolerances for thin workpieces may be challenging due to potential workpiece deflection. Proper fixturing and support are critical to maintaining thickness control.
Signs of wear include reduced cutting efficiency, decreased surface quality, and uneven wear patterns. Address wear by dressing the plate, replacing it, or reconditioning it according to manufacturer recommendations.
Fine Grinding Plates can be used for machining refractory materials, but it may require specialized abrasives and coolant/lubricant systems to manage the high heat generated during grinding.
Materials with low thermal conductivity can be prone to heat buildup during grinding. Use coolant, reduce pressure, and control speed to minimize heat-related issues.
Yes, Fine Grinding Plates can be used to achieve specific flatness requirements when combined with precise machine setup and control of grinding parameters.
Measuring surface roughness is important for quality control. Common methods include profilometers and surface roughness testers. Regular measurements help ensure the desired finish is achieved.
Fine Grinding Plates can produce slightly contoured surfaces but may not be suitable for highly convex or concave shapes. Specialized tools or processes may be needed for extreme contours.
Implementing recycling systems for abrasive waste and responsible coolant disposal are ways to reduce environmental impact. Follow local regulations and best practices for waste management.
Fine Grinding Plates can be used for precision machining of hardened steel and tool steels, but the choice of plate type and abrasive grit size should match the hardness and requirements of the workpiece.
Dressing tools are used to maintain the sharpness of abrasive grains on Fine Grinding Plates. The frequency of dressing depends on factors like plate wear and the specific application. Follow manufacturer recommendations.
Yes, Fine Grinding Plates are often used for fine-tuning or correcting dimensions on machined parts to achieve precise tolerances and desired surface finishes.
Challenges in achieving high parallelism can include workpiece deflection and uneven pressure distribution. Solutions may involve optimizing fixturing, controlling pressure, and using proper machine setup.
The recommended coolant concentration can vary depending on the coolant type and manufacturer’s specifications. Maintaining the correct concentration is crucial for coolant effectiveness. Follow the manufacturer’s guidelines.
Fine Grinding Plates can be used to remove oxide layers and surface contaminants from materials like stainless steel. Choose the appropriate abrasive grit size and plate type for the specific application.
Yes, Fine Grinding Plates can be used for aerospace applications that demand tight tolerances and high surface finish quality. Precise machine setup and control are essential for meeting aerospace standards.
While some applications may permit both dry and wet grinding with Fine Grinding Plates, it’s essential to follow manufacturer recommendations and adjust parameters accordingly.
Fine Grinding Plates can be used for finishing 3D-printed or additive-manufactured components to achieve precise dimensions and surface quality. Careful setup and control are necessary for optimal results.
Fine Grinding Plates are generally used for precision and fine finishing applications. For high material removal rates and aggressive grinding, other abrasive methods may be more suitable.
Industries Used In
Tab Content
Accessories
Tab Content
Recommendations
- Select the Appropriate Plate Type: Choose the Fine Grinding Plate with the right abrasive material and bond type that matches the workpiece material and the desired surface finish. Consider factors like hardness, abrasiveness, and material removal rates.
- Inspect the Plate: Before installation, carefully inspect the Fine Grinding Plate for any damage or irregularities. Ensure that the plate is in good condition and free from defects that could affect its performance.
- Mount the Plate Securely: Follow the manufacturer’s guidelines for mounting the Fine Grinding Plate onto your grinding machine’s spindle or shaft. Ensure that it is securely and properly attached to prevent vibrations or wobbling during operation.
- Use Proper Coolant/Lubrication: Implement an appropriate coolant or lubrication system to control heat generation during the grinding process. Proper cooling helps prevent thermal damage to the workpiece and extends the life of the Fine Grinding Plate.
- Monitor and Control Grinding Parameters: Pay attention to feed rates, depth of cut, and other grinding parameters to achieve the desired material removal rates and surface finish. Adjust these parameters as needed to optimize performance.
- Dress the Plate When Necessary: If your Fine Grinding Plate features a dressing mechanism or if external dressing is required, use it as recommended to maintain the sharpness and effectiveness of the abrasive grains.
- Workpiece Preparation: Ensure that the workpiece is properly prepared, including proper cleaning and alignment. Secure the workpiece firmly to minimize vibration and maintain dimensional accuracy.
- Safety Precautions: Follow all safety guidelines and wear appropriate personal protective equipment (PPE) when operating the grinding machine and working with Fine Grinding Plates. Ensure that your team is trained on safe usage procedures.
- Quality Control: Implement a quality control process to inspect and measure the machined components to ensure they meet the desired specifications for parallelism, dimensional accuracy, and surface finish.
- Maintenance and Care: Regularly inspect and maintain the Fine Grinding Plate, including cleaning and, if necessary, re-dressing or replacing worn abrasive segments. Proper maintenance prolongs the life and performance of the plate.
- Workpiece Alignment: Ensure that the workpiece is correctly aligned with the grinding plate. Proper alignment helps maintain dimensional accuracy and prevents uneven material removal.
- Workpiece Cleaning: Before grinding, thoroughly clean the workpiece to remove contaminants, oils, and debris. A clean workpiece promotes better adhesion between the workpiece and the abrasive surface.
- Workpiece Fixturing: Use appropriate fixturing or clamping mechanisms to secure the workpiece firmly during the grinding process. Minimize vibrations and ensure consistent contact between the workpiece and the plate.
- Process Stability: Maintain stable and consistent process conditions throughout the grinding operation. Variations in feed rates, coolant flow, or other parameters can affect the quality of the finished workpiece.
- Progressive Approach: Consider using a progressive grinding approach, starting with coarser grit sizes and gradually transitioning to finer grit sizes for achieving the desired surface finish and dimensional accuracy.
- Documentation and Records: Keep detailed records of grinding parameters, tooling setup, and workpiece specifications for each job. This documentation can help troubleshoot issues and ensure consistency in future operations.
- Operator Training: Ensure that operators are adequately trained in the operation of the grinding machine and the use of Fine Grinding Plates. Knowledgeable operators are essential for achieving consistent and high-quality results.
- Tool Inspection: Periodically inspect the Fine Grinding Plate for signs of wear, damage, or uneven wear patterns. Replace or re-dress the plate as needed to maintain optimal performance.
- Coolant Management: Properly manage the coolant or lubricant used during grinding. Ensure it is clean, properly filtered, and at the right temperature to effectively control heat and maintain workpiece integrity.
- Surface Finish Evaluation: Use appropriate surface measurement equipment, such as profilometers or surface roughness testers, to evaluate and confirm the achieved surface finish meets the required specifications.
- Material Selection: Choose the appropriate Fine Grinding Plate based on the material composition of the workpiece. Different materials may require different plate compositions and abrasive characteristics for optimal results.
- Batch Size Considerations: When planning your machining processes, consider batch sizes. Fine Grinding Plates can be highly efficient for larger production runs, but adjustments may be needed for smaller batches to maintain consistency.
- Customization Options: Explore customization options with the manufacturer. Some Fine Grinding Plate suppliers offer tailored solutions to meet specific application requirements, including custom plate shapes and abrasive patterns.
- Grinding Sequence: Plan the sequence of grinding steps if you have multiple operations. Determine whether pre-grinding or post-grinding steps are needed to achieve the desired results.
- Tool Balancing: Ensure that the grinding machine and Fine Grinding Plate are properly balanced to minimize vibrations during operation. Imbalanced tools can lead to reduced surface quality and accelerated wear.
- Safety Interlocks: Check that safety interlocks and emergency stop mechanisms on the grinding machine are in proper working condition. Safety should always be a top priority in machining operations.
- Operator Feedback: Encourage operators to provide feedback on tool wear and performance. Early detection of wear or other issues can prevent production disruptions and ensure consistent results.
- Waste Management: Develop a waste management plan for used Fine Grinding Plates and waste materials generated during the grinding process. Dispose of waste in compliance with environmental regulations.
RPM’S Recommendations
Typical operating RPM (revolutions per minute) range for Fine Grinding (Fixed Abrasive) Plates can vary depending on several factors, including the plate design, the type of abrasive material used, the workpiece material, and the specific machining application. However, in general, the operating RPM for fine grinding plates often falls within the range of approximately 500 to 3,000 RPM. Here’s a breakdown of this range:
1. Lower RPM Range (500-1,500 RPM):
- Lower RPM settings are often used for fine grinding applications that require precision and surface finish. These lower speeds are suitable for achieving fine surface finishes with minimal heat generation.
- Applications such as optics, ceramics, and certain metals may benefit from lower RPM settings to minimize heat-related issues and maintain dimensional accuracy.
2. Mid-Range RPM (1,500-2,000 RPM):
- Mid-range RPM settings are common for many general-purpose fine grinding applications. They strike a balance between material removal rates and surface finish quality.
- These RPM settings are often used for materials like hardened steels, tool steels, and various alloys where a combination of precision and material removal is required.
3. Higher RPM Range (2,000-3,000 RPM):
- Higher RPM settings are typically employed for applications that prioritize material removal rates. The increased speed can help remove material more efficiently but may produce a coarser surface finish.
- Applications involving softer materials or stock removal tasks may benefit from higher RPM settings.
It’s important to note that the optimal operating RPM can vary based on the specific plate design, the abrasiveness of the abrasive material, and the desired results for a particular application. Manufacturers of Fine Grinding Plates often provide recommendations for the best operating RPM based on their product specifications and the materials you intend to process. Additionally, the coolant/lubrication system, feed rates, and other process parameters should also be considered to achieve the desired machining outcomes.
Recommended Coolants
The recommended coolant to use with Fine Grinding (Fixed Abrasive) Plates can vary depending on factors such as the workpiece material, the plate type, and the specific machining application. However, water-soluble coolants are commonly used for fine grinding operations due to their effectiveness in controlling heat generation and maintaining workpiece integrity. Within the category of water-soluble coolants, there are several types to consider:
- Synthetic Coolants: Synthetic coolants are water-based and formulated with synthetic additives. They offer excellent cooling properties, lubrication, and rust protection. They are often used in precision grinding applications, including those involving hard materials.
- Semi-Synthetic Coolants: Semi-synthetic coolants are a blend of synthetic and mineral oil-based additives. They provide good cooling and lubrication properties while being cost-effective. Semi-synthetic coolants are suitable for a wide range of materials and applications.
- Soluble Oil Coolants: Soluble oil coolants are emulsions of mineral oil and water. They provide good lubrication and rust protection. Soluble oil coolants are often used in heavy-duty grinding operations, such as those involving ferrous materials.
- Straight Oil Coolants: Straight oil coolants are mineral oil-based and do not contain water. They offer excellent lubrication but have limited cooling capabilities. They are typically used for grinding applications where cooling is less critical, such as low-speed, heavy grinding.
When selecting a coolant for your specific fine grinding application, consider the following factors:
- Workpiece Material: The type of material being ground can influence the choice of coolant. Some materials may be more prone to thermal damage, so an efficient coolant with excellent cooling properties may be necessary.
- Plate Type: Different Fine Grinding Plates may have specific recommendations regarding coolant compatibility and performance. Follow the manufacturer’s guidelines for coolant selection.
- Machine Setup: The design and capabilities of your grinding machine, including the coolant delivery system, should be considered when choosing a coolant type.
- Regulatory Compliance: Ensure that the selected coolant complies with environmental and safety regulations in your area.
- Coolant Concentration: Follow the manufacturer’s recommendations for mixing coolant concentrate with water to achieve the desired concentration level. Maintaining the correct concentration is essential for optimal coolant performance.
- Coolant Maintenance: Implement a regular coolant maintenance program, including monitoring coolant condition, pH levels, and cleanliness. Regularly replace or replenish coolant to ensure consistent performance.
Recommended Steps
The number of steps required to achieve the desired outcome when using Fine Grinding (Fixed Abrasive) Plates can vary depending on the specific application, workpiece material, and the level of precision and surface finish required. Generally, fine grinding processes may involve multiple steps to progressively refine the workpiece surface. Here’s an overview of the typical steps involved:
- Rough Grinding: If your workpiece has significant material to be removed or is relatively rough, you may begin with a coarse-grit Fine Grinding Plate. This step aims to remove bulk material quickly.
- Intermediate Grinding: After the rough grinding step, you may transition to an intermediate-grit Fine Grinding Plate. This step helps refine the surface further and reduce surface imperfections.
- Fine Grinding: The primary fine grinding step involves using a plate with a finer abrasive grit size. This step focuses on achieving the desired surface finish while maintaining dimensional accuracy.
- Final Finish: In applications that require an exceptionally smooth and polished surface, a final finish step may be necessary. A plate with a very fine abrasive grit size is used to achieve the desired surface quality.
Trouble Shooting Guide
Issue |
Possible Causes |
Recommended Solutions |
---|---|---|
Uneven Surface Finish |
|
|
Workpiece Chatter |
|
|
Excessive Heat Generation |
|
|
Poor Dimensional Control |
|
|
Abrasive Plate Wear |
|
|
Suboptimal Surface Finish |
|
|
Plate Loading or Glazing |
|
|
Inconsistent Results |
|
|
Plate Dressing Difficulties |
|
|
Workpiece Distortion |
|
|
Material Compatibility |
|
|
Plate Imbalance |
|
|
Noise and Vibration |
|
|
Subsurface Damage |
|
|
Plate Misalignment |
|
|
Excessive Material Removal |
|
|
Workpiece Sticking |
|
|
Plate Wear and Tear |
|
|
Environmental Impact |
|
|
Surface Cracking |
|
|
Workpiece Edge Chipping |
|
|
Inconsistent Plate Wear |
|
|
Glaze Formation |
|
|
Workpiece Warping |
|
|
Fine Grinding Plate Alignment |
|
|
Residual Stress in Workpiece |
|
|
Plate Bond Failure |
|
|
How This Works
Flat Honing and fine grinding, also referred to as top & bottom grinding or disk grinding, proves to be a highly effective production method for mass-producing exceptionally precise tools and parts across various industries and applications. Remarkable precision in both height and parallelism of the finished products can be achieved through this method.
This technique involves setting up a configuration where tools or parts are ground from one side or both sides using substantial diamond cylindrical wheels/discs. When these two wheels are employed, they rotate in opposite directions.
The components or tools to be ground are securely affixed within carriers and positioned onto the lower grinding wheel. Throughout the machining process, the carriers revolve around the surface of the grinding wheel.
Features
- Abrasives are permanently bonded to the plates, versus lapping which uses free abrasives in a slurry
- Workpiece motion is cycloidal using toothed carriers, similar to lapping
- Easier part cleanup due to use of water or oil as lubricant (versus abrasive slurry)
- Standard and custom plate sizes and configurations are available for use on large variety of equipment types
- Plates available for custom applications up to 1200 mm diameter
- To create the best solution for your application, we can provide an unlimited number of combinations of plate segment geometries, bond hardness and matrix structures
- Abrasive crystals available as small as 6 micron and as large as 300 µm with tightly controlled particle size distribution (PSD)
- Abrasive crystals can be diamond (natural and synthetic), CBN or conventional silicon carbide or aluminum oxide
- Large Varity of plate abrasive patterns available
Benefits
- Up to 10 times reduction in cost per part compared to loose-abrasive lapping
- Excellent surface finish
- Significantly reduces cleaning costs since no slurry is used
- Very consistent, high stock removal rates
- Excellent plate wear characteristics
- Used for both roughing and finishing operations
- Standard and custom bond formulations
- Wide range of crystal sizes & types
- Uniform part thickness
Application
- Hardened Steels
- Tungsten Carbide
- Powdered Metals
- Ceramics
- Quartz
- Sapphire
- Silicon
- Composites (graphite, laminates)
- Fuel & Hydraulic components
Advantages
- Precision Made: SMART CUT Fine Grinding Plates have been engineered to deliver precision beyond compare. Whether it's achieving high parallelism or maintaining tight dimensional control, these plates excel in meeting your exacting requirements.
- Large Range of Sizes: We understand that one size does not fit all. That's why our plates come in a range of diameters, from a compact 450mm (17 inches) to an impressive 1000mm (40 inches) and beyond. This flexibility ensures you can find the perfect fit for your specific application.
- Fixed Abrasive Technology: With fixed abrasive technology, our plates offer consistent and predictable results, eliminating the variability associated with traditional lapping processes. This means you can count on repeatable excellence in every job.
- Enhanced Efficiency: Say goodbye to time-consuming lapping procedures. SMART CUT Fine Grinding Plates significantly reduce processing time while maintaining top-tier quality standards, ultimately leading to improved productivity and cost savings.
- Exceptional Surface Finish: SMART CUT plates produce superior surface finishes, reducing the need for secondary finishing steps. Your parts will emerge with a pristine surface that meets the highest industry standards.
- Versatile Applications: From precision optics to critical mechanical components, our plates are perfect for a wide range of applications where precision and surface quality are non-negotiable.
- Unmatched Precision and Parallelism: Elevate your machining operations to a new level of precision with SMART CUT Fine Grinding Plates. These plates are meticulously engineered to ensure the highest level of parallelism, making them the go-to choice for applications where minute deviations are unacceptable. Experience the confidence that comes with consistently precise results.
- Reduced Downtime, Enhanced Productivity: Say goodbye to the time-consuming and labor-intensive lapping processes. SMART CUT Fine Grinding Plates are designed for efficiency, significantly reducing processing times. This means reduced downtime, increased throughput, and ultimately, improved productivity for your operations.
- Optimal Control, Minimal Variability: Achieve remarkable consistency and process control with our fixed abrasive technology. The abrasive particles remain firmly in place, ensuring minimal variability in your machining processes. Count on reliable, repeatable results with every use, eliminating the need for constant adjustments.
Equipment Used On
Fine Grinding Plates are typically used on fine grinding machines, which are specialized precision machining equipment designed for achieving high-precision grinding, superior surface quality, and tight dimensional control. These machines are equipped with various components and features to ensure the efficient use of Fine Grinding Plates. Here are some common types of equipment where Fine Grinding Plates find application:
- Fine Grinding Machines: These machines are specifically designed for fine grinding operations. They come in various configurations, including single-sided and double-sided machines. Fine Grinding Plates are used as a critical component in these machines to achieve precise material removal and surface finishing.
- Lapping Machines: In some cases, Fine Grinding Plates can also be used as a replacement for traditional lapping processes. Lapping machines are designed for achieving extremely high-precision surface finishes. Fine Grinding Plates help improve the efficiency and accuracy of lapping operations.
- Double-Disk Grinding Machines: Double-disk grinding machines utilize rotating abrasive wheels on both sides of the workpiece. Fine Grinding Plates can be integrated into these machines to achieve parallelism and tight dimensional control on double-sided grinding applications.
- Optical Grinding Machines: Fine Grinding Plates are commonly used in the optics industry, where precision is crucial. Optical grinding machines utilize Fine Grinding Plates to produce high-quality optical components, such as lenses and prisms.
- Semiconductor Wafer Grinding Machines: In semiconductor manufacturing, Fine Grinding Plates are used in wafer grinding machines to achieve the precise thickness and surface quality required for semiconductor wafers.
- Aerospace and Automotive Component Grinding Machines: Fine Grinding Plates find applications in the aerospace and automotive industries, where critical components require precision grinding. These machines help achieve the desired surface quality and dimensional accuracy.
- Precision Machining Centers: Some precision machining centers may also incorporate Fine Grinding Plates as part of their tooling to enhance the quality of finished components.
Related Products
SMART CUT® Water Soluble Coolant
(General Materials Formula)
High-Performance Fully Synthetic Coolant & Lubricant for Diamond Slicing, Dicing, Drilling, and Grinding & Machining of Ceramics, Glass, Optics, Quartz, Silicon, and Other Hard & Brittle Materials
SMART CUT® Water Soluble Coolant (General Materials Formula) is a fully synthetic, non-oily, and non-foaming coolant and lubricant engineered to meet the rigorous demands of slicing, dicing, drilling, sectioning, wafering, grinding, and polishing operations involving hard and brittle materials. This advanced formula has been specifically developed for use with ceramics, precision optics, quartz, silicon, sapphire, and other materials commonly found in semiconductor, photonics, and materials research applications.SMART CUT® Monocrystalline Diamond Powder for Grinding, Polishing, & Lapping
SMART CUT® Diamond Powder is meticulously engineered for lapping and polishing applications, produced under stringent high-pressure and high-temperature conditions. Each batch is rigorously graded to meet strict standards, ensuring an exceptional particle size distribution for each specified size. We provide both natural and synthetic diamond powder, available in monocrystalline, polycrystalline, and natural forms. Our range includes ultra-fine sub-micron sizes (as small as 1/10 micron) to more robust abrasive sizes of 80-120 microns, along with a comprehensive spectrum of mesh sizes for various diamond abrasives.
Discover the Right Diamond Powder for Your Application: Choosing Between Monocrystalline and Polycrystalline Diamonds >>>
Diamond Suspensions
UKAM Industrial Superhard Tools offers a wide range of water-based and oil-based diamond suspensions, tailored to the requirements of specific applications. Our ready-to-use diamond suspensions combine micron diamond sizes graded at the highest level of precision with chemical formulations engineered to offer excellent material removal rate and surface quality. Diamond suspensions are used in various industries for lapping and polishing of hard materials.
Recently Viewed Products
ARE YOU USING RIGHT TOOLS
FOR YOUR APPLICATION?
LET US
HELP YOU
HAVING ISSUES WITH
YOUR CURRENT TOOLS?
Knowledge Center
02
Jun
How to properly use Diamond Tools
UKAM Industrial Superhard Tools manufactures precision diamond tools for a large variety of applications, materials, and industries.
Share this Article with Friend or Colleague
Metal Bonded Diamond Tools are “impregnated” with diamonds. This means that selected...
02
Jun
Why use diamond
Diamond is the hardest material known to man kind. When used on diamond/tools, diamond grinds away material on micro (nano) level. Due to its hardness Diamond will work all types of materials from...
02
Jun
Diamond vs CBN (cubic boron nitride) Tools
Cubic Boron Nitride (CBN) is a synthetic material that is renowned for its exceptional hardness and high thermal stability. It is composed of boron and nitrogen atoms arranged in a crystal lattice structure, similar to...
02
Jun
What is Diamond Mesh Size and how to select best one for your application
Diamond grit size can be defined as the size of the diamond particles used in the bond matrix. The larger the diamond particles (grit size) the faster the tool will cut.
Share this Article with Friend or...
02
Jun
What is Diamond Concentration and which to use for your application
Diamond concentration is measured based on the volume of diamond within a section of the tool. It is typically defined as Concentration 100, which equates to 4.4 carats per cubic centimeter of the diamond layer...
02
Jun
Diamond Tool Coolants Why, How, When & Where to Use
Coolant is one of the most overlooked variables in the overall diamond or cbn tool machining process. Effective and proper use of coolant and recalculating coolant system will pay off in terms of improved surface...
18
Jul
Get to Know the Diamond Tool Bond Types and Which to use for your application
The indication of this premature loss of diamond is deep pocket left behind. The presence of many pockets means the diamond is wasted without being used. Each diamond must protrude high to cut fast with...
17
May
Get to Know the Diamond Tool Bond Types and Which to use for your application
Selecting the appropriate diamond bond type for specific applications is crucial for several reasons. Diamond bond type directly affects the tool's performance, efficiency, and longevity. Different bond types determine how well a tool can withstand...
- Unmatched Selection For Many Applications
- Superior Quality & Consistency
- Immediate Worldwide Delivery
- Technical Support & Expertise
- American Based Manufacturer
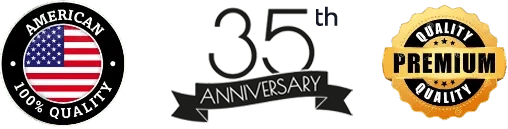

- Different Product
- Different Technology
- Different Company
- Expect MORE from your tools
Let Us HELP You!
Subscribe To Our Newsletter
Signup for email offers, updates, and more
Contact Us
- 25205 & 25201 Avenue Tibbits Valencia CA 91355 USA
-
Phone : (661) 257-2288
FAX : (661) 257 -3833 - lel@ukam.com
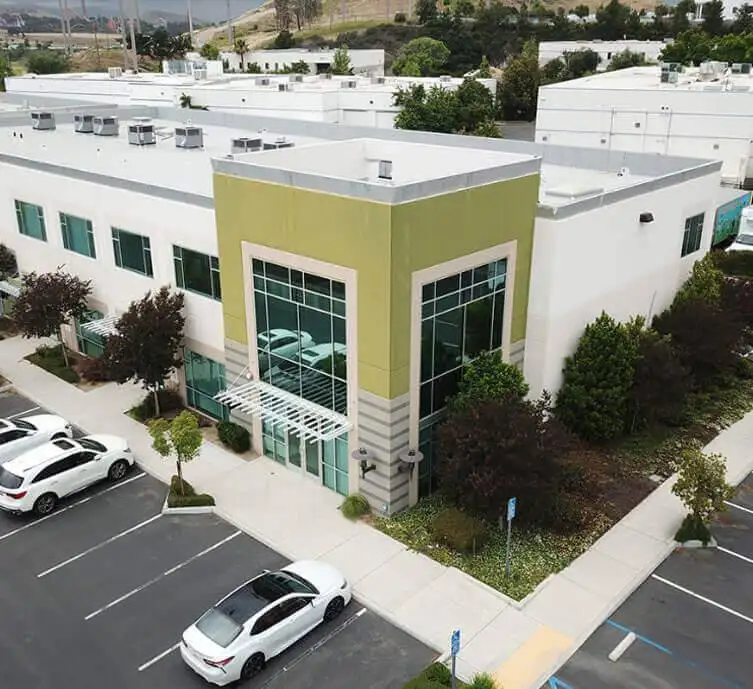
UKAM Industrial Superhard Tools is a U.S. High Technology, Specialty Diamond Tool & Equipment manufacturer. We specialize in producing ultra thin, high precision cutting blades, precision cutting machines diamond drills, diamond micro tools, standard & custom advanced industrial diamond tools and consumables.
- 25205 & 25201 Avenue Tibbits Valencia CA 91355 USA
-
Phone : (661) 257-2288
FAX : (661) 257 -3833 - lel@ukam.com
- 25205 & 25201 Avenue Tibbits Valencia CA 91355 USA
-
Phone : (661) 257-2288
FAX : (661) 257 -3833 - lel@ukam.com
DIAMOND TOOLS BY BOND
EQUIPMENT
KNOWLEDGE CENTER
OUR PRODUCTS
COMPANY
CUSTOMER SERVICE
Shipping Methods


Safe & Secure Payments

© Copyright 1990-2025. UKAM Industrial Superhard Tools – Terms of Use