-
0 items in quote
No products in the Quote Basket.
SMART CUT® Diamond Notch
Grinding Wheel – Electroplated (Nickel Bond)
SMART CUT ® Single & Multi Layered Electroplated Diamond Notch Grinding Wheel is designed for high-precision notch grinding of semiconductor wafers, including materials such as Silicon (Si), Silicon Carbide (SiC), Gallium Arsenide (GaAs), and Sapphire. Engineered using advanced electroplating technology, this wheel ensures exceptional performance in wafer processing, offering a high level of precision and durability for demanding semiconductor applications.
DESCRIPTION
SPECIFICATIONS
FREQUENTLY ASKED QUESTIONS
INDUSTRIES USED IN
ACCESSORIES
USAGE RECOMMENDATION
DESCRIPTION
Tab Content
SPECIFICATIONS
- Inside Thickness: 38.0 ± 0.2 mm, 30.0 ± 0.2 mm
- Outer Diameter: 3.90 ± 0.1 mm, 4.24 ± 0.2 mm
- Groove Tolerance: Up to 5 grooves, with shape tolerance ≥ 1 degree at aperture angle
- Grain Size: Available in mesh sizes #600 to #1500
- Deflection Accuracy: ≥ 5 µm for precise grinding results
FREQUENTLY ASKED QUESTIONS
⦁ Electroplated Wheels: These wheels feature a multi-layered electroplated diamond coating, offering excellent cutting efficiency, minimal wear, and consistent performance. They are best for precision grinding with a lower risk of contamination.
⦁ Sintered (Metal Bond) Wheels: These wheels use a metal bond for higher durability and longer life. They are ideal for tougher grinding applications where enhanced material removal and extended service life are required.
The SMART CUT Diamond Notch Grinding Wheel is designed specifically for high-precision grinding of semiconductor wafers, including materials such as Silicon (Si), Silicon Carbide (SiC), Gallium Arsenide (GaAs), and Sapphire. These wheels are ideal for the semiconductor industry, where accuracy and consistency are crucial.
What is the maximum and minimum grain size available for the SMART CUT Diamond Notch Grinding Wheel?
The SMART CUT wheels are available in a wide range of grain sizes, from #600 to #1500 mesh, allowing for both coarse and fine grinding depending on your specific application.
The SMART CUT Diamond Notch Grinding Wheel offers multiple angle options of 11°, 20°, and 22°, as well as depth options of 1.09 mm and 0.43″. These customizable specifications allow the wheel to meet the exact requirements for your wafer notching processes.
The groove shape tolerance for this wheel is ≥1 degree at the aperture angle, ensuring high precision and accuracy in notch grinding.
While the primary application for the SMART CUT Diamond Notch Grinding Wheel is semiconductor wafer notching, it may also be used for other high-precision grinding and notching tasks that require fine-tuned cutting performance and minimal wear.
The F-type grooves are typically used for general applications, while the R-type grooves are better suited for specialized processes, such as mirror edge grinding. The choice of groove type depends on the specific requirements of the wafer material and the desired notch geometry.
SMART CUT technology ensures that the diamond grain is consistently and precisely applied, providing superior wear resistance, improved cutting efficiency, and extended service life. Additionally, the proprietary dressing technology (AD-C) helps maintain the wheel’s optimal performance and longevity.
The deflection accuracy of the SMART CUT Diamond Notch Grinding Wheel is ≥5 µm, ensuring high precision and stability during the grinding process, which is essential for semiconductor wafer notching.
To maintain the performance and lifespan of the SMART CUT wheel, regular dressing is recommended. Our proprietary dressing technology (AD-C) enhances the wheel’s service life by keeping the diamond grain exposed for efficient grinding. Regular monitoring of wear and checking for run-out is also advised to ensure optimal performance.
The SMART CUT Diamond Notch Grinding Wheel stands out due to its superior durability, customizable specifications, and advanced technology. With an optimized bond for extended life and reduced wear, it provides better performance and longevity compared to other brands, especially for high-demand applications like semiconductor wafer notching.
The SMART CUT wheels are available in multiple sizes, with inner thicknesses of 30.0 ± 0.2 mm and 38.0 ± 0.2 mm, outer diameters ranging from 3.90 ± 0.1 mm to 4.24 ± 0.2 mm, and groove numbers of 1-2. Custom sizes may be available upon request.
Yes, the SMART CUT Diamond Notch Grinding Wheel is designed to handle both coarse and fine grinding processes. With a grain size range from #600 to #1500 mesh, it provides flexibility for various grinding needs depending on your application.
The SMART CUT wheel provides higher precision, longer life, and better performance compared to conventional grinding wheels. Its ability to handle higher precision notching and fine-tuning capabilities make it ideal for semiconductor wafer processing, where the notch area’s quality is critical. Additionally, its advanced bond technology helps extend wheel life while maintaining consistent performance.
The lifespan of the SMART CUT Diamond Notch Grinding Wheel depends on the application and the material being processed. However, thanks to its advanced bonding technology and the use of high-quality diamond grain, the wheel offers extended service life, even in high-demand applications. Using the proprietary AD-C dressing technology further enhances wheel longevity.
The wheel may need dressing when you notice a decline in performance, such as a decrease in grinding efficiency, excessive heat generation, or rougher surface finishes. Regular monitoring of the wear patterns and inspecting the run-out accuracy will help you determine when dressing is required to restore optimal performance.
While the SMART CUT Diamond Notch Grinding Wheel is primarily designed for semiconductor wafers, it can also be used on other hard and brittle materials, such as ceramics, certain metals, and glass. However, the best results are achieved when used within its intended semiconductor wafer notching applications.
⦁ Electroplated Diamond Wheels: Offer exceptional cutting efficiency, reduced wear, and finer precision for applications that require a higher level of accuracy. They are ideal for applications where frequent dressing or a more delicate finish is required.
⦁ Sintered Metal Bond Wheels: Provide superior durability and wear resistance, making them the ideal choice for more aggressive grinding applications that require faster material removal. They last longer under heavy use and are better suited for high-volume production.
Yes, the SMART CUT Diamond Notch Grinding Wheel is designed to be compatible with a wide variety of grinding machines commonly used in the semiconductor and precision machining industries. Always ensure that the grinding machine supports the specific size and specifications of the wheel you are using.
For optimal performance, we recommend using appropriate cooling fluids (such as water-soluble coolants or oils) to reduce heat generation during the grinding process. Proper cooling helps prevent overheating, which can affect wheel life and performance, as well as ensure a smoother and more consistent grinding result.
While diamond grinding wheels generally have limited reconditioning possibilities compared to other types of grinding wheels, the SMART CUT Diamond Notch Grinding Wheel can be maintained and refreshed using the proprietary AD-C dressing technology. This technology helps expose fresh diamond particles and ensures optimal performance over time, reducing the need for reconditioning.
⦁ Shank Diameter Tolerance: h6, ensuring precise fitment and stable performance during grinding operations.
⦁ Deflection Accuracy: ≥ 5 µm, maintaining high precision throughout the grinding process.
⦁ Groove Shape Tolerance: ≥ 1 degree at aperture angle, ensuring the highest notch accuracy.
The number of grooves on the SMART CUT Diamond Notch Grinding Wheel can be customized to suit your specific application needs. Single groove designs are suitable for simpler, single-notch applications, while multi-groove designs can be used for more complex, multi-notch operations. Having multiple grooves allows for improved efficiency and precision when processing semiconductor wafers with multiple notch requirements.
The maximum operating speed (RPM) for the SMART CUT Diamond Notch Grinding Wheel should be determined based on the specific diameter and application requirements. Typically, higher speeds are used for finer grain sizes, while slower speeds may be appropriate for coarse grinding. Always refer to the product specifications for the specific wheel you are using to ensure safe operation.
⦁ Finer Grain Sizes (e.g., #1500 mesh): Provide a smoother finish and are ideal for precision grinding applications where high surface quality is critical.
⦁ Coarser Grain Sizes (e.g., #600 mesh): Offer faster material removal rates, making them suitable for heavy-duty grinding applications that prioritize speed over surface finish.
Yes, SMART CUT offers custom sizes and specifications based on your specific needs. If you have unique wafer sizes, groove configurations, or bond requirements, we can work with you to create a tailored solution that meets your operational demands.
When using any grinding wheel, including the SMART CUT Diamond Notch Grinding Wheel, always adhere to the following safety precautions:
⦁ Wear appropriate personal protective equipment (PPE) such as safety goggles, gloves, and hearing protection.
⦁ Ensure that the grinding wheel is properly mounted and balanced to prevent vibration or instability.
⦁ Follow the manufacturer’s guidelines for maximum operating speeds (RPM) and avoid exceeding them.
⦁ Use proper cooling to reduce heat build-up and prevent damage to both the wheel and workpiece.
INDUSTRIES USED IN
Tab Content
ACCESSORIES
Tab Content
USAGE RECOMMENDATION
Tab Content
Features:
- Multi Electroplated Diamond Coating: The multi-layered electroplated diamond coating delivers outstanding cutting efficiency and minimal wear, offering consistent performance over a long lifespan.
- Stainless Steel Core: Provides enhanced stability and strength, reducing the risk of deformation under high grinding forces.
- Non-contaminated Nickel Deposit Bond: Ensures a strong bond that maintains the integrity of the material being processed, preventing contamination during grinding.
- Precision Angles and Depth: Customizable to meet specific application needs, with available angles of 11°, 20°, and 22° and depth options of 1.09 mm and 0.43”.
- Diamond Mesh Range: Available in 600-1500 mesh sizes, catering to a variety of semiconductor wafer notching requirements.
- Groove Types: Available in both F and R-type grooves for flexible customization in notch grinding processes.
Application:
SMART CUT ® Single & Multi Layered Electroplated Diamond notch grinding wheel is specifically designed for the semiconductor industry, ideal for precision grinding of wafers made from materials such as Silicon, Silicon Carbide, Gallium Arsenide, and Sapphire. The electroplated construction ensures high cutting efficiency with minimal wear and excellent finish, making it an excellent choice for wafer notching operations.
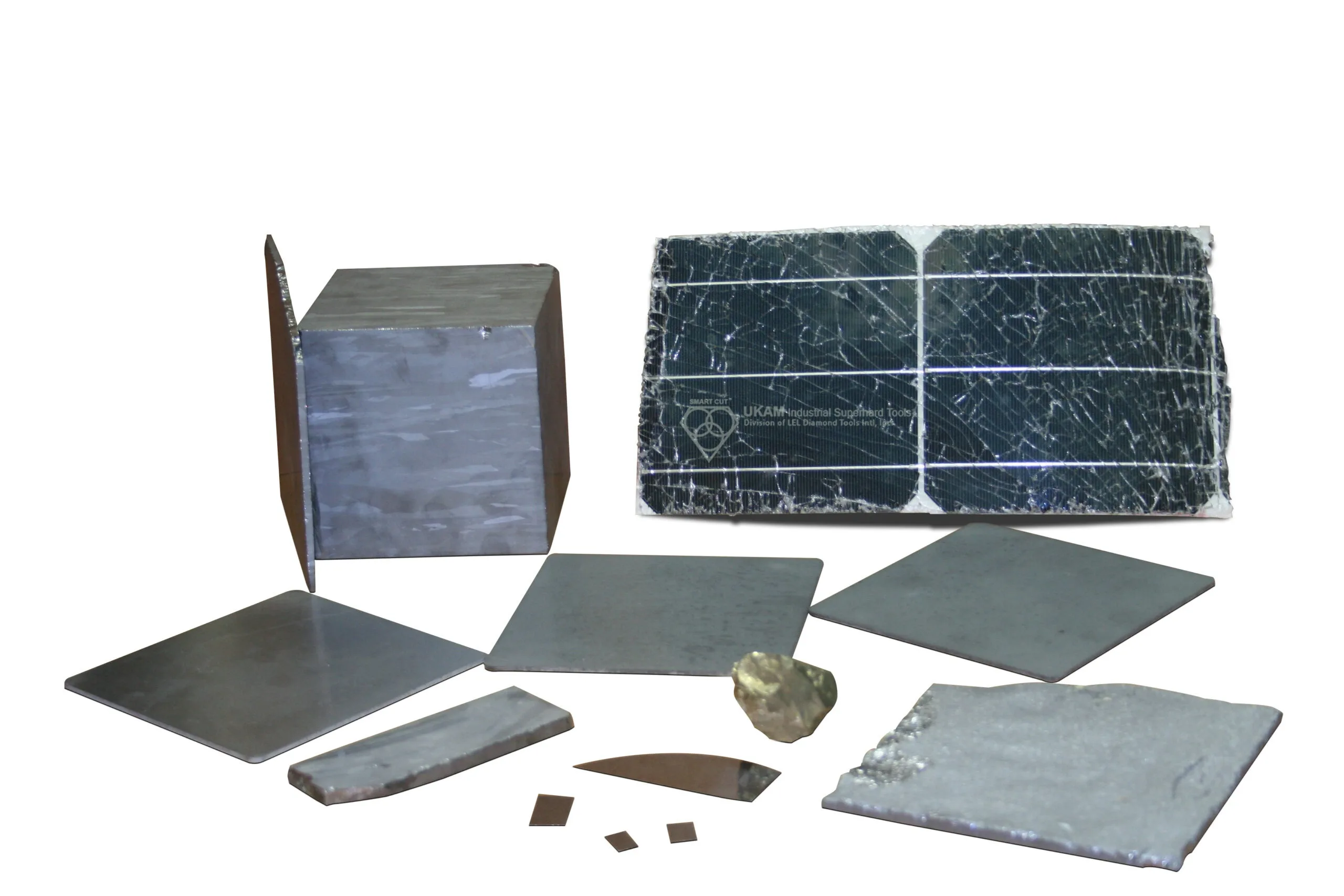
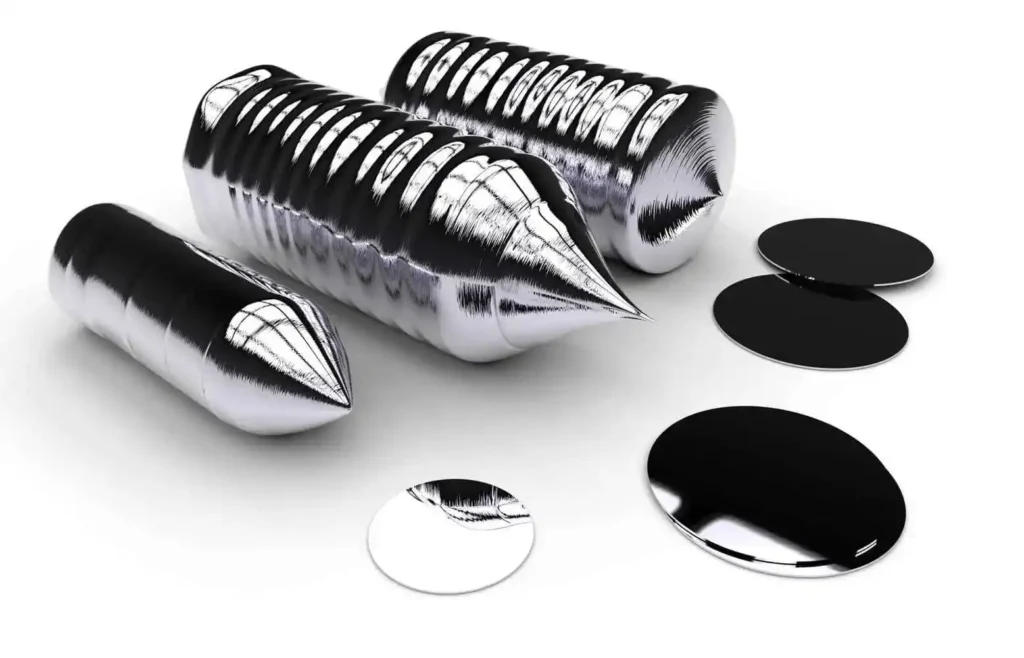
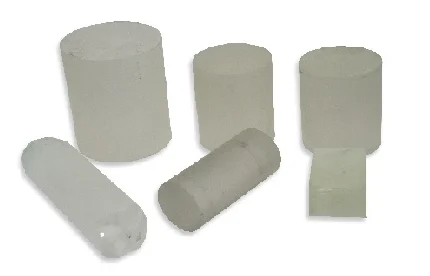
Advantages:
- Precision and Durability: Designed for high-precision and long-lasting performance in semiconductor wafer notching.
- Minimal Wear: Electroplated diamond coating reduces wear and tear, ensuring consistent grinding results over time.
- Flexibility: Customizable in terms of groove types and depth, suited for various types of semiconductor wafers.
About Nickel Bond
(Electroplated) Tools
Electroplated (nickel bond) diamond products usually have a single layer of diamonds, held by a tough durable nickel alloy. Nickel is frequently used as a base for plating diamond. Because of its excellent strength, toughness and flexibility during the plating process. Electroplated diamond products are able to retain their original shape and dimensions thought their working life. Unlike sintered (meal bond) or resin bond diamond products, where diamond particles are buried in bond and held together by metal or resin binder deep inside.
Electroplating allows diamond particles to protrude from the bond matrix, providing a free, faster cutting action with minimum heat generation.
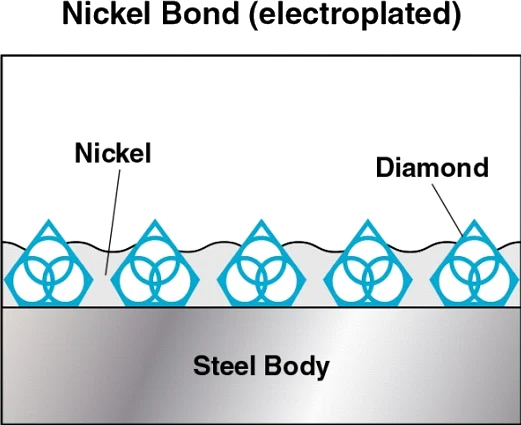
Electroplated Diamond Products Manufactured by UKAM Industrial are Multi Layered. They have 3 layers of diamonds, not just 1 layer of diamonds like conventional electroplated diamond tools.
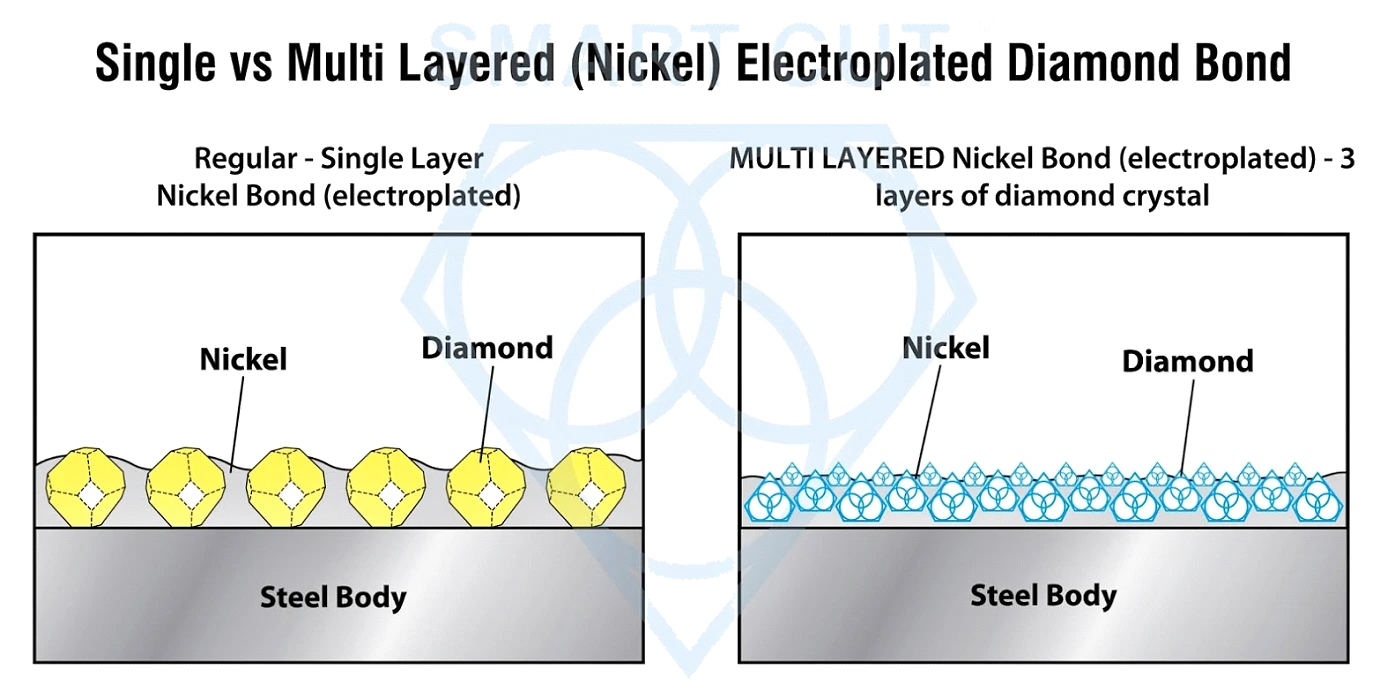
Multi Layered
Electroplated Diamond & CBN Coatings
They have several layers of diamonds, held by a tough durable nickel alloy. Providing high diamond concentration, better diamond crystal retention and maximum diamond particle (grit) exposure/protrusion ratio. This provides freer, faster cutting action with minimum heat generation. Advantages of this type of technology include: longer tool life, more uniformity in performance, less stress to material being worked on, minimum material deformation, and better preservation of true material micro structure. This is specially important for more delicate, sensitive applications such as: glass, crystals, silicon wafers, carbon composites, sapphire, etc.
Electroplating is the only bond that allows different diamond crystal protrusion/exposure through use of different coating thicknesses. Usually the exposure ratio is based on the application (materials to be cut) The final specification depends primarily on the machining task and the associated necessary chip clearance space. For high-speed grinding the coating thickness should be about 30 to 40% of the grit particle diameter, when grinding or cutting glass fibre-reinforced plastics 30 to 50%, when machining ceramic material and cemented carbide 60 to 70%, and when machining stone up to 100%.
How SMART CUT® Bond Works?
Step 1
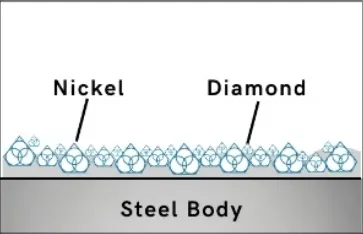
Sharpest And Finest Quality Diamonds
Diamonds or CBN Crystals are activated only at the exposed layer. As Bond Matrix layer begin to wear out, diamonds in a new Bond Matrix layer are immediately activated, substituting the already used up diamond layer. The SMART CUT® Bond Diamond Bond makes sure every diamond is in the right place. and at the right time, working where you need it most.
Step 2
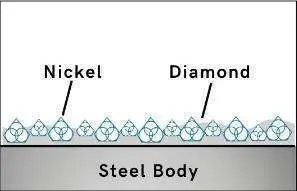
Diamonds or CBN Crystals
The newly exposed diamonds don’t effect diamonds already working on the material. Unlike many other diamond bonds, diamonds in a SMART CUT® remains sharp and grow sharper with each cut, prolonging product life and consistent performance.
Step 3
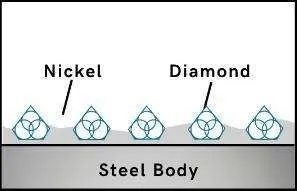
Advanced Formulated Open Diamond Bond Design
This advanced formulated open diamond bond design insures minimal chipping, fast
cut, constant speed of cut, minimal cutting noise, and most important of all, consistent performance.
About Diamond Notching Wheels
Diamond notch grinding wheels are versatile tools used in semiconductor manufacturing for both notching and edge grinding. These wheels are designed to create precise grooves or notches on semiconductor wafers, which are essential for singulation and dicing. In addition to this, they are also used for edge grinding, which plays a crucial role in preparing the wafer for subsequent processing.
When used for edge grinding, diamond notch grinding wheels help smooth rough or jagged edges that result from the wafer slicing process. The edges of wafers are often fragile, and rough edges can lead to breakage during handling or further processing. By using diamond wheels for edge grinding, these edges can be precisely smoothed, reducing the risk of chipping or fracturing. This ensures that the wafer can be handled more safely and processed with higher efficiency in later stages.
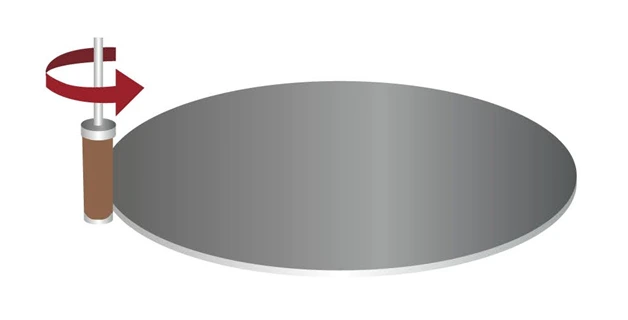
Edge grinding with diamond notch grinding wheels also ensures that the wafer maintains its geometry and dimensions. It allows the wafer to retain its integrity, even after the edges are ground, which is vital for processes like dicing. When wafers are later diced into individual chips, a clean, smooth edge helps the dicing saw make a more precise cut along the notches, reducing stress on the material and improving the overall yield.
The precision provided by diamond abrasive wheels ensures that the edges are ground uniformly and with minimal material removal, which is important for maintaining the wafer's structure. Additionally, grinding the edges of the wafer creates a smoother surface, making it less likely to sustain damage during handling or automated processing. This not only improves the quality of the wafer but also prevents defects from arising later in the process.
Diamond notch grinding wheels offer long tool life due to the durability of the diamond abrasives, which means they can be used for both notching and edge grinding over extended periods without frequent replacements. The tools also provide high precision, which is crucial for semiconductor manufacturing, where even small deviations can lead to defects or inefficiencies in production. As a result, the use of diamond notch grinding wheels in edge grinding helps ensure that semiconductor wafers are properly prepared for the next stages of processing and ultimately results in higher-quality ICs.
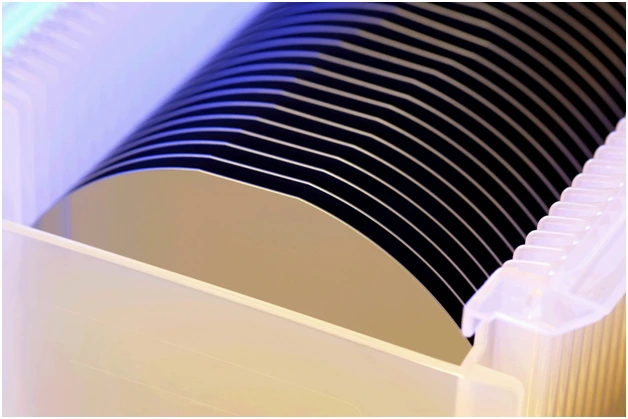
Coolants play an essential role in edge grinding, minimizing thermal stress and flushing away silicon particles from the grinding interface. This prevents overheating and reduces the risk of surface contamination and damage. An excellent coolant for this application.
SMART CUT® HD-2 is a synthetic coolant specifically designed for the cutting of semiconductor materials, including sapphire, silicon, germanium, single-crystal SiC, and II-VI crystals. This coolant offers excellent cut rates and imparts outstanding surface finishes with reduced warp and total thickness variation (TTV). It is ideal for diamond abrasive cropping, squaring, and wafering of silicon ingots and wafers.
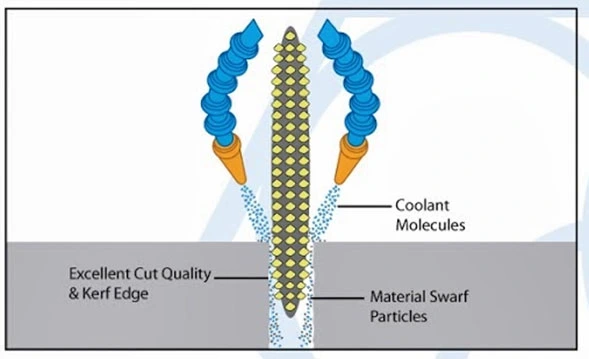
Diamond Notch Grinding Wheels Electroplated vs. Metal
Sintered (Metal Bond) Table of Comparison
Attribute |
Electroplated Metal Bond |
Sintered Metal Bond |
---|---|---|
Bond Type |
Electroplated coating of metal (e.g., nickel) |
Metal matrix sintered at high temperature |
Abrasive Durability |
High precision, but wears faster |
Durable with consistent abrasive exposure |
Wear Rate |
Higher wear rate due to less durable bond |
Lower wear rate, lasts longer |
Precision |
Very high precision in notching |
High precision, but can wear more slowly |
Tool Life |
Shorter tool life compared to sintered wheels |
Longer tool life, more durable |
Cutting Performance |
Effective for finer notching and precise cuts |
Excellent cutting performance, especially for harder materials |
Cost |
Lower cost |
Higher cost |
Applications |
Ideal for low-volume, precision work or intricate notching |
Used in high-volume manufacturing where long-lasting tools are needed |
Cooling Efficiency |
Requires more cooling for optimal performance |
Better cooling efficiency due to larger gaps between abrasives |
Heat Resistance |
Lower heat resistance, may suffer from excessive heat buildup |
Higher heat resistance, performs better under extreme conditions |
Related Products
SMART CUT® Diamond Cylindrical Grinding Wheels
SMART CUT® Diamond Cylindrical Grinding Wheels are engineered for the precise peripheral grinding of silicon ingots, making them an ideal choice for industries such as semiconductors, electronics, automotive, and photovoltaics. These high-performance grinding wheels are designed to process the outer surfaces of silicon ingots, ensuring accurate orientation flats are created, which are essential for subsequent processing steps. The addition of the orientation flat, a marked edge indicating the crystallographic plane of the wafer, is crucial for the wafer's alignment in future manufacturing processes.
During the post-slicing phase, wafers undergo shaping and smoothing through peripheral grinding.
SMART CUT® Diamond Edge Grinding Wheels (Electroplated)
SMART CUT® Diamond Edge Grinding Wheels are engineered to deliver exceptional performance for precision grinding applications, providing superior results in both rough and fine grinding. These wheels are ideal for use in industries that require highly accurate EDM processing and consistent wafer-to-wafer results. Manufactured with synthetic diamond grit, SMART CUT® wheels offer improved surface roughness and extended tool life due to their tightly controlled diamond distribution and uniform bond structure.
Band Saw Blades
SMART CUT® Braised Bond Diamond Band Saw Blades
ID blades
Diamond Wire
SMART CUT Diamond wire produces minimum kerf loss, less sub-surface damage, and contamination free coolant. Used for precision cutting of various types of artificial crystal, ceramic, quartz glass, monocrystalline silicon, polycrystalline silicon, sapphire and special metal materials. Diamond Wire cutting is an environmentally friendly cutting process as it eliminates slurry recycling and disposal issues.
It is widely used for slicing artificial crystals, ceramics, quartz glass, monocrystalline and polycrystalline silicon, sapphire, and specialty metals. The design provides high dimensional accuracy and smooth surfaces, often eliminating the need for extensive secondary processing.
SMART CUT® HD Synthetic Low IFT Coolant/Lubricant For Diamond Wire Sawing Silicon
SMART CUT® is a synthetic coolant specifically designed for the cutting of semiconductor materials, including sapphire, silicon, germanium, single-crystal SiC, and II-VI crystals. This coolant offers excellent cut rates and imparts outstanding surface finishes with reduced warp and total thickness variation (TTV). It is ideal for diamond abrasive cropping, squaring, and wafering of silicon ingots using ID, band, and wire saws. SMART CUT® HD-2B can also be used as a non-re-circulating edge grinding coolant or lubricant for silicon wafers and ingots.
DIAMOND BACKGRINDING WHEELS
SMART CUT® Diamond Backgrinding Wheels are designed for precision thinning and flattening of silicon wafers, glass, and ceramic substrates. These high-performance wheels are used on backgrinding machines, including models from Disco, Okamoto, Strasbaugh, and other leading manufacturers. Available in sizes ranging from 8” to 14” O.D., they are engineered to handle a wide range of materials and applications, from semiconductor wafers to microelectronic packages.
Recently Viewed Products
ARE YOU USING RIGHT ID CUTTING BLADES
FOR YOUR APPLICATION?
LET US
HELP YOU
HAVING ISSUES WITH
YOUR CURRENT ID CUTTING BLADES?
Knowledge Center
08
Jul
Manufacturing Processes for Silicon Semiconductors From Ingot to Integrated Circuit
Share this Article with Friend or Colleague
1. Ingot Production
The journey begins with the creation of silicon ingots, which are pure silicon cylinders produced through methods like the Czochralski process. Once formed, these ingots undergo a...
08
Jul
The Comprehensive Guide to the Processes of Silicon Wafers Production
Share this Article with Friend or Colleague
The production of silicon wafers, an essential component in semiconductor manufacturing, involves several intricate steps to ensure precision and quality. This article explores the detailed processes depicted in...
- Unmatched Selection For Many Applications
- Superior Quality & Consistency
- Immediate Worldwide Delivery
- Technical Support & Expertise
- American Based Manufacturer
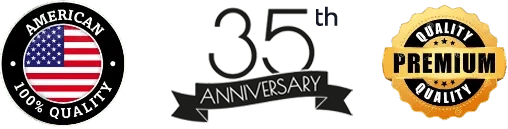

- Different Product
- Different Technology
- Different Company
- Expect MORE from your tools
Let Us HELP You!
Subscribe To Our Newsletter
Signup for email offers, updates, and more
Contact Us
- 25205 & 25201 Avenue Tibbits Valencia CA 91355 USA
-
Phone : (661) 257-2288
FAX : (661) 257 -3833 - lel@ukam.com
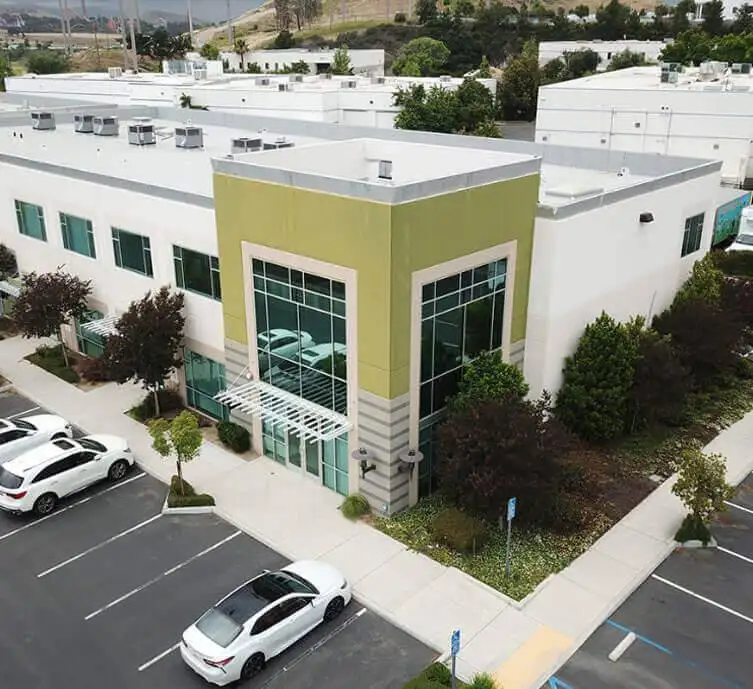
UKAM Industrial Superhard Tools is a U.S. High Technology, Specialty Diamond Tool & Equipment manufacturer. We specialize in producing ultra thin, high precision cutting blades, precision cutting machines diamond drills, diamond micro tools, standard & custom advanced industrial diamond tools and consumables.
- 25205 & 25201 Avenue Tibbits Valencia CA 91355 USA
-
Phone : (661) 257-2288
FAX : (661) 257 -3833 - lel@ukam.com
- 25205 & 25201 Avenue Tibbits Valencia CA 91355 USA
-
Phone : (661) 257-2288
FAX : (661) 257 -3833 - lel@ukam.com
DIAMOND TOOLS BY BOND
EQUIPMENT
KNOWLEDGE CENTER
OUR PRODUCTS
COMPANY
CUSTOMER SERVICE
Shipping Methods


Safe & Secure Payments

© Copyright 1990-2025. UKAM Industrial Superhard Tools – Terms of Use