-
0 items in quote
No products in the Quote Basket.
ID blades (Inside Diameter) Diamond Cutting Blades – SMART CUT Series
SMART CUT ID blades (inside diameter) diamond cutting plates are nickel bond product with diamond coating on the internal edge. Internal diameter is of the blade is what does the cutting. These blades are used for cutting large variety of ultra hard and brittle materials, with minimum amount of material loss. The high tensile strength stainless steel core provides excellent cutting quality and increased yield. SMART CUT series we provide large selecting of diamond sizes, kerf thickness, kerf shape, bond hardness for to best fit your specific application and requirements.
Description
Specifications
Frequently Asked Questions
Industries Used In
Accessories
Recommendations
Description
Unlike traditional blades, the cutting action is performed by the inside diameter, which is lined with premium quality diamonds. This arrangement ensures a concentrated cutting edge that reduces the material’s surface contact, thereby decreasing chipping and material waste.
Each blade is supported by a core made from high tensile strength stainless steel. This core not only contributes to the overall durability and longevity of the blade but also assists in maintaining a consistent cutting capability by preventing warping and vibrations during intense cutting sessions.
We offer a comprehensive range of diamond sizes to suit various material hardness and brittleness levels. Selecting the appropriate diamond size ensures optimal cutting performance and minimal kerf loss. Our SMART CUT™ SMART CUT ® ID blades can be customized in terms of kerf thickness and shape, accommodating the specific requirements of the materials being cut and the desired finish. Depending on the application, the hardness of the nickel bond can be adjusted. Softer bonds are typically used for harder materials to allow regular exposure of fresh diamonds, whereas harder bonds are suited for softer materials to extend the blade’s lifespan.
SMART CUT ® ID blades are ideal for industries and applications where precision and minimum amount of material loss is important, such as semiconductor manufacturing for wafer fabrication and microelectronic components where dimensional accuracy minimal kerf loss and minimal amount structural damage to material is required. optical and glass industries for cutting complex components used in optics and precision glass manufacturing, and material sciences.
Specifications
- Outside Diameters: 8″ (200mm) to 34″ (860mm)
- Blade Kerf Thickness: .005″ (0.127mm) to .010″ (.254mm)
- Inside Diameter: 3.25″ (82mm) to 12″ (305mm)
- Diamond Size: 60 mesh to 500 mesh
- Copy Type: Stainless Steel and High Speed Steel
- Diamond Concentration : High
- Application: Semiconductor Materials, Crystals, Ultra Hard & Brittle Materials, Optics and Composites
- Bond Type: Nickel Bond (Plated)
- Diamond Type: Synthetic or Natural
Frequently Asked Questions
- ID Diamond Blades: Designed for precision cuts from the inside, ideal for minimizing material loss in specialized applications.
- Diamond Wire Cutting: Uses a wire with diamond beads for cutting, suitable for large, long cuts and slicing through thick materials.
- Outside Diameter Cutting Blades: Feature diamond segments on the outer rim, commonly used for general cutting tasks.
- ID Diamond Blades: RPM recommendations vary by blade size and material but generally fall within the range of 5,000 to 10,000 RPM.
- Diamond Wire Cutting: Typically operates at lower RPMs, around 2,000 to 4,000 RPM, but varies based on wire thickness and material.
- Outside Diameter Cutting Blades: RPM recommendations depend on blade size, material, and machine specifications but often range from 5,000 to 15,000 RPM.
- ID Diamond Blades: Water-based coolants are commonly used to reduce heat and control dust during cutting.
- Diamond Wire Cutting: Water or specialized cutting fluids are used to lubricate the wire and control heat.
- Outside Diameter Cutting Blades: Water, oil, or air-based coolants may be used depending on the material being cut and the cutting process.
- ID Diamond Blades: Feed rates depend on the material, blade size, and machine, but they are generally slower due to the precision nature of ID cutting.
- Diamond Wire Cutting: Feed rates can be relatively fast for long cuts, with adjustments made for material hardness.
- Outside Diameter Cutting Blades: Feed rates vary based on blade diameter, material, and cutting machine but are typically faster than ID cutting.
- ID Diamond Blades: Offer high cut quality with minimal chipping, making them ideal for applications where precise, clean cuts are essential.
- Diamond Wire Cutting: Provides good cut quality but may have a slightly rougher surface finish compared to ID blades.
- Outside Diameter Cutting Blades: Cut quality varies based on blade type, material, and blade wear, with some potential for chipping, especially in harder materials.
- ID Diamond Blades: Ideal for intricate, smaller cuts, but can be used on larger materials as well.
- Diamond Wire Cutting: Well-suited for slicing through large materials, such as thick blocks or slabs.
- Outside Diameter Cutting Blades: Effective for a wide range of material sizes, with blade diameter and machine capacity being limiting factors.
- ID Diamond Blades: Replace when you notice a decline in cutting performance, visible wear on the blade, or signs of damage.
- Diamond Wire Cutting: Replace when the wire becomes worn or damaged, which can affect cut quality and safety.
- Outside Diameter Cutting Blades: Replace when the blade segments are worn, cracked, or chipped, as this can impact cutting efficiency and safety.
- ID Diamond Blades: Ideal for applications requiring precision, minimal material loss, and clean cuts, such as cutting sapphire, ceramics, and glass.
- Diamond Wire Cutting: Suitable for large-scale slicing, especially in materials like stone, composites, and silicon wafers.
- Outside Diameter Cutting Blades: Versatile for general cutting tasks, including concrete, asphalt, and metal cutting, with variations for specific materials and applications.
ID Diamond Blades are the preferred choice for applications prioritizing precision and minimal material loss. Their inside cutting design allows for accurate cuts with minimal waste.
ID Diamond Blades can be used for precision cuts in materials with varying hardness levels. Diamond Wire Cutting is suitable for a wide range of materials but may produce slightly rougher cuts. Outside Diameter Cutting Blades can cut materials with varying hardness but may require blade adjustments based on material properties.
All three cutting methods can generate dust, with ID Diamond Blades producing the least amount. Using appropriate dust control measures, such as water-based coolants and dust collection systems, is essential to minimize exposure and maintain a clean work environment.
ID Diamond Blades and Outside Diameter Cutting Blades can be used for bevel cuts or angled cuts by adjusting the cutting angle or the positioning of the material. Diamond Wire Cutting may not be as suitable for creating bevels due to its continuous wire design.
Cutting very thin materials with ID Diamond Blades may be challenging due to the blade’s thickness. Diamond Wire Cutting is more adaptable to slicing extremely thin materials, but care should be taken to prevent wire breakage.
All three cutting methods can be used for curved cuts, with ID Diamond Blades being particularly well-suited for creating precise circles or arcs. Diamond Wire Cutting and Outside Diameter Cutting Blades can also be used for curved cuts but may require special techniques or equipment for accuracy.
Diamond Wire Cutting and Outside Diameter Cutting Blades can be adapted for underwater cutting with appropriate equipment and safety measures. ID Diamond Blades are less commonly used underwater but may be suitable for specific applications with proper precautions.
ID Diamond Blades are well-suited for cutting brittle materials with minimal risk of cracking or delamination. Diamond Wire Cutting can also be used with care, but the continuous wire may generate more vibrations. Outside Diameter Cutting Blades may have a higher risk of causing cracks or delamination, depending on the material’s properties.
The choice of cutting method depends on factors such as the material, desired cut quality, precision requirements, material size, and available equipment. Consult with experienced professionals or blade manufacturers for guidance in selecting the most suitable method for your specific cutting needs.
ID Diamond Blades are generally better for heat-sensitive materials due to their precision and reduced heat generation. Diamond Wire Cutting can generate heat, especially when cutting hard materials, but adjustments can be made to control temperature. Outside Diameter Cutting Blades may produce more heat and require adequate cooling.
All three cutting methods can cut materials with embedded features, but caution is required to avoid damage to the cutting equipment. Proper planning, such as adjusting cutting parameters and monitoring progress, is crucial when cutting materials with hidden elements.
Safety is paramount when using any cutting method. Key safety considerations include wearing appropriate personal protective equipment (PPE), following safety guidelines provided by the manufacturer, ensuring proper machine operation and maintenance, and maintaining a safe working environment to prevent accidents.
All three cutting methods can cut extremely hard materials, but the choice depends on factors like material thickness and precision requirements. ID Diamond Blades are ideal for precision cuts, while Diamond Wire Cutting excels in slicing through thick and hard materials. Outside Diameter Cutting Blades are suitable for a wide range of hard materials.
The lifespan varies based on factors like material, blade quality, and usage. To maximize longevity, follow manufacturer recommendations, use the appropriate blade for your material, adjust cutting parameters as needed, maintain proper cooling, and perform regular maintenance to keep the cutting equipment in good condition.
Yes, Diamond Wire Cutting requires attention to wire tension, which affects cutting performance and safety. Regularly inspect and maintain the wire’s tension to ensure smooth operation. Follow manufacturer guidelines for wire tensioning and maintenance.
ID Diamond Blades are well-suited for creating small, intricate designs and patterns in materials like tile or glass art due to their precision. Diamond Wire Cutting and Outside Diameter Cutting Blades can also be used for such applications with the right techniques and equipment.
Cutting multiple layers or laminated materials with these methods may be possible but can pose challenges, such as achieving clean cuts and avoiding delamination. Proper technique, equipment selection, and material preparation are critical for successful cutting in such scenarios.
Proper disposal of used blades, wires, and associated materials is essential. Depending on the materials being cut, they may be considered hazardous waste. Adhere to local regulations and guidelines for disposing of cutting-related materials in an environmentally responsible manner.
Yes, ID Diamond Blades are well-suited for creating intricate shapes and patterns in materials for artistic or decorative purposes due to their precision. Diamond Wire Cutting and Outside Diameter Cutting Blades can also be used for artistic applications with the right techniques and equipment.
ID Diamond Blades are excellent for cutting materials with fragile or sensitive surfaces, as they minimize the risk of damage. Diamond Wire Cutting can be used with care, while Outside Diameter Cutting Blades may require additional precautions to prevent surface damage.
When using these cutting methods in cleanroom environments, consider factors like dust control, equipment cleanliness, and adherence to cleanroom protocols. Follow industry-specific guidelines to ensure the cleanliness and integrity of the cleanroom environment.
Outside Diameter Cutting Blades are commonly used for retrofitting or modifying existing structures, as they are versatile and can cut through a variety of materials. However, ID Diamond Blades and Diamond Wire Cutting may also be used for specific retrofitting tasks with the right equipment and techniques.
Regular maintenance of the cutting equipment is essential to ensure optimal performance and safety. Follow manufacturer recommendations for equipment maintenance, including cleaning, lubrication, blade or wire tensioning, and inspection of critical components.
ID Diamond Blades can be used for cutting materials with complex geometries and contours, making them suitable for applications where precise shaping is required. Diamond Wire Cutting and Outside Diameter Cutting Blades can also be used for cutting materials with complex shapes with the right setup and techniques.
When working in temperature-sensitive environments, consider the effects of temperature on both the material being cut and the cutting equipment. Adjust cutting parameters, cooling methods, and equipment accordingly to maintain safe and efficient cutting processes.
Yes, all three cutting methods can be used for cutting materials with varying thicknesses, including sandwiched composites or layered structures. Adjustments to cutting parameters and techniques may be necessary to accommodate different thicknesses.
ID Diamond Blades and Outside Diameter Cutting Blades are relatively portable and easy to set up on various cutting machines. Diamond Wire Cutting may require more specialized equipment and setup due to the wire tensioning and guiding systems.
When working in confined spaces or areas with limited accessibility, ensure that the cutting equipment can be safely positioned and operated. Consider the dimensions of the equipment, the material being cut, and any safety measures required for confined space work.
Diamond Wire Cutting and Outside Diameter Cutting Blades can be adapted for underwater cutting tasks with the right equipment and precautions. ID Diamond Blades are less commonly used underwater but may have specific applications with proper safety measures.
Training and certification requirements may vary by location and industry. It is advisable for operators to receive proper training and certification in the safe and efficient use of cutting equipment, especially in industrial or professional settings.
Outside Diameter Cutting Blades are often used for the removal or dismantling of large structures like bridges or buildings. Diamond Wire Cutting can also be employed for such tasks, while ID Diamond Blades may be used for precision cutting within the structure.
Noise levels can vary depending on the specific equipment and materials being cut. Implementing noise reduction measures, such as using noise barriers, quieter cutting equipment, or hearing protection for operators, can help reduce noise pollution in the work environment.
ID Diamond Blades are well-suited for cutting materials with abrasive components, as they are designed for precision and durability. Diamond Wire Cutting can also handle such materials, while Outside Diameter Cutting Blades may require adjustments and monitoring for wear when cutting abrasive materials.
Yes, all three cutting methods can be used for removing or sectioning large, bulky materials. Diamond Wire Cutting is particularly effective for slicing through thick materials, while ID Diamond Blades and Outside Diameter Cutting Blades can also be used for such tasks with the appropriate equipment.
Yes, all three cutting methods can be used for cutting materials with irregular or uneven surfaces. Proper equipment setup and techniques can help accommodate irregular shapes and surfaces.
When transporting materials cut using these methods, secure packaging and handling protocols should be followed to ensure the integrity of the cut pieces. Specialized packaging and protective measures may be necessary for delicate materials like semiconductor wafers.
ID Diamond Blades and Outside Diameter Cutting Blades can be used for creating beveled edges or chamfers on materials for specific applications or aesthetic purposes. Diamond Wire Cutting may not be as suitable for creating bevels due to its continuous wire design.
When cutting in corrosive environments or working with corrosive materials, it is essential to select appropriate cutting equipment and materials that are resistant to corrosion. Regular cleaning and maintenance of the cutting equipment are also crucial to prolong its lifespan.
All three cutting methods can be used for cutting materials with complex internal structures, but the specific approach may vary depending on the complexity and the desired outcome. ID Diamond Blades are suitable for precision cuts in such materials, while Diamond Wire Cutting and Outside Diameter Cutting Blades can also be used with proper techniques.
Yes, there are various specialized accessories and attachments available to enhance the capabilities of these cutting methods. These may include laser guidance systems for precise cuts, dust extraction systems for dust control, and additional safety features.
Yes, ID Diamond Blades, Diamond Wire Cutting, and Outside Diameter Cutting Blades can all be used for creating intricate perforations or patterns in materials for various applications, including filtration, decorative designs, or functional purposes.
When using these cutting methods in research and development settings or for prototyping purposes, it is important to consider factors such as precision, material properties, and the desired outcomes. Adjustments to cutting parameters and techniques may be necessary to achieve specific research or prototyping goals.
While ID Diamond Blades may be used for precise cuts in materials with embedded electronics, Diamond Wire Cutting and Outside Diameter Cutting Blades should be used with caution to avoid damage to sensitive electronic components. Specialized equipment and techniques may be necessary for such tasks.
When working with materials where magnetic or electric fields must be preserved, select cutting methods and equipment that minimize interference with these fields. Shielding or insulating the cutting equipment may also be necessary to maintain field integrity.
ID Diamond Blades are suitable for creating intricate joints or connections between materials, especially when precision is required. Diamond Wire Cutting and Outside Diameter Cutting Blades can also be used for creating joints, but adjustments and techniques may be needed for complex assemblies.
When working with hazardous materials or in environments with potential health risks, follow safety protocols and guidelines for handling and disposal. Ensure that the cutting equipment and personnel are adequately protected, and adhere to all safety regulations and requirements.
ID Diamond Blades can be used for creating controlled fractures or cracks in materials with precision. Diamond Wire Cutting and Outside Diameter Cutting Blades may also be used for controlled fracturing, but the process may vary depending on the material and equipment used.
In aerospace applications, precision and material integrity are critical. These cutting methods can be used for aerospace materials, but it’s essential to follow aerospace industry standards and guidelines for quality control, safety, and material specifications.
ID Diamond Blades are often used for cutting materials with fragile or delicate coatings or surface treatments, as they minimize the risk of damage. Careful consideration of cutting parameters and techniques is required for Diamond Wire Cutting and Outside Diameter Cutting Blades to avoid compromising surface treatments.
When working in high-vibration environments, consider the impact on cutting equipment stability and cutting precision. Secure the cutting equipment to minimize vibration-induced errors and ensure safe operation.
All three cutting methods can be used for cutting materials with embedded fluids or liquids, but precautions must be taken to contain or control the liquid during the cutting process. Safety measures should be in place to prevent spillage or contamination.
When cutting materials that may generate toxic fumes or gases, ensure proper ventilation and use appropriate personal protective equipment (PPE) to protect operators from inhalation hazards. Follow safety guidelines and regulations for working with hazardous materials.
ID Diamond Blades are well-suited for creating intricate details in materials, including jewelry and microfabrication. Diamond Wire Cutting and Outside Diameter Cutting Blades can also be used for such applications with specialized setups and techniques.
When cutting composite materials with specific fiber orientations, consider the orientation and arrangement of fibers. Adjust cutting parameters and techniques to achieve clean cuts while minimizing fiber damage. Proper dust control is also crucial when working with composite materials.
ID Diamond Blades are suitable for creating controlled grooves or channels in materials for applications like microfluidic devices. Diamond Wire Cutting and Outside Diameter Cutting Blades can also be used for such purposes with careful control of parameters and precise equipment setup.
When cutting materials under stress, tension, or compression for testing or analysis, it’s crucial to control the loading conditions and ensure that the cutting process does not introduce additional stress or alter the material properties. Consult relevant testing standards and guidelines for best practices.
When cutting materials that may release hazardous or volatile gases, it’s essential to employ appropriate ventilation and gas detection systems in the workspace. Operators should wear suitable respiratory protection, and safety protocols should address potential gas hazards.
The selection of blade size or wire thickness depends on factors such as material thickness, desired precision, and cutting machine specifications. Consult with blade or wire suppliers and consider the specific requirements of your cutting task to choose the most suitable size.
While ID Diamond Blades are suitable for creating microscale features, achieving nanoscale features typically requires specialized techniques such as focused ion beam (FIB) milling or electron beam lithography. These methods are more precise at the nanoscale level.
Specialized cutting fluids or coolants may be recommended for specific materials or applications to improve cutting efficiency and extend blade or wire life. Consult with coolant suppliers or blade manufacturers for recommendations tailored to your cutting needs.
ID Diamond Blades are suitable for cutting hardened materials, as their precision minimizes the risk of damage. Diamond Wire Cutting and Outside Diameter Cutting Blades can also be used for such materials with adjustments in cutting parameters and techniques.
Yes, these cutting methods can be used for removing or trimming excess material from 3D-printed or additive manufacturing components. The choice of method depends on the material and precision requirements of the task.
Yes, these cutting methods can be used for cutting materials with varying densities. Adjustments to cutting parameters and techniques may be needed to accommodate the different material properties within the structure.
When working with materials with high thermal conductivity, consider the potential for heat buildup during cutting. Adequate cooling and efficient heat dissipation methods are essential to maintain cutting efficiency and minimize thermal stress on the material.
Yes, these cutting methods can be used for creating controlled fractures or pre-cracks in materials for various purposes, including geological sampling. Precise control of the cutting process is important to achieve desired fracture patterns.
In applications where strict tolerances and dimensional accuracy are critical, ensure that the cutting equipment, tooling, and process are calibrated and monitored to meet the required precision standards. Quality control measures should be in place to verify dimensional accuracy.
ID Diamond Blades are suitable for cutting materials with specific surface coatings or treatments, as they minimize the risk of damage to the coatings. Diamond Wire Cutting and Outside Diameter Cutting Blades may require special care to avoid compromising surface treatments.
When cutting materials with anisotropic properties, be aware of the material’s directional characteristics. Adjust cutting parameters and techniques to account for anisotropy and ensure consistent and desired outcomes.
ID Diamond Blades are suitable for cutting materials with high internal stresses, as their precision minimizes the risk of unintended fractures. Diamond Wire Cutting and Outside Diameter Cutting Blades can also be used for such materials with care to avoid inducing additional stress.
When working with materials prone to chemical reactions or degradation upon exposure to air or moisture, it’s essential to minimize the exposure time during cutting. Implementing controlled environments or specialized cutting chambers can help mitigate these risks.
Yes, these cutting methods can be used for materials with varying hardness gradients, but adjustments in cutting parameters may be necessary to address the different hardness levels within the material.
When cutting materials with unique electrical properties, consider the potential impact of the cutting process on these properties. Use appropriate grounding and insulation techniques to protect the material’s electrical characteristics.
ID Diamond Blades are ideal for applications requiring minimal kerf width or material waste, such as semiconductor wafer dicing. Diamond Wire Cutting and Outside Diameter Cutting Blades may also be used for such purposes with consideration for kerf width and precision.
Typical safety measures include providing operators with appropriate personal protective equipment (PPE), ensuring proper equipment maintenance and setup, implementing safety protocols, and conducting operator training. Safety assessments and risk mitigation plans are also essential.
Yes, these cutting methods can be used for creating textured or patterned surfaces on materials to enhance properties like friction or adhesion. The choice of method depends on the material and the desired texture or pattern.
When cutting highly reflective materials, consider the potential for glare or reflections. Implementing anti-reflective measures, such as using non-reflective coatings or positioning the cutting equipment strategically, can help mitigate issues related to reflections.
While these cutting methods can be used in production environments, the cutting speed may vary based on the material and equipment. Diamond Wire Cutting and Outside Diameter Cutting Blades can provide faster cutting speeds compared to ID Diamond Blades in some cases.
When working with materials that produce hazardous or noxious odors during cutting, it’s essential to ensure proper ventilation and use suitable respiratory protection for operators. Controlling odors and emissions may require specialized exhaust systems or enclosures.
ID Diamond Blades are suitable for cutting materials prone to work hardening or changes in properties, as they minimize mechanical stresses. Diamond Wire Cutting and Outside Diameter Cutting Blades can also be used for such materials with care to avoid excessive stress.
When cutting materials with low thermal conductivity, consider the potential for heat buildup. Adequate cooling and efficient heat dissipation methods are crucial to maintain cutting efficiency and prevent thermal damage to the material.
Yes, these cutting methods can be used for creating fine channels or microfluidic networks in materials for biomedical or lab-on-a-chip applications. ID Diamond Blades are particularly well-suited for precise channel fabrication.
When cutting highly abrasive materials, the wear on cutting tools should be considered. Diamond tools, such as ID Diamond Blades, are more resistant to wear when cutting abrasive materials. However, regular inspection and maintenance of the cutting tools may be necessary.
Yes, these cutting methods can be used for materials with varying degrees of hardness. Adjustments to cutting parameters and techniques may be needed to address the different hardness levels within the material.
When working with materials sensitive to vibrations or shock, select cutting equipment that minimizes vibration. Isolation techniques, such as using vibration-damping mounts, may be necessary to protect delicate components.
Yes, these cutting methods can be used for creating custom shapes or profiles in materials, making them suitable for prototyping or small-scale production of specialized components. ID Diamond Blades are particularly precise for such tasks.
When working in environments with flammable materials or explosive atmospheres, ensure that all equipment and tools are intrinsically safe and compliant with relevant safety standards. Implement safety protocols and follow guidelines to prevent ignition sources and minimize risks.
Achieving submicron or nanoscale precision typically requires specialized nanofabrication techniques, such as electron beam lithography or focused ion beam (FIB) milling. ID Diamond Blades, Diamond Wire Cutting, and Outside Diameter Cutting Blades may not reach such precision levels.
When cutting materials with specific acoustic properties, consider the impact of the cutting process on these properties. Use appropriate damping or insulation techniques to maintain acoustic characteristics.
ID Diamond Blades are ideal for applications where minimal damage to the surrounding material is crucial, as they provide precision and control. Diamond Wire Cutting and Outside Diameter Cutting Blades may also be used with care and specialized techniques for such tasks.
When working with materials with unique optical properties, consider the potential impact of the cutting process on optical quality. Choose appropriate cutting methods and equipment that minimize optical distortion and maintain desired optical characteristics.
Yes, these cutting methods can be used for creating small, intricate features on materials for microelectronics or MEMS applications. ID Diamond Blades are particularly suitable for achieving precision in such tasks.
When working with ESD-sensitive materials, ensure that the cutting equipment and environment are ESD-safe. Use grounded equipment and follow ESD protection protocols to prevent damage to sensitive components.
Industries Used In
Tab Content
Accessories
Showing 1 – -1 of 13 results Showing all 13 results Showing the single result No results found
Sort by Price low to high
Filters Sort results
Reset Apply
Item No:UKAMDRST4 Description: Recommended for use in Diamond Tools 150 Grit Size (mesh size) or finer. Price: $15.39 |
Item No:UKAMDRST7 Description: Recommended for coarser grits found in segment wheels, core drills, or Blanchard grinding. Excellent performance on 120 grit tools. Price: $15.99 |
Item No: Description: 5/8″-11″ thread. Fits into drill press chuck. Shank adapter threads into 5/8″-11″ female thread of diamond drill. Can be used with any other tool with 5/8″-11″ thread. Price: $22.46 |
Item No: Description: 5/8″-11″ thread. Fits into drill press chuck. Shank adapter threads into 5/8″-11″ female thread of diamond drill. Can be used with any other tool with 5/8″-11″ thread. Price: $26.72 |
Item No:SMARTC1G Description: SMART CUT® General Materials Formula Synthetic Water Soluble Coolant Price: $34.81 |
Item No:UKAMDRST5 Description: Recommended for use in Diamond Tools 150 Grit Size (mesh size) or finer. Price: $39.47 |
Item No:UKAMDRST8 Description: Recommended for coarser grits found in segment wheels, core drills, or Blanchard grinding. Excellent performance on 120 grit tools. Price: $39.47 |
Item No:SMARTC2G Description: SMART CUT® General Materials Formula Synthetic Water Soluble Coolant Price: $99.81 |
Item No: Price: $154.87 |
Item No: Price: $154.87 |
Item No: Price: $235.00 |
Item No:SMARTC4A Description: SMART CUT® General Materials Formula Synthetic Water Soluble Coolant Price: $317.41 |
Item No:SMARTC7A Description: SMART CUT® General Materials Formula Synthetic Water Soluble Coolant Price: $1,745.00 |
Recommendations
Step 1: Material Selection and Preparation
- Begin by selecting the appropriate ID Diamond Blade based on the material you intend to cut. Ensure that the blade is compatible with the material’s hardness, thickness, and other characteristics.
- Inspect the material for defects, cracks, or contaminants on the surface. Address any issues before proceeding with cutting.
- Ensure that the ID Diamond Blade is appropriate for the material you intend to cut. These blades are commonly used for cutting materials like sapphire, advanced ceramics, glass boules, and large pieces of material. Verify compatibility before proceeding
- Select the appropriate blade size and thickness based on the material’s thickness and cutting requirements. Smaller blades may offer better precision for intricate cuts, while larger blades are suitable for thicker materials.
Step 2: Blade Mounting
- Mount the ID Diamond Blade securely onto a compatible cutting machine or saw. Follow the manufacturer’s instructions for blade installation, ensuring the blade is properly centered and tensioned.
- Properly mount the ID Diamond Blade on a compatible cutting machine or saw with the correct arbor size and specifications. Follow manufacturer instructions for blade installation and tensioning.
Step 3: Blade Cooling and Lubrication
- Set up a suitable coolant or lubrication system to maintain the blade’s temperature and prevent overheating during cutting. Ensure that the coolant flow rate and temperature are adjusted as needed for the specific material.
- Use a suitable coolant or lubrication system to dissipate heat generated during cutting. Cooling is essential to prevent overheating of the blade and material, which can lead to damage or reduced cutting efficiency.
Step 4: Cutting Speed and Feed Rate:
- Adjust the cutting speed and feed rate based on the material’s characteristics, thickness, and the blade’s specifications. Avoid excessive cutting speeds or feed rates, which can result in poor cut quality or blade wear.
Step 5: Safety Preparations
- Prioritize safety by providing operators with appropriate personal protective equipment (PPE), including safety glasses, hearing protection, and any additional gear required for your specific cutting environment.
- Ensure that the cutting area is well-ventilated, well-lit, and free from potential hazards.
Step 6: Precision and Control:
- ID Diamond Blades are known for their precision. Take advantage of this by using precise cutting machines and ensuring proper alignment and control during cutting operations.
Step 7: Workpiece Clamping and Alignment
- Secure the material to be cut using appropriate clamping or support mechanisms to prevent movement or vibration during cutting. Proper alignment is crucial for achieving precise cuts.
Step 8: Cutting Parameters Adjustment
- Adjust the cutting parameters, including cutting speed and feed rate, based on the material’s characteristics and thickness. Consult the blade manufacturer’s recommendations for initial settings.
Step 9: Blade Inspection
- Before starting the cutting operation, inspect the ID Diamond Blade for any signs of wear, damage, or deviations from the desired specifications. Replace the blade if necessary.
Step 10: Trial Cuts
- If you are working with an unfamiliar material or setup, consider conducting trial cuts on a sample piece to fine-tune cutting parameters and verify that the blade is performing as expected.
Step 11: Cutting Operation
- Start the cutting machine and carefully guide the material through the ID Diamond Blade. Maintain control and monitor the cut quality throughout the operation.
- Ensure that the blade remains adequately cooled and lubricated during the cutting process.
Step 12: Material Inspection
- After completing the cut, inspect the material for the quality of the cut surface. Look for signs of chipping, cracks, or any other defects.
Step 13: Blade Maintenance
- Clean the ID Diamond Blade after each cutting operation to remove debris and residues. Proper maintenance helps maintain blade performance.
- Periodically dress the blade to maintain its sharpness and cutting efficiency.
Step 14: Operator Safety
- Turn off the cutting machine and ensure that all safety protocols are followed when the cutting operation is complete. Operators should continue to wear PPE until they exit the cutting area.
Step 15: Documentation
- Maintain detailed records of the cutting parameters used, material specifications, blade maintenance activities, and any incidents or deviations from standard procedures. Documentation is essential for quality control and troubleshooting.
Step 16: Blade Storage
- Store the ID Diamond Blade in a clean, dry, and secure location when not in use. Handle the blade with care to avoid damage to the diamond coating or the blade itself.
Step 17. Blade Dressing and Alignment:
- Periodically check and dress the ID Diamond Blade to maintain its sharpness and cutting efficiency. Ensure the blade is properly aligned with the material to achieve accurate cuts.
Step 18. Workpiece Orientation:
- Consider the orientation of the workpiece and the direction of the cut to achieve the desired results. Adjust the cutting machine or setup accordingly.
Step 19. Blade Cooling System Maintenance:
- Regularly inspect and maintain the blade cooling system, including coolant flow rate and temperature control. Proper cooling is essential for preventing blade overheating and material damage.
ID Cropping Blade Parameters
Material |
Diamond Micron Size (µm) |
Blade Speed (m/s) |
Feed Rate (mm/min) |
Flow Cooling (l/h) |
---|---|---|---|---|
Aluminium nitride |
160 µm |
18 |
5-25 |
4 |
Aluminium oxide |
160 µm |
16 |
3-10 |
6 |
Ferrite |
40 µm |
18 |
10-50 |
2-4 |
Gallium arsenide (315) |
40 µm |
18 |
10-20 |
2-6 |
Gallium phosphide (315) |
40 µm |
18 |
10-20 |
2-6 |
Germanium |
40 µm |
19-21 |
30-70 |
2-6 |
GGG (Gadolinium Gallium Garnet) |
40 µm |
18 |
10-20 |
7-12 |
Graphite |
160 µm |
21 |
250 |
7-12 |
Indium arsenide |
40 µm |
18 |
10-20 |
2-6 |
Indium phosphite |
40 µm |
18 |
10-20 |
8-12 |
Lithium niobate |
40 µm |
18 |
20-40 |
2-6 |
Lithium tantalate |
40 µm |
20 |
3-10 |
6 |
Optical glass (BK7) |
160 µm |
15 |
5-20 |
8-10 |
Quartz |
160 µm |
12 |
15-30 |
8-12 |
Quartz glass |
160 µm |
15 |
5-20 |
8-10 |
Samarium cobalt |
140 µm / 40 µm |
18 |
10-30 |
7-12 |
Sapphire |
160 µm |
19 |
1-5 |
10-12 |
ID Saw Blades Trouble Shooting Guide
Sawmarks (Surface Quality Issues)
Sawmarks indicate irregularities in the blade’s movement, material interaction, or cooling efficiency.
Issue |
Possible Cause |
Solution |
---|---|---|
Overall Sawmarks |
- Irregular cutting edge - Dull cutting edge - Blade runout too high - Excess slurry on the blade
|
- Dress the blade regularly with a dressing stick to maintain uniformity. - Replace or recondition the blade to avoid excessive force. - Replace or recondition the blade to avoid excessive force. - Ensure proper blade mounting and inspect spindle alignment. - Adjust slurry flow and filtration to prevent buildup. |
Start of Slicing Sawmarks
|
- Dull cutting edge - Excessive feed rate |
- Verify blade sharpness before slicing. - Reduce feed rate at the beginning of the cut for smoother engagement. |
End of Slicing Sawmarks |
- Blade runout too high - Dull cutting edge |
- Minimize vibration by improving machine stability and balance. - Use a sharper blade with an appropriate bond and grit size. |
Bow (Material Warping During Cutting)
Material bowing or distortion can be caused by heat buildup, uneven forces, or improper machine setup.
Issue |
Possible Cause |
Solution |
---|---|---|
Convex Bow (Outward Warping) |
- Cutting edge irregularity - Improper coolant flow rate |
- Use precision-ground blades with consistent diamond distribution. - Adjust coolant flow to maintain uniform material cooling.
|
Concave Bow (Inward Warping) |
- Dull cutting edge - Blade runout too high |
- Select a blade with sharper diamond exposure to reduce friction. - Verify blade concentricity and use high-precision flanges. |
Tapered Cut |
- Excessive feed rate - Blade runout too high |
- Lower feed rate gradually instead of abrupt changes. - Reduce vibration by ensuring proper spindle and arbor alignment. |
Chipping (Edge Damage on Material)
Chipping at the start or end of a cut can result from improper blade condition, machine setup, or cutting parameters.
Issue |
Possible Cause |
Solution |
---|---|---|
Start of Slicing Chipping |
- Excessive feed rate - Dull cutting edge - Coolant flow too low |
- Reduce initial feed rate and gradually increase. - Replace the blade or select a finer grit size. - Increase coolant flow for better lubrication. |
End of Slicing Chipping |
- Blade runout too high - Dull cutting edge |
- Inspect blade mounting and reduce vibration. - Ensure the blade is sharp and properly bonded. |
Wafer Breakage (Catastrophic Failure of Material)
Wafer breakage can result in significant material loss, downtime, and increased costs.
Issue |
Possible Cause |
Solution |
---|---|---|
Breakage from Mounting Beam |
- Excess slurry on blade - Damaged blade core |
- Reduce slurry concentration and clean blade frequently. - Inspect blade core integrity for cracks and replace when necessary. |
Breakage During Cutting |
- Dull cutting edge - Excessive feed rate - Coolant flow too low - Coolant flow too high |
- Use a sharp blade and avoid excessive force. - Reduce feed rate to prevent material stress. - Increase coolant flow to dissipate heat. - Optimize coolant delivery to avoid excessive pressure. |
Application
- Silicon wafers
- Semiconductors
- Glass, quarts, & optics
- Magnetic materials such as neodymium
- Ferrous materials
- Ferrite
- Sapphire
- Many others
Equipment Used On
Universal application on all standard machines such as Meyer & Burger, TSK, STC, GMN
Advantages
- High accuracy
- Superior flatness
- Minimal kerf loss
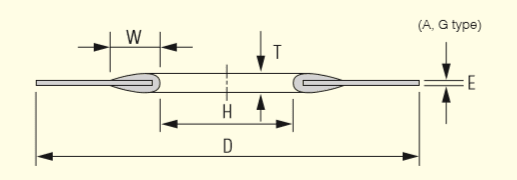
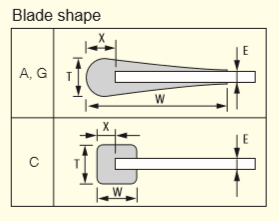
7064701, 7064702, 7064703, 7064704, 7064705
Here are popular specifications below (other specifications can be produced upon request)
Item Number |
Outside Diameter |
Inside Diameter |
---|---|---|
7064701 |
34″ (860mm) |
12″ (305mm) |
7064702 |
27″ (690mm) |
9.5″ (240mm) |
7064703 |
22″ (560mm) |
9.5″ (240mm) |
7064704 |
22″ (560mm) |
8″ (200mm) |
7064705 |
16.6″ (420mm) |
6″ (150mm) |
Other specifications are available upon request
Benefits:
- Minimal Material Loss: ID diamond blades are designed to cut from the inside of the material, which results in minimal material loss. This is especially critical when working with expensive or scarce materials like sapphire or advanced ceramics, where every bit of material is valuable.
- High Precision: These blades offer exceptional precision and accuracy in cutting. They are capable of creating intricate shapes and achieving tight tolerances, making them indispensable in industries that demand precision cutting.
- Smooth and Clean Cuts: ID diamond blades produce smooth and clean cuts on the inside of the material, reducing the need for additional finishing or polishing. This is vital in applications where the quality of the cut edge is essential.
- Reduced Vibration: ID diamond blades typically generate less vibration during cutting compared to other methods, which is advantageous when working with delicate materials that can be affected by vibration.
- Efficient for Large Pieces: In the case of cutting large pieces of material, ID diamond blades can be more efficient and accurate than alternative cutting methods like diamond wire blades. They allow for precise cuts on a larger scale.
- Specialized Applications: ID diamond blades are specifically designed for cutting from the inside, making them the preferred choice for tasks that require inner cuts, circular cuts, or intricate shapes in materials that are challenging to cut with conventional blades.
- Cost-Effective in Specific Situations: While ID diamond blades may have a higher initial cost, their efficiency and ability to minimize material waste can lead to cost savings in specialized industries where the value of the material being cut is high.
- Versatile in Material Compatibility: ID diamond blades can be used with a variety of hard and brittle materials, including sapphire, ceramics, glass, and more, making them versatile for different applications within the specialized industries.
ID Cropping Blades Parameters
Material |
Diamond Micron Size (µm) |
Blade Speed (m/s) |
Feed Rate (mm/min) |
Flow Cooling (l/h) |
---|---|---|---|---|
Aluminium nitride |
160 µm |
18 |
5-25 |
4 |
Aluminium oxide |
160 µm |
16 |
3-10 |
6 |
Ferrite |
40 µm |
18 |
10-50 |
2-4 |
Gallium arsenide (315) |
40 µm |
18 |
10-20 |
2-6 |
Gallium phosphide (315) |
40 µm |
18 |
10-20 |
2-6 |
Germanium |
40 µm |
19-21 |
30-70 |
2-6 |
GGG (Gadolinium Gallium Garnet) |
40 µm |
18 |
10-20 |
7-12 |
Graphite |
160 µm |
21 |
250 |
7-12 |
Indium arsenide |
40 µm |
18 |
10-20 |
2-6 |
Indium phosphite |
40 µm |
18 |
10-20 |
8-12 |
Lithium niobate |
40 µm |
18 |
20-40 |
2-6 |
Lithium tantalate |
40 µm |
20 |
3-10 |
6 |
Optical glass (BK7) |
160 µm |
15 |
5-20 |
8-10 |
Quartz |
160 µm |
12 |
15-30 |
8-12 |
Quartz glass |
160 µm |
15 |
5-20 |
8-10 |
Samarium cobalt |
140 µm / 40 µm |
18 |
10-30 |
7-12 |
Sapphire |
160 µm |
19 |
1-5 |
10-12 |
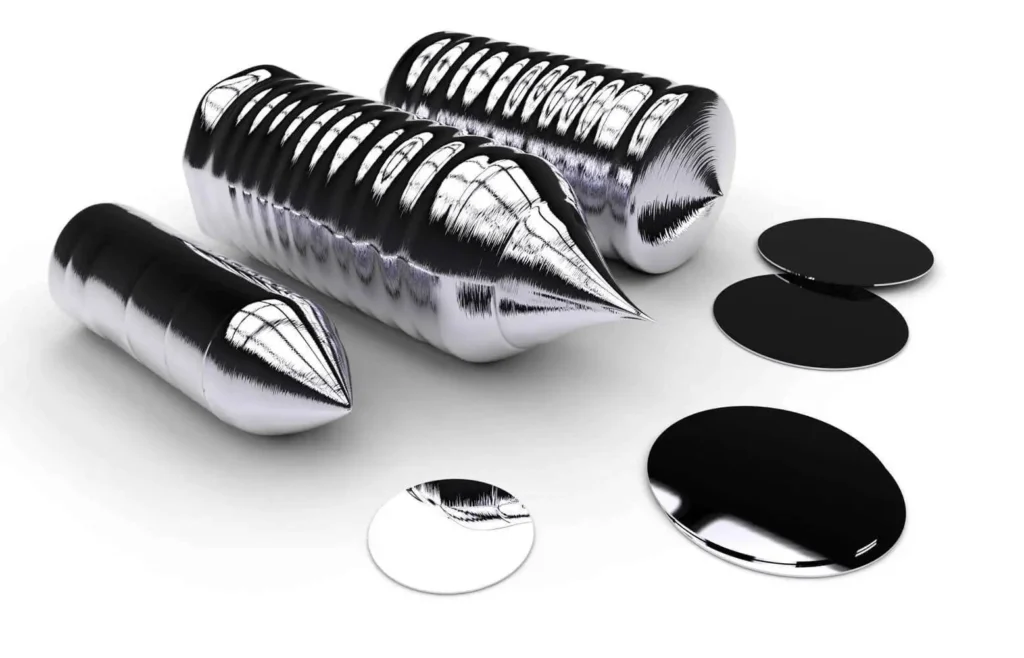
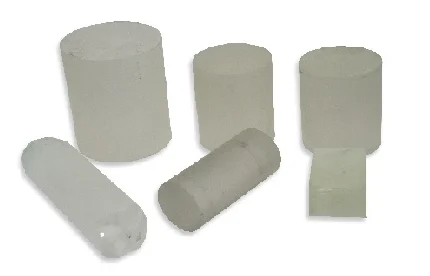
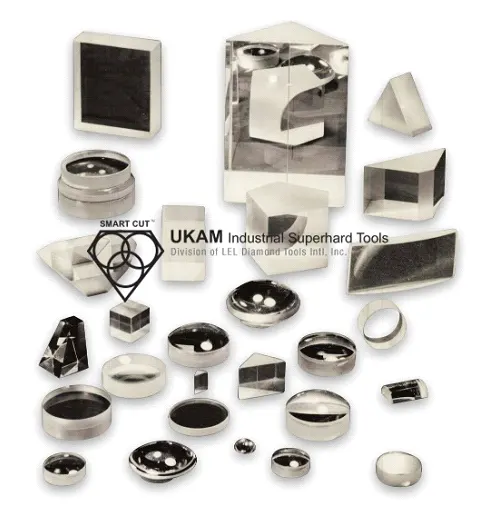
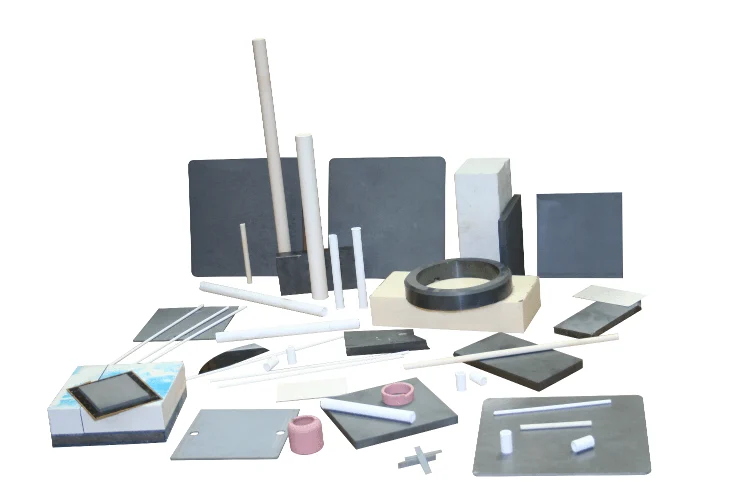
Cropping Silicon Using Inside Diamond Blades
The cropping process in industrial settings often involves resizing or sectionalizing materials into more manageable or specifically sized pieces using industrial diamond blades. These blades are favored for their precision and ability to handle a variety of materials, including ceramics, metals, composites, and advanced materials.
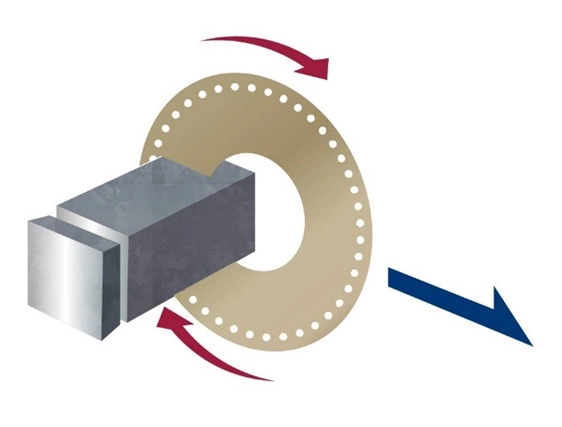
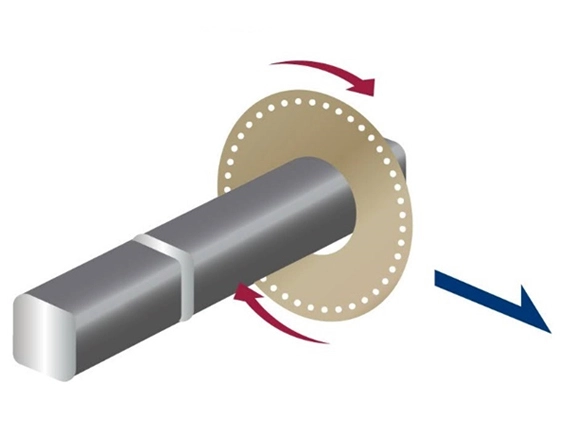
Industrial diamond (ID) blades are chosen for their exceptional hardness, which allows them to cut through tough materials with minimal wear. Their cutting edges are embedded with synthetic diamond grit, which provides a combination of sharpness and durability essential for efficient cropping. The advantages of using ID blades include precision cutting, which produces cleaner cuts with tighter tolerances than conventional blades; reduced material waste, which is crucial when working with expensive materials; enhanced cutting speed, as diamond blades can operate at higher speeds without sacrificing cut quality; and versatility, as they can handle a variety of materials from soft aluminum to hard quartz or ceramics.
When using ID diamond blades for cropping, it's important to consider several factors to optimize the process. The choice of blade should be suited to the material type and desired cut quality, with considerations for diamond grit size, concentration, and the matrix material. The cutting machine should be capable of handling the size and type of blade and provide the necessary power and stability. Adjusting the feed rate to match the material’s hardness and thickness is crucial; too fast a feed rate can cause blade overheating and wear, while too slow can reduce efficiency. Using appropriate coolants can prevent overheating and remove debris from the cutting area, affecting both cut quality and blade life. Regular checks for blade wear and tear are necessary, as even high-quality diamond blades deteriorate and require dressing to restore their cutting performance.
To achieve optimal results during the cropping process with ID diamond blades, technical specifications such as RPM (rotations per minute), blade diameter, and cutting depth must be precisely aligned with the material properties and the desired outcomes. For instance, cropping a piece of sintered carbide, a very hard material, would ideally be done using a thin kerf diamond blade with a fine grit size for a smooth surface finish. The machine's RPM should be adjusted to the lower end of the blade's capability to minimize the risk of chipping the carbide, and coolants should be used to keep the cutting zone clean and cool, enhancing the blade's lifespan and the quality of the cut.
How SMART CUT ® Bond Works?
Step 1
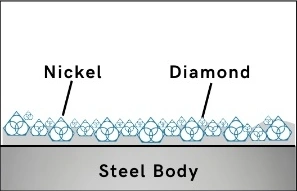
Sharpest And Finest Quality Diamonds
The sharpest and finest quality diamonds or CBN crystals that go into a SMART CUT® Diamond Bond, immediately penetrate into the material, grinding and polishing as they cut.
The newly exposed diamonds don’t effect diamonds already working on the material. Unlike many other diamond bonds, diamonds in a SMART CUT® Bond remains sharp and grow sharper with each cut, prolonging product life and consistent performance.
Step 2
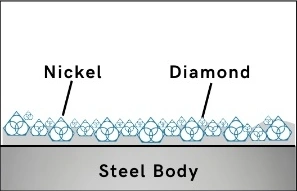
Diamonds or CBN Crystals
Diamonds or CBN Crystals are activated only at the exposed layer. As Bond Matrix layer begin to wear out, diamonds in a new Bond Matrix layer are immediately activated, substituting the already used up diamond layer. The SMART CUT® Diamond Hybrid Bond makes sure every diamond is in the right place and at the right time, working where you need it most.
Step 3
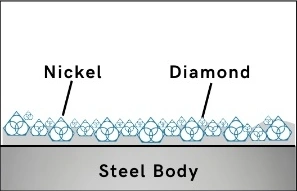
Advanced Formulated Open Diamond Bond Design
This advanced formulated open diamond bond design insures minimal chipping, fast cut, constant speed of cut, minimal cutting noise, and most important of all, consistent performance.
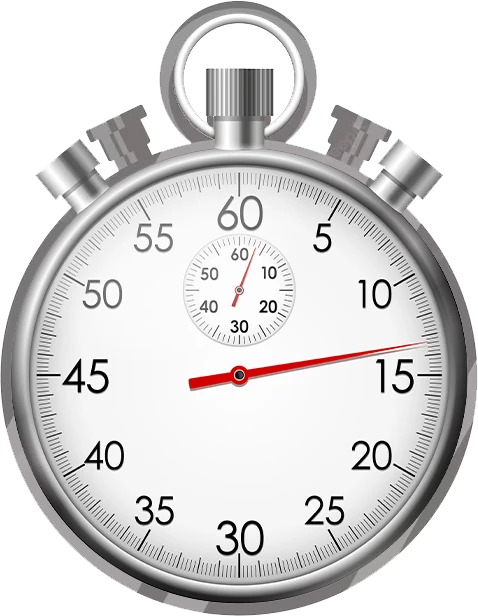
Faster
Cutting Action
ID Saw Blades made utilizing SMART CUT technology are much more aggressive than your conventional ID Blades. They can cut faster, while still leaving behind a smooth finish free of material deformation.
Longer
Life
In most cases ID saw blades manufactured utilizing SMART CUT technology, will outlast other conventional nickel bonded diamond CBN drills. SMART CUT diamond ID blades are more sturdy than Blades manufactured with conventional technologies. They are capable to retain their form and bond configuration all the way through the Blades life.
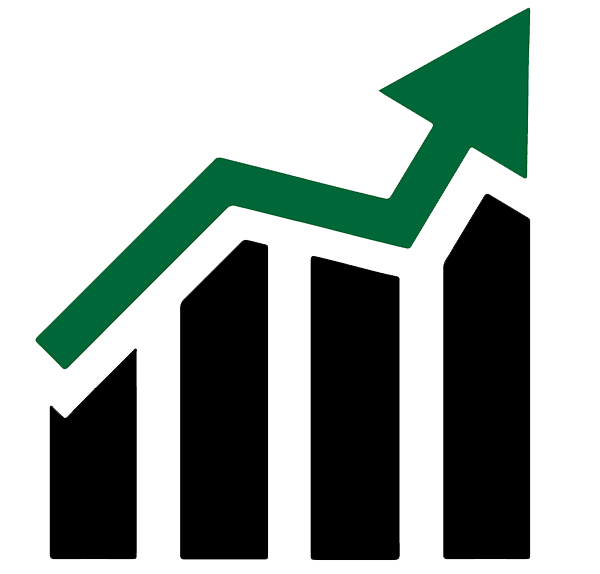

More
Consistent Performance
SMART CUT® Multi Layered Electroplated diamond cutting blade three diamond layers impregnated inside the bond matrix. Unlike Many Other Blade Types, they wear evenly, and are known for their consistency. You will get consistent cutting speed, and overall consistent performance, with minimum amount of dressing even on the hardest to cut materials.
Best
Performance & Value on the Market
SMART CUT® Multi Layered diamond cutting blades are the best investment you can make! They will more than pay for themselves in terms of overall performance and provide best Return on Investment.
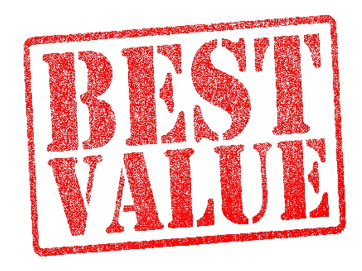
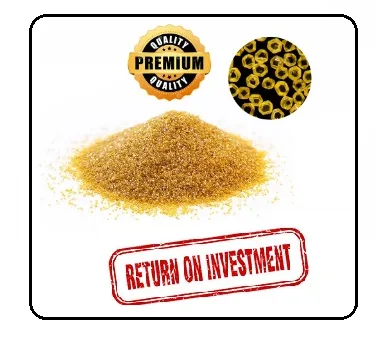
Manufactured Using
The Highest Quality Raw Materials
Only the highest quality synthetic diamonds and raw materials are used in the manufacturing process. The highest quality standards and product consistency is maintained, using sophisticated inspection and measurement equipment.
About Nickel Bond
(Electroplated) Tools
Electroplated (nickel bond) diamond products usually have a single layer of diamonds, held by a tough durable nickel alloy. Nickel is frequently used as a base for plating diamond. Because of its excellent strength, toughness and flexibility during the plating process. Electroplated diamond products are able to retain their original shape and dimensions thought their working life. Unlike sintered (meal bond) or resin bond diamond products, where diamond particles are buried in bond and held together by metal or resin binder deep inside.
Electroplating allows diamond particles to protrude from the bond matrix, providing a free, faster cutting action with minimum heat generation.
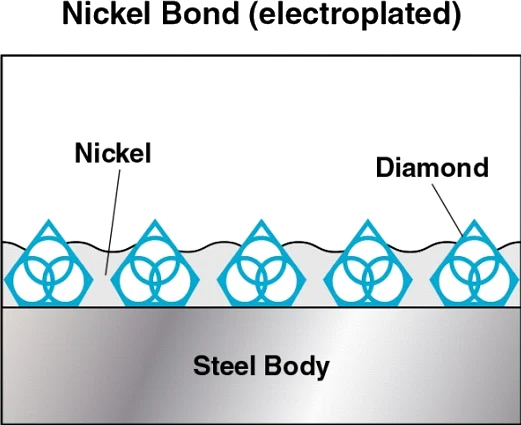
Recommended Coolant for ID Saw Blades
One of the most effective coolants available for diamond wire sawing and silicon slicing applications is SMART CUT® HD Synthetic Low IFT Coolant & Lubricant. This advanced coolant is specifically formulated to:
- Lower interfacial tension (IFT), improving wetting action and ensuring better coverage of the cutting area.
- Provide excellent lubricity, reducing blade friction and extending tool life.
- Minimizefoaming, ensuring smooth operation in high-speed cutting environments.
- Preventsilicon particle adhesion, reducing clogging and enhancing process efficiency.
Using SMART CUT® HD Synthetic Low IFT Coolant & Lubricant optimizes the slicing process by ensuring superior lubrication and thermal management.
Coolant Additives & Their Role
Specialized coolant such as SMART CUT® HD Synthetic Low IFT Coolant & Lubricant will significantly outperform deionized water and improve the effectiveness in the slicing process. The most commonly used coolant additives include:
- Surface-active fluids – Improve the spreading ability of the coolant, ensuring uniform cooling across the entire cutting area.
- Synthetic coolant oils – Provide additional lubrication and help minimize material adhesion to the cutting blade.
- Anti-corrosion agents – Protect machine components from oxidation and wear.
- Sapphire processing: Deliver precise dimensions for high-end sapphire windows and luxury watch components.
It is important to note that coolant additives should always be used unless they introduce process difficulties. When properly selected, they have a positive impact on cutting speed, yield, blade longevity, and surface quality.
Coolant Nozzle Positioning & Flow Optimization
The correct placement of coolant nozzles is critical to achieving optimal coolant distribution and uniform blade wear. Coolant nozzles should be positioned to:
- Ensure even coolant flow across the cutting area.
- Minimize temperature variations, reducing the risk of thermal distortion.
- Improve blade wear distribution, preventing premature wear on one side of the blade.
- Enhance debris removal, reducing particle accumulation and improving wafer cleanliness.
An even split of the coolant stream ensures that all parts of the blade receive equal cooling and lubrication, leading to consistent cutting performance and longer blade life.
Impact of Cooling Mode & Flow Rate on Cutting Performance
Research studies and industry experience have demonstrated that the mode of coolant supply and its flow rate have a significant impact on:
- The slicing process efficiency
- The surface finish of the silicon wafers
- The overall lifespan of ID saw blades
Key considerations when optimizing coolant supply:
- Flow rate optimization: Higher flow rates improve cooling efficiency but may also lead to excessive splashing or material loss.
- Mode of supply: Proper nozzle design and positioning ensure optimal coolant penetration.
- Coolant filtration: Effective filtration systems prevent recirculation of silicon debris, improving cutting precision.
SMART CUT® HD-2B
Synthetic Low IFT Coolant / Lubricant for ID Blades
SMART CUT® is a synthetic coolant specifically designed for the cutting of semiconductor materials, including sapphire, silicon, germanium, single-crystal SiC, and II-VI crystals. This coolant offers excellent cut rates and imparts outstanding surface finishes with reduced warp and total thickness variation (TTV). It is ideal for diamond abrasive cropping, squaring, and wafering of silicon ingots using ID, band, and wire saws. SMART CUT® HD-2B can also be used as a non-re-circulating edge grinding coolant or lubricant for silicon wafers and ingots.
SMART CUT® HD-2B Coolant enhances cutting performance by providing exceptional cooling and lubrication. The coolant's molecules interact with the cutting area, efficiently absorbing heat to prevent overheating.
While SMART CUT® HD-2B is not specifically designed to be mixed with water, its advanced formula works effectively in "once-through" systems, where it helps maintain optimal cutting conditions by reducing friction. This results in improved tool life, superior material quality, and smoother cuts. By dissipating heat effectively, SMART CUT® HD-2B minimizes tool wear, improves cut quality, and enables faster, more efficient cutting, all while ensuring a cleaner, more environmentally friendly process.
SMART CUT® HD-2B 2B acts as both a coolant and lubricant, effectively reducing heat generated by friction and minimizing surface tension. As a lubricant, it enhances the dispersion of material swarf, ensuring that swarf particles are effectively moved away from the diamond tool and cutting zone, preventing buildup within the kerf. The coolant's advanced formula works by bonding with the cutting area, helping to penetrate the kerf and flush out material debris, preventing chipping and internal cracking. Additionally, because SMART CUT® HD-2B keeps the cutting area clean and free from debris, it minimizes the need for secondary material processing and cleaning operations, enhancing overall efficiency and reducing maintenance requirements.
Related products
Related Products
SMART CUT® Diamond Cylindrical Grinding Wheels
SMART CUT® Diamond Cylindrical Grinding Wheels are engineered for the precise peripheral grinding of silicon ingots, making them an ideal choice for industries such as semiconductors, electronics, automotive, and photovoltaics. These high-performance grinding wheels are designed to process the outer surfaces of silicon ingots, ensuring accurate orientation flats are created, which are essential for subsequent processing steps. The addition of the orientation flat, a marked edge indicating the crystallographic plane of the wafer, is crucial for the wafer's alignment in future manufacturing processes.
During the post-slicing phase, wafers undergo shaping and smoothing through peripheral grinding.
SMART CUT® Diamond Notch
SMART CUT ® Single & Multi Layered Electroplated Diamond Notch Grinding Wheel is designed for high-precision notch grinding of semiconductor wafers, including materials such as Silicon (Si), Silicon Carbide (SiC), Gallium Arsenide (GaAs), and Sapphire. Engineered using advanced electroplating technology, this wheel ensures exceptional performance in wafer processing, offering a high level of precision and durability for demanding semiconductor applications.
SMART CUT® Diamond Edge Grinding Wheels (Electroplated)
SMART CUT® Diamond Edge Grinding Wheels are engineered to deliver exceptional performance for precision grinding applications, providing superior results in both rough and fine grinding. These wheels are ideal for use in industries that require highly accurate EDM processing and consistent wafer-to-wafer results. Manufactured with synthetic diamond grit, SMART CUT® wheels offer improved surface roughness and extended tool life due to their tightly controlled diamond distribution and uniform bond structure.
Band Saw Blades
SMART CUT® Braised Bond Diamond Band Saw Blades
Diamond Wire
SMART CUT Diamond wire produces minimum kerf loss, less sub-surface damage, and contamination free coolant. Used for precision cutting of various types of artificial crystal, ceramic, quartz glass, monocrystalline silicon, polycrystalline silicon, sapphire and special metal materials. Diamond Wire cutting is an environmentally friendly cutting process as it eliminates slurry recycling and disposal issues.
SMART CUT® HD Synthetic Low IFT Coolant/Lubricant For Diamond Wire Sawing Silicon
SMART CUT® is a synthetic coolant specifically designed for the cutting of semiconductor materials, including sapphire, silicon, germanium, single-crystal SiC, and II-VI crystals. This coolant offers excellent cut rates and imparts outstanding surface finishes with reduced warp and total thickness variation (TTV). It is ideal for diamond abrasive cropping, squaring, and wafering of silicon ingots using ID, band, and wire saws. SMART CUT® HD-2B can also be used as a non-re-circulating edge grinding coolant or lubricant for silicon wafers and ingots.
DIAMOND BACKGRINDING WHEELS
SMART CUT® Diamond Backgrinding Wheels are designed for precision thinning and flattening of silicon wafers, glass, and ceramic substrates. These high-performance wheels are used on backgrinding machines, including models from Disco, Okamoto, Strasbaugh, and other leading manufacturers. Available in sizes ranging from 8” to 14” O.D., they are engineered to handle a wide range of materials and applications, from semiconductor wafers to microelectronic packages.
Recently Viewed Products
Recently Viewed Products
ARE YOU USING RIGHT ID CUTTING BLADES
FOR YOUR APPLICATION?
LET US
HELP YOU
HAVING ISSUES WITH
YOUR CURRENT ID CUTTING BLADES?
Knowledge Center
08
Jul
Manufacturing Processes for Silicon Semiconductors From Ingot to Integrated Circuit
Share this Article with Friend or Colleague
1. Ingot Production
The journey begins with the creation of silicon ingots, which are pure silicon cylinders produced through methods like the Czochralski process. Once formed, these ingots undergo a...
08
Jul
The Comprehensive Guide to the Processes of Silicon Wafers Production
Share this Article with Friend or Colleague
The production of silicon wafers, an essential component in semiconductor manufacturing, involves several intricate steps to ensure precision and quality. This article explores the detailed processes depicted in...
- Unmatched Selection For Many Applications
- Superior Quality & Consistency
- Immediate Worldwide Delivery
- Technical Support & Expertise
- American Based Manufacturer
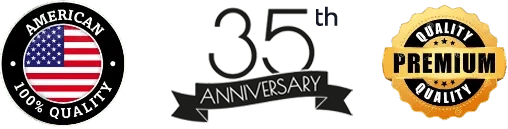

- Different Product
- Different Technology
- Different Company
- Expect MORE from your tools
Let Us HELP You!
Subscribe To Our Newsletter
Signup for email offers, updates, and more
Contact Us
- 25205 & 25201 Avenue Tibbits Valencia CA 91355 USA
-
Phone : (661) 257-2288
FAX : (661) 257 -3833 - lel@ukam.com
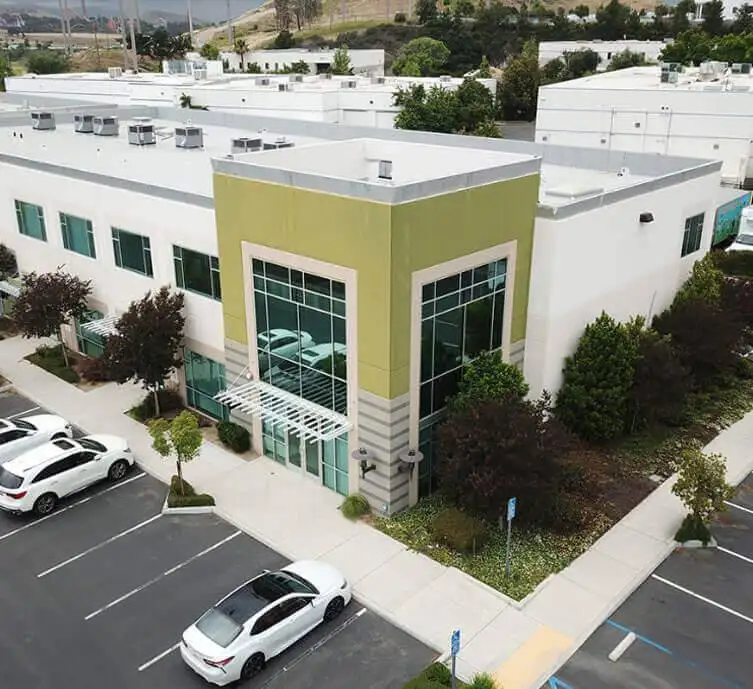
UKAM Industrial Superhard Tools is a U.S. High Technology, Specialty Diamond Tool & Equipment manufacturer. We specialize in producing ultra thin, high precision cutting blades, precision cutting machines diamond drills, diamond micro tools, standard & custom advanced industrial diamond tools and consumables.
- 25205 & 25201 Avenue Tibbits Valencia CA 91355 USA
-
Phone : (661) 257-2288
FAX : (661) 257 -3833 - lel@ukam.com
- 25205 & 25201 Avenue Tibbits Valencia CA 91355 USA
-
Phone : (661) 257-2288
FAX : (661) 257 -3833 - lel@ukam.com
DIAMOND TOOLS BY BOND
EQUIPMENT
KNOWLEDGE CENTER
OUR PRODUCTS
COMPANY
CUSTOMER SERVICE
Shipping Methods


Safe & Secure Payments

© Copyright 1990-2025. UKAM Industrial Superhard Tools – Terms of Use