Table of Contents
ToggleManufacturing diamond tools involves a series of technological processes to impregnated manmade or natural diamond into various diamond tools. Find info on how these types of tools are made.

This article outlines the step-by-step manufacturing process for the majority of industrial diamond and CBN tools. It serves as a general guide to provide a deeper understanding of how these tools are produced. While the actual production methods may vary depending on the specific tool type, this content is intended purely for educational insights. This information is presented for general educational purposes only.
1. BOND FORMULTSTIONS: INPUT OF RAW MATERIALS (POWDERS)
Industrial Diamonds:
-
Sources : Industrial diamonds can be sourced from either natural or synthetic methods.
-
Natural Diamonds: These are diamonds that, while not gemstone quality, are suitable for industrial use. They're mined from the earth in locations such as Russia, Australia, and various African countries.
-
Synthetic Diamonds: Produced using high-pressure, high-temperature (HPHT) methods or chemical vapor deposition (CVD) methods. Synthetic diamonds can offer more consistency in terms of size and quality, making them desirable for many industrial applications.
-
Selection: Choosing the right quality and type of diamond is essential. Factors considered include hardness, impurity levels, shape, and size.
Matrix Material:
-
Material Types: The matrix material, typically a metal alloy, holds the diamond particles in place. Common matrix materials include bronze, cobalt, nickel, and tungsten carbide.
-
Selection Criteria: The matrix's hardness, wear resistance, bonding capability with diamond, and thermal conductivity are critical factors in its selection.
Binders and Additives: These can be added to the matrix material to improve bonding, enhance wear resistance, or modify other properties of the tool.
B. Resin Bond Material:
-
Types of Resins: There are various types of resins that can be used, including phenolic, polyimide, and others. The choice of resin will depend on the specific requirements of the tool, like the intended use, expected life, and desired finish.
-
Modifiers and Fillers: Depending on the desired properties of the bond, different additives, modifiers, or fillers might be added to the resin. These can improve its wear resistance, adjust its hardness, or change its heat dissipation properties.
B. Resin Bond Material:
-
Resin Types and Their Characteristics:
-
Phenolic Resins: These are thermosetting polymers and are known for their good thermal stability and mechanical strength. They provide good adhesion and are often used for grinding wheels.
-
Polyimide Resins: They offer high thermal resistance and are suitable for applications where high temperatures are generated.
-
Epoxy Resins: Known for their excellent adhesion properties and chemical resistance. They might be used in combination with other resins to improve bond strength.
-
Fillers: Materials like glass fibers, bronze powder, or other metallic powders might be added to enhance the resin's wear resistance or conductivity.
-
Plasticizers: These can be added to improve the flexibility of the bond. This is especially crucial for applications requiring a more forgiving bond that doesn't easily crack or chip.
C. Catalysts and Accelerators:
-
Some resins require catalysts or accelerators to promote the curing process. The choice and quantity of these agents can influence the setting time and final properties of the bond.
1. Metallic Fillers:
-
Bronze and Copper Powder: These metallic powders are frequently used in resin bonds because they improve the tool's heat dissipation properties. They can help carry away the heat generated during cutting or grinding, thus preventing excessive wear on the tool.
-
Tungsten Carbide:This is a hard, high-density material that can increase the wear resistance of the tool. It's especially valuable in applications where the tool is exposed to high stress.
-
Aluminum Powder: It can be used to enhance the thermal conductivity of the bond, similar to bronze and copper.
2. Non-Metallic Fillers:
-
Glass Fibers: These can enhance the bond's structural integrity, making it more resilient against cracking or breaking.
-
Graphite: This material is sometimes added because of its lubricating properties, which can reduce friction during cutting or grinding.
-
Silica or Alumina: These materials can adjust the bond's hardness and wear resistance. They're especially useful in fine-grinding applications where a smooth finish is required.
3. Organic Fillers:
-
Rubber Particles: Rubber can be added to improve the bond's flexibility, making it less prone to chipping or breaking during use.
-
Cellulose Fibers: These can be used to increase the bond's structural integrity, especially in phenolic resins.
4. Filler Blends:
In many cases, manufacturers might use a blend of multiple fillers to achieve a specific set of properties. For example, a combination of bronze powder and glass fibers might be used to ensure good heat dissipation while maintaining structural integrity.
2. RAW MATERIALS QUALITY CONTROL PROCESS
Objective:
Ensure that all raw materials, including powders and diamonds, are inspected and tested to meet the required specifications for manufacturing high-quality diamond tools.
1. Intake Inspection:
Upon receiving raw materials, visually inspect the packaging for any damage or signs of contamination. Only packages that are sealed and temper free should be taken to the next step.
2. Material Documentation Verification:
Check the delivery notes, certificates of analysis (CoA), and other related documentation to ensure the raw materials are as per the order and match the specified requirements.
3. Sampling:
a. Select random samples from each batch of raw material received.
b. Ensure that the sampling is done using clean and appropriate equipment to avoid contamination.
4. Physical Testing of Diamonds:
a. Size Analysis: Using a sieve or other sizing mechanism, ensure the diamond particles are within the specified size range.
b. Morphology: Under a microscope, check the shape and surface quality of the diamonds.
c. Strength Test: Subject diamond particles to a compression or impact test to assess their strength and integrity.
5. Chemical Analysis of Powders:
a. X-ray Fluorescence (XRF): Use XRF to determine the elemental composition of the powders to ensure there are no unwanted elements present.
b. X-ray Diffraction (XRD): Confirm the phase composition of the powders to ensure the correct crystalline structure.
6. Other Tests (depending on the specific tool and application):
a. Particle Size Distribution (PSD): Determine the particle size distribution of the powders using laser diffraction or other appropriate methods.
b. Bulk Density: Measure the bulk density to ensure the powders will pack and process correctly.
c. Flowability Test: Ensure that the powders flow correctly for the manufacturing process.
d. Purity Test: Confirm that the diamond particles and powders meet the required purity levels.
7. Storage and Labeling:
a. After testing, approved materials should be labeled as "Quality Approved" and stored in designated areas.
b. Any material that does not meet specifications should be labeled as "Rejected" and isolated from approved materials to prevent use.
8. Data Recording and Traceability:
a. Record all test results and observations in a quality control logbook or digital system.
b. Maintain a traceable link between the raw material batch, the supplier, and the test results.
9. Periodic Supplier Review:
a. Regularly review supplier performance based on the quality of the materials delivered.
b. If a particular supplier consistently delivers sub-standard materials, consider sourcing from a different supplier or implementing stricter incoming inspection protocols.
10. Continuous Improvement:
a. Regularly review and update the quality control process based on feedback from the manufacturing team, tool performance in the field, and advancements in testing methodologies.
b. Implement training programs for QC staff to ensure they are up-to-date with the latest standards and testing methods.
11. Quality Control Approval:
Once all tests are passed and the material is deemed fit for use, the raw material batch is cleared for the manufacturing process.
By following this structured quality control process, a diamond tools manufacturing facility can ensure that their tools are consistently of high quality and performance.
3. PARTICLE SIZE VERIFICATIONS PROCESS USING SIEVES
Objective:
Ensure the powders used in diamond tool manufacturing are of the correct particle size, as this is crucial for the tool's performance, longevity, and overall quality.
1. Preparation:
a. Ensure the sieves are clean and free from previous residues. This can be achieved using a soft brush and/or an ultrasonic bath.
b. Select sieves with the appropriate mesh sizes according to the specification of the powders. Arrange sieves from the largest mesh size on top to the smallest at the bottom.
2. Sample Selection:
a. Take a representative sample from the batch of powder. The sample size should be adequate to ensure reliability but not so large as to overload the sieves.
3. Weighing:
a. Weigh the empty receiving pan and record its weight.
b. Weigh the selected powder sample and record its initial weight.
4. Sieving Process:
a. Place the powder sample onto the top sieve.
b. Secure the sieve stack onto a mechanical sieve shaker.
c. Start the sieve shaker and allow the powders to sieve for a predetermined time, ensuring a thorough separation of particles. The exact time can depend on the sieve shaker's specification and the nature of the powders.
4. Sieving Process:
a. Once the sieving is complete, carefully disassemble the sieve stack.
b. Weigh the amount of powder retained on each sieve and in the receiving pan. Record these weights.
6. Calculation:
Calculate the percentage of powder retained on each sieve and the percentage that passed through the finest sieve using the formula:
Percentage on Sieve=(Weight of powder on sieveInitial weight of sample)×100Percentage on Sieve=(Initial weight of sampleWeight of powder on sieve)×100
7. Analysis:
a. Compare the calculated percentages with the specified requirements for the powders.
b. Determine if the sample meets the particle size distribution requirements.
8. Documentation:
a. Record all weights, calculations, and observations in a dedicated logbook or digital system.
b. Attach a label to the batch indicating whether it has passed or failed the sieving test, based on the analysis.
9. Storage & Handling:
a. Store passed powders in designated areas, ready for further processing or use.
b. Isolate and label batches that do not meet the particle size requirements. These might be subjected to further milling or considered for alternative applications.
10. Cleaning:
a. After the process, clean the sieves using a soft brush to remove any residual powder. If necessary, use an ultrasonic bath for thorough cleaning. Ensure sieves are dried properly before storing.
4. POWDER MIXING PROCESS
Objective:
Ensure the powders used in diamond tool manufacturing are mixed thoroughly to form a homogenous mixture, essential for consistent tool quality and performance.
1. Preparation:
a. Clean the mixing equipment thoroughly to ensure there is no residue from previous batches.
b. Calibrate the equipment if necessary to ensure consistent and accurate operation.
c. Prepare the workspace, ensuring it's free from contaminants.
2. Powder Selection & Weighing:
a. Based on the desired formulation, select the required powders for the mixture.
b. Weigh each powder accurately as per the formulation specifications, ensuring precision to maintain consistent quality.
3. Pre-Mixing Inspection:
a. Visually inspect each powder for any noticeable impurities or clumps.
b. If agglomerates are observed, they should be broken down or sieved before mixing.
4. Sequential Addition:
a. Add the powders into the mixer in the sequence recommended by the formulation. Some powders may need to be added first due to their properties or interaction with other components.
5. Mixing Process:
a. Start the mixer at a slow speed initially to prevent powder loss or excessive dust generation.
b. Gradually increase the mixing speed as the powders begin to integrate.
c. Allow the mixture to mix for the predetermined time to ensure a homogenous blend. The duration can vary depending on the type and quantity of powders and the efficiency of the mixer.
6. Intermittent Inspection:
a. Periodically stop the mixer and take a small sample for inspection.
b. Visually inspect the sample for homogeneity. For more thorough analysis, small samples can be tested for properties like particle size distribution or composition to ensure even distribution.
7. Adjustments (if necessary):
a. If the mixture is not homogenous or if there are any observed discrepancies, additional mixing time can be given.
b. If required, adjust the quantity of specific powders slightly to achieve the desired consistency or composition. Ensure that any adjustments are documented.
8. Final Inspection:
a. Once mixing is complete, take a representative sample from different parts of the mixture (top, middle, bottom).
b. Conduct necessary tests to ensure the mixture meets the set specifications.
9. Transfer & Storage:
a. Transfer the homogenous mixture to a suitable container for storage or the next stage of the manufacturing process.
b. Label the container with relevant information such as batch number, date, and formulation.
10. Cleaning:
a. Clean the mixing equipment immediately after use to prevent cross-contamination with future batches.
b. Ensure residues are properly disposed of, especially if there are reactive or hazardous components.
5. POWDER MOLDING PROCESS
Objective:
Ensure powders are uniformly spread inside the mold cavity to achieve consistent density, shape, and size for the diamond tools.
1. Preparation:
a. Ensure molds are clean, free from previous residues, and undamaged.
b. Pre-treat the mold surfaces, if necessary, with release agents to facilitate easy demolding after the pressing process.
c. Calibrate any related equipment or instruments to ensure accuracy and consistency in molding.
2. Powder Pre-treatment (if required):
a. Depending on the properties of the powders and the desired end product, a binder or other additives might be required to assist in the molding process.
b. If used, ensure the binder is mixed uniformly with the powder.
3. Filling the Mold:
a. Gradually fill the mold cavity with the pre-treated powder.
b. Use vibration or tapping techniques to settle the powder, ensuring an even spread throughout the mold cavity without any air pockets.
4. Leveling:
a. Use a straight edge or scraper to level off the excess powder, ensuring the mold cavity is filled uniformly up to the desired height or weight.
5. Pressing/Compaction:
a. Close the mold, ensuring proper alignment.
b. Apply pressure using a hydraulic or mechanical press, ensuring even compaction of the powder inside the mold. The pressure and duration depend on the powder characteristics and desired density.
6. Inspection:
a. Once compaction is complete, open the mold and inspect the molded part for defects such as cracks, deformities, or unevenness.
b. If any defects are detected, the powder might need to be re-molded, or adjustments might be required in the pressure or filling process.
7. Ejection:
a. Carefully eject the compacted powder shape from the mold. Depending on the mold design, this could be manual or automated.
b. Handle the molded piece with care, as it might be fragile before any subsequent sintering or curing processes.
8. Post-Molding Treatment (if required):
a. Some products may require additional treatments like drying to remove any binder solvent or other post-molding processes.
b. Ensure these are carried out as per specified conditions to maintain the integrity of the molded shape.
9. Documentation:
Lorem ipsum dolor sit amet, consectetur a. Record the batch number, date, mold used, powder weight, pressing pressure, and any other relevant parameters.
b. Document any observed defects and related corrective actions.
10. Cleaning:
a. Clean the mold thoroughly after each cycle to ensure consistent performance and prevent cross-contamination.
b. Store molds in a clean, dry environment to prevent corrosion or damage.
6. HOT/COLD PRESSING PROCESS
Objective:
Ensure powders are uniformly spread inside the mold cavity to achieve consistent density, shape, and size for the diamond tools.
1. Preparation:
a. Ensure the pressing equipment, either hot or cold, is in optimal condition, clean, and free from any previous residues.
b. Calibrate any relevant equipment or instruments to ensure accurate and consistent pressing.
2. Mold Pre-treatment:
a. Pre-treat the mold surfaces with release agents to facilitate easy removal post-pressing.
b. Ensure molds are at the appropriate temperature, especially for hot pressing.
3. Filling the Mold:
a. Place the pre-molded powder shape or directly fill the powder into the mold, ensuring even distribution.
4. Cold Pressing:
(If the process involves an initial cold pressing followed by hot pressing, this step is crucial.)
a. Close and align the mold correctly.
b. Using a mechanical or hydraulic press, apply the predetermined pressure.
c. Maintain this pressure for the required duration to achieve desired density.
5. Hot Pressing:
a. If the product requires hot pressing, preheat the press to the desired temperature.
b. Position the cold-pressed product (or directly the powder if cold pressing is skipped) in the hot press.
c. Apply the predetermined pressure while maintaining the set temperature. The combination of heat and pressure ensures sintering and densification of the powders.
d. Maintain temperature and pressure for the specified duration.
e. Slowly cool down the pressed product to avoid thermal stresses or cracks.
6. Demolding:
a. After pressing, and once the product has cooled down to a safe handling temperature (for hot pressing), open the mold.
b. Carefully remove the pressed product to avoid any damage.
7. Inspection:
a. Inspect visually the pressed product for any visible defects like cracks, deformities, or inconsistencies.
b. Use non-destructive testing methods, if available, to ensure uniform density and other required properties throughout the product.
8. Post-Pressing Treatment (if required):
Some products may need additional processing such as tempering, annealing, or other heat treatments to enhance their properties.
9. Documentation:
a. Record all relevant parameters: batch number, date, mold used, pressing temperature, pressing pressure, and duration.
b. Document any observed defects, deviations, and related corrective actions.
10. Cleaning:
a. Clean the pressing equipment and molds after each cycle to ensure consistent performance and prevent contamination.
b. Store molds and pressing equipment in a clean, dry environment to prevent corrosion or damage.
7. SINTERING/FIRING PROCESS
Objective:
Use the sintering/firing process to enable powders to fully bond and fuse together, integrating with the diamond crystals, to achieve a solid, cohesive tool with enhanced properties.
1. Preparation:
a. Ensure the sintering/firing furnace is clean, calibrated, and free from residues from previous cycles.
b. Check that furnace temperature controls and monitoring systems are functional.
2. Placement of Pressed Product
a. Position the pressed products on sintering trays or supports that can withstand high temperatures and won't react with the products.
b. Ensure products are evenly spaced to allow for uniform heating and minimal thermal shadowing.
3. Preheating (optional, but often recommended):
a. Raise the temperature slowly to a predetermined preheat temperature to remove any residual moisture or binder.
b. Hold at this temperature for a set duration.
4. Ramp to Sintering Temperature:
a. Increase the temperature at a controlled rate to the main sintering temperature. The rate of heating can influence the final properties, so it's crucial to maintain it as per specifications.
5. Sintering:
a. Maintain the desired sintering temperature for the required duration. This allows powders to fully bond and fuse together, integrating with the diamond crystals.
b. The precise temperature and duration would depend on the powder mixture, diamond type, and desired final properties.
6. Controlled Cooling:
a. After the sintering process, reduce the furnace temperature at a controlled rate. Rapid cooling might induce thermal stresses, leading to cracks or warping.
b. Depending on the product and its composition, it may be necessary to hold at certain intermediate temperatures for a while during cooling.
7. Removal & Inspection:
a. Once the sintered products have cooled to a safe handling temperature, remove them from the furnace.
b. Visually inspect each product for obvious defects like cracks, discoloration, or deformities.
c. Further testing, like hardness or density measurements, can be conducted to ensure product quality.
8. FINISHING PROCESS
Objective:
Ensure the diamond tool achieves its desired final form, precise dimensions, and tight tolerances, optimizing its functionality and aesthetics.
1. Preparation:
a. Inspect the sintered product for any visible defects or irregularities. b. Determine the type of grinding required based on the tool's design specifications. c. Choose the appropriate grinding wheels or discs, taking into account the material of the diamond tool and the required finish.
2. OD (Outside Diameter) Grinding:
a. Secure the tool in the grinding machine, ensuring it's firmly held but not overly clamped to prevent deformation. b. Using the grinding wheel, methodically grind the outer diameter of the tool, maintaining a consistent feed rate and pressure. c. Periodically measure the diameter to ensure precision and consistency. d. Cool the tool during grinding using appropriate coolants to prevent overheating and potential material changes.
3. ID (Inside Diameter) Grinding:
a. Mount the tool, ensuring the inner diameter is accessible and properly aligned with the grinding mechanism. b. Utilize a suitable internal grinding wheel to grind the inner diameter of the tool. c. Ensure even material removal from the entire inner circumference for uniformity. d. Continuously monitor and measure to achieve the required inner diameter specifications.
4. Edge Grinding:
a. Secure the tool, focusing on the edges that require grinding. b. Employ a suitable grinding wheel or disc to methodically grind and smooth the tool's edges, ensuring sharpness or rounding as per the tool's design. c. Ensure edges are free from burrs, cracks, or inconsistencies.
5. Forming (Form Grinding):
a. Based on the tool's design, select a grinding wheel with the corresponding shape or profile. b. Secure the tool in the grinding machine, focusing on the areas requiring forming. c. Grind the tool's form, ensuring the profile or shape matches the design specifications. d. Measure and inspect the formed areas to confirm they match the desired geometry and tolerances.
9. TRUING AND DRESSING PROCESS
Objective:
Conditioning diamond tools through truing to achieve the desired form and through dressing to expose the diamond crystals, making the tool ready for optimal performance.
1. Preparation:
a. Ensure the truing and dressing equipment are clean, calibrated, and in good working condition. b. Inspect the diamond tool to be conditioned, noting any irregularities, distortions, or other anomalies.
2. Truing:
Purpose: To bring the diamond tool to its true geometric shape, correcting any irregularities or misalignment.
a. Secure the diamond tool in the truing machine. b. Select the appropriate truing tool or disc, depending on the diamond tool's material and design. c. Start the truing operation, maintaining a consistent feed rate and pressure. d. Monitor the tool's geometry continuously to ensure it conforms to the desired shape. e. Cool the tool during the truing process using appropriate coolants to prevent overheating or changes to the material. f. Once the truing process is complete, inspect the tool for correct geometry and form.
3. Dressing:
Purpose: To expose fresh diamond crystals by removing the bond material from the tool's surface, ensuring sharpness and readiness for cutting or grinding.
- Secure the diamond tool in the dressing device or machine. b. Choose a suitable dressing tool or stick, considering the bond material and the diamond grit size. c. Initiate the dressing process. The dressing tool will remove the bond material, revealing the embedded diamond crystals. d. Ensure even removal of bond material across the tool's surface to maintain uniform exposure of diamond crystals. e. Use coolants, if necessary, to avoid excessive heat buildup during the dressing process. f. After dressing, inspect the diamond tool's surface to ensure an even exposure of diamond crystals.
4. Inspection and Testing:
a. After both truing and dressing, visually inspect the tool for uniformity, correct geometry, and adequate exposure of diamond crystals. b. If available, conduct a test cut or grind to ensure the tool performs optimally. Adjustments can be made if performance is not up to standard.
10. FINAL INSPECTION AND PRODUCT QUALITY CONTROL PROCESS
Objective: Through meticulous inspection and measurement processes, guarantee that the final diamond tool corresponds to the highest industry standards and meets the client's demands.
1. Setting up the workspace:
a. Make sure it is clean and free of contaminants.
b. To ensure accuracy, calibrate all inspection and measurement tools.
c. Create the inspection checklist in accordance with internal quality standards and client demands.
2. Visual Inspection:
a. Look for any obvious flaws in the diamond tool, such as cracks, stains, abnormalities, or unevenness.
b. Check to see if the diamond crystals are equally and sufficiently exposed.
c. Verify that the tool's surface is free of any observable impurities or residues.
3. Dimensional Inspection:
a. Using precision measuring tools like micrometers, calipers, and gauges, measure the tool's dimensions. b. Check the tool's length, width, diameter, and other relevant dimensions against the client specifications. c. Ensure that the tool's geometry (like profiles or forms) matches the intended design.
4. Performance Testing (if applicable):
a. Conduct test cuts or grinds using the diamond tool to evaluate its performance. b. Measure the efficiency, cutting/grinding speed, and quality of the finished work. c. Adjust or rework the tool if performance does not meet the standards or specifications.
5. Bond and Diamond Crystal Inspection:
a. Use magnifying equipment or microscopes to inspect the bond material and the distribution of the diamond crystals. b. Ensure that the bond material is uniformly distributed, and there are no air pockets or voids. c. Confirm that diamond crystals are adequately exposed for optimal performance.
6. Hardness and Wear Testing:
a. Subject the tool to wear testing to gauge its lifespan and durability. b. Measure the hardness of the tool to ensure it meets the required standards and specifications.
7. Documentation:
a. Record all measurements, observations, and test results. b. Note any deviations from the client specifications or internal standards and the actions taken to address them. c. Maintain a batch record for traceability, including the manufacturing date, equipment used, operators, and inspection results.
8. Packaging Inspection:
a. Check that the packaging material is free from damage or defects. b. Ensure that packaging provides adequate protection to the diamond tool during transportation and storage. c. Confirm that labels, barcodes, or QR codes (if used) are correctly placed and readable.
9. Final Approval:
a. Once all inspection and quality control procedures are complete and the diamond tool meets all specifications, grant final approval for shipping. b. Seal the packaging and store the tool in a designated area awaiting dispatch.
10. Continuous Improvement and Feedback:
a. Gather feedback from clients on tool performance and longevity. b. Use this feedback, combined with inspection data, to drive continuous improvement in the manufacturing and inspection processes.
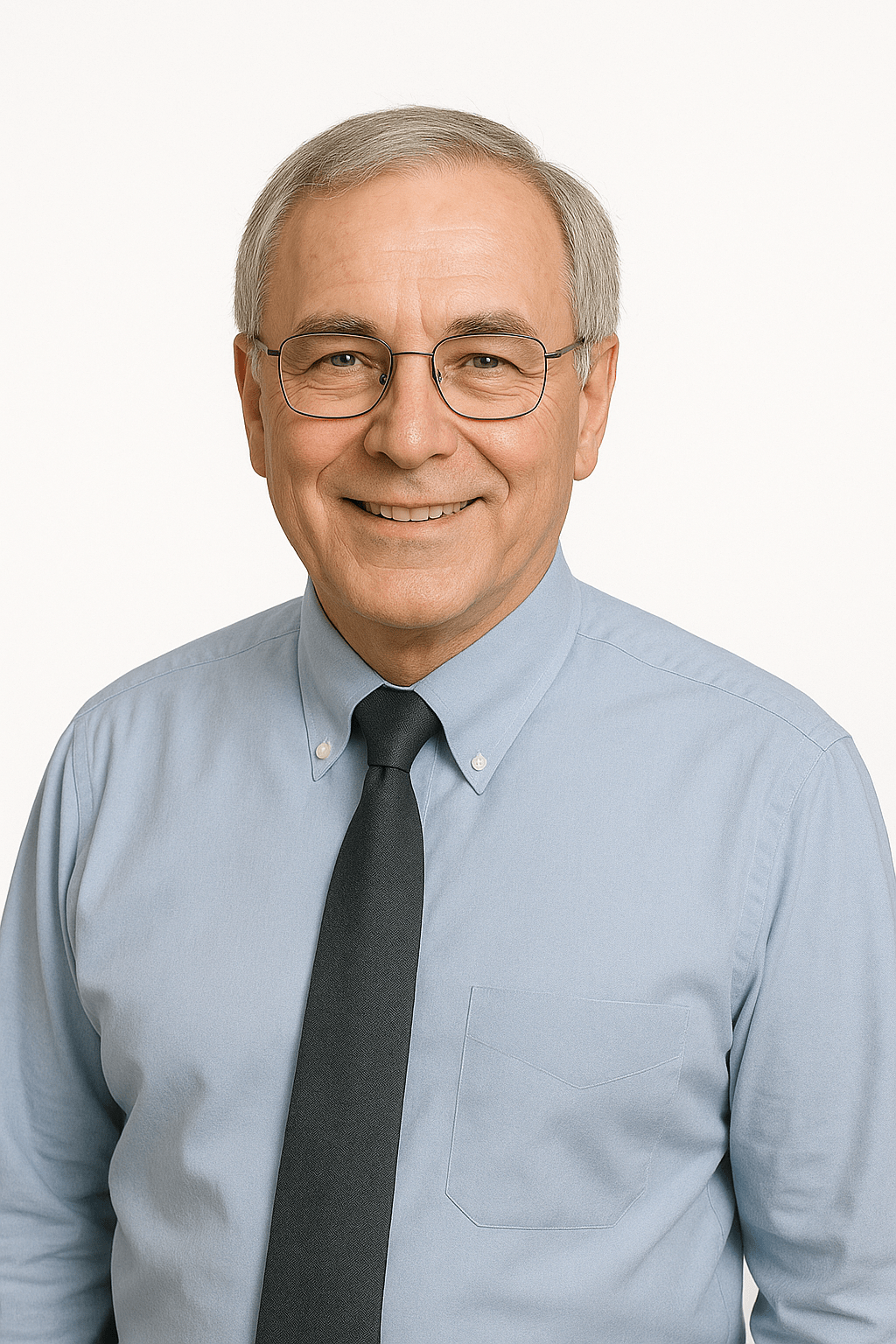
Alexander Schneider is a senior applications engineer and leading authority in the industrial diamond tooling industry, with over 35 years of hands-on experience in the development, application, and optimization of ultra-thin and high-precision diamond blades, diamond core drills, and diamond and CBN grinding wheels. His work spans a wide range of advanced materials including ceramics, glass, composites, semiconductors, and high-performance metals.
Throughout his career, he has collaborated with leading R&D institutions, national laboratories, and high-tech manufacturing companies across Europe, North America, and Asia, providing technical expertise and tailored solutions for demanding cutting and surface preparation applications.
Mr. Schneider has played a pivotal role in advancing precision cutting, sectioning, dicing, and grinding technologies used in research, production, and failure analysis. He is widely respected for his ability to optimize tool design and cutting parameters to meet exacting industry standards—balancing factors such as cut quality, blade life, material integrity, and process consistency.
As an author, Mr. Schneider is known for delivering practical, application-focused insights that translate complex technical challenges into clear, actionable strategies. His articles and technical guides serve as trusted resources for engineers, researchers, and manufacturers seeking to improve precision, reduce process variability, and enhance tool performance in critical applications.
ARE YOU USING RIGHT TOOLS
FOR YOUR APPLICATION?
LET US
HELP YOU
HAVING ISSUES WITH
YOUR CURRENT TOOLS?
Knowledge Center
How to Selecting Right Diamond Tools for your application
How to properly use Diamond Tools
Why use diamond
Diamond vs CBN (cubic boron nitride) Tools
What is Diamond Mesh Size and how to select best one for your application
What is Diamond Concentration and which to use for your application
Diamond Tool Coolants Why, How, When & Where to Use
Get to Know the Diamond Tool Bond Types and Which to use for your application
Choosing The Correct Diamond Bond Type
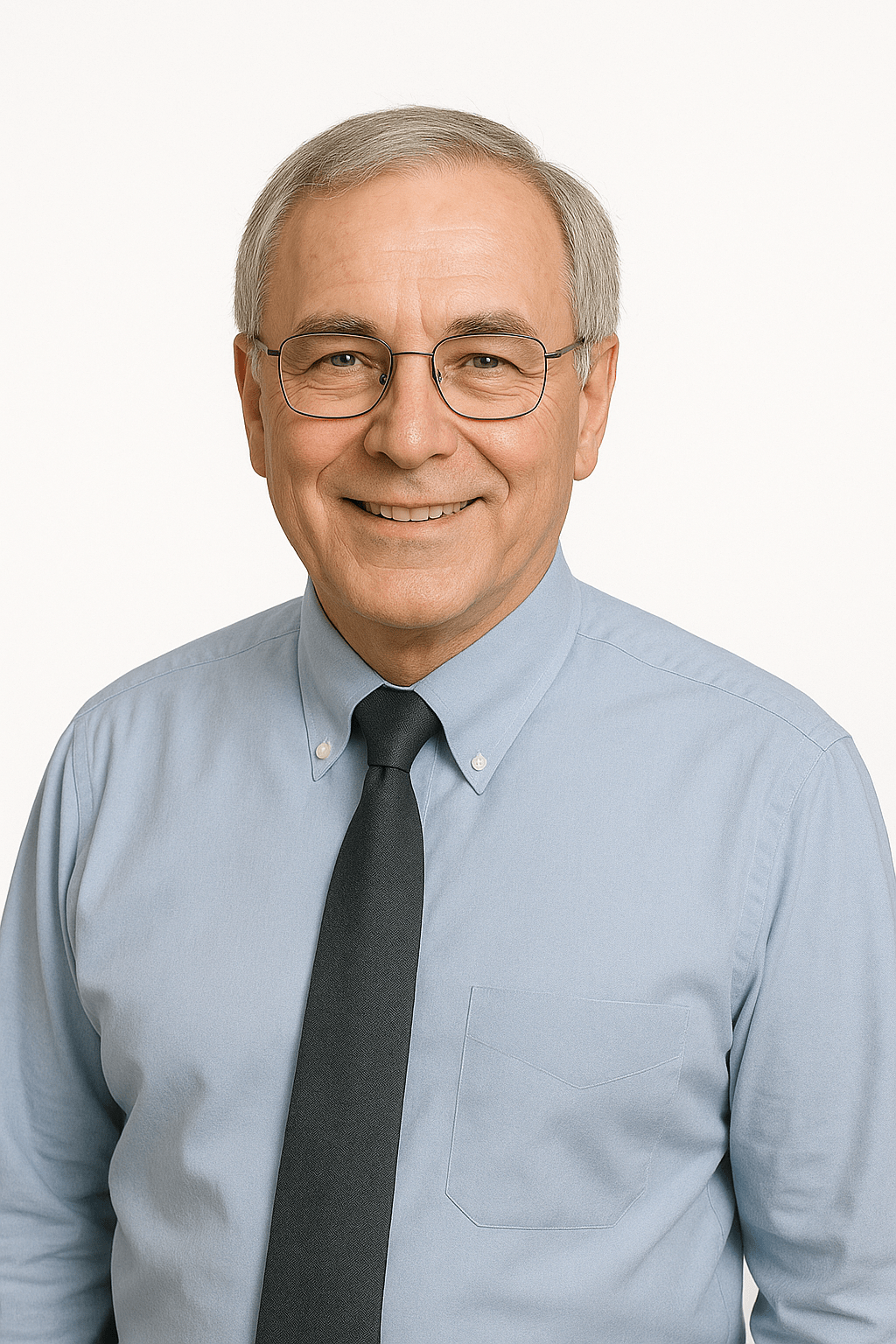
Alexander Schneider is a senior applications engineer and leading authority in the industrial diamond tooling industry, with over 35 years of hands-on experience in the development, application, and optimization of ultra-thin and high-precision diamond blades, diamond core drills, and diamond and CBN grinding wheels. His work spans a wide range of advanced materials including ceramics, glass, composites, semiconductors, and high-performance metals.
Throughout his career, he has collaborated with leading R&D institutions, national laboratories, and high-tech manufacturing companies across Europe, North America, and Asia, providing technical expertise and tailored solutions for demanding cutting and surface preparation applications.
Mr. Schneider has played a pivotal role in advancing precision cutting, sectioning, dicing, and grinding technologies used in research, production, and failure analysis. He is widely respected for his ability to optimize tool design and cutting parameters to meet exacting industry standards—balancing factors such as cut quality, blade life, material integrity, and process consistency.
As an author, Mr. Schneider is known for delivering practical, application-focused insights that translate complex technical challenges into clear, actionable strategies. His articles and technical guides serve as trusted resources for engineers, researchers, and manufacturers seeking to improve precision, reduce process variability, and enhance tool performance in critical applications.