Table of Contents
ToggleMachining with diamond tools and using diamond, laser, and water jet as cutting methods are all different processes with distinct advantages and applications
In selecting the most effective machining method is critical for achieving the desired precision, efficiency, and material performance. Among the most widely used methods are diamond machining, laser machining, and water jet machining. Each of these technologies has unique capabilities and characteristics that make them suitable for specific materials and operational needs.
Share this Article with Friend or Colleague
Diamond & CBN Machining: Diamond & CBN tools, including diamond blades, core drills, and grinding wheels, are well known for their ability to cut through extremely hard and brittle materials with exceptional precision. This method is commonly used for processing materials like glass, ceramics, stone, and hard metals, where achieving high accuracy and fine surface finishes is essential. Diamond tools are also highly durable and offer a long tool life, making them a valuable asset in industries that deal with challenging materials, such as advanced ceramics, optics, and composites.
Laser Machining: Laser machining utilizes highly concentrated beams of light to cut, drill, and mill various materials. The laser’s precision and ability to process complex geometries make it ideal for tasks requiring intricate designs or tight tolerances. Laser cutting is widely used in industries that process metals, plastics, and composites. However, laser machining can generate significant heat, which can affect the material properties, especially for heat-sensitive materials. Its high speed and non-contact nature make it a preferred choice in many applications, including electronics, automotive, and aerospace industries.
Water Jet Machining: Water jet machining uses high-pressure streams of water, sometimes mixed with abrasives, to cut through materials. This method is particularly effective for cutting thick or heat-sensitive materials, as it does not produce heat-affected zones (HAZ). Water jets are versatile and can cut a wide range of materials, from metals and glass to ceramics and composites. While water jet machining offers advantages in terms of cold cutting and environmental friendliness, it tends to be slower and less precise than diamond or laser machining for certain applications.
Importance of Selecting the Right Machining Method
Choosing the right machining technique depends on a variety of factors, including the material being processed, the precision required, the speed of operation, and the specific requirements of the project (e.g., cutting, drilling, or milling). The decision to use diamond, laser, or water jet machining should be based on a clear understanding of the material's properties—such as hardness, thickness, and heat sensitivity—as well as the desired surface finish and production efficiency.
For example, diamond machining is often the go-to solution for extremely hard or brittle materials like ceramics and stones due to its ability to produce high-precision cuts with minimal material damage. On the other hand, laser machining may be more suitable for fast and intricate cutting of thin metals or plastics. Meanwhile, water jet machining excels in cutting thicker materials or materials that are prone to heat damage, such as composites and glass.
In this article, we will explore how these three machining methods compare based on several critical factors:
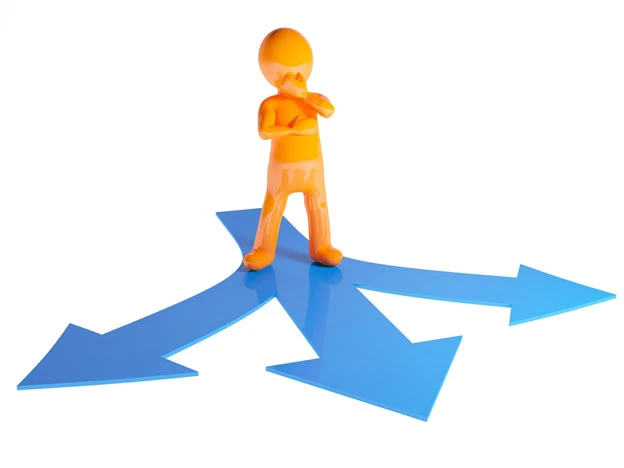
-
Material Hardness: The ability of each method to process hard, brittle, or soft materials.
-
Precision: The level of accuracy achievable with each method, including dimensional tolerances and surface finish.
-
Surface Finish: The quality of the material’s surface after machining, considering factors like smoothness and chipping.
-
Cost: The overall cost of machining, including initial investment, tool wear, maintenance, and operating expenses.
-
Speed: The efficiency and production output achievable with each method.
-
Environmental Considerations: The environmental impact of each technique, including waste production, energy consumption, and coolant or water use.
Feature/Aspect |
Diamond Machining |
Laser Machining |
Water Jet Machining |
---|---|---|---|
Material Suitability |
Best for hard, brittle materials (glass, ceramics, stone, metals, composites). Not ideal for soft materials. |
Suitable for metals, plastics, thin materials. Struggles with thick or heat-sensitive materials. |
Can handle a wide variety of materials, including thick metals, glass, ceramics, composites, and softer materials. |
Precision |
Extremely high precision and smooth surface finish, especially for hard materials. |
High precision but heat can affect surface quality, creating Heat-Affected Zones (HAZ). |
Moderate precision; generally less accurate than diamond or laser machining, but clean cuts with cold processing. |
Surface Finish |
Excellent surface finish with minimal chipping for hard and brittle materials. |
Good surface finish, but thermal effects may cause some surface roughness or distortions. |
Clean cut, but less polished surface compared to diamond tools; no heat-related imperfections. |
Cutting Speed |
Slower than laser and water jet, especially for thick materials. |
Very fast for thin materials but speed decreases with thickness. |
Moderate speed; slower than laser but can handle thicker materials. |
Cost |
High initial cost due to expensive diamond tools, but long tool life reduces long-term costs. |
High operating cost due to energy consumption, but low tool wear. |
Moderate to high cost; abrasive media adds to operational expenses, and water usage can be costly. |
Tool Durability |
Extremely long tool life, especially for cutting hard materials. |
No tool wear, but machinery maintenance is required. |
Abrasive components wear out, requiring frequent replacement. |
Heat Impact |
No heat generation, making it suitable for heat-sensitive materials. |
Generates heat, which can distort materials and create thermal stress. |
Cold cutting process, preventing heat-related damage. |
Thickness Capacity |
Best suited for thin to moderate material thicknesses. |
Limited effectiveness with very thick materials. |
Excels at cutting through thick materials like metal and stone. |
Environmental Impact |
Minimal environmental impact, but requires coolant for lubrication. |
High energy consumption and possible release of harmful fumes. |
Large water consumption and need for abrasive disposal, but no heat or fumes. |
Operating Speed |
Slower than laser and water jet, more precise but requires careful setup. |
Fast and efficient, especially for thin and moderate materials. |
Slower than laser for thinner materials, faster than diamond for thicker cuts. |
Applications |
Best for high-precision cuts in hard, brittle materials (glass, ceramics, stone, and composites). |
Used in electronics, automotive, and aerospace for cutting metals and plastics. |
Widely used in aerospace, construction, and for processing thick materials or composites. |
Understanding Diamond Machining
Diamond machining refers to the use of diamond-coated or diamond-impregnated tools for cutting, drilling, milling, grinding, and other material processing operations. Diamonds, known as the hardest naturally occurring material, offer exceptional cutting and abrasive properties. Diamond machining tools are designed to handle the most demanding applications, particularly where high precision, fine surface finish, and durability are essential.
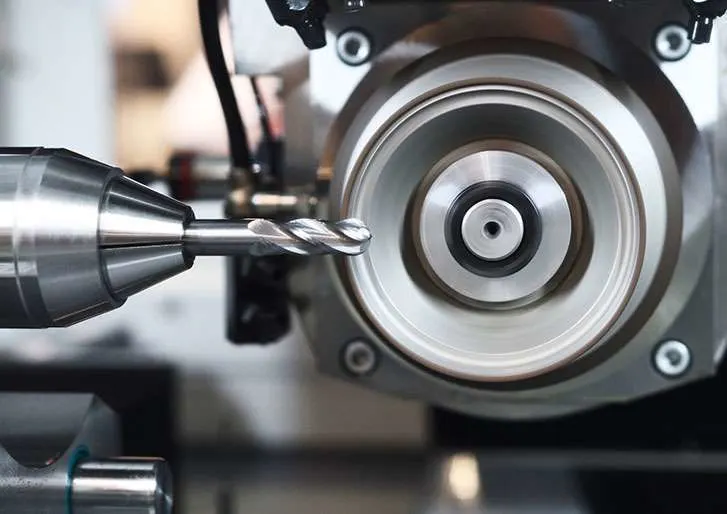
Diamond Tools for Machining
Cutting
Diamond blades are used for slicing and dicing hard materials like glass, ceramics, and stones. They can achieve extremely thin cuts with minimal kerf (material waste), making them ideal for applications requiring tight tolerances.
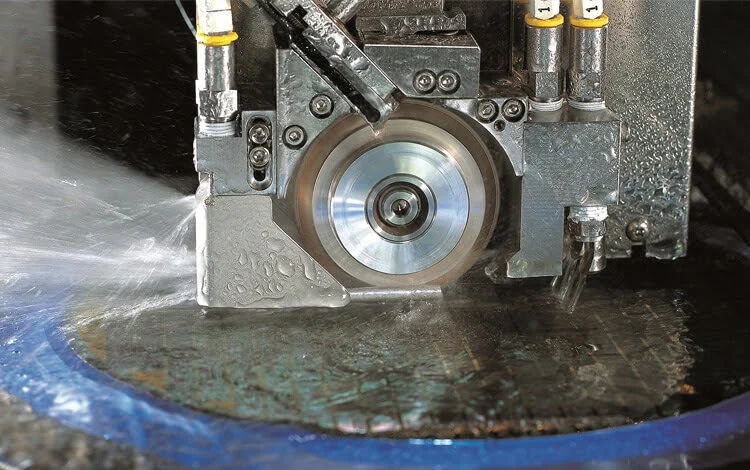

Drilling
Diamond core drills are employed for precision drilling in hard, brittle materials such as glass, ceramics, and certain metals. The diamond grit ensures minimal chipping and cracking, even with delicate or thin materials.
Milling
Diamond milling tools are used for creating intricate shapes and designs in hard materials. They are particularly effective in industries like optics, electronics, and aerospace, where precision is paramount.
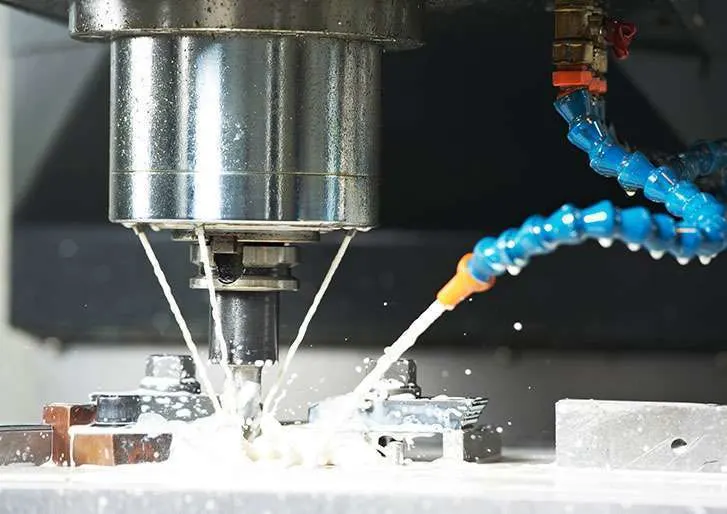
Common Applications of Diamond Machining
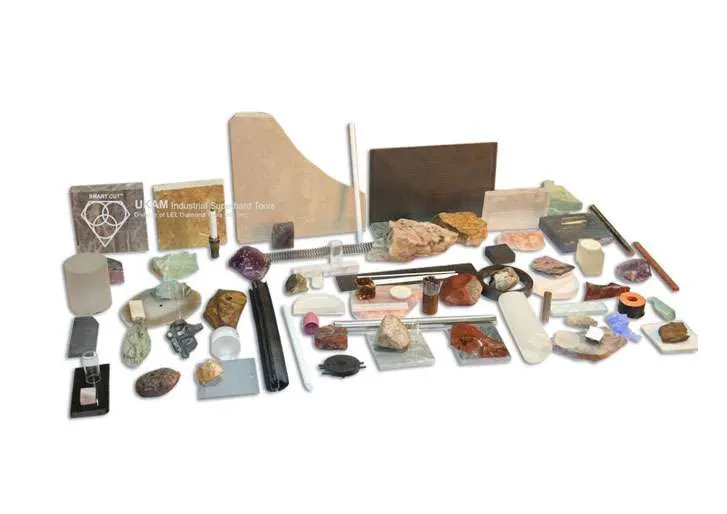
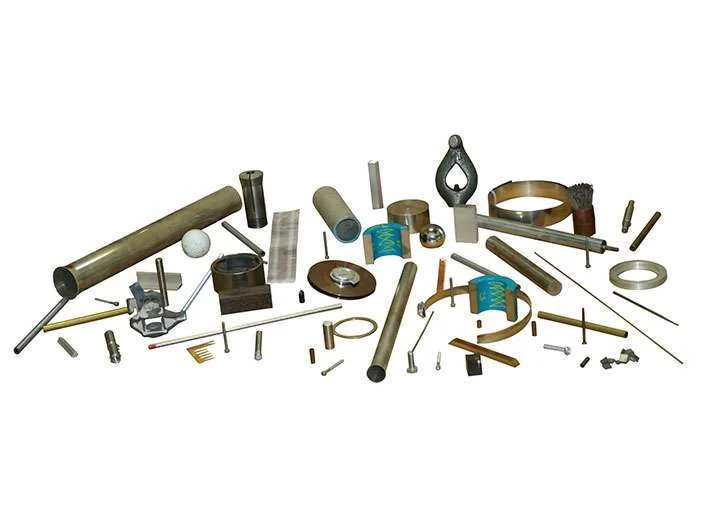
-
Glass: Diamond tools are widely used for cutting, drilling, and grinding glass due to the material’s brittle nature. Diamond blades allow for clean cuts with minimal chipping, while core drills ensure precise, crack-free holes.
-
Ceramics: Advanced ceramics, such as silicon carbide and alumina, are extremely hard and brittle. Diamond machining is essential for cutting and shaping these materials with high accuracy and surface quality.
-
Stone: Diamond tools are the go-to solution for cutting and processing natural stones like granite, marble, and quartz. Diamond saws, drills, and grinding tools are used to create intricate designs and finishes.
-
Metals: While diamond machining is typically associated with hard materials, it can also be used to process metals, especially when high precision is needed. Diamond tools are particularly effective with hard metals like tungsten carbide.
-
Composites: Diamond tools excel in machining advanced composites like carbon fiber and Kevlar, providing smooth, precise cuts without delamination.
Advantages of Diamond Machining
1. High Precision and Surface Finish
Diamond tools offer exceptional precision, allowing manufacturers to achieve intricate geometries and fine details in materials. The superior hardness of diamond ensures clean cuts, smooth edges, and minimal chipping, making it ideal for applications requiring high tolerance levels. The surface finish achieved with diamond machining is typically smoother compared to other methods, which is critical for industries like optics and advanced ceramics.
2. Superior Performance with Hard, Brittle Materials
Diamond machining excels where other methods struggle, particularly with hard and brittle materials like glass, ceramics, and certain composites. These materials are prone to cracking or breaking under conventional cutting forces. Diamond’s hardness and cutting ability allow it to process these materials without causing structural damage, ensuring a high-quality finish and minimal waste.
3. Long Tool Life and Durability
Diamond tools are known for their longevity and durability. Because diamonds are so hard, the tools wear down much slower than those made of traditional materials like carbide or high-speed steel. This extended tool life not only reduces replacement costs but also minimizes downtime in production processes, leading to greater overall efficiency and cost savings.
Limitations of Diamond Machining
1. Cost of Diamond Tools
One of the primary limitations of diamond machining is the cost of diamond tools. Due to the expense involved in manufacturing and processing diamonds, these tools can be significantly more expensive than those made from conventional materials. While the higher initial investment is often offset by the long tool life and superior performance, the upfront costs can be prohibitive for some operations, especially when working with materials that may not fully utilize diamond’s unique properties.
2. Limited Effectiveness with Softer Materials
Diamond tools are less effective when working with softer materials, such as plastics, wood, or certain metals like aluminum. In these cases, the hardness of the diamond can cause over-cutting, leading to poor surface finishes or even damage to the material. For softer materials, alternative tools like carbide or high-speed steel may be more appropriate, as they provide better control and surface quality without the risk of over-machining.
Types of Diamond Tools
Diamond Blades
Diamond blades are designed for high-precision cutting applications, particularly for hard and brittle materials. They come in various forms, including ultra-thin blades for slicing and dicing delicate materials, and segmented blades for cutting through thicker, more robust substances like stone and concrete.
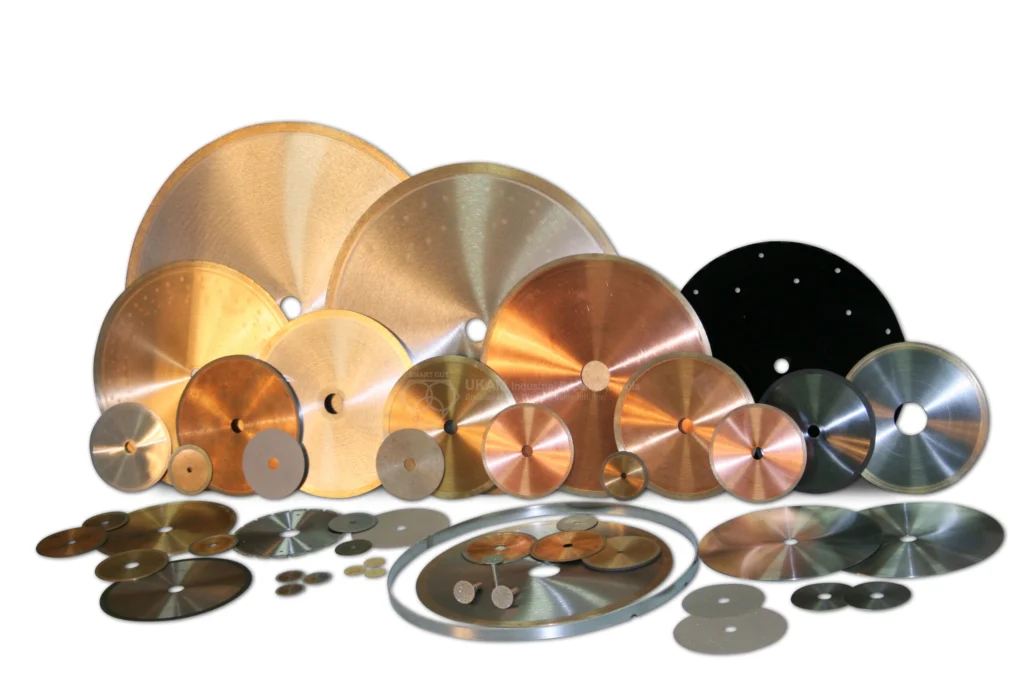
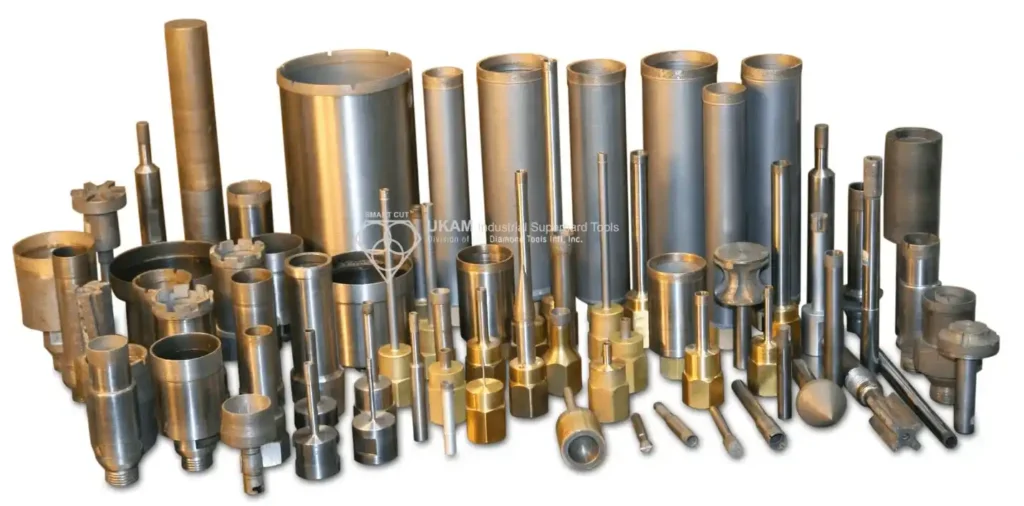
Diamond Core Drills
Diamond core drills are used for creating precise, clean holes in hard materials such as glass, ceramics, and composites. These drills are equipped with diamond grit along the cutting edges, allowing them to penetrate tough materials without causing cracks or chipping. Core drills are widely used in industries like construction, materials research, and electronics.
Diamond Carving Points
Diamond carving points are small, precise tools used for intricate carving and shaping applications in hard materials such as stone, glass, and ceramics. These tools are essential in industries like fine art, jewelry making, and dental technology, where detailed precision is required.
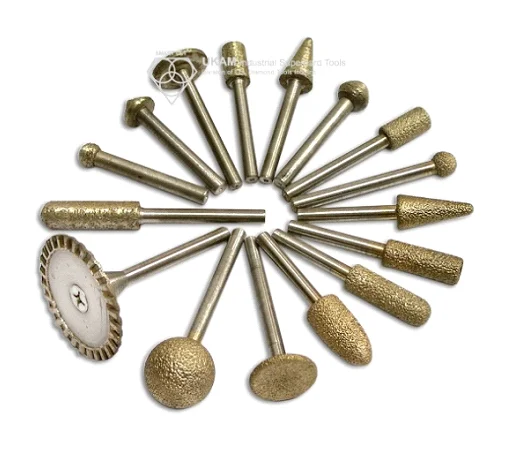
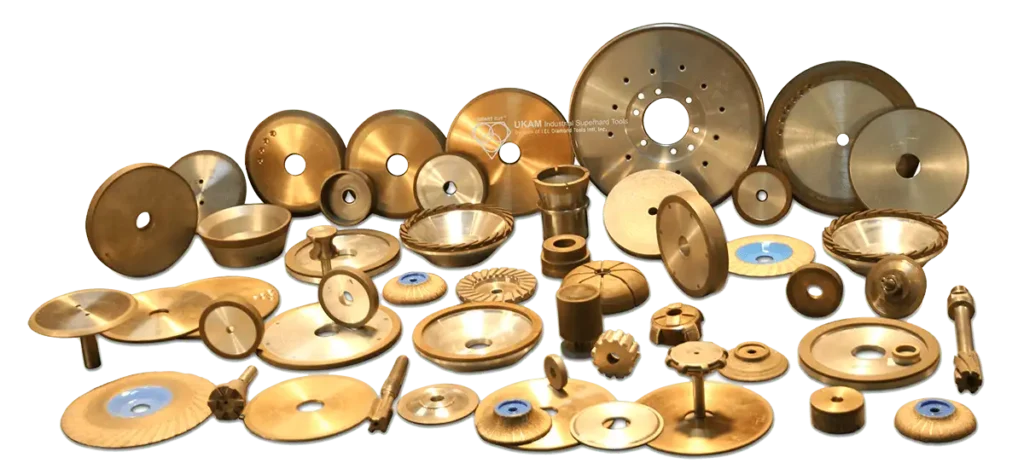
Diamond & CBN Grinding Wheels
Diamond grinding wheels are used for fine grinding and finishing applications. They are highly effective in polishing and smoothing hard materials, ensuring a flawless surface finish. Diamond grinding wheels are commonly used in metallography, optics, and the semiconductor industry, where smooth, polished surfaces are critical.
Feature/Aspect |
Details |
---|---|
Material Suitability |
Best for hard, brittle materials such as glass, ceramics, stone, metals, and composites. Not ideal for softer materials like plastics or wood. |
Precision |
Extremely high precision with clean cuts and minimal chipping, especially in hard and brittle materials. |
Surface Finish |
Excellent surface finish with smooth edges, making it ideal for applications requiring tight tolerances and fine detail. |
Cutting Speed |
Slower than laser and water jet for thick materials, but suitable for delicate operations requiring accuracy. |
Cost |
High initial cost due to the expense of diamond tools, but the long tool life often offsets the cost in the long term. |
Tool Durability |
Long tool life, as diamond’s hardness ensures the tools wear down slowly, leading to reduced tool replacement and downtime. |
Heat Impact |
No heat generation during cutting, making it ideal for heat-sensitive materials. |
Applications |
Commonly used in industries like optics, ceramics, stone processing, aerospace, and electronics where precision and surface finish are critical. |
Tool Types |
Diamond blades, core drills, carving points, grinding wheels, and other diamond-impregnated tools for various machining processes. |
Limitations |
High cost of tools and limited effectiveness with soft materials, where over-cutting or poor surface finish can occur. |
Environmental Impact |
Requires coolant for lubrication, but overall minimal environmental impact compared to other machining methods. |
Understanding Laser Machining
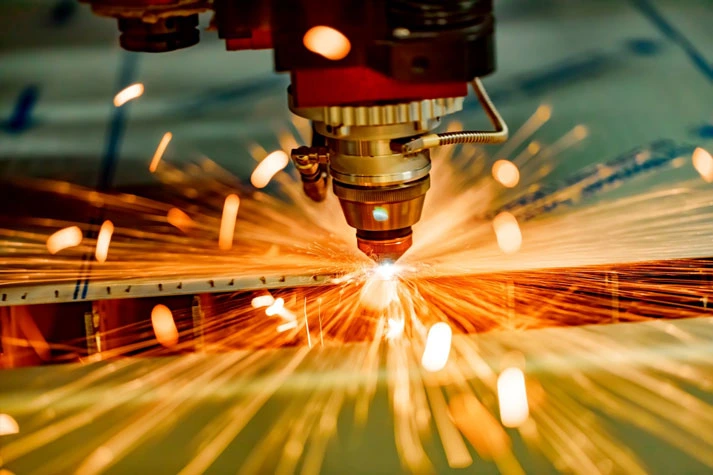
Laser machining refers to the use of high-powered, focused beams of light to cut, drill, or engrave materials with extreme precision. Laser cutting and drilling technology rely on the energy generated by the laser to heat, melt, or vaporize the material, allowing for highly accurate material removal. This method is widely used across industries where intricate cutting, drilling, and engraving are required due to its ability to handle complex designs and geometries. The process is non-contact, meaning that there is no physical tool touching the material, reducing tool wear and enabling the machining of delicate and intricate parts without damaging the workpiece.
Laser machining is versatile and can process a variety of materials, including metals (such as steel, aluminum, and titanium), plastics (including acrylics, polycarbonates, and PVC), and composites (like carbon fiber and glass-reinforced plastics). This flexibility makes laser machining a preferred choice in industries such as electronics, automotive, aerospace, and medical device manufacturing, where precision and complexity are crucial.
Advantages of Laser Machining
One of the main advantages of laser machining is its high precision and cutting speed. Lasers can produce extremely accurate cuts with tight tolerances, which is essential for industries that require intricate and detailed designs. The cutting speed is also very fast, particularly for thin materials, allowing for efficient production without sacrificing accuracy.
Since laser machining is a non-contact process, there is no direct interaction between the laser beam and the material. This significantly reduces tool wear and eliminates the need for frequent tool replacements, making the process cost-effective over time. Additionally, the lack of physical contact ensures that delicate or thin materials are not damaged or deformed during machining.
Laser machining is also capable of cutting complex geometries that would be difficult or impossible to achieve with traditional machining methods. The laser’s precision enables it to follow intricate designs, sharp angles, and tight curves with ease, making it ideal for applications such as electronics (cutting circuit boards), automotive parts, and medical devices (like surgical instruments and implants).
Limitations of Laser Machining
Despite its many advantages, laser machining does have limitations. One significant drawback is the creation of heat-affected zones (HAZ). The laser's intense heat can cause thermal distortion in the material, particularly around the edges of the cut. This is especially problematic for heat-sensitive materials, which may warp, crack, or change in structure due to the heat generated by the laser.
Another limitation is the high energy consumption associated with laser machining. The equipment required to generate and sustain the laser beam consumes large amounts of power, which can drive up operational costs, particularly for long-term or large-scale production runs.
Laser machining also has limited effectiveness with thicker materials. While lasers are excellent for cutting thin materials quickly and precisely, their efficiency decreases as the material thickness increases. For very thick or dense materials, the laser may struggle to cut through cleanly, and the heat buildup can exacerbate distortion or material degradation. This makes laser machining less suitable for cutting thick metals or composites compared to methods like water jet cutting or diamond tools.
Summarizing the key aspects of Laser Machining
Feature/Aspect |
Details |
---|---|
Material Suitability |
Metals (e.g., steel, aluminum, titanium), plastics (e.g., acrylics, polycarbonates), composites (e.g., carbon fiber, glass-reinforced). |
Precision |
Extremely high precision, capable of tight tolerances and intricate designs. |
Cutting Speed |
Very fast for thin materials; efficiency decreases with increasing thickness. |
Contact with Material |
Non-contact process, reducing tool wear and enabling delicate machining. |
Surface Finish |
Generally good, but may require post-processing due to potential heat-affected zones (HAZ). |
Tool Wear |
No direct tool wear since the laser does not physically touch the material. |
Complex Geometries |
Capable of cutting highly complex shapes and detailed patterns with sharp angles and tight curves. |
Heat Impact |
Heat-affected zones (HAZ) may cause material distortion, especially in heat-sensitive materials. |
Energy Consumption |
High energy consumption; lasers require significant power to operate, especially for long production runs. |
Thickness Capacity |
Effective for thin materials; limited effectiveness with very thick or dense materials. |
Applications |
Ideal for electronics, automotive, aerospace, and medical devices requiring precision cuts, complex shapes, and intricate designs. |
Limitations |
Thermal distortion in heat-sensitive materials, limited capability for cutting thick materials, high energy costs. |
Understanding Water Jet Machining
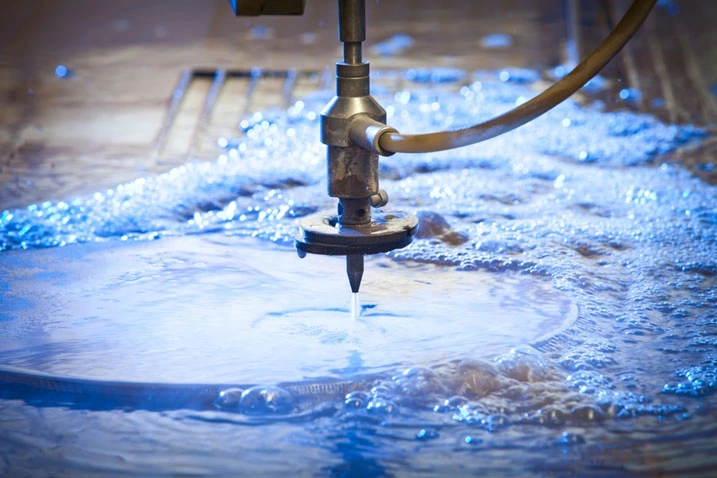
Water jet machining is a cutting process that uses a high-pressure stream of water to cut through various materials. There are two main types of water jet cutting: pure water jet cutting and abrasive water jet cutting.
-
Pure Water Jet Cutting involves using only high-pressure water to cut through softer materials like rubber, foam, plastics, and some composites. This method is effective for precise cutting without the use of abrasives, and is often used in industries like textiles, packaging, and food processing.
-
Abrasive Water Jet Cutting incorporates abrasive particles, such as garnet, into the high-pressure water stream. This allows the water jet to cut through harder and more durable materials like metals, ceramics, glass, and stone. The abrasive particles enhance the cutting power of the water jet, making it suitable for a wide range of industrial applications.
Water jet technology is unique in that it uses a cold cutting process. This means that no heat is generated during the cutting operation, making it an excellent choice for materials that are sensitive to thermal damage, such as composites, plastics, and metals prone to warping.
Materials Suited for Water Jet Cutting
Water jet machining is highly versatile and can cut a broad range of materials, making it popular across multiple industries. Some common materials that can be processed with water jet cutting include:
-
Metals: Steel, aluminum, titanium, copper, and other alloys can be cut with abrasive water jets, particularly for thicker materials where heat-affected zones (HAZ) would be problematic.
-
Glass: Glass can be cut without cracking or chipping, making water jet machining suitable for creating intricate shapes in glass panels.
-
Ceramics: Advanced ceramics such as alumina and silicon carbide can be cut with high precision.
-
Composites: Water jets are ideal for cutting fiber-reinforced composites like carbon fiber and Kevlar, as they prevent delamination and preserve material integrity.
-
Plastics and Foam: Pure water jets are often used to cut soft materials without the need for abrasives.
Advantages of Water Jet Machining
Despite its advantages, water jet machining does have some limitations. One key drawback is that it typically offers lower precision compared to diamond or laser machining. While water jets can achieve accurate cuts, the edges may not be as sharp or smooth, and post-processing may be required for precision finishes, especially in applications that demand tight tolerances.
Water jet machining also tends to have slower cutting speeds, particularly when processing harder materials. Although water jets can cut through thick or dense materials, the cutting process can be time-consuming compared to faster methods like laser cutting. This makes water jet machining less efficient for high-speed production in some cases.
Lastly, the maintenance of abrasive feed systems can be a challenge. Abrasive water jet cutting relies on a steady supply of abrasive materials to enhance cutting power, but the abrasive media can cause wear and tear on the equipment. Regular maintenance of the abrasive feed system is required to ensure consistent performance, which can increase operational costs over time. Additionally, disposal of the used abrasive material adds to both cost and environmental impact.
Limitations of Water Jet Machining
Despite its advantages, water jet machining does have some limitations. One key drawback is that it typically offers lower precision compared to diamond or laser machining. While water jets can achieve accurate cuts, the edges may not be as sharp or smooth, and post-processing may be required for precision finishes, especially in applications that demand tight tolerances.
Water jet machining also tends to have slower cutting speeds, particularly when processing harder materials. Although water jets can cut through thick or dense materials, the cutting process can be time-consuming compared to faster methods like laser cutting. This makes water jet machining less efficient for high-speed production in some cases.
Lastly, the maintenance of abrasive feed systems can be a challenge. Abrasive water jet cutting relies on a steady supply of abrasive materials to enhance cutting power, but the abrasive media can cause wear and tear on the equipment. Regular maintenance of the abrasive feed system is required to ensure consistent performance, which can increase operational costs over time. Additionally, disposal of the used abrasive material adds to both cost and environmental impact.
Comparison of Machining Methods Based on Material Types
Metals (e.g., Steel, Aluminum, Titanium)
Diamond Machining: Diamond tools can provide extremely high precision when cutting metals, particularly for delicate operations where tight tolerances and smooth surface finishes are required. However, diamond machining is generally slower when working with thick metals, as the process relies on abrasion rather than direct removal of material like laser or water jet cutting. Additionally, diamond tools tend to wear faster when working on harder metals.
Laser Machining: Laser machining is highly effective for fast and precise cuts in thin metals. It offers the advantage of high cutting speeds, especially for sheet metals. However, lasers can struggle with heat-sensitive alloys, where the intense heat generated by the laser can cause warping, distortion, or the creation of a heat-affected zone (HAZ). This can affect the material's structural properties, particularly with metals like aluminum and titanium, which are more susceptible to heat-related damage.
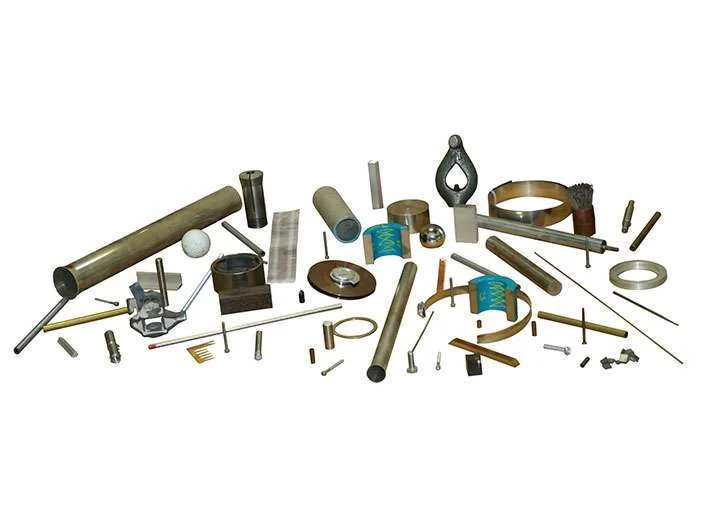
Water Jet Machining: Water jet machining is the preferred method for thicker metals and heat-sensitive alloys, as it operates without generating heat. This prevents the formation of heat-affected zones, making it an excellent choice for metals like titanium or certain high-strength alloys used in aerospace and automotive applications. While water jets are effective for thicker materials, the precision may be slightly lower compared to laser or diamond machining.
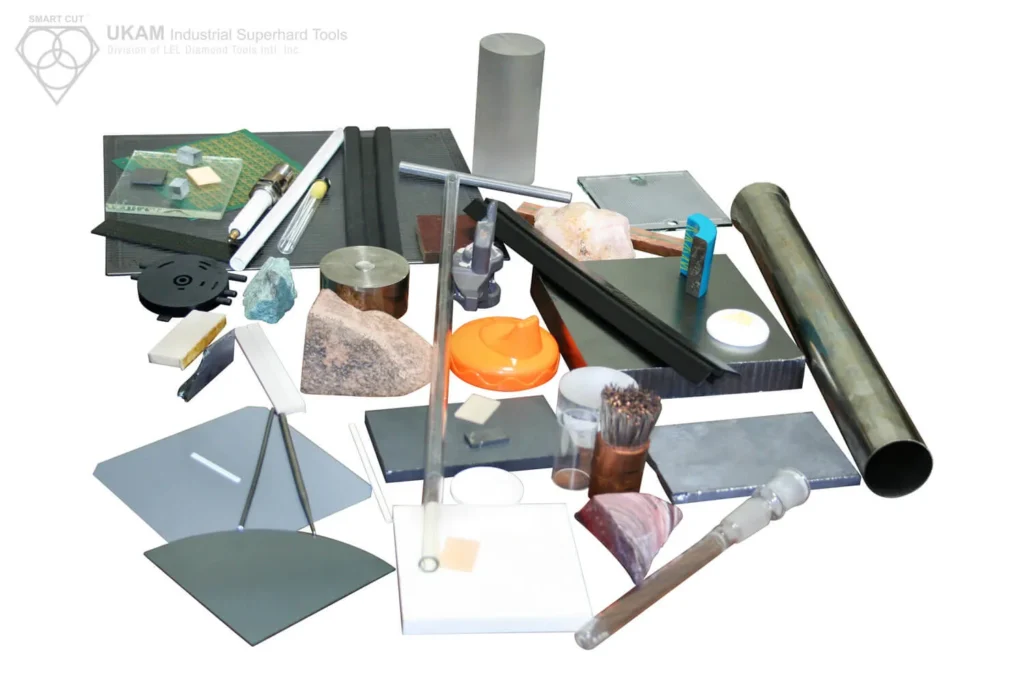
Hard Materials (e.g., Glass, Ceramics, Stone)
Diamond Machining: Diamond tools are the most suitable option for working with hard materials such as glass, ceramics, and stone. These materials are brittle and prone to chipping or cracking, but diamond tools can cut them with minimal chipping and deliver smooth, precise cuts. Diamond tools are commonly used in industries like optics, construction, and materials science for these applications.
Laser Machining: Laser cutting can be effective for thin glass and some ceramics, providing precise cuts. However, the intense heat generated by the laser can cause thermal stress in materials like ceramics, leading to cracks or warping. For heat-sensitive hard materials, laser cutting may not always be the best choice, especially if maintaining the structural integrity of the material is critical.
Water Jet Machining: Water jets are excellent for cutting thicker materials such as stone or dense ceramics, as the process does not produce heat and therefore avoids thermal stress. While water jet cutting is versatile for hard materials, it tends to be less precise than diamond machining, making it less suitable for applications where fine tolerances or high-quality surface finishes are required.
Soft Materials (e.g., Plastics, Composites)
Diamond Machining: Diamond tools are generally less effective for soft materials like plastics, as they tend to over-cut the material, resulting in poor surface finishes or unnecessary material removal. For softer materials, diamond tools may not provide the desired level of control.
Laser Machining: Laser cutting is often the best option for high-speed, precise cutting of plastics. The non-contact nature of the laser ensures smooth edges and minimal material waste, making it ideal for industries like packaging, electronics, and medical device manufacturing. However, care must be taken with heat-sensitive plastics to avoid melting or warping due to the laser's heat.
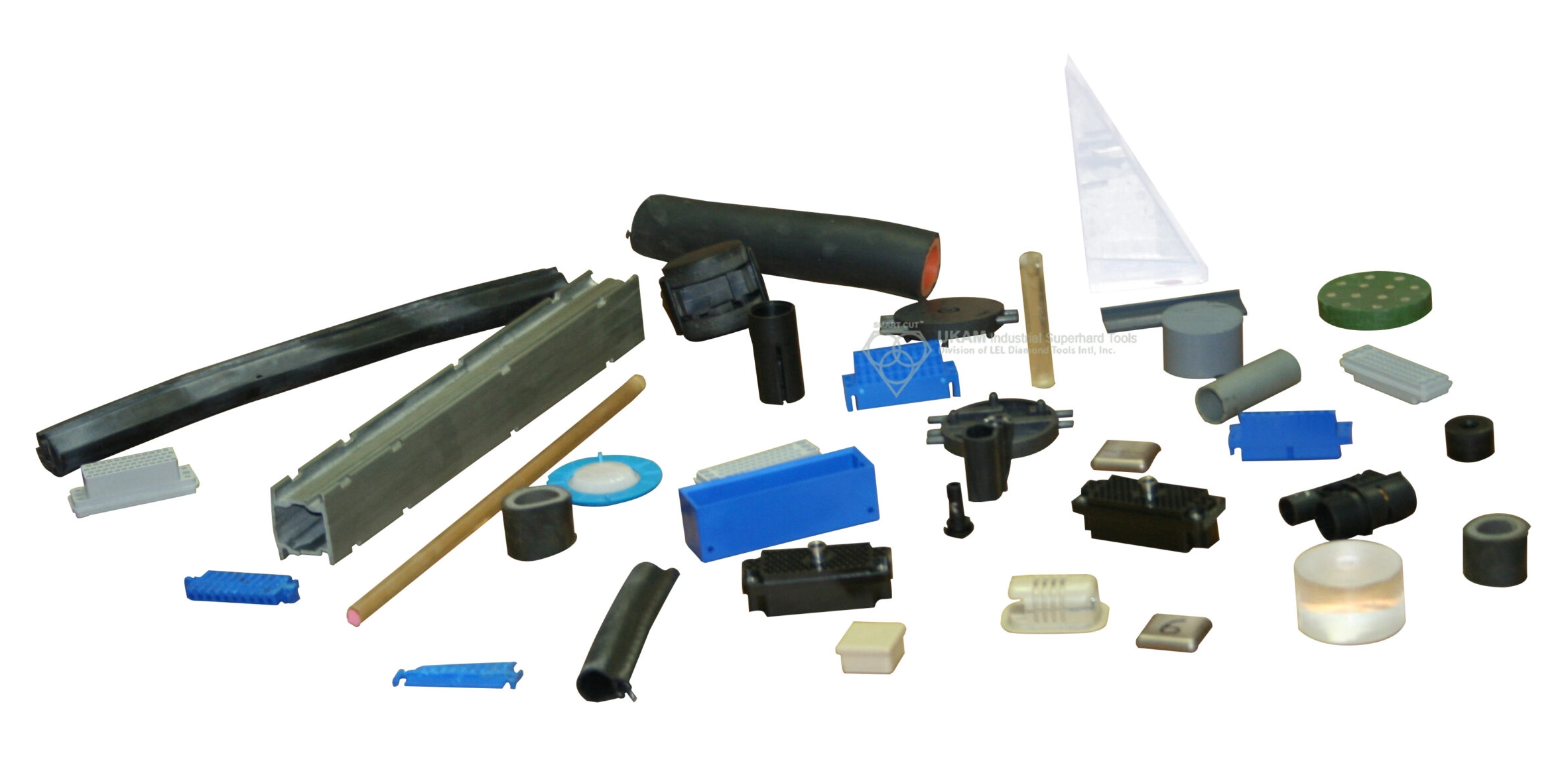
Water Jet Machining: Water jets are often preferred for composites and plastics, as they can cut these materials without causing thermal damage or delamination. Since the process involves no heat, it is particularly useful for materials that are prone to warping or distortion under high temperatures. Water jets provide clean cuts, though they may not be as fast or as precise as laser cutting for thin plastics.
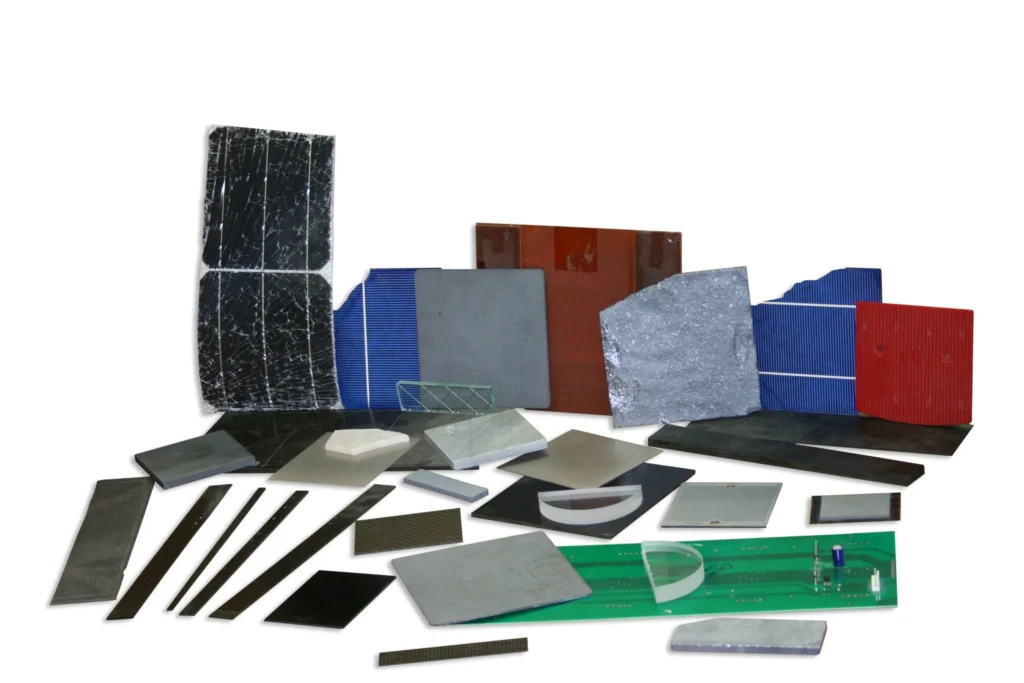
Advanced Composites (e.g., Carbon Fiber, Kevlar)
Diamond Machining: Diamond tools are capable of providing clean cuts in advanced composites like carbon fiber and Kevlar, but they generally operate slower than laser or water jet methods. The diamond tooling ensures that there is minimal damage to the material during the cutting process, making it suitable for applications where the integrity of the composite must be preserved.
Laser Machining: Laser cutting is not ideal for advanced composites due to the risk of delamination or heat distortion. The heat generated by the laser can cause the layers of the composite to separate, affecting the strength and durability of the material. This makes lasers less suitable for critical applications in industries like aerospace and automotive, where composite integrity is vital.
Water Jet Machining: Water jet cutting is considered the best option for advanced composites, as it offers clean, smooth edges without causing any thermal damage or delamination. The cold cutting process ensures that the integrity of the composite is maintained, making it ideal for cutting complex shapes in carbon fiber, Kevlar, and other high-performance composites used in industries like aviation, defense, and sports equipment.
Comparison Table
Material Type |
Diamond Machining |
Laser Machining |
Water Jet Machining |
---|---|---|---|
Metals (Steel, Aluminum, etc.) |
High precision, slow on thick metals. |
Fast, precise for thin metals, heat issues. |
Best for thick metals, no heat distortion. |
Hard Materials (Glass, Ceramics) |
Precise, minimal chipping. |
Effective on glass, thermal stress on ceramics. |
Good for thick materials, less precise. |
Soft Materials (Plastics, Composites) |
Less effective, over-cutting risk. |
High speed and precision, risk of melting. |
Preferred for composites, prevents delamination. |
Advanced Composites (Carbon Fiber, Kevlar) |
Clean cuts, slower. |
Risk of delamination, heat distortion. |
Best for clean, smooth edges, no heat damage. |
Cost Considerations
When comparing diamond machining, laser machining, and water jet machining, cost is a crucial factor to consider. Each method involves different levels of initial investment, operating costs, and ongoing maintenance, which can significantly impact a business's bottom line.
Initial Investment
The initial investment for each machining method varies based on the complexity and durability of the equipment. Diamond machining generally requires a lower initial investment compared to laser or water jet systems. Diamond tools such as blades, core drills, and grinding wheels are individually less expensive than the sophisticated machinery needed for laser and water jet cutting. However, high-precision diamond tools, particularly those designed for specialized applications, can be costly, but still less than the upfront cost of advanced laser and water jet systems.
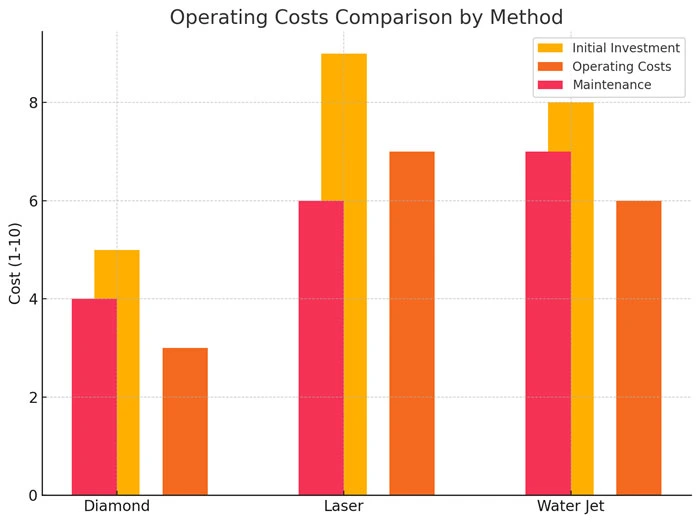
Laser machining involves a much higher initial investment. A laser cutting system includes high-power laser generators, motion control systems, and safety equipment, making the capital expenditure substantial. Depending on the power and capabilities of the laser (e.g., fiber vs. CO2 lasers), the cost can range significantly, with higher-end laser systems costing several hundred thousand dollars. This makes laser systems more expensive to acquire initially, particularly for companies that require high precision or large-scale production capabilities.
Water jet systems also have a high initial investment, often similar to or higher than laser systems. These machines require a high-pressure pump, abrasive delivery systems (for abrasive water jets), and intricate control mechanisms to maintain cutting accuracy. Water jet machines are especially costly when designed to cut thicker materials or large workpieces. However, for companies that need to cut a wide variety of materials, including thick metals, composites, and ceramics, the versatility of water jet systems may justify the higher upfront cost.
Operating Costs
Operating costs vary significantly between the three methods.
Diamond tools
Diamond tools have relatively low operating costs once purchased, as they have long tool lives, particularly when used on hard materials. The main cost factor is tool wear, which depends on the material being processed and the quality of the diamond tool. Although diamond tools last longer than traditional cutting tools, when they wear out, they must be replaced, which can be costly if the tools are highly specialized.
Laser machining, while highly efficient, has considerable energy consumption costs. Running a high-powered laser system requires significant electrical power, and the higher the laser power, the more energy it consumes. This energy usage can be a major cost driver, particularly in industries with large-scale production or where continuous operation is required. However, laser machining has very little tool wear since it is a non-contact process, reducing costs related to tool replacement.
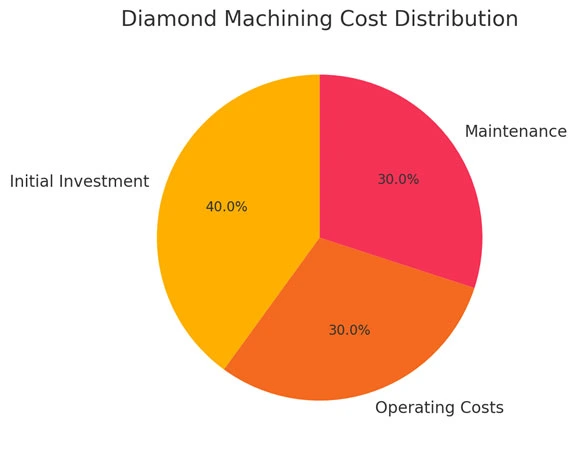
Water jet machining also incurs notable operating costs, primarily due to the need for abrasive materials in the abrasive water jet cutting process. Abrasive particles, usually garnet, must be continually replenished, and the volume of abrasive needed depends on the thickness and hardness of the material being cut. Abrasive costs can add up quickly, especially in high-volume production environments. Additionally, water consumption and the disposal of spent abrasives can contribute to ongoing operational expenses. While water jet machines have relatively low energy consumption compared to lasers, the abrasive feed system and water use make them more expensive to operate than diamond machining.
Maintenance and Downtime
Maintenance and downtime are key cost factors that influence long-term operational efficiency. Diamond tools, being extremely durable, have a long lifespan when used appropriately, particularly for cutting hard materials like glass, ceramics, and metals. Their robustness reduces the frequency of replacements and minimizes downtime related to tool changes. However, diamond tools do eventually wear out, especially when used on abrasive materials, and specialized tools can be costly to replace. Still, the longevity of diamond tools often offsets the cost of frequent replacements, making them a cost-effective option in terms of maintenance.
Laser systems
while non-contact and thus less prone to mechanical wear, require regular maintenance of the laser source, optics, and cooling systems. Dust and debris can affect the optics, and the laser’s power source may degrade over time, leading to costly repairs or replacements. Additionally, any misalignment in the laser system can lead to downtime, as recalibration may be needed to maintain cutting accuracy. The more sophisticated the laser, the more likely it is to require specialized maintenance, which can drive up costs and lead to production interruptions.
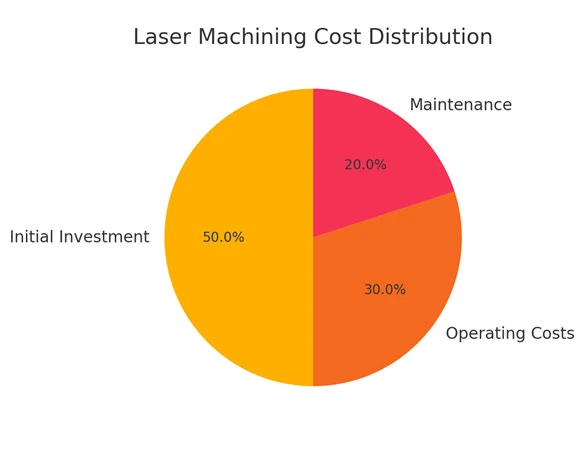
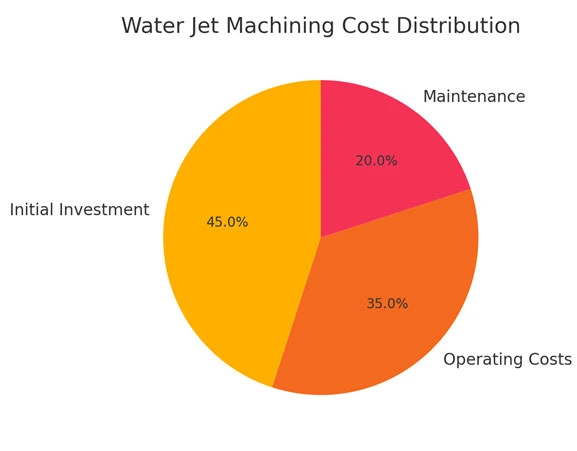
Water jet systems
require ongoing maintenance, especially in the abrasive feed system. The nozzles and orifices through which the high-pressure water and abrasive particles pass experience significant wear due to the constant flow of abrasive materials. These components need regular replacement, and failing to maintain them can result in decreased cutting precision or equipment damage. Additionally, pumps and high-pressure systems must be monitored and serviced regularly to avoid breakdowns. The need to dispose of spent abrasive also adds to the maintenance burden. Water jet systems, while highly effective for a range of materials, often have more frequent maintenance requirements than laser or diamond machining, which can result in higher operational costs and potential downtime.
Comparison table summarizing the cost considerations for Diamond Machining, Laser Machining, and Water Jet Machining:
Aspect |
Diamond Machining |
Laser Machining |
Water Jet Machining |
---|---|---|---|
Initial Investment |
Lower initial cost for individual tools, but specialized diamond tools can be expensive. |
High upfront cost for laser systems, especially high-powered ones. |
High initial cost for water jet systems, including pumps and abrasive delivery systems. |
Operating Costs |
Relatively low operating costs; the main expense is tool wear. |
High energy consumption; low tool wear. |
Abrasive costs can be significant; moderate energy and water costs. |
Tool Wear |
Tools have long life when used on hard materials but wear faster on abrasive materials. |
No direct tool wear due to non-contact process. |
Nozzle and orifice wear due to abrasive materials; regular replacement required. |
Energy Consumption |
Low energy consumption overall. |
High energy usage, particularly for high-powered lasers. |
Moderate energy usage; water and abrasive usage adds to costs. |
Maintenance & Downtime |
Diamond tools last long, reducing downtime, but need replacement when worn. |
Laser optics and cooling systems require regular maintenance, but mechanical wear is minimal. |
Abrasive feed systems and high-pressure pumps require frequent maintenance; downtime for part replacement is common. |
Material Suitability |
Best for hard, brittle materials; low cost for soft materials but limited effectiveness. |
Ideal for thin, heat-tolerant materials; high running cost for thick or heat-sensitive metals. |
Versatile for a wide range of materials, but abrasive costs and frequent maintenance add to operating expenses. |
Lifespan |
Long tool life under normal use; tool replacement cost can be high for specialized tools. |
Long lifespan of the laser system, but components like optics and cooling systems need periodic servicing. |
Shorter lifespan for high-wear components like nozzles and abrasive systems, increasing replacement costs. |
Precision and Surface Finish
When evaluating machining methods, precision and surface finish are critical factors, especially in industries that require detailed, high-quality results. Each machining method—diamond, laser, and water jet—offers unique capabilities in terms of precision and the surface finish they produce.
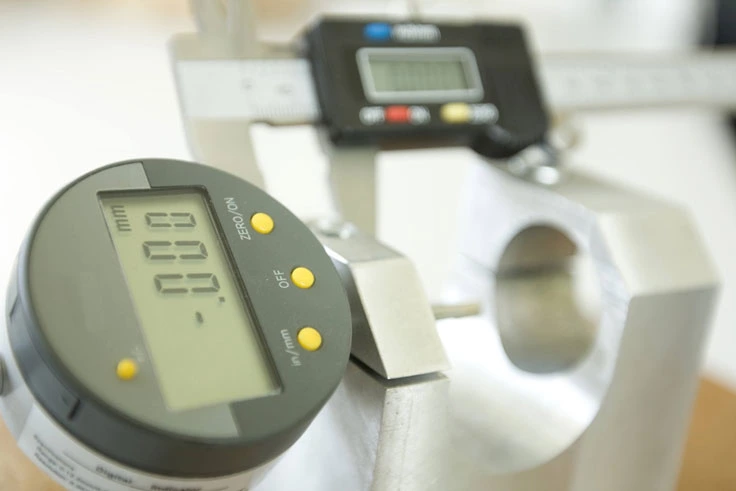
Diamond tools
Diamond tools are renowned for providing superior surface finishes, particularly when working with hard and brittle materials like glass, ceramics, and stone. The extreme hardness of diamond allows these tools to make clean, precise cuts without causing significant damage to the material. Because diamond tools cut with minimal force and friction, they result in smooth surfaces and reduce the risk of chipping or cracking, which is essential when working with brittle materials. This makes diamond tools ideal for industries like optics, ceramics, and semiconductor manufacturing, where high levels of accuracy and surface quality are required.
In addition to their cutting ability, diamond tools also excel in grinding and polishing applications, providing fine, polished finishes that are difficult to achieve with other machining methods. This advantage extends to materials like hard metals and composites, where diamond tools can achieve a flawless surface finish that may not be possible with laser or water jet methods.
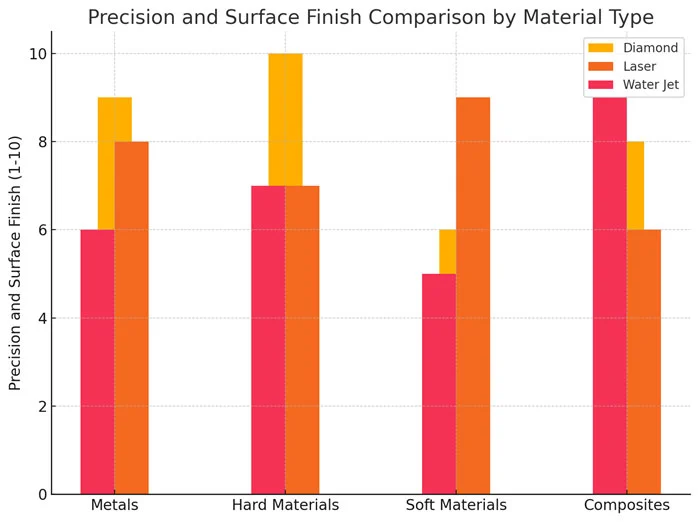
Laser Machining
Laser machining is highly regarded for its high precision, especially when cutting thin materials or intricate shapes. The laser beam's narrow focus allows for tight tolerances and clean cuts, making it a preferred choice in industries such as electronics, aerospace, and medical device manufacturing. Lasers can accurately cut complex geometries, including sharp corners and intricate patterns, without direct contact with the material.
However, one downside of laser machining is the potential for thermal effects on the surface of the material. Since lasers rely on intense heat to cut through materials, this can create heat-affected zones (HAZ) near the cut, where the material's properties may be altered due to the high temperatures. This can lead to surface imperfections, such as warping, melting, or changes in the material's structure, especially in heat-sensitive materials like certain plastics and metals. As a result, while laser cutting can achieve high precision, the surface finish may require post-processing to eliminate the effects of heat exposure.
Despite this limitation, lasers are excellent for cutting thin materials with high precision, and the resulting surface finish is typically very smooth for materials that can tolerate the heat, such as metals and plastics.
Water Jet Machining
Water jet machining offers clean cuts and is particularly effective for cutting thicker materials and heat-sensitive substances. Since water jets do not produce heat during the cutting process, they avoid the risk of thermal distortion, making them an ideal choice for materials that would otherwise warp or melt under heat, such as composites, rubber, and some metals.
line graph representing the Precision vs. Material Thickness for diamond, laser, and water jet machining methods:
-
Diamond Machining: Precision starts high but gradually decreases as material thickness increases, showing lower precision with thicker materials.
-
Laser Machining: Follows a similar trend to diamond, with high precision at thinner materials and a sharp decrease as the thickness grows.
-
Water Jet Machining: While precision starts lower than diamond or laser, it remains consistent and even improves with thicker materials, indicating that water jets handle thicker materials more effectively but with lower initial precision.
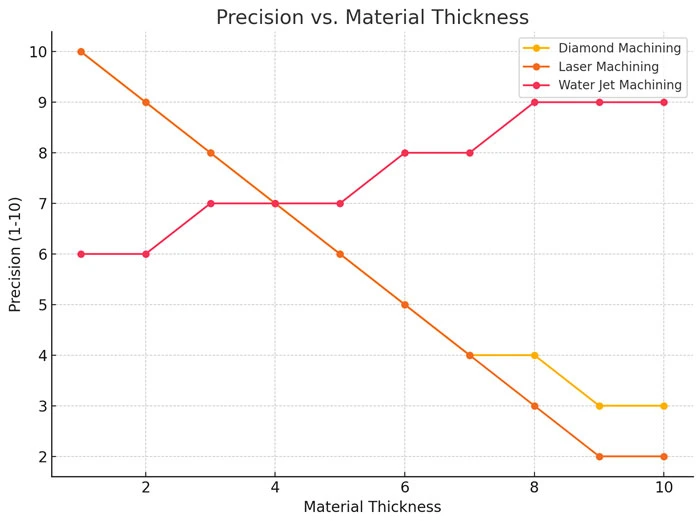
However, water jet machining generally offers lower precision compared to diamond or laser cutting. While water jets can achieve accurate cuts, especially when using abrasive materials, the edges may not be as sharp or smooth as those produced by laser or diamond tools. The surface finish produced by water jet cutting tends to be rougher, especially in harder or denser materials, where the abrasive process can leave a slightly uneven surface.
Additionally, because water jet cutting is a mechanical process, the high-pressure water stream combined with abrasive particles can wear down the material edges, leading to a less refined finish. In applications where fine tolerances or highly polished surfaces are required, water jet machining may not be the best option without additional post-processing.
Comparison table summarizing the Precision and Surface Finish of Diamond Machining, Laser Machining, and Water Jet Machining:
Aspect |
Diamond Machining |
Laser Machining |
Water Jet Machining |
---|---|---|---|
Precision |
Extremely high precision, especially for hard and brittle materials. Achieves tight tolerances. |
High precision for intricate shapes and thin materials, but may suffer from heat-affected zones (HAZ). |
Moderate precision; capable of cutting thick materials but less accurate than diamond or laser. |
Surface Finish |
Superior surface finish, smooth and polished. Ideal for applications requiring minimal chipping or cracking. |
Clean surface finish but may require post-processing due to thermal effects like warping or melting. |
Clean cuts but rougher surface finish compared to diamond or laser; may require post-processing. |
Thermal Impact |
No heat generation, making it ideal for heat-sensitive materials. |
Generates heat, which can lead to surface warping or melting, particularly in heat-sensitive materials. |
No heat, preventing thermal damage to heat-sensitive materials. |
Best for Material Type |
Best for hard, brittle materials like glass, ceramics, and stone. |
Best for thin materials like metals and plastics, but heat-sensitive materials may require caution. |
Best for thick materials, composites, and heat-sensitive materials where thermal damage is a concern. |
Post-Processing Needed |
Rarely required, typically results in a polished finish. |
Sometimes needed to remove thermal distortion or imperfections from the heat-affected zone. |
Often required to smooth out rough edges, especially in thicker or harder materials. |
Environmental and Safety Considerations
When selecting a machining method, it is important to consider the environmental impact and safety concerns associated with each process. Diamond, laser, and water jet machining each present unique environmental challenges and safety considerations that must be factored into decision-making.

Diamond Machining
Diamond machining has a relatively low environmental impact, especially when compared to laser and water jet machining. Since diamond tools are mechanical in nature and do not involve the generation of heat or large amounts of waste, their overall environmental footprint is minimal. The primary environmental concern in diamond machining is the use of coolant for lubrication and heat dissipation during cutting or grinding operations. While the coolant itself can be recycled, its use requires proper management and disposal to prevent environmental contamination. In industrial settings, coolants must be carefully handled and disposed of according to environmental regulations, ensuring that harmful chemicals do not enter the water supply or surrounding ecosystems.
From a safety standpoint, diamond machining is generally considered safer than laser or water jet machining. The process does not generate fumes, heat, or high-pressure hazards, and the use of coolant further reduces risks of overheating. However, there are some risks of inhaling dust or small particles during machining, particularly when working with materials like ceramics or glass. Proper dust extraction systems or personal protective equipment (PPE) such as masks and goggles can mitigate these risks, ensuring a safe working environment for operators.
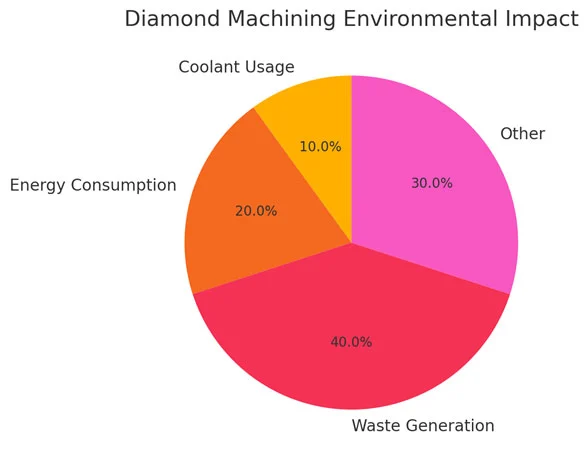
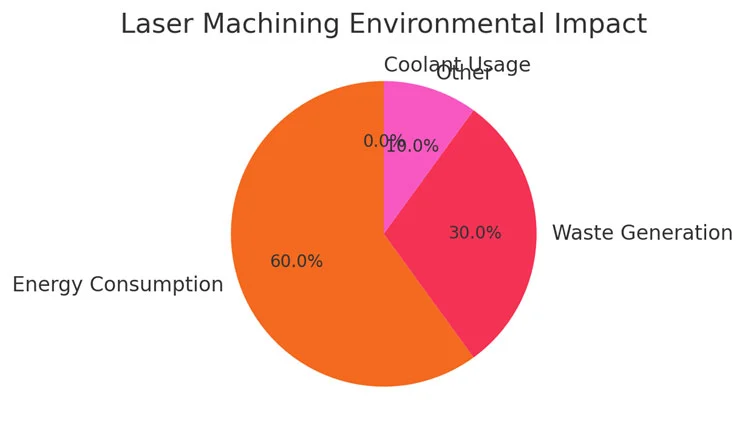
Laser Machining
Laser machining, while highly effective and precise, tends to have a higher environmental impact due to its energy-intensive nature. Laser cutting systems require significant amounts of power to generate the high-energy beams used in cutting or drilling materials. This high energy consumption contributes to the overall environmental footprint of the process, especially in industries with large-scale production requirements.
Additionally, laser machining can generate fumes and waste, particularly when cutting materials like plastics or metals. These fumes may contain harmful chemicals or particulate matter, necessitating proper ventilation systems to protect workers from exposure to toxic gases. Depending on the material being processed, waste byproducts may need to be collected and disposed of in a safe and environmentally responsible manner.
In terms of safety, laser machining requires stringent protocols due to the high-power lasers involved. Lasers can pose significant risks to operators, including burns, eye injuries, or fires if not properly contained or operated. Safety measures such as protective eyewear, enclosures for the laser cutting area, and interlocks to prevent accidental exposure are essential in laser machining environments. Additionally, operators need to be trained in proper laser safety protocols to minimize the risk of accidents.
Water Jet Machining
Water jet machining has a moderate environmental impact, primarily due to its high water consumption and the need for abrasive material management. Water jet systems use large volumes of water to generate the high-pressure streams required for cutting. Although the water can often be recycled within the system, the continuous operation of water jets necessitates significant water use, which may pose sustainability concerns in regions facing water scarcity.
In abrasive water jet cutting, abrasive materials such as garnet are mixed with the water stream to enhance cutting power. These abrasives become contaminated with material debris during the cutting process, creating a waste byproduct that must be disposed of properly. While some abrasives can be recycled or reused, contaminated abrasive waste often requires special handling and disposal to prevent environmental harm. Companies must adhere to local environmental regulations regarding the disposal of spent abrasives to avoid contaminating soil or water sources.
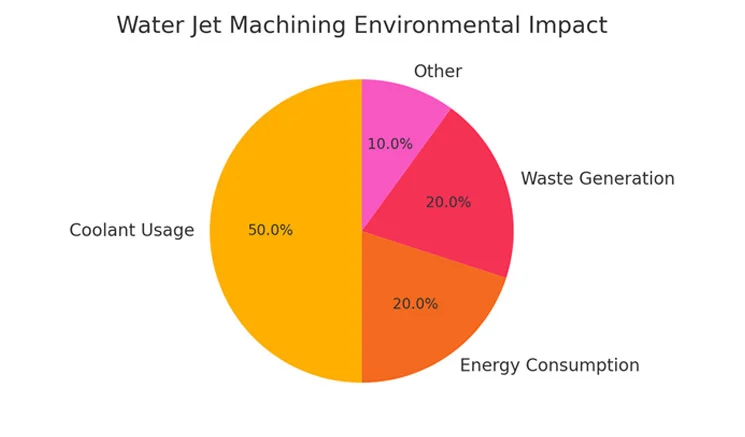
Water jet machining is generally safe for operators, as it does not produce hazardous fumes or heat during cutting. However, the high-pressure systems involved can pose risks, particularly in the event of equipment failure or operator error. Accidental exposure to the high-pressure water stream can result in severe injuries, so operators must be properly trained, and equipment must be regularly inspected and maintained to ensure safe operation. Additionally, personal protective equipment (PPE) such as gloves and goggles is recommended to protect workers from water and abrasive spray during operation.
Comparison table summarizing the Environmental and Safety Considerations of Diamond Machining, Laser Machining, and Water Jet Machining:
Aspect |
Diamond Machining |
Laser Machining |
Water Jet Machining |
---|---|---|---|
Environmental Impact |
Minimal impact, but requires proper disposal of coolant. |
High energy consumption and potential for harmful fumes and waste. |
Requires large amounts of water and abrasive management; moderate impact. |
Energy Consumption |
Low energy use, primarily mechanical. |
High energy use due to the power requirements of lasers. |
Moderate energy use, but high water consumption. |
Waste Management |
Coolant needs careful handling to prevent contamination. |
Potential fumes and waste byproducts from cutting metals or plastics. |
Spent abrasives need proper disposal; water recycling systems are common. |
Safety Concerns |
Safe with minimal risks; potential dust inhalation, requires PPE. |
Risks of burns, eye injury, and toxic fumes; strict laser safety protocols required. |
High-pressure water and abrasives can cause severe injury; operator training required. |
Fume/Heat Generation |
No heat or fumes generated during operation. |
High heat generation; potential toxic fumes from certain materials. |
No heat generated, reducing risk of thermal hazards or fumes. |
Water Consumption |
Minimal; coolant is used, but not in large volumes. |
None. |
High water usage; requires efficient recycling systems to minimize waste. |
Abrasive Management |
None required. |
None required. |
Requires management and disposal of abrasive materials (e.g., garnet). |
Choosing the Right Machining Method for Specific Applications
When selecting a machining method, it’s essential to consider the material being processed, the precision required, and the operational goals. Diamond, laser, and water jet machining methods each offer unique advantages, depending on the type of operation—whether it be cutting, drilling, milling, or other specialized tasks.

Cutting
When it comes to cutting, the choice between diamond, laser, and water jet machining depends largely on the material thickness and precision required for the job.
Diamond Cutting is ideal for hard and brittle materials such as glass, ceramics, and stone. The extreme hardness of diamond tools enables highly precise cuts with minimal chipping or cracking, even for thin and delicate materials. However, diamond cutting can be slower than laser or water jet cutting, especially for thicker materials, which may require multiple passes.
Laser Cutting excels in thin to moderate thickness materials like metals, plastics, and composites. The precision and speed of laser cutting make it a preferred option for intricate geometries and fine details. However, laser cutting generates heat, which can lead to thermal distortion or heat-affected zones (HAZ), particularly in heat-sensitive materials.
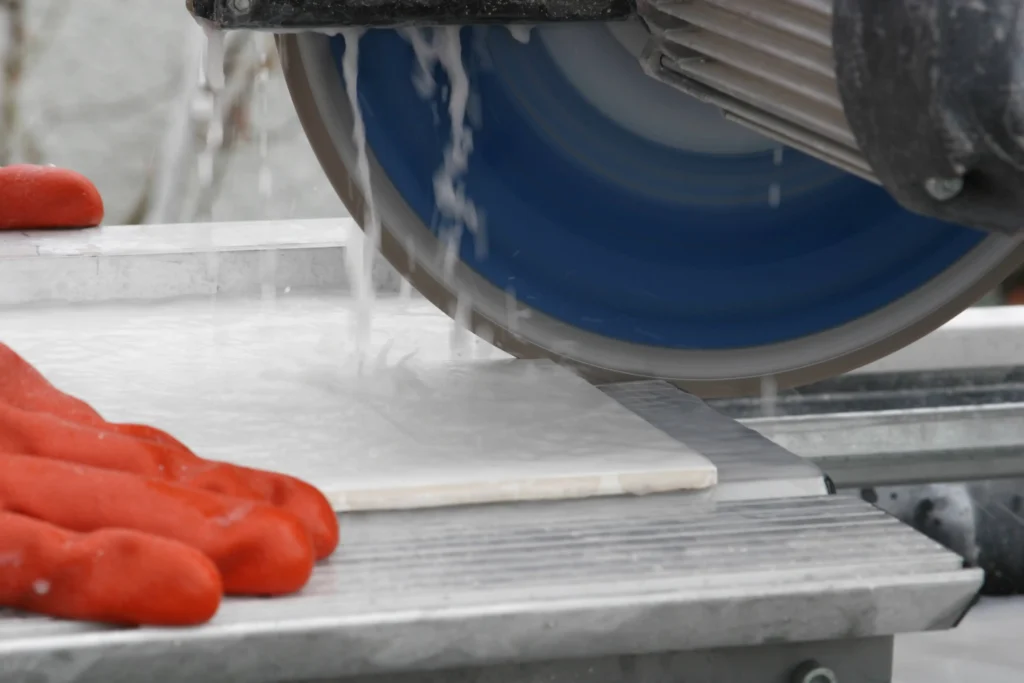
Water Jet Cutting is best suited for thicker materials or those sensitive to heat. Water jets can cut through metal, composites, glass, and ceramics without generating heat, thus avoiding thermal distortion. While water jet cutting can handle thicker materials, it generally offers lower precision compared to diamond or laser cutting, particularly for fine details or delicate materials.
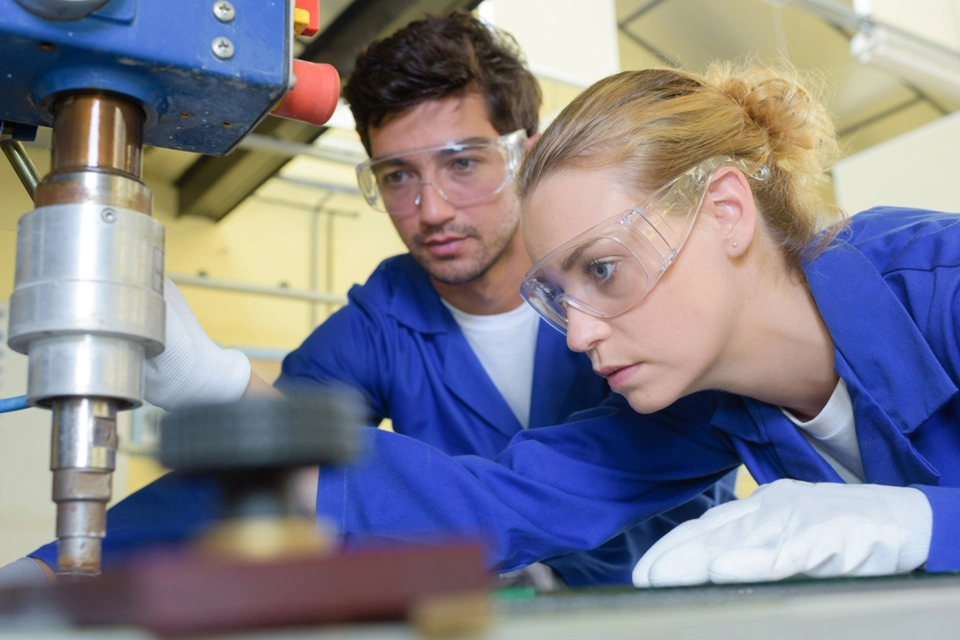
Drilling
For drilling operations, the choice between diamond, laser, and water jet methods depends on the material and the precision required.
Diamond Drilling is highly effective for hard and brittle materials like glass, ceramics, and stone. Diamond core drills can create precise, clean holes with minimal cracking or chipping. This method is widely used in industries like construction, optics, and materials science, where maintaining material integrity is crucial. Diamond drilling is not ideal for softer materials, where it may over-cut or damage the surface.
Laser Drilling provides high precision for thin materials such as metals and plastics, making it suitable for small, intricate holes. Laser drilling is used in industries like aerospace and electronics, where precise, small holes are required. However, the heat generated during laser drilling can distort certain materials, limiting its use for heat-sensitive substances.
Water Jet Drilling is less commonly used than cutting but can be applied to thicker materials or heat-sensitive composites. The cold-cutting process of water jets ensures no thermal damage, but the precision is typically lower compared to diamond or laser drilling. Water jet drilling may also be slower and require post-processing to achieve smooth surfaces.
Milling
For milling operations, precision and surface finish are critical, and the right method depends on the material being processed.
Diamond Milling is ideal for precision milling of hard, brittle materials such as ceramics, glass, and certain metals. Diamond milling tools provide a smooth surface finish and can handle intricate details without damaging the material. This method is commonly used in industries like aerospace, optics, and semiconductors, where both precision and material integrity are essential.
Laser Milling, while less common than laser cutting or drilling, can be applied to thin materials or delicate operations that require high precision. However, the thermal effects of laser milling make it less suitable for materials sensitive to heat. It is best used for small-scale precision work where intricate geometries are required.
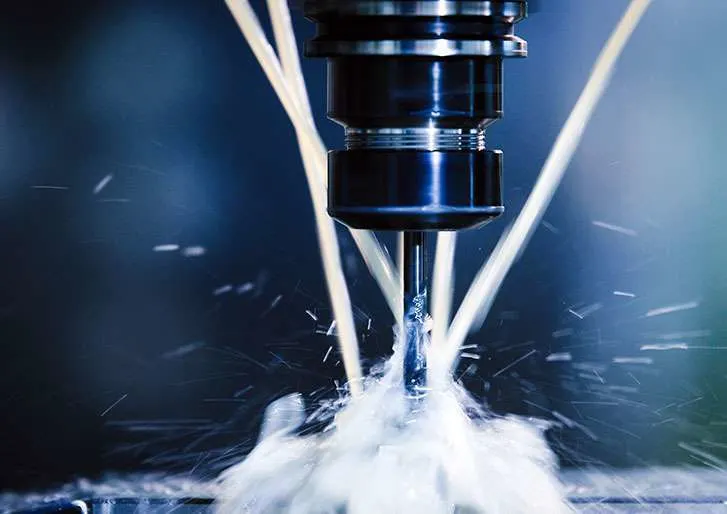
Water Jet Milling is rarely used due to the lower precision compared to diamond or laser methods, but it can be effective for rough milling or removing large amounts of material from thick or heat-sensitive materials. Water jet milling is often chosen when thermal effects need to be avoided, but it generally requires additional post-processing to refine the surface.
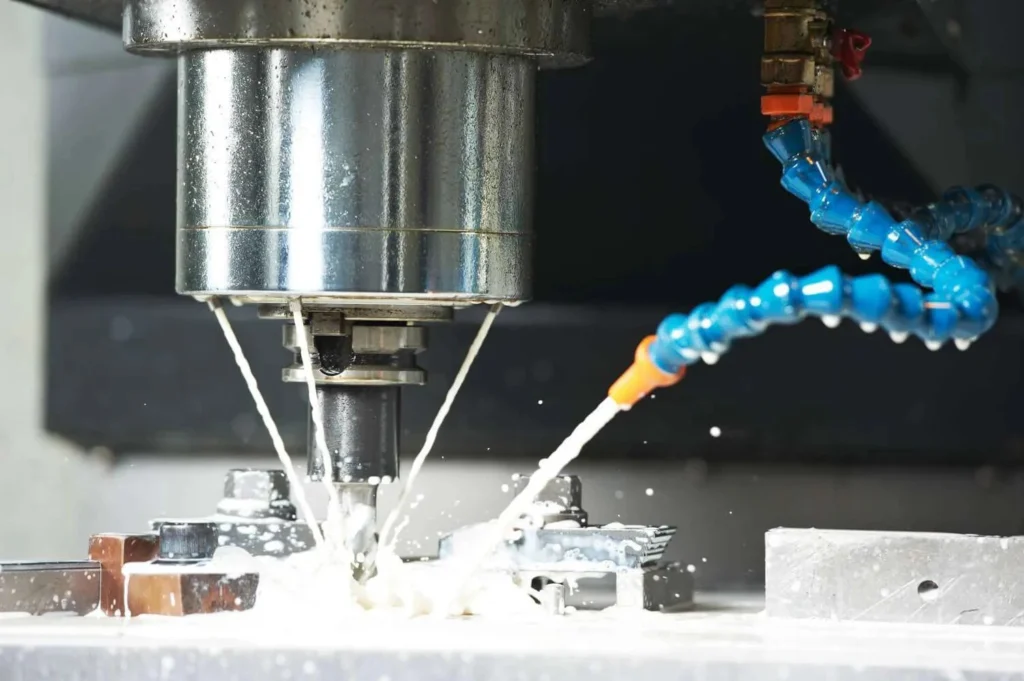
Specialized Operations
For specialized operations, choosing between diamond, laser, or water jet machining depends on the material requirements and operational goals.
Diamond Machining is best suited for hard, brittle materials that require a high-quality surface finish and precision cutting or drilling. Industries like optics, semiconductor manufacturing, and advanced materials research rely on diamond tools for these specialized applications, where the smallest imperfections can affect performance.
Laser Machining is optimal for operations requiring speed and precision in materials like metals, plastics, and composites. It is particularly valuable in industries such as aerospace, automotive, and electronics, where intricate designs and tight tolerances are essential. However, for heat-sensitive materials, lasers may not be the best option due to the risk of thermal damage.
Water Jet Machining is ideal for cutting or drilling thicker materials or composites that are sensitive to heat. Water jets can handle a wide range of materials, including metals, ceramics, and advanced composites like carbon fiber, making them versatile for industries like construction, defense, and manufacturing. While water jet machining lacks the precision of diamond or laser methods, it is the go-to option for heat-sensitive materials that could be damaged by other methods.
Comparison table summarizing the Choosing the Right Machining Method for Specific Applications between Diamond Machining, Laser Machining, and Water Jet Machining:
Aspect |
Diamond Machining |
Laser Machining |
Water Jet Machining |
---|---|---|---|
Cutting |
Best for hard, brittle materials (e.g., glass, ceramics, stone). High precision but slower for thicker materials. |
Excellent for thin materials (metals, plastics) with high precision; potential for thermal distortion in heat-sensitive materials. |
Ideal for thicker materials or heat-sensitive ones, but generally less precise than diamond or laser. |
Drilling |
Ideal for precise, clean holes in hard materials (e.g., glass, ceramics). Not suited for soft materials. |
Suitable for thin materials with small, intricate holes. Risk of thermal distortion in heat-sensitive materials. |
Effective for thicker materials without heat damage, but less precise; slower and may require post-processing. |
Milling |
Best for precision milling in hard materials, offering a smooth surface finish and intricate detail. |
Effective for delicate operations and small-scale precision, but not ideal for heat-sensitive materials. |
Used for rough milling in thick or heat-sensitive materials, with lower precision and requiring post-processing. |
Specialized Operations |
Excellent for high-quality, intricate operations in optics, semiconductors, and advanced materials. |
Preferred for high-speed, precise cutting in aerospace, automotive, and electronics. Not ideal for heat-sensitive materials. |
Ideal for cutting or drilling thick, heat-sensitive materials, or composites without thermal distortion. Versatile but lacks precision. |
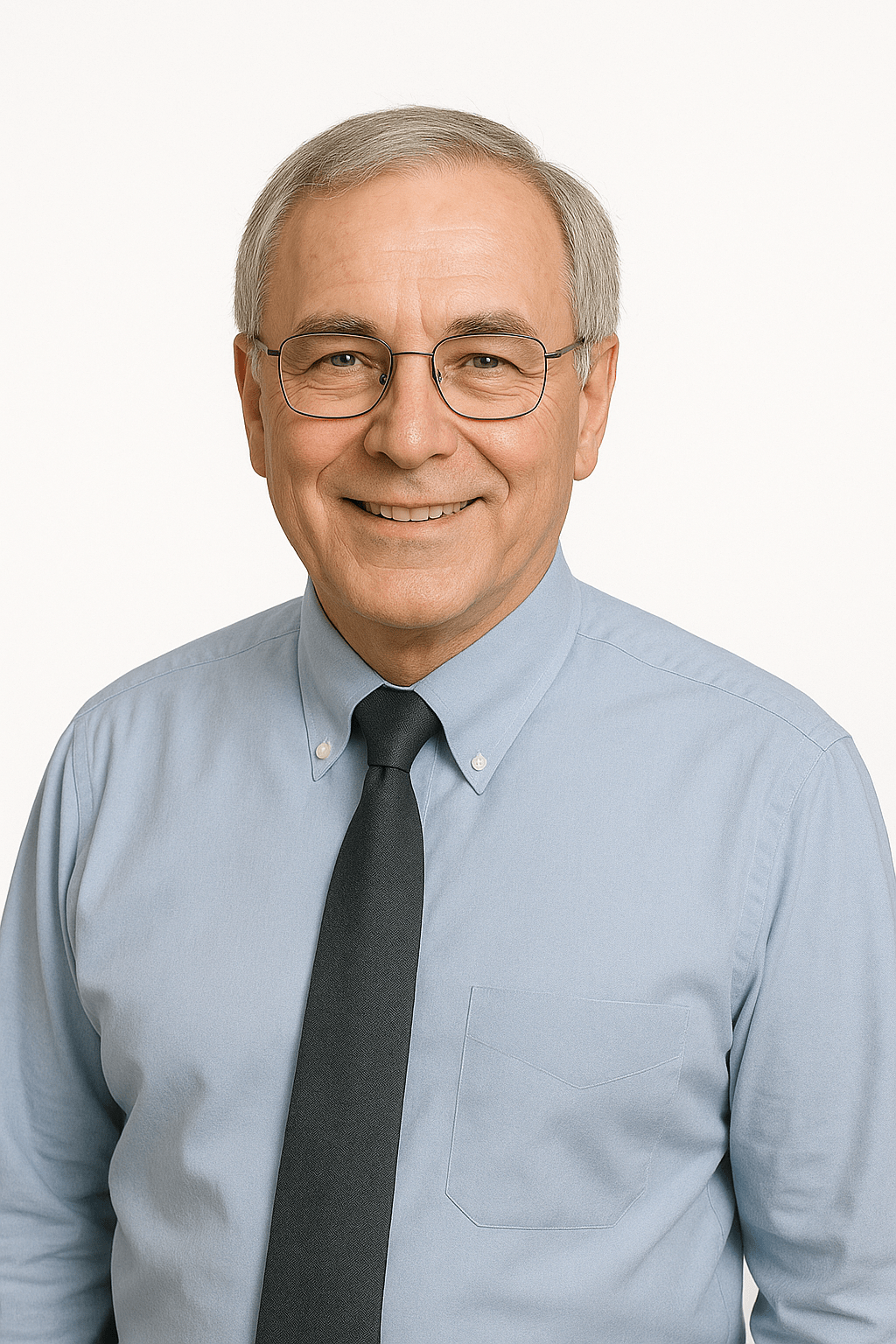
Alexander Schneider is a senior applications engineer and leading authority in the industrial diamond tooling industry, with over 35 years of hands-on experience in the development, application, and optimization of ultra-thin and high-precision diamond blades, diamond core drills, and diamond and CBN grinding wheels. His work spans a wide range of advanced materials including ceramics, glass, composites, semiconductors, and high-performance metals.
Throughout his career, he has collaborated with leading R&D institutions, national laboratories, and high-tech manufacturing companies across Europe, North America, and Asia, providing technical expertise and tailored solutions for demanding cutting and surface preparation applications.
Mr. Schneider has played a pivotal role in advancing precision cutting, sectioning, dicing, and grinding technologies used in research, production, and failure analysis. He is widely respected for his ability to optimize tool design and cutting parameters to meet exacting industry standards—balancing factors such as cut quality, blade life, material integrity, and process consistency.
As an author, Mr. Schneider is known for delivering practical, application-focused insights that translate complex technical challenges into clear, actionable strategies. His articles and technical guides serve as trusted resources for engineers, researchers, and manufacturers seeking to improve precision, reduce process variability, and enhance tool performance in critical applications.
ARE YOU USING RIGHT TOOLS
FOR YOUR APPLICATION?
LET US
HELP YOU
HAVING ISSUES WITH
YOUR CURRENT TOOLS?
Knowledge Center
How to Selecting Right Diamond Tools for your application
How to properly use Diamond Tools
Why use diamond
Diamond vs CBN (cubic boron nitride) Tools
What is Diamond Mesh Size and how to select best one for your application
What is Diamond Concentration and which to use for your application
Diamond Tool Coolants Why, How, When & Where to Use
Choosing The Correct Diamond Bond Type
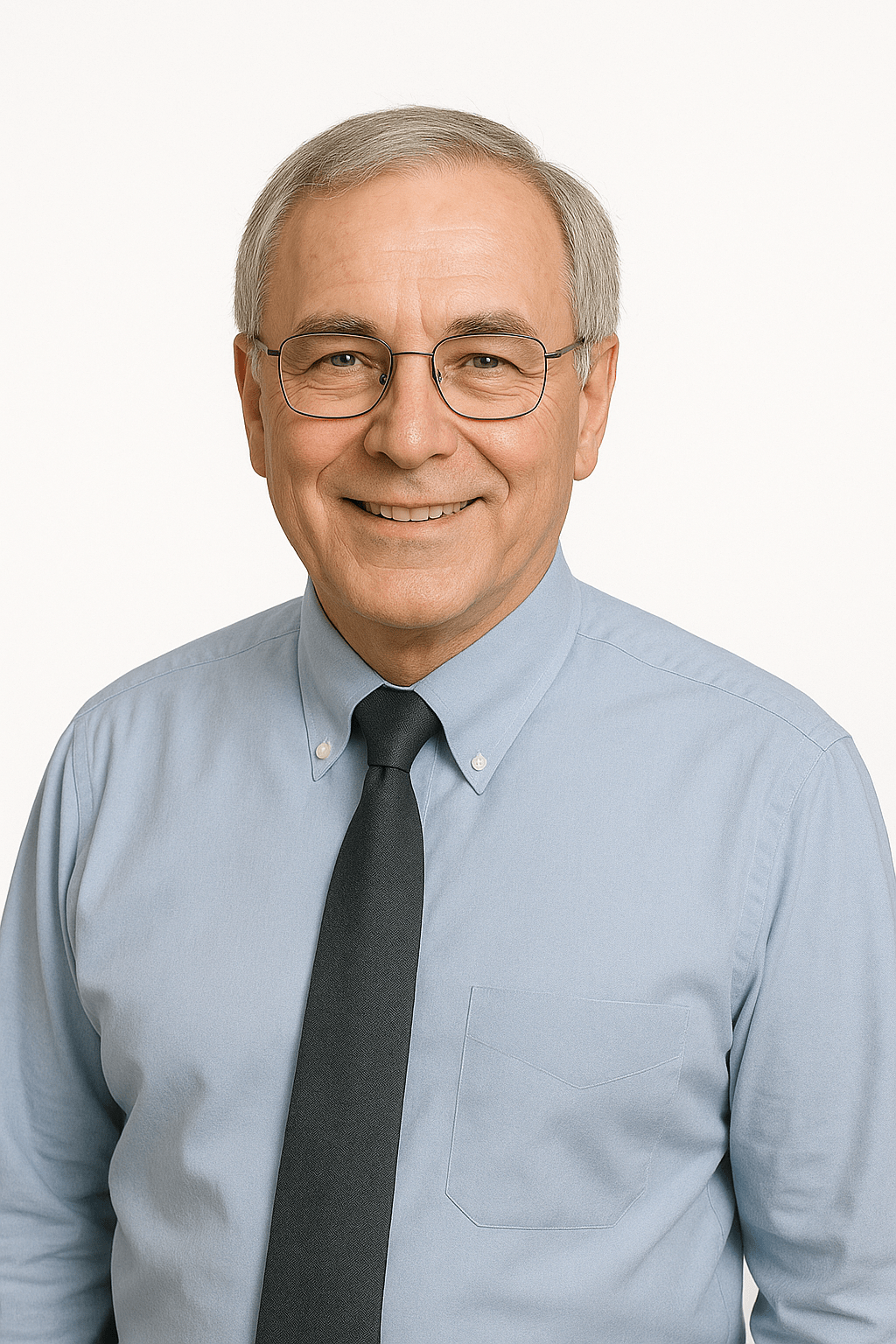
Alexander Schneider is a senior applications engineer and leading authority in the industrial diamond tooling industry, with over 35 years of hands-on experience in the development, application, and optimization of ultra-thin and high-precision diamond blades, diamond core drills, and diamond and CBN grinding wheels. His work spans a wide range of advanced materials including ceramics, glass, composites, semiconductors, and high-performance metals.
Throughout his career, he has collaborated with leading R&D institutions, national laboratories, and high-tech manufacturing companies across Europe, North America, and Asia, providing technical expertise and tailored solutions for demanding cutting and surface preparation applications.
Mr. Schneider has played a pivotal role in advancing precision cutting, sectioning, dicing, and grinding technologies used in research, production, and failure analysis. He is widely respected for his ability to optimize tool design and cutting parameters to meet exacting industry standards—balancing factors such as cut quality, blade life, material integrity, and process consistency.
As an author, Mr. Schneider is known for delivering practical, application-focused insights that translate complex technical challenges into clear, actionable strategies. His articles and technical guides serve as trusted resources for engineers, researchers, and manufacturers seeking to improve precision, reduce process variability, and enhance tool performance in critical applications.