material being cut will determine the type of diamond crystal will be used for the application. The harder the material the stronger diamond crystal has to be used
there is a wide range of natural and synthetic diamond crystals that can be used for any given application. Each one with different mechanical strengths, thermal stability and bond retention characteristics
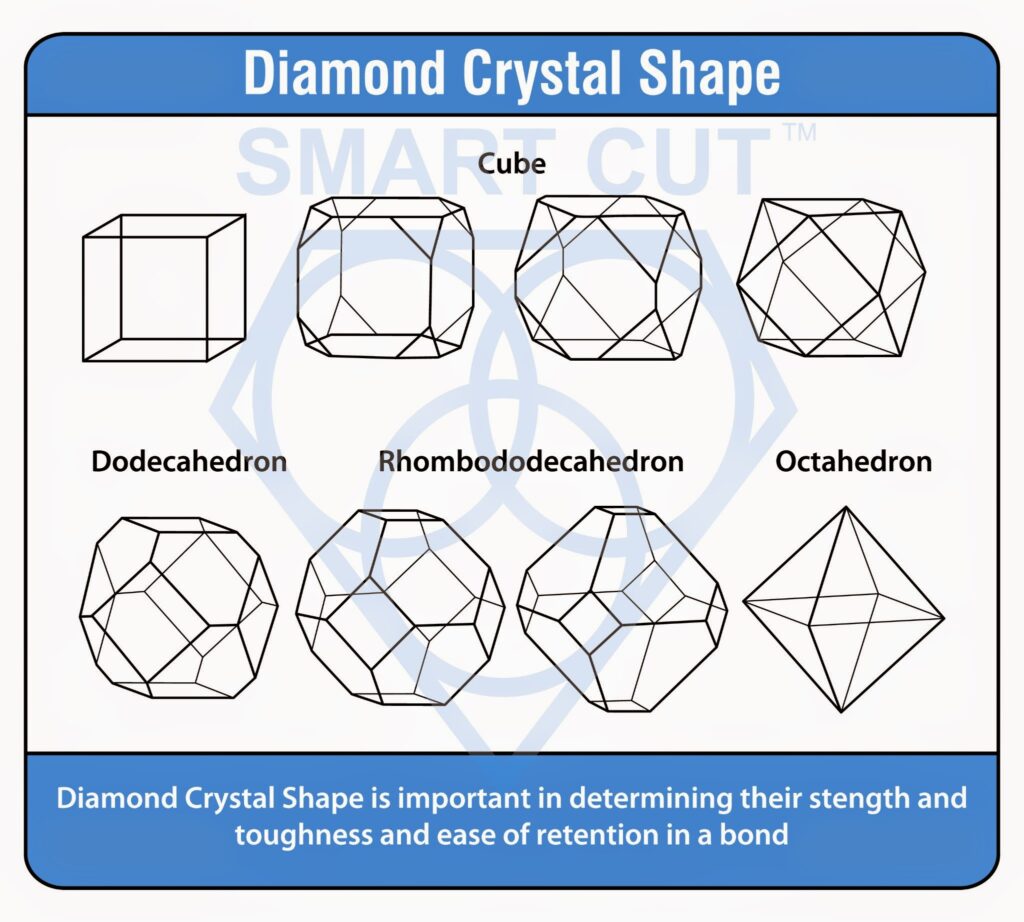
Diamond Crystal Shape
Diamond crystal shape is equally important in maintaining consistent quality in production of industrial diamond tools as diamond strength. Each type is designed for specific applications and specific quality requirements. Optimal shape of diamond crystal to use will depend on the application and can range from pure cube to a pure octahedron. Typically the most frequently used diamond crystals are somewhere in between the two shapes. This typically called cubo-otahedral.
Typically diamond crystallizes in a shape that is between hexagon (cube) and octahedron. Cubic faces often show square or rectangular shape.
Octahedral faces triangular or hexagonal shape. Sometimes Rhombohedral faces may show as well, showing up in rectangular or rhombohedral shape. Which is rare for synthetic diamond, because of the way its grown, yet very common for natural diamond crystal. Synthetic diamond shape is highly influenced by the temperature under which its synthesized and catalyst used such as Fe, Co, Ni, or other Alloys. Although most diamond crystals tend to gravitate towards the cubo-octahedral shape. The material differences and process variabilities used in synthetic diamond synthesis process are never perfect. They almost always show irregular shapes with rough surfaces, and contain metal inclusions and other internal defects. Even under same processing conditions, diamond crystals are randomly nucleated in reaction chamber will make them grow differently
Being able to control the shape with high degree of accuracy is important to maintain product quality and consistency. Furthermore the diamond crystal shape will be able to affect diamond crystal integrity and characteristics breaking down while in use. Diamond crystals/particles that have regular, cubo-octahedral shape are stronger then irregular diamond crystals/particles which have less well defined edges and rough faces. Cubo-octahedral shape diamond crystals are more blocky sharp edge shape, exhibiting consistent wear characteristics. The blocky shape provides greater resistance to fracturing, and thus provides the maximum number of cutting points and minimum surface contact. These tougher crystals will remove more material at faster rate, with less power/force. They are perfect for harder and more durable bond families, such as sintered (metal bond).
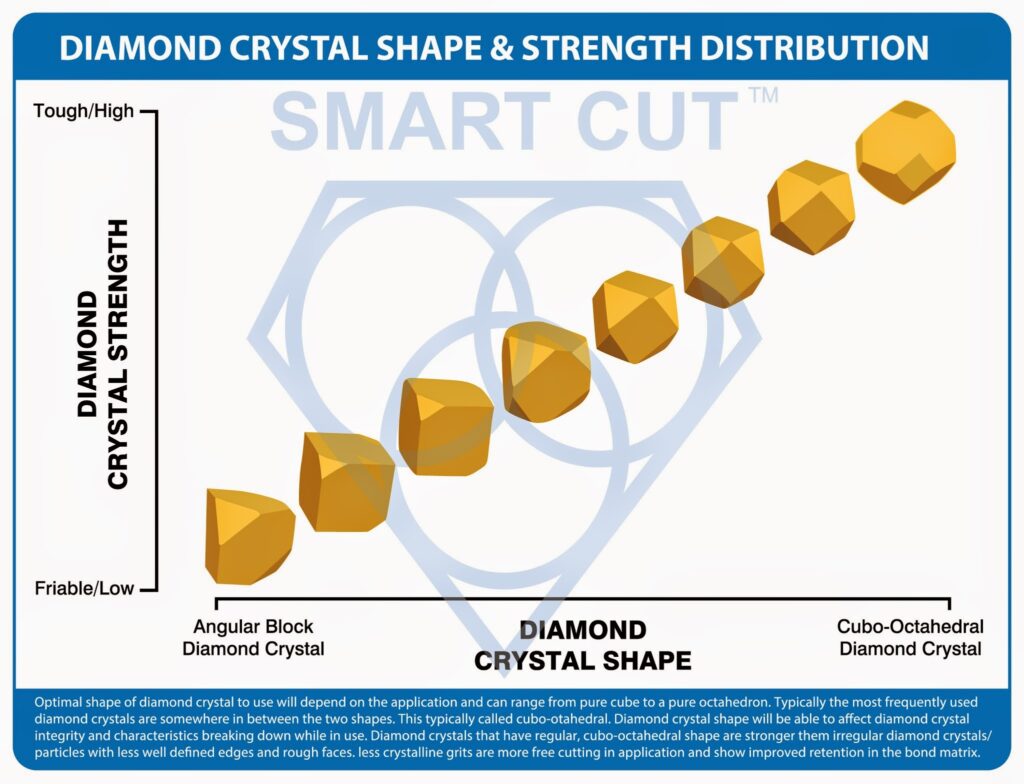
Where more irregular shape and angular diamond crystals (less crystalline) particles, are more free cutting and provide better retention in the bond matrix. These are typically used in less severe applications and more softer and brittle bond matrixes such as the resin bond.
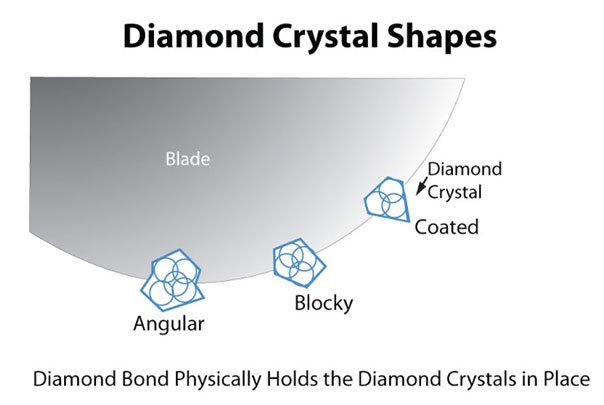