Choosing the correct diamond suspension, whether monocrystalline or polycrystalline, significantly impacts the quality and efficiency of the polishing and material removal processes. Understanding the properties and applications of both types of suspensions can help you select the most appropriate one for your specific needs.
Diamond suspensions play a crucial role in the sample preparation process, offering an efficient method for rapid stock removal and producing polished surfaces ready for detailed analysis. The choice of diamond suspension depends on several factors, including the type of material being polished, the surface finish required, and the specific characteristics of the polishing process.
Where and How Diamond Suspensions are Used?
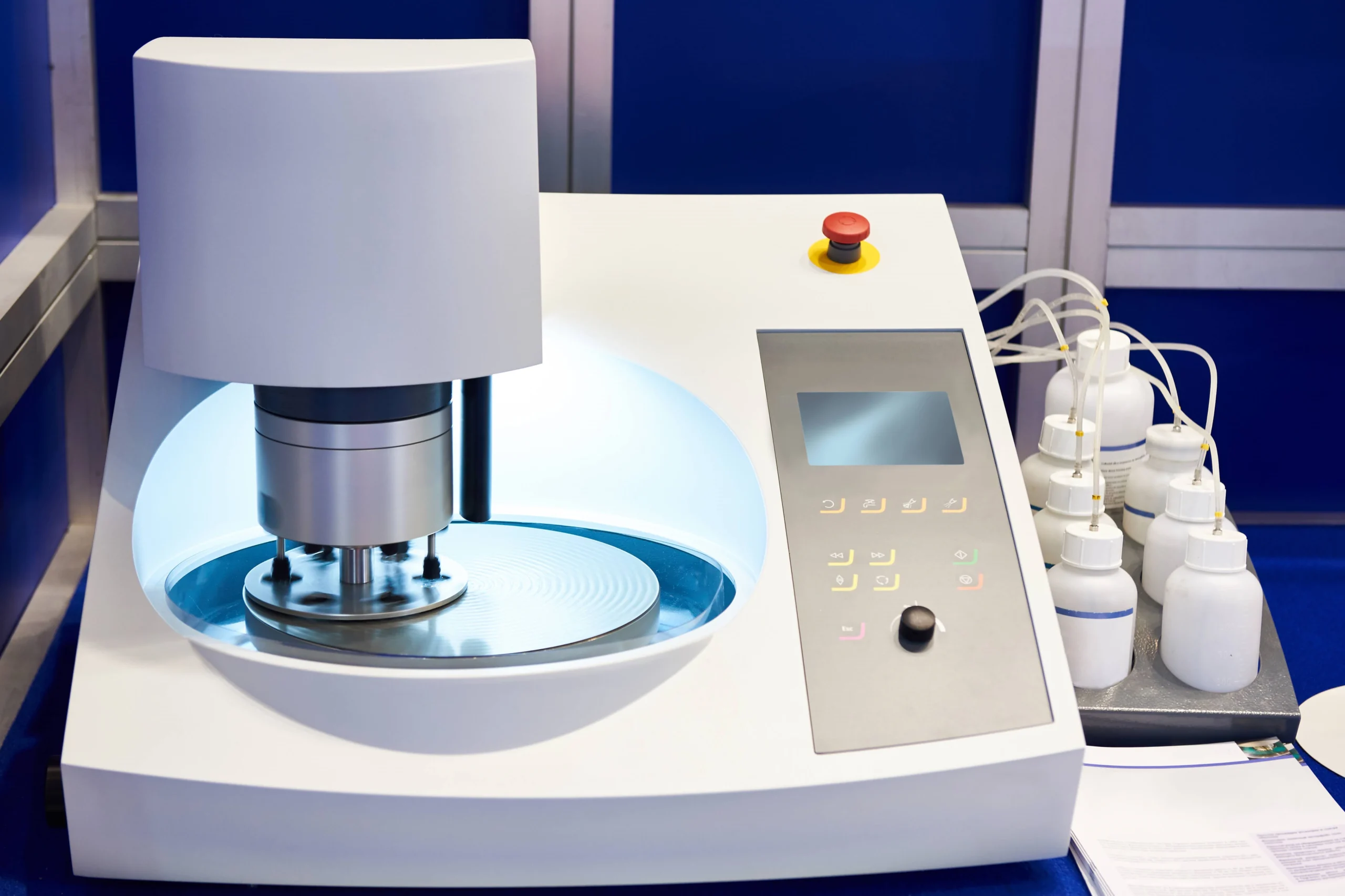
In sectors such as aerospace and automotive engineering, where exacting precision is paramount, monocrystalline diamond suspensions are preferred for their ability to meet precise surface specifications without damaging the material. Similarly, in the production of optics and electronics, monocrystalline diamonds are crucial due to their consistent particle size, which helps achieve the flawless polish needed for optimal optical clarity and electronic functionality. In the realm of material science research and development, polycrystalline diamond suspensions are valued for their adaptability to various materials and conditions. Their self-sharpening properties and efficient material removal rates are essential for rapid prototyping and meticulous experimentation.
Diamond Suspension Types Available
In diamond suspension manufacturing, "diamond type" indicates the form of diamond used in the suspension, with the most common types being monocrystalline and polycrystalline. Each type has unique characteristics that influence its behavior in polishing, grinding, and other abrasive applications.
Diamond suspensions are formulated with various, allowing for customization to meet the demands of different applications. The primary goal is to achieve a smooth, defect-free surface that meets the standards for further analysis, whether it's microscopic examination, metallography, or other forms of material assessment.
Monocrystalline diamond suspensions
Monocrystalline diamond suspensions are generally a good starting point for most polishing processes. They offer a balanced performance, with sharp, blocky particles that provide effective abrasive action. This makes monocrystalline suspensions suitable for a wide range of materials, from metals and ceramics to composites and other engineered substances. Their cost-effectiveness and durability contribute to their broad applicability.
Monocrystalline diamond is a cost-effective choice for effective stock removal and producing a good surface finish. Its slightly irregular shape, characterized by sharp, blocky edges with multiple cutting facets, allows it to perform well in general applications where the unique properties of polycrystalline diamond are not necessary. This makes monocrystalline diamond an attractive option for various industries seeking a balance between performance and affordability.
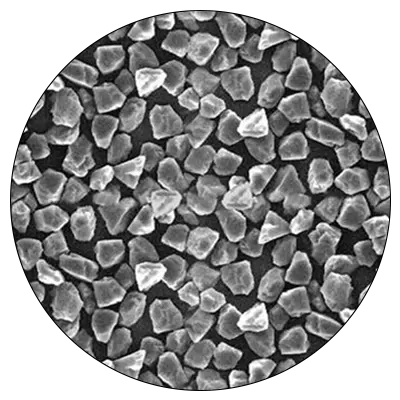
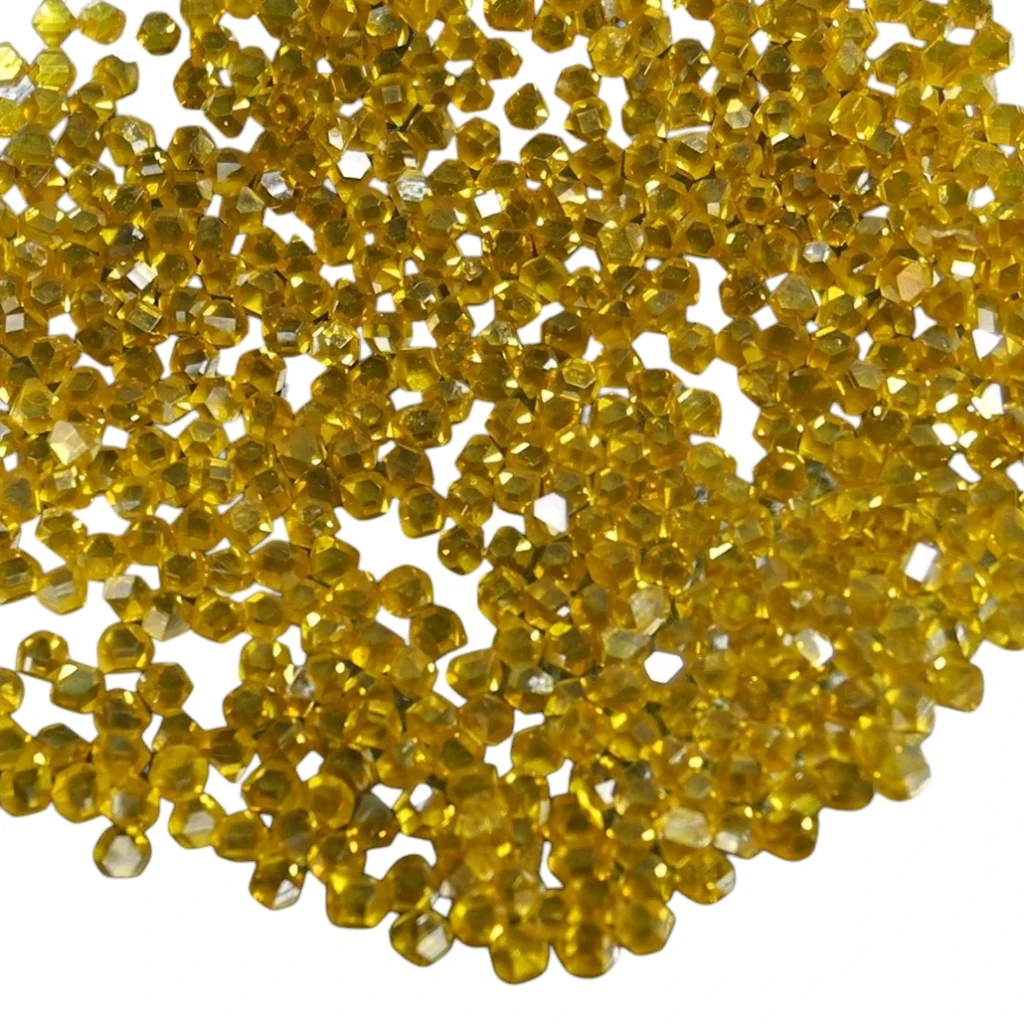
In terms of its cutting action, monocrystalline diamond's shape provides a reliable means of removing material, whether you're dealing with metals, ceramics, or composites. The single-crystal structure ensures that the edges remain sharp and durable, contributing to the suspension's longevity. This durability helps maintain consistent performance over time, reducing the need for frequent replacement or reapplication.
The cost-effectiveness of monocrystalline diamond comes from its simpler manufacturing process and wide-ranging applicability. It is generally more affordable than polycrystalline diamond, making it an excellent choice for general-purpose polishing, grinding, and other abrasive applications. This cost advantage can be crucial in large-scale operations where budget considerations play a significant role.
Monocrystalline diamond is recommended for a range of general applications. It is suitable for initial stock removal and intermediate polishing, providing a smooth transition between stages without excessive wear or surface damage. Its versatility allows it to be used across different industries, including manufacturing, metallurgy, and research laboratories.
While polycrystalline diamond offers superior stock removal rates and a more consistent surface finish in demanding applications, monocrystalline diamond is ideal for most general polishing needs. It is particularly effective for applications where aggressive cutting action isn't required or where cost considerations are a priority. The sharp, slightly irregular edges of monocrystalline diamond allow for effective abrasion, yet with a lower risk of excessive deformation or surface damage compared to more aggressive abrasives.
However, in certain cases, polycrystalline diamond suspensions are more appropriate. Polycrystalline diamonds are composed of multiple smaller crystals fused together, resulting in a multi-faceted structure with more cutting edges. This structure offers several advantages when polishing hard or sintered materials, where rapid stock removal is necessary to prepare a surface for further processing. Polycrystalline suspensions are known for their higher removal rates, allowing for faster preparation times compared to monocrystalline options.
The multi-faceted nature of polycrystalline diamond provides additional cutting edges, making it ideal for materials that require aggressive polishing. This can be particularly beneficial in applications where sintered materials or hard alloys are involved, as these materials can be challenging to polish with traditional abrasives. Polycrystalline suspensions are also effective in reducing surface deformation, resulting in a smoother and more uniform finish.
Choosing the right diamond suspension is essential for achieving optimal results. Factors to consider include:
-
Material Composition: The hardness and structure of the material determine which suspension is most suitable. Harder materials may require polycrystalline diamond for effective stock removal.
-
Desired Surface Finish: Depending on the level of polish required, the grit size and type of diamond suspension may vary. A finer finish may require smaller particles, while aggressive stock removal needs larger particles.
-
Polishing Equipment and Techniques: The choice of equipment and polishing techniques can influence the type of suspension used. Some machines work better with certain suspensions due to their design and operational parameters.
Characteristics and Benefits:
Monocrystalline diamond suspensions consist of single-crystal diamond particles. These particles tend to have a more uniform shape and size, leading to a more consistent scratch pattern during polishing. The primary advantages of monocrystalline diamond suspensions include:
-
Uniform Cutting Edges: Monocrystalline diamonds provide more predictable and consistent material removal, which is crucial for applications requiring high precision and a superior surface finish.
-
Durability: These particles are generally more robust and less likely to fracture under stress compared to polycrystalline diamonds.
-
Ideal for Soft to Medium-Hard Materials: Monocrystalline diamond is typically preferred for softer materials that do not cause premature fracturing of the diamond particles.
Applications:
Monocrystalline diamond is particularly effective in precision applications where surface integrity and finish are paramount. It is often used in polishing metals, ceramics, and certain types of optical materials where a smooth, fine finish is required.
Monocrystalline Diamond Grit Size Guide for Metallographic Samples
Material Type |
Rough Polishing Grit Size |
Intermediate Polishing Grit Size |
Fine Polishing Grit Size |
---|---|---|---|
Soft Metals (e.g., Aluminum) |
15-30 microns |
9-12 microns |
3-6 microns |
Medium Hardness Metals (e.g., Stainless Steel) |
9-15 microns |
6-9 microns |
1-3 microns |
Hard Metals (e.g., Titanium) |
6-12 microns |
3-6 microns |
1-2 microns |
Very Hard Metals (e.g., Tungsten Carbide) |
3-6 microns |
1-3 microns |
0.25-1 micron |
Copper and Its Alloys |
15-30 microns |
9-12 microns |
3-6 microns |
Nickel and Its Alloys |
9-15 microns |
6-9 microns |
1-3 microns |
Superalloys (e.g., Inconel) |
6-12 microns |
3-6 microns |
1-2 microns |
Cast Irons |
6-12 microns |
3-6 microns |
1-2 microns |
Soft Ceramics (e.g., Graphite) |
15-30 microns |
9-12 microns |
3-6 microns |
Hard Ceramics (e.g., Silicon Carbide) |
3-6 microns |
1-3 microns |
0.25-1 micron |
Magnesium and Its Alloys |
15-30 microns |
9-12 microns |
3-6 microns |
Brass and Bronze |
15-30 microns |
9-12 microns |
3-6 microns |
Precious Metals (e.g., Gold, Silver) |
9-15 microns |
6-9 microns |
1-3 microns |
High-Speed Steels |
6-12 microns |
3-6 microns |
1-2 microns |
Tool Steels |
6-12 microns |
3-6 microns |
1-2 microns |
Composites (e.g., Carbon Fiber) |
9-15 microns |
6-9 microns |
1-3 microns |
Glass and Quartz |
3-6 microns |
1-3 microns |
0.25-1 micron |
Plastics and Polymers |
15-30 microns |
9-12 microns |
3-6 micorns |
Biological Samples (e.g., Bone, Teeth) |
15-30 microns |
9-12 microns |
3-6 microns |
Layered Materials (e.g., PCBs, Laminates) |
9-15 microns |
6-9 microns |
1-3 microns |
Thermal Spray Coatings |
6-12 microns |
3-6 microns |
1-2 microns |
Advanced Alloys (e.g., Zirconium Alloys) |
6-12 microns |
3-6 microns |
1-2 microns |
Superconductors |
3-6 microns |
1-3 microns |
0.25-1 micron |
Refractory Metals (e.g., Molybdenum, Tantalum) |
3-6 microns |
1-3 microns |
0.25-1 micron |
Polycrystalline Diamond Suspensions
Characteristics and Benefits:
Polycrystalline diamond suspensions are made from diamond particles consisting of multiple crystals or grains. This structure confers several unique properties:
-
Fragmentation: Polycrystalline particles can break and present new cutting edges during polishing. This self-sharpening behavior is beneficial for maintaining effective stock removal over the suspension’s life.
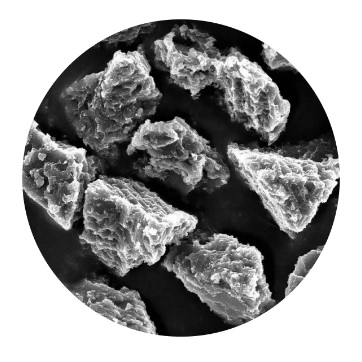
-
High Removal Rates: Ideal for harder materials that require aggressive material removal, polycrystalline diamond can achieve faster polishing rates.
-
Versatility: Works well across a broad range of materials, including those that may cause monocrystalline diamonds to fracture prematurely.
Applications:
This type of suspension is suitable for hard, tough materials such as advanced ceramics and certain types of composites. Its ability to self-sharpen makes it effective for high-stress environments and applications requiring significant material removal.
Recommended Application of Polycrystalline Diamond
Polycrystalline diamond is recommended for applications requiring rapid stock removal and enhanced polishing performance. Its multi-faceted structure allows for effective material removal while minimizing deformation. Applications that benefit from polycrystalline diamond include:
-
Polishing Hard Metals: Tool steels, titanium, and hard steel benefit from polycrystalline diamond's abrasive action.
-
Sintered Materials: Polycrystalline diamond is effective for sintered materials due to its higher stock removal rates.
-
Ceramics and Composites: The unique structure of polycrystalline diamond provides superior results when polishing ceramics, composites, and cermets.
Polycrystalline Diamond Grit Size Guide for Metallographic Samples
Material Type |
Rough Polishing Grit Size |
Intermediate Polishing Grit Size |
Fine Polishing Grit Size |
---|---|---|---|
Aluminum |
6 - 9 um |
3 - 6 um |
1 - 3 um |
Copper and Brass |
6 - 9 um |
3 - 6 um |
1 - 3 um |
Stainless Steel |
9 - 15 um |
6 - 9 um |
3 - 6 um |
Soft Steel |
6 - 9 um |
3 - 6 um |
1 - 3 um |
Hard Steel |
9 - 15 um |
6 - 9 um |
3 - 6 um |
Tool Steel |
9 - 15 um |
6 - 9 um |
3 - 6 um |
Titanium |
9 - 15 um |
6 - 9 um |
3 - 6 um |
Zinc, Tin, Lead |
3 - 6 um |
1 - 3 um |
<1 um |
Magnesium |
3 - 6 um |
1 - 3 um |
<1 um |
Nickel-based Alloys |
9 - 15 um |
6 - 9 um |
3 - 6 um |
Cobalt-based Alloys |
9 - 15 um |
6 - 9 um |
3 - 6 um |
Alumina |
15 - 30 um |
9 - 15 um |
6 - 9 um |
Silicon Nitride |
15 - 30 um |
9 - 15 um |
6 - 9 um |
Polymer Composites |
15 - 30 um |
9 - 15 um |
6 - 9 um |
Metal Matrix Composites |
15 - 30 um |
9 - 15 um |
6 - 9 um |
Ceramic Matrix Composites |
15 - 30 um |
9 - 15 um |
6 - 9 um |
Cermet |
15 - 30 um |
9 - 15 um |
6 - 9 um |
Glass |
15 - 30 um |
9 - 15 um |
6 - 9 um |
Carbon Composites |
15 - 30 um |
9 - 15 um |
6 - 9 um |
Additional Guide Details:
-
Copper and Its Alloys: These softer metals require similar grit sizes as aluminum to avoid excessive material removal which can deform the sample.
-
Nickel and Its Alloys: These materials, being tougher than copper but less so than hardened steels, balance the need for efficient material removal with the requirement to maintain structural integrity.
-
Superalloys: Known for their high temperature resistance, superalloys require careful handling to maintain their microstructural integrity during polishing.
-
Cast Irons: These materials can vary in hardness depending on their type (gray, ductile, etc.), but generally fall into the harder metals category, necessitating mid-range grit sizes.
-
Soft Ceramics: While generally more brittle, soft ceramics like graphite need a gentler approach similar to soft metals to prevent surface damage.
-
Hard Ceramics: Extremely hard and brittle, materials like silicon carbide require very fine grit sizes to achieve a smooth finish without introducing cracks or other defects.
-
Magnesium and Its Alloys: These lighter metals are similar to aluminum in terms of their softness and polishing needs.
-
Brass and Bronze: These copper alloys share polishing characteristics with pure copper but may require slightly different approaches due to variations in hardness.
-
Precious Metals: Often requiring high-quality finishes, precious metals benefit from finer polishing to enhance their natural luster.
-
High-Speed and Tool Steels: Known for their durability and resistance to wear, these materials need aggressive initial stages followed by fine polishing for optimal surface integrity.
-
Composites: These materials often include a mix of different substrates, requiring a balanced approach to avoid damaging the matrix or fibers.
-
Glass and Quartz: Extremely hard and brittle, these materials require very fine grit sizes for a flawless finish without introducing micro-cracks.
-
Plastics and Polymers: Softer and more susceptible to damage, these require gentle polishing to avoid heat generation and deformation.
-
Biological Samples: These unique materials, including bone and teeth, require careful handling to preserve delicate structures and features during preparation.
-
Layered Materials: These include printed circuit boards (PCBs) and various laminates which require careful handling to avoid delamination.
-
Thermal Spray Coatings: Typically used in aerospace and power generation, these coatings are hard and require mid-range to fine grits for proper finishing.
-
Thermal Spray Coatings: Typically used in aerospace and power generation, these coatings are hard and require mid-range to fine grits for proper finishing.
-
Advanced Alloys: Materials like zirconium alloys, often used in nuclear reactors, demand precise and gentle polishing to maintain their integrity.
-
Superconductors: Require ultra-fine finishing to ensure the surfaces do not impede electrical properties.
-
Refractory Metals: Known for their high melting points, these metals need finer grits to achieve the desired finish without damaging the material.
Monocrystalline Diamond Suspension Usage Recommendations:
Rough Polishing: This stage involves initial stock removal. Coarser grit sizes (9 - 30 um) are generally used, depending on the material's hardness and thickness. For metals like aluminum, copper, brass, and soft steel, 6 - 9 um grit sizes are typically sufficient. Harder metals, such as stainless steel, tool steel, and titanium, require 9 - 15 um for efficient stock removal. Ceramics, composites, and cermets generally need even coarser grits, from 15 to 30 um.
Intermediate Polishing: This stage refines the surface, preparing it for the final polish. Intermediate polishing usually employs finer grit sizes than rough polishing. For metals, the typical range is 3 - 9 um, with harder metals requiring coarser grits. Ceramics and composites benefit from intermediate polishing with 9 - 15 um.
Fine Polishing: The final stage aims to achieve a smooth and consistent surface finish. The grit size for fine polishing is typically in the range of 1 - 6 um, depending on the material. Softer metals like zinc, tin, lead, and magnesium often need finer grits (<1 - 3 um), while harder metals can use 3 - 6 um. Ceramics and composites generally fall within 6 - 9 um for this stage.
Factors that affect diamond suspension usage
-
Material Hardness: Harder materials require coarser grits for rough polishing, while softer materials need finer grits to avoid excessive abrasion.
-
Polishing Equipment: Ensure the polishing equipment is compatible with the selected grit size and can maintain consistent pressure and speed.
-
Desired Surface Finish: Depending on the level of precision required, adjust the grit size accordingly. Finer grit sizes yield smoother finishes, while coarser grits are better for rapid stock removal.
Natural Diamonds
Natural diamonds, derived from geological processes deep within the Earth over millions of years, are an alternative to synthetic diamonds in certain industrial applications, including diamond suspensions. While synthetic diamonds, such as monocrystalline and polycrystalline, are typically more common in manufacturing due to their consistent properties and lower cost, natural diamonds offer distinct characteristics that can be valuable in specific contexts.
Characteristics of Natural Diamond
Natural diamonds are formed through high-pressure and high-temperature conditions within the Earth's mantle, resulting in a unique crystalline structure. Here's what sets natural diamonds apart from synthetic ones:
-
Variability: Natural diamonds often exhibit more variability in terms of inclusions, impurities, and overall structure. This variability can lead to a broader range of physical properties, which might be beneficial in some applications.
-
Durability: Due to their geological origin, natural diamonds can be incredibly durable, making them suitable for high-wear applications.
-
Unique Properties: Natural diamonds may contain trace minerals or other inclusions that can alter their abrasive characteristics, providing unique polishing or grinding effects.
-
Higher Cost: Natural diamonds are generally more expensive than synthetic ones, due to the costs associated with mining and refining.
Applications for Natural Diamond in Diamond Suspensions
Natural diamond can be used in diamond suspensions for specific industrial applications where its unique properties offer advantages over synthetic diamonds. These applications typically require the following:
-
Durable Abrasives: Natural diamonds are valued for their durability and strength, making them ideal for applications that involve high wear and tear, such as certain types of grinding or cutting.
-
Specialized Surface Finishes: The natural variability in diamond structure can create unique surface finishes, desirable in specific industries like jewelry or precision optics.
-
Environmental Considerations: Some industries prefer natural diamonds due to their perceived environmental benefits, as they are sourced from the Earth rather than manufactured synthetically. However, this can depend on the mining practices used.
Comparing Natural and Synthetic Diamonds
When comparing natural diamonds with synthetic monocrystalline and polycrystalline diamonds, consider the following factors:
-
Consistency: Synthetic diamonds offer consistent properties, making them more predictable in manufacturing and industrial applications. Natural diamonds might vary due to their geological origin.
-
Cost: Natural diamonds are typically more expensive, affecting their practicality for large-scale industrial use.
-
Durability: Both natural and synthetic diamonds can be durable, but synthetic diamonds often have more controlled durability due to consistent manufacturing processes.
-
Environmental Impact: While some view natural diamonds as environmentally friendly, synthetic diamonds often have a lower environmental footprint due to controlled manufacturing and the absence of large-scale mining.
Choosing Natural Diamond for Diamond Suspensions
If you consider using natural diamonds in diamond suspensions, keep in mind these factors:
-
Specific Applications: Natural diamonds might be best for specialized applications where unique abrasive characteristics or durability are required.
-
Cost Considerations: Due to their higher cost, natural diamonds might be less practical for large-scale industrial applications.
-
Performance Requirements: Synthetic diamonds are typically more consistent, making them a better choice for applications requiring predictable performance.
Natural Diamond Grit Size Guide for Metallographic Samples
Material Type |
Rough Polishing Grit Size |
Intermediate Polishing Grit Size |
Fine Polishing Grit Size |
---|---|---|---|
Soft Metals (e.g., Aluminum) |
30-60 microns |
15-30 microns |
6-12 microns |
Medium Hardness Metals (e.g., Stainless Steel) |
25-50 microns |
15-25 microns |
6-12 microns |
Hard Metals (e.g., Titanium) |
20-40 microns |
10-20 microns |
3-6 microns |
Very Hard Metals (e.g., Tungsten Carbide) |
15-30 microns |
6-15 microns |
3-6 microns |
Copper and Its Alloys |
30-60 microns |
15-30 microns |
6-12 microns |
Nickel and Its Alloys |
25-50 microns |
15-25 microns |
6-12 microns |
Superalloys (e.g., Inconel) |
20-40 microns |
10-20 microns |
3-6 microns |
Cast Irons |
20-40 microns |
10-20 microns |
3-6 microns |
Soft Ceramics (e.g., Graphite) |
30-60 microns |
15-30 microns |
6-12 microns |
Hard Ceramics (e.g., Silicon Carbide) |
15-30 microns |
6-15 microns |
3-6 microns |
Magnesium and Its Alloys |
30-60 microns |
15-30 microns |
6-12 microns |
Brass and Bronze |
30-60 microns |
15-30 microns |
6-12 microns |
Precious Metals (e.g., Gold, Silver) |
25-50 microns |
15-25 microns |
6-12 microns |
High-Speed Steels |
20-40 microns |
10-20 microns |
3-6 microns |
Tool Steels |
20-40 microns |
10-20 microns |
3-6 microns |
Composites (e.g., Carbon Fiber) |
25-50 microns |
15-25 microns |
6-12 microns |
Glass and Quartz |
15-30 microns |
6-15 microns |
3-6 microns |
Plastics and Polymers |
30-60 microns |
15-30 microns |
6-12 microns |
Biological Samples (e.g., Bone, Teeth) |
30-60 microns |
15-30 microns |
6-12 microns |
Natural Diamond Suspension Usage Recommendations:
-
Rough Polishing: Utilizes coarser grits to rapidly remove material and eliminate significant surface imperfections.
-
Intermediate Polishing: Employs medium grit sizes to refine the surface further, preparing it for the final polishing stage.
-
Fine Polishing: Uses fine to ultra-fine grit sizes to achieve a high-quality finish with minimal surface deformations.
Comparison Table Between monocrystalline, polycrystalline, and natural diamond suspensions
Variable |
Monocrystalline Diamond |
Polycrystalline Diamond |
Natural Diamond |
---|---|---|---|
Structure |
Single-crystal with sharp edges |
Multi-faceted structure |
Natural structure with inclusions |
Cost |
Generally lower |
Typically higher due to complexity |
Higher due to mining and rarity |
Durability |
High due to single-crystal |
Good, but can wear faster |
Variable, often durable |
Abrasive Action |
Effective, but less aggressive |
Aggressive due to multi-faceted edges |
Varies; generally moderate |
Stock Removal Rate |
Moderate to high |
High to very high |
Moderate, but can vary |
Consistency |
Consistent due to manufacturing control |
Relatively consistent with some variability |
Less consistent due to natural origin |
Surface Finish |
Smooth, suitable for general applications |
Rougher, faster results |
Smooth to variable finish |
Applications |
General-purpose; metals, ceramics, composites |
High-performance; rapid stock removal |
Specialized applications where unique traits are needed |
Environmental Impact |
Generally lower due to synthetic production |
Controlled production, but can vary |
Higher impact due to mining |
Manufacturing Process |
Synthetic; controlled methods |
Synthetic; complex fusion process |
Mined from Earth; naturally formed |
Recyclability |
High; recyclable in many products |
Moderate; depends on manufacturing |
Lower due to variable structure |
Customer Support |
High; widely supported |
Good support; specialized knowledge |
Varies; less common in industry |
Temperature Tolerance |
Generally high; stable under most conditions |
High tolerance; durable under pressure |
Varies; often stable in diverse settings |
Resistance to Contamination |
Good; resists contamination with proper additives |
Moderate to good; requires stability agents |
Variable; susceptible to environmental factors |
pH Sensitivity |
Generally low; compatible with many substances |
Moderate; might require careful handling |
Can vary depending on natural content |
Shelf Life |
Generally long; stable under proper storage |
Moderate; can settle if not used promptly |
Lower; might degrade or settle over time |
Customization |
Good; can be tailored for specific applications |
Moderate; some custom formulations possible |
Lower; limited by natural structure |
Factors to Consider in
Selecting Right Diamond Suspension for your Application
Selecting the appropriate diamond suspension for a particular application involves a comprehensive evaluation of various factors that can significantly influence the final polishing results. The decision process requires a nuanced understanding of the specific requirements of the project and the properties of the diamond suspension. From the particle size and its concentration in the suspension to the environmental and safety implications of its use, each aspect plays a crucial role in determining the efficacy and efficiency of the polishing process.
1. Particle Size and Concentration
The particle size and concentration in the suspension should match the precision and finish requirements of the project. Fine grit sizes (1-3 microns) are typically used for achieving high finishes, while coarser grits (6-30 microns) are suitable for rapid material removal.
2. Viscosity and Vehicle
The fluid medium or vehicle used in the suspension affects how the diamond particles are dispersed and maintained during polishing. The viscosity should be compatible with the polishing equipment and techniques to ensure smooth application without sedimentation or phase separation.
3. Compatibility with Polishing Pads
The choice of diamond suspension should also consider the type of polishing pads used. Certain pads may work better with monocrystalline or polycrystalline suspensions based on their material and texture.
4. Specific Application Needs
Consider any specific requirements such as non-contaminating or chemically inert suspensions, especially in applications like semiconductor fabrication or optical lens polishing where material purity is critical.
5. Thermal Stability
Diamond suspensions must maintain their integrity and performance under the thermal loads typically encountered during polishing processes. Monocrystalline diamonds, with their more robust structure, generally exhibit superior thermal stability. This makes them suitable for applications involving prolonged exposure to friction-generated heat. On the other hand, polycrystalline diamonds, with their ability to present fresh cutting surfaces, can effectively manage heat by reducing friction through new particle exposure.
6. Chemical Compatibility
Certain polishing tasks may involve exposure to chemicals, either from the material being polished or from the environment. It is crucial that the diamond suspension is chemically inert to these substances to avoid degradation of the diamond particles or the vehicle. Polycrystalline diamonds are often preferred in environments where chemical abrasiveness is a concern due to their inherent toughness and less susceptibility to chemical wear.
7. Cost Considerations
Monocrystalline diamond suspensions are often more expensive than polycrystalline due to the cost of producing uniform, single-crystal diamonds. Budget constraints may influence the choice, particularly in large-scale or routine applications where the benefits of monocrystalline diamonds do not justify the additional cost. However, for highly specialized applications requiring the utmost precision and consistency, the investment in monocrystalline diamonds can be justified by the superior results.
8. Environmental and Safety Concerns
The environmental impact and safety of using diamond suspensions should also be considered. This includes evaluating the toxicity and disposal methods of the suspension medium and the diamond particles themselves. Manufacturers are increasingly offering eco-friendly and safer alternatives that minimize harmful emissions and are easier to dispose of in compliance with environmental regulations.
Diamond Suspension
Application Recommendations
When it comes to the application of diamond suspensions, achieving optimal results requires a thoughtful approach tailored to the specific needs of your materials and processes. Here are some expanded recommendations to guide your selection and use of diamond suspensions:
1. Trial and Error
The diverse responses of different materials to specific diamond suspensions necessitate initial testing phases. Conducting trials allows you to observe how a particular suspension performs with your material, enabling adjustments before full-scale application. This empirical approach helps in optimizing the process to achieve the desired outcomes effectively.
2. Consult with Experts
Leveraging the knowledge of specialists in diamond suspensions can significantly enhance your decision-making process. Our Application Engineers possess extensive expertise and have access to comprehensive data and case studies that illuminate the performance of various suspensions under different conditions. Their insights can be invaluable in selecting the right suspension that aligns with your unique requirements.
3. Consider Long-Term Costs
Initial cost assessments can be misleading. While monocrystalline diamond suspensions might appear more costly upfront, their durability and consistent performance can translate into greater cost-effectiveness over time. This is particularly true for applications requiring high precision and quality, where the superior performance of monocrystalline diamonds justifies the investment.
4. Adjustments and Fine-Tuning
The dynamic nature of manufacturing and material processing environments often requires ongoing adjustments to the diamond suspension used. Be prepared to fine-tune the concentration of diamond particles, modify particle sizes, and possibly switch between monocrystalline and polycrystalline types as your project evolves. This flexibility in managing your suspension can significantly influence the quality and efficiency of your finishing processes.
5. Regular Performance Reviews
Periodically reviewing the performance of your diamond suspensions can help identify potential areas for improvement. Regular assessments enable you to track the effectiveness of your current choices and make informed decisions about potential changes or upgrades needed to enhance process efficiency and product quality.
6. Integration with Process Controls
Integrate diamond suspension application within your broader process controls to ensure consistency and repeatability. Automated dosing systems, consistent agitation, and temperature control are critical factors that can influence the stability and effectiveness of your diamond suspensions, leading to better overall results.