Table of Contents
TogglePCD tools are used for processing aluminum and aluminum, aluminum alloys, copper, copper alloy, babbitt metal, wood, wood based fiber materials, aluminum oxide, reinforced floor boards, wear resistant plastic, Bakelite, graphite, stone materials, tungsten carbide, hard cartons. Epoxy resins, Fiberglass composites, Carbon-phenolic, Hard rubber, Plastics, Ceramics (unfired), Graphite
Polycrystalline Diamond (PCD), stand out for their utility in industrial applications. PCD is crafted through a meticulous process that combines small diamond particles using extreme heat and pressure, resulting in a material that exhibits exceptional hardness, robustness, and a range of properties beneficial to modern manufacturing.
Share this Article with Friend or Colleague
This introduction to Polycrystalline Diamond explores its composition, creation, and the unique attributes that make it indispensable in various industrial sectors. From cutting tough metals like tungsten carbide to precision machining of aluminum alloys and even in the delicate shaping of wood-based materials, PCD's applications are diverse. The article will show how this synthetic diamond form is transforming machining processes, offering unmatched durability and efficiency compared to other materials. As we explore the multifaceted uses of PCD, we will cover how and why its used aerospace, composites, metalworking, woodworking, and many other applications
What is Polycrystalline Diamond (PCD)?
Polycrystalline Diamond (PCD) is a synthetic diamond product that is produced by sintering together selected diamond particles with a metal matrix, under high temperatures and pressures. This process results in a highly durable and incredibly hard material that exhibits the superior wear resistance and thermal conductivity of diamond, combined with the toughness provided by the bonding matrix. PCD is distinct from single-crystal diamonds and is used predominantly in industrial applications requiring high abrasion resistance.
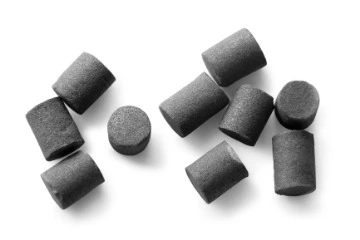
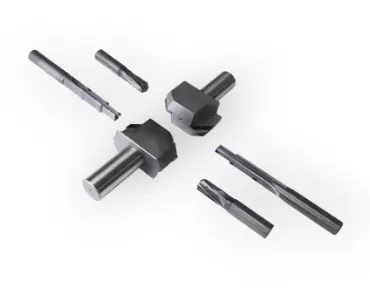
The Process of Creating PCD
The manufacturing of PCD involves two primary techniques: sintering and the application of high-pressure, high-temperature (HPHT) conditions. Initially, fine diamond particles are carefully selected and cleaned. These particles are then mixed with a metallic binder, typically cobalt, which acts as a catalyst in the sintering process. The mixture is placed in a press that subjects it to temperatures above 1,400°C and pressures exceeding 5 GPa.
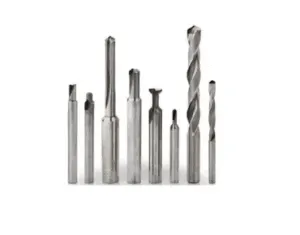
Under these extreme conditions, the diamond particles bond cohesively with the metal matrix, while retaining the core structure of diamond. This sintering process not only binds the diamonds together but also creates a network of interconnected diamond crystals throughout the material.
Comparison with Monocrystalline Diamonds
PCD differs significantly from monocrystalline diamonds, which are either naturally occurring or synthetic diamonds consisting of a single, continuous crystal structure. While monocrystalline diamonds exhibit exceptional hardness and clarity, their uniform crystalline orientation can lead to cleavage planes, which make them susceptible to fracturing under impact or when used in cutting tools.
In contrast, the polycrystalline nature of PCD eliminates these cleavage planes, offering enhanced toughness and resistance to breakage. The intergrown diamond crystals in PCD are oriented in multiple directions, which disperses stress and makes the material more durable under varying operational stresses. This structural difference not only increases the toughness of PCD but also enhances its thermal stability, making it ideal for high-temperature processing tasks where monocrystalline diamonds would falter.
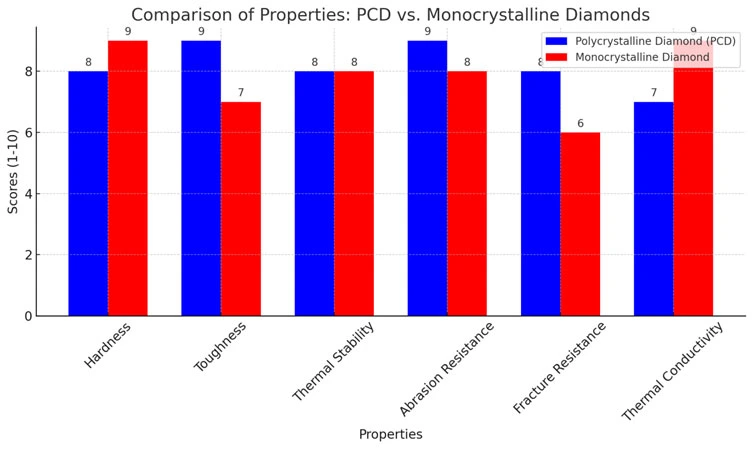
Table that compares the properties and characteristics of Polycrystalline Diamond (PCD) and Monocrystalline Diamonds:
Property |
Polycrystalline Diamond (PCD) |
Monocrystalline Diamond |
---|---|---|
Structure |
Composed of multiple diamond grains sintered together with a metal matrix. |
Single crystal structure without any grain boundaries. |
Hardness |
Extremely hard, slightly less than monocrystalline diamond due to the binder. |
The hardest material known, very high hardness. |
Toughness |
Higher toughness due to grain boundary strength and lack of cleavage planes. |
Less tough, with potential cleavage planes that can lead to fracturing. |
Thermal Stability |
Enhanced thermal stability due to the metal matrix and grain structure. |
High thermal conductivity but can be susceptible to thermal shock. |
Abrasion Resistance |
Exceptional abrasion resistance, suitable for cutting and grinding materials. |
Excellent abrasion resistance, though less optimal for certain tools. |
Fracture Resistance |
Higher fracture resistance due to its polycrystalline nature. |
Lower fracture resistance due to cleavage planes. |
Applications |
Ideal for industrial cutting tools, drilling bits, and abrasive applications. |
Often used in optics, electronics, and fine cutting applications. |
Manufacturing Cost |
Generally lower due to the use of a binder and less intensive production. |
Higher, as the synthesis of large, flawless monocrystals is challenging. |
Thermal Conductivity |
Good thermal conductivity, mitigated by the metal matrix. |
Very high thermal conductivity, superior in single-crystal form. |
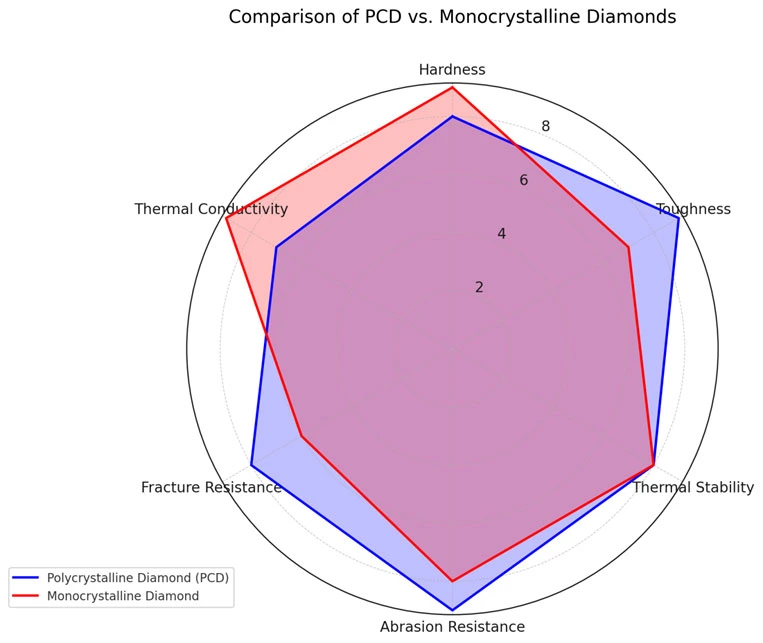
Properties of Polycrystalline Diamond
Polycrystalline Diamond (PCD) possesses a unique set of properties that make it an invaluable material in various industrial applications, particularly where extreme conditions require materials that can withstand high stress and wear. Below are some of the key properties of PCD:
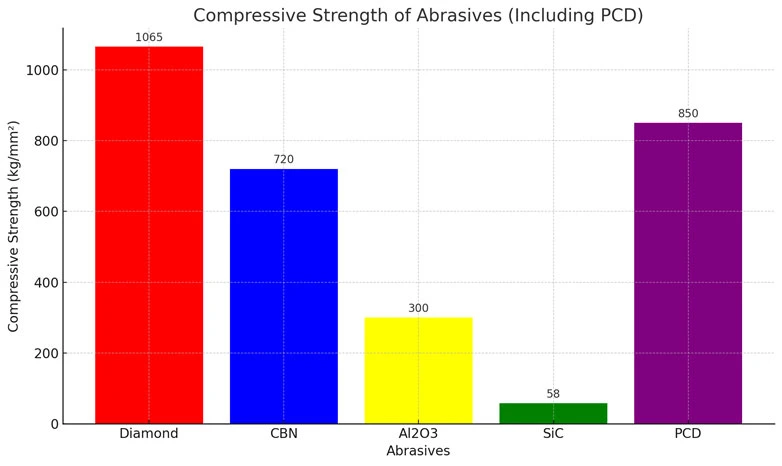
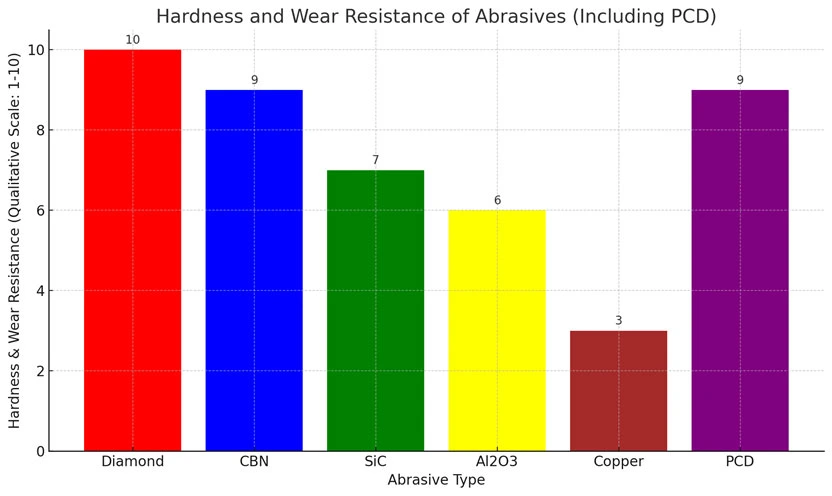
Hardness and Wear Resistance
PCD is renowned for its exceptional hardness, which is second only to natural diamonds. This extreme hardness provides superior wear resistance, making PCD tools ideal for cutting and machining applications that involve abrasive materials. The hardness of PCD ensures that the tools maintain their edge and dimensional integrity over long periods and under harsh working conditions, leading to increased tool life and reduced downtime for tool changes.
Thermal Conductivity and Heat Tolerance
One of the standout features of PCD is its high thermal conductivity, which is superior to most other tool materials, including tungsten carbide. This property allows PCD tools to dissipate heat quickly during machining processes, reducing the risk of heat-related damage to both the tool and the workpiece. High thermal conductivity also means that PCD tools can operate at higher speeds and feeds, increasing productivity without compromising tool integrity or the quality of the finished product.
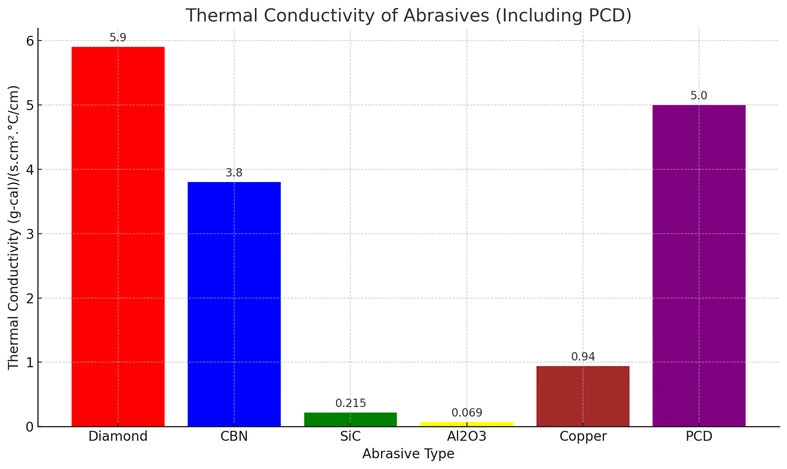
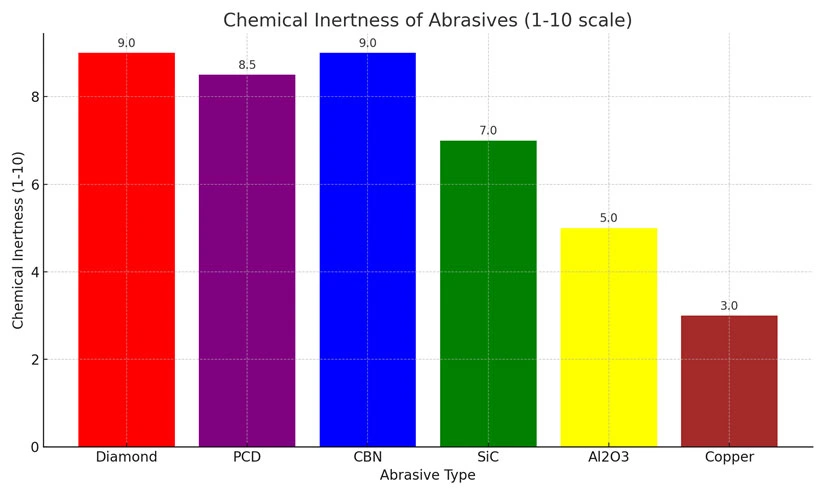
Chemical Inertness
PCD exhibits excellent chemical stability, making it inert to most acids and alkalis at room temperature. This chemical inertness is crucial in applications where materials are exposed to corrosive substances, ensuring that PCD tools do not degrade or lose effectiveness when machining materials like metal matrix composites or when used in environments exposed to corrosive chemicals. This property is particularly beneficial in industries such as mining, oil drilling, and chemical processing, where equipment is regularly exposed to aggressive environments.
Abrasion Resistance
The ability of PCD to resist abrasion is among its most valued properties. This resistance extends the service life of tools under abrasive conditions, which is critical in operations such as earth drilling, stone processing, and the machining of non-ferrous metals. PCD's abrasion resistance ensures consistent performance over time, leading to fewer tool changes, consistent quality in manufactured products, and lower overall production costs.
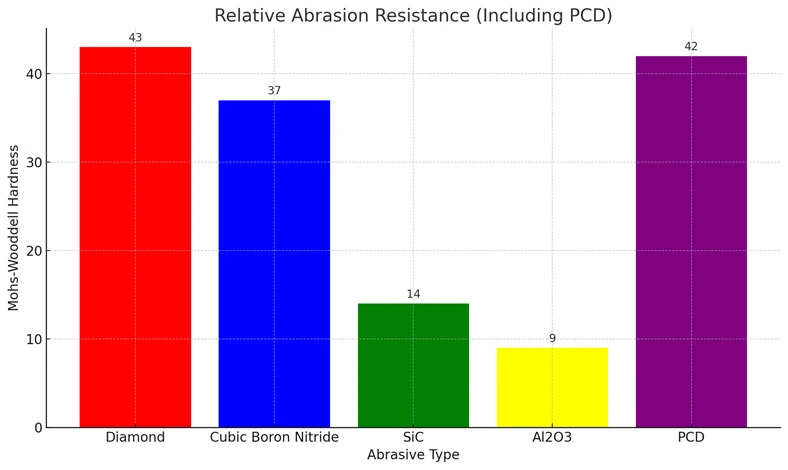
Properties of Polycrystalline Diamond (PCD) presented in a table format
Property |
Description |
---|---|
Hardness and Wear Resistance |
PCD is extremely hard, second only to natural diamonds, providing superior wear resistance. This hardness allows PCD tools to maintain sharpness and dimensional integrity, extending tool life and reducing downtime in abrasive machining applications. |
Thermal Conductivity and Heat Tolerance |
PCD has high thermal conductivity, which allows it to dissipate heat efficiently during machining. This property helps prevent heat-related damage to the tool and workpiece, enabling higher operational speeds and productivity without compromising the integrity of the tool or the quality of the finished product. |
Chemical Inertness |
PCD is chemically stable and inert to most acids and alkalis at room temperature, preventing degradation in corrosive environments. This makes it suitable for use in industries such as mining, oil drilling, and chemical processing where equipment is regularly exposed to harsh chemicals. |
Abrasion Resistance |
PCD's excellent abrasion resistance ensures that it withstands severe wear conditions, prolonging the service life of tools used in earth drilling, stone processing, and the machining of non-ferrous metals. This leads to consistent performance, fewer tool changes, and lower production costs. |
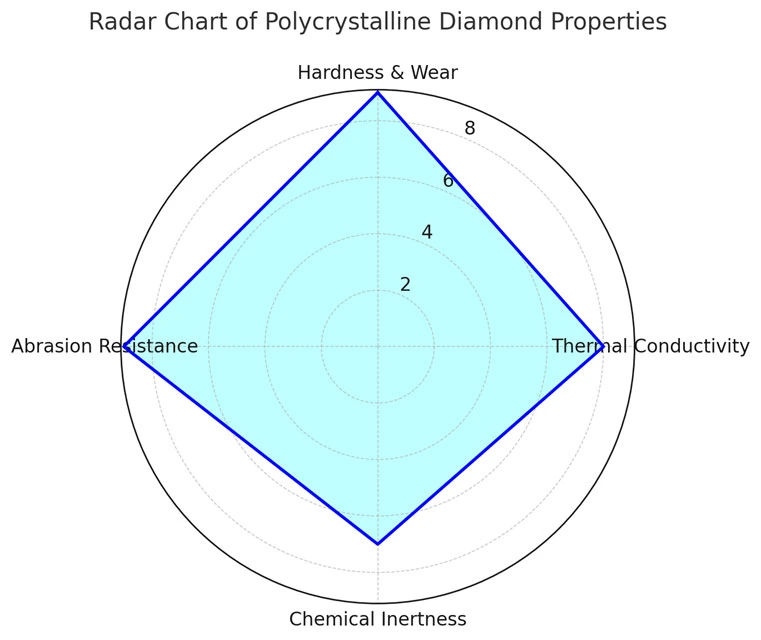
Comparison of PCD Tools with Conventional Diamond Tools, CVD Diamond Tools, Carbide, and Abrasives
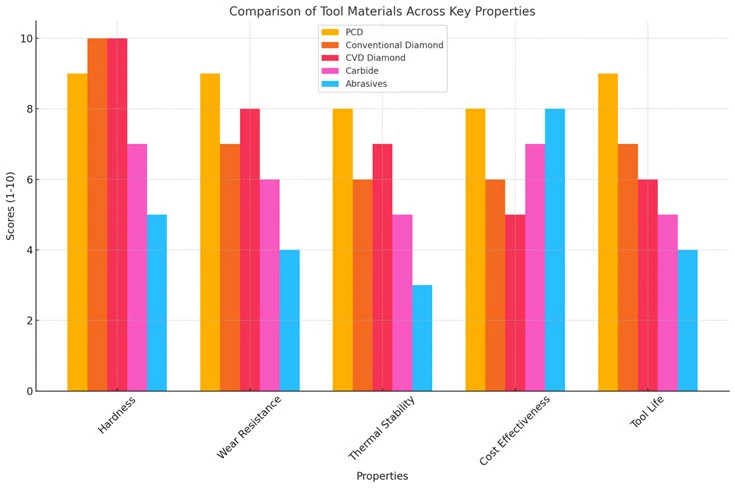
Polycrystalline Diamond (PCD) tools exhibit distinct advantages and some limitations when compared to other tool materials such as conventional diamond tools, Chemical Vapor Deposition (CVD) diamond tools, carbide, and abrasives. Here is an extended comparison of PCD tools against these materials:
PCD Tools vs. Conventional Diamond Tools (Natural or Monocrystalline Diamond): Both PCD and conventional diamond tools are extremely hard, but conventional tools may offer higher clarity and fewer impurities. However, PCD tools are generally tougher and better suited for high-impact and abrasive applications due to their polycrystalline nature, which provides superior wear resistance in abrasive material machining. This is attributed to their randomized crystal orientation, which prevents premature wear along cleavage planes. PCD tools also withstand higher temperatures without degrading, making them suitable for high-heat applications and more cost-effective in the long term due to their durability and extended service life.
PCD Tools vs. CVD Diamond Tools: CVD diamond tools can achieve similar levels of hardness and sometimes superior purity and uniformity compared to PCD. These tools are often engineered to specific needs and are free from the catalytic metals used in PCD. CVD diamond tools typically exhibit better thermal stability due to their purity and single-crystal nature. While CVD tools are preferred for precision applications requiring smooth finishes and detailed work, PCD tools are favored for their durability in high-wear applications. However, manufacturing CVD diamond tools is more energy-intensive and costly, making them less cost-effective than PCD tools for bulk and rough applications.
PCD Tools vs. Carbide: PCD tools surpass carbide in hardness and wear resistance, particularly in abrasive conditions. They also exhibit higher thermal conductivity, which leads to better heat dissipation during machining operations. The tool life of PCD is generally much longer than that of carbide when used in suitable applications, making PCD tools more economical over time despite higher initial costs.
PCD Tools vs. Abrasives: PCD tools enable higher material removal rates than abrasive tools, enhancing efficiency for large-scale and deep-cutting operations. While abrasive tools might provide finer finishes on some surfaces, PCD tools excel in delivering consistent performance over extended periods. PCD tools are versatile enough to handle a wider range of materials effectively, particularly in tough and high-wear environments. Economically, PCD tools offer advantages as they maintain their cutting edges without frequent replacements or dressing, significantly reducing downtime and operational costs.
Comparison table that outlines the key differences and properties of PCD, conventional diamond tools, CVD diamond tools, carbide, and abrasives:
Property |
PCD Tools |
Conventional Diamond Tools |
CVD Diamond Tools |
Carbide |
Abrasives |
---|---|---|---|---|---|
Hardness |
Extremely high |
Highest |
Extremely high |
High |
Moderate |
Wear Resistance |
Very high |
High |
High |
Moderate |
Low |
Thermal Stability |
High |
Moderate |
Very high |
Moderate |
Low |
Cost Effectiveness |
High in long-term applications |
Low due to high cost |
Moderate depending on application |
High initially, low over long term |
High due to frequent replacement |
Tool Life |
Longest |
Long but less than PCD |
Long |
Shorter compared to diamond tools |
Short |
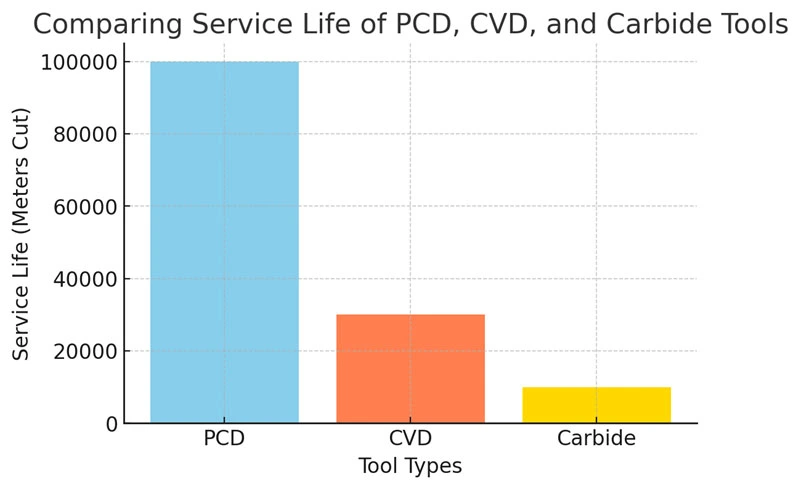
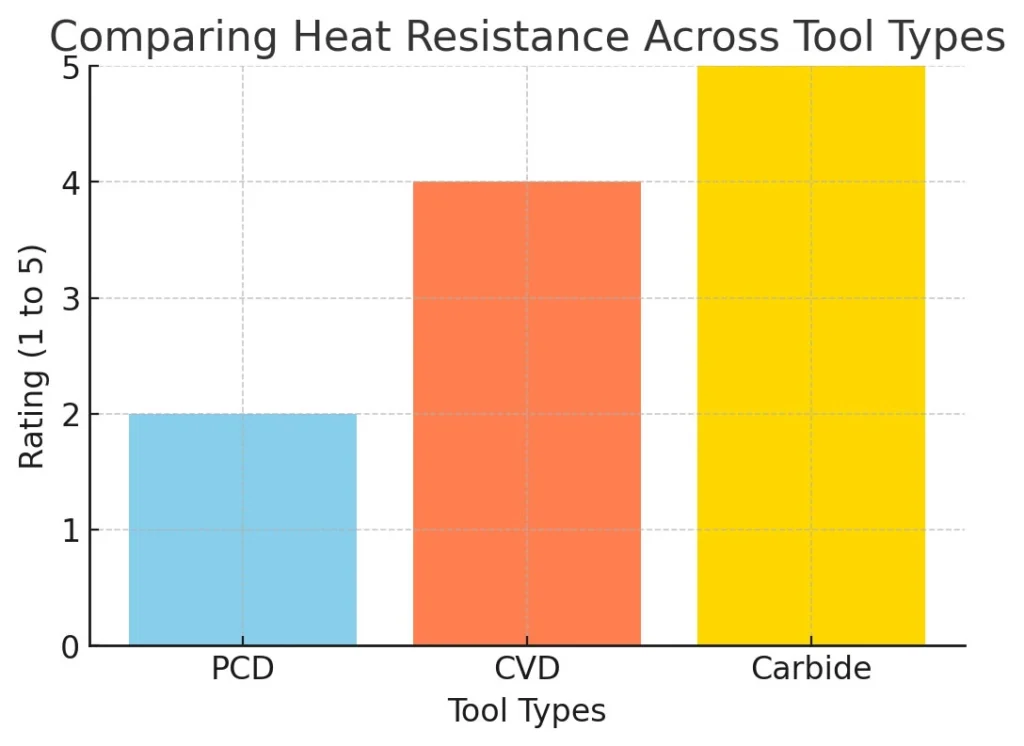
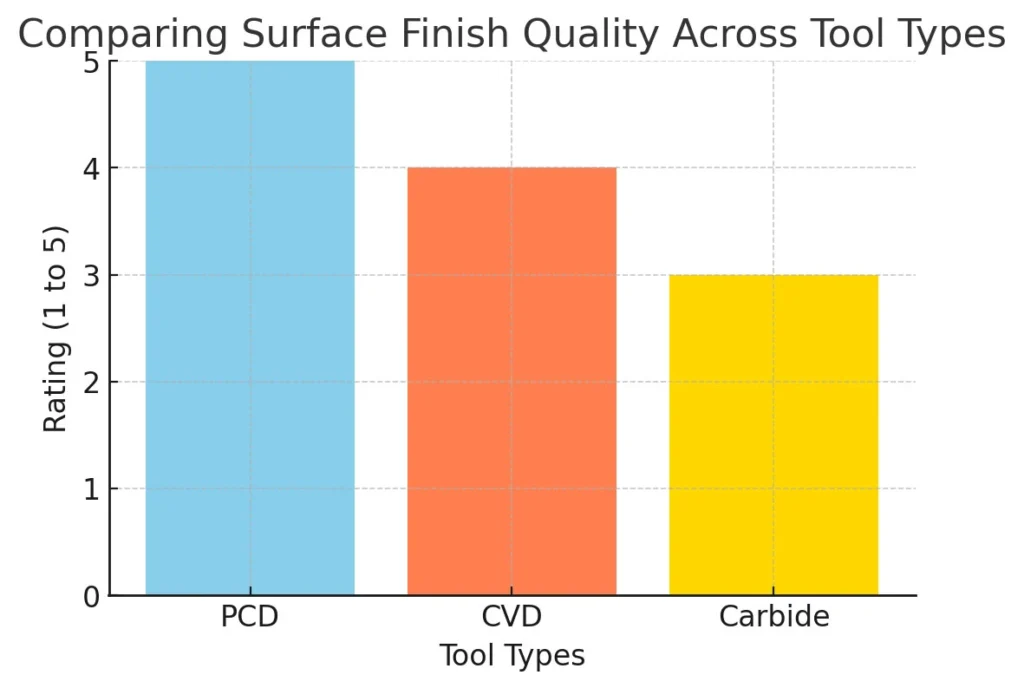
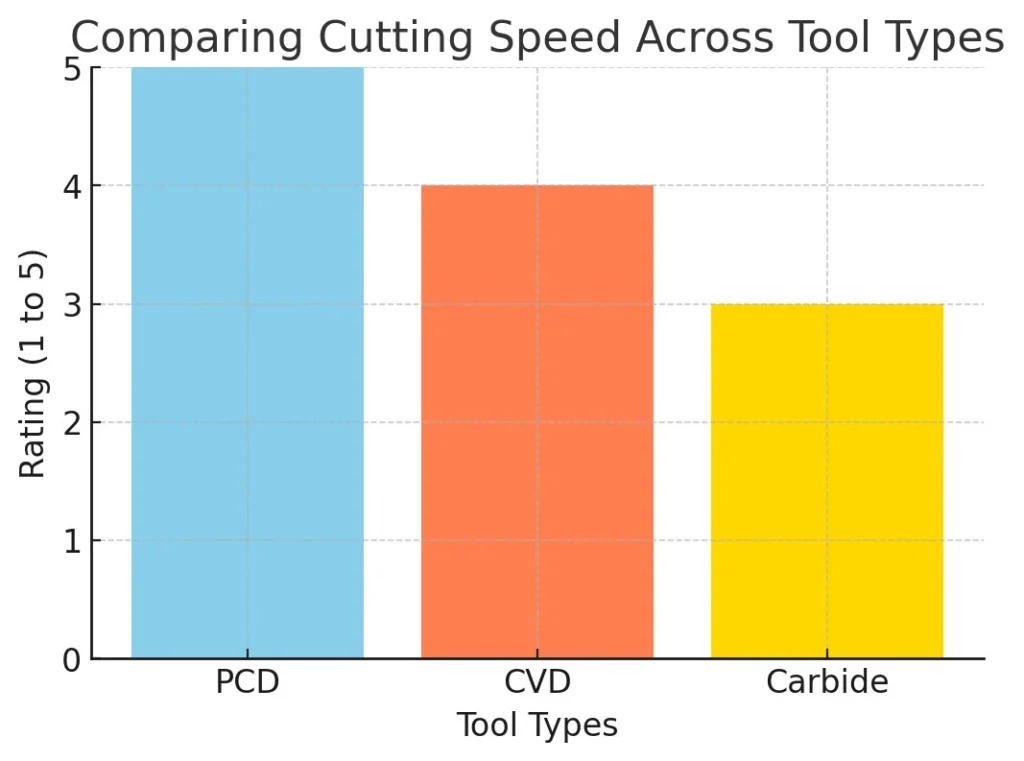
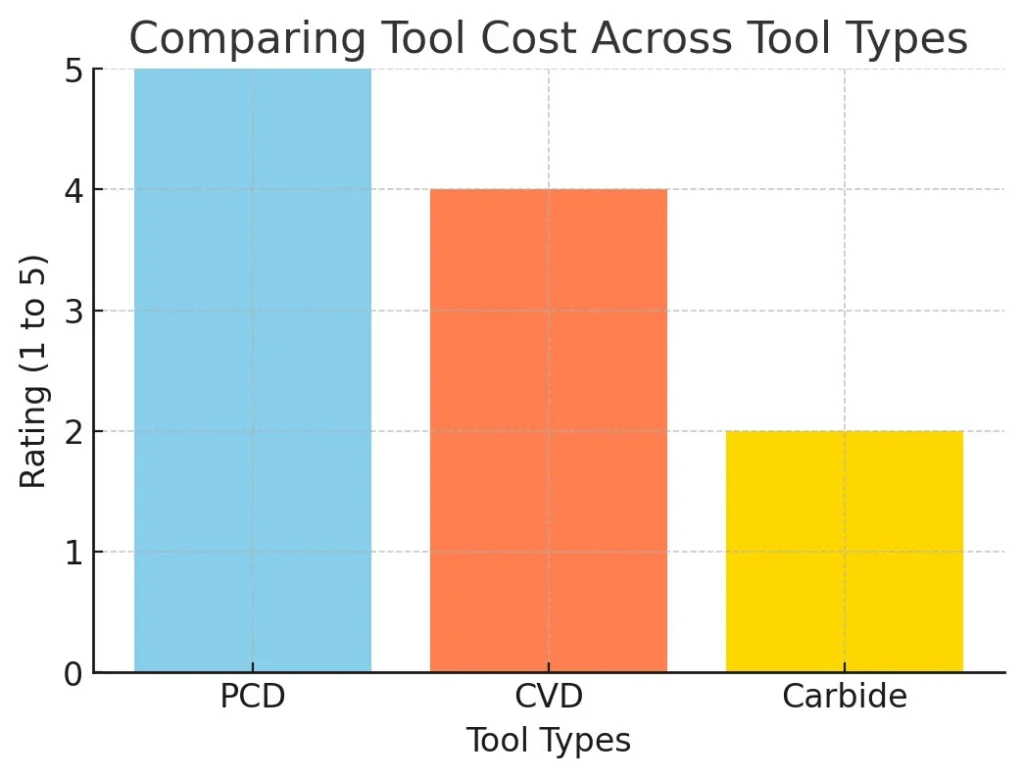
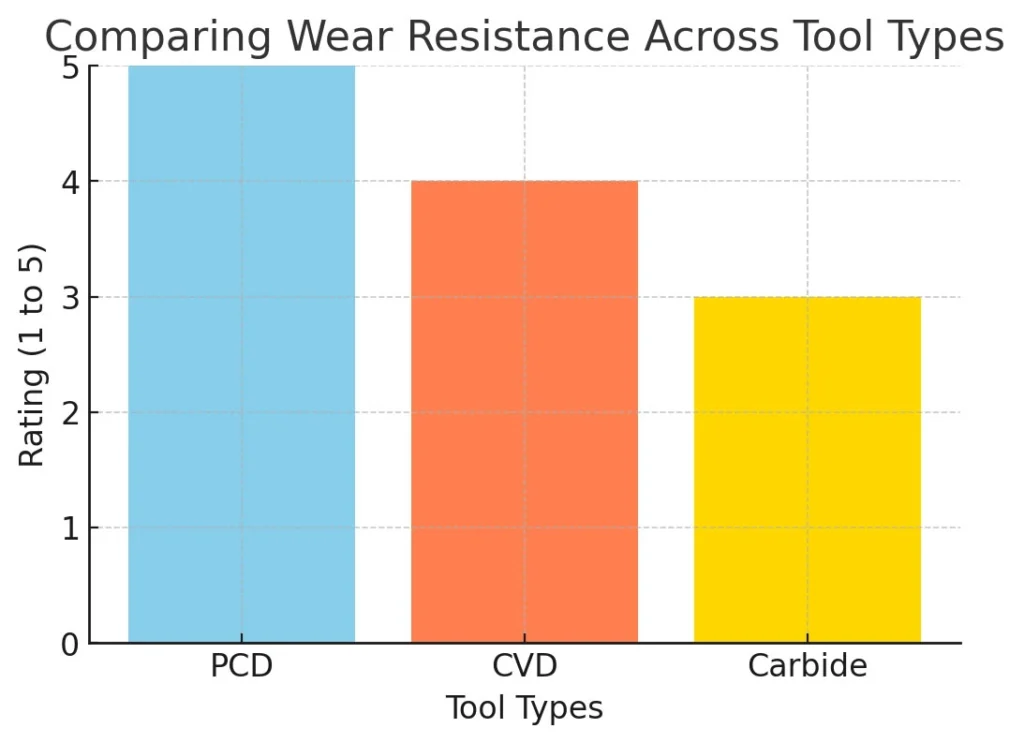
Application of PCD & Tools
PCD (Polycrystalline Diamond) tools are highly versatile, employed across a wide range of industries due to their exceptional hardness, wear resistance, and thermal conductivity. These tools are instrumental in machining non-ferrous and non-metallic materials such as aluminum and its alloys, which are susceptible to sticking and abrasion. Similarly, they are effective for machining copper and its alloys, along with specialized applications like babbitt metal, a soft alloy typically used in bearings. In the woodworking industry, PCD tools excel in sawing, milling, and drilling, handling wood and wood-based fiber materials with unparalleled durability and precision. This makes them ideal for working with reinforced floor boards and wear-resistant plastics, which can otherwise degrade other types of cutting tools rapidly.
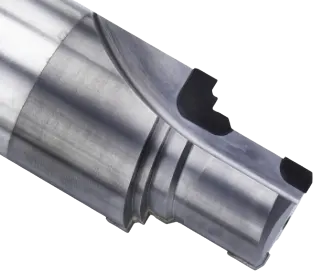
In sectors dealing with advanced materials, such as aluminum oxide, fiberglass composites, and carbon-phenolic materials, PCD tools offer the necessary robustness and thermal stability to process these abrasive materials efficiently without significant wear. For industrial materials like stone, tungsten carbide, and various types of graphite, PCD tools are invaluable due to their hardness and minimal thermal expansion, ensuring precise and enduring tooling.
Nonferrous Metals |
Nonmetallic Materials |
Composites |
---|---|---|
Aluminum Alloys |
Alumina, Fired |
Asbestos |
Brass Alloys |
Beryllia |
Fiberglass Epoxy |
Bronze Alloys |
Ceramics |
Filled Carbons |
Copper Alloys |
Bakelite |
Filled Nylon |
Lead Alloys |
Epoxy |
Filled Phenolic |
Manganese Alloys |
Glass |
Filled P.V.C |
Silver, Platinum |
Graphite |
Filled Silica |
Silicon-Aluminum |
Macor |
Filled Teflon |
Tungsten Carbides |
Rubber, Hard |
Wood, Manufactured |
Zinc Alloys |
Various Plastics |
PCD tools also find applications in machining hard plastics, Bakelite, hard rubbers, and some unfired ceramics, supporting industries from electronics to heavy-duty sectors such as mining and drilling with their broad utility.
On the other hand, PCBN (Polycrystalline Cubic Boron Nitride) tools are recognized for their proficiency in machining hard ferrous materials, a task challenging for other cutting tools. PCBN is particularly suited for machining hardened steels, tool steels, and mold steels, which require high hardness at elevated temperatures—common requirements in automotive and aerospace manufacturing for durable molds and precision components. Moreover, PCBN tools are effectively used for machining chilled cast iron and high chromium cast iron, known for their significant hardness and wear resistance, essential for components like engine blocks and cylinder heads in the automotive industry.
High-temperature alloys, including nickel-based superalloys used in jet engines and turbine parts, are another primary area where PCBN tools are indispensable. These tools maintain hardness and resist chemical wear even at high temperatures. Additionally, PCBN is employed for machining gray cast iron, widely used in constructing machine bases, and challenging non-ferrous materials like zinc alloys and sintered tungsten carbide, noted for their abrasive properties and potential to wear down other types of tools.
Materials |
Subcategories |
---|---|
Hard Cast Iron |
|
All Hard Cast Iron |
|
Chilled Cast Iron |
|
Nodular Cast Iron |
|
Soft Cast Iron |
|
Gray Cast Iron |
|
Sintered Iron |
|
Powdered Metals |
|
Sintered Iron |
|
Hardened Steels |
|
Tool Steels |
|
Die Steels |
|
Case Hardened Steels |
|
A.D. & M Series Steels |
|
Bearing Steels |
|
Superalloys |
|
Inconel 718 (-901, -600) |
|
Rene 77, 95 |
|
Hastelloy |
|
Waspaloy |
|
Stellite |
|
Colmonoy |
|
K-Monel |
Comparison table that outlines the key applications and advantages of PCD (Polycrystalline Diamond) and PCBN (Polycrystalline Cubic Boron Nitride) tools:
Material/Property |
PCD Tools |
PCBN Tools |
---|---|---|
Metals |
Aluminum and aluminum alloys, copper and copper alloys |
Hardened steel, tool steel, mold steel |
Wood and Composites |
Wood, wood-based fiber materials, reinforced floor boards |
Not typically used |
Advanced Materials |
Aluminum oxide, fiberglass composites, carbon-phenolic |
High chromium cast iron, nickel-based high temperature alloys |
Industrial Materials |
Stone materials, tungsten carbide, graphite |
Chilled cast iron, gray cast iron |
Plastics and Similar |
Hard plastics, Bakelite, hard rubber |
Zinc alloys, sintered tungsten carbide |
Hardness and Wear |
Extremely hard, excellent wear resistance |
Exceptionally hard, superior wear resistance in ferrous materials |
Thermal Stability |
High thermal stability, suitable for high-heat applications |
Very high thermal stability, especially at elevated temperatures |
Cost Effectiveness |
High in long-term applications due to durability |
High due to ability to machine hard-to-cut materials efficiently |
Suitable Applications |
Non-ferrous and non-metallic materials |
Hard ferrous materials and wear-resistant applications |
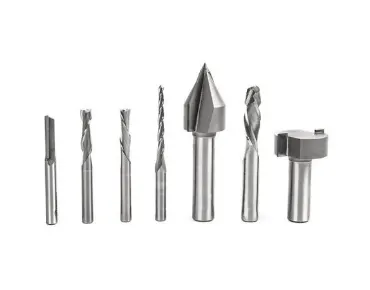
Comparison table outlining the types of PCD tools and their specific uses across various industries:
Type of PCD Tool |
Description |
Primary Uses |
Industries Benefited |
---|---|---|---|
PCD Inserts |
Tools with replaceable tips for turning, milling, and cutting. |
Machining aluminum and non-ferrous metals, precision cutting. |
Automotive, Aerospace, Metal Fabrication |
PCD Drills |
Specialized drills for creating precise holes. |
Drilling in composite materials like CFRP and aluminum stacks. |
Aerospace, Automotive, Construction |
PCD End Mills |
Milling tools for detailed and complex machining. |
Milling operations in aerospace applications, aluminum alloys. |
Aerospace, Automotive, Manufacturing |
PCD Reamers |
Used to refine holes to precise dimensions and smooth finishes. |
High-precision hole finishing in metals and composites. |
Automotive, Aerospace, Manufacturing |
PCD Saw Blades |
Saw blades designed for long-lasting cutting performance. |
Cutting wood, particle board, and other composite materials. |
Woodworking, Construction |
PCD Grinding Tools |
Abrasive tools for material removal and surface preparation. |
Polishing concrete floors, removing surface coatings. |
Construction, Stonework, Renovation |
PCD Wire Drawing Dies |
Dies used in the shaping of metal wires. |
Drawing fine wires from copper, aluminum, and other metals. |
Electrical, Communications, Manufacturing |
Advantages of Using Polycrystalline Diamond (PCD) Tools
ADVANTAGES OF PCD & PCBN Tools
-
Good surface finish
-
High accuracy
-
Longer tool life
-
Fast material removal rate
-
Lower energy cost
-
Eco friendly
-
Lower stock management
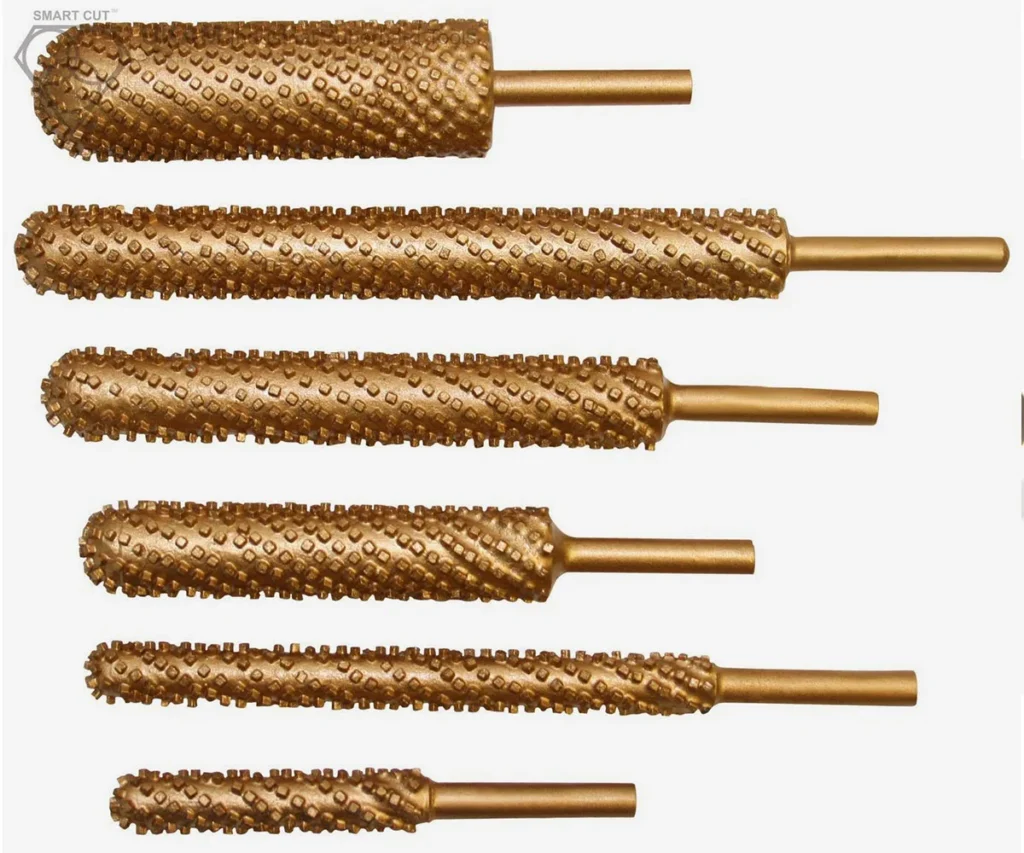
Cost-effectiveness Over the Tool's Lifecycle Polycrystalline Diamond (PCD) tools represent a significant upfront investment; however, their cost-effectiveness becomes apparent over the tool's lifecycle. The superior durability and extended lifespan of PCD tools mean fewer replacements, less frequent purchases, and reduced inventory costs. Over time, this leads to substantial savings, making PCD tools a prudent choice for operations that prioritize long-term budget management.
Reduced Machine Downtime Due to Superior Wear Resistance One of the principal advantages of PCD tools is their exceptional wear resistance. This quality is particularly valuable in high-volume production settings where tool durability directly influences operational efficiency. By enduring longer periods without wear, PCD tools minimize the frequency of tool changes, thereby reducing machine downtime. This consistent performance not only boosts productivity but also enhances the reliability of manufacturing processes.
Improved Surface Finish Quality on Machined Parts PCD tools are renowned for their ability to maintain a sharp cutting edge, which is crucial for achieving a high-quality surface finish on machined parts. Unlike other materials that may deteriorate under intense operational conditions, PCD maintains its integrity, ensuring that the quality of the surface finish remains consistent throughout the tool's lifespan. This is especially important in industries where precision and finish quality are critical, such as in the automotive or aerospace sectors.
Environmental Impact Due to Longer Tool Life and Less Waste The longer lifecycle of PCD tools also contributes positively to environmental sustainability. Longer-lasting tools mean less frequent replacement, which in turn leads to reduced consumption of raw materials and lower waste production. Additionally, the energy consumed in the manufacturing, transportation, and disposal of tools is significantly lowered. This reduction in waste and energy use is an important consideration for industries aiming to reduce their environmental footprint and comply with increasingly stringent environmental regulations.
starting parameters for machining with Polycrystalline Diamond (PCD), including additional materials like stainless steel, titanium alloys, and nickel alloys:
Recommended RPM’s
Workpiece Material |
Nose Radius |
Side Relief Degrees |
Positive Back Rake Angle Degrees |
Speed (sfm) |
Depth of Cut |
Feed Rate |
---|---|---|---|---|---|---|
Aluminum alloys |
0.006" - 0.040" |
5-10 |
0-10 |
3000 - 5000 |
0.005" - 0.020" |
0.002" - 0.008" |
(0.15-1.02mm) |
(914-1524 M/mm) |
(0.13-0.51mm) |
(0.051-0.20mm) |
|||
Copper alloys (including bronze) |
0.010" - 0.040" |
5-30 |
10-20 |
1500-3500 |
0.005" - 0.020" |
0.001" - 0.006" |
(0.25-1.02mm) |
(457-1067 M/mm) |
(0.13-0.51mm) |
(0.025-0.15mm) |
|||
Sintered cemented tungsten carbide |
0.040" - 0.250" |
5-12 |
0-6 |
30-50 |
0.0005" - 0.005" |
0.004" - 0.006" |
(1.02-6.00mm) |
(10-15 M/mm) |
(0.025-0.076mm) |
(0.10-0.15mm) |
|||
Glass fiber/plastic composites |
0.030" - 0.090" |
5-20 |
0-5 |
400-3600 |
0.001" - 0.003" |
0.001" - 0.010" |
(0.76-2.29mm) |
(122-1097 M/mm) |
(0.025-0.076mm) |
(0.025-0.25mm) |
|||
Carbon/plastic composites |
0.020" - 0.040" |
5-20 |
0-5 |
500-2000 |
0.010" - 0.100" |
0.005" - 0.015" |
(0.51-1.02mm) |
(152-610 M/mm) |
(0.25-2.54mm) |
(0.13-0.38mm) |
|||
High-alumina ceramics |
0.010" - 0.040" |
5-20 |
0-5 |
1200-2400 |
0.0005" - 0.005" |
0.001" - 0.004" |
(0.25-1.02mm) |
(365-730 M/mm) |
(0.013-0.13mm) |
(0.025-0.102mm) |
|||
Stainless steel |
0.010" - 0.030" |
5-15 |
5-10 |
600-1200 |
0.002" - 0.010" |
0.002" - 0.008" |
(0.25-0.76mm) |
(183-366 M/mm) |
(0.051-0.25mm) |
(0.051-0.20mm) |
|||
Titanium alloys |
0.010" - 0.030" |
5-15 |
0-5 |
200-800 |
0.002" - 0.008" |
0.001" - 0.005" |
(0.25-0.76mm) |
(61-244 M/mm) |
(0.051-0.20mm) |
(0.025-0.13mm) |
|||
Nickel alloys |
0.010" - 0.030" |
5-15 |
0-10 |
200-800 |
0.001" - 0.006" |
0.001" - 0.004" |
(0.25-0.76mm) |
(61-244 M/mm) |
(0.025-0.15mm) |
(0.025-0.10mm) |
These parameters are starting it provides a speed of 5 to 7 centimeters per minute, with a lifetime of 9.5 to 12.5 meters.
Polycrystalline Diamond (PCD) & Cubic Boron Nitride (PCBN) RPM’s & Feed Rates
Determining the proper RPMs, feed rates, and operational parameters for machining with Polycrystalline Diamond (PCD) and Cubic Boron Nitride (PCBN) tools requires careful consideration of the material properties, tool capabilities, and the desired outcomes of the machining process. Establishing the correct speeds and feeds is crucial not only for achieving the desired accuracy and surface finish but also for extending the tool life and ensuring efficient machining operations.
Understanding Material Hardness and Abrasiveness: The first step in setting the right parameters involves understanding the hardness and abrasiveness of the material to be machined. Harder materials typically require lower speeds to reduce tool wear, whereas softer materials can be machined at higher speeds. The presence of abrasive materials like silicon in aluminum alloys, for example, necessitates adjustments in the speed to prevent premature tool degradation.
Optimizing Tool Performance with RPMs: The RPM setting for PCD and PCBN tools depends largely on the diameter of the tool and the material being machined. Higher RPMs may be effective for soft, non-abrasive materials but can lead to excessive heat and tool wear when dealing with harder materials. It is important to start at a lower RPM and gradually increase, monitoring the tool wear and surface finish, until the optimal speed is identified.
Feed Rate Adjustments: The feed rate must be adjusted to match the RPMs, taking into consideration the tool's ability to remove material efficiently without overloading. A higher feed rate might be suitable for softer materials to prevent the tool from rubbing and generating excessive heat. In contrast, hard or brittle materials require a slower feed rate to minimize the risk of chipping or breaking the workpiece or the tool.
Depth of Cut and Tool Passes: The depth of cut should be set based on the tool's specifications and the strength of the material. Lighter cuts with multiple passes might be necessary for hard materials to avoid putting too much pressure on the tool. This strategy helps in maintaining the structural integrity of both the tool and the workpiece.
Machine Capability and Tooling Configuration: It's also vital to consider the capabilities of the machining equipment. The rigidity of the machine, the power available, and the stability of tool setup play significant roles in how effectively the RPMs and feed rates can be implemented. Adequate machine support is essential for high-precision work and for the longevity of PCD and PCBN tools.
Continuous Monitoring and Adjustment: Machining with advanced tools like PCD and PCBN is often a process of continuous learning and adjustment. Real-time monitoring of tool performance, surface finish, and tool wear can provide valuable feedback for adjusting parameters to meet specific machining needs. This adaptive approach allows for fine-tuning that optimizes tool performance and output quality.
Recommended speeds and feeds for Polycrystalline Diamond (PCD) tools
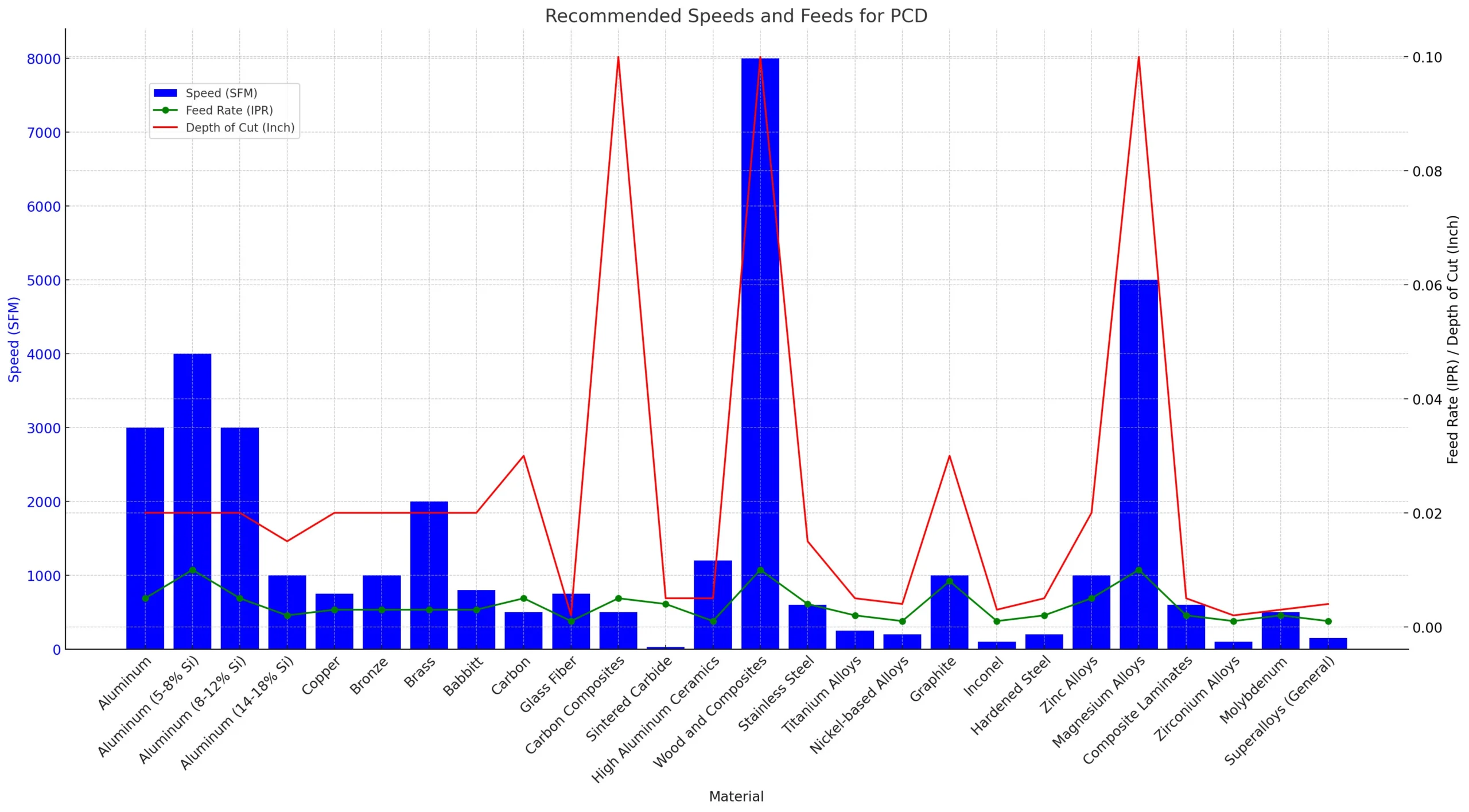
Material |
Speed (SFM) |
Feed Rate (IPR) |
Depth of Cut (Inch) |
---|---|---|---|
Aluminum |
3000-5000 |
.005- .008 |
.005- .020 |
Aluminum (5-8% Si) |
4000-6000 |
.010- .020 |
.005- .020 |
Aluminum (8-12% Si) |
3000-5000 |
.005- .015 |
.005- .020 |
Aluminum (14-18% Si) |
1000-3000 |
.002- .010 |
.003- .015 |
Copper |
750-1500 |
.003- .008 |
.005- .020 |
Bronze |
1000-1250 |
.003- .008 |
.005- .020 |
Brass |
2000-4000 |
.003- .010 |
.005- .020 |
Babbitt |
800-1200 |
.003- .010 |
.005- .020 |
Carbon |
500-1000 |
.005- .015 |
.005- .030 |
Glass Fiber |
750-1000 |
.001- .010 |
.001- .002 |
Carbon Composites |
500-2000 |
.005- .015 |
.010- .100 |
Sintered Carbide |
30-50 |
.004- .006 |
.0005- .005 |
High Aluminum Ceramics |
1200-2400 |
.001- .004 |
.0005- .005 |
Wood and Composites |
8000-13000 |
.010- .010 |
.010- .100 |
Stainless Steel |
600-1000 |
.004- .010 |
.002- .015 |
Titanium Alloys |
250-500 |
.002- .006 |
.001- .005 |
Nickel-based Alloys |
200-800 |
.001- .004 |
.001- .004 |
Graphite |
1000-3000 |
.008- .020 |
.005- .030 |
Inconel |
100-250 |
.001- .004 |
.0005- .003 |
Hardened Steel |
200-600 |
.002- .006 |
.0005- .005 |
Zinc Alloys |
1000-1500 |
.005- .010 |
.005- .020 |
Magnesium Alloys |
5000-7000 |
.010- .020 |
.010- .100 |
Composite Laminates |
600-1200 |
.002- .008 |
.001- .005 |
Zirconium Alloys |
100-400 |
.001- .003 |
.0005- .002 |
Molybdenum |
500-800 |
.002- .006 |
.001- .003 |
Superalloys (General) |
150-500 |
.001- .005 |
.0005- .004 |
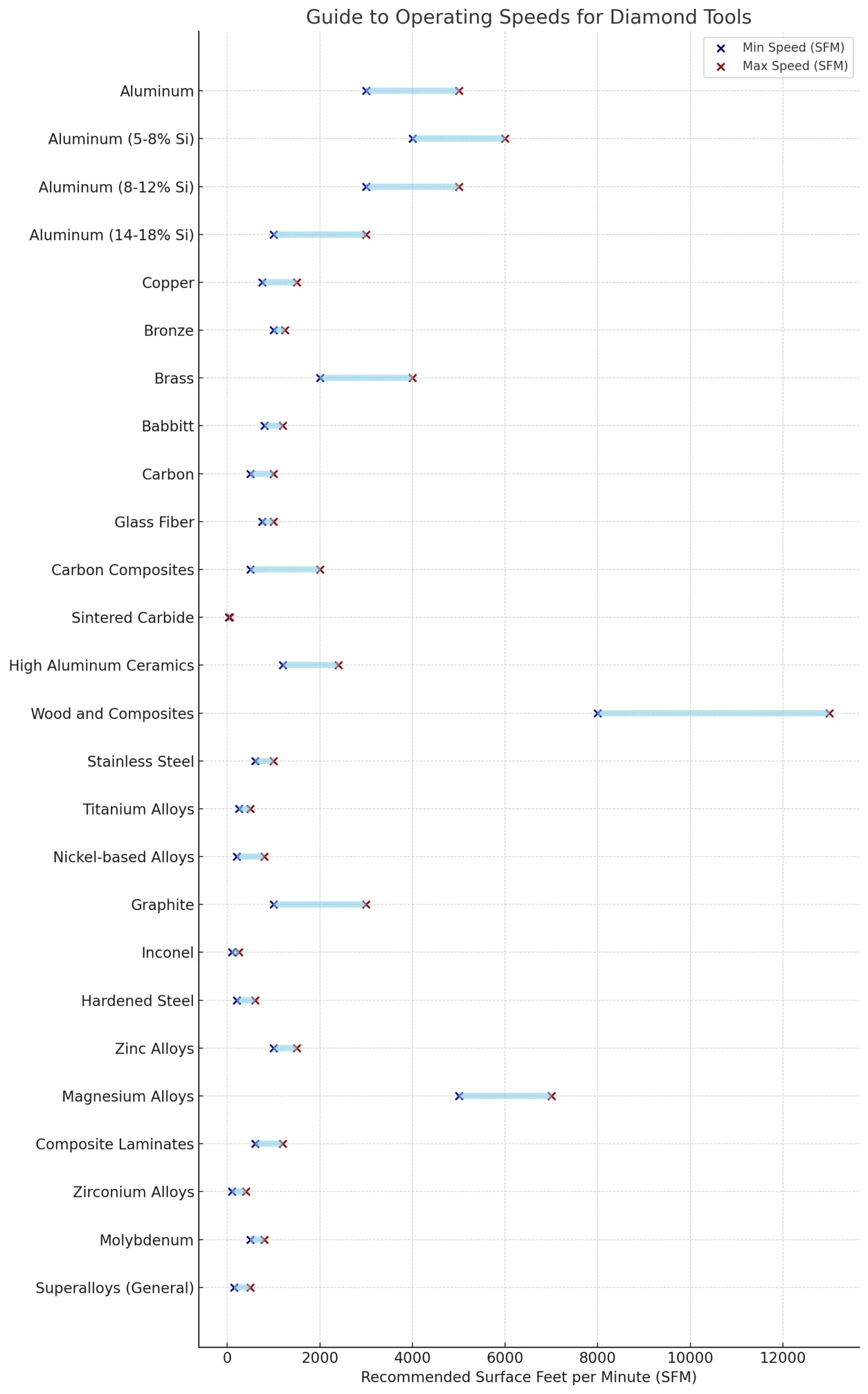
Recommended speeds and feeds for Polycrystalline CBN tools
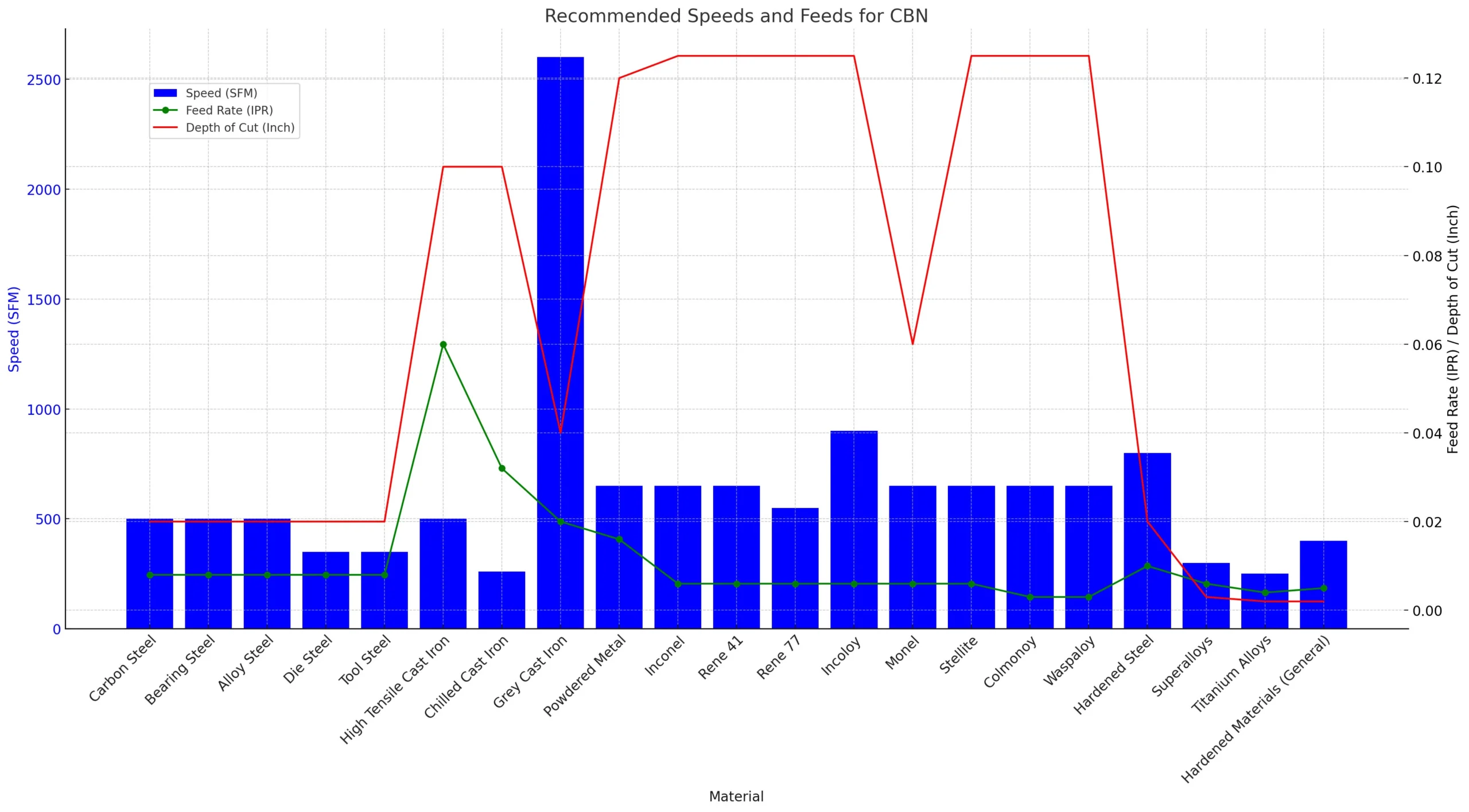
Material |
Speed (SFM) |
Feed Rate (IPR) |
Depth of Cut (Inch) |
---|---|---|---|
Carbon Steel |
200-500 |
.008 MAX |
.020 MAX |
Bearing Steel |
200-500 |
.008 MAX |
.020 MAX |
Alloy Steel |
200-500 |
.008 MAX |
.020 MAX |
Die Steel |
160-350 |
.008 MAX |
.020 MAX |
Tool Steel |
160-350 |
.008 MAX |
.020 MAX |
High Tensile Cast Iron |
200-500 |
.060 MAX |
.100 MAX |
Chilled Cast Iron |
130-260 |
.032 MAX |
.100 MAX |
Grey Cast Iron |
1000-2600 |
.020 MAX |
.040 MAX |
Powdered Metal |
500-650 |
.016 MAX |
.120 MAX |
Inconel |
500-650 |
.006 MAX |
.125 MAX |
Rene 41 |
500-650 |
.006 MAX |
.125 MAX |
Rene 77 |
450-550 |
.006 MAX |
.125 MAX |
Incoloy |
750-900 |
.006 MAX |
.125 MAX |
Monel |
550-650 |
.006 MAX |
.060 MAX |
Stellite |
550-650 |
.006 MAX |
.125 MAX |
Colmonoy |
550-650 |
.003 MAX |
.125 MAX |
Waspaloy |
550-650 |
.003 MAX |
.125 MAX |
Hardened Steel |
200-800 |
.004-.010 |
.005-.020 |
Superalloys |
100-300 |
.002-.006 |
.0005-.003 |
Titanium Alloys |
100-250 |
.001-.004 |
.0005-.002 |
Hardened Materials (General) |
150-400 |
.001-.005 |
.0005-.002 |
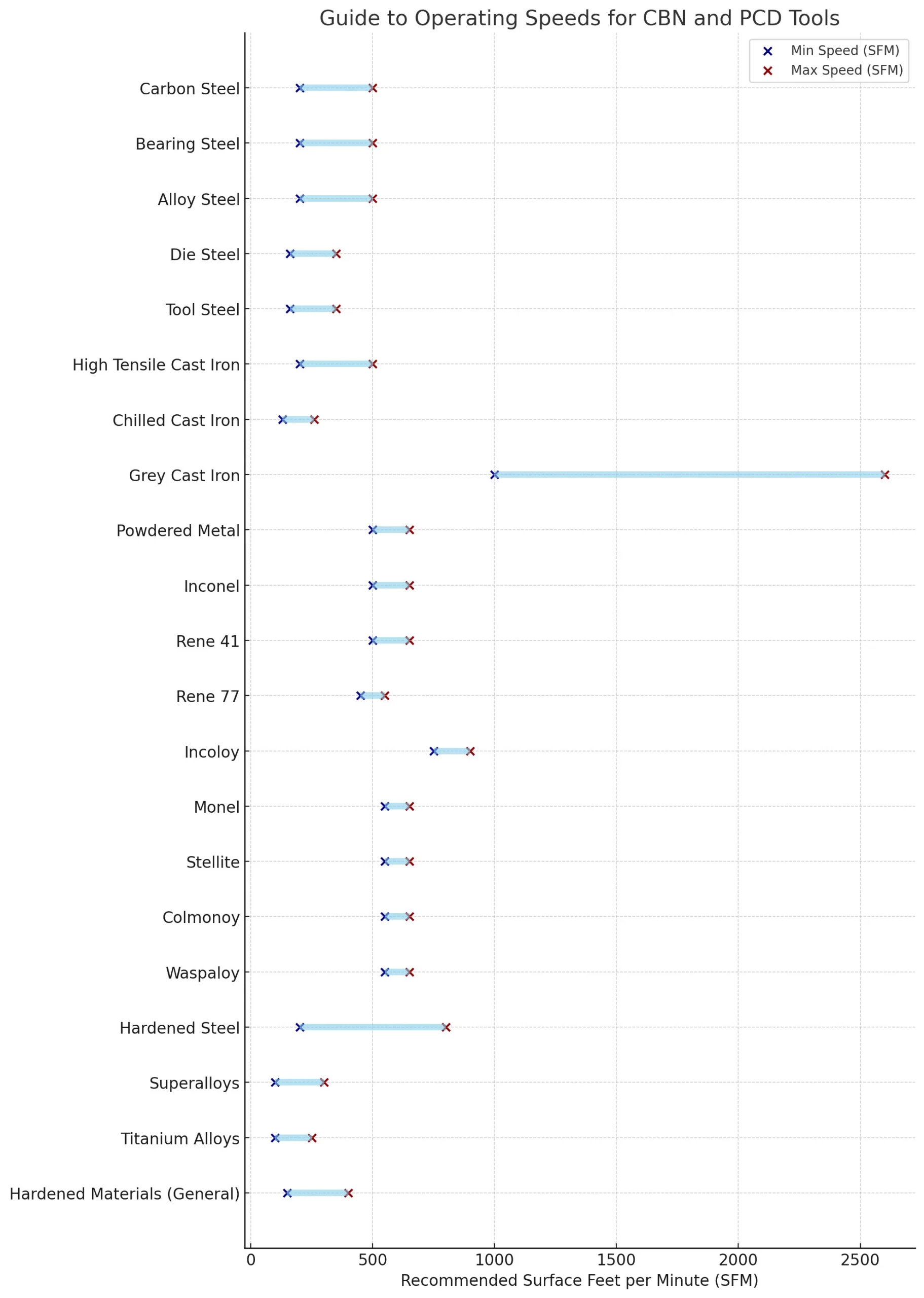
Cutting Speeds & Feed Rates for PCD, CVD, & Carbide Drills
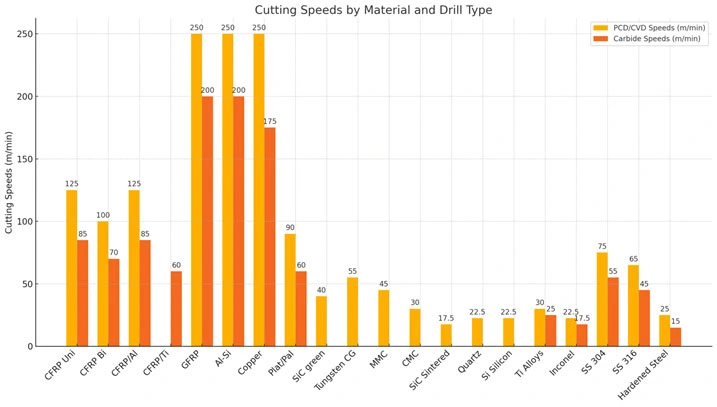
Here is a comparison table showing the cutting speeds and feed rates for PCD, CVD, & Carbide Drills
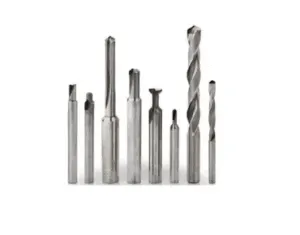
Material |
PCD/CVD Cutting Speed (m/min) |
Carbide Cutting Speed (m/min) |
Feed per revolution 2-3 (mm) |
Feed per revolution 4-5 (mm) |
Feed per revolution 6-7 (mm) |
Feed per revolution 7-8 (mm) |
Feed per revolution 8-10 (mm) |
---|---|---|---|---|---|---|---|
CFRP Unidirectional |
100 – 150 |
70 – 100 |
0.02-0.03 |
0.04-0.06 |
0.05-0.07 |
0.06-0.08 |
0.09-0.1 |
CFRP Bidirectional |
80 – 120 |
60 – 80 |
0.01-0.02 |
0.015-0.025 |
0.02-0.03 |
0.03-0.04 |
0.04-0.05 |
CFRP/Al * |
100-150 |
70 – 100 |
0.07-0.1 |
0.1-0.14 |
0.12-0.16 |
0.13-0.18 |
0.15-0.2 |
CFRP/Ti ** |
NA |
50 – 70 |
0.02-0.03 |
0.04-0.06 |
0.05-0.07 |
0.06-0.08 |
0.09-0.1 |
GFRP |
200 – 300 |
150 – 250 |
0.03 – 0.04 |
0.05-0.07 |
0.06-0.08 |
0.08-0.1 |
0.1-0.15 |
Aluminum-Si |
200 – 300 |
150 – 250 |
0.07-0.1 |
0.1-0.14 |
0.12-0.16 |
0.13-0.18 |
0.15-0.2 |
Copper |
200 – 300 |
150 – 200 |
0.05-0.08 |
0.08-0.12 |
0.1-0.13 |
0.12-0.16 |
0.13-0.18 |
Platinum, Paladium |
80-100 |
50-70 |
0.05-0.08 |
0.08-0.12 |
0.1-0.13 |
0.12-0.16 |
0.13-0.18 |
SiC green stage*** |
35-45 |
NA |
0.07-0.1 |
0.1-0.14 |
0.12-0.16 |
0.13-0.18 |
0.15-0.2 |
Tungsten Carbide green stage |
50-60 |
NA |
0.07-0.1 |
0.1-0.14 |
0.12-0.16 |
0.13-0.18 |
0.15-0.2 |
MMC: Al+SiC, Al+B2C |
40-50 |
NA |
0.01-0.02 |
0.015-0.025 |
0.02-0.03 |
0.03-0.04 |
0.04-0.05 |
CMC: SiC+SiC |
25-35 |
NA |
0.01-0.02 |
0.015-0.025 |
0.02-0.03 |
0.03-0.04 |
0.04-0.05 |
SiC, TC Sintered |
15-20 |
NA |
0.005-0.01 |
0.006-0.012 |
0.008-0.016 |
0.01-0.018 |
0.012-0.02 |
Quartz |
20-25 |
NA |
0.005-0.01 |
0.006-0.012 |
0.008-0.016 |
0.01-0.018 |
0.012-0.02 |
Single Crystal Silicon |
20-25 |
NA |
0.005-0.01 |
0.006-0.012 |
0.008-0.016 |
0.01-0.018 |
0.012-0.02 |
Titanium Alloys |
20-40 |
15-35 |
0.02-0.04 |
0.03-0.05 |
0.04-0.06 |
0.05-0.07 |
0.06-0.08 |
Inconel Alloys |
15-30 |
10-25 |
0.01-0.03 |
0.02-0.04 |
0.03-0.05 |
0.04-0.06 |
0.05-0.07 |
Stainless Steel 304 |
60-90 |
40-70 |
0.02-0.03 |
0.03-0.05 |
0.04-0.06 |
0.05-0.07 |
0.06-0.09 |
Stainless Steel 316 |
50-80 |
30-60 |
0.02-0.03 |
0.03-0.05 |
0.04-0.06 |
0.05-0.07 |
0.06-0.09 |
Hardened Steels |
20-30 |
10-20 |
0.01-0.02 |
0.015-0.025 |
0.02-0.03 |
0.03-0.04 |
0.04-0.05 |
Cutting Speeds & Feed Rates for PCD, CVD, & Milling Tools
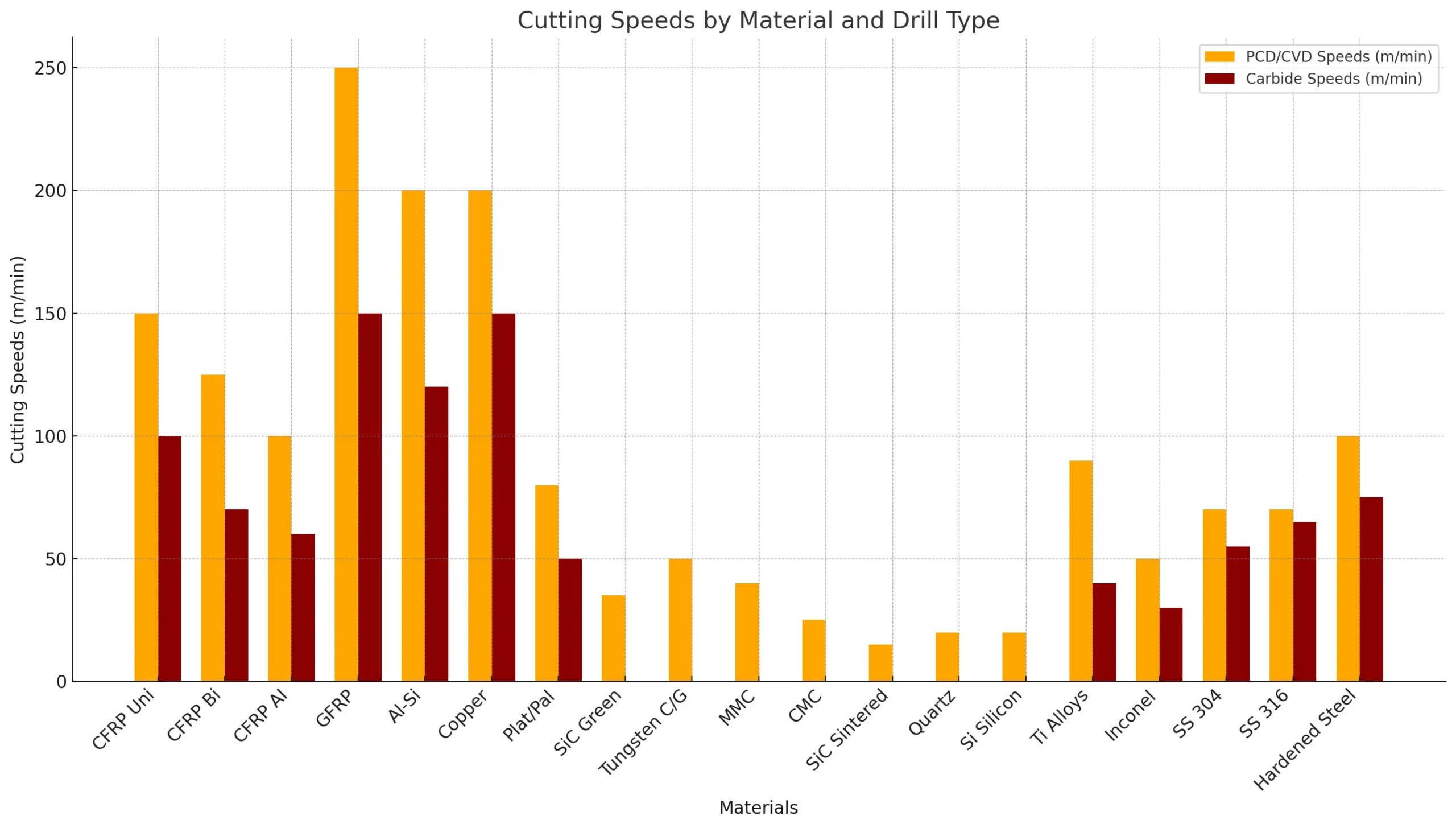
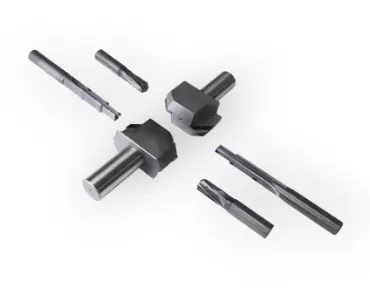
Material |
Cutting Speed (m/min) for PCD or CVD End-Mills |
Cutting Speed (m/min) for Carbide End-Mills |
Feed per Tooth (mm) by Diameter (2 – 3 mm) |
(4 – 5 mm) |
(6 – 8 mm) |
(8 – 10 mm) |
(10 – 12 mm) |
---|---|---|---|---|---|---|---|
CFRP Unidirectional |
150-200 |
100-150 |
0.015-0.02 |
0.02-0.025 |
0.025-0.03 |
0.03-0.035 |
0.035-0.04 |
CFRP Weave
|
100-150 |
70-120 |
0.01-0.015 |
0.015-0.02 |
0.02-0.025 |
0.025-0.03 |
0.03-0.035 |
GFRP |
250-300 |
150-200 |
0.015-0.02 |
0.02-0.025 |
0.025-0.03 |
0.03-0.035 |
0.035-0.04 |
Aluminum-Si |
200-300 |
120-170 |
0.015-0.02 |
0.02-0.025 |
0.025-0.03 |
0.03-0.035 |
0.035-0.04 |
Copper |
200-300 |
150-200 |
0.015-0.02 |
0.02-0.025 |
0.025-0.03 |
0.03-0.035 |
0.035-0.04 |
Platinum, Palladium
|
80-100 |
50-70 |
0.01-0.015 |
0.015-0.02 |
0.02-0.025 |
0.025-0.03 |
0.03-0.035 |
SiC green stage
|
35-45 |
NA |
0.01-0.015 |
0.015-0.02 |
0.02-0.025 |
0.025-0.03 |
0.03-0.035 |
Tungsten Carbide green stage
|
50-60 |
NA |
0.01-0.015 |
0.015-0.02 |
0.02-0.025 |
0.025-0.03 |
0.03-0.035 |
MMC: Al+SiC, Al+B2C
|
40-50 |
NA |
0.008-0.012 |
0.012-0.016 |
0.016-0.02 |
0.02-0.025 |
0.025-0.03 |
CMC: SiC+SiC
|
25-35 |
NA |
0.008-0.012 |
0.012-0.016 |
0.016-0.02 |
0.02-0.025 |
0.025-0.03 |
SiC, TC: Sintered
|
15-20 |
NA |
0.005-0.008 |
0.006-0.01 |
0.01-0.015 |
0.012-0.018 |
0.015-0.02 |
Quartz
|
20-25 |
NA |
0.005-0.008 |
0.006-0.01 |
0.01-0.015 |
0.012-0.018 |
0.015-0.02 |
Single Crystal Silicon |
20-25 |
NA |
0.005-0.008 |
0.006-0.01 |
0.01-0.015 |
0.012-0.018 |
0.015-0.02 |
Titanium |
90-120 |
40-60 |
0.005-0.007 |
0.008-0.011 |
0.012-0.015 |
0.016-0.018 |
0.019-0.022 |
High-Speed Steel
|
50-70 |
30-50 |
0.007-0.009 |
0.01-0.012 |
0.013-0.016 |
0.017-0.019 |
0.02-0.022 |
Hardened Steel
|
100-120 |
70-90 |
0.006-0.008 |
0.008-0.01 |
0.01-0.012 |
0.013-0.015 |
0.016-0.018 |
Magnesium Alloy
|
250-350 |
150-250 |
0.012-0.015 |
0.016-0.02 |
0.021-0.025 |
0.026-0.03 |
0.031-0.035 |
Brass and Bronze |
150-250 |
100-150 |
0.01-0.013 |
0.014-0.017 |
0.018-0.021 |
0.022-0.025 |
0.026-0.029 |
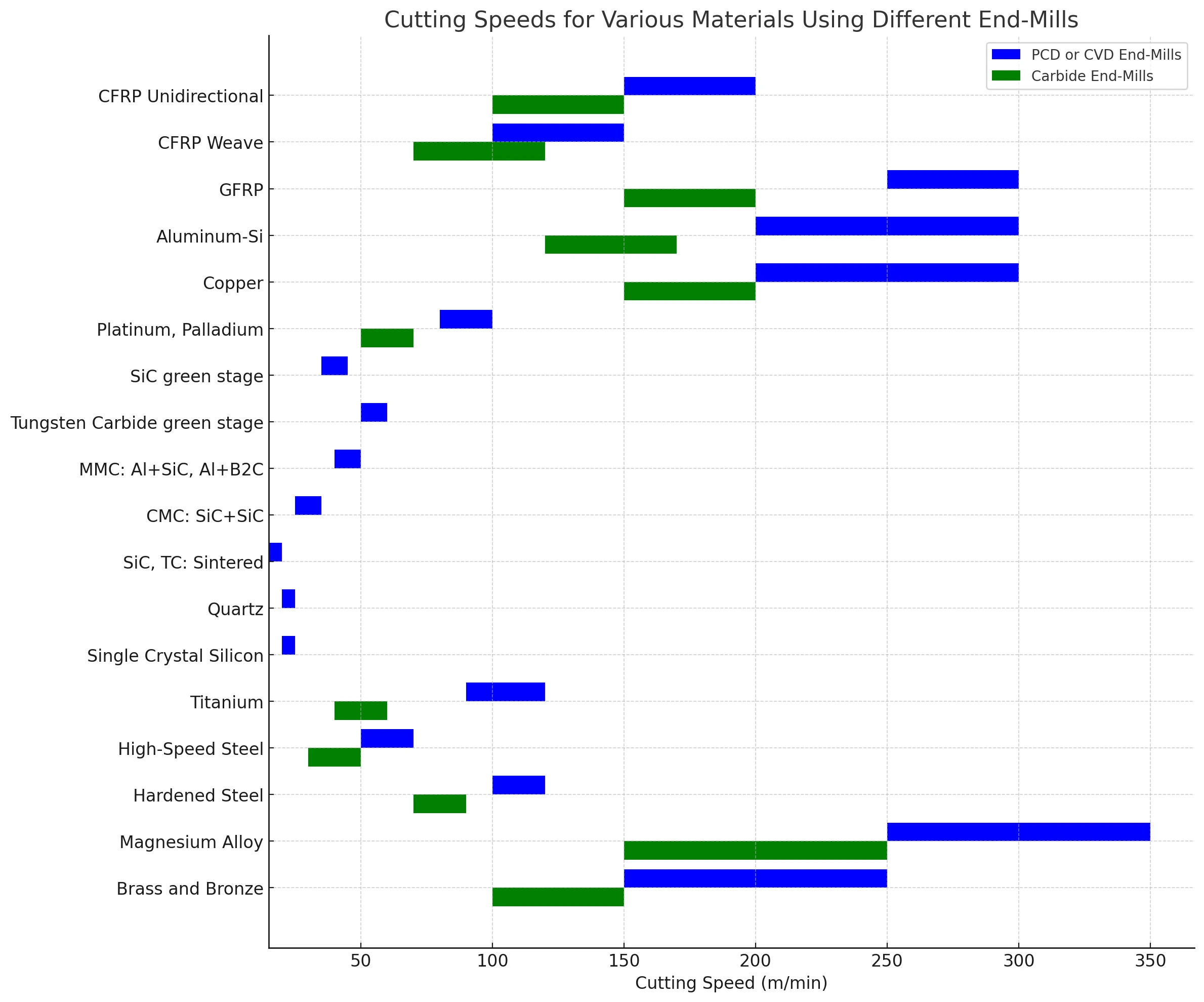
Operating Instructions, Usage, and Data for Polycrystalline Diamond (PCD) Tools
Polycrystalline Diamond (PCD) tools are renowned for their exceptional durability and precision in cutting hard materials. To optimize the performance and longevity of PCD tools, the following comprehensive guidelines and operational instructions should be adhered to. These recommendations serve as a foundational basis for initial settings, which can be finely adjusted based on accumulative experience and specific application needs.
Initial Setup and Calibration
The initial setup and calibration of Polycrystalline Diamond (PCD) tools are crucial steps in ensuring their effective use. Start by referencing the provided tables for initial speed, feed rates, and tool design configurations. These recommendations, developed through extensive testing, cater to various materials and cutting conditions and serve as a foundational starting point.
Install the PCD tool according to manufacturer instructions, making sure it is securely positioned within the tool holder with correct alignment to the workpiece. Adjust machine settings to match the recommended parameters for speed and feed, ensuring the equipment is capable of maintaining these settings consistently.
Perform trial runs using scrap material or a test piece similar to the final workpiece. This practice allows for the observation of the tool's performance under the initial settings and facilitates necessary adjustments without risking valuable materials. During these initial cuts, measure outcomes such as surface finish, dimensional accuracy, and tool wear to evaluate the effectiveness of the settings.
Based on the results of the trial runs, fine-tune the speeds, feeds, and tool configuration. For instance, if the surface finish is not as smooth as required, you might reduce the feed rate or adjust the tool's rake angle to achieve a better finish. Calibration is an iterative process that may require several adjustments to perfect the settings for a specific application.
Keep detailed records of all settings, adjustments, and outcomes for each type of material and tool configuration.
Regular Adjustments for Optimization
For optimal performance and efficiency, regular adjustments and monitoring of Polycrystalline Diamond (PCD) tools are essential. This dynamic approach allows operators to respond to changes in material behavior and cutting conditions, ensuring that the tools are always operating at their best.
As the cutting process unfolds, it's crucial to observe the performance of the PCD tools closely. Factors such as tool wear, surface finish, and the rate of material removal provide critical feedback on the effectiveness of current settings. Over time, materials may behave differently due to variations in composition, hardness, and other physical properties, necessitating adjustments to tool settings.
Adjustments to consider include:
-
Speed Adjustments: Altering the spindle speed can have a significant impact on cutting performance. An increase in speed might be necessary to reduce cutting forces and minimize tool wear, but this must be balanced against the machine's capabilities and the risk of inducing excessive heat or vibration.
-
Feed Rate Modifications: The feed rate controls how quickly a tool advances through the material. Adjusting this rate can improve the efficiency of material removal and influence the quality of the cut. A slower feed rate often enhances finish quality but at the expense of cutting speed. Conversely, increasing the feed rate can boost production throughput, though it may also increase wear on the tool.
-
Cutting Depth Adjustments: The depth of each cut directly affects the load on the tool. Deeper cuts can shorten the machining time but might increase mechanical stresses on the tool and the workpiece. Finding the optimal cutting depth is a balance between efficient material removal and maintaining tool integrity.
The process of making these adjustments should be systematic and based on actual performance data. Utilizing digital tools and machine sensors can provide real-time feedback on forces, temperature, and tool deflection, aiding in making informed decisions.
Moreover, implementing a scheduled review process for all settings on a regular basis—considering both the outputs of the machining process and the condition of the tool—ensures that adjustments are made proactively rather than reactively. This ongoing optimization cycle not only enhances tool performance but also contributes to more predictable and reliable machining operations.
Use of Coolants
The strategic application of coolants is vital in maximizing the efficiency and lifespan of Polycrystalline Diamond (PCD) tools. Coolants play several crucial roles in the cutting process, including managing temperature, lubricating the interface, and flushing away debris. This not only improves the cutting performance but also extends the tool's life by reducing wear.
Coolants help maintain a lower temperature at the cutting interface, crucial for preventing thermal expansion that can affect both the tool and the workpiece. This ensures more precise cuts and better dimensional stability. They also reduce friction between the tool and the workpiece, which not only saves energy but minimizes wear on the tool’s cutting edges, leading to smoother cuts and a finer finish.
During machining, especially in processes like deep-hole drilling or slotting, chips and other debris can accumulate and obstruct the tool's path if not cleared. Coolants are effective in removing these particles from the cutting area, keeping the surface clean and preventing any abrasive wear caused by the debris.
For machining sticky or ductile materials, coolants are essential as they prevent material from adhering to the tool, which could spoil the cutting process and the finish of the workpiece. They also play a key role in extending the tool's usable life by minimizing the thermal and abrasive stresses, which reduces tool costs and downtime for changes, thus enhancing overall productivity.
Choosing the right coolant is crucial and depends on the material and the machining process. Options range from oils to emulsions and synthetic solutions, each designed for specific conditions. Effective management of these coolants, including maintaining their cleanliness and concentration, ensures their performance is optimized throughout their use.
Handling and maintaining Polycrystalline Diamond (PCD) Tools
Handling and maintaining Polycrystalline Diamond (PCD) tools with precision and care is essential to ensure their longevity and maintain their cutting efficiency. PCD tools are exceptionally hard and wear-resistant but can be susceptible to chipping or fracturing if mishandled. Always handle these tools gently, using soft, padded materials to grip them during installation or removal. Avoid dropping or knocking them against hard surfaces to prevent any damage to the cutting edges.
It is crucial to store PCD tools in a designated, clean, and organized environment free from dust, moisture, and other environmental contaminants that could affect their performance. Tools should be kept individually in protective casings or holders that prevent them from touching each other, thus avoiding damage.
Regularly cleaning the tools to remove any build-up of materials or residues is important. This should be done using appropriate cleaning solutions and soft brushes to avoid scratching or damaging the cutting surfaces. Alongside cleaning, routine inspections should be conducted to check for signs of wear or damage such as unusual marks, chips, or blunting. Early detection of these issues allows for timely corrective measures, which might include reconditioning or replacing the tool.
Additionally, it's important to store PCD tools in a controlled environment where temperature and humidity levels are consistently maintained within safe ranges. Extreme temperatures and high humidity can lead to oxidation or other forms of chemical degradation that may weaken the tool's structure.
Ensure that everyone who handles PCD tools is properly trained in safe handling, cleaning, inspection, and storage techniques. Proper training minimizes the risk of accidental damage due to improper handling and ensures that all operators provide consistent care, thus extending the functional lifespan of the tools and optimizing their performance in cutting operations.
Depth of Cut
Depth of cut is a critical factor in machining that directly influences the efficiency and longevity of Polycrystalline Diamond (PCD) tools. Setting the appropriate depth of cut is crucial, as it must be proportional to the size and design of the PCD tool to avoid overloading and potential breakage. The depth should be adjusted to balance material removal efficiency with the mechanical stress exerted on the tool.
The optimal depth varies depending on the type of machining operation, the tool's geometry, and the material being machined. PCD tools, which are often used for hard and abrasive materials, require careful consideration to prevent excessive wear or damage. For harder materials, shallower depths are recommended to mitigate the risk of tool failure, while the tool’s specifications like diameter, thickness, and tip design also dictate the aggressiveness of the cutting conditions.
Balancing cutting efficiency with tool stress is important. Deeper cuts can reduce the number of passes needed, increasing efficiency. However, this also increases the load on the tool, leading to higher temperatures at the cutting edge and faster wear rates. Starting with a conservative depth of cut and then adjusting based on tool performance and wear patterns is advisable.
Adjustments should also be made based on real-time observations of tool performance and workpiece quality. Indicators such as surface finish, chip formation, and the presence of noise or vibration during cutting can guide whether the depth of cut is optimal.
Modern machining centers and computer-aided manufacturing (CAM) software enhance the ability to optimize toolpaths and depths of cut. These technologies can predefine strategies that dynamically adjust the depth of cut, ensuring efficient material removal while extending tool life.
Tool Assembly Cleanliness
Maintaining the cleanliness of the tool assembly is imperative for ensuring the optimal functioning and longevity of Polycrystalline Diamond (PCD) tools. Every component of the tool assembly must be meticulously cleaned and inspected to avoid any contamination that could affect performance. Proper seating and support of the tool are essential for achieving precise cuts and maintaining tool integrity.
Ensuring cleanliness starts with the preparation of each component before assembly. All parts should be thoroughly cleaned using appropriate solvents that remove oils, grime, and any particulates from previous operations. Special attention should be given to the tool holder and spindle interface, as these areas are critical for accurate tool alignment and stability during operation.
After cleaning, components should be dried completely to prevent any moisture from causing corrosion or degradation, especially on critical surfaces that interface with the tool. Using compressed air or clean, lint-free cloths can be effective in removing residual moisture and debris from the assembly parts.
Proper seating of the tool within its holder is crucial for effective cutting. Misalignment can lead to uneven wear, increased strain on the tool, and poor quality cuts. Each component should be inspected for wear or damage before assembly. Worn or damaged parts can compromise the entire tool's functionality and should be replaced or repaired to maintain the precision and efficiency of the tool assembly.
Furthermore, the support mechanisms such as clamps, bolts, and other fasteners should be checked for their integrity. These should be fastened to the manufacturer's specified torque settings to ensure they securely hold the tool during operations without overtightening, which could warp or damage the tool.
Regular maintenance routines should be established to clean and inspect tool assemblies, ideally before and after each use. This includes checking for any signs of wear or buildup of materials that could impact performance
Strategic cutting techniques
Strategic cutting techniques are crucial for maximizing the effectiveness of Polycrystalline Diamond (PCD) tools in various machining operations. Each type of operation requires specific approaches to ensure optimal tool engagement, efficient material removal, and high-quality finishes on machined parts.
In turning operations, it's important to position the cutting edge of the PCD tool on or below the center line of the workpiece. This positioning ensures adequate clearance and prevents the tool from rubbing against the workpiece, which can lead to wear and degrade the finish quality of the part. Properly setting the tool height relative to the center line also improves surface finish and dimensional accuracy.
For boring operations, adjusting the cutting to occur on or above the center line of the bore enhances the cutting action and enables more efficient material removal. This setup allows the tool to exert a more effective cutting force, leading to smoother bore surfaces and more accurate hole diameters.
Climb milling is particularly advantageous for milling operations with PCD tools. This method involves feeding the workpiece into the cutter in the same direction as the cutter's rotation, which exerts a downward force on the material, keeping the tool in compression—its strongest state. This technique reduces the cutting forces on the tool, minimizing tool deflection and vibration, which in turn extends tool life and improves the surface finish of the milled part.
Adjusting feed rates and cutting speeds is also crucial across all operations to tailor the process to the material's hardness and specific requirements of the operation, leveraging the unique properties of PCD tools. Effective chip control is vital, especially in turning and milling, where poor chip evacuation can interfere with the cutting process and potentially damage the tool or workpiece. Employing chip breakers, optimizing coolant flow, and using high-pressure air or coolant jets for chip evacuation can significantly enhance the machining process.
Furthermore, optimizing the tool path can reduce the number of tool passes required, minimize tool wear, and improve overall process efficiency. Advanced CAD/CAM software can be particularly useful in planning and simulating tool paths to allow for adjustments before actual machining begins.
Optimizing Speeds for Reduced Cutting Forces
Optimizing the operating speeds of machining tools is a critical strategy for enhancing performance and extending tool life, particularly when using Polycrystalline Diamond (PCD) tools. Implementing higher speeds can significantly reduce the cutting forces exerted on the tool, which in turn minimizes wear and tear and improves the quality of the cut.
When a machining operation is conducted at higher speeds, the cutting forces involved are often reduced. This reduction in force is due to the fact that higher speeds can smooth the cutting process, leading to less resistance between the tool and the material. As a result, there is less stress on the tool, which helps to prevent premature tool wear and potential breakage.
However, it is crucial to ensure that the machinery used is capable of handling these higher speeds. The equipment must have sufficient power and rigidity to maintain precision at increased speeds. Machines with high-speed capabilities are typically designed to withstand the dynamic forces and vibrations associated with such operations, ensuring that the quality of machining is not compromised.
Additionally, when operating at higher speeds, it's important to consider the thermal effects on both the tool and the workpiece. High-speed machining can generate significant heat, which, if not properly managed, can affect the tool's performance and the material properties of the workpiece. Implementing adequate cooling systems, such as high-pressure coolant jets, can help dissipate heat effectively, preserving the integrity of the tool's cutting edge and the dimensions and finish of the workpiece.
Moreover, to fully benefit from high-speed machining, it may be necessary to adjust other parameters such as feed rate and depth of cut. These adjustments should be made based on the specific material being machined and the desired outcome of the operation. For example, increasing the speed might require adjustments in the feed rate to optimize material removal rates and achieve the best surface finish.
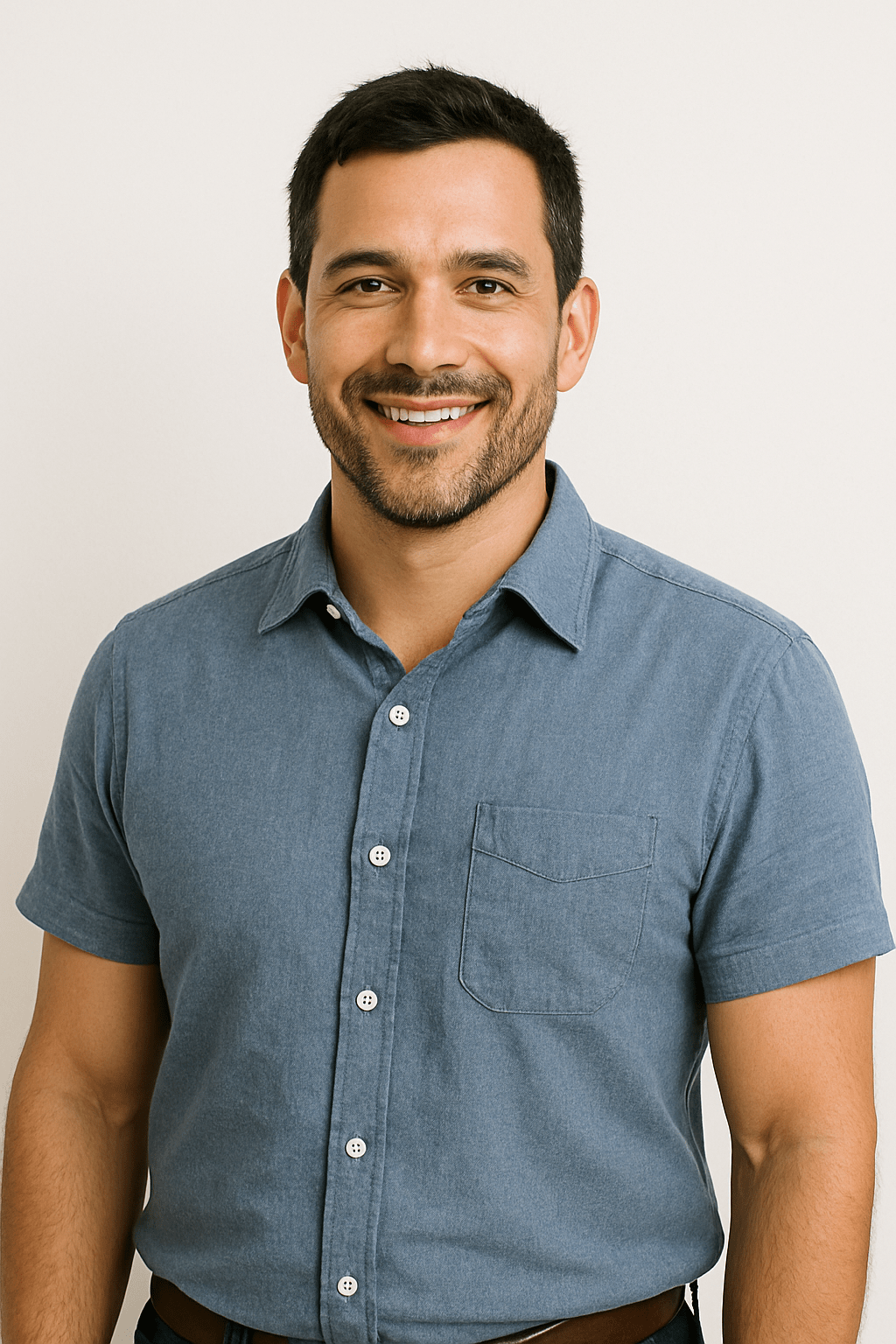
Carlos Sanchez is a senior technical specialist and field applications trainer with more than 17 years of experience in the use and optimization of industrial diamond tools, including ultra-thin diamond blades, core drills, and CBN grinding wheels. With a foundation in industrial engineering and technical operations, Mr. Sanchez has worked extensively with manufacturers and laboratories around the world, providing hands-on support and practical training for a wide range of cutting, grinding, and sample preparation applications.
Fluent in both English and Spanish, Carlos is known for his ability to translate complex tooling concepts into clear, actionable procedures for engineers, technicians, and production staff. His approach emphasizes real-world process improvement, tool longevity, and operator education—ensuring clients get the most out of their diamond tooling investments.
As an author, Mr. Sanchez shares field-tested insights on tool performance optimization, defect prevention, training methodologies, and troubleshooting common cutting issues.
ARE YOU USING RIGHT PCD Diamond & CBN TOOLs
FOR YOUR APPLICATION?
LET US
HELP YOU
HAVING ISSUES WITH
YOUR CURRENT PCD Diamond & CBN Tools?
Knowledge Center
How to Selecting Right Diamond Tools for your application
How to properly use Diamond Tools
Why use diamond
Diamond vs CBN (cubic boron nitride) Tools
What is Diamond Mesh Size and how to select best one for your application
What is Diamond Concentration and which to use for your application
What is Chemical Vapor Deposition and its application
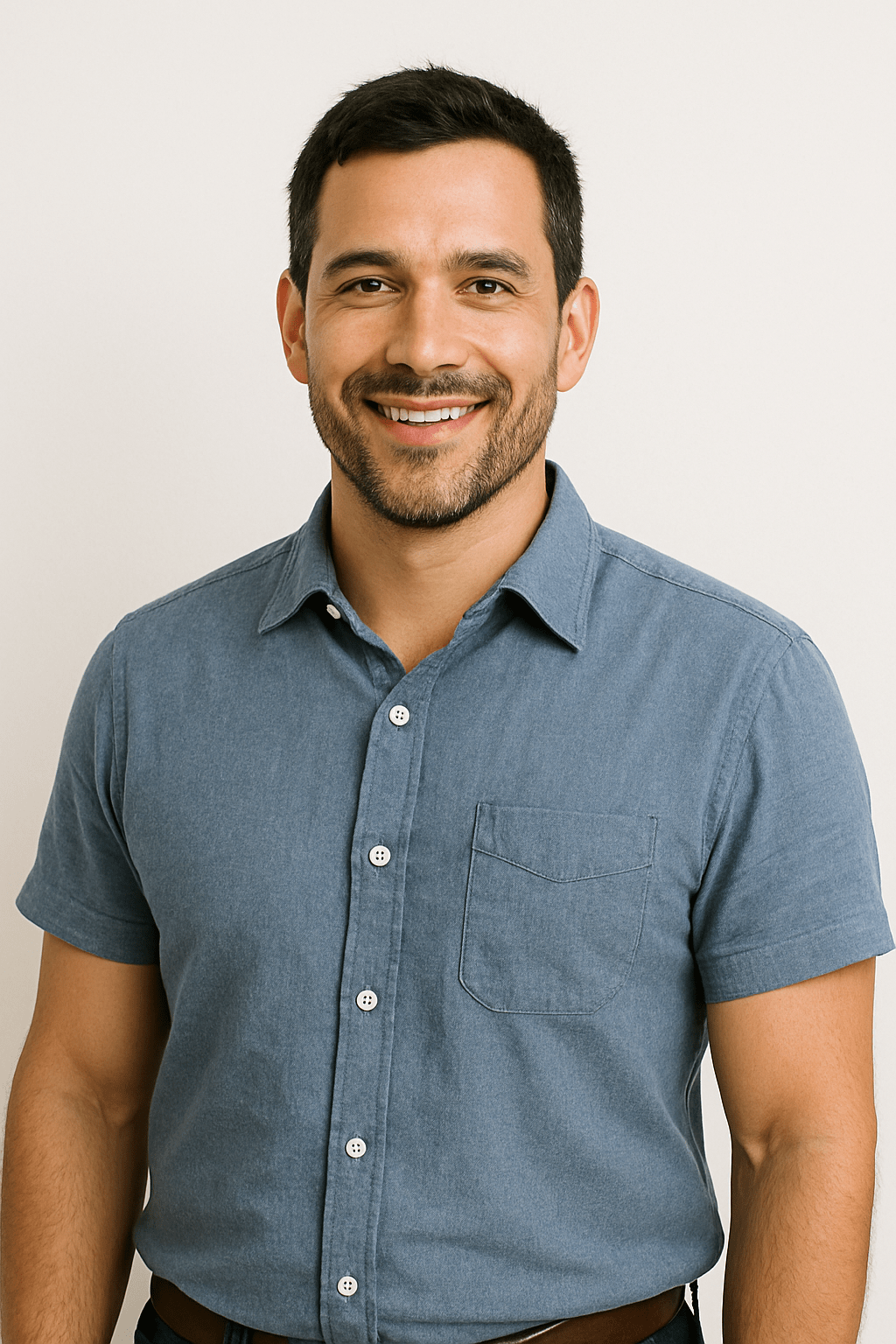
Carlos Sanchez is a senior technical specialist and field applications trainer with more than 17 years of experience in the use and optimization of industrial diamond tools, including ultra-thin diamond blades, core drills, and CBN grinding wheels. With a foundation in industrial engineering and technical operations, Mr. Sanchez has worked extensively with manufacturers and laboratories around the world, providing hands-on support and practical training for a wide range of cutting, grinding, and sample preparation applications.
Fluent in both English and Spanish, Carlos is known for his ability to translate complex tooling concepts into clear, actionable procedures for engineers, technicians, and production staff. His approach emphasizes real-world process improvement, tool longevity, and operator education—ensuring clients get the most out of their diamond tooling investments.
As an author, Mr. Sanchez shares field-tested insights on tool performance optimization, defect prevention, training methodologies, and troubleshooting common cutting issues.