Table of Contents
ToggleWhat is Diamond Grit Size?
In the United States, the mesh size used to classify diamond grits corresponds to the number of sieve meshes per linear inch. This means that a higher mesh number indicates finer diamond grits, characterized by smaller particles, whereas lower numbers signify coarser grits, consisting of larger particles. This system is crucial for categorizing diamond particle sizes which typically range in diameter from less than 1 millimeter—often too small to be seen unaided by the human eye—to the consistency of beach sand.
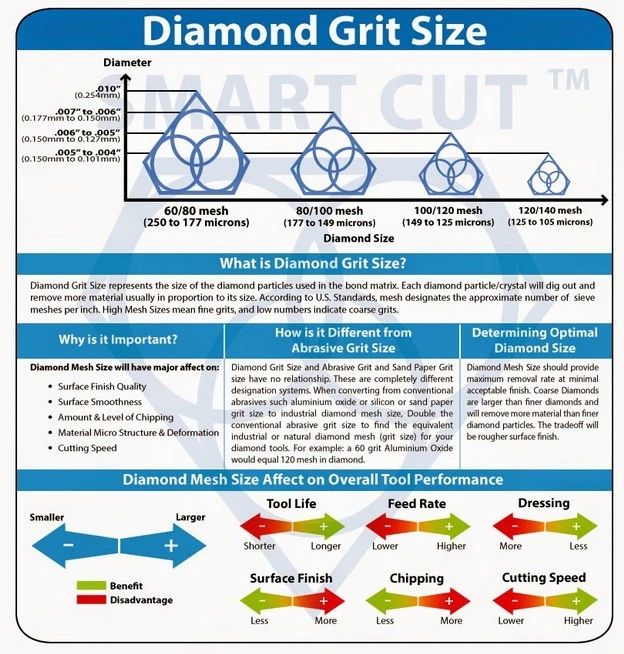
Diamond Particle Size and Material Removal Efficiency
Each diamond particle or crystal acts as a cutting tool in itself, removing material from a workpiece in proportion to its size. Larger diamond particles or crystals remove more material, leading to faster cutting rates but rougher surface finishes. Conversely, smaller diamond particles achieve slower material removal rates but can produce finer, smoother surface finishes. This differentiation is significant in applications where the precision of the finished surface is critical.
Range of Diamond Crystal/Particle Sizes
Diamond crystals or particles are available in a wide range of sizes, from as large as 16/20 mesh (about 1,000 microns) down to as small as 10 nanometers. The size range includes everything from visibly large particles to those that require advanced microscopy for detection.
Classification of Diamond Grits for Industrial Use
For industrial applications, diamond particles are often categorized into two broad bands of grit sizes commonly referred to as "saw grits" and "wheel grits." Saw grits are typically larger and used in applications requiring rapid material removal, such as in sawing or rough cutting operations. Wheel grits are generally finer and used in precision grinding and polishing applications.
The sizing of diamond particles larger than 40 microns is generally performed using sieves. These sieves consist of cross-woven metal wires, usually stainless steel, which create numerous square holes. The process involves placing diamond crystals on the sieve and shaking or vibrating them for a fixed period. This action allows the particles to bounce around and pass through the holes based on their size.
Sieving Process and Grit Band Classification
The sieving system is arranged with the mesh having the largest apertures at the top and the smallest at the bottom. As the diamond crystals are sifted, they are divided into two portions: those that pass through the holes and those that remain on the screen. Consequently, each diamond particle or grit size is narrowed down to a specific band, defined by two sieve aperture sizes (top and bottom). This band indicates the range of particle sizes for each classified grit, ensuring that each fits within specified tolerances for their intended industrial use.
How to Determine Diamond Mesh/Grit Size?
Determining the diamond mesh or grit size involves understanding the method by which these measurements are taken. Mesh size is typically defined by counting the number of openings in one inch of a screen. For example, a 100 mesh screen means there are 100 openings across one linear inch of screen, and a 120 mesh screen has 120 openings, and so on. As the mesh number increases, the size of the openings and the particles that pass through them decreases. However, mesh sizing is not an extremely precise form of measurement due to variations in wire thickness used in the screen of the sieve, which can slightly alter the size of openings.
For diamond grit sizes smaller than 40 microns, traditional sieving becomes less effective due to the reduced size of the particles. At this point, more precise methodologies such as laser diffraction and scanning electron microscopy (SEM) are employed. These methods allow for accurate measurement of very small particles, which is crucial for applications requiring a high degree of precision.
The mesh design implies that as the weave gets finer, the wires come closer together, eventually leaving virtually no space between them. This factor is critical in very fine mesh sizes used for polishing and finishing applications where consistency and precision are vital. Additionally, many manufacturers characterize diamond grit sizes by particles per carat count, which ensures a consistent number of particles per carat, providing a strict tolerance for each mesh size. This ensures a high degree of consistency in performance.
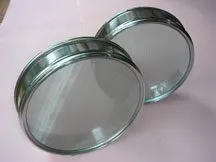
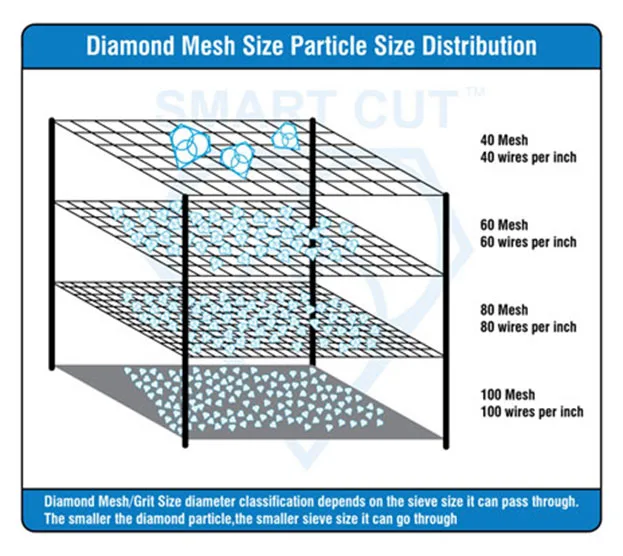
The standards for mesh sizes differ between the US and Europe. The American system, governed by ANSI standards, is based on the number of holes per inch of the screen. This system uses a direct scale where a higher mesh number indicates smaller particle sizes. Conversely, the European system, governed by FEPA standards, uses the average diameter in microns of the particles to define mesh size. Thus, a larger micron designation indicates coarser particles, opposite to the American system.
For example, in the American system, a 60 mesh indicates coarser and larger/blocky diamond particles compared to a 220 mesh, which would be used for finer, more detailed work. In the European system, a particle size of 160 microns would be used for quicker, rougher cutting tasks, whereas a 40-micron size would be better suited for finishing tasks requiring finer cuts.
When selecting diamond grit for a specific application, it's crucial to consider the material to be processed and the desired outcome. Coarser grits (lower mesh numbers in the US system or higher micron numbers in the European system) are effective for rapid material removal and initial shaping. They are typically used in the early stages of a process where speed is more critical than the finish.
Finer grits are used for detailed work and finishing because they create a smoother surface on the material. They are essential in applications requiring a high-quality finish, such as in fine jewelry making or precise optical work.
Understanding Diamond Grit Size Designation Range & Distribution
Diamond grit size is a critical factor in the performance of diamond tools, and it is commonly specified by a range, such as 60/80 mesh. This designation indicates that the majority of diamond particles fall between the 60 mesh and 80 mesh size range, with 70 mesh often being the average particle size. Understanding this designation and the distribution of particle sizes within a specified range is crucial for selecting the appropriate diamond tool for specific applications.
Mesh Size and Particle Distribution:
Designation by Range: The range notation, such as 60/80 mesh, means that the majority of diamond particles are sized between the sieves for 60 mesh and 80 mesh. The number represents the number of holes per inch in the sieve screen, so a 60 mesh screen has 60 openings per inch, and an 80 mesh screen has 80 openings per inch.
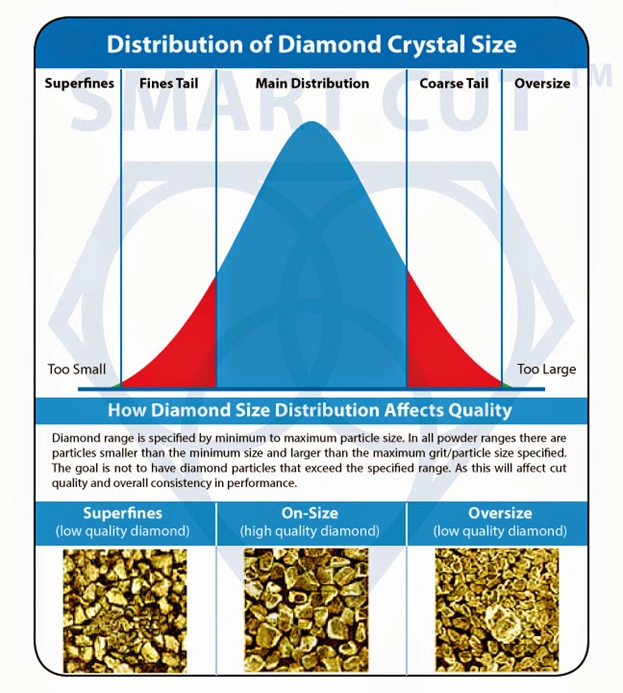
Mean Size: The mean, or average, size of the particles in this range typically centers around the midpoint. In the example of 60/80 mesh, the mean would be close to 70 mesh.
Usage of "+" and "-" in Mesh Size Description:
"+" Indicator: The "+" before a mesh size, such as +70 mesh, indicates that the particles are retained by the 70 mesh sieve. This means that these particles are larger than the mesh opening size of the 70 mesh sieve.
"-" Indicator: Conversely, the "-" before a mesh size, such as -70 mesh, indicates that the particles pass through the 70 mesh sieve, meaning they are smaller than the openings in that sieve.
Particle Size Consistency:
90%+ Particle Consistency: Typically, when a range is specified, over 90% of the particles will lie within the indicated range. For example, with a designation of -10 / +30 mesh, more than 90% of the particles will pass through a 10-mesh sieve (indicating they are smaller than 2.0 mm) but be retained by a 30-mesh sieve (indicating they are larger than 0.595 mm).
Single Mesh Designation: If the material is described with a single mesh indicator like -30 mesh, it implies that 90% or more of the particles will pass through a 30-mesh sieve, thereby being smaller than 0.595 mm.
Selection for Specific Applications:
The selection of diamond grit size based on mesh designation is essential for achieving desired outcomes in cutting, grinding, or polishing operations. For example, coarser grits (larger particles, lower mesh number) are typically used for rapid material removal in rough cutting operations. In contrast, finer grits (smaller particles, higher mesh number) are used for detailed and finish work where a smooth surface finish is required.
Manufacturers of diamond tools use these designations to formulate tools that can deliver the right balance between cutting speed and surface finish, ensuring that the tools are optimally matched to the application.
Understanding and controlling the particle size distribution within a designated range is crucial for tool manufacturers to ensure consistent tool performance. This consistency is vital for applications requiring high precision, such as in the semiconductor or fine jewelry industries, where even minor deviations in tool performance can significantly affect the quality of the final product.
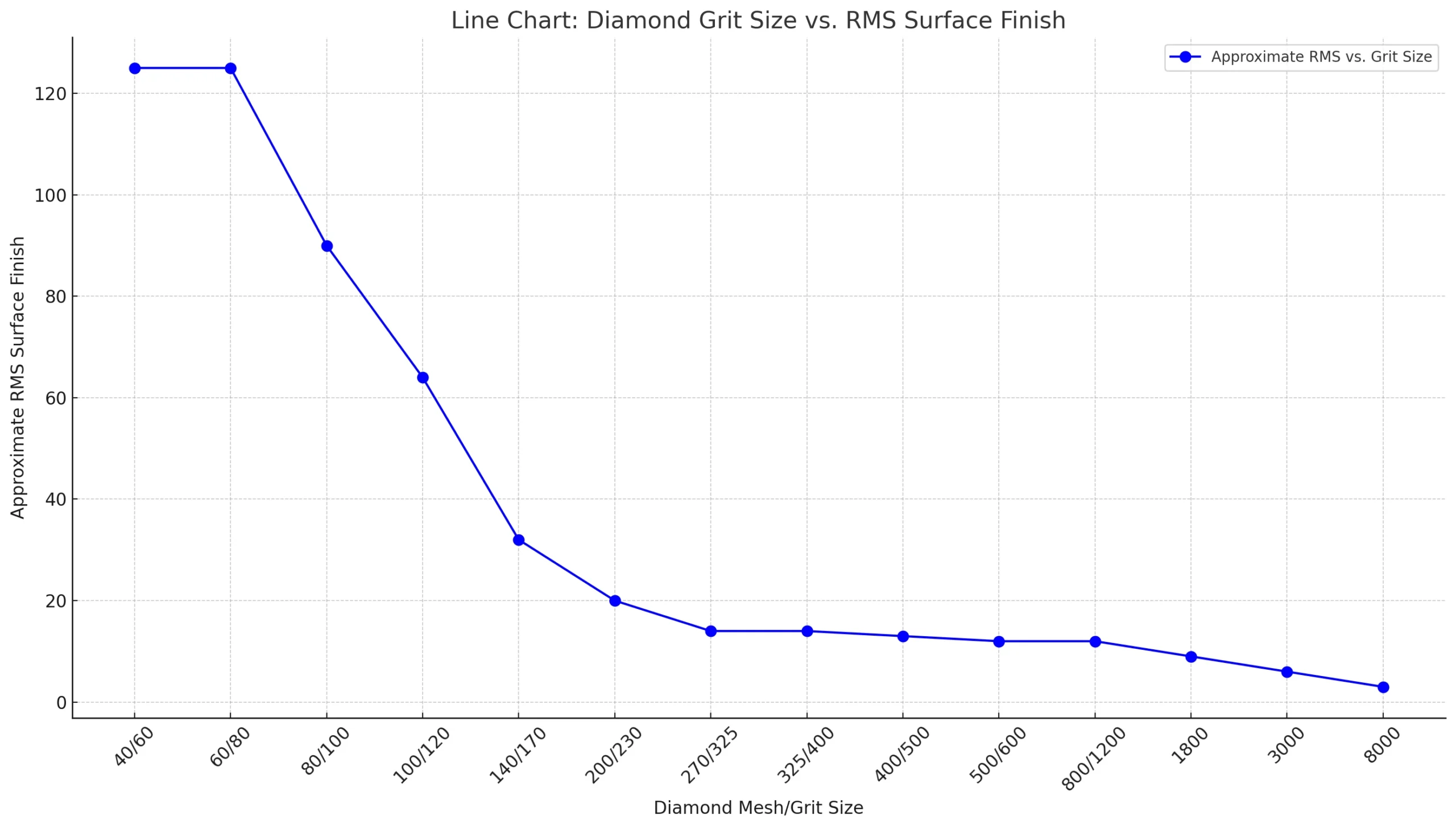
Diamond Definition |
Diamond Mesh/Grit Size |
Diamond Micron Size |
Recommended Application |
Approximate RMS |
---|---|---|---|---|
Saw Grit |
40/60 |
297 |
Sawing |
125-200 |
Super Course |
60/80 |
213 |
Roughing (Heavy Stock Removal) |
125-150 |
Large Course |
80/100 |
163 |
Medium Roughing |
90-125 |
Course |
100/120 |
137 |
Semi Roughing (Semifinish Drilling) |
64-90 |
Medium |
140/170 |
97 |
Rough Finishing (Finish |
32-48 |
Fine |
200/230 |
68 |
Finishing |
20-24 |
Extra Fine |
270/325 |
49 |
Fine finishing |
14-16 |
Super Fine |
325/400 |
47 |
Extra finishing |
14-15 |
45 Microns* |
400/500 |
45 |
Super finishing |
13-14 |
30 Microns* |
500/600 |
30 |
Polishing |
12 |
15 Microns* |
800/1200 |
15 |
Polishing |
12 |
9 Microns* 8/10 6/12 |
1,800 |
9 |
Polishing |
|
6 Microns* 4/8 |
3,000 |
6 |
Fine polishing |
|
3 Microns* |
8,000 |
3 |
Extra polishing |
|
What is the Difference Between Coarse, Medium, and Medium Size Diamond Grit Size?
Coarser and finer diamond grit sizes each play distinct roles in the performance of diamond tools across various industrial applications. Adding medium-sized grits to this spectrum provides a more nuanced understanding of how each size range can be optimized for specific materials and desired results.
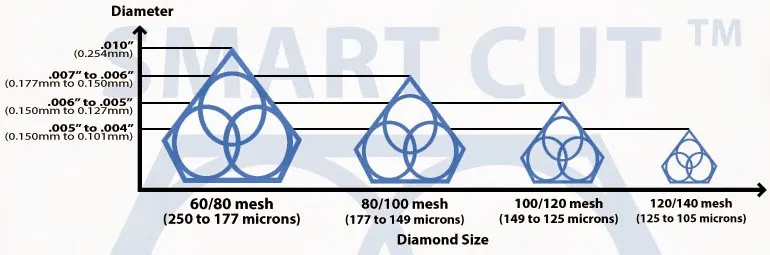
Coarser Diamond Grit Sizes: Typically ranging between 20 mesh to 120 US mesh (300 to 120 microns FEPA), coarser diamond grits are characterized by their ability to protrude significantly from the bond matrix. This protrusion allows them to cut into materials more aggressively, which is particularly beneficial for applications requiring rapid material removal. The large size of these grits enhances clearance, facilitating easier ejection of swarf (waste material), especially when substantial material needs to be removed per tool revolution. This not only speeds up the cutting process but also extends the lifespan of the tool due to the reduced wear and tear compared to finer grits. Coarser grit sizes are often preferred in situations where speed takes precedence over the quality of the finish, such as in the initial stages of stone cutting or rough sculpting.
Medium Diamond Grit Sizes: Sitting between the coarser and finer grits, medium diamond grit sizes generally range from 150 to 220 US mesh (160 to 240 microns FEPA). These grit sizes offer a balance between aggressive material removal and finer finishing. They are particularly useful in applications where both aspects are critical, providing a compromise that allows for efficient material removal with a moderate level of surface finish. Medium grits are versatile and commonly used in transitional stages of machining processes, where they prepare surfaces for final finishing or serve as the primary tool in moderate roughing applications. They are often employed in the fabrication of parts that require a good surface finish without the need for the ultra-smooth results provided by finer grits.
Finer Diamond Grit Sizes: Ranging from 220 to 600 US mesh (240 to 600 microns FEPA), finer diamond grits are essential for applications demanding high precision and an excellent finish. Their smaller size allows for a more controlled and delicate approach to cutting, making them ideal for tasks where surface integrity and aesthetics are paramount. These grit sizes are crucial for the final polishing phases in gemstone processing, precision optics manufacturing, and fine metal finishing. Finer grits ensure a high-quality finish by smoothing surfaces to a high degree and are indispensable in industries like electronics, where they are used for precision cutting of delicate semiconductor materials.
Diamond Grit Size Range |
Application Example |
---|---|
20/30 Mesh |
Diamond sawing and drilling of very abrasive materials. Such as sandstone, concrete, asphalt. Drilling of Reinforced concrete, frame sawing of abrasive sandstone |
30/40 mesh |
Diamond sawing and drilling of stone, concrete, reinforced concrete and asphalt. Frame sawing of abrasive sandstone |
40/50 mesh |
Diamond sawing, drilling and milling of stone (granite, diorite, gabbro, less abrasive sandstone, limestone, dolomite, marble), concrete and refractoriness; wire sawing of stone and construction materials; calibrating of stone slabs |
50/60 mesh |
Diamond sawing and drilling of very hard fine grained igneous stone (granite, grandodiirte) and refractoriness. circular sawing frame sawing and drilling of fine grained sdimentary and metamorphic stone (limestone, barble. Calibrating of stone slabs |
60/80 mesh |
Diamond sawing, drilling and milling of glass, calibrating of ceramic tiles |
This illustration is a "Diamond Mesh Size Application Chart" which serves as a reference for selecting the appropriate diamond mesh size based on the desired application and finish. Here's a breakdown of each column in the chart:
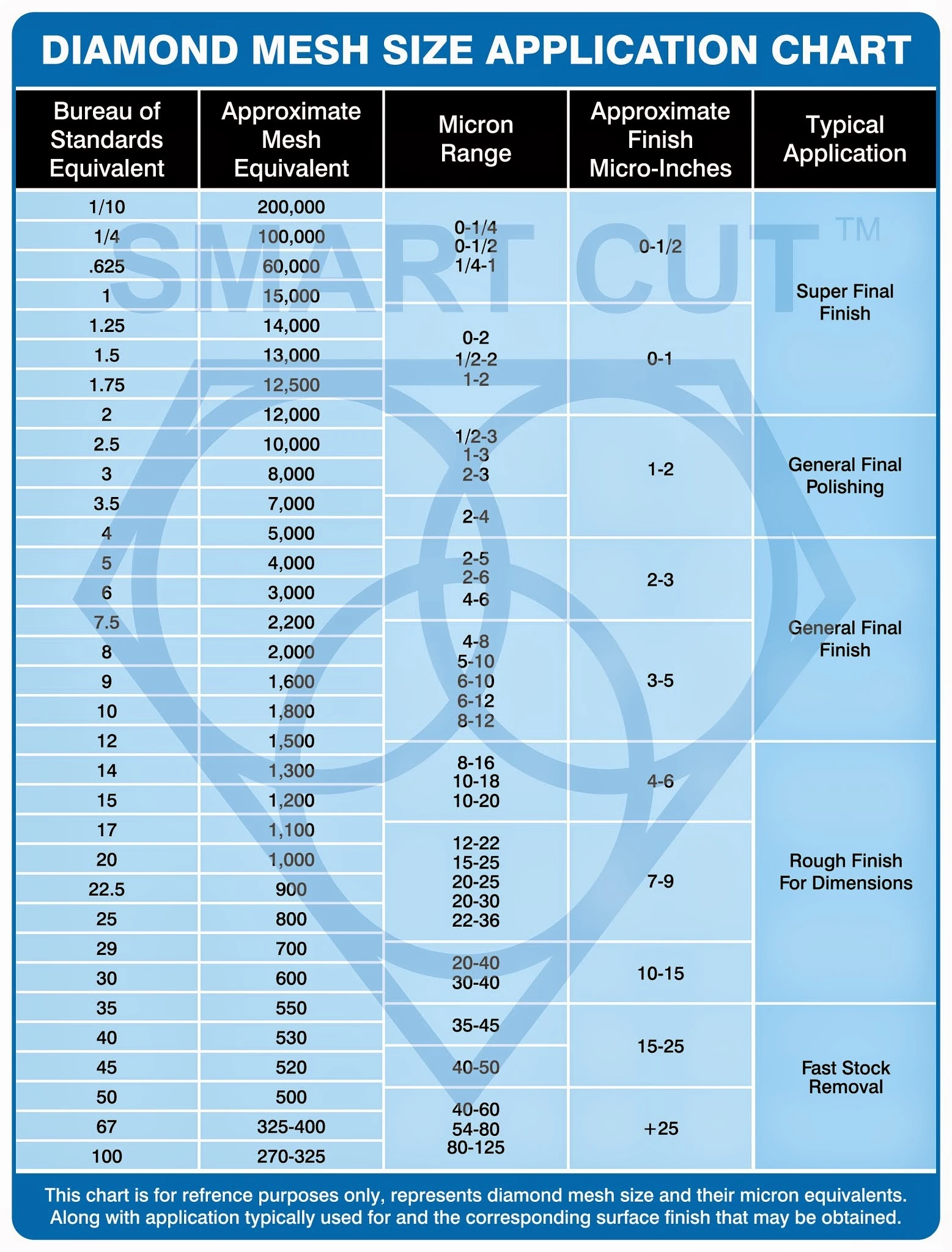
-
1. Bureau of Standards Equivalent: This column represents a standardized scale for grading the size of diamond grains. The numbers decrease as the grain size becomes finer.
-
2. Approximate Mesh Equivalent: This column indicates the mesh size, which refers to how many holes per inch in a standard screen, corresponding to the diamond grain size. A higher number indicates smaller, finer grains.
-
3. Micron Range: This shows the range of particle sizes in microns for each mesh size. A micron is one-millionth of a meter. This column is crucial for understanding the exact size range of the diamond particles.
-
4. Approximate Finish Micro-Inches: This column provides a rough estimate of the surface finish that can be achieved with each mesh size, measured in micro-inches. A lower number here indicates a smoother finish.
-
5. Typical Application: The last column lists the typical applications for each mesh size, ranging from "Super Final Finish" for very fine particles to "Fast Stock Removal" for coarser grains.
How to Select the Right Diamond Grit Size
Selecting the right diamond grit size is a nuanced process that involves balancing efficiency and quality to meet specific application needs. This choice affects both the cutting speed and the surface finish, which are essential for achieving optimal performance in various industrial settings.
The optimal diamond grit size should facilitate maximum material removal while maintaining a minimal acceptable finish. Achieving this balance is crucial because a very coarse grit might remove material quickly but could leave a rough surface that might be unsuitable for the final application. Conversely, a very fine grit, while providing an excellent finish, might slow down production unacceptably.
In many scenarios, especially where a high-quality finish is required, achieving the desired surface cannot be accomplished in a single step. Instead, a multi-stage process is often necessary, starting with a coarser grit to quickly remove the bulk of the material. Subsequent steps involve progressively finer grits to refine the surface to the desired quality. Additional finishing operations such as lapping or polishing may be required to achieve the final surface quality. This sequential approach is typical in industries like gemstone polishing, precision optics, and high-specification metal fabrications.
The definition of what constitutes a "coarse" or "fine" diamond grit size varies significantly across different industries due to varying material properties and final product requirements. For example, the semiconductor and optics industries typically need very fine grit sizes because any surface imperfections directly impair functionality. Conversely, in natural stone and metal fabrication, coarser grits may be adequate for initial cutting and shaping, with finer grits reserved for final surface finishes.
The choice of grit size is also influenced by the type of diamond bond and the specific tool used. Various bonding matrices—such as sintered or metal bond, resin bond, nickel bond, and brazed bond—differ in their grit retention and wear resistance, which impacts grit performance under different conditions. Moreover, the type of tool—whether a cut-off blade, grinding wheel, core drill, or router—also dictates the appropriate grit size. For example, a diamond saw used for cutting concrete can use a much coarser grit than a diamond drill used for making precision holes in glass or ceramics.
What is considered too coarse for one application may be too fine for another. The appropriate grit size for cutting through a thick piece of natural stone might be entirely unsuitable for delicate processes like semiconductor wafer fabrication, where even microscopic irregularities can lead to defective components.
Material Hardness:
Soft Materials:For softer materials such as aluminum, soft ceramics, plastics, soft woods, and certain composites, using larger diamond grit sizes (lower mesh number, such as 20-60 mesh) is often effective. These larger particles allow for more aggressive cutting action, necessary to quickly remove material without excessive pressure. This results in faster task completion and reduced risk of clogging. The aggressive cutting provided by larger grits allows tools to operate at higher speeds without bogging down, which is beneficial in industries like woodworking or in rapid prototyping with softer materials. Tools designed for softer materials typically feature deeper diamond impregnation and specific bond matrices that ensure the diamonds are held firmly but still exposed enough to cut efficiently.
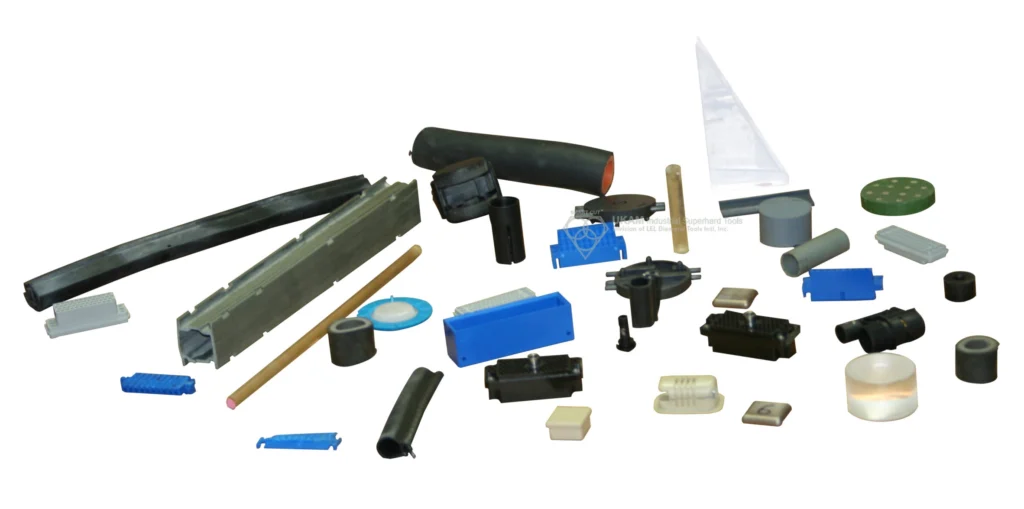
The relationship between diamond grit size and cutting speed is a fundamental aspect to consider when selecting the right tool for specific applications. Larger grit sizes are capable of removing material more rapidly, which naturally leads to increased cutting speed. This trait is particularly advantageous in scenarios where speed is prioritized over the quality of the finish. Such conditions are often found in bulk material removal tasks or in rough cutting stages where the primary objective is to quickly shape the material rather than achieve a refined surface.
Hard Materials: In contrast, hard materials such as hardened steel, sapphire, tungsten carbide, high-performance ceramics, and certain types of glass require smaller diamond grit sizes (higher mesh number, such as 100-300 mesh). The finer grit allows for more controlled and precise cutting, which minimizes substrate damage and ensures high-quality finishes. When cutting hard materials, smaller diamond particles work by slowly grinding away the material rather than chipping it away. This requires more patience and control but results in higher precision cuts, which is crucial in manufacturing precision engineering components, optical parts, and intricate jewelry designs. Tools for harder materials are often constructed with a harder bonding material to hold the diamond grit more securely, helping maintain the sharpness of the cut and prolonging the tool's life by reducing diamond pull-out.
Optimization Strategies: Some cutting tasks may benefit from multi-grit strategies or using tools that incorporate multiple grit sizes. Varying the grit along a single tool, such as a saw blade or a grinding wheel, can combine aggressive material removal with a finer finish. Innovations in tool manufacturing often involve creating hybrid tools that feature different types of diamond grits or combining diamond grits with other abrasive materials to optimize cutting performance for specific applications.
Cutting Speed:
The relationship between diamond grit size and cutting speed is a fundamental aspect to consider when selecting the right tool for specific applications. Larger grit sizes are capable of removing material more rapidly, which naturally leads to increased cutting speed. This trait is particularly advantageous in scenarios where speed is prioritized over the quality of the finish. Such conditions are often found in bulk material removal tasks or in rough cutting stages where the primary objective is to quickly shape the material rather than achieve a refined surface.
However, this increase in speed with larger grit sizes comes with the potential downside of compromising the smoothness of the finished surface. The coarser grits might leave a rougher texture, which could be undesirable or even problematic in applications where the aesthetic or functional quality of the surface is critical.
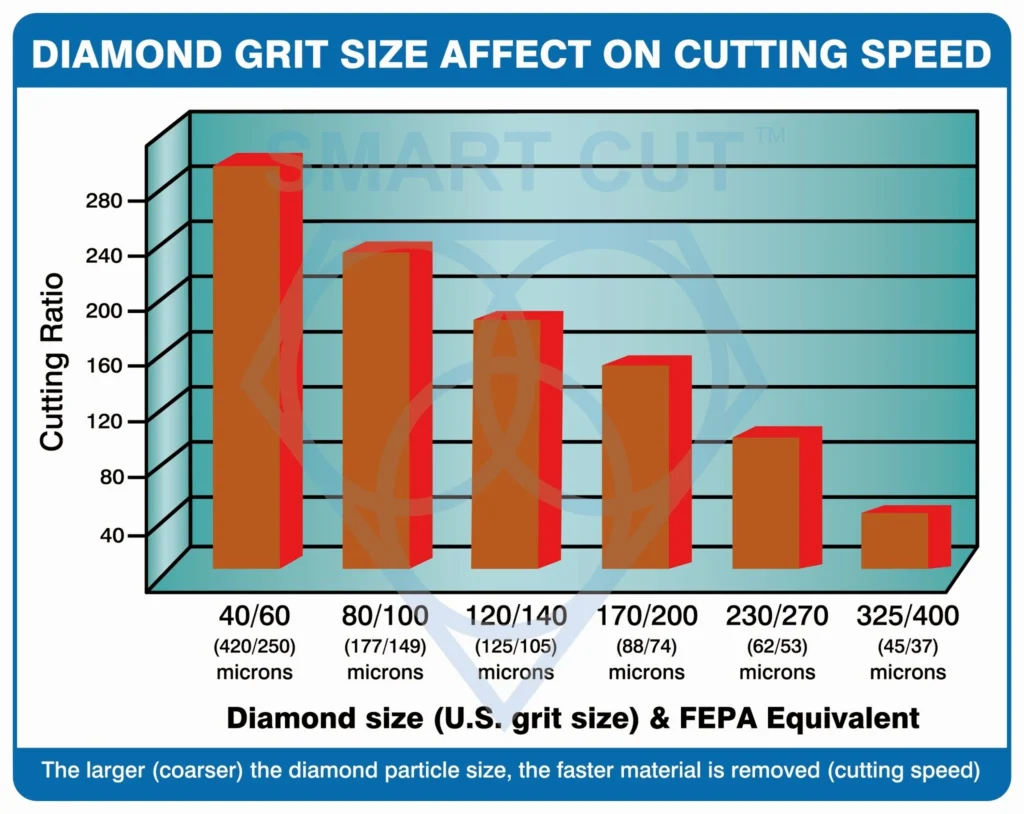
On the other hand, smaller grit sizes offer a contrasting set of advantages and drawbacks. While they tend to reduce the cutting speed due to their finer cutting action, they significantly enhance the quality of the cut. The finer grits achieve this by creating a smoother finish on the surface, making minute, controlled cuts that minimize damage to the material. This precision is essential in applications that demand high accuracy and minimal surface damage, such as in the finishing stages of fine jewelry or in the manufacturing of precise optical components.
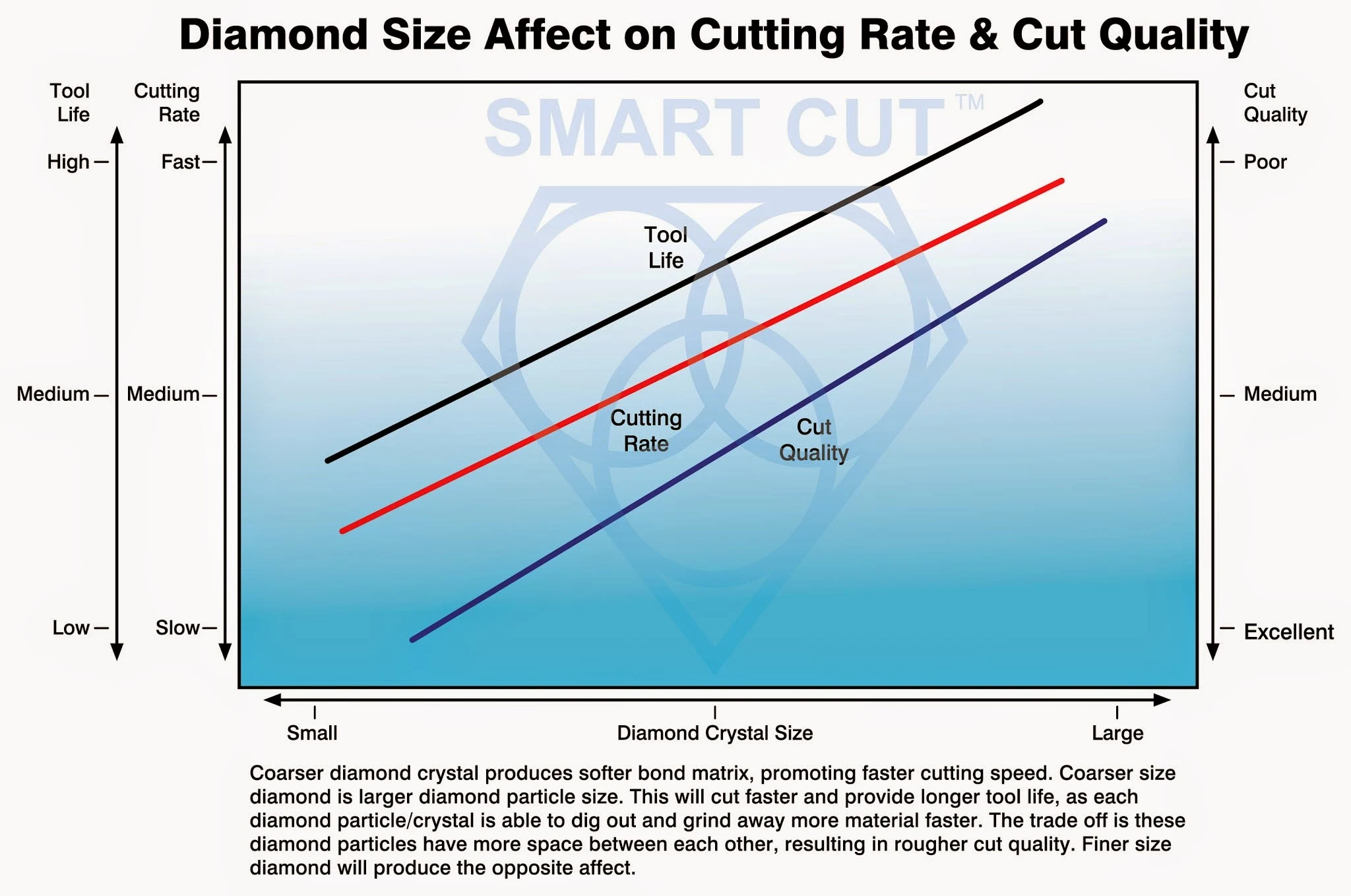
1. Axes:
-
Vertical axis on the left: Represents the cutting rate, with "Fast" at the top and "Slow" at the bottom.
-
Horizontal axis at the bottom: Indicates the diamond crystal size, ranging from "Small" to "Large".
2. Lines
-
Red line: Represents tool life. It shows that as the diamond crystal size increases, the tool life also increases, meaning that tools with larger diamond particles last longer.
-
Blue line: Indicates cutting rate. This line illustrates that larger diamond crystals can cut faster, hence the cutting rate increases as the crystal size grows.
-
Purple line: Depicts cut quality. This line shows an inverse relationship, where smaller diamond crystals lead to better (excellent) cut quality, and larger crystals result in poorer cut quality.
Surface Finish Requirements:
Understanding the impact of diamond grit size on surface finish requirements is crucial for selecting the right tool for a specific application. The choice of grit size significantly influences the nature of the finish on the material being processed, which can range from rough to ultra-smooth.
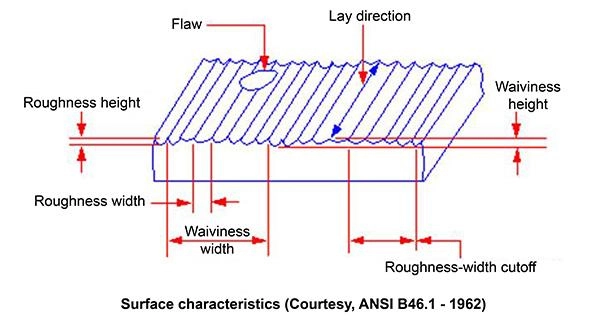
Rough Finishes: When a rough finish is acceptable or desired, larger grit sizes are typically employed. These coarser grits are effective in rapidly removing material, which is particularly useful in the initial stages of cutting, shaping, or bulk material removal. In such scenarios, the priority is more on efficiency and speed rather than on achieving a fine surface quality. Larger grit sizes, with their aggressive cutting action, can significantly expedite these processes but at the expense of leaving a rougher surface texture. This is often seen in the construction industry, during the initial cutting of stones or concrete, where the final finish is not the primary concern.
Smooth Finishes: Conversely, for applications where a high-quality, smooth finish is crucial, finer grit sizes are indispensable. These smaller grits make more delicate cuts, which smoothens the surface and reduces imperfections. This finer approach is essential in fields such as optics, where the clarity and precision of lenses and mirrors must meet strict specifications to function correctly. Similarly, in the jewelry industry, achieving a high polish on precious metals and gems is vital for aesthetic appeal and craftsmanship quality. Using finer grit sizes not only enhances the appearance of these materials but also reduces the need for extensive subsequent finishing processes. The smoother surface created with finer grits minimizes the steps required in polishing and finishing, thus saving time and resources while ensuring that the end products meet the high standards expected in these industries.
Tool Lifespan and Wear:
The relationship between diamond grit size and tool lifespan and wear is a critical consideration in the selection of diamond tools. This aspect influences both the cost-effectiveness and efficiency of operations, as the longevity and durability of tools directly impact production timelines and maintenance costs.
Larger Grit Sizes and Tool Wear: Using larger grit sizes can lead to quicker tool wear, especially under conditions where the tool faces high resistance or is used on very hard materials. Larger diamond particles are more aggressive in their cutting action, which allows them to remove material more quickly. However, this aggressive removal tends to exert greater stress on both the diamond particles and the tool matrix. In situations where the material being cut is particularly hard or abrasive, the larger grits can become dislodged or fractured, thereby reducing the effectiveness of the tool and increasing the frequency of tool replacement or maintenance. This can be particularly problematic in industries where tools must operate under continuous or high-load conditions, such as in mining or heavy fabrication.
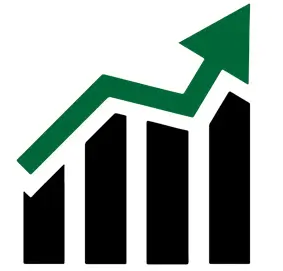
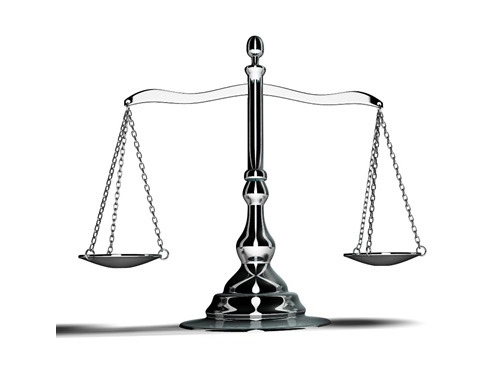
Finer Grits and Tool Longevity: Conversely, finer grit sizes tend to wear at a slower rate. The finer particles cut more gently and are less likely to become dislodged from the tool matrix. This gentle cutting action allows finer grit tools to last longer, as the wear on the tool is distributed more evenly across many cutting points. This distribution helps in maintaining the tool's structural integrity and cutting efficiency over a longer period. Moreover, the finer grits create less stress on the tool during each interaction with the material, which not only prolongs the tool's life but also often results in a higher-quality finish on the workpiece.
Although finer grits might require more time to complete a cutting or grinding task, their ability to extend tool lifespan can significantly offset the slower operational speed by reducing downtime for tool changes and maintenance. This is particularly valuable in precision manufacturing settings, such as in the production of aerospace components or intricate medical devices, where maintaining tool integrity and achieving consistent results over time are paramount.
Balancing Grit Size, Wear, and Performance: Choosing the right grit size involves balancing the need for efficient material removal with the desire to minimize tool wear and maximize tool lifespan. In practice, this often means selecting a grit size that is coarse enough to achieve acceptable cutting speeds but fine enough to ensure the longevity of the tool under specific operating conditions. For many operations, this may also involve using a combination of different grit sizes throughout the stages of the manufacturing process, starting with a coarser grit for rapid material removal and transitioning to finer grits for finishing tasks where precision and tool longevity are more critical.
Material Removal Rate and the Impact of Coarser Diamond Grits
In the context of industrial diamond tools used for cutting, grinding, or polishing, the material removal rate (MRR) is a critical factor, especially in projects where speed and efficiency are paramount. The selection of diamond grit size plays a substantial role in influencing the MRR, with coarser grits often being the preferred choice for applications requiring high throughput.
Understanding Material Removal Rate (MRR)
Material Removal Rate (MRR) refers to the volume of material removed per unit of time during the machining process. It is commonly measured in cubic millimeters per minute (mm³/min) but can also be expressed in other volume per time units depending on the industry and specific application. The MRR is influenced by several factors, including the hardness and abrasiveness of the material being processed, the type of machining operation, the cutting speed, feed rate, and notably, the grit size of the diamond tool.
Role of Coarser Diamond Grits in Enhancing MRR
Coarser diamond grits are larger and possess more aggressive cutting abilities. They can penetrate deeper into the material with each pass compared to finer grits, thus removing more material in the same amount of time. This is particularly useful in rough cutting stages where the priority is to shape the material rather than finish it. Using coarser grits can significantly increase the efficiency of the cutting process by reducing the number of passes needed to remove a set volume of material. This efficiency is crucial in large-scale manufacturing processes where time and throughput are critical metrics. Additionally, coarser grits are less prone to clogging with material residues, which can be a significant issue with finer grits especially when working with sticky or soft materials. Better chip evacuation with coarser grits also enhances heat dissipation, reducing the risk of thermal damage to both the tool and the workpiece.
Applications Suitable for Coarser Diamond Grits
In applications such as stone quarrying, initial cuts in metal fabrication, and rough shaping of ceramics, coarser diamond grits are ideal. They allow rapid removal of material to approximate the desired shape before finer details and surface finishes are applied. In tasks like removing large volumes of concrete or asphalt, coarser grits are essential. They help achieve the necessary depth and volume of removal more quickly than finer grits could. When the precision of the final surface is not a primary concern, such as in the creation of blanks or preforms in various materials, coarser grits provide a cost-effective solution by maximizing MRR and minimizing tool wear.
Considerations When Using Coarser Grits
While coarser grits increase MRR, they also tend to leave a rougher surface finish. If a smooth finish is required, a subsequent pass with finer grits will be necessary, which should be planned as part of the process. Although coarser grits generally last longer under rough conditions, they still require regular checks and maintenance to ensure optimal performance and to prevent potential failure due to excessive wear or damage. The benefits of coarser grits can be maximized by optimizing other cutting parameters such as the cutting speed, feed rate, and the cooling/lubrication system used during the cutting process.
Practical Guidelines: Determining the Appropriate Diamond Grit Size
1. Assess the Material:
Begin by thoroughly analyzing the material that will be cut or ground. Key factors to consider include the hardness and abrasiveness of the material. Hardness refers to the material's ability to resist surface deformation, while abrasiveness indicates how quickly it can wear down the cutting tool. Materials such as hardened steel, ceramics, and certain types of stone can be particularly challenging due to their toughness and abrasive nature.
2. Define the Desired Outcome:
Clearly articulate what you need to achieve with the cutting or grinding process. This includes:
Surface Finish: Decide on the level of smoothness required on the material's surface after the process. Finer finishes generally require finer grit sizes.
Cutting Speed vs. Precision: Determine the priority between cutting speed and the precision of the cut. If speed is more critical, a coarser grit may be beneficial; if precision is paramount, a finer grit should be considered.
Consistency and Control: Assess how critical it is to maintain consistency and control during the cutting or grinding process, as this can also influence the choice of grit size.
3. Consult Specifications:
Review the specifications for the application or process. These specifications often include detailed recommendations for grit sizes based on the type of material being worked and the desired outcomes. Manufacturer recommendations can be invaluable in providing a starting point for selecting the right grit size, as they are based on extensive testing and industry experience.
4. Trial and Testing:
Whenever feasible, conduct a trial run with different grit sizes to empirically determine which one offers the best balance between speed, finish quality, and tool lifespan. This step is particularly important because it allows for real-world testing of the theoretical choices made in earlier steps. Trials should aim to replicate the actual conditions under which the tools will be used as closely as possible.
Document Results: Keep detailed records of each trial, noting the grit size used, the material processed, the speed of operation, the quality of the finish, and the rate of tool wear. This data can be invaluable for making informed decisions not only for the current task but for similar future applications.
Evaluate and Adjust: Based on the outcomes of the trials, evaluate whether the chosen grit size meets the expectations and requirements. If not, adjust the grit size up or down accordingly and perform additional tests until the optimal configuration is found.
Diamond Grit Size Effect on Cut Quality and Cutting Speed
Diamond grit size is a pivotal factor in the performance of diamond cutting tools. It significantly influences the cut quality, cutting speed, and the overall efficiency of the material processing operation. Understanding how diamond grit size affects these factors can greatly assist in optimizing cutting processes for different materials and applications.
Surface Finish Quality and Smoothness
The surface finish quality and smoothness achieved during cutting are directly influenced by the size of the diamond grit. Finer grit sizes, represented by higher mesh numbers, produce a smoother and more refined surface. This is because smaller diamond particles create finer scratches on the material surface, reducing the visible marks and roughness. Conversely, coarser grits, with lower mesh numbers, result in more pronounced scratches and a rougher finish. This makes finer grits ideal for applications requiring a high-quality finish, such as in the optics or jewelry industries, where surface aesthetics and precision are critical.
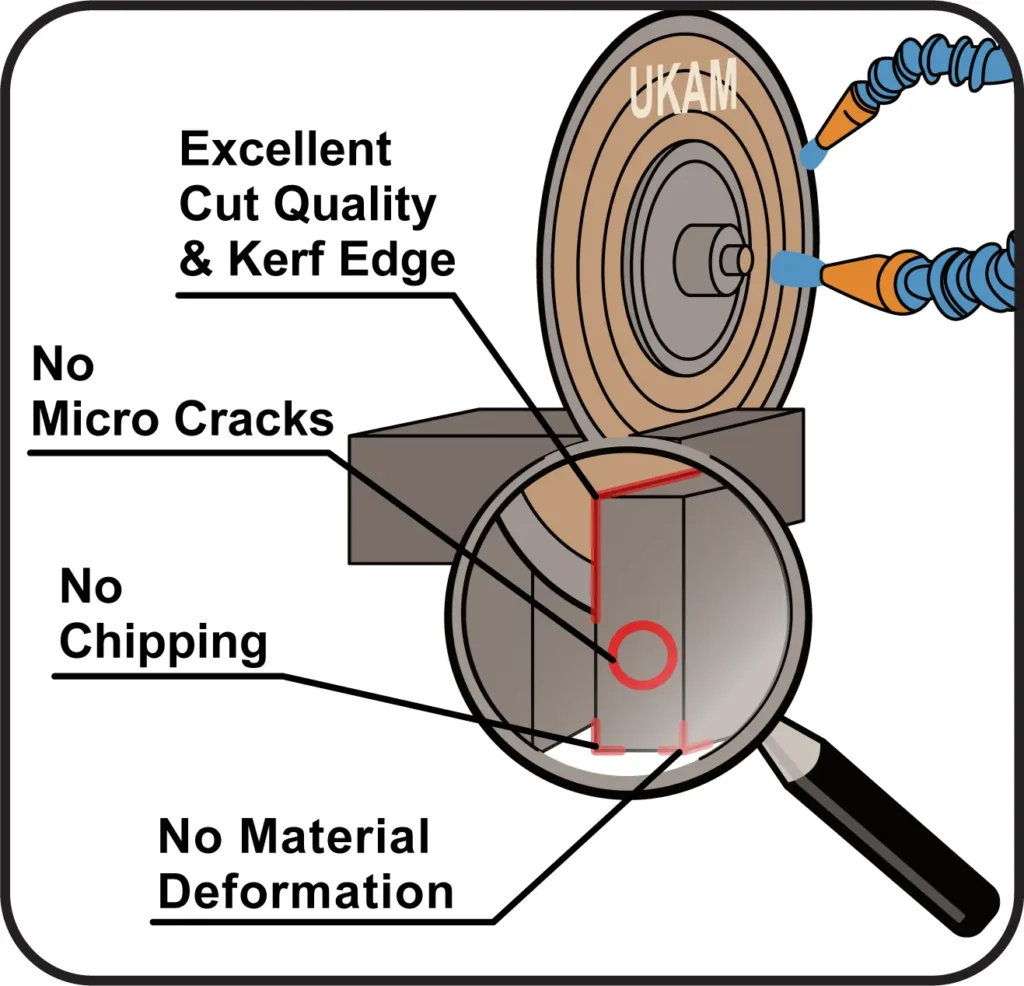
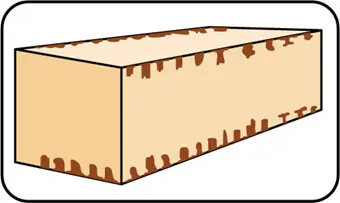
Amount and Level of Chipping
Chipping, a common defect in cutting operations, is also affected by diamond grit size. Larger diamond particles tend to exert more force on the material per cutting pass, which can increase the likelihood of chipping, especially in brittle materials like glass or ceramics. Smaller particles, while slower at cutting, typically produce less force per pass, leading to a reduced incidence of chipping. This characteristic is particularly important in industries where the integrity of the material edges is crucial, such as in semiconductor manufacturing or precision engineering.
Material Microstructure and Deformation
The impact of diamond grit size extends to the microstructural level of the materials being cut. Coarser grits can cause significant deformation of the material at the microscopic level due to their aggressive cutting action. This can alter the material's inherent properties and potentially induce internal stresses or cracks. In contrast, finer grits tend to minimize these effects, preserving the original microstructure of the material better. This aspect is vital in applications like materials research or aerospace engineering, where maintaining the material integrity is paramount.
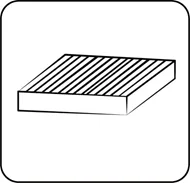
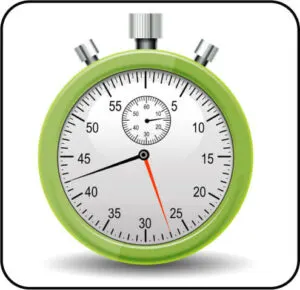
Cutting Speed
Cutting speed is another critical aspect influenced by the size of the diamond particles. Larger grits are capable of removing more material per unit of time, thus achieving faster cutting speeds. This is advantageous for applications where time efficiency is more important than the finish quality, such as in rough cutting operations in construction or stone quarrying. However, for precision applications where the quality of the cut is more important, finer grits, despite their slower speed, are often preferred due to their ability to produce a superior finish.
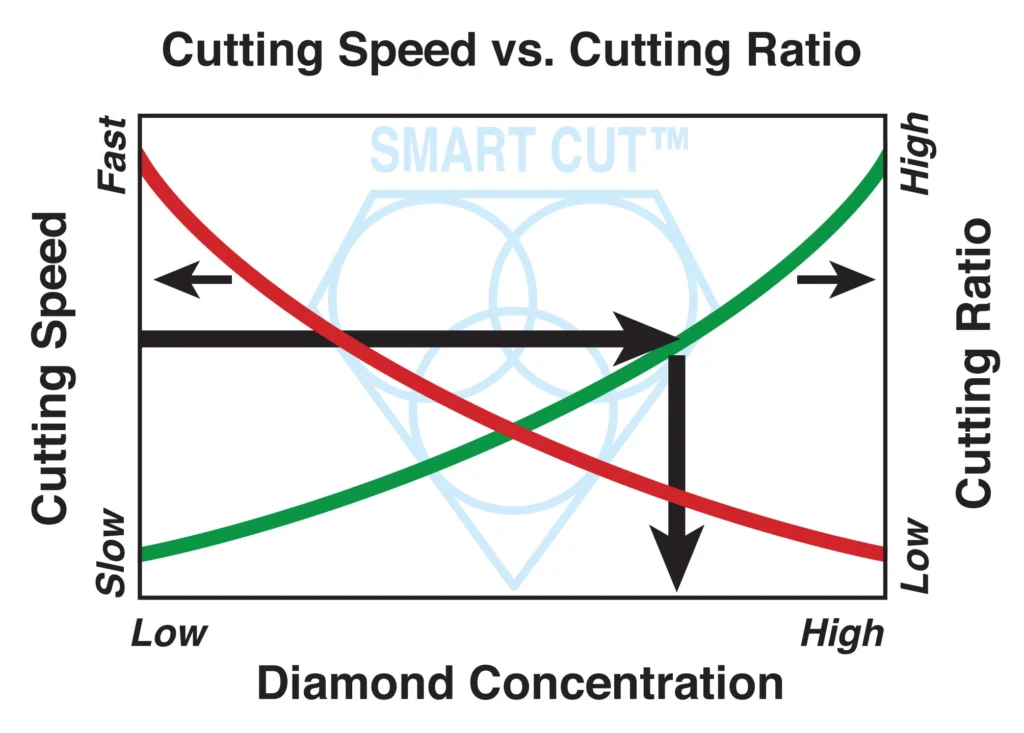
1. Axes:
-
Horizontal Axis (X-axis): Represents the size of the diamond grit, ranging from "Small" to "Large". This size influences the behavior of the cutting tool in terms of both finish and speed.
-
Vertical Axis (Y-axis): The axis is implicitly indicated by the arrows pointing to how surface finish and cutting speed change with grit size.
2. Lines
-
Green Line (Surface Finish): This line shows that a smaller diamond grit size results in a smoother finish, indicated by the line moving from "Rough" to "Smooth" as the grit size decreases. Conversely, larger grit sizes tend to produce a rougher finish.
-
Red Line (Cutting Speed): Demonstrates that larger diamond grit sizes allow for faster cutting speeds, moving from "Slow" to "Fast". Smaller grit sizes slow down the cutting process.
-
nteractions of Lines: The crossover of the lines suggests an inverse relationship between surface finish and cutting speed relative to diamond grit size. As the diamond grit size increases, the cutting speed improves but at the expense of surface finish quality.
Why Selecting the Right Grit Size Matters
Selecting the correct grit size for diamond cutting and grinding tools is a decision that significantly impacts the overall performance and outcomes of machining processes. The choice of grit size affects several critical aspects of material processing, including efficiency, quality of the finished surface, and cost-effectiveness. Understanding these impacts can guide users in making informed decisions that optimize their operations and enhance their final products.
Impact on Performance
Cutting or Grinding Efficiency: The efficiency of cutting or grinding is directly related to how effectively the tool interacts with the material. Coarser grit sizes are beneficial for quickly removing material, which is an advantage in settings where speed is crucial. For example, during the initial stages of stone shaping or when performing rough metal fabrications, larger grit sizes (lower mesh numbers) can facilitate a faster completion of these tasks. This rapid removal rate not only speeds up the process but also helps in managing large volumes, which is essential in industries like construction and heavy manufacturing.
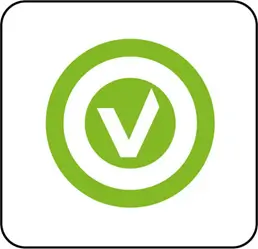
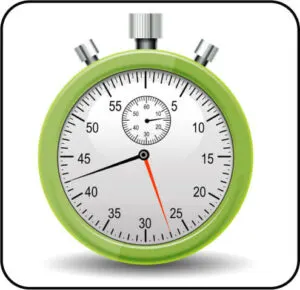
Precision and Finishing:On the other hand, finer grit sizes play a critical role in applications that demand high precision and fine finishes. Although these finer grits remove material at a slower rate, they are indispensable for achieving detailed work and high-quality finishes necessary in many advanced manufacturing processes. Applications that benefit from finer grits include the finishing of optical lenses, where even minor imperfections can degrade clarity, and the production of precision aerospace parts, which must meet stringent specifications for safety and performance.
Finer grits are also crucial in the jewelry industry, where the quality of the finish directly affects the aesthetic and commercial value of the pieces. By using finer grit sizes, craftsmen can ensure smooth surfaces and detailed enhancements that meet high standards of jewelry design. In these applications, selecting a grit that precisely matches the required level of precision ensures that efficiency is maintained without compromising the quality of the finished product.
Balancing Efficiency with Quality: The challenge in optimizing efficiency in cutting and grinding lies in balancing the need for quick material removal with the requirement for high-quality finishes. Selecting the right diamond grit size is a critical decision that affects this balance.
Coarser grits may be selected to maximize removal rate and efficiency in the early stages of a process, while finer grits may be employed in later stages to achieve the desired finish and precision. For many industries, using a combination of grit sizes throughout the manufacturing process can be an effective strategy. Starting with coarser grits for initial cuts and switching to finer grits for finishing touches allows manufacturers to optimize both the speed of production and the quality of the outputs.
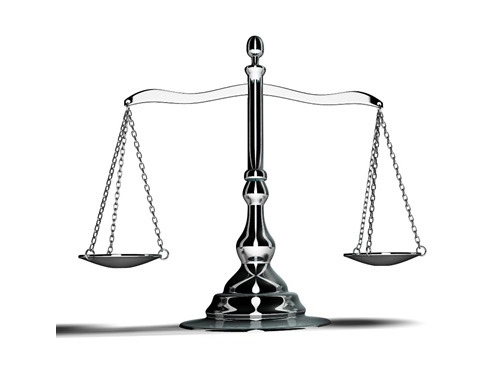
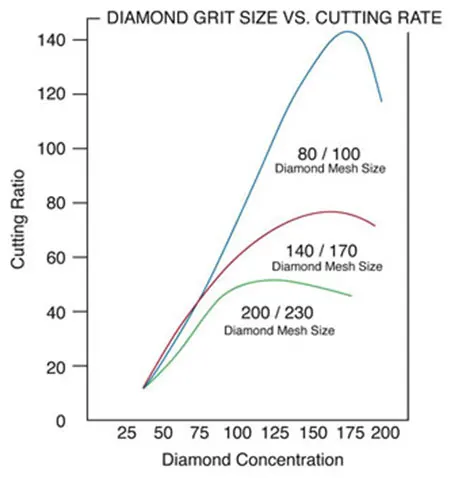
1. Axes:
-
Horizontal Axis (X-axis): Shows the diamond concentration, ranging from 25 to 200. This measures how densely the diamond particles are packed in the cutting tool.
-
Vertical Axis (Y-axis): Indicates the cutting ratio, which is a measure of cutting efficiency or productivity. The scale ranges from 0 to 140.
2. Lines
-
Blue Line (80/100 Diamond Mesh Size): This curve shows a sharp increase in cutting rate as diamond concentration increases, peaking at a certain point before dramatically dropping. This mesh size is likely coarse and facilitates fast cutting initially, but may become inefficient beyond a specific concentration threshold.
-
Green Line (140/170 Diamond Mesh Size): Represents a more moderate increase in cutting rate with increasing diamond concentration, peaking at a lower rate than the blue line. This suggests a finer grit that provides a more consistent cutting rate over a broader range of concentrations but does not reach the high peak of coarser grits.
-
Red Line (200/230 Diamond Mesh Size): Indicates the finest grit among the three, showing a gradual and steady increase in cutting rate, peaking at the lowest point among the three lines. This suggests that while finer grit provides a steady cutting performance, its peak efficiency is lower compared to coarser grits.
Quality in Cutting and Grinding Processes:
Surface Quality:The grit size of diamond tools plays a pivotal role in determining the quality of the surface after a cutting or grinding operation. Finer grits are instrumental in producing a smoother and more refined surface, which is not only aesthetically pleasing but also functionally superior. This enhanced surface quality is especially crucial in industries where the visual and tactile finish of products is paramount.
For instance, in gemstone polishing, the final appearance of the stone significantly influences its market value. Finer grits help achieve a high gloss and remove any superficial scratches or imperfections that could detract from the stone's brilliance. Similarly, in the production of precision optics, such as lenses for cameras or microscopes, the clarity and accuracy of the optical surface are directly affected by surface finish. A smoother finish ensures that the optical properties of the lens are optimal, reducing light scattering and improving performance.
The advantage of using finer grits also extends to reducing the need for extensive post-process finishing. When a high-quality surface finish is achieved directly from the primary cutting or grinding process, subsequent steps such as additional polishing or reworking can be minimized or eliminated, saving time and resources.
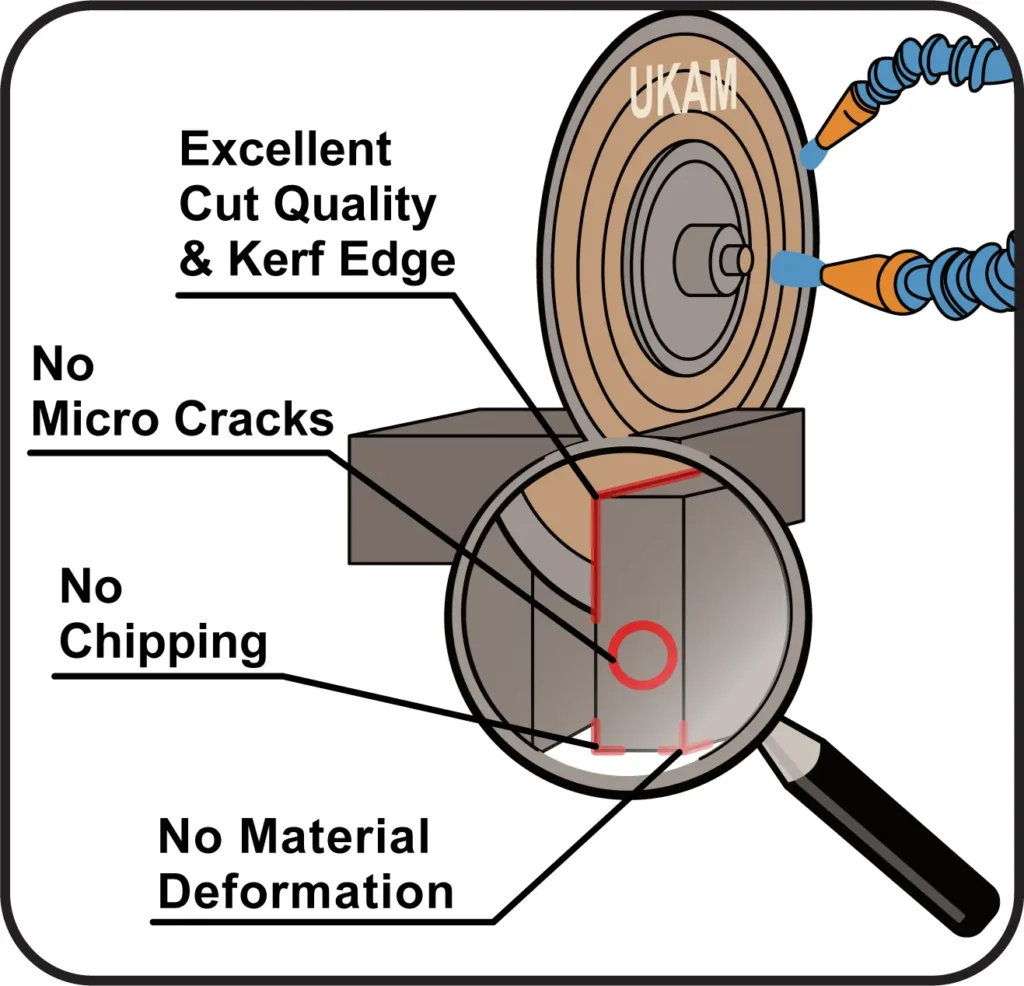
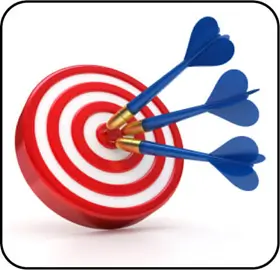
Consistency: Uniformity in particle size of the diamond grit not only affects the initial outcomes of cutting or grinding but also ensures consistent performance throughout the tool's life. This consistency is vital for applications where precision and reliability are critical. In semiconductor manufacturing, for example, the quality of the cut can affect the functionality of the chips, as even minor variations can lead to defects that render a semiconductor device non-functional.
Similarly, in medical device fabrication, where components often require high precision to ensure they function correctly in medical procedures, consistency in the grit size of cutting tools helps in achieving uniformity in production. This uniformity is essential for maintaining tight tolerances and ensuring that each component meets rigorous health and safety standards.
Furthermore, uniform grit size contributes to predictable results in manufacturing processes, reducing the incidence of defects and improving overall production efficiency. It allows manufacturers to set more precise machine settings and reduces the variability in product quality, which is crucial for maintaining high customer satisfaction and adhering to strict industry regulations.
Strategic Importance of Grit Selection: Choosing the right grit size is thus not merely a technical decision but a strategic one. It impacts not only the direct costs associated with manufacturing but also the long-term reputation of the product and the brand. In high-stakes industries, where quality and consistency can differentiate leading brands from the competition, the careful selection of diamond grit size becomes a core element of the manufacturing strategy.
Cost-effectiveness in Diamond Tool Selection:
Tool Wear and Longevity: The longevity and wear rate of diamond tools are significantly affected by the choice of grit size, which in turn influences the overall cost-effectiveness of operations. Coarser grits, while effective for quick material removal, may wear down more rapidly because they typically operate under more aggressive conditions. This accelerated wear can be attributed to the larger diamond particles being more prone to fracture and dislodgement during heavy-duty operations.
In contrast, finer grits, which are used to achieve more precise and high-quality finishes, generally exhibit a slower wear rate. This is because the smaller diamond particles are less likely to break away from the tool matrix, allowing the tool to maintain its cutting ability over a longer period. However, the more gradual material removal rate of finer grits can extend the duration of the cutting or grinding process, potentially increasing labor costs. This trade-off must be carefully considered, particularly in operations where time efficiency is crucial.
Balance of Performance and Wear: Achieving cost-effectiveness in diamond tool usage largely hinges on finding the right balance between performance and tool wear. An optimal grit size selection is key to this balance, enabling efficient cutting or grinding while minimizing tool degradation. By choosing a grit size that aligns well with the material properties and the desired outcome, manufacturers can reduce the need for frequent tool changes and minimize downtime, both of which contribute to lowering the overall cost per cut or ground surface.
Furthermore, extending the tool's useful life not only reduces direct tooling costs but also decreases the environmental impact associated with tool production and disposal. This makes effective grit size selection not only a matter of economic efficiency but also of sustainability.
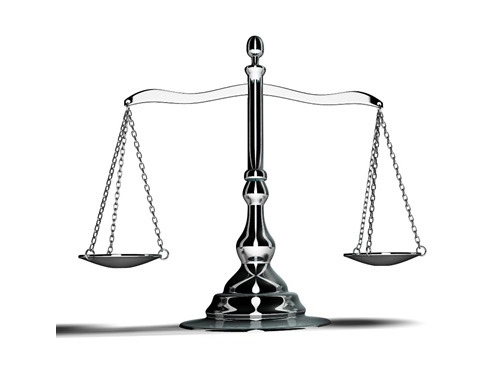
Material Waste and Efficiency: The impact of grit size on material waste is another crucial factor in the cost-effectiveness equation. Coarser grits may remove more material than necessary, leading to significant wastage. This is especially costly when working with high-value materials such as precious stones or advanced alloys, where excess material removal translates directly into financial loss.
On the other hand, while finer grits help in minimizing material waste by allowing for more controlled and precise material removal, their slower operation can increase energy consumption and operational costs. In industries where materials cost is high, the savings from reduced material waste can often outweigh the higher operational costs, making finer grits a more cost-effective choice overall.
Understanding the difference between diamond grit size and abrasive grit size used in materials like aluminum oxide, silicon carbide, or sandpaper is crucial for professionals in the cutting, grinding, and polishing industries. These are distinct grading systems, each with specific applications and effects on material processing.
How Diamond Mesh Sizes Influences the Performance of Diamond & CBN Tools
The choice of diamond and CBN mesh sizes impacts a wide range of tool performance metrics and operational variables. By carefully selecting the appropriate mesh size, users can optimize the balance between speed, precision, tool life, and cost-effectiveness according to specific materials and cutting conditions.
Tool Life varies with mesh size; finer diamond meshes lead to increased wear and tear, resulting in shorter tool life. Conversely, coarser meshes enhance tool longevity due to their robust cutting capabilities, allowing them to withstand harsher conditions better.
Surface Finish is also affected; smaller mesh sizes produce a smoother finish, making them suitable for precision applications requiring high-quality surfaces. Larger mesh sizes, which create rougher finishes, are preferred for initial rough cuts where precision is less critical.
Feed Rate differences emerge as well; finer particles remove less material per pass, resulting in lower feed rates. In contrast, coarser particles can remove more material per pass, significantly increasing the feed rate and overall efficiency of the cutting process.
Chipping is another consideration; smaller diamond meshes reduce chipping, providing cleaner cuts and more defined edges. Larger meshes increase the likelihood of chipping, potentially leading to less precise edges.
Cutting Speed is slower with finer grit sizes due to the gradual material removal. However, larger mesh sizes facilitate faster cutting speeds thanks to their more aggressive cutting action.
Dressing Frequency is higher with smaller mesh sizes because the finer particles wear out more quickly. Coarser grits, however, maintain their form longer, reducing the need for frequent dressing.
Energy Consumption can be higher with finer meshes as more passes are often required to achieve the desired material removal. Coarser meshes typically consume less energy due to their ability to remove more material in fewer passes.
Heat Generation increases with smaller mesh sizes due to the increased friction and slower removal rates. Conversely, coarser meshes generate less heat, helping to reduce friction-related heat during faster cuts.
Tool Pressure must be higher when using finer meshes to effectively remove material. Coarser meshes require less force, allowing the tool to do more of the work with less exerted pressure.
Vibration levels are lower with finer meshes due to their smoother cutting action, which can enhance both operator comfort and precision. Higher vibrations associated with coarser meshes might negatively impact both precision and comfort during use.
Material Waste is minimized with finer meshes, which allow for more precise material removal. Coarser meshes tend to produce more waste due to their aggressive removal approach.
Tool Cost and Maintenance are further considerations; tools with finer diamond meshes might be more expensive due to the costs associated with precision manufacturing and may require more frequent maintenance. Tools with coarser meshes often cost less over time due to lower replacement frequency and reduced maintenance needs.
Material Compatibility rounds out the list of considerations. Finer meshes are better for softer, more delicate materials, while coarser meshes excel with harder, tougher materials.
Comparison Table showing how different diamond mesh sizes affect various performance and operational variables in diamond & cbn tools
Variable |
Effect of Smaller Diamond Mesh Size |
Effect of Larger Diamond Mesh Size |
---|---|---|
Tool Life |
Shorter due to increased wear and tear |
Longer due to robust cutting capability |
Surface Finish |
Smoother, suitable for precision applications |
Rougher, generally more suitable for initial rough cuts |
Feed Rate |
Lower, due to finer particles removing less material per pass |
Higher, as coarser particles can remove more material |
Chipping |
Less, providing cleaner cuts |
More, potentially resulting in less precise edges |
Cutting Speed |
Slower, due to finer grit size |
Faster, benefiting from aggressive cutting |
Dressing Frequency |
Higher, due to quicker wear of finer particles |
Lower, as coarser grits maintain their form longer |
Energy Consumption |
Potentially higher, as more passes may be required |
Lower, due to fewer passes needed for material removal |
Heat Generation |
Higher, due to increased friction and slower removal |
Lower, as faster cuts can reduce friction-generated heat |
Tool Pressure |
Higher, requiring more force to achieve effective cutting |
Lower, as the tool does more work with less force |
Vibration |
Less, due to finer cutting action |
More, potentially impacting precision and operator comfort |
Material Waste |
Lower, due to precise material removal |
Higher, due to aggressive material removal |
Tool Cost |
Potentially higher, due to precision manufacturing costs |
Lower, due to less frequent need for replacements |
Maintenance |
More frequent, increasing operational downtime |
Less frequent, reducing downtime |
Material Compatibility |
Better for softer, more delicate materials |
Better for harder, tougher materials |
Operator Skill Level |
Higher skill required for optimal use |
Lower skill may suffice due to the tool's robust nature |
Variations in Cutting Speed and Surface Finish Across Different Diamond Bond Types
The performance characteristics of diamond tools, such as cutting speed and surface finish, vary significantly across different bond types, even when using the same grit size. This variation is primarily due to the inherent properties of the bonding materials and their interaction with the diamond grits embedded within them.
Cutting Speed Variability: For instance, a sintered (metal bond) tool with a 120 mesh grit size will demonstrate a different cutting speed compared to an electroplated or resin bond tool of the same grit size. Metal bonds are generally more robust and durable, allowing for a more aggressive cutting approach that can handle tougher materials efficiently. This means that a metal bond tool can maintain a higher cutting speed as it resists wear and maintains its diamond exposure better under harsh conditions.
On the other hand, electroplated and resin bond tools, while also capable of utilizing a 120 mesh grit, might exhibit slower cutting speeds under similar conditions. Resin bonds, in particular, are softer and more flexible, which tends to cushion the diamonds. This results in a less aggressive cut and consequently, a slower speed. Electroplated bonds, which typically present a single layer of diamonds, offer excellent initial cutting speeds but may wear down quicker than sintered bonds, especially on tough materials.
Surface Finish Discrepancies: Moreover, the surface finish achievable with different bond types using the same grit size also varies dramatically. A 120 mesh resin bond tool is likely to produce a smoother and more aesthetically pleasing finish compared to a sintered (metal bond) tool with the same grit size. The softer nature of resin allows for a finer finish as the bond material can adapt to the contours of the surface being worked on, reducing gouging and scratch marks.
In contrast, even a finer grit such as 600 mesh in a sintered (metal bond) tool might not match the smooth finish provided by a 120 mesh resin bond tool. Metal bonds are designed for durability and cutting efficiency, not necessarily for achieving the finest finishes. The hard, rigid nature of metal bonds can result in a finish that, while acceptable for many industrial applications, does not have the refined quality often required in decorative or precision work where resin bonds excel.
What is generally considered coarse, medium, and fine grit sizes for each type of diamond bond. This classification can help in selecting the appropriate grit size based on the bond type for different applications.
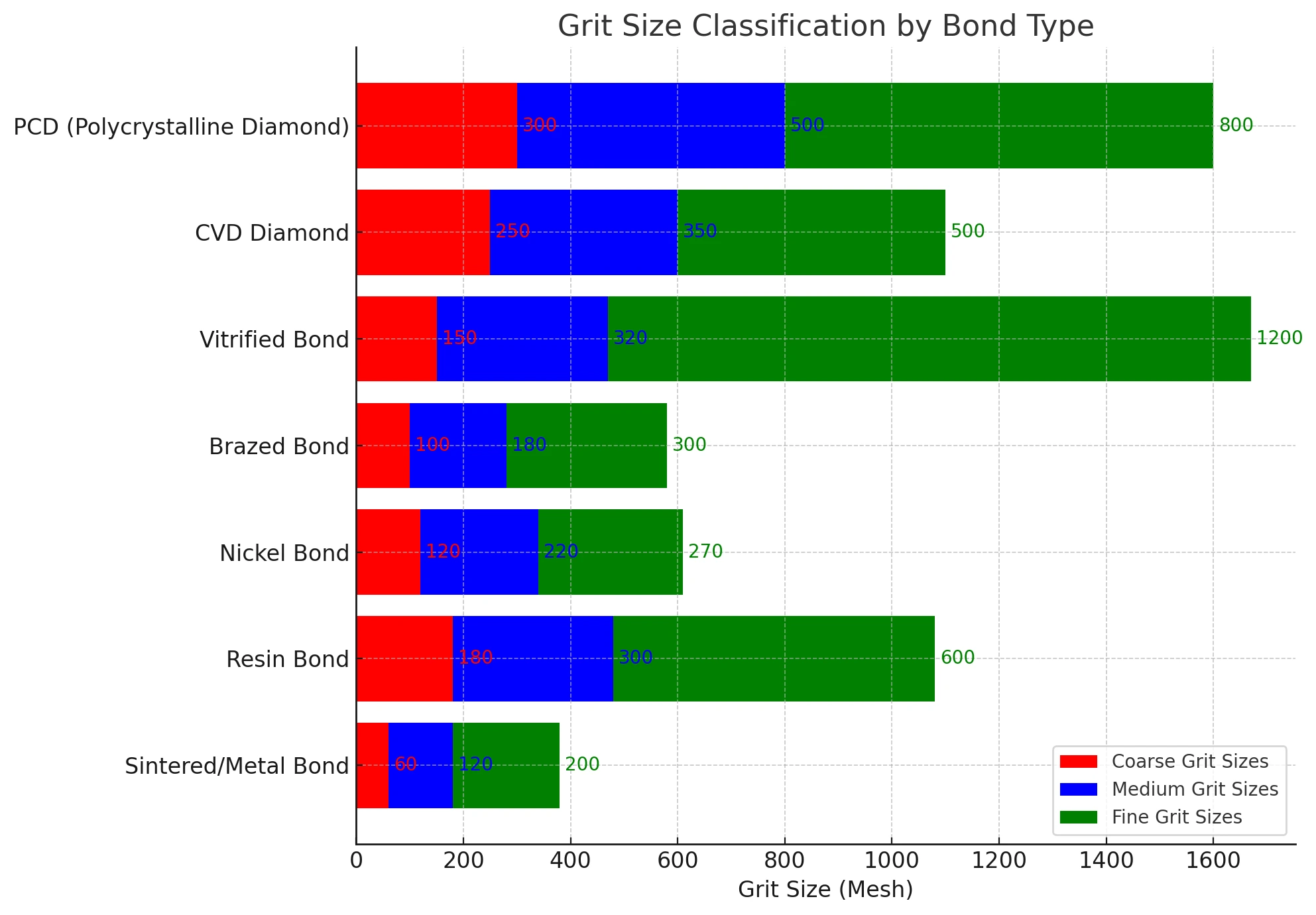
Bond Type |
Coarse Grit Sizes |
Medium Grit Sizes |
Fine Grit Sizes |
---|---|---|---|
Sintered/Metal Bond |
30-60 mesh |
70-120 mesh |
140-200 mesh |
Resin Bond |
100-180 mesh |
200-300 mesh |
320-600 mesh |
Nickel Bond |
80-120 mesh |
150-220 mesh |
230-270 mesh |
Brazed Bond |
40-100 mesh |
120-180 mesh |
200-300 mesh |
Vitrified Bond |
80-150 mesh |
180-320 mesh |
400-1200 mesh |
CVD Diamond |
150-250 mesh |
260-350 mesh |
400-500 mesh |
PCD (Polycrystalline Diamond) |
150-300 mesh |
350-500 mesh |
600-800 mesh |
Explanation of Grit Size Classifications:
-
Coarse Grit Sizes: These are larger diamond particles that are effective for rapid material removal. They are suitable for rough processing where the finish is not the primary concern but rather the speed of material removal is prioritized.
-
Medium Grit Sizes: These grits offer a balance between material removal rate and surface finish quality. They are used for more controlled cutting or grinding, where both the efficiency of operation and the smoothness of the finish are important.
-
Fine Grit Sizes: These consist of smaller diamond particles that are essential for finishing operations. They are used where a high-quality surface finish is crucial, such as in fine polishing or detailed and precise cutting operations.
Diamond Grit Size vs. Conventional Abrasive Grit Size
Diamond Grit Size: This is measured in terms of mesh size, which refers to the number of holes per inch of a screen through which the diamond particles are sized. Diamond mesh size is inversely related to the diamond particle size—larger mesh numbers indicate smaller particles.
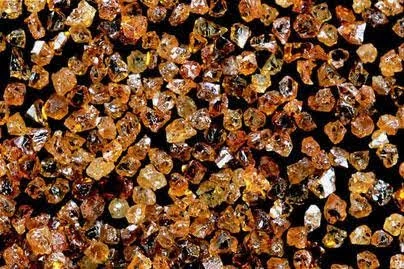
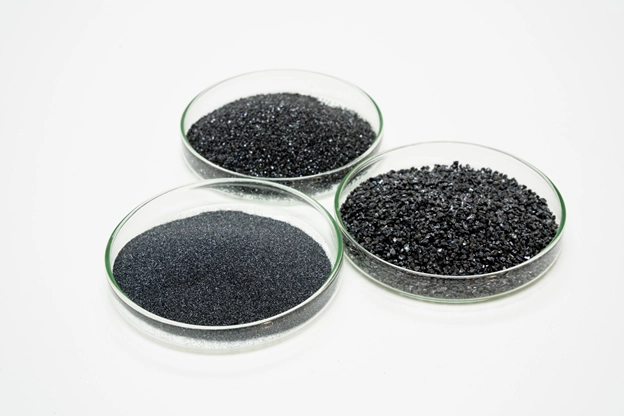
Abrasive Grit Size (Aluminum Oxide, Silicon Carbide, etc.): For conventional abrasives used in sandpaper and other similar applications, grit size is determined by the number of abrasive particles that fit within a specific area of the sieve screen used during grading. Unlike diamond mesh size, larger grit numbers in conventional abrasives denote finer particles.
Diamond Abrasive Grit Size Comparison Chart
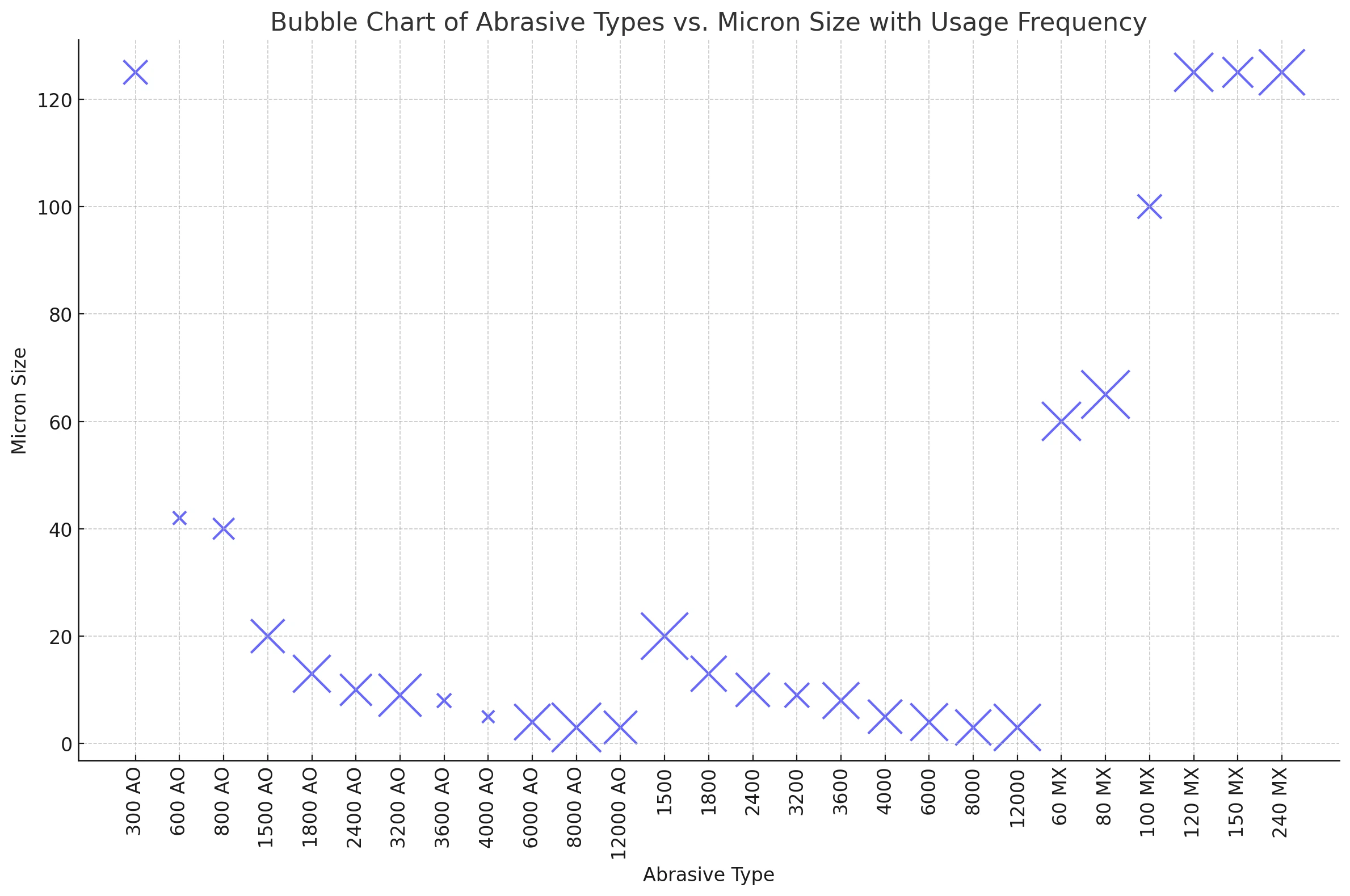
Abrasive Type |
ANSI or CAMI (USA) |
FEPA (Euro) |
Apex or Structured Abrasives |
Micron |
---|---|---|---|---|
Micro-Mesh Aluminum Oxide |
||||
300 AO |
- |
P120 |
A-160 |
125 |
600 AO |
- |
P400 |
A-45 |
42 |
800 AO |
- |
P600 |
A-35 |
40 |
1500 AO |
- |
P1200 |
A-16 |
20 |
1800 AO |
- |
P1500 |
A-10 |
13 |
2400 AO |
- |
P2000 |
A-06 |
10 |
3200 AO |
- |
P2500 |
- |
9 |
3600 AO |
- |
- |
- |
8 |
4000 AO |
- |
- |
A-05 |
5 |
6000 AO |
- |
- |
- |
4 |
8000 AO |
- |
- |
- |
3 |
12000 AO |
- |
- |
- |
3 |
Micro-Mesh Cushioned Abrasive Regular |
||||
1500 |
- |
P1000 |
- |
20 |
1800 |
- | P1500 | - |
13 |
2400 |
- |
P2000 |
- |
10 |
3200 |
- |
P2500 |
- |
9 |
3600 |
- |
- |
- |
8 |
4000 |
- |
- |
- |
5 |
6000 |
- |
- |
- |
4 |
8000 |
- |
- |
- |
3 |
12000 |
- |
- |
- |
3 |
Micro-Mesh Cushioned Abrasive MX |
||||
60 MX |
120 | P240 | A-80 | 60 |
80 MX |
180 | P180 | A-100 | 65 |
100 MX |
- |
P150 | A-130 | 100 |
120 MX | - |
P120 |
A-160 |
125 |
150 MX |
- |
P100 |
A-160 |
125 |
180 MX |
- |
- |
- |
- |
240 MX |
Content | P80 | Content |
125 |
320 MX | - | - | - | - |
360 MX |
- | - | - | - |
400 MX |
- | - | - | - |
600 MX |
- | - | - | - |
800 MX |
- | - | - | - |
1200 MX | - | - | - | - |
1500 MXD |
- |
- |
- |
- |
1800 MXD |
- | - | - | - |
Here is a table that categorizes different grit sizes for micro and macro abrasives, describing their typical use cases based on grain size and their corresponding diameter in micrometers:
Abrasives Grit Sizes Comparison & Application Chart
Category |
Grit Number |
Description |
Diameter (Micrometers) |
Typical Use |
---|---|---|---|---|
Micro Abrasives |
||||
Ultra Fine |
1,500 |
The most fine-grained abrasives |
8.4 to 12.6 |
For achieving extremely smooth finishes |
2,000 |
||||
2,500 |
||||
Super Fine |
800 |
Refines inconsistencies, not strong enough to remove material |
15.3 to 23.0 |
For refining surfaces without significant material removal |
1,000 |
||||
1,200 |
||||
Extra Fine |
400 |
More abrasive than super fine, removes very little material |
25.8 to 36.0 |
For light material removal and fine polishing |
500 |
||||
600 |
||||
Very Fine |
240 |
The coarsest micro abrasives |
40.5 to 58.5 |
For fine surface preparation and finishing |
280 |
||||
320 |
||||
Macro Abrasives |
||||
Very Fine |
150 |
The finest-grained macro abrasives |
60 to 100 |
For fine surface preparation less fine than micro abrasives |
180 |
||||
220 |
||||
Fine |
100 |
Leaves small scratches, but not a smooth finish | 115 to 162 |
For initial stages of surface smoothing |
120 | ||||
Medium |
60 |
Results in a medium-coarse surface texture |
190 to 265 |
For moderate material removal and texturing |
80 |
||||
Coarse |
40 |
Rapid material removal |
336 to 425 |
For rapid material removal and coarse texturing |
50 |
||||
Extra Coarse |
36 |
Removes materials most quickly |
530 to 1,815 |
For heavy material removal, such as sanding heavily painted or varnished surfaces |
16 |
||||
12 |
Material Differences:
Diamond abrasives are made from carbon atoms formed under high-pressure, high-temperature conditions, making them extraordinarily hard and durable. This makes diamond abrasives particularly effective for cutting, grinding, and polishing harder materials. Conventional abrasives, such as aluminum oxide or silicon carbide, are generally softer and less durable than diamonds. They are suitable for a wider range of materials but might wear down quicker when used on very hard materials.
Application Suitability:
Diamond abrasives due to their exceptional hardness, diamond abrasives are ideal for high-precision cutting in tough materials like stone, reinforced concrete, glass, and advanced ceramics. They provide a high-quality finish and are cost-effective for such applications due to their longevity. Conventional Abrasive Grit are more suited for softer or less demanding materials and applications, including wood sanding, metal polishing, and some types of stone finishing. They are also typically less expensive and more readily available than diamond abrasives.
Conversion Between Abrasive and Diamond Grit Sizes
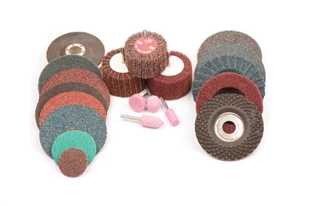

When transitioning from conventional abrasive grit sizes to diamond grit sizes, the relationship isn’t direct because the two systems measure different characteristics of the abrasive particles. However, a rough rule of thumb is to double the conventional abrasive grit size to approximate the diamond mesh size. For instance:
A 60 grit size in aluminum oxide or silicon carbide, typically used in sandpaper, would roughly correspond to a 120 diamond mesh size. This conversion helps in selecting a diamond abrasive with a comparative coarseness, aiming to achieve similar surface finishes or cutting characteristics.
When selecting an abrasive for a specific application, it is essential to consider not only the grit size but also the material's physical properties, the intended use, and the desired outcome. Misalignment in these factors can lead to suboptimal performance, increased costs, or damage to the material.
Key differences between diamond grit size, abrasive grit size, and sandpaper grit size. Each type has unique characteristics that make them suitable for specific applications:
Feature |
Diamond Grit Size |
Abrasive Grit Size (e.g., Aluminum Oxide, Silicon Carbide) |
Sandpaper Grit Size |
---|---|---|---|
Material Hardness |
Extremely hard (10 on Mohs scale) |
Very hard (9 to 9.5 on Mohs scale) |
Varies depending on the abrasive material |
Cost |
High due to material and processing costs |
Moderate, generally cheaper than diamond |
Relatively low |
Durability |
Very high durability and longevity |
High but less than diamond |
Lower, wears out quicker especially on hard surfaces |
Thermal Conductivity |
High, which helps in heat dissipation during cutting |
Lower than diamond, heat buildup can be an issue |
Generally low, can lead to clogging and quick wear |
Usage |
Cutting and grinding very hard materials (metals, ceramics) |
Grinding and finishing metals, wood |
Primarily for wood, plastics, and softer metals |
Efficiency |
High efficiency in cutting, maintains sharpness longer |
Efficient but wears faster under heavy use |
Suitable for surface preparation, not for heavy cutting |
Grit Shape |
Can be tailored for specific applications (blocky, sharp) |
Standardized shapes, less customizable |
Consistent, uniform grit size |
Friability |
Customizable (from friable to non-friable) |
Typically less friable than diamond |
Generally non-friable |
Application Specificity |
High-precision tools for specific tasks |
Broad range of applications, less specialized |
Wide range, general purpose sanding |
Usage of the Chart:
This chart is useful for understanding the approximate equivalency in grit size across different types of abrasives. It helps in selecting the correct grit for a specific application when switching between materials or tools, such as moving from a diamond grinding wheel to sandpaper for finishing tasks. For instance, if a task begins with a diamond grit of 100/120 for rough grinding, it can be finished with a sandpaper of about 120 grit to achieve a similar roughness profile.
Limitations:
It's important to note that these equivalencies are approximate and can vary between manufacturers and specific products. The actual performance and results might differ based on the material composition, bonding methods, and specific application conditions. Always refer to manufacturer guidelines and product specifications for precise selections.
This chart provides a foundational understanding but should be used as a general guide rather than an exact standard.
This comparison is essential for understanding the relative coarseness or fineness across different materials, which is crucial when transitioning between different types of abrasive tools. Here’s a simplified cross-reference chart based on general standards:
Diamond Grit Size (Mesh) |
Approximate Diameter (Microns) |
Equivalent Abrasive Grit Size (Mesh) |
Equivalent Sandpaper Grit (CAMI*) |
---|---|---|---|
60/80 |
250 to 177 |
80 |
80 |
80/100 |
177 to 149 |
100 |
100 |
100/120 |
149 to 125 |
120 |
120 |
120/140 |
125 to 105 |
150 |
150 |
140/170 |
105 to 88 |
180 |
180 |
170/200 |
88 to 74 |
220 |
220 |
200/230 |
74 to 63 |
240 |
240 |
230/270 |
63 to 53 |
280 |
280 |
270/325 |
53 to 45 |
320 |
320 |
325/400 |
45 to 38 |
400 |
400 |
400/500 |
38 to 32 |
500 |
500 |
-
Diamond Grit Size (Mesh): Indicates the number of holes per inch of a sieve through which the grit can pass, with larger numbers indicating smaller particles.
-
Approximate Diameter (Microns): Provides a measure of the average particle diameter in microns.
-
Equivalent Abrasive Grit Size (Mesh): Refers to similar mesh sizes for non-diamond abrasives like aluminum oxide or silicon carbide, used in general abrasive tools.
-
Equivalent Sandpaper Grit (CAMI): Corresponds to the grit sizes defined by the Coated Abrasives Manufacturers Institute (CAMI) standard for sandpaper, commonly used in the U.S.
Diamond Grit Size vs Sand Paper Grit Size
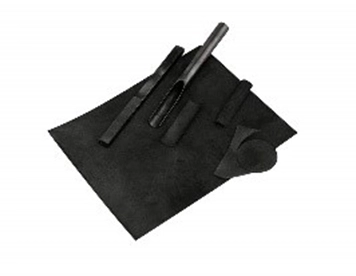
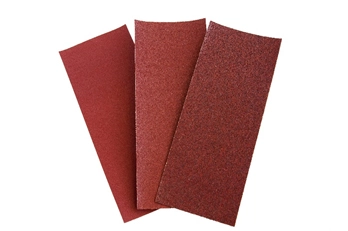
Grit size in abrasives signifies the size of the particles embedded in the abrasive material. In both diamond and sandpaper grits, smaller numbers indicate larger, coarser particles, and higher numbers indicate smaller, finer particles. These particles play a critical role in determining the texture of the finish on the material being worked.
Sandpaper grit sizes are often measured in terms of the grit number within the CAMI (Coated Abrasive Manufacturers Institute) in the U.S., or the FEPA (Federation of European Producers of Abrasives) standards. Higher numbers indicate a higher density of smaller particles, which produce a finer finish. Sandpaper uses various abrasive materials such as aluminum oxide and silicon carbide.
The correlation between diamond grit size and sandpaper grit size isn't straightforward due to differences in scale and application. For example, very coarse diamond grit (40-60 mesh) corresponds roughly to coarse sandpaper grits (40-60 CAMI), and fine diamond grit (240-400 mesh) is comparable to very fine sandpaper (240-400 CAMI).
These correlations are approximations. The specific application, whether cutting, grinding, or polishing, might affect the choice of grit size more significantly than a direct comparison of grit numbers would suggest. For instance, a certain mesh size in diamond might be used for rough concrete polishing, whereas the equivalent in sandpaper grit could be used for finishing wood or metal, highlighting the difference in material hardness and abrasiveness handled by each type of grit.
Sandpaper is used on a wide variety of materials but typically those that are much softer than those handled by diamond abrasives.
-
Coarse Sandpaper Grits (40-60 CAMI) are used for stripping away layers such as paint or varnish, and for rough-shaping wood.
-
Medium Sandpaper Grits (80-120 CAMI) are generally used for smoothing wood surfaces in preparation for painting or varnishing, and for removing smaller imperfections.
-
Fine Sandpaper Grits (150-220 CAMI) provide a smoother finish suitable for final finishing touches before applying a coat of paint or varnish.
-
Very Fine Sandpaper Grits (240-400 CAMI) are often employed in the final finishing stages of woodworking projects, between coats of paint or varnish to achieve an ultra-smooth finish.
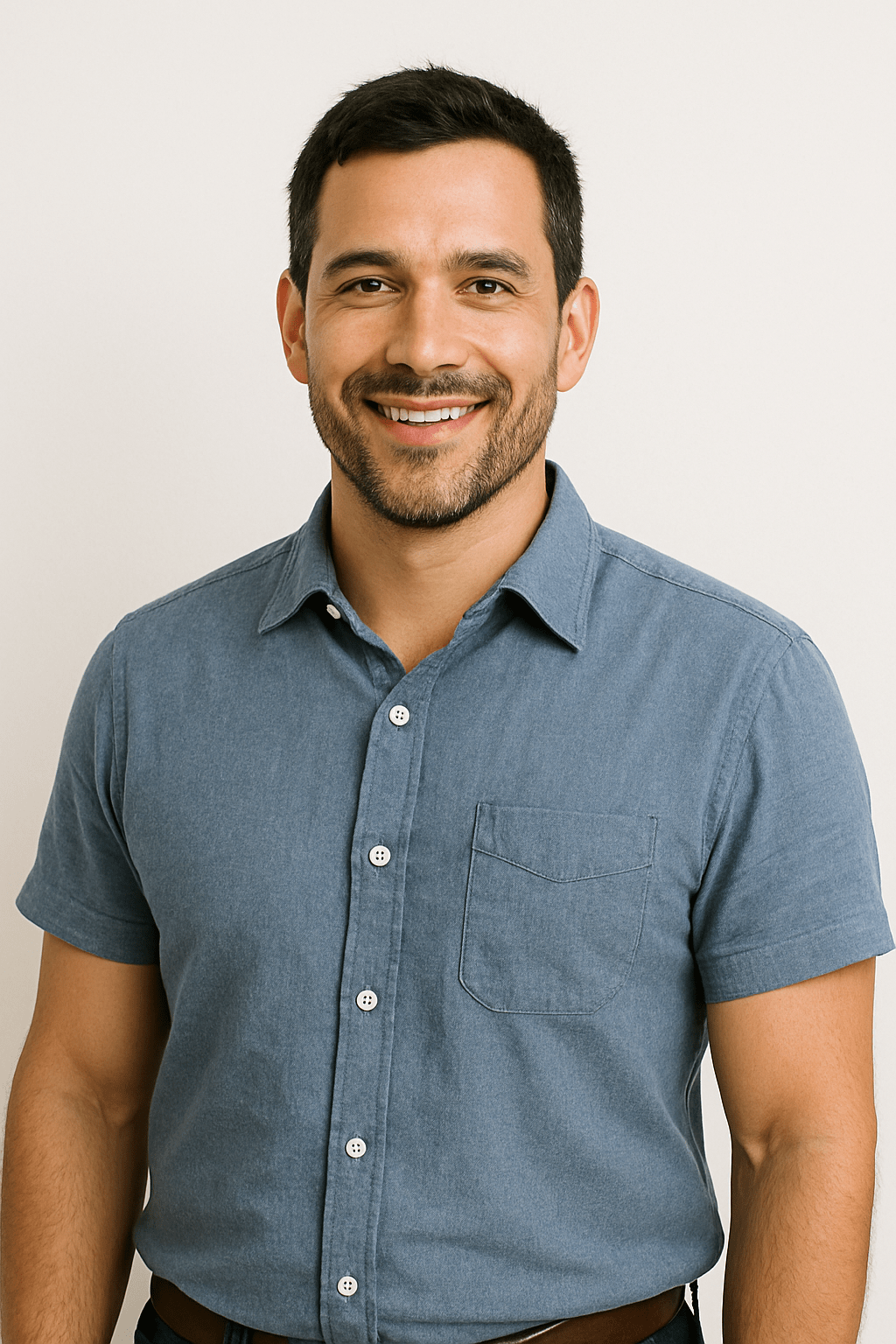
Carlos Sanchez is a senior technical specialist and field applications trainer with more than 17 years of experience in the use and optimization of industrial diamond tools, including ultra-thin diamond blades, core drills, and CBN grinding wheels. With a foundation in industrial engineering and technical operations, Mr. Sanchez has worked extensively with manufacturers and laboratories around the world, providing hands-on support and practical training for a wide range of cutting, grinding, and sample preparation applications.
Fluent in both English and Spanish, Carlos is known for his ability to translate complex tooling concepts into clear, actionable procedures for engineers, technicians, and production staff. His approach emphasizes real-world process improvement, tool longevity, and operator education—ensuring clients get the most out of their diamond tooling investments.
As an author, Mr. Sanchez shares field-tested insights on tool performance optimization, defect prevention, training methodologies, and troubleshooting common cutting issues.
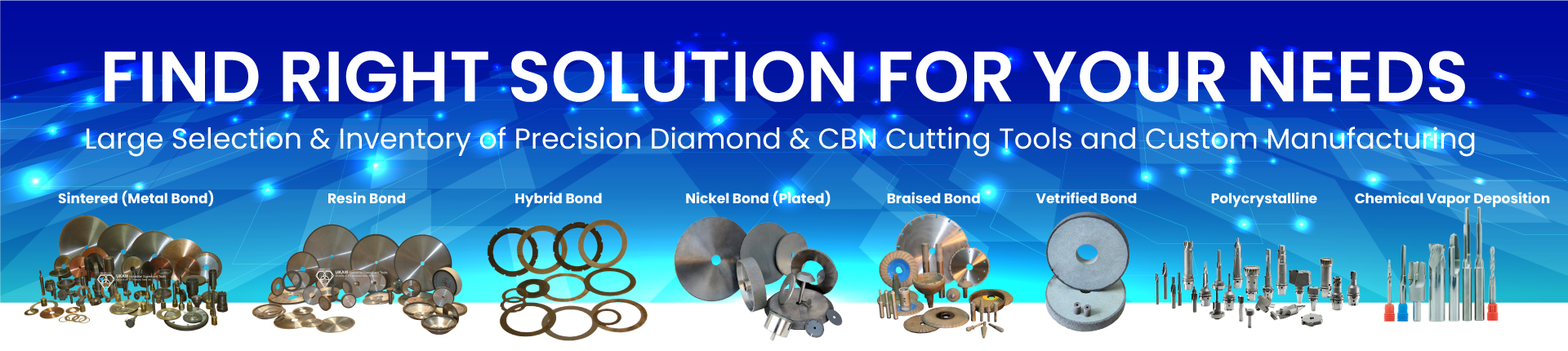
ARE YOU USING RIGHT TOOLS
FOR YOUR APPLICATION?
LET US
HELP YOU
HAVING ISSUES WITH
YOUR CURRENT TOOLS?
Knowledge Center
How to Selecting Right Diamond Tools for your application
How to properly use Diamond Tools
Why use diamond
Diamond vs CBN (cubic boron nitride) Tools
What is Diamond Mesh Size and how to select best one for your application
What is Diamond Concentration and which to use for your application
Diamond Tool Coolants Why, How, When & Where to Use
Choosing The Correct Diamond Bond Type
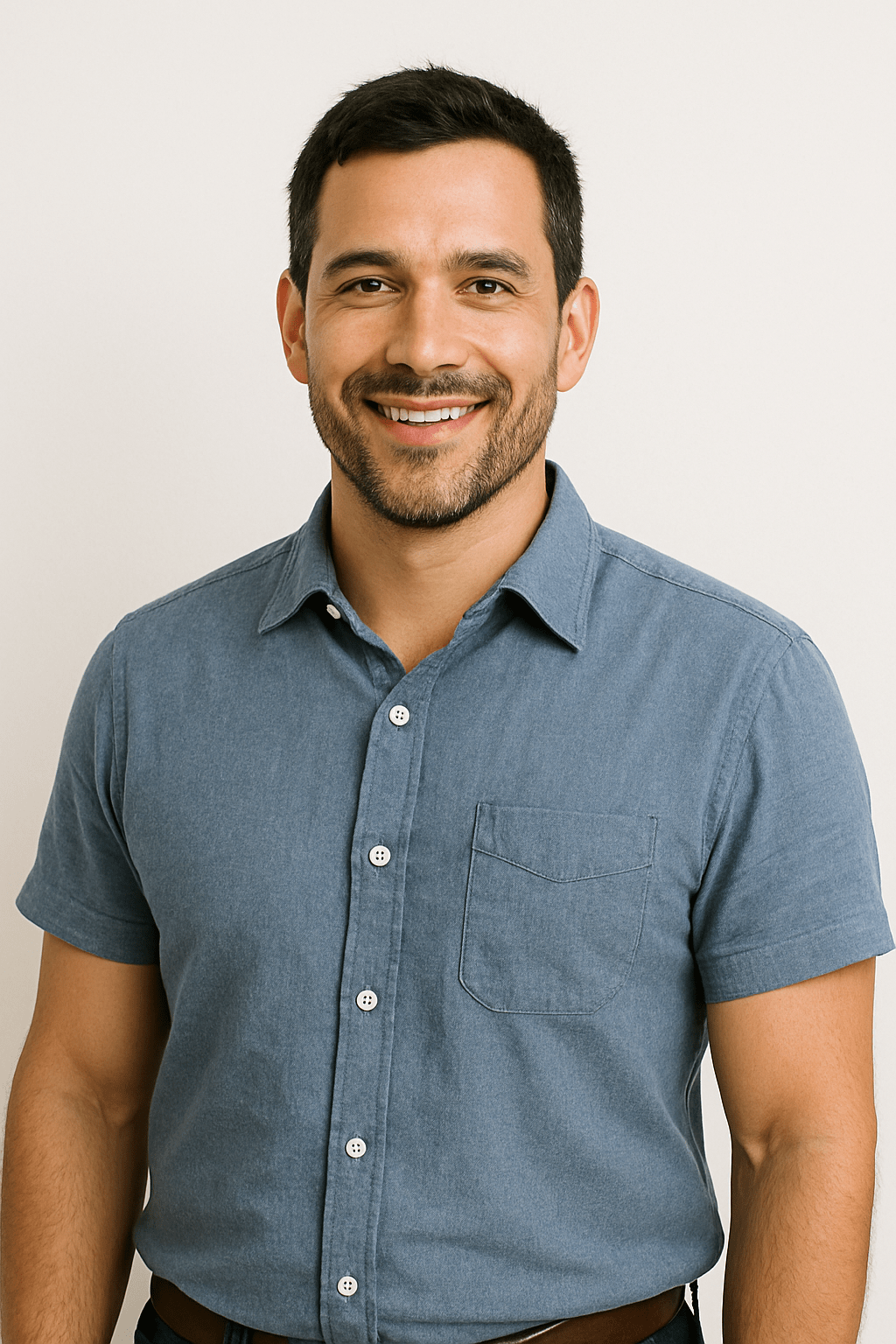
Carlos Sanchez is a senior technical specialist and field applications trainer with more than 17 years of experience in the use and optimization of industrial diamond tools, including ultra-thin diamond blades, core drills, and CBN grinding wheels. With a foundation in industrial engineering and technical operations, Mr. Sanchez has worked extensively with manufacturers and laboratories around the world, providing hands-on support and practical training for a wide range of cutting, grinding, and sample preparation applications.
Fluent in both English and Spanish, Carlos is known for his ability to translate complex tooling concepts into clear, actionable procedures for engineers, technicians, and production staff. His approach emphasizes real-world process improvement, tool longevity, and operator education—ensuring clients get the most out of their diamond tooling investments.
As an author, Mr. Sanchez shares field-tested insights on tool performance optimization, defect prevention, training methodologies, and troubleshooting common cutting issues.