Table of Contents
Toggle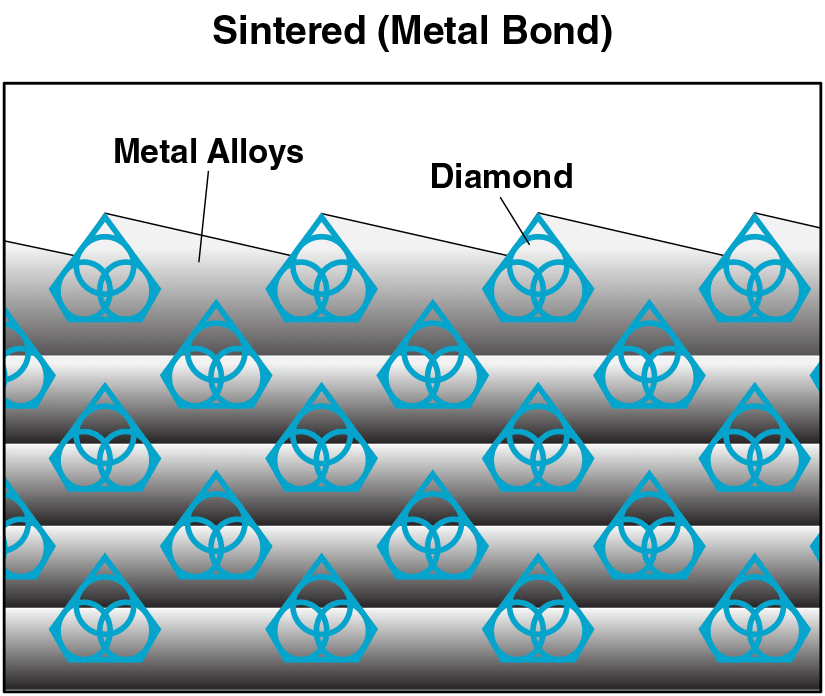
Sintered (Metal bonded) diamond tools have multiple layers of diamonds impregnated inside the metal matrix. Diamonds are furnaces sintered in a matrix made of iron, cobalt, nickel, bronze, copper, tungsten, alloys of these powders or other metals in various combinations. Metal Bonded Diamond Tools are “impregnated” with diamonds. This means that selected diamonds are mixed and sintered with specific metal alloys to achieve the best cutting performance possible on any materials such as sapphire, advanced ceramics, optics, glass, granite, tile and etc. The metal bond surrounding the diamonds must wear away to continuously keep re-exposing the diamonds for the diamond tool to continue cutting. Sintered (metal bonded) diamond tools are recommended for machining hard materials from 45 to 75 on Rockwell Scale (5 to 9.5 on mohe's scale of hardness).
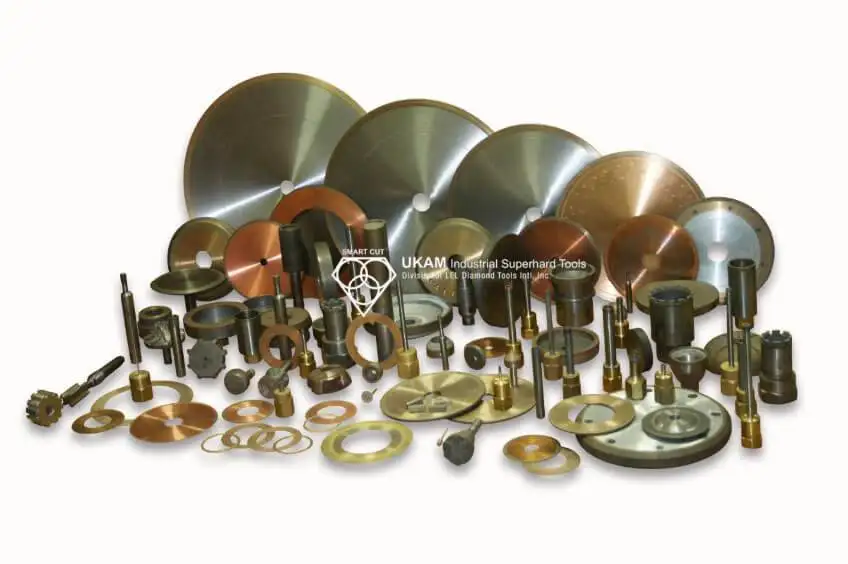
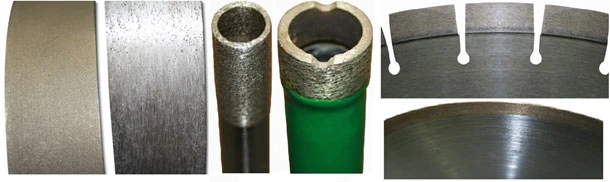
Sintered (Metal bond) diamond tools utilize various metallurgical powders to firmly keep the diamond crystals in place, with minimum wear. The compacted materials are then hot pressed or sintered to full density. Heating rate, applied pressure, sintering temperature and holding time, are all controlled according to the matrix composition.
This means that selected diamonds are mixed and sintered with specific metal alloys to achieve the best cutting performance possible large variety of materials. This bond type can utilize the highest quality and grade industrial diamonds (strong and blocky shape) monocrystaline particles. For this reason this bond family requires higher horsepower equipment and lower cutting speeds. Compared to their resin bond, nickel bond, braised bond, and vitrified bond counterparts. Sintered (Metal bond) is the strongest of all the bond families. Offering the longest life, greatest variety of specifications and fields of use available. While its not the optimum solution for all applications, Its one of the most widely used bond across most industries today.
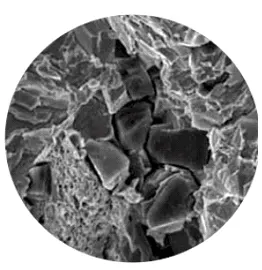
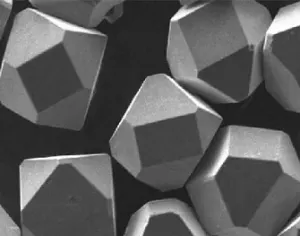
All types and forms of diamond tools are available with this bond matrix. Such as diamond wheels used for grinding, diamond cut off wheels use for cutting, slotting, grooving, diamond core drills and bits used for drilling, reaming and milling. Diamond router bits, carving points and form tools used for shaping and forming. Complex tool shapes can be made, angles and radiuses ground to fit customers objectives. High precision tolerances can be maintained through precision grinding of the tools faces. Large variety of diamond grit sizes from 20 to 600 mesh can be used in conjunction with diamond concentration as low as 12 to 100 con, along with different bond harnesses, bond matrixes, and diamond crystal types to achieve the clients desired surface finish, cutting speed, tool life and consistency.
Sintered Bond Families
The bond "matrix" is composed of various metal powders hot pressed together in a mold, under high pressure and high temperature usually ranging from 750 to 900°C. Sintered (metal bond) usually has (3) three bond families, which is based on main metallurgical powder used. The bond can be either
-
bronze based
-
cobalt
-
steel type (iron, tin, cobalt, etc)
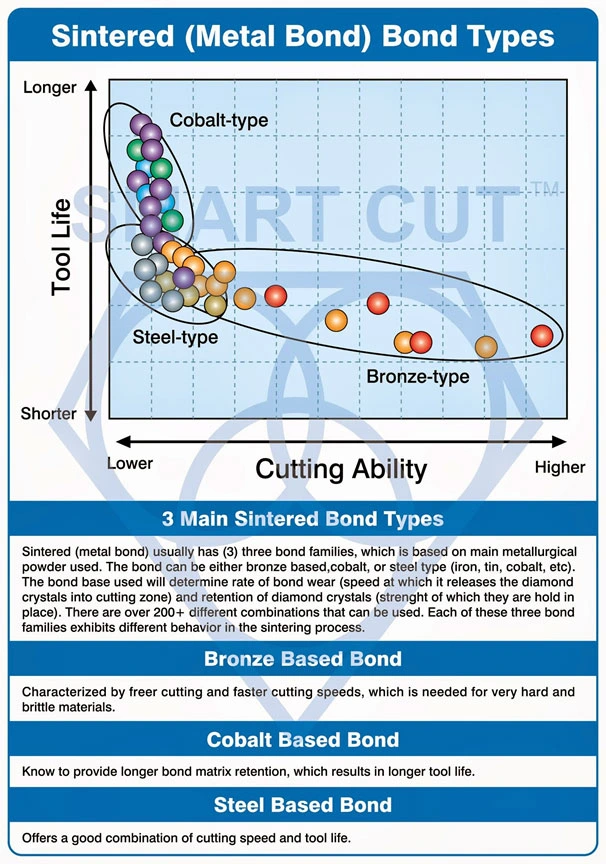
Bronze based bond
Characterized by freer cutting and faster cutting speeds, which is needed for very hard and brittle materials.
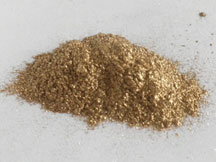
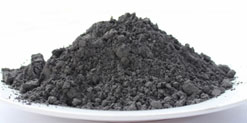
Cobalt based bonds
Know to provide longer bond matrix retention, which results in longer tool life. This type of bond is widely used for majority of stone and concrete applications (such as granite countertop fabrication, installation and construction materials). Majority of diamond tools, blades and bits readily available in stores are based on this bond structure.
Steel based bonds
Frequently between the two other bond families (middle of the road). Offering a good combination of cutting speed and tool life. Such bond family is frequently implemented in very abrasive material applications such as sandstone, alumina oxide, silicon carbide which wears most tools really fast.
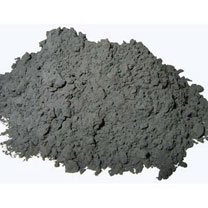
Other metallurgical powders (such as iron, copper tin, bronze alloys, tungsten, tungsten carbide, nickel alloys, silver, and many others) are used as additives or substitutes to provide forming characteristics, control rate of bond wear (speed at which it releases the diamond crystals into cutting zone) and retention of diamond crystals (strength of which they are hold in place). There are over 200+ different combinations that can be used. Each of these three bond families exhibits different behavior in the sintering process.
Its the job of the diamond tool manufacturer to select the right bond composition formula for the clients specific application, as well as clients specific objectives (surface finish, cutting speed, life), and usage environment (RPM's, equipment, coolant used, etc).
Technological Processes of producing Sintered (metal bond) Diamond Tools
Sintered (Metal Bond) Diamond Tools can be produced utilizing several processes. Depending on the type, application, and volume of the tools being produced. Some of these include:
-
normal sintering in a furnace with a sintering mould or in a continuous furnace
-
pressure sintering
-
hot isostatic pressing (HIP method)
pressure sintering is most widely used and preferred process today. Given this process flexibility/adoptability, capability to form and maintain complex shapes, ease of handling, high level of control of parameters and capability to do small batches and custom runs. In this process, the pre-pressed blank or the loose metallurgical powders that have been metered is brought to sintering temperature in a mould and compacted at the same time. This process utilizes a hydraulically operated press, which is usually equipped with a pyroscope or thermocouple to monitor the temperature cycle and time according to predetermined process.
To prevent melting loss on the graphite and oxidation of the metal powder, the equipment can be provided with a protective gas hood. The chamber is initially evacuated and subsequently flushed with an inert gas. Several extension stages also exist to provide varying degrees of automation.
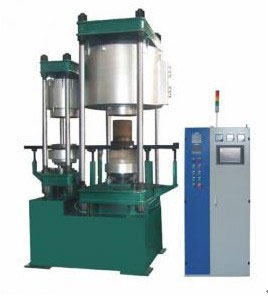
Cold Pressing Process
Depending on the process and types of tools produced, Cold Pressing is usually the first step of the production process. After all the powders used in the bond matrix have been dosed, granulated, and evenly spread in the mold cavity. They are cold pressed in order to obtain their sold shape/form, as well as to achieve desired density.
is extremely important that the generator power is adequate—too low generator power results in long heating times. In addition a lot of heat may migrate into the tool blank and cause stress (tension) problems. Correct frequency selection and generator heating power ensures that the heat is produced only in a limited space.
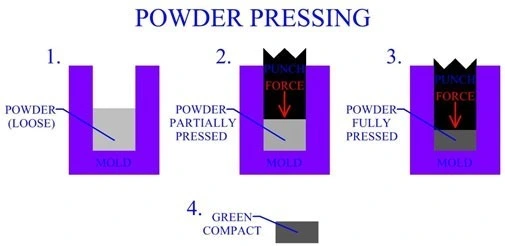
thermal stability of the diamond is obviously important in metal bonds. Low-temperature bonds, comprising cobalt, nickel, bronze, and/or iron (in low concentrations), or a combination of these metals, preserve the strength of the diamond crystals best. In addition, if not managed properly, the metal in the bond can catalyze back-conversion of the surface of the diamond to graphite, weakening retention in the bond. In many cases bond retention can be improved by the use of diamonds with coatings, particularly titanium or chromium. In contrast to coatings for resin bonds, coatings for metal bonds are quite thin, ≈ 1 µm, and form chemical bonds with both the diamond (as the metal carbide) and the metal matrix. Other bonding materials do not sinter well at temperatures below 900 °C, and in these cases the bond can be cold pressed and then infiltrated with molten metal (braze alloy) or hot-pressed above 1000 °C. If temperatures are too high or exposure times too long, the diamond impact strength will be reduced.
Customizing Sintered (Metal Bond) Diamond & CBN Tools
Customization of Sintered (Metal Bond) Diamond Tools for specific materials is a critical aspect of tool design and application, ensuring optimal performance, precision, and longevity. This process involves tailoring tool characteristics such as diamond grit size, concentration, bond hardness, and matrix composition to match the specific properties and requirements of the material being processed. Here's a detailed exploration of how these tools are customized for various materials:
1. Understanding Material Properties
-
Hardness and Abrasiveness: The hardness and abrasiveness of the material determine the diamond size and bond hardness. Harder materials require finer diamond grits with a harder bond to resist premature wear, while abrasive materials necessitate a softer bond for faster diamond exposure.
-
Brittleness: Brittle materials like certain ceramics or glass demand tools with a high diamond concentration to minimize chipping and ensure smooth cuts.
-
Thermal Conductivity: Materials with low thermal conductivity may require bonds that dissipate heat effectively to prevent thermal damage to the workpiece.
-
Machining Challenges: Heavier, denser materials may require more power to machine and can lead to increased tool wear.
2. Diamond Grit Size and Concentration
-
Fine Grits: Used for hard, brittle materials requiring high precision and minimal surface damage. Fine grits produce smoother finishes but at slower cutting speeds.
-
Coarse Grits: Ideal for softer, more abrasive materials where rapid material removal is prioritized over surface finish.
-
Diamond Concentration: Adjusting the diamond concentration allows for balancing between cutting speed and tool life. High concentrations improve tool longevity but may reduce cutting efficiency, while lower concentrations increase cutting speed but wear out the tool faster.
3. Bond Hardness and Composition
-
Hard Bonds: Suitable for abrasive materials as they wear slowly, continuously exposing new diamonds. Materials such as asphalt or green concrete often require tools with hard bonds.
-
Soft Bonds: Used for hard materials that can quickly wear down the diamonds. The softer bond matrix wears away quicker, ensuring new diamonds are exposed for consistent cutting performance.
-
Matrix Composition: The choice of metal alloy (e.g., bronze, cobalt, or iron-based) affects the tool's wear rate and cutting performance. Innovations in alloy compositions, including the use of hybrid and composite matrices, allow for nuanced adjustments to tool properties.
4. Tool Geometry and Design
-
Segmented vs. Continuous Rim: Segmented rims are preferred for cutting harder, denser materials, offering better cooling and debris removal. Continuous rims provide smoother cuts in brittle materials such as glass and tile.
-
Profile and Shape: Custom tool shapes and profiles are designed to meet specific application requirements, such as unique cutting angles, grooving, or profiling tasks. The geometry affects the stress distribution and cutting efficiency.
5. Application-Specific Considerations
-
Cutting Speed vs. Finish Quality: Depending on the application, tools may be optimized for fast cutting speeds or high-quality finishes. This involves trade-offs in diamond size, bond type, and tool geometry.
-
Wet vs. Dry Cutting: The choice between wet and dry cutting tools is determined by the material and cutting environment. Wet cutting tools, often required for materials prone to thermal damage, use water for cooling and dust suppression.
-
Equipment Compatibility: Customization also considers the power and specifications of the cutting equipment to ensure optimal tool performance and lifespan.
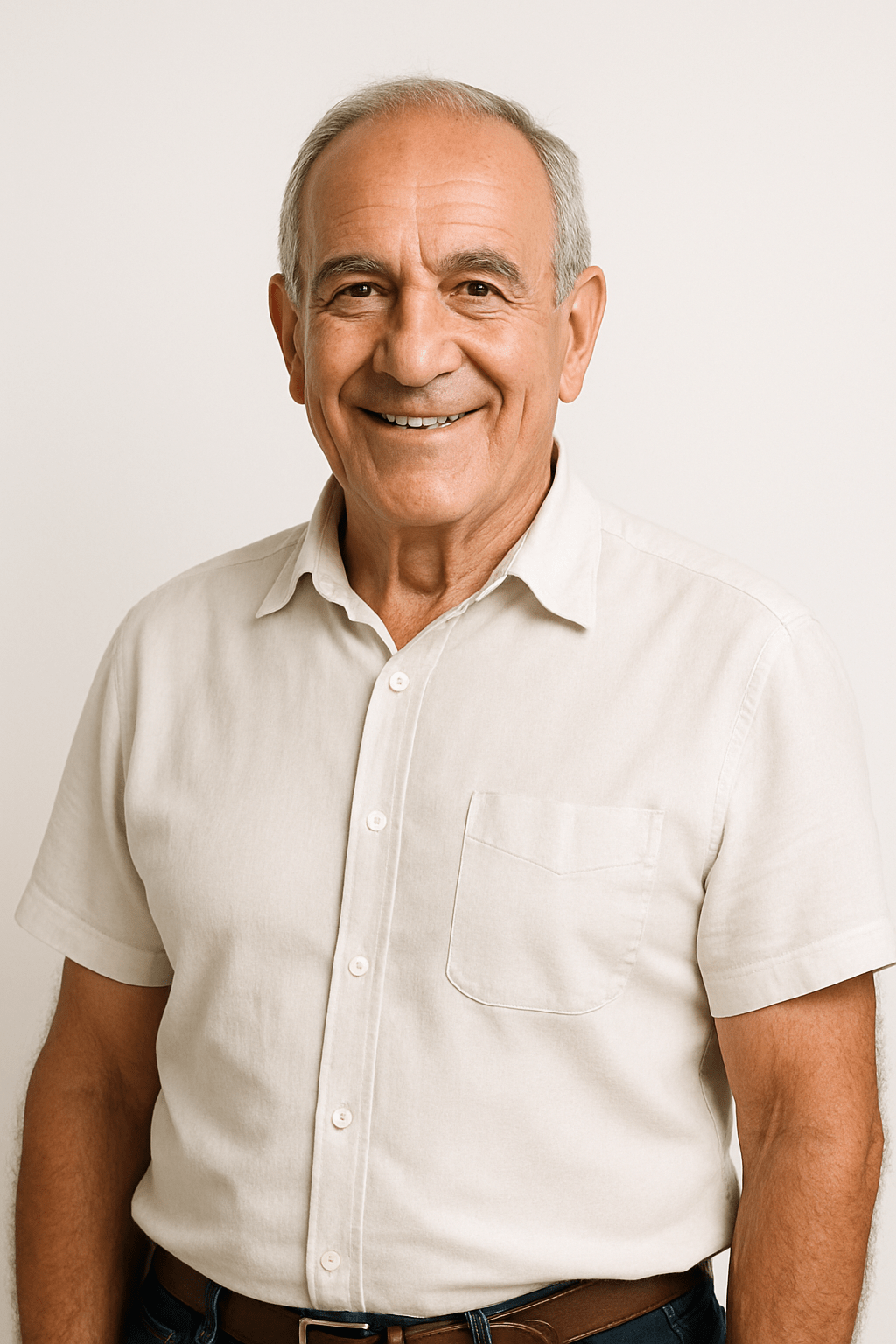
Leon Meyer is a veteran manufacturing engineer and technical consultant with over 50 years of experience in the development, implementation, and troubleshooting of industrial diamond tooling systems. Having spent his career at the intersection of tool design, precision manufacturing, and production engineering, Mr. Meyer is widely regarded as one of the most experienced voices in the application of ultra-thin diamond blades, sintered core drills, and CBN grinding wheels across heavy industry, advanced materials, and research sectors.
Known for his pragmatic, no-nonsense approach, Leon has advised manufacturers across the United States, Europe, and East Asia—helping streamline cutting processes, extend tool life, and solve complex issues related to material breakage, chipping, and tolerance drift. His expertise has directly contributed to improved production efficiency in industries ranging from aerospace alloys and technical ceramics to optics, composites, and high-nickel superalloys.
As an author, Mr. Meyer brings a lifetime of field knowledge to his writing, with a focus on real-world problem solving, cost-performance optimization, and tool reliability under demanding conditions.
ARE YOU USING RIGHT TOOLS
FOR YOUR APPLICATION?
LET US
HELP YOU
HAVING ISSUES WITH
YOUR CURRENT TOOLS?
Knowledge Center
How to Selecting Right Diamond Tools for your application
How to properly use Diamond Tools
Why use diamond
Diamond vs CBN (cubic boron nitride) Tools
What is Diamond Mesh Size and how to select best one for your application
What is Diamond Concentration and which to use for your application
Diamond Tool Coolants Why, How, When & Where to Use
Get to Know the Diamond Tool Bond Types and Which to use for your application
Choosing The Correct Diamond Bond Type
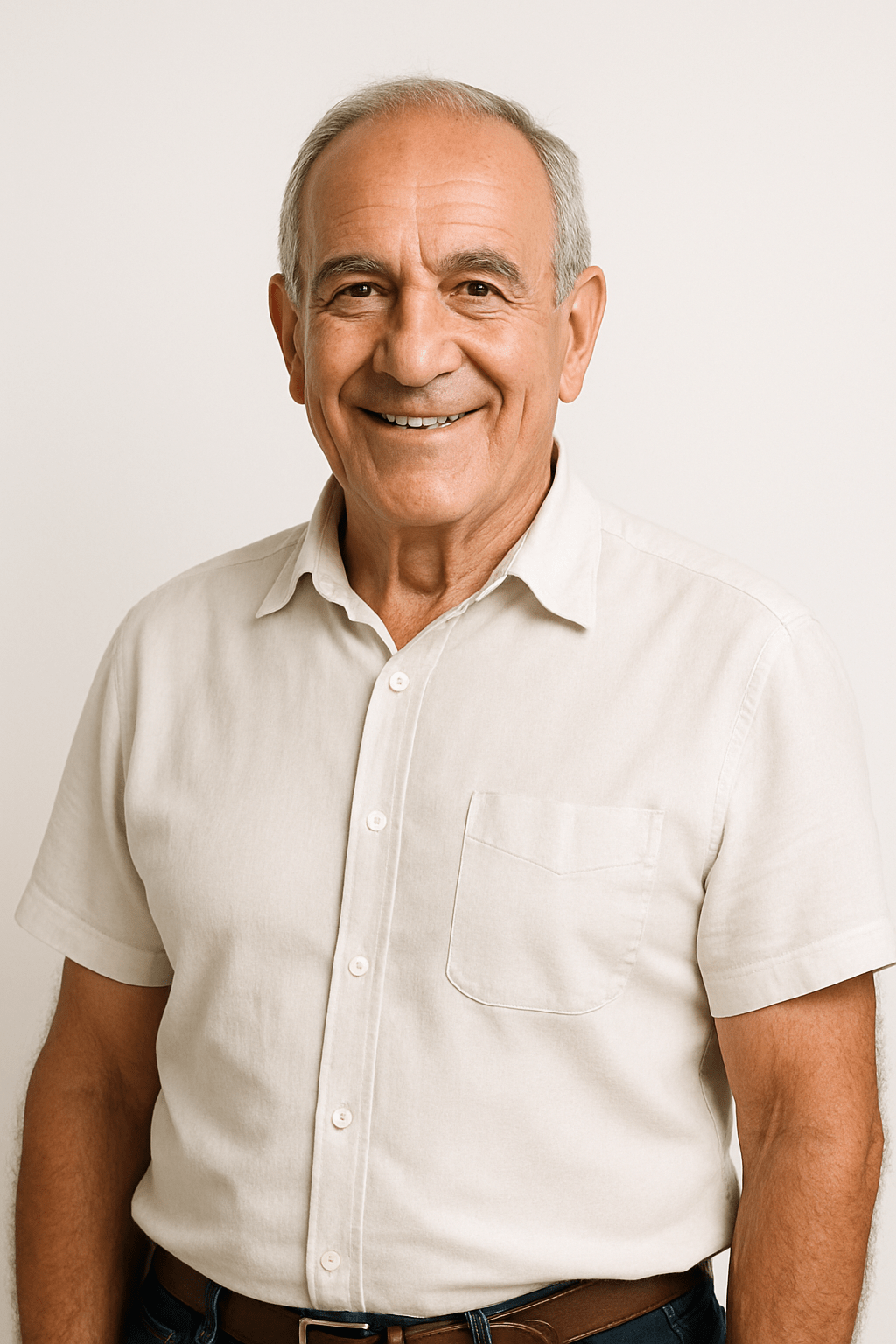
Leon Meyer is a veteran manufacturing engineer and technical consultant with over 50 years of experience in the development, implementation, and troubleshooting of industrial diamond tooling systems. Having spent his career at the intersection of tool design, precision manufacturing, and production engineering, Mr. Meyer is widely regarded as one of the most experienced voices in the application of ultra-thin diamond blades, sintered core drills, and CBN grinding wheels across heavy industry, advanced materials, and research sectors.
Known for his pragmatic, no-nonsense approach, Leon has advised manufacturers across the United States, Europe, and East Asia—helping streamline cutting processes, extend tool life, and solve complex issues related to material breakage, chipping, and tolerance drift. His expertise has directly contributed to improved production efficiency in industries ranging from aerospace alloys and technical ceramics to optics, composites, and high-nickel superalloys.
As an author, Mr. Meyer brings a lifetime of field knowledge to his writing, with a focus on real-world problem solving, cost-performance optimization, and tool reliability under demanding conditions.