Table of Contents
ToggleThe resin bond is an organic bond matrix formed through the application of high pressure and high temperature. The majority of resin bond diamond tools utilize phenolic resin as the bonding agent. Typically, this bond is cured at temperatures ranging from 150 to 200 degrees Celsius. Resin bonds are the softest among all bond types, making them ideal for applications requiring a smooth surface finish. They are widely used in grinding applications across a broad spectrum of materials.
One of the unique characteristics of the resin bond diamond matrix is its ability to wear down quickly, promoting the self-sharpening of the tool. As the bond wears, diamond particles are released from the matrix, allowing new, sharp diamond grains to be exposed. This self-sharpening property is particularly beneficial for efficiently cutting or grinding hard and brittle materials, making resin bond tools highly versatile.
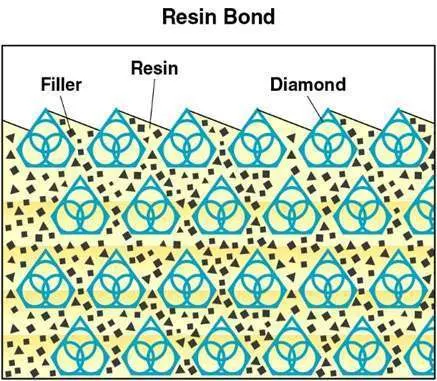
A key advantage of the resin bond is its ability to minimize chipping and, in many cases, eliminate the need for secondary finishing operations like grinding, polishing, or fire polishing. Resin bond diamond and CBN tools are particularly well-suited for applications where achieving a high-quality cut and surface finish is crucial. Compared to sintered (metal bond) tools, resin bond tools provide a significantly superior surface finish.
ADVANTAGES:
-
Unmatched Cut Quality (eliminates secondary finishing operations)
-
Faster & Freer Speed
-
Less Heat Generation than other bond types
-
Less Stress to material than other bond types
-
Will work the hardest material (even natural diamond)
-
Can be used dry (without coolant) when needed
-
Can withstand Higher Temperature than sintered (metal bond) tools
-
Perfect for fragile and delicate materials
-
Minimize Chipping, Improve Surface Finish, Minimize Material Deformation
BENEFITS:
-
Increase Tool Life
-
Reduce Chipping
-
Reduce Tool Wear
-
Increase Process Consistency
-
Maintain Consistent Cutting Speed
-
Reduce Blade Change & Mounting Cost
-
Reduce Cost
ADVANTAGES:
-
maximum cutting performance
-
no glazing
-
faster cutting action
-
improved surface finish qualityy
-
better coolant retention
-
No Material Deformation
-
No Contamination
-
Longer Life than any other Resin Bond Tools in Industry
-
Self-sharpening matrix
-
Superior cut quality
-
The widest variety of bond matrixes
The application range for resin bond diamond and CBN tools includes cutting, grinding, and polishing hard, brittle, or delicate materials, especially where low heat generation or enhanced surface quality is required. CBN resin bond tools are specifically recommended for cutting and grinding hard steels above Rc 60 at high speeds, offering efficient performance and excellent surface finishes.
Example of Applications Resin Bond Diamond Tools are Used:
-
ceramics
-
glass tubing
-
optical glass
-
carbides
-
composites
-
semiconductor materials
-
magnetic materials
-
exotic metals
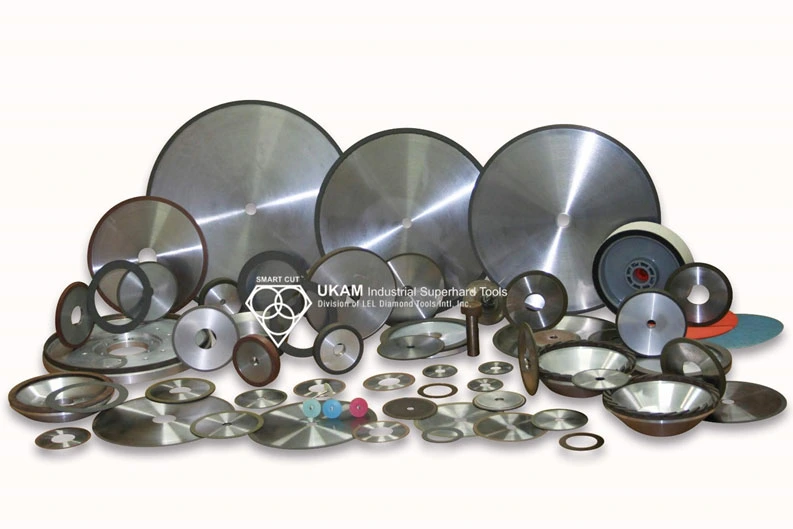
Best Cut Quality & Surface Finish
Resin bond diamond and CBN tools are designed to deliver exceptional cut quality and surface finish, making them highly recommended for applications where these attributes are critical. Compared to sintered (metal bond) tools, resin bond tools provide a significantly superior surface finish.
They are ideal for cutting, grinding, and polishing a range of hard, brittle, or delicate materials, such as ceramics, glass tubing, optical glass, carbides, composites, and exotic metals, especially when low heat generation or enhanced surface finish is desired. To achieve optimal performance, these tools should be used at higher speeds. CBN resin bond tools, in particular, are recommended for cutting and grinding hard steels with a hardness above Rc 60 at high speeds.
The performance of resin bond tools is influenced by the controlled use of various organic and inorganic fillers, including ceramic and metallic powders, which adjust properties like hardness, wear resistance, heat resistance, diamond crystal retention, and lubrication. With a low Young’s modulus, resin bonds exhibit "free-cutting" characteristics, contributing to faster cutting speeds, superior surface finish, and minimal chipping. These properties make them effective for achieving efficient material removal while maintaining an excellent surface finish.
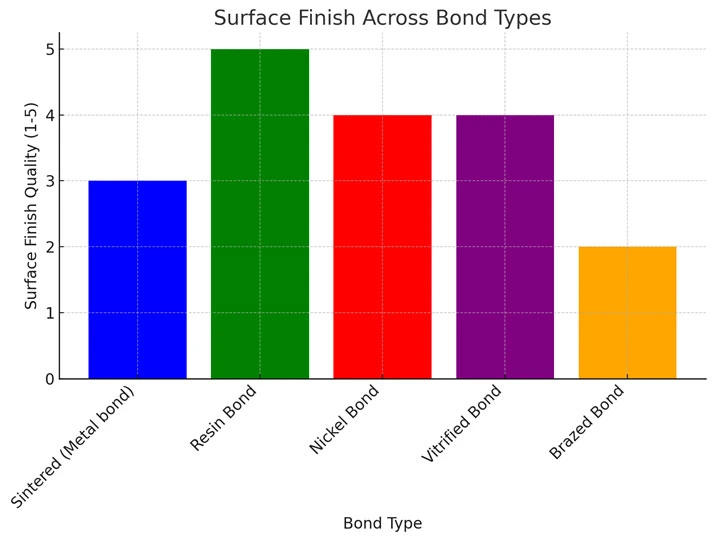

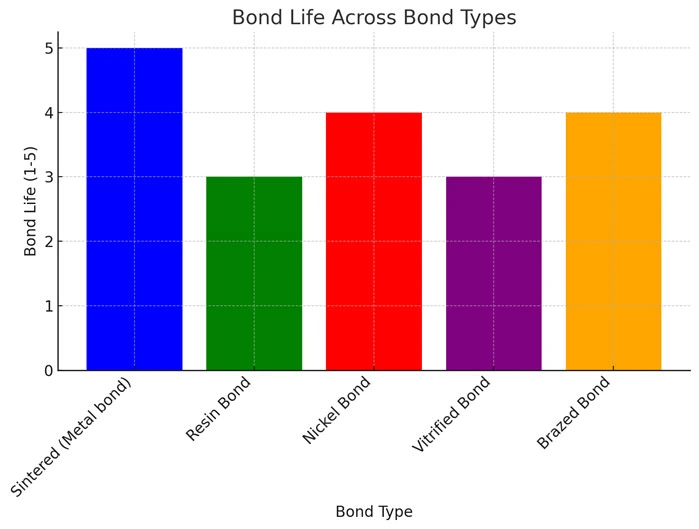
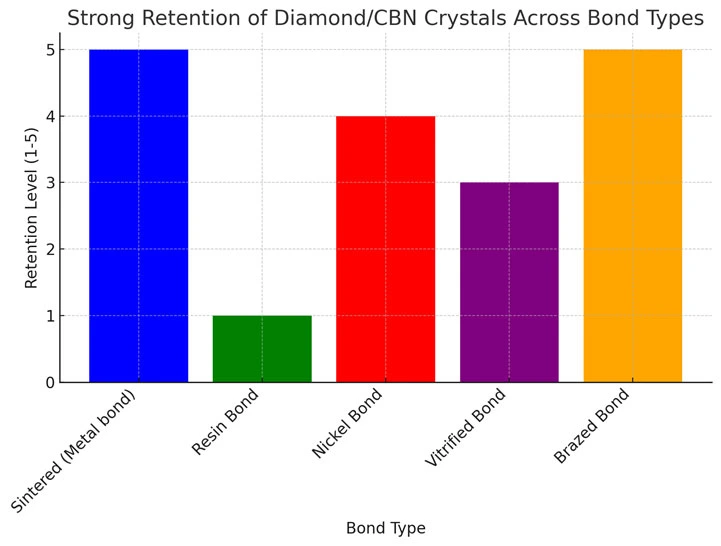
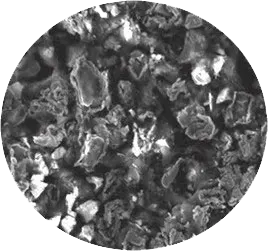
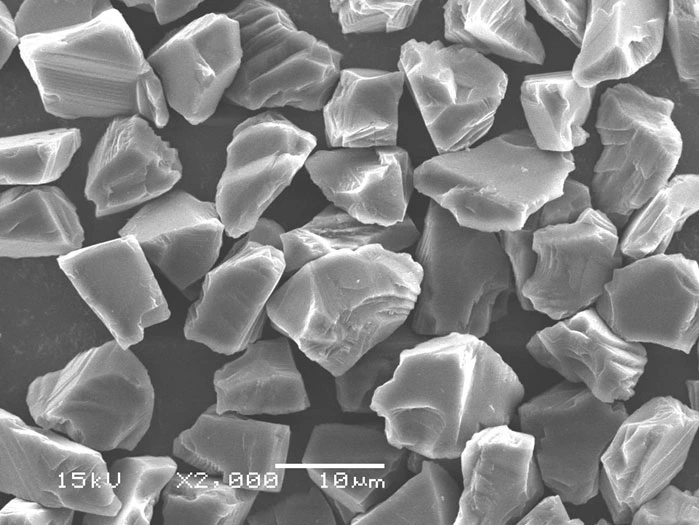
Diamond Type Used for Resin Bond Diamond Tools
The diamond and CBN crystals used in resin bond tools differ significantly from those used in metal bond tools. Typically, resin bond diamond tools utilize polycrystalline, low-strength, metal-clad diamond crystals. These crystals are irregular in shape and prone to micro-fracturing, which promotes the creation of new cutting edges during use. This continual renewal of sharp edges provides the self-sharpening characteristic that resin bond tools are known for. The preference for metal-coated and unevenly shaped diamond crystals enhances retention within the bond, further improving tool performance and longevity.
Resin bond diamond tools are most often used with a coolant to improve performance and reduce heat build-up; however, they can also be effectively used dry for certain applications. The incorporation of specialized fillers or the use of specifically coated diamond crystals can aid in reducing heat generation, making these tools versatile across a range of cutting, grinding, and polishing operations.
Resin Bond Diamond Tools Composition
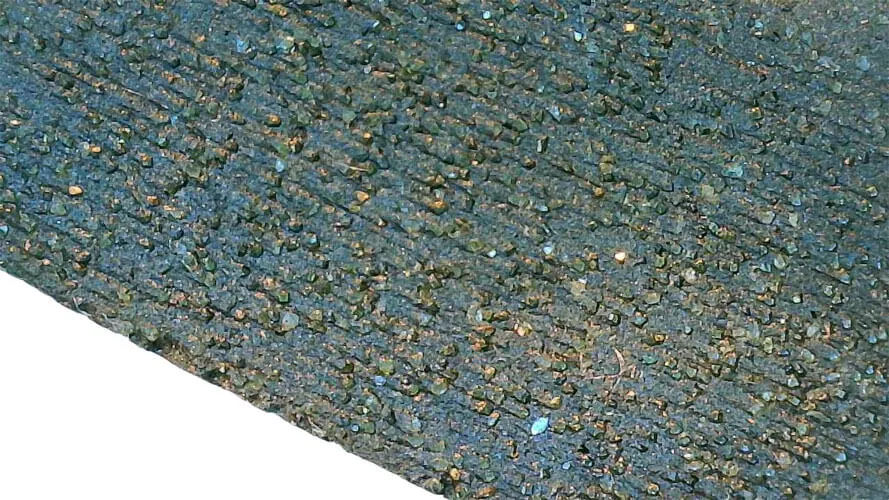
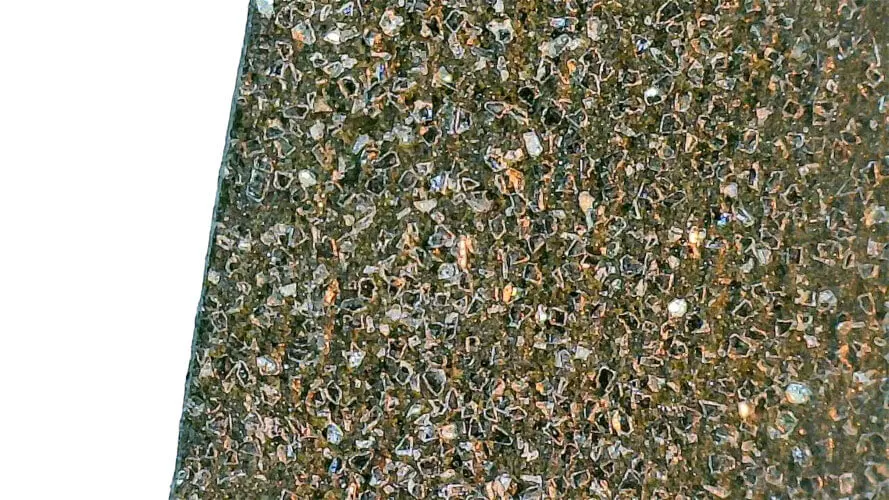
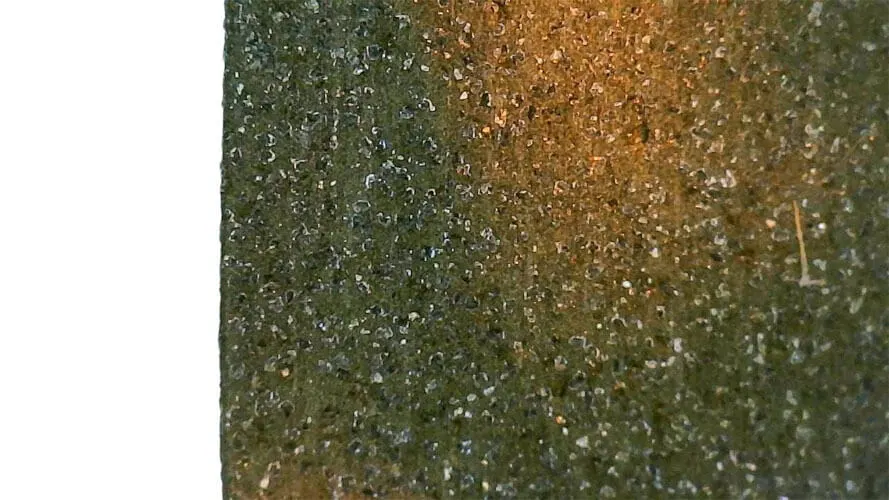
The majority of resin bond diamond tools are composed of phenolic resins or thermally stable phenol aralkyl resins. These resins, used in the form of fine powder, make up about 30% to 40% of the bond in both dry and wet diamond wheels. To enhance the bond's strength, the resins are mixed with fillers such as aluminum oxide or silicon carbide. Additionally, various additives like oxide-based drying agents, graphite, or polytetrafluoroethylene (PTFE) lubricants, and powders of aluminum, copper, or silver are incorporated in small amounts. These additives play a crucial role in reducing frictional heat generated during cutting and improving heat dissipation.
The structure of resin bond diamond and CBN tools is carefully designed to achieve a balance between performance and durability. The components and manufacturing processes are tailored to optimize the functionality and efficiency of the tools, providing advantages over other bond types.
Abrasive Grains (Diamond or CBN): The primary component of these tools is the abrasive grains—either diamond or CBN. Diamond crystal are best suited for non-ferrous, ultra-hard, and brittle materials like glass, ceramics, and composites. In contrast, CBN is ideal for grinding ferrous materials, including hardened steels, cast irons, and superalloys, due to its superior thermal stability and resistance to oxidation. The selection of the size, concentration, and type of abrasive grains is based on the material being processed and the desired cut quality.
Resin Bond Matrix
The bond matrix is made up of synthetic resin, primarily phenolic or polyimide, which binds the abrasive grains together. These resins are chosen for their flexibility, strength, and capability to support the self-sharpening mechanism of the abrasive grains. The resin bond determines key performance characteristics such as hardness, wear resistance, and cutting efficiency. A softer bond facilitates rapid material removal and higher cutting rates, whereas a harder bond ensures prolonged tool life and precision in surface finish.
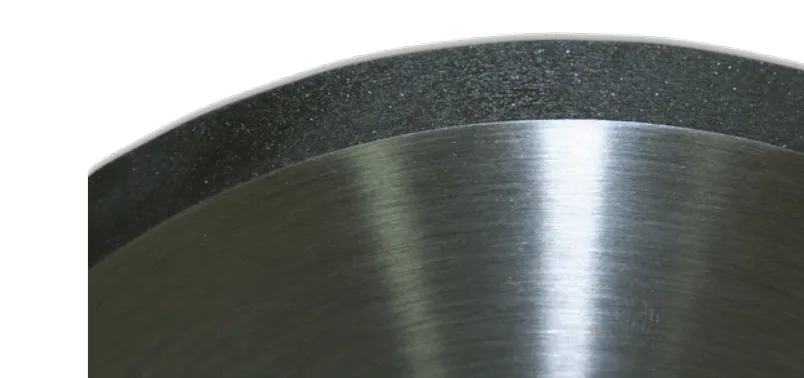
Fillers and Additives:
Fillers and additives are integrated into the resin bond matrix to enhance performance and regulate heat generation during cutting or grinding. These materials can modify the bond’s properties, adjusting hardness, promoting heat dissipation, and increasing wear resistance. Some fillers improve the flow properties of the resin during manufacturing, while others enhance grinding efficiency by reducing friction and improving chip clearance.
Reinforcement Materials For applications requiring greater strength and durability, reinforcement materials such as fibers, copper, or bronze can be added to the bond. These reinforcements contribute to the tool's overall strength, rigidity, and resistance to deformation, enabling it to handle higher grinding forces and temperatures without compromising performance.
Example of Fillers Used for Resin Bond Diamond Tools:
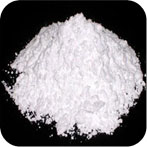
Alumina Oxide
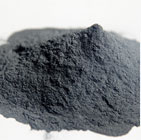
Silicon Carbide
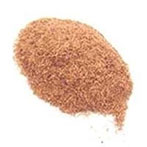
Silicon Carbide
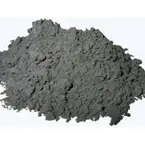
Silicon Carbide
How Resin Bond Diamond Tools are Manufactured

Manufacturing resin bond diamond and CBN tools involves a detailed, multi-step process designed to optimize performance and meet application-specific needs. The aim is to achieve the correct balance between bond strength, flexibility, abrasive concentration, and tool geometry, ensuring high efficiency in cutting, grinding, and shaping various materials.
The fundamental components of these tools are the abrasive grains—diamond or CBN—selected based on the material being processed. Diamond is the preferred choice for non-ferrous, ultra-hard, and brittle materials like ceramics, glass, and composites. Conversely, CBN is better suited for grinding ferrous metals, such as hardened steels, cast irons, and superalloys, due to its superior thermal stability and oxidation resistance. The chosen grain size, type, and concentration directly influence cut quality, tool durability, and efficiency.
How SMART CUT® Resin Bond Works?
The sharpest and finest quality diamonds or CBN crystals that go into a SMART CUT® Diamond Resin Bond, immediately penetrate into the material, grinding and polishing as they cut.
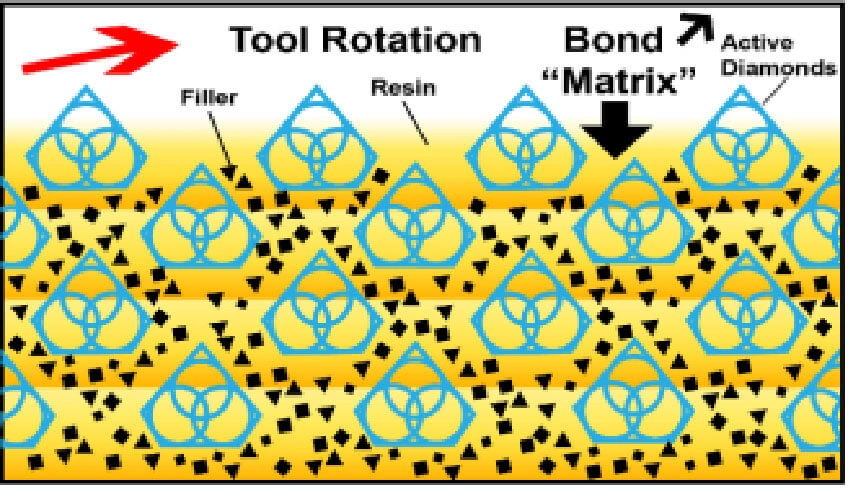
Diamonds or CBN Crystals are activated only at the exposed layer. As Bond Matrix layer begin to wear out, diamonds in a new Bond Matrix layer are immediately activated, substituting the already used up diamond layer. The SMART CUT® Diamond Resin Bond makes sure every diamond is in the right place and at the right time, working where you need it most.
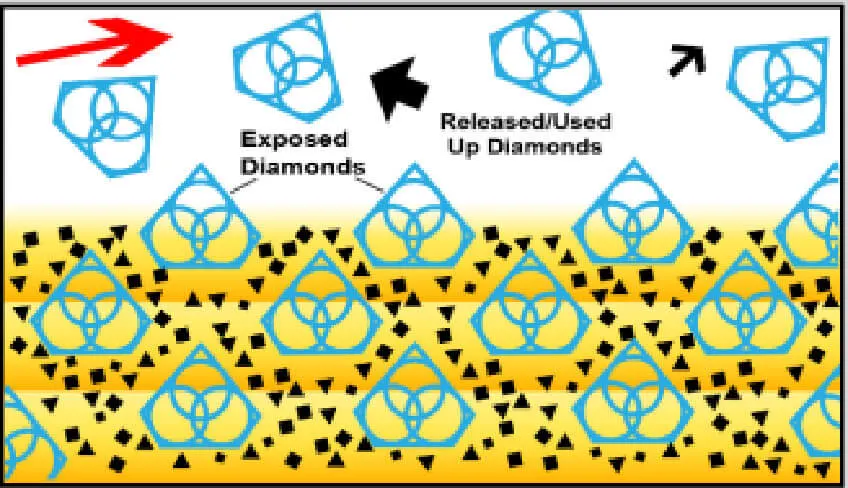
The newly exposed diamonds don't effect diamonds already working on the material. Unlike many other diamond bonds, diamonds in a SMART CUT® Resin Bond remains sharp and grow sharper with each cut, prolonging product life and consistent performance.
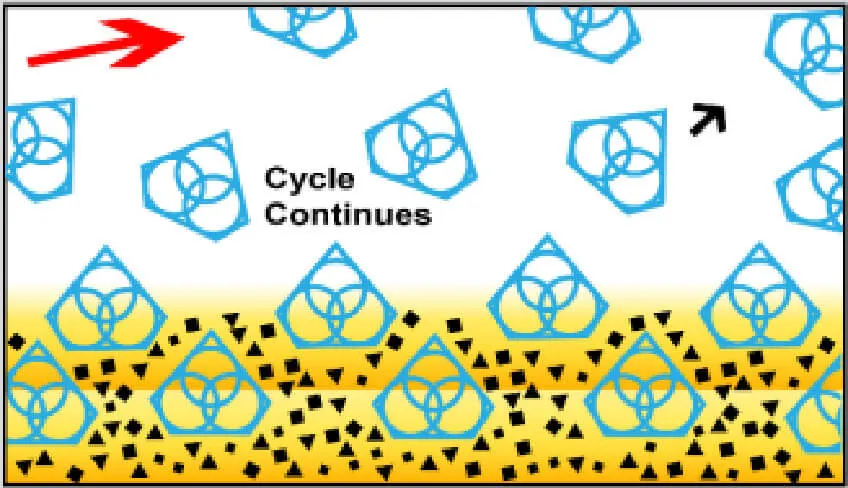
This advanced formulated open diamond bond design insures minimal chipping, fast cut, constant speed of cut, minimal cutting noise, and most important of all, consistent performance.
The resin bond matrix serves as the binding agent and is often made from phenolic or polyimide resins. Compared to other bonds like metal or vitrified, the resin bond is softer and more flexible, allowing for the self-sharpening characteristic of the tool, as the resin wears away to expose fresh abrasive particles. Softer bonds promote rapid material removal, while harder bonds provide a precise finish and extended tool life.
Fillers and additives play a significant role in adjusting bond properties and enhancing performance. To improve heat dissipation, reduce friction, and optimize chip clearance, fillers such as metal powders, graphite, and other compounds are added. Additionally, in some cases, reinforcement materials like fibers, copper, or bronze are incorporated to boost the tool's strength, rigidity, and resistance to deformation, allowing it to withstand intense grinding forces and higher temperatures.
The manufacturing process begins with mixing and blending the abrasive grains, resin powders, fillers, and reinforcements to achieve an even distribution. This uniformity is vital for consistent performance and tool longevity. The blended mixture is then shaped into a mold corresponding to the final tool design, whether a wheel, blade, or disc, and pressed to compact the components. Pressing can be either cold or hot, with the goal of achieving the appropriate density and bonding between the resin and abrasive grains.
After pressing, the tool undergoes a curing process in a controlled furnace or oven. The tool is heated to specific temperatures to harden the resin bond, ensuring a secure hold on the abrasive grains and establishing the desired strength and flexibility. Once cured, the tool may require finishing processes such as trimming, grinding, or dressing to achieve precise dimensions and surface quality. The tool then undergoes thorough quality checks to verify bond integrity, abrasive concentration, and performance during cutting or grinding.
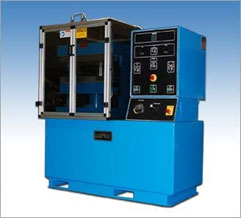
Hot Pressing Process and Mechanical Keying
One method employed in the manufacturing of resin bond diamond tools is hot pressing. In this process, the mix of abrasive grains and resin bond can be directly pressed onto the tool hub, which often contains undercuts or surface irregularities along its circumference. These undercuts act as mechanical keys, enhancing the bond between the resin and the hub and thereby improving the overall structural integrity of the tool. This mechanical keying ensures that the abrasive layer remains securely attached during high-speed cutting operations, minimizing the risk of bond delamination or tool failure.
Diamond Concentration and its Impact
The concentration of diamond within the resin bond tool is another critical factor influencing its performance. This concentration typically ranges from 50 to 125, translating to approximately 12.5% to 31.25% by volume of abrasive content. The higher the concentration of diamond particles, the more aggressive and durable the cutting action, making it suitable for challenging applications that demand rapid material removal and extended tool life. Conversely, lower concentrations are ideal for applications that require a finer finish and less aggressive cutting. Therefore, manufacturers carefully select the concentration of diamond based on the specific material being processed and the required cut quality, feed rate, and tool lifespan.
Metal Clad Diamond for Enhanced Performance
To further enhance the tool’s cutting efficiency and longevity, most resin bond diamond tools utilize metal-clad diamond. Metal cladding involves coating the diamond particles with a thin layer of metal, which can include nickel-based alloys, copper, or silver. Nickel-clad diamonds are the most commonly used, typically containing between 30% to 60% by weight of the nickel alloy. The nickel coating may feature a rough, spiky surface to improve the retention of the diamond particles within the resin bond matrix. This textured surface enhances the mechanical locking of the diamond grains, providing excellent resistance to dislodgment during severe cutting or grinding conditions. Moreover, the metal cladding improves heat dissipation, thereby reducing thermal damage to both the tool and the workpiece, which is particularly important during high-speed and high-pressure operations.
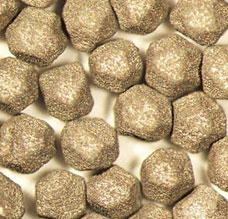
The Role of the Resin Bond Matrix
The resin bond matrix acts as the binding agent that holds the abrasive grains together. Composed of synthetic resins—most commonly phenolic or polyimide—the bond is designed to be flexible, yet durable, allowing for self-sharpening of the abrasive grains. When the grains wear down, the resin bond gradually breaks away, exposing fresh cutting edges to maintain consistent performance. The resin bond can be engineered for different hardness levels depending on the specific application. Softer resin bonds promote fast cutting and higher material removal rates, whereas harder bonds are used for precision work and to achieve superior surface finishes.
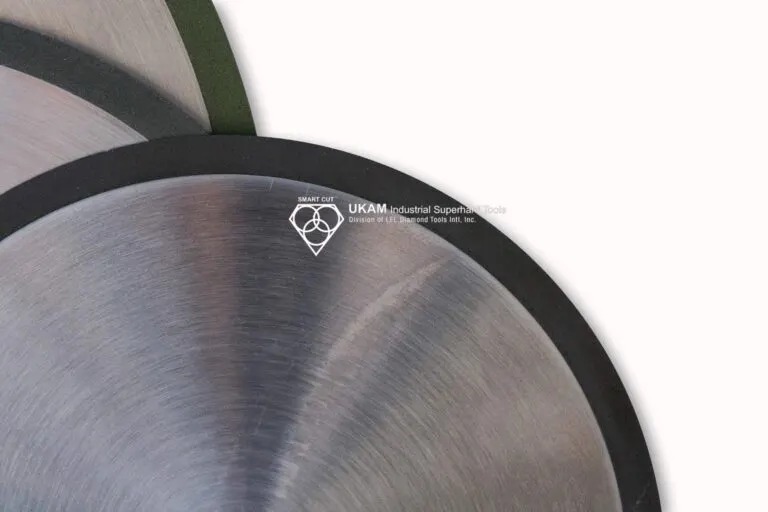
Fillers, Additives, and Reinforcements
The resin bond is often enhanced with fillers, additives, and optional reinforcement materials. Fillers can serve several purposes, such as controlling the hardness of the bond, improving heat dissipation, and modifying the cutting behavior to achieve specific results like reduced friction or optimized chip clearance. Reinforcement materials such as fibers, copper, or bronze may be added to improve the overall strength and rigidity of the tool. These reinforcements enable the tool to endure high grinding forces and temperatures, making it suitable for heavy-duty applications without deforming or wearing prematurely.
Manufacturing Steps: Mixing, Molding, and Curing
The manufacturing process begins with the precise mixing and blending of all components, ensuring even distribution of the abrasive grains, resin bond, fillers, and any reinforcements. Consistency in mixing is crucial, as it directly impacts the tool's performance, cutting behavior, and longevity. The mixed compound is then transferred to a mold corresponding to the desired shape of the tool, whether it be a wheel, blade, or disc.
Pressing the mixture into shape can be achieved through either cold or hot pressing, depending on the type of resin used. In hot pressing, the mixture is compacted under high pressure and elevated temperatures to achieve the required density and bond strength. This process not only shapes the tool but also enhances the bond between the resin and the abrasive grains, resulting in a tool with optimal performance characteristics.
Following the pressing stage, the tool undergoes a curing process, which involves heating it in a controlled furnace or oven to solidify the resin bond. The temperature and duration of the curing process are precisely managed to ensure that the bond hardens properly and securely holds the abrasive grains. The curing process imparts the necessary strength, flexibility, and self-sharpening properties to the resin bond, which are crucial for the tool's performance in its final application.
Finishing and Quality Control
Once the tool has been cured, it may require additional finishing processes such as trimming, grinding, or dressing. These steps ensure that the tool achieves its precise dimensions, balance, and surface quality. The finishing process is crucial to remove any irregularities or excess material that could hinder performance or cause instability during operation.
Before the tool is released for industrial use, it undergoes rigorous quality control and performance testing. These tests include checking the integrity of the bond, the concentration and distribution of abrasive grains, and the tool's dimensional accuracy. Performance tests often simulate real-world cutting or grinding conditions to ensure the tool meets the required specifications, such as cut quality, surface finish, and efficiency.
Tailored Manufacturing for Application-Specific Performance
The manufacturing process of resin bond diamond and CBN tools is highly customizable, allowing us to tailor tools to meet the specific needs of various applications. This level of customization encompasses everything from the selection of abrasive grain size, type, and concentration, to the formulation of the resin bond matrix and inclusion of additives. By fine-tuning these elements, manufacturers can produce tools optimized for a wide range of material processing tasks, from aggressive cutting to precision grinding. Whether for applications requiring rapid material removal or those demanding a flawless surface finish, resin bond diamond and CBN tools can be designed to deliver superior performance and extended tool life.

Through the careful selection of components and control over the manufacturing process, these tools achieve a balance between durability, efficiency, and precision, ensuring that they meet the highest standards for their respective industrial applications.
Compression Molding Process for Manufacturing Resin Bond Diamond & CBN Tools
Compression molding is a widely used technique in the manufacturing of resin bond diamond and CBN tools. It involves placing the mixed abrasive compound into a mold and then applying heat and pressure to shape and cure the tool simultaneously. This process not only ensures the tool’s proper shape and density but also enhances the bond between the abrasive grains and the resin matrix, contributing to the tool’s overall performance and longevity.
In compression molding, the mixture of abrasive grains (diamond or CBN), resin powders, fillers, and any reinforcement materials is carefully measured and poured into a mold that has the desired shape and size of the final tool. The mold is then closed, and high pressure is applied, compacting the mixture into the mold’s shape.
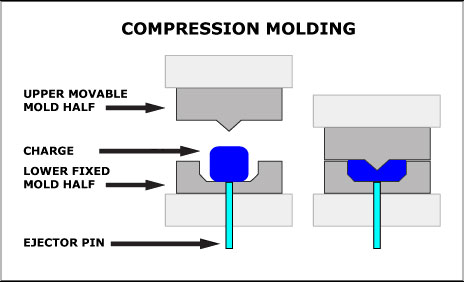
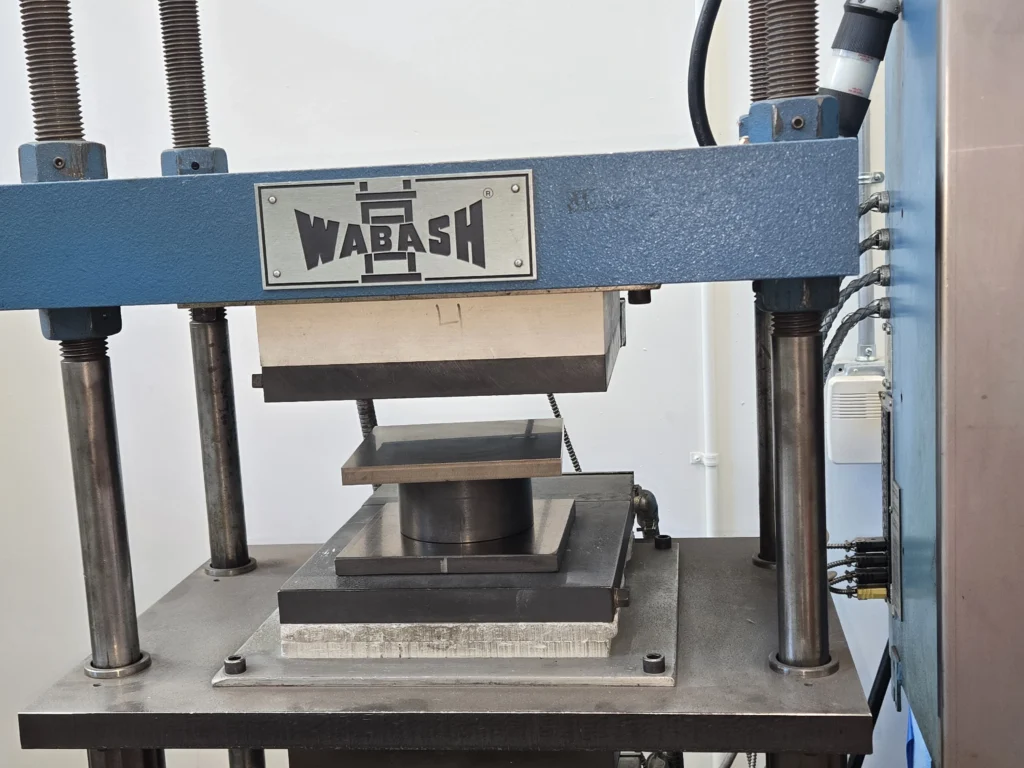
During the pressing phase, heat is applied to the mold, causing the resin bond to soften and flow, filling in any cavities and gaps between the abrasive grains. The combination of heat and pressure during compression molding is essential, as it ensures uniform distribution of the bond throughout the tool and securely binds the abrasive particles.
The benefits of using compression molding in manufacturing resin bond tools are numerous:
Improved Density and Strength - Compression molding allows for high compaction of the resin bond and abrasive mixture, resulting in a dense and durable structure. This density ensures that the tool has a consistent material composition, leading to greater strength and enhanced cutting or grinding efficiency. The high-density structure also minimizes porosity, which can improve the overall lifespan and stability of the tool during use.
Enhanced Mechanical Keying and Abrasive Retention - The pressure applied during the molding process promotes superior mechanical bonding between the abrasive grains and the resin matrix. If the diamond or CBN particles are metal-clad (nickel, copper, or silver coating), the heat and pressure also help to embed the abrasive more effectively into the bond. This mechanical keying enhances abrasive retention, which is critical for withstanding high forces and temperatures during aggressive cutting or grinding operations, and prevents premature dislodging of the abrasive grains.
Consistent and Precise Shaping - Compression molding enables precise control over the tool’s shape, size, and dimensions. The mold defines the final geometry of the tool, and the uniform pressure applied ensures that the tool’s form is accurate and consistent, which is particularly important for precision tools like diamond grinding wheels or ultra-thin cutting blades. The controlled environment during compression molding allows for the creation of complex shapes and profiles that may not be easily achieved through other manufacturing processes.
Reduced Curing Time and Improved Bond Strength - Since the application of heat and pressure happens simultaneously during compression molding, the curing process is typically faster compared to traditional cold pressing methods followed by separate curing. This reduces production time and enhances the strength and flexibility of the resin bond, allowing for a tool with high performance and durability. The simultaneous curing process also ensures that the bond cures uniformly, which contributes to better mechanical properties and tool consistency.
Process Control and Customization - Compression molding offers a high degree of customization over the final properties of the resin bond diamond or CBN tool. By controlling the temperature, pressure, and duration of the molding process, manufacturers can fine-tune the tool’s bond characteristics, such as hardness, wear resistance, and flexibility. For instance, applying higher pressure can result in a denser tool for aggressive grinding, while lower pressure can produce a softer bond for applications requiring a smoother surface finish. Temperature adjustments can also affect the bond's flow and setting, optimizing performance for specific applications.
Suitable for High-Volume Production - Compression molding is efficient and suitable for high-volume production, allowing multiple tools to be manufactured simultaneously. Molds can be designed to produce several tools at once, ensuring uniformity across batches and significantly improving manufacturing efficiency. This makes the process cost-effective for both large-scale production runs and smaller batches requiring high precision and quality control.
Integration with Hot Pressing Techniques - Compression molding is often integrated with hot pressing, where the mix is pressed under high temperatures to achieve a high-density bond. This method allows for direct bonding of the abrasive layer onto the tool’s hub (if present), which is advantageous for grinding wheels or cutting discs that require a strong, integrated hub structure. The hub, often made with undercuts or irregularities, helps to improve mechanical keying and overall tool stability.
Aspect |
Hot Pressing |
Compression Molding |
---|---|---|
Purpose |
Shape, compact, and cure simultaneously |
Primarily for shaping, followed by curing |
Temperature Range |
Higher temperatures (160°C - 250°C+) |
Lower temperatures; heat may be optional |
Pressure Applied |
High pressure (up to 200 MPa or more) |
Moderate pressure |
Curing Process |
Curing occurs during pressing |
Separate curing step often required |
Tool Properties |
Dense, uniform, high strength |
Variable density, potentially lower strength |
Production Time |
Faster cycle time due to simultaneous steps |
Longer cycle time due to separate curing |
Application |
Precision, high-performance tools |
General-purpose shaping, less precision |
Resin Bond Diamond Tools Manufacturing Variables:
Manufacturing resin bond diamond tools involves a variety of critical variables that must be carefully controlled to produce a tool optimized for its intended application. Each variable plays a significant role in determining the final tool’s performance, longevity, and overall effectiveness in cutting, grinding, or polishing. Here is an in-depth look at some of the most important variables that influence the manufacturing process and the properties of resin bond diamond tools:
-
Diamond Type Used
-
Diamond Concentration
-
Pressure Used
-
Temperature Used
-
Curing Cycle Time
-
Fillers Used
-
Bond Formula (proportion of components)
Diamond Type Used
The type of diamond used in resin bond tools greatly impacts cutting efficiency, durability, and surface finish. Diamond particles come in different grades, shapes, and qualities, and they are selected based on the specific material to be processed. Common types include:
-
Monocrystalline Synthetic Diamonds: These diamonds are tough, have high thermal stability, and provide effective cutting for hard, brittle materials like ceramics, glass, and stone.
-
Polycrystalline Diamond (PCD): PCD features a microstructure with multiple cutting edges that result in a self-sharpening action, making them suitable for aggressive grinding and applications requiring enhanced surface finish.
-
Metal-Clad Diamonds: Diamonds coated with a thin layer of metal (nickel, copper, or silver) offer improved heat dissipation, wear resistance, and bonding with the resin matrix, especially under severe cutting conditions.
The choice of diamond type depends on the workpiece material, desired tool lifespan, and quality of the finish. A proper selection can enhance tool performance and optimize the balance between cutting speed and wear resistance.
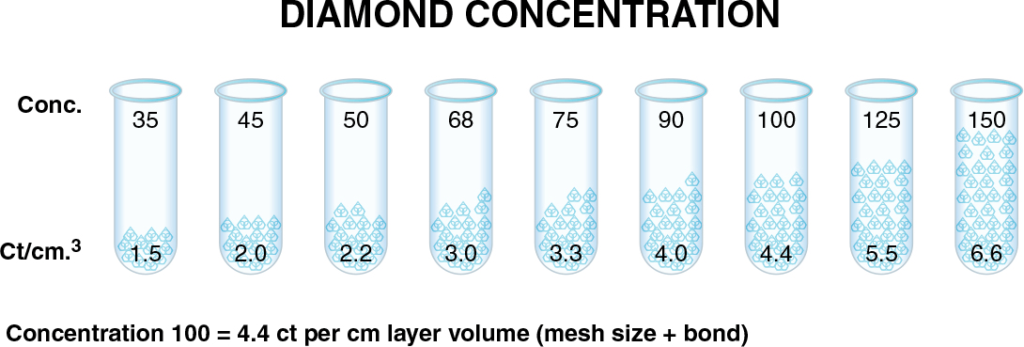
Diamond Concentration
Diamond concentration refers to the volume of diamond abrasive present in the tool relative to the bond matrix. It is typically expressed as a concentration value, where a concentration of 100 equates to 25% by volume of diamond in the total mixture. The concentration affects tool aggressiveness, cutting rate, and durability:
-
Low Diamond Concentration: (50-75 concentration) provides less aggressive cutting and is suitable for softer or more easily abraded materials where a finer finish is needed.
-
High Diamond Concentration: (100-150 concentration) provides more aggressive cutting and is used for harder materials or high-production environments where fast material removal is crucial.
A higher concentration results in a longer tool life and greater cutting efficiency, but it also increases the cost. Therefore, concentration is chosen based on the application, cost considerations, and desired tool performance.
Pressure Used
The pressure applied during the pressing stage of tool manufacturing significantly affects the density, strength, and abrasive retention of the resin bond diamond tool. Higher pressure ensures better compaction of the resin bond and abrasive mixture, leading to:
-
Higher Tool Density: Increases the strength and durability of the tool, enhancing performance in aggressive grinding and high-speed cutting.
-
Improved Abrasive Retention: Ensures that diamond particles are securely embedded within the bond, minimizing abrasive grain loss during operation.
-
Better Mechanical Keying: Helps improve the mechanical bond between the diamond particles and the resin matrix, particularly important for maintaining tool integrity under high loads.
The amount of pressure used varies according to the tool's size, shape, bond hardness, and required performance characteristics.

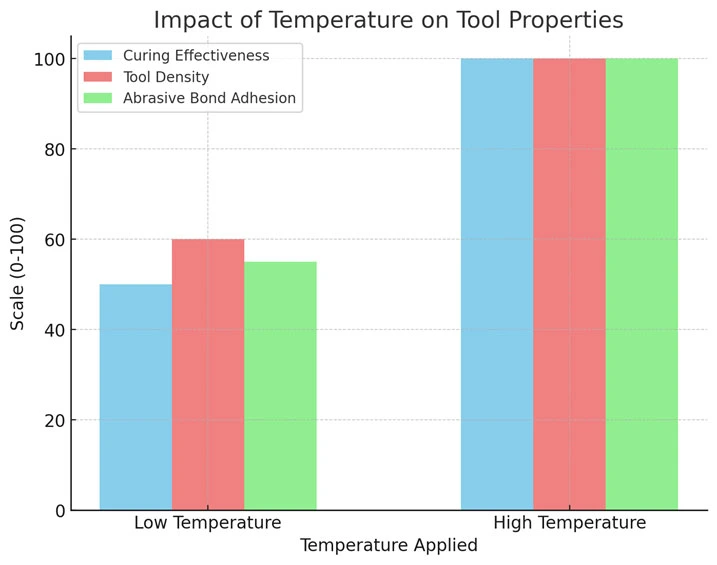
Temperature Used
Temperature control during the manufacturing process is crucial, especially when hot pressing or curing resin bond tools. The right temperature ensures optimal flow of the resin, proper curing, and maximizes the tool's performance properties:
-
High Temperatures (Hot Pressing): Ensure full curing of the resin bond, high tool density, and optimal abrasive-bond adhesion. Temperatures generally range from 160°C to 250°C, depending on the resin type.
-
Lower Temperatures (Cold Pressing with Curing): May require a longer curing time but prevent degradation of resin properties and allow for better control over bond flexibility.
The selection of temperature settings is influenced by the bond type, tool design, and intended application, as it directly affects the final mechanical properties of the tool.
Curing Cycle Time
Temperature control during the manufacturing process is crucial, especially when hot pressing or curing resin bond tools. The right temperature ensures optimal flow of the resin, proper curing, and maximizes the tool's performance properties:
-
Short Curing Times: Used when fast production cycles are required, but they may not allow the bond to fully develop its optimal properties, potentially compromising tool performance.
-
Longer Curing Times: Allow the bond to fully harden, achieving maximum strength, flexibility, and consistency in tool performance.
Curing time is typically tailored to the resin type and desired bond hardness, with optimal curing ensuring a balance between bond strength and tool sharpness.
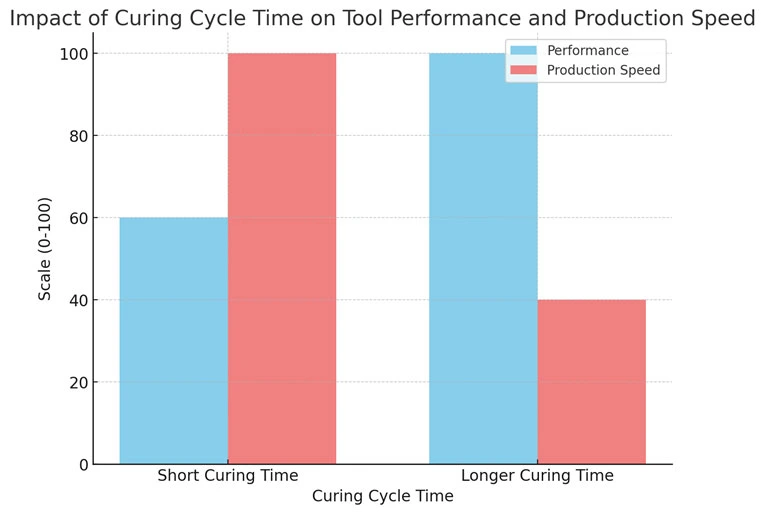
Fillers Used
Fillers and additives are integrated into the resin bond matrix to modify the tool’s properties, enhance performance, and improve grinding efficiency. These fillers can influence factors such as:
-
Heat Dissipation: Fillers like graphite or copper are used to improve thermal conductivity, reducing heat buildup during high-speed grinding or cutting.
-
Bond Hardness and Flexibility: Fillers like glass powder, ceramic particles, or metal oxides can modify the hardness and toughness of the resin bond, creating a balance between tool flexibility and wear resistance.
-
Chip Clearance and Friction Reduction: Additives such as lubricants can reduce friction during cutting and improve chip removal, preventing clogging and ensuring a smoother cut.
The choice of fillers depends on the application’s requirements, such as cutting speed, surface finish, tool life, and the workpiece material.
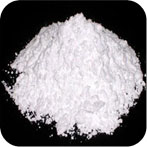
Alumina Oxide
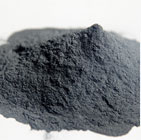
Silicon Carbide
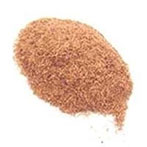
Silicon Carbide

Silicon Carbide
Bond Formula (Proportion of Components)
The bond formula is the specific composition of the resin matrix and its components, including abrasives, fillers, reinforcements, and resin type. The proportion and type of each component are selected to achieve a balance between tool hardness, cutting performance, and flexibility:
-
Resin Type and Proportion: Different resins, such as phenolic or polyimide, offer varying degrees of flexibility, hardness, and thermal stability. The resin proportion affects the overall bond strength and its ability to hold the abrasive grains.
-
Abrasive Proportion and Distribution: The amount and distribution of diamond or CBN within the bond matrix influence cutting aggression, tool life, and surface finish.
-
Filler and Additive Balance: The right balance of fillers helps optimize heat dissipation, bond hardness, and lubrication, ensuring the tool performs effectively in its specific application.
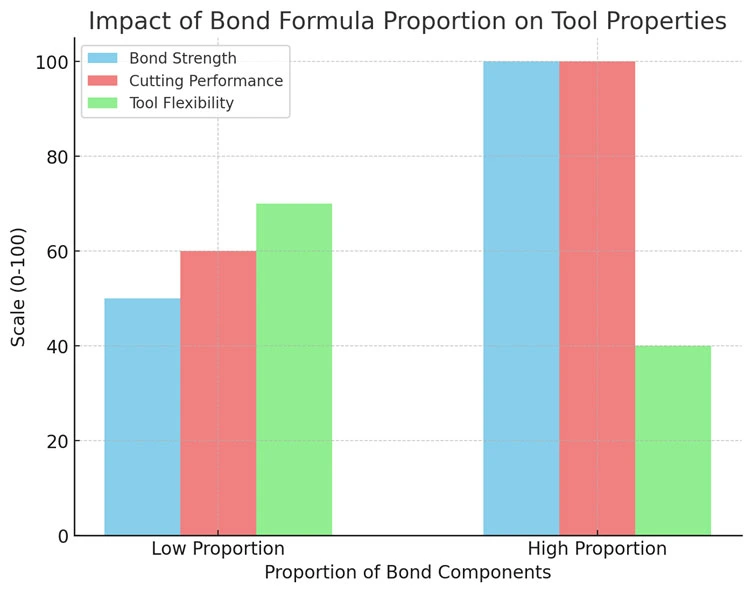
The bond formula is carefully developed and tailored to each tool type, depending on the desired characteristics and end-use application. Fine-tuning this formula allows for the production of tools with precise performance, including achieving the correct balance between material removal rate, surface finish, and tool longevity.
What Makes Us Different?
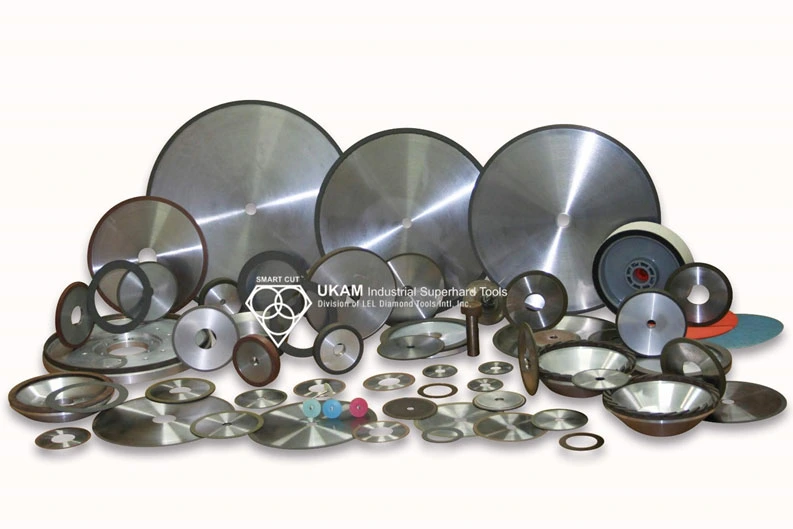
UKAM Industrial manufactures resin bond diamond and CBN tools using advanced molding processes, offering a wide range of geometries, diamond sizes, concentrations, and bond hardness levels. We are capable of maintaining high-precision tolerances on tool diameter, thickness, and can grind almost any form or radius required. Our resin bond diamond tools and wheels are available in diameters as small as 2mm (0.080") up to 609mm (24") and thicknesses ranging from as thin as 0.10mm (0.004") to as thick as 101mm (4"). We offer diamond and CBN grit sizes from 60 mesh to as fine as 3 microns, with thickness tolerances starting as tight as 5 microns and above.
A variety of popular resin bond tool specifications are readily available in stock as part of our inventory program, and we can manufacture nearly any custom specification with a relatively short lead time. For a free quote or to discuss your application needs, contact us today!
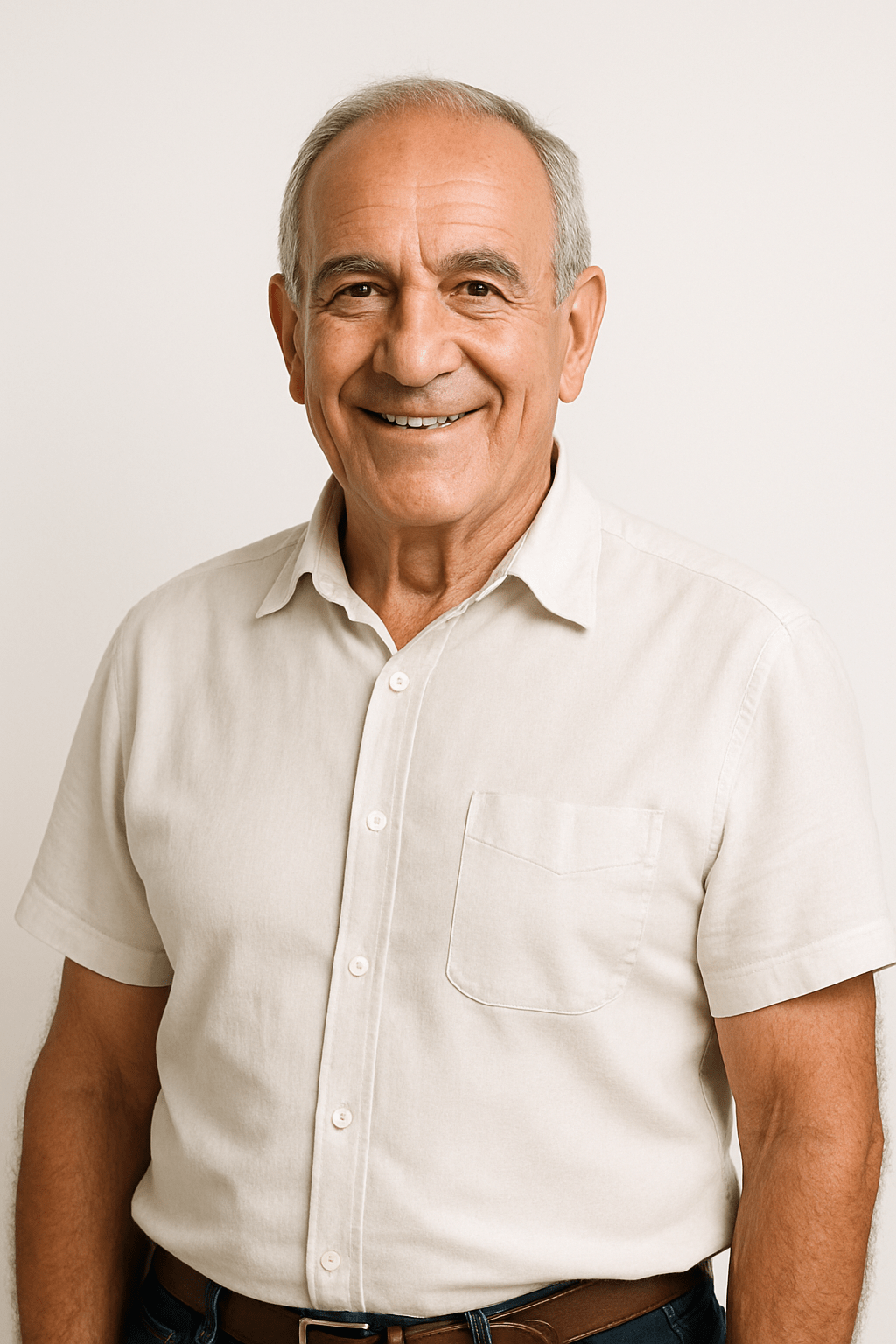
Leon Meyer is a veteran manufacturing engineer and technical consultant with over 50 years of experience in the development, implementation, and troubleshooting of industrial diamond tooling systems. Having spent his career at the intersection of tool design, precision manufacturing, and production engineering, Mr. Meyer is widely regarded as one of the most experienced voices in the application of ultra-thin diamond blades, sintered core drills, and CBN grinding wheels across heavy industry, advanced materials, and research sectors.
Known for his pragmatic, no-nonsense approach, Leon has advised manufacturers across the United States, Europe, and East Asia—helping streamline cutting processes, extend tool life, and solve complex issues related to material breakage, chipping, and tolerance drift. His expertise has directly contributed to improved production efficiency in industries ranging from aerospace alloys and technical ceramics to optics, composites, and high-nickel superalloys.
As an author, Mr. Meyer brings a lifetime of field knowledge to his writing, with a focus on real-world problem solving, cost-performance optimization, and tool reliability under demanding conditions.
ARE YOU USING RIGHT TOOLS
FOR YOUR APPLICATION?
LET US
HELP YOU
HAVING ISSUES WITH
YOUR CURRENT TOOLS?
Knowledge Center
How to Selecting Right Diamond Tools for your application
How to properly use Diamond Tools
Why use diamond
Diamond vs CBN (cubic boron nitride) Tools
What is Diamond Mesh Size and how to select best one for your application
What is Diamond Concentration and which to use for your application
Diamond Tool Coolants Why, How, When & Where to Use
Get to Know the Diamond Tool Bond Types and Which to use for your application
Get to Know the Diamond Tool Bond Types and Which to use for your application
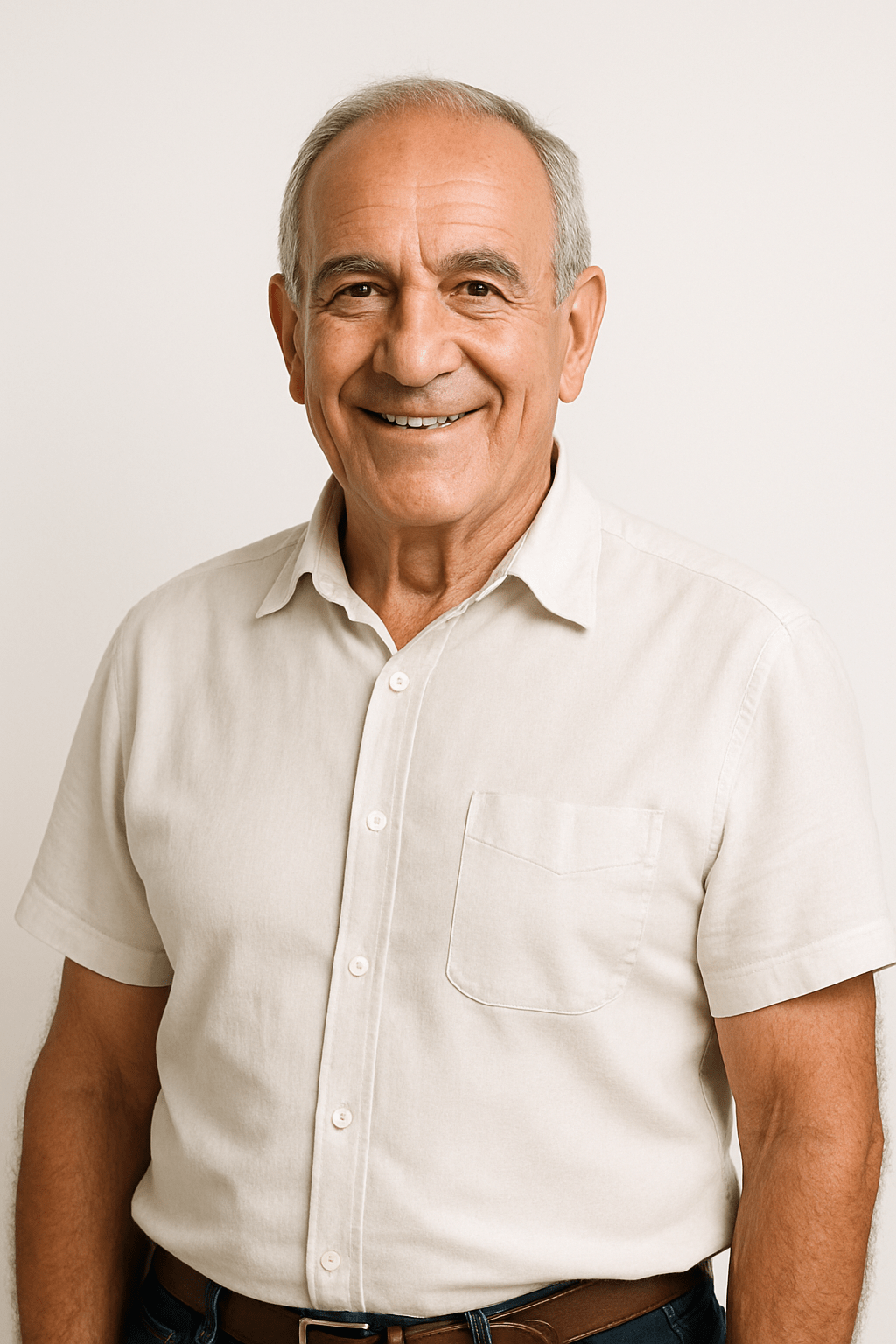
Leon Meyer is a veteran manufacturing engineer and technical consultant with over 50 years of experience in the development, implementation, and troubleshooting of industrial diamond tooling systems. Having spent his career at the intersection of tool design, precision manufacturing, and production engineering, Mr. Meyer is widely regarded as one of the most experienced voices in the application of ultra-thin diamond blades, sintered core drills, and CBN grinding wheels across heavy industry, advanced materials, and research sectors.
Known for his pragmatic, no-nonsense approach, Leon has advised manufacturers across the United States, Europe, and East Asia—helping streamline cutting processes, extend tool life, and solve complex issues related to material breakage, chipping, and tolerance drift. His expertise has directly contributed to improved production efficiency in industries ranging from aerospace alloys and technical ceramics to optics, composites, and high-nickel superalloys.
As an author, Mr. Meyer brings a lifetime of field knowledge to his writing, with a focus on real-world problem solving, cost-performance optimization, and tool reliability under demanding conditions.