-
0 items in quote
No products in the Quote Basket.
SMART CUT® Precision
Gang Arbors & Hubs
SMART CUT® Precision Gang Arbors & Hubs - Your Key to Precision Machining Excellence!
Are you in search of the ultimate solution for your OD grinding, vertical spindle grinding, precision slicing, and dicing needs? Look no further! SMART CUT® Precision Gang Arbors & Hubs are engineered to meet your machining requirements with unparalleled precision and versatility. For holding individual or gang stacked diamond blades or carbide saw blades.
Description
Specifications
Frequently Asked Questions
Industries Used In
Accessories
Recommendations
Description
Compatible with Leading Equipment Brands
Our SMART CUT® Precision Gang Arbors & Hubs are the trusted choice of professionals and manufacturers across various industries. They seamlessly integrate with equipment from renowned brands like MTI, Disco, Veeco, K&S/ADT, MECO/FICO, and many others, ensuring compatibility and reliability.
Specifications
- Standard and custom size arbors and hubs
- Body material can be
- Anodized aluminum
- Heat treated steel
- Stainless steel
- Titanium
- Shoulder perpendicularity: 0.000050 in.
- Radial runout of Arbor or Hub: < 0.0002 in.
- Axial runout of blade assembly: < 0.0002 in.
- Shafts as long as 40 in
Frequently Asked Questions
SMART CUT arbors and hubs are designed to be versatile and can often accommodate non-standard or custom blade configurations. Contact SMART CUT to discuss your specific blade requirements.
Yes, SMART CUT arbors and hubs can be integrated into robotic automation systems, making them suitable for automated material handling and machining processes.
To select the correct size, consider the blade diameter, thickness, and the specifications of your machining equipment. SMART CUT’s technical support team can assist you in choosing the right size based on your application.
Yes, SMART CUT arbors and hubs can be employed for both roughing and finishing operations. Their precision and adaptability make them versatile tools for various stages of machining.
SMART CUT arbors and hubs may require balancing based on the specific application and equipment. Balancing should be performed as needed to ensure smooth and vibration-free machining at high speeds.
SMART CUT arbors and hubs are compatible with various cutting fluids and coolants commonly used in machining processes. It’s important to select the appropriate cutting fluid or coolant based on the material being machined and the specific machining requirements.
Common signs that maintenance or replacement may be needed include increased vibration during machining, reduced cutting accuracy, visible wear on components, and decreased cutting efficiency. Regular inspection can help detect these issues.
Handle SMART CUT arbors and hubs with care to avoid damage. Clean them according to the manufacturer’s recommendations, typically using a mild solvent or cleaning solution. Store them in a clean, dry, and protected environment, especially during transportation, to prevent damage and contamination.
When changing blades or adjusting spacers, follow these general steps:
- Ensure the machine is safely powered off.
- Loosen any locking mechanisms on the arbor or hub.
- Carefully remove or replace blades, making sure they are properly seated.
- Adjust spacers as needed to achieve the desired configuration.
- Tighten all locking mechanisms securely.
- Conduct a visual inspection to verify the setup before resuming machining.
SMART CUT arbors and hubs can be used in high-speed machining applications, but it’s crucial to select the appropriate material and specifications based on the specific requirements of your high-speed machining equipment and materials being processed.
Yes, SMART CUT arbors and hubs can be used in both wet and dry machining processes. They are adaptable to various machining environments and can be paired with appropriate coolant or lubrication systems for wet machining when necessary.
The weight capacity of SMART CUT arbors and hubs depends on factors such as the material, size, and configuration. For applications with specific weight requirements, it’s advisable to consult with SMART CUT to select the most suitable product.
Maintenance intervals and lubrication requirements can vary based on usage and environmental conditions. SMART CUT typically provides maintenance guidelines in their product documentation. Regular inspection, cleaning, and lubrication are recommended to ensure consistent performance.
Safety is paramount when working with precision machining equipment. Always follow safety guidelines provided by the equipment manufacturer and ensure that operators are trained in safe operation practices. Proper personal protective equipment (PPE) should be worn when necessary.
Yes, SMART CUT arbors and hubs are compatible with CNC (Computer Numerical Control) machines. Their precision and versatility make them a valuable addition to CNC machining processes.
When not in use, SMART CUT arbors and hubs should be stored in a clean and dry environment, protected from dust and contaminants. It’s recommended to use appropriate storage racks or containers to prevent damage or distortion of the equipment.
SMART CUT Precision Gang Arbors & Hubs are primarily designed for external machining operations. For internal machining, you may need specialized tools or equipment, depending on your specific requirements.
The extended shaft capability allows you to work with larger workpieces or reach deeper into the machining area, providing greater flexibility in your machining processes and accommodating various setups.
Yes, SMART CUT arbors and hubs are designed to hold individual blades or gang-stacked blade configurations, offering versatility for different machining needs and applications.
Multiple pitches and shoulder positions on a single arbor or hub provide adaptability for diverse machining requirements. This feature allows you to fine-tune your setup and optimize your machining processes for different projects.
SMART CUT offers truing and restacking services to assist with maintaining the accuracy and performance of your equipment. Contact SMART CUT’s technical support team to inquire about these services and schedule truing and restacking as needed.
- Ensure that the arbor or hub is securely fastened to your machining equipment according to manufacturer guidelines.
- Check and confirm the concentricity and alignment of the blades and hubs.
- Regularly inspect the blades and hubs for signs of wear and damage, replacing any worn components promptly.
- Follow SMART CUT’s recommended maintenance schedule for cleaning and lubrication to keep your equipment in top condition.
Yes, these arbors and hubs can be integrated into automated machining systems, enhancing efficiency and precision in automated production processes.
Yes, SMART CUT arbors and hubs can be used with coolant or lubrication systems to help improve cutting efficiency and extend the lifespan of cutting tools.
SMART CUT Precision Gang Arbors & Hubs are designed to be versatile and can often be retrofitted onto existing machinery, provided they are compatible with the equipment’s specifications. It’s advisable to consult with SMART CUT to confirm compatibility and receive guidance on retrofitting.
Shoulder perpendicularity refers to the precision of the arbor or hub’s shoulder relative to its shaft. SMART CUT’s shoulder perpendicularity of 0.000050 inches ensures that the blade assembly is held accurately, minimizing errors in your machining processes.
Radial runout measures any deviation from a true circular path. It is crucial for precision machining as it directly affects the accuracy of the finished workpiece. SMART CUT’s radial runout of less than 0.0002 inches guarantees precise machining results.
Axial runout measures the concentricity of the blade assembly with the arbor or hub’s central axis. A low axial runout, as provided by SMART CUT (< 0.0002 inches), ensures that your blades are centered accurately, enhancing machining accuracy.
Yes, SMART CUT arbors and hubs are versatile and can securely hold both diamond blades and carbide saw blades, making them suitable for a wide range of machining applications.
SMART CUT Precision Gang Arbors & Hubs are commonly used in applications such as OD grinding, vertical spindle grinding, precision slicing, and dicing across various industries, including semiconductor manufacturing, electronics, and precision optics.
The choice of material depends on your specific machining needs. For corrosion resistance and lightweight applications, aluminum may be suitable, while steel and stainless steel offer durability. Titanium provides high strength and is ideal for demanding applications. Consult SMART CUT for material recommendations.
Having multiple diameters and thicknesses on the same arbor streamlines your machining setup. It reduces the need to change arbors frequently, saving time and improving efficiency.
Yes, these arbors and hubs are designed for reusability. By changing spacers and adapting the setup, you can use them for various machining applications, making them a cost-effective choice for manufacturers.
Restacking blades on SMART CUT arbors and hubs is designed to be user-friendly. While basic knowledge of blade handling is helpful, no specialized tools or extensive training are typically required.
Regular inspection and cleaning are recommended to maintain the performance of SMART CUT arbors and hubs. Following the manufacturer’s guidelines for maintenance and usage is essential for extended lifespan and consistent performance.
Industries Used In
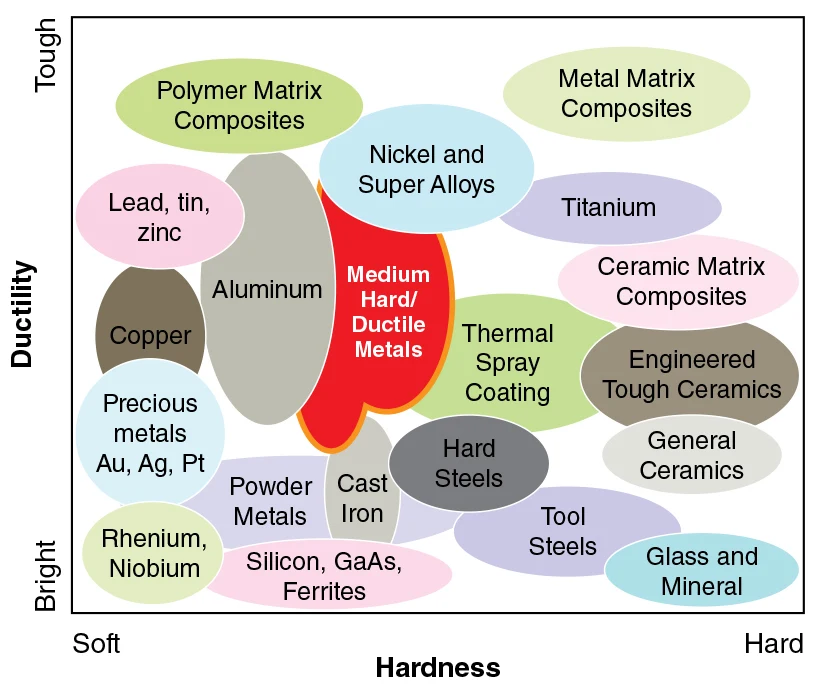

INDUSTRIES USED IN:
- Advanced Ceramics
- Composites
- Glass
- Geology
- Quartz
- Materials Research
- Medical Devices
- Metallography
- Photonics / Optics
- Semiconductor
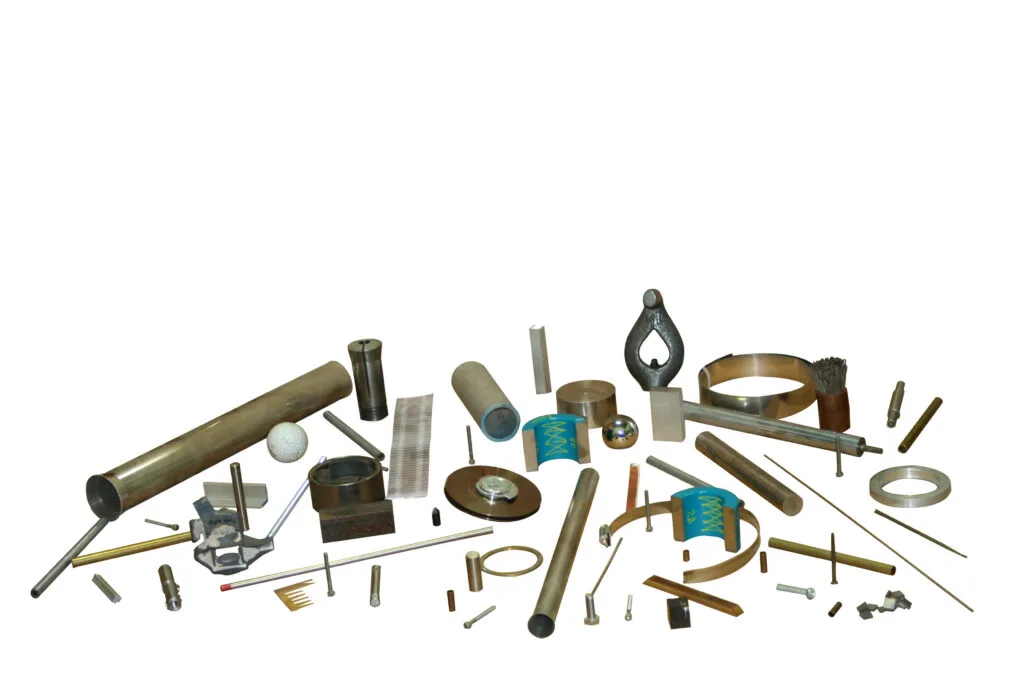
Ferrous & Non-Ferrous Metals:
- Plain Carbon Steels
- Electronic Packages
- Stainless Steels Plastics
- Tool Steels Fasteners
- Aluminum Refractories
- Copper Base Alloys Integrated Circuits
- Magnesium Thermal Spray Coatings
- Titanium Metal Matrix Composites
- Biomedical Wafers
- Petrographic
- PCB.s Ceramics
Accessories
Content
Recommendations
Content
Advantages
- Secure Blade Positioning: Our precision design guarantees a secure and reliable hold on your blades, minimizing the risk of errors and enhancing overall safety.
- Exceptional Pitch Tolerances: Achieve perfection with pitch tolerances as tight as ± 0.0001 inches, ensuring the utmost accuracy in your machining operations.
- Efficiency Redefined: Reduce setup time with SMART CUT's arbors and hubs, which come equipped with multiple diameters and thicknesses on the same arbor, streamlining your workflow.
- User-Friendly: Our products are designed with ease of use in mind, making it simple for users to restack blades and change spacers for different applications.
- Sustainability: SMART CUT Gang Arbors & Hubs are reusable for multiple applications, thanks to their adaptable nature and interchangeable components.
- Versatility: Enjoy the convenience of multiple pitches and shoulder positions on the same arbor or hub, giving you unparalleled flexibility in your machining processes.
- Truing and Restacking Services: SMART CUT offers additional services to keep your equipment in top shape, ensuring long-term performance and reliability.
Features
- Standard and Custom Sizes: Choose from a wide range of standard sizes or opt for custom solutions tailored to your unique specifications.
- Diverse Materials: Our arbors and hubs are available in a variety of materials, including anodized aluminum, heat-treated steel, stainless steel, and titanium, allowing you to select the perfect material for your application.
- Unmatched Precision: With shoulder perpendicularity as tight as 0.000050 inches, radial runout of less than 0.0002 inches, and axial runout of the blade assembly also under 0.0002 inches, SMART CUT ensures precision like no other.
- Extended Shafts: Need a longer shaft? No problem! Our arbors and hubs accommodate shafts as long as 40 inches, providing flexibility for a wide range of applications.
Examples of Some of the Equipment Used On:
- MTI
- Disco
- Veeco
- K&S/ADT
- MECO/FICO
- & Many Others
Benefits
- Precision design holds blades securely in position
- Extremely accurate pitch tolerances to ± 0.0001 in.
- Minimize setup time by including multiple diameters and thickness on the same arbor
- Easy for user to restack
- Reusable for many applications by changing spacers
- Multiple pitches and shoulder positions on the same arbor or hub • Truing and restacking services
Related Products
Diamond Grinding Wheels (Electroplated) – Concave
SMART CUT® Electroplated Diamond Cabbing Grinding Wheels – Concave are precision-engineered tools designed specifically for carving, shaping, and grinding concave surfaces in a variety of hard, brittle, and delicate materials such as stone, glass, ceramics, quartz, and advanced composites. The unique curved grinding surface enables users to achieve smooth, even contours and recessed forms that are difficult to accomplish with flat or standard profile wheels.
DIAMOND GRINDING WHEELS (Electroplated) – Non Textured Steel Hub
SMART CUT® Electroplated (Nickel Bonded) Diamond Grinding Wheels with non-textured solid steel hubs are engineered for users who demand precision, durability, and high-performance results in their grinding operations. These wheels are manufactured using premium-grade synthetic diamonds and a precision-controlled electroplating process that exposes each diamond crystal at its optimal cutting point, delivering maximum grinding efficiency, faster cutting action, and a superior surface finish with minimal loading.
DIAMOND GRINDING WHEELS (Electroplated) – Non Textured PLASTIC HUB
SMART CUT® Electroplated (nickel bonded) diamond grinding wheels, with plastic center core. Made with the highest quality diamonds for longer grinding life, clean and faster cutting. Can be used on all conventional grinders made today. Such as Diamond Pacific, Barranca, Maxant, Graves, as well as other cabbing machines. All wheels have a 1in. Diameter and include bushing to accommodate 3/4in., 5/8in. and 1/2in. arbors. Individually boxed. The plastic hubs are lighter and can be used on less powerful grinding machines. We do not offer re-plating of the wheels, it is more cost effective to re-cycle the wheels.
Recently Viewed Products
ARE YOU USING RIGHT TOOLS
FOR YOUR APPLICATION?
LET US
HELP YOU
HAVING ISSUES WITH
YOUR CURRENT TOOLS?
Knowledge Center
02
Jun
How to properly use Diamond Tools
UKAM Industrial Superhard Tools manufactures precision diamond tools for a large variety of applications, materials, and industries.
Share this Article with Friend or Colleague
Metal Bonded Diamond Tools are “impregnated” with diamonds. This means that selected...
02
Jun
Why use diamond
Diamond is the hardest material known to man kind. When used on diamond/tools, diamond grinds away material on micro (nano) level. Due to its hardness Diamond will work all types of materials from...
02
Jun
Diamond vs CBN (cubic boron nitride) Tools
Cubic Boron Nitride (CBN) is a synthetic material that is renowned for its exceptional hardness and high thermal stability. It is composed of boron and nitrogen atoms arranged in a crystal lattice structure, similar to...
02
Jun
What is Diamond Mesh Size and how to select best one for your application
Diamond grit size can be defined as the size of the diamond particles used in the bond matrix. The larger the diamond particles (grit size) the faster the tool will cut.
Share this Article with Friend or...
02
Jun
What is Diamond Concentration and which to use for your application
Diamond concentration is measured based on the volume of diamond within a section of the tool. It is typically defined as Concentration 100, which equates to 4.4 carats per cubic centimeter of the diamond layer...
02
Jun
Diamond Tool Coolants Why, How, When & Where to Use
Coolant is one of the most overlooked variables in the overall diamond or cbn tool machining process. Effective and proper use of coolant and recalculating coolant system will pay off in terms of improved surface...
18
Jul
Get to Know the Diamond Tool Bond Types and Which to use for your application
The indication of this premature loss of diamond is deep pocket left behind. The presence of many pockets means the diamond is wasted without being used. Each diamond must protrude high to cut fast with...
17
May
Get to Know the Diamond Tool Bond Types and Which to use for your application
Selecting the appropriate diamond bond type for specific applications is crucial for several reasons. Diamond bond type directly affects the tool's performance, efficiency, and longevity. Different bond types determine how well a tool can withstand...
- Unmatched Selection For Many Applications
- Superior Quality & Consistency
- Immediate Worldwide Delivery
- Technical Support & Expertise
- American Based Manufacturer
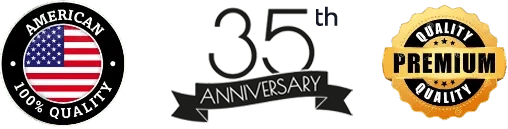

- Different Product
- Different Technology
- Different Company
- Expect MORE from your tools
Let Us HELP You!
Subscribe To Our Newsletter
Signup for email offers, updates, and more
Contact Us
- 25205 & 25201 Avenue Tibbits Valencia CA 91355 USA
-
Phone : (661) 257-2288
FAX : (661) 257 -3833 - lel@ukam.com
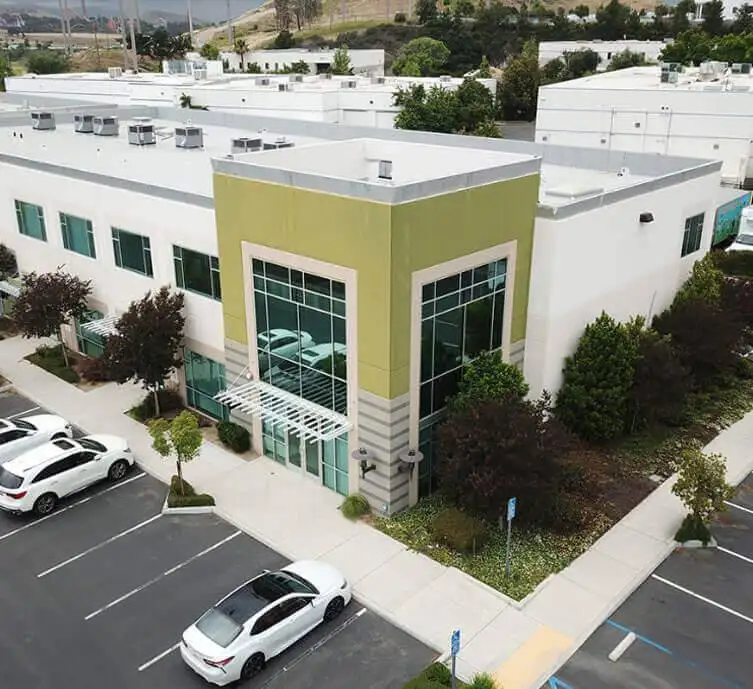
UKAM Industrial Superhard Tools is a U.S. High Technology, Specialty Diamond Tool & Equipment manufacturer. We specialize in producing ultra thin, high precision cutting blades, precision cutting machines diamond drills, diamond micro tools, standard & custom advanced industrial diamond tools and consumables.
- 25205 & 25201 Avenue Tibbits Valencia CA 91355 USA
-
Phone : (661) 257-2288
FAX : (661) 257 -3833 - lel@ukam.com
- 25205 & 25201 Avenue Tibbits Valencia CA 91355 USA
-
Phone : (661) 257-2288
FAX : (661) 257 -3833 - lel@ukam.com
DIAMOND TOOLS BY BOND
EQUIPMENT
KNOWLEDGE CENTER
OUR PRODUCTS
COMPANY
CUSTOMER SERVICE
Shipping Methods


Safe & Secure Payments

© Copyright 1990-2025. UKAM Industrial Superhard Tools – Terms of Use