-
0 items in quote
No products in the Quote Basket.
DIAMOND GRINDING WHEELS (Electroplated) - Non Textured PLASTIC HUB
SMART CUT® Electroplated (nickel bonded) diamond grinding wheels, with plastic center core. Made with the highest quality diamonds for longer grinding life, clean and faster cutting. Can be used on all conventional grinders made today. Such as Diamond Pacific, Barranca, Maxant, Graves, as well as other cabbing machines. All wheels have a 1in. Diameter and include bushing to accommodate 3/4in., 5/8in. and 1/2in. arbors. Individually boxed. The plastic hubs are lighter and can be used on less powerful grinding machines. We do not offer re-plating of the wheels, it is more cost effective to re-cycle the wheels.
DESCRIPTION
SPECIFICATIONS
FREQUENTLY ASKED QUESTIONS
INDUSTRIES USED IN
ACCESSORIES
USAGE RECOMMENDATION
DESCRIPTION
SMART CUT™ Electroplated (nickel bonded) diamond grinding wheels, with plastic center core. Made with the highest quality diamonds for longer grinding life, clean and faster cutting. Can be used on all conventional grinders made today. Such as Diamond Pacific, Barranca, Maxant, Graves, as well as other cabbing machines. All wheels have a 1in. Diameter and include bushing to accommodate 3/4in., 5/8in. and 1/2in. arbors. Individually boxed. The plastic hubs are lighter and can be used on less powerful grinding machines. We do not offer re-plating of the wheels, it is more cost effective to re-cycle the wheels.
SPECIFICATIONS
Specification | Description |
---|---|
Type | Electroplated (nickel bonded) diamond grinding wheels |
Hub Material | Plastic |
Quality of Diamonds | Highest quality |
Equipment Compatibility | Can be used on all conventional grinders (e.g., Diamond Pacific, Barranca, Maxant, Graves, and many others) |
Diameters Available | 6” (150mm) to 8” (200mm) – Other Diameters can be produced upon request |
Diamond Grit Sizes Available | 60 mesh to 600 mesh (other diamond grit sizes can be produced upon request) |
Bushing Included | Yes, to accommodate 3/4in., 5/8in., and 1/2in. arbors (other arbor sizes can be produced upon request) |
Packaging | Individually boxed |
FREQUENTLY ASKED QUESTIONS
The SMART CUT™ Electroplated Diamond Grinding Wheels are designed for grinding, shaping, and cutting various materials. They are suitable for use on most conventional grinders available today. Electroplating refers to the process of using an electric current to bond the diamonds to the grinding wheel’s surface. The nickel acts as the bonding medium, ensuring a high-quality and durable attachment of the diamonds to the wheel. They can be used for grinding various materials, including stones, ceramics, metals, and other hard materials. Yes, these wheels can be used on most conventional grinders, including brands like Diamond Pacific, Barranca, Maxant, Graves, and other cabbing machines. The mesh or grit size refers to the granularity of the diamonds on the wheel. The lower the number, the coarser the grit, and the faster the material removal. Conversely, a higher number indicates a finer grit for more detailed or polished work. The plastic hub makes the grinding wheel lighter, allowing it to be used on less powerful grinding machines. Additionally, it provides flexibility in terms of accommodating different arbor sizes with the included bushings. The arbor size refers to the hole’s diameter in the center of the grinding wheel where it attaches to the grinder. Our wheels come with a 1-inch diameter and include bushings to accommodate 3/4in., 5/8in., and 1/2in. arbors, ensuring compatibility with various grinder models. We do not offer re-plating services. Given the costs involved, it is more economical to recycle and replace the wheels once they’ve reached the end of their usable life. Your choice of grit size depends on the type of work you’re undertaking. Coarser grits (like 60 mesh) are ideal for rapid material removal, while finer grits (like 600 mesh) are suited for polishing or detailed work. Yes, each grinding wheel is individually boxed for safe and secure transportation. SMART CUT™ grinding wheels are made with the highest quality diamonds to ensure longer grinding life, cleaner, and faster cutting, setting them apart from many competitor It’s essential to keep the grinding wheel clean and free from debris. Regularly inspect for any wear or damage, and always use the wheel at the manufacturer’s recommended speed. Always wear appropriate safety gear, like goggles and gloves, when operating any grinding machinery. Ensure the wheel is correctly attached to the grinder and free from damage before use. Keep the working area well-lit and free from distractions. While the SMART CUT™ Electroplated Diamond Grinding Wheels can handle both wet and dry grinding, using them with a coolant or water can help extend their lifespan and prevent overheating. It’s recommended to store the grinding wheels in a cool, dry place, away from direct sunlight. Keeping them in their original packaging can also protect them from environmental factors and potential damage. Our grinding wheels are designed to be compatible with most conventional grinders. The included bushings allow for adjustments to different arbor sizes. If you’re unsure, please provide the specifications of your machine to our customer support for guidance. The lifespan depends on usage, materials being ground, and proper maintenance. With regular use and proper care, customers generally find our grinding wheels last longer than many competing products. Absolutely. Always ensure the machine is turned off and unplugged while changing the wheel. Wear safety gloves and ensure the new wheel is securely fastened before starting the machine again. The nickel bonding is designed to be durable and resist common forms of corrosion. However, storing the wheel in a dry environment can further ensure its longevity. The plastic hub is engineered to maintain a proper balance of the wheel during operation, ensuring smooth performance and reduced vibrations. SMART CUT™ technology emphasizes the optimal distribution of diamonds on the wheel, ensuring consistent grinding, longer wheel life, and faster cutting speeds. While we encourage recycling, you should check with local waste management or recycling centers about the best disposal methods for used grinding wheels. Yes, especially the finer grit sizes, which are designed for detailed or precision grinding work. The plastic hub is significantly lighter than traditional metal hubs, reducing the overall weight and strain on grinding machines. The RPM usually decreases as the diameter of the grinding wheel increases. For a grinding wheel of around 6 to 8 inches typical RPM values range from 3,500 to 6,000 RPM depending on material. Softer materials might allow for higher RPMs, while harder materials might require slower RPMs for efficient grinding. Water soluble coolants are often the most common coolants used for grinding. They are made by mixing water with a coolant concentrate. These coolants are known for their excellent cooling properties. Dressing a grinding wheel involves the process of renewing the wheel’s surface to ensure it’s sharp and clean. This helps in maintaining the wheel’s performance, ensures precision grinding, and can extend the wheel’s lifespan. Electroplated diamond grinding wheels have a single layer of diamond particles. While they don’t typically require frequent dressing like resin-bonded wheels, occasional dressing can help maintain optimal performance, especially if the wheel becomes glazed or loaded with material. For electroplated diamond wheels, using a silicon carbide dressing stick or a softer, fine-grit diamond wheel can be effective. Unlike other types of grinding wheels, electroplated diamond wheels don’t need frequent dressing. Dress only when you notice a decrease in grinding efficiency or when the surface becomes glazed or loaded. Turn on the grinder and let it reach full speed. Hold the dressing stick flat against the wheel’s surface, ensuring you cover the entire wheel face. Move the stick back and forth until the wheel’s surface feels sharp and clean. No. Dressing is for renewing the surface of the wheel. If your wheel has deep chips or cracks, it may be unsafe to use, and replacing the wheel is recommended. Always ensure you wear safety glasses, and keep your fingers and hands away from the wheel’s surface. Dressing can produce dust, so consider using a dust mask if working in an enclosed space. Dressing primarily focuses on renewing the wheel’s surface. While minor adjustments to the profile can sometimes be made, significant reshaping requires specialized tools and techniques. After dressing, you might need to realign the tool rest or make other minor adjustments to maintain accuracy in your grinding tasks. If the wheel feels smooth, it’s taking longer to grind, or you notice decreased grinding performance, it may be time to dress the wheel. Another indicator is if you see material buildup or a shiny glaze on the wheel’s surface. Over-dressing can remove the diamond particles since they are only a single layer in electroplated wheels. If this happens, the wheel might become less efficient. Monitor its performance, and if grinding becomes inefficient, consider replacing the wheel. Non-textured wheels offer a smooth and consistent grinding surface, which can result in a uniform finish. Textured wheels, on the other hand, might be designed to increase the rate of material removal or enhance cooling by allowing better water flow between the wheel and the workpiece. Lifespan can vary based on various factors like usage, material being ground, and wheel quality. However, in general, non-textured wheels can wear more uniformly, potentially offering a longer lifespan. Textured wheels might wear unevenly due to the varied surface, but they might also allow for faster grinding in certain applications. The plastic hub is significantly lighter than steel hubs. This makes the SMART CUT™ wheel more suitable for less powerful grinding machines and can reduce the overall wear on the grinder’s motor. Steel hubs typically offer better overall balance due to their uniformity and weight. However, high-quality plastic hubs like those in the SMART CUT™ wheels are designed for good balance during operations. The grinding efficiency isn’t solely determined by the hub material but also by the diamond grit, bonding method, and wheel design. However, steel hubs can handle more force and might be suitable for heavy-duty grinding tasks, while plastic hubs might be best for lighter tasks or precision grinding. While specific prices vary, plastic hub wheels like the SMART CUT™ are often more cost-effective than their steel counterparts. However, users should also consider factors like lifespan, efficiency, and application suitability when evaluating cost. Yes, the SMART CUT™ Electroplated Diamond Grinding Wheel is designed to be used on all conventional grinders made today, much like most steel hub wheels. However, always ensure the machine’s RPM ratings and other specifications are compatible with the chosen wheel. Plastic hubs are more lightweight, resulting in reduced transportation emissions. Additionally, the SMART CUT™ wheels’ emphasis on being recyclable highlights an eco-friendly approach. Steel, while heavier, is also recyclable. Both materials have environmental merits, but specific environmental impact can vary based on manufacturing practices. Steel hubs generally conduct heat better than plastic, aiding in heat dissipation. However, the overall heat management will also depend on factors like wheel design, coolant use, and grinding speed. Both types of wheels require regular inspection for wear, damage, and balance. Steel hubs might be more resistant to physical impact, while plastic hubs might be more susceptible to damage from certain solvents or extreme temperatures. Always refer to the manufacturer’s care instructions. A concave diamond grinding wheel has a curved or bowl-like shape, where the grinding surface is inwardly curved. This unique shape allows for specific grinding and shaping tasks that flat or convex wheels can’t perform. Concave diamond grinding wheels are primarily used for: While flat and convex wheels are used for general grinding, shaping, and surface finishing tasks, concave wheels are specialized tools designed primarily for carving out rounded grooves or creating specific shapes that require an inward curve. The advantages include: While they can be used for some overlapping tasks, concave wheels are specialized tools. Using them for tasks suited for flat or convex wheels might not be efficient and can lead to uneven wear of the wheel. Using concave wheels might require a more delicate touch, especially when working with gemstones. It’s essential to ensure even pressure and constantly check the depth and uniformity of the groove or shape being carved. The size or curvature you need will depend on the specific application. Consider the size of the groove or shape you want to create and choose a wheel that matches those dimensions. : General care, like regular cleaning and inspection for damage, is essential for all types of grinding wheels. Due to their shape, concave wheels might require more careful cleaning to ensure that all residue is removed from the curved surface. Yes, the same type of coolant or lubrication can be used, but always refer to the manufacturer’s recommendations to ensure compatibility.
We aim to offer comprehensive support and information to all our customers. Should you have any more questions or unique requirements, our team is always here to help.
Are there any specific maintenance or care instructions that differ between the two types of wheels?
Carving and shaping rounded grooves in gemstones and other hard materials.
Creating concave facets in gemstones for unique jewelry designs.
Grinding and shaping the insides of hollow tools or parts.
Precision Grinding: The curved shape allows for precise carving of rounded shapes and grooves.
Unique Designs: It enables unique gemstone designs, especially in gemstone jewelry.
Efficiency: Achieving such shapes with flat or convex wheels would be more time-consuming and less precise.
Reduced Tool Requirement: Instead of using multiple tools for creating a curved design, a concave wheel can often achieve the desired result on its own.
INDUSTRIES USED IN
Tab Content
ACCESSORIES
Showing 1 – -1 of 16 results Showing all 16 results Showing the single result No results found
Sort by Name A – Z
Filters Sort results
Reset Apply
Image | Item No. | Description | Price | Quantity | Add to cart |
---|---|---|---|---|---|
Color: 5/8″-11″ thread. Fits into drill press chuck. Shank adapter threads into 5/8″-11″ female thread of diamond drill. Can be used with any other tool with 5/8″-11″ thread. | $26.72 | Max: Min: 1 Step: 1 | |||
Color: 5/8″-11″ thread. Fits into drill press chuck. Shank adapter threads into 5/8″-11″ female thread of diamond drill. Can be used with any other tool with 5/8″-11″ thread. | $22.46 | Max: Min: 1 Step: 1 | |||
1 Gallon Blue SMART CUT® General Materials Formula Synthetic Water Soluble Coolant | $99.81 | Max: Min: 1 Step: 1 | |||
1 Quart Blue SMART CUT® General Materials Formula Synthetic Water Soluble Coolant | $34.81 | Max: Min: 1 Step: 1 | |||
5 Gallons Blue SMART CUT® General Materials Formula Synthetic Water Soluble Coolant | $317.41 | Max: Min: 1 Step: 1 | |||
55 Gallons Blue SMART CUT® General Materials Formula Synthetic Water Soluble Coolant | $1,745.00 | Max: Min: 1 Step: 1 | |||
1/2″ x 1/2″ x 6.0″ White Recommended for coarser grits found in segment wheels, core drills, or Blanchard grinding. Excellent performance on 120 grit tools. | $8.65 | Max: Min: 1 Step: 1 | |||
1.0″ x 1.0″ x 6.0″ White Recommended for coarser grits found in segment wheels, core drills, or Blanchard grinding. Excellent performance on 120 grit tools. | $15.99 | Max: Min: 1 Step: 1 | |||
1/2″ x 1/2″ x 6.0″ White For use on diamond tools 150 to 220 Grit Size. | $8.65 | Max: Min: 1 Step: 1 | |||
1.0″ x 1.0″ x 6.0″ Black Recommended for use in Diamond Tools 150 Grit Size (mesh size) or finer. | $15.39 | Max: Min: 1 Step: 1 | |||
2.0″ x 2.0″ x 6.0″ Black Recommended for use in Diamond Tools 150 Grit Size (mesh size) or finer. | $39.47 | Max: Min: 1 Step: 1 | |||
1.0″ x 1.0″ x 6.0″ Black Recommended for coarser grits found in segment wheels, core drills, or Blanchard grinding. Excellent performance on 120 grit tools. | $15.99 | Max: Min: 1 Step: 1 | |||
2.0″ x 2.0″ x 6.0″ Black Recommended for coarser grits found in segment wheels, core drills, or Blanchard grinding. Excellent performance on 120 grit tools. | $39.47 | Max: Min: 1 Step: 1 | |||
$154.87 | Max: Min: 1 Step: 1 | ||||
$154.87 | Max: Min: 1 Step: 1 | ||||
$235.00 | Max: Min: 1 Step: 1 |
USAGE RECOMMENDATION
Instructions for Using Diamond Cabbing Wheels:
- 1. Setup: Ensure that your cabbing machine is on a stable surface and is set up according to the manufacturer’s instructions. Check that all the wheels are securely attached.
- 2. Water Supply: Make sure the water supply is turned on and flowing over the wheel before starting the machine. Water should continuously drip or stream onto the wheel during operation.
- 3. Starting the Machine: Turn on the machine and let the wheels come to full speed.
- 4. Grinding/Shaping: Hold the stone against the wheel, starting with the coarsest grit. Move the stone back and forth, ensuring even coverage. Always keep the stone wet.
- 5. Progressing Through Grits: Once the desired shape is achieved, move on to the next finest grit wheel and repeat the process. Clean the stone between grits to avoid contamination.
- 6. Polishing: After the finest grinding wheel, move on to the polishing wheels if your setup includes them.
- 7. Checking Progress: Frequently check your progress by drying the stone and inspecting it under a good light.
- 8. Finishing Up: Once you’re satisfied with the polish, turn off the machine and thoroughly clean both the stone and your workstation.
- 9. Maintenance: Clean your wheels after use, and store them in a dry place. Regularly inspect them for wear and replace when needed.
- 10. Wheel Rotation: Make a note of the direction in which your wheels rotate. Typically, working with the rotation gives more aggressive grinding, while working against the rotation gives a smoother finish.
- 11. Heat: While water acts as a coolant, be mindful of the heat generated due to friction. Overheating can damage the material or the diamond wheel. If the material gets too hot, give it a moment to cool down.
- 12. Slurry: The mix of water and stone residue that forms is called slurry. Regularly remove slurry buildup as it can impact the effectiveness of the wheel.
- 13. Hand Position: Always keep your fingers away from the rotating wheel. Some people use a dop stick, which is a holder for the stone, to keep their fingers safe.
- 14. Wheel Sequence: Having a dedicated, consistent sequence for your wheels helps in maintaining the process flow. It’s usually best to have a progression from coarse to fine.
- 15. Cleaning the Stone: Before moving to a finer grit, thoroughly clean the stone to remove any coarser particles that might scratch it in the next stages.
- 16. Flats:While shaping the cabochon, be cautious of creating ‘flats’, which are flat spots on the surface that should ideally be domed.
- 17. Edge Treatment: Pay special attention to the edges of the stone, as they can often chip or get ground away more quickly than the center. Some lapidarists prefer to slightly bevel the bottom edge to prevent chipping.
- 18. Continuous Movement: Avoid staying in one spot for too long. Continuous movement ensures even grinding and polishing.
- 19. Backing Material: If the stone is fragile or thin, you might want to use a backing material to give it added strength. Common materials include black basalt, obsidian, or even epoxy.
- 20. Storage: If you’re not using your cabbing machine for an extended period, consider covering it to prevent dust accumulation.
- 21. Practice with Samples: Especially when starting, it’s beneficial to practice on sample or less valuable stones to get the hang of the equipment and technique.
- 22. Magnification: Using a jeweler’s loupe or magnifying glass can help in checking the surface for scratches before moving on to the next stage.
- 23. Documentation: Keep notes on the types of stones you work with and the specific techniques or wheel sequences you find most effective. This will be a valuable reference for future projects.
- 24. Wear and Tear: Over time, the center of the wheel might wear down more than the edges, especially if you tend to use the center more. To maximize the lifespan of your wheels, periodically shift your work position slightly.
- 25. Vibration: Check for any vibrations in your cabbing machine. Excessive vibration can cause uneven grinding and can even damage the machine or the stone.
- 26. Backing Plates: Ensure that the backing plates of your diamond wheels are flat and free from warping. An uneven plate can lead to inconsistent grinding.
- 27. Wheel Storage: If you have additional or replacement wheels, store them flat and supported to prevent any warping.
- 28. Dopping: While many cabbers start working a stone by hand, they often switch to “dopping” — attaching the stone to a stick with wax or glue — when it’s time for the final stages. This provides better control.
- 29. Templates: If you’re aiming for a specific shape, like an oval or teardrop, use a template. This can help in achieving consistent shapes, especially if you’re making multiple pieces.
- 30. Custom Grinding: For stones with unique inclusions or features you want to highlight, consider custom grinding the stone rather than adhering strictly to a template. This can showcase the stone’s best features.
Showing 1 – -1 of 14 results Showing all 14 results Showing the single result No results found
Sort by Price low to high
Filters Sort results
Reset Apply
Image | Item No. | Outside Diameter | Thickness | Diamond Mesh/Grit Size | Price | Quantity | Add to cart |
---|---|---|---|---|---|---|---|
6" (152.4mm) | 1.5" (38.1mm) | 600 mesh | $132.00$150.00 | Max: Min: 1 Step: 1 | |||
6" (152.4mm) | 1.5" (38.1mm) | 360 mesh | $143.00$163.00 | Max: Min: 1 Step: 1 | |||
6" (152.4mm) | 1.5" (38.1mm) | 180 mesh | $149.97$170.00 | Max: Min: 1 Step: 1 | |||
6" (152.4mm) | 1.5" (38.1mm) | 220 mesh | $149.98$163.00 | Max: Min: 1 Step: 1 | |||
6" (152.4mm) | 1.5" (38.1mm) | 100 mesh | $154.00$175.00 | Max: Min: 1 Step: 1 | |||
6" (152.4mm) | 1.5" (38.1mm) | 80 mesh | $165.00$188.00 | Max: Min: 1 Step: 1 | |||
6" (152.4mm) | 1.5" (38.1mm) | 60 mesh | $176.00$200.00 | Max: Min: 1 Step: 1 | |||
8" (203.2mm) | 1.5" (38.1mm) | 600 mesh | $176.00$220.00 | Max: Min: 1 Step: 1 | |||
8" (203.2mm) | 1.5" (38.1mm) | 360 mesh | $187.00$213.00 | Max: Min: 1 Step: 1 | |||
8" (203.2mm) | 1.5" (38.1mm) | 180 mesh | $193.50$220.00 | Max: Min: 1 Step: 1 | |||
8" (203.2mm) | 1.5" (38.1mm) | 220 mesh | $193.50$220.00 | Max: Min: 1 Step: 1 | |||
8" (203.2mm) | 1.5" (38.1mm) | 100 mesh | $198.00$225.00 | Max: Min: 1 Step: 1 | |||
8" (203.2mm) | 1.5" (38.1mm) | 80 mesh | $213.00$243.00 | Max: Min: 1 Step: 1 | |||
8" (203.2mm) | 1.5" (38.1mm) | 60 mesh | $231.00$263.00 | Max: Min: 1 Step: 1 |
25-5051S,25-5050S,25-5048S,25-5049S,25-5047S,25-5046S,25-5045S,25-5058S,25-5057S,25-5055S,25-5056S,25-5054S,25-5053S,25-5052S,
Related Products
SMART CUT® Diamond Grinding Wheels – Sintered(Metal Bond)
SMART CUT® Series Sintered (metal bond) Diamond Grinding Wheels are the longest lasting diamond wheels for cabbing available today. When you need to grind hundreds of cabs. SMART CUT® series Sintered (metal bond) Diamond Grinding Wheels are an excellent investment that will provide: best performance, quality, consistency and overall ROI (Return on Investment). They have a full 3mm of diamond matrix, and solid aluminum cores. These wheels will typically last like many plated or braised diamond cabbing wheels put together. SMART CUT® Sintered diamond wheels will also grind each cab aggressively (first cab as fast as the last). When using SMART CUT® Sintered diamond wheels, we recommend using one diamond mesh/grit size larger for sintered diamond tools as compared to plated or brazed wheels. Reducer rings available to fit most machines.
- Longest Life Possible
- Faster & More Aggressive
- Unmatched Consistency
- Best (ROI) Return on Investment
Diamond Grinding Wheels (Electroplated) – Concave
SMART CUT® Electroplated Diamond Cabbing Grinding Wheels – Concave are precision-engineered tools designed specifically for carving, shaping, and grinding concave surfaces in a variety of hard, brittle, and delicate materials such as stone, glass, ceramics, quartz, and advanced composites. The unique curved grinding surface enables users to achieve smooth, even contours and recessed forms that are difficult to accomplish with flat or standard profile wheels.
SMART CUT® RESIN BOND DIAMOND WHEELS
SMART CUT® Resin Bond Diamond Wheels offer a superior alternative to conventional Nova and Flex wheels, engineered specifically for cabbing, contour grinding, and precision finishing applications. These wheels are manufactured using a proprietary high-performance resin bond matrix combined with premium-grade synthetic diamond particles, delivering exceptional grinding efficiency, surface quality, and extended tool longevity.
One of the most notable advantages of SMART CUT® Resin Diamond Wheels is their immediate usability—no break-in period is required. Unlike traditional wheels that demand conditioning or dressing prior to use, these wheels are ready to perform straight out of the box, saving time and eliminating unnecessary preparation.
DIAMOND GRINDING WHEELS (Electroplated) – Non Textured PLASTIC HUB
SMART CUT® Electroplated (nickel bonded) diamond grinding wheels, with plastic center core. Made with the highest quality diamonds for longer grinding life, clean and faster cutting. Can be used on all conventional grinders made today. Such as Diamond Pacific, Barranca, Maxant, Graves, as well as other cabbing machines. All wheels have a 1in. Diameter and include bushing to accommodate 3/4in., 5/8in. and 1/2in. arbors. Individually boxed. The plastic hubs are lighter and can be used on less powerful grinding machines. We do not offer re-plating of the wheels, it is more cost effective to re-cycle the wheels.
Recently Viewed Products
ARE YOU USING RIGHT TOOLS
FOR YOUR APPLICATION?
LET US
HELP YOU
HAVING ISSUES WITH
YOUR CURRENT TOOLS?
Knowledge Center
02
Jun
How to properly use Diamond Tools
UKAM Industrial Superhard Tools manufactures precision diamond tools for a large variety of applications, materials, and industries.
Share this Article with Friend or Colleague
Metal Bonded Diamond Tools are “impregnated” with diamonds. This means that selected diamonds...
02
Jun
Why use diamond
Diamond is the hardest material known to man kind. When used on diamond/tools, diamond grinds away material on micro (nano) level. Due to its hardness Diamond will work all types of materials from...
02
Jun
Diamond vs CBN (cubic boron nitride) Tools
Cubic Boron Nitride (CBN) is a synthetic material that is renowned for its exceptional hardness and high thermal stability. It is composed of boron and nitrogen atoms arranged in a crystal lattice structure, similar to...
02
Jun
What is Diamond Mesh Size and how to select best one for your application
Diamond grit size can be defined as the size of the diamond particles used in the bond matrix. The larger the diamond particles (grit size) the faster the tool will cut.
Share this Article with Friend or...
02
Jun
What is Diamond Concentration and which to use for your application
Diamond concentration is measured based on the volume of diamond within a section of the tool. It is typically defined as Concentration 100, which equates to 4.4 carats per cubic centimeter of the diamond layer...
02
Jun
Diamond Tool Coolants Why, How, When & Where to Use
Coolant is one of the most overlooked variables in the overall diamond or cbn tool machining process. Effective and proper use of coolant and recalculating coolant system will pay off in terms of improved surface...
17
May
Get to Know the Diamond Tool Bond Types and Which to use for your application
Selecting the appropriate diamond bond type for specific applications is crucial for several reasons. Diamond bond type directly affects the tool's performance, efficiency, and longevity. Different bond types determine how well a tool can withstand...
09
Oct
How to Properly Use Diamond Carving Points
Diamond carving points are essential tools for anyone working with hard materials like glass, stone, and metals. These tools help with detailed tasks like engraving and finishing, providing good control and helping you work efficiently....
- Unmatched Selection For Many Applications
- Superior Quality & Consistency
- Immediate Worldwide Delivery
- Technical Support & Expertise
- American Based Manufacturer
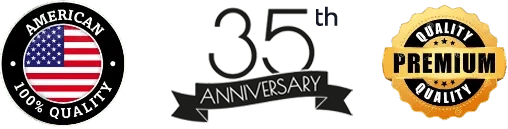

- Different Product
- Different Technology
- Different Company
- Expect MORE from your tools
Let Us HELP You!
Subscribe To Our Newsletter
Signup for email offers, updates, and more
Contact Us
- 25205 & 25201 Avenue Tibbits Valencia CA 91355 USA
-
Phone : (661) 257-2288
FAX : (661) 257 -3833 - lel@ukam.com
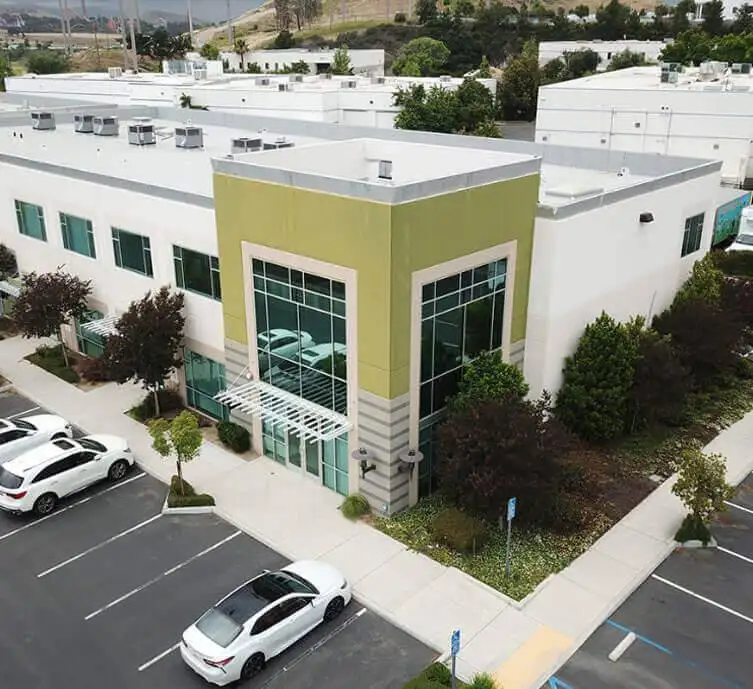
UKAM Industrial Superhard Tools is a U.S. High Technology, Specialty Diamond Tool & Equipment manufacturer. We specialize in producing ultra thin & high precision cutting blades and precision cutting machines diamond drills, diamond micro tools, standard & custom advanced industrial diamond tools and consumables.
- 25205 & 25201 Avenue Tibbits Valencia CA 91355 USA
-
Phone : (661) 257-2288
FAX : (661) 257 -3833 - lel@ukam.com
- 25205 & 25201 Avenue Tibbits Valencia CA 91355 USA
-
Phone : (661) 257-2288
FAX : (661) 257 -3833 - lel@ukam.com
DIAMOND TOOLS BY BOND
EQUIPMENT
KNOWLEDGE CENTER
OUR PRODUCTS
COMPANY
CUSTOMER SERVICE
Shipping Methods


Safe & Secure Payments

© Copyright 1990-2025. UKAM Industrial Superhard Tools – Terms of Use