-
0 items in quote
No products in the Quote Basket.
DESCRIPTION
SPECIFICATIONS
INDUSTRIES USED IN
FAQ
ACCESSORIES
USAGE RECOMENDATION
DESCRIPTION
Tab Content
SPECIFICATIONS
- Shape:Diamond Cylinder
- Diameters: 1mm to 10mm
- shank diameter: 3/32″ (2.35mm)
- Overall length: 1.5″
- Bond Type: Nickel Bond (plated)
- Diamond Grit Size: 120 mesh
INDUSTRIES USED IN
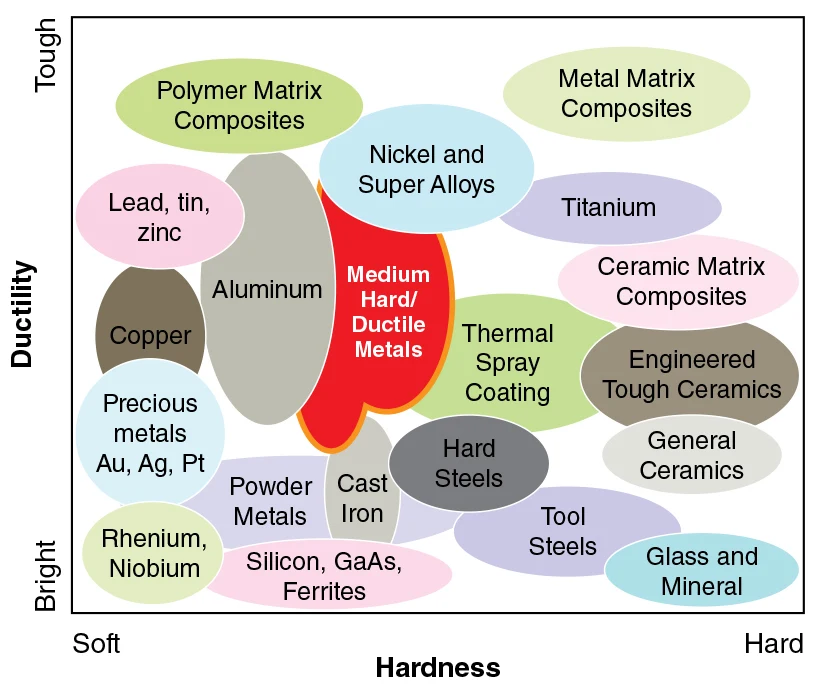

INDUSTRIES USED IN:
- Advanced Ceramics
- Composites
- Glass
- Geology
- Quartz
- Materials Research
- Medical Devices
- Metallography
- Photonics / Optics
- Semiconductor
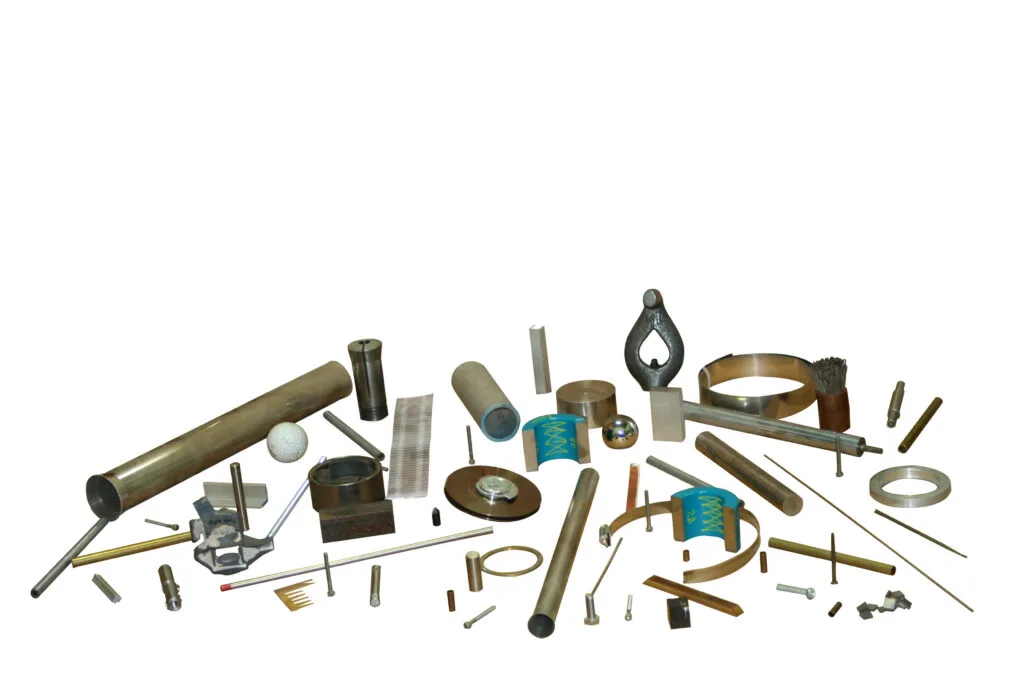
Ferrous & Non-Ferrous Metals:
- Plain Carbon Steels
- Electronic Packages
- Stainless Steels Plastics
- Tool Steels Fasteners
- Aluminum Refractories
- Copper Base Alloys Integrated Circuits
- Magnesium Thermal Spray Coatings
- Titanium Metal Matrix Composites
- Biomedical Wafers
- Petrographic
- PCB.s Ceramics
FAQ
Our carving points are versatile and can be used on a range of materials, including glass, stone, ceramics, and metal.
Yes, our Electroplated Diamond Carving Points are designed to be compatible with most rotary tools.
The carving points are extremely durable, thanks to the high-quality electroplated diamond coating.
Yes, our carving points come in a variety of shapes and sizes to suit different applications.
The carving points can be easily cleaned with water and a soft brush. Store them in a dry place to ensure their longevity.
The carving points are very sharp, thanks to the high-quality diamonds used in the electroplating process.
Yes, our carving points are also suitable for wood carving, providing precision and fine detailing.
Please check with the retailer or contact our customer service for information on warranties.
The choice of size and shape depends on the specific requirements of your project. For intricate detailing, a finer tip is recommended, while a rounded tip is suitable for smoother curves.
The carving points are typically sold in sets. Please check with the retailer for availability of individual carving points.
The longevity of the diamond coating depends on the usage and material being worked on, but it is designed to be long-lasting and durable.
Yes, our carving points are safe to use when operated correctly. However, it is important to follow safety instructions and wear protective gear during use.
Yes, our carving points are perfect for engraving on glass, allowing you to create intricate designs with ease.
The diamonds used in our carving points are of optimal hardness to cut through tough materials while providing a smooth and clean finish.
Yes, our Electroplated Diamond Carving Points are suitable for both professional and hobbyist use.
Electroplated diamonds are bonded to the surface through an electroplating process, providing a strong and durable coating that is superior to other types of diamond coatings.
Yes, our carving points can be used on metals, allowing you to add personalized engravings to jewelry, watches, and other metal accessories.
Yes, the electroplated diamond coating provides rust resistance, ensuring the longevity of the carving points.
If you are not satisfied with the product, please contact our customer service team, and we will do our best to address your concerns.
For best results, ensure that you are using the correct size and shape for your project, and follow all safety instructions and guidelines provided with the product.
No, the Electroplated Diamond Carving Points cannot be resharpened. However, their durable design ensures they remain sharp for extended periods.
The ideal speed setting depends on the material you are working on. We recommend starting with a lower speed and gradually increasing until you find the most suitable setting for your project.
Yes, the fine tip and precision design of our carving points make them ideal for carving lettering or text on various materials.
Yes, our carving points are designed to be suitable for both left and right-handed users.
We recommend storing the carving points in their original packaging or a suitable storage case, keeping them dry and protected from dust and debris.
We recommend using our carving points with a rotary tool for optimal performance and safety. Using them with a drill press may not provide the desired results.
Please check with the retailer or contact our customer service for information on satisfaction guarantees.
To prevent overheating, avoid applying excessive pressure, and allow the tool to do the work. It is also recommended to take regular breaks during extended use.
Our carving points are designed for use on glass, stone, ceramics, and metal. We recommend consulting with a professional before using them on precious stones or gems.
Our Electroplated Diamond Carving Points are designed to offer superior quality, performance, and versatility compared to other similar products on the market. Their high-quality diamond coating and precise craftsmanship make them the ideal choice for both professionals and hobbyists alike.
While the carving points can be used on wet surfaces, we recommend using them on dry surfaces for best results and to prolong their lifespan.
The choice of carving point depends on the material you are working with and the level of detail required. For intricate detailing, a finer tip is recommended, while a rounded tip is suitable for smooth curves.
Yes, our carving points are suitable for carving softer stones like soapstone, allowing for precision and fine detailing.
The Electroplated Diamond Carving Points cannot be sharpened. They are designed to remain sharp for extended periods of use.
Yes, our carving points are ideal for intricate pottery or ceramic work, providing precision and fine detailing.
Yes, our Electroplated Diamond Carving Points are compatible with Dremel tools and most other rotary tools.
Always wear appropriate safety gear, including goggles and gloves, and follow all instructions and guidelines provided with the product.
While the carving points are primarily designed for engraving and sculpting, they may also be used for cutting certain materials.
Yes, the carving points are easy to clean with water and a soft brush. We recommend drying them thoroughly before storing.
The lifespan of the carving points depends on the frequency of use and the materials being worked on. With proper care and maintenance, they are designed to last for extended periods.
The primary purpose of these carving points is for engraving and sculpting. They are not recommended for polishing or buffing.
The carving points may not come with a user manual or guide. However, you can find instructions on how to use them with your specific rotary tool in the tool’s manual.
Always ensure that the rotary tool is turned off and unplugged before changing the carving points. Use the tool’s collet or chuck to securely attach the carving point, and test it at a low speed before starting your project.
While the carving points can be used for intricate detailing, professional art restoration work should be left to qualified experts with the appropriate tools and knowledge.
The electroplated diamond coating provides resistance to wear and tear, ensuring the longevity of the carving points.
The carving point should be securely attached to the rotary tool’s collet or chuck and should not wobble or come loose during use. Always test the carving point at a low speed before starting your project.
While the carving points are suitable for small to medium-sized sculpting projects, larger-scale projects may require specialized tools and equipment.
Yes, our carving points are designed with precision and are suitable for engraving on delicate materials such as glass and ceramics.
The recommended maintenance includes cleaning the carving points with water and a soft brush after each use, and storing them in a dry place.
Yes, our carving points are ideal for creating custom jewelry, allowing you to add intricate designs and engravings to your pieces.
Yes, the electroplated diamond coating is designed to handle hard stones like granite and marble with precision and ease.
The carving points are designed to be compatible with most rotary tool brands, but we recommend checking with the manufacturer or retailer to ensure compatibility with your specific tool.
Yes, the carving points are suitable for relief carving, allowing you to create intricate designs with depth and dimension.
Absolutely! These carving points are ideal for adding textures to a variety of surfaces, enhancing your creative projects.
Store the carving points in their original packaging or a protective case, away from moisture and extreme temperatures, to prevent damage.
While the carving points can be used on metals, they are not specifically designed for rust removal and may not be the most effective tool for this purpose.
Yes, the carving points are user-friendly and suitable for both beginners and experienced crafters.
Yes, the carving points can be used on acrylic and plastic materials, but caution should be taken to avoid melting the material.
If a carving point breaks or becomes damaged, discontinue use immediately and contact our customer service team for assistance.
The carving points are primarily designed for engraving, sculpting, and carving. While they may be capable of drilling small holes, we recommend using a drill bit for this purpose
The carving points are primarily designed for engraving, sculpting, and carving. While they may be capable of drilling small holes, we recommend using a drill bit for this purpose.
Yes, the fine tip of our carving points is perfect for stippling or dot work, allowing you to create detailed designs with ease.
The carving points can be used on softer woods, but they are primarily designed for harder materials like stone, glass, and metal.
Yes, the carving points can be used to add intricate textures and patterns to clay or pottery.
The carving points are not recommended for engraving on leather as the material is soft and may not provide the desired results.
When using the carving points on metal, always wear protective gear including safety glasses and gloves to prevent injuries.
The carving points are made from high-quality steel with an electroplated diamond coating for optimal performance and durability.
While the carving points are suitable for use on a variety of materials, we recommend consulting with a professional before using them on gemstones.
To ensure the longevity of the carving points, clean them after each use, store them in a dry place, and avoid dropping them as this could damage the tip.
The carving points are designed to be compatible with most rotary tool attachments, but we recommend checking with the manufacturer or retailer for compatibility with your specific attachments.
Yes, our carving points are perfect for creating engraved designs on ceramic tiles, allowing you to add personalized touches to your home decor.
The carving points are suitable for use on various types of glass, including tempered and stained glass, providing precise and intricate detailing.
Yes, the carving points are perfect for creating mandalas or circular designs, with their precision allowing for symmetrical and detailed patterns.
The recommended way to clean the carving points is with water and a soft brush, ensuring they are dried thoroughly before storage.
While the carving points can be used on fiberglass materials, caution should be taken to avoid damaging the surface.
Yes, the carving points are suitable for engraving on metal jewelry, allowing you to add intricate designs and personalization to your pieces.
The precision design and high-quality diamond coating of the carving points make them perfect for intricate and detailed work, providing clean and precise lines.
Yes, the carving points are suitable for use on slate and other natural stones, allowing for detailed sculpting and engraving.
While the carving points can be used on some synthetic materials, we recommend checking the material compatibility before use.
Yes, the carving points can be used to create textures on metal surfaces, adding depth and dimension to your projects.
We recommend avoiding using the carving points on soft and flexible materials, as they may not provide the desired results. Always check material compatibility before use.
ACCESSORIES
Showing 1 – -1 of 16 results Showing all 16 results Showing the single result No results found
Sort by Name A – Z
Filters Sort results
Reset Apply
Image | Item No. | Description | Price | Quantity | Add to cart |
---|---|---|---|---|---|
Color: 5/8″-11″ thread. Fits into drill press chuck. Shank adapter threads into 5/8″-11″ female thread of diamond drill. Can be used with any other tool with 5/8″-11″ thread. | $26.72 | Max: Min: 1 Step: 1 | |||
Color: 5/8″-11″ thread. Fits into drill press chuck. Shank adapter threads into 5/8″-11″ female thread of diamond drill. Can be used with any other tool with 5/8″-11″ thread. | $22.46 | Max: Min: 1 Step: 1 | |||
1 Gallon Blue SMART CUT® General Materials Formula Synthetic Water Soluble Coolant | $99.81 | Max: Min: 1 Step: 1 | |||
1 Quart Blue SMART CUT® General Materials Formula Synthetic Water Soluble Coolant | $34.81 | Max: Min: 1 Step: 1 | |||
5 Gallons Blue SMART CUT® General Materials Formula Synthetic Water Soluble Coolant | $317.41 | Max: Min: 1 Step: 1 | |||
55 Gallons Blue SMART CUT® General Materials Formula Synthetic Water Soluble Coolant | $1,745.00 | Max: Min: 1 Step: 1 | |||
1/2″ x 1/2″ x 6.0″ White Recommended for coarser grits found in segment wheels, core drills, or Blanchard grinding. Excellent performance on 120 grit tools. | $8.65 | Max: Min: 1 Step: 1 | |||
1.0″ x 1.0″ x 6.0″ White Recommended for coarser grits found in segment wheels, core drills, or Blanchard grinding. Excellent performance on 120 grit tools. | $15.99 | Max: Min: 1 Step: 1 | |||
1/2″ x 1/2″ x 6.0″ White For use on diamond tools 150 to 220 Grit Size. | $8.65 | Max: Min: 1 Step: 1 | |||
1.0″ x 1.0″ x 6.0″ Black Recommended for use in Diamond Tools 150 Grit Size (mesh size) or finer. | $15.39 | Max: Min: 1 Step: 1 | |||
2.0″ x 2.0″ x 6.0″ Black Recommended for use in Diamond Tools 150 Grit Size (mesh size) or finer. | $39.47 | Max: Min: 1 Step: 1 | |||
1.0″ x 1.0″ x 6.0″ Black Recommended for coarser grits found in segment wheels, core drills, or Blanchard grinding. Excellent performance on 120 grit tools. | $15.99 | Max: Min: 1 Step: 1 | |||
2.0″ x 2.0″ x 6.0″ Black Recommended for coarser grits found in segment wheels, core drills, or Blanchard grinding. Excellent performance on 120 grit tools. | $39.47 | Max: Min: 1 Step: 1 | |||
$154.87 | Max: Min: 1 Step: 1 | ||||
$154.87 | Max: Min: 1 Step: 1 | ||||
$235.00 | Max: Min: 1 Step: 1 |
USAGE RECOMENDATION
Step 1: Preparation:
- Gather all necessary materials and ensure you have the correct carving point for your project.
- Wear appropriate safety gear including goggles, gloves, and a dust mask if needed.
Step 2: Set-Up:
- Ensure your rotary tool is turned off and unplugged.
- Attach the carving point to the rotary tool according to the tool’s instructions.
- Securely fasten the carving point in the collet or chuck of the rotary tool.
- Plug in and turn on your rotary tool.
Step 3: Testing:
- Test the carving point on a scrap piece of material to ensure it is properly attached and working correctly.
- Adjust the speed of your rotary tool according to the material you are working with.
Step 4: Engraving or Sculpting:
- Hold the rotary tool like a pen, with a firm but comfortable grip.
- Gently touch the carving point to the material, starting at one end of your design.
- Move the carving point along the material, following your design or pattern.
- Use steady and controlled movements, letting the tool do the work.
- Work in small sections, periodically checking your progress.
Step 5: Finishing:
- Once you have completed your design, turn off and unplug the rotary tool.
- Carefully remove the carving point from the tool.
- Clean the carving point with water and a soft brush, and dry thoroughly before storing.
- Store the carving point in its original packaging or a protective case.
Step 6: Maintenance:
- Regularly clean and inspect your carving points for any signs of wear or damage.
- Replace any carving points that become dull or damaged.
Step 7: Post-Project Cleaning and Storage:
- After using the carving points, it is important to clean them thoroughly to remove any debris or residue.
- Use a soft brush and water to gently clean the carving points. Avoid using any harsh chemicals or abrasive materials as this can damage the electroplated diamond coating.
- Dry the carving points completely before storing them to prevent rust or corrosion.
- Store the carving points in a dry and cool place, away from direct sunlight or extreme temperatures.
- If possible, store the carving points in their original packaging or a protective case to prevent them from getting damaged.
Step 8: Regular Maintenance:
- Regularly inspect your carving points for any signs of wear or damage. If you notice any issues, replace the carving point immediately to avoid any accidents or injuries.
- If the carving point becomes dull over time, consider having it sharpened by a professional to extend its lifespan.
Step 9: Safety Precautions:
- Always use the carving points in a well-ventilated area to avoid inhaling any dust or debris.
- If you are working on a project that produces a lot of dust, consider using a dust collector or vacuum to keep the area clean.
- Be aware of your surroundings and keep any loose clothing or hair away from the rotary tool while it is in operation.
Step 10: Creativity and Experimentation:
- Once you are comfortable with the basic operation of the carving points, don’t be afraid to experiment and get creative with your projects.
- Try different techniques and patterns to achieve unique and intricate designs.
- Share your work with others and learn from fellow crafters to continuously improve and expand your skills.
Step 11: Advanced Techniques:
- As you gain more experience, you can start experimenting with advanced techniques such as layering and cross-hatching to add depth and texture to your projects.
- Practice on scrap materials first before applying these techniques to your final project.
Step 12: Combining Materials:
- Try using the carving points on different materials such as glass, ceramics, or even gemstones to create unique and personalized pieces.
- Experiment with combining different materials in one project to add contrast and interest.
Using the Right RPM’s for your Application
The optimal RPM (revolutions per minute) for using electroplated diamond carving points depends on several factors, including the material being carved, the size and shape of the carving point, and the specific project requirements. However, here are some general guidelines to consider:
1.Soft Materials (e.g., wood, plastic):
- Use a lower RPM, typically between 5,000 to 15,000 RPM, to prevent overheating and minimize the risk of damaging the material.
2.Hard Materials (e.g., glass, stone, metal):
- Use a higher RPM, typically between 10,000 to 30,000 RPM, to effectively cut through the material and achieve a smooth finish.
3.Intricate or Detailed Work:
- Use a lower RPM to have more control and precision when working on intricate or detailed designs.
4. General Carving and Shaping:
- Use a moderate RPM that provides a balance between cutting efficiency and control.
It is important to always start with a lower RPM and gradually increase it until you find the optimal speed for your specific project. Additionally, always refer to the manufacturer’s guidelines and recommendations for using electroplated diamond carving points, as they may provide specific RPM ranges for their products.
Recommended Coolant & Application
When using electroplated diamond carving points, introducing a coolant can help reduce heat, minimize dust, and potentially extend the life of the carving points. Water is typically used as a coolant for this type of application. Here’s how to use and introduce coolant:
Coolant to Use:
- Use clean water as a coolant. It is the most common and safest option for cooling and lubricating the carving points during operation.
How to Introduce Coolant:
Dipping Method:
- Dip the carving point in water before starting the carving or engraving process.
- Periodically withdraw the carving point and dip it back in water to keep it cool.
Spray Bottle Method:
- Fill a spray bottle with clean water.
- Spray the water onto the material being carved to keep the carving point cool during operation.
Sponge Method:
- Soak a sponge in water and place it near your working area.
- Periodically touch the carving point to the wet sponge to cool it down.
Additional Tips:
- Ensure that your rotary tool is compatible with the use of coolant and that it is protected from water to avoid any electrical hazards.
- If you’re working on an electrical device or material that may be damaged by water, be extra cautious to prevent water from coming into contact with electrical components.
- Always follow the manufacturer’s guidelines and recommendations for using coolant with electroplated diamond carving points.
Recommended Feed Rates
The feed rate and pressure to apply when using electroplated diamond carving points depend on several factors, including the material being carved, the hardness of the diamond, the size and shape of the carving point, and the specific project requirements. However, here are some general guidelines to consider:
Feed Rate:
- The feed rate should be adjusted based on the material being carved. For softer materials like wood or plastic, a slower feed rate is usually sufficient. For harder materials like stone or glass, a moderate to faster feed rate may be needed.
- It’s important to allow the tool and carving point to do the work, rather than forcing the tool through the material.
Pressure to Apply:
- Apply light to moderate pressure when using the carving points. Too much pressure can cause the carving point to wear down quickly, damage the material, or even break the point.
- It’s important to maintain a consistent pressure to achieve a smooth and even carving or engraving.
Additional Tips:
- Always start with a light pressure and adjust as needed based on the material and desired outcome.
- Pay attention to the feedback from the tool and material. If you notice any unusual sounds or resistance, adjust the feed rate or pressure accordingly.
- Be patient and take your time, especially when working on intricate or detailed designs.
Remember that practice and experience are key to finding the optimal feed rate and pressure for your specific projects. It may take some trial and error to find the right balance, but with time and practice, you will develop a feel for what works best.
Selecting Right Diamond Carving Point Shape for your Application
The shape of the electroplated diamond carving point to use depends on the specific project requirements and the desired outcome. Here are some general guidelines to consider:
Cylinder or Diamond Bullet Shapes:
- Ideal for carving, shaping, and hollowing out areas.
- Great for working on flat and curved surfaces.
Diamond Bullet or Spherical Shapes:
- Suitable for creating rounded details, concave cuts, and hollowing out areas.
- Perfect for carving curved lines and patterns.
Pointed or Needle Shapes:
- Excellent for fine detailing, engraving, and precision work.
- Ideal for creating intricate patterns and designs.
Wheel or Disc Shapes:
- Suitable for cutting, shaping, and grinding flat surfaces.
- Great for creating straight lines and edges.
Tapered Shapes:
- Ideal for carving and shaping in tight or hard-to-reach areas.
- Perfect for creating angles and bevels.
Flame Shapes:
- Flame shapes are versatile and can be used for both detailed work and larger carvings.
- They are suitable for carving, shaping, and finishing work.
Oval Shapes:
- Oval shapes are perfect for smooth contouring and shaping.
- They are great for creating rounded edges and smooth finishes.
Inverted Diamond Bullet Shapes:
- Inverted Diamond Bullet shapes are ideal for creating v-cuts and angled details.
- They can be used for precision work in tight corners and intricate designs.
Parallel Shapes:
- Parallel shapes are great for carving flat and even surfaces.
- They are often used for leveling and smoothing out areas.
Custom Shapes:
- Custom-shaped carving points are available for specific applications and unique project requirements.
- These may include shapes designed for specific materials, patterns, or artistic effects.
Rounded Cylinder Shapes:
- Rounded cylinder shapes are ideal for creating soft curves and contours.
- They can be used for both carving and smoothing out rough areas.
Tapered Cylinder Shapes:
- Tapered cylinder shapes provide precision and control for carving intricate details.
- They are great for working in tight spaces and creating defined edges.
Elliptical Shapes:
- Elliptical shapes are perfect for creating smooth, flowing lines and curves.
- They can be used for both carving and finishing work.
Square or Rectangular Shapes:
- Square or rectangular shapes are ideal for creating straight lines and sharp angles.
- They can be used for carving, shaping, and edging.
Specialty Shapes:
- Specialty shapes are designed for specific applications, such as carving lettering or creating specific patterns.
- They may include unique shapes that are not typically found in standard sets.
When choosing the shape of the electroplated diamond carving point, consider the following:
- Material: Different shapes may work better on certain materials.
- Detail Level: Finer details may require smaller, more pointed shapes, while larger areas may benefit from broader shapes.
- Comfort and Control: Choose a shape that feels comfortable in your hand and gives you the best control over the carving process.
- Versatility: Some shapes are more versatile and can be used for various tasks, while others are more specialized.
- Experimentation: Don’t be afraid to experiment with different shapes to find the one that works best for your project.
- Mixing and Matching: Sometimes, a combination of shapes may be necessary to achieve the desired result.
- Learning from Others: Watch tutorials or ask experienced carvers for advice on which shapes work best for specific applications.
It’s important to consider the size and shape of the area you are working on, as well as the level of detail required for the project. For larger areas and rough shaping, choose a larger, more robust carving point. For fine detailing and precision work, opt for a smaller, more pointed carving point.
Experimenting with different shapes and sizes will help you find the perfect carving point for your needs and preferences. As you gain experience, you will develop a sense of which shapes work best for different applications and materials.
Equipment Diamond Carving Points are Used On:
Electroplated diamond carving points are typically used with a rotary tool or a die grinder. Here are the details:
Rotary Tool:
- A rotary tool is a handheld, motor-driven device that rotates a variety of attachments at high speeds.
- Rotary tools are versatile and can be used for a wide range of applications, including carving, engraving, polishing, grinding, and more.
- They are available in both corded and cordless versions, with cordless versions providing more mobility and flexibility.
- Popular brands include Dremel, Foredom, Proxxon, and Black & Decker.
Die Grinder:
- A die grinder is a more powerful, industrial-grade version of a rotary tool.
- It is typically used for heavy-duty applications, such as grinding, cutting, and polishing metals and other hard materials.
- Die grinders are available in both electric and pneumatic (air-powered) versions.
- They are generally more robust and durable than rotary tools and can handle more demanding tasks.
When choosing a rotary tool or die grinder for your electroplated diamond carving points, consider the following:
- Power Source: Consider whether a corded or cordless tool is more suitable for your needs.
- Speed Range: Look for a tool that offers a range of speeds, as this will give you more control over the carving process.
- Collet Size: Ensure that the tool has a collet size that is compatible with the shank size of your carving points.
- Ergonomics: Choose a tool that feels comfortable in your hand and allows for precise control.
- Brand and Model: Consider the brand and model of the tool, as this can affect the availability of accessories and replacement parts.
Using the right equipment will enhance your carving experience and allow you to achieve the best possible results with your electroplated diamond carving points.
Using the Right Collet or Chuck to hold the diamond carving points on your machine
For electroplated diamond carving points, using a collet chuck is typically recommended. A collet chuck provides a secure and precise method for holding the carving point, allowing for better control and accuracy during the carving or engraving process. Here are the main differences and benefits of each:
Collet Chuck:
- Provides a secure and precise hold on the carving point.
- Minimizes vibration and wobble, resulting in smoother and more accurate carving or engraving.
- Allows for easy and quick tool changes.
- Suitable for smaller diameter shanks, which are common with diamond carving points.
Check or Chuck:
- Typically used for holding larger diameter tools or accessories.
- May not provide as precise or secure a hold on smaller diameter carving points.
- May require additional accessories or adapters to hold smaller diameter shanks.
In conclusion, for electroplated diamond carving points, which often have smaller diameter shanks, a collet chuck is preferred due to its ability to securely and precisely hold the carving point, resulting in better control, accuracy, and overall performance during the carving or engraving process.
Using the Right Diamond Grit Size for your Application
The diamond grit size to use depends on the specific application and the material you are working with. Here are some general guidelines:
Coarse Grit (30-60 grit):
- Ideal for heavy material removal, shaping, and grinding.
- Suitable for working with harder materials like stone, glass, and metal.
Medium Grit (70-120 grit):
- Suitable for general-purpose carving and shaping.
- Works well on a variety of materials including wood, stone, and glass.
Fine Grit (150-300 grit):
- Perfect for finishing, polishing, and detailed work.
- Suitable for all types of materials including wood, stone, glass, and metal.
Extra Fine Grit (above 300 grit):
- Ideal for final polishing and achieving a smooth, mirror-like finish.
- Suitable for all types of materials including wood, stone, glass, and metal.
It is always best to start with a coarser grit to remove excess material and shape the piece, then progressively move to finer grits to achieve the desired smoothness and finish. Also, remember to follow the manufacturer’s recommendations and guidelines for the specific electroplated diamond carving points you are using.
Selecting Right Bond Type to use for your Diamond Carving Points
When selecting the right bond type for your application, it’s essential to consider the material you will be working with, the desired outcome, and the specific requirements of your project. Here are some general guidelines on how to choose between sintered (metal bond), plated, brazed bond, and resin bond:
Sintered (Metal Bond):
- Best suited for hard materials like stone, glass, and ceramics.
- Durable and long-lasting, making it ideal for heavy-duty applications.
- Provides a slower cutting speed but offers a longer tool life.
Plated:
- Suitable for a wide range of materials including stone, glass, and ceramics.
- Ideal for detailed work and precision carving.
- Provides a faster cutting speed but may wear out more quickly than sintered bonds.
Brazed Bond:
- Suitable for hard materials like stone, glass, and ceramics.
- Offers a good balance between cutting speed and tool life.
- Ideal for both heavy-duty applications and detailed work.
- Offers very fast cutting speed and aggressive and free grinding.
- Can by used dry (without coolant) in some applications
Resin Bond:
- Best suited for softer materials like marble, limestone, and composite materials.
- Ideal for polishing and achieving a smooth finish.
- Provides a faster cutting speed but may wear out quickly on harder materials.
- Consider the hardness of the material you will be working with. Harder materials typically require a stronger bond type, while softer materials may be better suited to a softer bond.
- Consider the level of precision and detail required for your project. Detailed work may require a finer bond type, while heavy-duty applications may benefit from a stronger bond.
Selecting Right Diameter to use for your application
When selecting the right tool diameter of the head or tip of an electroplated diamond carving point, consider the following factors:
Material Thickness:
- For thicker materials, a larger diameter may be more suitable as it can handle more material removal.
- For thinner or more delicate materials, a smaller diameter can provide more precision and control.
Detail Level:
- For intricate and detailed work, choose a smaller diameter tip that allows for precision and intricate control.
- For rough shaping or larger carvings, a larger diameter tip may be more appropriate.
Size of the Work Area:
- For large areas, a larger diameter tip can cover more surface area and speed up the process.
- For smaller or confined spaces, a smaller diameter tip will provide better access and control.
Desired Outcome:
- Consider the final outcome you want to achieve. If you’re looking for a smooth and polished finish, a smaller diameter may be more suitable. If you’re looking to remove a lot of material quickly, a larger diameter may be more appropriate.
Compatibility with Your Tool:
- Make sure the diameter of the head or tip is compatible with your rotary tool or die grinder. Check the collet size and ensure it can accommodate the diameter of the carving point.
User Experience and Skill Level:
- For beginners or those less experienced, starting with a medium-sized diameter might be more manageable and allow for better control.
- As you gain more experience, you can then experiment with different diameters to find what works best for your specific needs.
Type of Carving or Engraving:
- For deep carving or engraving, a larger diameter might be more appropriate to remove more material.
- For surface detailing or light engraving, a smaller diameter will provide more precision.
Tool RPM and Feed Rate:
- Consider the recommended RPM and feed rate for the specific diameter of the tool. Different diameters may perform optimally at different speeds and feed rates.
Cost and Availability:
- Take into account the cost and availability of the specific diameter you are considering. Some diameters may be more readily available than others.
Personal Preference:
- Ultimately, personal preference plays a role in selecting the right diameter. Through trial and error, you may find that you prefer working with a specific diameter based on your individual carving or engraving style.
When selecting the right tool diameter, it’s crucial to find a balance between the requirements of the material, the level of detail, and your personal preference and experience. It may take some experimentation to find the diameter that works best for you, but the effort will be worth it in the end when you achieve the desired results for your project.
2090501, 2090502, 2090503, 2090504, 2090505, 2090506, 2090507, 2090508, 2090509
Showing 1 – 9 of 9 results Showing all 9 results Showing the single result No results found
Sort by Price low to high
Filters Sort results
Reset Apply
Image | Item No | Outside Diameter | Shank Diameter | Price | Quantity | Add to cart |
---|---|---|---|---|---|---|
1mm (.040”) | 3/32” (2.35mm) | $9.98 | Max: Min: 1 Step: 1 | |||
2mm (.080”) | 3/32” (2.35mm) | $9.98 | Max: Min: 1 Step: 1 | |||
3mm (.118”) | 3/32” (2.35mm) | $15.95 | Max: Min: 1 Step: 1 | |||
4mm (.118”) | 3/32” (2.35mm) | $15.95 | Max: Min: 1 Step: 1 | |||
5mm (.196”) | 3/32” (2.35mm) | $22.95 | Max: Min: 1 Step: 1 | |||
7mm (.275”) | 3/32” (2.35mm) | $24.95 | Max: Min: 1 Step: 1 | |||
8mm (.314”) | 3/32” (2.35mm) | $24.95 | Max: Min: 1 Step: 1 | |||
9mm (.354”) | 3/32” (2.35mm) | $31.95 | Max: Min: 1 Step: 1 | |||
10mm (.393”) | 3/32” (2.35mm) | $31.95 | Max: Min: 1 Step: 1 |
How SMART CUT® Bond Works?
Step 1
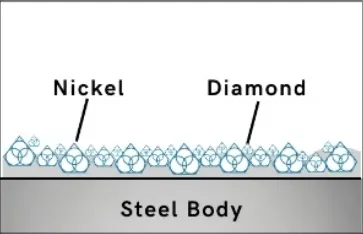
Sharpest And Finest Quality Diamonds
Diamonds or CBN Crystals are activated only at the exposed layer. As Bond Matrix layer begin to wear out, diamonds in a new Bond Matrix layer are immediately activated, substituting the already used up diamond layer. The SMART CUT® Bond Diamond Bond makes sure every diamond is in the right place. and at the right time, working where you need it most.
Step 2
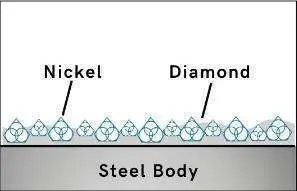
Diamonds or CBN Crystals
The newly exposed diamonds don’t effect diamonds already working on the material. Unlike many other diamond bonds, diamonds in a SMART CUT® remains sharp and grow sharper with each cut, prolonging product life and consistent performance.
Step 3
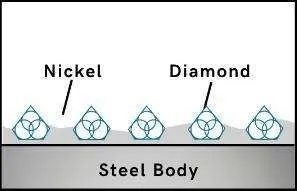
Advanced Formulated Open Diamond Bond Design
This advanced formulated open diamond bond design insures minimal chipping, fast
cut, constant speed of cut, minimal cutting noise, and most important of all, consistent performance.
About Nickel Bond (Electroplated) Tools
Electroplated (nickel bond) diamond products usually have a single layer of diamonds, held by a tough durable nickel alloy. Nickel is frequently used as a base for plating diamond. Because of its excellent strength, toughness and flexibility during the plating process. Electroplated diamond products are able to retain their original shape and dimensions thought their working life. Unlike sintered (meal bond) or resin bond diamond products, where diamond particles are buried in bond and held together by metal or resin binder deep inside.
Electroplating allows diamond particles to protrude from the bond matrix, providing a free, faster cutting action with minimum heat generation.
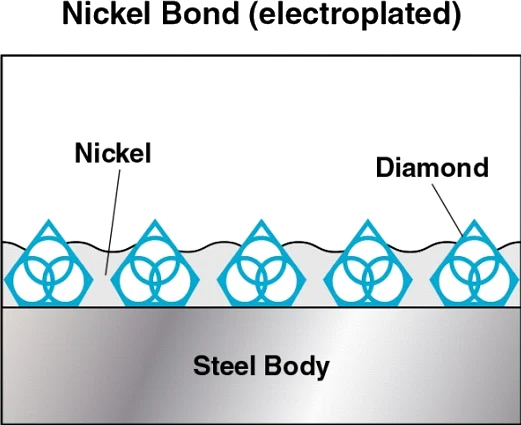
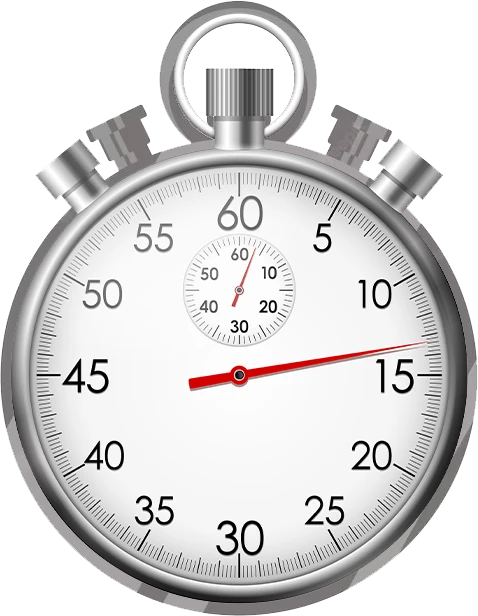
Faster & Freer Action
Diamond drills made utilizing SMART CUT technology are much more aggressive than your conventional Tools. They can cut faster, while still leaving behind a smooth finish free of material deformation.
Longer Life
In most cases tools manufactured utilizing SMART CUT technology, will outlast other conventional nickel bonded diamond CBN drills. SMART CUT diamond CBN tools are more sturdy than tools manufactured with conventional technologies. They are capable to retain their form and bond configuration all the way through the tools life.
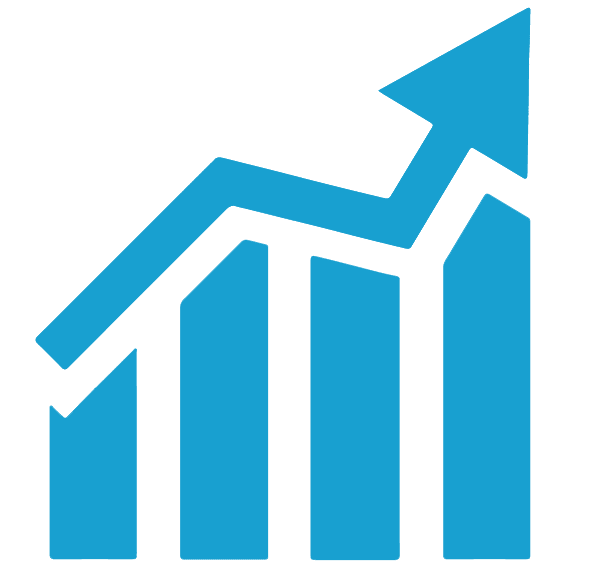
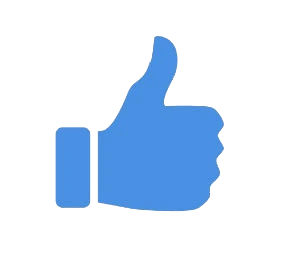
More Consistent Performance
SMART CUT Multi Layered Electroplated diamond cutting blade three diamond layers impregnated inside the bond matrix. Unlike Many Other blade Types, they wear evenly, and are known for their consistency. You will get consistent cutting speed, and overall consistent performance, with minimum amount of dressing even on the hardest to cut materials
Manufactured Using The Highest Quality Raw Materials
Only the highest quality synthetic diamonds and raw materials are used in the manufacturing process. The highest quality standards and product consistency is maintained, using sophisticated inspection and measurement equipment.
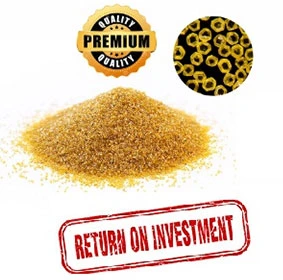
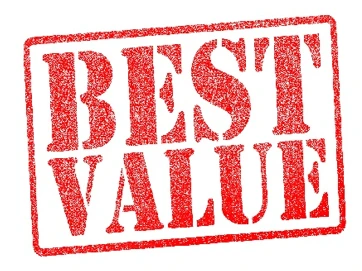
Best Performance & Value on the Market
SMART CUT Multi Layered Electroplated Diamond Drills are the best investment you can make! Although they may cost more than electroplated (nickel bond), Diamond Drills. They will more than pay for themselves in terms of overall performance and provide best Return on Investment.
Why Choose Us?
Optimize your application to ultimate level of efficiency
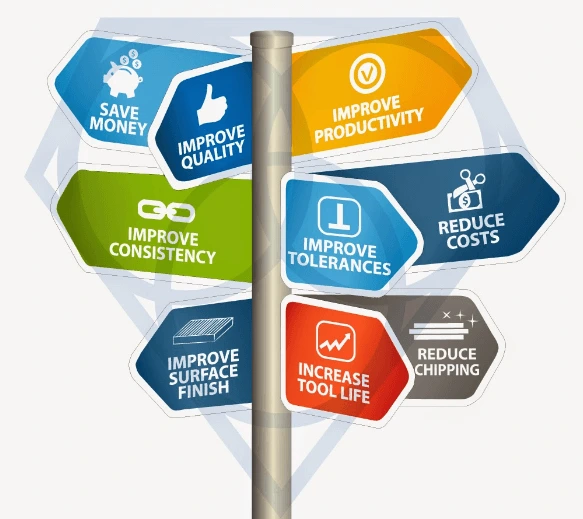
- Unmatched Selection For Many Applications
- Unmatched Technical Support & Expertise
- Superior Quality & Consistency
- Super Technology & innovation
- Immediate Worldwide Delivery
- American Based Manufacturer
-
Custom
Manufacturing - Better Value manufacturer Direct Price
Why Work With Us?
Read More
We produce diamond consumables for some of the leading world OEM manufacturers. We offer Manufacturers Direct Prices
We have the largest variety of diamond & cbn wafering blades available in stock. As well as large inventory of diamond & abrasive consumables. We also custom manufacture diamond and cbn tools, consumables and machines to better fit customer specific needs. Just about any tools & consumables can be designed and manufactured per client drawing or specificrtion
WE ARE A PARTNER IN YOUR SUCCESS
Our proprietory diamond chemistory , precision , manufacturing metods , quality control methods allow us to control and regulate the dozens of variables to that affect consumable life , quality , and consistency.
The more you understand about what we can do for you the better our partnership will be. Here you will find most comprehensive source of information and optimizing and improving your cutting , drilling , grinding and polishing on the web. find everything you ever wanted to know about diamond tools.
AMERICAN MANUFACTURER
"ONE OF THE MOST EXPERIENCED COMPANIES IN THE INDUSTRY"
Save Money Save up to 650%
COMPARE TO: BUEHLER , STRUERS , LECO & MANY OTHERS
Large Inventory & Custom Manufacturing
Umatched Technical Support
Developing close ties with our customers is the foundation of our business. At the core of
our company is a team of world class engineers, knowledgeable customer service personnel here to serve you. Whether is designing or manufacturing a special solution. We will go out of our way to optimizing your process to ultimate level of efficiency
Superior Quality & Consistency
EXPECT MORE FROM YOUR TOOLS
Comprehensive Source Of Information For Sample Preparation
Advanced Technology
As one of the few remaining independent U.S.Diamond Tool & machine builders. We have the experience & tradition to help you remain at frontier of technology Our experience has been further enhanced by acquiring assets and processes from some of the oldest American tool
manufacturers, along with their decades of experience and R& D. This has positioned us as one of the most experienced companies in the industry .Depend on us to bring you technology of tomorrow today.
Experience Makes All The Differences
Over the years we have worked with some of the leading Fortune 500 companies , thousands of universities , government and private research labs , and small organisations. We have made thousands of custom tools , built custom machines , work-holding fixtures , etc for hundreds of applications. Many of our staff members have been working in their respective fields for over 50 years and have gained a wealth of knowledge over the years
Let Us Help You
Related Products
Diamond Bullet, Plated Carving Point, set of 5 pcs
Diamond Cone, Plated Carving Point, set of 5 pcs
Diamond Cylinder, Plated Carving Point, set of 5 pcs
Diamond Flame, Plated Carving Point, set of 5 pcs
Diamond Rounded Tapered Cylinder, Plated Carving Point, set of 5 pcs
Diamond Tapered Inverted Cone, Plated Carving Point, set of 5 pcs
Diamond Tapered inverted cylinder, Plated Carving Point, set of 5 pcs
Plated Diamond Carving Point Set of 30 pcs
Plated Diamond Carving Point Set of 50 pcs
Recently Viewed Products

ARE YOU USING RIGHT DIAMOND CARVING POINTS
FOR YOUR APPLICATION?
LET US
HELP YOU
HAVING ISSUES WITH
YOUR CURRENT DIAMOND CARVING POINTS?
Knowledge Center
02
Jun
How to properly use Diamond Tools
UKAM Industrial Superhard Tools manufactures precision diamond tools for a large variety of applications, materials, and industries.
Share this Article with Friend or Colleague
Metal Bonded Diamond Tools are “impregnated” with diamonds. This means that selected...
02
Jun
Why use diamond
Diamond is the hardest material known to man kind. When used on diamond/tools, diamond grinds away material on micro (nano) level. Due to its hardness Diamond will work all types of materials from...
09
Oct
How to Properly Use Diamond Carving Points
Diamond carving points are essential tools for anyone working with hard materials like glass, stone, and metals. These tools help with detailed tasks like engraving and finishing, providing good control and helping you work efficiently....
- Unmatched Selection For Many Applications
- Superior Quality & Consistency
- Immediate Worldwide Delivery
- Technical Support & Expertise
- American Based Manufacturer
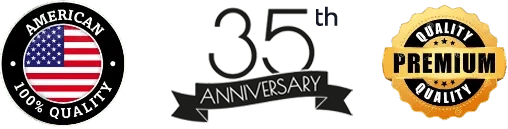

- Different Product
- Different Technology
- Different Company
- Expect MORE from your tools
Let Us HELP You!
Subscribe To Our Newsletter
Signup for email offers, updates, and more
Contact Us
- 25205 & 25201 Avenue Tibbits Valencia CA 91355 USA
-
Phone : (661) 257-2288
FAX : (661) 257 -3833 - lel@ukam.com
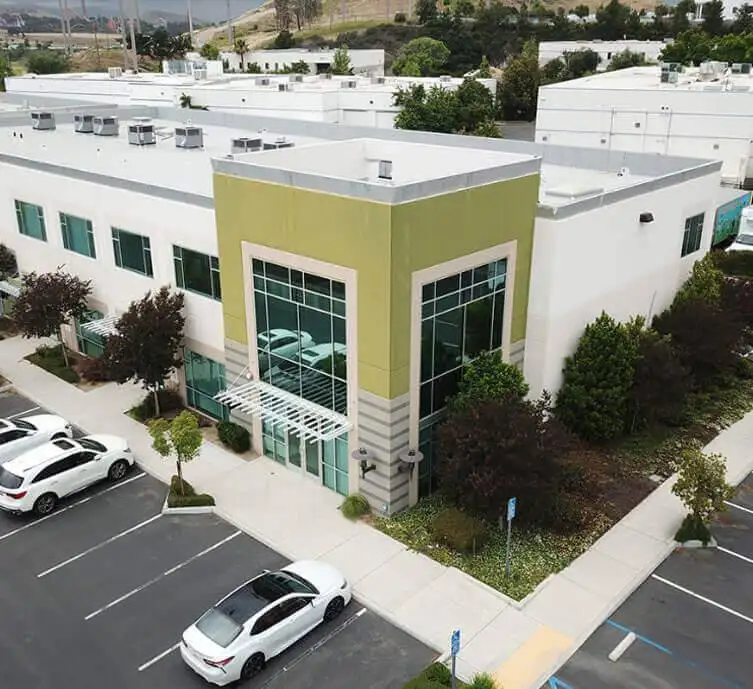
UKAM Industrial Superhard Tools is a U.S. High Technology, Specialty Diamond Tool & Equipment manufacturer. We specialize in producing ultra thin, high precision cutting blades, precision cutting machines diamond drills, diamond micro tools, standard & custom advanced industrial diamond tools and consumables.
- 25205 & 25201 Avenue Tibbits Valencia CA 91355 USA
-
Phone : (661) 257-2288
FAX : (661) 257 -3833 - lel@ukam.com
- 25205 & 25201 Avenue Tibbits Valencia CA 91355 USA
-
Phone : (661) 257-2288
FAX : (661) 257 -3833 - lel@ukam.com
DIAMOND TOOLS BY BOND
EQUIPMENT
KNOWLEDGE CENTER
OUR PRODUCTS
COMPANY
CUSTOMER SERVICE
Shipping Methods


Safe & Secure Payments

© Copyright 1990-2025. UKAM Industrial Superhard Tools – Terms of Use