-
0 items in quote
No products in the Quote Basket.
SMART CUT®
DIAMOND BACKGRINDING WHEELS
SMART CUT® Diamond Backgrinding Wheels are designed for precision thinning and flattening of silicon wafers, glass, and ceramic substrates. These high-performance wheels are used on backgrinding machines, including models from Disco, Okamoto, Strasbaugh, and other leading manufacturers. Available in sizes ranging from 8” to 14” O.D., they are engineered to handle a wide range of materials and applications, from semiconductor wafers to microelectronic packages.
These wheels are available in various bond types to suit different needs, including:
- Sintered (Metal Bond)
- Resin Bond
- Vitrified Bond
- Plated (Nickel Bond)
DESCRIPTION
SPECIFICATIONS
FREQUENTLY ASKED QUESTIONS
INDUSTRIES USED IN
ACCESSORIES
USAGE RECOMMENDATION
DESCRIPTION
Each bond type is customizable to meet the specific requirements of your application and material, ensuring optimal performance. By utilizing SMART CUT® Diamond Backgrinding Wheels, you can achieve:
- Improved Heat Dissipation: Reduces thermal resistance, critical for high-power devices.
- Increased Structural Integrity: Minimizes the risk of sub-surface damage, which could affect device reliability.
- Precise Thickness Control: Achieves wafer thicknesses down to less than 100 microns in certain applications.
SPECIFICATIONS
SMART CUT® Diamond Backgrinding Wheels are customizable to fit your specific needs. Common specifications include:
- Diameter: Available in 175 mm, 200 mm, 350 mm, and other sizes.
- Thickness: Ranges from 30 mm to 45 mm.
- Inside Diameter: Various options, including 76 mm, 127 mm, and others.
- Customizable Dimensions: All dimensions such as T, E, W, and X can be tailored to fit your requirements.
FREQUENTLY ASKED QUESTIONS
The available grit sizes typically range from coarse (around 60 grit) to ultra-fine (above 3000 grit), depending on the specific requirements of the grinding process.
The grit size choice depends on the desired surface finish and material removal rate. Coarser grits remove material faster but leave a rougher finish, while finer grits give a smoother finish but work more slowly.
Lifespan varies based on usage, the material being ground, and the wheel’s specifications. However, due to the hardness of diamond, these wheels generally have a longer lifespan compared to conventional abrasive wheels.
Store in a cool, dry place away from direct sunlight. Avoid storing under conditions of high humidity or drastic temperature changes.
Yes, diamond grinding wheels can be used for other materials like sapphire, gallium arsenide, and other compound semiconductors. However, the grinding parameters might need adjustments.
Ensure proper wheel dressing, maintain consistent grinding pressure, and use appropriate coolants to prevent thermal damage.
Common bond materials include resin, metal, vitrified, and electroplated. The choice of bond affects the wheel’s wear rate, heat dissipation, and grinding performance.
Resin bonds offer good flexibility and are suitable for fine grinding. Metal bonds are durable and used for rough grinding. Vitrified bonds have good form retention, and electroplated bonds offer precision.
RPM recommendations vary based on the wheel’s diameter, material being processed, and the desired finish. Always refer to the manufacturer’s guidelines.
Yes, especially wheels with vitrified and metal bonds. Redressing restores the wheel’s surface, typically using a dressing tool or stick.
Higher diamond concentrations offer longer wheel life but might result in higher grinding temperatures. Lower concentrations provide faster material removal but may wear out the wheel faster.
Always wear safety glasses, use guards on grinding machinery, and ensure proper ventilation. Also, avoid forcing the wheel onto the material; let the abrasive do the work.
Water-based coolants are commonly used. They dissipate heat effectively and prevent dust buildup.
Regular wheel dressing, consistent grinding parameters, and using a wheel with appropriate specifications for the job can help achieve this.
Yes, many diamond back grinding wheels are designed to integrate seamlessly with automated grinding systems.
While diamond grinding wheels might have a higher initial cost, their longer lifespan and efficiency can make them more cost-effective in the long run.
Yes, many manufacturers offer custom solutions tailored to specific applications or requirements.
While CMP offers exceptional surface finishes, diamond grinding is generally faster and can be more cost-effective for bulk material removal.
Used grinding wheels, especially those with specific bond materials, may have disposal guidelines. It’s best to consult with the manufacturer or local regulations.
Lead times vary by manufacturer and order volume. It’s best to check directly with suppliers.
Remember that specific answers can vary based on the grinding wheel’s manufacturer, so always refer to the manufacturer’s documentation or customer support for precise information.
INDUSTRIES USED IN
- Silicon (Si)
- Gallium arsenide (GaAs)
- Silicon carbide (SiC)
- Sapphire
- Gallium Nitride (GaN)
- Germanium (Ge)
- Ferrite
- Quartz and Fused Silica
- Other Compound Semiconductors
- LT (Lithium Tantalate) and LN (Lithium Niobate):
- Advanced Ceramics
- Diamond
- Glass Substrates
- Tungsten Carbide
- Piezoelectric Materials
ACCESSORIES
USAGE RECOMMENDATION
Tab Content
Features:
- High Material Removal Rate (MRR): Designed for fast and efficient material removal, allowing for increased productivity.
- High Precision & Accuracy: Engineered to achieve precise thinning and flattening with minimal deviation.
- Longer Tool Life: Durable construction increases the lifespan of the wheel, reducing replacement costs.
- Minimal Subsurface Damage: Achieves thinning without introducing damaging micro-cracks or surface defects.
- Minimal Heat Generation: Designed to reduce heat buildup during grinding, ensuring high-quality wafer surfaces.
- Reduced Material Contamination and Deformation: Maintains the integrity of the wafer with minimal contamination or deformation.
Application:
- Semiconductor Wafers: Essential for thinning wafers prior to dicing, improving heat dissipation for high-power devices.
- Microelectronic Packages: Provides precision grinding for microelectronic components.
- Other Advanced Materials: Suitable for a variety of hard and brittle materials.
Type |
Profile sketch |
Common Specifications in mm |
||
---|---|---|---|---|
Diameter D |
Thickness T |
Inside Diameter |
||
6A2 |
|
175 200 350 |
30-35 35 45 |
Inside Diameter 76 127 |
6A2T |
|
195 280 350 |
22.5-25 30 35 |
170 228.6 235 |
6A2T (three ellipses) |
|
209 |
22.5-23 |
158 |
All Dimensions: T, E, W, X can be customized to fit your requirements
Semiconductor wafers are routinely thinned prior to dicing to aid the sawing operation and to allow the final assembled package thickness to be minimized. For semiconductor devices required to operate at high power levels, wafer thinning improves the ability to dissipate heat by lowering the thermal resistance of die. As final thickness is decreased, the wafer progressively becomes less able to support its own weight and to resist the stresses generated by post backgrinding processes. Thus, it is important to reduce the damage caused by backgrinding.
UKAM Industrial Superhard Tools has the technology and expertise to help you optimize your backgrinding process to ultimate level of efficiency.
About Diamond Back Grinding
Back grinding is a crucial process in semiconductor manufacturing, aimed at thinning silicon wafers after circuits have been constructed on their front side. This step is essential for reducing the thickness of wafers, improving heat dissipation, and enhancing flexibility for various packaging applications, especially in high-performance electronics where efficient heat management and compact packaging are vital.
The process starts by mounting the wafers on a special adhesive film that secures them during grinding. This is crucial as it prevents any damage or breakage that could occur due to the thinning process. The primary tool used for back grinding is a grinding wheel made of a diamond-bonded matrix, which is capable of grinding silicon quickly and with precision. This grinding must be carefully controlled to reach the desired wafer thickness, often less than 100 microns for some applications.
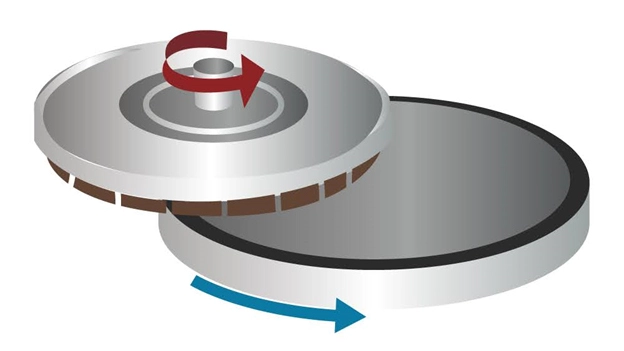
During grinding, a cooling fluid is often used to prevent excessive heat build-up which could damage the wafer's surface and the underlying circuits. The fluid also assists in removing the silicon particles that are ground off. An excellent solution for this application is our
After grinding, the wafers may undergo a stress relief process, such as etching or applying a stress-relief layer, to remove any micro-cracks or surface stresses induced by the grinding.
One of the main challenges of back grinding is maintaining the integrity of the wafer surface. The process must be precise enough to thin the wafer without causing surface damage that could impair the functionality of the circuits. Handling and cleaning the wafers post-grinding are also critical, as any residual stress or particles left on the wafer can affect subsequent processes or the final performance of the semiconductor device. Additionally, the grinding process can introduce sub-surface damage, such as micro-cracks and dislocations, which might not be visible but can affect the reliability and performance of the semiconductor devices. To address these issues, advanced techniques like dry polishing or chemical mechanical polishing (CMP) are often employed after back grinding to remove or reduce such damage.
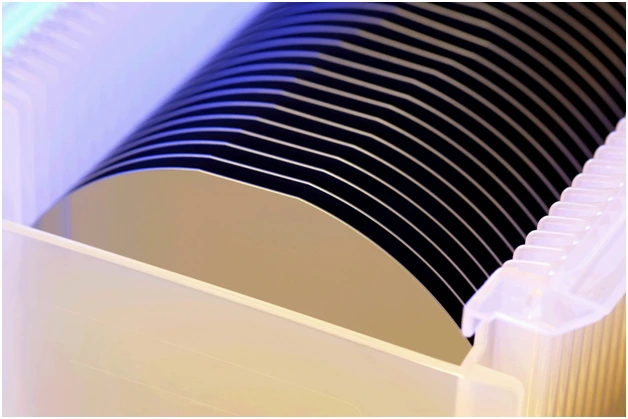
Case Study: Performance of SMART CUT® Diamond
Grinding Wheels for Silicon Wafer Processing
This case study demonstrates the performance of SMART CUT® Diamond Grinding Wheels in a backgrinding application for 8" and 12" silicon wafers. One of our client conducted a trial comparing the performance of SMART CUT® grinding wheels against a competitor’s wheels, utilizing different bond types and machinery.
Wafer Type: 8" Silicon Wafer
Specification |
Diamond Bond 4000 |
Diamond Bond 6000 |
---|---|---|
Machine Used |
DISCO_850 |
DISCO_850 |
Current (A) |
6.5 – 8.5 |
7.5 – 9.5 |
Tip Wear (um) |
0.6 – 2.0 |
0.4 – 1.5 |
Surface Roughness (Ra, um) |
0.022 |
0.015 |
Observations:
The SMART CUT® Diamond Bond 4000 grinding wheel delivered a consistent material removal rate (MRR) with minimal tip wear and a surface roughness of 0.022 µm. The competitor’s product, on the other hand, showed higher tip wear and a higher surface roughness of 0.025 µm, indicating a higher rate of wear and less efficient grinding.
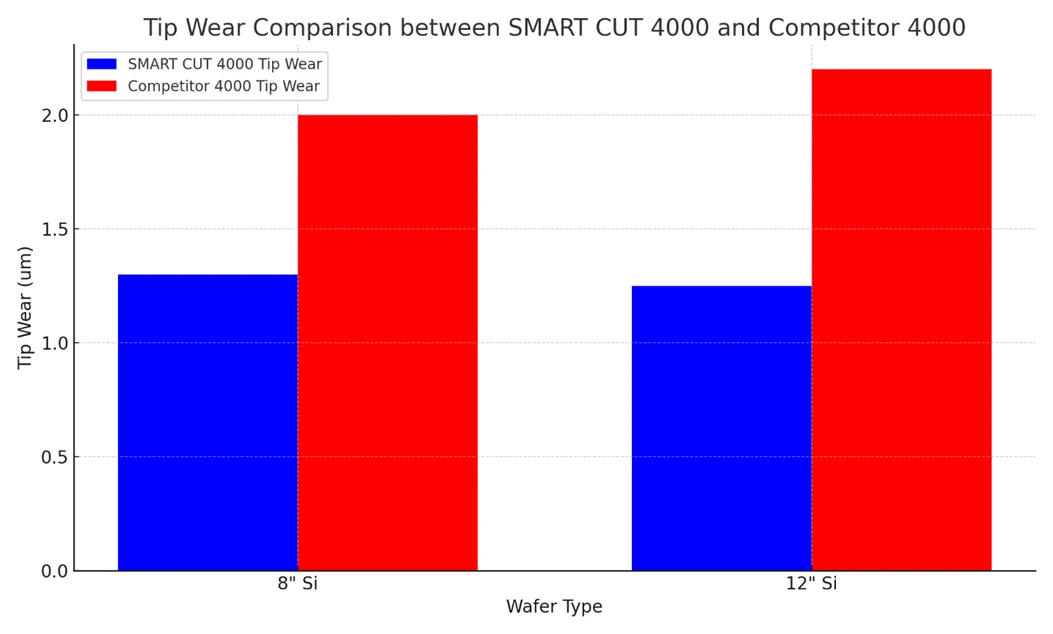
Wafer Type: 12" Silicon Wafer
Specification |
Diamond Bond 4000 |
---|---|
Machine Used |
DISCO_8560 |
Current (A) |
7.0 – 9.0 |
Tip Wear (um) |
0.5 – 2.0 |
Surface Roughness (Ra, um) |
0.020 |
Observations:
For the 12" wafers, the SMART CUT® Diamond Bond 4000 grinding wheel showed exceptional durability with lower tip wear, ensuring the wafer's surface remained consistent. The surface roughness was 0.020 µm, which is optimal for high-performance applications requiring precision. The competitor’s wheel demonstrated significantly higher wear rates and slightly higher roughness values, which could potentially impact the wafer’s final quality.
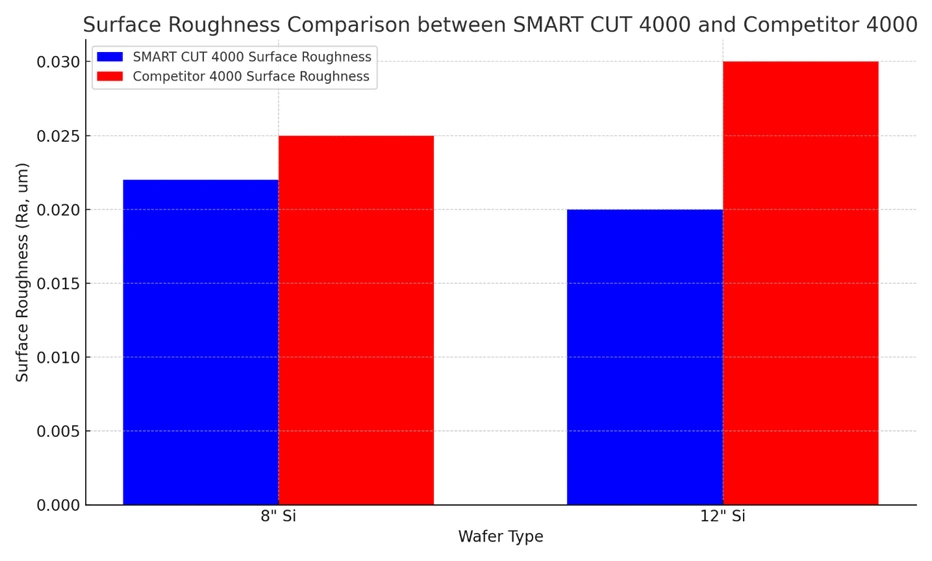
Wafer Type: 8" Silicon Wafer – Competitor Comparison
Specification |
XRP |
Competitor |
---|---|---|
Machine Used |
DISCO_840 |
DISCO_850 |
Current (A) |
5.5 – 7.0 |
5.0 – 6.5 |
Tip Wear (um) |
0.3 – 0.8 |
0.9 |
Surface Roughness (Ra, um) |
0.010 |
0.015 |
Observations:
SMART CUT® wheels outperformed the competitor's wheels with reduced tip wear and lower surface roughness. The competitor's wheels resulted in a rougher surface with significantly more wear. The XRP bond on the SMART CUT® wheels further ensured lower power consumption during grinding, increasing overall efficiency.
Key Performance Metrics:
- Higher Material Removal Rate (MRR): SMART CUT® wheels provide faster material removal with less wear, ensuring high productivity.
- Longer Wheel Life: The wheels maintain a longer life cycle, reducing tool replacement costs.
- Lower Surface Roughness: Achieving precise surface finishes with lower roughness is critical for high-end semiconductor applications.
- Optimal Tip Wear: SMART CUT® wheels show consistent performance with minimal tip wear, extending wheel life and maintaining grinding consistency.
SMART CUT® Diamond Grinding Wheels for silicon wafer processing delivered superior performance compared to a leading competitor's products. These wheels provided efficient material removal, minimal tip wear, and lower surface roughness, making them ideal for high-precision applications in semiconductor manufacturing. The results demonstrate the wheels long-lasting performance and high productivity, offering a significant return on investment for companies in the wafer grinding industry.
Related Products
SMART CUT® Diamond Cylindrical Grinding Wheels
SMART CUT® Diamond Cylindrical Grinding Wheels are engineered for the precise peripheral grinding of silicon ingots, making them an ideal choice for industries such as semiconductors, electronics, automotive, and photovoltaics. These high-performance grinding wheels are designed to process the outer surfaces of silicon ingots, ensuring accurate orientation flats are created, which are essential for subsequent processing steps. The addition of the orientation flat, a marked edge indicating the crystallographic plane of the wafer, is crucial for the wafer's alignment in future manufacturing processes.
During the post-slicing phase, wafers undergo shaping and smoothing through peripheral grinding.
SMART CUT® Diamond Notch
SMART CUT ® Single & Multi Layered Electroplated Diamond Notch Grinding Wheel is designed for high-precision notch grinding of semiconductor wafers, including materials such as Silicon (Si), Silicon Carbide (SiC), Gallium Arsenide (GaAs), and Sapphire. Engineered using advanced electroplating technology, this wheel ensures exceptional performance in wafer processing, offering a high level of precision and durability for demanding semiconductor applications.
SMART CUT® Diamond Edge Grinding Wheels (Electroplated)
SMART CUT® Diamond Edge Grinding Wheels are engineered to deliver exceptional performance for precision grinding applications, providing superior results in both rough and fine grinding. These wheels are ideal for use in industries that require highly accurate EDM processing and consistent wafer-to-wafer results. Manufactured with synthetic diamond grit, SMART CUT® wheels offer improved surface roughness and extended tool life due to their tightly controlled diamond distribution and uniform bond structure.
Band Saw Blades
SMART CUT® Braised Bond Diamond Band Saw Blades
ID blades
Diamond Wire
SMART CUT Diamond wire produces minimum kerf loss, less sub-surface damage, and contamination free coolant. Used for precision cutting of various types of artificial crystal, ceramic, quartz glass, monocrystalline silicon, polycrystalline silicon, sapphire and special metal materials. Diamond Wire cutting is an environmentally friendly cutting process as it eliminates slurry recycling and disposal issues.
SMART CUT® HD Synthetic Low IFT Coolant/Lubricant For Diamond Wire Sawing Silicon
SMART CUT® is a synthetic coolant specifically designed for the cutting of semiconductor materials, including sapphire, silicon, germanium, single-crystal SiC, and II-VI crystals. This coolant offers excellent cut rates and imparts outstanding surface finishes with reduced warp and total thickness variation (TTV). It is ideal for diamond abrasive cropping, squaring, and wafering of silicon ingots using ID, band, and wire saws. SMART CUT® HD-2B can also be used as a non-re-circulating edge grinding coolant or lubricant for silicon wafers and ingots.
Recently Viewed Products
ARE YOU USING RIGHT TOOLS
FOR YOUR APPLICATION?
LET US
HELP YOU
HAVING ISSUES WITH
YOUR CURRENT TOOLS?
Knowledge Center
02
Jun
How to properly use Diamond Tools
UKAM Industrial Superhard Tools manufactures precision diamond tools for a large variety of applications, materials, and industries.
Share this Article with Friend or Colleague
Metal Bonded Diamond Tools are “impregnated” with diamonds. This means that selected...
02
Jun
Why use diamond
Diamond is the hardest material known to man kind. When used on diamond/tools, diamond grinds away material on micro (nano) level. Due to its hardness Diamond will work all types of materials from...
02
Jun
Diamond vs CBN (cubic boron nitride) Tools
Cubic Boron Nitride (CBN) is a synthetic material that is renowned for its exceptional hardness and high thermal stability. It is composed of boron and nitrogen atoms arranged in a crystal lattice structure, similar to...
02
Jun
What is Diamond Mesh Size and how to select best one for your application
Diamond grit size can be defined as the size of the diamond particles used in the bond matrix. The larger the diamond particles (grit size) the faster the tool will cut.
Share this Article with Friend or...
02
Jun
What is Diamond Concentration and which to use for your application
Diamond concentration is measured based on the volume of diamond within a section of the tool. It is typically defined as Concentration 100, which equates to 4.4 carats per cubic centimeter of the diamond layer...
02
Jun
Diamond Tool Coolants Why, How, When & Where to Use
Coolant is one of the most overlooked variables in the overall diamond or cbn tool machining process. Effective and proper use of coolant and recalculating coolant system will pay off in terms of improved surface...
18
Jul
Get to Know the Diamond Tool Bond Types and Which to use for your application
The indication of this premature loss of diamond is deep pocket left behind. The presence of many pockets means the diamond is wasted without being used. Each diamond must protrude high to cut fast with...
17
May
Choosing The Correct Diamond Bond Type
Selecting the appropriate diamond bond type for specific applications is crucial for several reasons. Diamond bond type directly affects the tool's performance, efficiency, and longevity. Different bond types determine how well a tool can withstand...
- Unmatched Selection For Many Applications
- Superior Quality & Consistency
- Immediate Worldwide Delivery
- Technical Support & Expertise
- American Based Manufacturer
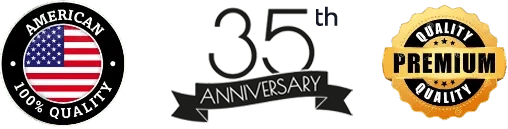

- Different Product
- Different Technology
- Different Company
- Expect MORE from your tools
Let Us HELP You!
Subscribe To Our Newsletter
Signup for email offers, updates, and more
Contact Us
- 25205 & 25201 Avenue Tibbits Valencia CA 91355 USA
-
Phone : (661) 257-2288
FAX : (661) 257 -3833 - lel@ukam.com
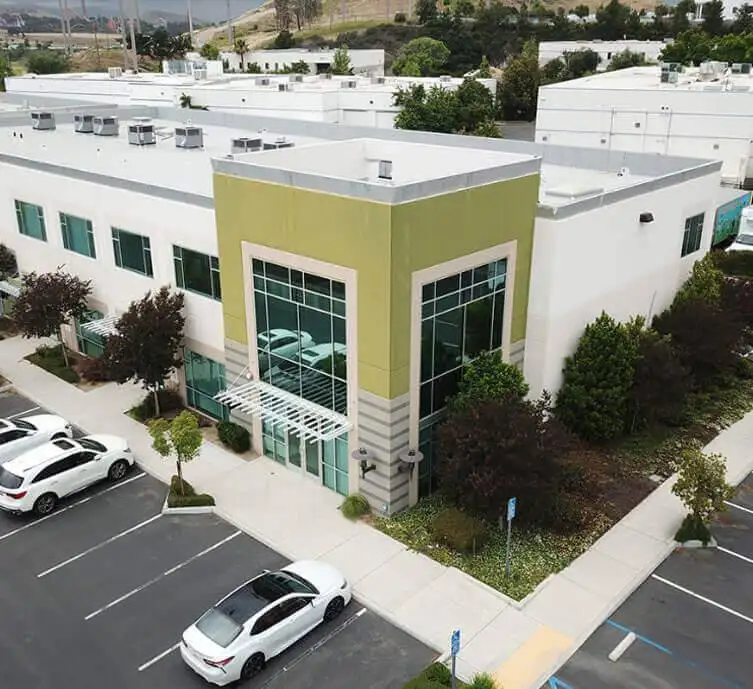
UKAM Industrial Superhard Tools is a U.S. High Technology, Specialty Diamond Tool & Equipment manufacturer. We specialize in producing ultra thin, high precision cutting blades, precision cutting machines diamond drills, diamond micro tools, standard & custom advanced industrial diamond tools and consumables.
- 25205 & 25201 Avenue Tibbits Valencia CA 91355 USA
-
Phone : (661) 257-2288
FAX : (661) 257 -3833 - lel@ukam.com
- 25205 & 25201 Avenue Tibbits Valencia CA 91355 USA
-
Phone : (661) 257-2288
FAX : (661) 257 -3833 - lel@ukam.com
DIAMOND TOOLS BY BOND
EQUIPMENT
KNOWLEDGE CENTER
OUR PRODUCTS
COMPANY
CUSTOMER SERVICE
Shipping Methods


Safe & Secure Payments

© Copyright 1990-2025. UKAM Industrial Superhard Tools – Terms of Use