-
0 items in quote
No products in the Quote Basket.
Band Saw Blades Electroplated (Nickel Bond)
SMART CUT® All diamond band saw blades are custom manufactured to fit your exact material, needs and application requirements. We will work with you to determine your needs, and recommend the right parameters for your specific material / application.
SMART CUT® Diamond Band Saw Blades have proven the be an effective diamond machining tools on a large variety of materials and applications. With diamonds firmly attached to ultra thin metal body, Diamond Band Saw Blades remain the tool of choice for many diamond cutting and machining jobs. Perfect Solution for cutting large variety of ultra hand and brittle materials such as: quartz, glass, carbon, silicon, ceramics or composites. Large variety of diamond band saw blade specifications are available to fit any application.
DESCRIPTION
SPECIFICATIONS
INDUSTRIES USED IN
FAQ
ACCESSORIES
USAGE RECOMENDATION
DESCRIPTION
Blades are cut and welded to clients specification, weld is guaranteed for the life of the blade. Only the highest quality raw materials are used in the manufacturing process is carefully controlled, matching your application with the right bond type, grit size, bond hardness and composition.
A band saw’s blade is diamond coated by electroplating, a process in which an electrical current deposits the coating onto the blade. This produces a hard, brittle Ni matrix that holds the diamonds in place and permits precise cutting on a variety of materials.
This process utilizes a flexible, toothed blade is welded into an endless band that rides on wheels driven by two pulleys and is guided through the work cut off or contour. Ideally Diamonds Band Saws Blades should be used on Band Saw Machines designed for this purpose. A friction saw is a special band saw capable of achieving band velocities of up to 15,000 sfpm or more.
SPECIFICATIONS
- Blade Thicknesses Available : 0.20″ to .035″
- Blade Widths Available : 1/4″ to 1.5″
- Grit sizes available : 35 to 120 mesh
- Blade edge configurations available : continuous rim, segmented, gulleted, Scallop Segment
- Blade Backing Materials : Steel Alloy, Stainless Steel
- Coolant methods : Wet, Dry
- Average Band Saw Blade Life : 40 to 80 hours. Some has shown to last as long as 192 hours.
INDUSTRIES USED IN
Tab Content
FAQ
Tab Content
ACCESSORIES
Tab Content
USAGE RECOMENDATION
- Material Compatibility: Always ensure that the blade is suitable for the material you are cutting. Diamond blades are designed for specific materials and using them on incompatible substances can damage the blade or the material.
- Proper Installation: Ensure that the blade is correctly installed on the saw. The blade should be tensioned according to the manufacturer’s specifications to avoid slippage or breakage.
- Cutting Speed: Maintain an appropriate cutting speed. Too fast can overheat the blade and material, causing damage; too slow can reduce efficiency and cause unnecessary wear on the blade.
The recommended RPM (Revolutions Per Minute) for diamond band saw blades can vary significantly based on several factors including the type of material being cut, the diameter of the blade, the hardness of the material, and the specific design of the blade. Here are some general guidelines to consider:
- Material Type: Different materials require different cutting speeds. For example, softer materials like some types of ceramic or glass may be cut at higher speeds, while harder materials like quartz or granite require slower speeds.
- Blade Diameter: The larger the diameter of the blade, the slower the RPM should be. This is because a larger blade will have a higher cutting speed at the edge even with a lower RPM.
- Manufacturer’s Recommendations: Always check the manufacturer’s guidelines for the blade. These guidelines are based on extensive testing and are designed to optimize the blade’s performance and lifespan.
- Cooling Considerations: Higher speeds can generate more heat. If adequate cooling (like a water coolant system) is not in place, it’s advisable to use a lower RPM to prevent overheating the blade and the material.
- Type of Coolant: Water is often used as a coolant for diamond band saw blades, especially when cutting stone, glass, or tile. For some applications, especially in metal cutting, a water-soluble coolant or cutting oil is preferred to reduce friction and remove cuttings more effectively.
- Coolant Concentration: If you’re using a water-soluble coolant, ensure it’s mixed at the correct concentration. Too much water in the mixture can reduce its effectiveness, while too much concentrate can be wasteful and potentially harmful to the blade and workpiece.
- Continuous Flow: Ensure a continuous and adequate flow of coolant to the blade. The coolant should be applied directly where the cutting action is taking place to maximize its cooling and lubricating effects.
- Prevent Overheating: The primary purpose of the coolant is to keep the blade and the material being cut cool. Overheating can damage both the blade and the material and can also lead to dangerous situations.
- Coolant Cleanliness: Regularly clean and replace the coolant to prevent contamination. Dirty or contaminated coolant can reduce cutting efficiency and cause damage to the blade.
- Environmental Considerations: Be aware of the environmental and health implications of the coolant you choose. Some coolants may require special handling or disposal methods.
- Preventing Corrosion: If you’re using a water-based coolant, be mindful of the potential for rust and corrosion on your saw and blades. Consider adding a rust inhibitor to the coolant or regularly applying a rust preventative to your equipment.
- Coolant Distribution System: Maintain your coolant distribution system, ensuring that nozzles or hoses are not clogged and are positioned correctly to deliver coolant effectively to the blade.
- Avoiding Dry Cutting: Unless specifically designed for dry use, always use coolant with diamond band saw blades. Dry cutting can significantly reduce the life of the blade and degrade its performance.
- Coolant Temperature: In very hot conditions, the coolant itself can become warm. Consider ways to keep the coolant temperature down, as overheating can reduce its effectiveness.
- Safety and Health: Always use coolants in a well-ventilated area, and wear appropriate protective gear to avoid contact with skin and eyes. Some coolants may emit harmful vapors or be irritating to the skin.
- Recycling and Reuse: Some coolant systems allow for the recycling and filtration of the coolant for reuse. This can be both cost-effective and environmentally friendly.
- Compatibility with Materials: Ensure that the coolant is compatible with the material you are cutting. Some materials may react adversely with certain coolants.
- Coolant Pressure and Volume: Adjust the pressure and volume of the coolant to suit the cutting conditions. Different materials and cutting speeds may require different coolant pressures and volumes for optimal performance.
- Cutting Precision: For very precise cuts, a slower RPM may be beneficial as it allows for more control.
- Blade Wear and Tear: Using a higher RPM than recommended can lead to increased wear and a shorter lifespan for the blade. Conversely, a speed that is too low may result in inefficient cutting and unnecessary strain on the saw.
- Specific Applications: Some specialized applications may have unique RPM requirements. For instance, cutting very dense or abrasive materials often requires lower RPMs to minimize blade wear.
- Saw Capabilities: Ensure that the RPMs you choose are within the operational range of your saw. Operating a saw at an RPM it’s not designed for can be dangerous and damage the saw.
- Experience and Skill Level: Experienced users may be able to safely and effectively operate the saw at different RPMs based on their understanding of the material and the cutting process.
- Trial and Error: Sometimes, finding the optimal RPM requires a bit of experimentation, starting at a lower speed and gradually increasing it while monitoring the cutting performance and the condition of the blade.
- Lubrication and Cooling: Use an appropriate coolant or lubricant when cutting. This reduces heat build-up, prevents blade overheating, and extends the life of the blade.
- Safety Gear: Always wear appropriate safety gear including eye protection, ear protection, and gloves. Diamond cutting can produce small, sharp particles that pose a risk.
- Regular Inspections: Regularly inspect the blade for damage or wear. Look for missing or damaged diamonds and check the overall condition of the blade.
- Avoid Twisting: Keep the blade straight during cuts. Twisting or bending the blade can cause it to break.
- Feed Rate: Control the feed rate of the material into the blade. Forcing the material too quickly can overload and damage the blade.
- Blade Cleaning: Keep the blade clean from any build-up of material, which can affect its cutting efficiency.
- Storage: Store the blade in a dry, safe place where it won’t be damaged.
- Professional Advice: If unsure about the type of blade needed for a specific job, consult with a professional or refer to the manufacturer’s guidelines.
- Regular Maintenance: Ensure regular maintenance of the saw to keep it in good working condition, which also helps in extending the life of the blade.
Feed Rates
- Material Hardness: Softer materials can generally be cut at higher feed rates, while harder materials require a slower feed rate. For example, cutting marble will have a different optimal feed rate than cutting granite.
- Blade Specifications: The feed rate should match the specifications of the blade being used. Different blades are designed for different materials and cutting speeds. Always refer to the manufacturer’s guidelines.
- Thickness of the Material: Thicker materials require a slower feed rate to ensure an even and consistent cut. Pushing the blade too fast through a thick material can lead to blade deflection, uneven wear, or breakage.
- Type of Cut: Straight cuts can usually be made at a higher feed rate than curved or intricate cuts. For detailed work, a slower feed rate allows for greater precision.
- Blade Wear: A new blade can typically handle a faster feed rate. As the blade wears, you may need to adjust the feed rate to compensate for the reduced cutting efficiency.
- Cooling and Lubrication: Adequate cooling and lubrication can allow for slightly higher feed rates, as they help prevent blade overheating and material burning.
- Machine Capability: Ensure that the feed rate is within the capabilities of your cutting equipment. Overloading the machine can lead to poor cuts and potential damage to the machine or blade.
- Visual and Auditory Cues: Pay attention to the sound of the blade and the appearance of the cut. Chattering, excessive noise, or a rough cut surface can indicate that the feed rate is too high.
- Experience and Judgment: Operator experience plays a significant role in determining the right feed rate. Experienced operators can judge the optimal speed based on the cutting conditions and blade performance.
- Material Fracture Tendencies: Some materials are more prone to chipping or fracturing. A slower feed rate can reduce the risk of damaging these materials.
- Trial and Error: Sometimes finding the optimal feed rate requires experimentation. Start at a lower feed rate and gradually increase it while monitoring the cut quality and blade behavior.
- Safety Considerations: Always prioritize safety. A feed rate that is too high can be dangerous and may lead to loss of control or blade breakage.
- Consistency: Maintain a consistent feed rate throughout the cut for the best results. Inconsistent feeding can lead to blade wandering or irregular cuts.
- Feed Rate Units: Feed rates are typically measured in inches per minute (IPM) or millimeters per minute (mm/min). Ensure you are using the correct units and measurements.
- Blade Break-In: New diamond band saw blades often require a break-in period. Start with softer materials or less aggressive cutting to gradually expose new diamond grit. This can improve the overall performance and longevity of the blade.
- Avoid Overheating: Continuously monitor the blade temperature during use. Overheating can cause the metal to warp and the diamonds to lose their effectiveness. If the blade becomes too hot, pause cutting and allow it to cool down.
- Proper Tensioning: Maintain correct tension on the blade. Too much tension can lead to blade breakage, while too little can result in inaccurate cuts. Refer to the saw manufacturer’s guidelines for proper tensioning procedures.
- Use the Right Blade Width: Choose a blade width that is appropriate for the material and the type of cut you want to make. Wider blades are typically better for straight cuts, while narrower blades are ideal for cutting curves.
- Clean Cuts: Ensure that each cut is clean and straight. A wobbling or chattering blade can indicate a problem with the saw or the blade, and it can also lead to uneven wear or damage to the blade.
- Adjust for Blade Drift: Some band saws exhibit blade drift, where the blade does not cut in a perfectly straight line. Adjust the fence or your cutting technique to compensate for this drift to achieve accurate cuts.
- Use Variable Speed Saws When Possible: If your saw allows for speed adjustment, use this feature to match the speed to the hardness of the material. Harder materials often require slower speeds.
- Gradual Entry on Thick Materials: When starting a cut on a thick or dense material, begin slowly and increase the feed rate gradually. This approach helps in preventing blade shock and reduces the risk of chipping.
- Avoiding Blade Twist: When cutting curves, be mindful not to twist the blade excessively. Sharp turns can strain the blade and cause premature wear or breakage.
- Periodic Resting: Allow the blade to rest periodically during prolonged cutting sessions. This prevents continuous heat build-up and extends blade life.
- Disposal and Replacement: Once a blade becomes too worn or damaged, dispose of it properly and replace it with a new one. Continuing to use a damaged blade can be inefficient and unsafe.
- Training and Experience: If you’re new to using a diamond band saw, consider getting training or advice from experienced users. Understanding the nuances of these blades can greatly improve your cutting technique and safety.
- Blade Direction and Alignment: Ensure that the blade is mounted in the correct direction and is perfectly aligned with the band saw. Misalignment can cause uneven wear and poor cutting performance.
- Avoid Dry Cutting: Unless the blade is specifically designed for dry cutting, always use water or an appropriate coolant. Dry cutting with a blade meant for wet use can lead to overheating and premature wear.
- Regular Blade Cleaning: Over time, cutting residue can build up on the blade, affecting its performance. Regular cleaning helps maintain its cutting efficiency and prolongs its lifespan.
- Monitor Blade Wear: Be attentive to signs of wear such as reduced cutting performance, increased noise, or unusual vibrations. These signs can indicate that the blade needs to be replaced.
- Cutting Technique: For thicker materials, use a “step cutting” technique where you make a series of gradually deeper cuts. This approach can reduce the stress on the blade and improve the quality of the cut.
- Reduce Blade Fatigue: Alternate between different blades if you are making a large number of cuts. This allows each blade to rest and cool down, reducing the risk of fatigue and breakage.
- Avoid Impact or Shock: Never force the blade into the material. A smooth, steady approach is best. Impact or shock can cause diamond grit to dislodge or the blade to break.
- Correct Blade Storage: Store unused blades in a safe, dry place, ideally hanging or laid flat in a way that does not put stress on the blade. Avoid kinking or bending the blade.
- Manufacturer’s Instructions: Always follow the manufacturer’s instructions for use, maintenance, and safety. Different blades may have specific requirements or recommendations.
- Prevent Corrosion: After use, especially with water or coolant, dry the blade to prevent rust and corrosion. This is particularly important for the non-diamond parts of the blade.
- Blade Tracking: Regularly check and adjust the blade tracking. Proper tracking ensures that the blade runs smoothly on the wheels of the saw, reducing wear and the risk of blade deviation.
- Sharp Turns and Corners: When cutting sharp corners or intricate patterns, reduce the feed rate and carefully guide the material. Forcing the blade through tight turns can damage it.
- Understand Blade Specifications: Familiarize yourself with the blade’s specifications such as diamond grit size, concentration, and bond hardness. This information helps in selecting the right blade for a specific material and cutting requirement.
- Respect Load Capacity: Be mindful of the blade’s load capacity. Overloading can lead to blade deformation and potential breakage.
- Professional Maintenance: Consider having your blades professionally sharpened or re-tipped if they become dull. This can be more cost-effective than purchasing new blades.
- Safety First: Lastly, prioritize safety above all else. If you’re ever uncertain about a cutting task, seek professional advice or assistance to prevent accidents.
- Understand Blade Limits: Be aware of the maximum and minimum thicknesses and types of materials your blade is designed to cut. Using a blade outside of its intended range can lead to poor performance and potential blade damage.
- Controlled Feed Pressure: Apply a consistent and controlled feed pressure when cutting. Erratic pressure can cause blade deflection or breakage, and uneven wear.
- Avoid Blade Binding: Ensure that the material being cut does not pinch the blade. Blade binding can cause excessive wear and potential blade breakage.
- Material Stability: Secure the material being cut firmly. Movement during cutting can lead to inaccurate cuts and increase the risk of blade damage.
- Coolant Flow and Quality: Check the flow and quality of the coolant regularly. Ensure that the coolant is reaching the point of the cut and that it is not contaminated, as dirty coolant can harm the blade’s performance.
- Avoid Excessive Bending: When cutting curves, avoid bending the blade excessively as it can lead to metal fatigue and eventual failure.
- Use Appropriate Blade Speeds: Different materials require different blade speeds for optimal cutting. Consult the blade and material specifications for the recommended speeds.
- Blade Thickness Awareness: Be aware of the blade’s thickness and how it relates to the kerf (the width of the cut). This is important for precision cutting and avoiding material waste.
- Regular Breaks During Intensive Use: If using the blade intensively, give it and the saw regular breaks to prevent overheating.
- Blade Dressing: Periodically dress the blade to expose fresh diamond edges. This is especially important for blades that see a lot of use.
- Support Material Adequately: Ensure that larger or heavier materials are adequately supported to prevent blade pinching or deflection.
- Handle with Care: Diamond blades are robust in cutting but can be fragile if mishandled. Avoid dropping or striking the blade.
- Blade Path Clearance: Ensure that the path of the blade is clear of obstructions, including clamps, to prevent accidental contact and potential damage.
- Blade Compatibility with Saw: Ensure the blade is compatible with your particular band saw, considering factors like blade length, width, and tooth pitch.
- Avoid Reactive Materials: Be cautious when cutting materials that may react with water or coolants, such as certain metals, as this can cause damage or safety hazards.
- Record Keeping: Keep records of blade usage, including types of materials cut and hours of operation. This can help in scheduling maintenance and predicting blade life.
- Environmental Considerations: Be mindful of the environmental conditions in which you are working. Extreme temperatures and humidity can affect both the material being cut and the blade.
- User Training and Awareness: Ensure that all operators are adequately trained and aware of the proper usage and safety procedures for diamond band saw blades.
- Blade Disposal: Dispose of used or damaged blades properly, considering local regulations and safety practices.
- Stress Relief Cuts: When cutting large or thick materials, make relief cuts to reduce stress on the blade. This technique involves making additional cuts to remove material and prevent binding.
- Avoiding Side Pressure: Apply cutting pressure in a straight line. Side pressure can bend the blade and lead to uneven wear or breakage.
- Correct Blade Orientation: Make sure the blade’s direction of rotation is correct. A blade installed backwards will be ineffective and can be damaged.
- Material Clamping: Properly clamp or secure the material being cut to prevent movement. Unstable materials can cause irregular cuts and put extra stress on the blade.
- Regular Saw Maintenance: In addition to blade maintenance, ensure that the saw itself is in good condition. This includes checking the guide bearings, tension mechanism, and overall alignment.
- Blade Guide Adjustment: Adjust the blade guides correctly to support the blade close to the cut. This prevents blade deflection and ensures straighter cuts.
- Blade Teeth Per Inch (TPI) Selection: Choose the appropriate TPI for your blade based on the material’s thickness. Generally, a higher TPI is better for thinner materials, and a lower TPI for thicker materials.
- Avoiding Quick Stops and Starts: Avoid abrupt stops and starts during cutting, as this can jar the blade and potentially lead to damage.
- Using a Push Stick for Small Pieces: When cutting small pieces, use a push stick or other device to feed the material. This keeps hands away from the blade and minimizes the risk of injury.
- Cutting at a Consistent Angle: Maintain a consistent angle when feeding the material into the blade. Inconsistent angles can lead to irregular cuts and put uneven stress on the blade.
- Proper Saw Alignment: Ensure that the saw’s wheels, guides, and table are properly aligned according to the manufacturer’s specifications. Misalignment can cause the blade to wear unevenly or break.
- Blade Tension Monitoring: Regularly check the blade tension, as it can change with temperature fluctuations and use. Incorrect tension can lead to poor cutting performance or blade failure.
- Understanding Blade Life Expectancy: Be aware of the typical life expectancy of your blade under normal conditions and plan for replacement accordingly.
- Post-Use Inspection: After each use, inspect the blade for any signs of damage, including chips, cracks, or missing segments. Early detection of damage can prevent more serious issues.
- Avoiding Hazardous Materials: Do not cut materials that might be hazardous, such as materials containing asbestos or other harmful substances.
- Record Blade Performance Issues: Keep a log of any issues encountered during cutting. This can help in troubleshooting and identifying when a blade needs to be replaced or serviced.
- Environmental Cleanliness: Keep the work area clean and free of debris. A cluttered or dirty environment can lead to accidents and affect cutting accuracy.
- Proper Handling and Storage: Handle blades with care, avoiding any actions that could bend or twist them. Store them in a way that prevents physical damage.
- Regular Calibration of Equipment: Regularly calibrate your saw to ensure accurate cuts. Misalignment can lead to increased wear on the blade and poor quality cuts.
- Safety Checks: Perform routine safety checks on the saw and blade before each use. Ensure all safety guards are in place and functioning.
- Personal Protection Equipment (PPE): Always wear appropriate PPE, such as safety glasses, gloves, and hearing protection, when operating the saw.
- Avoid Cross-Contamination: Use different blades for cutting different materials to prevent cross-contamination, which can affect cutting performance and blade life.
- Gradual Increase in Cutting Load: When starting a cutting session, gradually increase the cutting load to allow the blade to warm up, which can prevent shock and wear.
- Regular Coolant Replacement: Change the coolant regularly to prevent contamination, which can affect the cutting process and potentially damage the blade.
- Inspect for Unusual Noises or Vibrations: Be alert to any unusual noises or vibrations during operation, as these can be early signs of blade or equipment issues.
- Use of Blade Stabilizers: Consider using blade stabilizers, if appropriate, to reduce blade vibration and enhance cutting precision.
- Proper Material Support: Ensure that the material is adequately supported both before and after the cut to prevent any unnecessary blade stress or deflection.
- Avoid Abrupt Force: Never apply abrupt force to the blade, either in the cutting direction or laterally. Gentle, consistent pressure is key.
- Maintain a Clean Blade Path: Regularly clean the path of the blade, including guides and wheels, to prevent buildup that can affect the blade’s performance.
- Periodic Professional Assessment: Have your equipment and blades periodically assessed by a professional to ensure they are in optimal condition.
- Educate on Emergency Procedures: Make sure all operators are aware of emergency procedures in case of blade breakage or equipment failure.
- Use the Right Machine for the Blade: Ensure that the saw machine used is suitable for the type of diamond band saw blade, considering factors like power, speed, and size.
- Monitor Blade Alignment During Use: Regularly check the alignment of the blade during use, as it can shift, especially when cutting tougher materials.
- Balanced Blade Wear: Rotate the blade usage if possible, to ensure even wear, which can extend the life of the blade.
- Avoid Twisting the Blade Off the Material: When finishing a cut, avoid twisting the blade off the material, as this can damage the blade.
- Proper Decommissioning of Blades: Decommission blades that are beyond their useful life in a responsible manner, respecting safety and environmental guidelines.
- Attention to Blade’s Running Direction: Ensure that the blade’s running direction matches the indicated direction on the saw. Reversed blades will underperform and can be damaged.
- Check for Material Defects: Before cutting, inspect the material for defects or foreign objects that might damage the blade.
- Lubrication of Moving Parts: Regularly lubricate all moving parts of the saw to ensure smooth operation and reduce wear on the blade.
- Use Blades with Suitable Diamond Grit: Choose a blade with a diamond grit size that is appropriate for the material being cut for optimal performance.
- Safety Training for New Operators: Provide comprehensive safety and operational training for new operators, including practical demonstrations and supervised practice sessions.
- Respect Maximum Depth of Cut: Do not exceed the blade’s maximum depth of cut. Overextending the blade can lead to damage and unsafe conditions.
- Environmental Factors: Consider the impact of environmental factors like humidity and temperature on both the material being cut and the blade.
- Preventive Maintenance Schedule: Establish and adhere to a regular preventive maintenance schedule for both the saw and the blades.
- Ensure Emergency Stop Accessibility: Make sure that the emergency stop button or feature on the saw is easily accessible during operation.
- Understanding Blade’s Limitations: Recognize that even the highest quality diamond band saw blades have limitations and are not indestructible.
Diamond Band Saw Trouble Shooting Guide
Problem
Possible Causes
Solutions
Blade Breakage
Excessive tension
Reduce blade tension
Improper blade size for machine
Ensure correct blade size is used
Excessive feed pressure
Adjust feed pressure to recommended level
Fatigue from repeated bending
Check and adjust blade tracking
Blade Dulling Quickly
Incorrect blade speed
Adjust to optimal speed for material
Inadequate coolant or wrong type
Check coolant flow and type; replace if necessary
Cutting material too hard for blade
Use a blade suitable for the material hardness
Overuse without rest
Allow intervals of rest for the blade
Inaccurate Cuts
Worn or damaged blade guides
Inspect and replace blade guides as needed
Blade misalignment
Align the blade correctly
Incorrect blade tension
Adjust blade tension to recommended level
Using a blade with incorrect tooth pitch
Use a blade with appropriate tooth pitch
Excessive Vibration
Worn bearings
Inspect and replace bearings if needed
Misaligned wheels
Align the saw wheels properly
Damaged blade
Replace the blade
Loose components in the machine
Tighten all loose parts and components
Difficulty in Starting the Cut
Dull blade
Replace or sharpen the blade
Incorrect blade for material type
Select the appropriate blade for the material
Insufficient coolant
Ensure adequate coolant flow
Improper technique
Review and adjust cutting technique
Excessive Noise
Blade hitting machine parts
Check and adjust blade tracking
Loose components
Tighten all loose parts and components
Worn or damaged blade
Inspect blade for damage and replace if necessary
Uneven Wear on Blade
Improper blade tension
Adjust blade tension to even out wear
Misaligned blade
Realign the blade
Uneven material surface
Ensure material is uniformly supported
Uneven Cut Surface
Worn or damaged blade teeth
Replace or sharpen the blade
Blade running at incorrect speed
Adjust blade speed according to material specifications
Improper blade tension
Adjust tension to recommended levels
Excessive Blade Wear
Continuous operation without breaks
Allow the blade to rest periodically
Cutting abrasive materials
Use blades designed for abrasive materials
Insufficient or inappropriate coolant
Use the correct coolant and ensure proper flow
Saw Not Cutting Straight
Blade guides misaligned
Realign the blade guides
Worn or damaged blade
Replace the blade
Machine components out of calibration
Calibrate machine components
Frequent Blade Slippage
Insufficient blade tension
Increase blade tension to proper level
Worn or damaged drive wheels
Replace or repair the drive wheels
Coolant on the blade or wheels
Clean the blade and wheels, ensure coolant is controlled
Coolant Issues
Clogged coolant nozzles
Clean or replace the nozzles
Insufficient coolant flow
Adjust the coolant system for better flow
Incorrect coolant mixture
Ensure the correct mixture and type of coolant
Increased Power Consumption
Blade binding in the cut
Check for proper blade alignment and tension
Dull blade increasing resistance
Replace or sharpen the blade
Motor or drive system issues
Inspect and service the motor and drive system
Difficulty in Blade Installation
Incorrect blade length or width
Use the correct size of blade for your saw
Tension mechanism issues
Inspect and repair the tension mechanism
Misalignment of blade path components
Align the components properly
Blade Deviates from Cut Line
Incorrect blade tension
Adjust tension to recommended levels
Worn or damaged blade teeth
Replace the blade
Misaligned blade guides
Adjust or replace blade guides
Rapid Tooth Strip Off
Excessively hard material
Use a blade designed for harder materials
Too high feed rate
Reduce feed rate
Insufficient blade tension
Adjust blade tension
Blade Binding
Misaligned workpiece
Ensure proper workpiece alignment
Inadequate support for workpiece
Use appropriate supports to stabilize workpiece
Blade worn or damaged
Replace the blade
Irregular Tooth Wear
Uneven material hardness
Check material consistency
Incorrect blade for material type
Select the appropriate blade for the material
Improper blade tension
Adjust tension to recommended levels
Slow Cutting Speed
Blade becoming dull
Replace or sharpen the blade
Incorrect blade speed for material
Adjust the blade speed according to material type
Inadequate power supply to saw
Check and ensure proper power supply
Noise or Chatter During Cutting
Loose components in the saw
Tighten all loose parts and components
Blade tension too low
Increase blade tension
Worn or damaged blade guides
Replace or adjust blade guides
Difficulty in Controlling Cut Direction
Blade too wide for the curve being cut
Use a narrower blade for tight curves
Inadequate blade tension
Adjust tension to recommended levels
Worn or damaged blade
Replace the blade
Excessive Coolant Spatter
High coolant pressure
Adjust the coolant pressure to a lower setting
Misaligned coolant nozzles
Adjust the nozzle alignment
Excessive blade speed
Reduce blade speed
Motor Overheating
Overloading the saw
Reduce feed rate and check for correct blade usage
Inadequate ventilation
Ensure proper ventilation around the motor
Electrical issues
Check and fix any electrical connections and components
Problem
Possible Causes
Solutions
Reduced Cutting Precision
Blade wear and tear
Replace the blade with a new one
Incorrect blade type for the task
Use a blade type more suited to the material
Machine calibration issues
Calibrate the saw according to manufacturer’s guide
Frequent Overheating of Blade or Saw
Continuous operation without adequate cooling
Ensure regular cooling intervals; check coolant system
Overfeeding the material
Reduce feed rate to decrease strain on the blade
Inefficient coolant system
Check and repair the coolant system
Increased Material Waste
Blade wandering off course
Check blade alignment and tension
Incorrect blade width for the material
Use a blade width appropriate for the material
Improper feed rate
Adjust the feed rate for more efficient cutting
Blade Becomes Stuck in Material
Insufficient blade tension
Increase blade tension
Debris build-up on the blade
Clean the blade regularly
Worn or damaged blade teeth
Replace the blade
Difficulty in Blade Tracking
Misalignment of wheels or guides
Adjust the alignment of wheels and guides
Worn or damaged tires on wheels
Replace tires on wheels
Blade not properly seated
Reinstall the blade correctly
Inconsistent Blade Life
Variation in material hardness
Use a blade suited for varying material hardness
Fluctuating feed rates
Stabilize feed rate
Inconsistent maintenance practices
Establish a regular maintenance routine
Excessive Noise During Start-up
Loose components or covers
Tighten all loose components and covers
Motor or belt issues
Inspect and repair/replace motor or belts
Dry or unlubricated moving parts
Lubricate moving parts according to guide
Difficulty in Adjusting Blade Tension
Faulty tension adjustment mechanism
Repair or replace the tension adjustment mechanism
Worn tension springs
Replace tension springs
Corrosion or debris in tensioning components
Clean and lubricate tensioning components
Problem
Possible Causes
Solutions
Frequent Resetting of Circuit Breaker
Electrical overload
Check electrical load and reduce if necessary
Short circuit in saw wiring
Inspect and repair any wiring issues
Faulty motor
Inspect and replace the motor if necessary
Blade Falling Off the Wheels
Insufficient blade tension
Adjust the blade tension
Worn or improperly aligned wheel tires
Replace or realign the wheel tires
Damaged or misaligned blade wheels
Repair or replace the blade wheels
Inefficient Cutting of Curves
Blade too wide for tight curves
Use a narrower blade for tighter curves
Incorrect blade tension
Adjust the blade tension
Improper saw speed
Adjust the saw speed to match the cutting requirement
Vibration in the Saw
Unbalanced wheels
Balance the wheels
Loose components in the saw
Tighten all loose parts and components
Worn bearings or drive belts
Replace worn bearings or drive belts
Difficulty in Maintaining Cut Line
Blunt blade teeth
Sharpen or replace the blade
Incorrect blade for the type of material
Use a blade that is suitable for the material
Misalignment of blade guides
Adjust or replace the blade guides
Excessive Dust and Debris Accumulation
Inadequate dust extraction system
Improve or install a proper dust extraction system
Blade not clearing debris
Check blade type and condition
effectively
replace if necessary
Overloading the saw with material
Reduce the volume of material processed at a time
Difficulty in Blade Alignment
Misaligned blade tracking
Adjust the blade tracking
Worn out blade tensioning components
Replace or repair tensioning components
Debris on blade path
Clean the blade path thoroughly
Blade Chipping or Cracking
Impact with hard or foreign objects in material
Inspect material for foreign objects before cutting
Excessive tension or feed pressure
Adjust tension and feed pressure
Use of blade beyond its lifespan
Replace the blade regularly
Blade Loses Tension During Cutting
Defective tension mechanism
Repair or replace the tension mechanism
Expansion of blade due to heat
Allow blade to cool; adjust tension as necessary
Worn tensioning components
Replace worn components
Material Burn Marks
Too slow cutting speed
Increase the cutting speed
Dull blade
Replace or sharpen the blade
Insufficient coolant
Increase coolant flow or check coolant quality
Blade Produces Rough Cut
Incorrect blade for the material
Use a blade suited for the material
Blade teeth are dull or damaged
Sharpen or replace the blade
Excessive feed pressure
Adjust feed pressure to recommended levels
Saw Struggles to Start Cutting
Low power supply
Check electrical supply and correct any issues
Blade not properly sharpened
Sharpen the blade or replace if necessary
Misalignment of blade or guides
Realign blade and guides as necessary
Inconsistent Blade Movement
Worn or loose drive belts
Replace or tighten the drive belts
Fluctuating power supply
Stabilize the power source or correct electrical issues
Damaged blade wheels
Inspect and replace damaged blade wheels
Difficulty in Changing Blades
Stiff blade tensioning system
Lubricate or repair tensioning system
Misaligned blade guides
Adjust or realign the blade guides
Corroded or jammed blade clamps
Clean, lubricate, or replace blade clamps
Excessive Wear on Blade Back
Blade rubbing against machine parts
Adjust blade tracking and guides
Improper blade tension
Adjust tension to the correct level
Worn blade guides
Replace or adjust the blade guides
Intermittent Cutting Issues
Intermittent electrical issues
Check and repair any electrical connections
Variable material density
Adjust cutting approach based on material density
Inconsistent blade tension
Regularly check and adjust blade tension
Saw Stops Mid-Cut
Overheating due to continuous use
Allow the saw to cool down; use intermittently
Electrical issues, like overheating or faulty wiring
Inspect and repair electrical components
Motor failure
Check the motor and replace if necessary
Blade Wandering During Cut
Blade tension too low
Adjust the blade tension
Worn or improper blade for the material
Replace the blade with a suitable type
Misalignment of blade guides or wheels
Adjust or replace the guides or wheels
Excessive Kerf Width
Blade width too wide for the application
Use a narrower blade
Blade wearing unevenly
Replace the blade; check machine alignment
Improper blade tension
Adjust the blade tension correctly
Coolant Leakage or Spillage
Loose or damaged coolant hoses
Tighten or replace coolant hoses
Overflow from the coolant reservoir
Check and adjust coolant levels
Incorrect coolant nozzle position
Reposition the coolant nozzles
Blade Corrosion or Rusting
Exposure to moisture or improper storage
Store blades in a dry environment; use rust inhibitors
Lack of proper blade maintenance
Clean and oil the blade regularly
Use of corrosive coolants
Switch to a non-corrosive coolant
Motor Vibration or Noise
Imbalanced motor rotor
Inspect and balance the motor rotor
Worn motor bearings
Replace motor bearings
Misalignment of motor with saw components
Realign the motor with the saw components
Difficulty in Maintaining Constant Speed
Variable power supply
Stabilize power source
Drive belt slippage or wear
Adjust or replace the drive belt
Malfunctioning speed control mechanism
Repair or replace the speed control
Blade Teeth Breaking Off
Hitting hard inclusions in the material
Inspect material for hardness variations before cutting
Excessive feed rate
Adjust the feed rate to be more gentle
Fatigue from repeated bending or twisting
Avoid twisting the blade; replace if it becomes fatigued
Table of comparision between plated and braised bond
Comparison Criteria
Electroplated Diamond Band Saw Blades
Brazed Bond Diamond Band Saw Blades
Bonding Process
Diamond particles are adhered to the blade surface through electroplating, involving a current-driven deposition from a diamond-containing solution.
Diamond particles are attached using a brazing process, where diamond grit is mixed with a brazing alloy and heated to bond the diamonds to the blade.
Durability
Generally, have a shorter lifespan due to easier detachment of diamond particles, and more prone to wear and tear.
Tend to be more durable due to stronger bonding, offering a longer lifespan and better performance under heavy-duty conditions.
Application
Best suited for lighter, precision cutting tasks. Often used for cutting softer materials or when a finer cut is needed.
Ideal for heavy-duty cutting and tougher materials. Suitable for demanding applications due to their durability and strength
Cost
Generally less expensive due to the simpler manufacturing process.
More costly owing to the complex brazing process and the blade’s longer lifespan.
Suitability for Specific Tasks
Better for delicate or precision work; suitable for materials like glass, ceramic, and thin stone.Generally less expensive due to the simpler manufacturing process.
Preferred for cutting harder materials such as thick stone, concrete, and reinforced materials, where durability and longevity are crucial.
Bonding Process
Uses electroplating to adhere diamond particles onto the blade surface.
Employs brazing, mixing diamond grit with a brazing alloy and heating to bond to the blade.
Durability
Shorter lifespan, more prone to wear and tear.
Longer lifespan, better performance under heavy-duty conditions.
Application
Ideal for lighter, precision tasks and softer materials.
Suited for heavy-duty cutting and tougher materials.
Cost
Generally less expensive.
Typically more costly
Suitability for Specific Tasks
Better for delicate, precision work; used for glass, ceramic, and thin stone.
Preferred for hard materials like thick stone, concrete, and reinforced materials.
Cutting Speed
Generally offers faster cutting speeds in softer materials.
May cut slower but more effectively through hard materials.
Precision
Provides finer cuts, suitable for detailed and precision work.
Less precise than electroplated but still effective for most applications.
Versatility
Limited to softer materials and precision tasks.
More versatile, can handle a range of materials and applications.
Maintenance Requirements
Lower maintenance due to simpler design, but may require more frequent replacement.
Higher initial durability reduces frequent maintenance but may require specialized care.
Environmental Impact
Lesser environmental impact in production but may contribute to more waste due to shorter lifespan.
Greater initial environmental impact due to brazing process but less waste over time.
Diamond band saw comparison electroplated vis braised bond
Comparison Criteria
Electroplated Diamond Band Saw Blades
Brazed Bond Diamond Band Saw Blades
Bonding Process
Electroplating bonds diamond particles onto the blade surface.
Brazing process mixes diamond grit with a brazing alloy, heating to bond to the blade.
Durability
Shorter lifespan, prone to wear and tear
Longer lifespan, performs better under heavy-duty conditions.
Application
Best for lighter tasks and softer materials.
Suited for heavy-duty cutting and tougher materials.
Cost
Generally less expensive.
Typically more costly.
Specific Task Suitability
Ideal for delicate, precision work; used for glass, ceramic, and thin stone.
Better for hard materials like thick stone, concrete, and reinforced materials.
Cutting Speed
Faster in softer materials.
Slower but more effective in hard materials.
Precision
Provides finer, more detailed cuts.
Less precise but effective for most applications.
Versatility
Limited to softer materials and precision tasks.
Handles a range of materials and applications.
Maintenance
Lower maintenance but may need frequent replacement.
Higher initial durability, may require specialized care.
Environmental Impact
Less impact in production but more waste due to shorter lifespan.
Greater initial impact, less waste over time.
Manufacturing Complexity
Simpler manufacturing process.
More complex manufacturing due to brazing.
Blade Thickness
Typically thinner, allowing for finer cuts
Generally thicker, providing strength for tougher materials.
Heat Resistance
Lower heat resistance, can be a limitation in some applications.
Higher heat resistance, beneficial for prolonged use and tough materials.
Reusability
Limited reuse potential due to wear and tear.
Higher reuse potential due to durability.
Ideal User Profile
Suitable for hobbyists or professionals needing precision in softer materials.
Ideal for industrial applications or professionals cutting tough materials regularly.
Bonding Process
Electroplating bonds diamond particles onto the blade surface.
Brazing process with a mixture of diamond grit and brazing alloy.
Durability
Shorter lifespan due to wear and tear.
Longer lifespan with better performance under heavy-duty conditions.
Application
Best for lighter, precision tasks in softer materials.
Suited for heavy-duty cutting in tougher materials.
Cost
Generally less expensive.
Typically more costly.
Specific Task Suitability
Ideal for delicate, precision work in materials like glass and ceramic.
Better for hard materials like stone and concrete
Cutting Speed
Faster in softer materials.
Slower but more effective in hard materials.
Precision
Provides finer, detailed cuts.
Effective but less precise.
Versatility
Limited to specific tasks in softer materials.
Versatile across a range of materials and applications.
Maintenance
Lower maintenance, frequent replacement needed.
Durable, may require specialized maintenance.
Environmental Impact
Less impact in production, more waste due to shorter lifespan.
Greater initial impact, less waste over time
Manufacturing Complexity
Simpler manufacturing process.
More complex due to the brazing process.
Blade Thickness
Thinner, allowing finer cuts.
Thicker, providing strength for tougher materials.
Heat Resistance
Lower, can be a limitation in some applications.
Higher, advantageous for prolonged use and tough materials.
Reusability
Limited due to wear and tear.
Higher due to durability
Ideal User Profile
Suitable for hobbyists or precision tasks in softer materials.
Ideal for industrial applications in tougher materials
Blade Life Extension
Limited options for extending blade life.
Longer blade life with potential for re-tipping or reconditioning.
Ease of Use
Generally easier to handle due to lighter construction.
May require more skill due to heavier and more robust construction.
Repairability
Limited repair options; often require replacement.
More repairable, especially if the blade body remains intact.
Initial Sharpness
Usually sharper initially, but loses sharpness quicker.
Less sharp initially but maintains sharpness longer.
Heat Generation
Can generate more heat in faster cutting, affecting blade life.
Generates less heat due to robust construction, benefiting longevity.
Description
Specifications
Frequently Asked Questions
Industries Used In
Accessories
Recommendations
Description
A band saw’s blade is diamond coated by electroplating, a process in which an electrical current deposits the coating onto the blade. This produces a hard, brittle Ni matrix that holds the diamonds in place and permits precise cutting on a variety of materials.
This process utilizes a flexible, toothed blade is welded into an endless band that rides on wheels driven by two pulleys and is guided through the work cut off or contour. Ideally Diamonds Band Saws Blades should be used on Band Saw Machines designed for this purpose. A friction saw is a special band saw capable of achieving band velocities of up to 15,000 sfpm or more.
Specifications
- Blade Thicknesses Available : 0.20″ to .035″
- Blade Widths Available : 1/4″ to 1.5″
- Grit sizes available : 35 to 120 mesh
- Blade edge configurations available : continuous rim, segmented, gulleted, Scallop Segment
- Blade Backing Materials : Steel Alloy, Stainless Steel
- Coolant methods : Wet, Dry
- Average Band Saw Blade Life : 40 to 80 hours. Some has shown to last as long as 192 hours.
Frequently Asked Questions
Industries Used In
Accessories
Recommendations
- Material Compatibility: Always ensure that the blade is suitable for the material you are cutting. Diamond blades are designed for specific materials and using them on incompatible substances can damage the blade or the material.
- Proper Installation: Ensure that the blade is correctly installed on the saw. The blade should be tensioned according to the manufacturer’s specifications to avoid slippage or breakage.
- Cutting Speed: Maintain an appropriate cutting speed. Too fast can overheat the blade and material, causing damage; too slow can reduce efficiency and cause unnecessary wear on the blade.
The recommended RPM (Revolutions Per Minute) for diamond band saw blades can vary significantly based on several factors including the type of material being cut, the diameter of the blade, the hardness of the material, and the specific design of the blade. Here are some general guidelines to consider:
- Material Type: Different materials require different cutting speeds. For example, softer materials like some types of ceramic or glass may be cut at higher speeds, while harder materials like quartz or granite require slower speeds.
- Blade Diameter: The larger the diameter of the blade, the slower the RPM should be. This is because a larger blade will have a higher cutting speed at the edge even with a lower RPM.
- Manufacturer’s Recommendations: Always check the manufacturer’s guidelines for the blade. These guidelines are based on extensive testing and are designed to optimize the blade’s performance and lifespan.
- Cooling Considerations: Higher speeds can generate more heat. If adequate cooling (like a water coolant system) is not in place, it’s advisable to use a lower RPM to prevent overheating the blade and the material.
- Type of Coolant: Water is often used as a coolant for diamond band saw blades, especially when cutting stone, glass, or tile. For some applications, especially in metal cutting, a water-soluble coolant or cutting oil is preferred to reduce friction and remove cuttings more effectively.
- Coolant Concentration: If you’re using a water-soluble coolant, ensure it’s mixed at the correct concentration. Too much water in the mixture can reduce its effectiveness, while too much concentrate can be wasteful and potentially harmful to the blade and workpiece.
- Continuous Flow: Ensure a continuous and adequate flow of coolant to the blade. The coolant should be applied directly where the cutting action is taking place to maximize its cooling and lubricating effects.
- Prevent Overheating: The primary purpose of the coolant is to keep the blade and the material being cut cool. Overheating can damage both the blade and the material and can also lead to dangerous situations.
- Coolant Cleanliness: Regularly clean and replace the coolant to prevent contamination. Dirty or contaminated coolant can reduce cutting efficiency and cause damage to the blade.
- Environmental Considerations: Be aware of the environmental and health implications of the coolant you choose. Some coolants may require special handling or disposal methods.
- Preventing Corrosion: If you’re using a water-based coolant, be mindful of the potential for rust and corrosion on your saw and blades. Consider adding a rust inhibitor to the coolant or regularly applying a rust preventative to your equipment.
- Coolant Distribution System: Maintain your coolant distribution system, ensuring that nozzles or hoses are not clogged and are positioned correctly to deliver coolant effectively to the blade.
- Avoiding Dry Cutting: Unless specifically designed for dry use, always use coolant with diamond band saw blades. Dry cutting can significantly reduce the life of the blade and degrade its performance.
- Coolant Temperature: In very hot conditions, the coolant itself can become warm. Consider ways to keep the coolant temperature down, as overheating can reduce its effectiveness.
- Safety and Health: Always use coolants in a well-ventilated area, and wear appropriate protective gear to avoid contact with skin and eyes. Some coolants may emit harmful vapors or be irritating to the skin.
- Recycling and Reuse: Some coolant systems allow for the recycling and filtration of the coolant for reuse. This can be both cost-effective and environmentally friendly.
- Compatibility with Materials: Ensure that the coolant is compatible with the material you are cutting. Some materials may react adversely with certain coolants.
- Coolant Pressure and Volume: Adjust the pressure and volume of the coolant to suit the cutting conditions. Different materials and cutting speeds may require different coolant pressures and volumes for optimal performance.
- Cutting Precision: For very precise cuts, a slower RPM may be beneficial as it allows for more control.
- Blade Wear and Tear: Using a higher RPM than recommended can lead to increased wear and a shorter lifespan for the blade. Conversely, a speed that is too low may result in inefficient cutting and unnecessary strain on the saw.
- Specific Applications: Some specialized applications may have unique RPM requirements. For instance, cutting very dense or abrasive materials often requires lower RPMs to minimize blade wear.
- Saw Capabilities: Ensure that the RPMs you choose are within the operational range of your saw. Operating a saw at an RPM it’s not designed for can be dangerous and damage the saw.
- Experience and Skill Level: Experienced users may be able to safely and effectively operate the saw at different RPMs based on their understanding of the material and the cutting process.
- Trial and Error: Sometimes, finding the optimal RPM requires a bit of experimentation, starting at a lower speed and gradually increasing it while monitoring the cutting performance and the condition of the blade.
- Lubrication and Cooling: Use an appropriate coolant or lubricant when cutting. This reduces heat build-up, prevents blade overheating, and extends the life of the blade.
- Safety Gear: Always wear appropriate safety gear including eye protection, ear protection, and gloves. Diamond cutting can produce small, sharp particles that pose a risk.
- Regular Inspections: Regularly inspect the blade for damage or wear. Look for missing or damaged diamonds and check the overall condition of the blade.
- Avoid Twisting: Keep the blade straight during cuts. Twisting or bending the blade can cause it to break.
- Feed Rate: Control the feed rate of the material into the blade. Forcing the material too quickly can overload and damage the blade.
- Blade Cleaning: Keep the blade clean from any build-up of material, which can affect its cutting efficiency.
- Storage: Store the blade in a dry, safe place where it won’t be damaged.
- Professional Advice: If unsure about the type of blade needed for a specific job, consult with a professional or refer to the manufacturer’s guidelines.
- Regular Maintenance: Ensure regular maintenance of the saw to keep it in good working condition, which also helps in extending the life of the blade.
Feed Rates
- Material Hardness: Softer materials can generally be cut at higher feed rates, while harder materials require a slower feed rate. For example, cutting marble will have a different optimal feed rate than cutting granite.
- Blade Specifications: The feed rate should match the specifications of the blade being used. Different blades are designed for different materials and cutting speeds. Always refer to the manufacturer’s guidelines.
- Thickness of the Material: Thicker materials require a slower feed rate to ensure an even and consistent cut. Pushing the blade too fast through a thick material can lead to blade deflection, uneven wear, or breakage.
- Type of Cut: Straight cuts can usually be made at a higher feed rate than curved or intricate cuts. For detailed work, a slower feed rate allows for greater precision.
- Blade Wear: A new blade can typically handle a faster feed rate. As the blade wears, you may need to adjust the feed rate to compensate for the reduced cutting efficiency.
- Cooling and Lubrication: Adequate cooling and lubrication can allow for slightly higher feed rates, as they help prevent blade overheating and material burning.
- Machine Capability: Ensure that the feed rate is within the capabilities of your cutting equipment. Overloading the machine can lead to poor cuts and potential damage to the machine or blade.
- Visual and Auditory Cues: Pay attention to the sound of the blade and the appearance of the cut. Chattering, excessive noise, or a rough cut surface can indicate that the feed rate is too high.
- Experience and Judgment: Operator experience plays a significant role in determining the right feed rate. Experienced operators can judge the optimal speed based on the cutting conditions and blade performance.
- Material Fracture Tendencies: Some materials are more prone to chipping or fracturing. A slower feed rate can reduce the risk of damaging these materials.
- Trial and Error: Sometimes finding the optimal feed rate requires experimentation. Start at a lower feed rate and gradually increase it while monitoring the cut quality and blade behavior.
- Safety Considerations: Always prioritize safety. A feed rate that is too high can be dangerous and may lead to loss of control or blade breakage.
- Consistency: Maintain a consistent feed rate throughout the cut for the best results. Inconsistent feeding can lead to blade wandering or irregular cuts.
- Feed Rate Units: Feed rates are typically measured in inches per minute (IPM) or millimeters per minute (mm/min). Ensure you are using the correct units and measurements.
- Blade Break-In: New diamond band saw blades often require a break-in period. Start with softer materials or less aggressive cutting to gradually expose new diamond grit. This can improve the overall performance and longevity of the blade.
- Avoid Overheating: Continuously monitor the blade temperature during use. Overheating can cause the metal to warp and the diamonds to lose their effectiveness. If the blade becomes too hot, pause cutting and allow it to cool down.
- Proper Tensioning: Maintain correct tension on the blade. Too much tension can lead to blade breakage, while too little can result in inaccurate cuts. Refer to the saw manufacturer’s guidelines for proper tensioning procedures.
- Use the Right Blade Width: Choose a blade width that is appropriate for the material and the type of cut you want to make. Wider blades are typically better for straight cuts, while narrower blades are ideal for cutting curves.
- Clean Cuts: Ensure that each cut is clean and straight. A wobbling or chattering blade can indicate a problem with the saw or the blade, and it can also lead to uneven wear or damage to the blade.
- Adjust for Blade Drift: Some band saws exhibit blade drift, where the blade does not cut in a perfectly straight line. Adjust the fence or your cutting technique to compensate for this drift to achieve accurate cuts.
- Use Variable Speed Saws When Possible: If your saw allows for speed adjustment, use this feature to match the speed to the hardness of the material. Harder materials often require slower speeds.
- Gradual Entry on Thick Materials: When starting a cut on a thick or dense material, begin slowly and increase the feed rate gradually. This approach helps in preventing blade shock and reduces the risk of chipping.
- Avoiding Blade Twist: When cutting curves, be mindful not to twist the blade excessively. Sharp turns can strain the blade and cause premature wear or breakage.
- Periodic Resting: Allow the blade to rest periodically during prolonged cutting sessions. This prevents continuous heat build-up and extends blade life.
- Disposal and Replacement: Once a blade becomes too worn or damaged, dispose of it properly and replace it with a new one. Continuing to use a damaged blade can be inefficient and unsafe.
- Training and Experience: If you’re new to using a diamond band saw, consider getting training or advice from experienced users. Understanding the nuances of these blades can greatly improve your cutting technique and safety.
- Blade Direction and Alignment: Ensure that the blade is mounted in the correct direction and is perfectly aligned with the band saw. Misalignment can cause uneven wear and poor cutting performance.
- Avoid Dry Cutting: Unless the blade is specifically designed for dry cutting, always use water or an appropriate coolant. Dry cutting with a blade meant for wet use can lead to overheating and premature wear.
- Regular Blade Cleaning: Over time, cutting residue can build up on the blade, affecting its performance. Regular cleaning helps maintain its cutting efficiency and prolongs its lifespan.
- Monitor Blade Wear: Be attentive to signs of wear such as reduced cutting performance, increased noise, or unusual vibrations. These signs can indicate that the blade needs to be replaced.
- Cutting Technique: For thicker materials, use a “step cutting” technique where you make a series of gradually deeper cuts. This approach can reduce the stress on the blade and improve the quality of the cut.
- Reduce Blade Fatigue: Alternate between different blades if you are making a large number of cuts. This allows each blade to rest and cool down, reducing the risk of fatigue and breakage.
- Avoid Impact or Shock: Never force the blade into the material. A smooth, steady approach is best. Impact or shock can cause diamond grit to dislodge or the blade to break.
- Correct Blade Storage: Store unused blades in a safe, dry place, ideally hanging or laid flat in a way that does not put stress on the blade. Avoid kinking or bending the blade.
- Manufacturer’s Instructions: Always follow the manufacturer’s instructions for use, maintenance, and safety. Different blades may have specific requirements or recommendations.
- Prevent Corrosion: After use, especially with water or coolant, dry the blade to prevent rust and corrosion. This is particularly important for the non-diamond parts of the blade.
- Blade Tracking: Regularly check and adjust the blade tracking. Proper tracking ensures that the blade runs smoothly on the wheels of the saw, reducing wear and the risk of blade deviation.
- Sharp Turns and Corners: When cutting sharp corners or intricate patterns, reduce the feed rate and carefully guide the material. Forcing the blade through tight turns can damage it.
- Understand Blade Specifications: Familiarize yourself with the blade’s specifications such as diamond grit size, concentration, and bond hardness. This information helps in selecting the right blade for a specific material and cutting requirement.
- Respect Load Capacity: Be mindful of the blade’s load capacity. Overloading can lead to blade deformation and potential breakage.
- Professional Maintenance: Consider having your blades professionally sharpened or re-tipped if they become dull. This can be more cost-effective than purchasing new blades.
- Safety First: Lastly, prioritize safety above all else. If you’re ever uncertain about a cutting task, seek professional advice or assistance to prevent accidents.
- Understand Blade Limits: Be aware of the maximum and minimum thicknesses and types of materials your blade is designed to cut. Using a blade outside of its intended range can lead to poor performance and potential blade damage.
- Controlled Feed Pressure: Apply a consistent and controlled feed pressure when cutting. Erratic pressure can cause blade deflection or breakage, and uneven wear.
- Avoid Blade Binding: Ensure that the material being cut does not pinch the blade. Blade binding can cause excessive wear and potential blade breakage.
- Material Stability: Secure the material being cut firmly. Movement during cutting can lead to inaccurate cuts and increase the risk of blade damage.
- Coolant Flow and Quality: Check the flow and quality of the coolant regularly. Ensure that the coolant is reaching the point of the cut and that it is not contaminated, as dirty coolant can harm the blade’s performance.
- Avoid Excessive Bending: When cutting curves, avoid bending the blade excessively as it can lead to metal fatigue and eventual failure.
- Use Appropriate Blade Speeds: Different materials require different blade speeds for optimal cutting. Consult the blade and material specifications for the recommended speeds.
- Blade Thickness Awareness: Be aware of the blade’s thickness and how it relates to the kerf (the width of the cut). This is important for precision cutting and avoiding material waste.
- Regular Breaks During Intensive Use: If using the blade intensively, give it and the saw regular breaks to prevent overheating.
- Blade Dressing: Periodically dress the blade to expose fresh diamond edges. This is especially important for blades that see a lot of use.
- Support Material Adequately: Ensure that larger or heavier materials are adequately supported to prevent blade pinching or deflection.
- Handle with Care: Diamond blades are robust in cutting but can be fragile if mishandled. Avoid dropping or striking the blade.
- Blade Path Clearance: Ensure that the path of the blade is clear of obstructions, including clamps, to prevent accidental contact and potential damage.
- Blade Compatibility with Saw: Ensure the blade is compatible with your particular band saw, considering factors like blade length, width, and tooth pitch.
- Avoid Reactive Materials: Be cautious when cutting materials that may react with water or coolants, such as certain metals, as this can cause damage or safety hazards.
- Record Keeping: Keep records of blade usage, including types of materials cut and hours of operation. This can help in scheduling maintenance and predicting blade life.
- Environmental Considerations: Be mindful of the environmental conditions in which you are working. Extreme temperatures and humidity can affect both the material being cut and the blade.
- User Training and Awareness: Ensure that all operators are adequately trained and aware of the proper usage and safety procedures for diamond band saw blades.
- Blade Disposal: Dispose of used or damaged blades properly, considering local regulations and safety practices.
- Stress Relief Cuts: When cutting large or thick materials, make relief cuts to reduce stress on the blade. This technique involves making additional cuts to remove material and prevent binding.
- Avoiding Side Pressure: Apply cutting pressure in a straight line. Side pressure can bend the blade and lead to uneven wear or breakage.
- Correct Blade Orientation: Make sure the blade’s direction of rotation is correct. A blade installed backwards will be ineffective and can be damaged.
- Material Clamping: Properly clamp or secure the material being cut to prevent movement. Unstable materials can cause irregular cuts and put extra stress on the blade.
- Regular Saw Maintenance: In addition to blade maintenance, ensure that the saw itself is in good condition. This includes checking the guide bearings, tension mechanism, and overall alignment.
- Blade Guide Adjustment: Adjust the blade guides correctly to support the blade close to the cut. This prevents blade deflection and ensures straighter cuts.
- Blade Teeth Per Inch (TPI) Selection: Choose the appropriate TPI for your blade based on the material’s thickness. Generally, a higher TPI is better for thinner materials, and a lower TPI for thicker materials.
- Avoiding Quick Stops and Starts: Avoid abrupt stops and starts during cutting, as this can jar the blade and potentially lead to damage.
- Using a Push Stick for Small Pieces: When cutting small pieces, use a push stick or other device to feed the material. This keeps hands away from the blade and minimizes the risk of injury.
- Cutting at a Consistent Angle: Maintain a consistent angle when feeding the material into the blade. Inconsistent angles can lead to irregular cuts and put uneven stress on the blade.
- Proper Saw Alignment: Ensure that the saw’s wheels, guides, and table are properly aligned according to the manufacturer’s specifications. Misalignment can cause the blade to wear unevenly or break.
- Blade Tension Monitoring: Regularly check the blade tension, as it can change with temperature fluctuations and use. Incorrect tension can lead to poor cutting performance or blade failure.
- Understanding Blade Life Expectancy: Be aware of the typical life expectancy of your blade under normal conditions and plan for replacement accordingly.
- Post-Use Inspection: After each use, inspect the blade for any signs of damage, including chips, cracks, or missing segments. Early detection of damage can prevent more serious issues.
- Avoiding Hazardous Materials: Do not cut materials that might be hazardous, such as materials containing asbestos or other harmful substances.
- Record Blade Performance Issues: Keep a log of any issues encountered during cutting. This can help in troubleshooting and identifying when a blade needs to be replaced or serviced.
- Environmental Cleanliness: Keep the work area clean and free of debris. A cluttered or dirty environment can lead to accidents and affect cutting accuracy.
- Proper Handling and Storage: Handle blades with care, avoiding any actions that could bend or twist them. Store them in a way that prevents physical damage.
- Regular Calibration of Equipment: Regularly calibrate your saw to ensure accurate cuts. Misalignment can lead to increased wear on the blade and poor quality cuts.
- Safety Checks: Perform routine safety checks on the saw and blade before each use. Ensure all safety guards are in place and functioning.
- Personal Protection Equipment (PPE): Always wear appropriate PPE, such as safety glasses, gloves, and hearing protection, when operating the saw.
- Avoid Cross-Contamination: Use different blades for cutting different materials to prevent cross-contamination, which can affect cutting performance and blade life.
- Gradual Increase in Cutting Load: When starting a cutting session, gradually increase the cutting load to allow the blade to warm up, which can prevent shock and wear.
- Regular Coolant Replacement: Change the coolant regularly to prevent contamination, which can affect the cutting process and potentially damage the blade.
- Inspect for Unusual Noises or Vibrations: Be alert to any unusual noises or vibrations during operation, as these can be early signs of blade or equipment issues.
- Use of Blade Stabilizers: Consider using blade stabilizers, if appropriate, to reduce blade vibration and enhance cutting precision.
- Proper Material Support: Ensure that the material is adequately supported both before and after the cut to prevent any unnecessary blade stress or deflection.
- Avoid Abrupt Force: Never apply abrupt force to the blade, either in the cutting direction or laterally. Gentle, consistent pressure is key.
- Maintain a Clean Blade Path: Regularly clean the path of the blade, including guides and wheels, to prevent buildup that can affect the blade’s performance.
- Periodic Professional Assessment: Have your equipment and blades periodically assessed by a professional to ensure they are in optimal condition.
- Educate on Emergency Procedures: Make sure all operators are aware of emergency procedures in case of blade breakage or equipment failure.
- Use the Right Machine for the Blade: Ensure that the saw machine used is suitable for the type of diamond band saw blade, considering factors like power, speed, and size.
- Monitor Blade Alignment During Use: Regularly check the alignment of the blade during use, as it can shift, especially when cutting tougher materials.
- Balanced Blade Wear: Rotate the blade usage if possible, to ensure even wear, which can extend the life of the blade.
- Avoid Twisting the Blade Off the Material: When finishing a cut, avoid twisting the blade off the material, as this can damage the blade.
- Proper Decommissioning of Blades: Decommission blades that are beyond their useful life in a responsible manner, respecting safety and environmental guidelines.
- Attention to Blade’s Running Direction: Ensure that the blade’s running direction matches the indicated direction on the saw. Reversed blades will underperform and can be damaged.
- Check for Material Defects: Before cutting, inspect the material for defects or foreign objects that might damage the blade.
- Lubrication of Moving Parts: Regularly lubricate all moving parts of the saw to ensure smooth operation and reduce wear on the blade.
- Use Blades with Suitable Diamond Grit: Choose a blade with a diamond grit size that is appropriate for the material being cut for optimal performance.
- Safety Training for New Operators: Provide comprehensive safety and operational training for new operators, including practical demonstrations and supervised practice sessions.
- Respect Maximum Depth of Cut: Do not exceed the blade’s maximum depth of cut. Overextending the blade can lead to damage and unsafe conditions.
- Environmental Factors: Consider the impact of environmental factors like humidity and temperature on both the material being cut and the blade.
- Preventive Maintenance Schedule: Establish and adhere to a regular preventive maintenance schedule for both the saw and the blades.
- Ensure Emergency Stop Accessibility: Make sure that the emergency stop button or feature on the saw is easily accessible during operation.
- Understanding Blade’s Limitations: Recognize that even the highest quality diamond band saw blades have limitations and are not indestructible.
Diamond Band Saw Trouble Shooting Guide
Problem
Possible Causes
Solutions
Blade Breakage
Excessive tension
Reduce blade tension
Improper blade size for machine
Ensure correct blade size is used
Excessive feed pressure
Adjust feed pressure to recommended level
Fatigue from repeated bending
Check and adjust blade tracking
Blade Dulling Quickly
Incorrect blade speed
Adjust to optimal speed for material
Inadequate coolant or wrong type
Check coolant flow and type; replace if necessary
Cutting material too hard for blade
Use a blade suitable for the material hardness
Overuse without rest
Allow intervals of rest for the blade
Inaccurate Cuts
Worn or damaged blade guides
Inspect and replace blade guides as needed
Blade misalignment
Align the blade correctly
Incorrect blade tension
Adjust blade tension to recommended level
Using a blade with incorrect tooth pitch
Use a blade with appropriate tooth pitch
Excessive Vibration
Worn bearings
Inspect and replace bearings if needed
Misaligned wheels
Align the saw wheels properly
Damaged blade
Replace the blade
Loose components in the machine
Tighten all loose parts and components
Difficulty in Starting the Cut
Dull blade
Replace or sharpen the blade
Incorrect blade for material type
Select the appropriate blade for the material
Insufficient coolant
Ensure adequate coolant flow
Improper technique
Review and adjust cutting technique
Excessive Noise
Blade hitting machine parts
Check and adjust blade tracking
Loose components
Tighten all loose parts and components
Worn or damaged blade
Inspect blade for damage and replace if necessary
Uneven Wear on Blade
Improper blade tension
Adjust blade tension to even out wear
Misaligned blade
Realign the blade
Uneven material surface
Ensure material is uniformly supported
Uneven Cut Surface
Worn or damaged blade teeth
Replace or sharpen the blade
Blade running at incorrect speed
Adjust blade speed according to material specifications
Improper blade tension
Adjust tension to recommended levels
Excessive Blade Wear
Continuous operation without breaks
Allow the blade to rest periodically
Cutting abrasive materials
Use blades designed for abrasive materials
Insufficient or inappropriate coolant
Use the correct coolant and ensure proper flow
Saw Not Cutting Straight
Blade guides misaligned
Realign the blade guides
Worn or damaged blade
Replace the blade
Machine components out of calibration
Calibrate machine components
Frequent Blade Slippage
Insufficient blade tension
Increase blade tension to proper level
Worn or damaged drive wheels
Replace or repair the drive wheels
Coolant on the blade or wheels
Clean the blade and wheels, ensure coolant is controlled
Coolant Issues
Clogged coolant nozzles
Clean or replace the nozzles
Insufficient coolant flow
Adjust the coolant system for better flow
Incorrect coolant mixture
Ensure the correct mixture and type of coolant
Increased Power Consumption
Blade binding in the cut
Check for proper blade alignment and tension
Dull blade increasing resistance
Replace or sharpen the blade
Motor or drive system issues
Inspect and service the motor and drive system
Difficulty in Blade Installation
Incorrect blade length or width
Use the correct size of blade for your saw
Tension mechanism issues
Inspect and repair the tension mechanism
Misalignment of blade path components
Align the components properly
Blade Deviates from Cut Line
Incorrect blade tension
Adjust tension to recommended levels
Worn or damaged blade teeth
Replace the blade
Misaligned blade guides
Adjust or replace blade guides
Rapid Tooth Strip Off
Excessively hard material
Use a blade designed for harder materials
Too high feed rate
Reduce feed rate
Insufficient blade tension
Adjust blade tension
Blade Binding
Misaligned workpiece
Ensure proper workpiece alignment
Inadequate support for workpiece
Use appropriate supports to stabilize workpiece
Blade worn or damaged
Replace the blade
Irregular Tooth Wear
Uneven material hardness
Check material consistency
Incorrect blade for material type
Select the appropriate blade for the material
Improper blade tension
Adjust tension to recommended levels
Slow Cutting Speed
Blade becoming dull
Replace or sharpen the blade
Incorrect blade speed for material
Adjust the blade speed according to material type
Inadequate power supply to saw
Check and ensure proper power supply
Noise or Chatter During Cutting
Loose components in the saw
Tighten all loose parts and components
Blade tension too low
Increase blade tension
Worn or damaged blade guides
Replace or adjust blade guides
Difficulty in Controlling Cut Direction
Blade too wide for the curve being cut
Use a narrower blade for tight curves
Inadequate blade tension
Adjust tension to recommended levels
Worn or damaged blade
Replace the blade
Excessive Coolant Spatter
High coolant pressure
Adjust the coolant pressure to a lower setting
Misaligned coolant nozzles
Adjust the nozzle alignment
Excessive blade speed
Reduce blade speed
Motor Overheating
Overloading the saw
Reduce feed rate and check for correct blade usage
Inadequate ventilation
Ensure proper ventilation around the motor
Electrical issues
Check and fix any electrical connections and components
Problem
Possible Causes
Solutions
Reduced Cutting Precision
Blade wear and tear
Replace the blade with a new one
Incorrect blade type for the task
Use a blade type more suited to the material
Machine calibration issues
Calibrate the saw according to manufacturer’s guide
Frequent Overheating of Blade or Saw
Continuous operation without adequate cooling
Ensure regular cooling intervals; check coolant system
Overfeeding the material
Reduce feed rate to decrease strain on the blade
Inefficient coolant system
Check and repair the coolant system
Increased Material Waste
Blade wandering off course
Check blade alignment and tension
Incorrect blade width for the material
Use a blade width appropriate for the material
Improper feed rate
Adjust the feed rate for more efficient cutting
Blade Becomes Stuck in Material
Insufficient blade tension
Increase blade tension
Debris build-up on the blade
Clean the blade regularly
Worn or damaged blade teeth
Replace the blade
Difficulty in Blade Tracking
Misalignment of wheels or guides
Adjust the alignment of wheels and guides
Worn or damaged tires on wheels
Replace tires on wheels
Blade not properly seated
Reinstall the blade correctly
Inconsistent Blade Life
Variation in material hardness
Use a blade suited for varying material hardness
Fluctuating feed rates
Stabilize feed rate
Inconsistent maintenance practices
Establish a regular maintenance routine
Excessive Noise During Start-up
Loose components or covers
Tighten all loose components and covers
Motor or belt issues
Inspect and repair/replace motor or belts
Dry or unlubricated moving parts
Lubricate moving parts according to guide
Difficulty in Adjusting Blade Tension
Faulty tension adjustment mechanism
Repair or replace the tension adjustment mechanism
Worn tension springs
Replace tension springs
Corrosion or debris in tensioning components
Clean and lubricate tensioning components
Problem
Possible Causes
Solutions
Frequent Resetting of Circuit Breaker
Electrical overload
Check electrical load and reduce if necessary
Short circuit in saw wiring
Inspect and repair any wiring issues
Faulty motor
Inspect and replace the motor if necessary
Blade Falling Off the Wheels
Insufficient blade tension
Adjust the blade tension
Worn or improperly aligned wheel tires
Replace or realign the wheel tires
Damaged or misaligned blade wheels
Repair or replace the blade wheels
Inefficient Cutting of Curves
Blade too wide for tight curves
Use a narrower blade for tighter curves
Incorrect blade tension
Adjust the blade tension
Improper saw speed
Adjust the saw speed to match the cutting requirement
Vibration in the Saw
Unbalanced wheels
Balance the wheels
Loose components in the saw
Tighten all loose parts and components
Worn bearings or drive belts
Replace worn bearings or drive belts
Difficulty in Maintaining Cut Line
Blunt blade teeth
Sharpen or replace the blade
Incorrect blade for the type of material
Use a blade that is suitable for the material
Misalignment of blade guides
Adjust or replace the blade guides
Excessive Dust and Debris Accumulation
Inadequate dust extraction system
Improve or install a proper dust extraction system
Blade not clearing debris
Check blade type and condition
effectively
replace if necessary
Overloading the saw with material
Reduce the volume of material processed at a time
Difficulty in Blade Alignment
Misaligned blade tracking
Adjust the blade tracking
Worn out blade tensioning components
Replace or repair tensioning components
Debris on blade path
Clean the blade path thoroughly
Blade Chipping or Cracking
Impact with hard or foreign objects in material
Inspect material for foreign objects before cutting
Excessive tension or feed pressure
Adjust tension and feed pressure
Use of blade beyond its lifespan
Replace the blade regularly
Blade Loses Tension During Cutting
Defective tension mechanism
Repair or replace the tension mechanism
Expansion of blade due to heat
Allow blade to cool; adjust tension as necessary
Worn tensioning components
Replace worn components
Material Burn Marks
Too slow cutting speed
Increase the cutting speed
Dull blade
Replace or sharpen the blade
Insufficient coolant
Increase coolant flow or check coolant quality
Blade Produces Rough Cut
Incorrect blade for the material
Use a blade suited for the material
Blade teeth are dull or damaged
Sharpen or replace the blade
Excessive feed pressure
Adjust feed pressure to recommended levels
Saw Struggles to Start Cutting
Low power supply
Check electrical supply and correct any issues
Blade not properly sharpened
Sharpen the blade or replace if necessary
Misalignment of blade or guides
Realign blade and guides as necessary
Inconsistent Blade Movement
Worn or loose drive belts
Replace or tighten the drive belts
Fluctuating power supply
Stabilize the power source or correct electrical issues
Damaged blade wheels
Inspect and replace damaged blade wheels
Difficulty in Changing Blades
Stiff blade tensioning system
Lubricate or repair tensioning system
Misaligned blade guides
Adjust or realign the blade guides
Corroded or jammed blade clamps
Clean, lubricate, or replace blade clamps
Excessive Wear on Blade Back
Blade rubbing against machine parts
Adjust blade tracking and guides
Improper blade tension
Adjust tension to the correct level
Worn blade guides
Replace or adjust the blade guides
Intermittent Cutting Issues
Intermittent electrical issues
Check and repair any electrical connections
Variable material density
Adjust cutting approach based on material density
Inconsistent blade tension
Regularly check and adjust blade tension
Saw Stops Mid-Cut
Overheating due to continuous use
Allow the saw to cool down; use intermittently
Electrical issues, like overheating or faulty wiring
Inspect and repair electrical components
Motor failure
Check the motor and replace if necessary
Blade Wandering During Cut
Blade tension too low
Adjust the blade tension
Worn or improper blade for the material
Replace the blade with a suitable type
Misalignment of blade guides or wheels
Adjust or replace the guides or wheels
Excessive Kerf Width
Blade width too wide for the application
Use a narrower blade
Blade wearing unevenly
Replace the blade; check machine alignment
Improper blade tension
Adjust the blade tension correctly
Coolant Leakage or Spillage
Loose or damaged coolant hoses
Tighten or replace coolant hoses
Overflow from the coolant reservoir
Check and adjust coolant levels
Incorrect coolant nozzle position
Reposition the coolant nozzles
Blade Corrosion or Rusting
Exposure to moisture or improper storage
Store blades in a dry environment; use rust inhibitors
Lack of proper blade maintenance
Clean and oil the blade regularly
Use of corrosive coolants
Switch to a non-corrosive coolant
Motor Vibration or Noise
Imbalanced motor rotor
Inspect and balance the motor rotor
Worn motor bearings
Replace motor bearings
Misalignment of motor with saw components
Realign the motor with the saw components
Difficulty in Maintaining Constant Speed
Variable power supply
Stabilize power source
Drive belt slippage or wear
Adjust or replace the drive belt
Malfunctioning speed control mechanism
Repair or replace the speed control
Blade Teeth Breaking Off
Hitting hard inclusions in the material
Inspect material for hardness variations before cutting
Excessive feed rate
Adjust the feed rate to be more gentle
Fatigue from repeated bending or twisting
Avoid twisting the blade; replace if it becomes fatigued
Table of comparision between plated and braised bond
Comparison Criteria
Electroplated Diamond Band Saw Blades
Brazed Bond Diamond Band Saw Blades
Bonding Process
Diamond particles are adhered to the blade surface through electroplating, involving a current-driven deposition from a diamond-containing solution.
Diamond particles are attached using a brazing process, where diamond grit is mixed with a brazing alloy and heated to bond the diamonds to the blade.
Durability
Generally, have a shorter lifespan due to easier detachment of diamond particles, and more prone to wear and tear.
Tend to be more durable due to stronger bonding, offering a longer lifespan and better performance under heavy-duty conditions.
Application
Best suited for lighter, precision cutting tasks. Often used for cutting softer materials or when a finer cut is needed.
Ideal for heavy-duty cutting and tougher materials. Suitable for demanding applications due to their durability and strength
Cost
Generally less expensive due to the simpler manufacturing process.
More costly owing to the complex brazing process and the blade’s longer lifespan.
Suitability for Specific Tasks
Better for delicate or precision work; suitable for materials like glass, ceramic, and thin stone.Generally less expensive due to the simpler manufacturing process.
Preferred for cutting harder materials such as thick stone, concrete, and reinforced materials, where durability and longevity are crucial.
Bonding Process
Uses electroplating to adhere diamond particles onto the blade surface.
Employs brazing, mixing diamond grit with a brazing alloy and heating to bond to the blade.
Durability
Shorter lifespan, more prone to wear and tear.
Longer lifespan, better performance under heavy-duty conditions.
Application
Ideal for lighter, precision tasks and softer materials.
Suited for heavy-duty cutting and tougher materials.
Cost
Generally less expensive.
Typically more costly
Suitability for Specific Tasks
Better for delicate, precision work; used for glass, ceramic, and thin stone.
Preferred for hard materials like thick stone, concrete, and reinforced materials.
Cutting Speed
Generally offers faster cutting speeds in softer materials.
May cut slower but more effectively through hard materials.
Precision
Provides finer cuts, suitable for detailed and precision work.
Less precise than electroplated but still effective for most applications.
Versatility
Limited to softer materials and precision tasks.
More versatile, can handle a range of materials and applications.
Maintenance Requirements
Lower maintenance due to simpler design, but may require more frequent replacement.
Higher initial durability reduces frequent maintenance but may require specialized care.
Environmental Impact
Lesser environmental impact in production but may contribute to more waste due to shorter lifespan.
Greater initial environmental impact due to brazing process but less waste over time.
Diamond band saw comparison electroplated vis braised bond
Comparison Criteria
Electroplated Diamond Band Saw Blades
Brazed Bond Diamond Band Saw Blades
Bonding Process
Electroplating bonds diamond particles onto the blade surface.
Brazing process mixes diamond grit with a brazing alloy, heating to bond to the blade.
Durability
Shorter lifespan, prone to wear and tear
Longer lifespan, performs better under heavy-duty conditions.
Application
Best for lighter tasks and softer materials.
Suited for heavy-duty cutting and tougher materials.
Cost
Generally less expensive.
Typically more costly.
Specific Task Suitability
Ideal for delicate, precision work; used for glass, ceramic, and thin stone.
Better for hard materials like thick stone, concrete, and reinforced materials.
Cutting Speed
Faster in softer materials.
Slower but more effective in hard materials.
Precision
Provides finer, more detailed cuts.
Less precise but effective for most applications.
Versatility
Limited to softer materials and precision tasks.
Handles a range of materials and applications.
Maintenance
Lower maintenance but may need frequent replacement.
Higher initial durability, may require specialized care.
Environmental Impact
Less impact in production but more waste due to shorter lifespan.
Greater initial impact, less waste over time.
Manufacturing Complexity
Simpler manufacturing process.
More complex manufacturing due to brazing.
Blade Thickness
Typically thinner, allowing for finer cuts
Generally thicker, providing strength for tougher materials.
Heat Resistance
Lower heat resistance, can be a limitation in some applications.
Higher heat resistance, beneficial for prolonged use and tough materials.
Reusability
Limited reuse potential due to wear and tear.
Higher reuse potential due to durability.
Ideal User Profile
Suitable for hobbyists or professionals needing precision in softer materials.
Ideal for industrial applications or professionals cutting tough materials regularly.
Bonding Process
Electroplating bonds diamond particles onto the blade surface.
Brazing process with a mixture of diamond grit and brazing alloy.
Durability
Shorter lifespan due to wear and tear.
Longer lifespan with better performance under heavy-duty conditions.
Application
Best for lighter, precision tasks in softer materials.
Suited for heavy-duty cutting in tougher materials.
Cost
Generally less expensive.
Typically more costly.
Specific Task Suitability
Ideal for delicate, precision work in materials like glass and ceramic.
Better for hard materials like stone and concrete
Cutting Speed
Faster in softer materials.
Slower but more effective in hard materials.
Precision
Provides finer, detailed cuts.
Effective but less precise.
Versatility
Limited to specific tasks in softer materials.
Versatile across a range of materials and applications.
Maintenance
Lower maintenance, frequent replacement needed.
Durable, may require specialized maintenance.
Environmental Impact
Less impact in production, more waste due to shorter lifespan.
Greater initial impact, less waste over time
Manufacturing Complexity
Simpler manufacturing process.
More complex due to the brazing process.
Blade Thickness
Thinner, allowing finer cuts.
Thicker, providing strength for tougher materials.
Heat Resistance
Lower, can be a limitation in some applications.
Higher, advantageous for prolonged use and tough materials.
Reusability
Limited due to wear and tear.
Higher due to durability
Ideal User Profile
Suitable for hobbyists or precision tasks in softer materials.
Ideal for industrial applications in tougher materials
Blade Life Extension
Limited options for extending blade life.
Longer blade life with potential for re-tipping or reconditioning.
Ease of Use
Generally easier to handle due to lighter construction.
May require more skill due to heavier and more robust construction.
Repairability
Limited repair options; often require replacement.
More repairable, especially if the blade body remains intact.
Initial Sharpness
Usually sharper initially, but loses sharpness quicker.
Less sharp initially but maintains sharpness longer.
Heat Generation
Can generate more heat in faster cutting, affecting blade life.
Generates less heat due to robust construction, benefiting longevity.
How it Works
Material removal is accomplished in two steps:
- Step 1: Frictional heat softens the substrate and the teeth scoop out the molten material.
- Step 2: Carbon steel bands are used for flexibility to obtain maximum band life. Method is excellent for cutting extremely hard substrates.
Advantages
- Cuts Longer & Faster : The blades stay sharper throughout a longer life and can be reversed.
- Cuts smoother : Minimal Vibration and high stability are features of the cutting action.
- Cut Safer & Better : Their snag free action reduces the risks of breakages and allows more aggressive cutting
- Cuts Cleaner : Minimal waste, whilst the cutting action reduces chipping and cut surface damage.
- Cuts Cheaper : Long life, high performance and Consistent quality bring a significantly better ROI.
Diamond Band Saw Blade Comparison
Wafering Blade Bond Types |
Continous Rim |
Segmented Rim |
Gulleted Rim |
Dotted Rim |
---|---|---|---|---|
Image |
|
|
||
Sketch |
|
|
|
|
Cross Section |
|
|
||
Close Up |
|
|
|
|
Bond Characteristics |
Most commonly used diamond band saw blade. It can be used in almost any application. Its best suited for cutting thin wall and delicate materials. |
Provides better transport of coolant and better chip removal, with softer, longer chipping materials. However the surface finish on material is somewhat rougher than left by continuous rim blade there should always be two teeth simultaneously engaging the material. |
Faster and more aggressive cutting. Their best use is for dry cutting applications, where coolant cannot be used and for softer and more gummy materials. |
|
Steel Backing Material |
Stainless steel |
Stainless steel |
Carbon steel |
Stainless steel |
(Diamond/CBN)Sizes Available |
25/35 to 325/400 mesh |
25/35 to 325/400 mesh |
25/35 to 325/400 mesh |
60/80 to 140/170 mesh |
Blade Width Available |
¼”,1/2”,3/4”,1”,1.25”,1.5”-2” |
¼”,1/2”,3/4”,1”,1.25”,1.5”-2” |
½”,3/4”,1”,1.25” |
1”, 1.5” |
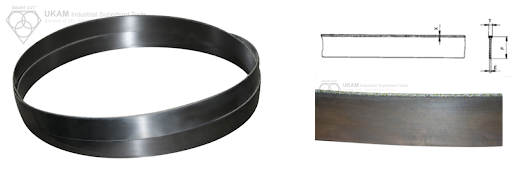
Diamond Band Saw
CONTINUOUS RIM
Continuous Rim Diamond Band Saw Blades are the most commonly used diamond band saw blade. It can be used in almost any application. Its best suited for cutting thin wall and delicate materials.
Diamond Band Saw
GULLETED
Gulleted Diamond Band Saw Blades are used for faster and more aggressive cutting. Theirbest use is for dry cutting applications, where coolant cannot be used and for softer and more gummy materials.
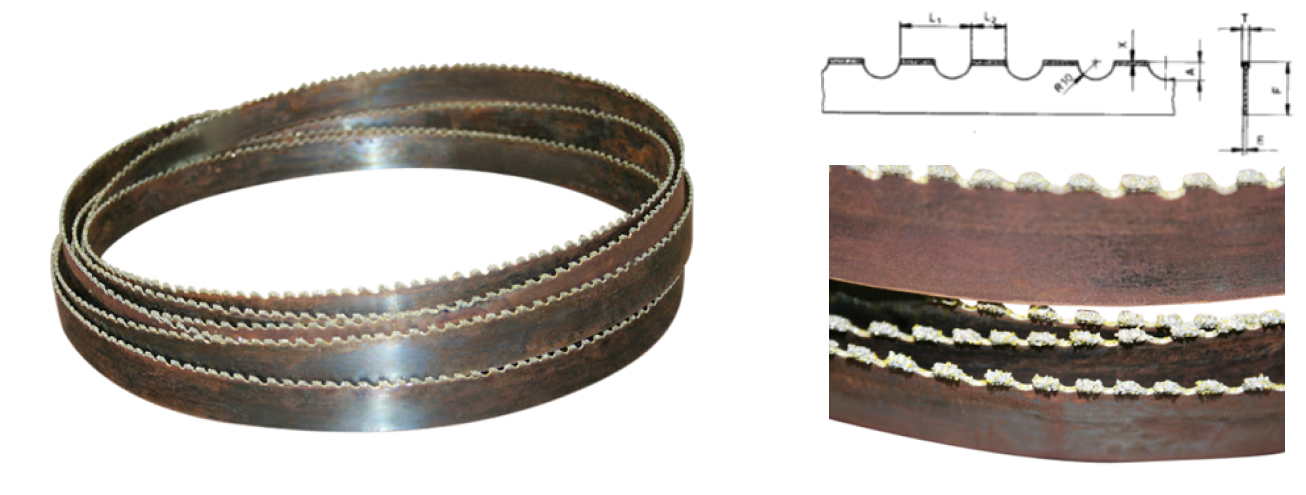
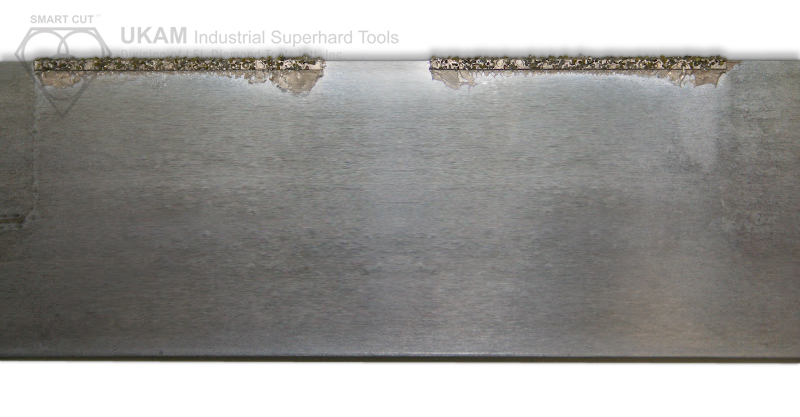
SEGMENTED RIM Diamond Band Saw
Segmented diamond band saw blades provides better transport of coolant and better chip removal, with softer, longer chipping materials. However the surface finish on material is somewhat rougher than left by continuous rim blade there should always be two teeth simultaneously engaging the material.
How SMART CUT® Bond Works?
Step 1
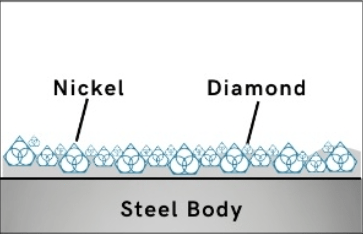
Sharpest And Finest Quality Diamonds
Diamonds or CBN Crystals are activated only at the exposed layer. As Bond Matrix layer begin to wear out, diamonds in a new Bond Matrix layer are immediately activated, substituting the already used up diamond layer. The SMART CUT® Bond Diamond Bond makes sure every diamond is in the right place. and at the right time, working where you need it most.
Step 2
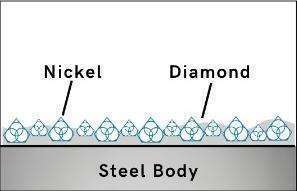
Diamonds or CBN Crystals
The newly exposed diamonds don’t effect diamonds already working on the material. Unlike many other diamond bonds, diamonds in a SMART CUT® remains sharp and grow sharper with each cut, prolonging product life and consistent performance.
Step 3
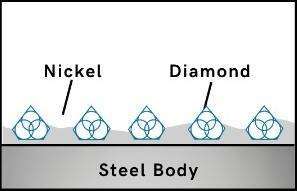
Advanced Formulated Open Diamond Bond Design
This advanced formulated open diamond bond design insures minimal chipping, fast
cut, constant speed of cut, minimal cutting noise, and most important of all, consistent performance.
Application for Electroplated Diamond Band Saw Blades
Material |
Work Height (Inches) |
Recommended Band |
Edge Configuration |
Band Speed (SFPM) |
KERF Loss |
Coolant |
---|---|---|---|---|---|---|
Quartz/Glass |
1-6 |
1" x .020" |
Continuous or Segmented |
2000-2500 |
0.040" |
Yes |
Silicon (Electronic) |
1-6 |
1" x .020" |
Continuous |
1800-2200 |
0.040" |
Yes |
Silicon (Solar) |
1-6 |
1" x .020" |
Continuous |
1800-2200 |
0.040" |
Yes |
Ceramic |
1-6 |
1" x .020" |
Continuous |
1800-2200 |
0.040" |
No |
Carbide |
1-4 |
3/4" x .020" |
Continuous |
1800-2200 |
0.035" |
No |
Granite |
1-4 |
1" x .020" |
Continuous or Segmented |
1800-2200 |
0.055" |
Yes |
Marble |
1-4 |
1" x .020" |
Continuous or Segmented |
2000-2500 |
0.040" |
Yes |
Pyrex |
1-4 |
1" x .020" |
Continuous |
1800-2200 |
0.040" |
Yes |
Masonry Materials |
1-4 |
1" x .020" |
Continuous or |
1800-2200 |
0.040" |
Yes |
Carbon/Graphite |
1-6 |
1" x .020" |
Segmented or |
2000-2500 |
0.040" |
No |
Fiberglass FRP |
Any |
1" x .020" |
Gulleted |
2000-2500 |
0.040" |
No |
Glass Reinforced Rubber |
1-6 |
1" x .020" |
Segmented or |
2000-2500 |
0.040" |
No |
Fiberglass Laminate |
Any |
1" x .020" |
Gulleted |
2000-2500 |
0.040" |
No |
Transite |
Any |
1" x .020" |
Segmented |
2000-2500 |
0.040" |
No |
Wire Reinforced Rubber |
Any |
1" x .035" |
Continuous |
2000-2500 |
0.072" |
No |
Asbestos/Cement Pipe |
1-6 DIA |
1" x .020" |
Segmented |
2000-2500 |
0.040" |
No |
Friction Products |
Any |
1" x .035" |
Segmented |
2000-2500 |
0.072" |
No |
**Note that kerf loss is dependant on diamond grit selected.
Table of comparision between Plated and Braised Bond Diamond Band Saw Blades
Comparison Criteria |
Electroplated Diamond Band Saw Blades |
Brazed Bond Diamond Band Saw Blades |
---|---|---|
Bonding Process |
Diamond particles are adhered to the blade surface through electroplating, involving a current-driven deposition from a diamond-containing solution. |
Diamond particles are attached using a brazing process, where diamond grit is mixed with a brazing alloy and heated to bond the diamonds to the blade. |
Durability |
Generally, have a shorter lifespan due to easier detachment of diamond particles, and more prone to wear and tear. |
Tend to be more durable due to stronger bonding, offering a longer lifespan and better performance under heavy-duty conditions. |
Application |
Best suited for lighter, precision cutting tasks. Often used for cutting softer materials or when a finer cut is needed. |
Ideal for heavy-duty cutting and tougher materials. Suitable for demanding applications due to their durability and strength |
Cost |
Generally less expensive due to the simpler manufacturing process. |
More costly owing to the complex brazing process and the blade's longer lifespan. |
Suitability for Specific Tasks |
Better for delicate or precision work; suitable for materials like glass, ceramic, and thin stone.Generally less expensive due to the simpler manufacturing process. |
Preferred for cutting harder materials such as thick stone, concrete, and reinforced materials, where durability and longevity are crucial. |
Bonding Process |
Uses electroplating to adhere diamond particles onto the blade surface. |
Employs brazing, mixing diamond grit with a brazing alloy and heating to bond to the blade. |
Durability |
Shorter lifespan, more prone to wear and tear. |
Longer lifespan, better performance under heavy-duty conditions. |
Application |
Ideal for lighter, precision tasks and softer materials. |
Suited for heavy-duty cutting and tougher materials. |
Cost |
Generally less expensive. |
Typically more costly |
Suitability for Specific Tasks |
Better for delicate, precision work; used for glass, ceramic, and thin stone. |
Preferred for hard materials like thick stone, concrete, and reinforced materials. |
Cutting Speed |
Generally offers faster cutting speeds in softer materials. |
May cut slower but more effectively through hard materials. |
Precision |
Provides finer cuts, suitable for detailed and precision work. |
Less precise than electroplated but still effective for most applications. |
Versatility |
Limited to softer materials and precision tasks. |
More versatile, can handle a range of materials and applications. |
Maintenance Requirements |
Lower maintenance due to simpler design, but may require more frequent replacement. |
Higher initial durability reduces frequent maintenance but may require specialized care. |
Environmental Impact |
Lesser environmental impact in production but may contribute to more waste due to shorter lifespan. |
Greater initial environmental impact due to brazing process but less waste over time. |
Band Diamond Band Saw Blade Selecting Guid
Here are some recommendation on selecting the right diamond band saw blade for your application.
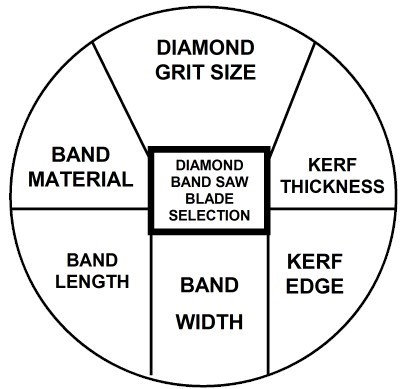
Band Saw Blade Cross Section
Cross section should be specified as wide and as thick as possible (as the application will allow). Please note the diameter of the pulley. Steel band thickness should be in the range 1:1000 with respect to the diameter by the type of cut. For straight cuts, specify the maximum possible band height.
For contours, band height should be selected as follows:
Cutting Edge / Tooth Shape
In principle, continuous rim diamond band saw blade can be used of cutting all materials. The cutting edge is recommend for thin walled an delicate materials. If segmented band saw blade design is used, there should always be two teeth simultaneously engaging the material. The advantages of segmented design are better transport of coolant and better chip removal,with softer, long chipping materials. Howerver, the surface finish on the material is somewhat rougher.
Diamond Mesh/Grit Size
Recommended diamond size will very depending on application. Primary factors to determine proper diamond size include:
- Desired surface finish
- Desired cutting speed
- Cutting characteristics of material
- Cutting width
- Machine parameters
Long chipping materials should be cut with coarser diamond size band saw blades.
Diamond Band Saw Blade Setup Procedure
With new developments of advanced materials, the diamond band saw blade has played a key role in effective sawing and development of these materials. Proper use and installation of diamond band saw blade is critical to its cutting efficiency and life. The following suggestions, will help you get the most out of your diamond band sawing operation.
- Step 1: Place new band saw blade over band saw machine wheels and through guides.
- Step 2: Set band saw machine guides to .001" - .0015" over diamond band saw width.
- Step 3: Place tensigage on the diamond band saw blade in intentioned condition.
- Step 4: Zero gage, then tension to 1.5 units. Diamond Band Saw Blade tension should be set as low as possible to saw your material while still maintaining straight cuts.
- Step 5: Run Diamond Band Saw Blade slowly to properly track on tires.
- Step 6: Release the tension and retention to 1.5 units. Check the tension at beginning of each shift.
- Step 7: Make sure your diamond band saw blade is not toughing back up bearings. Rubbing back up bearings will cause premature failure in the backing material if the diamond band.
- Step 8: Set table speed to cut at four square inches per minute. This is only a recommended starting point. Keeping accurate records on every band saw blade will help you adjust the feed rate to optimize the total square inches of sawing for one diamond band saw blade.
- Step 9: Set band speed to approximately 1500-2500 surface feet per minute. Again, keep accurate records on every band.
- Step 10: Allow only enough table feed to permit the diamonds to cut freely. Overfeed will cause the diamond band saw blade to rub excessively against back up bearings resulting in early fatigue.
- Step 11: When stopping production reduce diamond band saw blade speed to eliminate start up shock.
- Step 12: Make sure to remove tension from diamond band saw blade when not in use.
- Step 13: Occasionally dress diamond band saw blade will clean, sharpen and renew the diamonds.
- Step 14: Weekly inversion of the diamond band saw blade may improve cutting life.
It is recommended that diamond band saw blades be used on most saws, ideally ones with 26″ wheels or larger. This set up procedure will help reduce the problam of early diamond band saw blade fatigue.
Diamond Band Saw Machine Maintenance
Proper mounting and use of diamond band saw blade will insure maximum productivity and life of both your diamond band saw blade and machine. Here are some recommendations and steps to follow on a daily basis:
- Guide Blocks - Checks periodically for war and regrind as neede. Setting the guides for .001" - .0015" band clearance is important for straight cuts.
- Backup Bearings - Check periodically for war.
- Uppper Guideposts - Ste as close to work piece as possible.
- Upper Wheel Slide Assembly - As this area seriously effects band tensioning it must be kept clean. Flush the area with coolant at least once per day.
- Lower wheel Area - Again flush with coolant once per day.
- Tires - Grooves in the tires must be kept clean to prevent hydroplaning and to maintain proper tracking. Check during installation of each new band saw blade.
- Overall Cleanliness - Wiping sown the machine daily can help remind everyone to maintain all the important parts inside the Machine.
- Operator Training - The most important of all, including keeping accurate records on each and every diamonds band saw blade.
Proper setup, use and maintenance of your diamond band saw blades will optimize blade life as well as increase total square inches of material cut by one diamond band saw blade.
Why Work With Us?
Comprehensive Source Of Information On Dicing Blades
We understand that your success depends on select the right dicing blade, and optimizing your dicing parameters to best fit your applications/needs. The more you understand about what we can do for you, the better our partnership will be. On our website you will find the Most Comprehensive Source of Information on Everything you wanted to know about diamond dicing blades & industrial diamond tools.
Large Inventory & Custom Manufacturing
Largest Inventory of Precision & Ultra Thin Diamond Dicing Blades in the U.S. Available in different sizes, thickness, arbor sizes, diamond concentrations, diamond mesh sizes, and bond hardness's.
Experience Makes All The Difference
"ONE OF THE MOST EXPERIENCED COMPANIES IN THE INDUSTRY"
Over the years we have enjoyed working with all types if clients, regardless of size. Proprietary dicing blade chemistry, precision manufacturing methods, modern quality control methods, allow us to control and regulate the dozens of variables that affect blade life, quality of cut, surface finish. Reducing and often eliminating additional steps often required after cutting.
Umatched Technical Support
We Are a Partner In Your Success
Developing close ties with our customers is the foundation of our business. At the core of
our company is a team of world class engineers, knowledgeable customer service personnel here to serve you. Whether is designing or manufacturing a special solution. We will go out of our way to optimizing your process to ultimate level of efficiency.
Advanced
Technology
American Manufacturer As one of the few remaining independent U.S.Diamond Tool & machine builders. We have the experience & tradition to help you remain at frontier of technology Our experience has been further enhanced by acquiring assets and processes from some of the oldest American tool manufacturers, along with their decades of experience and R& D. This has positioned us as one of the most experienced companies in the industry.
Superior Quality &
Consistency
Expect More From Your Tools
Our unique bond formulations, tool designs, stringent requirements, and utilization of exceptionally high-quality diamonds and raw materials ensure top-notch products that adhere to strict ISO 9000 standards.
Our proprietary technology allow us to control and regulate the dozens of variable that affect toolife, quality, & consistency
Related Products
SMART CUT® Diamond Cylindrical Grinding Wheels
SMART CUT® Diamond Cylindrical Grinding Wheels are engineered for the precise peripheral grinding of silicon ingots, making them an ideal choice for industries such as semiconductors, electronics, automotive, and photovoltaics. These high-performance grinding wheels are designed to process the outer surfaces of silicon ingots, ensuring accurate orientation flats are created, which are essential for subsequent processing steps. The addition of the orientation flat, a marked edge indicating the crystallographic plane of the wafer, is crucial for the wafer's alignment in future manufacturing processes.
During the post-slicing phase, wafers undergo shaping and smoothing through peripheral grinding.
SMART CUT® Diamond Notch
SMART CUT ® Single & Multi Layered Electroplated Diamond Notch Grinding Wheel is designed for high-precision notch grinding of semiconductor wafers, including materials such as Silicon (Si), Silicon Carbide (SiC), Gallium Arsenide (GaAs), and Sapphire. Engineered using advanced electroplating technology, this wheel ensures exceptional performance in wafer processing, offering a high level of precision and durability for demanding semiconductor applications.
SMART CUT® Diamond Edge Grinding Wheels (Electroplated)
SMART CUT® Diamond Edge Grinding Wheels are engineered to deliver exceptional performance for precision grinding applications, providing superior results in both rough and fine grinding. These wheels are ideal for use in industries that require highly accurate EDM processing and consistent wafer-to-wafer results. Manufactured with synthetic diamond grit, SMART CUT® wheels offer improved surface roughness and extended tool life due to their tightly controlled diamond distribution and uniform bond structure.
SMART CUT® Braised Bond Diamond Band Saw Blades
ID blades
Diamond Wire
SMART CUT Diamond wire produces minimum kerf loss, less sub-surface damage, and contamination free coolant. Used for precision cutting of various types of artificial crystal, ceramic, quartz glass, monocrystalline silicon, polycrystalline silicon, sapphire and special metal materials. Diamond Wire cutting is an environmentally friendly cutting process as it eliminates slurry recycling and disposal issues.
SMART CUT® HD Synthetic Low IFT Coolant/Lubricant For Diamond Wire Sawing Silicon
SMART CUT® is a synthetic coolant specifically designed for the cutting of semiconductor materials, including sapphire, silicon, germanium, single-crystal SiC, and II-VI crystals. This coolant offers excellent cut rates and imparts outstanding surface finishes with reduced warp and total thickness variation (TTV). It is ideal for diamond abrasive cropping, squaring, and wafering of silicon ingots using ID, band, and wire saws. SMART CUT® HD-2B can also be used as a non-re-circulating edge grinding coolant or lubricant for silicon wafers and ingots.
DIAMOND BACKGRINDING WHEELS
SMART CUT® Diamond Backgrinding Wheels are designed for precision thinning and flattening of silicon wafers, glass, and ceramic substrates. These high-performance wheels are used on backgrinding machines, including models from Disco, Okamoto, Strasbaugh, and other leading manufacturers. Available in sizes ranging from 8” to 14” O.D., they are engineered to handle a wide range of materials and applications, from semiconductor wafers to microelectronic packages.
Recently Viewed Products
ARE YOU USING DIAMOND BAND SAW BLADES
FOR YOUR APPLICATION?
LET US
HELP YOU
HAVING ISSUES WITH
YOUR DIAMOND BAND SAW BLADES?
Knowledge Center
17
Sep
Diamond Band Saw Blades Usage Recommendations & Best Practices
Diamond band saw blades are used for cutting large variety of materials from ultra hard ceramics to glass and composite materials. This article covers all critical usage recommendations and best practices for diamond band saw...
04
Aug
Diamond Wire vs band saw blades and circular blades
Diamond wire, band saw blades, and circular blades are all cutting tools used in various industries for different purposes. Each tool has its advantages and applications
For cutting ultra hard...
08
Jul
The Comprehensive Guide to the Processes of Silicon Wafers Production
Share this Article with Friend or Colleague
The production of silicon wafers, an essential component in semiconductor manufacturing, involves several intricate steps to ensure precision and quality. This article explores the detailed processes depicted in...
08
Jul
Manufacturing Processes for Silicon Semiconductors From Ingot to Integrated Circuit
Share this Article with Friend or Colleague
1. Ingot Production
The journey begins with the creation of silicon ingots, which are pure silicon cylinders produced through methods like the Czochralski process. Once formed, these ingots undergo a...
- Unmatched Selection For Many Applications
- Superior Quality & Consistency
- Immediate Worldwide Delivery
- Technical Support & Expertise
- American Based Manufacturer
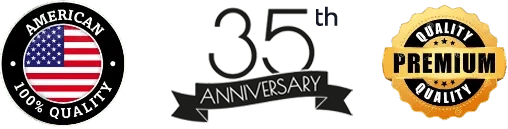

- Different Product
- Different Technology
- Different Company
- Expect MORE from your tools
Let Us HELP You!
Subscribe To Our Newsletter
Signup for email offers, updates, and more
Contact Us
- 25205 & 25201 Avenue Tibbits Valencia CA 91355 USA
-
Phone : (661) 257-2288
FAX : (661) 257 -3833 - lel@ukam.com
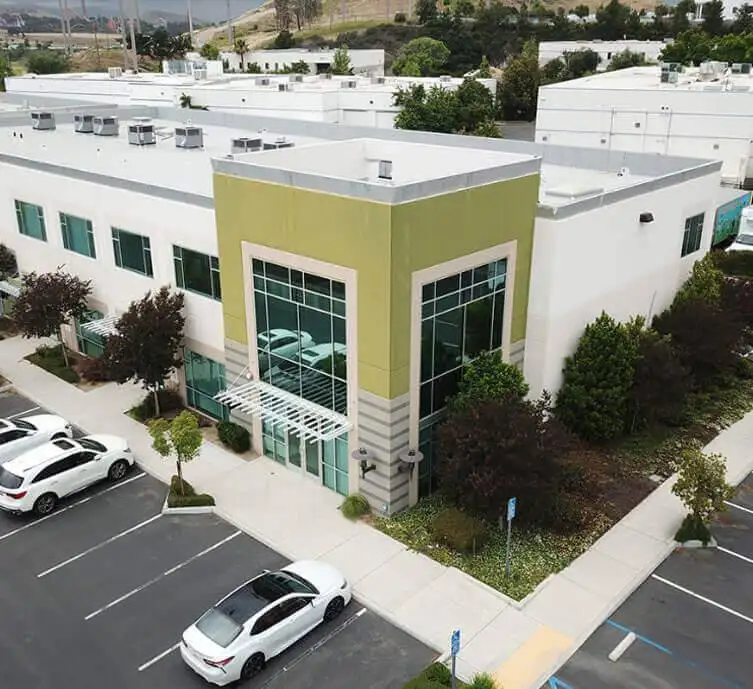
UKAM Industrial Superhard Tools is a U.S. High Technology, Specialty Diamond Tool & Equipment manufacturer. We specialize in producing ultra thin & high precision cutting blades and precision cutting machines diamond drills, diamond micro tools, standard & custom advanced industrial diamond tools and consumables.
- 25205 & 25201 Avenue Tibbits Valencia CA 91355 USA
-
Phone : (661) 257-2288
FAX : (661) 257 -3833 - lel@ukam.com
- 25205 & 25201 Avenue Tibbits Valencia CA 91355 USA
-
Phone : (661) 257-2288
FAX : (661) 257 -3833 - lel@ukam.com
DIAMOND TOOLS BY BOND
EQUIPMENT
KNOWLEDGE CENTER
OUR PRODUCTS
COMPANY
CUSTOMER SERVICE
Shipping Methods


Safe & Secure Payments

© Copyright 1990-2025. UKAM Industrial Superhard Tools – Terms of Use