Table of Contents
ToggleDiamond carving points are essential tools for anyone working with hard materials like glass, stone, and metals. These tools facilitate detailed tasks such as engraving and finishing, offering precise control and enabling you to work efficiently. However, knowing how to use these tools properly can make a significant difference in their effectiveness and longevity.
Share this Article with Friend or Colleague
This guide will help you learn the right ways to use diamond carving points. Whether you're just starting out or you have some experience, you'll find tips on setting up your equipment, and using the right techniques for different tasks. By following these steps, you can get the best results from your tools and do great work on your projects.
Step 1: Preparation:
Before commencing any carving project, it is crucial to assemble all necessary materials and verify that you have selected the correct diamond carving point suited for your specific task. This involves evaluating the hardness and texture of the material you will be working with and matching it with an appropriately shaped and sized diamond point to achieve optimal results.
Equally important is prioritizing your safety by donning appropriate protective gear. Protective goggles are essential to shield your eyes from any particles or debris that might be dislodged during the carving process.
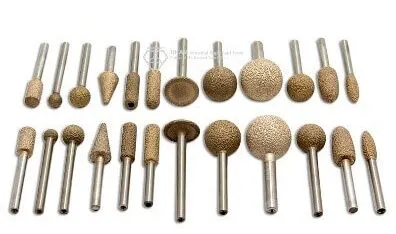
Gloves will protect your hands not only from the sharp edges of the material being carved but also from any accidental slips that may occur while handling the power tool. Additionally, considering the fine dust that can be generated during the carving, wearing a dust mask is advisable to prevent inhalation of any potentially harmful particles. This preliminary preparation sets the stage for a safe and effective carving session, ensuring both the quality of your work and your personal safety are maintained.
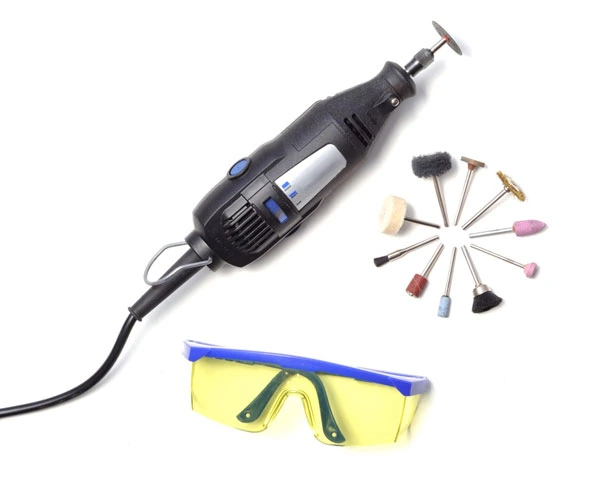
Step 2: Set-Up
Before you begin the actual carving, setting up your equipment correctly is vital for both safety and functionality. Start by making sure your rotary tool is turned off and unplugged. This precaution prevents the tool from accidentally activating while you are setting it up, which could lead to injuries.
Next, attach the diamond carving point to the rotary tool. Follow the specific instructions provided by the tool's manufacturer to ensure it is fitted correctly. Typically, this involves inserting the carving point into the collet or chuck of the rotary tool. It’s important to secure the carving point tightly; a loose carving point can lead to imprecise carving or even become a projectile hazard if it detaches during use.
Once you are confident that the carving point is securely fastened and the setup is stable, plug in your rotary tool. You’re now ready to turn it on and begin the carving process.
Ensuring that these setup steps are meticulously followed can greatly enhance your control over the tool and contribute to achieving the desired outcomes in your carving project.
Step 3: Testing
Before diving into your main project, it is essential to conduct a preliminary test to ensure that everything is set up correctly. Start by selecting a scrap piece of material similar to what you will be working on. This test piece will help you verify that the carving point is properly attached and functioning as expected without risking your actual workpiece.
Use the scrap material to make a few test cuts. This will allow you to check that the carving point is securely fastened and not showing any signs of wobbling or detachment. If any issues arise, it's crucial to recheck the attachment and make any necessary adjustments before proceeding.
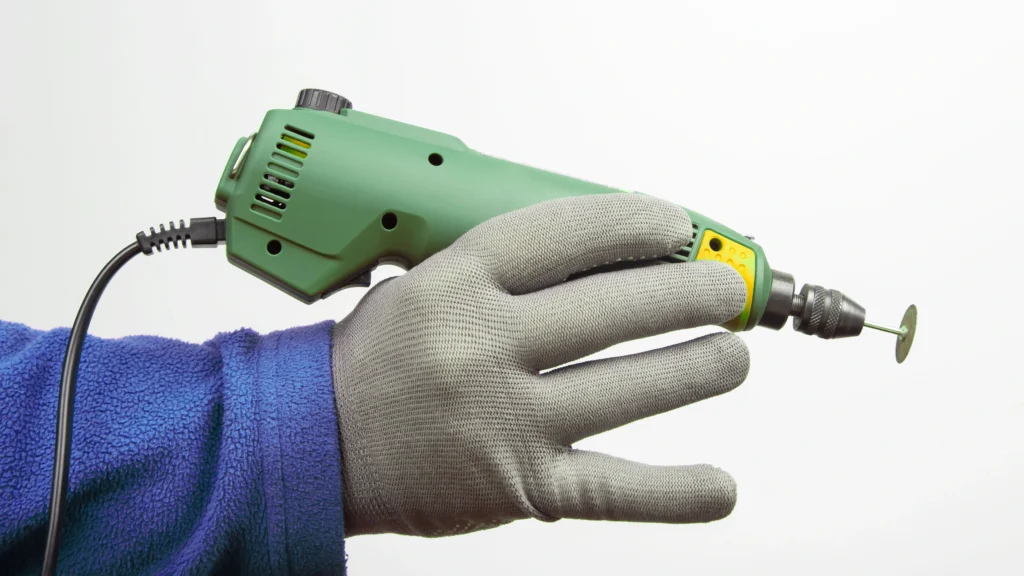
Additionally, this testing phase is an ideal time to adjust the speed of your rotary tool. The correct speed setting is crucial and varies depending on the material's hardness and your desired level of control and finish. Start at a lower speed and gradually increase it to find the optimum setting that allows for efficient carving without overheating the tool or the material. These adjustments and checks are fundamental to ensure a smooth transition to more detailed work on your main project.
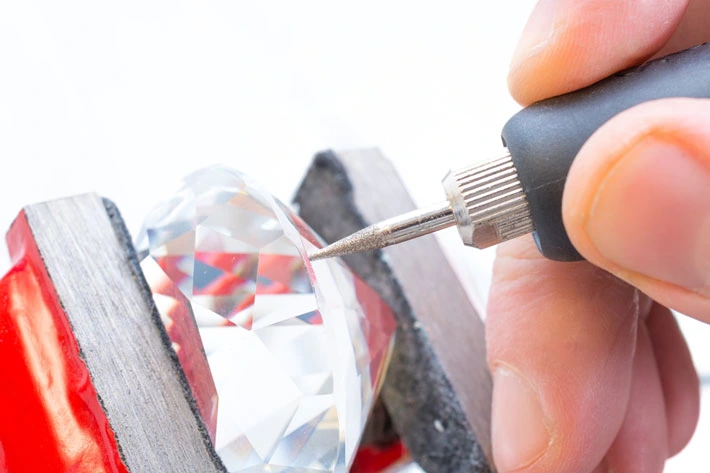
Step 4: Engraving or Sculpting
Once your setup and preliminary tests are complete, you can begin the engraving or sculpting process. Handling the rotary tool correctly is key to achieving precise and fine results. Hold the tool similarly to how you would a pen, with a firm yet comfortable grip. This posture allows for greater control and precision in your movements.
Start by gently touching the carving point to the material at the starting point of your design. It's important to initiate contact with a light touch to prevent the tool from slipping or gouging the material unexpectedly. Begin moving the carving point along the material, carefully following the outline of your design or pattern.
Maintain steady and controlled movements throughout the process. The key is to let the tool do most of the work without applying excessive force.
Forcing the tool can lead to uneven engraving, potential tool damage, or even breakage of the carving point.
Focus on working in small sections; this approach allows for better management of detailed areas and makes it easier to monitor your progress. Periodically stop to check the results of your engraving or sculpting. This periodic assessment helps in making any needed adjustments to your technique or tool settings, ensuring that each segment of your design meets your standards before moving on to the next.
Carving Techniques
Mastering the effective handling and control of a rotary tool is essential for achieving high precision in carving projects. A firm yet comfortable grip on the tool, similar to how one might hold a pen, is crucial. This specific grip enhances control over the tool, facilitating delicate and precise movements that are paramount when crafting intricate details or achieving artistic effects. It is beneficial to experiment with various holding positions to discover the one that offers optimal control while minimizing fatigue, especially during extended carving sessions.
The positioning and movement of the tool also play significant roles. For intricate work, it's advantageous to use short, smooth strokes, which allow for greater accuracy and detail. When working on larger areas or roughing out shapes, longer, more fluid strokes may be more effective. It's important to always move the tool in a direction away from your body to enhance safety and control.
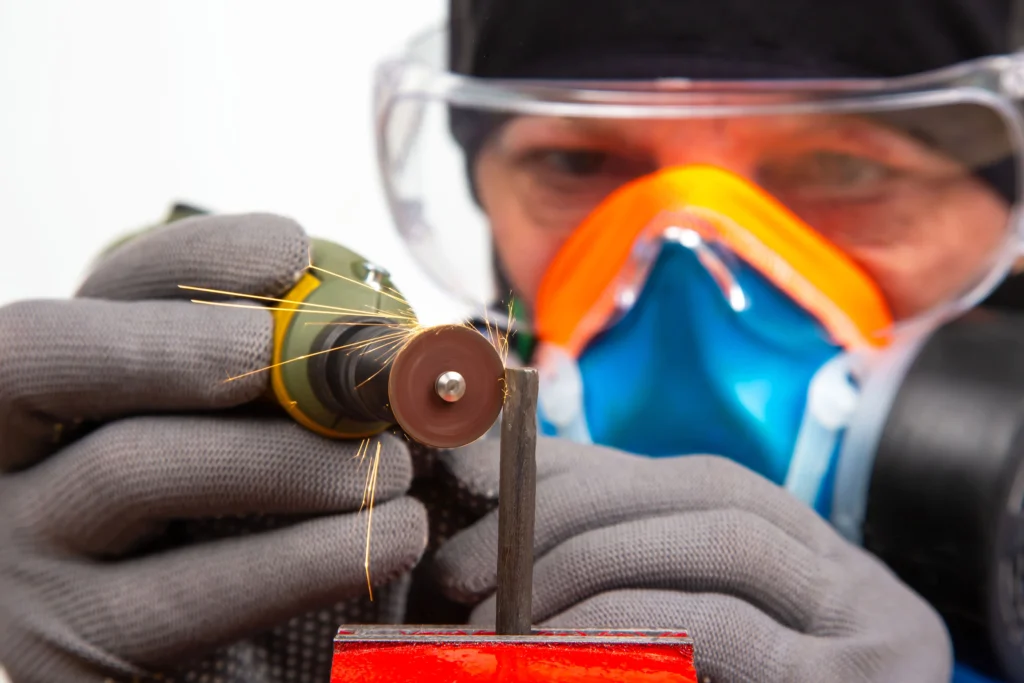
Adjusting the speed and pressure applied during the carving process is critical and can greatly influence the final outcome. Different materials require tailored approaches based on their hardness and the finish you aim to achieve. For instance, softer materials such as soapstone or wood typically require lower speeds to avoid tearing or chipping. Conversely, harder materials like gemstones or hard metals might need higher speeds to penetrate the surface effectively.
Starting at a lower speed setting and incrementally adjusting upward allows you to determine the most effective speed that interacts optimally with the material without causing damage. Likewise, initiating with only light pressure is recommended, increasing it cautiously as needed. This method ensures that the carving point does the work, reducing the likelihood of errors or unnecessary tool wear.
Understanding the nuances of speed and pressure in relation to the material's characteristics is crucial. For example, materials like acrylic and plastic can melt or burn if carved at too high a speed, whereas materials like granite or hardened steel require high speeds to make any impact.
Step 5: Finishing
After completing your design, the next step is to properly finish and care for your tools. Begin by turning off the rotary tool and unplugging it from the power source. This ensures safety while handling the tool and during the cleaning process.
Carefully remove the carving point from the rotary tool. It's important to handle the point cautiously to avoid damage to both the tool and the point itself.
Once the carving point is removed, proceed to clean it. Use water and a soft brush to gently remove any debris or particles that have accumulated on the point during the engraving or sculpting process. Thorough cleaning not only preserves the quality of the diamond carving point but also ensures that it remains sharp and effective for future use.
Dry the carving point thoroughly after washing. Ensure that no moisture remains as this could potentially damage the point or lead to rust formation in metal parts.
Finally, store the carving point safely. It is advisable to return it to its original packaging or place it in a protective case. Proper storage protects the carving point from environmental factors and accidental drops or impacts, ensuring that it remains in good condition and ready for your next project.
Step 6: Maintenance
Maintaining your diamond carving points is essential to ensure their longevity and performance. Regular cleaning and inspection should be part of your routine after each use. Check each carving point for any signs of wear or damage such as nicks, bends, or dullness. This inspection helps in identifying issues early, which can prevent further damage or poor performance during subsequent uses.
If a carving point becomes dull or shows visible damage, it's crucial to replace it immediately. Working with a damaged or dull point can result in poor engraving quality and can also put additional strain on both the tool and the material you are working with.
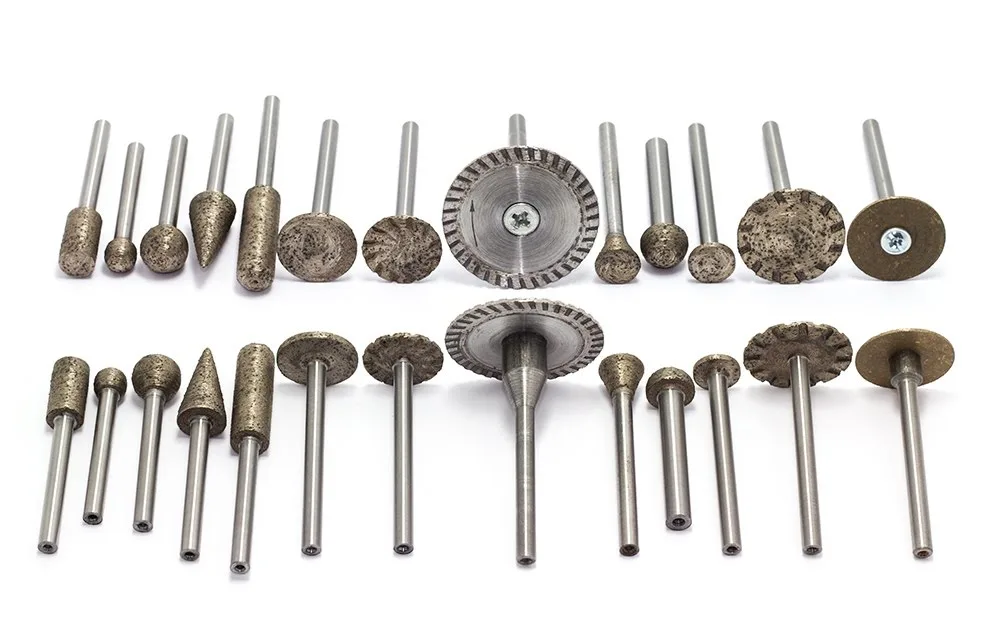
Regular replacement of carving points ensures that your work remains precise and that your tools function efficiently. This proactive approach to maintenance not only prolongs the life of your rotary tool but also helps in achieving consistently high-quality results in your carving projects.
Step 7: Post-Project Cleaning and Storage
Proper post-project cleaning and storage of diamond carving points are essential to maintain their effectiveness and prolong their lifespan. After completing your carving tasks, it's imperative to thoroughly clean the carving points to remove any accumulated debris or residue. This step is crucial because any leftover material can harden and become difficult to remove later, potentially impairing the performance of the carving points.
To clean the carving points effectively, use a soft brush and lukewarm water. Gently scrub the surface of the carving points to dislodge any particles. It’s important to avoid using harsh chemicals or abrasive cleaning materials, as these can damage the delicate electroplated diamond coating that provides the carving ability of the points. Such damage not only diminishes the performance but also shortens the tool's useful life.
After cleaning, ensure that the carving points are completely dry before storage. Any moisture left on the tools can lead to rust or corrosion, particularly if the points have any metallic components. Drying can be achieved by wiping them with a soft, dry cloth and then leaving them to air dry in a well-ventilated area away from direct heat sources.
For storage, choose a location that is dry and cool. Exposure to direct sunlight or extreme temperatures can cause expansion or other deformities, which might compromise the integrity of the diamond coating. Ideally, the carving points should be stored in their original packaging or a protective case. These containers are designed to protect the tools from physical impacts and environmental conditions. If the original packaging is not available, an alternative is to use a sturdy box with individual compartments lined with a soft material to keep the points separated and cushioned.
Using the Right RPM’s for your Application
Selecting the optimal RPMs (revolutions per minute) for diamond carving points is essential to maximize efficiency and precision in your carving projects. The correct speed can significantly influence the quality of the cut and the longevity of both the tool and the material being worked. Below are expanded guidelines to help you choose the best RPM for various scenarios:
Soft Materials (e.g., wood, plastic)
When carving softer materials, it's vital to use a lower RPM to prevent overheating which can lead to material deformation. RPMs ranging from 5,000 to 15,000 are typically sufficient. This speed range helps in preserving the material's integrity, avoiding burn marks, and ensuring that the finer details of the design are not compromised by excessive force or speed.
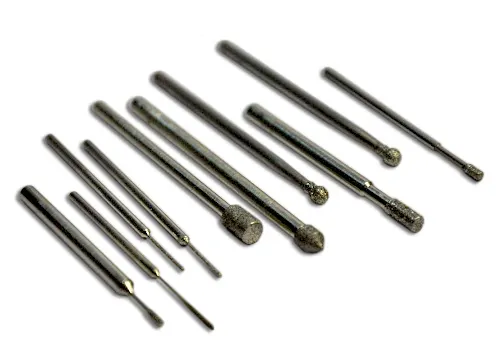
Hard Materials (e.g., glass, stone, metal)
For harder materials, which are more challenging to penetrate, a higher RPM is recommended. Speeds between 10,000 to 30,000 RPM enhance the carving point's ability to efficiently slice through tough substances, facilitating a more manageable carving process and finer finish. It is important to monitor the tool's performance as excessively high speeds can sometimes lead to premature wear or potential breakage of the carving point.
Intricate or Detailed Work:
Precision is key in detailed work, requiring a controlled, lower RPM. Slower speeds afford the artisan better command over the tool, reducing the likelihood of errors and unwanted scratches or gouges. This is particularly crucial when working on complex patterns or delicate materials where one small slip can ruin the aesthetics of the piece.
General Carving and Shaping:
General carving and shaping benefit from a moderate RPM setting, which balances cutting power with maneuverability. This balance is crucial for effective material removal while still allowing the operator to guide the tool smoothly along intended paths.
Adapting to Material Response:
Always be attentive to how the material responds as you carve. Different materials and even different pieces of the same type of material can behave unpredictably. If you notice excessive chipping or cracking, it might be necessary to adjust the speed downward. Conversely, if the tool seems to bog down or not make efficient progress, gradually increasing the speed might be warranted.
Safety and Equipment Care:
Always prioritize safety by wearing appropriate protective gear and operating within the tool manufacturer’s recommended speed ranges. Regularly inspect your tools for wear and ensure they are maintained correctly to avoid accidents and achieve the best results.
By starting at a lower RPM and carefully adjusting based on the tool's performance and the material's response, you can greatly enhance the quality of your work and the enjoyment of your crafting experience. Additionally, referring to the manufacturer’s guidelines can provide valuable specifics that might not be universally applicable but are crucial for the particular tools and materials you are using.
Recommended Coolant & Application
Utilizing a coolant when working with electroplated diamond carving points is essential for maintaining optimal performance and prolonging the life of your tools. Water is the preferred coolant due to its accessibility, effectiveness in heat reduction, and safety in various applications. Here’s an in-depth look at how to effectively incorporate coolant during your carving processes
Choosing the Right Coolant:
Clean water is the ideal choice for most carving and engraving tasks involving electroplated diamond points. It efficiently cools the points, reducing the heat generated during operation, which can otherwise lead to premature wear or potential damage to both the tool and the material.
Methods of Introducing Coolant
-
Dipping Method: Begin by dipping the carving point into water before initiating the engraving or carving process. Continue to dip the tool periodically throughout the operation to maintain coolness and reduce dust and debris accumulation.
-
Spray Bottle Method: Fill a spray bottle with clean water and spray directly onto the material's surface where the carving is being performed. This method helps keep the carving point cool and also minimizes dust around the working area.
-
Sponge Method: Keep a water-soaked sponge nearby your working station. Periodically touch the carving point to the sponge to cool it down. This method is particularly useful for quick and localized cooling without interrupting the workflow.
Additional Considerations and Safety Tips:
-
Ensure the rotary tool you are using is compatible with the use of liquids. Protect all electrical components of the tool from water exposure to prevent any electrical hazards.
-
Be particularly cautious if the material or device you are working on is sensitive to water or electrical interactions. Avoid allowing water to contact any electrical parts to prevent damage or hazards.
-
Always adhere to the manufacturer’s guidelines regarding the use of coolants. These recommendations can provide specific instructions tailored to your tools, ensuring safety and efficiency.
Implementing these practices will not only enhance the effectiveness of your diamond carving points but also contribute to a safer and more controlled working environment. By carefully selecting and applying coolant, you can significantly improve the carving experience, ensuring that your tools perform at their best and last longer.
Recommended Feed Rates
Determining the optimal feed rate and pressure for using diamond carving points & tools is an intricate process that hinges on several critical factors. The hardness of the diamond, the characteristics of the material being carved, and the specifics of the project all play pivotal roles. Here is a deeper exploration of how to fine-tune these parameters, specifically focusing on challenging materials like glass and stone:
For hard materials such as stone or glass, finding the right balance in feed rate is crucial. Typically, a moderate to slightly faster feed rate proves beneficial. This balance allows the diamond points to effectively penetrate the material, facilitating efficient carving without putting undue stress on the tool. The hardness of the material affects the selection of the right feed rate; denser stones like granite may require a slightly higher rate compared to softer stones like limestone to prevent the tool from stalling.
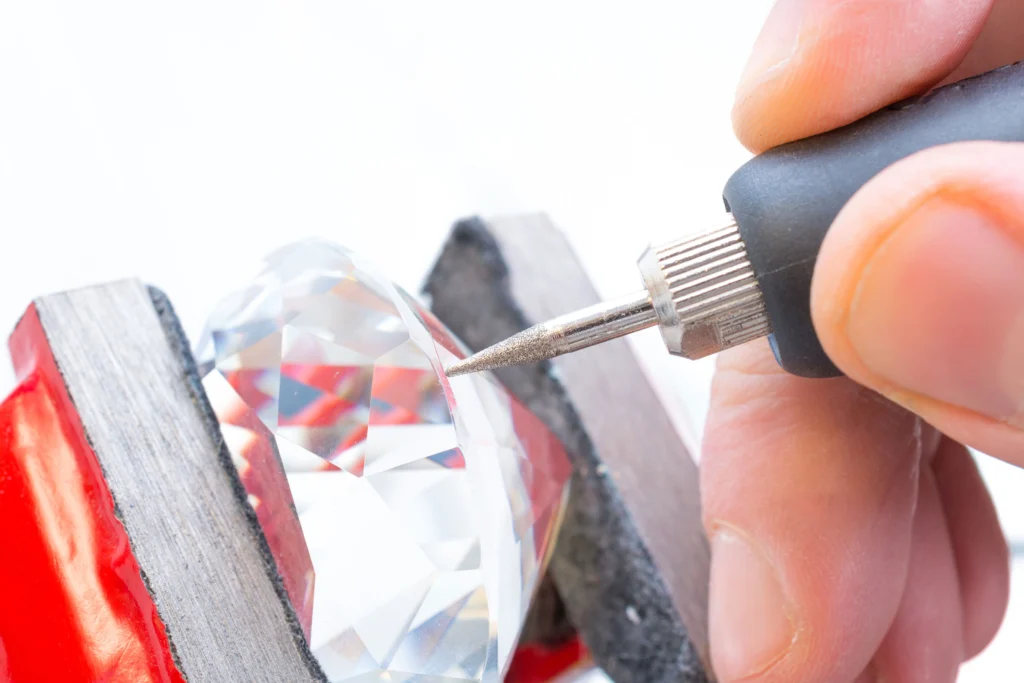
Meanwhile, delicate glass work demands a more nuanced approach to avoid chipping or cracking. Additionally, the size and shape of the diamond carving point influence the ideal feed rate, with larger or more robust points capable of handling higher feed rates, while intricate or smaller points might need slower speeds to accurately carve without causing damage. Deep cuts require careful management of feed rates to prevent tool deflection or breakage, and it's advisable to incrementally adjust the feed rate as the depth of the cut increases.
Pressure to Apply
Maintaining a steady, moderate pressure is key when applying pressure. Consistency helps prevent the diamond point from skipping across the surface or digging in too deeply, which could mar the material or harm the tool. The response of the diamond carving point during the process can indicate if the pressure needs adjustment; if the tool seems to be laboring or vibrating excessively, reducing the pressure might be necessary. Conversely, if the tool is not engaging the material effectively, a slight increase in pressure might be required. Different materials will react differently to the same pressure settings; for instance, glass requires a gentler touch to prevent cracks and fissures, while dense stones can tolerate more forceful engagement.
When beginning a new project or working with a new material, it's beneficial to start with lower settings for both feed rate and pressure. This cautious approach allows you to gauge the material's response and adjust accordingly without risking damage. Introducing a suitable coolant can help reduce friction and heat buildup, which in turn allows for higher feed rates and pressures without compromising the integrity of the material or the tool. It's also important to regularly check the condition of your diamond carving points. Worn tools may not only reduce efficiency but can also affect the necessary feed rate and pressure, as dull points require different settings compared to sharp ones.
Remember that practice and experience are key to finding the optimal feed rate and pressure for your specific projects. It may take some trial and error to find the right balance, but with time and practice, you will develop a feel for what works best.
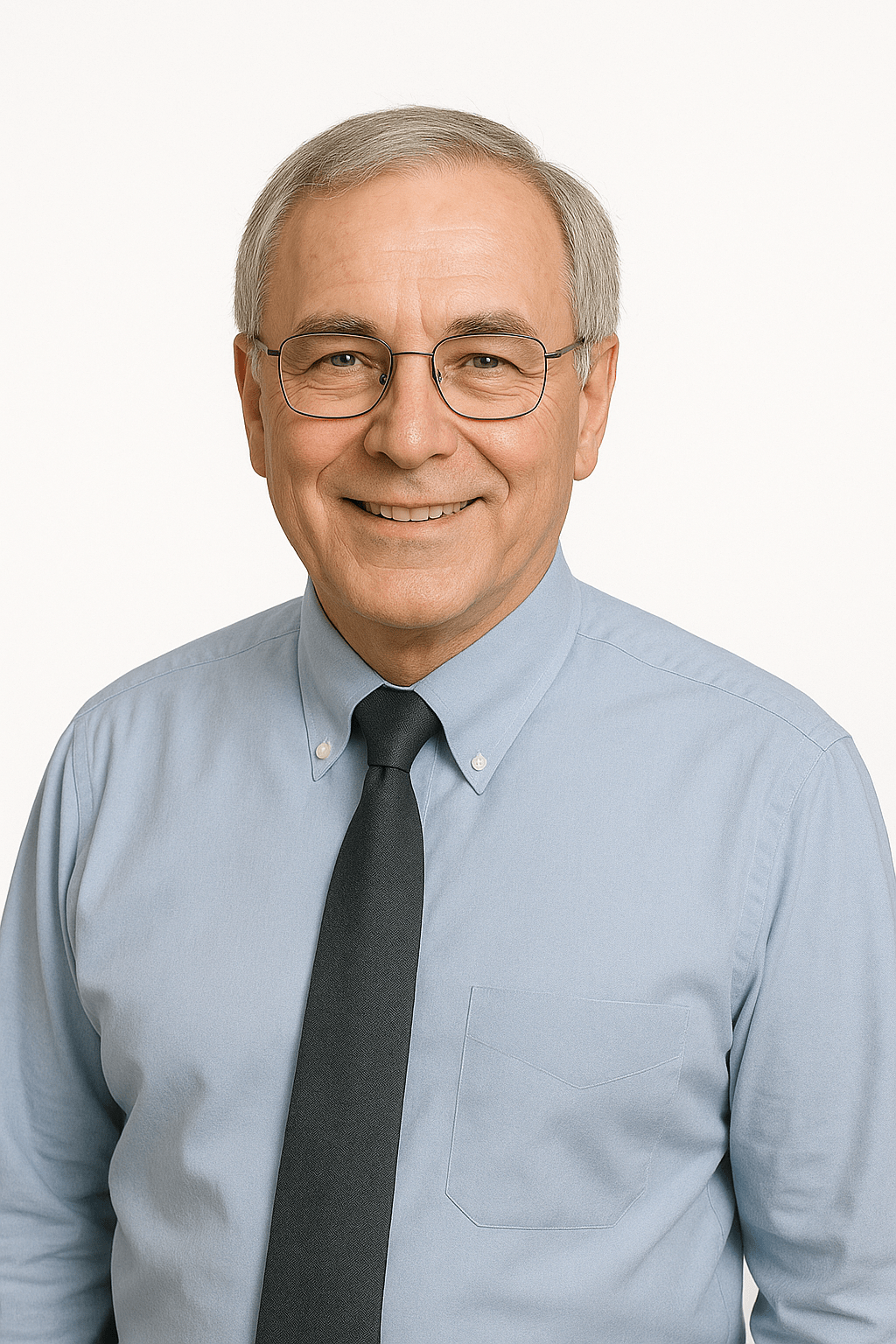
Alexander Schneider is a senior applications engineer and leading authority in the industrial diamond tooling industry, with over 35 years of hands-on experience in the development, application, and optimization of ultra-thin and high-precision diamond blades, diamond core drills, and diamond and CBN grinding wheels. His work spans a wide range of advanced materials including ceramics, glass, composites, semiconductors, and high-performance metals.
Throughout his career, he has collaborated with leading R&D institutions, national laboratories, and high-tech manufacturing companies across Europe, North America, and Asia, providing technical expertise and tailored solutions for demanding cutting and surface preparation applications.
Mr. Schneider has played a pivotal role in advancing precision cutting, sectioning, dicing, and grinding technologies used in research, production, and failure analysis. He is widely respected for his ability to optimize tool design and cutting parameters to meet exacting industry standards—balancing factors such as cut quality, blade life, material integrity, and process consistency.
As an author, Mr. Schneider is known for delivering practical, application-focused insights that translate complex technical challenges into clear, actionable strategies. His articles and technical guides serve as trusted resources for engineers, researchers, and manufacturers seeking to improve precision, reduce process variability, and enhance tool performance in critical applications.
ARE YOU USING RIGHT TOOLS
FOR YOUR APPLICATION?
LET US
HELP YOU
HAVING ISSUES WITH
YOUR CURRENT TOOLS?
Knowledge Center
How to Selecting Right Diamond Tools for your application
How to properly use Diamond Tools
Why use diamond
Diamond vs CBN (cubic boron nitride) Tools
What is Diamond Mesh Size and how to select best one for your application
What is Diamond Concentration and which to use for your application
Diamond Tool Coolants Why, How, When & Where to Use
Choosing The Correct Diamond Bond Type
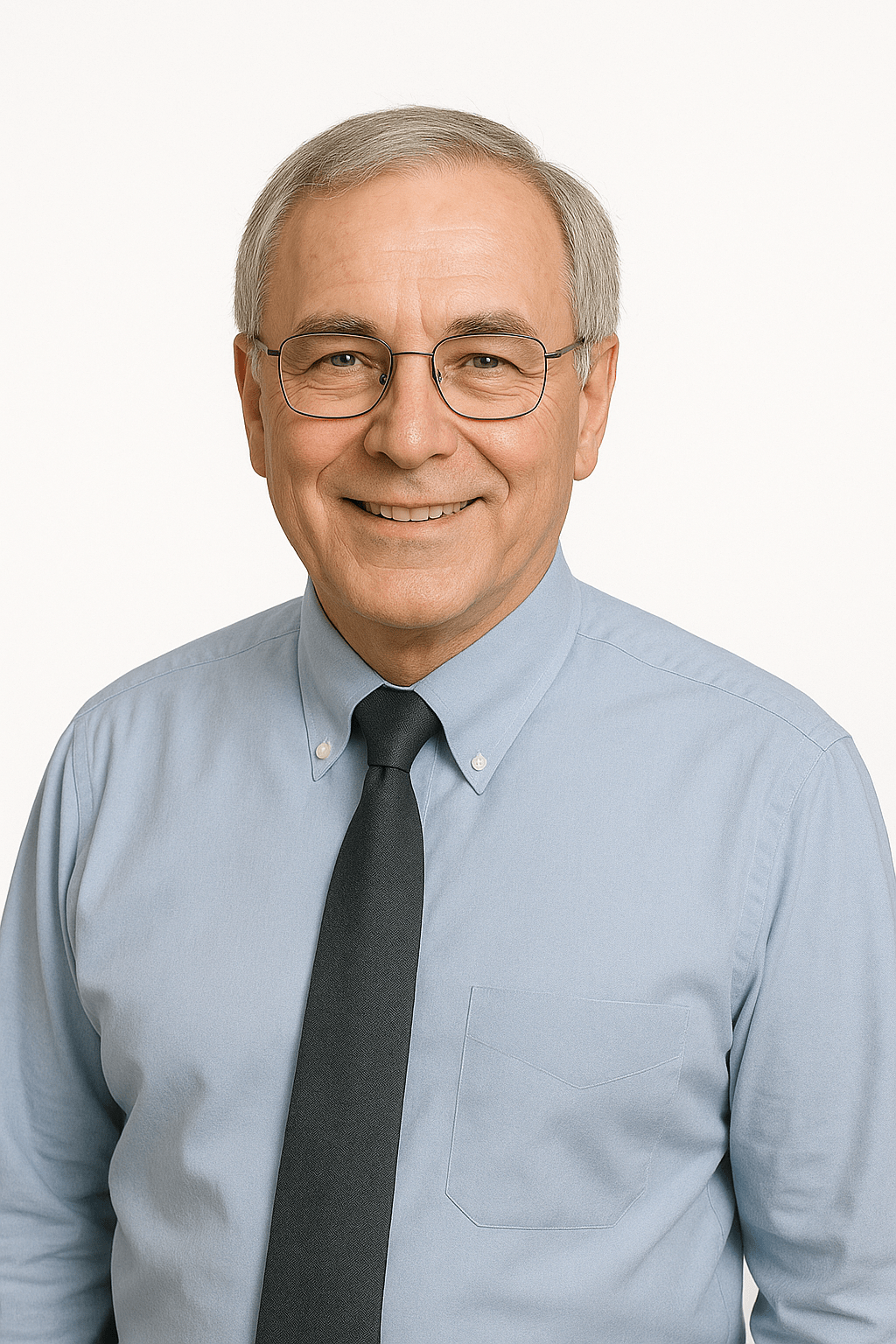
Alexander Schneider is a senior applications engineer and leading authority in the industrial diamond tooling industry, with over 35 years of hands-on experience in the development, application, and optimization of ultra-thin and high-precision diamond blades, diamond core drills, and diamond and CBN grinding wheels. His work spans a wide range of advanced materials including ceramics, glass, composites, semiconductors, and high-performance metals.
Throughout his career, he has collaborated with leading R&D institutions, national laboratories, and high-tech manufacturing companies across Europe, North America, and Asia, providing technical expertise and tailored solutions for demanding cutting and surface preparation applications.
Mr. Schneider has played a pivotal role in advancing precision cutting, sectioning, dicing, and grinding technologies used in research, production, and failure analysis. He is widely respected for his ability to optimize tool design and cutting parameters to meet exacting industry standards—balancing factors such as cut quality, blade life, material integrity, and process consistency.
As an author, Mr. Schneider is known for delivering practical, application-focused insights that translate complex technical challenges into clear, actionable strategies. His articles and technical guides serve as trusted resources for engineers, researchers, and manufacturers seeking to improve precision, reduce process variability, and enhance tool performance in critical applications.