Table of Contents
ToggleWhich to use for your application?
Diamond shape plays a significant role in the effectiveness of polishing solutions, affecting both the polishing rate and the quality of the final finish. Understanding the differences between monocrystalline and polycrystalline diamond shapes can help you choose the best solution for your specific application.
Selecting the appropriate diamond shape depends on several factors:
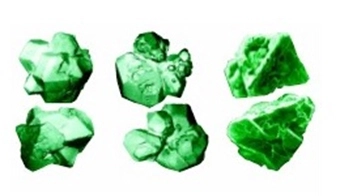
-
Material Type: For harder materials, polycrystalline diamonds are often the best choice due to their aggressive abrasive action. Monocrystalline diamonds work well with softer materials and general-purpose applications.
-
Polishing Rate: If rapid stock removal is required, polycrystalline diamonds are preferable. Monocrystalline diamonds offer a more controlled polishing rate, suitable for smooth finishes.
-
Surface Finish: For a smoother finish, monocrystalline diamonds are generally the better choice. Polycrystalline diamonds are more aggressive, providing faster results but with a rougher finish.
What is Monocrystalline Diamond?
Monocrystalline diamonds consist of a single continuous crystal structure. Because of this, they typically have sharp, blocky edges, giving them effective abrasive properties. The sharpness and uniform structure contribute to their durability, making them suitable for a range of applications, from fine polishing to aggressive grinding.
This distinctive formation gives it unique properties that make it valuable in many industrial and scientific applications. They are also among the hardest known materials, ensuring durability and resilience under intense conditions.
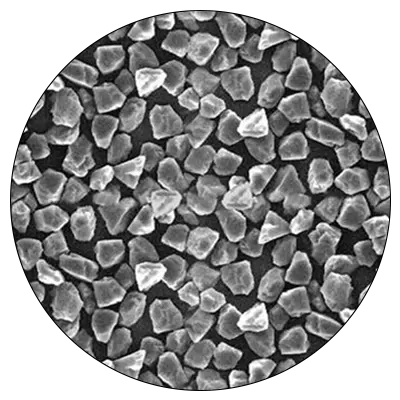
How is What is Monocrystalline Diamond Made?
Monocrystalline diamonds are generally produced using high-pressure, high-temperature (HPHT) methods or chemical vapor deposition (CVD). These processes mimic the natural formation of diamonds in the Earth's crust or create the ideal conditions for diamond growth.
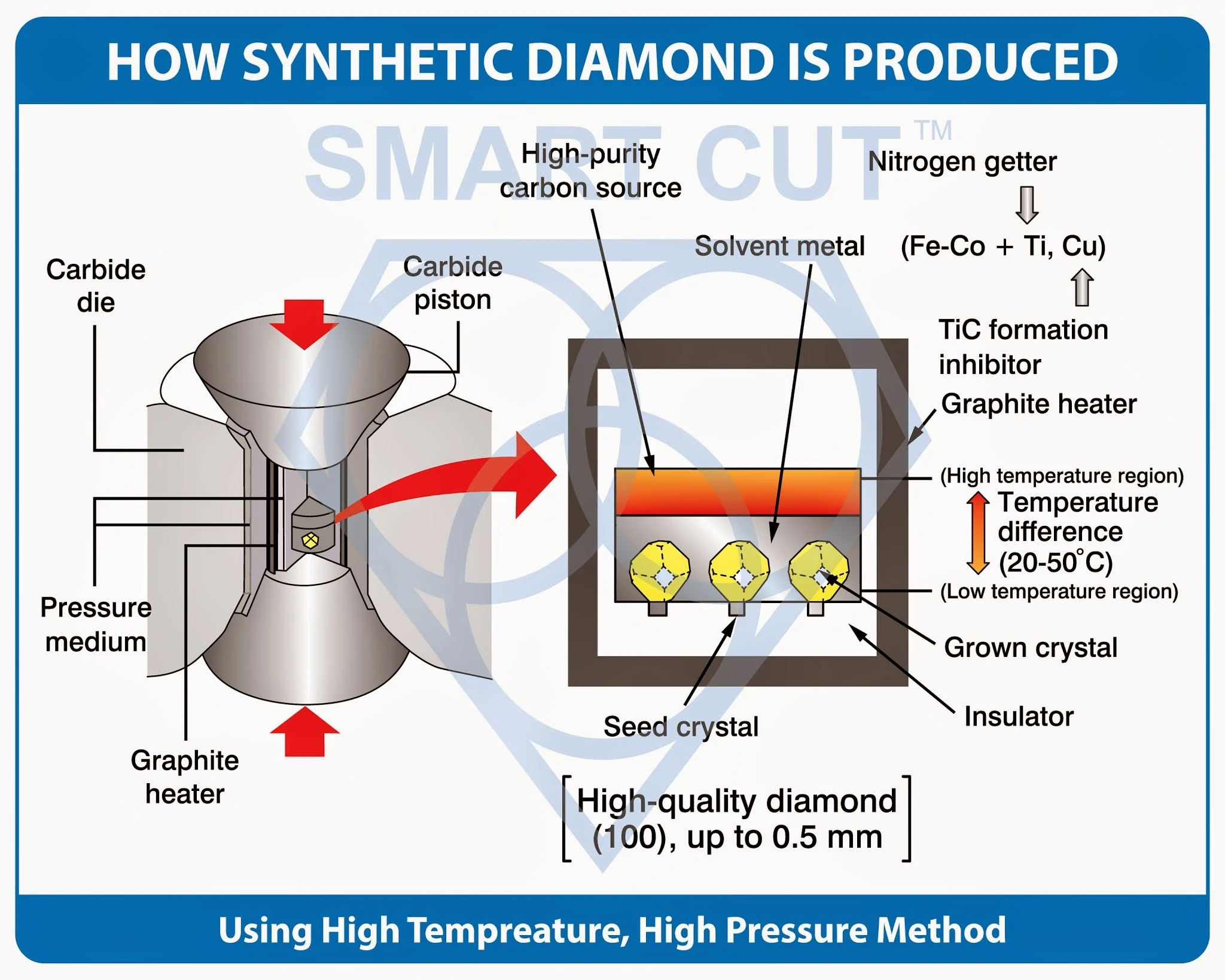
-
HPHT Method: This process involves subjecting carbon to extreme pressure and temperature, encouraging the formation of single-crystal diamond.
-
CVD Method: This method involves creating a plasma of carbon-based gases that deposit onto a substrate, allowing for the growth of single-crystal diamond.
What is the application for Monocrystalline Diamond?
Monocrystalline diamond's unique properties lend themselves to various applications. In the tool industry, these diamonds are ideal for cutting and drilling ultra-hard materials due to their durability and sharp edges. In polishing and grinding, they are valued for their efficiency and consistency, providing reliable results across different materials. The semiconductor industry uses monocrystalline diamonds for their high thermal conductivity and electrical insulating properties. In the optics field, their high clarity and purity make them suitable for lenses and other precision components. Additionally, the jewelry industry values monocrystalline diamonds for their aesthetic appeal.
Despite their many benefits, there are some considerations to keep in mind when using monocrystalline diamond in industrial applications. Assess the specific requirements of your project, including the desired level of abrasiveness, durability, and final surface finish. Proper maintenance and care of equipment are also crucial, as even the most durable materials require upkeep to maintain performance.
Monocrystalline diamonds are characterized by their single-crystal structure, formed from a continuous crystal lattice without any interruptions or joints.
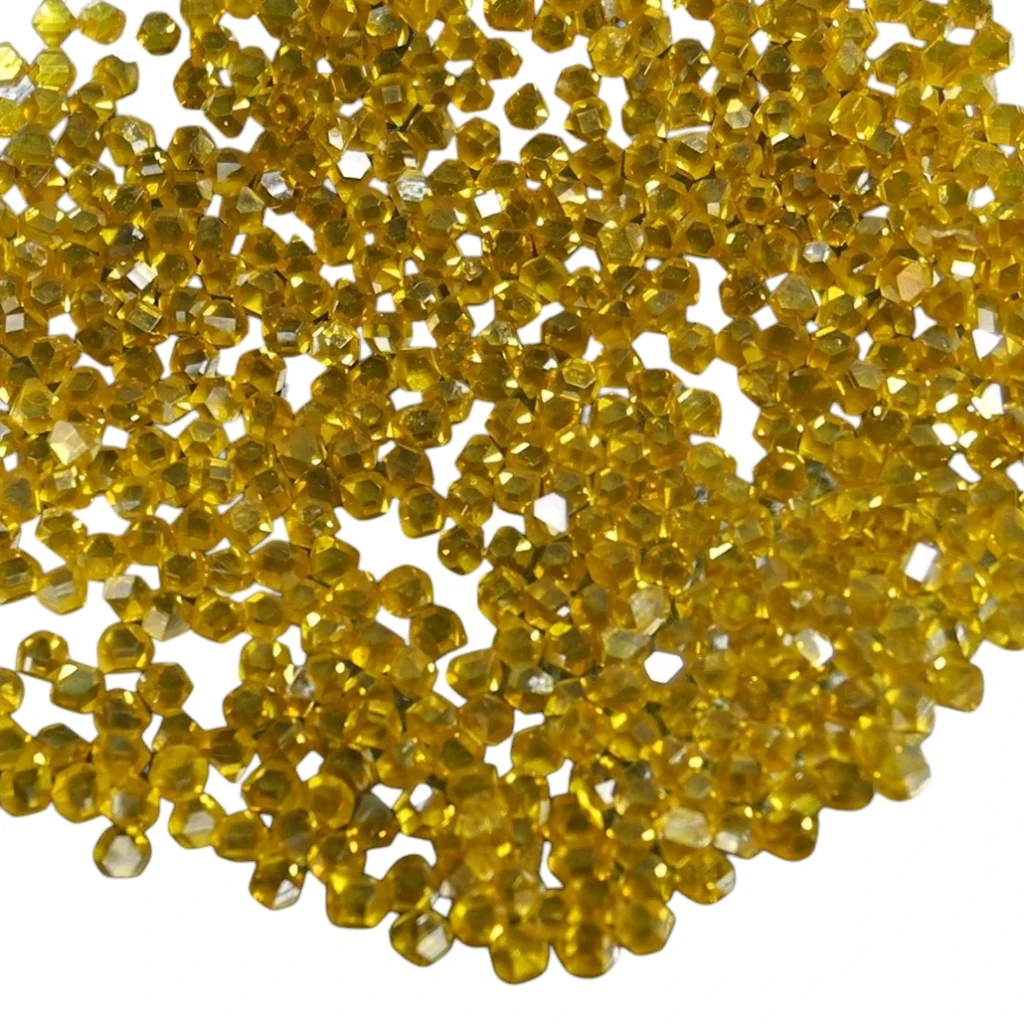
This single-crystal formation sets them apart from polycrystalline diamonds, which are made up of multiple smaller crystals fused together. Because of their singular structure, monocrystalline diamonds have sharp, blocky edges, which contribute to their effectiveness in cutting, grinding, and polishing applications. These sharp edges provide excellent abrasive action, making them ideal for industrial use.
Monocrystalline diamonds are known for their high hardness and durability. As some of the hardest materials on Earth, they can endure intense conditions without significant wear, making them reliable for heavy-duty applications. Their durability ensures that they can be used repeatedly without losing their effectiveness. Additionally, monocrystalline diamonds typically exhibit high clarity and purity due to their continuous crystal structure, which is why they are often chosen for optical applications and precision machining.
The advantages of monocrystalline diamonds are numerous. Their durability is a key benefit, as they can withstand harsh conditions and maintain their abrasive qualities over time. The sharp cutting edges allow for effective material removal, whether it's cutting through hard surfaces or grinding them down to a smooth finish. This effectiveness makes monocrystalline diamonds a popular choice for industrial applications that require reliable performance.
Advantages of Monocrystalline Diamond
Monocrystalline diamond offers several key advantages that make it desirable for industrial and scientific applications:
-
Durability: The robust single-crystal structure of monocrystalline diamonds enables them to endure intense operational conditions with minimal wear.
-
Efficient Cutting: Thanks to their sharp, blocky shape, these diamonds excel in abrasive actions necessary for effective cutting, grinding, and polishing.
-
Cost Efficiency: Generally more economical than their polycrystalline counterparts, monocrystalline diamonds offer a cost-effective solution for various applications.
-
Consistent Performance: The uniformity in their structure guarantees reliable and consistent results across diverse applications.
-
Extended Usage:The durability and hardness of monocrystalline diamonds allow for prolonged operational life without significant degradation.
-
Lower Material Removal Rates: Their structure naturally removes material more slowly, which, while increasing polishing time, results in finer finishes with less surface deformation. This quality is especially beneficial in applications requiring meticulous surface smoothness.
Monocrystalline diamonds are often used in diamond suspensions where consistent performance and cost-effectiveness are important. They are generally more affordable than polycrystalline diamonds due to their simpler structure and manufacturing process. However, their single-crystal nature can mean they are less effective in applications requiring higher rates of material removal or those needing a multi-faceted cutting action.
Applications of Monocrystalline Diamond
Monocrystalline diamond's unique properties make it suitable for a variety of applications, including:
-
Cutting and Drilling Tools: The sharp edges and high hardness of monocrystalline diamonds make them ideal for cutting and drilling applications, especially in ultra-hard materials.
-
Polishing and Grinding: In diamond suspensions, monocrystalline diamonds are valued for their durability and sharpness, providing effective abrasive action for polishing and grinding.
-
Optical Components: Due to their high clarity and purity, monocrystalline diamonds are used in optics, including lenses, prisms, and other precision components.
-
Semiconductor Industry: Monocrystalline diamonds are used in semiconductor manufacturing for their high thermal conductivity and electrical insulating properties.
-
Jewelry and Gemstones: Monocrystalline diamonds are also used in the jewelry industry for their aesthetic appeal and high value.
In terms of cost, monocrystalline diamonds are generally more affordable than their polycrystalline counterparts. This cost-effectiveness makes them a practical option for various industries, from manufacturing to research and development. Their consistent structure contributes to uniform performance, which is crucial in applications where precision and reliability are paramount.
Monocrystalline Diamond Shape
Monocrystalline diamonds are composed of a single continuous crystal structure. This structure gives them sharp, blocky edges, resulting in an effective abrasive action. The distinct shape allows for precise cutting, grinding, and polishing, making monocrystalline diamonds ideal for applications requiring accuracy and a smooth finish.
-
Abrasive Action: The sharp edges of monocrystalline diamonds provide effective cutting and grinding, enabling controlled material removal. This characteristic is particularly useful in applications where a smooth, consistent finish is needed.
-
Durability: The single-crystal structure contributes to the durability of monocrystalline diamonds. Their sharp edges retain their shape over extended use, ensuring consistent performance.
-
Applications: Monocrystalline diamonds are typically used in general-purpose polishing, where a moderate to high level of abrasive action is required. They are suitable for a wide range of materials, including metals, ceramics, and composites.
Characteristics of Monocrystalline Diamond
-
Single-Crystal Structure: Monocrystalline diamonds are formed from a single continuous crystal lattice, distinguishing them from polycrystalline diamonds, which consist of multiple smaller crystals fused together.
-
Sharp Edges: The single-crystal structure leads to sharp, blocky edges, offering effective abrasive action for cutting, grinding, and polishing.
-
High Hardness and Durability: Monocrystalline diamonds are among the hardest materials, ensuring durability and resilience even under intense conditions.
-
Clarity and Purity: Due to their single-crystal nature, monocrystalline diamonds typically have high clarity and purity, making them desirable for optical applications and precision machining.
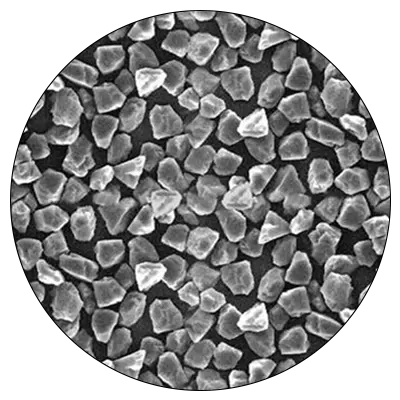
Considerations for Using Monocrystalline Diamond
When selecting monocrystalline diamond for industrial applications, consider the following:
-
Application Requirements: Assess the specific requirements of your application, such as the level of abrasiveness needed, durability, and desired finish.
-
Polishing Techniques: Monocrystalline diamond suspensions work best with specific polishing techniques. Ensure your equipment and methods align with these requirements for optimal results.
-
Maintenance and Wear: While monocrystalline diamonds are durable, proper maintenance and care of polishing equipment are essential to ensure longevity and consistent performance.
-
Monocrystalline diamond serves as a highly effective and budget-friendly abrasive for a variety of applications that require stock removal and polishing. Its slightly irregular shape, with multiple cutting edges, provides efficient abrasive action, allowing for effective material removal without excessive deformation or surface damage. This versatility makes it an excellent choice for a range of general-purpose applications, especially where the unique characteristics of polycrystalline diamond are not necessary.
Durability and Consistency
Monocrystalline diamond's single-crystal structure contributes to its durability, ensuring it can withstand repeated use without significant wear. This consistency in performance is crucial for applications that demand reliable results over time. The sharp edges and blocky shape maintain their effectiveness through multiple uses, providing a stable abrasive action across different materials.
Cost-Effective Performance
One of the key advantages of monocrystalline diamond is its cost-effectiveness. The manufacturing process for monocrystalline diamonds is generally simpler and more affordable compared to polycrystalline, allowing it to be produced at a lower cost. This cost advantage makes monocrystalline diamond an attractive option for industries and projects with budget constraints, enabling high-quality polishing and grinding without excessive expenditure.
Wide Range of Applications
Monocrystalline diamond is suitable for a variety of applications across multiple industries, including manufacturing, metallurgy, and research. Its effectiveness in stock removal and intermediate polishing makes it a popular choice for preparing surfaces for further analysis or finishing. The slightly irregular shape with multiple cutting edges allows for a smooth transition from initial material removal to finer polishing stages.
Ideal for General Applications
Monocrystalline diamond is ideal for general applications where the specific features of polycrystalline diamond are not required. It offers a good balance of performance and cost, providing reliable abrasive action without the additional expense of more specialized abrasives. This makes it an excellent choice for general-purpose polishing, grinding, and other abrasive tasks in various industries.
Limitations and Considerations
While monocrystalline diamond is effective for many applications, it may not be suitable for all scenarios. For example, when dealing with very hard or sintered materials, polycrystalline diamond might be more appropriate due to its higher stock removal rates and consistent surface finish. Monocrystalline diamond, with its slightly irregular shape, may not achieve the same level of performance in such cases.
What is Polycrystalline Diamond?
Polycrystalline diamonds are composed of multiple smaller crystals fused together, creating a multi-faceted structure. This complex arrangement gives them more cutting edges, leading to higher stock removal rates and shorter polishing times. The multi-faceted nature allows for more aggressive abrasion, making them ideal for tough materials like hard metals, ceramics, and composites.
Polycrystalline diamonds are generally used in applications that require rapid material removal, high polishing rates, or resistance to surface deformation. Their unique structure provides versatility and efficiency in challenging environments, where durability and speed are critical.
-
Abrasive Action: The multi-faceted shape of polycrystalline diamonds provides more cutting edges, leading to a higher stock removal rate. This characteristic is ideal for applications where rapid polishing is required.
-
Aggressiveness: The numerous cutting edges in polycrystalline diamonds allow for more aggressive abrasive action, making them suitable for tough materials like hard metals, ceramics, and composites.
-
Applications: Polycrystalline diamonds are often used in high-performance applications, where aggressive stock removal and shorter polishing times are desired. They are suitable for advanced materials, precision engineering, and high-demand applications.
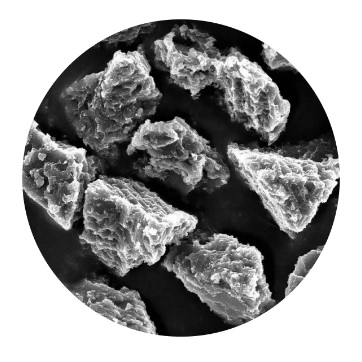
Comparing Monocrystalline and Polycrystalline Diamond Shapes
The choice between monocrystalline and polycrystalline diamond shapes depends on the specific requirements of the polishing or grinding process. Here's a comparison between the two shapes:
-
Stock Removal Rate: Polycrystalline diamonds typically offer a higher stock removal rate due to their multi-faceted structure. Monocrystalline diamonds provide a moderate rate, suitable for general-purpose applications.
-
Surface Finish: Monocrystalline diamonds tend to produce a smoother surface finish due to their sharp, blocky edges. Polycrystalline diamonds can be more aggressive, leading to a rougher finish but with faster results.
-
Durability: Monocrystalline diamonds are generally more durable due to their single-crystal structure. Polycrystalline diamonds, while durable, may wear down faster due to their multiple cutting edges.
Key Attributes of Polycrystalline Diamonds
-
Higher Removal Rates: The multi-faceted structure allows for quicker polishing, reducing the time required to achieve the desired finish.
-
Faster Preparation Times: Polycrystalline formulations are more efficient, leading to shorter polishing cycles and increased productivity.
-
Better Surface Finish: The multiple cutting edges produce less deformation, resulting in a smoother, higher-quality finish.
-
Ideal for High-Performance Applications: Polycrystalline diamonds are suited for demanding applications where speed and quality are critical, such as optics and precision engineering.
Comparison of Monocrystalline and Polycrystalline Diamonds
Monocrystalline and polycrystalline diamonds each offer distinct benefits and are chosen based on specific application requirements. Here's a comparison:
-
Durability: Monocrystalline diamonds are generally more durable, with a single-crystal structure that withstands repeated use. Polycrystalline diamonds, while also durable, might wear down faster due to their multi-faceted composition.
-
Abrasiveness: Polycrystalline diamonds offer more cutting edges, making them more abrasive and effective for aggressive polishing and grinding. Monocrystalline diamonds are effective for general-purpose polishing but might be less aggressive.
-
Cost: Monocrystalline diamonds are typically more cost-effective due to their simpler structure. Polycrystalline diamonds can be more expensive, but their higher efficiency might justify the additional cost.
-
Applications: Monocrystalline diamonds are suitable for general applications with moderate polishing needs. Polycrystalline diamonds excel in high-performance scenarios requiring rapid stock removal and efficient polishing.
Choosing the Right Diamond Shape for your application Table of Comparison
Feature |
Monocrystalline Diamond |
Polycrystalline Diamond |
---|---|---|
Particle Structure |
Single crystal particles |
Multiple crystal particles per grain |
Cutting Action |
Provides uniform, consistent cutting edges |
Self-sharpening, offers fresh cutting edges as particles fracture |
Surface Finish |
Generates very smooth surfaces with consistent scratch patterns |
Capable of both smooth finishes and rapid stock removal depending on particle size |
Material Suitability |
Ideal for softer to medium-hard materials that do not easily fracture diamond particles |
Suitable for very hard materials, including advanced ceramics and composites |
Thermal Stability |
Higher thermal stability due to robust single-crystal structure |
Good thermal management through particle fragmentation |
Chemical Stability |
Generally high, but depends on the purity and manufacturing process |
Excellent, often enhanced by the toughness and varied crystal orientations |
Cost |
Generally less expensive, offering a cost-effective solution for high wear conditions |
Typically more expensive due to higher production costs of uniform, single crystals |
Application Examples |
Used in precision engineering, optics polishing, fine-finish metallography |
Used in high-stress environments such as machining hard composites, aggressive material removal |
Advantages |
Superior for achieving high-quality finishes, maintains edge integrity under less severe conditions |
Superior for achieving high-quality finishes, maintains edge integrity under less severe conditions |
Disadvantages |
Higher cost, less effective for rapid stock removal or very hard materials |
May produce less consistent surface finishes due to particle fracturing |
Durability |
Tends to wear down more slowly due to the strength of the single crystals |
Higher rate of particle breakdown can be beneficial for maintaining aggressive cutting action |
Particle Fracture |
Lower tendency to fracture, maintains a consistent cutting surface longer |
Higher tendency to fracture, but this creates new sharp edges for effective material removal |
Consistency of Results |
Consistently smooth finish ideal for applications requiring high precision |
Variability in scratch patterns, suitable for applications where finish is less critical |
Economic Efficiency |
Higher upfront costs but can be offset by longer lifespan and less frequent need for replacement |
Lower initial cost, efficient for large volume applications due to frequent renewing of edges |
Environmental Impact |
Manufacturing process is less intensive in terms of energy and waste production |
Manufacturing can be more resource-intensive, but modern techniques are improving sustainability |
Ease of Use |
May require more skilled operation to achieve best results due to uniform particle size |
Generally easier to achieve effective results quickly, less sensitive to operational variations |
Selectivity |
More selective in application, not universally ideal across all materials |
Broad applicability, capable of handling diverse materials with effectiveness |
Customization |
Often tailored for specific industries and applications |
Wide range of off-the-shelf products suitable for various needs |
Choosing Between Monocrystalline and Polycrystalline
When deciding between monocrystalline and polycrystalline diamond suspensions, several crucial factors should be considered to ensure you select the right type for your specific needs. These factors include the rate of polishing, cost implications, the desired surface finish, and the material properties of the workpiece. Here's an expanded view of each factor to aid in making an informed decision:
Polishing Rate:
-
Polycrystalline diamonds are designed for environments where rapid material removal is necessary. They are highly effective in quickly reducing material due to their multi-crystalline structure, which offers multiple cutting points.
-
Monocrystalline diamonds, on the other hand, are better suited for slower, more controlled material removal. This makes them ideal for applications where precision is more critical than speed.
Cost:
-
Monocrystalline diamonds tend to be more cost-effective, making them an attractive option for operations that are sensitive to budget constraints. Their simpler production process compared to polycrystalline diamonds contributes to their lower cost.
-
Polycrystalline diamonds may come at a higher initial cost but can offer better long-term value in terms of durability and efficiency, especially in tough, abrasive applications.
Surface Finish:
-
Polycrystalline diamonds are known for their ability to achieve a smoother finish with minimal surface deformation. Their irregular particle shapes and multiple cutting edges uniformly wear down the surface, leading to a finer finish.
-
Monocrystalline diamonds provide a less aggressive polishing action, which is still highly effective for achieving a high-quality polished surface but may not reduce surface roughness as quickly as polycrystalline diamonds.
Application Type:
-
For ceramics and similar brittle materials, monocrystalline diamonds are often preferred due to their predictable behavior and less aggressive material removal, which helps prevent substrate damage.
-
For metals, composites, and advanced materials, polycrystalline diamonds are typically chosen. Their robust structure and ability to present fresh cutting surfaces make them more effective for handling tough materials and complex, demanding applications.
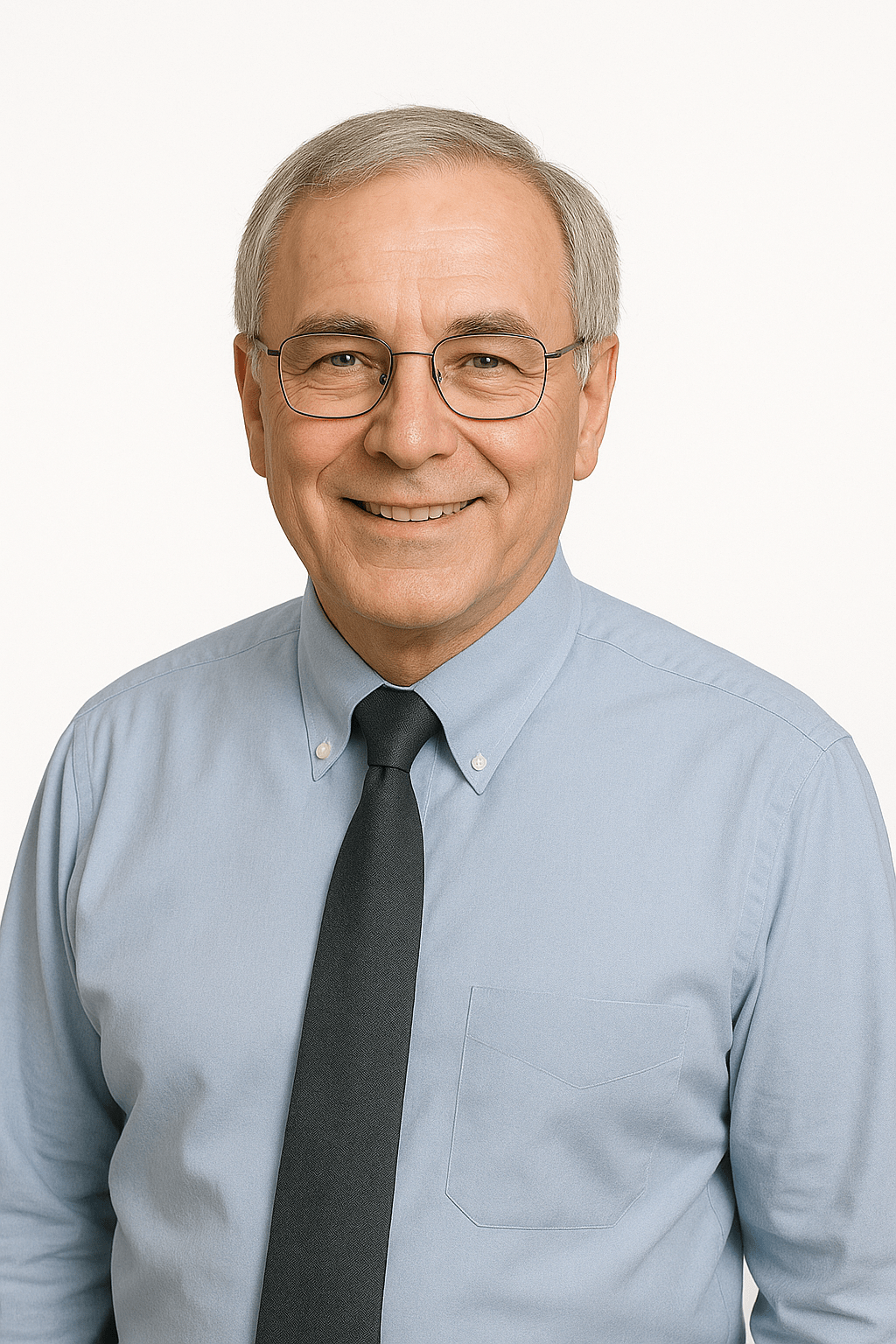
Alexander Schneider is a senior applications engineer and leading authority in the industrial diamond tooling industry, with over 35 years of hands-on experience in the development, application, and optimization of ultra-thin and high-precision diamond blades, diamond core drills, and diamond and CBN grinding wheels. His work spans a wide range of advanced materials including ceramics, glass, composites, semiconductors, and high-performance metals.
Throughout his career, he has collaborated with leading R&D institutions, national laboratories, and high-tech manufacturing companies across Europe, North America, and Asia, providing technical expertise and tailored solutions for demanding cutting and surface preparation applications.
Mr. Schneider has played a pivotal role in advancing precision cutting, sectioning, dicing, and grinding technologies used in research, production, and failure analysis. He is widely respected for his ability to optimize tool design and cutting parameters to meet exacting industry standards—balancing factors such as cut quality, blade life, material integrity, and process consistency.
As an author, Mr. Schneider is known for delivering practical, application-focused insights that translate complex technical challenges into clear, actionable strategies. His articles and technical guides serve as trusted resources for engineers, researchers, and manufacturers seeking to improve precision, reduce process variability, and enhance tool performance in critical applications.
ARE YOU USING RIGHT TOOLS
FOR YOUR APPLICATION?
LET US
HELP YOU
HAVING ISSUES WITH
YOUR CURRENT TOOLS?
Knowledge Center
How to Selecting Right Diamond Tools for your application
How to properly use Diamond Tools
Why use diamond
Diamond vs CBN (cubic boron nitride) Tools
What is Diamond Mesh Size and how to select best one for your application
What is Diamond Concentration and which to use for your application
Diamond Tool Coolants Why, How, When & Where to Use
Choosing The Correct Diamond Bond Type
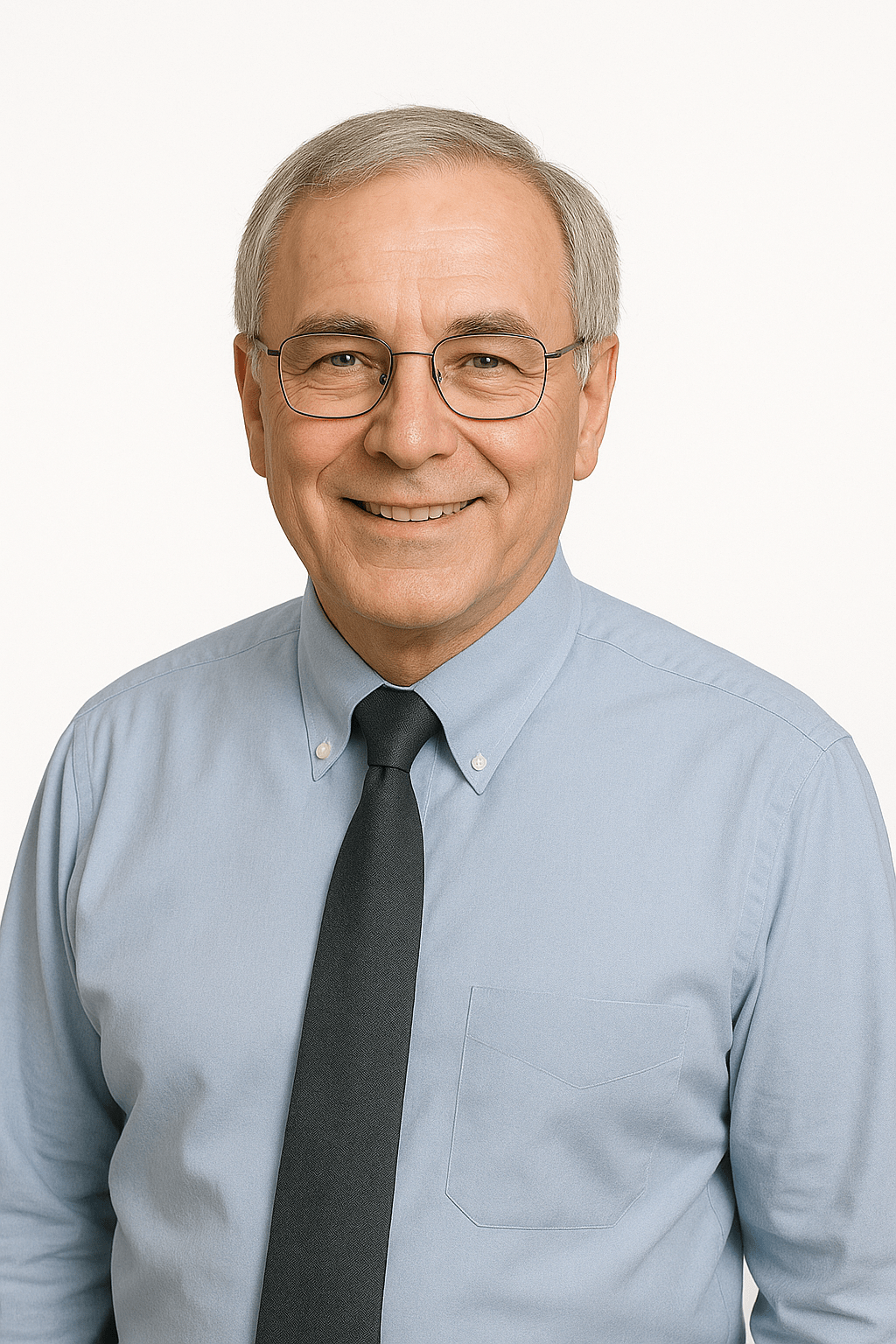
Alexander Schneider is a senior applications engineer and leading authority in the industrial diamond tooling industry, with over 35 years of hands-on experience in the development, application, and optimization of ultra-thin and high-precision diamond blades, diamond core drills, and diamond and CBN grinding wheels. His work spans a wide range of advanced materials including ceramics, glass, composites, semiconductors, and high-performance metals.
Throughout his career, he has collaborated with leading R&D institutions, national laboratories, and high-tech manufacturing companies across Europe, North America, and Asia, providing technical expertise and tailored solutions for demanding cutting and surface preparation applications.
Mr. Schneider has played a pivotal role in advancing precision cutting, sectioning, dicing, and grinding technologies used in research, production, and failure analysis. He is widely respected for his ability to optimize tool design and cutting parameters to meet exacting industry standards—balancing factors such as cut quality, blade life, material integrity, and process consistency.
As an author, Mr. Schneider is known for delivering practical, application-focused insights that translate complex technical challenges into clear, actionable strategies. His articles and technical guides serve as trusted resources for engineers, researchers, and manufacturers seeking to improve precision, reduce process variability, and enhance tool performance in critical applications.