Learn important diamond drill methodology. understand diamond drill specifications and their differences Selecting the right Diamond Drills/Bits for your application is key to obtaining desired diamond drilling results. Using the Right Diamond Drill will help you Save Time & Money. As well as avoid an unnecessary trial & error process.
Selecting the Right Diamond Drill / Bit for your application
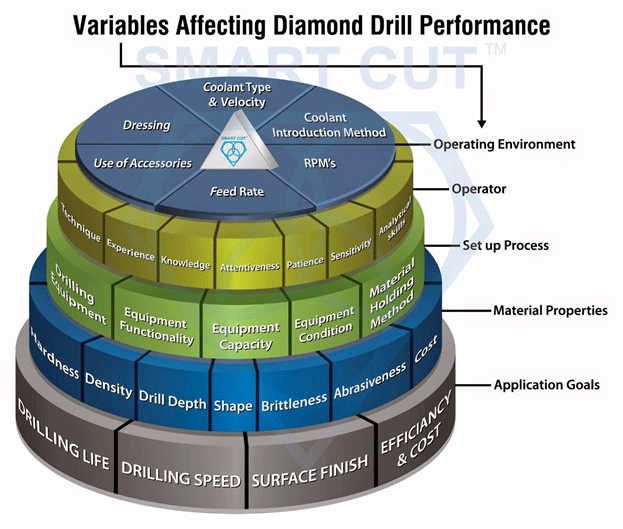
Selecting the right Diamond Drills/Bits for your application is key to obtaining desired diamond drilling results. Using the Right Diamond Drill will help you Save Time & Money. As well as avoid an unnecessary trial & error process. The article below was designed for diamond drill/bit users of all skill and experience levels. Ranging from beginner (novice) to experienced manufacturing engineer, researcher, contractor or hobby enthusiast. The following are some factors to consider when selecting the right diamond drill for your application.
Today's growing variety and ever changing materials, Manufacturers, R & D facilities, hobbyists and everyone else involved in diamond drilling encounter wide variety of applications and challenges. The ever increasing variety of advanced, new generation, ultra hard, composite, micro, and exotic materials transform the way we look at diamond drilling. And set many age old diamond drills/bits and drilling methods obsolete. New materials require different technology and methods.
And although, today's market place offers the Manufacturing Engineer, R & D Scientist, Hobby Enthusiast, Contractor and Home Owner hundreds of choices of diamond drills/bits, accessories, and equipment. It offers little advice on how the user can implement these tools to accomplish their specific objectives. Many users still spend days and even weeks, trying different diamond drills/bits, and experimenting with different types of drilling equipment. An expensive and time consuming trial and error process, which can be avoided with proper understanding of your material and objectives you need to accomplish. Proper preparation, attention to detail, and following basic diamond drilling technique can make the difference in the success of your diamond drilling operation.
Material to Be Drilled
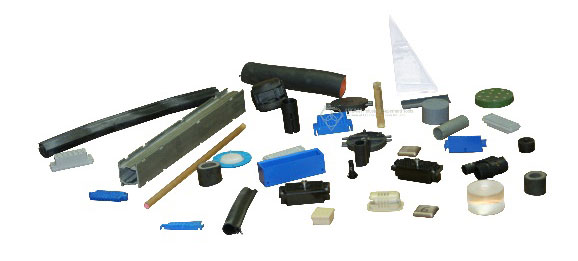
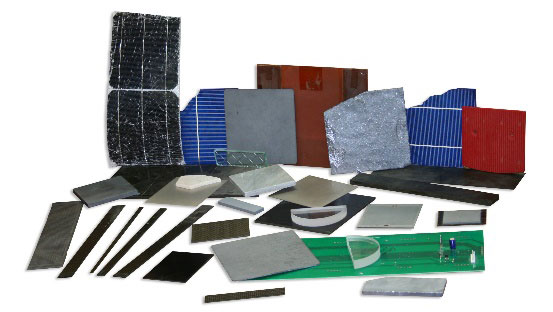
a.) Hardness of Material – Materials you are planning to drill will have a large impact in the types of diamond drills, equipment, and accessories you will be able to use. If you are drilling ultra hard materials such as sapphire, alumina, other types of advanced ceramics, high metallic content materials, precious and natural stone. It is generally recommended that you use a sintered (metal bonded) diamond drill. However, if you are drilling softer and less expensive materials such as glass, composites, soft stone and tile, an electroplated (nickel bonded) diamond drill may be a better and more cost effective solution. As a rule of thumb harder materials require softer bond, to drill faster and freer. While softer and abrasive materials require a harder bond, to last longer. Material Hardness is defined as the materials capability to resist deformation. All materials are classified by their scale of hardness. Material hardness is measured by many different hardness scales such as Mohs, Vickers, Knoop and other scales of hardness. Further information on determining and understanding hardness of your material is available in this article below.
b.) How expensive is your material - Material cost will play an important role in selection of the right diamond drill/bit for your application. if the material you are planning to drill is precious, valuable, or expensive. Diamond drill/bit cost will play a minor role in your drilling operation. It is suggested that you obtain a thin wall diamond core drill to minimize material loss and deformation. It’s always a good idea to have some type of an estimate of target cost and quality per hole.
c.) Material Thickness (maximum drilling depth) – The thicker the material you are planning to drill, the greater amount of coolant and pressure is required. Applications requiring you to drill over 1" (25.4mm) should be tread in a different way. We recommend running coolants from multiple directions. Through drill center, from side of drill, as well as drilling submerged in coolant. This will insure maximum amount of coolant and lubrication reaching your drilling zone. Running high pressure of coolant through center of your diamond drill/bit by using a water swivel adapter is highly recommended for drilling material over 1" (25.4mm) Thick. Longer Drilling depths may require drilling in several steps and using more than one diamond core drill / diamond drill bit.
d.) Material Geometry & Density - Each material has different density, hardness, composition. For this reason a diamond drills/bits and techniques that may work on one material, may not work on another material. To obtain optimum drilling results, each diamond drill should be ideally made to factor in the unique differences and properties of each material. Shape, Size, Diameter, Hardness, and Brittleness of your material will affect not only your diamond drill/bit selection, but your choice clamping methods (holding your material in place), drilling equipment, speeds & feeds you can use.
Equipment to be used
The equipment you will be using and its physical condition, will dictate the speeds (RPM’s), feeds, and coolants you can use along with your diamond drills/bits. Hence, somewhat limiting your diamond drill selection. No matter what diamond drill you use or how well its made, it will not provide the performance you are looking for, if you don’t use the right drilling equipment for your application. Diamond drills are usually used on the following equipment:
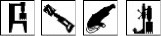
-
Drill Press
-
Angle Grinder/Hand Held Grinder
-
Cordless Drill / Hand Held Drill
-
CNC / Milling Machine
-
High Speed Air Spindle
-
Many Other Types of Equipment
Drill presses, milling machines, or CNC machines are used in most industrial manufacturing applications. R & D facilities also tend to utilize the same equipment. Hobby Enthusiasts, Contractors, and Home Owners most often use hand held Drills, followed by drill presses, drilling rigs, and angle grinders. Proper drilling equipment for your diamond drilling application is discussed in further detail in this article below.
Application / Number of Holes to be Drilled
Your diamond drill requirements will greatly vary with your application & frequency of use and diamond drill/bit intended application. Diamond Drills, Diamond Core Drills, Diamond Drill Bits, Diamond Bits (usually mean same thing) are generally used for:

a.) Industry / Production - Diamond Drills/Bits are used everyday in thousands industries & operations to manufacture products yield (output per cost) from their diamond drills/bits. What is common about these applications is the Diamond Drill/Bit will be used every day or several times a day, drilling several thousand holes/cores or until the drill is warn out and replaced. Metal Bond (Sintered) diamond drills are usually recommended for this type of heavy duty use. However, if you have a very fine or specific finish requirement and do not polish material after drilling. HYBRID Bond diamond drill or even Multi-Layered Electroplated Diamond Core Drills used with water swivel adapter to run high pressure of coolant through center of your diamond drill/bit may be the best solution for your application. No matter what stage your manufacturing operation, UKAM Industrial Superhard Tools has the Experience & Solutions to help you resolve even the most complex manufacturing challenges. Discover why thousands of manufacturing around the world turn to UKAM Industrial Superhard Tools to optimize their diamond drilling & machining operation to ultimate level of efficiency. that play an important role in our everyday lives. Ranging from advanced/technical ceramic parts machining, composite aerospace applications, optical lenses machining, stone countertop fabrication and much more. Diamond Drill & technical requirements are diverse as the manufacturing operations that use them. Typically manufacturing engineers & machinists demand a high level of consistency, accuracy,
b.) Research & Development - Diamond Drill requirements in Research are diverse as fields and researchers that used them. Whether is drilling a hole or obtaining core sample. Most researchers & application engineers are primarily concerned about preserving material true micro structure and introducing least amount of damage & deformation possible to material being worked on. Research Applications range from materials sciences, advanced materials, advanced/technical ceramics, optics, metallography, geology, composites to new and breakthrough fields such as MEMS, Biotechnology and Nano Technology. Typical Research diamond drill/bit users include Universities, Government or Commercial Laboratories, Military Research Facilities, Space & Science Organizations, as well as R & D departments of large organizations. UKAM Industrial Superhard Tools understands the challenges faced by faced by R & D Organizations and has developed diamond drills/bits, accessories, and TOTAL SOLUTIONS to address most common R & D applications. We are constantly engaged in R & D and process development ourselves to keep up with increasing demands of the complex / advanced material world / community.
c.) Hobby / Craft – Diamond Drills/Diamond Drill Bits are used for thousands of diverse type of art & craft applications. Materials frequently range from river rocks, all types of glass, jewelry, beads, lapidary (semi precious & precious stones). What is common about many of these applications is that the diamond drill will be used occasionally for a specific job and than stored for later use. If you are planning to make less than a 100 holes, we recommend you use an electroplated (nickel bonded) diamond drill. Electroplated diamond drills are recommended for beginning (novice) users, because they are usually more forgiving to operator error & mistakes. However, if you are planning to use the drill a number of times through the year. Sintered (metal bonded) diamond drill is a better overall solution and investment. Whether you are just starting out or are an experienced/accomplished crafts person, UKAM Industrial Superhard Tools has the solution to optimize your diamond drilling operation and help you reach the next level. Save money, time, and frustration. By using the right diamond drill/bit for your application the first time. Discover why the leading artisans commissioned by well known organizations such as Faberge, Courtie, Antique Restoration Houses, well known glass & stained glass artists, and jewelry manufacturers use & prefer diamond drills/bits manufactured by UKAM Industrial Superhard Tools.
Diamond drills for contractor applications
User Goals / Objectives
a.) Drill Hole in Material
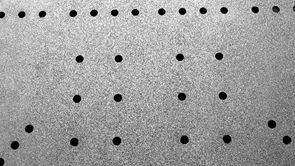
most drilling application involve drilling holes in variety of materials. In this case a hole is the end product. And obtaining an even, round hole is the desired result. The users focus should be on (OD) Outside Diameter of the drill. Either a hallow Diamond Core Drill or Diamond Solid Drill (without hole) can be used for this application. Faster drilling speeds and more efficient drilling results will be obtained with a so called Hallow Diamond Core Drill. Diamond Sold Drills are primarily used for drilling smaller size holes from .001" to 3/8". Hollow Diamond Core Drills are used for drilling larger size holes.
b.) Obtain Core (Material Plug)
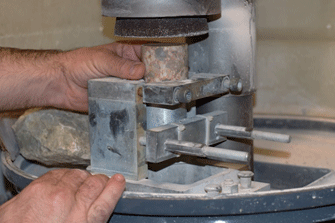
for some diamond drill users, obtaining the material core (center plug) that becomes stuck inside the core drill is the desired result. In this case the material core (plug) is the end product, not the hole itself. A core can only be obtained using so call "hallow diamond core drill". The diamond drills (ID) Inside Diameter becomes a critical dimension (parameter). We often manufacture diamond core drills, specifically to fit each individual customers requirements and tolerances. Please, specify that you need to obtain the Core when ordering diamond drills. Inside Diameters (ID) for most of our standard stock drills are listed in our web site.
Ejecting the center core from center of diamond core drill becomes an important factor. Core can be manually removed from core drill through center of drill or slots provided on body of diamond drill. The most efficient way of removing core from center of drill, is using high pressure of coolant from water swivel adapter. Just increase pressure of coolant, every time core becomes stuck inside your drill. This is the fastest, easiest, and most efficient method for removing material center core.
Technical Requirements/Specifications
d.) Chipping/Finish Requirements – Diamond Mesh Size (grit size) of your diamond core drill/drill bit will play a major role in determining the surface finish quality, smoothness, level of chipping, and material microstructure damage/deformation you will obtain. if you have an application where surface finish and chipping is a critical factor, a sintered (metal bond) diamond drill with a very fine diamond grit may be the best solution. Using Multi-Layered Electroplated Diamond Core Drills in combination with water swivel adapter to run high pressure of coolant through center of your diamond drill/bit. And synthetic water soluble coolant will help you obtain the best surface finish quality possible. More detailed explanation of diamond mesh size in correlation to surface finish quality is presented in this article below.
e.) Tolerances – if you are using diamond drills to drill holes in a product that requires on specific tolerances, you will need a custom diamond drill specifically designed for your application. Tolerance may be specified on OD, ID, run out and concentricity of the diamond drill.
f.) Material Cost – if the material you are drilling drill precious, valuable, or expensive. The diamond drill cost will play a minor role in your drilling operation. It is suggested that you obtain a thin wall diamond core drill to minimize material loss and deformation. It’s always a good idea to have some type of an estimate of target cost and quality per hole.
Coolant to be used


Your capability to use coolant while drill, will seriously effect your diamond drill selection. Most diamond core drills must be used with coolant. Typical coolants used with diamond drills/bits include regular city water, synthetic water soluble coolant, & mineral oil. Shorter drill life, material and drill deformation will result when using drills dry. Electroplated (nickel bonded) diamond core drills may be used dry (without water) depending on the application (material being drilled). UKAM Industrial Superhard Tools does have the capability to manufactured diamond drills to be used without coolant. However, using diamond drills dry is not recommended on most applications. When chance prevails, use all diamond drills with coolant. If use of coolant with your diamond drill/bit is not possible for fear of contamination or any other reasons, consider using compressed air as form of coolant. Although it will not substitute coolants described above, it will be better than drilling dry.
Diamond Drill Variables
Bond Hardness – Ability of the bond matrix to hold diamonds. As the hardness of the bond is increased, its diamond retention capabilities increase as well. However the trade off is slower drilling speed. Life of the diamond drill is usually increased with hardness of its bond matrix. Bonds are designated on their scale of hardness from Soft, Medium, and Hard. There are dozens of variations and classification schemes based on bond degree of hardness or softness. Using diamond drills with optimum bond hardness for your application is important to successful drilling operation. Bond matrix that is too soft for the material being drilled will release diamond particles faster than needed, resulting in faster wear and shorter diamond drill life. On other hand bond matrix that is too hard will result in much slower drilling speeds and require constant dressing to expose the next diamond layer. As rule of thumb, harder materials such as sapphire and alumina (Al203) generally require a softer bond. Whereas softer and more brittle materials require a harder bond.
EXAMPLE OF DIAMOND CORE DRILL BONDS & THEIR APPLICATIONS FOR SINTERED (METAL BOND) DRILLS
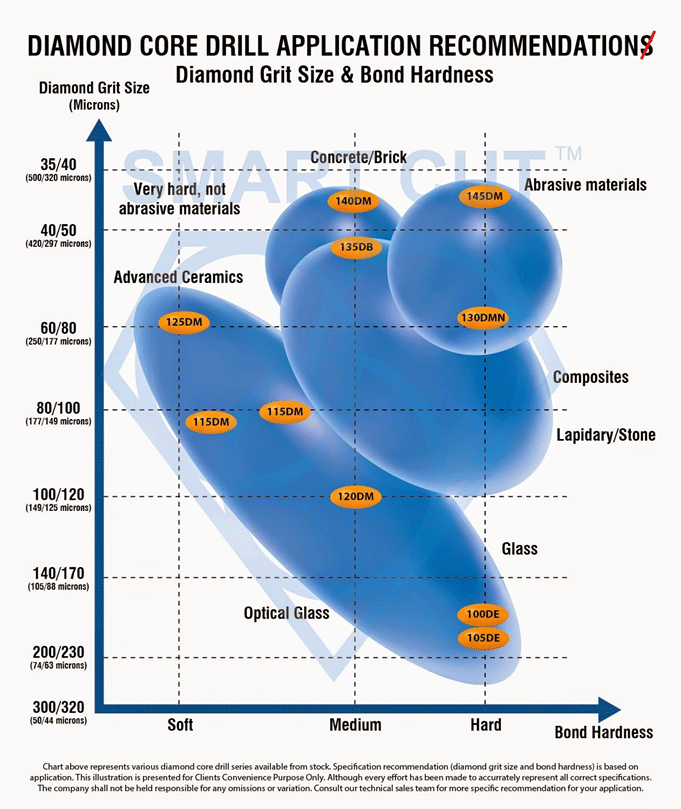
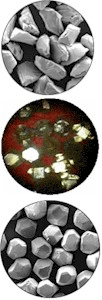
Diamond Grit Size (Mesh Size) – grit size (mesh size) is generally selected depending on the speed you wish to operate the drill and surface finish of your material. The size of the diamond crystals, commonly referred to as mesh size, determines the number of diamond cutting points exposed on the surface of a diamond drill. Diamond Mesh/Grit Size is similar to various grit sizes found on sand paper, which usually comes in coarse, medium, find, & super fine grits. According to U.S. Standards, mesh designates the approximate number of sieve meshes per inch. High Mesh Sizes mean fine grits, and low numbers indicate coarse grits. Diamond Mesh Size plays a major role in determining the surface finish quality, smoothness, level of chipping, and material microstructure damage/deformation you will obtain.
Finer mesh size diamonds such as 220 and 320 grit are much smaller in size than coarser diamond particles. And will give you a very smooth surface finish, with minimal amount of chipping on edges. These mesh sizes are usually used for drilling advanced and optical materials such as: LiNbO3, YVO4, GaAs, and optical materials.
Courser diamond particles such as 80 and 100 grit are much larger in diameter and are frequently used fast drilling / material removal on more harder materials such as granite, sapphire, stone, silicon carbide, zirconia, Al2O3, stainless steels, and other advanced ceramics and materials with high metallic content. Which usually do not require a very fine surface finish.
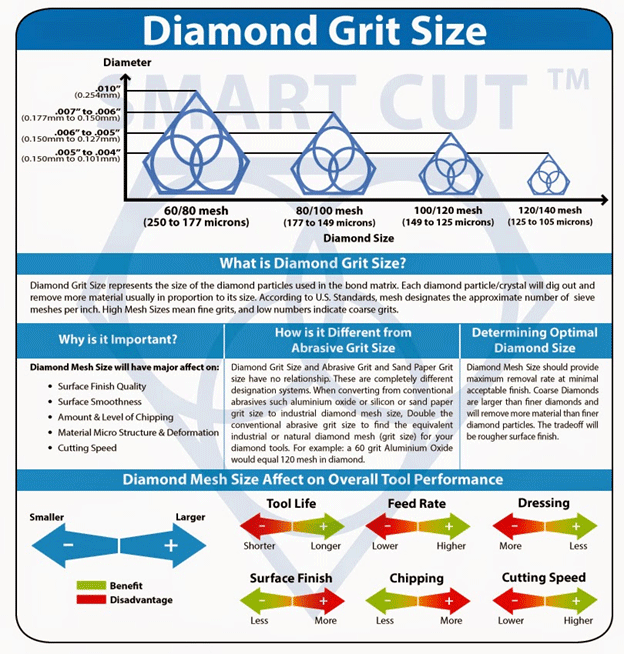
The diamond mesh size in a cutting tool also directly relates to the number of crystals per carat and the free cutting capability of the diamond tool. The smaller the mesh size, the larger the diamond crystals, while larger mesh size means smaller diamond. A 30/40 Mesh blocky diamond has about 660 crystals per carat, while a 40/50 Mesh diamond will have 1,700 crystals per carat. Specifying the proper mesh size is the job of the diamond drill manufacturer. Producing the right number of cutting points can maximize the life of the tool and minimize the machine power requirements. As an example, a diamond tool manufacturer may choose to use a finer mesh size to increase the number of cutting crystals on a low concentration tool, which improves tool life and power requirements.
Diamond Mesh size does have considerable effect on drilling speed. Coarse Diamonds are larger than finer diamonds and will remove more material than finer diamond particles. This means that coarse diamond drills are more aggressive for material removal than the finer diamond drills and will drill faster. However, the tradeoff is increase in material micro structure damage. If you are drilling fragile, more delicate materials then finer mesh size diamond drills are recommended. Diamond mesh size (grit size) should provide maximum removal rate at minimal acceptable finish. Often the desired finish (hole/core quality) cannot be achieved in a single step/operation. Lapping or polishing may be necessary to produce desired surface finish, as a secondary step in your diamond drilling operation / process.
Understanding Diamond Drill/Bit Mesh/Grit Size & Surface Finish Quality
When converting from conventional abrasives such aluminum oxide or silicon or sand paper grit size to industrial diamond mesh size, double the conventional abrasive grit size to find the equivalent industrial or natural diamond mesh (grit size) for your diamond drills/bits. For example: a 60 grit Aluminum Oxide would equal 120 grit in diamond.
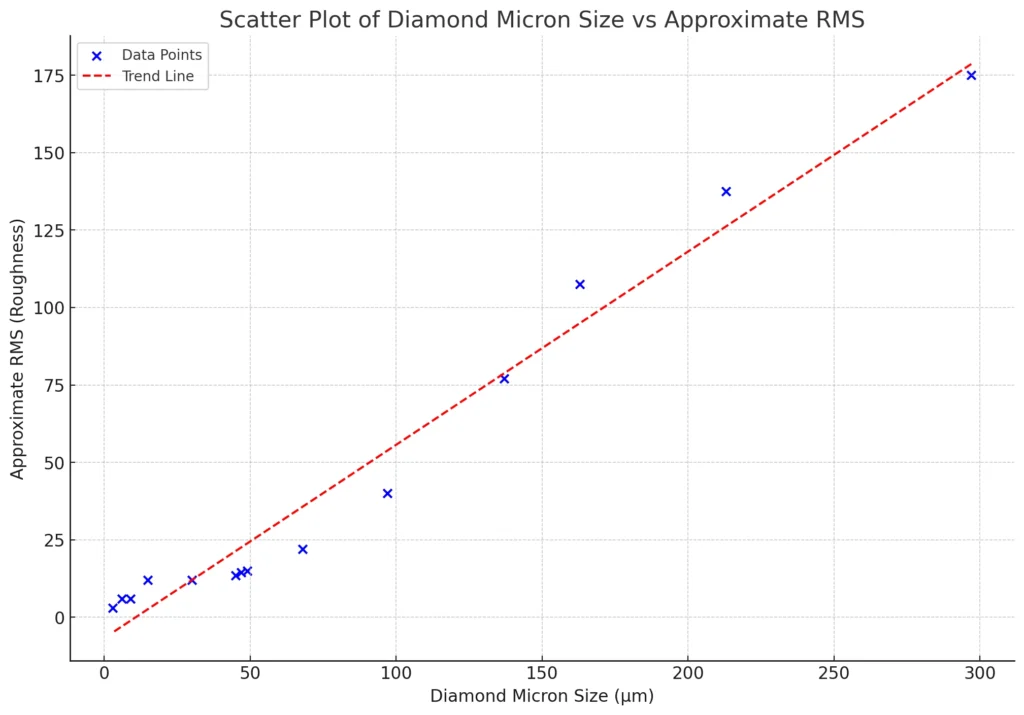
scatter plot of diamond micron size versus approximate RMS values, with a red trend line indicating the overall relationship between these two variables. The scatter plot helps visualize the correlation, suggesting that as the diamond micron size decreases, there tends to be an improvement in the surface finish quality (lower RMS values).
Diamond Definition |
Diamond Mesh/Grit Size |
Diamond Micron Size |
Recommended Application |
Approximate RMS |
---|---|---|---|---|
Saw Grit |
40/60 |
297 |
Sawing |
125-200 |
Super Course |
60/80 |
213 |
Roughing (Heavy Stock Removal) |
125-150 |
Large Course |
80/100 |
163 |
Medium Roughing (General Drilling) |
90-125 |
Course |
100/120 |
137 |
Semi Roughing (Semifinish Drilling) |
64-90 |
Medium |
140/170 |
97 |
Rough Finishing (Finish Drilling) |
32-48 |
Fine |
200/230 |
68 |
Finishing |
20-24 |
Extra Fine |
270/325 |
49 |
Fine finishing |
14-16 |
Super Fine |
325/400 |
47 |
Extra finishing |
14-15 |
45 Microns* |
400/500 |
45 |
Super finishing |
13-14 |
30 Microns* |
500/600 |
30 |
Polishing |
12 |
15 Microns* |
800/1200 |
15 |
Polishing |
12 |
9 Microns* 8/10 6/12 |
1,800 |
9 |
Polishing |
|
6 Microns* 4/8 |
3,000 |
6 |
Fine polishing |
|
3 Microns* |
8,000 |
3 |
Extra polishing |
Diamond Concentration - The proportion, and distribution of diamond abrasive particles, also known as concentration. Has an effect on overall drilling performance and price of your diamond drill. Diamond concentration, commonly referred to as CON, is a measure of the amount of diamond contained in a
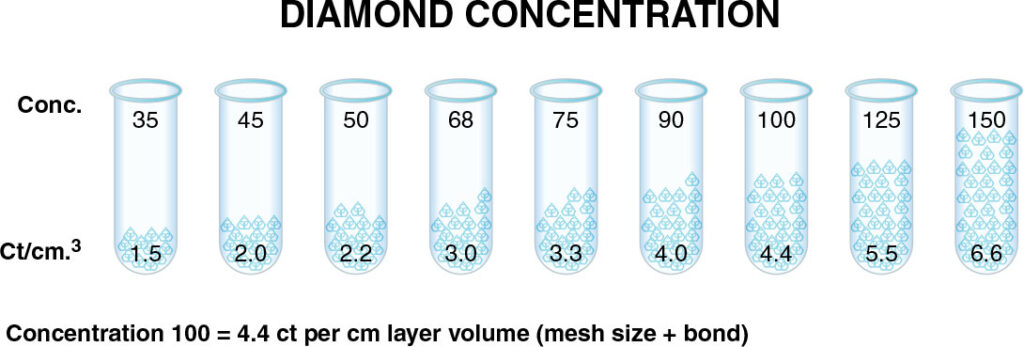
The bond, defined as: Concentration 100 = 4.4 ct per cm layer volume (mesh size + bond). Based on this definition a concentration of 100 means that the diamond proportion is 25% by volume of diamond layer, assuming at diamond density is 3.52 g/cm3 and 1 ct = 0.2g.

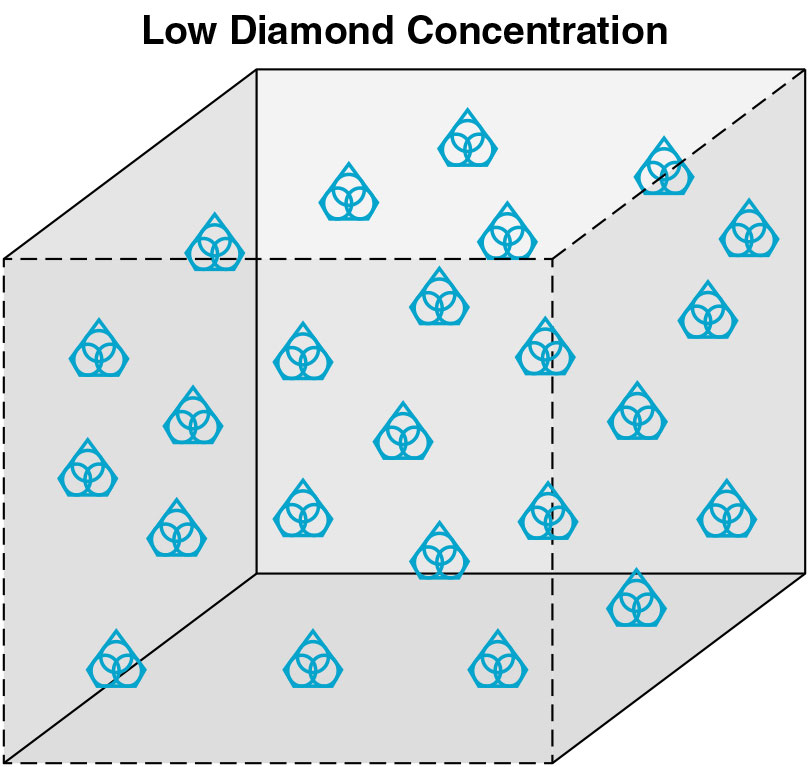
Nominal diamond concentration in precision diamond drills range from 0.5 ct/cm3 to 6 ct/cm3. This means diamond concentrations are available from 8 to 135). Selecting the Right Diamond Concentration can be critical in optimizing your Diamond Drilling Operation. Selecting Optimum Diamond Concentration for your application will depend on a large number of factors, such as:
-
Material Being Drilled
-
Diamond Drill Bond Type and Hardness
-
Diamond Mesh Size
-
Drilling Speeds
-
Coolants being used
Diamond Concentration will play a major role in determining the life and drilling speed of your Diamond Drill. Higher diamond concentration is recommended and usually used for cutting softer and more abrasive types of materials. However, the trade off is significantly slower drilling speed. Low diamond concentration is recommended and widely used for drilling ultra hard and brittle materials. Optimum performance can be achieved when the diamond tool manufacturer utilizes their experience and analytical capabilities to balance diamond concentration and other factors to achieve optimum performance for the diamond drill/bit user. UKAM Industrial Superhard Tools has the experience & applications laboratory to help you select all the right variables for your unique application.
Wall Thickness – the thinner the wall thickness of your diamond drill/bit, faster the speed (RPM) your drill may run, less chipping and heat your drill generates, and smoother and higher quality of the finish. Thin wall diamond core drills provide the following advantages:
-
less loss of material
-
minimum material deformation
-
less heat generation
-
faster drilling speed
-
less chipping
-
better finish quality
The trade off is shorter diamond drill life. Thin wall diamond core drills will wear much faster thicker wall diamond drills. UKAM Industrial Superhard Tools has the capability to manufacture diamond core drills with wall thickness as ULTRA THIN as .003" (76 microns) to as thick as .236" (6mm) & as thick as you want
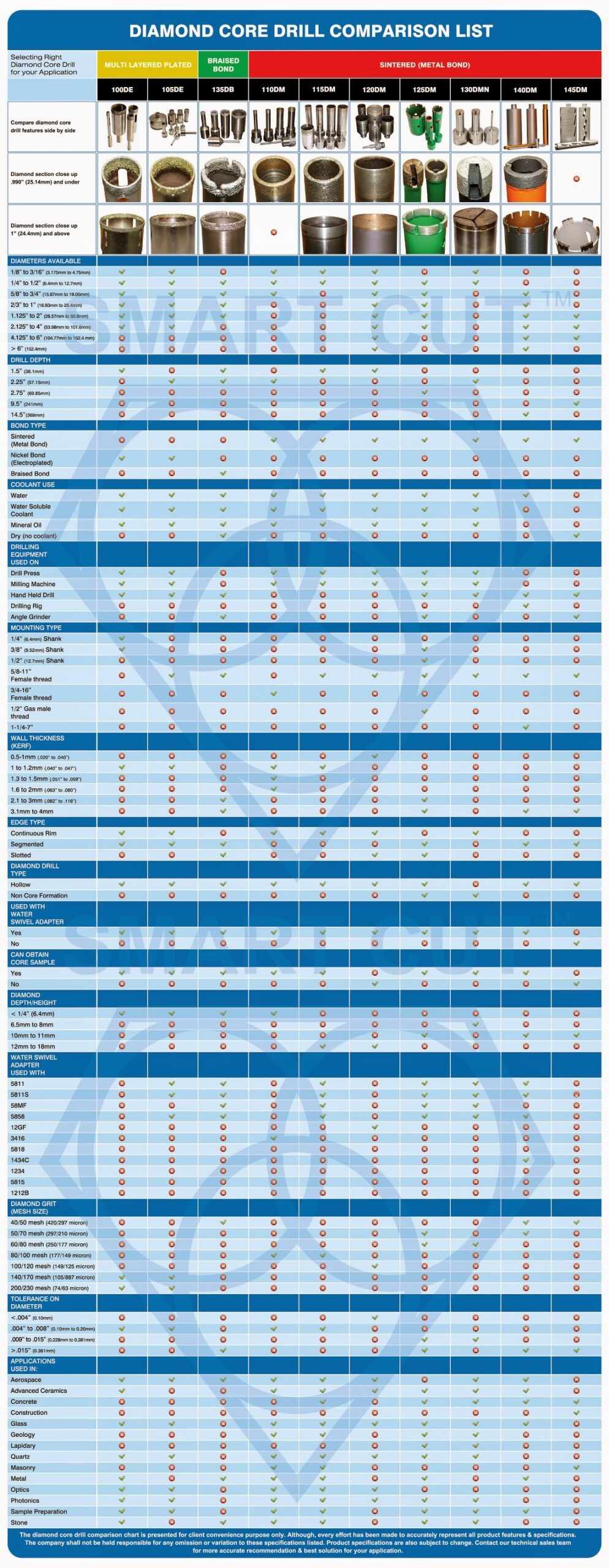
DIAMOND DRILL SELECTION PARAMETERS
Wall thickness
-
Ultra thin wall (.010” to .020”)
-
Very Thin Wall .021” to .040”
-
Thin Wall (.041” to .060”)
-
Standard Wall (.061” to .100”)
-
Heavy Wall (.100”+)
Diameter
-
.001” to .005”
-
.006” to .030”
-
.031” to .124”
-
.125” to .500”
-
.501” to 3.99”
-
4.0” to 11.99”
-
12.00” +
Bond Type
-
Nickel bond (Electroplated)
-
Sintered (Metal Bond)
-
Braised Bond
-
Chemical Vapor Deposition
-
Polycrystalline
Mounting Type
-
2.35mm straight shank
-
3mm straight shank
-
6mm straight shank
-
¼” shank
-
3/8” straight shank
-
½” straight shank
-
5/8-11”
-
1-14" Female Thread
-
1/2" Gas Male (Belgium Mount)
-
3/4-16" Female Thread
-
1-1/4-7" Female Thread
-
M14 Male Thread
-
5/8-18" female thread
-
1-1/2-12"
-
2-1/2-12"
-
Jacobs mounting
-
Habit mounting
Coolant Used
-
Yes
-
No
-
Tolerances on diameter or ID
Tolerances
-
Tolerances on Outside Diameter
-
Tolerance on Inside Diameter
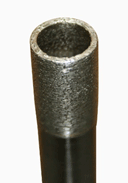
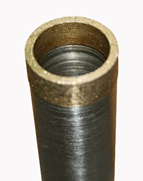
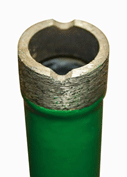
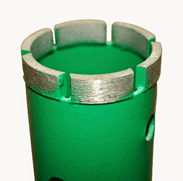
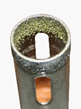
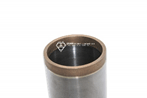
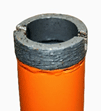
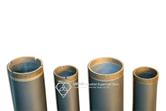
DIAMOND CORE DRILL / BIT DESIGN
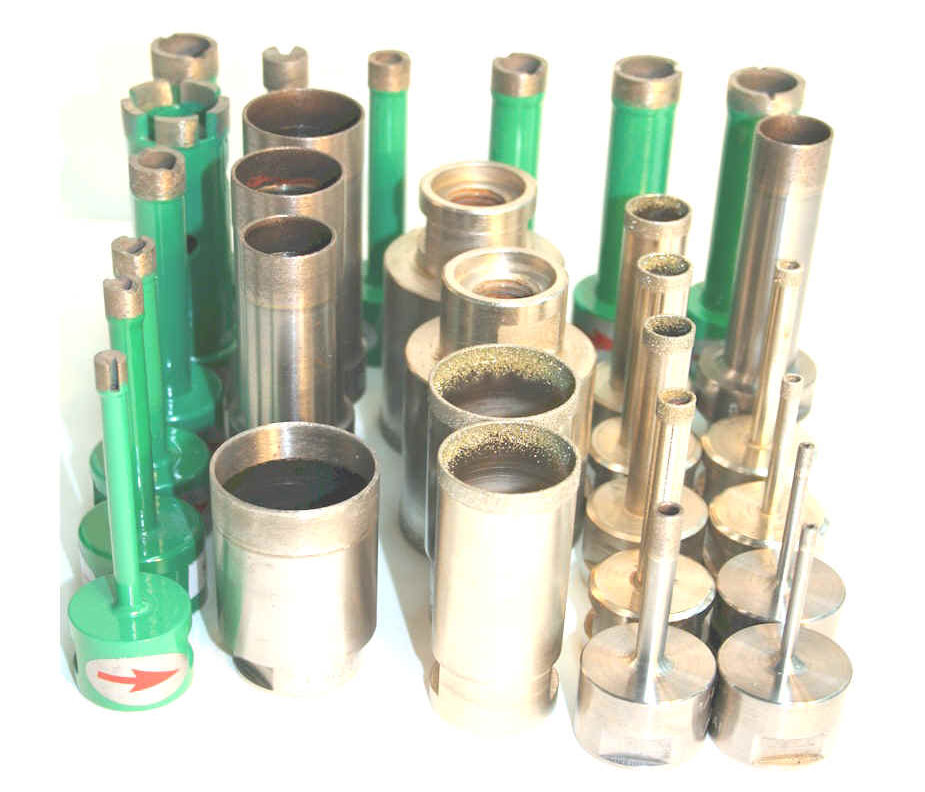
UKAM Industrial Superhard Tools manufactures & stocks Diamond Drills/Bits to customer desired specifications, outside & inside diameters, drilling depths, bond types, diamond grit sizes, mountings, & tolerances. Below is a diagram (technical drawing) that will help you better understand different diamond drill/bit specifications that can be altered based on your requirements.
Diamond Core Drill/Bit Mounting Methods: Diamond Drills/Bits must be either mounted on a collet or made with straight shank. Diamond Drills mounted on a collet can be used with water swivel adapter to run high pressure of coolant through center of drill. Diamond drills with straight shank are meant to be placed in drilling machine chuck and cannot be used with water swivel adapter. We recommend using diamond drills/bits that are mounted on a collet. You can always purchase a shank adapter that will thread into the collet, that will convert your diamond drill into a straight shank mounting. Various industries used different collets (mounting methods).
Most often used collets are 5/8-11", 5/8-18, 1-14, 3/4-16, 7/8-14, 1-1/4-7", BRANSON (Ultrasonic) and Others. Standard shank sizes are usually 1/4", 3/8", and 1/2" diameter.
DIAMETERS:
D = Outside Diameter D1 = Inside Diameter D3 = Shank Diameter
D4 = Shank Inside Diameter
HEIGHTS:
H = Total Drill Length H1 = Diamond Depth (diamond height) H2 = Drilling Depth (how deep you can drill) H3 = Shank Length
THICKNESS:
TH = Drill Tube Wall Thickness TH1 = Outside Diameter Diamond Section Relief TH2 = Inside Diameter Diamond Section Relief
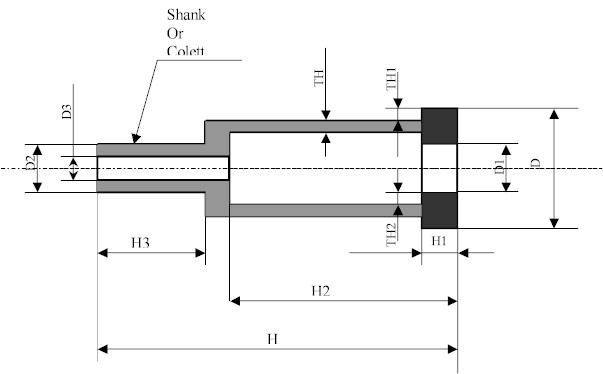
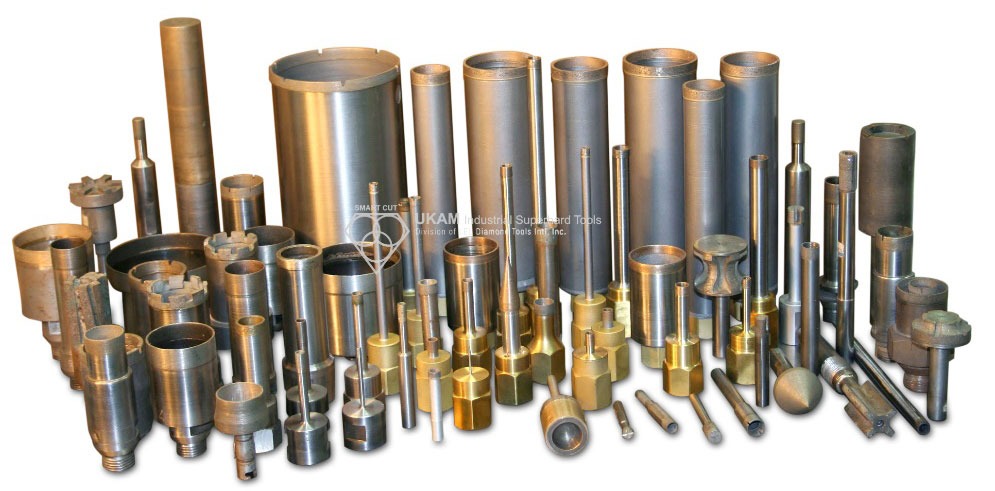
Diamond Core Drill Types:
Diamond Solid Drill/Tool Types:
-
diamond hollow core drills unmounted (tube only)
-
diamond hollow core drills mounted (with female or male thread or straight shank per client spec)
-
ID Core drills
-
non core formation
-
bottoming drills
-
diamond dual core drills.
-
disintegrating drills
-
diamond chamfering tools
-
diamond seamers
-
diamond hole saws
-
ultra thin wall diamond core drills
-
thin wall diamond core drills
-
standard wall diamond core drills
-
heavy wall diamond core drills
-
Continuous Rim (Crown) Diamond Core drills
-
Slotted diamond core drills
-
segmented diamond core drills
-
diamond core drills for ultra sonic drilling machines
-
concrete & construction diamond core bits
-
diamond carving points
-
diamond mounted points
-
diamond counter tools
-
diamond grinding pins
-
diamond routers
-
diamond ID grinding points
-
diamond jig grinding mandrels/pins
-
diamond countersinks
-
diamond counter bores etc
-
Diamond Milling Tools
-
Diamond Generating Tools
-
diamond face grinding tools
-
Diamond Chamfer Tools
-
Diamond Radius Tools
-
Diamond Profiling Tools
-
Diamond Ball Nose Tools
-
Diamond Round End Tools
-
Diamond Full Ball Tools
-
Diamond Bottom Grinding Tools
-
Diamond Bottom Grinding Tools
-
Diamond Reamers
-
Diamond Honing Tools
-
Diamond Tapered Hones
-
Diamond Threading tools
-
diamond endmills
-
diamond hole/bore finishing tools
-
diamond cone grinding tools
-
diamond burs for industry/hobby
-
Diamond Profile Tools
-
Diamond Radois Tools
-
Diamond Radius Tools
-
Diamond Chamfer Tools
-
Diamond expanding laps/mandrels
Diamond Reamers, Diamond Threading tools, Diamond Engraving Tools, Diamond Radius Tools, Diamond Chamfer Tools, & many other custom tools made to your specifications
These tools are used for many different industries grinding and shaping material into different forms, expanding exiting inside diameters, grinding, finishing and polishing existing material. Grinding different angles and radius, creating cavities of various forms, milling, deburring, Thread grinding.
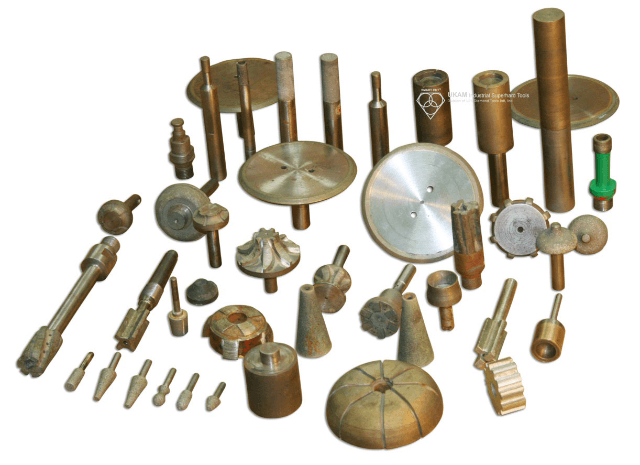
- Diamond carving points
- Diamond mounted points
- Diamond counter tools
- Diamond grinding pins
- Diamond routers
- Diamond ID grinding points
- Diamond jig grinding mandrels/pins
- Diamond countersinks
- Diamond counter bores etc
- Diamond Generating Tools
- Diamond Milling Tools
- Diamond face grinding tools
- Diamond Chamfer Tools
- Diamond Radius Tools
- Diamond Profiling Tools
- Diamond Ball Nose Tools
- Diamond Round End Tools
- Diamond Full Ball Tools
- Diamond Bottom Grinding Tools
- Diamond Reamers
- Diamond Honing Tools
- Diamond Tapered Hones
- Diamond Threading tools
- Diamond hole/bore finishing tools
- Diamond cone grinding tools
- Diamond burs for industry/hobby
- Diamond Profile Tools
- Diamond Radois Tools
- Diamond Radius Tools,
- Diamond Chamfer Tools
- Diamond expanding laps/mandrels
- Diamond Engraving Tools & Diamond CNC Engraving Tools
Dual Diamond Core Drills
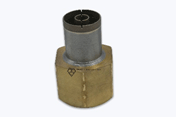
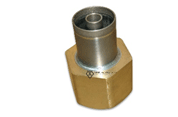
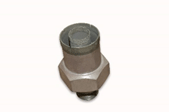
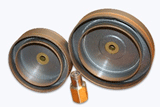
dual core drills are used to produce one single part/ring these will drill out the core and drill hole in material at same time hence increasing productivity and dimensional accuracy of different parts we can grind the outside and inside diameter of these tools to very high precision tolerances grind slots to improve cutting speed, and grind various radiuses
Non core formation Drills / Bottoming Drills
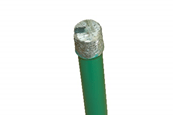
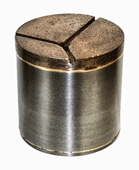
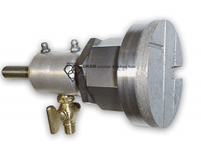
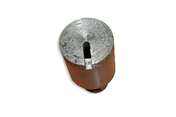
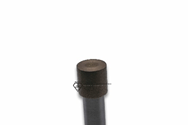
Diamond Bottoming Drills/Tools, sintered (metal bond) are used for making Blind Holes in all types of material ranging in hardness from sapphire, to quartz and slate. A bottoming tool does not have a core, and essentially works as both a diamond drill and grinding disc. The bottoming tools works by grinding the bottom and inside of the hole to a flat surface.
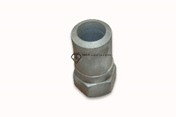

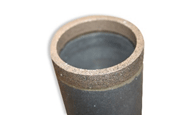
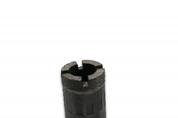
Off Centric Diamond Drill
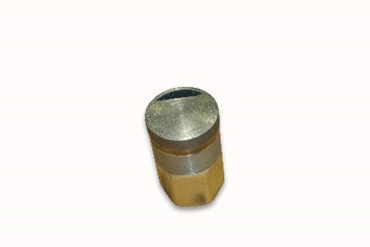
Designed with what is commonly called Half Moon shaped ID, allowing the core drill to move material and coolant at the same time as it drills the hole. ID (Inside Diameter) of the Diamond Drills/Bit is made larger (off center). OD (outside diameter) is made smaller to accomplish this purpose.
Non Coring / DISINTEGRATING ID Diamond Drill
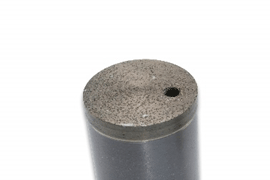
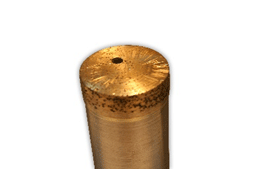
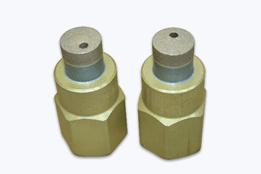
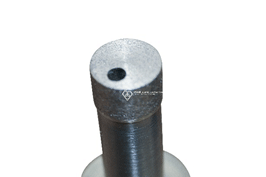
Inside diameter of this diamond drill is offset. It is still considered a diamond core drill because it has a slot on side for coolant to pass through center of the diamond drill. This type of diamond drill leaves no core behind (destroys core when drilling), because its ID (inside diameter) is Offset.
Diamond Countersinks, Diamond Counterbores, & Diamond Chamfer Tools
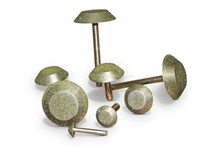
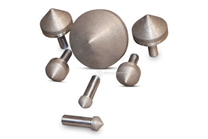
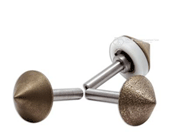
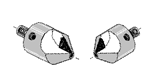
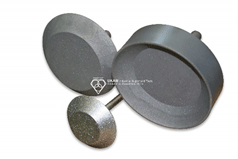
diamond & cbn countersinks are used to create conical holes, expanding existing holes, breaking corners and chamfering holes and polishing existing holes in large variety of materials. Available from stock in many specifications and we can also custom manufacture to fit almost any application/requirement.
diameters: .003” (75 microns) to 8” (200mm)
Angle/Radius: almost any
diamond bond types: Sintered (metal bond), Nickel Bond, Brazed Bond, PCD (polycrystalline diamond) , CVD (chemical vapor deposition) diamond
Diamond Drills & Tools for ultrasonic technology
Our ultrasonic tools for ultrasonic drilling, ultrasonic grinding and ultrasonic milling are, due to their technical properties, the solution for the ultrasonic processing of brittle hard materials. The bond hardness, the material of the bond matrix, the grain quality and the diamond concentration are designed so that they can withstand the additionally generated oscillating movement kinematics when using ultrasound.
Slotted Diamond Drill Design
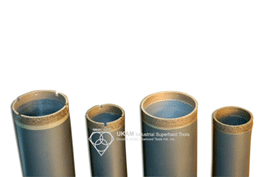
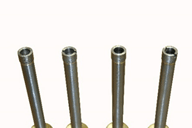


Making slots in diamond drill tip will usually make them drill faster and freer in hard materials. Slots help reduce diamond drill heat generation, and better propel coolant through the drilling zone. The width of slot depends on hardness of material. Diamond Drills manufactured for drilling harder materials require more slots than diamond drills made for softer materials. Slots are recommended for thick wall diamond drills, helping increase drilling speed and efficiency.
Find out more... What you should know before you buy your next diamond drill
For more & help on selecting the right diamond drill for your application. Contact UKAM Industrial Superhard Tools Engineering Department at Phone: (661) 257-2288.
Understanding Material Hardness & its Affect on Diamond Drill/Bit Performance
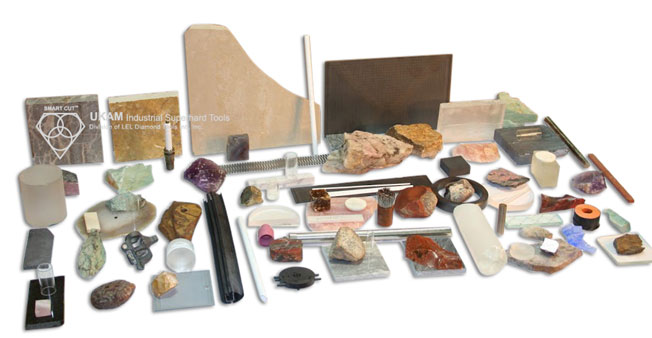
Material Hardness has several meanings. Most common definition for material hardness refers to its ability to resist deformation. Scientifically hardness is defined by energy density (energy per unit volume) required to create strain in material. While there are many ways, scales, and classification schemes to measure material hardness. In this article we will address the most simple explanation.
Mohs scale of Abrasion Hardness is the most simple and well known material hardness measurement and classification methods. In this scale material hardness is measured by scratch test of rubbing each material against another. All material harnesses are arranged in 10 ranks. Each rank is calibrated by a standard mineral. Below find these minerals in their rank of hardness from softest to hardest.
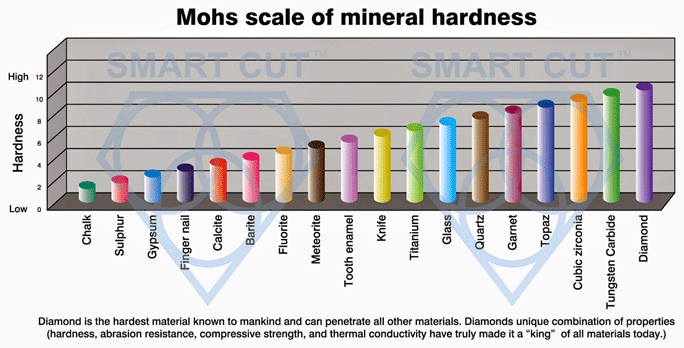
Mohs Scale of Hardness
1 Gypsum
2 Calcite
3 Fluorite
4 Apatite
5 Orthoclase
6 Quartz
7 Topaz
8 Corundum
10 Diamond
Hierarchy of Material Hardness
Hierarchy
Rank
Examples of Minerals / Materials
Ultrasoft
< 5
graphite, salt, talc, lead, teflon
Soft
5-8
silver, copper, calcite, fluorite
Normal
8-10
magnesia, glass, steel, quartz
Hard
10-12
WC, SiC, Al203, Si3N4, B4C
Superhard
> 12
cubic boron nitride, Diamond
Proposed Scale of Hardness for Industrial Materials
Material
Formula
Mohs Hardness
Knoop Hardness
Rank
Industrial Hardness
Graphite
C
1 -
12
3.6
3
Molybdenite
MoS2
1 -
17
4.1
4
Aluminum, annealed
Al
2 -
25
4.6
Table Salt
NaCl
2
30
4.9
Gypsum
CaSo4
2
32
5.0
Silver
Ag
2+
60
5.9
6
Mild Steel, annealed
Fe
2+
123
6.9
Calcite
CaCO3
3
135
7.1
7
Copper
CaCO3
3
135
7.1
7
Indium Antimonide
InSB
4+
220
7.8
8
Magnesia
MgO
5-
370
8.5
Glass
Soda lime
6-
530
9.0
9
Tool Steel
Fe
6+
700
9.5
9
Quartz
SiO2
7
820
9.7
Chromium
Cr
7
935
9.9
Zirconia
ZrO2
8-
1160
10.2
10
Cemented WC
WC-Co(8%)
8-
1200
10.2
Beryllia
BeO
8-
1250
10.3
Silicon
Se
8
1400
10.5
Titanium nitride
TiN
9-
1800
10.8
Corundum
Al203
9
2100
11
11
Silicon Nitride
Si3N4
9
2100
11
Tungsten Carbide
WC
9+
2400
11.2
Titanium Carbide
TiC
9+
2470
11.3
Silicon Carbide
SiC
9+
2880
11.5
Boron Carbide
B4C
9+
3000
11.6
Sintered cBN
BN
10-
3200
11.6
Cubic boron nitride
BN
10-
4800
11.6
12
Sintered diamond
c
10-
5000
12.3
Diamond (Type IIa)
c
10
9000
13.1
13
Understanding Diamond Drill/Bit Bond Types & their Application
DIAMOND DRILL & CORE DRILL BOND
Table of Comparison
Diamond Drill Types | Sintered (Metal Bond) | Nickel Bond (Plated) | Braised Bond | Chemical Vapor Deposition |
![]() | ![]() | ![]() | ![]() | |
![]() | ![]() | ![]() | ||
SEM Bond Cross Section | ![]() | ![]() | ![]() | |
BOND ILLUSTRATION | ![]() | ![]() | ![]() | |
Application |
|
|
|
|
Bond Characteristics | multiple layers of diamonds impregnated inside the metal matrix Provide longest life compared to all the other bond families. Sintered (metal bond) drills wear evenly, and are known for their long life & consistency. Used in vast majority of cutting applications. | have a single layer of diamonds, held by a tough durable nickel alloy. diamond particles to protrude from the bond matrix, providing a free, faster cutting action with minimum heat generation | Brazed Bond Diamond Drills are produced inside vacuum oven at a high temperature, single layer of diamond crystal bonded to steel body with very high diamond exposure | CVD diamond coating takes place in a vacuum chamber using a hot-filament, chemical vapor deposition (CVD) process. The crystalline diamond slowly grows on the surface of cutting tools (usually made from carbide) forming a continuous coating of up to 20 microns in thickness. |
Advantages |
|
|
|
|
(Diamond/CBN) Sizes Avaialble | 25 mesh to 8,000 mesh (375 micron to 3 micron | 25 mesh to 8,000 mesh (375 micron to 3 micron) | 25 mesh to 600 mesh (375 micron to 30 micron) | |
Diamond Concentration | 25 to 200 con | 100 to 250 con | 100 to 250 con | |
Smallest Diameter Available | .006” (.15mm) Solid & .020” (0.5mm) hollow | .002” (.050mm) solid & .010” (0.25mm) hollow | .040” (1mm) | .001” (.025mm) |
Coolant Used | Should be used with synthetic water soluble coolant or mineral oil, or water at minimum for many applications | can be used without coolant in many applications | Can be used dry (without any coolant) for most applications | Can be used both with and without coolant depending on material being drilled and drilling depth |
Drill Life | Longest | Shortest | Medium | |
Drilling Speed | Fast | Fast | Very Fast | Medium |
Cost | Medium | Lowest | Lowest | Medium |
Sintered (Metal Bond) Diamond Drills
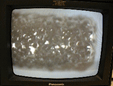
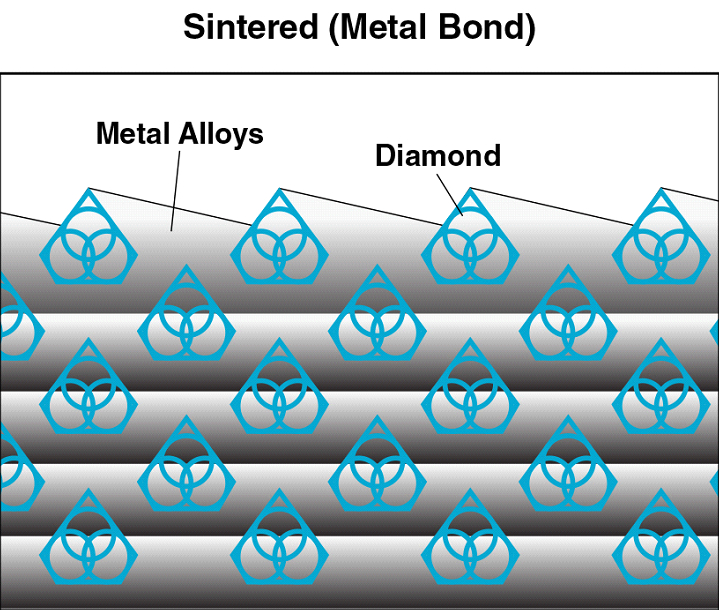
Metal bonded diamond core drills have diamonds sintered and multiple layers of diamonds impregnated inside the metal matrix. Diamonds are furnaces sintered in a matrix made of iron, cobalt, nickel, bronze, copper, tungsten, alloys of these powders or other metals in various combinations. Metal Bonded Diamond Tools are “impregnated” with diamonds. The compacted materials are then hot pressed or sintered to full density. Heating rate, applied pressure, sintering temperature and holding time, are all controlled according to the matrix composition.
This means that selected diamonds are mixed and sintered with specific metal alloys to achieve the best cutting performance possible on any materials such as sapphire, advanced ceramics, optics, glass, granite, tile and etc. The metal bond surrounding the diamonds must wear away to continuously keep re-exposing the diamonds for the diamond tool to continue cutting.
Sintered (metal bonded) diamond tools are recommended for machining hard materials from 45 to 75 on Rockwell Scale (5 to 9.5 on mohs scale of hardness). As a general rule of thumb, Metal Bond (sintered) diamond drills last longer than other diamond drills available.
They can be used in almost all diamond drilling application ranging from very soft & abrasive materials to ultra hard materials. Typical applications include in order from hardness: Composites, Glass, Concrete, Sandstone/flagstone, Natural Stone, Optical Materials, Precious & Semiprecious stone, Advanced/Technical Ceramics, Advanced Materials, & Many Others. Sintered (metal bonded) diamond drills/bits are used & preferred in most Industrial/Manufacturing, R & D, Professional Contractor, & Serious Hobby Enthusiast / Craftsmen users. Sintered (metal bond) diamond core drills/bits are most widely used diamond drills across almost all industries & applications. They wear evenly, and are known for their long life & consistency. Precision & Accurate tolerances either on OD, ID, Run Out & Concentricity can only be obtained with sintered (metal bond) diamond drills.
Sintered (metal bond) diamond core drills/bits Require PROPER USE & SOLID UNDERSTANDING of Proper Diamond Drill/Diamond Tool Principals. Experience well help as well. Careless handling or use in imprecise machinery will result in diamond drill wrecking/breaking, bending or cracking the bond and will prevent future use.
Drilling life will vary with manufacturer & application/material factors described in this guide below. While there is no way to accurately predicting diamond drill life, with most conventional sintered (metal bonded) diamond drills, you can expect 350 to 1200 holes, parts machined, or cores. In laboratory tests, Diamond Drills with SMART CUT™ technology have shown to last 2,000+ holes on many applications/materials. Sintered (metal bonded) diamond core drills/bits with SMART CUT™ technology are the latest technology available in diamond drills. And represent the best value and performance per hole or part.
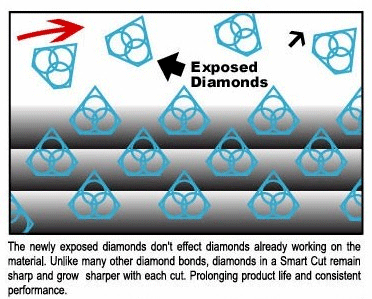
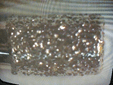
Electroplated (Nickel Bond) Diamond Drills
Electroplated Diamond Core Drills & Electroplated Thin Wall Diamond Core Drills have a high diamond concentration and maximum diamond particle (grit) exposure/protrusion ratio. This provides freer, faster drilling action with minimum heat generation. Electroplated Diamond Drills provide excellent performance on softer materials ranging from 6 to 1 on mohs scale of hardness. While electroplated diamond drills, specifically manufactured by UKAM Industrial, will still work on harder materials (up to 9 on mohs scale). Diamond drill life will be (very short) significantly reduced. Diamonds stay on the surface of the drill allowing for fast material removal. Perfect for softer, more ductile, and gummable materials.

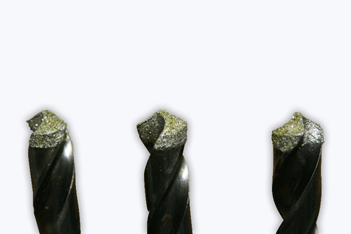


Not recommended for drilling very abrasive materials such as sandstone and concrete (they will wear out on these materials almost immediately). Electroplated Diamond Drills last less than metal bond, hybrid bond drills and are the least expensive diamond drills available. They provide very smooth surface finish quality & less thermal damage to the part being drilled.
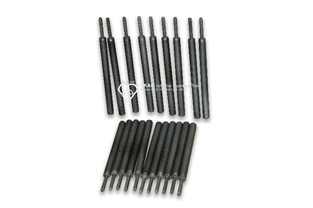
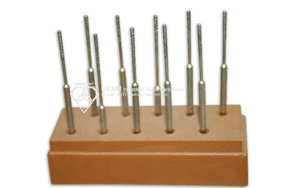
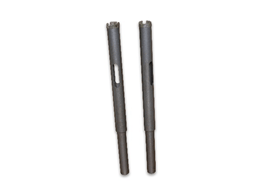
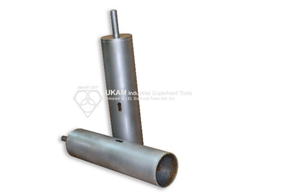
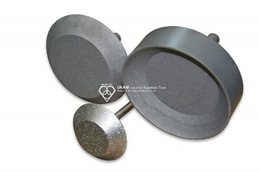
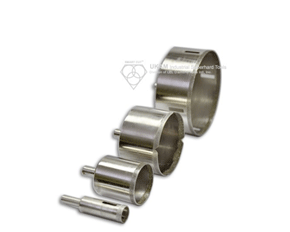
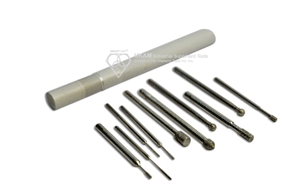
Electroplated diamond drills are frequently used in glass and composite industries (as well as some photonics / optics) applications. Electroplated Diamond Drills are designed for small & occasional use. They are widely used by beginning diamond drill users (novices) in numerous hobby/craft applications. As well as home owners and contractors requiring to drill a few holes when installing tile, marble, shower doors, glass mirrors, and etc. (not recommended for professional or serious industrial use). They are also usually more forgiving to operator/user drilling mistakes than most other types of diamond drills/bits. Electroplated core drills are just about the only type of diamond drill that may be used dry (without coolant) in a few applications if needed. Best performance and results will be achieved when drilling less than 1/4" (6.35") into material. Performance in many applications will decline when drilling thicker materials.
Brazed Bond Diamond Drills
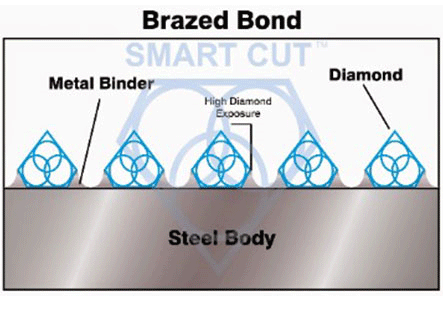
Brazed Diamond Diamond Drills are produced using and process that creates a fusion between the diamonds and the metal bond. While they may appear similar to electroplated (nickel bond) diamond drills. They are produced utilizing completely different process. Brazed Bond Diamond Drills are produced inside vacuum oven at a high temperature, single layer of diamond crystal bonded to steel body with very high diamond exposure.
Not only does it promote high diamond exposure, but it also eliminates the loss of diamond particles through pull-out. The diamond section will not strip or peel from the steel body. This translates into multiple benefits, including: aggressive tools that last longer, cut faster, run cooler and load less, providing increased productivity and part consistency.
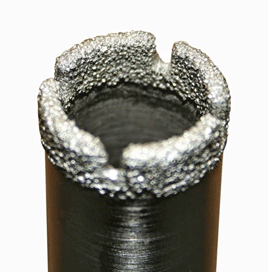
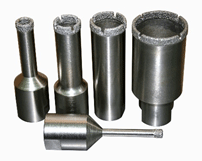

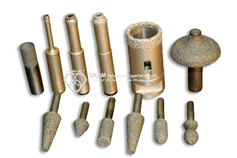
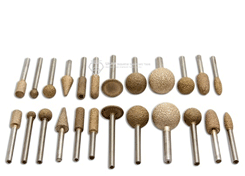
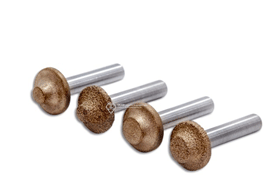
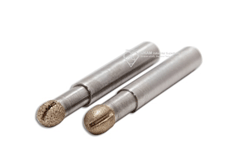
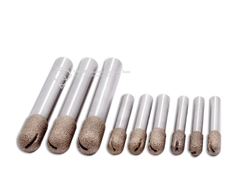
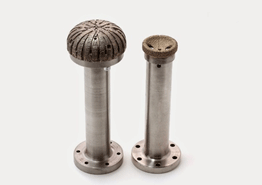
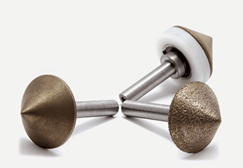
Brazed Bond Diamond Drills are perfect for drilling and machining tough-to-cut materials where fast stock removal and deep cuts are required. Including applications such as: non-metallic materials such as graphite epoxy, FRP, graphite, fiberglass, friction material, honeycomb and other composites.
PCD (Polycrystalline Diamond) is composed of diamond particles that are sintered with a metallic binder at extreme temperatures and pressures, creating the hardest and one of the most abrasion resistant materials used in cutting tools. These inserts are braised on to cutting tools and are used in machining applications in many applications where you find carbide tooling that includes sawing, routing, drilling and profiling to maximize tool life and reduce production cost
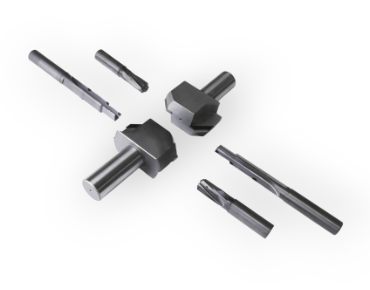
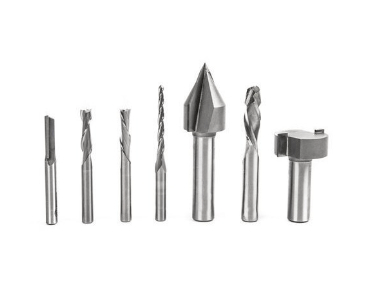
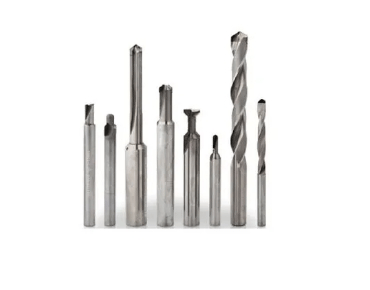
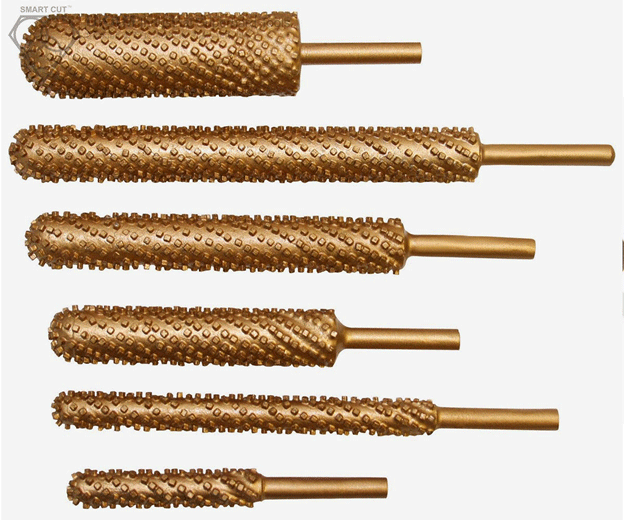
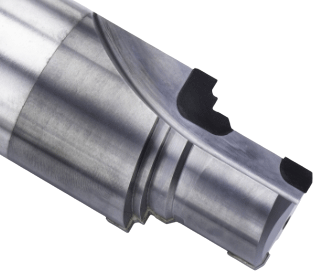
Application of PCD & Tools
PCD tools are used for processing aluminum and aluminum, aluminum alloys, copper, copper alloy, babbitt metal, wood, wood based fiber materials, aluminum oxide, reinforced floor boards, wear resistant plastic, Bakelite, graphite, stone materials, tungsten carbide, hard cartons. Epoxy resins, Fiberglass composites, Carbon-phenolic, Hard rubber, Plastics, Ceramics (unfired), Graphite
PCBN cutting tools are used for hardened steel, tool steel, mold steel, bearing steel, chilled cast iron, high chromium cast iron, nickel based high temperature alloy, gray cast iron, zinc alloys, sintered tungsten carbide & many other nonferrous materials that are difficult to machine. Find Out More about PCD Diamond & CBN Tools >>>
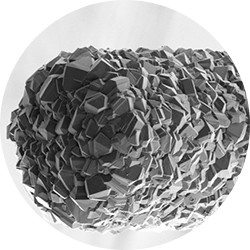
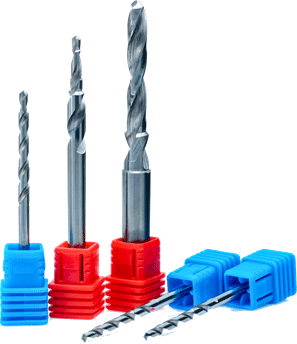
CVD (Chemical Vapor Deposition) Diamond Drills
CVD Diamond Drills - CVD diamond coating takes place in a vacuum chamber using a hot-filament, chemical vapor deposition (CVD) process. Carbon gases are introduced into the vacuum chamber where high temperatures cause carbon atoms to re-bond into a 100% pure crystalline diamond structure. The crystalline diamond slowly grows on the surface of cutting tools (usually made from carbide) forming a continuous coating of up to 20 microns in thickness. Standard carbide tooling with this type of coating depending on application will last 10 to 50 times longer.
Application of CVD Tools
Used on softer and gummy materials where usually tungsten carbide tooling is used by wears out or has to be reshaped quickly. Applications such as machining graphite, hard carbon, green ceramic, carbon fiber, reinforced polymers, fiberglass, plastics, wood laminates, non ferrous metals Find Out More about CVD Diamond Tools >>>
Evaluating Diamond Drill/Bit Performance
The performance of a diamond drill/bit for just about any application / material can be evaluated under various criteria. The importance of any criteria depends on your requirements.
Diamond Drill Life - The life of a diamond drill/bit is determined by the number of holes or it can drill (parts machined). It is fairly difficult to estimate the life of diamond drill. Diamond drill life is affected by various factors such as the application, bond type, drill manufacturer, and experience of user in properly using the drill. Diamond drill life will be discussed in further detail in this guide below. The following considerations play a major role in diamond drill life:
-
hardness and abrasiveness of the material being drilled
-
speed and power of drill
-
amount of pressure used (feed rate)
-
proper use of coolant (type of coolant, coolant force, & direction)
-
Drilling Depth
-
Material Holding Method
-
operator experience (Understanding Proper Diamond Drill Usage Principals and Adjusting them as need to better fit their particular application & objectives)
-
overall age and condition of drilling equipment (precision, accuracy, & repeatability of drilling equipment used)
-
quality, hardness, sharpness, and mesh size of the diamonds
-
hardness of the bond compared to the material being drilled
-
experience and technology of manufacturer in keeping diamonds in the bond
Surface Finish Quality - The quality of the surface finish is evaluated by the amount of chips generated on the face of the material. Surface finish consists of three basic components: form, waviness and roughness. Although there are more then 100 ways to measure a surface and analyze results. A visual check is the most simple & easiest way of measuring (checking) surface finish quality. The most common scientific way of measuring surface finish quality is using Ra, or Arithmetic Average Roughness. It basically reflects the average height of roughness component irregularities from a mean line. Ra provides a simple value for accept/reject decisions.
Break in time - A diamond drill requires time to break in, to produce relatively chip free performance. The period of time under which this occurs, separates one diamond drill/bit from another.
Frequency of Dressing - The less you have to dress your diamond drill, the better off you will be.
UNDERSTANDING DIAMOND DRILL LIFE & PERFORMANCE
How many holes will this diamond drill last?
Why did my diamond drill wear out after only ....
the list of questions goes on. These are just some of the typical questions that our engineering staff answers every day. To help you better understand the factors & variables that play a major role in life/performance of your diamond drill/bit we have written an explanation below. We hope you will find this guide helpful.
Material Hardness + Density + Drilling Depth + Material Shape/Geometry + RPM's + Feed Rate + Coolant Used + Drilling Equipment Type/Condition + Material Holding Method + Operator Experience
DIAMOND DRILL LIFE & OVERALL PERFORMANCE
Diamond Drill Life & Overall Performance will vary with material hardness, density, Drilling Depth. Few other factors that play a role in diamond drill life include: RPM's (drilling speed), Feed Rate, Geometry (shape) of Material, Coolant being Used, Coolant feed rate and Direction. Drilling Equipment, Material Clamping Method & experience of operator. While there is now way of accurately predicting Life of your diamond drill. It can be optimized by following Principals of Proper Diamond Drill / Tool Usage. There may also be some experimenting, as well as trial & error involved in the part of the end user. Highly experienced diamond drill users may find some variations in diamond drill life or performance even when working on same material & application for several years. While this phenomena is not too common, it does occur. The machining environment around us is constantly changing. A slight change or variation in any variable can have significant impact on your diamond drilling results. Material being drilled can vary in composition or density even when coming from same manufacturer or source.
Slight change in coolant feed rate, coolant direction, RPM's, even the way the material is held in place can make the difference. Frequently the cause of the problem may not be obvious and may take as much as several failed attempts to surface. Fore more information on optimizing your Diamond Drilling Operation to ultimate level of performance >>>
When encountering problems or variation in diamond drill performance. Few stop to think about or carefully examine their drilling process. Many users immediately suspect quality of the diamond drill and are quick in labeling the drill "Defective" or "Poor Quality". This is very rarely the case. Usually in over 90% of these cases the diamond drill itself was not at fault. Most Respectable & Experienced Diamond Drill Manufactures have rigid quality control and inspection processes set in place. Controlling everything from raw material input, output, to final inspection. What a number of diamond drill users don't realize the technical aspects & delicate nature of diamond drilling/machining process. Unlike carbide, high speed steel, & other types of drills. Diamond drill works by grinds away material on micro (nano) level. Carbide and other types drills on the other hand cut material with a sharp cutting edge. A simple example of the minute details and understanding that play a major role in your diamond drilling process. What is important to understand is that almost all diamond drill/bit users, regardless of experience or technical background will make some type of an unintended operator error while using their diamond drills/bits. With this in mind, UKAM Industrial Superhard Tools has assembled a list of most common diamond drill operator errors made by users in all industries & applications. Looking through this guide will help you RESOLVE MOST COMMON DIFFICULTIES you may have in using your diamond drills/bits, as well as AVOID MOST COMMON PROBLEMS in the first place. DIAMOND DRILL / BIT TROUBLESHOOTING GUIDE >>>
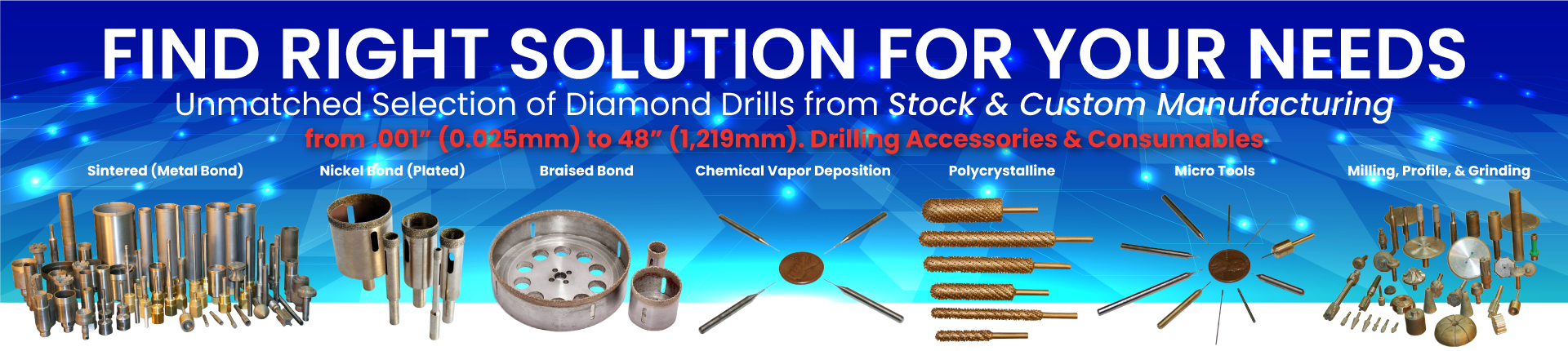
ARE YOU USING RIGHT DIAMOND CORE DRILLS & TOOLS
FOR YOUR APPLICATION?
LET US
HELP YOU
HAVING ISSUES WITH
YOUR CURRENT DIAMOND CORE DRILLS & TOOLS?
Knowledge Center
Select right Diamond Drill for your application
How to Properly Use Precision Diamond Drills
Diamond Drills Guide
Diamond Tools Guide – Selecting Right Drills & Tools for your application
Optimizing your Diamond Drilling Operation
Micro Drilling Guide
Selecting Right Drilling Equipment for your Application. What you features & functionality you should look for?
Diamond Core Drill & Drill Trouble Shooting Guide
Understanding & Calculating Return on Investment for Diamond Core Drills & Other Tools
Understanding Tradeoffs – Searching for Perfect Diamond Drill & Tool
Why Use Diamond Drills?
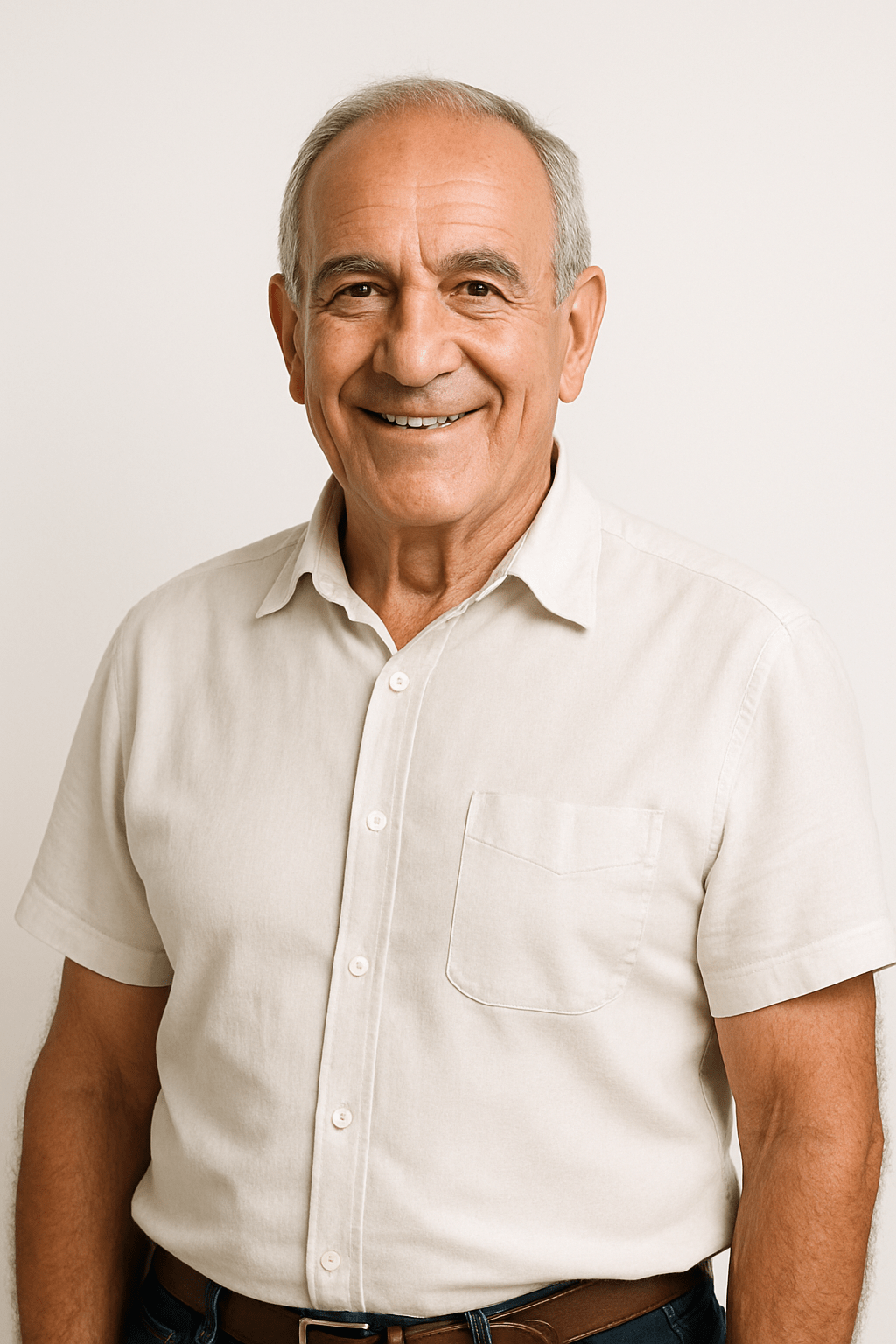
Leon Meyer is a veteran manufacturing engineer and technical consultant with over 50 years of experience in the development, implementation, and troubleshooting of industrial diamond tooling systems. Having spent his career at the intersection of tool design, precision manufacturing, and production engineering, Mr. Meyer is widely regarded as one of the most experienced voices in the application of ultra-thin diamond blades, sintered core drills, and CBN grinding wheels across heavy industry, advanced materials, and research sectors.
Known for his pragmatic, no-nonsense approach, Leon has advised manufacturers across the United States, Europe, and East Asia—helping streamline cutting processes, extend tool life, and solve complex issues related to material breakage, chipping, and tolerance drift. His expertise has directly contributed to improved production efficiency in industries ranging from aerospace alloys and technical ceramics to optics, composites, and high-nickel superalloys.
As an author, Mr. Meyer brings a lifetime of field knowledge to his writing, with a focus on real-world problem solving, cost-performance optimization, and tool reliability under demanding conditions.